AB Sciex API 3200 System Installation instructions

Hardware Guide
API 3200™System
D1000092204 B
May 2010

This document is provided to customers who have purchased AB SCIEX equipment to use in the
operation of such AB SCIEX equipment. This document is copyright protected and any reproduction of
this document or any part of this document is strictly prohibited, except as AB SCIEX may authorize in
writing.
Equipment that may be described in this document is protected under one or more patents filed in the
United States, Canada, and other countries. Additional patents are pending.
Software that may be described in this document is furnished under a license agreement. It is against the
law to copy, modify, or distribute the software on any medium, except as specifically allowed in the license
agreement. Furthermore, the license agreement may prohibit the software from being disassembled,
reverse engineered, or decompiled for any purpose.
Portions of this document may make reference to other manufacturers and/or their products, which may
contain parts whose names are registered as trademarks and/or function as trademarks of their respective
owners. Any such usage is intended only to designate those manufacturers' products as supplied by
AB SCIEX for incorporation into its equipment and does not imply any right and/or license to use or
permit others to use such manufacturers' and/or their product names as trademarks.
AB SCIEX makes no warranties or representations as to the fitness of this equipment for any particular
purpose and assumes no responsibility or contingent liability, including indirect or consequential
damages, for any use to which the purchaser may put the equipment described herein, or for any adverse
circumstances arising therefrom.
For research use only. Not for use in diagnostic procedures.
The trademarks mentioned herein are the property of AB Sciex Pte. Ltd. or their respective owners.
AB SCIEX™ is being used under license.
AB SCIEX
71 Four Valley Dr., Concord, Ontario, Canada. L4K 4V8.
AB SCIEX LP is ISO 9001 registered.
© 2010 AB SCIEX.
Printed in Canada.

Document Number: D1000092204 B 3
Contents
Chapter 1 System Overview . . . . . . . . . . . . . . . . . . . . . . . . . . . . . . . 5
Principles of the System . . . . . . . . . . . . . . . . . . . . . . . . . . . . . . . . . . . 6
Applications for the System . . . . . . . . . . . . . . . . . . . . . . . . . . . . . . . 6
Features of the Instrument. . . . . . . . . . . . . . . . . . . . . . . . . . . . . . . . 6
How the Instrument Works. . . . . . . . . . . . . . . . . . . . . . . . . . . . . . . . 6
Parts of the Instrument . . . . . . . . . . . . . . . . . . . . . . . . . . . . . . . . . . . . 7
Power Controls. . . . . . . . . . . . . . . . . . . . . . . . . . . . . . . . . . . . . . . . . 8
Sample Introduction Features and Status Indicators . . . . . . . . . . . . 8
I/O Panel . . . . . . . . . . . . . . . . . . . . . . . . . . . . . . . . . . . . . . . . . . . . . 9
Gas Panel . . . . . . . . . . . . . . . . . . . . . . . . . . . . . . . . . . . . . . . . . . . . 10
Source Exhaust System . . . . . . . . . . . . . . . . . . . . . . . . . . . . . . . . . 11
Vacuum Chamber . . . . . . . . . . . . . . . . . . . . . . . . . . . . . . . . . . . . . 12
Shutting Down and Turning on the System . . . . . . . . . . . . . . . . . . . 12
Instrument Safe Fluids . . . . . . . . . . . . . . . . . . . . . . . . . . . . . . . . . . . 14
Source/Gas Parameters . . . . . . . . . . . . . . . . . . . . . . . . . . . . . . . . . . 14
Turbo V™ Ion Source Settings . . . . . . . . . . . . . . . . . . . . . . . . . . . . . 15
Compound Parameters . . . . . . . . . . . . . . . . . . . . . . . . . . . . . . . . . . 15
Related Documentation . . . . . . . . . . . . . . . . . . . . . . . . . . . . . . . . . . 16
Technical Support. . . . . . . . . . . . . . . . . . . . . . . . . . . . . . . . . . . . . . . 16
Chapter 2 3200 Series Parameters . . . . . . . . . . . . . . . . . . . . . . . . . 17

Contents
4 Document Number: D1000092204 B

Document Number: D1000092204 B 5
1
System Overview
The API 3200™ LC/MS/MS system includes a triple quadrupole mass
spectrometer, a Turbo V™ ion source, a computer, and the Analyst®software.
Figure 1-1 API 3200™ instrument and bench
WARNING! If you need to move the system, contact an FSE to assist you. Risk of
personal injury or instrument damage.
Note: Before you operate the instrument, make sure you have read the Safety Practices
guide.
Line Adjustment
Transformer
Roughing Pump
Bench
Mass Spectrometer
Front View
Ion Source

System Overview
6 Document Number: D1000092204 B
Principles of the System
This section describes features and applications of the API 3200™ LC/MS/MS
system.
Applications for the System
The API 3200 system is designed for quantitative analysis of small molecules.
This application involves measurement of specific molecular weight compounds,
usually a drug or metabolite in a liquid sample, and their resulting fragment ions
for determining the exact quantity of the compound in the sample of interest.
Quantitation is performed using a standard curve of mass spectrometer signal
intensity for various known concentrations of the compound. The signal in the
test sample is then compared to the standard curve to determine the
concentration.
The typical scan type used for this application is MRM (Multiple Reaction
Monitoring).
Features of the Instrument
The API 3200 system is a benchtop triple quadrupole mass spectrometer for
sensitive quantitative analyses of biomolecules found in a wide variety of
biological matrices. It has the following features:
•The standard Turbo V™ ion source provides a plug-and-play
TurboIonSpray®probe and APCI probe, a durable ceramic interface, and
compatibility with high flow rates.
•LINAC®collision cell eliminates cross-talk and allows for multi-component
analysis during an LC run.
•Rugged Curtain Gas™ interface technology combined with improved gas
dynamics reduces maintenance and increases uptime.
•Scanning in a mass range of m/z 5–1800.
•Integrated switching valve and integrated syringe pump provide
convenient sample introduction flexibility.
•Additional compatible sources, including the DuoSpray™ ion source,
PhotoSpray®ion source, and NanoSpray®III ion source components,
provide further flexibility.
•IDA (Information Dependent Acquisition) maximizes the amount of
information that can be acquired in an LC scan.
•Compatible with additional software packages, such as Metabolite ID
software, Automaton software, BioAnalyst™ software, and more.
How the Instrument Works
The API 3200 mass spectrometer has a series of quadrupole filters that transmit
ions according to their m/z (mass-to-charge ratios). Ions entering the ion path are
first focused by Q0 before passing into Q1.
Q1 is a filtering quadrupole that sorts the ions before they enter Q2, a LINAC
collision cell in which ions can be broken into fragments by collisions with gas
molecules. This technique allows for the design of experiments that measure the
m/z of product ions to determine the composition of the parent ions. After

Hardware Guide
Document Number: D1000092204 B 7
passing through Q2 the ions enter Q3 for additional filtering, and then enter the
detector. In the detector, the ions create a current that is converted into a voltage
pulse. The voltage pulses leaving the detector are directly proportional to the
quantity of ions entering the detector. The instrument monitors these voltage
pulses and converts the information into a signal. The signal represents the ion
intensity for a particular m/z and the instrument displays this formation as a mass
spectrum. For more information, see the following figure, Figure 1-2 Ion optics
path.
Figure 1-2 Ion optics path
The API 3200 system uses the Turbo V ion source to produce ions from liquid
samples. The Turbo V source can use either the TurboIonSpray probe or the APCI
(atmospheric pressure chemical ionization) probe. The instrument is configured to
perform complex MS/MS analysis, but for less rigorous analytical requirements it
can perform single MS scans.
Parts of the Instrument
This section contains diagrams of the instrument and general descriptions of the
main components.
Figure 1-3 Front view
Curtain Plate
DP (Orifice)
Skimmer
IQ1 IQ2 LINAC
®
Collision
Cell
IQ3
ST
DF (Deflector)
Detector
CUR (Curtain Gas™ flow)
EP (Q0) RO1 (Q1) RO2 (Q2) RO3 (Q3)
Front View
Mass Spectrometer
Ion Source
Integrated
Switching
Valve
Integrated
Syringe
Pump

System Overview
8 Document Number: D1000092204 B
Figure 1-4 Back view
Power Controls
The API 3200™ instrument power controls are located near the back left corner
of the instrument, wherein the power distribution module is enclosed. This area
contains the main power switch and the external AC power supply outlet.
Figure 1-5 Power switch and supply
Sample Introduction Features and Status Indicators
This section describes the features and controls housed on the front left area of
the instrument, adjacent to the source housing.
SHEATH
GAS
MAX 105 PSIG
CAD
GAS
MAX 60 PSIG
VALVE
WASTE OUT
EXHAUST
WASTE OUT
CURTAINGAS
SUPPLY
Max 60 PSIG
GAS 1 / GAS 2
Max 105 PSIG
EXHAUST SUPPLY
MIN 55 PSIG MAX 60 PSIG
SERIAL
SOURCES
CAD GAS
BACKING PUMP
AUX I/O IEEE-4888
Rear View
Ion Source
Mass Spectrometer
I/O Panel
Gas Panel
Roughing
Pump
Connection
AC Power
Supply
CAD Gas
Adjustment
Valve
Main Power
Switch
207-242V
50-60 Hz 10A
External
A/C Power Supply

Hardware Guide
Document Number: D1000092204 B 9
The Instrument Status lights indicate the status of the instrument vacuum. When
the operational vacuum conditions are satisfied and the instrument is in analysis
mode, the Ready light (green) is illuminated and the Fault light (red) is
extinguished. The Fault light flashes when a vacuum fault is detected. In Pump-
Down mode, the Ready light flashes for the duration of the sequence.
Directly below the source housing is a set of conveniently integrated sample
introduction features. An integrated switching valve with associated Load and
Inject buttons (marked A and B, respectively) can be used as a manual injector
when optimizing for an analyte using FIA, or for diverting LC flow when any
precipitate or salts initially come off the LC column. Below that, an integrated
syringe pump is available for infusing standards when calibrating the instrument
or optimizing for an analyte.
Figure 1-6 Sample introduction features and status indicators
I/O Panel
The input/output panel is located at the center back of the chassis. This panel
contains several connection ports for the system:
•The IEEE-488 (GPIB) port provides a connection to the system’s computer.
LOAD INJECT
AB
Integrated
Switching
Valve
Integrated
Syringe
Pump
INSTRUMENT STAUS
INSTRUMENT STATUS
FAULT
FAULT
READY
READY
LOAD INJECT
AB

System Overview
10 Document Number: D1000092204 B
•The sources port facilitates communication to optional ion sources, such
as the control valve for the DuoSpray™ ion source, or provision of 24 VDC
for the PhotoSpray®ion source.
•The AUX I/O outlet allows for communication with necessary peripheral
devices, such as autosamplers or UV detectors.
•A serial port provides a connection point for additional device
communications.
Figure 1-7 I/O panel
Gas Panel
The gas panel houses the gas supply connections and the external connections
for the source exhaust system.
I/O Panel
SERIAL
SOURCES AUX I/O IEEE-488

Hardware Guide
Document Number: D1000092204 B 11
Figure 1-8 Gas panel
Source Exhaust System
The source exhaust system is a safety feature that isolates the sample vapors and
exhaust products from the laboratory environment. The ion source requires that
this exhaust system is properly connected and functioning. The exhaust pump
draws the solvent vapors from the enclosed source housing and delivers them to
the exhaust-waste-out fitting, and then to a waste bottle outside the instrument.
It is recommended that these vapors be passed through this waste bottle and
then vented to a fume hood or outside port.
WARNING! Hazardous Materials: Take all necessary precautions to ensure the safe
disposal of the source exhaust. Follow all applicable local regulations.
EXHAUSTSUPPLY
MIN 55 PSIG MAX 60PS
IG
SHEATH
GAS
MAX105 PSIG
CAD
GAS
MAX 60 PSIG
CADGAS
VALVE
WASTE OUT
EXHAUST
WASTE OUT
CURTAINGAS
SUPPLY
Max60PSIG
GAS1/GAS2
Max 105P
SIG
SERIAL
SOURCES AUXI/OIEEE-488
207-242V
50-60 Hz10
A
BACKING
PUMP
Gas Panel
SHEATH
GAS
MAX 105 PSIG
CAD
GAS
MAX 60 PSIG
VALVE
WASTE OUT
EXHAUST
WASTE OUT
CURTAIN GAS
SUPPLY
MAX 60 PSIG
GAS 1 / GAS 2
MAX 105 PSIG
EXHAUST SUPPLY
MIN 55 PSIG MAX 60 PSIG

System Overview
12 Document Number: D1000092204 B
Figure 1-9 Source exhaust system
A filtered nitrogen or zero air gas supply (oil free) is delivered to the source
exhaust pump at pressures indicated on the gas panel at the back of the
instrument. The preceding figure shows the exhaust supply connection points for
the API 3200 instrument.
Vacuum Chamber
The vacuum chamber houses the mass filter rail, including the ion optics, the
quadrupole rod sets, the collision cell, and the ion detector.
Shutting Down and Turning on the System
Use the following procedures if you need to shut down or turn on the system.
To shut down the system
1. In the Analyst®software, complete or stop any ongoing scans.
2. Turn off the sample flow to the instrument.
EXHAUSTSUPPLY
MIN 55 PSIG MAX 60 PSIG
SHEATH
GAS
MAX105 PSIG
CAD
GAS
MAX 60 PSIG
CADGAS
VALVE
WASTE OUT
EXHAUST
WASTEOUT
CURTAINGAS
SUPPLY
Max60PSIG
GAS1/GAS2
Max105P
SIG
SERIAL
SOURCES AUXI/OIEEE-488
207-242V
50-60 Hz10
A
BACKING
PUMP
Gas Panel
Front Bulkhead
Assembly
Pressure
Switch
Venturi
Pump
Exhaust Waste Out
Exhaust Supply
Ion Source
EXHAUST SUPPLY
MIN 55 PSIG MAX 60 PSIG
SHEATH
GAS
MAX 105 PSIG
CAD
GAS
MAX 60 PSIG
VALVE
WASTE OUT
EXHAUST
WASTE OUT
CURTAIN GAS
SUPPLY
MAX 60 PSIG
GAS 1 / GAS 2
MAX 105 PSIG

Hardware Guide
Document Number: D1000092204 B 13
CAUTION! Potential Instrument Damage: Shut off the sample flow before you
shut down the instrument.
3. In the Analyst software, deactivate the hardware profile and then close the
application software.
4. Stop the Analyst®Service. (See the Software Reference Guide for the
Analyst software.)
CAUTION! Leave the roughing pump running for a minimum of 15 minutes
after turning off the instrument’s main power switch. When the main power
switch is turned off, the turbo pumps continue to rotate without power for a
few minutes and continue to provide vacuum to the vacuum chamber. If, during
this time, the roughing pump is turned off, the pressure in the vacuum line
between the roughing pump and the turbo pumps increases. The increase in
back pressure can create an incorrect load on the turbo pumps’ bearings and
can cause a catastrophic failure of the turbo pumps.
CAUTION! If the instrument is to be shut down for any length of time, we
recommend that the vacuum chamber be vented to prevent exhaust from the
roughing pump being sucked back into the vacuum chamber. To vent the
vacuum chamber, follow steps 5 to 7.
CAUTION! If the vacuum chamber is not going to be vented while the
instrument is shut down, we recommend the roughing pump remain turned on
to prevent the pump exhaust from being sucked back into the vacuum chamber.
If you do not want to vent the vacuum chamber, skip steps 6 and 7.
5. Turn off the main power to the instrument. As you face the instrument
where the instrument name is visible and with the source to your left, the
switch is located on the bulkhead at the back right corner of the chassis.
6. After fifteen minutes, turn off the roughing pump. The power switch is
located beside the power supply input attachment on the roughing
pump.
7. Let the vacuum chamber vent naturally through the orifice for ten minutes
to allow the instrument to reach atmospheric pressure.
8. Unplug the mains power cord to the instrument from the rear bulkhead
near the main power switch for the instrument.
To turn on the system
Certain conditions outside the direct control of the instrument firmware must be
satisfied before the turbo pumps will be initiated. The Curtain Gas™ supply must
be turned on at the source, and the roughing pump must be turned on manually.
Note: The roughing pump has its own power toggle switch and must be turned
off manually. The roughing pump is not controlled remotely by the system
controller.

System Overview
14 Document Number: D1000092204 B
Interlocks (pressure switches) monitored by the firmware detect if the Curtain Gas
supply and the roughing pump are switched on. If the interlocks are not satisfied,
the turbo pumps are not initiated.
CAUTION! If the ion source is removed, the system electronics will be disabled,
interrupting any data acquisition tasks. The turbo pump and the vacuum system will not
be affected.
1. Turn on the roughing pump, if it was turned off. The power switch is
located beside the power supply input attachment on the roughing
pump.
2. Make sure that all gas supplies are flowing correctly to the instrument.
3. Plug the mains power cord into the bulkhead.
4. Turn on the main power switch.
5. Make sure that the GPIB (general purpose interface bus) cable is
connected to both the instrument and the computer.
6. Turn on the computer, if it was turned off, and then start the Analyst®
software.
Instrument Safe Fluids
The following fluids can safely be used with the instrument:
•Methanol (0 to 100%)
•Acetonitrile (0 to 100%)
•Water
•Formic acid (0 to 1%)
•Ammonium acetate (0 to 1%)
Source/Gas Parameters
The parameters in Table 1-1 are optimized for different LC conditions involving
flow rate. For more information about the parameters, see the Analyst®software
Help system.
Note: The roughing pump has its own power toggle switch and must be turned
on manually. The roughing pump is not controlled remotely by the system
controller.
Note: This list is not complete. If you are uncertain about a specific fluid, do not use the
fluid until confirmation is received from AB SCIEX that it will not present a hazard.
Note: We recommend that you run the instrument with the Curtain Gas™flow set to at
least 20 to maintain good instrument performance.

Hardware Guide
Document Number: D1000092204 B 15
Turbo V™ Ion Source Settings
Table 1-2 shows the recommended starting values for the X- and Y-axis
parameters. For more information, see the Turbo V™ Ion Source Operator’s
Guide.
Compound Parameters
In general, you can use the preset values for most of the parameters in Table 1-3.
For more information about the parameters, see the Analyst®software Help
system.
Table 1-1 Source/Gas Parameters
Parameter Value
Curtain Gas (CUR) 20
IonSpray Voltage (IS) 5000
Temperature (TEM) 700
Ion Source Gas (GS1) 60
Ion Source Gas 2 (GS2) 60
Table 1-2 Vertical and Horizontal Parameters
Parameter Value
X-axis 5
Y-axis 5
Table 1-3 Compound Parameters
Parameter Value
CAD Gas Use the preset value and optimize for your
compound.
DP (Declustering Potential) Use the preset value and optimize for your
compound.
EP (Entrance Potential) Use the preset value.
CXP (Collision Cell Exit
Potential)
Use the preset value and optimize for your
compound.
CE (Collision Energy) Use the preset value and optimize for your
compound.
IE1 (Ion Energy 1) — For
experienced instrument
operators only
Do not adjust.
IE3 (Ion Energy 3) — For
experienced instrument
operators only
Do not adjust.

System Overview
16 Document Number: D1000092204 B
Related Documentation
The guides and tutorials for the instrument and the Analyst software are installed
automatically with the software and are available from the Start menu: All
Programs > AB SCIEX. A complete list of the available documentation can be
found in the online Help. To view the Analyst software Help, press F1.
Technical Support
AB SCIEX and its representatives maintain a staff of fully-trained service and
technical specialists located throughout the world. They can answer questions
about the instrument or any technical issues that may arise. For more information,
visit the web site at http://www.absciex.com.

Document Number: D1000092204 B 17
2
3200 Series Parameters
The following tables contain generic parameters for the 3200 series of
instruments. The first number under each scan type is the preset value; the range
of numbers is the accessible range for each parameter.
Table 2-1 3200 Series Instrument Parameters
Parameter
ID Access
ID
Positive ion mode Negative ion mode
Q1 Q3 MS/MS Q1 Q3 MS/MS
CUR CUR 10 10 10 10 10 10
10 to 50 10 to 50 10 to 50 10 to 50 10 to 50 10 to 50
CAD CAD 0 2 3 0 2 3
n/a 0 to 12 0 to 12 n/a 0 to 12 0 to 12
IS(1) IS 5000 5000 5000 –4200 –4200 –4200
0 to 5500 0 to
5500
0 to
5500
–4500 to
0
–4500 to
0
–4500 to
0
IS(2) IS 1000 1000 1000 –1000 –1000 –1000
0 to 5500 0 to
5500
0 to
5500
–4500 to
0
–4500 to
0
–4500 to
0
IS(4) IS 1500 1500 1500 –1500 –1500 –1500
0 to 2500 0 to
2500
0 to
2500
–2500 to
0
–2500 to
0
–2500 to
0
NC(3) NC 1 1 1 –1 –1 –1
0 to 5 0 to 5 0 to 5 –5 to 0 –5 to 0 –5 to 0
NC(5) NC 1 3 3 –3 –3 –3
0 to 5 0 to 5 0 to 5 –5 to 0 –5 to 0 –5 to 0
TEM(1,3,4,5) TEM 0 0 0 0 0 0
0 to 750 0 to 750 0 to 750 0 to 750 0 to 750 0 to 750
OR DP 20 20 20 –20 –20 –20
0 to 400 0 to 400 0 to 400 –400 to 0 –400 to 0 –400 to 0
Q0 EP 10 10 10 –10 –10 –10
(EP = –Q0) 1 to 12 1 to 12 1 to 12 –12 to –1 –12 to –1 –12 to –1
IQ1 IQ1 Q0 +(– 1) Q0 +(–
1)
Q0 +(– 1) Q0 + 1 Q0 + 1 Q0 + 1
(IQ1 = Q0 + offset) –2 to –1 –2 to –1 –2 to –1 1 to 2 1 to 2 1 to 2
(1) TurboIonSpray®ion source (2) NanoSpray® ion source (3) DuoSpray™ ion source (1 =
TurboIonSpray ion source, 2 = Heated Nebulizer) (4) PhotoSpray®ion source (5) Heated
Nebulizer (6) 1 = On, 0 = Off

3200 Series Parameters
18 Document Number: D1000092204 B
ST ST Q0 +(–5) Q0
+(–5)
Q0 +(–5) Q0 + 5 Q0 + 5 Q0 + 5
(ST = Q0 + offset) –8 to –2 –8 to –2 –8 to –2 2 to 8 2 to 8 2 to 8
RO1 IE1 1 n/a 1 –1 n/a –1
(IE1 = Q0 – RO1) 0.5 to 2 0.5 to 2 –2 to
–0.5
–2 to
–0.5
RO1 RO1 n/a Q0 + (–
2)
n/a n/a Q0 + 2 n/a
(RO1 = Q0 + offset) –2 to
–0.5
0.5 to 2
IQ2 CEP Mass
Depende
nt
n/a Mass
Depend
ent
Mass
Depende
nt
n/a Mass
Depende
nt
(CEP = Q0 – IQ2) 0 to 188 0 to 188 –188 to 0 –188 to 0
IQ2 IQ2 n/a RO2 + 0 n/a n/a RO2 + 0 n/a
(IQ2 = RO2 + offset) 0 to 2 –2 to 0
RO2 CE n/a n/a 30 n/a n/a –30
(CE = Q0 – RO2) 5 to 130 –130 to
–5
RO2 RO2 –100 –20 n/a 100 20 n/a
–150 to
–20
–130 to
–5
20 to 150 5 to 130
IQ3 CXP n/a Mass
Depend
ent
5 n/a Mass
Depende
nt
–5
(CXP = RO2 – IQ3) 0 to 58 0 to 58 –58 to 0 –58 to 0
IQ3 IQ3 –125 n/a n/a 125 n/a n/a
–200 to
–100
100 to
200
RO3 IE3 n/a 4 4 n/a –4 –4
(IE3 = RO2 – RO3) 0.5 to 8 0.5 to 8 –8 to –0.5 –8 to
–0.5
RO3 RO3 –150 n/a n/a 150 n/a n/a
–200 to
–150
150 to
200
EX EX –200 –200 –200 200 200 200
n/a n/a n/a n/a n/a n/a
Table 2-1 3200 Series Instrument Parameters (cont’d)
Parameter
ID Access
ID
Positive ion mode Negative ion mode
Q1 Q3 MS/MS Q1 Q3 MS/MS
(1) TurboIonSpray®ion source (2) NanoSpray® ion source (3) DuoSpray™ ion source (1 =
TurboIonSpray ion source, 2 = Heated Nebulizer) (4) PhotoSpray®ion source (5) Heated
Nebulizer (6) 1 = On, 0 = Off

Hardware Guide
Document Number: D1000092204 B 19
DF DF –100 –100 –100 100 100 100
–400 to 0 –400 to
0
–400 to 0 0 to 400 0 to 400 0 to 400
CEM CEM 1800 1800 1800 1800 1800 1800
500 to
3297
500 to
3297
500 to
3297
500 to
3297
500 to
3297
500 to
3297
GS1 GS1 20 20 20 20 20 20
0 to 90 0 to 90 0 to 90 0 to 90 0 to 90 0 to 90
GS2 GS2 0 0 0 0 0 0
0 to 90 0 to 90 0 to 90 0 to 90 0 to 90 0 to 90
ihe(6) ihe 1 1 1 1 1 1
0 to 1 0 to 1 0 to 1 0 to 1 0 to 1 0 to 1
C2 C2 0 0 0 0 0 0
n/a n/a n/a n/a n/a n/a
XA3 XA3 0 0 0 0 0 0
n/a n/a n/a n/a n/a n/a
XA2 XA2 0 0 0 0 0 0
n/a n/a n/a n/a n/a n/a
IHT(2) IHT 40 40 40 40 40 40
0 to 250 0 to 250 0 to 250 0 to 250 0 to 250 0 to 250
svp(3) svp 1 1 1 1 1 1
1 to 2 1 to 2 1 to 2 1 to 2 1 to 2 1 to 2
Table 2-2 3200 QTRAP®System Parameters For LIT Scan Types Only
Parameter ID Access ID Positive ion mode Negative ion mode
CAD CAD High High
Low–Medium–High Low–Medium–High
FI2 CEP Mass Dependent Mass Dependent
0 to 188 –188 to 0
ROS CE 30 –30
(Q0 – RO2) 5 to 130 –5 to –130
AF2* AF2 100 100
0 to 200 0 to 200
*MS/MS/MS only ** Resolution Parameter
Table 2-1 3200 Series Instrument Parameters (cont’d)
Parameter
ID Access
ID
Positive ion mode Negative ion mode
Q1 Q3 MS/MS Q1 Q3 MS/MS
(1) TurboIonSpray®ion source (2) NanoSpray® ion source (3) DuoSpray™ ion source (1 =
TurboIonSpray ion source, 2 = Heated Nebulizer) (4) PhotoSpray®ion source (5) Heated
Nebulizer (6) 1 = On, 0 = Off

3200 Series Parameters
20 Document Number: D1000092204 B
AF3 AF3 Mass-Speed Dependent Mass-Speed Dependent
0 to 5 0 to 5
EXB EXB Mass-Speed Dependent Mass-Speed Dependent
–200 to 0 0 to 200
DF DF –400 400
n/a n/a
C2B C2B Mass-Speed Dependent Mass-Speed Dependent
–500 to 500 –500 to 500
CES CES 0 0
–50 to 50 –50 to 50
Table 2-2 3200 QTRAP®System Parameters For LIT Scan Types Only (cont’d)
Parameter ID Access ID Positive ion mode Negative ion mode
*MS/MS/MS only ** Resolution Parameter
Table of contents
Other AB Sciex Laboratory Equipment manuals
Popular Laboratory Equipment manuals by other brands
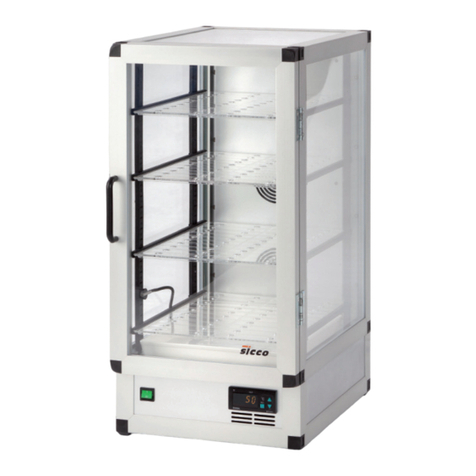
SICCO
SICCO V 1830-07 operating instructions
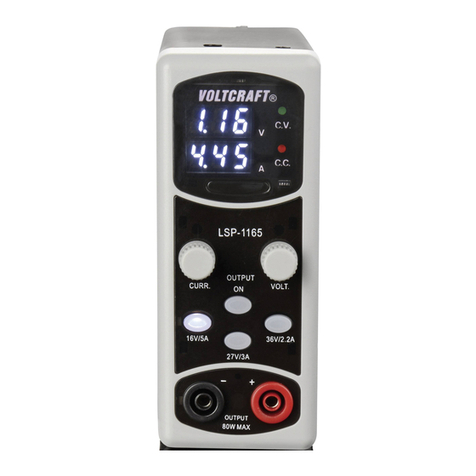
VOLTCRAFT
VOLTCRAFT LSP-1165 operating instructions
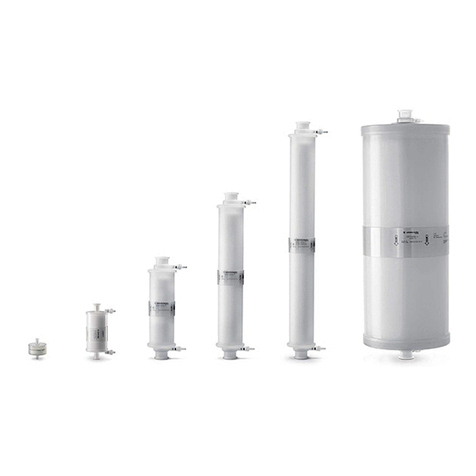
Sartorius Stedim Biotech
Sartorius Stedim Biotech Sartobind Q Series operating instructions
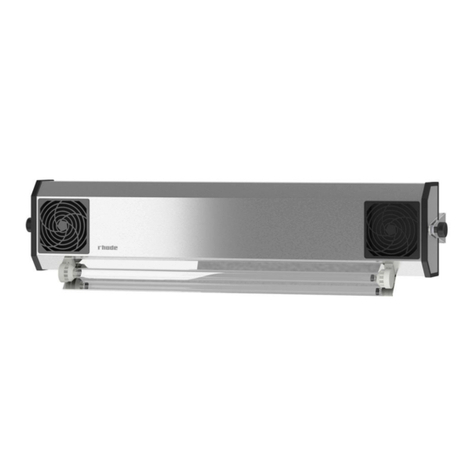
RHODE
RHODE INOX Series Manual instruction

BioLAB
BioLAB BCFHR-303 Operation manual

Hettich
Hettich ROTANTA 460 Repair instructions
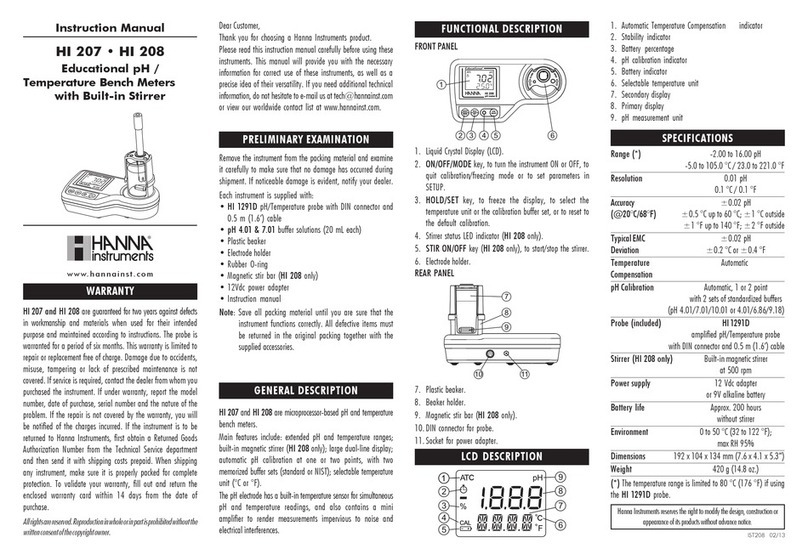
Hanna Instruments
Hanna Instruments HI 207 instruction manual
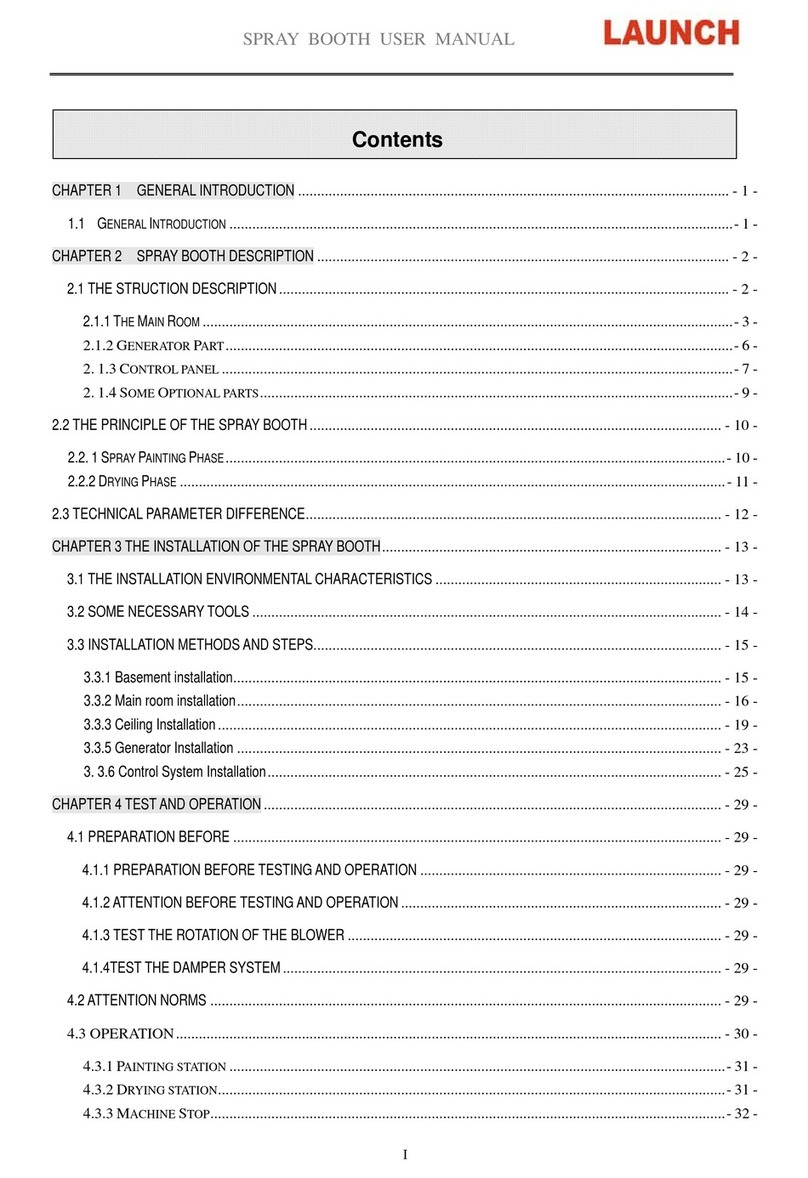
Launch
Launch CCH201 user manual
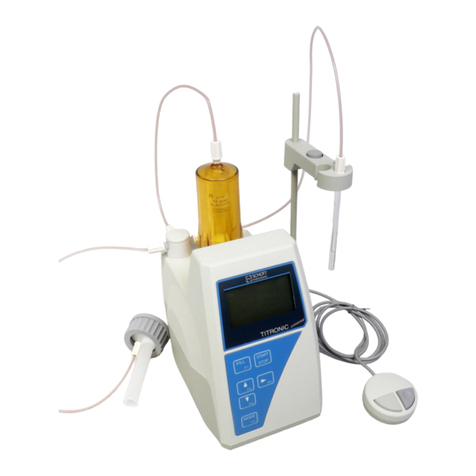
SCHOTT
SCHOTT TITRONIC universal operating instructions
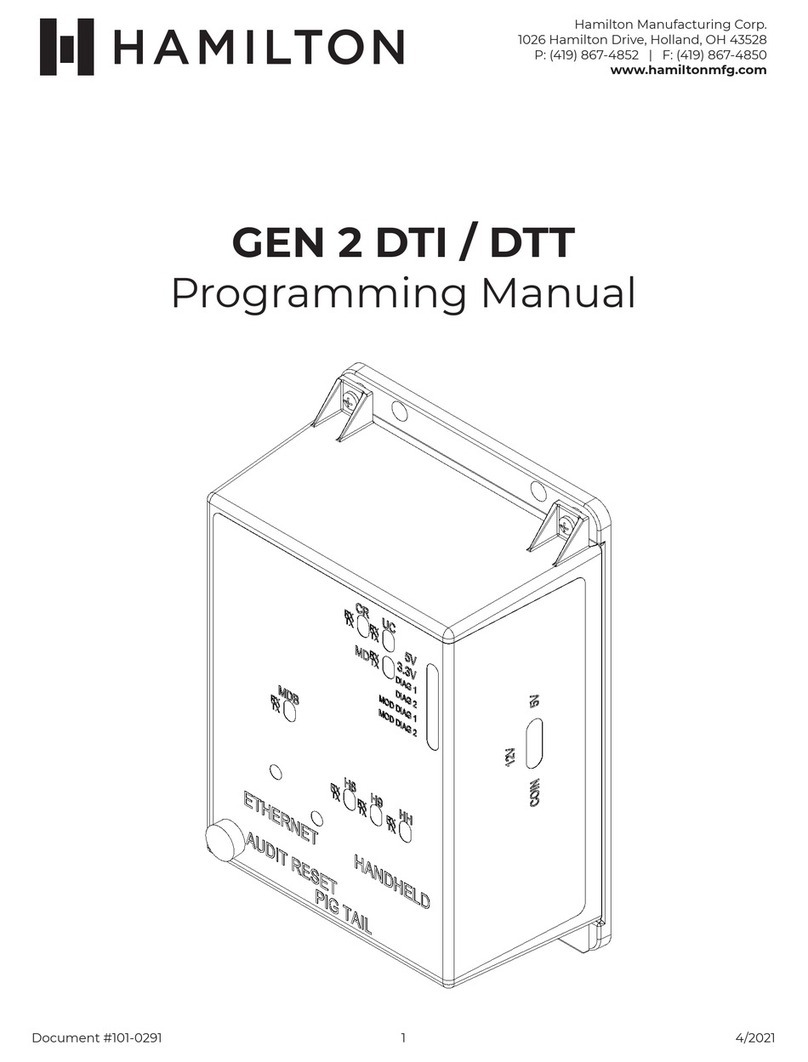
Hamilton
Hamilton GEN 2 DTI Programming manual

Agilent Technologies
Agilent Technologies 1260 Infinity user manual

Omni International
Omni International GLH 850 user manual