Wecon LX5V-2TC-BD User manual

1
LX5V-2TC-BD BD Module Manual
1 Installation
▪ Before installation, it must be ensured that the PLC host and the related device of the BD module terminal
wiring are powered off reliably. The shell is inserted into the BD module slot of PLC host, and then locked
with two standard screws for fixation.
▪ Two standard terminal heads are equipped with this BD module. After connecting the wiring, insert them
into its terminal. After confirming that the host, BD module, wiring, etc. are installed correctly, it can be
powered on for use.
▪✎Note:
● Please install the BD module firmly and fix it on PLC. Poor contact may lead to failure.
● Tightening torque for fixing BD module or PLC top cover is 0.3N.m to0.6N.m. Please tighten it firmly to
avoid malfunction.
▪Warning: Cut off the power before installing, removing or wiring the BD module to avoid electric shock or
product damage.
2 Appearance and terminal
Table1Terminal distribution
Table2LED lamp function description
Indicator
lamp
Description
PWR
ON when power-on (when the program is running, it will be ON).
COM
It flashes when communicating with PLC normally, and it is OFF when timeout.
CH1
Channel 1 lamp: Always on in range; Flashing outside the range (type K: -100℃to
1200℃; type J: -100℃to 600 ℃); Off when the channel is closed.
CH2
Channel 2 lamp: Always on in range; Flashing outside the range (type K: -100℃to
1200℃; type J: -100℃to 600℃); Off when the channel is closed.
2-wire K/J thermocouple
L2-
Channel 2 sensor signal input
negative
L2+
Channel 2 sensor signal input
positive
NC
L1+
Channel 1 sensor signal input
positive
L1-
Channel 1 sensor signal input
negative
V1.0

2
3 Specification
(1) General specification: Same as PLC main unit. (Please refer to the accompanying manual of the PLC
main unit.)
(2) Power supply specification: The power supply is provided internally by PLC
(3) Performance specifications:
Project
Description
Digital circuit
5VDC, 90mA (from the internal circuit of the main unit)
Analog input
signal
Thermocouple: Type K or J (both types can be used per channel)
Sensor current
1mA
Rated
temperature
range
Type K: -100℃to 1200℃
Type J: -100℃to 600℃
Digital output
Type K: -1000 to 12000
Type J: -1000 to 6000
12-bit conversion, 11 data bits +1 sign bit
Measurement
accuracy
Type K: 0.4℃
Type J: 0.3℃
Total accuracy
Full range±0.5% (full range + 1℃)
Conversion
speed
2-channel 700ms
Conversion
features

3
4 Wiring
Cut off the power before installing, removing or wiring the BD module to avoid electric shock or
product damage.
✎Note:
● Do not place signal cables near high voltage power cables or in the same trunk line. Otherwise, it may
be disturbed or surged. Keep a safe distance between signal cable and power cable, at least 100mm.
● Ground the shielding of shielded wire or shielded cable. But the ground point and high voltage line
cannot be the same.
● Never weld any cable ends. Ensure that the number of connecting cables does not exceed the
designed number of units.
● Do not connect cables whose dimensions are not allowed to avoid poor contact or damage to
products.
● Fix the cable so that no force directly acts on the terminal line or cable connection area.
● The tightening torque of terminal is 0.5Nm to 0.6N.m. Please tighten it to prevent malfunction.
● Do not use empty terminals.
4.1 Applicable cables
(1) AWG25-16 is used for connection with output device.
(2) Maximum terminal tightening torque is 0.5N.m to 0.6N.m.
(3) Using different types of cables may cause poor contact with terminals. Please use pressfit terminals for
good contact.
Line number and cross-sectional area
Line
number
Cross-sectional
area (mm2)
End processing
AWG26
0.1288
Stranded cable: Strip off the sheath, rub the core wire,
and then connect the cable.
Single-core cable: Strip off the sheath and connect the
cable.
...
...
AWG16
1.309
4.2 I/O Mode
Thermocouple input mode

4
5 Description of PLC device
(1) When connected to LX3 series PLC, please refer to LX3 series BD module manual.
(2) When connected to LX5 series PLC, if the firmware version of PLC is lower than 2.051 (excluding 2.051),
or BD module is not configured by host computer, it can be controlled by the following system devices:
Table3Device allocation
PLC model
BD
model
Device
Expansion port 1 description
Device
Expansion port 2 description
LX5V
2TC
SM2010
CH1: Input mode switch flag
OFF: Thermocouple type K
ON: Thermocouple type J
SM2030
CH1: Input mode switch flag
OFF: Thermocouple type K
ON: Thermocouple type J
SM2011
CH2: Input mode switch flag
OFF: Thermocouple type K
ON: Thermocouple type J
SM2031
CH2: Input mode switch flag
OFF: Thermocouple type K
ON: Thermocouple type J
SD2010
The temperature of CH1 at 0.1°C
(Type K: -100℃to 1200℃: -1000 to
12000;
Type J: -100℃to 600℃: -1000 to
6000)
SD2030
The temperature of CH1 at 0.1°C
(Type K: -100℃to 1200℃: -1000 to
12000;
Type J: -100℃to 600℃: -1000 to
6000)
SD2011
The temperature of CH2 at 0.1°C
(Type K: -100℃to 1200℃: -1000 to
12000;
Type J: -100℃to 600℃: -1000 to
6000)
SD2031
The temperature of CH2 at 0.1°C
(Type K: -100℃to 1200℃: -1000 to
12000;
Type J: -100℃to 600℃: -1000 to
6000)
(3) You can select device through I/O mapping to use the configuration function of new BD module. For
details, please refer to "6.1 Parameter configuration".
6 Instructions
6.1 Parameter configuration
① Open the host computer software and create a new project, double-click “Project Manager” →
“Extended Function” → "BD Module Configuration" Noteto enter “BD settings” interface;
② Configure the currently connected PLC (take the LX5V-2416 model as an example) and BD module
model on the BD module configuration interface: Select “LX5V-2TC" in the device bar on the right side
of the BD module configuration interface and double-click to add it to the corresponding slot position of
PLC (slot number 1 or 2, the software will select slot 1 by default, and right-click to move down to slot
2);
③ After adding the BD module to the slot, double-click or right-click to select configuration parameters to
enter LX5V-2TC-BD configuration parameters interface, as shown in the following figure. Configure
related parameters on this interface.

5
Note: This function is only supported in the following versions of host computer, slave computer and BD
module:

6
(1) Supported host computer versions: Wecon PLC Editor2 2.1.204 and above, as shown in the following
figure:
(2) Supported slave computer versions: 2.051 and above, as shown in the following figure:
(3) Supported BD module version number: 1013 and above, as shown in the following figure:

7
The parameter configuration interface is as below:
1、Module setting: Set response time (The response time is the interval time between PLC acquisition of
BD module data. Range: 0.1ms to 3276.7ms).
2、TC configuration:
1Check enable channel to set whether to enable the current BD module channel.
2Sensor type: The default sensor type is K thermocouple (Type K and J are optional, and you can set
through the drop-down box).
3Setting the filtering intensity can reduce the jitter of BD channel value. The default configuration of
filter intensity is 4. Level 0 is the lowest and level 9 is the highest. The filter intensity can be adjusted
according to actual use.
4Check enable overrun detection to judge that when the upper and lower limits of temperature exceed
the current setting temperature, the host computer will prompt an error.
✎Note: Different types of thermocouples can measure different temperature ranges.
5Check enable calibration, you could calculate the gain offset according to the following formula to

8
convert the corresponding channel value:
Channel value = actual temperature value × gain value + offset value
When the channel value deviates from the actual temperature value, the channel can be calibrated by
setting the gain offset, for example:
If the type of thermocouple connected to the current channel is K:
▪ The input temperature of control channel is 0℃, the value of acquisition channel is 50 (unit: 0.1℃),
and the actual channel value should be 0 (unit: 0.1℃).
▪ The input temperature of control channel is 1100℃, the value of acquisition channel is 11100 (unit:
0.1℃), and the actual channel value should be 11000 (unit: 0.1℃)
Suppose the gain is a, and the offset is b, then
ba
ba
*1110011000
*500
,
Solve and get
9.77384-b
995475.0a
The calibration can be completed by setting the corresponding gain
offset to the current channel.
3、Set I/O mapping. The channels are mapped to R device according to the current number of BD module
channels by default. As shown in the following figure, BD module CH1 to CH2 is mapped to device R0 to R1.
4、After the above configuration is completed, check the program, download the configuration to PLC, and
STOP→RUN configuration takes effect.

9
6.2 Ladder Diagram
1、Programming example that does not use the host computer software "BD module configuration"
function. For device allocation, please refer to "5 PLC device description".
2.Programming example using "BD module configuration" function of host computer software:
6.3 BD monitoring interface and buffer memory
Open the module monitoring interface, select BD module, select LX5V-4ADI from the list of BD modules
on the right to monitor it online, and check the current BD module communication status and error
information in time.
① TC buffer memory (BFM): used for BD module status monitoring.
BFM
addres
Power
-off
Read-
write
Memory name
Default
Range
Description
Switch CH1 to type K thermocouple
Switch CH2 to type K thermocouple
Write the temperature value of CH1 to register D0
Write the temperature value of CH2 to register D0
Map CH1 into R0 device
Map CH2 into R1 device

10
s
hold
0x2000
×
R/W
Channel 1 channel
enable
1
0 to 1
0: Channel closed; 1: Channel open
0x2001
×
R/W
Channel 1 sensor type
0
0 to 1
0: Type K thermocouple; 1: Type J
thermocouple
0x2002
×
R/W
Channel 1 filter intensity
4
0 to 9
0: Minimum filter strength; 9:
Maximum filter strength
0x2080
×
R
Channel 1 channel value
32767
-32768 to 32767
Unit: 0.1℃
0x2082
×
R
Channel 1 status
information
1
0 to 2
0: Channel closed; 1: Channel
opened
2: Channel value exceeds the range
0x2084
×
R
Channel 1 error code
0
0 to 1
0: No error; 1: Channel value
exceeds the range
0x2100
×
R/W
Channel 2 channel
enable
1
0 to 1
0: Channel closed; 1: Channel open
0x2101
×
R/W
Channel 2 sensor type
0
0 to 1
0: Type K thermocouple; 1: Type J
thermocouple
0x2102
×
R/W
Channel 2 filter intensity
4
0 to 9
0: Minimum filter strength; 9:
Maximum filter strength
0x2180
×
R
Channel 2 channel value
32767
-32768 to 32767
Unit: 0.1℃
0x2182
×
R
Channel 2 status
information
1
0 to 2
0: Channel closed; 1: Channel
opened
2: Channel value exceeds the range
0x2184
×
R
Channel 2 error code
0
0 to 1
0: No error; 1: Channel value
exceeds the range
② Universal buffer memory (BFM): used to diagnose the communication status of the currently connected
BD module.
BFM
address
Power
-off
hold
Read-
write
Functi
on
Memory name
Default
Range
Description
0x200
×
R
Current maximum
package length
0
0 to0xFFFF
The maximum length of the
currently sent package
0x202
×
R
Number of
retransmissions
0
0 to0xFFFF
Number of retransmissions
0x204
×
R
Number of
retransmissions of
subpackages
0
0 to0xFFFF
Number of retransmissions of
subpackages
0x206
×
R
Received times of sync
frames
0
0 to0xFFFF
Received times of sync frames
0x208
×
R
Sent times of sync
frames
0
0 to0xFFFF
Sent times of sync frames
0x20A
×
R
Control the number of
transmissions
0
0 to0xFFFF
Control the number of
transmissions
0x20C
×
R
Control the number of
receptions
0
0 to0xFFFF
Control the number of receptions
0x20E
×
R
Number of subscriptions
sent
0
0 to0xFFFF
Number of subscriptions sent
0x210
×
R
Number of subscriptions
received
0
0 to0xFFFF
Number of subscriptions received
0x212
√
R/W
Latest error code
0
Only 0 can be
written.
Protocol internal error code, write 0
to clear
0x214
×
R
Number of bytes sent
0
0 to 0xFFFFFFFF
Number of bytes sent
0x218
×
R
Number of valid bytes
sent
0
0 to 0xFFFFFFFF
Number of valid bytes sent
0x21C
×
R
Number of bytes
received
0
0 to 0xFFFFFFFF
Number of bytes received
0x220
×
R
Number of valid bytes
received
0
0 to 0xFFFFFFFF
Number of valid bytes received
0x224
×
R
Communication time
(unit s)
0
0 to 0xFFFFFFFF
Normal communication time since
the BD module is powered on
Table of contents
Other Wecon Control Unit manuals
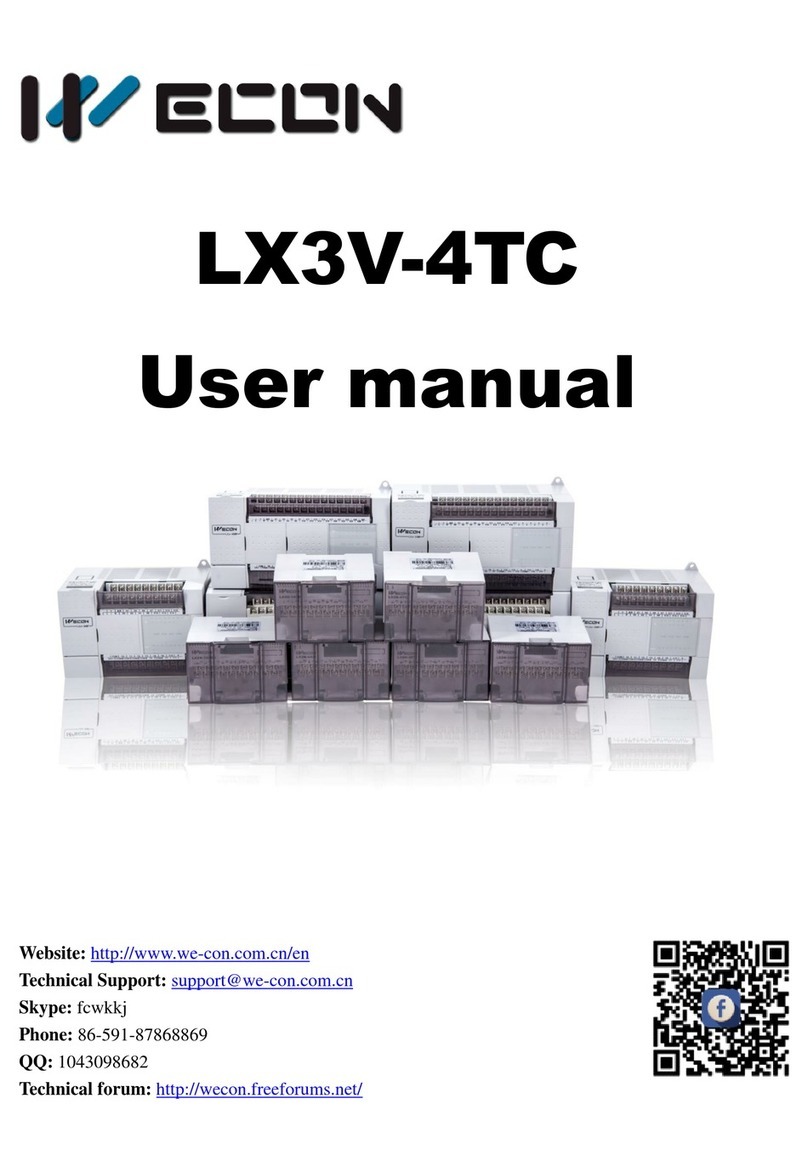
Wecon
Wecon LX3V-4TC User manual
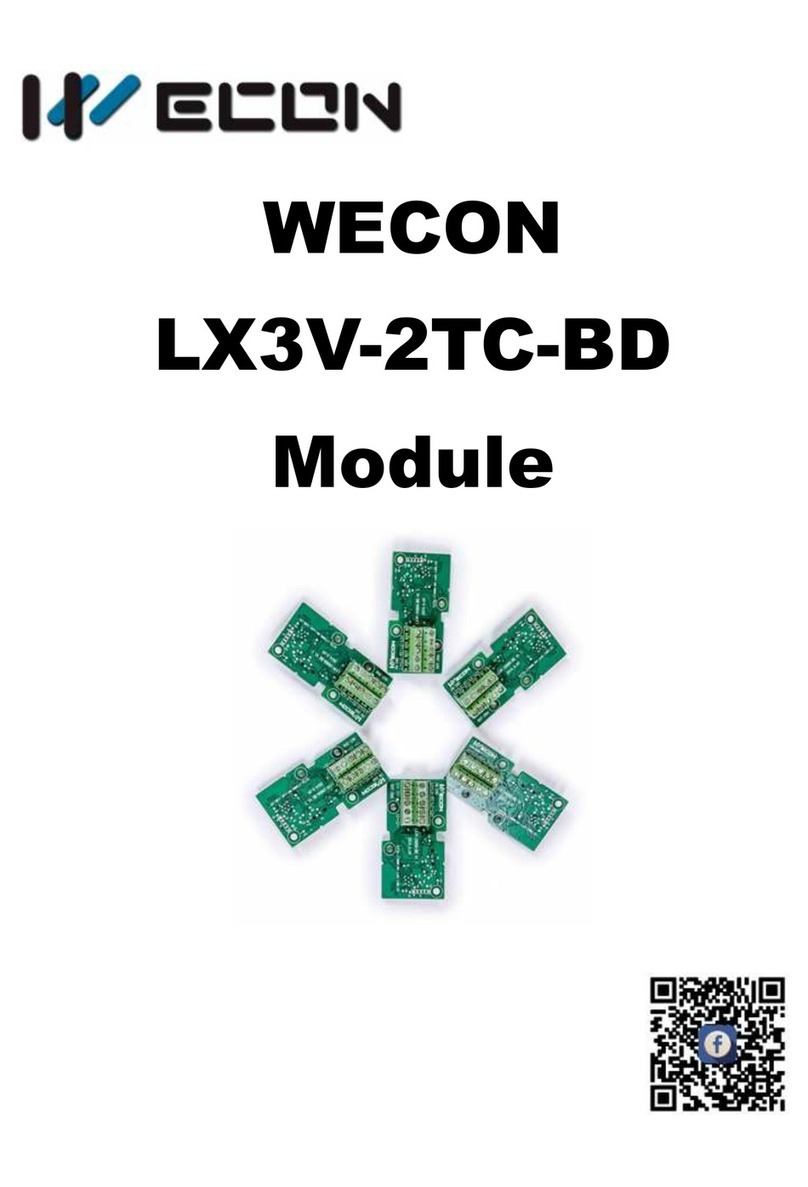
Wecon
Wecon LX3V-2TC-BD User guide
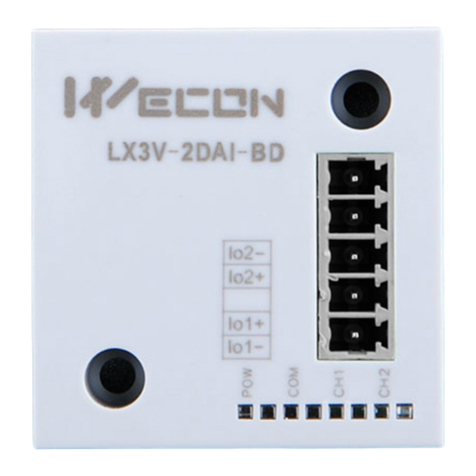
Wecon
Wecon LX3V-2DAI-BD User manual
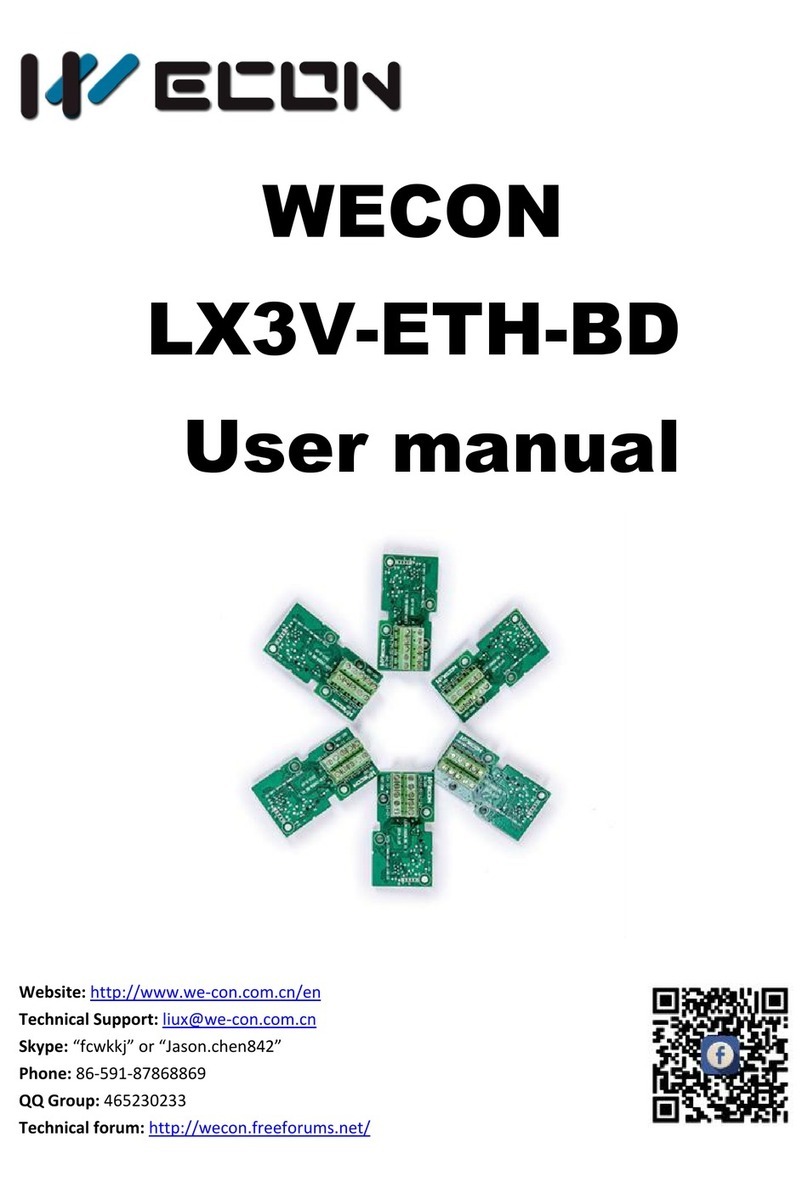
Wecon
Wecon LX3V-ETH-BD User manual
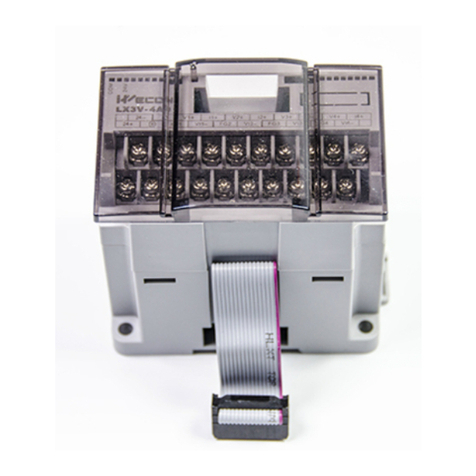
Wecon
Wecon LX3V-4AD Quick start guide
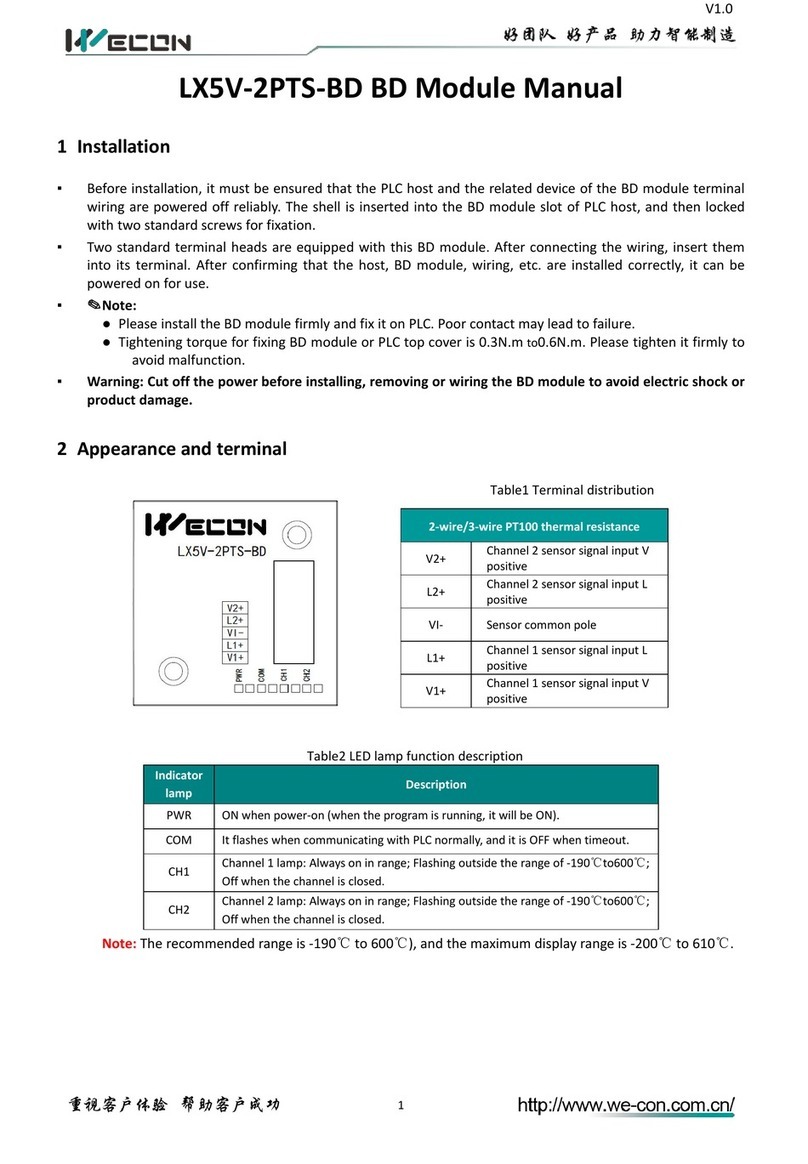
Wecon
Wecon LX5V-2PTS-BD User manual

Wecon
Wecon LX3V-16EY User manual
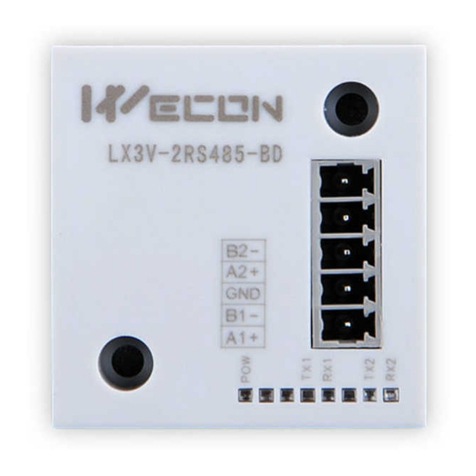
Wecon
Wecon LX3V-2DAV-BD User manual
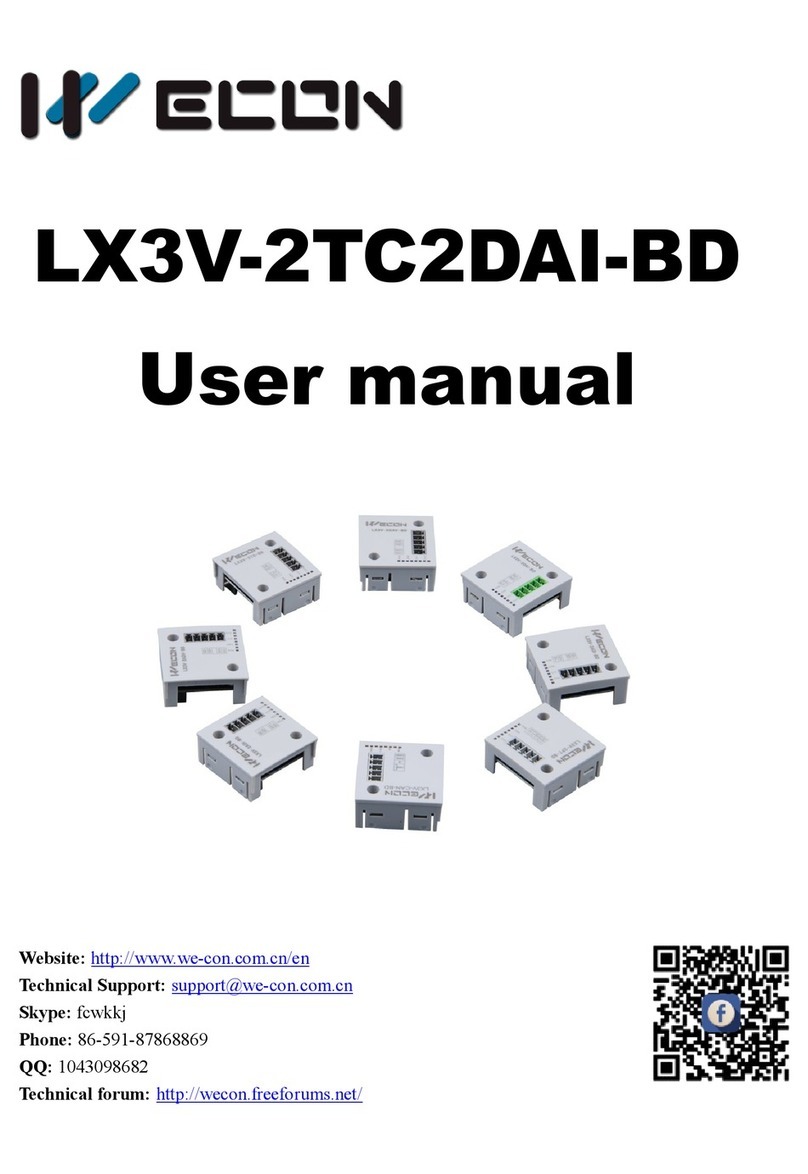
Wecon
Wecon LX3V-2TC2DAI-BD User manual
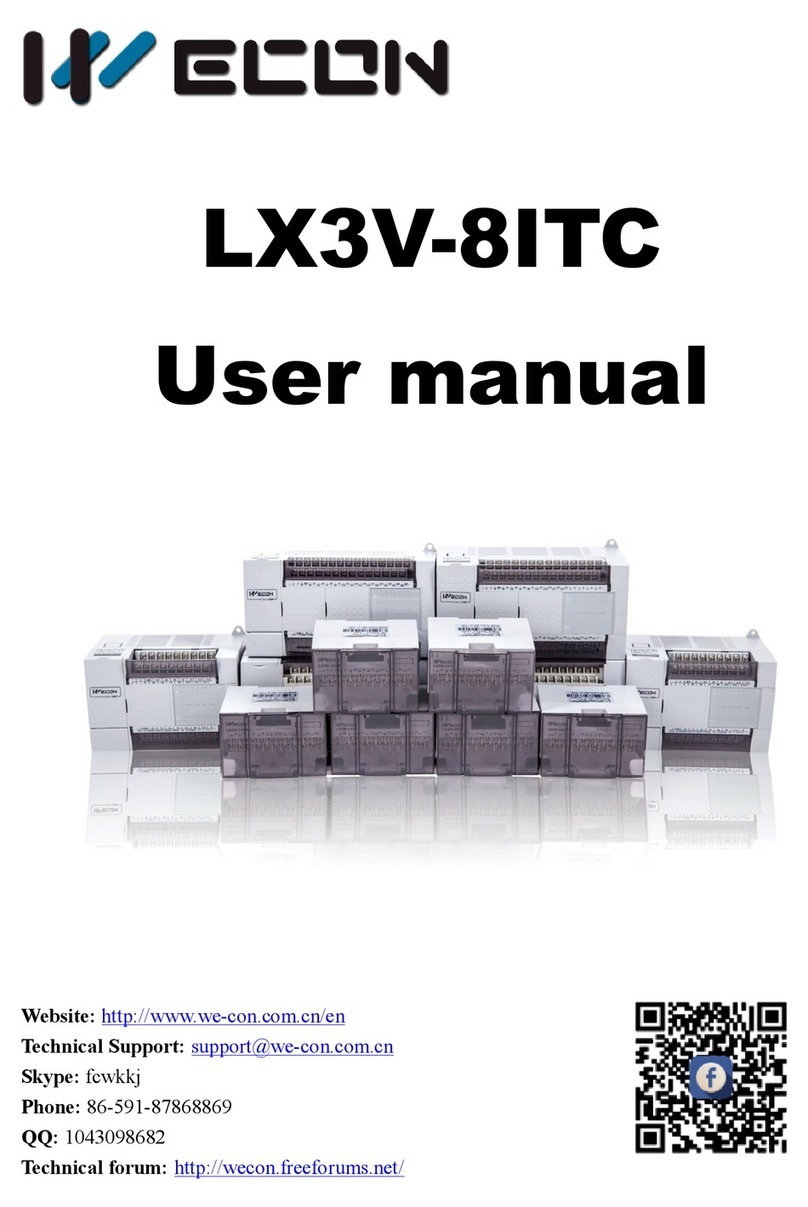
Wecon
Wecon LX3V-8ITC User manual
Popular Control Unit manuals by other brands
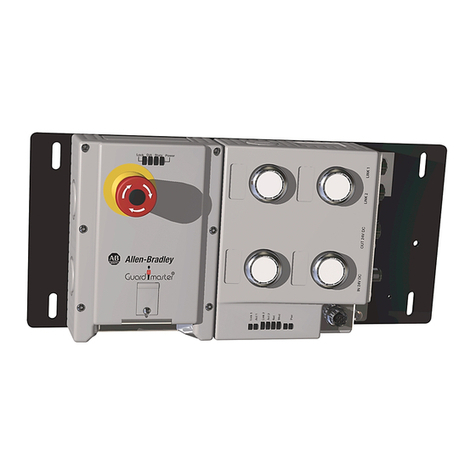
Rockwell Automation
Rockwell Automation Allen-Bradley Compact GuardLogix 5370... Application Technique

Novar
Novar ETM-2040 installation instructions
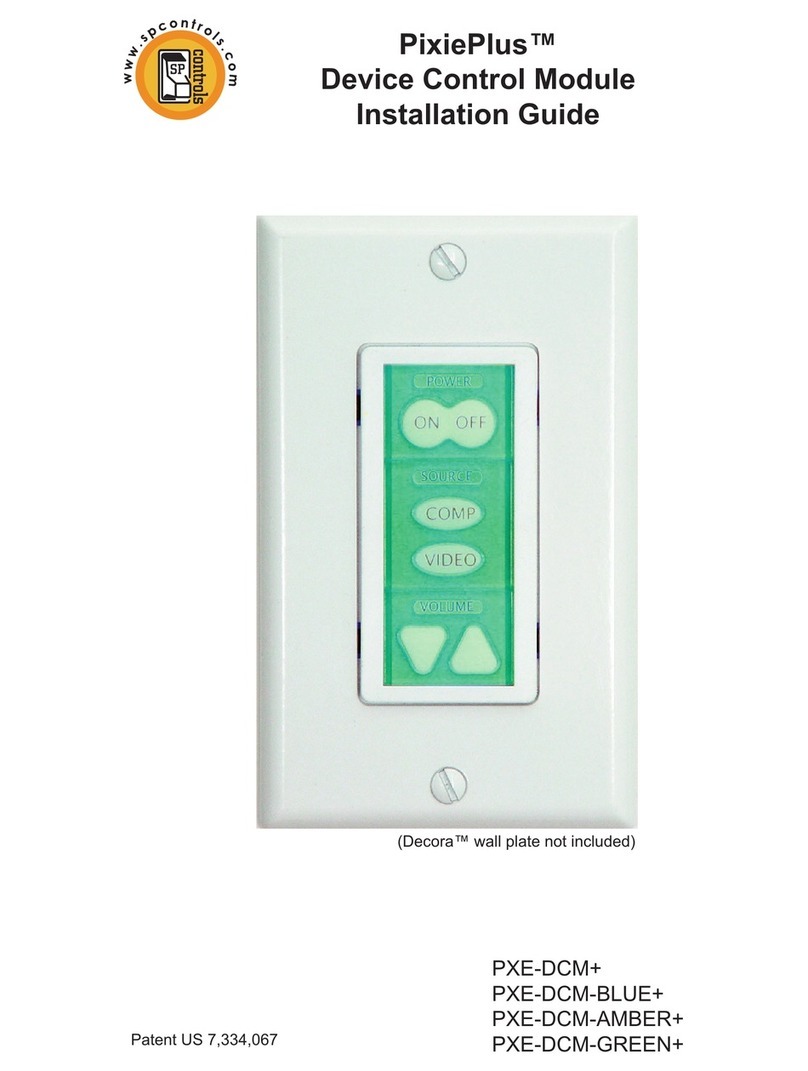
SP Controls
SP Controls PixiePlus PXE-DCM PLUS installation guide
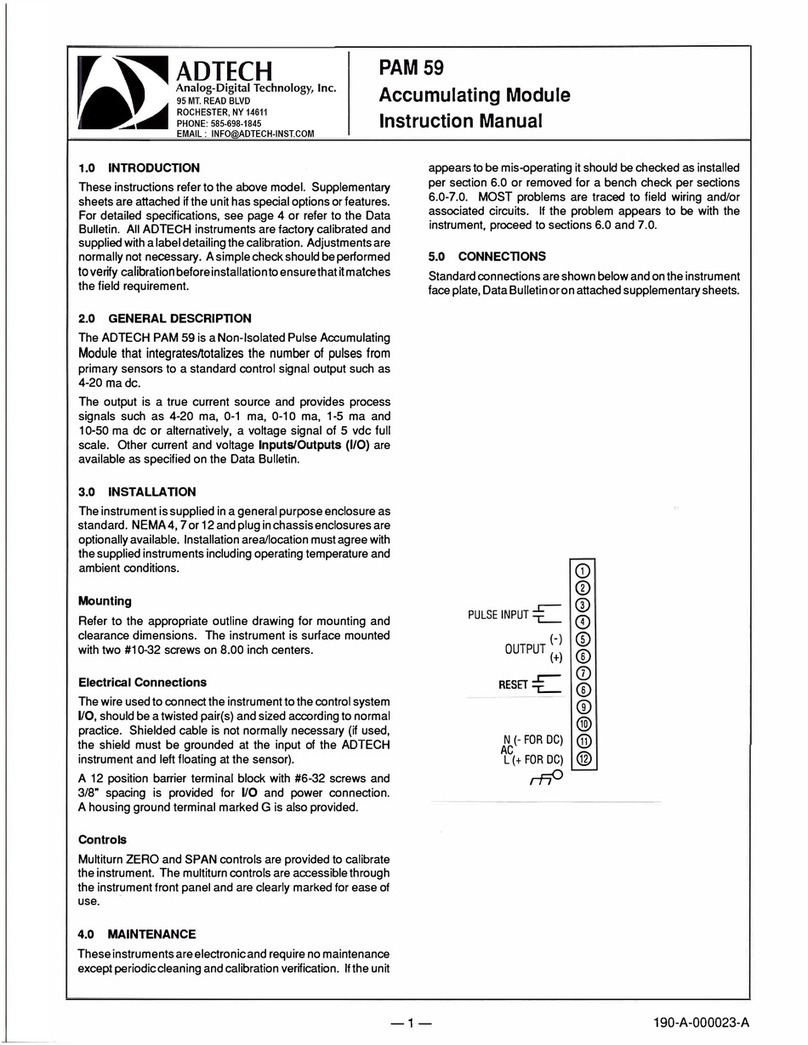
Adtech
Adtech PAM59 instruction manual
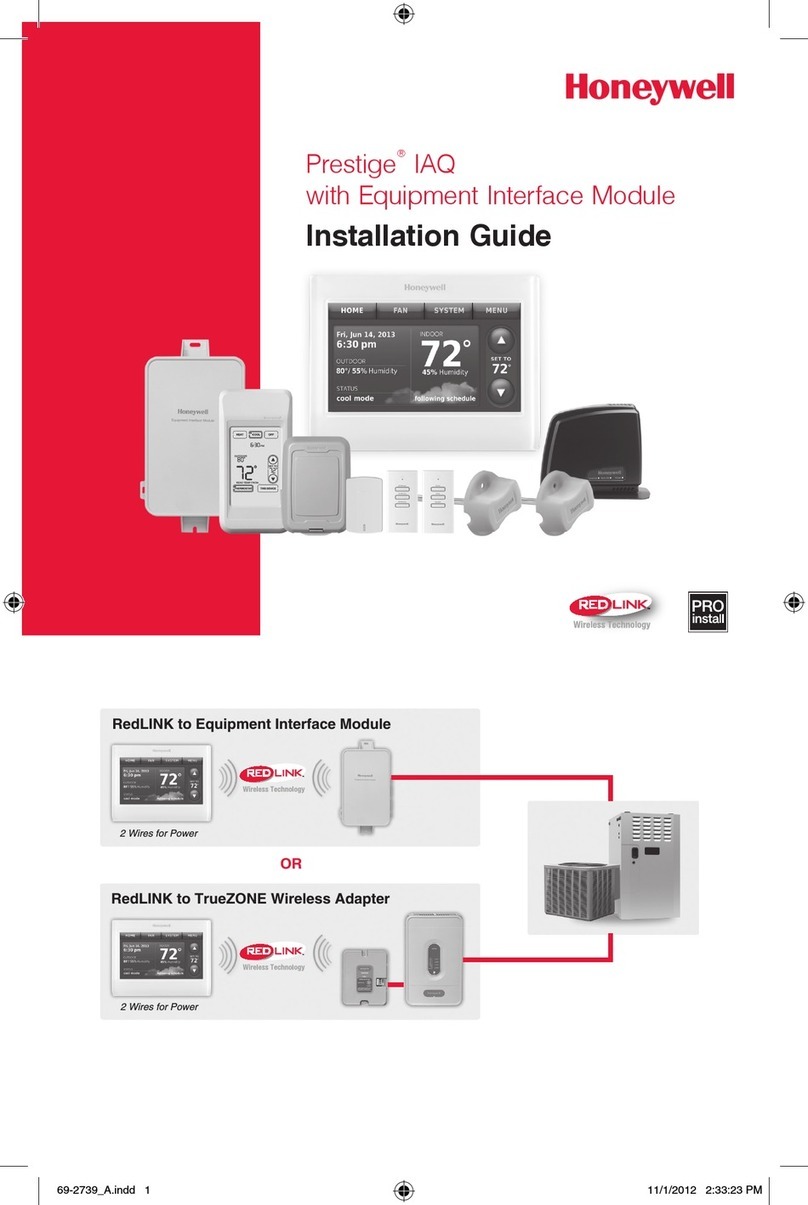
Honeywell
Honeywell Prestige THX9421R02 installation guide
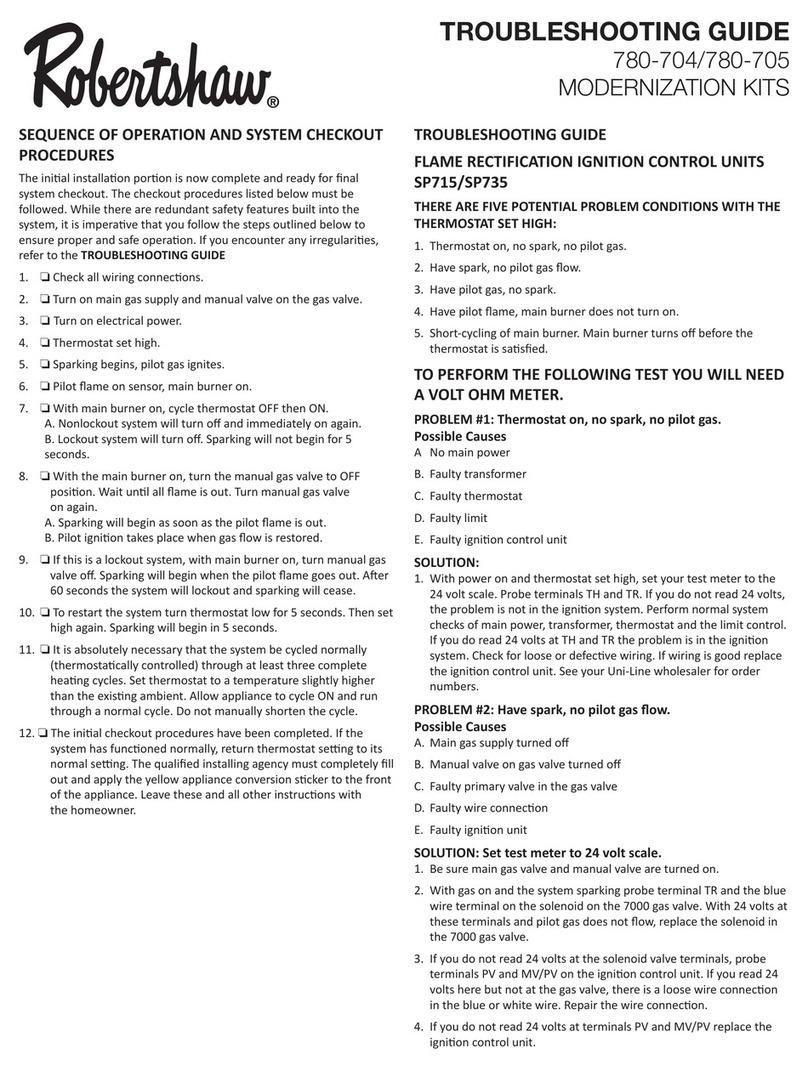
Robertshaw
Robertshaw 780-704 troubleshooting guide