WELBA WTS-300 User manual

1. Introduction
105204 –WTS-300-E - V4.1 - 20.01.2022 Page 1
Universal tank control
WTS-300
Installation and operating instructions
for plant engineering companies,
installers and service engineers
Firmware V4.3
Measuring - Controlling - Regulating
All from the same source
Programmable via
configuration software
WELBA „KONSOFT"
WTS-300 G1

1. Introduction
Page 2105204 –WTS-300-E -V4.1 - 20.01.2022
1. Introduction................................................................................................................................................ 5
1.1 Information about this operating instructions ................................................................................ 5
1.2 Limitation of liability ....................................................................................................................... 6
1.3 Warning notices in these operating instructions............................................................................ 6
1.4 Device description......................................................................................................................... 7
1.5 Type designation........................................................................................................................... 7
1.6 Item supplied................................................................................................................................. 8
1.7 Dimensions.................................................................................................................................... 8
1.8 Sensor dimensions and technical data.......................................................................................... 8
1.9 Technical data of control unit ........................................................................................................ 9
2. Safety ...................................................................................................................................................... 10
2.1 General Information..................................................................................................................... 10
2.2 Intended use................................................................................................................................ 12
2.3 Wiring, screening, earthing.......................................................................................................... 13
2.4 Electrical safety ........................................................................................................................... 13
3. Installation ............................................................................................................................................... 14
3.1 Location and climatic conditions.................................................................................................. 14
3.2 Unpacking and storage ............................................................................................................... 14
3.3 Installation of housing.................................................................................................................. 14
3.4 Fitting the sensor......................................................................................................................... 15
4. Electrical connection ............................................................................................................................... 16
4.1 Safety during installation ............................................................................................................. 16
4.2 Procedure.................................................................................................................................... 16
4.3 Wiring .......................................................................................................................................... 17
4.4 Connection diagram (Delivery configuration)............................................................................. 18
4.5 Wiring the digital inputs ............................................................................................................... 19
4.6 Connection robot......................................................................................................................... 19
4.7 Connection of external pressure sensor (optional) ..................................................................... 19
5. Operation................................................................................................................................................. 20
5.1 Function overview........................................................................................................................ 20
5.1.1 OFF mode (stand-by)........................................................................................................ 20
5.1.2 Cooling mode.................................................................................................................... 20
5.1.3 Continuous stirring mode.................................................................................................. 21
5.1.4 Cleaning mode.................................................................................................................. 21
5.2 The configuration software KONSOFT........................................................................................ 23
5.3 Guideline for the initial installation / parameterization................................................................. 24
5.4 Setting the date and time ........................................................................................................... 26
5.5 Operation in levels....................................................................................................................... 27
5.6 Operation of working level........................................................................................................... 28
5.6.1 Button functions ................................................................................................................ 29
5.6.2 Meaning of the LED‘s........................................................................................................ 30
5.6.3 Operation modes............................................................................................................... 32
6. Cleaning .................................................................................................................................................. 36
6.1 Cleaning methods (cooling tank-configurations)......................................................................... 36
6.1.1 Circulation cleaning with a beaker .................................................................................... 36
6.1.2 Circulation cleaning with two dosing pumps..................................................................... 36
6.1.3 Displacement cleaning with feed container, dosing pumps in circulation pipe................. 37
6.1.4 Displacement cleaning with feed container and dosing pumps........................................ 37
6.2 Cleaning programme diagram (Maximum configuration)........................................................... 38
6.3 Explanation and programming of the cleaning process.............................................................. 40
6.3.1 Factory setting................................................................................................................... 40

1. Introduction
105204 –WTS-300-E - V4.1 - 20.01.2022 Page 3
6.3.2 Determination of the number of individual rinsing cycles ..................................................40
6.3.3 Different methods of water intake......................................................................................41
6.3.4 Cleaning with alkaline or acidic detergents .......................................................................42
6.3.5 Disinfection ........................................................................................................................42
6.3.6 Time of detergent dosing...................................................................................................42
6.4 Parameterization of the cleaning stages......................................................................................43
6.4.1 Cleaning methods..............................................................................................................43
6.5 Abort of the cleaning ....................................................................................................................56
6.5.1 Cleaning cycle completely finished...................................................................................56
6.5.2 Manual abort of the cleaning ............................................................................................56
6.5.3 Abort of the cleaning due to faults .....................................................................................56
6.5.4 Power failure during cleaning ............................................................................................57
6.6 Dosing of detergent and / or water intake by flow metering.........................................................58
6.6.1 General information and first steps....................................................................................58
6.6.2 Dosing of the quantity-controlled detergent and disinfectant.............................................59
6.6.3 Quantity-controlled water intake........................................................................................59
6.6.4 Testing / determining the number of pulses of the flow sensors per litre ..........................60
7. Tank monitor and general fault handling .................................................................................................61
7.1 Description of tank monitor operation ..........................................................................................61
7.2 Tank monitor: Milk removal YES or NO.......................................................................................63
7.3 Tank monitor: Handling multiple faults.........................................................................................66
7.4 Tank monitor: Display fault memory ............................................................................................66
7.5 Listing fault codes and their description.......................................................................................67
7.5.1 Critical tank monitor alarms (red).......................................................................................67
7.5.2 Informative tank monitor alarms (green)............................................................................68
7.5.3 System alarms - cleaning ..................................................................................................70
7.5.4 System alarms - cooling.....................................................................................................72
7.5.5 System alarms - external sensors .....................................................................................73
7.5.6 System alarms in general ..................................................................................................73
7.5.7 Test alarm..........................................................................................................................73
8. Setting of parameters...............................................................................................................................74
8.1 Change and save parameter values............................................................................................74
8.2 Level “General cooling parameters” (c parameters)......................................................76
8.3 Level “Extended cooling parameters” (P parameters).....................................................78
8.4 Level “General cleaning parameters” (n parameters)......................................................88
8.5 Level “Extended cleaning parameters 1” (r parameters)......................................................92
8.6 Level “Extended cleaning parameters 2” (L parameters) .....................................................98
8.7 Level “Service parameters” (E parameters)...................................................100
8.8 Level “General tank monitor parameters” (h parameters) ...................................................102
8.9 Level “Extended tank monitor parameters” (H parameters) ..................................................104
8.10 Level “Alarm - Event assignment” (F parameters)...................................................106
8.11 Level “Configuration” (A parameters) ..................................................108
8.12 Level “I/O test parameters” (o. parameters) ..................................................116
9. Other information –General ..................................................................................................................119
9.1 Butterfly valve (manual or pneumatic) .......................................................................................119
9.2 Safety switch for manual butterfly valve.....................................................................................119
9.3 Sensor correction procedure......................................................................................................120
9.4 Function second temperature sensor ........................................................................................120
9.5 Test functions.............................................................................................................................121
9.5.1 Test alarm F99.................................................................................................................121
9.5.2 Function test "Do-Not-Load LED" and "external alarm light"...........................................121
9.6 Procedure following power failure..............................................................................................122
9.7 Power pack or operation via external power supply ..................................................................123
9.8 Agitator monitoring module (optionally) .....................................................................................124

1. Introduction
Page 4105204 –WTS-300-E -V4.1 - 20.01.2022
9.9 I/O Expansion module ESIO ..................................................................................................... 125
9.10 USB module ESUSB................................................................................................................. 125
9.11 Integrated multifunction-time relay............................................................................................ 126
9.12 Safety chain for 'remote start' functions .................................................................................... 128
9.13 RS485 interface......................................................................................................................... 129
9.14 General measures when using electronic control systems....................................................... 130
9.15 Robot control............................................................................................................................. 133
9.15.1 Cleaning release by robot............................................................................................... 134
9.15.2 Compressor switch-on delay / pre-agitating.................................................................... 135
9.15.3 Compressor lock via digital input (by robot).................................................................... 135
10. Other information - Cooling................................................................................................................... 136
10.1 Automatic start continuous agitating or cooling mode............................................................... 136
10.1.1 Automatic start to continuous agitating mode after exiting cooling mode....................... 136
10.1.2 Automatic start to cooling mode after successful cleaning............................................. 136
10.2 Different variants for cooling start delay.................................................................................... 137
10.3 Emergency cooling / Sensor fault.............................................................................................. 139
10.4 Level alarm during cooling (Fault code F52)........................................................................... 139
10.5 Connection /Parameterization external analogue pressure sensor .......................................... 140
10.6 Tanks and silos with multiple cooling stages (cooling step control).......................................... 141
10.7 Tank overflow protection ........................................................................................................... 142
10.8 Anti-freezing protection by means of low pressure monitoring ................................................. 143
10.9 Thermal protection - / Fault monitoring compressor [P72]........................................................ 144
10.10 Fault messages low pressure (F80).......................................................................................... 145
10.11 Fault Messages High Pressure (F81)........................................................................................ 145
11. Other information - Cleaning................................................................................................................. 146
11.1 Detergent supply via beaker...................................................................................................... 146
11.2 Setting of a break in the cleaning programme .......................................................................... 146
11.3 Heating control .......................................................................................................................... 147
11.4 Influence on the temperature of the tank wall ........................................................................... 147
11.5 Boost pump function (booster pump)........................................................................................ 147
11.6 Level control setting................................................................................................................... 148
11.7 Relay function 'set level 2 to relay'............................................................................................ 148
11.8 Function of pressure switch –Effect on pump and heater........................................................ 149
11.9 Air in the cleaning pump -> automatic venting.......................................................................... 149
11.10 Service functions for testing the cleaning cycle ........................................................................ 150
11.10.1 Start cleaning with the desired cleaning stage (0 to 8)................................................... 150
11.10.2 Single step function during cleaning ............................................................................... 150
12. Other information - Tank monitor .......................................................................................................... 151
12.1 Activation delay tank monitor [H90]........................................................................................... 151
12.2 EMAIL-, alarm + remote maintenance module ESIPM ............................................................. 151
12.3 SMS, alarm + remote maintenance module ESGSM................................................................ 151
Publisher:
Welba GmbH
Electronic Control Engineering
Gewerbepark Siebenmorgen 6
D-53547 Breitscheid
Fon:
Fax:
+49 (0)2638 / 9320-0
+49 (0)2638 / 9320-20
info@welba.de
www.welba.de

1. Introduction
105204 –WTS-300-E - V4.1 - 20.01.2022 Page 5
1. Introduction
1.1 Information about this operating instructions
These operating instructions are intended for the use by plant engineers, installers
or service technicians of the WTS-300 universal tank control. This manual contains
all necessary suggestions, Information, recommendations and advice for the safe
and proper installation and commissioning of the tank control. It is only with the
knowledge of this operating instruction that errors in the tank control system can be
avoided and a trouble-free operation is guaranteed.
Read the assembly instructions carefully and adhere to the recommendations de-
scribed in order to ensure proper operation. In addition, the local accident prevention
regulations and general safety regulations are to be observed for the field of appli-
cation of the tank control.
When delivered, the parameterization of the WTS-300 does not neces-
sarily correspond to the intended use. This must be adjusted accord-
ingly during the installation.
Basically, the installer of the system is responsible for the commission-
ing of the control.
Operation instruction for the operator
The plant engineers, the installer or the service technician must prepare operating
instructions for the operator of the tank control (farmer). In this case the parameteri-
zation of the delivery state must be clearly documented.
We recommend to only document those parameters which the operator of the tank
control needs.
When preparing the operating instructions for the operator the local regulations have
to be observed –see chapter “Safety”.
These operating instructions include important technical and safety in-
formation. It is vital to carefully study all these instructions before the
installation of the control or in case of any other work with the control!
The manufacturer accepts no liability for errors and reserves the right to make tech-
nical changes at any time. All rights reserved.
NOTICE for storing the operating instructions
This instruction manual is part of the product and must always be readily available
for the service technician.
WARNING
NOTICE

1. Introduction
Page 6105204 –WTS-300-E -V4.1 - 20.01.2022
1.2 Limitation of liability
The proper function of the WTS-300 depends on many external factors
on which the manufacturer has no influence. The manufacturer accepts
no liability for any damages on the milk cooling tank, the connected
components or the milk. The integrated tank monitor supports only the
control of the milk quality and does neither absolve the farmer (as op-
erator of the milk tank) nor the driver of the milk collecting truck from
the duty of care. Both parties have to ensure that the milk is transport-
able before it is removed from the tank.
All information and instructions in this manual have been compiled taking into ac-
count the applicable standards and regulations, the state of the art and our long-term
experiences.
WELBA GmbH does not assume any liability for damages due to:
- Non-observance of the installation instruction
- Improper use
- Installation by unqualified staff
- Non-professional installation by third parties
- Unauthorized modifications
- Technical modifications
- Use of unapproved spare parts (e.g. batteries)
Otherwise, our general terms and conditions as well as the terms of delivery of
WELBA GmbH and the legal regulations valid at the time of conclusion of the con-
tract are applicable.
We reserve the right to make technical changes in the context of improving the prop-
erties of use and further developments.
1.3 Warning notices in these operating instructions
Important safety information in these assembly instructions are identified by sym-
bols. These instructions on occupational safety must be adhered to and followed. In
these cases, behave particularly carefully in order to avoid accidents, personal injury
and property damage.
In addition to the information in these assembly instructions, the general and local
safety and accident prevention regulations must also be observed and instructed!
Nature and source of danger
This warning signs warns of an imminent danger to health and life of people. Failure
to comply with this warning will result in extremely serious injuries, including death.
Nature and source of danger
This warning signs warns of a possibly dangerous situation for the health of people.
Failure to observe these warning notices can result in serious injuries, including
death.
Nature and source of danger
This warning sign warns of a possibly dangerous situation for the health of people.
Failure to observe these warnings can lead to minor or moderate injuries.
Note
General notes contain application tips and particularly useful information, but no
warnings about dangers.
WARNING
WARNING
DANGER!
ATTENTION
NOTICE

1. Introduction
105204 –WTS-300-E - V4.1 - 20.01.2022 Page 7
These operating instructions contain important technical and safety in-
formation. Please readcarefully before installation and before any work
on or with the regulator.
These instructions have been compiled with maximum care and attention. However,
their content does not constitute an assurance of product features.
The manufacturer cannot be held liable for errors and may at any time make changes
serving technical progress. All rights reserved.
1.4 Device description
Die The WTS-300 is an universal tank control unit that combines various
basic functions in one unit
- a milk cooling thermostat
- an extensive cleaning control
- an extended robot interface
- an extended tank monitoring system
All functions can be parameterised separately and universally.
The control unit has various operating modes:
- OFF mode (tank is empty)
- Cooling mode
- Continuous stirring mode
- Cleaning mode
WELBA „KONSOFT"
The free of charge configuration Software KONSOFT provides a simple
parameterization and updating of the WTS-300 as well as a comfortable
evaluation of the determined data.
See section 5.2
The KONSOFT PC-Software has been thoroughly tested and has proven itself hundreds
of times in customer use. Despite all care, we point out that the use of the free PC-Software
is at your own risk. WELBA does not accept any liability for damages or loss of data result-
ing from the installation or use of the Software.
1.5 Type designation
The type designation of your controller is attached to the holder frame.
NOTICE
NOTICE

1. Introduction
Page 8105204 –WTS-300-E -V4.1 - 20.01.2022
1.6 Item supplied
- Controller WTS-300
- Holder
- Rubber seal
- Sensor TF1A-2
- Fixing screws
- Any optional accessories ordered.
1.7 Dimensions
1.8 Sensor dimensions and technical data
A Sensors other than our standard type are available on request (dif-
ferent bush form or cable length).
Some of the options are shown here.
Sensor element
KTY 81-210
Bush material
1.4301 (V2A)
Bush length
40 mm
Bush diameter
6,0 mm +/- 0,1
Cable material
PVC
Measurement range
-10 .. 70° C
Cable length
standard 2 metres
177
106
45
T1
T2
°C
RESET
Robot
STOP
Mode
Valve open
RobotStop
Data
40 mm
6,0 mm
6,1 mm

1. Introduction
105204 –WTS-300-E - V4.1 - 20.01.2022 Page 9
1.9 Technical data of control unit
Operating voltage
230V AC +/-10%, 50/60 Hz
Relay contact
12 performance relays
expandable by 6 relays*
max. switching current
6 x each 6A AC1 - 250V AC
4 x each 10A AC1 - 250V AC
2 x each 12A AC1 - 250V AC
max. current per terminal
12A - 250V AC
max. switching voltage
250V AC - 50..60 Hz
Display
13 mm LED-Display, 4 digits
Display range
-999 .. 9999
LED switching status displays
3 mm LED
Number of sensor inputs
1 or 2
Measurement range
-5° .. +95°C
Temperature resolution
0,1°C
Sensor input
for KTY 81-210 (optionally PT-100)
Control mode
two-step controller
Hysteresis*
0,1 K .. 99,9 K ((standard adjusting 0.7 K)
Water detection
via 2 independent level monitors
Target temperature T1*
Target temperature T2*
standard adjusting 8°C
standard adjusting 4°C
Digital inputs
8 (via optocoupler)
expandable by 5 digital inputs*
Interface
2x RS-485
Supply ext. pressure sensor
12V +/-3V max. 40 mA
Connection
Plug-in screw connections
for cables up to 2.5 mm²
Housing
- Front dimension
- Front panel cut out
- Insertion depth
177 x 106 mm
157 x 97 mm
45 mm
Protection
- Housing front
- Rear
The control is open on the rear, as it is de-
signed for installation in a closed housing IP 64
IP 00
IP 20
Electrical safety
Protection class II,
Overvoltage category III, pollution degree I
Environment specifications:
- Operation temperature
- Storage temperature
- max. humidity 75% (no dew)
0° .. +50°C
-20° .. +70°C
75% (no dew)
Technical data subject to change.
* via I/O expansion module ESIO-001

2. Safety
Page 10 105204 –WTS-300-E -V4.1 - 20.01.2022
2. Safety
2.1 General Information
The plant engineering company, the installer or the service engineer
must prepare operating instructions for the operator, taking account of
the controller's parameters as supplied.
We recommend referring only to the parameters which the end user
needs for safe operation.
In preparing the operating instructions for the end user, especially the
chapter on “Safety”, account must be taken of local regulations.
The parameter settings of the WTS-300 as supplied do not correspond
to the intended use. This can lead to undefined behaviour by individual
components when the system is commissioned.
For this reason, no actuators should be connected when starting oper-
ation. Load circuits should be separated.
The general principle is that the plant constructor is responsible for
putting the controller into operation.
IMPORTANT NOTICE ON LIABILITY
The faultless function of the WTS-300 depends on many external fac-
tors, which the manufacturer has no influence on. The manufacturer
assumes no liability for damage to the milk cooling tank, the connected
components or the milk. The integrated tank monitor thus only sup-
ports the milk quality and does not release the farmer (as operator of
the milk cooling tank) or the driver of the milk collecting truck from the
duty of care. These must ensure, before withdrawing from the tank, that
the milk is transportable.
NOTICE
WARNING

2. Safety
105204 –WTS-300-E - V4.1 - 20.01.2022 Page 11
IMPORTANT NOTICE ABOUT THE ACCUMULATORS
See section 9.7
(required when using the tank monitor)
The life of the accumulators is limited. The built-in accumulators must
be replaced by new ones every two years at the latest.
Only (!) charged accumulators of the following specification may be
used: 1.2 V NiMh - size AA (min. 2.000 mAh)
DO NOT USE BATTERIES !!! EXPLOSIVE !!!!!
These operating instructions contain important technical and safety in-
formation. Please read carefully before installation and before any work
on or with the regulator.
It is the duty of the party commissioning the system to ensure compli-
ance with the following guidelines.
The universal tank controller may only be installed by an authorised
specialist, observing all local safety requirements.
Access to the environment when connected must be restricted to spe-
cialised personnel.
Universal tank controllers contain live components. They must be built
into the plant in such a way that contact with such live components is
impossible.
The controller is not suitable for use in explosive atmospheres. Danger
of explosion. Use only outside areas subject to explosive atmospheres.
The device must not be used if the housing or connection terminals are
damaged.
No fluids must penetrate the housing.
The universal tank control may not be exported to the USA without the
manufacturer's express permission!
DANGER!
WARNING
WARNING

2. Safety
Page 12 105204 –WTS-300-E -V4.1 - 20.01.2022
2.2 Intended use
These operating instructions contain important technical and safety in-
formation. Please readcarefully before installation and before any work
on or with the regulator!
Universal tank controllers WTS-300 are designed to control heating systems, con-
densing units, alarms, fans, etc. in milk cooling tanks as well as to monitor milk qual-
ity. Furthermore, connected milking robots can be controlled. Any other use of the
device is permitted only with prior written permission from the manufacturer.
The controller is intended only for incorporating into machinery, display panels or
switchboxes etc. and when fitted corresponding to protection class 2 (double or re-
inforced insulation). It is only allowed to be put into operation in installed state. The
use of the control is permitted in devices of protection class 1 and 2. The controller
must not be modified or converted in any way.
The universal tank controller is ready for use only when the parameters have been
set appropriately. Its use before this has been done would have no benefits and
could also damage the equipment or adversely affect the milk to be temperature-
controlled.
Responsibility for the faultless functioning of the connected devices lies with the plant
engineer or the installer or the service engineer who has installed and commissioned
the WTS-300.
The device is fitted with a resistance temperature sensor.
The controller is not suitable for use in explosive atmospheres. Danger of explosion.
Use only outside areas subject to explosive atmospheres.
The WTS-300 fulfils the EC requirements for electromagnetic compatibility (EMC)
and the Low Voltage Directive (LVD).
The safety components meet the VDE regulations.
NOTICE

2. Safety
105204 –WTS-300-E - V4.1 - 20.01.2022 Page 13
2.3 Wiring, screening, earthing
When selecting wiring materials and installing and connecting the temperature con-
troller to the electricity supply, account must be taken of DIN VDE 0100 “Erection of
power installations with rated voltages below 1000” or the relevant national regula-
tions (e.g. based on IEC 60364).
- Whereverpossible, keep input, output and supply leads and sensor cable phys-
ically separate from each other and do not lay them parallel to each other.
- Mains voltage cables and low-voltage cables must not be laid in one cable.
- Use screened and twisted interface and sensor cables.
- Earth the screening of temperature sensors unilaterally in the switchbox.
- Ensure correctly wired potential equalisation.
2.4 Electrical safety
- The controller itself and the associated control circuits and load circuits must
be protected separately and in accordance with the local regulations.
- The separate protection of the control- and load circuit must be carried out ac-
cording to local conditions!
- In order to prevent destruction of the relay or semiconductor relay outputs in
the event of a short-circuit, the load circuit should be fused to the maximum
permissible output current.
- As well as incorrect installation, wrong parameter settings can also adversely
affect the correct functioning of the controller. For this reason, safety devices
that are independent of the controller should always be used, e.g. high and low
pressure valves or temperature limiters. Account should be taken of the local
safety regulations in this connection.
- The load circuit (relay outputs K1 to K12) must be fused in accordance with the
connected components.
- The connection of external voltages to the digital inputs can lead to the destruc-
tion of the control.
- Caution: All cables to the digital inputs must be shielded and kept as short as
possible. EMC.
Important note concerning the external fuse
- The transformer, which is installed in the WTS-300, has a two-chamber safety
winding, which is only short-circuit-proof due to the built-in thermal protection.
If the temperature exceeds 145 ° C, there is a risk of damage!
Protect control unit with an external fuse of 160mA!
NOTICE

3. Installation
Page 14 105204 –WTS-300-E -V4.1 - 20.01.2022
3. Installation
3.1 Location and climatic conditions
It is essential not to install the device under the following conditions:
- severe jolting, vibration or magnetic fields
- permanent contact with water
- relative humidity of more than 90%
- sharply fluctuating temperatures (condensation)
- dust, flammable gases, vapours, solvents,
- operation in an aggressive atmosphere (ammonia or sulphur fumes) - risk of
oxidation
- operation in the immediate vicinity of radio transmitters with high levels of spu-
rious radiation.
A physical separation between the device and inductive consumers is recom-
mended.
3.2 Unpacking and storage
If the packaging is damaged or something is missing, do not fit the temperature con-
troller. In this case please contact Welba.
If you keep the temperature controller for a period before using it, store it in a clean
dry place at a temperature of between -20°C and +70°C.
3.3 Installation of housing
For fixing the housing please follow the instructions:
Place the seal carefully in the groove. Ensure it is not twisted.
Insert the housing from the front through the switchboard cut-out.
Attach the holding frame in the rear position as shown by the picture.
Fasten the housing by using the screws provided.
all drillings ø 4 mm
166
95
157
97
R4

3. Installation
105204 –WTS-300-E - V4.1 - 20.01.2022 Page 15
3.4 Fitting the sensor
The sensor cable must not be chafed or kinked.
There must be no substantial mechanical pressure on the sensor tube.
Do not place the sensor and the high-voltage cable in the same cable
conduit (not even within the switchbox).
Temperature range sensor cable -10°C .. +70°C
The WTS-300 has been designed for connection to various types of sensor (see
technical data). It can function properly only if one of those sensor types is installed
and the parameters are correctly set.
When setting the temperature controller parameters (and whenever the sensor is
replaced) the “actual value correction” [Parameter C91] must be adjusted so that the
temperature measured corresponds to that shown on the display. A reference ther-
mometer should be used for this purpose.
See section 9.3
Pay attention to the permitted temperature range for sensor cable exposure.
Changing the sensor cable length
lf it is necessary to shorten or lengthen the sensor cable on installation (or if a sensor
other than the one supplied is to be fitted), the "actual value correction" parameter
must be adjusted accordingly. See section 9.3
40 mm
6,0 mm
6,1 mm
WARNING

4. Electrical connection
Page 16 105204 –WTS-300-E -V4.1 - 20.01.2022
4. Electrical connection
4.1 Safety during installation
Before connecting ensure that the mains voltage is the same as indi-
cated on the device's type plate.
Incorrect electrical connection can cause damage to the regulator and
to the equipment.
The temperature controller should be disconnected from the mains
voltage while connecting plant components or the sensor.
No appliances with current levels in excess of the maximum values in-
dicated in the technical data should be connected to the relay contacts.
No other consumers may be connected to the controller's mains termi-
nals.
4.2 Procedure
In order to avoid injury to persons or damage to connected compo-
nents, connections must in all cases be undertaken in the following or-
der!
Pull out all the controller's plug-in terminals.
Put the controller in position in the housing or switchboard.
Connect all components and sensors in accordance with section 4.4 (Circuit dia-
gram) to the plug-in terminals.
(Do not yet plug the terminals into the controller!)
Connect the mains cable to plug-in terminal A1 / A2.
Plug terminal A1/ A2 into the controller.
Close the switchbox and turn on the mains voltage.
Switch on the controller and set the parameters
(possibly using the optional WELBA-KONSOFT configuration software).
Plug the pre-cabled plug-in terminals of the components into the controller.
Close the switchbox.
WARNING
WARNING

4. Electrical connection
105204 –WTS-300-E - V4.1 - 20.01.2022 Page 17
4.3 Wiring
Correct wiring in accordance with the information in the accompanying description
and local regulations is essential. Take particular care to ensure that the AC supply
is not connected to the sensor input or other low-voltage inputs or outputs.
The various relay contacts may only be connected with uniform tension.
Use copper wire (except for the sensor connection) and ensure that all supply leads
and connection terminals are dimensioned to suit the relevant current rating.
When connecting the controller and selecting the wiring materials to be used, it is
essential to comply with the provisions of DIN VDE 0100 “Erection of power instal-
lations with rated voltages below 1000” or the relevant national regulations.
Furthermore, all connections must comply with the relevant VDE regulations or cor-
responding national regulations.
- Within the two relay groups (K3 to K6) and (K9 to K12), the respective relays
are connected with each other on one side. They connect the respective volt-
age which has been connected at the feed point (terminals 8 and 17) to the
load.
- Compressor, cleaning pump and heater must not be connected directly to the
relays on the control unit. These must be switched by additional contactors. In
individual cases, it must be checked whether additional motor protection
switches or other safety devices are to be installed.
- Contactors are to be fitted with an RC protective circuit.
- Connection of the digital inputs:
- Only the output signal of the control provided at terminal 38 must be connected
to the digital inputs (via potential-free switching contacts)!

4. Electrical connection
Page 18 105204 –WTS-300-E -V4.1 - 20.01.2022
4.4 Connection diagram (Delivery configuration)
Electrical connections must be as shown in the diagram below.
Use cable bushes.
Make sure that cables cannot chafe.
Observe relay current rating.
In all cases use contactors for pump, compressor and heater.
Do not feed digital inputs with external voltage! Use potential-free switches.
ATTENTION => Delivery configuration
The final assignment of components to the relay outputs is set in the A parameters
(A1 to A20). See section 8.11
The assignment of components to the digital inputs is set in the A parameters (A21
to A33). See section 8.11
Safety switch
Remote start cooling
Dry protection heating
Thermal protection pump
Water pressure switch
Thermal protect. compres.
Release cleaning
Impulse milk pump
See 9.15.1
Akku
Alarm horn
(Tank monitoring
alarm)
Robot STOP
Acid detergent
L1 –Supply
Heater
Cleanig pump
Drain valve
Butterfly valve
Alkaline detergent
Welba Power
pack ONLY
(8x AA)
Digital inputs
Connect digital inputs
with potential-free
contacts!
Sensor 1
Sensor 2
(optional)
Input 4..20 mA
GND
12V +/- 3V
Level 2
Level 1
Connection pressure sensor
GND * = capacitively decoupled from GND
If the tank housing is to be used as one of
the two level poles, this pole must be con-
nected to GND*.
Lev2
Lev1
Warm water valve
L1 –Supply
Cold water valve
Compressor
Agitator

4. Electrical connection
105204 –WTS-300-E - V4.1 - 20.01.2022 Page 19
4.5 Wiring the digital inputs
Terminals 39 to 46 are digital optocoupler inputs. These are used to monitor and
process external switching contacts. These switching contacts must be potential-
free! The signal provided by the controller at terminal 38 must be fed separately to
each individual switching contact.
3938 4140 4342 44 4645
A21
A22
A23
A24
A25
A26
A27
A28
4.6 Connection robot
If the WTS-300 and the robot have a separate power supply, the robot can still be
stopped (by corresponding connection) in the event of power failure.
Robot requires an active signal to stop (high-active)
[A41] = 0: In the event of a power failure, the robot is not stopped
(Connection to terminal 6 / 4)
[A41] = 2: In the event of a power failure, the robot is stopped
(Connection to terminal 6 / 5)
Robot needs to lose the signal to stop (low active)
[A41] = 1: In the event of a power failure, the robot is stopped
(Connection to terminal 6 / 4)
[A41] = 3: In the event of a power failure, the robot is not stopped
(Connection to terminal 6 / 5)
4.7 Connection of external pressure sensor (optional)
Terminals 27 | 28 | 29 must be used only for the connection of an external pressure
sensor. See section 10.5
Internal power supply
via terminal 27
12 V +/- 3 V - max. 40 mA
If the sensor cannot be pow-
ered by internal power supply:
Use external power supply.
Parameter assignment
Connect digital inputs with
potential-free contacts!
Digital inputs
from robot
from robot
Connection pressure sensor two-wire
Connection pressure sensor three-wire
Pressure sensor
two-wire
signal
4..20 mA
signal
4..20 mA
signal
4..20 mA
signal
4..20 mA
Pressure sensor
two-wire
Pressure sensor
three-wire
Pressure sensor
three-wire
NOTICE

5. Operation
Page 20 105204 –WTS-300-E -V4.1 - 20.01.2022
5. Operation
5.1 Function overview
The WTS-300 is a universal tank control unit which combines all the
basic functions in one device:
- milk cooling control
- comprehensive cleaning control
- an extended robot interface
- an extended tank monitor
All basic functions can be selected and operated from the working
level. The control unit can also be adapted to a wide range of different
system types and sizes. This takes place through the thematically or-
ganised parameter levels.
Within the working level the control unit differentiates between various
operating modes:
5.1.1 OFF mode (stand-by)
Shows the current time.
All LEDs are out
(Exceptions: robot, outlet valve and tank monitor LEDs may be lit)
All output relays are deactivated
(Exceptions: robot, outlet valve and tank monitor alarms may be active)
CAUTION: The control unit is live even when switched off!
5.1.2 Cooling mode
(can NOT be started from cleaning mode)
Two freely definable target temperatures can be selected by pressing a button.
If the milk temperature exceeds the selected target temperature (T1 or T2) by the
hysteresis value, the compressor contactor and agitator are switched on automati-
cally. Once the target temperature is attained, the compressor contactor switches
off, while the agitator continues to run for the set “after-stirring“ period.
During cooling breaks the agitator switches on periodically, in accordance with the
set 'pause time', in order to ensure an even temperature throughout the milk.
Independently of this, during cooling, short or long “intermediate stirring” can be
switched on by pressing a button.
Cooling can be triggered in different ways:
- manually using the “START COOLING“ button
- via digital input “Remote start to cooling“ (by robot or external button)
- automatically following cleaning (only in conjunction with robot)
Cooling now starts in accordance with the pre-set starting mode:
Immediately or after a cooling start delay, with periodic cooling boosts, etc.
Working level
for normal daily operation
General cooling parameters
Extended cooling parameters
General cleaning parameters
Extended cleaning parameters 1
Extended cleaning parameters 2
Service parameter
General tank monitor parameter
Extended tank monitor parameter
Alarm configuration
Configuration
I/O test parameter
Other manuals for WTS-300
2
Table of contents
Other WELBA Controllers manuals
Popular Controllers manuals by other brands
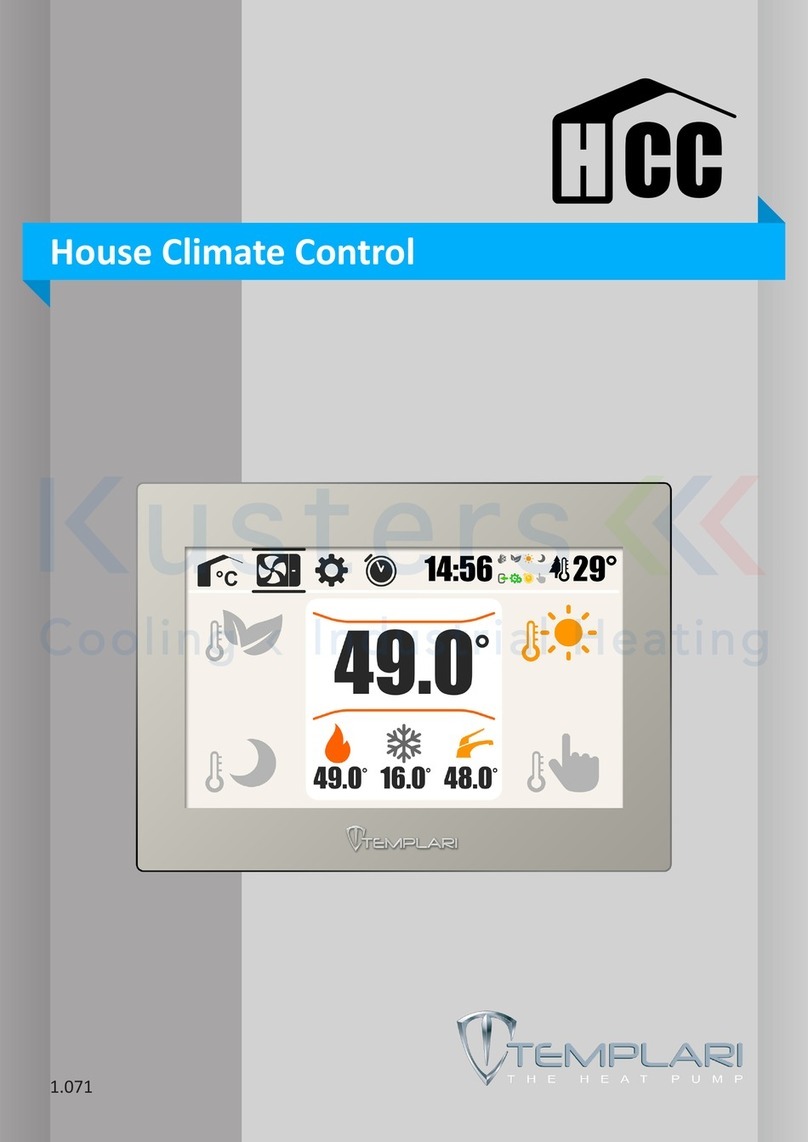
Templari
Templari HCC manual
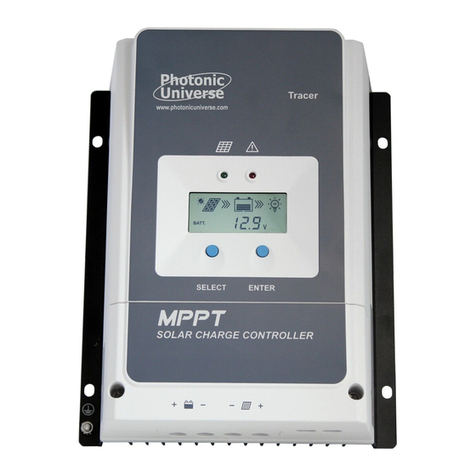
Photonic Universe
Photonic Universe AN Series user manual
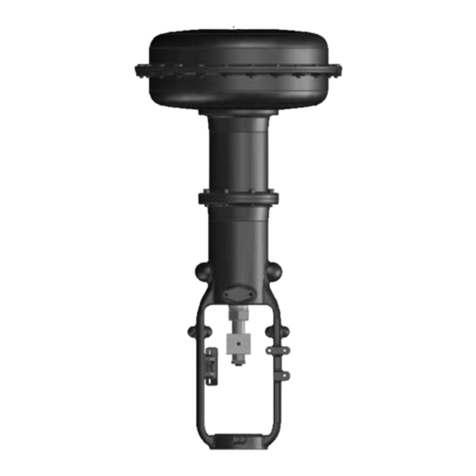
Emerson
Emerson Fisher 657C instruction manual

Elimko
Elimko E-70-O user manual
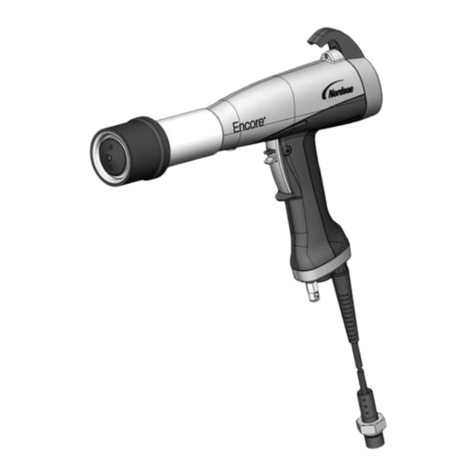
Nordson
Nordson Encore Installation, troubleshooting, repair

Isimet
Isimet LA Series Installation, Operations, Start-up and Maintenance Instructions