ABB SPEF 3A2 C Parts list manual

RESET
STEP
PROGRAM
ALARM
IRF
o
I
L3
I
L2
I
L1
I
∆
I
X1
RS 489 001 - AA Ser.No. 01234
SPEF 3A2 C
f
n= 50Hz
60Hz
aux
U
=24V-
Serial port
1
2
3
4
5
6
7
8
REGISTERS
L1
I
L2
I
L3
I
t
%
[ ]
( )
>
I
o
I
t
%
[ ]
( )
>
I
o
I
%
[ ]
∆
t
%
[ ]
>
( )
I
∆
0
1
2
3
4
5
6
OPERATION IND.
I
start
>
I
alarm
>
I
start
>
o
I
alarm
>
ostart
>
I
∆
alarm
>
I
∆
0
3>
I
SGF
SGB
I
>[ ]
A
s
>
t
I
>
o
[ ]
A
s
>
t
o
I
%
[ ]
∆>
s
>
t
∆
I
>
I
>
∆
[ ]
[ ]
[ ]
B470959B
SPA
118
[ ]
A
[ ]
A
[ ]
A
[ ]
A
x
SPEF 3A2 C
Fault indicator
User´s manual and Technical description

2
SPEF 3A2 C
Fault indicator
1MRS 751719-MUM EN
Issued 1999-11-25
Modified 2002-10-09
Version B (replaces 34 SPEF 1 EN1)
Checked MK
Approved OL
Data subject to change without notice
Contents Characteristics ................................................................................................................ 3
Application .....................................................................................................................3
Alarming functions ......................................................................................................... 3
Connection diagram ....................................................................................................... 4
Connections ................................................................................................................... 5
Technical data (modified 2002-10) ................................................................................. 7
Description of function .................................................................................................. 9
Resetting possibilities .................................................................................................... 10
Analog outputs for phase current, residual current or phase unbalance ......................... 10
Front panel ................................................................................................................... 11
Operation indicators ..................................................................................................... 11
Settings ......................................................................................................................... 12
Programming switches .................................................................................................. 13
Measured data .............................................................................................................. 15
Recorded data ............................................................................................................... 16
Main menus and submenus of settings and registers. .................................................... 18
Event codes................................................................................................................... 20
Data to be transferred over the bus ............................................................................... 21
Fault codes.................................................................................................................... 24
Maintenance and repairs ............................................................................................... 24
Spare parts .................................................................................................................... 24
Dimensions and instructions for mounting .................................................................. 25
Ordering numbers and information required with order .............................................. 25

3
Application The fault indicator SPEF 3A2 C is used in
disconnectorterminal units (DTU)withKOHU
24A1 or KOKU 072G3 current sensors to indi-
cate short-circuit faults, earth faults and broken
lines in a medium voltage distribution network.
With the fault indicator it is possible to get
information about measured and set values via a
disconnector terminal unit to a SPIDER or
MicroSCADA. This information can be used
e.g. to locate faults in a medium voltage distri-
bution network.
If no serial communication (SPA bus) is avail-
able, it is possible to use output relays and analog
outputs. The analog outputs are continuously
monitoring the condition of the network and
the output relays are signalling fault indications.
Fig. 1. Function of the fault indicator type SPEF 3A2 C.
Alarming
functions
Three-phase definite time
overcurrent indicator
Definite time earth-fault
indicator
Phase unbalance
indicator
Serial communication
51
51N
37
I
> alarm
I
0
> alarm
∆
I
alarm
Analog output
I
load
Analog output
I
0
Analog output ∆
I
IRF
SERIAL I/O
funcblck
Control
input BS
I
L1
I
L2
I
L3
Characteristics Three-phase overcurrent unit with definite time
characteristic
Phase unbalance indicator with definite time
characteristic
Neutral residual overcurrent unit
Alternative analog or digital outputs if SPA bus
not available
Digital display of measured and set values and
sets of data recorded at the moment when a fault
occurs
All measured values are displayed in amperes
All settings may be entered via the push-buttons
on the front panel or via a personal computer
Continuous self-supervision of hardware and
software. At a permanent internal fault all stages
and outputs are blocked. This fault signal can be
read via Weidmuller connection X1-6.

4
Connection
diagram
Fig 2. Connection diagram of the fault indicator.
Abbreviations of signal names
IL1, IL2, IL3 Phase currents
I0Residual current
∆I Phase unbalance
SGF, SGB Switchgroups for the selection of functions
ALARM Alarm indicator
IRF Internal fault
I> Alarm, I0Alarm and Output relays
∆I Alarm
Iload (phase current), Analog output signals
I0(residual current) and
∆I (phase unbalance)
1
SGF 1/5
t
o
>
I
o
>
SPEF 3A2 C
∆I> t
&
&
SGF1/6
1
1
∆
HW
∑
IL1
IL2
IL3
X1-8
X1-9
X1-10
X1-11
X1-14
X1-15
X1-16
X2
X1-3
X1-2
X1-1
X1-17
X1-18
SGF 1/1
I
max
-I
min
I
max
>1s/ 80ms
SGF 1/3
>1s/ 80ms
SGF 1/2
X1-7
X1-12
X1-13
SGB /3
SGB /2
SGB /1
IRF
t>
SGF 1/4
1
>1s/ 80ms
I>
+
-
X1-6
24 Vdc
BLOCK_CO.FH3
IL1
IL3
IL2
+
-
SPEC 3
KOHU 24A1
Motor
drive
Disconnector
Control unit
SPOC 21XC
step &
program
Unbalance contact
(SPST,NO)
Earth-fault contact
(SPST,NO)
step &
program
ALARM
Reset
Io (analog out)
I (analog out)
Unbal. (analog out)
Common
Overcurrent contact
(SPST,NO)
Common
Remote reset
input BS
Reset indicators, output relays and registers
Reset indicators and output relays
Reset indicators
Serial port
Filter
HW
step &
program
Filter
HW
Filter
HW
Can be used instead
of serial interface
load
load
load

5
Connections Inputs for phase current
Terminal Function
X1-1 IL1
X1-2 IL2
X1-3 IL2
X1-7 Common ground for phase currents
Cable's shield
Auxiliary supply voltage 24 V dc
Terminal Function
X1-17 +24 Vdc
X1-18 GND, internally connected to X1-7
Protective earth
Terminal Function
Protective earth terminal
Remote reset input BS
The fault indicator can be externally reset via the control input
Terminal Function
X1-12 Input+ 18…30 Vdc, 10 mA floating
X1-13 Input-
Output relays
Terminal Function
X1-8 For overcurrent, closing contact
X1-9 For residual current, closing contact
X1-10 For unbalance, closing contact
X1-11 Common
Internal device fault signal
Terminal Function
X1-6 Internal device fault. At an internal fault the voltage level drops from 5 V to
below 2 V
X1-18 GND, internally connected to X1-7

6
Analog output signals
Terminal Function
X1-14 Analog real-time readout (0…5 V) of maximum current of the phases L1-L3.
The scaling is user selectable by changing the range selector. This range selector is
settable with the serial parameter S10 or at front panel, submenu of the set-
ting I>.
X1-15 Analog real-time readout (0…5 V) of residual current I0. The scaling is user
selectable by changing the range selector. This range selector is settable with the serial
parameter S11 or at front panel, submenu of the setting I0>.
X1-16 Analog real-time readout (0…5 V) of phase unbalance ∆I.
X1-18 GND, internally connected to X1-7.
Serial communication connections
Current loop connection to SPOC 2XX with cable SPA-ZP27A07
Terminal Function
X2-2 TxD- to SPOC 2XX, 0/5 mA
X2-8 TxD+ to SPOC 2XX
X2-5 RxD+ from SPOC 2XX, 0/5-20 mA
X2-6 RxD- from SPOC 2XX
SPA logic/RS232 connection to PC with cable SPA-ZP5A
Terminal Function
X2-2 TxD, output
X2-3 RxD, input
X2-9 +10 Vdc, supply voltage for SPA-ZP5A
X2-7 GND
Fibre optic bus connection module SPA-ZC21
Terminal Function
X2-2 TxD, output
X2-3 TxD, input
X2-9 +10 Vdc, supply voltage for SPA-ZC21
X2-7 GND
Fibre optic bus connection module SPA-ZC17 or SPA-ZC22 with cable SPA-ZP14A2
Terminal Function
X2-2 TxD, output
X2-3 RxD, input
X2-7 GND
The fault indicator SPEF 3A2 C is interfaced with the SPA serial communication bus through a 9-
pole, D-type subminiature connector X2 located on the front panel of the device.

7
Technical data
(modified 2002-10)
Energizing inputs Primary Output of the
Current current sensors
(KOHU24A/KOKU
073G2)
Measurement range of phase input currents 0…700 A 0…0.174 A
*) Thermal withstand capability
- continuously 400 A 0.1 A
- for 1 s 20 kA 2.3 A
*) Dynamic current withstand,
half-wave value 50 kA 5.7 A
Measurement range of neutral
input current 0…70 A 0…0.02 A
Input impedance <100Ω
Rated frequency 50/60 Hz
*) According to IEC 60255-6 with the KOHU/KOKU current sensors and the connection box SPEC 3.
Overcurrent stage I>
Starting current I> 30…300 A
Starting time, typical 60 ms
Operate time t> 0.06…300 s
Resetting time, typical 60 ms
Drop-off/pick-up ratio, typical 0.95
Operation time accuracy ±2% of set value or ±25 ms
Operation accuracy ±3% of set value
Neutral overcurrent stage I0>
Starting current I0> 2…20 A
Starting time, typical 60 ms
Operating time t0> 0.1…300 s
Resetting time, typical 60 ms
Drop-off/pick-up ratio, typical 0.95
Operation time accuracy ±2% of set value or ±25 ms
Operation accuracy ±5% of set value and ±1% of Iload**)
**) Summation error is about 1% of measured load current.
Phase unbalance stage ∆I>
Starting current ∆I> 10…60%
Starting time, typical 90 ms
Operate time t∆> 1.0…300 s
Resetting time, typical 90 ms
Drop-off/pick-up ratio, typical 0.90
Operation time accuracy ±2% of set value or ±75 ms
Operation accuracy ±5% of displayed value
Output contact ratings
According to IEC 60255-0-20:
- Rated voltage 250 V ac
- Resistive load 2 A at 30 Vdc/250 Vac
- Inductive load (L/R < 7 ms)***) 2 A at 30 Vdc
- Making and conducting capacity 5 A, 0.5 s
- Minimum load 10 mA at 5 Vdc
***) L/R ≤7 ms according to contact ratings of the signal output relays used.

8
Analog outputs
Voltage range 0…5 V
Minimum load impedance 10 kΩ
Response delay < 500 ms
Inaccuracy Iload 5% or ±30 mV when current > 5 A
I05% or ±30 mV
∆I ±200 mV when Iphase
(IL1 or IL2 or IL3) max ≥10 A
External control inputs
External control voltage level 18…30 Vdc
Typical control current of input circuit 10 mA
Data transmission
Transmission mode serial bus
Protocol SPA bus
Selectable data transfer rates 4800 or 9600 Bd
Power supply
Supply 20…30 V dc
Power consumption 1.5…3 W (depending on relays
and indicators)
Test voltages
For output relays:
Insulation test according to IEC 60255-5 2 kV, 50 Hz, 1 min
Impulse test according to IEC 60255-5 5 kV, 1.2/50 µs, 0.5 J
Insulation resistance test according to IEC 60255-5 >100 MΩ, 500 Vdc
Disturbance tests
Current inputs are measured with the
connection box SPEC 3 and a connection cable
of at least two meter. High frequency interference
test voltage, inputs and output between them-
selves and to the fault indicator frame as per:
Common mode acc. to IEC 60255-22-1 2.5 kV, 1 MHz
Differential mode acc. to IEC 60255-2-1 1 kV, 1 MHz
Common mode acc. to ANSI C37.90.1-1989 2.5 kV, 1 MHz
Fast transient test IEC 60255-22-4, cl. III 2 kV
Electrostatic discharge test acc. to
IEC 60255-22-2, cl. III
- contact discharge 6 kV
- air discharge 8 kV
Environmental conditions
Enviromental condition tests are made on
SPEF 3A2 C without current sensors.
Specified ambient service temperature range -10°C to +55°C
Transport and storage temperature range -40°C to +70°C, 72 h + 72 h
Temperature influence on the operating values over
the specified ambient service temperature range <0.02%/°C
Climatic environmental tests
- dry heat test acc. to IEC 60068-2-2 +55°C/16h
- dry cold test acc. to IEC 60068-2-1 -10°C/16h
- damp heat test acc. to IEC 60068-2-30 RH=93%, 55°C, 6 cycles
Degree of protection by enclosure of the
device case as per IEC 60529 IP 20
Mass of the fault indicator about 1.3 kg

9
Description of
functions
Overcurrent unit
The overcurrent unit of the fault indicator SPEF
3A2 C is designed for single-phase, two-phase or
three-phase operation.
The stage starts if the current on one of the
phases exceeds the setting value of the stage
concerned. When starting the concerned stage
indicates starting on the digital display on the
front panel. If the overcurrent situation lasts
long enough to exceed the set operate time, the
stage that started provides an alarm signal. At
the same time the alarm indicator is lit with
yellow light. The yellow indicator remains on
although the stage resets. The alarm indicator is
reset with the reset button. The alarm signal is
always routed to overcurrent contact X1-8.
The start current setting range I> of the unit is
30…300 A. The operating time t> is set in
seconds within the setting range, 0.06…300 s.
The operation of overcurrent stage is provided
with a latching facility (SGF1/4) keeping the
alarm output energized, although the signal
which caused the operation disappears. The
output relays may be reset by pressing the PRO-
GRAM push-button, by pressing the RESET
and PROGRAM push-buttons simultaneously,
by remote control over the external input or over
the SPA bus using the command V101 or the
command V102.
The minimum pulse length for the signal deliv-
ered by the I> stage can be set to 80 ms or 1 s
(switch SGF1/1).
Note!
The latching function for I> stage (SGF1/4) will
overrun this function.
Earth fault unit The non-directionalearth fault indicatoris based
on the sum of phase currents.
The earth fault stage starts if the energizing
current I0exceeds the set starting level of the
stage concerned. When starting the concerned
stage indicates starting on the display on the
front panel. If the above mentioned criterions
are fulfilled long enough to exceed the set oper-
ate time, the stage that started provides an alarm
signal. At the same time the yellow alarm indi-
cator is lit with yellow light. The yellow indica-
tor remains on although the stage resets. The
alarm indicator is reset with the reset button.
The alarm signal is always routed to the earth
fault contact X1-9.
The setting range I0> of the earth fault unit is
2…20 A or ∞(indicated by "- - -"). The operate
time t0> is set in seconds within the setting range
0.1…300 s.
The operation of earth fault stage is provided
with a latching facility (SGF1/5) keeping the
alarm output energized, although the signal
which caused the operation disappears. The
output relays may be reset by pressing the PRO-
GRAM push-button, by pressing the RESET
and PROGRAM push-buttons simultaneously,
by remote control over the external input or over
the SPA bus using the command V101 or the
V102.
The operation of earth fault unit may be set out
of operation by means of switch SGF1/7. When
the earth fault unit is out of operation the
display indicates "- - -", which means that the
operation value is infinite.
The minimum pulse length for the signal deliv-
ered by the I0> stage can be set to 80 ms or 1 s with
switch SGF1/2.
Note!
The latching function for I0> stage (SGF1/5)
will overrun this function.

10
Analog outputs
for phase cur-
rent, residual
current or phase
unbalance
The fault indicator is provided with three analog
outputs to be connected to any external device.
When this facility is used, the max. phase cur-
rent, residual current or phase unbalance can at
any instant be read out by a meter or a program-
mable logic controller. The outputs are 0…5
Vdc signals. The scaling for phase current and
residual current outputs are dependent on the
setting of range selectors. These range selectors
can be changed via submenus on the front panel
or serial parameters S10 (I>) and S11 (I0>). The
selected range values for I> are 10 A, 20 A, 50 A,
100 A, 200 A and 500 A and for I0> 5 A,10 A,
20 A, 50 A and 100 A.
E.g: If the range selector parameter for phase
current is set to 500 then the scaling of the
primary current 0…500 A is 0…5 V over the
phase current output X1-14. Thus a phase cur-
rent of 100 A will give 1 V over output X1-14.
Phase unbalance
unit
The phase unbalance unit constitutes a definite
time current unbalance unit.
The unbalance of the power system is detected
by monitoring the highest and the lowest phase
current values, i.e. the unbalance = 100% x
(ILmax-ILmin)/ILmax. At full unbalance the dis-
play shows 100% which equals a negative phase
sequence current I2= 57.8%. If the unbalance
exceeds the set operating level ∆I, the unit starts
and a timer is started.
If the unbalance situation lasts long enough to
exceed the set operate time, the phase unbalance
stage provides an alarm signal. At the same time
the yellow alarm indicator is lit. The yellow
indicator remains on although the stage resets.
The alarm indicator is reset with the reset but-
ton. The alarm signal is always routed to unbal-
ance contact X1-10.
The setting range of the starting current is
10…60% or ∞(indicated as "- - -"). The basic
operate time is set within the range 1…300 s.
The operation of the phase unbalance stage ∆I is
provided with a latching facility (SGF1/6) keep-
ing the alarm output energized, although the
signal, which caused the operation disappears.
The output relays may be reset by pressing the
PROGRAM push-button, pressing the RESET
and PROGRAM push-buttons simultaneously,
by remote control over the external input or over
the SPA bus using the command V101 or the
V102.
The operation of unbalance unit may be set out
of operation by means of switch SGF1/8. When
the unbalance unit is set of operation the display
indicates "- - -", which means that the operation
value is infinite.
The minimum pulse length for the signal deliv-
ered by the ∆I stage can be set to 80 ms or 1 s with
switch SGF1/3. The latching function for the
∆I> stage (SGF1/6) will overrun this function.
Note!
To secure a proper operation of the phase
unbalance unit in a two-phase application, the
two phase currents should be summed up in the
third phase current transformer, i.e. a virtual
third phase is established.
Note!
To prevent the fault indicator unit from un-
wanted alarm signals, the earth fault and
unbalance units will be blocked by the overcur-
rent unit. Additionally, the unbalance will be
blocked in a single earth fault situation.
Resetting
possibilities
The start and operation indicators on the front
panel of the module, the latched output relays
and registers 1-8 can be reset locally or by remote
control as presented in the following table:
Resetting of start Resetting of latched Resetting indicators
and operation output relay of values recorded
RESET X
PROGRAM &
display off X X
STEP & RESET X X X
parameter V101 X X
parameter V102 X X X
BS & SGB/1=1 X
BS & SGB/2=1 X X
BS & SGB/3=1 X X X

11
RESET
STEP
PROGRAM
ALARM
IRF
o
I
L3
I
L2
I
L1
I
∆
I
X1
RS 489 001 - AA Ser.No.
01234
SPEF 3A2 C
f
n= 50Hz
60Hz
aux
U
=24V-
Serial port
1
2
3
4
5
6
7
8
REGISTERS
L1
I
L2
I
L3
I
t
%
[ ]
( )
>
I
o
I
t
%
[ ]
( )
>
I
o
I
%
[ ]
∆
t
%
[ ]
>
( )
I
∆
0
1
2
3
4
5
6
OPERATION IND.
I
start
>
I
alarm
>
I
start
>
o
I
alarm
>
ostart
>
I
∆
alarm
>
I
∆
0
3>
I
SGF
SGB
I
>[ ]
A
s
>
t
I
>
o
[ ]
A
s
>
t
o
I
%
[ ]
∆>
s
>
t
∆
I
>
I
>
∆
[ ]
[ ]
[ ]
B470959B
SPA
118
[ ]
A
[ ]
A
[ ]
A
[ ]
A
x
Front panel
Type designation
Registers and
Operation
indicators
Serial port
connection
Type number
and serial
number
Simplified device symbol
Indicators for measured current
values and Self-supervision
alarm indicator.
Display
Indicators for different setting
values. Reset and step display
push-button
Programming push-button
Alarm indicator
Output and input connections
Fig 3. Front panel of the fault indicator SPEF 3A2 C
Operation
indicators
Each stage has its own operation indicator shown
as a red figure to the left on the digital display.
Further, all stages have a common indicator
named "ALARM"; a yellow LED indicates that
the module has delivered an alarm signal.
The red operation indicator on the display re-
mains illuminated when the stage resets, thus
indicating which stage has operated.
If the start of a stage does not last long enough
to cause an alarm, the start indication on the
display is normally self-reset when the stage is
reset. If needed, the start indicators can be given
a latching function by means of switches SGF2/
1…3.
The following table explains the start and alarm
indicators on the display.
Indication nr Explanation
1 I> start The overcurrent stage I> has started
2 I> alarm The overcurrent stage I> has given an alarm
3I
0> start The earth fault stage I0> has started
4I
0> alarm The earth fault stage I0> has given an alarm
5∆I> start Stage ∆I> has started
6∆I> alarm Stage ∆I> has given an alarm
The red self-supervision alarm indicator IRF
indicates that the self-supervision system has
detected a permanent fault. The indicator is lit
about 1 minute after the fault has been detected.
At the same time the plug-in module delivers a
signal to the self-supervision system output
connection X1-6. Additionally, in most cases, a
fault code showing the nature of the fault ap-
pears on the display of the module. The fault
code, which consists of a red figure one and a
green code number, cannot be erased from the
display of the module by resetting. When a fault
occurs, the fault code should be recorded and
stated when service, is ordered.

12
Settings The setting values are shown by the right-most
three digits of the display. A lit indicator close to
a setting value symbol shows which setting value
is indicated on the display.
Note!
A symbol "//" in the text indicates that the
following item is found in a submenu.
Setting Parameter Setting range
(Primary values)
I> (A) The starting current of the I> stage // 30…300 A
Selection of the operative range expressed in amperes deter- 10 A, 20 A,
mined by the max. phase current, corresponding to the output 50 A, 100 A,
signal 0…5 V. 200 A, 500 A
t> (s) The operate time of the I> stage, expressed in seconds 0.06…300 s
I0> (A) The starting current of the I0> stage // 2…20 A
Selection of the operative range expressed in amperes deter- 5 A, 10 A,
mined by the max. I0current, corresponding to the output 20 A, 50 A,
signal 0…5 V. 100 A
t0> (s) The operate time of the I0> stage, expressed in seconds 0.1…300 s
∆I> Setting ∆I> for the unbalance indicator in per cent of the 10…60%
highest phase current, expressed as a percentage
t∆(s) The operate time of the ∆I> stage, expressed in seconds 1.0…300 s
SGF1 The checksum of the programming switchgroups SGF1, SGF2
SGF2 and SGB. The functions of the different switches are described
SGB in separate paragraphs. An example of calculating the checksum
is given in the general description of the D-type SPC relay
modules

13
Programming
switches
Additional functions required by individual
applications are selected by means of the
switchgroup SGF, indicated on the front panel.
The number of the switches, 1…8, and the
switch positions, 0 and 1, are indicated when the
switchgroups are being set. In normal service
only the checksums are shown.
Switchgroups SGF1
and SGF2 Switch Function Factory
setting
SGF1/1 Choosing the minimum pulse length for the signal delivered by the 0
I> stage.
Note! The latching function for the I> stage (SGF1/4) will overrun this
function.
When SGF1/1=0, the minimum pulse length of the signal delivered
by the I> stage is 1 s.
When SGF1/1=1, the minimum pulse length of the signal delivered
by the I> stage is 0.08 s.
SGF1/2 Choosing the minimum pulse length for the signal delivered by the 0
I0> stage.
Note! The latching function of the I0> stage (SGF1/5) will overrun
this function.
When SGF1/2=0, the minimum pulse length of the signal delivered
by the I0> stage is 1 s.
When SGF1/2=1, the minimum pulse length of the signal delivered
by the I0> stage is 0.08 s.
SGF1/3 Choosing the minimum pulse length for the signal delivered by the 0
∆I> stage.
Note! The latching function for the ∆I> stage (SGF1/6) will overrun
this function.
When SGF1/3=0, the minimum pulse length of the signal delivered
by the ∆I> stage is 1 s.
When SGF1/3=1, the minimum pulse length of the signal delivered
by the ∆I> stage is 0.08 s.
SGF1/4 Latching function for the alarm signal of the overcurrent stage I> 0
When SGF1/4=0, the alarm signal returns to its initial state, i.e. the
output relay drops off, when the signal causing th operation falls
below the starting level.
When SGF1/4=1, the alarm signal remains on, i.e. the output relay
remains operated although the measuring signal falls below the
starting level.
Then the alarm signal of the overcurrent stage I> must be reset by
pressing the RESET and PROGRAM push-buttons simultaneously
or by using the command V101. When the display is off the signals
can also be reset by pressing only the PROGRAM push button.

14
Switch Function Factory
setting
SGF1/5 Latching function for the alarm signal of earth fault stage I0>. 0
When SGF1/5=0, the alarm signal returns to its initial state, i.e. the
output relay drops off, when the signal causing the operation falls
below the starting level.
When SGF1/5=1, the alarm signal remains on, i.e. the output relay
remains operated although the measured signal falls below the
starting level.
Then the alarm signal of the earth fault stage I0> must be reset by
pressing the RESET and PROGRAM push-buttons simultaneously
or using command V101. When the display is off the signals can also
be reset by pressing only the PROGRAM push button.
SGF1/6 Latching function for the alarm signal of unbalance stage ∆I>. 0
When SGF1/6=0, the alarm signal returns to its initial state, i.e. the
output relay drops off, when the signal causing the operation falls
below the starting level.
When SGF1/6=1, the alarm signal remains on, i.e. the output relay
remains operated although the measured signal falls below the
starting level.
Then the alarm signal of the unbalance stage ∆I> must be reset by
pressing the RESET and PROGRAM push-buttons simultaneously
or by using command V101. When the display is off the signals can
also be reset by pressing only the PROGRAM push button.
SGF1/7 The earth fault stage can be set out of operation by means of 0
this switch.
SGF1/8 The unbalance stage can be set out of operation by means of 0
this switch.
SGF2/1 Switches SGF2/1…3 are used for selecting the mode of operation 0
SGF2/2 of the start indicators of the different stages and the LEDs for the 0
SGF2/3 measured currents. When the switches are in position 0 the start 0
indicators are all automatically reset when the fault is cleared.
In order to get a hand reset start indication for the stages, their
respective switches have to be in position 1. When the switches are
in position 0 the LEDs for the measured currents are not affected by
a start, and when the switches are in position 1 it is possible to get
information of which phase activated a start.
When SGF2/1=1, the start indicator of the overcurrent stage I> has
to be manually reset.
When SGF2/2=1, the start indicator of the earth fault stage I0> has
to be manually reset.
When SGF2/3=1, the start indicator of the unbalance stage ∆I> has
to be manually reset.
SGF2/4 Reserved for future use 0
SGF2/5 Reserved for future use 0
SGF2/6 Reserved for future use 0
SGF2/7 Reserved for future use 0
SGF2/8 Reserved for future use 0

15
Remote reset input
switchgroup SGB Switch Function Factory
setting
SGB/1 Remote reset of indicators 0
When SGB/1=0, the indicators are not reset by signal BS.
When SGB/1=1, the indicators are reset by signal BS.
SGB/2 Remote reset of indicators and output relays 0
When SGB/2=0, the indicators and output relays are not reset by
signal BS.
When SGB/2=1, the indicators and output relays are reset by
signal BS.
SGB/3 Remote reset of indicators, output relays and memorized values. 0
When SGB/3=0, the indicators, output relays and memorized values
are not reset by signal BS.
When SGB/3=1, the indicators, output relays and memorized values
are reset by signal BS.
SGB/4 Reserved for future use 0
SGB/5 Reserved for future use 0
SGB/6 Reserved for future use 0
SGB/7 Reserved for future use 0
SGB/8 Reserved for future use 0
Measured data The measured values are shown by the three
right-most digits of the display. The currently
measured data are indicated by an illuminated
LED indicator on the front panel.
Indicator Measured data
IL1 Line current on phase L1 in ampere
IL2 Line current on phase L2 in ampere
IL3 Line current on phase L3 in ampere
I0Neutral current in ampere
∆I The actual value of phase unbalance in per cent of the highest phase current

16
Recorded data When the fault indicator provides an alarm
signal, the current values at the moment of the
alarm, the duration of the start of the different
units and other parameters are stored in a
five-place memory stack. A new event moves the
old values up one place and adds the new value
to the first place of the stack which contains
registers 1…8. Five events are memorized - if a
sixth alarm occurs, the oldest set of values will be
lost. A master reset (pressing the push-buttons
RESET and PROGRAM simultaneously) of
the relay erases all the contents of the register
blocks.
The left-most red digit displays the register
address and the other three digits the recorded
information.
Note! A symbol "//" in the text indicates that the
following item is found in a submenu.
Register Recorded information
1 Line phase current L1 (n) measured in ampere //
Event (n-1) value of line phase current L1 //
Event (n-2) value of line phase current L1 //
Event (n-3) value of line phase current L1 //
Event (n-4) value of line phase current L1 //
2 Line phase current L2 (n) measured in ampere //
Event (n-1) value of line phase current L2 //
Event (n-2) value of line phase current L2 //
Event (n-3) value of line phase current L2 //
Event (n-4) value of line phase current L2 //
3 Line phase current L3 (n) measured in ampere //
Event (n-1) value of line phase current L3 //
Event (n-2) value of line phase current L3 //
Event (n-3) value of line phase current L3 //
Event (n-4) value of line phase current L3 //
4 Duration of the latest starting situation (n) of overcurrent stage I> as a percentage
of the set operating time t>. When the concerned stage has alarmed the counter
reading is 100 per cent. //
Duration of event (n-1) starting of stage I> //
Duration of event (n-2) starting of stage I> //
Duration of event (n-3) starting of stage I> //
Duration of event (n-4) starting of stage I> //
Number of startings of the stage I> in the range 0…255.
5 Neutral current measured in ampere //
Event (n-1) value of neutral current //
Event (n-2) value of neutral current //
Event (n-3) value of neutral current //
Event (n-4) value of neutral current //
6 Duration of the latest starting situation (n) of stage I0> expressed as a percentage
of the set operate time t0>. When the concerned stage has alarmed the counter
reading is 100 per cent. //
Duration of event (n-1) starting of stage I0>//
Duration of event (n-2) starting of stage I0>//
Duration of event (n-3) starting of stage I0>//
Duration of event (n-4) starting of stage I0>//
Number of startings of the stage I0> in the range 0…255.
7 Phase unbalance ∆I in per cent of the highest phase current //
Event (n-1) value of phase unbalance ∆I//
Event (n-2) value of phase unbalance ∆I//
Event (n-3) value of phase unbalance ∆I//
Event (n-4) value of phase unbalance ∆I//

17
Register Recorded information
8 Duration of the latest starting situation (n) of stage ∆I> expressed as a percentage
of the set operating time t∆. When the concerned stage has alarmed the counter
reading is 100 per cent. //
Duration of event (n-1) starting of stage ∆I> //
Duration of event (n-2) starting of stage ∆I> //
Duration of event (n-3) starting of stage ∆I> //
Duration of event (n-4) starting of stage ∆I> //
Number of startings of the stage ∆I> in the range 0…255.
0 Display of external control signals. The right-most digit indicates the state of
the control input of the unit. The following states may be indicated:
0 = no control signal
1 = the control signal is active
From this register "0" it is possible to move on to the TEST mode, where the
alarming signals of the module are activated one by one in the following order
and indicated by the flashing setting indication LED:
Alarm from I>
Alarm from I0>
Alarm from ∆I>
For further details see the description "General characteristics of D-type SPC
relay units".
A The address code of the fault indicator, required by the serial communication
system. //
The selection of the data transfer rate of the serial communication. //
The bus traffic monitor indicating the operating state of the serial communication
system. If the module is connected to a system including a control data commu-
nicator and if the communication system is operating, the counter reading of the bus
traffic monitor will be zero. Otherwise the numbers 0…255 are continuously
rolling in the display. //
Password required for the remote control of the settings. The password must
always be entered via the serial communication before a setting can be altered
remotely.
I
>[ ]
A
s
>
t
I
>
o
[ ]
A
s
>
t
o
I
%
[ ]
∆>
s
>
t
∆
[ ]
[ ]
[ ]
The registers 1…8 are set to zero by pressing the
push-buttons RESET and PROGRAM simul-
taneously. The registers are also cleared if the
auxiliary power supply to the module is inter-
rupted. The address code of the unit, the data
transfer rate of the serial communication and
the password are not erased by a voltage failure.
Instructions for setting the address and the data
transfer rate are given in the manual "General
characteristics of D type SPC relay units".
The recorded information contains a time stamp
which includes date and time in the form at:
yy-dd hh, mm; ss, sss.
The time stamps of the registers can be read via
theserial busby using parametersV19, V39…99
(see page 21 "Data to be transferred over the
bus"). After a power supply interruption or
start-up, date and time should be set via the bus
by using parameters T and D (se page 23).

18
Main menus and
submenus of
settings and
registers
Normal status, display off
Current on phase L1
Current on phase L2
Current on phase L3
Neutral current Io
4
Operate time t>
1
1
Start value Io>
2
1
Setting of functional
switchgroup SGF1
Event (n-1)
value of phase L1 Event (n-2)
value of phase L1
Latest memorized, event (n)
value of phase L1
112
Event (n-1)
value of phase L2 Event (n-2)
value of phase L2
Latest memorized, event (n)
value of phase L2
212
Event (n-1)
value of phase L3 Event (n-2)
value of phase L3
Latest memorized, event (n)
value of phase L3
31 2
Duration of event (n-1)
starting of stage I> Duration of event (n-2)
starting of stage I>
1 2
61 2
71 2
812
Duration of event (n-1)
starting of stage Io> Duration of event (n-2)
starting of stage Io>
Duration of event (n-1)
starting of stage ∆I> Duration of event (n-2)
starting of stage ∆I>
Status of external relay
blocking / control signal
0
Communication rate
setting [Bd] Loss of bus traffic time
counter 0..255 s
Relay unit identification
address for communication
A12
Start value I>
0 000
IRF t> to> t∆>
Duration of event (n)
starting of stage I>
Duration of event (n)
starting of stage Io>
Duration of event (n)
starting of stage ∆I>
SUBMENUS FWD. STEP 1 s
REV. STEP 0.5 s
M
A
I
N
M
E
N
U
R
E
V.
S
T
E
P
.5
s
F
W
D.
S
T
E
P
1
s
1
2
3
4
6
7
8
A
MAIN MENU SUBMENUS
STEP 0.5 s PROGRAM 1 s
Phase unbalance
∆
I
Operate time to>
Start value ∆I>
Operate time t∆>
Setting of functional
switchgroup SGF2 Setting of functional
switchgroup SGB
Range selector of
I
load
analog output
Range selector of
I
o
analog output
51 2
Latest memorized event (n)
value of neutral current
5
Event (n-1) value of
neutral current Event (n-2) value of
neutral current
Latest memorized, event (n)
value of phase unbalance ∆IEvent (n-1) value of
phase unbalance ∆IEvent (n-2) value of
phase unbalance ∆I
Fig 4. Main menus and submenus of the fault indicator SPEF 3A2 C

19
The measures required for entering a submenu
or a setting mode, the setting procedure and
how to use the TEST mode are described in
detail on data sheet "General characteristics of
the D-type relay modules". Below a short guide.
Desired step or operation Push-button Action
Forward step in main or submenu STEP Press > 0.5 s
Rapid scan forward in main menu STEP Keep depressed
Reverse step in main or submenu STEP Press < 0.5 s
Entering a submenu from the PROGRAM Press 1 s
main menu
Entering or leaving a setting mode PROGRAM Press for 5 s
Increasing a value in a setting mode STEP
Moving the cursor in a setting mode PROGRAM Press about 1 s
Storing a value in a setting mode STEP & PROGRAM Press simultaneously
Resetting memorized values + STEP & PROGRAM
output relays
Resetting output relays PROGRAM Note!
Display must be off
Event (n-3)
value of phase L1 Event (n-4)
value of phase L1
Event (n-3)
value of phase L2 Event (n-4)
value of phase L2
Event (n-3)
value of phase L3 Event (n-4)
value of phase L3
Duration of event (n-3)
starting of stage I> Duration of event (n-4)
starting of stage I>
Event (n-3) value of
neutral current
Duration of event (n-3)
starting of stage Io> Duration of event (n-4)
starting of stage Io>
Duration of event (n-4)
starting of stage ∆I
Password for
altering settings
4
4
4
3
3
3
3
3
3
3
3
4
4
4
4
4
3
Duration of event (n-3)
starting of stage ∆I
1
2
3
4
5
6
7
8
A
Event (n-3) value of
neutral current
Event (n-3) value of
phase unbalance ∆IEvent (n-4) value of
phase unbalance ∆I
5Number of startings of the
stage I> since last reset
5
5
Number of startings of the
stage Io> since last reset
Number of startings of the
stage ∆I> since last reset

20
Event codes When the fault indicator module SPEF 3A2 C
is linked to a control data communicator over
the SPA bus, the module will provide time-
stamped events e.g. to a printer. The events are
printed out in the format: time, user-specified
text and event code. The events are generated on
start, alarm, resetting and output relay opera-
tion. Every function has its own code designa-
tion from E1…E18. Masking parameters can be
used to inhibit events from being generated by
one or several functions. An event buffer is
capable of memorizing up to eight events. If
more than eight events occur before the content
of the buffer has been sent to the communicator
an overflow event "E51" is generated. This
event has to be reset by writing a command "0"
to parameter C over the SPA bus. More infor-
mation about the serial communication over the
SPA bus can be found in the document "SPA-
BUS COMMUNICATION PROTOCOL",
34 SPACOM 2 EN1.
Code Event Number Default value
representing of the factor
the event
E1 Start of stage I> 1 1
E2 Start of stage I> reset 2 0
E3 Alarm of stage I> 4 1
E4 Alarm of stage I> reset 8 0
E5 Start of stage I0>161
E6 Start of stage I0> reset 32 0
E7 Alarm of stage I0>641
E8 Alarm of stage I0> reset 128 0
Default checksum for mask V155 85
E9 Starting of stage ∆I> 1 1
E10 Starting of stage ∆I> reset 2 0
E11 Alarming of stage ∆I> 4 1
E12 Alarming of stage ∆I> reset 8 0
Default checksum for mask V156 5
E13 Output signal I> alarm activated 1 1
E14 Output signal I> alarm reset 2 0
E15 Output signal I0> alarm activated 4 1
E16 Output signal I0> alarm reset 8 0
E17 Output signal ∆I> alarm activated 16 1
E18 Output signal ∆I> alarm reset 32 0
Default checksum for mask V157 21
E50 Restarting * -
E51 Overflow of event register * -
E52 Temporary interruption in data communication * -
E53 No response from the module
over the data communication * -
E54 The module responds again
over the data communication * -
0 Not included in the event reporting
1 included in the event reporting
* No code number
- Cannot be programmed
Note!
The event codes E52…E54 are only generated
by the data communicator unit. (SACO 100M,
SRIO 1000M, etc.)
Table of contents
Other ABB Measuring Instrument manuals

ABB
ABB 6553 Series User manual
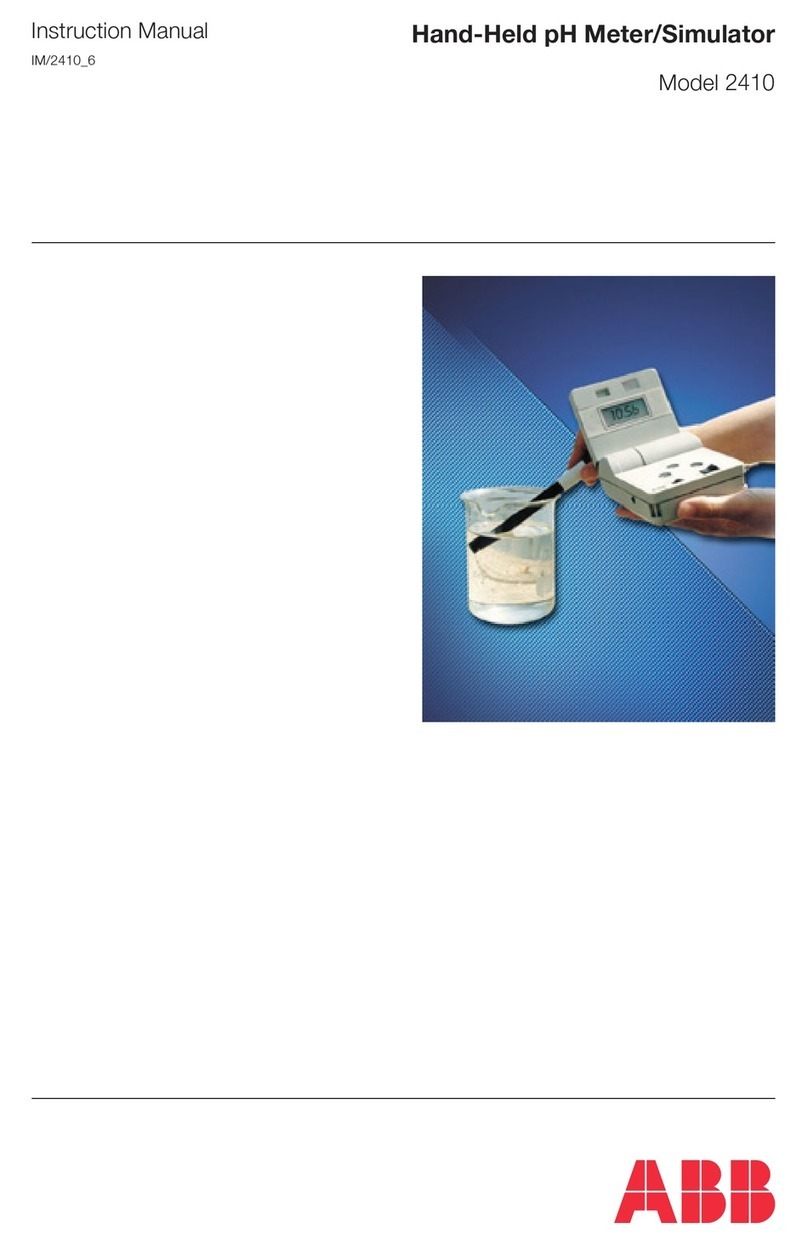
ABB
ABB 2410 User manual
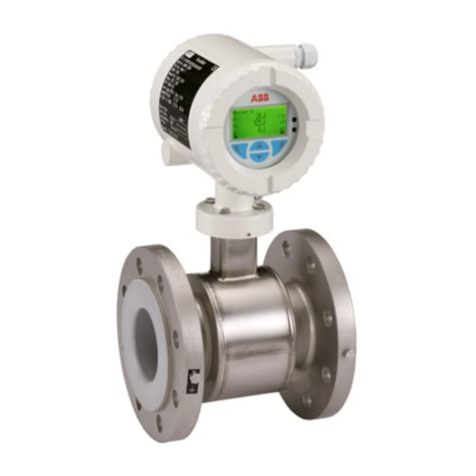
ABB
ABB HART FEP300 Installation and operation manual

ABB
ABB Navigator 600 Series User manual
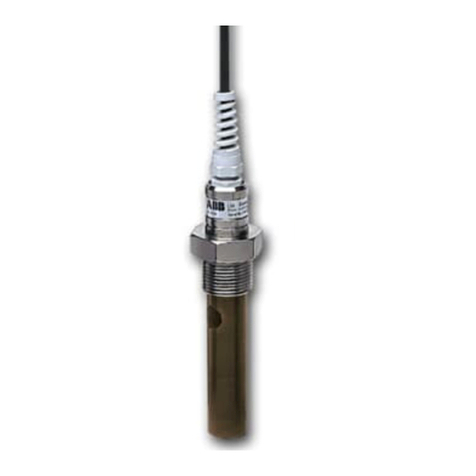
ABB
ABB AC211 User manual
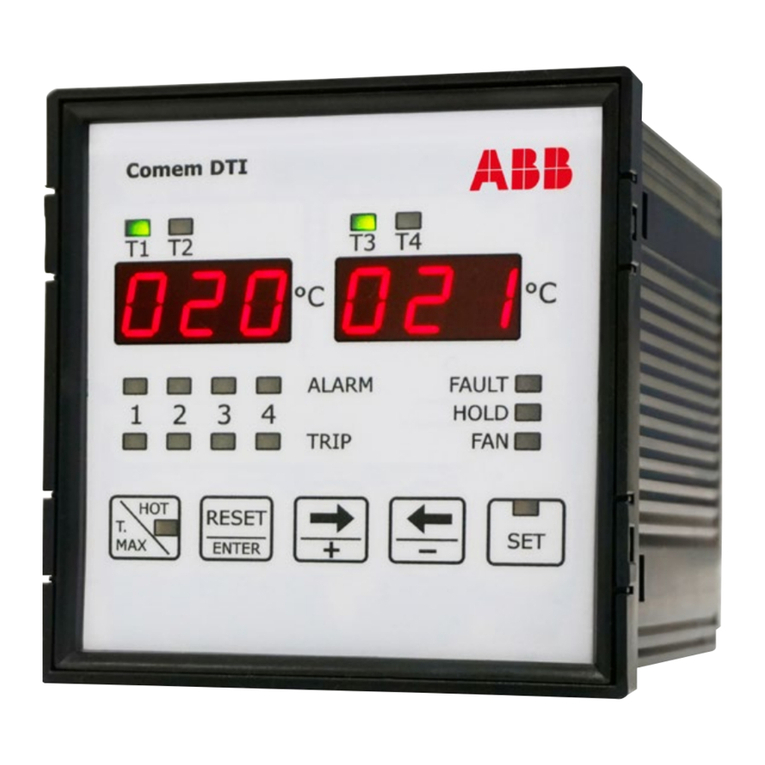
ABB
ABB Comem DTI User manual

ABB
ABB 4620 User manual

ABB
ABB Gas Sampling Probe 2 User manual
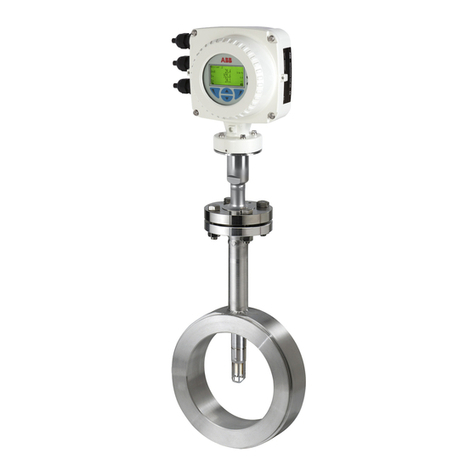
ABB
ABB SensyMaster FMT430 User manual

ABB
ABB C1900 Series User manual
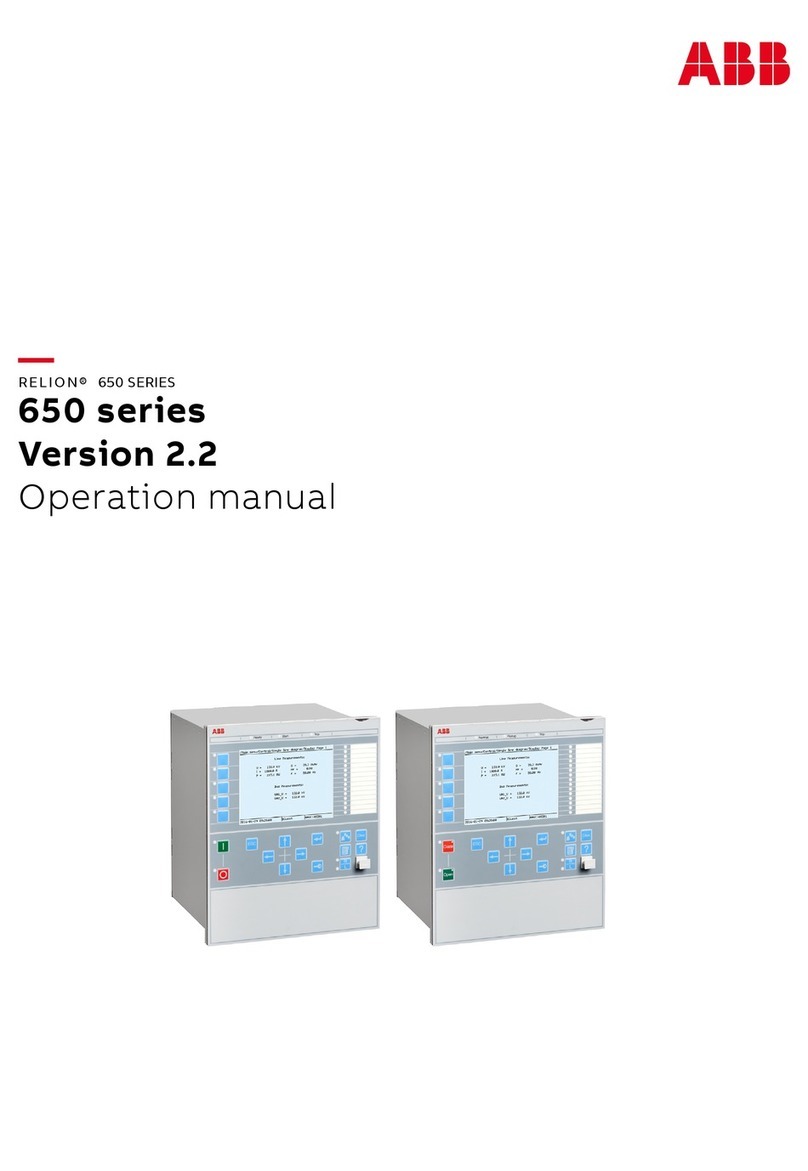
ABB
ABB RELION 650 SERIES User manual

ABB
ABB Aztec 600 User manual

ABB
ABB AX418 User manual

ABB
ABB VA Master FAM540 Training manual
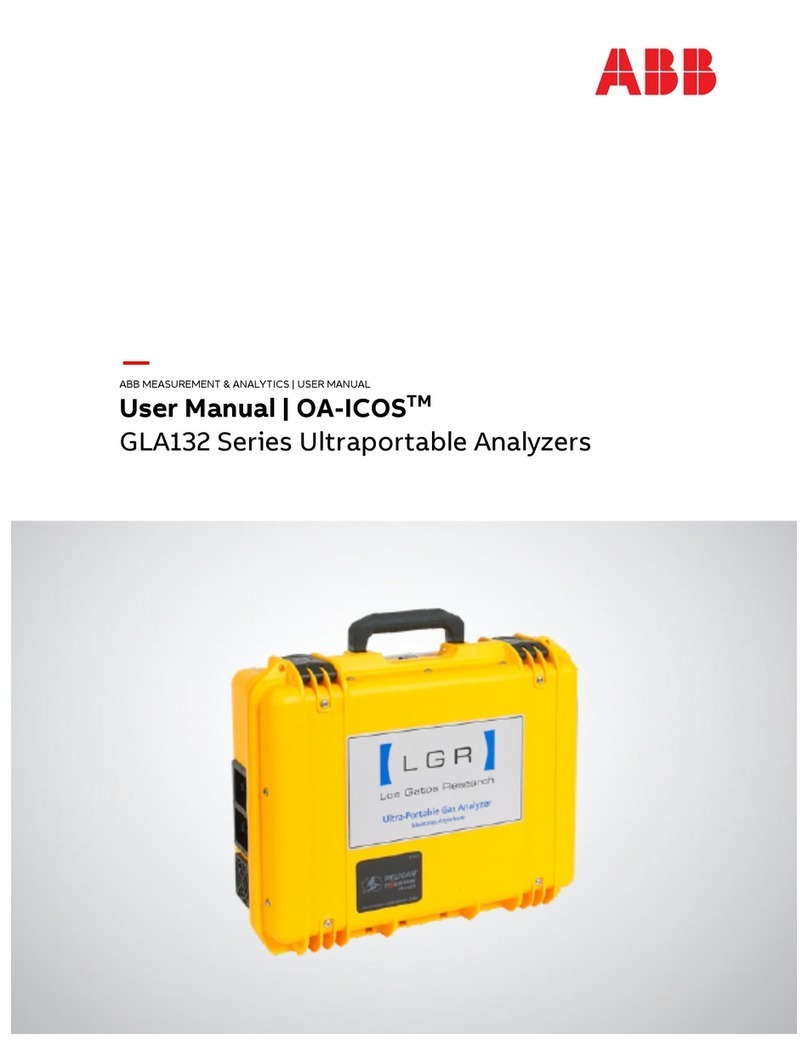
ABB
ABB GLA132 Series User manual

ABB
ABB COPA-XM 3000 Series User manual
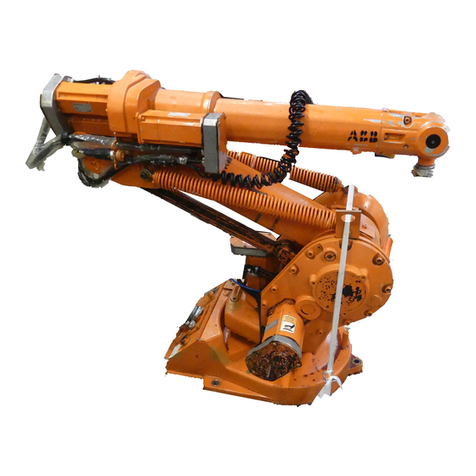
ABB
ABB Levelmeter 2000 User manual
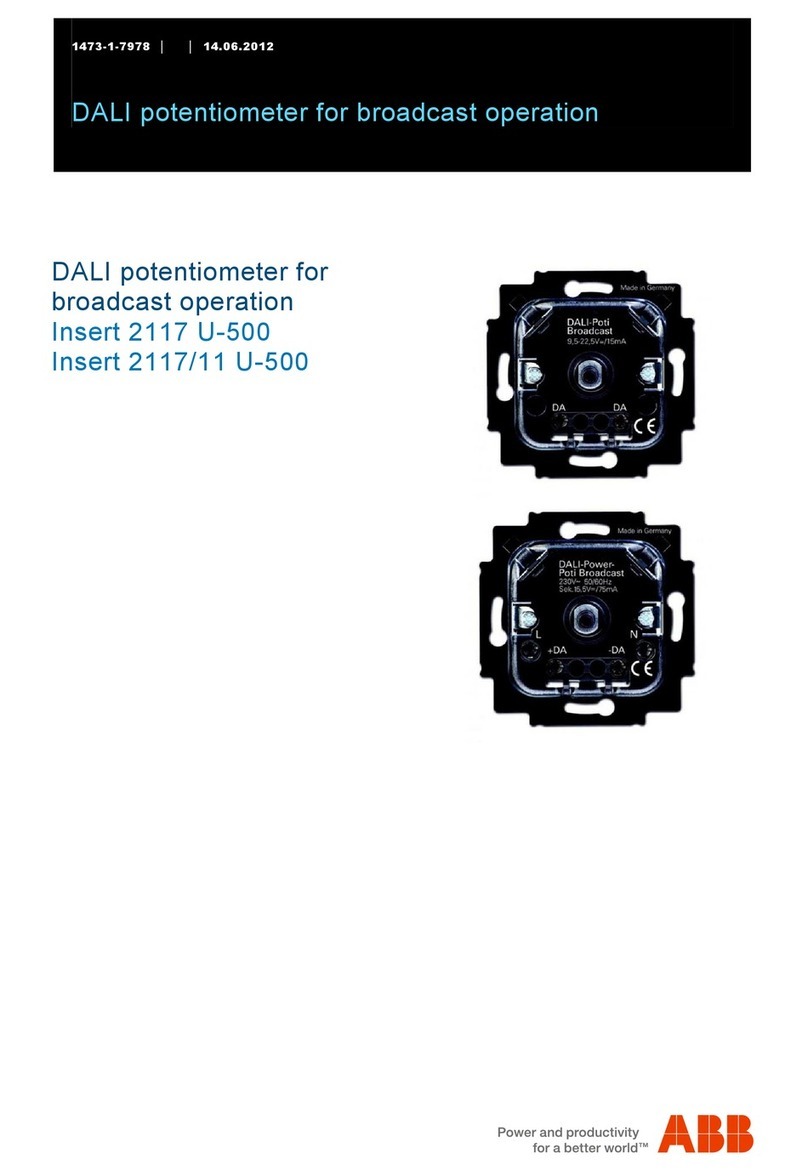
ABB
ABB 2117 U-500 User manual

ABB
ABB AnalyzeIT 7600 Series User manual
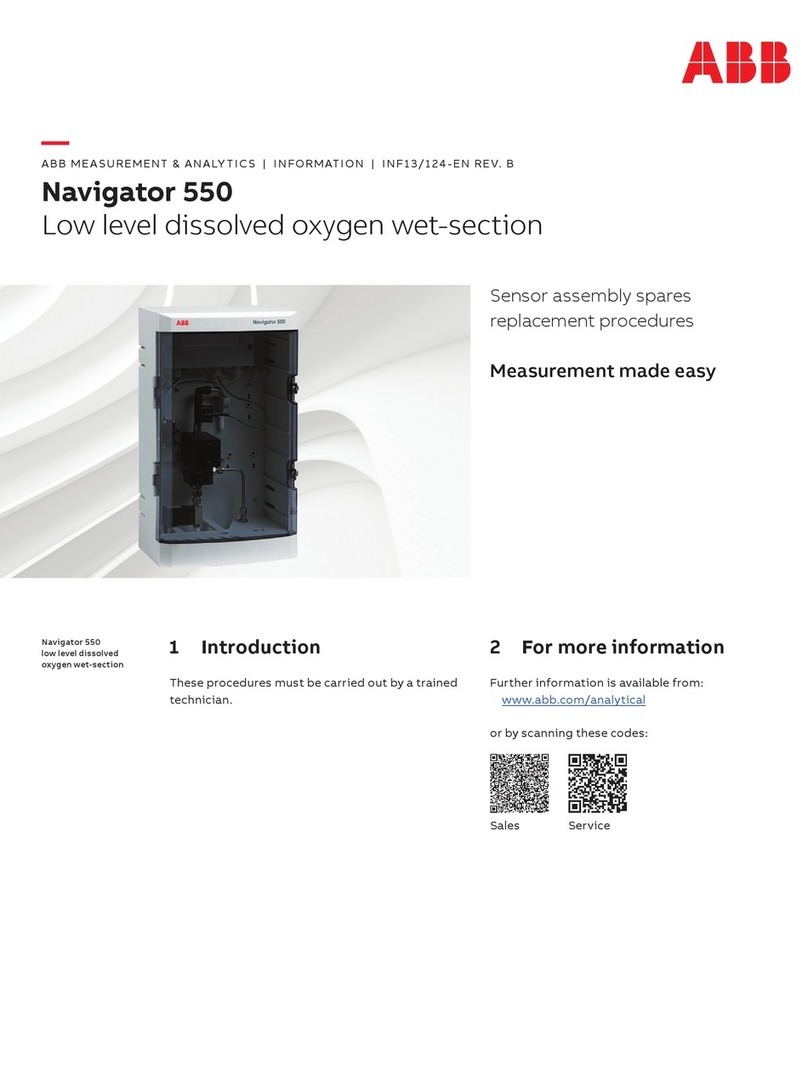
ABB
ABB Navigator 550 User manual