zeeltronic PCDI-24V User manual









Other zeeltronic Controllers manuals
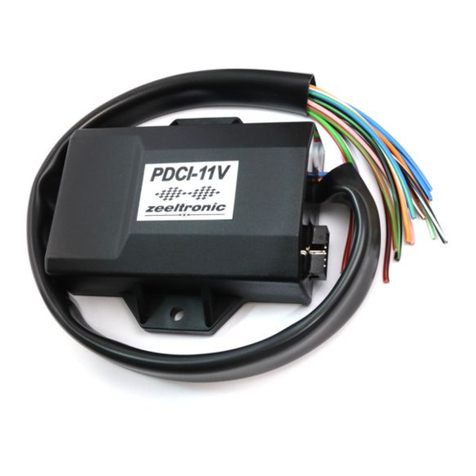
zeeltronic
zeeltronic PDCI-11V User manual
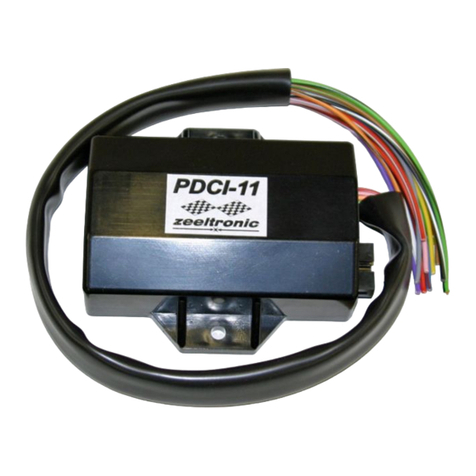
zeeltronic
zeeltronic PDCI-11 User manual

zeeltronic
zeeltronic PDCI-24VT Owner's manual
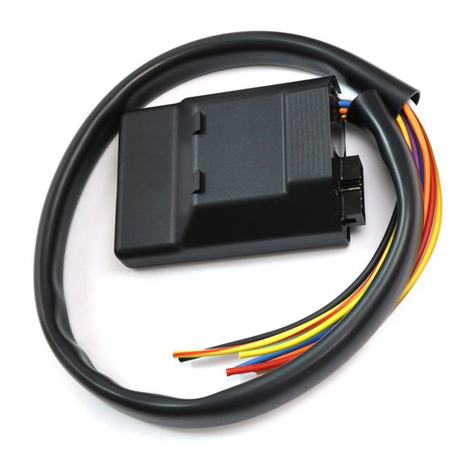
zeeltronic
zeeltronic PCDI-10 User manual
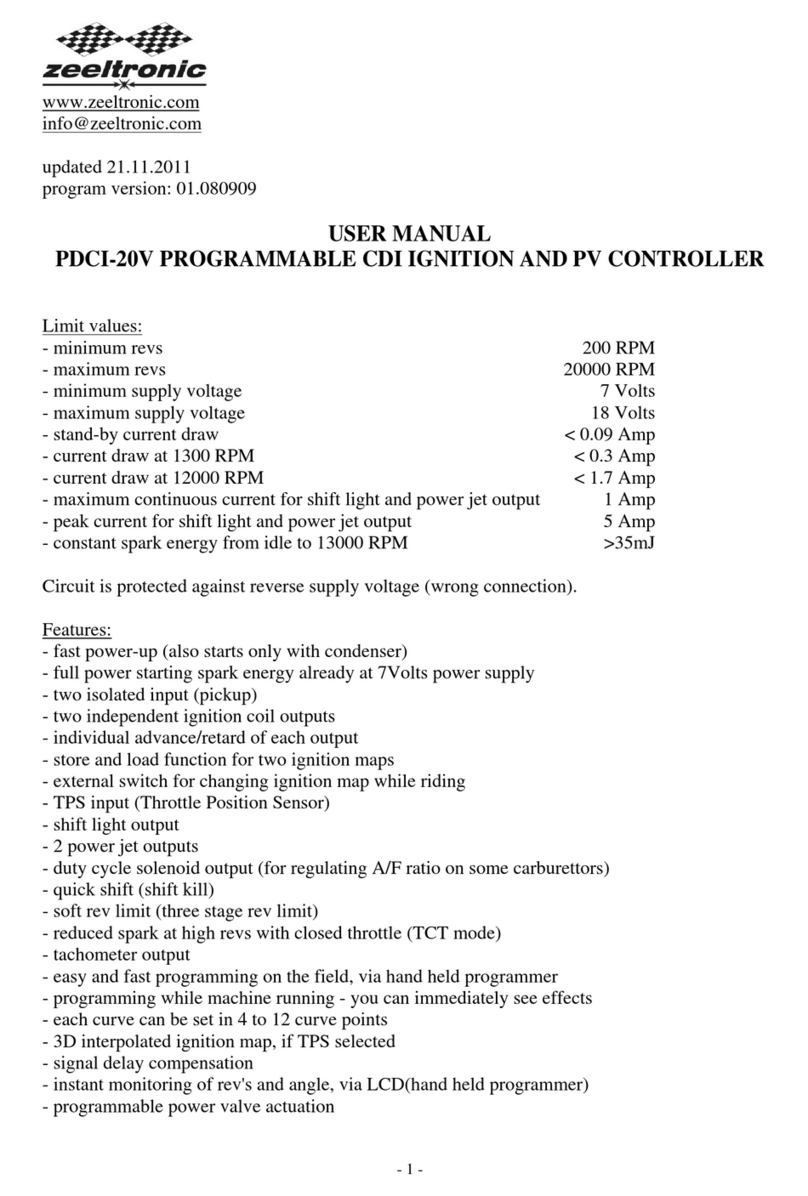
zeeltronic
zeeltronic PDCI-20V User manual
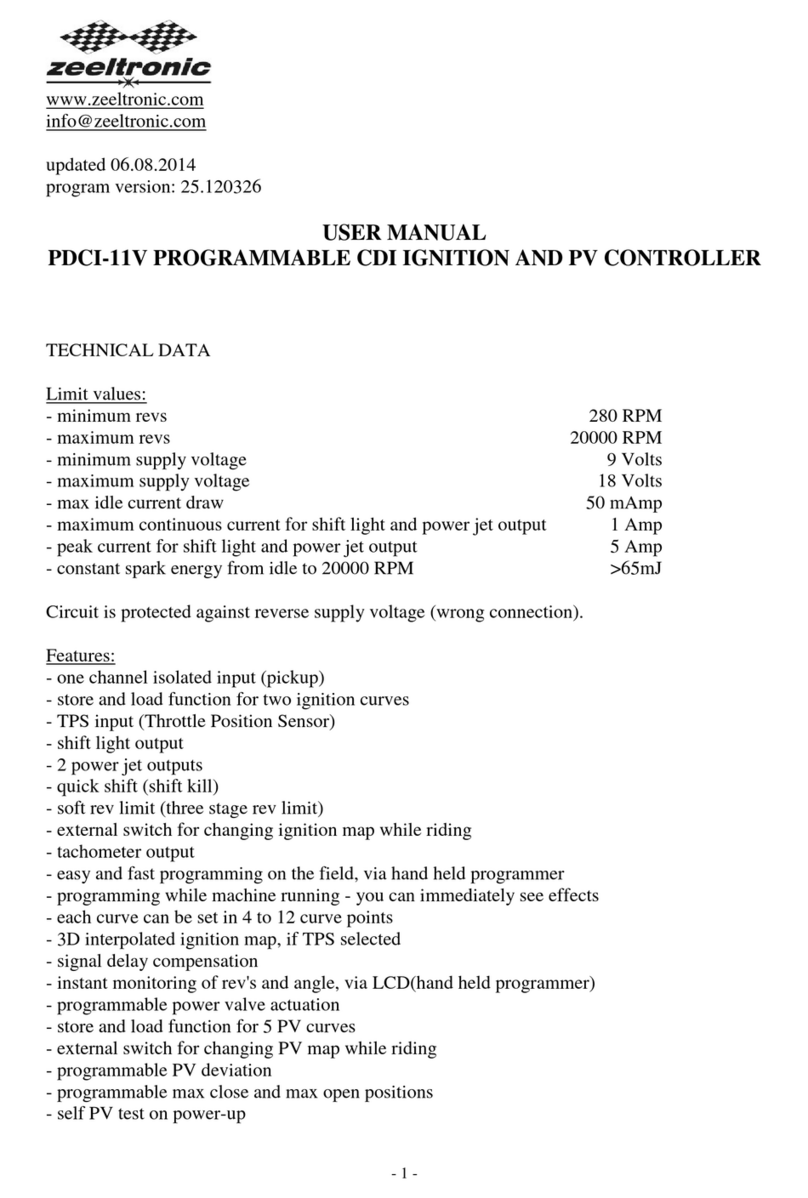
zeeltronic
zeeltronic PDCI-11V User manual
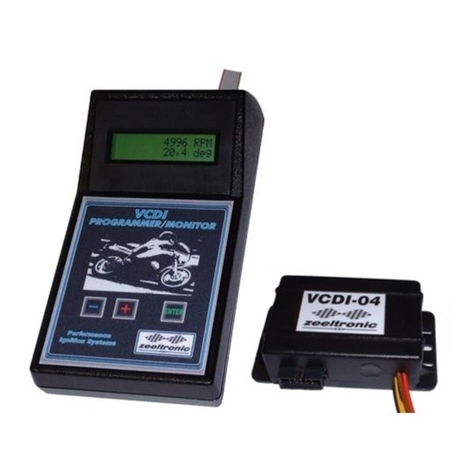
zeeltronic
zeeltronic VCDI-04 User manual
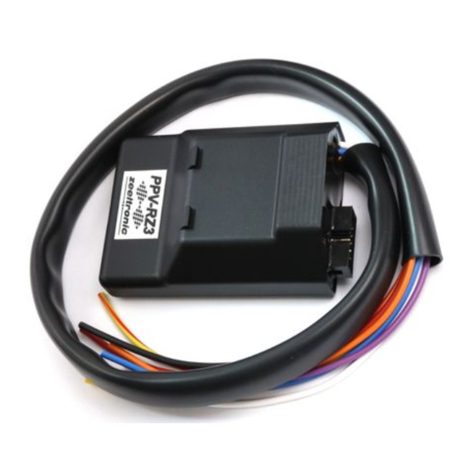
zeeltronic
zeeltronic PPV-RZ3 User manual
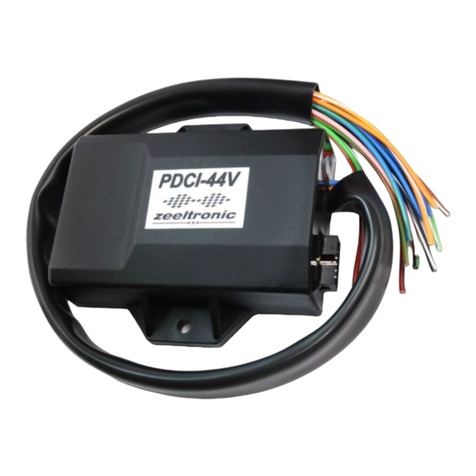
zeeltronic
zeeltronic PDCI-44V User manual

zeeltronic
zeeltronic PSR-S01 User manual
Popular Controllers manuals by other brands
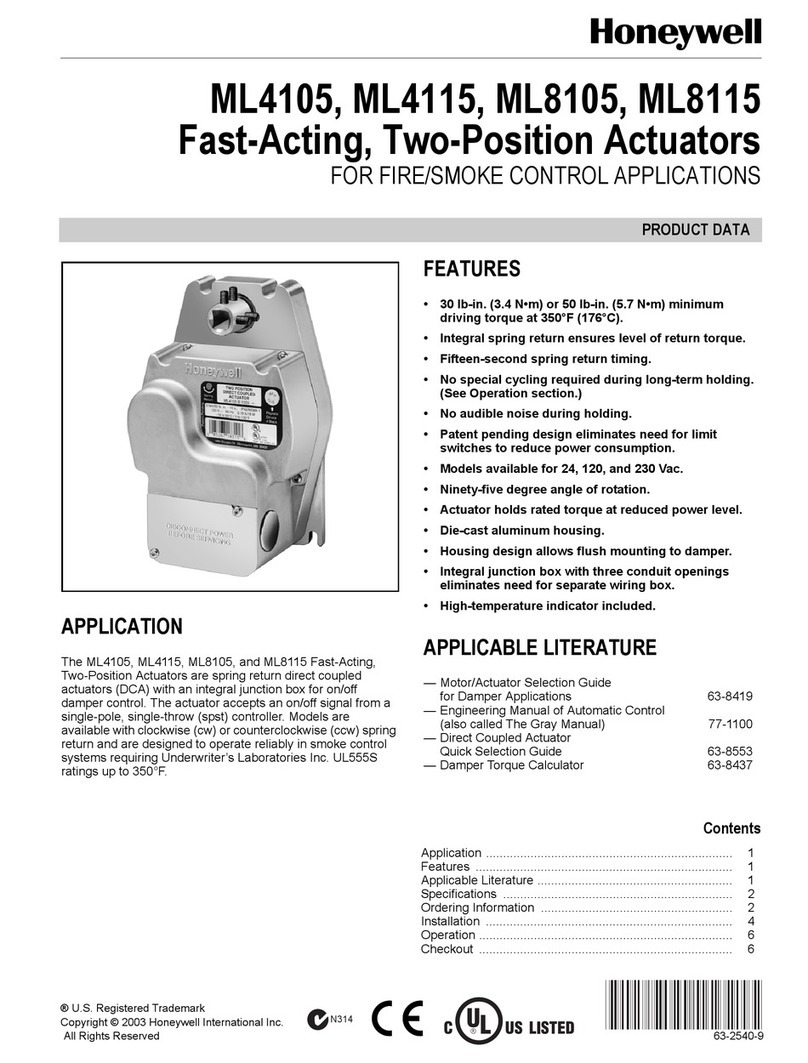
Honeywell
Honeywell ML4105 Product data
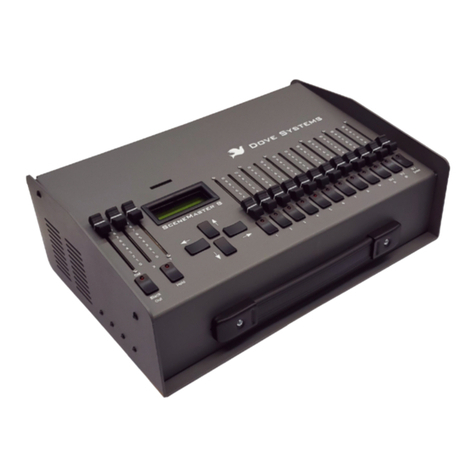
Dove Lighting Systems
Dove Lighting Systems SceneMaster 8 user manual

Voicebird
Voicebird Voicebird Mini user guide
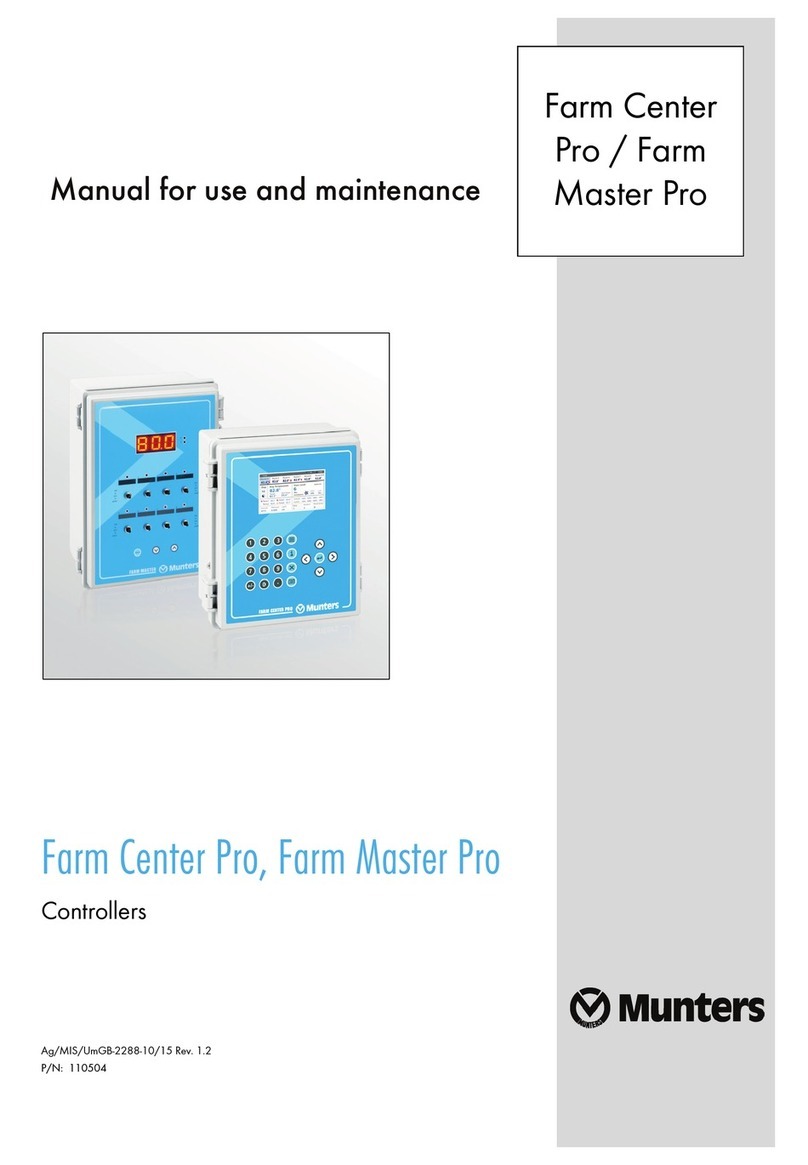
Munters
Munters Farm Center Pro Manual for use and maintenance
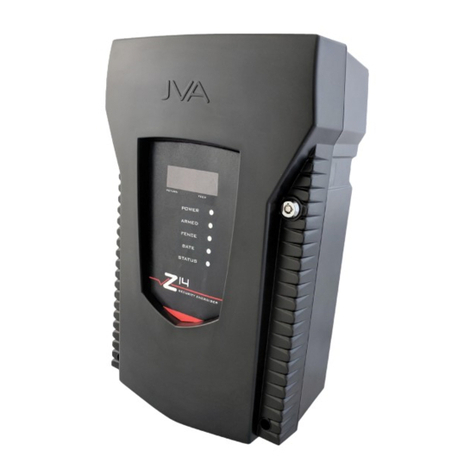
Pakton
Pakton JVA Z Series user manual
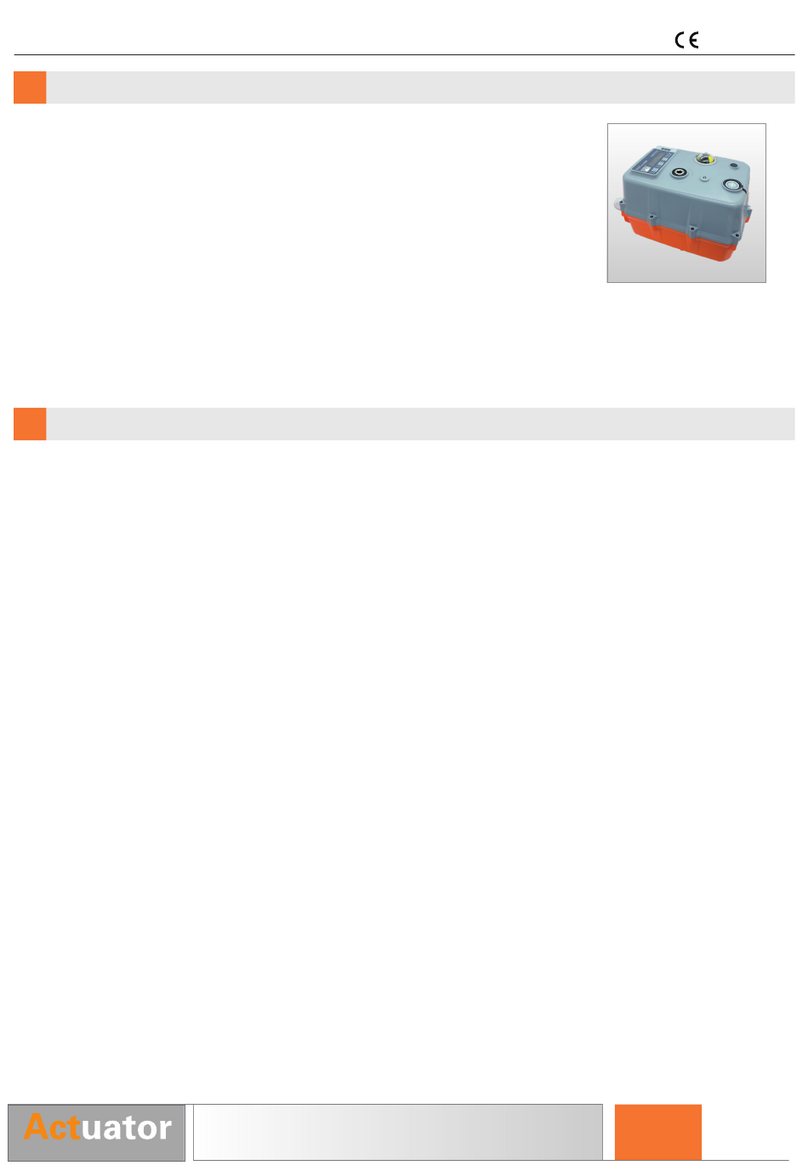
Actuator Systems
Actuator Systems TCR-40C Series Usage instructions