ZIMO MX10 User manual

INSTRUCTION MANUAL
The ZIMO
COMMAND STATION MX10
Chapter
1. ... First start up of the ZIMO system ..................................................................4
2. ... Power supply and technical specifications.....................................................5
3. ... Typical system configurations........................................................................6
4. ... The MX10AVP Connection board................................................................10
5. ... Layout track, programming track, AOS in/out’s ...........................................13
6. ... DCC format, feedback, database ................................................................15
7. ... Firmware update of the MX10 via USB stick ...............................................16
8. ... Operation and controls ................................................................................17
8.1.The Normal MX10 Operating Screen..................................................................... 17
8.2.Voltage & Current Settings –VOLT & AMPERE MAIN.......................................... 18
8.3. Broadcast stop, Track power off, Overcurrent, Low voltage –STOP & OFF......20
8.4. BaseCab LOCO (Driving without a Cab)...............................................................22
8.5. BaseCab OP PROG (CV-Programming without cab)........................................... 23
8.6. BaseCab SERV ADR (Decoder address programming).......................................23
8.7. BaseCab SERV PROG (CV-Programming)..........................................................23
8.8. The MX10 MENU (Main Menu)............................................................................. 24
8.9. USB flash drive software updates ........................................................................31
8.10. Decoder update and sound upload..................................................................... 31
9. ... “Roco Z21” App and other app’s on th MX10 ..............................................32
10... The interlocking programm “ESTWGJ” on the MX10 ..................................33
11... USB connection to the computer.................................................................35
Annex: EMC test report / TÜV Austria..................................................................36
EDITION
2013 03 15
2013 10 15
2013 11 23
2014 02 28
2014 04 04
2014 04 05
2014 12 02
2014 12 03
2014 12 10
2014 12 16
2015 02 04
2015 04 10
2015 05 27
2015 07 21
2015 10 20
2015 12 07
2016 02 11
2016 04 05
2017 06 01
2017 10 12
Some parts of this manual may relate to not fully implemented features. The final
implementation may vary from the present text or pictures.

Page 2 OPERATING MANUAL COMMAND STATION MX10
Display (128 x 64 pixel, RGB- backlit)
Normal operating screen
BLUE
Primary volt and amp values, track 1, track 2, communication‘s statistics, AOS
VOLT & AMP Main settings
YELLOW
Output voltage, maximum permissible current for track 1, track 2
, Bt. 1 ()
VOLT & AMP Detail settings
YELLOW
Turn-off times, differential (current jump) turn-off, tolerance
2 sec
STOP & OFF
RED
Broadcast stop BCS, track 1 power OFF, track 2, overcurrent OVC (Short circuit)
Button 3 ()
BaseCab LOCO
GREEN
Set vehicle address, use rotary knob for driving, use buttons for functions
Button 2
(MENU)
GRAY
Select menu choices by turning and pressing rotary knob
M,,
DCC SERV PROG
YELLOW
Read and program CV‘s at the programming track 2 (Schiene 2)
M,,
MX10 Config
GRAY
Several settings such as language, radio channel, sniffer inputs, booster…
Various information i.e. software version, statistic, date/time…
USB-Stick
UPDATE & SOUND
GRAY
Decoder update and sound project uploads via USB stick
KEY TO SYMBOLS: Rotary knob, turn rapidly back and forth Scroll with rotary knob Press rotary knob Button 1() Button 2 (M)Button 3()
USB (Host) socket
Accepts a USB
flash drive.
Insert
UPDATE & SOUND
Select a file for
decoder update,
sound upload, and
for MX10’s own
update.
Rotary knob
Normal operating screen BLUE –Protected against unintentional actuation: brief push or turn NO effect
(rapid turning left/right) .Enters main setting page for VOLT & AMP (display YELLOW) .
(press for 2 sec) Broadcast stop BCS and operating state STOP & OFF (display RED)
(press for 1 sec) Cancels broadcast stop and returns to normal operation (or to previously active state)
(press for 4 sec) .SYSTEM OFF (track 1& 2 OFF, CAB power OFF, display OFF etc.)
(press for 1 sec) SYSTEM ON
Outside of normal operation (-screen) – Scroll and Select, Adjust, Drive Direction…
3 buttons
Normal operating screen BLUE –
Button 1() AOS operating sequences, settings and control display
Button 2(MENU) Menu for operating mode selection GRAY
Button 3() Operating mode LOCO DIRECT GREEN
STOP & OFF (after rotary knob or short circuit) RED
Button 1 BCS, OFF, ON for track 1 Button 2…for track 2
BaseCab GREEN
Button 1, 2, 3 (after selecting a group) Function switching
UPDATE & SOUND BLUE (GREEN )
Button 1Starts decoder update Button 2 Starts sound upload
Button 3() (unless otherwise assigned) returns to normal screen (BLUE)
Sockets for ZIMO CAN and XNET
CAN bus for 6-pin connection with ZIMO
cabs and modules; additionally: sniffer in-
puts on 8-pin socket.
Note: Stationary StEin modules are connected on
the rear side of the MX10.
XNET socket for the connection with ROCO
Locmouse and similar; on the 8-pin socket
(additionally): second ZIMO CAN bus and
second XNET bus (in reserve).
SUSI socket
For quick sound uploads via
SUSI interface.

OPERATING MANUAL COMMAND STATION MX10 Page 3
Schiene 2,
Powered by
external DC power supply
10 - 35 V =
80 - 600 Watt
Only electrically insulated
power supplies are allowed!
The MX10 starts automati-
cally after the power supply
is connected and turned on.
Outputs: track1 (“Schiene 1”) | DC track voltage (DC out) S1, S2 |track 2 (“Schiene 2“)
2-pin socket for track 1 (“Schiene 1“) –usually for the main track
2-pin socket for track 2 (“Schiene 2“) –for programming or 2nd main track.
“Digital current” (DCC, MM, poss. other future formats such as mfx, sx)
Polarity N, P is of no importance in simple layout applications,
but is important on layouts with track sections or block control using compo-
nents such as MX9 modules, StEin modules or boosters.
The track 1 (Schiene 1), track 2 (Schiene 2) outputs can be set individually
(different) in terms of voltage, amp limits etc., depending on configuration
and situation with the same or different data signal.
3-pin socket “DC out”: S1 (to track1), M = “Ground”, S2 (to track2)
to power stationary modules such as StEin, track section, reverse loop modules
etc. (within the MX10 DCC end stage limits).
All necessary plugs are included.
Audio-socket (Line-out)
For amplified sound-
playback primarily
through internal speak-
ers (from warning
sounds to complete
sound projects; appli-
cation is not ready by
2017).
Sockets for ZIMO CAN and LAN
CAN Bus - for a 6-pin connection with ZIMO
cabs and modules, and/or
- for an 8-pin connection with
ZIMO stationary modules “StEin” and com-
patible boosters
(CAN and synchronisation for external DCC
output stages).
LAN interface as an alternative network to
the USB computer connection, or the
W-LAN Router (Tablet-Apps…)
AOS inputs and LED outputs
8 logic inputs (responds to negative and positive voltage,
e.g. rail power) for
- External buttons for panic STOP and track power OFF
- Rail contacts for internal AOS‘ (automated operations)
- Rail contacts for external AOS‘ (automated operations)
6 LED outputs (up to 25 mA) for signals or other lights, con-
trolled by AOS‘
5V and GROUND supply pins.
2.4 GHz antenna for Mi-Wi wireless network
Zimo uses “Mi-Wi”, a "mesh network" based
on components and software from Microchip,
derived from the ZigBee standard for wireless
cab communication. The messages are
passed from node to node until they reach
their destination, even if no direct radio link is
available.
Expandable to wireless decoder communica-
tion.
USB (device) socket
USB computer hock-up
socket for switch panel
applications and config-
uration software.
The transfer rate corre-
sponds to 1 M baud; the
necessary protocol is
available at the ZIMO
web site.
Loconet socket
Ready for future implementation.

Page 4 OPERATING MANUAL COMMAND STATION MX10
General notes:
This manual reflects (matches) the product- and software version at delivery. The device
may show further features after an update. New versions of this manual are published on the
ZIMO website www.zimo.at .
ZIMO devices should not be operated in extreme surroundings (heat, humidity). The air cir-
culation into and out of the device should not be restricted (i.e. by covering).
The cable connection should not be squeezed or put under physical tension or twisted. In
order to have a faultless power- and data transmission, make sure that all connections have
a solid fit.
The device should not sty under voltage unattended. The power supply unit(s) must be dis-
connected from the mains using a switchable socket strip or pulling the plug(s).
Children under the age of 8 years must be under supervision of an adult when operating the
device.
Improper use or opening of the device without consulting ZIMO may lead to danger or loss of
warranty.
For further information about ZIMO products, sound projects for locos or software from ZIMO
partners, please visit our website at http://www.zimo.at/web2010/index.html
1. First start up of the ZIMO system
The ZIMO system is usually offered as a
starter set. Different types of sets are of-
fered, this manual refers to a set with:
1 command station MX10
1 cab MX32 or MX32FU
1 power supply with 30 V / 240 VA or
more
Different plugs, CAN cable, power cable
(adapter may be necessary)
In a first step, all connections must be es-
tablished with the material (cables, plugs
…) included (picture see page 6):
oMX32 cab using the CAN bus cable to the command station MX10 (“ZIMO CAN” socket)
oThe track system to the terminal “Schiene 1” (track 1) or “Schiene 2” (track 2) of the
MX10. Track 2 may be used as a separate main track but can also be switched into “Ser-
vice mode” for programming.
oThe power supply cable to the terminal “DC in”. Polarity must be correct, there is no dan-
ger in any case.
oThe power supply to the mains (110 –240 V ~). In case the MX10 does not start (boot),
change cables of the plug in the terminal “DCC in” on the MX10 (wrong polarity)
The command station MX10 starts when power is supplied through “DC in”. The boot se-
quence shows a red, than blue screen.
The cab switches itself on subsequently (30 sec.). In case of…
..a new MX32, it shows the LOCO IN
screen. Enter the address of the loco you
want to drive:
..a used MX32 (with locos in it’s memory), it
shows the LOCO or the SWI screen. Continue
driving the loco or add an new one be pressing
the A-key to switch to the LOCO IN screen.
After entering the address in the screen, press
the F-key to activate the newly entered loco –
the screen turns into the LOCO screen
You can drive the new loco now using the
slider, the R- and the function keys.
To drive a new loco, press the A-key
to switch to the LOCO IN screen and
add a new address. Activate the new
loco by pressing the F-key.
ATTENTION: It is important to use the cable with the identical plugs on both sides!
address
A-key
F-key

OPERATING MANUAL COMMAND STATION MX10 Page 5
2. Power supply and technical specifications
The ZIMO command station MX10 (and thus all connected control system components and the entire
model railroad layout) is supplied by an external power supply; this provides the so-called "primary"
power. A product offered by ZIMO as well as a third-party product can be used as a power supply unit,
as long as it complies with the basic conditions:
The power supplies available from ZIMO meet these criteria’s. Consult the product and price lists for
the currently available power supplies or for the ones supplied with the starter sets. The example here
shows a ZIMO standard power supply with 30V and 8A output; this 240 W –device is included in
the current starter sets but can also be ordered separately.
The track output voltages of the MX10 is reduced to values between
10 –24 V by the internal DC converter, depending on the Volt & Amp
settings (corresponding chapter).
Due to the internal power consumption of the MX10, the voltage differ-
ence between the MX10 input and track output must be 3V or more.
The maximum track voltage must be 3 V below the voltage available
from the power supply.
The total track current may be higher than the power supply current: the
smaller the track voltage compared to the power supply, the higher the cur-
rent (max. double). In the case of a 240 W power supply unit, total currents
of 8A (at 24V) and 15A (at 12V) can be expected.
There are however other power consumers besides the track outputs (i.e.
attached cabs etc.), that limit the available power according to configura-
tion settings.
The power supply output is connected with
the “DC in” socket (at the rear, left) of the
MX10.
Observe polarity (+ / -) !
There will be NO damage to the MX10
if polarity is reversed, but it won’t run
either.
Track 1 output (Schiene 1)
Default
-Track voltage ………………………………..………….
(adjustable in 0.2 V increments).…..
10 to 24 V
16 V
-Boot-up current ……………………………..…………….
(adjustable in 1 A increments).…….
1 to 12 A
5 A
-Track voltage boot-up time ….…………………....
(adjustable in 1 sec increments).…..
1 to 60 sec
1 sec
-Overcurrent threshold ……………………...………………
(adjustable in 0.1 A increments).…..
1 to 12 A
5 A
-Overcurrent turn-off speed ………..…………………
(adjustable in 0.1 sec increments)
0.1 to 5 sec
0.2 s.
-Tolerated transgression of overcurrent threshold...
(adjustable in 0.5 A increments).…..
0 to 4 A
0 A
for the time of….………..
(adjustable in 0.5 sec increments)…
1 to 60 sec
0 sec
-Spark suppression (Select from Off /Lev1 /Lev2)................
Level 1…………………..……
8 A
OFF
Level 2……(sensitive)…...
4 A
Track 2 output (Schiene 2)
Default
-Track voltage ………………………………..………….
(adjustable in 0.2 V increments).…..
10 to 24 V
16 V
-Boot-up current ……………………………..…………….
(adjustable in 1 A increments).…….
1 to 8 A
3 A
-Track voltage boot-up time ….…………………....
(adjustable in 1 sec increments).…..
1 to 60 sec
1 sec
- Overcurrent threshold ……………………...………………
(adjustable in 0.1 A increments).…..
1 to 8 A
3 A
-Overcurrent turn-off speed …..………………………
(adjustable in 0.1 sec increments)...
0.1 to 5 sec
0.2 s.
-Tolerated transgression of overcurrent threshold...
(adjustable in 0.5 A increments).…..
0 to 4 A
0 A
for the time of ….…
(adjustable in 0.5 sec increments)…
1 to 60 sec
0 sec
- Spark suppression (Select between OFF /Lev1 /Lev2)................
Level 1……………………..…
8 A
OFF
Level 2…..( sensitive)........
4 A
DC outputs S1 and S2
DC output 30 V
(Power supplied to other devices connected to the CAN bus).…..
4 A
DC output 12 V
(Power for XNET and Loconet devices)........................................
2 A
LED outputs
(6 pins on 2 x 8-pin plugs) –constant 15 mA current... …….
max. 25 mA
“out 5” and “out 6” useful for relays ..….
100 mA
AOS inputs
(8 pins on 2 x 8-pin plugs) –Switch to ground or switch-threshold
0 to 32 V
Audio output
(2.5 mm phone jack) ……………………………………………..
Line-out
RailCom
Detector track1
Measurable minimum amplitude of RailCom signal
4 mA
Sample rate (3-times oversampling)...........................
750 kHz
Detector track 2
Measurable minimum amplitude of RailCom signal.
4 mA
Sample rate (3-times oversampling)..........................
750 kHz
ZACK
Detector track1
Detection threshold ………………………………….
500 mA
Detector track 2
Detection threshold ………………………………….
500 mA
Cable communication
ZIMO CAN bus 1………………..
(ZIMO CAN socket, front and back) …………….
125 kBd
………………………..
Prepared for …………………………………………
512 kBd
ZIMO CAN bus 2 ………………..
(with special 8-conducter cable on: XNET socket) ………
125 kBd
………..………………
Depending on protocol, up to………………………………….
512 kBd
XNET …………………………………………………………………………………………..
62,5 kBd
XN2 ………………………………..
(2. XNET or OPEN DCC Bus) not yet in use......................... ...
512 kBd
Loconet ……………………………
only hardware installed at this time ……………….....………....
16.6 kBd
USB device (client) interface...
…………………………………………………………..
1 Mbit/s
USB 2.0 host interface ………
(for USB stick and future applications) ............…………..
12 Mbit/s
LAN ………………………………..
(ethernet, also for W-LAN routers) ............................…...
10 Mbit/s
Radio communication
Mi-Wi network (derivative of ZigBee stds., 2.4GHz) approx. …
20 kbit/s
Internal memory:
DRAM und SRAM (random access memory)
64 MB
NAND Flash (pictures, databanks, switch panels, sound files..)
4 GB
DC input: external power supply with galvanically insulated DC output……………
20 - 35 V
applicable maximum current……………………………………………………………………………..
3 –30 A
for small layout operations (@ 3A track voltage)………………….………………………………….....
80 Watt
for full capacity (up to 25 A total track current)….…………..............................…………….
600 Watt
ATTENTION:
Classic TRANSFORMERS of any kind are NOT ALLOWED with an MX10 (neither those with
rectifiers); ZIMO Trafos (although they were formerly used with the MX1) or old model railroad
transformers are NOT ALLOWED either.
MX10 backside

Page 6 OPERATING MANUAL COMMAND STATION MX10
3. Typical system configurations
The MX10 is ZIMO’s central unit for a digital multi-train system or, in other words the "digital center", or
according to the NMRA - terminology, the digital “command station".
The command station provides a stabilised, short circuit protected voltage to the tracks (from each of
the two rail outputs) along with the control information for vehicles and accessories, in either the stand-
ard DCC* data format (see below) and/or in the MOTOROLA** data format (to which the factory-
installed decoder in Märklin vehicles react).
*) DCC (Digital Command Control): originally standardized by the NMRA (National Model Railroad Association) and
since 2010 further specified by the European manufacturers association VHDM ("Rail Community"), is used by digital
systems and decoders from "Digital plus" (Lenz), ROCO-digital, LGB multi-train (Massoth), Digitrax, ESU, Uhlenbrock
and others.
**) MOTOROLAis not yet implemented.
The MX10 is connected with other ZIMO devices by means of CAN bus connectors and cables: the in-
put devices - known as cabs (MX2, MX31, MX32), the stationary modules ("StEin modules) or the ac-
cessory and track section modules (MX7, MX8 and MX9).
The usual minimum configuration of a ZIMO digital control system with MX10 looks like this:
The MX32 and MX32FU (in tethered mode) can be connected to either the rear or front MX10 CAN
bus socket. Since these two CAN bus sockets are linked internally and thus interconnect to the ZIMO
MX10 CAN 1, cabs can be plugged into the rear and front simultaneously. For example: the rear sock-
et can be used for permanently connected MX32’s (or bus wire) while the front socket is used to
charge the MX32FU battery when needed.
A more elaborate layout configuration with solely “new” products is shown below:
MX32FU radio cabs can be operated in tethered or radio mode. When operated with the current
MX10 command station –in contrast to earlier ZIMO systems –NO additional radio module is re-
quired, as this is already installed in the command station.
or
NOTE: Arrangements without cabs are also possible in case of computer control only or operat-
ing through virtual input devices (mobile phones, tablets... via USB, LAN).

OPERATING MANUAL COMMAND STATION MX10 Page 7

Page 8 OPERATING MANUAL COMMAND STATION MX10
Details on connections of “old” and “new” ZIMO cabs as well
as control units of other manufacturers
Various input devices can be connected to the ZIMO system with an MX10 command station for oper-
ating and configuring vehicles and accessories:
- ZIMO CAN bus:
All generation ZIMO cabs such as the MX2, MX21, MX31, MX32, ZIMO radio modules MXFU (to
connect with the “old” radio cabs MX21FU and MX31FU). Only the current generation MX32 cabs
can take full advantage of all MX10 functions.
The Roco central station Z21 can also be connected to the ZIMO CAN bus to take advantage of the
Roco mobile phone and tablet apps.
- “Mi-Wi”, the MX10’s integrated radio module:
The new generation ZIMO MX32FU radio cabs also contain a radio processor and can communicate
with the MX10.
- XNET:
The “red” Roco Lokmaus, Massoth DiMAX Navigator and other compatible devices.
The use of other products will be tested only as needed.
- WLAN (i.e. a router connected to the LAN socket of the MX10):
Wi-Fi enabled mobile phones and tablet PC’s (and of course other mobile Wi-Fi devices).
- Other bus systems such as Loconet and S88:
the hardware of these interfaces is installed but not functional with the initial MX10 firmware. Any fu-
ture implementation depends on demand.
- USB Client interface:
Virtual (computer) cabs within switch panels and decoder configuration programs such as STP,
ESTWGJ, Train Controller, ADaPT etc.
- Sniffer input:
track outputs of a third-party system can be connected here to reproduce their data at the MX10
outputs.
The ZIMO CAN bus:
The MX10 has two 8-pin connectors for the CAN bus, one on the front and one on the back of the de-
vice. The six middle pins of these two connectors form the so-called ZIMO CAN bus and are com-
pletely identical. Since these are connected together internally, all devices connected to these CAN
sockets with 6-pin CAN bus cables are connected in parallel. It does not matter which of these sock-
ets the cabs, MX8 accessory modules, MX9 track section modules or other devices are connected to.
The distinction between these two sockets simply refers to the two outer pins:
The socket on the back is equipped with additional lines for the control-signal synchronization of StEin
modules and the front socket is used, together with an 8-pin CAN cable, as a “Sniffer input”.
Each cab (MX32, MX31, MX2, MX21...) also has two identical 6-pin sockets, which allow the power
and data lines to be looped from cab to cab. A 6-conductor bus wire can be installed alternatively with
6-pin distributors and sockets, so more cabs can be connected as needed.
The “CAN2“ – Bus:
The “XNET” socket also contains the connections for “CAN2”, a second CAN bus, in addition to the
XNET itself. This is needed when the new system devices (MX10-MX32) are used together with the
“old” MX31 cabs and/or accessory and track section modules MX8 and MX9.
The following wiring must be observed when “old” cabs such as the MX31, MX21, MX2 or radio mod-
ules MXFU are used together with the new MX32 or MX32FU cabs:
- the “old” devices (MX31…) are connected with a “normal” CAN bus cable to either the front or the
rear ZIMO CAN bus socket.
- the “new” devices (MX32, MX32FU) must be connected to the front XNET socket (!) with the spe-
cial cable “8POLAxM” (8-pin plug on the MX10 end and 6-pin plug on the cab end). This special
cable connects the “CAN2” (=second CAN bus) XNET socket pins with the CAN pins of the cab.
Because a more extensive and faster protocol is used
between the command station MX10 and the
MX32/MX32FU (which the older devices do not under-
stand), both CAN buses are needed simultaneously.
As soon as a device operating in the old CAN protocol
is connected to the system bus, the MX10 automatical-
ly switches over to the so-called “MX1 mode”. This
mode is restricted to no RailCom, 12 functions etc…
In order to retain all the new
functions of the MX32, it is
necessary to connect it to
the ZIMO CAN2 (XNET)
socket. There are no
restrictions in wireless
operation.
The same type of wiring is to be used when connecting MX8 and/or MX9 modules. These modules
are connected like the older cabs (MX31…) to the “normal” ZIMO CAN bus socket, while the MX32 is
connected to the XNET socket as described above.
Radio communication via “Mi-Wi“:
The MX10 and the ZIMO radio cabs MX32FU are equipped with a “Mi-Wi” radio module from Micro-
chip (who also provides the “PIC” microcontroller).
The "Mi-Wi" protocol is based on the "ZigBee" standard in the 2.4 GHz band, but offers higher effi-
ciency and lower resource consumption. Compared to Bluetooth, "Mi-Wi" (as well as ZigBee) provides
a greater range of up to several 100 m and unlike W-LAN (Wi-Fi) offers an integrated network capabil-
ity, as well as a higher data transfer when compared to the 344 MHz technology (of the "old" ZIMO
cabs), and is approved worldwide.
Potential disadvantages of the 2.4 GHz technology with respect to the penetration ability inside of
buildings compared to 344 MHz can be offset if necessary by the network capability on the one hand,
or by using 900 MHz - "Mi-Wi' modules on the other hand (instead of 2.4 GHz).
MX31
MX32

OPERATING MANUAL COMMAND STATION MX10 Page 9
The Massoth DiMAX Navigator on the MX10:
DiMAX Navigator cabs can only be used in radio mode, with the DiMAX radio module connected to
the MX10 XNET socket (i.e.: „Design for X-Press-Net & LocoNet, MS813102").
The DiMAX receiver module has three sockets. The center socket with the label "XpressNet" is con-
nected with a 4-pole XpressNet cable or with a 6-pole ZIMO CAN bus cable to the MX10 command
station’s "XNET" socket. When using a conventional ZIMO CAN bus cable, the outer two cores remain
unused.
There is no handover/takeover procedure with Massoth devices as there is with ZIMO. Even so, the
ZIMO MX32 indicates in the upper bar that a third-party device affects the active address via Xpress-
Net with the message "XNET-control". The speed or function changes coming from the DiMAX are
also displayed on the MX32. The MX32 can directly control the address currently active on the DiMAX
without takeover procedure.
The ROCO multiMAUS on the MX10:
Roco multMAUS throttles are connected to the XNET socket on MX10’s front with a “normal” 6-pole
CAN bus cable. If MX32(FU) are used at the same time, they can be connected to the ZIMO CAN
socket or operated in radio mode. The functionality of the MX32 will not change, unless MX8 and/or
MX9 modules are connected to the MX10 as well. In this case, the MX32 operates with the “old” MX1
CAN protocol, which is limited to 12 functions and RailCom is disabled.
If MX8 and/or MX9 modules are used in this constellation and the MX32’s should retain all their func-
tions, an adapter (splitter) for the X-Net socket must be used that makes the CAN2 accessible. Such
This also applies to all other X-Net operated throttles that make the CAN2 connector inaccessible.

Page 10 OPERATING MANUAL COMMAND STATION MX10
ZIMO CAN
Ribbon cable
(16 poles)
12V M 30V
Jumpers on „CAN-1“
Jumpers on „CAN-2“
4. The MX10AVP Connection board
This connection board is available as accessory and not included in the MX10 starter sets.
The “MX10 Connection board” is a dis-
tributor board with convenient sockets
and terminals. The board itself has no
active electronic components.
As the MX10 has many connections in a
tight place in front and rear, some con-
nections are pooled: i.a. “CAN-2” and
“XNet”. Some connections are pin head-
ers in order to save space.
The “MX10 Connection board” useful in
giving you enough connections to plug
all possible “old” and “new” ZIMO devic-
es by keeping an overview.
The picture on the right shows the typi-
cal wiring possible between the MX10
and the MX10 Connection board. The
cables and plugs are supplied with the
MX10 Connection board.
Not all connections may be needed, de-
pending on the use.
First example:
The simplest use for the MX10 Connection board is the one as a distribution board for the ZIMO CAN
bus. In total there are 5 CAN bus sockets available: the MX10 holds two (one front, one rear), the
MX10AVP Connection board holds four sockets. This is useful to “daisy chain” the devices.
The jumpers situated next to the sockets marked “CAN-1/2” of the MX10AVP Connection board must
be plugged into the position “CAN-1”. All four CAN sockets are in parallel.
As long as only devices from the “new” ZIMO generation such as the MX32 are in use, it is irrelevant if
the cables between the MX10 and the MX10AVP Connection board show 6- or 8-cores. For the rea-
son of standardization, we recommend to use 8-pole CAN bus cables. We recommend 6-pole cables
to connect the cabs, as these cables are more flexible.
Second example:
In case of using “old” (MX31, MX31FU) and “new” (MX32, MX32FU) cabs simultaneously, both the old
and the new CAN bus protocol have to be used at the same time, so that the new cabs can operate
with their full functions. The “old” cabs have to be connected to CAN-1, the “new” cabs to CAN-2.
The jumpers next to the
sockets hosting “new”
cabs must be placed in
position CAN-2.
The advantage in using
the MX10 Connection
board: the cabs receive
the full CAN power sup-
ply of 30 V when con-
nected with the “special”
CAN bus cable
(8POLA1M). Specially
advantageous when
loading the batteries of
MX32FU.
ZIMO CAN XNET

OPERATING MANUAL COMMAND STATION MX10 Page 11
Jumpers on „Booster”
Jumpers on “CAN-1”
Jumpers on „Booster”
Jumpers on “CAN-2”
Third example:
In this case, only ZIMO devices from the “new” generation are in use: MX32 cabs and Stationary
module “StEin”, all using the CAN-1 socket. Stationary modules StEin (as well as MX10 in booster
mode) do also use timing information for the DCC track signal on top of the CAN data bus. In such
case, it is necessary to connect the devices with 8-pole cables in the following manner:
- from rear the side of the MX10 to the socket on MX10AVP Connection board and
- from the MX10AVP Connection board to the Stationary module StEin.
In order to lead the signal trough the MX10AVP Connection board, the (four possible) jumpers have to
be set in position “Booster”.
In any case, all devices can forward the CAN bus as all of them have more than one socket. MX32
can also be connected on StEin, as these pass all 8 cores of the CAN bus (although only using six of
them).
Fourth example:
In this last example, the “old” and “new” generation of ZIMO cabs and modules are used together. As
already described, both CAN buses are needed:
- “old” cabs (till MX31), all accessory- and track section modules (MX8, MX9 with valid ad-
dresses 801 –863 and 901 –963) are connected to CAN-1 and
- “new” cabs (MX32 …) as well as Stationary modules StEin are connected to CAN-2.
The jumpers next to the sockets hosting MX32 cabs and Stationary modules StEin have to be set in
position “CAN-2”.

Page 12 OPERATING MANUAL COMMAND STATION MX10
Command station MX10
MX10AVP Connection
board
Roco multiMaus (Xpress-
Net device)
Further applications:
The MX10 AVP Connection board may be used at the same time or instead of the abovementioned
CAN bus applications as:
- connection to XpressNet devices such as the Roco Lokmaus or multiMaus as well as the
DiMax Navigator (radio version). The MX10 Command station operates two separate
XpressNets which are combined on one “XNET” socket in the front of the device. Two sepa-
rate sockets (“XNET-1” and “XNET-2”) can be found on the MX10AVP Connection board.
- external easy to use circuitry instead of the 2x 8-pin plugs on MX10’s back side. MX10AVP
offers eight inputs and eight outputs on terminal strips.
Connection of a Roco multiMaus on one of two XNET sockets of a MX10AVP Connection board.
Blank page, space for still more applications

OPERATING MANUAL COMMAND STATION MX10 Page 13
5. Layout track, programming track, AOS in/out’s
The command station MX10 has two track connections:
the output “Schiene 1“ (track 1), to which normally the “main track” is connected, that is the ac-
tual layout.
the output “Schiene 2“ (track 2), can be used for a second main track, an accessory power bus
(with separately adjustable voltage, current limit, etc.), a programming track (for programming de-
coder addresses and CV’s in service mode) or an update track (to update decoder software and
sound upload).
The "track 2" is fully drivable with identical DCC signals applied to as on the main line, except when
a programming operation is currently running in service mode,. If "track 2" is used as programming
track being part of the main layout track, it must be totally insulated from the main track. Please pay
attention that polarity is the same on both tracks (n, p terminals), as the gaps will be bridged by the
wheels when driving on/off the programming track.
The track output voltages are are
fully-stabilized and separately ad-
justable over a wide range (each
from 10 to 24 V, see chapter "Appli-
cation ...").
The current limits (1 –12A on track
1 and 1 –8A on track 2) and the
shut-off times (0.1 –5 sec., for
bridging brief short circuits at cross-
ing frogs etc.) are the most im-
portant settings: the so-called “main
settings”.
A number of safeguards are incorporated into the MX10 to prevent damage to the track and vehicles
during short circuits, despite the large driving currents available. These safeguards are especially
important when smaller scales (N, TT) are in use:
- The design of the high-frequency switching regulator with a low output capacitance ensures that no
large power surges occur from discharging capacitors during short circuits.
- A special spark suppression circuit (adjustable in three steps) recognizes arising electric arcs and
cuts them off by internally bridging the output terminals.
- Through a special "adaptive overcurrent detection" setting, the power switch-off can be defined to
take place when a sudden rise in current is detected, even before the actual overcurrent threshold
has been reached.
Voltage and maximum current on the programming track in SERVICE MODE (SERV PROG):
Entering the service mode with the default setting, usually from a cab with the E-Key + MN-Key, sets
the program track automatically to
11 V and 0.3 A (maximum current at first) or 0.1 A (maximum current after 100 msec).
This corresponds to the published standards of the Rail Community (Association of DCC product man-
ufacturers).
The idea behind the strict current limitation during programming is to avoid damage to vehicles and
electronics even if, i.e. the decoder is wired incorrectly. However, not all vehicles are built to get by with
as little power, as there may be energy storage capacitors that need to be charged, or consumers that
are not connected to the decoder and therefore cannot be turned off.
To overcome these shortfalls, it is possible to modify these standard-compliant voltage and current set-
tings for the programming track, by changing the settings in
MX10 Main Menu VOLT & AMP DETAIL SERV: track voltage, Max current
A WARNING will be shown on the cab display during SERV PROG if the SERV PROG settings differ
from the ones above!
Using an external programming track relays:
If this track output is intended to be used alternatively as section of a layout and as programming track,
the corresponding wires can be exchanged manually or more comfortably switched between the two
with the help of a relay.
The relay is connected –as shown in the drawing below–to the “5V” pin and “out-6” pin of the16-pin
plug. The relay should have two sets of switch-over contacts and be loadable with 5 A (even better 10
A).
The relay is controlled automatically by the MX10 in such a way that the track output 2 is connected
with the programming track as long as a cab is set to SERV PROG, otherwise it is connected with the
layout.
NOTE: This is the standard
application of the “out-6” pin.
However, this pin can also be
reconfigured (see “DCC
SERV PROG settings) and
thus would no longer be
available for controlling a pro-
gramming relay.

Page 14 OPERATING MANUAL COMMAND STATION MX10
The MX10 as a decoder update module (software planned for 2017):
One of the basic tasks of a modern digital command station is to support the uploading of new software
versions and sound projects to the decoder. Separate update devices or sound programmers are no
longer needed - at least for decoders of the system manufacturer, in this case ZIMO (but are of course
still available in the form of the MXULFA, if no MX10 is at hand).
Uploading new software and sound projects to the decoder can be carried out directly from the
plugged-in USB stick or a computer via the USB interface. But the MX10 can also keep a large number
of decoder update collection files and sound projects in its own flash memory and use them when
needed.
Booster-Solutions:
Thanks to the high track current of the MX10 (up to 12A + 8A), there is seldom a need for additional
boosters except maybe in very large layouts or large scales. In such situations, preference should be
given to an additional MX10, which is synchronized with the "Master MX10" (software planned for
2017).
The use of third-party boosters is possible but less effective because communication with such devices
is only possible using the outdated NMRA "Control Bus".
Connecting external emergency stop buttons:
The AOS inputs (1…8) on the 16-pin socket can be used for different tasks, especially for the “AOS”
(Automated Operating Sequences).
The AOS inputs “in-5” to “in-8” are intended for emergency stop buttons (as long as their assignment is
not changed): There are a total of 8 options available; the most often opted feature is probably to trig-
ger a BCS (Broadcast stop) on "track 1"; such an emergency stop button must be connected to "in-7"
and pulled low to be activated (system ground = ground pin available on 16-pin plug).
If a broadcast stop is issued, the corresponding information is
displayed on the command station and all connected (teth-
ered or radio) cabs. The broadcast stops can be cancelled
(with “ON”) from the same screen.
The illustration below shows all possible emergency stop button connections, with which a
BCS (Broadcast stop) as emergency *) or as breaking to speed step 0 *) can be triggered as
well as track power OFF for either “track 1” or “track 2”.
*) BCS (broadcast stop) “as emergency” means immediate stopping without braking distance (depending on
motor and gearbox design with very little or no run-out, which could lead to derailments), and “breaking to
speed step 0” means stopping according to the set deceleration rate in CV #4.
MX10 display
MX32 display
NOTE: in early software versions where this ABA input feature is not yet available, the line
"Boo UE" at the ZIMO CAN socket can be used for the external emergency stop button.

OPERATING MANUAL COMMAND STATION MX10 Page 15
6. DCC format, feedback, database
DCC and MOTOROLA are part of the standard MX10 configuration from the outset. Hardware and
software however are open to accept other protocols, in particular mfx (with RDS feedback) and Selec-
trix, as planned for the future. Also conceivable would be an extension in the direction of new and more
efficient methods of data communication by rail.
RailCom® and ZIMO Loco number identification:
Within the ZIMO system (of the MX10 / MX32 / StEin generation) “bidirectional communication” accord-
ing to “RailCom®” is an integral part of all relevant components.
The MX10 is equipped with two “Precision-Global-RailCom®-Detectors; a separate detector for
each track output.
"Global" is a notion from the RailCom® standard (as from NMRA) and indicates the reception of Rail-
Com® messages that are independent of the current vehicle position (= the track section), such as
feedback of speed, power consumption, alarms, turnout positions, read-out CV values, etc. *).
"Precision" means that the reception and evaluation of RailCom® messages is not carried out accord-
ing to the standardized threshold values of simple detectors, but that the RailCom® signal is first digit-
ized and subsequently analyzed to decipher even heavily weakened and garbled messages. This
makes the detectors resistant to influences that can occur in the practical application of a large layout,
for example the removal of large parts of RailCom® feedback current caused by illuminated coaches..
*) "Local detectors", however, deal with the identification of vehicles in individual track sections; this task is performed
by the "StEin" modules (= stationary modules) within the ZIMO system. However, these modules don’t just operate as
simple local detectors, but also read global messages (and forward them to the MX10 command station), because the
quality of reception in large layouts can often be better in individual track-sections than at the command station’s loca-
tion.
The ZIMO MX10 command station also reads the "loco number pulses" of ZIMO decoders, which are
used in addition to RailCom® as an acknowledgment for the reception of DCC packages. This works
also with decoders from before 2005, when RailCom® was not yet existing and the ZIMO loco number
identification was the only available decoder feedback system.
RailCom® is a registered trademark from Lenz Elektronik GmbH
The organisation of data transmission via the layout tracks:
In addition to supplying the layout with power, a digital command station must above all accept the ve-
hicle and accessory information from input devices (cabs, computer…) and send that information along
to the decoders in an efficient and reliable manner with minimum time-delay.
In the course of this we always have to take the interference-prone data channel into account, as it ex-
ists in the world of model railroads due to contact interruptions between rails and vehicles.
Therefore, a sophisticated priority scheme is used that determines how the available transmission time
is allocated among the different data packets. Distinction is made between the following priority levels;
higher priority (0, 1, 2...) means more frequent transmission:
0. Protocol requirements (request-for-service slots, time sync for decoders and more).
1. Changes in file content from cab, computer etc. (i.e. new speed settings, functions…)
2. Data for active addresses in the foreground of a cab,
3. Data for addresses of “secondary objects” tied to foreground addresses, i.e. consists,
4. Data for addresses of computer cabs (STP, ESTWGJ, TrainController, etc.),
5. Data for addresses in the LoR (Loco Recall) of cabs or favorites list in a computer,
6. Data for addresses in the system’s databank (that don’t fall into one of the higher priorities),
7. Scan cycle to find unregistered addresses.
ATTENTION: NO RailCom® messages will be received (neither on track-1 nor track-2) during
programming in SERV PROG mode (with track-2 as the programming track).

Page 16 OPERATING MANUAL COMMAND STATION MX10
7. Firmware update of the MX10 via USB stick
The current software version:
Is available as a free download from the ZIMO website:
www.zimo.at "Update & Sound" "Update System (MX10, MX32 ...)"
A so-called container software file is used for updating the MX10 and MX32 (FU) since the introduction of
software version 01.17. This container file contains all necessary files for a software update of both devic-
es (MX10 and MX32). So you need to download, unzip and store only one single file to the USB flash
drive.
The currently loaded version can be viewed on the MX10 menu (M button 2) under the heading "MX10
Config" and from there to "Version Info". The current software version of the radio processor and XILINX
can also be found here.
The proper USB flash drive:
As shown on the left, the flash drive must be formatted to
FAT32 for the MX10 software update. The cluster size (al-
location unit size) must be set to 4096 Bytes (= 4 kB).
Most flash drives bought today are already in this format.
If an older or a differently formatted stick is used, the stick
must first be reformatted, whereby the box “Quick Format”
remains unchecked.
With the proper flash drive at hand, you may transfer the
MX10 software. It is important that the data file(s) for the
MX10 are copied to the root memory of the usb. stick, as
the MX10 is not capable of reading folders. The update
.zip file (available free from zimo.at) must therefore be un-
zipped before it is loaded into the USB flash drive.
The flash drive must not be dedicated to ZIMO updates on-
ly as other “unknown” files do not interfere with the update
process.
These properties also apply to the MX32 (FU) update!
The update procedure:
The MX10 firmware update is done during normal operation with the help of a USB flash drive. If a USB
flash drive with useful MX10 data files is inserted, ALL MX10 outputs will be disabled. All devices,
modules and decoders powered by the MX10 are therefore immediately turned off. In order to prevent
damage to vehicles by abrupt stops, it is recommended to bring all vehicles to a standstill and prepare the
entire layout for the power shut-down the MX10 will initiate, before you connect the USB flash drive.
With the normal BLUE operating screen,
plug the flash drive containing the appropriate (USB stick)
software into the USB socket of the MX10.
The available data on the usb. stick is automatically read by the MX10 and displayed in a
TURQUOIS update list:
Currently available update options on the flash drive are
shown in “bold” type. Lines not in bold represent update
files that could also be used by the MX10 but are NOT
PRESENT ON THIS USB flash drive.
The “MX10 Update (all)” contains:
- MX10 main processor update
- Radio processor update
- XILINX update
- Languages (DE, E)
- CV list
- Decoder descriptions
- MX10 sounds (e.i. error sound)
Scroll with the rotary knob (if several files are shown): Set cursor () to “MX10 Update (all)”
Press the rotary knob The display color changes
to RED, and the version number and creation date of the
MX10 update is shown.
Press the rotary knob (again) to start software
update. After completion (about 10 seconds), the display
prompts for the next step.
After each update, the MX10 has to be unplugged and rebooted after a waiting period of at
least 1 minute to reliably restart the processor and all components affected by the update
with the new software.
If no usable file is found on the usb. stick due i.e. to damaged data, or an empty stick, the note (also in
TURQUOIS):
“NO ZIMO FILES FOUND”
is displayed instead of the list. In this case, the flash drive must be removed and checked for an exist-
ing (or correct) update file. After removing the USB flash drive, the MX10 shows the normal BLUE
screen again (without rebooting).
Update
NOTE: Turning the knob instead of pressing it or pressing another button cancels the updated pro-
cedure immediately and returns to the normal operating mode. In such a case, remove and recon-
nect the USB flash drive.
ATTENTION: Windows 7 or newer cannot format USB
flash drives that are larger than 32GB to FAT32!

OPERATING MANUAL COMMAND STATION MX10 Page 17
DCC signal statistics (number of
sent command packets per sec);
xx DCC = DCC packets only
xx MM = MM packets only .
.
RailCom statistics (number
of received messages as
answers to DCC commands).
CAN bus statistics (number of CAN packets);
CAN xxx E = number of CAN packets per sec
CAN xxx E yy% = as above with percentage error
Temperature measured on the circuit board.
8. Operation and controls
After connecting and switching on the power supply, the MX10 starts automatically and completes the
start-up sequence that takes a few seconds.
The RED start-up (boot) screen shows various information of
the boot sequence, among other things: start-up current and
start-up time. Both are adjustable as may be needed when en-
ergy storages are in use in the locos.
In case LAN is connected to the MX10 and a valid IP-address
is set, “LAN link active” is shown during the boot period. If the
USB-port is connected, the screen shows “V Com link active”.
In case both connections were made, the USB port will turn
itself off.
At the end of the boot sequence, the normal operating screen
appears in BLUE. The display shows the actual voltage and
current values of the two track outputs as well as some com-
munications data (DCC, CAN...). The prominent number
shown in the middle of the display is the current power con-
sumption of "track-1" (Schiene-1).
8.1. The Normal MX10 Operating Screen
AOS In/Outputs, displays the status
of all 14 rear connections.
Voltage and current from
the power supply unit at the
input "DC in", which
supplies the MX10 as well
as the entire the layout
(“primary power”).
Voltage and current at output
“track-1“(Schiene-1
includes DC output S1).
Voltage and current at output
“track-2“(Schiene-2 includes DC output S2).
*) The current "DC-in" input (from the power supply unit) value shown is not a measured value, but rather calcu-
lated from the output currents (track outputs 1, 2 as well as the 12 V and 30 V outputs and the internal con-
sumption of the unit), while taking into account the efficiency of the voltage converters.
The primary purpose is to estimate whether the power supply has sufficient power reserves.
**) Sporadic flicker of the letter "E" indicates single errors on the CAN bus, such as those that may occur when
connecting / disconnecting a device. These typically cause no problems. If there are more than 10 errors per
second the screen is switched to "E" with a percentage value of erroneously arriving packets (compared to
the total number of packets that stands behind "C"); an error rate of several % may be an indication of a bad
CAN bus transmission situation (i.e. caused by long, poorly terminated cables).
LEAVING this “normal screen” is only possible for the following events:
(USB stick) Plug in USB Stick (containing files for the MX10 update and / or decoder update files and
sound files in the root directory) TURQUOIS display: with USB stick options.
(See chapter 7, 8.8 & 8.9)
Turn knob quickly back and forth Display YELLOW: VOLT & AMP setting (chap. 8.2).
Press/hold the knob for 2 sec. Display RED: broadcast stop (BCS) and power OFF (chap. 8.3).
Press button 3()Display GREEN:“BaseCab“, driving and programming (chap. 8.4., …, 8.7)
Press button 2(Menu)Display GRAY:MX10 MENU (chap. 8.8).
Press button 1 () Display GRAY: AOS (Automated Operating Sequences)
Overcurrent on the track Display RED:OVC on track-1 or -2 (one track remains operational). (8.3)
Under-voltage from the power supply Display RED: Power supply inadequate.
For an overview on:
MENU see chapter 8.8

Page 18 OPERATING MANUAL COMMAND STATION MX10
8.2. Voltage & Current Settings –VOLT & AMPERE MAIN
Starting point: the normal BLUE operating screen, quickly turn
the rotary knob left/right to enter the YELLOW voltage and cur-
rent adjustment screen.
VOLT & AMPERE MAIN (Main settings)
APPLICATION:
Use the rotary knob to scroll: move the cursor () to the value to be changed.
Press the rotary knob Selected () number is framed, ready for changes.
Turn the rotary knob to change the value of the selected number,
in case of a voltage value: immediate effect on the relevant track output
in case of a current limit: shows threshold value, measured value reappears later.
Press the rotary knob to save the new value, continue scrolling with the rotary knob.
RETURN to normal operation or the menu:
Press button 3() Return to the normal BLUE operating screen
Move cursor ()to “EXIT“ and press the rotary knob
Timeout after 3 seconds of inactivity Back to the normal screen
or
Press button 2(MENU)to open menu screen GRAY
CONTINUE to the Detail Settings:
Press button 1() Continue to the Voltage & Ampere –detail screen YELLOW
–VOLT & AMPERE DETAIL
VOLT & AMPERE DETAIL (Detail settings)
This YELLOW screen is also accessible via the menu line
VOLT & AMPERE DETAIL (chap. 8.8)
The “Detail settings” offer a variety of parameters
that go beyond the “Main settings” for optimum
adaptation to individual needs.
Each parameter is shown separately and adjusted
individually for track-1 and track-2 outputs, and is
identified in the display as 1: and 2:
Lines SERV: are available for address and CV
programming in service mode (i.e. track-2 as pro-
gramming track) as well as the lines UPD: for up-
date and sound upload processes.
The default values can remain unchanged in many
applications, especially when the potential power
capacity (output current) of the device is not fully
exploited.
APPLICATION:
Use the rotary knob to scroll: move the cursor () to the value to be changed.
Only two or three lines are visible simultaneously, scroll up/down for more content.
The entire parameter list appears twice (for track 1 and track 2)
Press the rotary knob Selected () number is framed, ready for changes.
Use the rotary rotary knob to change the value of the framed number.
Press button 3() (instead of rotary knob) reverses erroneous setting.
Press the rotary knob to save the new value.
RETURN to normal operation:
Press button 3() Returns to the normal BLUE operating screen
Current: OVC threshold
Track voltage for track 1 top line;
track 2 bottom line
NOTE: the possible adjustments on the “main settings”
page correspond to the “Voltage” and “SHORT thresh-
old” in the “detail settings” (see description below). This
screen can also be opened via the menu line “VOLT &
AMPERE MAIN” (see chapter 8.8).
NOTE: during programming operations at “track 2”
(Schiene-2) in Service Mode, the values in lines “2”
change to the values defined for “SERV”; the same ap-
plies to decoder update operations. This may result in a
track voltage increase or decrease.

OPERATING MANUAL COMMAND STATION MX10 Page 19
The meaning of the parameters in the “VOLT & AMPERE Detail Settings“,
for 1: (track-1) and 2: (track-2)
Track voltage Range 10 V - 24 V Default 16 V
The target output voltage for track-1 or track-2. This voltage is maintained within 1 V; if this is not
possible, the track power is turned off “UNV” (UNnder Voltage, usually due to a weak power supply).
Start-up current Range 0.5 A - 16 A Default is set equal to OVC threshold
When powering up the track (system start up or after a short circuit), the “start up current” applied
during the “start up time” (see below) is higher than the one defined at the “overcurrent threshold”,
which allows the back-up capacitors in the locomotives on the layout to be charged. The inrush cur-
rent required for this is in the range of 100 –300 mA for vehicles fitted with capacitors according to
standards, for non-compliant vehicles the current may often be much higher.
Start-up time Range 0 sec - 60 sec Default 0 sec
The “start up current” (see above) is applied to the track output for the time specified here when pow-
ering up the track. This limitation can force a reduction of the track output voltage (which rises slowli-
er); the shutdown due to low voltage is disabled for this reason.
OVC threshold Range 1 A - 12 A Default 5 A (Track-1), 3 A (Track-2)
OVC = Overcurrent. The current at the track outputs shall be limited to the “OVC threshold”defined
here (provided the adaptive threshold current does not result in an even lower limit, see “OVC adap-
tive”); the output shall be switched off after the “OVC turn off time”is reached (see below). The only
exception is the “Tolerance current” (see parameter below), which may be higher during the “Toler-
ance time”.
OVC Turn-off time Range 0.1 sec - 5 sec Default 0.2 sec
When the current threshold is exceeded (either relatively acc. to “OVC adaptive”or absolutely speci-
fied in the “OVC threshold”), the track output is first limited to the constant current threshold, leading
to a forced reduction of the track voltage. After the “OVC turn-off time”defined here has elapsed –
and the overcurrent condition persists –the track output is turned off. The turn-off time permits i.a.,
that momentary shorts due to wrongly polarized frogs are being ignored.
OVC Adaptive Range 0.1 A - 6 A Default 2 A
Whereas the uppermost current on the outputs is defined by the “OVC threshold”, the “OVC adaptive”
defines how big sudden increases in the current consumption may be. Huge increases shall lead to a
shutdown, independent from the absolute limit.
OVC Adapt. time Range 1 sec –10 sec (at least 5 x the turn-off time) Default 2 sec
The extent of the “OVC Adapt.” current step is the difference between the higher curr. and the aver-
age current in the time before. The average value is created during the “OVC Adaptive time”. This
setting should not be changed.
OVC Tolerance current Range 0 A - 6 A Default 0 A
The “OVC threshold”(max.allowable track power, see above) may be exceeded by the defined “OVC
tolerance current” for the specified “OVC tolerance time”(below). The shutdown occurs thereafter by
applying the turn-off time (as described above).
OVC Tolerance time Range 0 sec - 60 sec Default 0 sec
See description above (OVC Tolerance current).
Spark suppression Range OFF - LEV 1 –LEV2 Default LEV 2
Special electronic circuitry in the track output end stages ensure that no big sparks can occur in a
short circuit situation (i.e. between wheel and rail when driving over frogs or during derailments), de-
spite the high output currents.
The meaning of the parameters in the “VOLT & AMPERE Detail Settings“,
for PROG: (track-2 as programming track)
SERV: Track power Range 10 V - 24 V Default 12 V
Target output voltage for track-2 during a programming procedure in Service Mode (SERV PROG);
In driving mode, the operating voltage setting for track-2 (“2:”) is valid.
SERV: OVC Threshold Range 400 mA, 1 A - 8 A Default 400 mA
OVC = Overcurrent. The current at the track output (track-2 in Service Mode) shall be limited to the
“OVC threshold”defined here.
The “400 mA”setting essentially corresponds to the relevant standard of the “Rail Community”
(VHDM) RCN-216: The power consumption is limited to this relatively low value, and a subsequent
check is made after 150 msec to see whether the current has fallen to 100 mA. The programming
procedure will continue only if this condition is met, otherwise the track power is turned off. This is a
security measure for traditional programming tracks, to prevent overheating and subsequent dam-
age caused by wrong decoder connections.
When set to 1A…: no specific time-dependent limits apply; the current is limited to 300 mA to damp-
en the acknowledgment pulse (so that the engine does not “jump”) while waiting for a decoder ac-
knowledgment.
SERV: OVC Turn-off time Range 0.1 sec - 5 sec Default 0.1 sec
See track-1 and track-2 description for details. This value is very short by default because there are
normally no turnouts (with possible shorts caused by a frog) in a programming track.
Upd: Track voltage Range 10 V - 24 V Default 12 V
Target voltage at output track-2 during an update or sound upload procedure; in driving mode the
operating voltage setting for track-2 ("2:“) is valid.
Upd: OVC Threshold Range 1 A - 8 A Default 3 A
OVC = Overcurrent. The current at the track output shall be limited to the “OVC threshold”defined
here.
Upd: OVC Turn-off time Range 0.1 sec - 5 sec Default 0.1 sec
See track-1 and track-2 description for operational details. This value is very short by default be-
cause there are normally no turnouts (with possible shorts caused by a frog) in a programming track.
NOTE: concerning acknowledgment detection in SERV PROG:
The MX10 automatically checks whether the quiescent current of the vehicle on the programming
track after a program or read-out command drops
- within a specific time (1 sec)
- below a specific value (100 mA below the value set in “SERV: OVC Threshold“,
i.e. 300 mA, if OVC Threshold is set by default to 400 mA),
- no great fluctuations are present (less than 10 % of the quiescent current, provided
the quiescent current itself is higher than 10 mA).
If this quiescent current condition is not met, a corresponding error message is displayed in the
MX32 cab display such as “Vehicle idle current to high (xxx mA)”.

Page 20 OPERATING MANUAL COMMAND STATION MX10
8.3. Broadcast stop (BCS, BCSe), Track power off (OFF),
Overcurrent (OVC), Low voltage (UNV) –STOP & OFF
Starting point: the normal BLUE operating screen
Status of track-1: BCS –Broadcast stop
Pressing button 1() changes track output 1 to OFF.
Status of track-2 (below): Normal driving is maintained,
button 2 (MENU)can be used to switch between states.
This screen is also accessible via the MENU line STOP & OFF (chap. 8.8); However when scrolling
through the menu, the status of each track output is ON. To stop the traffic on track 1 press button 1()
and for track 2 press button 2(MENU).
Broadcast stop (BCS) and track power off (OFF) can also be switched on or off from the cabs, where
the relevant information will also be shown.
Button 1 Track-1 The status of track-1 or track-2 can be switched cyclically with
or buttons 1 or 2, independent of each other:
Button 2 Track-2
BCS (Broadcast stop) OFF (Power off) ON (Normal operation) BCS OFF etc.
e.g.:
As soon as both track outputs are powered up again
automatic switch (after 2 sec) to normal operation,
with the normal BLUE operating screen
Press button 3() to enter the “not quite normal” *) normal operating screen in RED
*) “not quite normal” means that the BCS and OFF states
are NOT cancelled and will also appear in the blue dis-
play; therefore engines on track-1 will NOT run.
The purpose for this “not quite normal” screen is to still
have access to OS, MENU and LOCO with buttons 1, 2 or
3 (as with the “real” normal screen). This allows for full
operation even though one of the two track outputs, for
example, is stopped or turned off.
Do the following to switch from the “not quite normal display” back to the “STOP & OFF” screen:
(to be able to switch the track-1 and 2 states again with button 1 and 2)
Press button 2(MENU)Displays the MX10 MENU GRAY
(with cursor at STOP & OFF)
and again:
Press button 2(MENU)normal operating screen in BLUE
or
Press/hold the rotary knob (4 sec.)
STOP & OFF - Screen RED
The status of track-1 or track-2 can be switched cyclically
and independently of each other again .
When switching from the “not quite normal screen” to the STOP & OFF screen by pressing/holding
the rotary knob, note the following:
Track 1 state: ON
BCSe
BCSe / OFF
No change
Track 2 state: No change
This means: if the power on track 1 is switched on, entering the stop screen again will set track-1 to
broadcast stop (BCSe) again.
Cancelling the rotary knob initiated broadcast stop; Return to the normal screen:
Briefly press the rotary knob Track-1 BCSe = ON,display returns to the normal BLUE operating
screen
Press/hold the rotary knob for 2
sec. or double-click
(within 1 second)
Display changes to RED, STOP & OFF - screen:
Broadcast stop (BCS) on track-1,
Normal operation is maintained on track-2.
NOTE: Press/hold rotary knob for 8
sec. SYS OFF = STANDBY. All out-
puts (tracks, DCC, CAN bus) are
switched off. Thus the cabs are also
switched off.
ATTENTION: the command station
stays under voltage, the controller is
active. Make sure the device stays
under supervision.
ATTENTION: This applies only if either the knob was pressed / held in the normal screen to initi-
ate a broadcast stop (track-1 = BCSe and track-2 = ON) or if the same state in the STOP & OFF
screen is restored manually (by repeatedly pressing the buttons 1() and 2(MENU)).
Other manuals for MX10
2
Table of contents
Popular Control System manuals by other brands
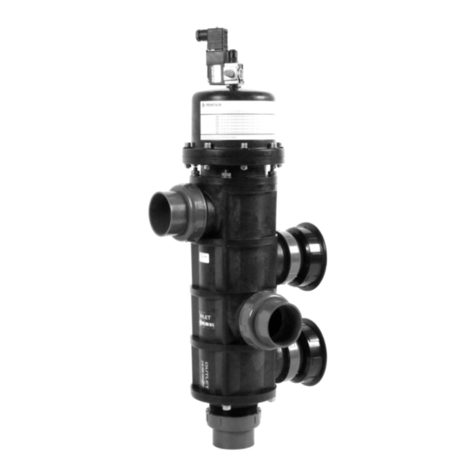
Pentair
Pentair ProValve installation guide
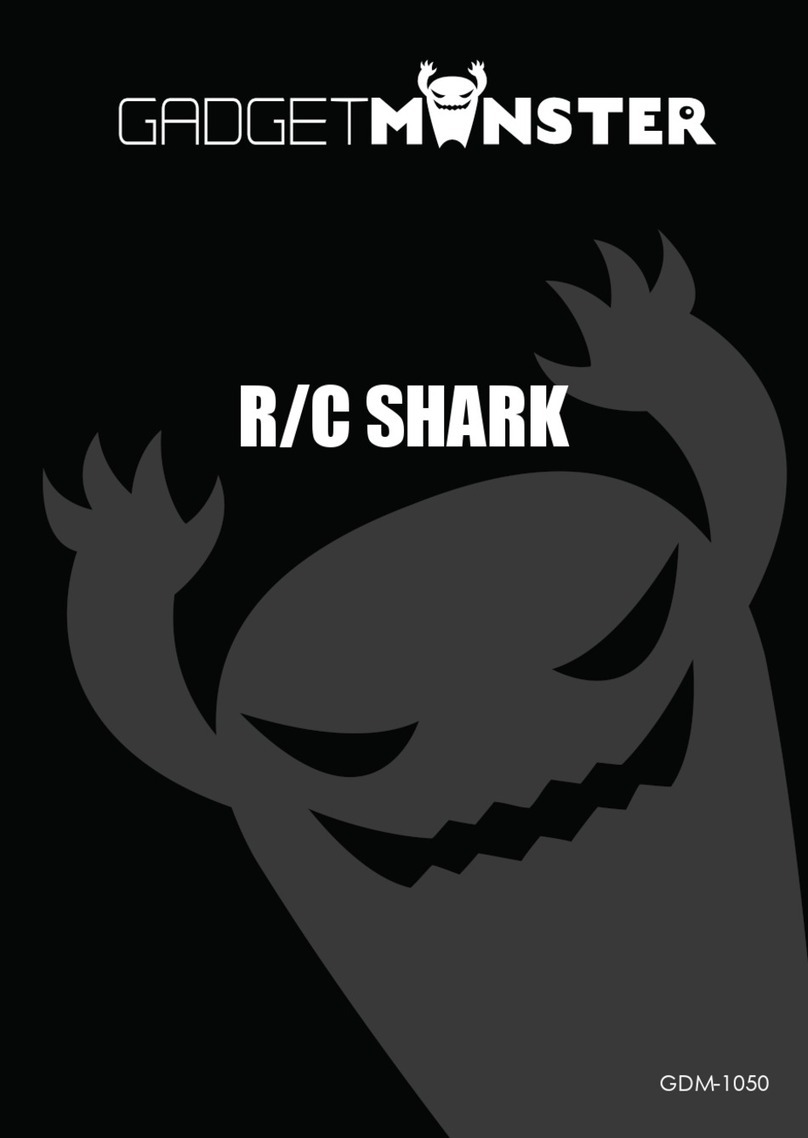
GADGETMONSTER
GADGETMONSTER R/C SHARK manual
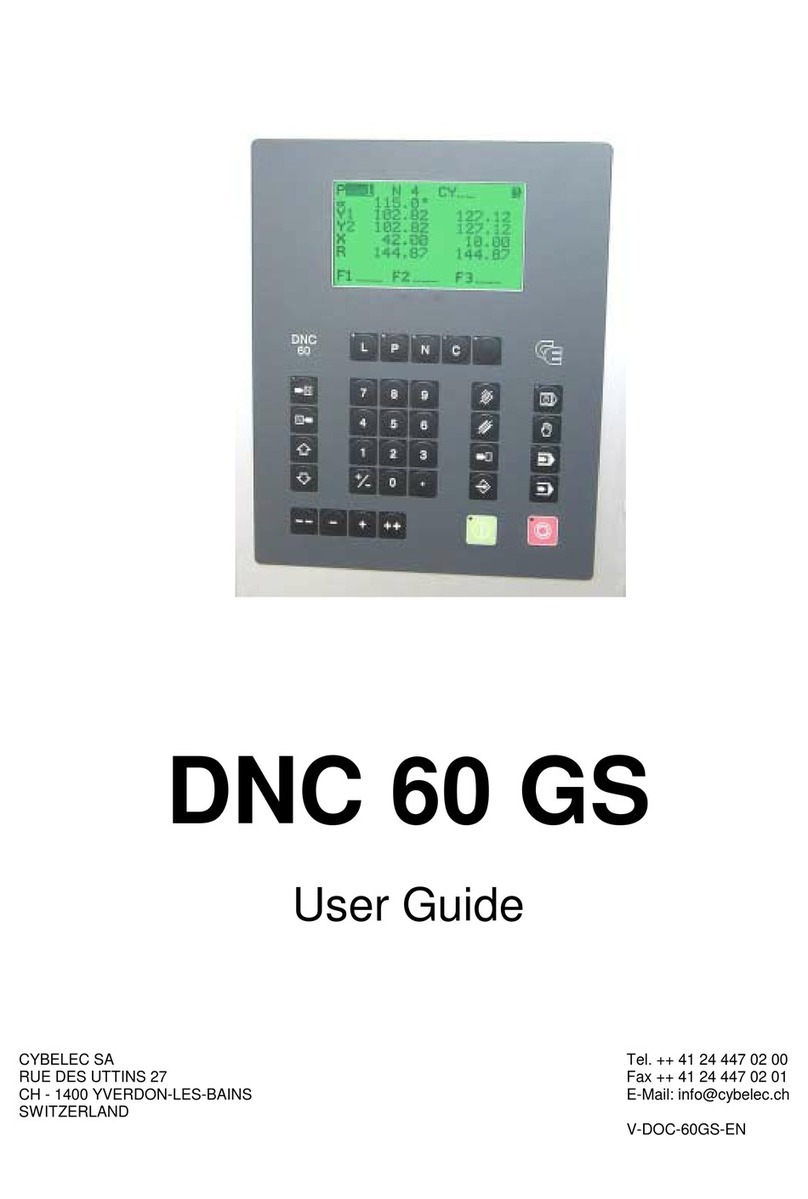
CYBELEC
CYBELEC DNC 60 GS user guide
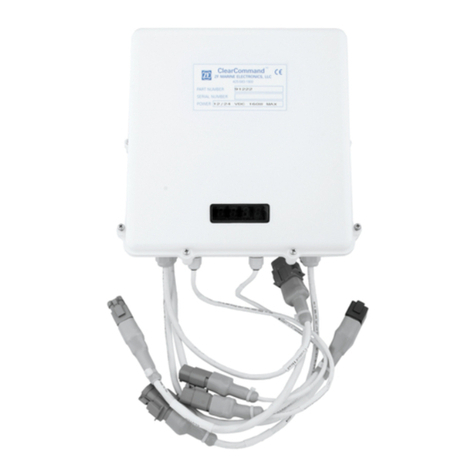
ZF Marine
ZF Marine ClearCommand 9000 Series Installation, operation and troubleshooting manual
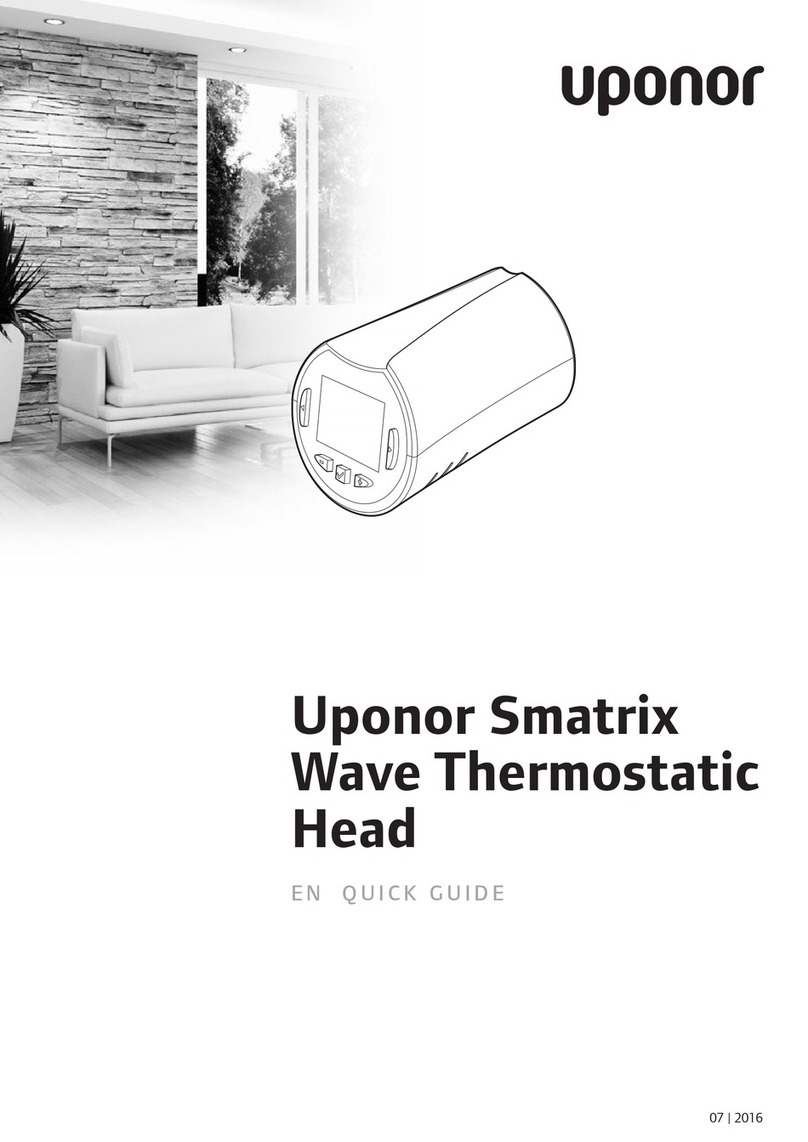
Uponor
Uponor Smatrix Wave T-162 quick guide

eqss
eqss OverWatch Dingli S03-ACE Series installation manual