YASKAWA SI-ES3 User manual




















Other manuals for SI-ES3
2
Other YASKAWA Control Unit manuals
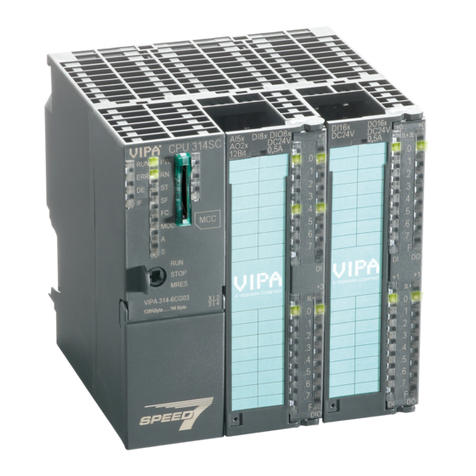
YASKAWA
YASKAWA SPEED7 CPU-SC 313-5BF23 User manual
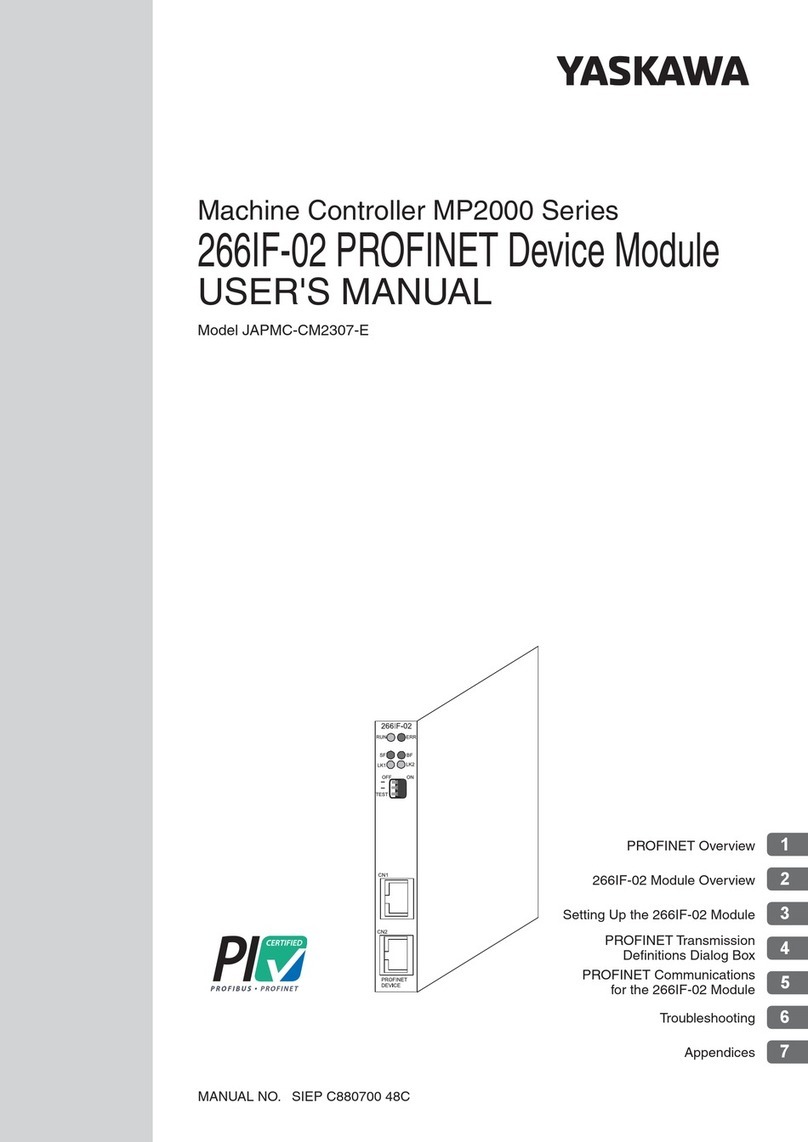
YASKAWA
YASKAWA MP2000 Series User manual
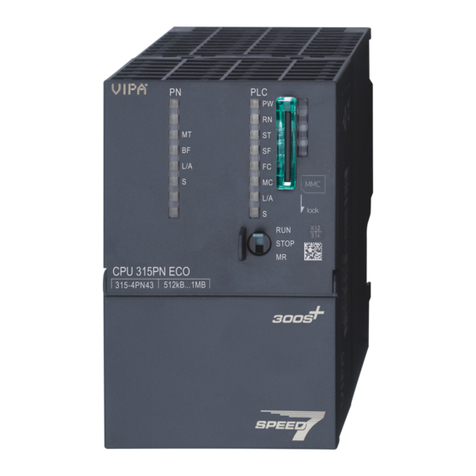
YASKAWA
YASKAWA System 300S+ CPU 315-4PN43 User manual
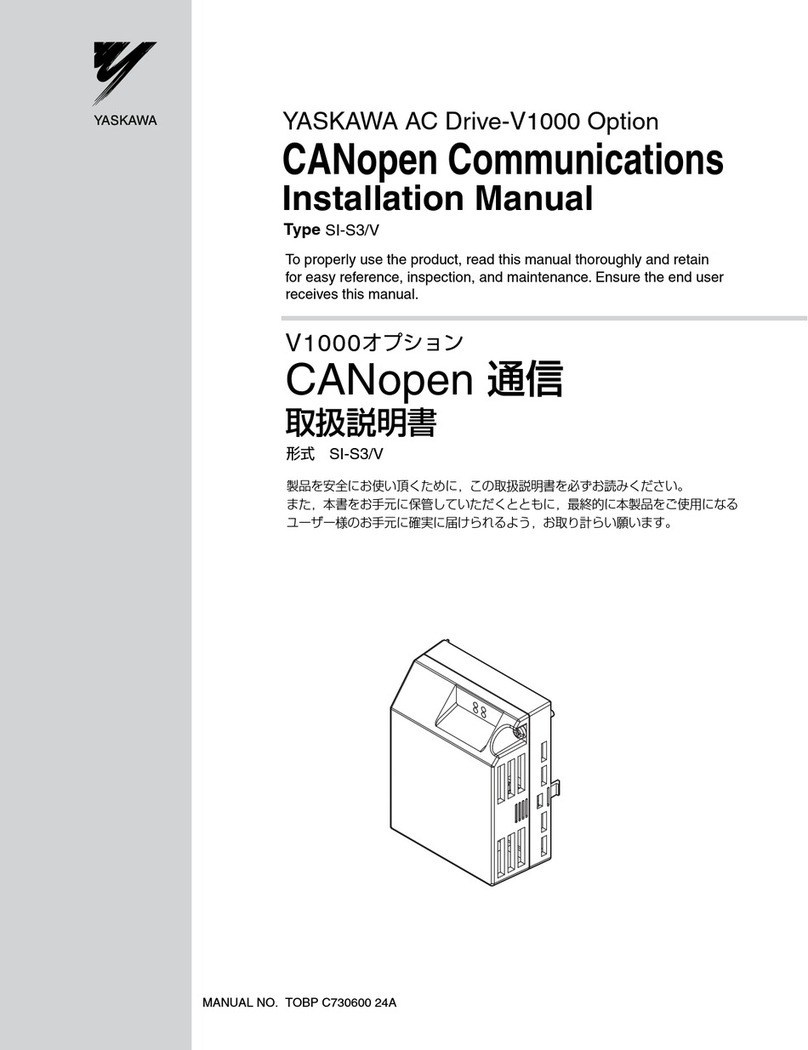
YASKAWA
YASKAWA CANopen SI-S3/V User manual
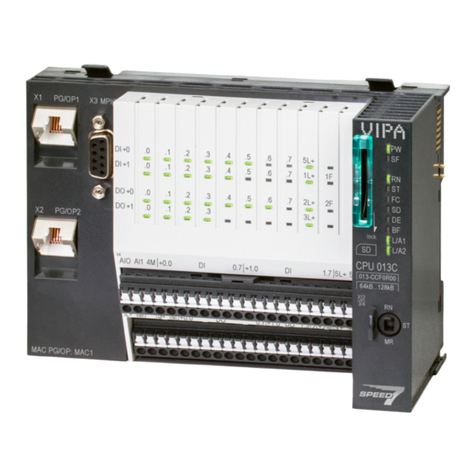
YASKAWA
YASKAWA VIPA System SLIO User manual
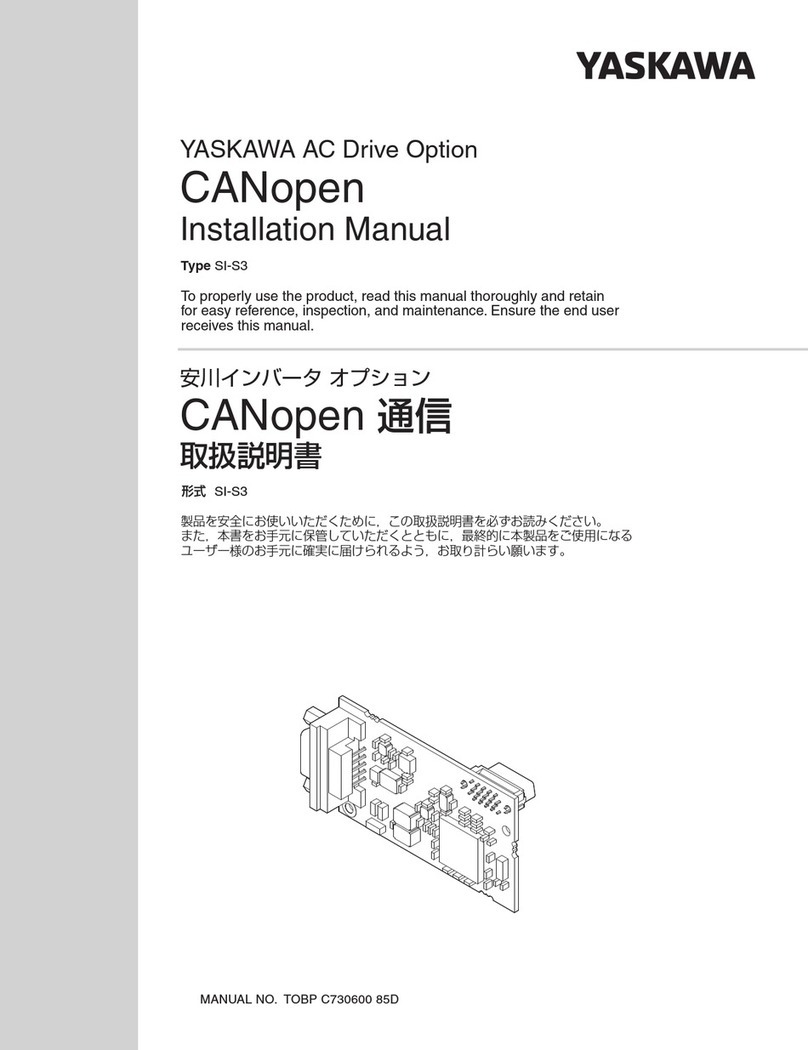
YASKAWA
YASKAWA CANopen SI-S3 User manual

YASKAWA
YASKAWA JEPMC-OP3C01-E User manual
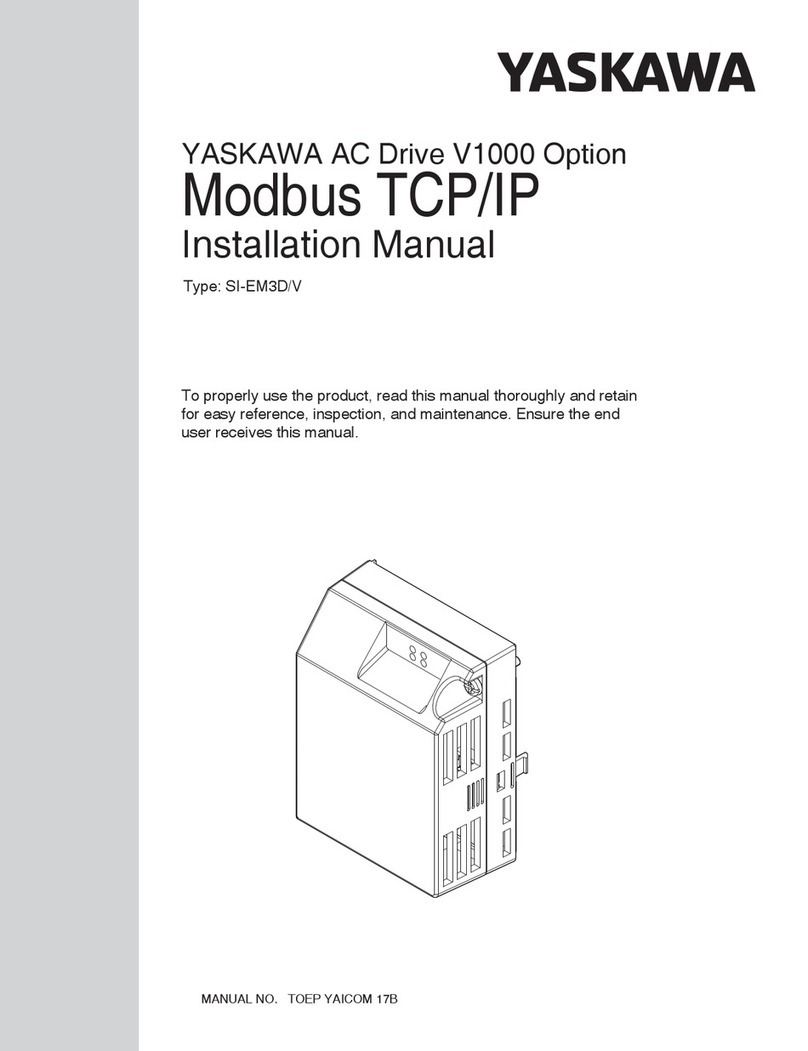
YASKAWA
YASKAWA V1000 SI-EM3D/V User manual

YASKAWA
YASKAWA VIPA SLIO FM 050 User manual
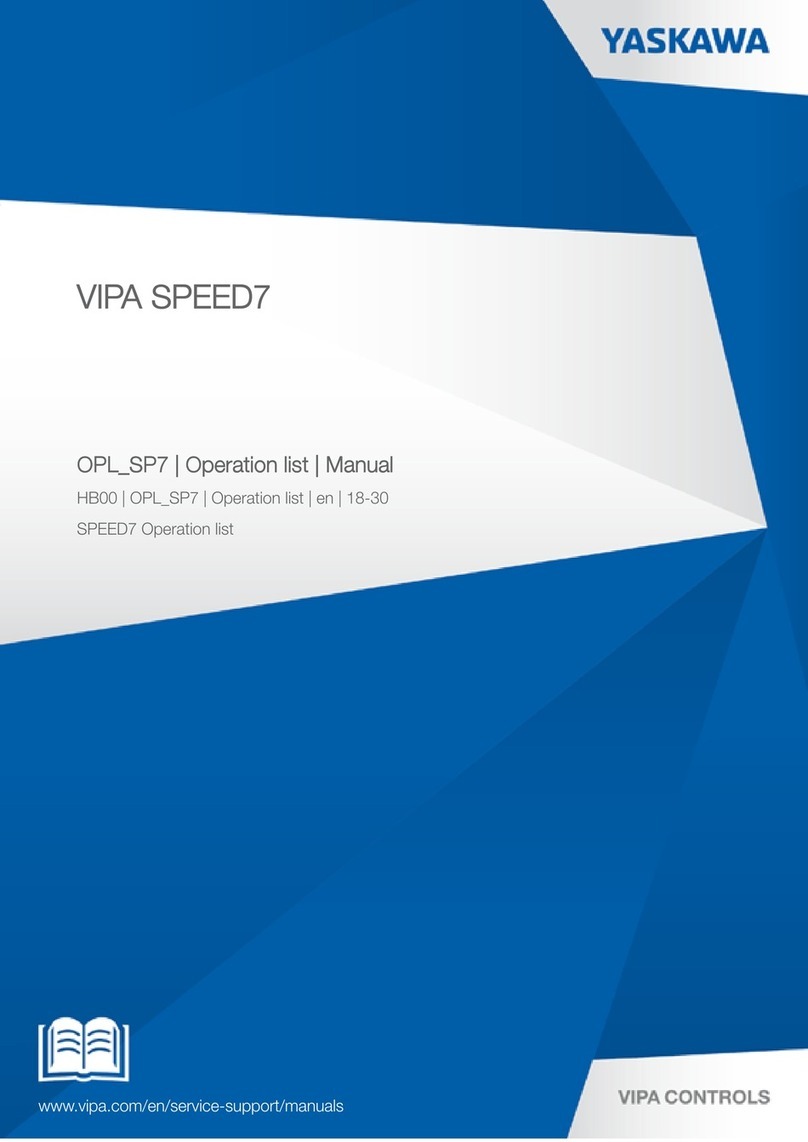
YASKAWA
YASKAWA VIPA SPEED7 User manual
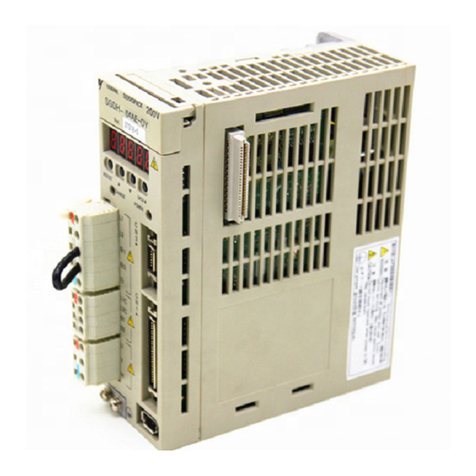
YASKAWA
YASKAWA MECHATROLINK Sigma 2 Series User manual
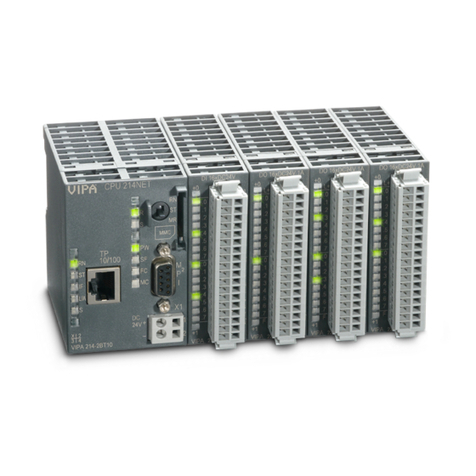
YASKAWA
YASKAWA VIPA System 200V User manual
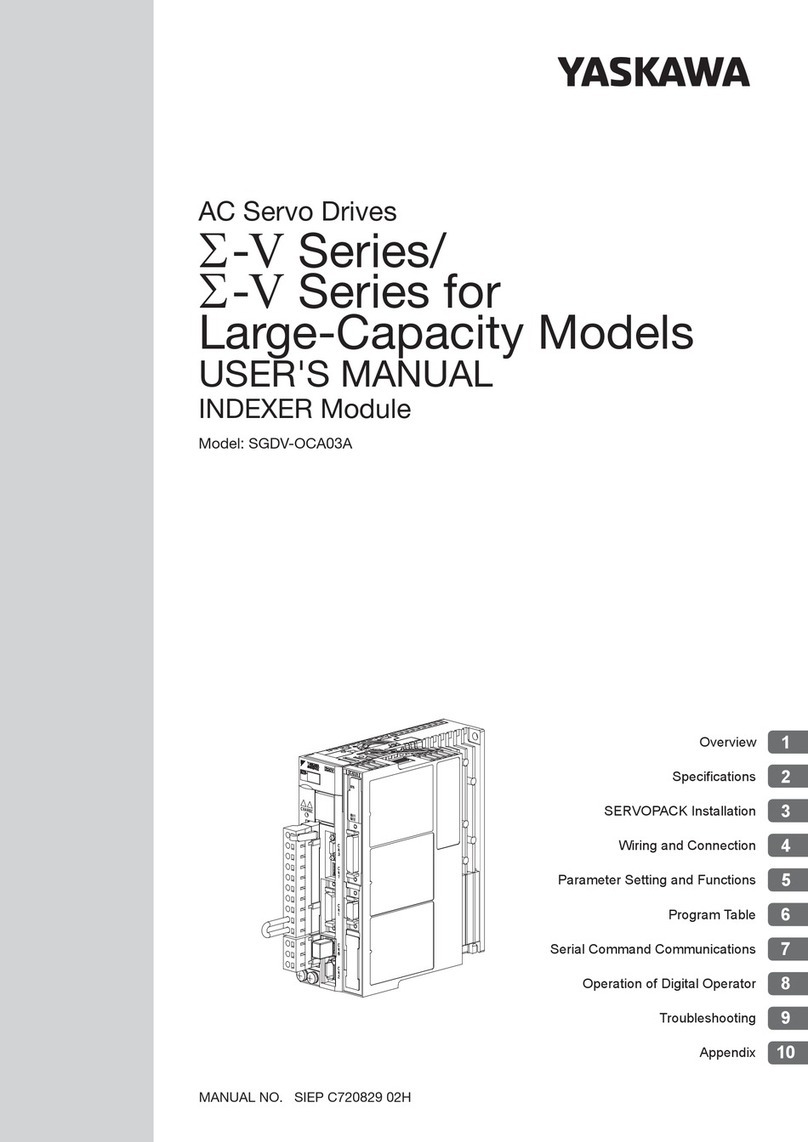
YASKAWA
YASKAWA S-V Series User manual

YASKAWA
YASKAWA CM006 User manual
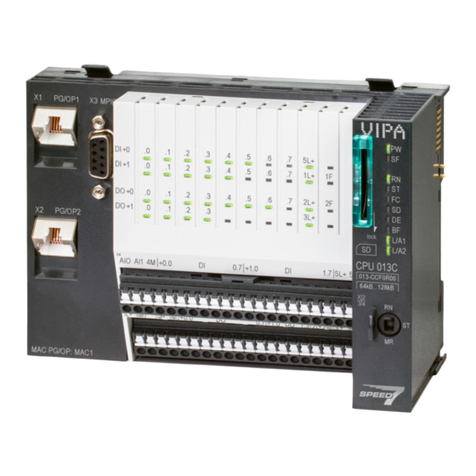
YASKAWA
YASKAWA VIPA System SLIO User manual

YASKAWA
YASKAWA FM 054 User manual
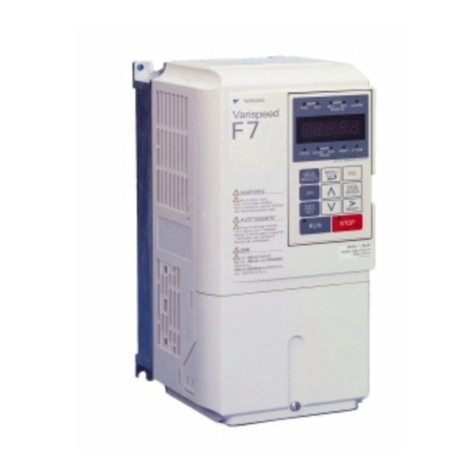
YASKAWA
YASKAWA Varispeed f7 User manual
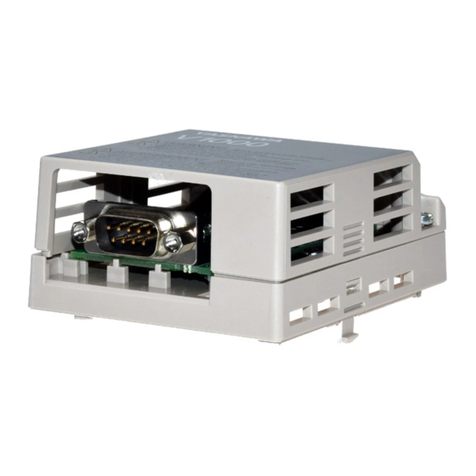
YASKAWA
YASKAWA SI-EP3/V User manual
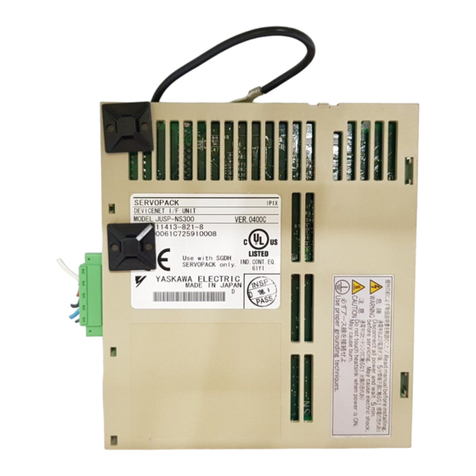
YASKAWA
YASKAWA S-II Series User manual

YASKAWA
YASKAWA 62K-JJK0 User manual
Popular Control Unit manuals by other brands
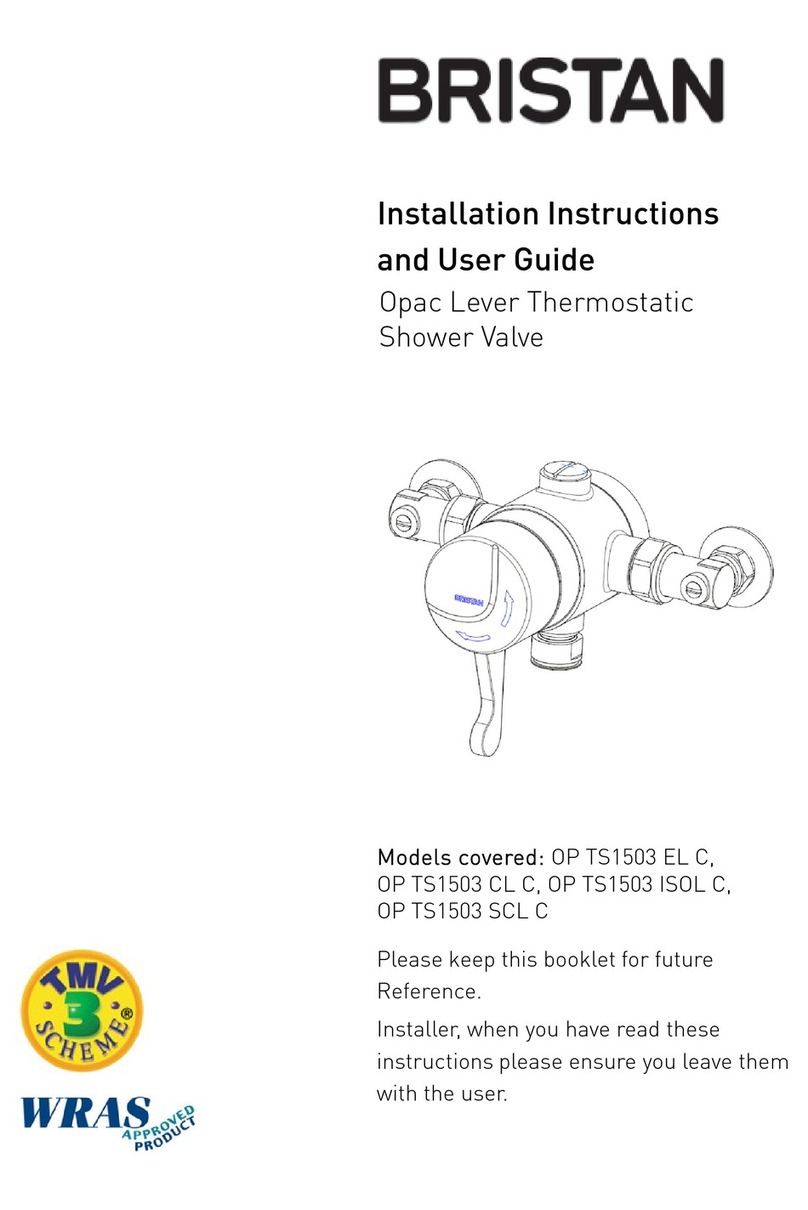
Bristan
Bristan OP TS1503 CL C Installation instructions and user guide
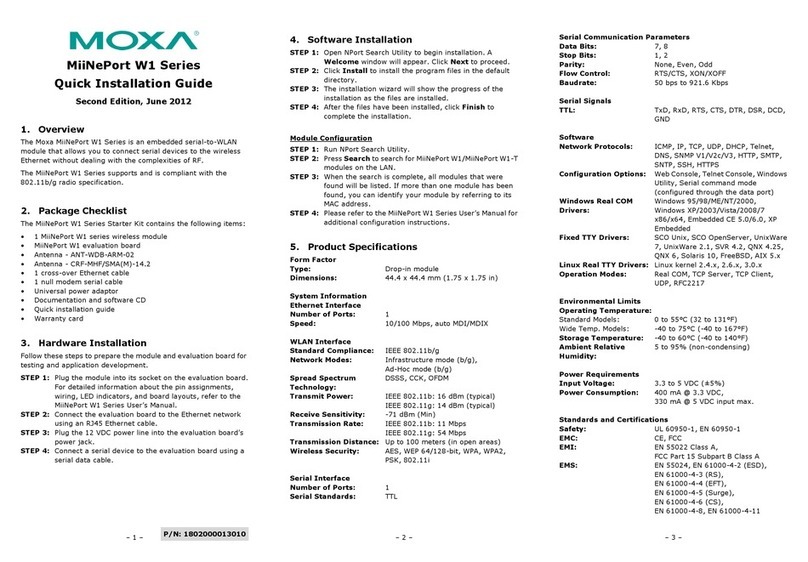
Moxa Technologies
Moxa Technologies MiiNePort W1 Series Quick installation guide
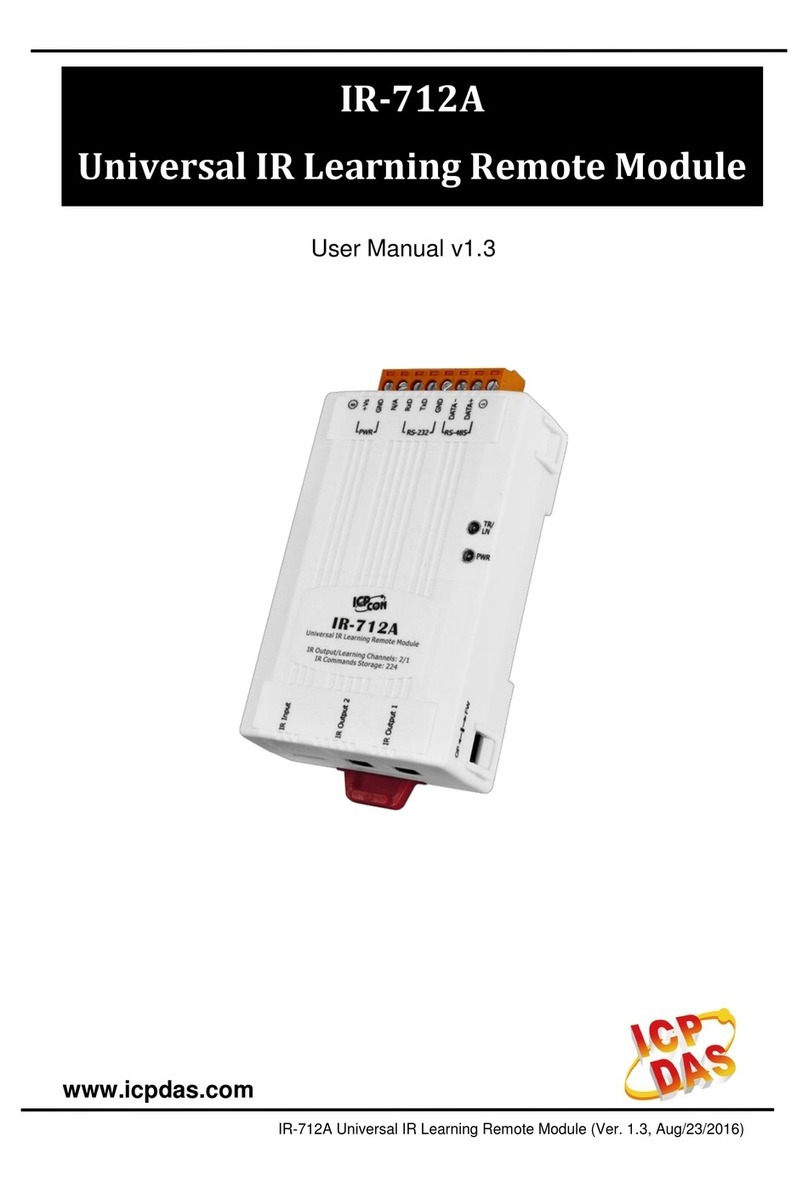
ICPDAS
ICPDAS IR-712A user manual
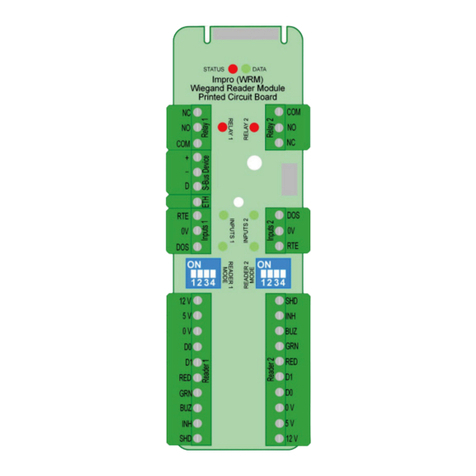
impro technologies
impro technologies HMW701-0-0-NN-XX installation manual
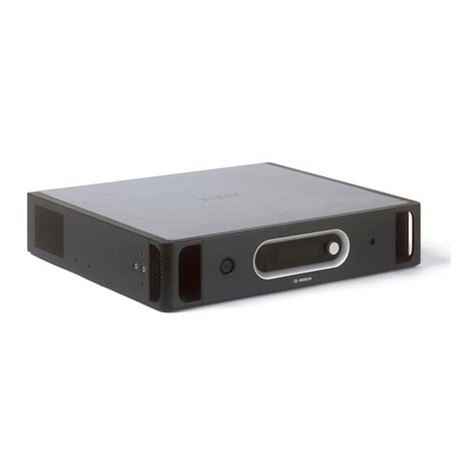
Bosch
Bosch CCU-Modul Important information

Genebre
Genebre 2272 Installation, operation and maintenance manual
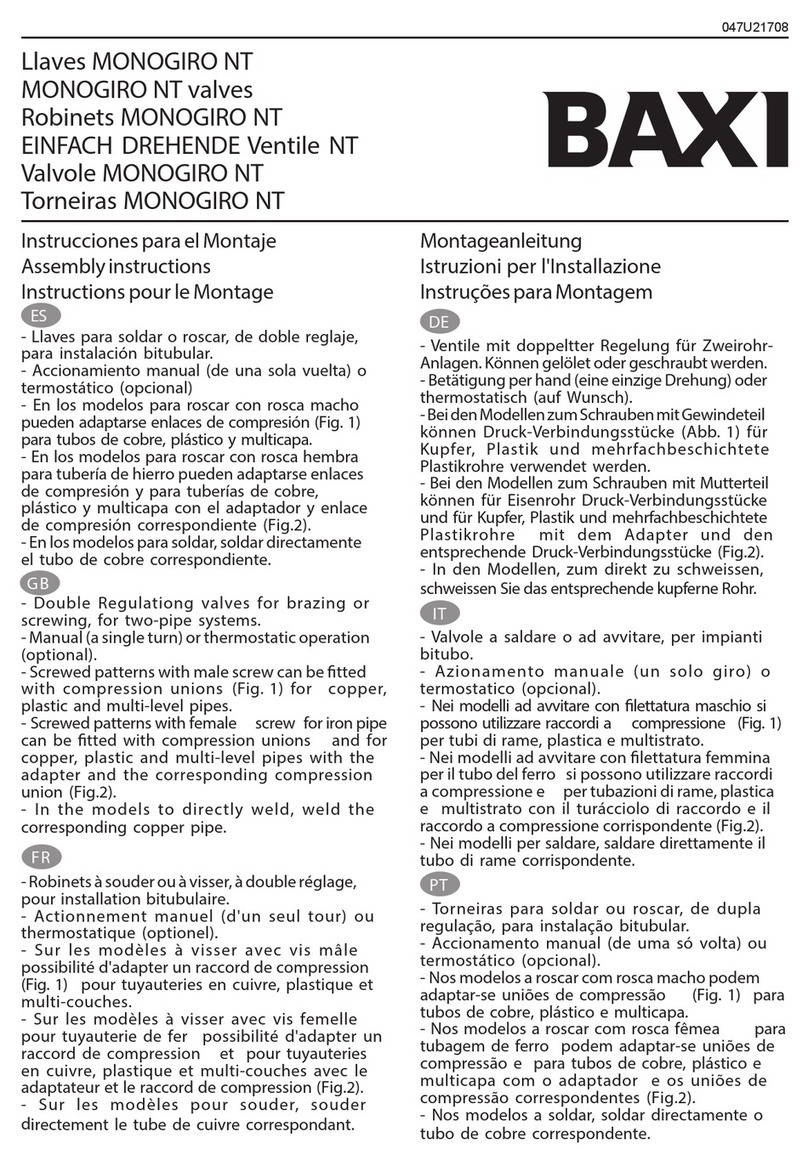
Baxi
Baxi MONOGIRO NT Series Assembly instructions
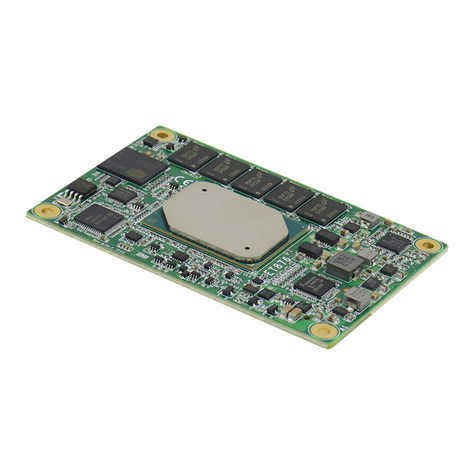
IBASE Technology
IBASE Technology ET876 Series user manual

GMV
GMV GreenLift 3010 2CH A3 Installation, use and maintenance manual
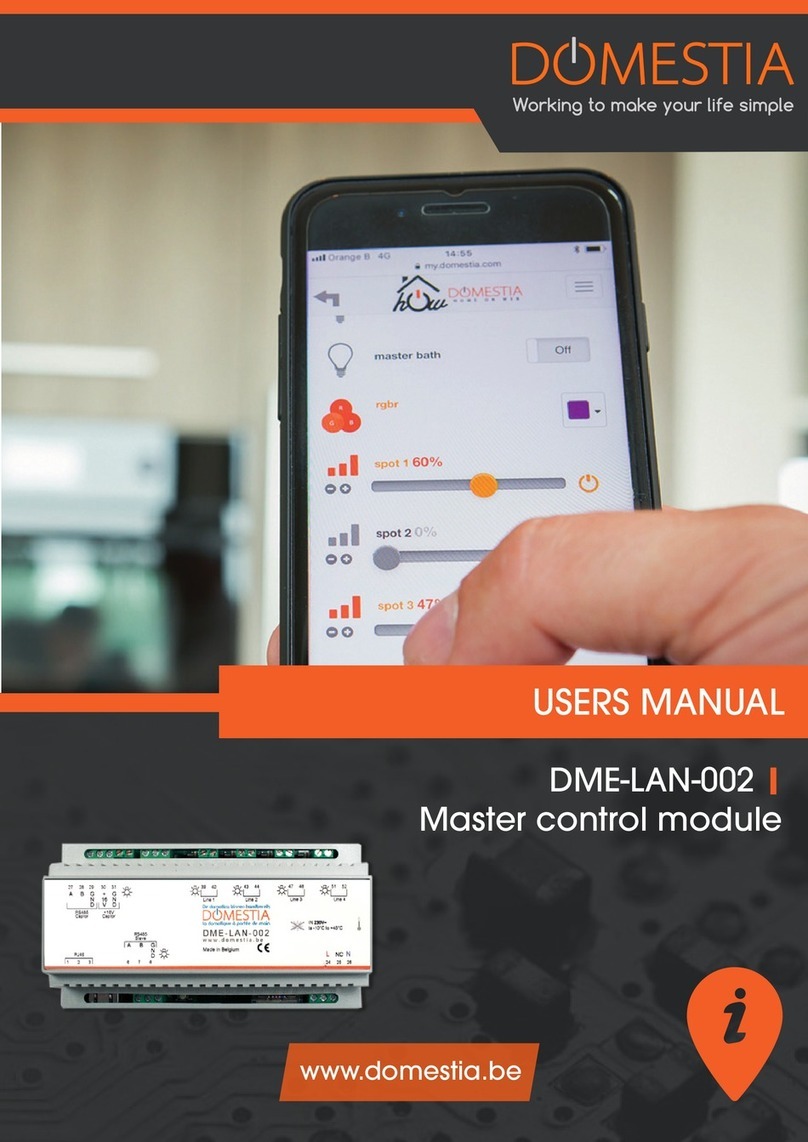
Domestia
Domestia DME-LAN-002 user manual
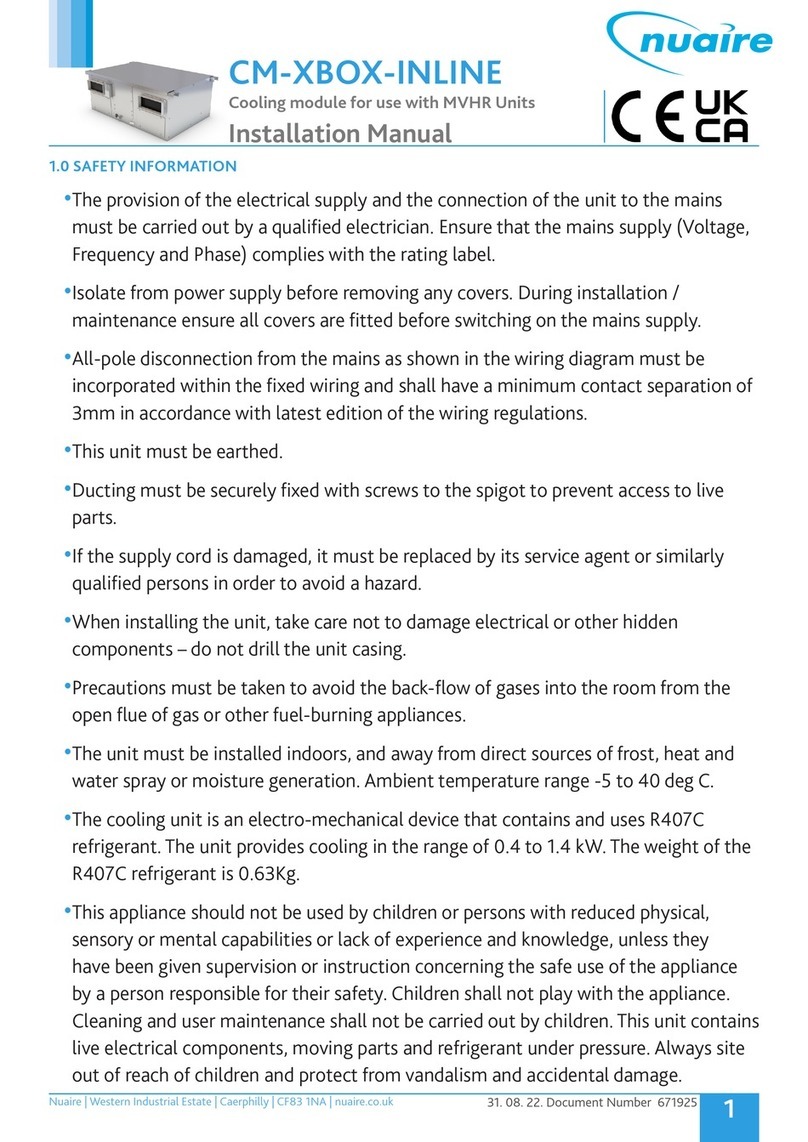
NuAire
NuAire CM-XBOX-INLINE installation manual
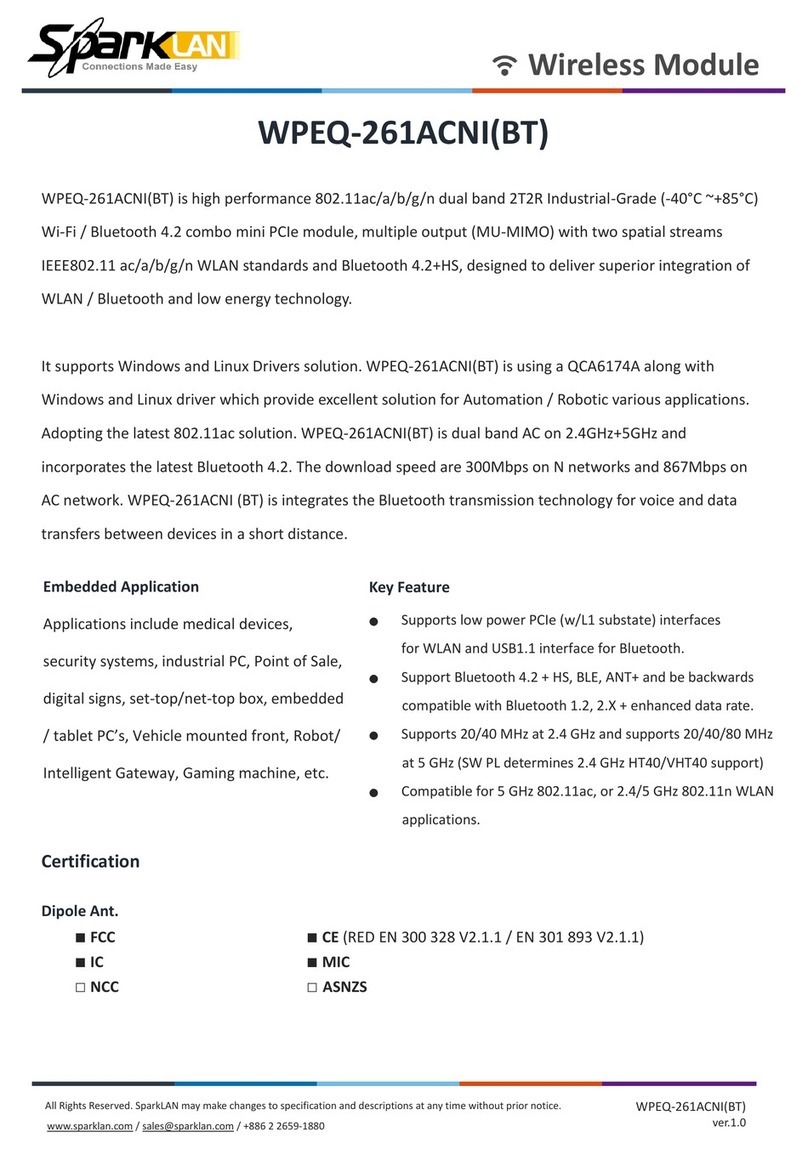
Sparklan
Sparklan WPEQ-261ACNI user manual