ZPA Pečky MODACT MOKED 63 User manual

Type numbers 52 325 - 52 329
Electric Part-turn (90°) Actuators
for Ball and Flap Valves
9/19
MOUNTING INSTRUCTIONS
MODACT MOKED 63 T. No. 52 325
MOKED 125 T. No. 52 326
MOKED 250 T. No. 52 327
MOKED 500 T. No. 52 328
MOKED 1000 T. No. 52 329
MODACT MOKED CONTROL
MOKED 1000 T. No. 52 329
MOKED 1000 T. No. 52 329
MODACT MOKED CONTROL
MODACT MOKED CONTROL

ZPA Pečky, a.s. is certified company in accordance with ISO 90001 as amended.

CONTENS
1. Application ............................................................................................................3
2. Operating conditions; Operating position ..........................................................................3
3. Operation Mode, Service life of actuators ..........................................................................4
4. Technical data .........................................................................................................5
5. Actuator outfit ........................................................................................................6
6. Electric parameters ..................................................................................................6
7. Electronic outfit .......................................................................................................7
7.1 DMS2 ED .........................................................................................................7
7.2 Procedure of setting parameters by means of push-buttons ................................................9
7.3 Procedure of setting parameters by program DMS2 ....................................................... 11
7.4 Autodiagnostics ............................................................................................... 12
7.5 Restoring parameters from backup .......................................................................... 12
7.6 DMS2 ........................................................................................................... 19
7.7 Procedure of setting parameters by program DMS2 ....................................................... 19
Table – basic parameters ....................................................................................... 29–32
Dimensional sketch of electric actuators MODACT MOKED .................................................. 32–36
8. Assembly and putting actuator into operation .................................................................. 37
9. Operation and maintenance of actuators ........................................................................ 37
Spare parts ............................................................................................................. 38
1. APPLICATION
The actuators MODACT MOKED are designed for shifting control elements by a reversible rotary motion with
the turning angle of the output part 90°, including cases when tight closure in end positions is required. Typical example
of using is control of ball and flap valves in similar installations in the regime of remote control as well as automatic
regulation. The electric actuators MODACT MOKED are mounted directly on the controlled element.
2. OPERATING CONDITIONS, OPERATING POSITION
Operating conditions
The actuators MODACT MOKED are resistant against effect of operating conditions and external effects of
classes AC1, AD5, AD7, AE5, AE6, AF2, AG2, AH2, AK2, AL2, AM-2-2, AN2, AP3, BA4 and BC3 according to
ČSN 33 2000-5-51 ed. 3.
When the actuator is installed on a free area it is recommended to fit it with a light shelter against direct impact
of atmospheric effects. The shelter should overlap the actuator contour by at least 10 cm at the height of 20 – 30 cm.
When actuators are to be installed in the working environment with temperature below +10 °C and in the environment
with relative humidity above 80 %, it is always necessary to use an anti-condensation heater fitted to the actuator.
The electric actuators can be installed in areas with non-flammable and non-conductive dust, provided that
this does not adversely influence their function. Here, it is necessary to strictly observe ČSN 34 3205. It is
recommended to remove dust as soon as its layer is about 1 mm thick.
Notes:
The area under a shelter means the one where falling of atmospheric precipitations under and angle up to 60° from
the vertical is prevented.
The electric actuator must be installed in a place where cooling air has a free access. Minimum distance from a wall for
access of air is 40 mm. Therefore, the area where the electric actuator is installed must be sufficiently large, clean and ventilated.
Surrounding temperature
Operating temperature for the MODACT MOKED is from -40 °C to +60 °C.
Classes of external effects – excerpt from ČSN 33 2000-5-51 ed. 3.
Class:
1) AC1 – elevation above sea level ≤ 2000 m
2) AD5 – spouting water; water can spout in any direction
AD7 – water occurrence – shallow dipping
3

4
3) AE5 – medium dustiness
AE6 – strong dustiness
4) AF2 – occurrence of corrosive or polluting substances from atmosphere. Presence of corrosive polluting
substances is significant.
5) AG2 – medium mechanical stress by impacts – common industrial processes
6) AH2 – medium mechanical stress by vibrations – common industrial processes
7) AK2 – serious risk of growth of vegetation and moulds
8) AL2 – serious danger of the occurance of animals (insects, birds, small animals)
9) AM-2-2 – normal level of the signal voltage. No additional requirements
10) AN2 – medium solar radiation with intensities > 500 W/m2 and ≤ 700 W/m2
11) AP3 – medium seismic effects; acceleration > 300 Gal ≤ 600 Gal
12) BA4 – personal abilities. Instructed people.
13) BC3 – frequent contact with the earth potential. Persons coming frequently into contat with “live” parts or
standing on a conducting base.
Actuator are not intended for use in residential environments and may not secure an adequate protection of receiving
a radio signal in these environments.
Operating position
The actuators can be operated in any operating position.
3. OPERATION MODE, SERVICE LIFE OF ACTUATORS
Operation mode
The actuators can be operated with the type of loading S2 according to ČSN EN 60 034-1. The run period at temperature
+50 °C is 10 minutes; the mean value of loading torque should not exceed 60 % of the value of maximum tripping torque Mv.
The actuators can also work in the regime S4 (interrupted run with start-up) according to ČSN EN 60 034-1. Load factor
N/N+R is max. 25 %; the longest working cycle (N+R) is 10 minutes (course of working cycle is shown in the figure).
The highest number of closing operations in automatic regulation is 1200 cycles per hour. Mean value of loading torque with
load factor 25 % and surrounding temperature +50 °C is not higher than 40 % of maximum tripping torque Mv.
The highest mean value of loading torque is equal to rated torque of the actuator.
Corrosion protection
Actuators are standardly delivered with surface treatment corresponding to category of corrosion aggressiveness
C1, C2 and C3 according to ČSN EN ISO 12944-2.
On customer's request is possible to do surface treatment correcponding to category of corrosion aggressiveness
C4, C5-I and C5-M.
In following table is provided and overview of environment for each categories of corrosion aggressiveness accor-
ding to ČSN EN ISO 12944-2.
Corrosion
aggressiveness
level
Example of typical environment
Outdoor
Indoor
C1 Heated buildings with clean atmosphere
(very low) e.g. offices, shops, schools, hotels.
C2 Atmosphere with low level of pollution. Unheated buildings, in which may occur
(low) Mostly outdoor areas. condensation, e.g. stocks, sports halls.
C3 Urban industrial atmospheres, Production areas with high humidity and low air
(middle) mild pollution of sulfur dioxide. pollution, e.g. food industry, processing
Seaside areas with middle salinity. factories, breweries.
C4 Industrial areas and seaside areas Chemical plants, swimming pools,
(high) with middle salinity. seaside shipyard.
C5-I
(very high Industrial areas with high humidity Buildings or areas with predominantly continuous
– industrial) and aggressive atmosphere. condensation and high air pollution.
C5-M
(very high Seaside areas with high salinity. Buildings or areas with predominantly
– seaside) continuous condensation and high air pollution.

5
Service life of actuators
The actuator intended for shut-off valves must be able to perform at least 10,000 operating cycles (C - O - C).
The actuator intended for regulating purposes must be able to perform at least 1 million cycles with operation time (during
which the output shaft is moving) at least 250 hours. Service life in operating hours (h) depends on load and number of swit-
ching. Not always, high frequency of switching influences positively accuracy of regulation. For attaining the longest possible
faultless period and service life, frequency of switching is recommended to be set to the lowest number of switching necessary
for the given process. Orientation data of service life derived from the set regulation parameters are shown in the following table.
Service life of actuators for 1 million starts
Service life [h] 830 1 000 2 000 4 000
Number of starts [1/h] Max. number of starts 1200 1 000 500 250
4. TECHNICAL DATA
Supply voltage of electric motor:
According to Table 1 1 x 230 V, +10 %, -15 %, 50 Hz ±2 %
3 x 230/400V, +10 %, -15 %, 50 Hz ±2 %
(or as shown on the motor rating plate)
Other supply voltage for electric actuators should be discussed with the manufacturer.
Protective enclosure
Protective enclosure of actuators: MODACT MOKED – IP 67 according to ČSN EN 60529.
Noise
Level of acoustic pressure A max. 85 dB (A)
Level of acoustic output A max. 95 dB (A)
Tripping torque
Tripping torque is set at the manufacturer according to the customer's requirements within the range given in Table No. 1.
If setting of tripping torque is not required maximum tripping torque of the required type number of the electric actuator is set.
Self-locking
The actuators are self-locking. Self-locking of the electric actuators is ensured by a mechanical or electromagnetic
brake of the electric motor.
Sense of rotation
When looking at the output shaft in the direction towards the control box, the CLOSE direction of rotation is identical
with the clockwise sense.
Working stroke
Rated working stroke of electric actuator is 90°.
Manual control
Manual control is performed directly by a handwheel (without clutch). It can be used even when the electric motor
is running (the resulting motion of the output shaft is determined by the function of the differential gear). When the
Run time
N
Idle time
R
Cycle time
Course of working cycle
Mz
starting torque
≥
1,3 . Mv
Mstř
mean value of loading torque
Mv
maximum value of tripping torque

handwheel is rotated clockwise the output shaft of the actuator also rotates clockwise (when looking at the shaft towards
the control box). On condition that the valve nut is provided with left-hand thread, the actuator closes the valve.
Torque-limit switches in the actuator are set and work when the actuator is under voltage.
When using the manual control, ie. actuator is controlled mechanically, the torque-limit switches
doesn´t work and the valve can be damaged.
5. ACTUATOR OUTFIT
Position indicator
The actuator can be fitted with a display as an option for DMS2 ED electronic system. Actuator with DMS2 electronic
system is equipped with two-line display. MOKED actuator can be also fitted with a mechanical local position indicator.
Anti-condensation heater
The actuators are fitted with an anti-condensation heater preventing condensation of water vapour. Connects to net
with voltage of230 V mains and is connected to a thermostat.
Local control
The local control is used to control the actuator from the installation site.
Local control, when equipped with anactuator, consists of two switches. One chooses between LOCAL mode – 0 – REMOTE
and the other between OPEN – STOP – CLOSE.
6. ELECTRIC PARAMETERS
External electric connection
The terminal board of the actuator is fitted with terminals allowing one copper or aluminium conductor with a maximum
cross-section of 2.5 mm2 or two conductors with the same cross-sectional area up to 1 mm2 to be connected.
Connecting of actuators with connector – on special request.
Actuator internal wiring
The internal wiring diagrams of the MODACT MOKED actuators with terminal designation are shown in this
Mounting and operating instructions.
Each actuator is provided with its internal wiring diagram on the inner side of the actuator cover. The terminals are
marked on a self-adhesive label attached to a carrying strip under the terminal block.
Isolation resistance
Isolation resistance of electric control circuits against the frame and against each other is min. 20 MΩ. After a dump
test, isolation resistance of control circuits is min. 2 MΩ. See Technical specifications for more details.
Overheating protection of electric motor
All electric motors have thermal fuses in their winding. They serve as an additional protection; they do not substitute
the overcurrent protection or circuit breaking.
The fuses of single-phase electric motors are internally interconnected with the winding and, in case of overheating,
they cut out the electric motor; after cooling down, they cut it in automatically.
The fuses of three-phase electric motors are separately led out and they can be connected into control or signalling
circuits. They are connected to the actuator terminal board as a standard for MOKED 63 (type no. 52 325) only.
Load-bearing capacity is 250 V AC / 2.5 A.
Electric strength of electric circuits isolation
Circuits of anti-condensation heater 1 500 V, 50 Hz
Electric motor Un = 1 x 230 V 1 500 V, 50 Hz
Un = 3 x 230/400 V 1 800 V, 50 Hz
Deviations of basic parameters
Tripping torque ±15 % of max. tripping torque
Shifting time of output shaft +10 %
- 15 % of rated value
Setting of working stroke ±1°
6

Clearance at output part type no. 52 325, 52 326, 52 328 max. 1,5°
type no. 52 327, 52 329 max. 2,5°
Protection
The electric actuators are fitted with external and internal protecting terminal for securing protection against
dangerous shock voltage.
The protecting terminals are marked according to ČSN IEC 417 (34 5555).
The actuator must be properly secured against both overload and short circuit.
7. ELECTRONIC OUTFIT
Electro-mechanical control board is replaced with the electronic system DMS2 or DMS2 ED. Both systems scan
position of the output shaft and torque of the electric actuator by contact-free magnetic sensors. Long service life is
guaranteed for the contact-free sensors that do not get mechanically worn.
The sensor of the output shaft position is absolute and does not require any backup power supply in case supply
voltage is disconnected during operation of the electric actuator. Both systems can be set and monitored by a computer
with controlling program (set parameter can be backed up on a computer) or manually without a computer (for the
electronics DMS2, parameters can be manually set and it can be checked without computer only if the system is
equipped with a display and local control). They contain diagnostic functions - error messages on the display, memory
of recent failures and number of occurrences of respective failures.
The more simple system DMS2 ED substitutes the electro-mechanical board and/or provides for controlling
the electric actuator by input analog signal as in the version Control.
The system DMS2 enables the electric actuator to be used for two-position and three-position regulation or to be
connected to the industrial bus bar Profibus.
7.1 DMS2 ED
Basic outfit:
Control unit
main part of the system DMS2.ED - includes microcomputer, position sensor, 3 signal lamps LED,
4 push-buttons for simple setting and checking the actuator, connectors for connecting the torque
sensor, source board, and interface RS 232 (connection of computer for setting and diagnostics).
Torque unit
Source unit
electronic power supply, user's terminal board (connection of power supply and control signals), 2
torque relays, 2 position relays, 2 signalling relays, 1 relay for signalling errors (READY), switch of
resistance anti-condensation heater, connectors for connecting electronic brake, resistance heater
of analog module, and connector for interconnection with the control unit.
Optional outfit:
Analog module
output of feed-back signal 4 – 20 mA, in version CONTROL input of control signal 0/4 – 20 mA
Position indicator LED display
Local control
Contactors
Phase failure monitoring
module
This module is connected to all three power phases. If any outage occurs phase, the module
stops the actuator. Outwardly, this stop will appear as an impulse thermal protection.
Parameters:
Scanning of position contact-less, magnetic
Scanning of torque contact-less, magnetic
Working stroke see Tables 1, 2
Torque blocking 0 – 20 s at reversing in limit positions
Input signal 0(4) – 20 mA with switched on regulator function
Local/Remote control, Local open/close
Output signal 7 x relay 250 V AC, 3 A (MO, MZ, PO, PZ, SO, SZ, READY)
Position signal 4 – 20 mA max. 500 Ω, active/passive, galvanic-isolated,
LED display
Power supply of electronic 230 V AC, 50 Hz, 4 W, over-voltage category II
7

Realization:
Replacement of electric- the provided relay contacts substitute position, torque and signalling micro-switches;
mechanical board current feed-back signal 4 – 20 mA can also be brought out; the actuator is controlled by
the superior control system with signals “open” and “close”.
CONTROL The electronics covers also function of the regulator; the output shaft position is controlled
by analog input signal.
Function and setting of output relays
The output relays replace end-limit micro-switches; to some extent, function of the output relays differs according to
chosen mode of electronics or it can be selected, preferably by the setting program.
Relay MO, MZ, SO, SZ
In the version Control, the function of relay MO/MZ is same as that of motor relays.
Their operation is controlled by:
– regulation loop (deviation of required and actual position)
– active errors
Any induced active error will change over both relays to a standstill position (coils not energized). In case of errors,
the relays with a function of torque relays (in both versions DMS2 ED and DMS2 ED Control) are also controlled.
Relays SZ, SO, READY
Relay READY
- It usually signalizes errors + warning + not remote,
it can be changed-over to any offered signalization
Relay 3/SZ
- It usually signalizes position closed, it can be chan-
ged-over to any offered signalization
Relay 4/SO
- It usually signalizes position open, it can be
changed-over to any offered signalization
Relay 3/SZ Relay 4/SO
Ready Relay
OFF
warning
errors
warning or errors
errors or no remote
errors or warning or no remote
torgue O or Z
OFF
position O
position Z
torque O
torque Z
torque + position O
torque + position Z
opening
closing
motion
position
negated position
local control
remote control
control OFF
torgue O or Z
motion - blinker
For SO and SZ relays
the following functions
have been added:
Moment O negated:
after reaching the set
moment in the direction
the relay will open.
Moment Z negated:
after reaching the set
moment in the direction
the relay closes.
Moment O or Z nega-
ted:
after reaching. build
moment in direction clo-
sed or the relay will open.
MO torque open
(also changes-over to errors) motor open
MZ torque closed
(also changes-over to errors) motor close
PO position open torque open (also changes-over to errors ) + optional
tripping in position open (parameter Tripping)
PZ position closed torque closed (also changes-over to errors ) + optio-
nal tripping in position closed (parameter Tripping)
Relay DMS2 ED DMS2 ED Control

9
Setting program
The setting program is same for communication with the electronics DMS2ED and DMS2. The users' version can be freely
downloaded.
Note: In the window “Parameters” of the setting program, column “Access”, the word “NO” designates parameters that cannot
be changed by the user (change of these parameters is blocked).
7.2
PROCEDURE OF SETTING PARAMETERS BY MEANS OF PUSH-BUTTONS
For simple programming of required operating parameters, the control unit is fitted with four push-buttons:
MENU, P, O, C and three signal lamps.
Yellow Red Green State
- - - System without feeding
- - lit on Everything OK – working regime (remote, local or switched off control)
- blinking lit on Error or warning – working regime (remote, local or switched off control)
lit on - lit on Enter or exit of Setting of parameters by means of push-buttons
or Setting of parameters by means of PC
blinking - lit on
blinking blinking lit on Setting of parameters by means of push-buttons
blinking blinking lit on
In adjustment, follow the paragraphs “VERIFICATION of APPARATUS FUNCTION And its LOCATION”,
“fitting on VALVE” and “ADJUSTMENT of ACTUATOR with VALVE” of these instructions.
For safety reasons, the system is delivered in the state of induced error of Calibration when the functions are
limited in order to reduce the risk of damage to the actuator by wrong wiring.
Record of position CLOSED, OPEN and AUTOCALIBRATION
–
The actuator must be adjusted in such a way that the recorded position would switch off the actuator before it is swit-
ched off by torque. For tight closure, the torque relay for torque Closed is only connected into the control circuit. The
actuator can be shifted either manually or electrically. The actuator in version CONTROL can be started from menu
MOTOR in program DMS2. In this case, the actuator does not react to the set position and can only be stopped by the
torque relay. In controlling from menu MOTOR, no torque may be induced. The torque must be left manually.
If, during adjustment, the torque is reached in the end-limit position, the torque must be left by means of a hand wheel.
– The actuator is set to position Closed and position Closed is stored by long pressing of push-button C (without
entering the Menu).
– The actuator is set to position Open and position Open is stored by long pressing of push-button O.
– The calibration routine is started by means of push-button P (in remote control) that, in the three-position regulation,
will measure actual inertial masses of the system and store them into the memory of the control unit. In the two-
position regulation, pressing of push-button P only cancels the error of Calibration.
– In recording the end-limit positions, signalling relays and the position transducer are also set.
– In case the actuator stroke is to be increased and the switching off is set to “from position”, the actuator will
switch off during shifting in position O or 100 %. To further change the position, press C or O, and, while
Parametr – Parameter
Změna – Change
Chyba – Error
Přístup – Access
Setrvačnost (0,1 %) – Inertia [0.1 %]
Setr. Doběh (0,1 s) – Inertial run-out [0.1 s]
Necitlivost (%) – Insensitivity [%]
NE – NO
COM POWER TORK
AIN
LED1 LED2 LED3
MENU POC
Colours of diodes:
LED1 – yellow (menu number)
LED2 – red (parameter value)
LED3 – green
Push-buttons and signal lamps LED on control unit DMS2.ED.S and DMS2.ED.S90

10
keeping it depressed, the actuator can be further shifted. After required position is reached, it is stored to
memory by pressing push-button C or O.
Parameters that can be changed by user are set by manufacturer as follows:
1. Tripping torques: 100% or required value (it is not recommended to change the value
without consulting the supplier of the valve, etc.).
2. Relay 3 and relay 4: signalization SZ 1 % and SO 99 % of stroke
3. Time of blocking: 0 s
4. Position of blocking: 5 % of stroke from end-limit positions (it is not recommend to change
the value by more than 10 %)
5. Characteristics of position transducer: closed 4 mA, open 20 mA
6. Relay READY: errors + warning + not remote
In version CONTROL:
1. Setting of control signal: closed 4 mA, open 20 mA
2. Insensitivity of actuator in regulation: 1 % (it is not recommended to set insensitivity higher than 3 %)
3. Response in case of loss of control signal: stop
4. Way of switch off in end-limit positions: torque + PO + PZ
Overview of MENU
BROWSING THROUGH MENU
–
The setting regime is entered by pressing and keeping depressed push-button MENU for at least 2 s; LED1 is then lit on.
– Shortly press MENU to select the basic MENU – menu M1 to M8 (LED1 signalizes the menu number); by short
pressing of P, O, C they are entered (LED2 signalizes particular parameter).
– Shortly press P to select required value of the parameter. In case the parameter can be set to several values, they
are changed by short pressing of P (number of blinking of LED2 indicates its value). Keep pressing of P to record
the chosen parameter; the record is confirmed by lighting on of LED2.
– Shortly press MENU to gradually set the required menu and parameters.
–
After setting all required parameters, exit the setting menu by pressing and keeping depressed push-button
MENU for at least 2 s. The setting menu will also be left in case that no push-button is pressed within 1 minute.
MENU 1 – Setting of tripping torques
– After entering the menu by means of push-button C or O, select required torque.
– Shortly press P to select the set value of the parameter 50 – 100 % (5 – 10 blinking of LED2) and keep pressing
push-button P to store the parameter to memory.
MENU 2 – Setting function of signalling relays
– Basic setting of the signalling relays is SZ 1 % and SO 99 % of stroke.
– In case different setting is required, it can be changed after shifting the actuator to required position by means of
push-button C or O.
– Using push-button P, perform basic setting SZ 1 % and SO 99 % of stroke.
MENU 3 – Setting of blocking of torque in end-limit positions
– Shortly press P to select the set value of blocking time 0 – 20 s (0 – 20 blinking of LED2) and keep pressing push-
-button P to store the parameter to memory.
– Keep pressing push-button C to store actual position for blocking torque on the side Closed to memory.
– Keep pressing push-button O to store actual position for blocking torque on the side Open to memory.
MENU 4 – Setting transducer characteristics
– Shortly press P to select the value 4 – 20 mA – 1x blinking of LED2 or 20 – 4 mA – 2x blinking of LED2, and keep
pressing push-button P to store the parameter to memory.
Other menus only serve for board setting in version Control
MENU 5 – Setting control signal in 3P regulation
– Shortly press P to select value 4 – 20 mA - 1x blinking of LED2,
or 20 – 4 mA - 2x blinking of LED2,
or 0 – 20 mA - 3x blinking of LED2,
or 20 – 0 mA - 4x blinking of LED2
and keep pressing push-button P to store the parameter to memory.

11
MENU 6 – Setting insensitivity in three-position regulation
– Shortly press P to select value 1 – 10 % (1 – 10x blinking of LED2) and keep pressing push-button P to store
the parameter to memory.
MENU 7 – Response in case of losing control signal in three-position regulation
– Shortly press P to select value OPEN - 1x blinking of LED2,
or CLOSE - 2x blinking of LED2,
or STOP - 3x blinking of LED2,
and keep pressing push-button P to store the parameter to memory.
MENU 8 – Way of switching off in end-limit positions in 3P regulation
– Shortly press P to select value TORQUE - 1x blinking of LED2,
or TORQUE + PO - 2x blinking of LED2,
or TORQUE + PZ - 3x blinking of LED2,
TORQUE + PO + PZ - 4x blinking of LED2,
And keep pressing push-button P to store the parameter to memory.
7.3
PROCEDURE OF SETTING PARAMETERS BY PROGRAM DMS2
– Before starting the actuator, it is necessary to set some parameters of the system by means of program
DMS2 on PC.
–
For safety reasons, the system is delivered in the state of induced error of Calibration when the functions are
limited in order to reduce the risk of damaging the actuator by wrong wiring. In controlling the actuator from program
DMS2, its run is stopped when any torque is induced.
Working torque
– Check and, if necessary, set the value of working torque 50 – 100 % in program DMS2.
Record of positions OPEN, CLOSED and AUTOCALIBRATION
The actuator should be adjusted so that the recorded position would stop the actuator before it is switched
off by torque. The actuator is shifted manually or electrically. The actuator in version CONTROL can be started
from menu MOTOR in program DMS2. In this case, the actuator does not respond to the set position and is
switched off by torque. In controlling from menu MOTOR, no torque may be induced. The torque should be left
manually.
Main window of setting program Selection of electronics

12
Record of position CLOSED:
– In the required position, press push-button Z in the program and confirm the approved record.
Record of position OPEN:
– In the required position, press push-button O in the program and confirm the approved record.
The recorded values are confirmed by pressing push-button START in program DMS2. For the actuator in
version CONTROL, change over the actuator to remote control and, by pressing push-button START, start the
autocalibration. By short starting of the motor in both directions, the actuator measures inertia and changes
over to the regulating regime. Information on the course of autocalibration is signalized next to push-button
START. The autocalibration cannot be started in case the torque relay is switched off. The torque should be left
manually.
Other parameters
Check and, if necessary, change other parameters:
Control signal 4 – 20 mA, 20 – 4 mA, 0 – 20 mA, 20 – 0 mA
Insensitivity 1 – 10 %
Function in case of error open, close, stop, to position
Time of torque blocking in end-limit positions 0 – 20 s
Position of torque blocking in end-limit positions 1 – 10 %
Output of position signal 4 – 20 mA, 20 – 4 mA
Function READY combined error
Note: Signal READY is brought out as contact of the relay on the terminal board. If the state ERROR or WARNING
is not detected (setting can be made of what is to be evaluated as error or warning), the contact is closed; in case
of error, warning, or if feeding of electronics is interrupted, the contact is opened. The state of the relay READY is
indicated by the LED diode on the source board.
7.4 AUTODIAGNOSTICS
DMS2 ED performs continuously its diagnostics and, if a problem is detected, it reports warning or error. The warning
or error is signalized by LED of the display and, possibly, by relay Ready. The warning has no effect on operation of the
system, the error stops the actuator.
Assigning or switching off of warnings and errors is set in window “Warning and error” of the setting program (it is
opened by clicking one of parameters Warning 1 – 4 or Error 1 – 4 in window “Parameters”).
The error or warning are reported by opening the relay READY and by blinking of the red LED diode on the control
unit. Particular error is specified by program DMS2 or on the display.
7.5 RESTORING PARAMETERS FROM BACKUP
With the feeding switched off, press push-buttons O and C at the same time. Then, switch on feeding and wait until
red and yellow LED diodes light on. The backup parameters are read.

13
List of warnings and errors
No. Name Warning1 Error1 Description
1 Safe * X Input Safe activated
2 Control signal X Value of control signal ≤ 3 mA (it applies to ranges 4 – 20/20 – 4 mA)
4 Torque X Induced torque beyond end-limit positions or disconnected torque sensor
6 Thermal protection X Thermal protection input activated
7 Sense of rotation X Reverse sense of rotation (for CONTROL only)
8 EEPROM X Wrong control sum of parameters in EEPROM
9 RAM X Wrong control sum of parameters in RAM
10 Parameters X Wrong parameters in EEPROM
11 Setting regimes X Setting regime from push-buttons or PC
12 Torque sensor X Disconnected or defective torque sensor
13 Sensor 1 X Error of sensor of position 1 (lowest stage)
14 Sensor 2 X Error of sensor of position 2
15 Sensor 3 X Error of sensor of position 3
16 Sensor 4 X Error of sensor of position 4 (highest stage)
17 Calibration X Autocalibration not carried out
18 Torque setting X Wrong setting of torques (parameters Torque O/Z 50/100 %)
19 Stroke X Wrong setting of stroke (parameters Position O/Z)
20 Rotation error X The actuator does not rotate
21 High temperature X Permitted max. temperature exceeded (parameter Temperature max.)
22 Low temperature X Permitted min. temperature exceeded (parameter Temperature min.)
23 LCD internal * X Display of LCD internal does not communicate or not added
in parameter CAN of configuration
24 LCD external * X Display of LCD external does not communicate or not added
in parameter CAN of configuration
25 Fieldbus * X Module of industrial bus does not communicate or not added
in parameter CAN of configuration
26 CAN * X Error of bus CAN (short circuit, interruption, only sensor communicates)
27 Fieldbus activity* X Connection to industrial bus not active
28 Phase * X Inverse order of phases or some phase missing
29 Relay of service life X Service life of relay MO/MZ at CONTROL exceeded
(parameter Relay of service life)
30 Reset X Non-standard Reset of unit induced (watchdog etc.)
31 ROM X Wrong control sum of program in ROM
32 CAN version * X Sensor, LCD display or module Fieldbus have incompatible
versions of firmware
33 Wrong command * X Commands Open and Close entered at the same time
34 Wrong inertia - - Wrong inertia measured by autocalibration (for autocalibration only)
35 Wrong run-down - - Wrong run-down measured by autocalibration (for autocalibration only)
41 Wrong position X Servo-drive is in position 25 % behind working stroke
1) Assignment can vary depending on the version of firmware of the sensor control unit.
* Applies to DMS2 only.
Memory of number of induced warnings and errors
– For all ascertained warnings and errors, DMS2.ED uses counters of occurrence of these warnings and errors during
operation of the system.
– Values of the counters are stored to the EEPROM memory and are preserved even in case of the power supply fall-out.
– Reading of the counters is possible by means of the program for PC
– Clearing of the counters is possible by means of the program for PC with the level of authorization “SERVICE”.
Memory of recently induced warnings and errors
– DMS2.ED stores three recently induced warnings and errors to the EEPROM memory.
– Recent warnings and errors can be displayed and erased by means of the program for PC.

14
Example of wiring diagram of electronics DMS2 ED in version Substitution of electro-mechanical board
with single-phase electric motor
Torque
sensor
Position
sensor
Local control
Source board
Remote allowed
In version without local
control, the jumper from
terminal U is connected
to terminal 2
Supply mains
Analog
module
Active output
Passive output
Remote
“Open”
Remote
“Close”
Note: Here, contacts of relay MO, MZ, SO, SZ are shown with power supply switched off; with power supply switched off contacts PO, PZ are shifted to the position drawn in dashed line.
E0010
“R” “ L” “O” “C”

15
Example of wiring diagram of electronics DMS2 ED in version Substitution of electro-mechanical board with three-phase electric motor
Note: Here, contacts of relay MO, MZ, SO, SZ are shown with power supply switched off; with power supply switched off contacts PO, PZ are shifted to the position drawn in dashed line.
EM0011M
In version without local
control the jumper from
terminal U is connected
to terminal 2
Remote allowed
Torque
sensor
Position
sensor
“R” “ L” “O” “C”
Local control
Analog
module
Source board
Active output
Passive output
Remote
Remote
“Close”
“Open”
Motor
open
Motor
close
Supply mains

16
Example of DMS2ED electronics connection with phase failure monitoring module and dual local control switch
Local control
E0102
„R“ „L“ „O“ „C“ „R“ „L“
Source board
Plate
watch
phases
In version without local
control the jumper from
terminal U is connected
to terminal 2
Remote allowed
Torque
sensor
Position
sensor
Analog
module
Remote
„Open“
Remote
„Close“
Power relays board

17
Example of wiring diagram of electronics DMS2 ED in version Control with single-phase electric motor
Torque
sensor
Position
sensor
Local control
Source board
In version without local
control the jumper from
terminal U is connected
to terminal 2
Supply mains
Active output
Passive output
Analog
module
Note: Here, contacts of relay MO, MZ, SO, SZ are shown with power supply switched off; with power supply switched off contacts PO, PZ are shifted to the position drawn in dashed line.
E0012
“R” “ L” “O” “C”

18
Example of wiring diagram of electronics DMS2 ED in version Control with three-phase electric motor
Torque
sensor
Position
sensor
Local control
Source board
In version without local
control the jumper from
terminal U is connected
to terminal 2
Power relays board
Analog
module
Active
output
Passive
output
3x400 V
Note: Here, contacts of relay MO, MZ, SO, SZ are shown with power supply switched off; with power supply switched off contacts PO, PZ are shifted to the position drawn in dashed line.
E0013
“R” “ L” “O” “C”

19
7.6 DMS2
Main properties of DMS2:
–
Complete control of the actuator run of the two- and three-position regulation or connection to the industrial bus Profibus.
– Synoptic signalization of operation and service data on the character LCD display 2 x 12.
–
Autodiagnostics of error reports on the LCD display, memory of recent failures and number of occurrences of respective
failures.
– Setting of parameters by the PC program and by local control provided that the actuator is fitted with local control.
Basic outfit:
The control unit is the main part of the system DMS2; it comprises:
– Microcomputer and memory of parameters
– Position sensors
– 2 signalling LED
– Connectors for connecting the torque sensor, relay board, and two-position inputs, source board, communication
adapter, LCD display, and local control
Torque unit provides for scanning torque by the contactless sensor
Source unit – two types exist:
DMS2.ZAN for the two-position or three-position control of the actuator by binary signals “Open” and “Close” or by
analog signal 0(4) – 20 mA.
DMS2.ZPR for controlling the actuator by the industrial bus Profibus.
Both units include the feeding source for electronics, two relays for controlling the power switches (contactors or
contactless switches) of the electric motor, guarding of sequence of phases (in case the actuator is fed by three-phase
voltage), circuits for connecting the anticondensation heater, and input terminals for connecting the thermo-contact
from the electric motor. The units are fitted with the power terminal board for connecting the power supply. The units
are fitted with a connector for the display and local control.
Unit DMS2ZAN also contains:
– input circuits for the two-position and three-position control of the actuator and terminals for connecting external
control signals
– input of signal SAFE – information on external failure
– relay – total of five; four (signalling) can be set for reporting of position, torque, or other operation states of the
actuator; the fifth (Ready) is used for reporting of errors, warnings, and other states when the actuator cannot
faultlessly perform its function, and the terminals to which contacts of the relay are connected
– circuits of the feedback current signal – information on position of the actuator output shaft
Unit DMS2.ZPR also contains:
– circuits for communication with the superior control system through the industrial bus Profibus DP, input and output
terminals for connecting the bus, and termination resistors with a switch.
Display unit – two-row display, 2 x 12 alpha-numeric characters
Unit of push-buttons – sensors of push-buttons “open”, “close”, “stop” and the rotary switch “local, remote, stop”.
The actuator can be fitted with contactors.
7.7
PROCEDURE OF SETTING PARAMETERS BY PROGRAM DMS2
Before putting the actuator into operation, it is necessary to set some parameters of the system by means of
program DMS2 on PC.
Before adjustment, check the actuator according to the paragraph ASSEMBLING AND PUTTING THE ACTUATOR INTO
OPERATION.
Warning:
For safety reasons (reduced risk of damage to the actuator by wrong wiring), the system is delivered in the state of
the induced error of CALIBRATION when the functions are limited and, during controlling the actuator from program
DMS2, its run is stopped if any torque is induced.
Note:
The setting program is the same for electronics DMS2 ED. See the figure on page 11 for the main window
and the window of Selection of electronics.

20
Working torque
– Check and, if necessary, set the value of the working torque 50 – 100 % in program DMS2.
Tripping in end-limit positions
– Check and, if necessary, set the way of tripping in the end-limit positions::
– Torque
– Torque + position O
– Torque + position Z
– Torque + position O + Z
End-limit positions - working stroke
– Position Z
– Shift to position Closed either manually or by means of menu Motor in program DMS2.
– The actuator can only be controlled by means of the program if no torque is induced. The torque should be left
manually.
– Press push-button Z to confirm consent with the record.
– Position O
– Shift to position Open either manually or by means of menu Motor in program DMS2.
– The actuator can only be controlled by means of the program if no torque is induced. The torque should be left
manually.
– Press push-button O to confirm consent with the record.
Autocalibration
– The autocalibration can only be started by means of the program if no torque is induced. The torque should be left
manually.
– The autocalibration is started by push-button Start in program DMS2.
– Wait until the autocalibration is completed; information on its course is signalized next to push-button Start.
Other parameters
Check and, if necessary, change other parameters:
Control signal 4 – 20 mA 20 – 4mA 0 – 20 mA 20 – 0 mA
2 position Bus
Insensitivity 1 – 1 0 %
Function SAFE Open Close Stop To position
Active SAFE O V 230 V
Time of blocking torque
in end-limit positions 0 – 20 s
Position of blocking torque
in end-limit positions 1 – 10 %
Output of position signal 4 – 20 mA 20 – 4 mA
Function READY
Switched off Warning Errors Warning or error
- Combined error Errors or not Errors or warning Torque “O” or “Z”
remote or not remote
Switched off Position O Position Z
Torque O Torque Z
Torque and position O
Torque and position Z
Relay 1 – 4 Opening Closing Motion Position
position N Local control Emote control Control switched off
Torque O/Z Motion - blinker
Position Relay 1 – 4 0 – 100 %
Note: SAFE - input information on the error of an external device can be set so that the actuator would respond as to
its own error.
This manual suits for next models
5
Table of contents
Other ZPA Pečky Controllers manuals
Popular Controllers manuals by other brands

LOVATO ELECTRIC
LOVATO ELECTRIC ATL500 instruction manual
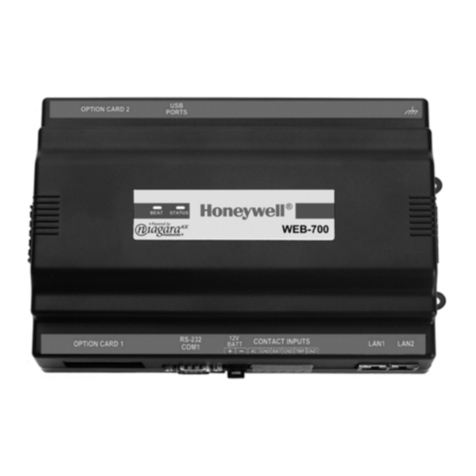
Honeywell
Honeywell WEB-700 installation instructions
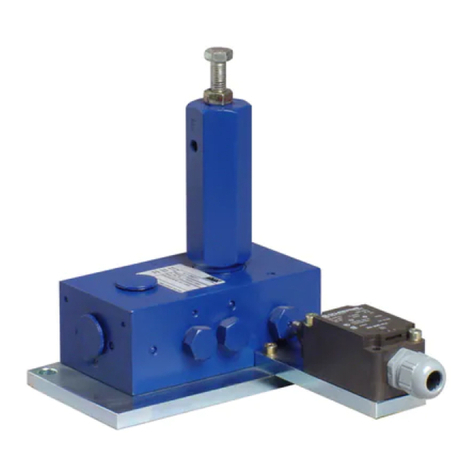
SKF
SKF DU1-GKS EEX operating instructions

Mitsubishi
Mitsubishi MELSEC Q Series user manual

Danfoss
Danfoss ERC 213 installation guide
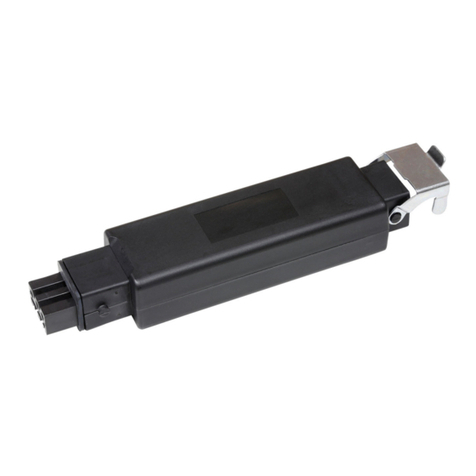
elsner elektronik
elsner elektronik 70711 Technical specifications and installation instructions