WEG SCW100 Series User manual

Starter Manager
SCW100
User's Manual
Motors | Automation | Energy | Transmission & Distribution | Coatings

User Manual
Series: SCW100
Language: English
Document: 10006801366 / 01
Model: Modbus-RTU
Firmware version: V1.0X
Publication Date: 08/2021

Summary of the Revisions
The information below describes the revisions made to this manual.
Version Revision Description
V1.0X R00 First edition
V1.0X R01 General review

Summary
1 SAFETY INSTRUCTIONS ....................................................................... 1-1
1.1 SAFETY WARNINGS IN THIS MANUAL .........................................................................................1-1
1.2 PRELIMINARY RECOMMENDATIONS ..........................................................................................1-1
2 GENERAL INFORMATION......................................................................2-1
2.1 ABOUT THE MANUAL .....................................................................................................................2-1
2.2 TERMS AND DEFINITIONS USED IN THE MANUAL....................................................................2-1
2.3 NUMERICAL REPRESENTATION.................................................................................................. 2-2
2.4 ABOUT THE SCW100 ..................................................................................................................... 2-2
2.5 HOW TO SPECIFY THE SCW100 MODEL .................................................................................... 2-4
2.6 RECEIVING AND STORING ........................................................................................................... 2-4
3 INSTALLING AND CONNECTING ..........................................................3-1
3.1 MECHANICAL INSTALLATION ...................................................................................................... 3-1
3.1.1 Environment Conditions ....................................................................................................... 3-1
3.1.2 Positioning and Fixing .......................................................................................................... 3-1
3.2 ELECTRICAL INSTALLATION........................................................................................................ 3-2
3.3 ENERGIZATION .............................................................................................................................. 3-4
3.4 CONNECTING THE STARTER MODULES OR I/O DEVICES ...................................................... 3-5
3.5 CONNECTING THE RS485 INTERFACE ....................................................................................... 3-5
4 OPERATING MODES ..............................................................................4-1
5 MODBUS ADDRESS/PARAMETER DESCRIPTION ............................5-1
5.1 FIRMWARE VERSION..................................................................................................................... 5-1
5.2 READING OF THE ROTATING SWITCHES ................................................................................... 5-1
5.3 STATUS OF THE DIGITAL INPUTS ................................................................................................ 5-2
5.4 STATUS OF THE DIGITAL OUTPUTS ............................................................................................ 5-2
5.5 RS485 - ADDRESS ......................................................................................................................... 5-3
5.6 RS485 - BAUD RATE ...................................................................................................................... 5-3
5.7 RS485 - BYTE CONFIGURATION .................................................................................................. 5-3
5.8 RS485 - TIME FOR DETECTING COMMUNICATION FAULT ...................................................... 5-3
5.9 RS485 - ACTION FOR COMMUNICATION FAULT ....................................................................... 5-4
5.10 CONTACTOR CLOSING AND OPENING TIME ........................................................................... 5-4
5.11 OPERATION COUNTERS.............................................................................................................. 5-5
5.12 SAVING OPERATION COUNTERS IN MEM NV .......................................................................... 5-6
5.13 RESET OPERATION COUNTERS ................................................................................................ 5-6
5.14 STATUS OF THE STARTERS ........................................................................................................ 5-7
5.15 ERROR AND ALARM LOG ........................................................................................................... 5-9
5.16 OPERATING MODES ...................................................................................................................5 -11
5.17 TIMEOUT OF THE CONTACTORS ..............................................................................................5 -11
5.18 CPU TEMPERATURE...................................................................................................................5-12
5.19 FACTORY RESET .........................................................................................................................5 -12
5.20 FORWARD START COMMAND ..................................................................................................5-13
5.21 REVERSE START COMMAND ....................................................................................................5-13
5.22 STOP COMMAND........................................................................................................................5-14
5.23 DIGITAL OUTPUT COMMAND5 .................................................................................................5-14
6 DIAGNOSTICS VIA LEDS .......................................................................6 -1
7 TECHNICAL CHARACTERISTICS ......................................................... 7-1
7.1 MECHANICAL DATA.........................................................................................................................7-2

Quick Parameter Reference
4 | SCW100
0QUICK PARAMETER REFERENCE
Modbus
Parameter/
Address
Description Adjustable Range Factory
Setting
User
Setting Properties Page
001 Firmware Version 0.0 to 655.35 - ro, 16 bit 5-1
010 Rotating Switch S1 0 to 15 - ro, 8 bit 5-1
011 Rotating Switch S2 0 to 15 - ro, 8 bit 5-1
012 Rotating Switch S3 0 to 15 - ro, 8 bit 5-1
015 Status of the Digital Inputs Bit 0 = DI1
Bit 1 = DI2
Bit 2 = DI3
Bit 3 = DI4
Bit 4 = DI5
Bit 5 = DI6
Bit 6 = DI7
Bit 7 = DI8
Bit 8 = DI9
Bit 9 = DI10
Bit 10 = DI11
Bit 11 = DI12
- ro, 12 bit 5-2
016 Status of the Digital Outputs Bit 0 = DO1
Bit 1 = DO2
Bit 2 = DO3
Bit 3 = DO4
Bit 4 = DO5
Bit 5 = DO6
Bit 6 = DO7
Bit 7 = DO8
- ro, 8 bit 5-2
020 RS485 - Address 0 to 255 - ro, 8 bit 5-3
021 RS485 - Baud Rate 0 = 9600 kbps
1 = 19200 kbps
2 = 38400 kpbs
3 = 57600 kbps
4 = 76800 kpbs
-ro, enum 5-3
022 RS485 - Byte Configuration 0 = no parity, 2sb
1 = even parity, 1sb
2 = odd parity, 1 sb
-ro, enum 5-3
100 RS485 - Time for Communication
Fault
0.0 to 6553.5 s 0.0 s rw, 16 bit 5-3
101 RS485 - Action for Communication
Fault
0 = No Action
1 = Turn off Outputs
1rw, enum 5-4
120 P1 Contactor 1 Closing Time 0 to 65535 ms - ro, 16 bit 5-4
121 P1 Contactor 1 Opening Time 0 to 65535 ms - ro, 16 bit 5-4
122 P1 Contactor 2 Closing Time 0 to 65535 ms - ro, 16 bit 5-4
123 P1 Contactor 2 Opening Time 0 to 65535 ms - ro, 16 bit 5-4
124 P2 Contactor 1 Closing Time 0 to 65535 ms - ro, 16 bit 5-4
125 P2 Contactor 1 Opening Time 0 to 65535 ms - ro, 16 bit 5-4
126 P2 Contactor 2 Closing Time 0 to 65535 ms - ro, 16 bit 5-4
127 P2 Contactor 2 Opening Time 0 to 65535 ms - ro, 16 bit 5-4
128 P3 Contactor 1 Closing Time 0 to 65535 ms - ro, 16 bit 5-4
129 P3 Contactor 1 Opening Time 0 to 65535 ms - ro, 16 bit 5-4
130 P3 Contactor 2 Closing Time 0 to 65535 ms - ro, 16 bit 5-4
131 P3 Contactor 2 Opening Time 0 to 65535 ms - ro, 16 bit 5-4
132 P4 Contactor 1 Closing Time 0 to 65535 ms - ro, 16 bit 5-4
133 P4 Contactor 1 Opening Time 0 to 65535 ms - ro, 16 bit 5-4
134 P4 Contactor 2 Closing Time 0 to 65535 ms - ro, 16 bit 5-4
135 P4 Contactor 2 Opening Time 0 to 65535 ms - ro, 16 bit 5-5
150 P1 C1 Operation Counter 0 to 65535 - ro, 16 bit 5-5
151 P1 C2 Operation Counter 0 to 65535 - ro, 16 bit 5-5
152 P2 C1 Operation Counter 0 to 65535 - ro, 16 bit 5-5
153 P2 C2 Operation Counter 0 to 65535 - ro, 16 bit 5-5
154 P3 C1 Operation Counter 0 to 65535 - ro, 16 bit 5-5
155 P3 C2 Operation Counter 0 to 65535 - ro, 16 bit 5-5
156 P4 C1 Operation Counter 0 to 65535 - ro, 16 bit 5-5
157 P4 C2 Operation Counter 0 to 65535 - ro, 16 bit 5-5
158 Save Operation Counters in the mem NV false to true false rw, bool 5-6

Quick Parameter Reference
SCW100 | 5
0
Modbus
Parameter/
Address
Description Adjustable Range Factory
Setting
User
Setting Properties Page
160 Reset P1 C1 Operation Counter 0 to 65535 0 rw, 16 bit 5-6
161 Reset P1 C2 Operation Counter 0 to 65535 0 rw, 16 bit 5-6
162 Reset P2 C1 Operation Counter 0 to 65535 0 rw, 16 bit 5-6
163 Reset P2 C2 Operation Counter 0 to 65535 0 rw, 16 bit 5-6
164 Reset P3 C1 Operation Counter 0 to 65535 0 rw, 16 bit 5-6
165 Reset P3 C2 Operation Counter 0 to 65535 0 rw, 16 bit 5-6
166 Reset P4 C1 Operation Counter 0 to 65535 0 rw, 16 bit 5-6
167 Reset P4 C2 Operation Counter 0 to 65535 0 rw, 16 bit 5-6
200 P1 Status 0 to 65535 - ro, 16 bit 5-7
201 P1 Status - Contactor 0 to 1 - ro, 16 bit 5-7
202 P1 Status - Error 0 to 65535 - ro, 16 bit 5-7
203 P1 Status - Alarm 0 to 65535 - ro, 16 bit 5-8
204 P2 Status 0 to 65535 - ro, 16 bit 5-7
205 P2 Status - Contactor 0 to 1 - ro, 16 bit 5-7
206 P2 Status - Error 0 to 65535 - ro, 16 bit 5-7
207 P2 Status - Alarm 0 to 65535 - ro, 16 bit 5-8
208 P3 Status 0 to 65535 - ro, 16 bit 5-7
209 P3 Status - Contactor 0 to 1 - ro, 16 bit 5-7
210 P3 Status - Error 0 to 65535 - ro, 16 bit 5-8
211 P3 Status - Alarm 0 to 65535 - ro, 16 bit 5-8
212 P4 Status 0 to 65535 - ro, 16 bit 5-7
213 P4 Status - Contactor 0 to 1 - ro, 16 bit 5-7
214 P4 Status - Error 0 to 65535 - ro, 16 bit 5-8
215 P4 Status - Alarm 0 to 65535 - ro, 16 bit 5-8
300 P1 - Last Error 1 0 to 65535 - ro, 16 bit 5-9
301 P1 - Last Error 2 0 to 65535 - ro, 16 bit 5-9
302 P1 - Last Error 3 0 to 65535 - ro, 16 bit 5-9
303 P1 - Last Error 4 0 to 65535 - ro, 16 bit 5-9
304 P1 - Last Error 5 0 to 65535 - ro, 16 bit 5-9
305 P2 - Last Error 1 0 to 65535 - ro, 16 bit 5-9
306 P2 - Last Error 2 0 to 65535 - ro, 16 bit 5-9
307 P2 - Last Error 3 0 to 65535 - ro, 16 bit 5-9
308 P2 - Last Error 4 0 to 65535 - ro, 16 bit 5-9
309 P2 - Last Error 5 0 to 65535 - ro, 16 bit 5-9
310 P3 - Last Error 1 0 to 65535 - ro, 16 bit 5-9
311 P3 - Last Error 2 0 to 65535 - ro, 16 bit 5-9
312 P3 - Last Error 3 0 to 65535 - ro, 16 bit 5-9
313 P3 - Last Error 4 0 to 65535 - ro, 16 bit 5-9
314 P3 - Last Error 5 0 to 65535 - ro, 16 bit 5-9
315 P4 - Last Error 1 0 to 65535 - ro, 16 bit 5-9
316 P4 - Last Error 2 0 to 65535 - ro, 16 bit 5-9
317 P4 - Last Error 3 0 to 65535 - ro, 16 bit 5-9
318 P4 - Last Error 4 0 to 65535 - ro, 16 bit 5-9
319 P4 - Last Error 5 0 to 65535 - ro, 16 bit 5-10
320 P1 - Last Alarm 1 0 to 65535 - ro, 16 bit 5-10
321 P1 - Last Alarm 2 0 to 65535 - ro, 16 bit 5-10
322 P1 - Last Alarm 3 0 to 65535 - ro, 16 bit 5-10
323 P1 - Last Alarm 4 0 to 65535 - ro, 16 bit 5-10
324 P1 - Last Alarm 5 0 to 65535 - ro, 16 bit 5-10
325 P2 - Last Alarm 1 0 to 65535 - ro, 16 bit 5-10
326 P2 - Last Alarm 2 0 to 65535 - ro, 16 bit 5-10
327 P2 - Last Alarm 3 0 to 65535 - ro, 16 bit 5-10
328 P2 - Last Alarm 4 0 to 65535 - ro, 16 bit 5-10
329 P2 - Last Alarm 5 0 to 65535 - ro, 16 bit 5-10
330 P3 - Last Alarm 1 0 to 65535 - ro, 16 bit 5-10
331 P3 - Last Alarm 2 0 to 65535 - ro, 16 bit 5-10
332 P3 - Last Alarm 3 0 to 65535 - ro, 16 bit 5-10
333 P3 - Last Alarm 4 0 to 65535 - ro, 16 bit 5-10
334 P3 - Last Alarm 5 0 to 65535 - ro, 16 bit 5-10
335 P4 - Last Alarm 1 0 to 65535 - ro, 16 bit 5-10

Quick Parameter Reference
6 | SCW100
0Modbus
Parameter/
Address
Description Adjustable Range Factory
Setting
User
Setting Properties Page
336 P4 - Last Alarm 2 0 to 65535 - ro, 16 bit 5-10
337 P4 - Last Alarm 3 0 to 65535 - ro, 16 bit 5-10
338 P4 - Last Alarm 4 0 to 65535 - ro, 16 bit 5 -11
339 P4 - Last Alarm 5 0 to 65535 - ro, 16 bit 5 -11
400 P1 - Operating Mode 0 = Start
1 = Transparent
0 rw, 16 bit 5-11
401 P2 - Operating Mode 0 = Start
1 = Transparent
0 rw, 16 bit 5-11
402 P3 - Operating Mode 0 = Start
1 = Transparent
0 rw, 16 bit 5-11
403 P4 - Operating Mode 0 = Start
1 = Transparent
0 rw, 16 bit 5-11
404 P1 - Contactor Timeout 20 to 5000 ms 500 ms rw, 16 bit 5-11
405 P2 - Contactor Timeout 20 to 5000 ms 500 ms rw, 16 bit 5-11
406 P3 - Contactor Timeout 20 to 5000 ms 500 ms rw, 16 bit 5-12
407 P4 - Contactor Timeout 20 to 5000 ms 500 ms rw, 16 bit 5-12
500 CPU Temperature -100 to 100 ºC - ro, s16 bit 5-12
1000 Reset to Factory Settings 0 to 65535 0 rw, 16 bit 5-12
1100 Forward Start Command Bit 0 = Starter 1 - forward
Bit 1 = Starter 2 - forward
Bit 2 = Starter 3 - forward
Bit 3 = Starter 4 - forward
0 rw, 4 bit 5-13
1105 Reverse Start Command Bit 0 = Starter 1 - reverse
Bit 1 = Starter 2 - reverse
Bit 2 = Starter 3 - reverse
Bit 3 = Starter 4 - reverse
0 rw, 4 bit 5-13
1110 Stop Command Bit 0 = Starter 1 - stop
Bit 1 = Starter 2 - stop
Bit 2 = Starter 3 - stop
Bit 3 = Starter 4 - stop
0 rw, 4 bit 5-14
1115 Digital Output Command Bit 0 = DO1
Bit 1 = DO2
Bit 2 = DO3
Bit 3 = DO4
Bit 4 = DO5
Bit 5 = DO6
Bit 6 = DO7
Bit 7 = DO8
0 rw, 8 bit 5-14
Data Type Description
bool It represents a bit where value 0 (zero) means false, and value 1 (one) true
enum Enumerated type (8 unsigned bits), it contains a list of values describing the function for each item
8 bit Unsigned 8-bit integer, ranging from 0 to 255
16 bit Unsigned 16-bit integer, ranging from 0 to 65,535
s16 bit Signed 16-bit integer, ranging from -32,768 to 32,767
32 bit Unsigned 32-bit integer, ranging from 0 to 4,294,967,295

Safety Instructions
SCW100 | 1-1
1
1 SAFETY INSTRUCTIONS
This manual contains the information necessary for the correct use of the SCW100 Starter Manager.
It was developed to be used by people with proper technical training or qualification to operate this kind of equipment.
1.1 SAFETY WARNINGS IN THIS MANUAL
The following safety warnings are used in this manual:
DANGER!
Not following the procedures recommended in this warning may lead to death, serious injuries and
considerable material damages.
ATTENTION!
Failure to observe the procedures recommended in this warning may lead to material damages.
NOTE!
The text aims at providing important information for the correct understanding and proper operation
of the product.
1.2 PRELIMINARY RECOMMENDATIONS
DANGER!
Only qualified personnel, familiar with the SCW100 and related equipment, must plan or perform the
installation, commissioning, operation and maintenance of this equipment.
Such personnel must follow the safety instructions described in this manual and/or defined by local
regulations.
Failure to comply with the safety instructions may result in death, serious injury and/or equipment
damage.
NOTE!
For the purposes of this manual, qualified personnel are those trained and able to:
Install, ground, power up and operate the SCW100 in accordance with this manual and the safety
legal procedures in force.
Use the protective equipment according to the established regulations.
Provide first aid.
DANGER!
Always disconnect the general power supply before touching any electrical component connected
to the SCW100.
ATTENTION!
The electronic boards have electrostatic discharge sensitive components. Do not touch the
components or connectors directly.
NOTE!
Read this manual thoroughly before installing or operating this equipment.

General Information
SCW100 | 2-1
2
2 GENERAL INFORMATION
2.1 ABOUT THE MANUAL
This manual contains directions to install and commission WEG SCW100 Starter Manager and describes its main
features.
For information on other functions, accessories and operating conditions, refer to the following manual:
Modbus-RTU communication manual.
This manual is available for download on WEG website: www.weg.net.
2.2 TERMS AND DEFINITIONS USED IN THE MANUAL
A: ampere, electric current level unit of measurement.
V: volt, voltage unit of measurement.
PC: personal computer.
PE: protective earth.
DC: direct current.
PLC: programmable logic controller.
s: second, unit of measurement of time.
ms: millisecond = 0.001 seconds.
m: meter, unit of measurement of length.
mm: millimeter = 0.001 m.
ºC: temperature unit in degrees celsius.
NV: non-volatile.
CPU: central process unit.
I/O: acronym for input/output.
DI: acronym for digital input.
DO: acronym for digital output.
LSB: least significant bit/byte.
MSB: most significant bit/byte.
RTU: remote terminal unit.
SELV: separated extra-low voltage (extra low voltage system that is electrically separated from the earth).
PELV: protected extra-low voltage system that is not electrically separated from the earth but satisfies, in an
equivalent way, all the requirements of a SELV.

General Information
2-2 | SCW100
2
2.3 NUMERICAL REPRESENTATION
Decimal numbers are represented by means of digits without suffix. Hexadecimal numbers are represented with
the letter 'h' after the number.
2.4 ABOUT THE SCW100
The SCW100 (Smart Connection WEG) is a motor starter manager with a line of accessories developed to ensure
the drive and complete management of electric motor starters. It has an isolated fieldbus communication network,
RS485 with Modbus-RTU protocol, which allows connection to a PLC (edge device) that can send commands
and read diagnostics, processing and providing information for a higher level network.
The Starter Manager (SCW100-SM) performs all the work so that the starters operate properly, being responsible
for the drive and diagnostics, such as operating time, number of operations, reversals, etc. Such information can
be exchanged with the master controller via communication network.
The Starter Modules (SCW100-CM) are directly fitted (no screws required) to the contactors of the CWB9…18/
CWB25…38 line and MPW40 motor-protective circuit breaker. They generate the signals necessary for the Starter
Manager analysis (SCW100-SM). For details on mounting, refer to the installation guide that accompanies the
product (SCW100-CM). This installation guide is also available for download on the website: www.weg.net.
There are specific models of Starter Modules (SCW100-CM) according to the starter type: forward drive with
protection (motor-protective circuit breaker and contactor), reverse drive with protection (motor-protective circuit
breaker and two contactors), forward drive without protection (contactor), reverse drive without protection (two
contactors). It also allows you to connect auxiliary input and output devices (I/O) (pushbuttons, indication, drive
switches etc).
The interconnection between the Starter Manager (SCW100-SM) and the Starter Modules (SCW100-CM) is
made by RJ45 cables (SCW100-RJ). A single cable allows total control of the starter, without requiring any other
element for the control circuit, which ensures fast and simple installation, in addition to guaranteeing the correct
assembly (error-proof).

General Information
SCW100 | 2-3
2
(a) Starter manager (SCW100-SM) (b) Forward start contactor module (SCW100-CM-001)
(c) Reverse start contactor module (SCW100-CM-002) (d) Forward starter module (SCW100-CM-011)
(e) Reverse starter module (SCW100-CM-012) (f) Input and output devices (I/O)
Figure 2.1: SCW100 components

General Information
2-4 | SCW100
2
2.5 HOW TO SPECIFY THE SCW100 MODEL
To specify the SCW100 model, see the catalog available for download on the website: www.weg.net.
2.6 RECEIVING AND STORING
The SCW100 is supplied packaged in a cardboard box. This package contains a label outside describing the main
characteristics of the product: model, WEG stock item, serial number, manufacturing date and firmware version.
In order to open the package:
1. Place the package on a table.
2. Open the package.
3. Remove the product.
Check if:
The identification label matches the purchased model.
Damages occurred during transportation. If any problem is found, contact the carrier immediately.
If the SCW100 is not installed soon, keep it in the package closed and store it in a clean and dry location with
temperature between -25 ºC and 80 ºC (-13 ºF and +176 ºF).

Installing and Connecting
SCW100 | 3-1
3
3 INSTALLING AND CONNECTING
This chapter describes the procedures for the electric and mechanical installation of the SCW100. The directions
and suggestions must be observed in order to ensure the safety of people and equipment and the proper operation
of the SCW100.
3.1 MECHANICAL INSTALLATION
The Smart Connection SCW100 was designed for industrial or professional use only, to be installed in electrical
panels or the like.
3.1.1 Environment Conditions
Avoid:
Direct exposure to sunlight, rain, excessive moisture or sea air.
Inflammable or corrosive liquids or gases.
Excessive vibration.
Dust, metallic particles or oil mist.
Closeness to strong magnetic fields or high-current cables.
Environmental conditions for operation:
Temperature: 0 °C to 55 °C (32 ºF to 131 ºF).
Air relative humidity: 5 % to 90 % non-condensing.
Pollution degree: 2, with non-conductive pollution. Condensation must not cause conduction through the
accumulated residues.
Exclusive use for Zones A and B according to IEC 61131-2.
Maximum altitude: 2000 m (6.600 ft) above sea level - rated conditions. For applications at higher altitudes,
contact WEG.
3.1.2 Positioning and Fixing
The Starter Manager (SCW100-SM) can be installed in any position. The Starter Modules are fitted to the contactors
of the CWB9…18/CWB25..38 line and MPW40 motor-protective circuit breaker. For details on mounting, refer
to the installation guide that accompanies the product (SCW100-CM). This installation guide is also available for
download on the website: www.weg.net.
Figure 3.1: Mounting the Starter Manager (SCW100-SM) on DIN rail 35 mm (1.32 in)

Installing and Connecting
3-2 | SCW100
3
3.2 ELECTRICAL INSTALLATION
DANGER!
The following information is a guide for proper installation. Comply with applicable regulations for
electrical installations.
The Starter Manager (SCW-100-SM), shown in Figure 3.2 on page 3-2, is supplied with two removable terminal
blocks: one for the power cable connections (connector 5) and another for the RS485 communication interface
(connector 6) - both with 4 pins each. It also has four RJ45 terminals (connectors 1 to 4) to connect the Starter
Modules (accessories of the SCW100 line) or input and output devices. The connection is made through a RJ45
cable (SCW100-RJ), available in lengths of 1 m (3.28 ft) and 2 m (6.56 ft).
ATTENTION!
The RJ45 connectors available on the front of the Starter Manager (SCW100-SM) are exclusive for
connection to the Starter Modules (SCW100-CM). These connectors must not be connected to
ethernet networks, at risk of damaging the product.
ATTENTION!
It is recommended to use RJ45 cables (SCW100-RJ) of the SCW100 line. If cables with dimensions
different from the ones provided are required, they must not exceed 2 m (6.56 ft) and withstand the
minimum current of 500 mA.
5
4
3
2
1
6
8
1
Figure 3.2: SCW100-SM connections
The following table shows the formation of RJ45 connector pins:
Pin n° Designation Signal Description
1 Input 1 Direction status 1 Input active if the power contacts of output contactor 1 (direction 1) are closed
2 Input 2 Direction status 2 Input active if the power contacts of output contactor 2 (direction 2) are closed
3 Input 3 Motor protector status Input active if the motor protector power contacts are closed
40 Vdc – –
5Output 1 Direction control 1 Drives the direct motor control
6Output 2 Direction control 2 Drives the reverse motor control
724 Vdc Common for sensors Power supply for outputs 1 and 2 (pins 5 and 6)
80 Vdc – –

Installing and Connecting
SCW100 | 3-3
3
SCW100-CM-001
SCW100-SM
SCW100-RJ
S CW10 0 - CM - 011 SCW100-CM-012
SCW100-CM-002
Figure 3.3: Connections of the SCW100-SM to the Starter Modules (SCW100-CM)

Installing and Connecting
3-4 | SCW100
3
3.3 ENERGIZATION
The Starter Manager (SCW100-SM) is powered through connector 5 Figure 3.2 on page 3-2, as indicated in
Table 3.1 on page 3-4.
Table 3.1: Power supply connector terminals
Pin Lettering Description
1A1 24 Vdc - Control system power supply
2A1 (AUX ) 24 Vdc - Digital output power supply
3A2 0 Vdc - Power supply reference
4 PE Protective earth
4
2 A
+
-
24 V
3 2 1
Figure 3.4: Example of the DC power supply connection
ATTENTION!
Use a SELV/PELV power supply. The input power supply voltage must be compatible with the
SCW100-SM rated voltage.
ATTENTION!
To ensure proper protection for your equipment, use a type-T fuse with current capacity compatible
with the load.
ATTENTION!
Pin 4 (PE) of the power connector must be connected to a protective earth.
ATTENTION!
It is recommended that the 24 Vdc power supply for the digital outputs (pin 2 of the power supply
connector) pass through the machine/ equipment safety circuit so as to guarantee that, in emergency
situations, loads driven by the Starter Manager (SCW100-SM) will be turned off via function redundancy.

Installing and Connecting
SCW100 | 3-5
3
3.4 CONNECTING THE STARTER MODULES OR I/O DEVICES
The Starter Modules or input and output devices (I/O) are connected through the RJ45 connectors. There are 4
groups (connectors 1 to 4 - Figure 3.2 on page 3-2), divided according to Table 3.2 on page 3-5.
Table 3.2: RJ45 connector terminals
RJ45 Connectors
Description
Pin Group 1
(Connector 1)
Group 2
(Connector 2)
Group 3
(Connector 3)
Group 4
(Connector 4)
1DI1 DI4 DI7 DI10 Digital inputs 1, 4, 7, 10
2DI2 DI5 DI8 DI11 Digital inputs 2, 5, 8, 11
3DI3 DI6 DI9 DI12 Digital inputs 3, 6, 9, 12
40 Vdc Digital input and output power supply reference
5DO1 DO3 DO5 DO7 Digital outputs 1, 3, 5, 7
6DO2 DO4 DO6 DO8 Digital outputs 2, 4, 6, 8
724 Vdc 24 Vdc output - Digital input power supply
80 Vdc Digital input and output power supply reference
ATTENTION!
To connect I/O devices, the maximum current per digital output must not exceed 250 mA.
3.5 CONNECTING THE RS485 INTERFACE
The RS485 interface connections of the Starter Manager (SCW100-SM) must be made through connector 6
Figure 3.1 on page 3-1, according to Table 3.3 on page 3-5 and detailed in Figure 3.3 on page 3-3.
Table 3.3: RS485 interface connector terminals
Pin Lettering Description
5B (+) Terminal B (Line +)
6SHIELD Cable shield
7A (-) Terminal A (Line -)
8GND Reference 0 V
NOTE!
For the settings of the RS485 network, refer to the communication manual. This manual is available
for download on WEG website: www.weg.net.
5678
Ref (0 V)Ref (0 V)
Shield Shield
B (+)
B (+)
A (-)
A (-)
Figure 3.5: Example of connection to the RS485 network

Installing and Connecting
3-6 | SCW100
3
ATTENTION!
Pin 6 (SHIELD) of the RS485 interface connector must be connected to a protective earth.
NOTE!
For further details regarding the settings of the Starter Manager (SCW100) to operate on a network,
refer to the SCW100 communication manuals, available for download on the website: www.weg.net.

Operating Modes
SCW100 | 4-1
4
4 OPERATING MODES
The SCW100 has two operating modes: Starter and Transparent. It is programmed at the factory to the "Starter"
mode, which simplifies the control, monitoring and diagnostics on the components of a forward and reverse
starter. In this operating mode, the SCW100 performs the complete management of motor starters, reporting
errors, alarms, times, diagnostics, etc.
The "Transparent" mode is intended to connect discrete components to the digital inputs and outputs of the
SCW100. In this mode, errors, alarms, times and diagnostics in general, related to the starting of motors, are not
checked. The transparent mode has three (3) digital inputs and two (2) digital outputs available for general purpose
in each RJ45 connector, that is, they can activate indication lamps, contactors, etc. and read pushbuttons, auxiliary
contacts, etc. This mode can be thought of as a remote digital input/output (I/O) unit.
To configure the operating mode, check the modbus addresses 400 to 403.
ATTENTION!
In the "transparent" mode, the maximum current per digital output must not exceed 250 mA.

Description of the Modbus Parameters/Addresses
SCW100 | 5-1
5
5 MODBUS ADDRESS/PARAMETER DESCRIPTION
5.1 FIRMWARE VERSION
The value read corresponds to the firmware version of the SCW100.
Modbus address: 001.
001 – Firmware Version
Adjustable
Range:
0.0 to 655.35 Factory Setting: -
Properties: ro, 16 bit
Value read: "123", corresponds to version "1.23" of the equipment firmware.
5.2 READING OF THE ROTATING SWITCHES
Hexadecimal-type rotary switches S1, S2 and S3, located on the side of the product, are used for the settings of
the Modbus-RTU network.
The value read of each switch is between 0 and 15, which represents 00 h to 0 Fh in hexadecimal.
Modbus addresses and function of each switch:
010 – Rotary Switch S1 - LSB (Least Significant Byte) of the Address
011 – Rotary Switch S2 - MSB (Most Significant Byte) of the Address
Adjustable
Range:
0 to 15 Factory Setting: -
Properties: ro, 8 bit
Modbus addresses 010 and 011 indicate the selected serial address using configuration switches S1 and S2.
Each device on the network must have an address that is different from all others.
012 – Rotary Switch S3 - Baud Rate, Stop Bits and Parity
Adjustable
Range:
0 to 15 Factory Setting: -
Properties: ro, 8 bit
The modbus address 012 indicates the baud rate of the serial interface in bits per second, parity and stop bits
for the bytes of the serial interface, selected using the configuration switch S3. This setting must be the same for
all the devices connected to the network.
NOTE!
If the configuration of switch S1, S2 or S3 is changed, it will only be valid after the SCW100 is turned
off and back on.
NOTE!
For further details regarding the settings of the Starter Manager (SCW100) to operate on a network,
refer to the SCW100 communication manuals, available for download on the website: www.weg.net.
Other manuals for SCW100 Series
1
This manual suits for next models
1
Table of contents
Other WEG Controllers manuals
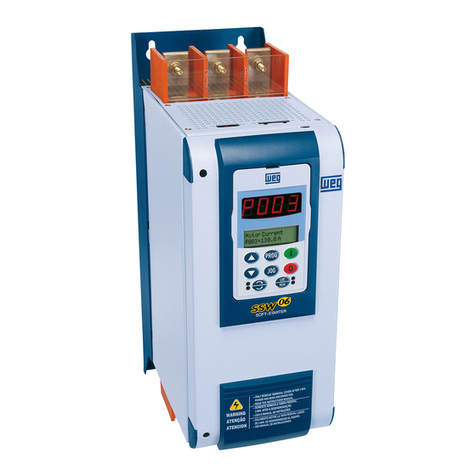
WEG
WEG SSW06 User manual
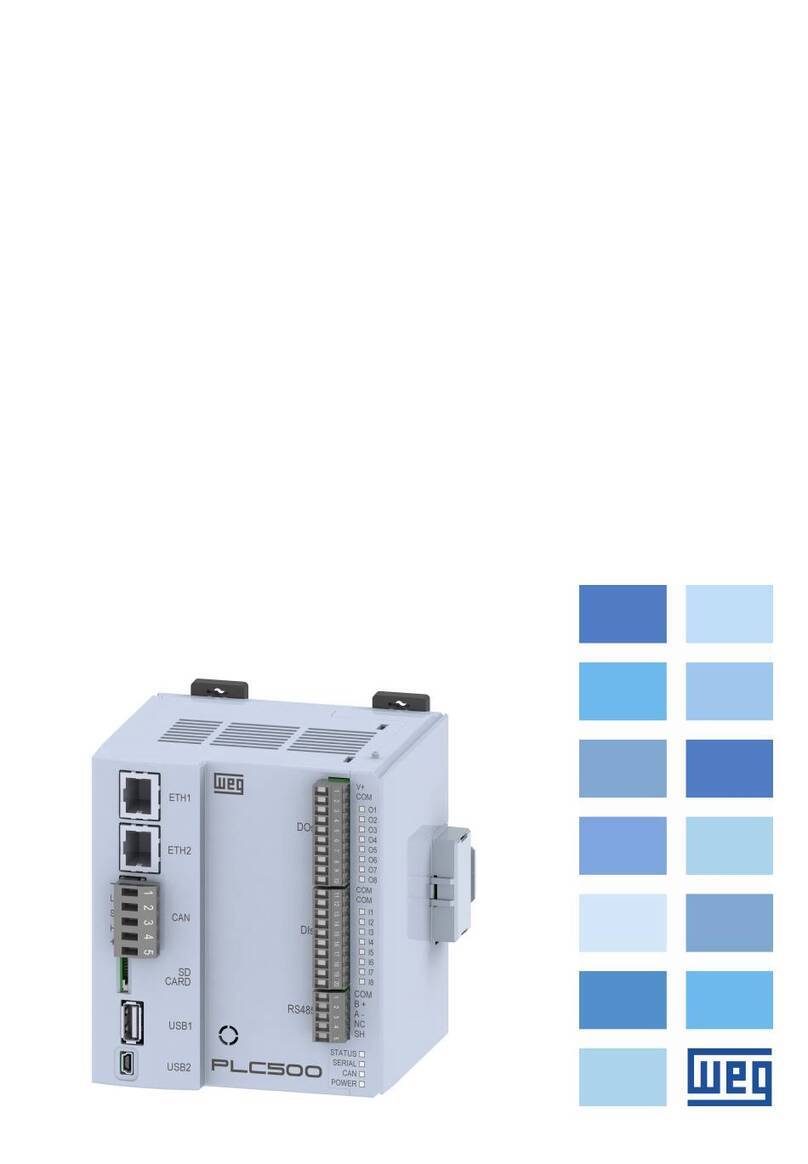
WEG
WEG PLC500 Installation and operating instructions
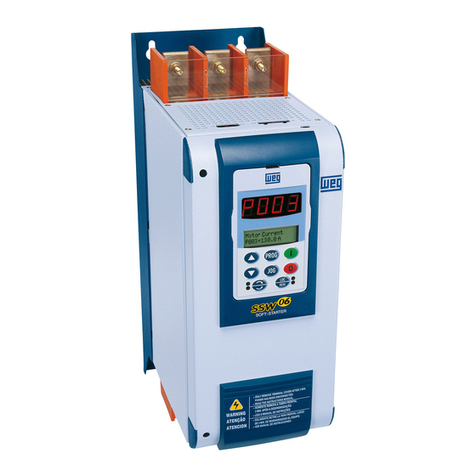
WEG
WEG SSW06 User manual
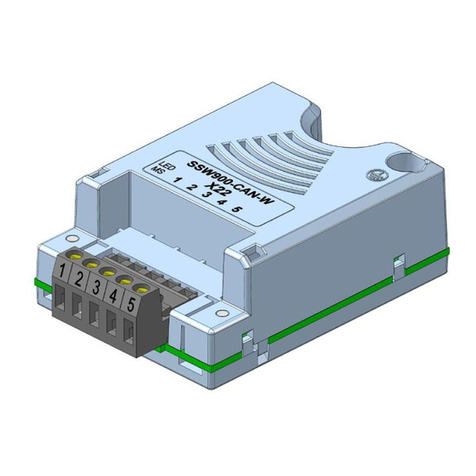
WEG
WEG SSW900-CAN-W User manual
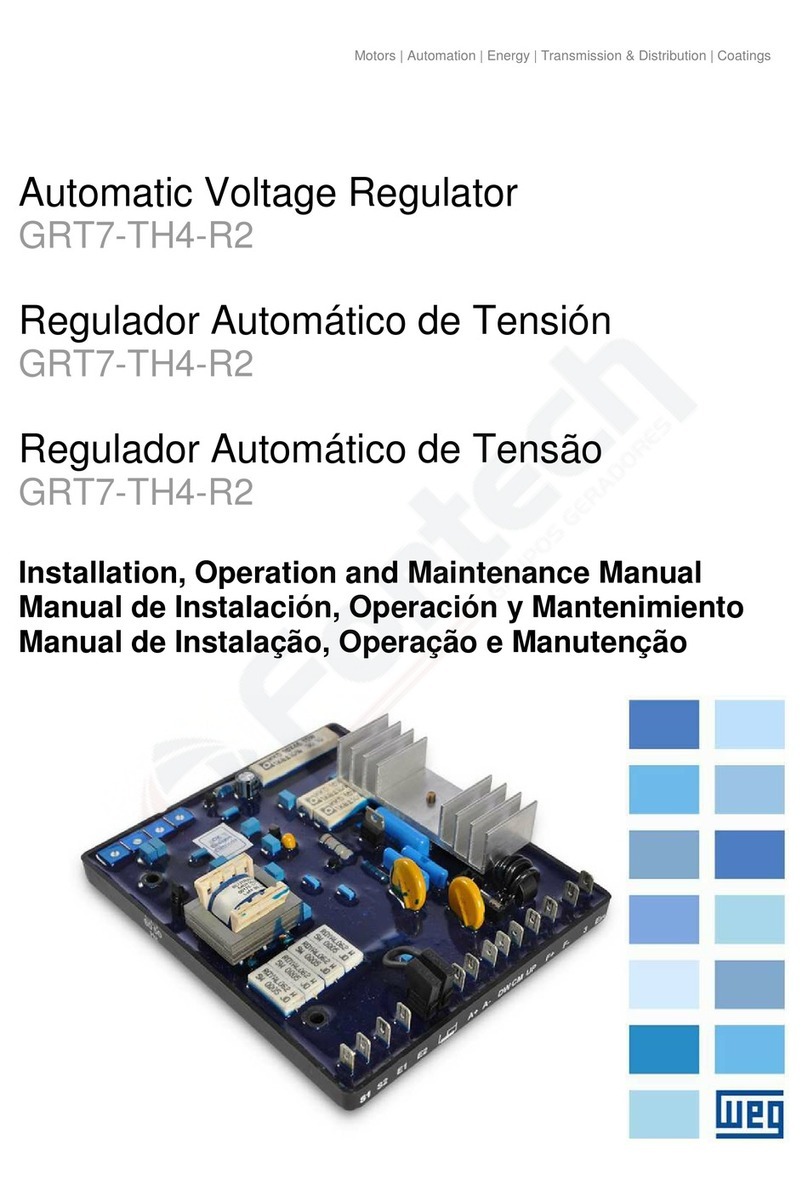
WEG
WEG GRT7TH4 R2 User manual
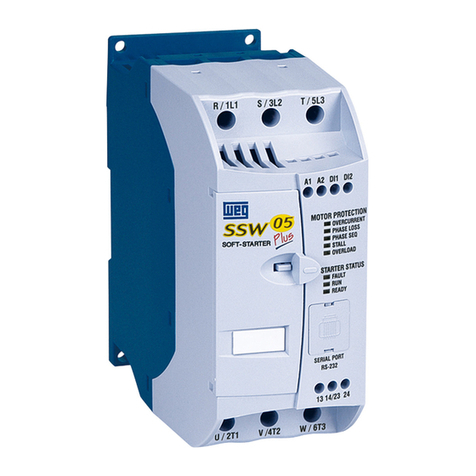
WEG
WEG SSW-05 User manual
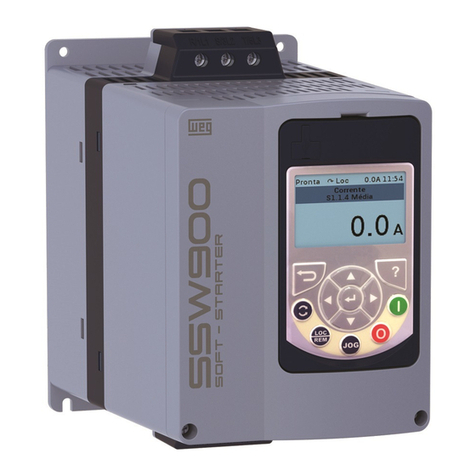
WEG
WEG Anybus Modbus TCP User manual
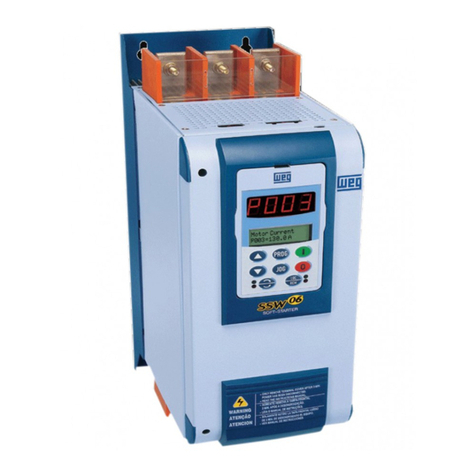
WEG
WEG SSW06 Use and care manual
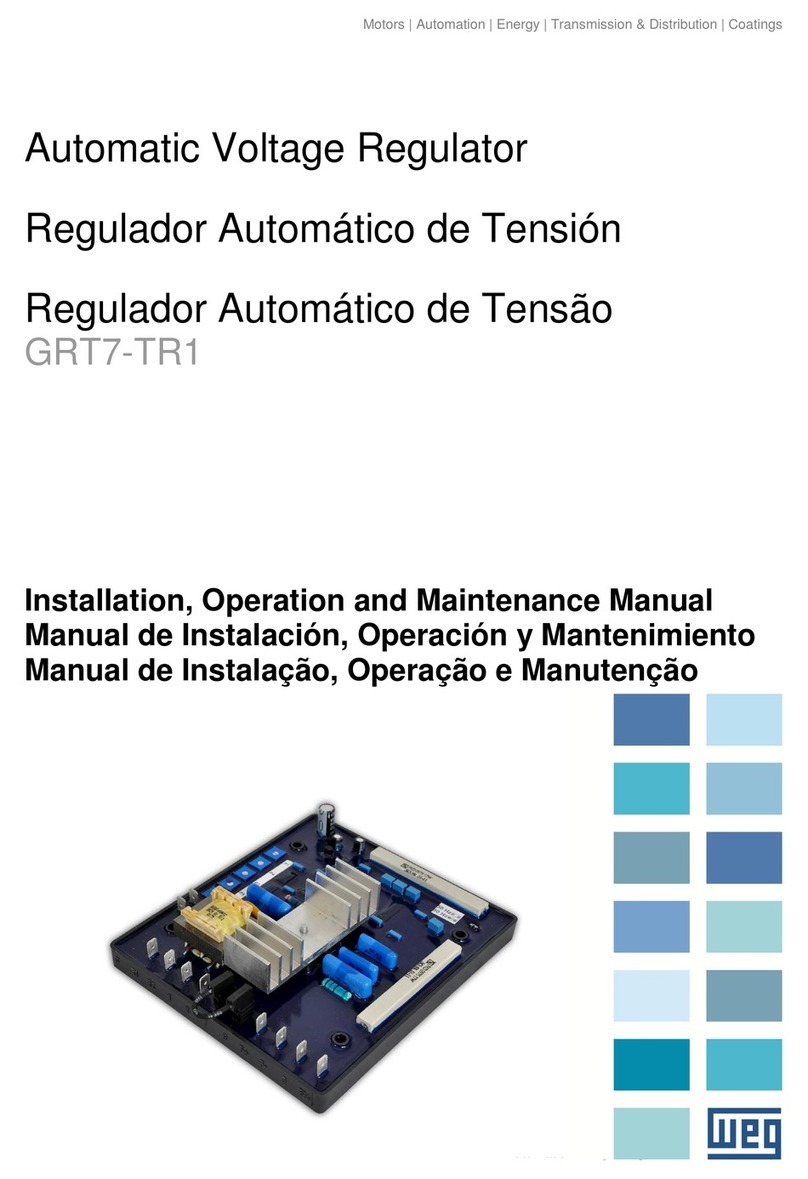
WEG
WEG GRT7-TR1 User manual
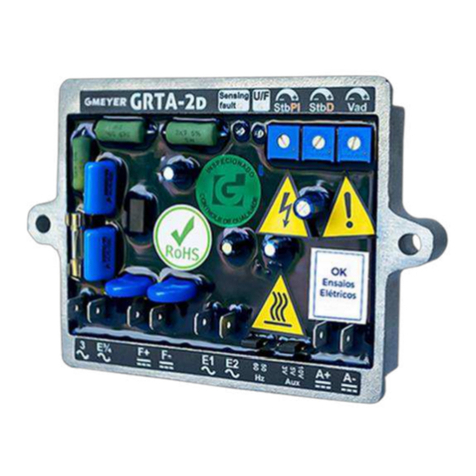
WEG
WEG GRTA-2D User manual
Popular Controllers manuals by other brands
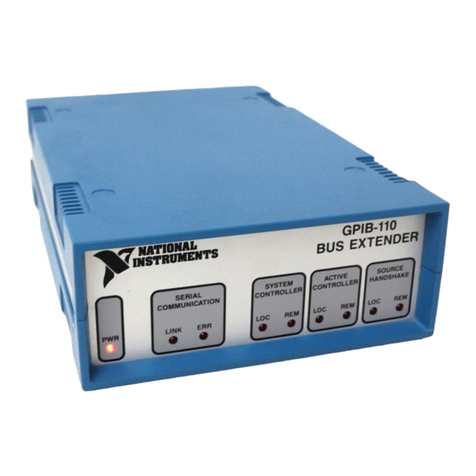
National Instruments
National Instruments GPIB-110 user manual
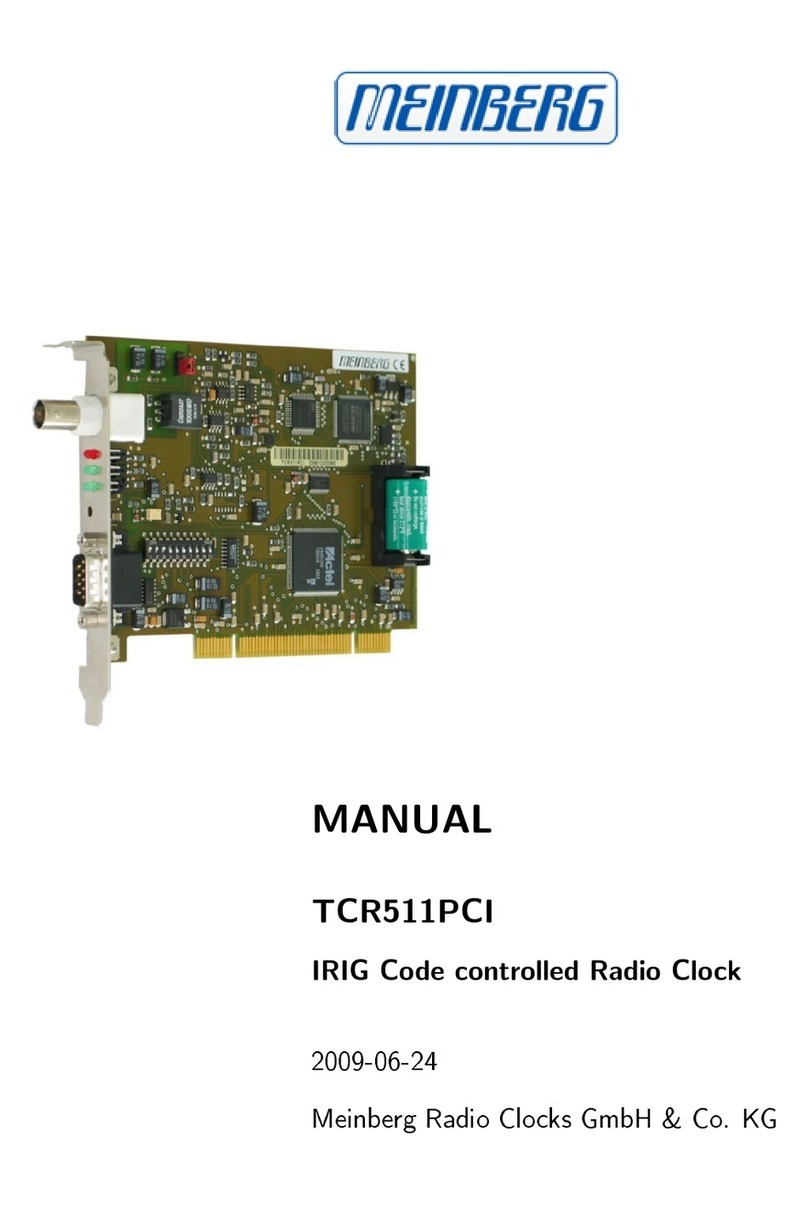
Meinberg
Meinberg TCR511PCI manual
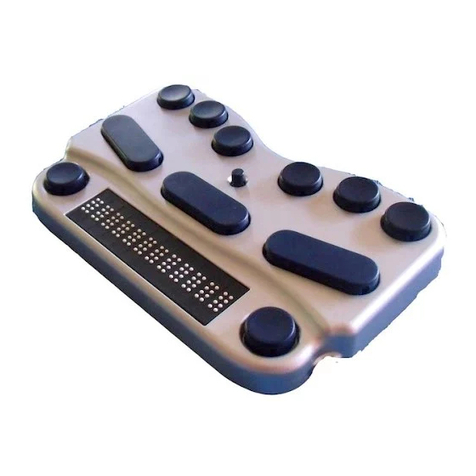
Harpo
Harpo BraillePen 12 quick start
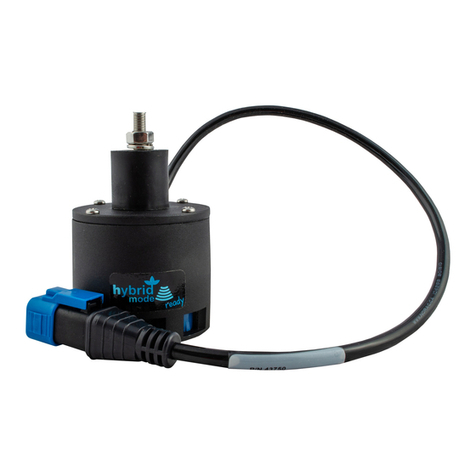
Norac
Norac UC5 Topcon X30 installation manual
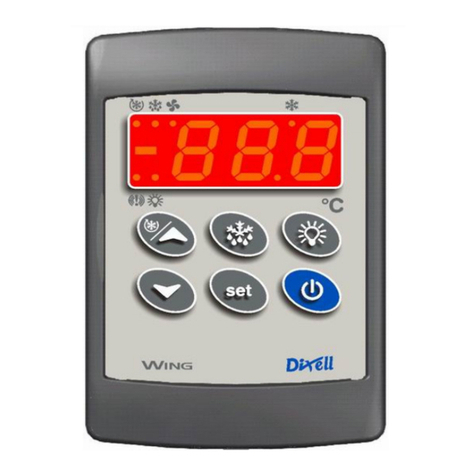
dixell
dixell XW35VS Installing and operating instructions
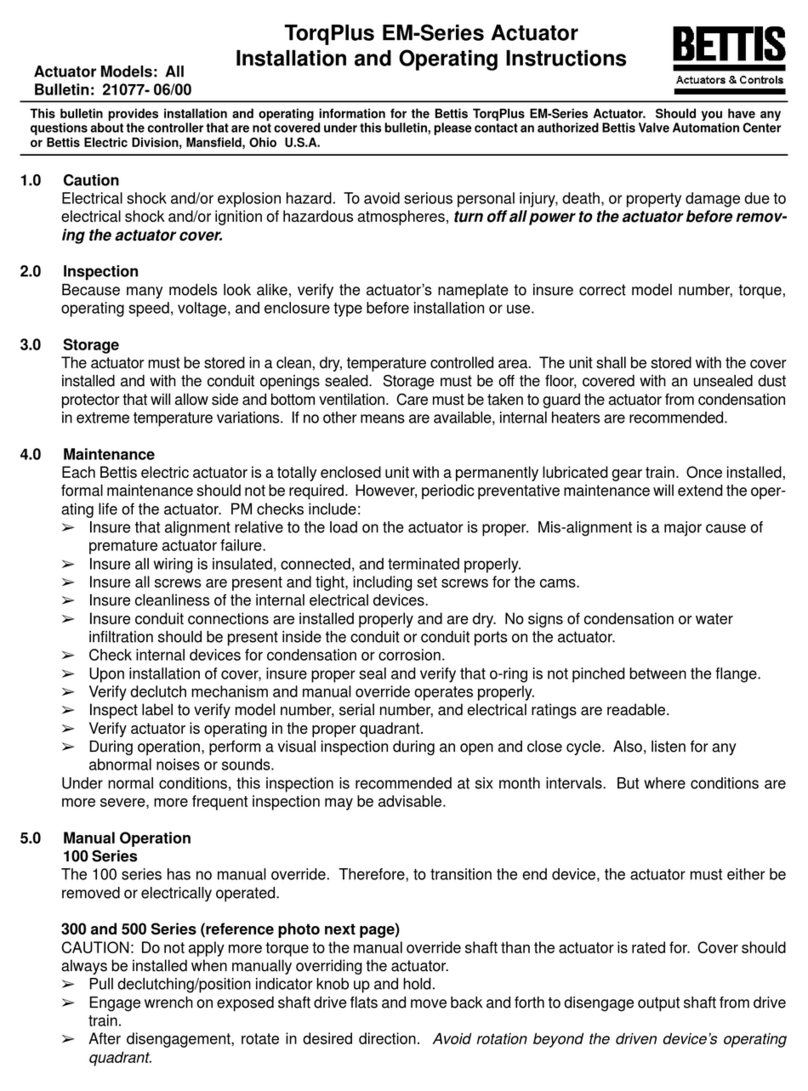
Bettis
Bettis TorqPlus EM Series Installation and operating instructions