Wavelength Electronics QCL500 LAB User manual

USER GUIDE
Low-Noise QCL Driver — Laboratory Series1
Firmware versions 1.5 and later operate with the
LabVIEW Virtual Instrument application and the Remote Command Set
ORDERING INFORMATION
PART NO DESCRIPTION
QCL500 LAB 500 mA Low Noise QCL Instrument
QCL1000 LAB 1.0 A Low Noise QCL Instrument
QCL1500 LAB 1.5 A Low Noise QCL Instrument
QCL2000 LAB 2.0 A Low Noise QCL Instrument
NOISESCAN Noise Characterization Scan
55-110014 SMA-BNC Cable
55-110015 USB Cable
WCB310 Shielded SMA-SMA Cable
QCLTL-LO Resistive Test Load for QCL500 or
QCL1000
QCLTL-1500 Resistive Test Load for QCL1500
QCLTL-2000 Resistive Test Load for QCL2000
RCKMT-LABSNGL 19” Single Unit Rack Mount Kit
RCKMT-LABDUAL 19” Double Unit Rack Mount Kit
INTLK REPL KIT
(included with purchase)
Interlock Replacement Kit with BNC
terminator and modied D-SUB
connector to override interlocks
e
Pb
RoHS
Compliant
Applies to Product Revision A,
rmware 1.5 and later
© Apr 2023
1Covered by U.S. Patents 6,696,887; 6,867,644 and 7,176,755. Licensed from Battelle Memorial Institute
The datasheet for the QCL LAB Series Firmware Version 0.79 (compatible with the QuickConnect Application) is located at:
www.teamwavelength.com/download/datasheets/qcl-lab079.pdf
QCL
TABLE OF CONTENTS
GENERAL OVERVIEW 2
SAFETY 3
QUICK CONNECT GUIDE 4
PIN DESCRIPTIONS 6
ELECTRICAL SPECIFICATIONS 7
OPERATING INSTRUCTIONS
(STAND-ALONE) 9
REMOTE OPERATING INSTRUCTIONS 16
TROUBLESHOOTING 17
ADDITIONAL TECHNICAL NOTES 20
MECHANICAL SPECIFICATIONS 22
CE DECLARATION OF CONFORMITY 23
WARRANTY & CERTIFICATION 24
PAGE

2
• Output currents of 500 mA, 1 A, 1.5 A, 2 A
• Low noise: <0.4 μA RMS up to 100 kHz
(QCL500, typical)
• Compliance voltage is adjustable, 10 to 20 V
(NOTE: The unit will only deliver the voltage
that the load requires, up to the compliance
voltage limit.)
• Analog modulation up to 2-3 MHz
• Analog modulation input between
-5V and +5V
• Constant Current Mode operation
• Touchscreen with intuitive user interface
• CE compliant, compatible with CDRH laser
regulations
• Feature-rich for research projects
»USB and Ethernet interfaces with software
included
»Auto voltage/current scan function
»Data collection using a computer or USB
ash drive
»Field upgradeable rmware
»Sophisticated error handling
»Save and recall functions for specic set
ups
• Rack mountable: 2 U height and ½ rack width
• Safety features protect your QCL investment
»Adjustable soft-clamp current limit, with
Brick-Wall Never-Exceed circuitry
»Password protection available to lock out a
selectable control set
»Keyswitch, active, and passive interlocks
»Brown-out & overvoltage protection
»Power supply overcurrent protection
»Driver over-temperature protection circuit
»Relay shorts output when current is
disabled
»AC input and patented power supply
ltering
»2 second turn-on delay — adjustable
»1.5 msec current ramp
F E A T U R E S
GENERAL OVERVIEW
THE LOWEST-NOISE DRIVER
AVAILABLE
These low noise QCL instruments have the lowest current
noise density of any commercially available. Powering your
QCL with this patented1driver gives you narrow linewidth,
stable center wavelength, and repeatable scans.
INTUITIVE USER INTERFACE AND
SUPERIOR SOFTWARE CONTROL
With Wavelength’s plug and play instrument, you have the
ability to quickly set the controls using either the instrument or
a remote computer.
PROTECT YOUR QCL INVESTMENT
All the essential control and monitor functions you expect in a
Wavelength laser driver are incorporated into this instrument,
along with protection circuitry to safeguard your QCL from
minor power source faults, over-temperature conditions, and
electrical faults.
The soft-clamping current limit can be set without enabling the
driver output, and uses a brick-wall never-exceed limit circuit
to protect the QCL from potentially damaging overcurrent
situations.
OEM VERSION AVAILABLE
Once you have nalized your work, the QCL circuitry is
available in compact OEM versions.
APPLICATIONS
Due to their unique construction, QCLs operate with high
power in the near-IR through terahertz ranges. These
wavelengths are particularly suited to detection of molecules
signicant to humans.
Applications for the lower noise QCL driver include: remote
detection of explosive materials, medical diagnosis using the
breath, non-invasive glucose testing, emissions monitoring of
the atmosphere or marine environments, and pharmaceutical
process quality control. Additional applications include
anesthesia and hospital air quality monitoring, leak detection,
and remote imaging.
1Covered by U.S. Patents 6,696,887; 6,867,644 and
7,176,755. Licensed from Battelle Memorial Institute

3
SAFETY
DEFINITIONS
CHASSIS GROUND Symbol
CAUTION: A condition that has the potential to
cause damage to property or instrument.
WARNING: A condition that has the potential to
cause bodily harm or death.
GENERAL
• Observe all Cautions and Warnings both in the User
Guide and on the instrument.
• Use the QCL instrument as specied in this guide or the
protection provided by this instrument may be impaired
and the warranty will be voided.
• Use good laser safety practices when using the QCL
instrument.
• Before proceeding, it is critical that you take precautions
to prevent electrostatic discharge (ESD) damage to your
laser.
• Locking the instrument with the keyswitch disables the
output current. The key can only be removed when in the
LOCK position.
POWER CORDS
• This equipment is grounded through the AC power cord
grounding conductor.
• Use only the earth-grounded power cords that are
recommended in this user guide.
• Route power cords and other cables so that they cannot
be damaged.
• Position the QCL instrument in a location that makes it
easy to quickly disconnect the power cord.
• To avoid re hazard, use only the specied power cords
with the correct grounding, voltage, and current ratings.
FUSES
• Disconnect the power to the QCL instrument before
changing the fuses.
• To prevent damage to the QCL instrument when replacing
fuses, locate and correct the problem that caused the fuse
to blow before re-applying power.
• To avoid re hazard, use only the specied fuse with the
correct type number, voltage, and current ratings, and use
only the recommended replacement parts.
CAUTIONS
The QCL instrument has no user-serviceable parts.
Other than the fuses, the QCL instrument is not
designed to be maintained by the user nor does it
contain any parts that can be repaired by the user.
All maintenance and repairs must be performed by
Wavelength or the warranty will be void.
Use a soft cloth to remove dust from the QCL
instrument. Do not expose the QCL instrument to
any liquids, sprays, or solvents. To avoid electrical
shock, unplug the power cord before cleaning the
instrument.
Before connecting to the power source, make sure
the correct cables and voltage for your area are
set. The voltage selection is available on the back
of the instrument. See the Quick Start Guide for
instructions on changing the voltage.
WARNINGS
Position the QCL instrument so that access to the
Main Power On/O switch on the back panel is
easily accessed.
Do not use the QCL instrument if there is evidence
of damage from shipping; damaged equipment
can present signicant safety hazards. If you
suspect the QCL instrument is damaged, contact
Wavelength technical support before attempting to
operate the instrument.
To avoid electrical shock, use the recommended
earth-grounded power cables and properly earth-
grounded, 3-prong receptacles only. Failure to
follow this precaution can result in severe injury.
To avoid injury, do not tell the engineers how to
do their jobs. Let them muddle through until they
decide to read the User Guide.

4
QUICK CONNECT GUIDE
INSTALL FUSE & SELECT VOLTAGE
Figure 1. Fuse Box and Voltage Selector
1. On the back panel, locate the Fuse Box and Voltage
Selector receptacle. (See the Rear Panel diagram on
page 10 for the location.)
2. Insert a small athead screwdriver into the slot (1) at the
top of the receptacle and twist to open faceplate. The red
fuse drawer and fuses are located in the Ship Kit.
3. On the face of the fuse drawer are two voltage choices.
Based on your country, select the proper fuses to install.
VOLTAGE FUSE PART NUMBER
100-120 V 1.25 A, 250 V,
fast blow
Littelfuse 5 x 20 mm,
Part #02351.25HXP
220-240 V 0.63 A, 250 V,
fast blow
Littelfuse 5 x 20 mm,
Part #0217.630MXP
CAUTION: It is imperative that the correct voltage
is used. Serious damage can occur if the incorrect
voltage is selected.
4. Insert the fuses as shown in Figure 2, with a short fuse at
the contact end of the receptacle. Then, turn the drawer
until the correct voltage label is at the top and replace it
in the receptacle. Press rmly to make sure the drawer is
completely seated. It should be ush with the receptacle.
Figure 2. Fuse Installation and Voltage Selector
5. Close the faceplate, again pressing rmly until it is ush.
The correct voltage label is shown through the Voltage
Window (2) on the faceplate.
WIRE A TEST LOAD
Use of a test load is recommended for setup of the QCL
instrument. Use the Wavelength test loads listed on page 1, or
when building your own test load, a 10 Ω resistor with a 50 W
power rating is recommended for the QCL500, QCL1000,
and QCL1500. For the QCL2000, a 50 W 5 Ω resistor is
recommended.
• Install the test load by either connecting to the QCL SMA
port or wiring the load to PIN 5 and PIN 9 on the QCL
D-SUB as shown in Figure 3.
QCL
SMA QCL
1
1 NOTE: The SMA case is electrically connected to the QCL chassis.
QCL D-SUB
6789
12345
Figure 3. QCL Wiring Diagram
-V
Pin 9 QCL +
or SMA Outer Ring
Pin 5 QCL -
or SMA Center Pin
QCL Driver
Current Sink
QCL
Figure 4. QCL Polarity Diagram

5
SETUP INTERLOCKS
The Wavelength Interlock Replacement Kit includes a male
D-SUB with the passive interlock pins shorted and a BNC
terminator.
1. For the passive interlock, on the back panel, short PIN 1
and PIN 2 on the QCL D-SUB.
2. For the active interlock, on the back panel, insert a BNC
terminator in the ACTIVE LOCK BNC port.
3. On the front panel, the keyswitch must be on UNLOCK to
enable the current to the QCL.
TURN ON POWER
1. On the back panel, press the power switch to the |. The
front panel power button light pulses slowly.
2. On the front panel, press the Power button. The button
illuminates, the touchscreen activates, and the Control
screen is active.
3. The front panel displays dashes instead of digits until the
unit has nished its power-up sequence (~10 seconds).
SET LIMITS
1. Press to access the Limit Screen.
2. On the Limit screen, press the blue Limit Current value
and rotate the Adjustment knob to change to the desired
value. The instrument will beep when set.
NOTE: The Max Supply Voltage and Cable Resistance values
can be ignored for now.
ADJUST SETPOINT
1. Press to access the Control Screen.
2. Press the Setpoint current value and turn the Adjustment
knob to change it. The instrument will beep when set.
ENABLE CURRENT
Press the ENABLE button. There is a standard 2-second
delay before the button illuminates and the current ows.
SHUTDOWN THE INSTRUMENT
If the Enable button is illuminated, current is still owing to
the test load. Before shutting down, the current needs to be
turned o.
1. Press the Enable button. The button light will turn o and
current to the QCL test load will stop.
2. On the front panel, press the Power button. The
touchscreen will go black but the button light slowly
pulses blue to indicate that the back Power button is still
on. NOTE: Turning o only the front Power button puts
the instrument in Standby mode.
3. On the back panel, press the power switch to O.

6
PIN DESCRIPTIONS
QCL D-SUB
Figure 5. Female 9-Pin D-SUB
Table 1. QCL D-SUB Pin-Out
PIN DESCRIPTION
1, 2 Passive interlock pins (must be shorted to enable
current)
3 Chassis ground
4 Not used
5 * QCL- (negative)
6 Not used
7 Not used
8 Not used
9 * QCL+ (positive)
SHELL Chassis ground
* NOTE: Use Pins 5 and 9 for current to the QCL.
QCL SMA
QCL- (negative)
QCL+ (ground)
Figure 6. SMA Pin-Out
QCL POLARITY
-V
Pin 9 QCL +
or SMA Outer Ring
Pin 5 QCL -
or SMA Center Pin
QCL Driver
Current Sink
QCL
Figure 7. QCL Polarity Diagram
MONITOR D-SUB
Figure 8. Male 9-Pin D-SUB
Table 2. Monitor D-SUB Pin-Out
PIN DESCRIPTION
1 Alignment LED (+5 V) can source 250 mA
2 Alignment LED ground
3 QCL current enabled indicator (+5 V TTL)
high = disabled
low, ground = enabled
4 QCL current enabled indicator ground
5 Not used
6 Analog setpoint monitor
7 Analog monitor ground
8 Analog output current monitor
9 Analog monitor ground
BNC PINS
ACTIVE SIGNAL
GROUND
Figure 9. BNC Pins
TRANSFER FUNCTIONS BY MODEL
External modulation input, setpoint monitor, and analog
current monitor transfer functions:
QCL500 LAB: 0.1 A / V.
QCL1000 LAB: 0.2 A / V.
QCL1500 LAB: 0.3 A / V.
QCL2000 LAB: 0.4 A / V.
The input range is always -5 V to +5 V.
ACTIVE INTERLOCK BNC
Ground the center pin to the outer shell to override the interlock
and allow the current to ow to the QCL. If an external circuit
won’t be used, a 50 Ω or 75 Ω terminator is acceptable.
TRIGGER BNC
See Additional Capabilities on page 16.

7
ELECTRICAL SPECIFICATIONS
DRIVER OUTPUT CURRENT MIN TYP MAX UNITS NOTES
Output Current 0.5, 1.0, 1.5, or 2.0 A
RMS Noise Current 0.4 1.0 1.3 μA RMS QCL1000 at 500 mA output, 100 kHz test bandwidth
Noise Current Density 1 2 4 nA / √Hz QCL1000 at 500 mA, 10 Ω test load
Stability, short and long term 5 10 15 ppm 25°C ambient
Temperature Coecient 5 10 18 ppm / °C
Compliance Voltage Range 10 20 V
Internal Supply Voltage can be adjusted from the front
panel.
NOTE: With this current source, the voltage developed
across the load (laser) is not driven by the controller,
but by Ohm’s Law and the resistance of the load
(laser).
Slow Start Current Ramp (after
Enabled) 1.5 msec To setpoint
Delayed Start 2 sec User adjustable
EXTERNAL MODULATION MIN TYP MAX UNITS NOTES
Modulation Bandwidth 2 3 MHz Sinewave
Rise/Fall Time 250 / 200 nsec To full scale
Slew Rate 30 V / µsec
Depth of Modulation 90 % At 500 kHz
External Modulation Input
Range -5 to +5 V
Input Impedance 1 kΩ
External Modulation Input
Damage Threshold -10 to +10 V BNC Connector
MONITORS AND OUTPUTS VALUE UNIT NOTES
Setpoint Resolution 16 bits 5V = fullscale output
Display Accuracy Measurement
Resolution 24 Bits
Accuracy, Current Output
Monitor vs. Actual Current
(display or analog output)
0.2 % > 5% of full scale
0.5 % < 5% of full scale
Accuracy, Current Setpoint vs.
Actual Current
0.2 % Internal setpoint
0.2 % External modulation
Accuracy, Analog Setpoint
Monitor1
5 % >10% of full scale
25 % <10% of full scale
1Current Setpoint Monitor is a reference signal only, and may deviate from the actual setpoint by up to 5% when the setpoint is greater
than 10% of full scale.
CONTINUED ON FOLLOWING PAGE

8
POWER SUPPLY
REQUIREMENTS VALUE NOTES
AC Power Supply and Line
Frequency 100-120 / 220-240 VAC, 2 A, 50-60 Hz Switch selectable: 100-120 V and 220-240 V,
appropriate power cord supplied
Fuse for 220-240 V 0.63 A, 250 V, fast blow 5 × 20 mm, Part #0217.630MXP, Littelfuse
Fuse for 100-120 V 1.25 A, 250 V, fast blow 5 × 20 mm, Part #02351.25HXP, Littelfuse
Power Consumption 9.8 Watts At idle, no output to QCL load
GENERAL SPECIFICATIONS VALUE NOTES
Warm-up Time 1 Hour
Remote Interface USB, Ethernet
Warranty One (1) Year
Safety Tested To
IEC 61000-3-2
IEC 61000-3-3
IEC 61000-4-2
IEC 61000-4-3
IEC 61000-4-4
IEC 61000-4-5
IEC 61000-4-6
IEC 61000-4-8
IEC 61010-1
European Council Directive 2004/108/EC &
European Council Directive 2006/95/EC
ABSOLUTE MAXIMUM
RATINGS VALUE UNIT NOTES
Case Operating Temperature
Range -40 to 50 °C
Humidity 80 % Relative humidity at 30°C (non-condensing)
Weight 12 (~5.4) lbs (kg)
Size 3.47 × 8.86 × 17.72
(89 × 226 × 450)
inches3
(mm3)

9
OPERATING INSTRUCTIONS (STAND-ALONE)
WHAT’S IN THE BOX
• QCL Instrument
• Power Cable, type appropriate for nal location
• Red fuse tray
• Two 0.63 A fuses and two 1.25 A fuses for fuse box on the
back panel
• USB Flash Drive, includes all necessary software,
instrument documentation, and additional storage space
• Keys for the keyswitch
• Interlock Replacement Kit (interlocks for QCL D-SUB and
Active Interlock BNC)
THEORY OF OPERATION
The QCL Series low noise drivers are designed expressly to
drive quantum cascade lasers, and utilize patented1circuitry
to deliver ultra-low noise current and still maintain a wide
modulation bandwidth.
The QCL drivers are controlled current sources; they deliver
the current commanded by the setpoint. The current source
continually monitors the actual output current, compares it to
the setpoint, and adjusts the current if there is a dierence
between the two signals.
As current is driven through the load, there is a voltage drop
across the load proportional to the load resistance and current.
As the current increases, the voltage drop may increase to
the point that it reaches the Compliance Voltage limit of the
current source. Once that occurs the current source is no
longer able to increase the current driven to the load even if
you increase the setpoint.
The QCL driver includes features that help protect your laser,
and also make the driver more versatile in a wide array of
applications. These features are explained in detail in the
Operating Instructions.
• The user-adjustable current limit prevents overdriving the
laser even if the external modulation signal is above the
maximum drive current for the laser.
• Over- and under-voltage protection circuits protect the
driver and QCL if the power supply voltages fall outside of
the acceptable operating range.
• Over-temperature protection circuits safely shut down
the output if the internal temperature of the QCL driver
rises to an unsafe level. The fan turns on to manage the
internal temperature.
• Output slow-start ramps the current to setpoint over
1.5 msec.
• A mechanical relay shorts the output connections when
the output is disabled, and when the QCL driver is
powered o.
1Covered by U.S. Patents 6,696,887; 6,867,644 and
7,176,755. Licensed from Battelle Memorial Institute.
The External Modulation Input can be used for adding to
or subtracting from the internal setpoint on the QCL LAB
Instrument. Inputting positive voltages will result in adding
to the setpoint, while inputting negative voltages will result in
subtracting from the setpoint.
These instructions are for operating the QCL Laboratory
Series instrument. Fuses are provided but not installed. After
installing the fuses in the fuse box, be sure to install the fuse
box so the correct voltage for your country is showing. We
also recommend using a test load until you are familiar with
operation of the instrument.
REQUIRED AND OPTIONAL
EQUIPMENT
FOR SET UP
• Small, narrow headed athead screwdriver (required)
• Test load (optional)
• Wavelength Interlock Replacement Kit with interlock
overrides (optional)
COMPUTER REQUIREMENTS FOR
REMOTE OPERATION ONLY (OPTIONAL)
Operating System: Windows XP SP2 or later
Note: See page 16 for Remote Operation
ESD INFORMATION
Before proceeding, it is critical that you take precautions to
prevent electrostatic discharge (ESD) damage to the load.
ESD damage can result from improper handling of sensitive
electronics, and is easily preventable with simple precautions.

10
REAR PANEL
ETHERNETUSB
QCL
CHASSIS
GND QCL
MONITORS
SERIAL #
TRIGGEREXT
MOD
ACTIVE
LOCK
FUSE ~250V, 1.25AF (5 x 20mm)
100-120 VAC, 1.25 A, 50-60 Hz
WARNING: Before powering on
device, verify voltage setting is
correct and proper fuses are
installed.
CAUTION:
No user serviceable parts. Do
not remove cover.
Covered by U.S. Patents:
6,696,887
6,867,644
7,176,755
FUSE ~250V, 0.63AF (5 x 20mm)
220-240 VAC, 0.63 A, 50-60 Hz
!
1
2
35810
9
67
4
13
12
11
Figure 10. Rear Panel
Table 3. Rear Panel Functions
NAME DESCRIPTION
1 Fan Vent Do not block air ow.
2 Chassis Ground Physical connection to chassis and electrical earth ground.
3 QCL SMA SMA connector, alternate connection to QCL.
4 QCL D-SUB 9-Pin female D-SUB connector.
5 Monitors 9-Pin male D-SUB connector.
6 USB USB port, connection between instrument and a computer.
7 Ethernet Ethernet port, connection between instrument and a computer or network.
8 EXT MOD External Modulation: BNC connector, setpoint signal generator input.
9 Active Lock BNC connector, active interlock, tie center pin to GND to enable output.
10 Trigger BNC connector output, allows instrument to trigger external device for synchronizing
measurement.
11 Fuse Box and Voltage
Selector
Removable fuse drawer allows user to switch between 115 V and 230 V. Fuses need to be
installed prior to operation.
12 Power Switch AC power switch that powers the instrument.
13 Power Plug IEC AC line input.

11
INSTALL FUSES AND SELECT
PROPER VOLTAGE
Figure 11. Fuse Box and Voltage Selector
1. On the back panel, locate the Fuse Box and Voltage
Selector receptacle. (See the Rear Panel diagram on
page 10 for the location.)
2. Insert a small athead screwdriver into the slot (1) at the
top of the receptacle and twist to open faceplate. The red
fuse drawer and fuses are located in the Ship Kit.
3. On the face of the fuse drawer are two voltage choices.
Based on your country, select the proper fuses to install.
VOLTAGE FUSE PART NUMBER
100-120 V 1.25 A, 250 V,
fast blow
Littelfuse 5 x 20 mm,
Part #02351.25HXP
220-240 V 0.63 A, 250 V,
fast blow
Littelfuse 5 x 20 mm,
Part #0217.630MXP
CAUTION: It is imperative that the correct voltage
is used. Serious damage can occur if the incorrect
voltage is selected.
4. Insert the fuses as shown in Figure 12, with a short fuse
at the contact end of the receptacle. Then, turn the drawer
until the correct voltage label is at the top and replace it
in the receptacle. Press rmly to make sure the drawer is
completely seated. It should be ush with the receptacle.
Figure 12. Fuse Installation and Voltage Selector
5. Close the faceplate, again pressing rmly until it is ush.
The correct voltage label is shown through the Voltage
Window (2) on the faceplate.
CONNECT POWER
Insert the female end of the IEC AC power cord into the Power
receptacle on the back panel and then plug the male end into
the power source.
WIRE A TEST LOAD
Use of a test load is recommended for setup of the QCL
instrument. Use the Wavelength test loads listed on page 1, or
when building your own test load, a 10 Ω resistor with a 50 W
power rating is recommended for the QCL500, QCL1000,
and QCL1500. For the QCL2000, a 50 W 5 Ω resistor is
recommended.
• Install the test load by either connecting to the QCL SMA
port or wiring the load to PIN 5 and PIN 9 on the QCL
D-SUB as shown in Figure 13.
QCL
SMA QCL
1
1 NOTE: The SMA case is electrically connected to the QCL chassis.
QCL D-SUB
6789
12345
Figure 13. QCL Wiring Diagram
-V
Pin 9 QCL +
or SMA Outer Ring
Pin 5 QCL -
or SMA Center Pin
QCL Driver
Current Sink
Test Load
Figure 14. Test Load Polarity Diagram

12
SET UP INTERLOCKS
The Wavelength Interlock Replacement Kit includes a male
D-SUB with the passive interlock pins shorted and a BNC
terminator.
1. For the passive interlock, on the back panel, short PIN 1
and PIN 2 on the QCL D-SUB.
2. For the active interlock, on the back panel, insert a BNC
terminator in the ACTIVE LOCK BNC port.
3. On the front panel, the keyswitch must be on UNLOCK to
enable the current to the QCL.
NOTE: To disable operation, turn the keyswitch to the
LOCKED position. The key can only be removed when in the
locked position.
TEXT AND ICON COLOR KEY
TEXT
Text indicates current state.
White, Green Uneditable eld, for information only.
Blue Editable eld, touch to select or toggle eld
(text highlights and changes color), adjust
using either the touchscreen or adjustment
knob. Instrument beeps and text returns to
blue when values are set. Touch again to
cancel selection.
ICONS
Icon color indicates current state.
Blue Screen is active.
Grey Screen is inactive, touch icon to access that screen.
FRONT PANEL
QCL
1
000
LAB
ENABLE
DATA
POWER
1
5
3
2
4
Figure 15. Front Panel
Table 4. Front Panel Functions
NAME DESCRIPTION
1 Power Button Powers the application electronics. Glows blue when application electronics power is on and unit
is operational, slow pulses blue when on Standby and only the back panel power switch is on.
2 Adjustment Knob Turn to adjust the numeric values. Instrument beeps when values are set.
3 Enable Button Allows instrument to deliver current to the QCL. Glows blue when current is enabled.
4 Keylock Switch UNLOCK allows laser output current to ow, LOCK disables laser output current. NOTE: The
key can be removed only in LOCK position.
5 Data Port USB ash drive, used to update the rmware or save data. This is not used for remote USB
control of the instrument.

13
TURN ON QCL INSTRUMENT
1. Press the Power switch on the back panel to |. The front
panel power button light slowly pulses.
2. Press the Power button on the front panel, the button
illuminates, touchscreen is activated, and the Control
screen is active.
NOTE: Turning o front Power button powers down the
application electronics and puts the unit into standby
mode. Turning o rear Power switch powers down all
electronics and settings return to factory default.
3. The front panel displays dashes instead of digits until the
unit has nished its power-up sequence (~10 seconds).
SET LIMITS
1. Press to access the Limit Screen.
2. Press Limit Current, Maximum Supply Voltage, and/or
Cable Resistance values and rotate the Adjustment knob
to change each value. The instrument will beep when set.
Figure 16. Limit Screen
NOTES:
• The Limit Current should not exceed the damage current
threshold of your QCL.
• The Maximum Internal Supply Voltage can be lowered
to minimize internal instrument temperature or to act as a
compliance voltage clamp on the QCL output current. See
Additional Technical Notes on page 20 for optimization
instructions.
• The Cable Resistance range is 0 – 4 Ω.
QCL Voltage displays the voltage at the QCL DSUB or
SMA terminals. To account for voltage loss across the
cable to the QCL, you can enter a non-zero value for
Cable Resistance.
The QCL Voltage will now display as:
Voltage Displayed = Voltage@Pins - (Cable Resistance x Operating Current)
• The minimum limit current is about 8% of full scale.
ADJUST THE SETPOINT
1. Press to access the Control Screen.
2. Press the Setpoint value and turn the Adjustment knob
until the desired operating current is displayed.
Figure 17. Control Screen
NOTE: The Control screen is on by default when the
instrument is turned on. The Mode is Constant Current by
default and cannot be changed.
DISPLAY EXISTING CURRENT AND
VOLTAGE VALUES
Press to access the Monitor Screen.
Values on this screen cannot be changed and are for
information only.
Figure 18. Monitor Screen

14
ENABLE THE QCL INSTRUMENT
Press the Enable button on the front panel. The button will
glow blue only when current is delivered to the load. There is
a standard 2-second delay before the button illuminates and
current ows.
VI SCAN
1. On the Control screen, press to access the VI
scan screen.
2. Press the Current Start value to select the current at
which to start the scan. Turn the Adjustment knob to
change it.
Figure 19. Scan Screen
3. Press the Current Stop value to select the current at
which to stop the scan.
4. Press the Step Size value to select the current interval at
which to take a measurement. The maximum interval is
10% of full scale. Minimum step is 1% of full scale.
5. Press the Time Interval value to select the amount of time
to allow the current to settle. For the best data accuracy,
use a Time Interval of 2 seconds or more. The minimum
time interval is 0.1 seconds.
6. Insert the USB ash drive in the USB slot on the front
panel.
7. Press the green Run button to start the scan. When
nished, data is saved to the USB ash drive with
the lename viscanxx.txt, where xx starts at 00 and
increments.
8. To stop mid-scan, press the red Stop button to abort the
scan. Any data collected during the aborted scan is saved
to the USB ash drive.
NOTES:
• The step interval time is approximate. In the scan les,
time intervals are slightly more than the step interval
indicated on the instrument. Each interval builds on the
previous one.
• Should the Step Size interval not nish at the Stop Current,
the reading is still taken and recorded. For example,
if the Start Current is 250 mA and the Stop Current is
1.04 A with a Current Step of 250 mA, a reading is taken
at 1000 mA (1 A) and 1040 mA (1. 04 A) but not at 1250
mA (1.25 A).
• After a VI scan is completed, the output is disabled and
the setpoint is zeroed.
SAVE OR RECALL SETTINGS
Press to access the Save/Recall Screen.
Under Save Settings to, press the blue text
to toggle through the Prole options, select
one, and then press the Save icon.
The following variables are saved:
OPERATION SETTINGS VI SCAN SETTINGS
Setpoint VI Start Current
Current Limit VI Stop Current
Max Supply Voltage VI Step Size
Cable Resistance VI Time Interval
Display Brightness
Beeper Status
Figure 20. Save / Recall Screen
Under Recall Settings from, press the
blue text to toggle through the saved Prole
options, and then press the Recall icon to
recall the saved settings. Select Factory to
restore the settings to the factory defaults.

15
SETTINGS SCREEN
Press to access the Settings Screen
Move the slider bar on the touchscreen to change the display
brightness. Press the blue text to toggle the Beeper on-o
setting.
Figure 21. Settings Screen
LOCK OR UNLOCK SETTINGS
(OPTIONAL)
Settings are not locked.
This is the default. Critical values set with the
Adjustment knob can be locked. Press to lock
the settings.
Settings are locked.
Press to unlock the settings.
Settings are locked and password protected.
Locked settings that are password protected
can only be locked and unlocked using a remote
computer.
EXTERNAL MODULATION
(EXT MOD) BNC
This is the external modulation input. The voltage input on
this BNC sums with the DC value on the screen. The input
impedance is 1 kΩ. To calculate the external modulation
signal voltage, see the next section for the transfer function,
and use the following equation:
VEXT_MOD = ISETPOINT / Transfer Function
If the external modulation input causes the driver to reach the
current limit, the output signal will be clamped at the limit level
but will not switch o.
The bandwidth of the Current Monitor is lower than the
bandwidth of the output. To monitor the actual output
waveform at high frequencies, connect an oscilloscope across
the output pin on the MONITOR D-SUB, Pin 8 (positive), and
Pin 9 (ground) while using the resistor test load.
CAUTION: Connect the oscilloscope across the
test load only — never connect the oscilloscope
across a quantum cascade laser.
EXTERNAL MODULATION BNC
TRANSFER FUNCTIONS
The external modulation transfer function depends on the
QCL instrument model and is as follows:
QCL500 LAB: 0.1 A / V.
QCL1000 LAB: 0.2 A / V.
QCL1500 LAB: 0.3 A / V.
QCL2000 LAB: 0.4 A / V.
The input range is always -5 V to +5 V.

16
ADDITIONAL CAPABILITIES
ANALOG CURRENT MONITOR
This signal is the sum of the DC setpoint as shown on the
screen and the external modulation input.
To monitor the analog current level:
1. Connect the Analog output Current Monitor (PIN 8) on the
MONITOR D-SUB to an oscilloscope.
2. Connect an Analog Monitor Ground (PIN 7 or PIN 9) to
oscilloscope ground.
SETPOINT CURRENT MONITOR
This is a reference only and can be o by as much as 5%
when setpoint is >10% of full scale.
To monitor the setpoint current:
1. Measure the voltage on the Analog Setpoint Monitor
(PIN 6).
2. Ground for that measurement is the Analog Monitor
Ground (PIN 7 or PIN 9).
The setpoint monitor and analog current monitor transfer
functions depend on the QCL instrument model and are all
as follows:
QCL500 LAB: 0.1 A / V.
QCL1000 LAB: 0.2 A / V.
QCL1500 LAB: 0.3 A / V.
QCL2000 LAB: 0.4 A / V.
The input range is always 0 – 5 V.
ALIGNMENT LED DRIVE
+5 V, up to 250 mA sourced.
To drive an alignment LED, on the MONITOR D-SUB
1. Connect an LED to the Alignment LED +5V (PIN 1).
2. Ground the LED at the Alignment LED Ground (PIN 2).
ENABLE STATUS INDICATOR
This is a +5 V TTL indicator. If current to the QCL output
is enabled, the voltage between PIN 3 and PIN 4 on the
MONITORS D-SUB will be low. It will be high if current is
disabled.
USE THE TRIGGER SIGNAL
A trigger signal is provided so that external measurement
equipment can be synchronized with laser current. Exactly
10 msec after a remote change in setpoint, a 20 µsec positive
going pulse appears on the Trigger BNC plug.
To use the Trigger, connect a BNC cable to the TRIGGER
BNC output.
INSTALL THE QCL LABVIEW
INTERFACE APPLICATION
Complete installation instructions can be found in the LAB
Series Virtual Instrument Operating Guide.
The instructions explain how to download the .EXE le. If you
would like a copy of the .VI le, contact Technical Support.
USE REMOTE COMMANDS AND
NATIONAL INSTRUMENTS DAQ
CARD
Complete documentation of the remote commands supported
by the QCL LAB instrument can be found in the Remote
Command Set.
CUSTOM VIRTUAL INSTRUMENTS
Wavelength also oers custom Virtual Instrument applications
tailored to your specic needs. Contact Technical Support for
more information.
REMOTE OPERATING
INSTRUCTIONS
The following instructions are for QCL LAB Series
instruments running rmware Version 1.5 and
later. These use the LabVIEW Virtual Instrument
application or the Remote Command Set.

17
TROUBLESHOOTING
Table 5. Troubleshooting
PROBLEM POTENTIAL CAUSES SOLUTIONS
Front panel Power button does not turn on
The button has been pushed on and
o within 3 seconds.
The front panel Power button has a 3 second
delay between when it is turned o and on in
rapid succession. This is a safety mechanism
to ensure there is no damage to either the
QCL instrument or the attached load.
The rear panel switch is o. Turn the rear panel switch to the on or |
position.
The Enable button does not turn on
The button has been turned on and o
within 2 seconds.
The button cannot be pressed faster than
every 2 seconds.
The QCL D-SUB interlock or Active
Interlock connections are open, or the
keyswitch is in the LOCKED position
• Make sure PIN 1 and PIN 2 on the QCL
D-SUB are shorted.
• The “Active Lock” BNC connector may
be open. Install a BNC shorting plug.
• Rotate the key to the UNLOCKED
position.
The instrument experienced an
internal fault.
(See Error Messages on page 19.)
The instrument will remain disabled until
manually powered o and then on using the
rear panel power switch.
The instrument heatsink temperature
has exceeded 70ºC.
Allow the instrument to cool down and then
press the front panel power button.
The front panel Power button is not
on.
Press the Power button on the front panel to
enable the display.
The instrument is on but the front panel
display is blank
The instrument experienced an
internal fault.
(See Error Messages on page 19.)
Switch the back panel power button o and
then on again, and turn the front panel power
button on.
The internal temperature has reached
an unsafe level.
Allow the instrument to cool down and then
switch the back panel power button o and
then on again, and turn the front panel power
button on.
The front panel Power button is
pulsing on and o in standby mode.
Press the Power button on the front panel to
enable the display.
The date and time on my VI scan le are
wrong
The QCL instrument does not have a realtime
clock. When a VI scan le is created, the date
and time stamp are randomly chosen.
The VI scan les are not in the order that
they were created
Some les may have been deleted o
of the USB ash drive.
When les are deleted o of the USB ash
drive and new les are saved to it, the new
les are given sequentially the names of the
deleted les.
Unable to create new VI scans
The interlocks may not be satised.
Turn the keyswitch to UNLOCKED, or
install the ACTIVE LOCK BNC and passive
interlocks.
There are too many les on the USB
ash drive. Delete les from the USB ash drive.
I can’t nd my VI scan les VI scan les are named sequentially.
If les have been deleted from the ash drive,
any new les added are named sequentially
and have the names of the deleted les.
The fan keeps coming on The internal temperature is being
regulated.
To reduce internal heat generation, choose a
lower supply voltage. The instrument will shut
down if the internal temperature gets too hot.

18
PROBLEM POTENTIAL CAUSES SOLUTIONS
Noise current is higher than expected.
There may be ground loops in the
system; some system components
may be higher noise than expected;
cabling and shielding may be
inadequate.
Refer to Wavelength Electronics Application
Note AN-LD08: Manage Grounding to
Minimize Noise with the QCL Drivers:
www.teamwavelength.com/download/
applicationtechnotes/an-ld08.pdf
Also reference AN-LD09: Troubleshooting
Low Noise Systems:
www.teamwavelength.com/download/
applicationtechnotes/an-ld09.pdf
The output switched o unexpectedly
The instrument detected an internal
error.
(See Error Messages on page 19.)
Switch the back panel power button o and
then on again, and turn the front panel power
button on.
The internal temperature has
exceeded 70ºC.
Allow the instrument to cool down and then
press the front panel power button.
20 kHz noise is in the output current QCL driver is operating in current limit.
If safe for the quantum cascade laser,
increase the output current limit setting.
When actively operating in current limit, the
safety circuits add noise to the output.
If I run my QCL at about 5% of maximum
output current, the transfer function
becomes non-linear and I see distortion in
my output current waveform.
QCL driver resolution is too low.
Select a QCL driver with a much lower
maximum output current. For example,
to run 50 mA, request a QCL125 (125 mA
maximum output).
My instrument doesn’t show up in the list.
(Remote Only)
Your instrument may not be turned on. Power up the instrument and click Refresh
on the Choose Instrument window.
Your instrument may not be plugged in
to the computer.
Check that either a USB or Ethernet cable is
tightly connected to the instrument and to the
computer.
Your instrument may be on a dierent
sub-net.
Add the sub-net to the Choose Instrument
window and then click Refresh.
Actual current does not match the setpoint.
The setpoint exceeds the limit current
setting.
If the limit current can be increased without
damage to the QCL, increase the limit
current setting.
The QCL is compliance voltage
limited.
Increase the Max Supply Voltage slightly to
see if actual current increases. Follow the
instructions on page 20 to optimally set
the Max Supply Voltage.

19
Table 6. Error Messages
To clear error text, x the cause then press any icon or the Enable button.
ERROR POTENTIAL CAUSES SOLUTION
The USB ash drive is missing or not
accessible. Please make sure that a USB
ash drive is inserted into the front panel.
To run a local VI scan, a USB ash drive
must be in place.
Insert a USB ash drive in the data port on
the front panel.
The USB ash drive was removed. The
scan has been aborted.
To run a local VI scan, a USB ash drive
must be in place.
Insert a USB ash drive in the data port on
the front panel.
Output current is disabled. The keyswitch
is in the locked position.
The keyswitch is horizontal or in the locked
position.
Turn the keyswitch to the vertical or
unlocked position.
Output current disabled. Pins 1 & 2 on the
QCL D-SUB are not tied. The passive interlock is not shorted. Short Pin 1 and Pin 2 on the QCL D-SUB.
Output current disabled. The Active
Interlock is not shorted. The active interlock is not grounded. Ground the center pin of the Active Lock
BNC.
The internal temperature limit of the
instrument has been exceeded. Output
current has been disabled to protect the
laser.
The ambient air temperature is too high for
the instrument.
Reduce the ambient air temperature to
50ºC or less.
The VI scan was canceled by the user. The Stop button was pressed during the
scan.
Scan was canceled because output
current is disabled.
The Enable button was pressed during a
scan, cutting current to the load.
An open circuit was detected at the
load. Please verify the load and load
connections.
The instrument cannot drive current
through the load.
Make sure the QCL SMA or Pins 5 & 9 of
the QCL D-SUB are connected.
A short circuit was detected at the load
terminals. Please verify the load and load
connections.
The instrument is detecting that there is no
resistance where the load should be.
Make sure the QCL SMA or Pins 5 & 9 of
the QCL D-SUB are connected.
An internal error occurred while reading
data from hardware. Please contact the
factory for further assistance.
Contact Wavelength technical support for
further assistance.
A timeout occurred waiting for output.
Make sure the load is connected and
interlocks are satised.
Contact Wavelength technical support for
further assistance.
An internal error was detected. Please
contact the factory for further assistance.
Contact Wavelength technical support for
further assistance.
A fault in the internal +5V supply was
detected. Please contact the factory.
Contact Wavelength technical support for
further assistance.
A fault in the internal +15V supply was
detected. Please contact the factory.
Contact Wavelength technical support for
further assistance.
A fault in the internal -15V supply was
detected. Please contact the factory.
Contact Wavelength technical support for
further assistance.
A timeout occurred waiting for the internal
load power supply to stabilize. Please
contact the factory.
Contact Wavelength technical support for
further assistance.
A problem has been detected in the
instrument power supply. Please contact
the factory for further assistance.
Contact Wavelength technical support for
further assistance.
A current surge has been detected in the
instrument. Output has been disabled to
protect the laser.
Contact Wavelength technical support for
further assistance.
ERROR MESSAGES

20
ADDITIONAL TECHNICAL NOTES
This section includes useful technical information on these
topics:
• Reduce internal temperature or provide compliance
voltage limit
• Use Passive and Active interlocks
• Soft-clamp current limit
• Square wave response
• Remove the bail and feet from an instrument
• Update rmware
• Determine rmware version installed
REDUCE INTERNAL TEMPERATURE
OR PROVIDE COMPLIANCE
VOLTAGE LIMIT
At full current, the Maximum Compliance Voltage available
to the QCL is about 7.5 V below the maximum supply
voltage. This 7.5 V estimate decreases as operating current
decreases. To determine the best internal supply voltage for
your application, follow these steps:
1. Wire your QCL to the instrument and adjust the current
limit on the Limit screen and setpoint on the Control
screen for your application.
2. Press the Enable button to enable the output current. The
actual current displayed should match the setpoint.
3. On the Limit screen, select the blue MAX Supply Voltage
value and, using the Adjustment knob, adjust it down
slowly until the actual current starts to decrease. The QCL
current is now limited by the compliance voltage of the
instrument.
4. Using the Adjustment knob, now increase the MAX
Supply Voltage value until the current is no longer below
the setpoint. This is the optimal maximum supply voltage
for your setup.
5. On the Monitor screen, observe the QCL Voltage. This is
the voltage across the QCL at this operating current and
is the eective voltage limit to the QCL for your setup.
NOTE: If you reach 18 V on the MAX Supply Voltage
input and the current is still not compliance voltage limited,
the instrument is operating at its lowest voltage and the
voltage limit cannot be reduced further.
USE PASSIVE AND ACTIVE
INTERLOCKS
The passive interlock is designed to trigger if Pins 1 and 2 on
the QCL D-SUB are not shorted. Use this interlock with doors
and enclosures that trigger an open circuit when opened.
The active interlock (ACTIVE LOCK BNC) can be used with
a temperature controller or other active system component to
disable the current output if the QCL exceeds an acceptable
temperature operating range.
SOFT-CLAMP CURRENT LIMIT
The QCL driver employs a soft-clamping current limit that
begins to act at a current lower than the calculated absolute
current limit.
The Limit Current is the absolute current limit, which is the
current that will not be exceeded under any circumstance.
Because of the soft-clamp circuit, the actual current where the
limit circuit begins to act is 20% below the absolute current
limit. NOTE: When operating at low currents around 100 mA
with the QCL500 LAB, the limit circuit begins to act around
32 mA below the absolute current limit.
If the output current is between this point and the Absolute
Current Limit, the output response to the analog input
setpoint is nonlinear. The result is that the drive current will
asymptotically approach the absolute current limit, and will
never exceed it even if the external modulation setpoint
voltage far exceeds the current limit.
Figure 22 illustrates the behavior of the soft-clamp current
limit. In this case the analog input voltage setpoint signal is
a triangle wave, with the amplitude set so that the driver will
attempt to overdrive the current limit.
Figure 22. Soft Clamping Current Limit Behavior
This manual suits for next models
12
Table of contents
Other Wavelength Electronics Laboratory Equipment manuals
Popular Laboratory Equipment manuals by other brands
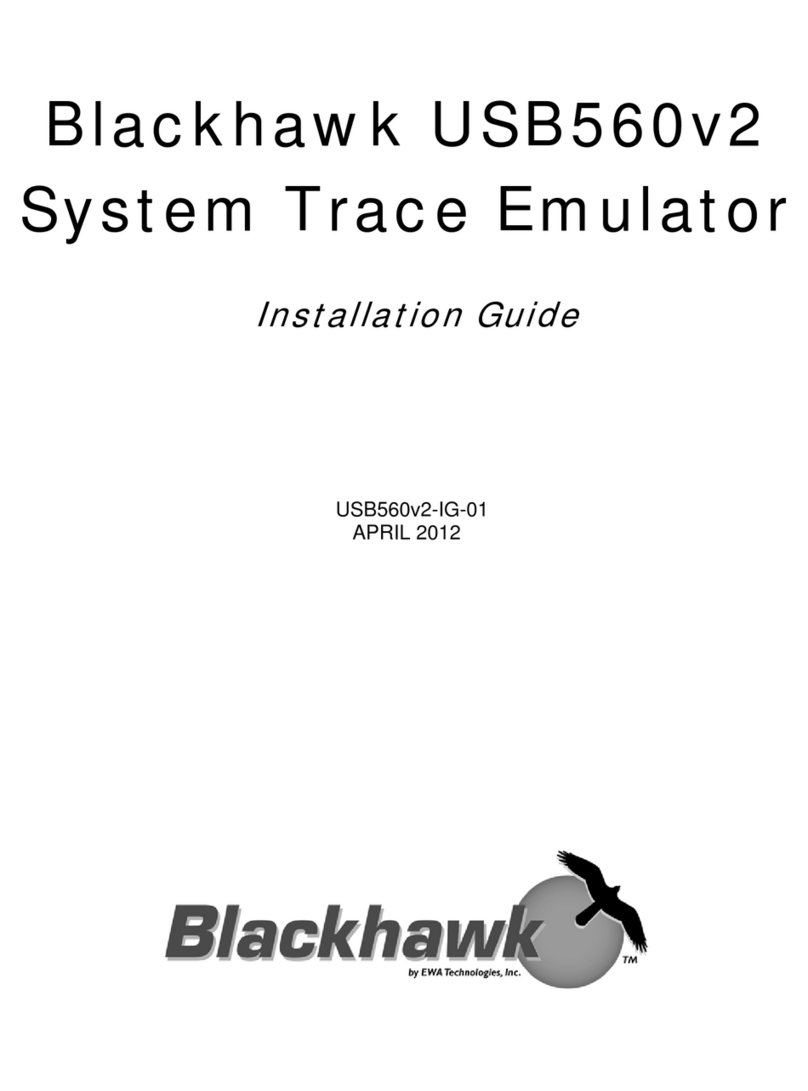
BlackHawk Labs
BlackHawk Labs USB560v2 installation guide
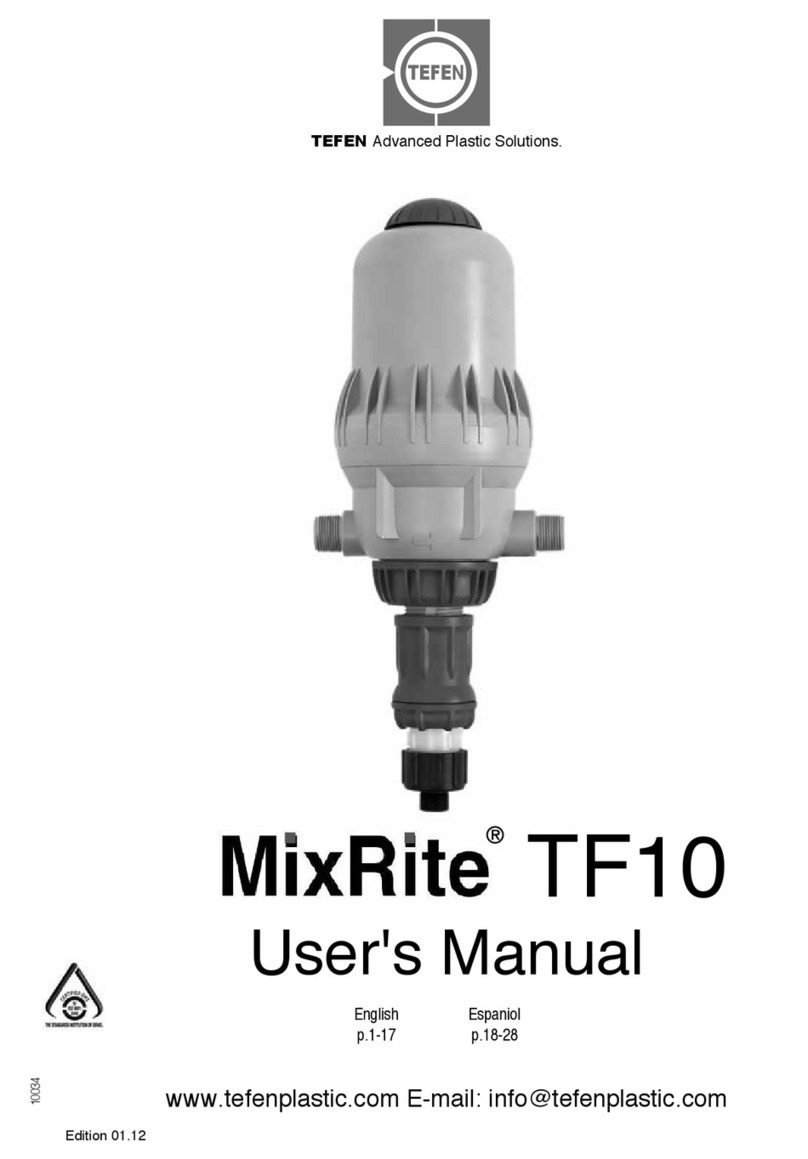
tefen
tefen MixRite TF10 user manual
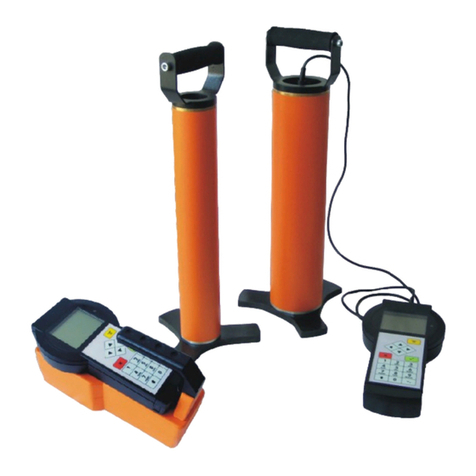
GF Instruments
GF Instruments GAMMA Surveyor user guide
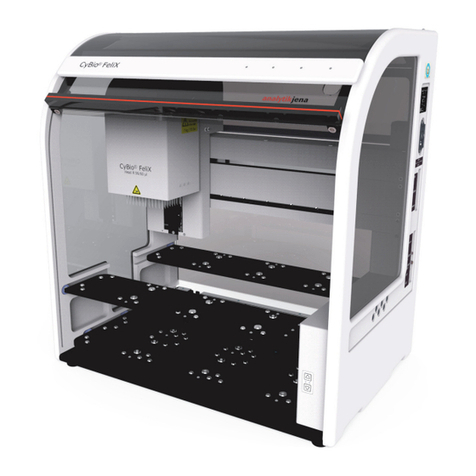
Endress+Hauser
Endress+Hauser Analytik Jena CyBio FeliX operating manual
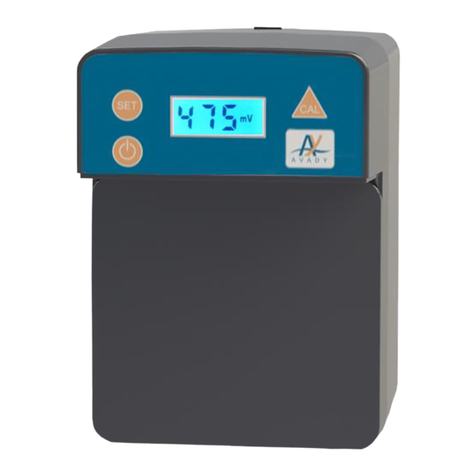
Avady
Avady ChloriProtect Rx Instruction and user's manual

IKA
IKA HB ECO instruction manual

Qiagen
Qiagen QIAcuity 911000 Information and installation guide
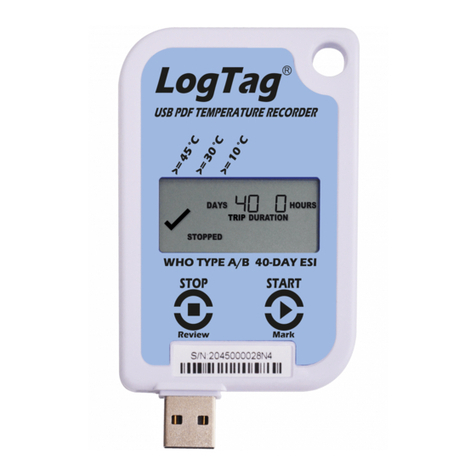
LogTag
LogTag USRID-16W Product user guide
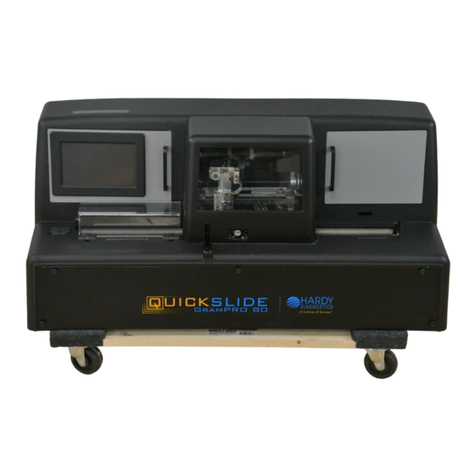
Hardy Diagnostics
Hardy Diagnostics QUICKSLIDE GramPRO-80 User's operating manual
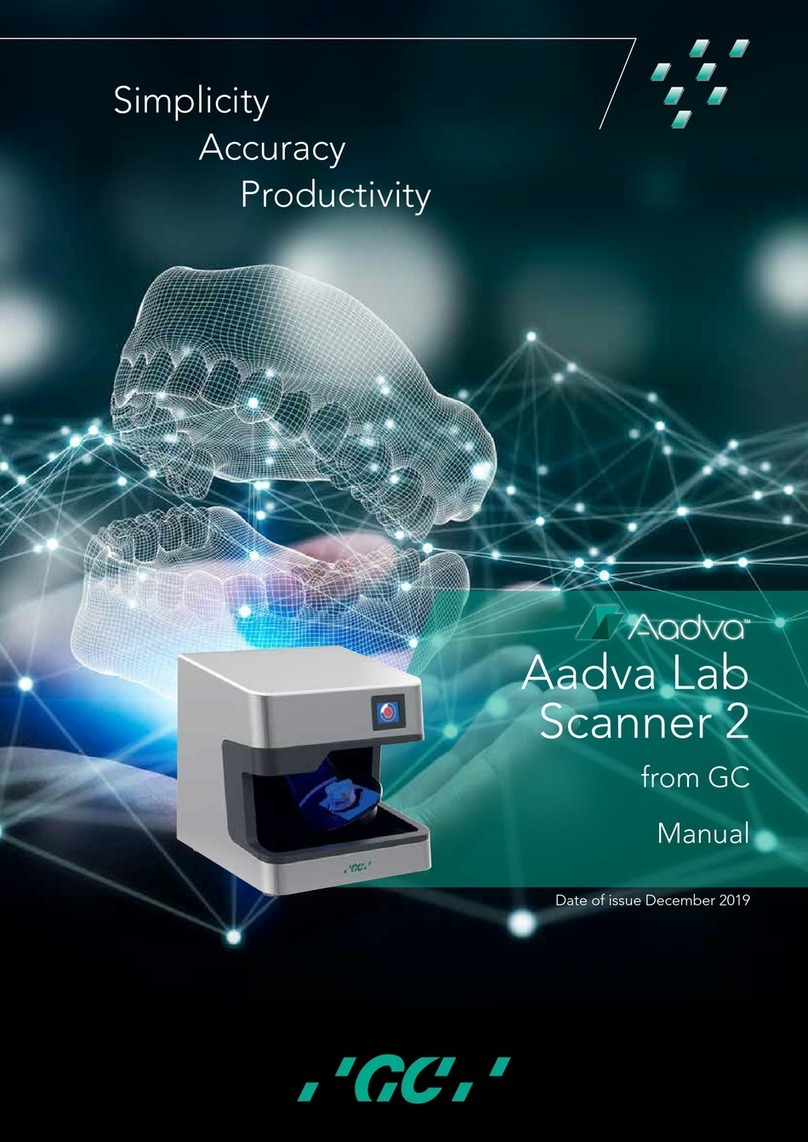
gc
gc Aadva Lab Scanner 2 manual
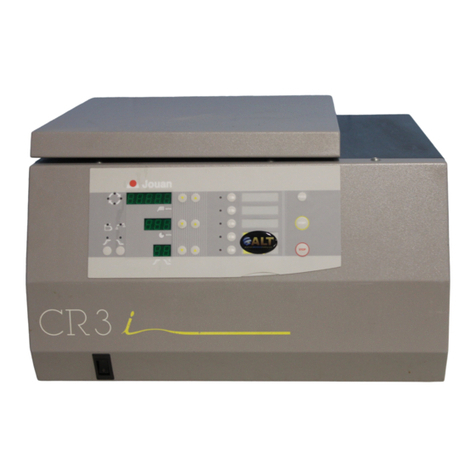
Jouan
Jouan C3i Service manual
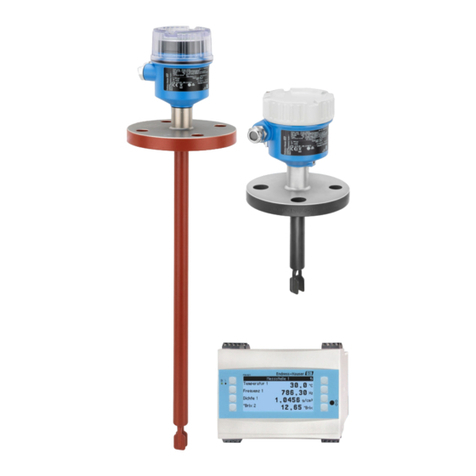
Endress+Hauser
Endress+Hauser Liquiphant FTL62 Density operating instructions