WoodFast WL1220A User manual

Instruction
Manual
IMPORTANT
For your safety, read
instructions carefully
before assembling or
using this product.
Save this manual for
future reference. Original Instruction
V.2-201911
WOOD LATHE
WL1220A

INDEX
1 GENERAL INFORMATION
1.1 FOREWORD
1.2 MACHINE IDENTIFICATION
1.3 CUSTOMER SERVICE RECOMMENDATIONS
2 SAFETY PRECAUTIONS
2.1 SAFETY REGULATIONS
2.2 RESIDUAL RISKS
2.3 SAFETY AND INFORMATION SIGNALS
3 SPECIFICATIONS
3.1 MAIN COMPONENTS
3.2 TECHNICAL SPECIFICATION
3.3 ELECTRICAL CONNECTION
3.4 NOISE LEVEL
4 INSTALLATION
4.1 INSTALL TOOL REST AND BASE ON LATHE BED
4.2 SPINDLE LOCK
4.3 ATTACHING SPUR CENTER ON THE HEADSTOCK
4.4 KNOCKOUT BAR
4.5 ATTACHING LIVE CENTER ON THE TAILSTOCK
4.6 INSTALL THE FACEPLATE TO THE HEADSTOCK
4.7 INSTALL TOOL HOLDER ON THE LATHE BED
4.8 SECURE LATHE TO A SOLID WORK SURFACE
5 ADJUSTMENTS AND OPERATIONS
5.1 ADJUSTING THE TOOL REST
5.2 ADJUSTING TAILSTOCK
5.3 CHANGING SPINDLE SPEEDS
6 MAINTENANCE
7 TROUBLE SHOOTING
8 DIAGRAMS AND COMPONENTS
-2-

1. GENERAL INFORMATION
1.1 FOREWORD
Some information and illustrations in this manual may difer from the machine in your possession, since all the configurations inherent
in the machine complete with all the optionals are described and illustrated. Therefore, refer only to that information strictly connected
with the machine configuration you have purchased.
With this manual we would like to provide the necessary information for maintenance and proper use of the machine. The distribution
network is at your service for any technical problem, spare parts or any new requirement you may have for the development of your
activity.
This manual must be read and understood before operating the machine. This will provde a better working knowledge of
the machine, for increased safety and to obtain the best results.
To facilitate its reading, the manual has been divided into sections pointing out the most important operations. For a
quick research of the topics, it is recommended to consult the index. To better stress the importance of some basic
passages, they have been marked by some preceding symbols:
1.2 MACHINE IDENTIFICATION
There is a identification plate fixed to the machine, containing the manufacturer's data, year of construction, serial
number and technical specifications.
1.3 CUSTOMER SERVICE RECOMMENDATIONS
Apply the machine to skilled and authorized technical staff to carry out any operation dealing with parts disassembly.
Keep to the instructions contained in this manual for the correct use of the machine.
Only skilled and authorized staff shall use and service the machine after reading this manual.
Respect the accident prevention regulations and the general safety and industrial medicine rules.
Indicates imminent risks which may cause serious injury to the operator or other persons. Be
careful and scrupulously follow the instructions.
A statement advising of the need to take care lest serious consequences result in harm to
material items such as the asset or the product.
CAUTION
WARNING
CAUTION
-3-

2. SAFETY PRECAUTIONS
2.1 SAFETY REGULATIONS
Read carefully the operation and maintenance manual before starting, using, servicing and
carrying out any other operation on the machine.
The manufacturer disclaims all responsibilities for damages to persons or things, which might be caused by any failure
to comply with the safety regulations.
- The machine operator shall have all necessary prerequisites in oder to operate a complex machiery.
- It is prohibited to use the machine when under the influence of alcohol, drugs or medication.
- All the operators must be suitably trained for use, adjustment and operation of the machine.
- The operators must carefully read the manual paying particular attention to the warning and safety notes. Furthermore,
they must be informed on the dangers associated with use of the machine and the precautions to be taken, and must
be instructed to periodically inspect the guards and safety devices.
- Before carrying out adjustment, repair or cleaning work, disconnect the machine from the electric power by setting the
main switch to stop.
- After an initial bedding-in period or many hours of operation, the driving belts may slacken; this causes an increase in
the tool stopping time (the stopping time must be less than 10 seconds). Immediately tighten them.
- The working area around the machine must be kept always clean and clear, in order to have an immediate and easy
access to the switchboard.
- Never insert materials which are different from those which are prescribed for the machine utilization. The material to
be machined must not contain any metal parts.
- Never machine pieces which may be too small or too wide ithrespect to the machine capacity.
- Do not work wood which has evident defects (cracks, knots, metal parts, etc.)
- Never place hands among the moving parts and/or materials.
- Keep hands clear from the tool; feed the piece with the aid of a pusher.
- Keep the tools tidy and far away from those not authorized persons.
- Never employ cracked nor uckled, neither not correctlyreground tools.
- Never use the tools beyond the speed limit recommended bythe producers.
- Carefully clean the rest surfaces of tools and make surethat they find perfectly horizontally positioned, and with no
dents at all.
- Always wear gauntlets when handling the tools.
- Mount the tools in the right machining direction.
- Never start the machine before having correctly installed all the protections.
- Connect the dust suction hoods to an adequate suction system; suction must always be activated when the machine is
switched on.
- Never open doors or protections when the machine or the system is operating.
- Many unpleasant experiences have shown that anybody may wear objects which could cause serious accidents.
Therefore, before starting working, take any bracelet, watch or ring off.
- Button the working garment sleeve well around the wrists.
- Take any garment off which, by hanging out, may get tangled in the MOVING UNITS.
- Always wear strong working footwear, as prescribed by the accident-prevention regulations of all countries.
- Use protection glasses. Use appropriate hearing protection systems (headsets, earplugs, etc.) and dust protection
masks.
- Never let unauthorized people repair, service or operate the machine.
- The manufacturer is not responsible for any damage deriving from arbitrary modifications made to the machine.
- Any transport, assembly and dismantling is to be made only by trained staff, who shall have specific skill for the
specified operation.
- The operator must never leave the machine unattended during operation.
- During any working cycle break, switch the machine off.
- In case of long working cycle breaks, disconnect the general power supply.
WARNING
-4-

2.2 RESIDUAL RISKS
Despite observance of all the safety regulations, and use according to the rules described in this manual, residual risks
may still be present, among which the most recurring are:
- contact with tool
- contact with moving parts (belts, pulleys, etc..)
- recoil of the piece or part of it
- accidents due to wood splinters or fragments
- tool insert ejection
- electrocution from contact with live parts
- danger due to incorrect tool installation
- inverse tool rotation due to incorrect electrical connection
- danger due to dust inhalation in case of working without vacuum cleaner.
Bear in mind that the use of any machine tool carries risks.
Use the appropriate care and concentration for any type of machining (also the most simple).
The highest safety is in your hands.
2.3 SAFETY AND INFORMATION SIGNALS
This signals may be applied on the machine; in some cases they indicate possible danger conditions, in others they
serve as indication.
Always take the utmost care.
SAFETY SIGNALS:
Risk of eye injury. Wear eye protection.
Wear hearing protection systems.
Danger of electric shock. Do not access the area when the machine is powered.
Carefully read and understand the manual before using the machine.
INFORMATION SIGNALS:
Indicate the technical characteristics, direction of rotation and inclination, block and release, etc.
Carefully following the directions to simply the use and adjustment of the machine.
The signals are graphically described and do not require further explanation.
-5-

To avoid electrocution or fire, any maintenance or repair
to electrical system should be done only by qualified
electricians using genuine replacement parts.
WARNING
3.3 ELECTRICAL CONNECTION
- Electrical installation should be carried out by competent,
qualified personnel.
- The mains connection should be made using the
terminal box.
- Replacement of the power supply cable should only be
done by a qualified electrician.
3. SPECIFICATIONS
3.2 TECHNICAL SPECIFICATION
-6-
1
2 3 4 56 7 8910 11 12
13 14
Volts, Hertz ......................................................................................................................
Amps................................................................................................................................
Motor Power.....................................................................................................................
Swing over Bed................................................................................................................
Distance between Centers...............................................................................................
Spindle Speeds................................................................................................................
Spindle Taper...................................................................................................................
Tailstock Ram Travel........................................................................................................
Number of Indexing Positions..........................................................................................
230V/50HZ
6A
750W
318mm
508mm
250-750/550-1650/1300-3850rpm
MT30X3.5
63mm
24
1. Tailstock Locking Lever
2. Tailstock Hand Wheel
3. Tailstock Assembly
4. Tailstock Locking Handle
5. Live Center
6. Spindle Hand Wheel
7. Headstock
8. Face Plate
9. Spur Center
10. Tool Rest Base
11. Tool Rest
12. Lathe Bed
13. Tool Rest Locking Level
14. Electronic Controls
3.1 MAIN COMPONENTS
Motor
CN8 CN9 CN3
MOTOR CABLE
DIGITAL READOUT
CABLE
ROTATION CONTROL
CABLE
POWER CABLE
SESOR
CABLE
POTENTIONMETER
CABLE
YELLOW
GREEN
BLUE
YELLOW
GREEN
BLUE
BROWN
BROWN
BLACK
WHITE

3.4 NOISE LEVEL
No load Load
Sound Pressure Level < 80dB(A) < 90dB(A)
Sound Power Level < 90dB(A) < 100dB(A)
The noise levels measured are emission levels and not necessarily the safe working level. Although there is a
correlation between the emission levels and the exposure levels, this cannot be used reliably to determine whether or
not further precautions are required. The factors which affect the actual level of operator exposure include the duration
of exposure, the ambient characteristics and other sources of emission, for example, the number of machines and
other adjacent machining. The permitted exposure values may also vary from country to country. Nevertheless, this
information allows the user of the machine to better evaluate the dangers and risks.
Other factors which reduce exposure to noise are:
- correct tool choice
- tool and machine maintenance
- use of hearing protection systems (e.g. headsets, earplugs,...)
WARNING Please use the hearing protection systems if the above mentioned noise levels
exceed 95dB(A).
-7-
4.1 INSTALL TOOL REST AND BASE ON
LATHE BED
WARNING
4. INSTALLATION
- Remove the tailstock assembly by releasing the locking
handle and sliding the assembly off the end of the lathe
bed.
- Slide the tool rest base onto the lathe bed and reinstall
the tailstock assembly.
- Loosen locking handle and insert tool rest into tool
rest base, adjust height up or down and tighten locking
handle.
Fig.4.1
4.2 SPINDLE LOCK
The indexing system must only be
used when the lathe is stationary
and the power is turned off.
Fig.4.2
TOOL SLIDE BEARING REST LOCK BUTTON
SPINDLE STOP PIN
Tailstock Assembly Toolrest Locking Handle
Index Locking Pin
WARNING
Indexing is a useful feature of the M320 lathe, allowing
accurate pattern work on projects such as straight fluting,
grooving, drilling, lay out and more.
Please note: The indexing system
must not be used as a method of
holding the spindle while removing
accessores such as face plates,
chuck ets. Damage caused to the
machine by doing so is not covered
by the warranty.
WARNING
The machine must not be plugged in and the power switch must be in the OFF position untill
installation is complete.

4.4 KNOCKOUT BAR
- The knockout bar is used to remove the spur center
from the headstock spindle. Insert knockout bar into hole
at opposite side from spur center.
Fig.4.4
4.5 ATTACHING LIVE CENTER ON THE
TAILSTOCK
- Insert the live center, with a No.2 Morse Taper shank
into the tailstock spindle.
TAILSTOCK HAND WHEEL
TAILSTOCK SPINDLE
TAILSTOCK’S TOP
Fig.4.5
- To remove live center from the tailstock spindle,
loosen locking handle and rotate the hand wheel
counterclockwise to retract spindle into the body of the
tailstock. The live center will be pushed out of the spindle.
4.6 INSTALL THE FACEPLATE TO THE
HEADSTOCK
- Thread the faceplate clockwhise onto the headstock
spindle. Next, tighten faceplate with supplied wrench.
TOP BAR
法兰盘
Fig.4.6
-8-
4.3 ATTACHING SPUR CENTER ON THE
HEADSTOCK
- Insert spur center, with a No.2 Morse Taper shank, into
the headstock spindle.
Fig.4.3
SPINDLE SPINDLE’S TOP
Headstock Spindle Spur Center
Knockout Bar
Live Center
Tailstock Spindle
Tailstock Handwheel
Face Plate

-9-
4.7 INSTALL TOOL HOLDER ON THE LATHE
BED
- Located the tool holder from the carton, and install it
onto the lathe bed with two pan head screws.
TOOL HOLDER
PAN HEAD SCREW
Fig.4.7
Tool Holder
Pan Head Screw
4.8 SECURE LATHE TO A SOLID WORK
SURFACE
- The lathe must be attached to a solid work surface or
stand. Four mounting holes are easily accessible at the
base of the lathe.
Fig.4.8
MOUNTING HOLES
5. ADJUSTMENTS AND OPERATIONS
5.1 ADJUSTING THE TOOL REST
- The tool rest base can be easily moved along the
lathe bed. Loosen locking lever counter clockwise, slide
tool rest base to new position, and tighten locking lever
clockwise.
- NOTE: Position the tool rest as close to the work piece
as possible. It should be 1/8” above the centerline of the
workpiece.
- To adjust clamping action of the tool rest base,
remove base and adjust nut clockwise to tighten and
counterclockwise to loosen.
Fig.5.1
5.2 ADJUSTING TAILSTOCK
- Loosen locking lever to move the tailstock along the
lathe bed to desired position. Tighten lever.
- To adjust clamping action of the tailstock, remove it
from lathe bed and adjust nut clockwise to tighten and
counterclockwise to loosen.
- To adjust tailstock spindle in or out, loosen locking
handle and turn handwheel. When the tailstock spindle is
in a desired position, tighten locking handle.
TAILSTOCK HAND WHEEL
LOCK BUTTON
LOCK HANDLE
Fig.5.2
TOOL SLIDE BEARING
REST
LOCK BUTTON
LOCK HANDLE
Mounting Holes
Locking Lever
Locking Handle
Tool Rest
Tool Rest Base
Locking Lever
Locking Handle
Hand Wheel

5.3 CHANGING SPINDLE SPEEDS
- The lathe features a three step motor and spindle
pulleys to provide variable spindle speeds. Open access
cover to change spindle speeds.
- With access cover open, loosen locking handle. Raise
lever to release tension on motor pulley and tighten
locking handle. Check speed and belt position chart in
the front of the headstock to determine spindle speed
required. Adjust the belt to proper tension with the raise
lever and tighten the locking handle.
- Turn the speed control dial clockwise, the spindle speed
will be increased. Turn counter colckwise, the speed will
be decrased.
- Turn off the lathe, place the directional switch to FWD,
the spindel is turn in clockwise. Switch to REW, the
spindle will turn in counter clockwise.
皮带护罩
涨紧手把 锁紧钮
调速旋钮
正反转按钮
Fig.5.3
6. MAINTENANCE
- Keep the lathe bed casting clean and lubricated.
- Keep the outside of the machine clean to ensure accurate operation of all moving parts and prevent excessive wear.
- Keep the ventilation slots of the motor clean to prevent it from overheating.
- Remove all saw dust and chips from the lathe after each use.
-10-
7. TROUBLE SHOOTING
Symptom Possible Cause Solution
Motor will not
start
Machine not plugged in
Low voltage
Loose connection
Plug the machine in
Motor
overheats
Motor overloaded
Air flow restricted on motor
Reduce load on motor
Clean out motor to obtain normal air flow
Excessive
motor noise
Bad motor
Pulley set screw loose
Have motor checked
Tighten set screw
Motor will not
develop full
power or stalls
Circuit overloaded with lights or other tools
Circuit too long or undersized wires
Voltage too low
Circuit breakers do not have sufficient capacity
Drive belt tension too high
Use of extension cord
Decrease the load on the circuit
Reduce the length of the wire or increase the wire
size
Have the voltage checked by an electrician
Have a licensed electrician install proper size
breaker
Adjust belt tension
Use heavier gauge extension cord or no extension
cord
Machine bogs
down during
cutting
Excessive deoth of cut
Turning tools are dull
Decrease depth of cut
Sharpen turning tools
For your own safety, always turn off and uppug the
machine before carrying out any troubleshooting.
WARNING
Do not make adjustments while the lathe is running,Ensure the switch is off,
power is disconnected and all moving parts have stopped before servicing.
Failure to comply may result in serious injury.
WARNING
CAUTION Before cleaning or carrying out maintenance work, disconnect the machine from the
power source (wall socket). Never use water or other liquids to clean the machine.
Use a brush. Regular maintenance of the machine will prevent unnecessary problem.
Belt Cover
Speed Control Dial
Direction
Switch
Locking
Handle
Tension
Lever

8. DIAGRAMS & COMPONENTS
71
24
25
25
33 34
7
6 1 62 63
64
6768 66
70
1 9 2 0 211817897 1 0 11 13 1412 15 16
47 60
69
85
86
87
88
48 49
50
51 65
8 9 90 91 9 2 93
14 3 25
22
623
26272829
30
31
32
3536
37383940
41 42 43 44 45 46
52 53 54 55 56 57 40 58 59
72
73
74 75 76 77 78
79
80818283
84
10
-11-

-12-
No.
Description
Part No.
QTY.
1 Bed 1
2 Hexagon socket cap screw 4
3 Flat washer 6
4 Lock washer 4
5 Tool holder 1
6 Cross pan head screw 2
7 Countersunk head screw 4
8 Cylinder head hex socket bolt 1
9 Bed cover plate door 1
10 Split washer 2
11 Half-Countersunk head screw 2
12 Plate 1
13 Motor pulley 1
14 Socket head cap screw 2
15 Poly-v-belt 1
16 Self-locking nut 1
17 Hex socket cap screw 2
18 Lock washer 2
19 Motor connecting plate 1
20 Big washer 1
21 Locking handle 1
22 Motor 1
23 Hex socket cap screw 2
24 Cross pan head screw 2
25 Cable plate 3
26 Locking handle 1
27 Tool rest 1
28 Tool rest base 1
29 Retaining ring 1
30 Threaded shaft & sleeve 1
31 Clamping plate
JMWL1203010002A
M6X30GB70B
WSH6GB97D1B
WSH6GB93B
JL93010017-001S
M6X12GB818B
M4X10GB819B
M5X12GB70B
JMWL1203011000A
CLP5GB896B
M4X10GB818B
JMWL1203010005
JMWL1203010007
M6X5GB80B
JMWL1203010001
M8GB889Z
M6X16GB70D2Z
WSH6GB93Z
JMWL1203010004
WSH8GB96Z
KTSB-1-B-M8X63X25
Z3612020
M6X16GB70D2B
M5X10GB818B
1502014-02
KTSB-1-B-M8X63X32
JMWL1203050001A-001G
JMWL1203050003
CLP15GB894D1B
JMWL1203050002
JL93030012 1
No.
Description
Part No.
QTY.
32 Self-locking nut 1
33 Locking lever 1
34 Retaining ring 1
35 Headstock cover 1
36 Hinge shaft 1
37 Wave washer 1
38 Bearing 1
39 Retaining ring 1
40 Socket head cap screw 3
41 Hand wheel 1
42 Roll pin 1
43 Index pin knob & shaft 1
44 Locating sleeve 1
45 Spring 1
46 Split washer 1
47 Threaded plate 1
48 Tapping screw 2
49 Support bracket 1
50 1
51 Headstock 1
52 Spindle pulley 1
53 Segmented RMP plate 1
54 Hexagon socket cap screw 2
55 Retaining ring C-clip 2
56 Bearing 1
57 Spindle 1
58 3" Face plate 1
59 Spur center 1
60 Cylinder head hex socket bolt 1
61 Cross pan head screw 1
62 Flat washer
M10GB889B
JMWL1203050004
CLP21GB894D1B
JMWL1203020001A-001S
JMWL1203020003
JL93010008
BRG6204-2RS-P5GB276
CLP20GB894D1B
M6X8GB80B
JMWL1203020013
PIN3X14GB879B
JMWL1203020008
JMWL1203020011
JMWL1203020009
CLP9GB896B
JL27010017
ST2D9X6D5GB845Z
JMWL1203020012
JMWL1203091001
JMWL1203020005A
JMWL1203020006A
JMWL1203020007
M4X10GB70Z
CLP47GB893D1B
BRG6005-2RSV2GB276
JMWL1203020004B
JMWL1203020010B
JL93011100
M5X8GB70D1B
M4X8GB818Z
WSH4GB97D1Z
1
No.
Description
Part No.
QTY.
63 Plate 1
64 Cross pan head screw 2
65 Socket head cap screw 2
66 Screw 2
67 Hinge 1
68 Hexagon socket cap screw 1
69 Flat washer 2
70 Set screw 1
71 Threaded shaft 1
72 Tailstock 1
73 Set screw 1
74 Retaining ring 1
75 Tailstock shaft 1
76 Hand wheel 1
77 Socket head cap screw 1
78 Rotation handle 1
79 Spring coil 1
80 Screw 1
81 Locking handle 1
82 Tailstock locking lever 1
83 Tailstock locking shaft 1
84 Live center 1
85 Nut 1
86 Compression spring 1
87 Clamping plate 1
88 Self-locking nut 1
89 Tapping screw 4
90 M16 Pull off 1
91 M20 Pull off 1
92 Electric box cover 1
93 Electric box
JMWL1203020014
M4X16GB819B
M6X10GB80B
M4X10GB823B
JMWL1203020002B
M5X16GB70B
WSH4GB97D1B
M5X25GB77B
JMWL1203040002
JMWL1203040003A
M5X12GB79B
CLP12GB896B
JL93030003
JMWL1203040005
M6X8GB80B
JL93030007
JMWL1203040007
JL93030008
JMWL1203041000
JMWL1203040001
JL93030001
JL93031000A
M5GB6170B
JMWL1203040004
JL93030012
M10GB889B
ST4D2X13GB845B
JL91046300
DJJH7120
JMWL1203090003-001S
JMWL1203091000F
1
Speed sensor

Table of contents
Other WoodFast Lathe manuals
Popular Lathe manuals by other brands
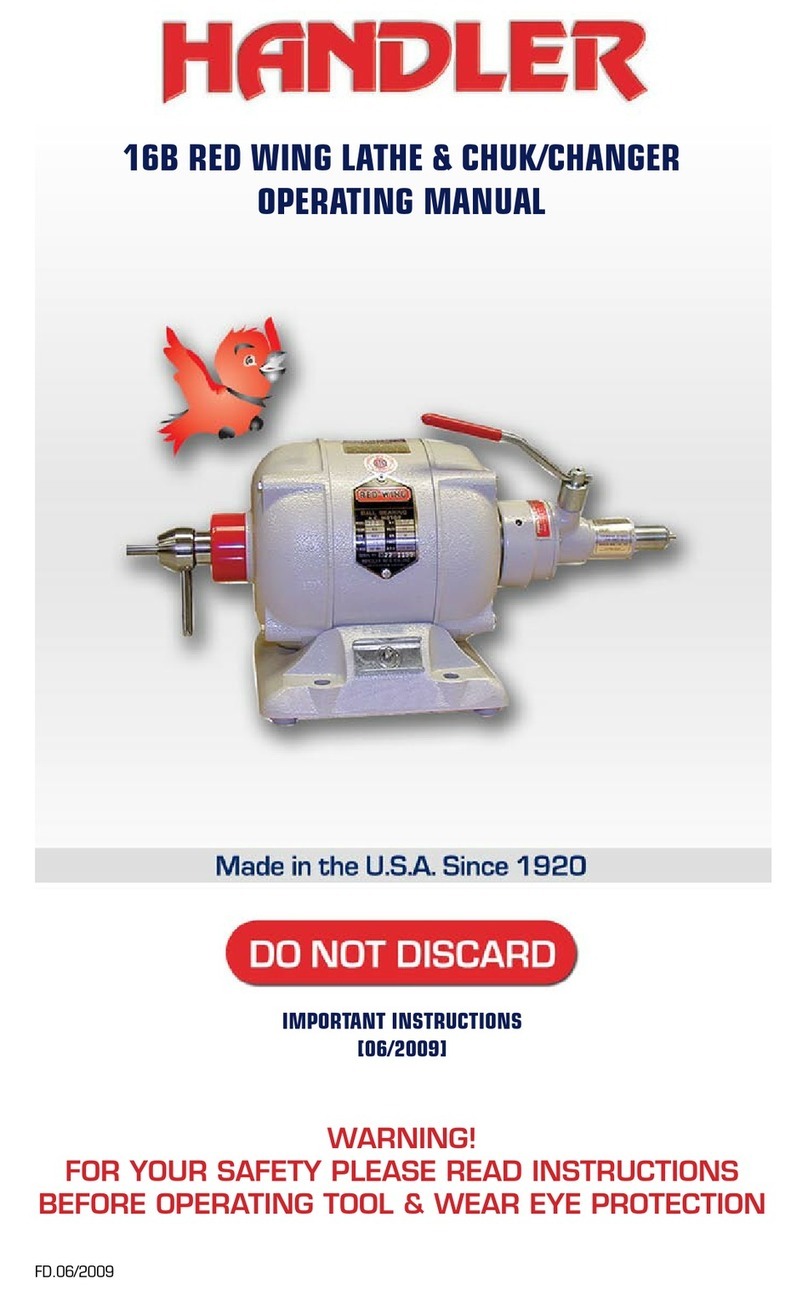
Handler
Handler Red Wing 16B operating manual
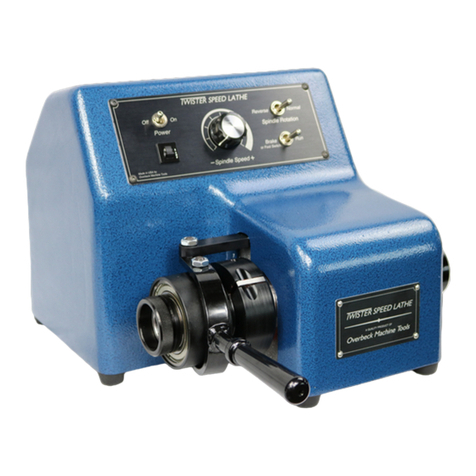
OVERBECK MACHINE
OVERBECK MACHINE LT-1BR owner's manual
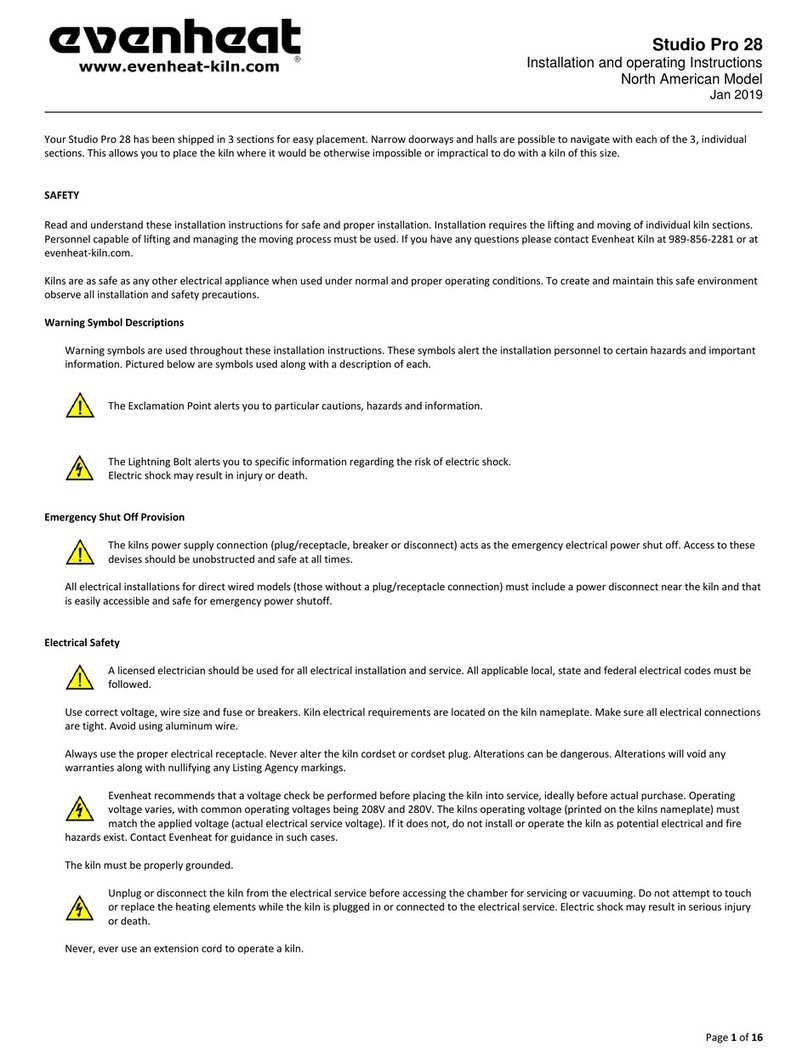
Evenheat
Evenheat Studio Pro 28 Installation and operating instructions
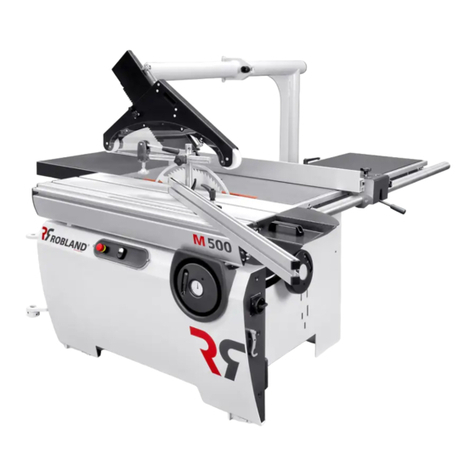
Robland
Robland M500 M manual
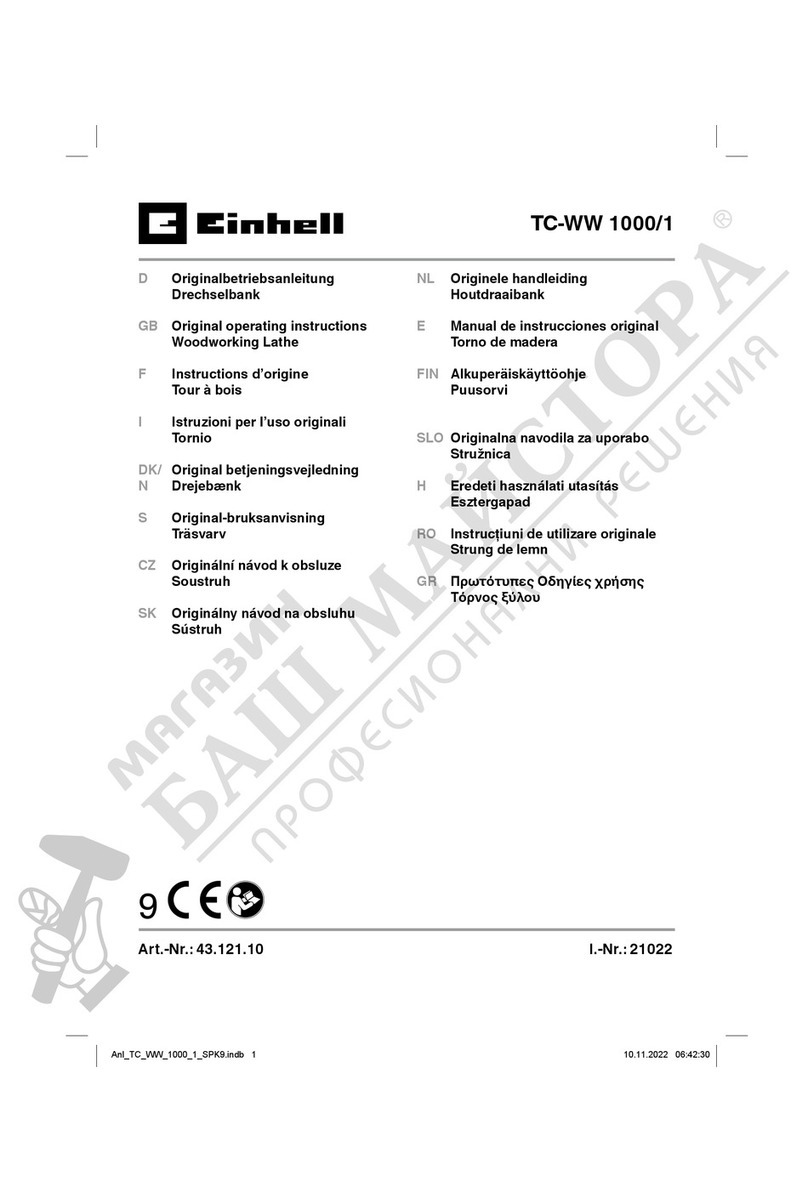
EINHELL
EINHELL TC-WW 1000/1 operating instructions
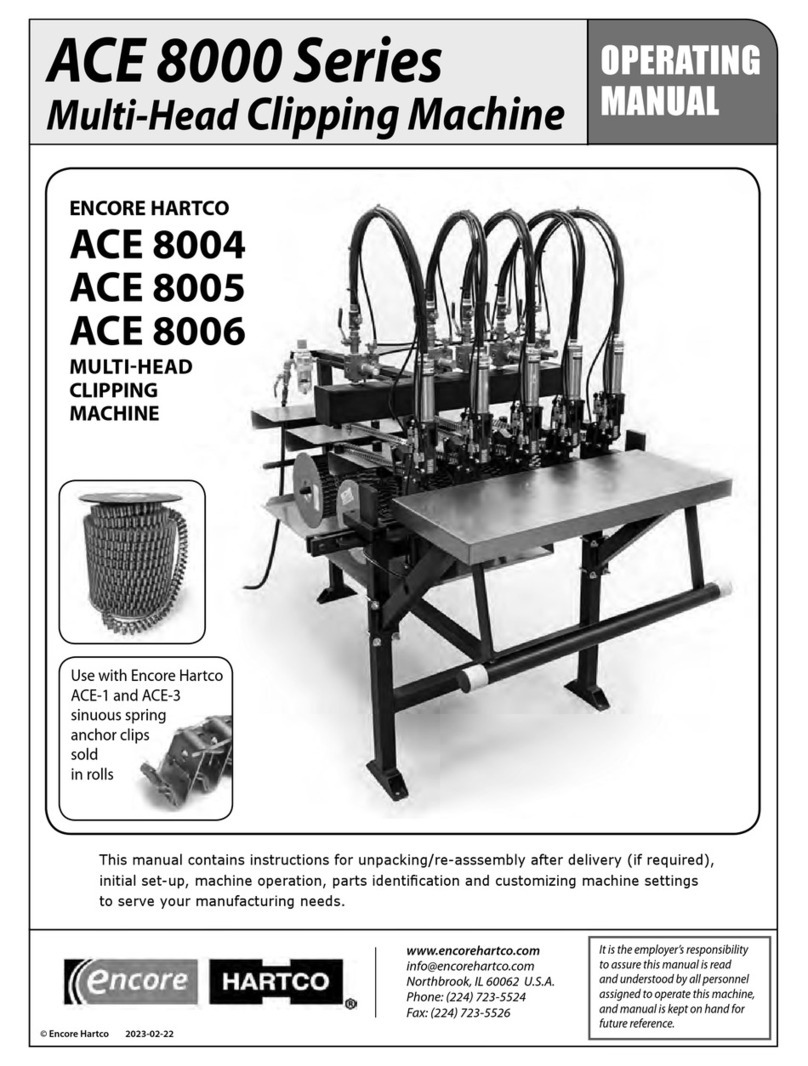
Encore Hartco
Encore Hartco ACE 8000 Series operating manual
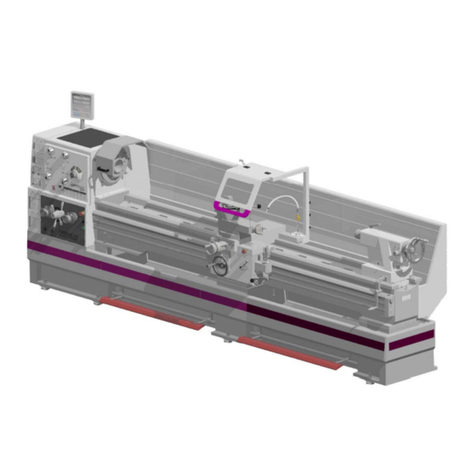
Optimum
Optimum OptiTurn TH 6620D operating instructions
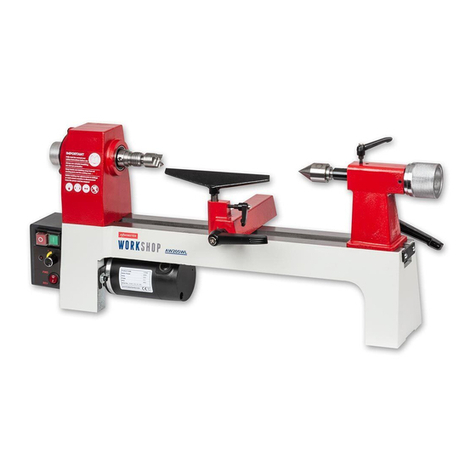
Axminster
Axminster WORKSHOP AW205WL Original instructions

Fervi
Fervi T999/230V Operation and maintenance manual
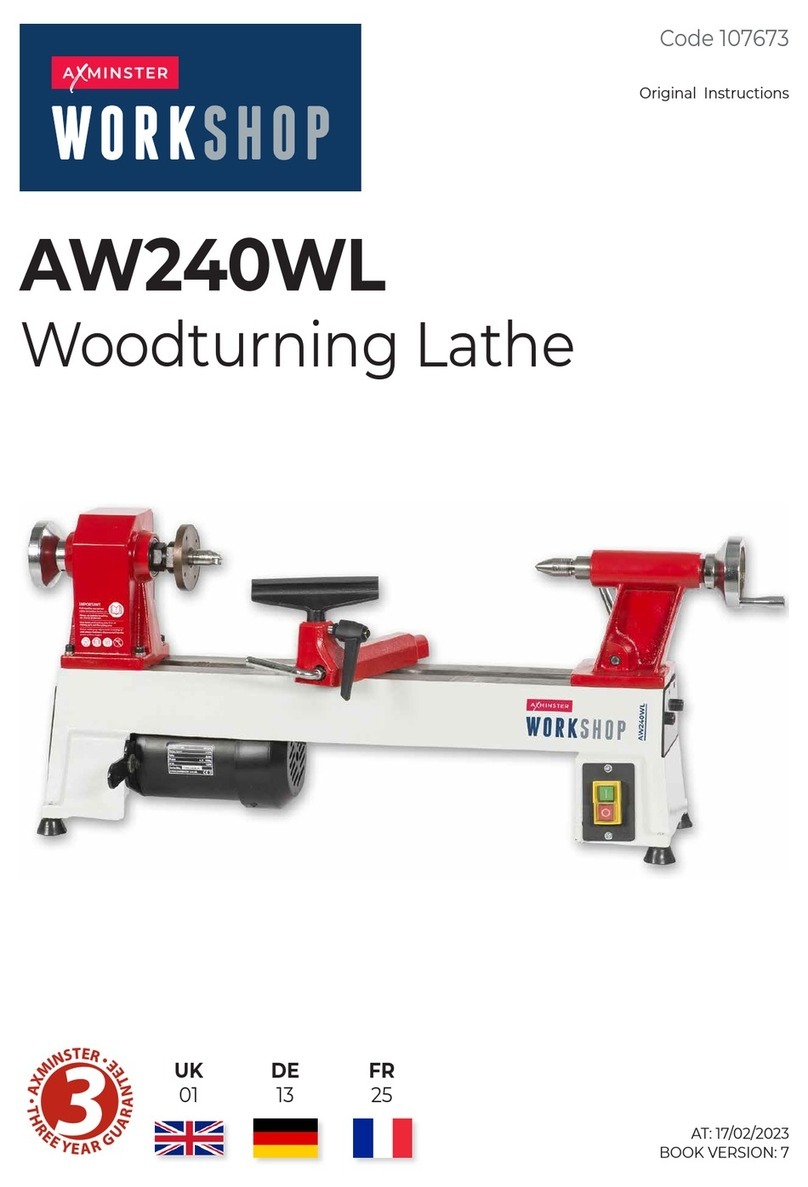
AXMINSTER WORKSHOP
AXMINSTER WORKSHOP AW240WL Original instructions
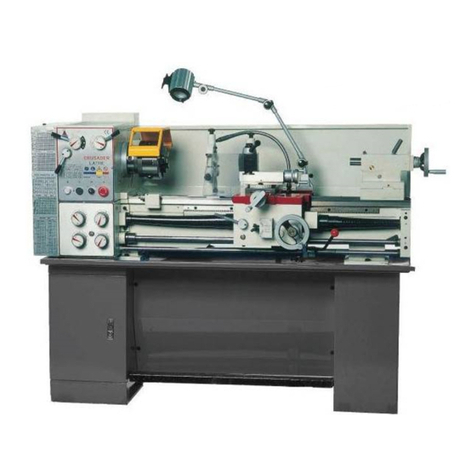
CHESTER
CHESTER Crusader VS Operation manual

Klutch
Klutch 49675 owner's manual