ABB CoriolisMaster FCM2000 Installation and operation manual

CI/FCM2000-EN CoriolisMaster FCM2000
EN
English
Commissioning Instruction
Mass Flowmeter
CoriolisMaster FCM2000
P R OF I
BU S
PROCESS FIELD BUS
®


CI/FCM2000-EN CoriolisMaster FCM2000 EN - 1
Neu
Mass Flowmeter
CoriolisMaster FCM2000
Commissioning Instruction - EN
CI/FCM2000-EN
07.2017
Rev. D
Original instruction
Manufacturer:
ABB Automation Products GmbH
Measurement & Analytics
Dransfelder Straße 2
D-37079 Göttingen
Germany
Tel.: +49 551 905-0
Fax: +49 551 905-777
Customer service center
Phone: +49 180 5 222 580
Fax: +49 621 381 931-29031
© Copyright 2017 by ABB Automation Products GmbH
Subject to changes without notice
This document is protected by copyright. It assists the user in safe and efficient operation of the device. The contents of this
document, whether whole or in part, may not be copied or reproduced without prior approval by the copyright holder.
Contents

Contents
2 - EN CoriolisMaster FCM2000 CI/FCM2000-EN
1Safety....................................................................................................................................................................3
1.1General information and notes for the reader ................................................................................................3
1.2Intended use...................................................................................................................................................4
1.3Improper use ..................................................................................................................................................4
1.4Technical limit values .....................................................................................................................................4
1.5Approved media .............................................................................................................................................5
1.6Target groups and qualifications ....................................................................................................................5
1.7Safety instructions for transport .....................................................................................................................5
1.8Safety instructions for electrical installation ...................................................................................................6
1.9Safety instructions for operation.....................................................................................................................6
2Design and function ............................................................................................................................................7
2.1ATEX and IECEx device overview .................................................................................................................7
3Transport..............................................................................................................................................................8
3.1Inspection .......................................................................................................................................................8
3.2General information on transport ...................................................................................................................8
4Installation............................................................................................................................................................9
4.1Electrical connection ......................................................................................................................................9
4.1.1Electrical connections between the transmitter and the flowmeter sensor.............................................9
4.1.2Electrical connections between the transmitter and the peripherals ....................................................10
4.2Ex relevant specifications.............................................................................................................................11
4.2.1ATEX/IECEx Ex approval......................................................................................................................12
5Commissioning..................................................................................................................................................14
5.1General information......................................................................................................................................14
5.2Information for safe operation – ATEX, IECEx ............................................................................................15
5.2.1Inspection ..............................................................................................................................................15
5.2.2Output Circuits ......................................................................................................................................15
5.2.3NAMUR Contact....................................................................................................................................16
5.2.4Information on changing the installation ...............................................................................................17
6Parameterization................................................................................................................................................19
6.1Data entry.....................................................................................................................................................19
6.2Entering data in short form ...........................................................................................................................21
7Appendix ............................................................................................................................................................22
7.1Other applicable documents ........................................................................................................................22
7.2Approvals and certifications .........................................................................................................................22

Safety
CI/FCM2000-EN CoriolisMaster FCM2000 EN - 3
1 Safety
1.1 General information and notes for the reader
Read these instructions carefully prior to installing and commissioning the device.
These instructions are an important part of the product and must be kept for later use.
These instructions are intended as an overview and do not contain detailed information on all
designs for this product or every possible aspect of installation, operation and maintenance.
For additional information or in case specific problems occur that are not discussed in these
instructions, contact the manufacturer.
The content of these instructions is neither part of any previous or existing agreement, promise
or legal relationship nor is it intended to change the same.
This product is built based on state-of-the-art technology and is operationally safe. It has been
tested and left the factory in a safe, maintenance-free state. The information in the manual must
be observed and followed in order to maintain this state throughout the period of operation.
Modifications and repairs to the product may only be performed if expressly permitted by these
instructions.
Only by observing all of the safety information and all safety/warning symbols in these
instructions can optimum protection of both personnel and the environment, as well as safe and
fault-free operation of the device, be ensured.
Information and symbols directly on the product must be observed. They may not be removed
and must be fully legible at all times.
Important
• An additional document with Ex safety information is available for
measuring systems that are used in potentially explosive areas (Applies to
FM / CSA only).
• Ex safety information is an integral part of this manual. As a result, it is
crucial that the installation guidelines and connection values it lists are also
observed.
The icon on the name plate indicates the
following:

Safety
4 - EN CoriolisMaster FCM2000 CI/FCM2000-EN
1.2 Intended use
This device is intended for the following uses:
• To convey liquids and gases (fluids), including unstable ones
• To meter the mass flow of the fluid directly
• To meter the volumetric flow of the fluid (indirectly via mass flow and density)
• To measure fluid density
• To measure fluid temperature
The following items are included in the intended use:
• Read and follow the instructions in this manual.
• Observe the technical ratings; refer to the section 1.4 „Technical limit values“.
• Use only allowed liquids for measurement; refer to the section1.5 „Approved media“.
1.3 Improper use
The following are considered to be instances of improper use of the device:
• Operation as a flexible adapter in piping, e.g., to compensate for pipe offsets, pipe vibrations,
pipe expansions, etc.
• As a climbing aid, e. g., for mounting purposes
• As a support for external loads, e. g., as a support for piping, etc.
• Adding material, e. g., by painting over the name plate or welding/soldering on parts
• Removing material, e. g., by spot drilling the housing
Repairs, alterations, and enhancements, or the installation of replacement parts, are only
permissible insofar as these are described in the manual. Approval by
ABB Automation Products GmbH must be sought for any activities beyond this scope. Repairs
performed by ABB-authorized specialist shops are excluded from this.
1.4 Technical limit values
The meter has been designed for use exclusively within the values stated on the name plate
and within the technical limit values specified on the data sheets.
The following technical limit values must be observed:
• The permissible pressure (PS) and the permissible fluid temperature (TS) must not exceed
the pressure/temperature ratings (see the section titled "Specifications").
• The maximum and minimum operating temperature limits must not be exceeded or
undershot.
• The permissible operating temperature must not be exceeded.
• The housing protection type must be observed during operation.
• The flowmeter sensor must not be operated in the vicinity of powerful electromagnetic fields,
e.g., motors, pumps, transformers, etc. A minimum spacing of approx. 1 m (3.28 ft) must be
maintained. For installation on steel parts (e.g., steel brackets), a minimum spacing of 100
mm (4") must be maintained. (These values have been calculated on the basis of IEC 801-2
and IEC TC77B.)

Safety
CI/FCM2000-EN CoriolisMaster FCM2000 EN - 5
1.5 Approved media
When using media, please note:
• Media (fluids) may only be used if, based on the state of the art or the operating experience
of the user, it can be assured that chemical and physical properties of the components
coming into contact with the fluids will not be adversely affected during the operating period.
• Specifically chloride media can cause not visible corrosion damages to all media wetted
components so that fluid can lead. The suitability of these materials for each application by
the operator to examine.
• Media (fluids) with unknown properties or abrasive media may only be used if the operator
can perform regular and suitable tests to ensure the safe condition of the meter.
• Observe the information on the name plate.
1.6 Target groups and qualifications
Installation, commissioning, and maintenance of the product may only be performed by trained
specialist personnel who have been authorized by the plant operator to do so. The specialist
personnel must have read and understood the manual and comply with its instructions.
Prior to using corrosive and abrasive measurement media, the operator must check the level of
resistance of all parts coming into contact with the wetted parts. ABB Automation Products
GmbH will gladly support you in selecting the materials, but cannot accept any liability in doing
so.
The operators must strictly observe the applicable national regulations with regards to
installation, function tests, repairs, and maintenance of electrical products.
1.7 Safety instructions for transport
Observe the following instructions:
• The center of gravity is off center.
• The flow direction must correspond to the direction indicated on the device, if labeled.
• Comply with the maximum torque for all flange connections.
• Install the devices without mechanical tension (torsion, bending).
• Install flange devices with coplanar counter flanges.
• Only install devices for the intended operating conditions and with suitable seals.
• Secure the flange bolts and nuts against pipeline vibrations.

Safety
6 - EN CoriolisMaster FCM2000 CI/FCM2000-EN
1.8 Safety instructions for electrical installation
The electrical connection may only be made by authorized specialist personnel according to the
electrical plans.
The electrical connection information in the manual must be observed; otherwise, the electrical
protection type may be adversely affected.
Ground the measurement system according to requirements.
1.9 Safety instructions for operation
During operation with hot fluids, contact with the surface may result in burns.
Aggressive fluids may result in corrosion or abrasion of the parts that come into contact with the
medium. As a result, pressurized fluids may escape prematurely.
Wear to the flange gasket or process connection gaskets (e.g., aseptic threaded pipe
connections, Tri-Clamp, etc.) may enable a pressurized medium to escape.
When using internal flat gaskets, these can become embrittled by CIP/SIP processes.

Design and function
CI/FCM2000-EN CoriolisMaster FCM2000 EN - 7
2 Design and function
Important
An additional document with Ex safety instructions is available for measuring systems that are
used in explosion hazardous areas (Applies to FM / CSA only).
As a result, it is crucial that the specifications and data it lists are also observed.
2.1 ATEX and IECEx device overview
Standard/Non-Ex Zone 1/21
Type ME22 A, U ... MS21 A, U ME27/28 B, E MS26 B, E
1. Remote mount
design
(small nominal
diameters)
Transmitter and
flowmeter sensor
−Standard/non-Ex
−Ex Zone 2/21, 22
−Ex Zone 1/21
Type ME24/25 A, U ... MS26 B, E
2. Remote mount
design
(small nominal
diameters)
Transmitter
−Standard/non-Ex
−Ex Zone 2/21, 22
Flowmeter sensor
−Ex Zone 1/21
Fig. 1: FCM2000 overview
G00387

Transport
8 - EN CoriolisMaster FCM2000 CI/FCM2000-EN
3 Transport
3.1 Inspection
Check the devices for possible damage that may have occurred during transport. Damages in
transit must be recorded on the transport documents. All claims for damages must be claimed
without delay against the shipper and before the installation.
3.2 General information on transport
Observe the following when transporting the device to the measurement site:
• The center of gravity is off center.
• Flanged units may not be lifted by the converter housing or terminal box.

Installation
CI/FCM2000-EN CoriolisMaster FCM2000 EN - 9
4 Installation
4.1 Electrical connection
4.1.1 Electrical connections between the transmitter and the flowmeter sensor
Connecting transmitter ME2 to flowmeter sensor MS2
G00389
92 91 85 86 87 88 89 90 93 94 95 96
3
11
11
11
11 21 6 7891054
ME27
Me28
M 22, 23, 24, 25E
MS21
Ms26
11
Fig. 2
91 / 92 Driver
93 / 94 / 95 / 96 Temperature
85 / 86 Sensor 1
87 / 88 Sensor 2
1Red
2Brown
3Green
4Blue
5Gray
6Violet
7White
8Black
9Orange
10Yellow
11"PA" equipotential bonding. When connecting transmitter to
flowmeter sensor MS26, transmitter also has to be connected to
"PA".

Installation
10 - EN CoriolisMaster FCM2000 CI/FCM2000-EN
4.1.2 Electrical connections between the transmitter and the peripherals
Input and output signals, supply power ME2/MS2
G00813
31 32 33 34 51 52 41 42 81 82
N
2-
L
1+
6
7
54321
51 52 81 82 41 42 31 32 33 34
3
77
2654
N
2-
L
1+
1
ME22
ME23
ME24
ME25
7
7
MS21
ME27
ME28
MS26
7
Fig. 3
1Supply power
Line voltage: UAC 100 ... 230 V AC, frequency 50/60 Hz,
terminals L, N,
Low voltage: UAC 24 V, frequency 50/60 Hz, terminals 1+, 2-
Low voltage: UDC 24 V
2Current output 1: can be selected via software
2a: function: active
Terminals: 31, 32; 0/4 … 20 mA (0 Ω≤RB ≤560 Ω, ME27/28: 0
Ω<= RB <= 300 Ω)
2b: alternate function: passive (option D)
Terminals: 31, 32; 4 ... 20 mA (0 Ω≤RB ≤600 Ω)
Source voltage 12 ≤Uq≤30 V
3Current output 2: can be selected via software
Function: passive
Terminals: 33, 34; 4 … 20 mA (0 Ω≤RB ≤600 Ω)
Source voltage 12 ≤Uq≤30 V
4a Passive pulse output, terminals: 51, 52
f
max = 5 kHz, pulse width 0.1 … 2,000 ms
Setting range: 0.001 … 1,000 pulses/unit
"Closed": 0 V ≤UCEL ≤2 V, 2 mA ≤ICEL ≤65 mA
"Open": 16 V ≤UCEH ≤30 V, 0 mA ≤ICEH ≤0.2 mA
4b Active pulse output
U = 16 ... 30 V, load ≥150 Ω, fmax = 5 kHz,
5Contact output, passive
Terminals: 41, 42
"Closed": 0 V ≤UCEL ≤2 V, 2 mA ≤ICEL ≤65 mA
"Open": 16 V ≤UCEH ≤30 V, 0 mA ≤ICEH ≤0.2 mA
6Contact input, passive
Terminals: 81, 82
"On": 16 V ≤UKL ≤30 V
"Off": 0 V ≤UKL ≤2 V
7"PA" equipotential bonding. When transmitter ME2 is connected
to flowmeter sensor MS26, transmitter ME2 also has to be
connected to "PA".
Important
An additional document with Ex safety instructions is available for measuring systems that are
used in explosion hazardous areas (Applies to FM / CSA only).
As a result, it is crucial that the specifications and data it lists are also observed.

Installation
CI/FCM2000-EN CoriolisMaster FCM2000 EN - 11
4.2 Ex relevant specifications
Important
An additional document with Ex safety instructions is available for measuring systems that are
used in explosion hazardous areas (Applies to FM / CSA only).
As a result, it is crucial that the specifications and data it lists are also observed.
Overview of the different output options
ATEX/IECEx Zone 2 ATEX/IECEx Zone 1
I
Output option A/B
in the order number
- Current output 1: active
- Current output 2: passive
- Pulse output: active/passive,
switchable
- Contact input and output: passive
- Current output 1: active
- Current output 2: passive
- Pulse output: active/passive,
switchable
- Contact input and output: passive
II
Output option D
in the order number
- Current output 1: passive
- Current output 2: passive
- Pulse output: active/passive,
switchable
- Contact input and output: passive
Version I: Active/Passive current outputs
Types: ME21/ME22/ME23/ME24 and ME25
Protection type "nA" (Zone 2) General operating values
U
(V)
I
(mA)
Ub
(V)
Ib
(mA)
Current output 1
Active
Terminals 31/32
30 30 30 30
Current output 2
Passive
Terminals 33/34
30 30 30 30
Pulse output
Active or passive
Terminals 51/52
30 65 30 65
Contact output
Passive
Terminals 41/42
30 65 30 65
Contact input
Passive
Terminals 81/82
30 10 30 10
All inputs and outputs are electrically isolated from each other and from the supply power.

Installation
12 - EN CoriolisMaster FCM2000 CI/FCM2000-EN
Types: ME26/ME27 and ME28
Protection type "nA"
(Zone 2)
General
operating values
Protection type "e"
(Zone 1)
Protection type "ib"
(Zone 1)
Ui
(V)
Ii
(mA)
Ub
(V)
Ib
(mA)
U
(V)
I
(A)
Uo
(V)
Io
(mA)
Po
(mW)
Co
(nF)
Copa
(nF)
Lo
(mH)
Current output 1
Active
Terminals 31/32
Terminal 32 is connected to
"PA"
20 100 500 217 0 3.8
30
30
30
30
60
35
Ui
(V)
Ii
(mA)
Pi
(mW)
Ci
(nF)
Cipa
(nF)
Li
(mH)
60 100 500 2.4 2.4 0.17
Current output 2
Passive
Terminals 33/34
Terminal 34 is connected to
"PA"
30 30 30 30 60 35 30 100 760 2.4 2.4 0.17
Pulse output
Passive
Terminals 51/52
30 65 30 65 60 35 15 30 115 2.4 2.4 0.17
Contact output
Passive
Terminals 41/42
30 65 30 65 60 35 15 30 115 2.4 2.4 0.17
Contact input
Passive
Terminals 81/82
30 10 30 10 60 35 30 60 500 2.4 2.4 0.17
All inputs and outputs are electrically isolated from each other and from the supply power. Only current outputs 1 and 2 are not electrically
isolated from one another.
Version II: Passive/Passive current outputs
Types: ME26/ME27 and ME28
Protection type "nA"
(Zone 2)
General
operating values
Protection type "e"
(Zone 1)
Protection type "ia"
(Zone 1)
Ui
(V)
Ii
(mA)
Ub
(V)
Ib
(mA)
U
(V)
I
(A)
Ui
(V)
Ii
(mA)
Pi
(mW)
Ci
(nF)
Cipa
(nF)
Li
(mH)
Current output 1
Passive
Terminals 31/32
30 30 30 30 60 35 60 300 2000 0,47 0,47 0,17
Current output 2
Passive
Terminals 33/34
30 30 30 30 60 35 60 300 2000 0,47 0,47 0,17
Pulse output
Passive
Terminals 51/52
30 65 30 65 60 35 60 300 2000 0,47 0,47 0,17
Contact output
Passive
Terminals 41/42
30 65 30 65 60 35 60 300 2000 0,47 0,47 0,17
Contact input
Passive
Terminals 81/82
30 10 30 10 60 35 60 300 2000 0,47 0,47 0,17
All inputs and outputs are electrically isolated from each other and from the supply power.
Important
If the protective conductor (PE) is connected in the flowmeter's terminal box, you must ensure that no dangerous
potential difference can arise between the protective conductor (PE) and the equipotential bonding (PA) in the
potentially explosive area.
4.2.1 ATEX/IECEx Ex approval
EC type-examination certificate in accordance with ATEX and IECEx
KEMA ATEX 08ATEX0150 X, KEMA 08 ATEX 0151X, or IECEx KEM 08.0034X

Installation
CI/FCM2000-EN CoriolisMaster FCM2000 EN - 13
4.2.1.1 Flowmeter sensor MS2 in accordance with ATEX
Model MS2
Zone 1
Ambient temperature -20 ... 50 °C (-4 ... 122 °F)
Temperature class
T1 180 °C (356 °F)
T2 180 °C (356 °F)
T3 180 °C (356 °F)
T4 125 °C (257 °F)
T5 80 °C (176 °F)
T6 −
Ambient and process conditions:
Tamb -20 ... 50 °C (-4 ... 122 °F)
Tmedium -50 ... 180 °C (-58 ... 356 °F)
Protection class IP 65, IP 67, and NEMA 4X/type 4X
Specific coding applies for ATEX and IECEx, depending on the design of the flowmeter sensor (compact or separate); see the overview on page
7).
Design MS26
Zone 1 Designation
ATEX II 2 G Ex ib IIC T5 ... T3
4.2.1.2 Transmitter ME2, separate design, in accordance with ATEX and IECEx
Ambient and process conditions:
Tamb -40 ... 60 °C (-40 ... 140 °F)
Protection class IP 65, IP 67, and NEMA 4X/type 4X
Specific coding applies for ATEX and IECEx, depending on the design of the flowmeter sensor (compact or separate); see the overview on page
7).
Design ME21 / ME24 / ME25 M, N
Designation
ATEX II 3 G Ex nR II T6
II 3 G Ex nR [nL] IIC T6
II 2 D Ex tD A21 IP6X T115 °C
FNICO field device
No fieldbus, no M12 plug
FNICO fieldbus, no M12 plug
No M12 plug
FNICO fieldbus
IECEx Ex nR II T6
Ex nR [nL] IIC T6
Ex tD A21 IP6X T115 °C
FNICO field device
No fieldbus, no M12 plug
FNICO fieldbus, no M12 plug
No M12 plug
FNICO fieldbus
Design ME27/ME28 for flowmeter sensor MS2
Zone 1 Designation
ATEX
Version II/III
II 2 G Ex d e [ia] [ib] IIC T6 2 passive analog outputs, outputs "ia"/"e", depending on user
wiring, or FISCO fieldbus
Version I II 2 G Ex d e [ib] IIC T6 Active/passive analog outputs, outputs "ib"/"e", depending on
user wiring
Version II/III II 2 D Ex tD [iaD] A21 IP6X T115 °C 2 passive analog outputs, outputs "ia"/"e", depending on user
wiring, or FISCO fieldbus
Version I II 2 D Ex tD [ibD] A21 IP6X T115 °C Active/passive analog outputs, outputs "ib"/"e", depending on
user wiring
FISCO field device FISCO fieldbus
Important
When using the device in explosion hazardous areas, the additional temperature
specifications in the section titled "Ex relevant specifications" on the data sheet or in the the
separate Ex safety instructions (SM/FCM2000/FM/CSA) must be observed.

Commissioning
14 - EN CoriolisMaster FCM2000 CI/FCM2000-EN
5 Commissioning
Important
An additional document with Ex safety instructions is available for measuring systems that are
used in explosion hazardous areas (Applies to FM / CSA only).
As a result, it is crucial that the specifications and data it lists are also observed.
5.1 General information
Inspection prior to switching on supply power
The following points must be checked before commissioning the device:
• The assignment of the flowmeter sensor to the transmitter must be correct.
• The wiring must be correct according to the electrical connections.
• The flowmeter sensor must be correctly grounded.
• The external data memory module (FRAM) must have the same serial number as the
flowmeter sensor.
• The external data memory module (FRAM) must be inserted at the correct location (see the
section titled "Transmitter replacement" in the operating instructions).
• The ambient conditions must meet the specifications.
• The supply power must match the information on the name plate.
Inspection after switching on supply power
The following points must be checked after commissioning the device:
• The parameter configuration must correspond to the operating conditions.
• The system zero adjustment must have been made.
General information
• If the flow direction indicated on the display is incorrect, it could mean that the signal lead
connections have been accidentally reversed.
• The locations and the sizes of the fuses can be found in the section titled "Replaceable parts
list" in the operating instructions.

Commissioning
CI/FCM2000-EN CoriolisMaster FCM2000 EN - 15
5.2 Information for safe operation – ATEX, IECEx
5.2.1 Inspection
Before installing the flowmeter sensor, check whether it has been damaged due to improper
transport. All claims for damages must be submitted to the shipper without delay and before
installation. You must comply with the installation conditions. Flowmeter sensors must be
commissioned and operated according to ElexV (German ordinance on electrical installations in
potentially explosive atmospheres), EN 60079-14 (setting up electrical installations in potentially
explosive atmospheres), and relevant national standards. In potentially explosive atmospheres,
installation, commissioning, maintenance, and servicing must only be performed by properly
trained personnel. The commissioning activities described here are performed after the
flowmeter has been installed and the electrical connection has been made. The supply power is
switched off. When operating the flowmeter in areas containing combustible dusts, comply with
EN 61241-0:2006.
Warning - General risks!
Comply with the following instructions when opening the housing:
• Make sure there is no explosion hazard.
• A fire permit is required.
• Power to all connecting cables must be switched off.
• When the housing is open, EMC protection is suspended.
• The surface temperature of the flowmeter sensor may exceed 70 °C (158 °F), depending
on the fluid temperature.
5.2.2 Output Circuits
Installation of Intrinsically Safe ”i” or Increased Safety ”e”
The output circuits are designed to be connected to either intrinsically safe or non-intrinsically
safe circuits. A combination of intrinsically safe and non-intrinsically circuits is not permissible.
For intrinsically safe output current circuits Potential Equalization must be maintained along the
entire circuit. The test voltage for the non-intrinsically safe circuits is Um = 60 V. When shipped
the black cable connectors are installed. If the signal outputs are to be connected to intrinsically
safe circuits, it is recommended that the included light blue caps be used for the corresponding
cable connectors.

Commissioning
16 - EN CoriolisMaster FCM2000 CI/FCM2000-EN
5.2.3 NAMUR Contact
The switching output and the pulse output (terminals 41, 42 / 51, 52) can be wired internally as
a NAMUR contact for the purpose of connecting to a NAMUR amplifier; this is achieved by
setting the jumpers accordingly. The standard wiring shown below is the factory default. The
switchover is performed via jumpers (Fig. 4). See also the section titled "Electrical connections".
G00368
Jumper positions
Standard configuration
preferred for Ex "e"
(default configuration)
NAMUR configuration
preferred for Ex "i"
Fig. 4: Positions of jumpers
The safety specifications for intrinsically safe circuits can be found on the EC type-
examination certificate.
• Make sure that the cover over the voltage supply connection is tightly closed. With
intrinsically safe output circuits, the terminal box can be opened.
• It is recommended that you use the cable glands supplied (not for the -40 °C [-40 °F]
version) for the output circuits as appropriate for the relevant type of protection:
• Intrinsically safe: Blue
• Non-intrinsically safe: Black
• The sensor and the transmitter housing must be connected via the equipotential bonding.
For intrinsically safe current outputs, equipotential bonding needs to be in place all the way
along the circuits.
• If the sensor is insulated, the maximum insulation thickness is 100 mm (4"). The transmitter
housing must not be insulated.
• After switching off the flowmeter, wait t > 2 minutes before opening the transmitter housing.
• When commissioning the flowmeter, refer to EN 61241-1:2004 regarding use in areas
containing combustible dust.
• The operator must ensure that, when connecting the protective conductor (PE), no potential
differences exist between the protective conductor and the equipotential bonding (PA), even
in the event of a fault.
Special information for use in Category 1:
• The inside of the meter tube or nominal sizes ≥DN 50 (2") may correspond to Category 1
(Zone 0). The corrosion resistance of the materials must be taken into account.
2121
12
12

Commissioning
CI/FCM2000-EN CoriolisMaster FCM2000 EN - 17
5.2.4 Information on changing the installation
Models ME26, ME27, and ME28 can be operated in various applications:
• When connected to an intrinsically safe circuit in Zone 1, as an intrinsically safe device
(Ex ia)
• When connected to a non-intrinsically safe circuit in Zone 1, as an explosion-proof device
(Ex d)
• When connected to a non-intrinsically safe circuit in Zone 2, as a "non-sparking" device (Ex
nA)
If a device which is already installed is to be used in a different application, i.e., its use is to be
changed, the following measures must be taken/checks must be made in accordance with the
applicable standards.
Models ME26/ME27/ME28
1st application 2nd application Measures
Zone 1:
Ex d, non-
intrinsically safe
circuits
Zone 1:
Intrinsically safe
circuits
• 500 VAC/1 min or 500 x 1.414 = 710 VDC/1 min
test between terminals 31 / 32, 33 / 34,
41 / 42, 51 / 52, 81 / 82, and / or 97 / 98 and
terminals 31, 32, 33, 34, 41, 42, 51, 52, 81,
82, 97, 98, and the housing
• Visual inspection, particularly of the electronic
circuit boards
• Visual inspection: no damage or explosion
can be detected
Zone 2:
Non-sparking (nA)
• 500 VAC/1min or 500 x 1.414 = 710 VDC/1min
test between terminals 31/32, 33/34, 41 / 42,
51 / 52, 81 / 82, and/or 97 / 98 and terminals
31, 32, 33, 34, 41, 42, 51, 52, 81, 82, 97, 98,
and the housing
• Visual inspection, particularly of the electronic
circuit boards
• Visual inspection: no damage or explosion
can be detected
Zone 1:
Intrinsically safe
circuits
Zone 1:
Ex d, non-
intrinsically safe
circuits
• Visual inspection: no damage to the threads
(cover, 1/2" NPT cable glands)
Zone 2:
Non-sparking (nA)
• No special measures
Zone 2:
Non-sparking (nA)
Zone 1:
Intrinsically safe
circuits
• 500 VAC/1 min or 500 x 1.414 = 710 VDC/1 min
test between terminals 31 / 32, 33 / 34, 41 /
42,
51 / 52, 81 / 82, and / or 97 / 98 and terminals
31, 32, 33, 34, 41, 42, 51, 52, 81, 82, 97, 98,
and the housing
• Visual inspection, particularly of the electronic
circuit boards
• Visual inspection: no damage or explosion
can be detected
Zone 1:
Ex d, non-
intrinsically safe
circuits
• Visual inspection: no damage to the threads
(cover, 1/2" NPT cable glands)

Commissioning
18 - EN CoriolisMaster FCM2000 CI/FCM2000-EN
Cables and cable entries
The devices are supplied either with cable glands or with 1/2" NPT threads; you specify which
you require in the order number. The cable glands supplied are ATEX-/IECEx-certified. In order
to achieve the required tightness, the outer cable diameter must be between 5 mm (0.2") and 9
mm (0.35").
Warning – Risk to persons!
Devices certified in accordance with CSA are only ever supplied with 1/2" NPT threads without
glands.
However, it is also possible to supply devices certified in accordance with ATEX or IECEx with
1/2" NPT threads without glands. In such cases, the user is responsible for ensuring that the
cable piping/glands are installed in accordance with the relevant national standards (e.g.,
NEC, CEC, ATEX 137, IEC 60079-14, etc.).
Special requirements of models ME2 / M, N (Zone 2 devices)
The transmitter housing (rectangular or round, compact or separate) can be operated in Zone 2
with protection class "restricted breathing" (nR). In such cases, please take note of the
following:
Warning – Risk to persons!
The user must check the device in accordance with IEC 60079-15 each time installation or
maintenance has been performed, or each time the housing has been opened.
Switch off the voltage supply and wait for at least two minutes before opening the housing. Then
remove a cable gland which is not being used. Cable glands certified to ATEX or IECEx are
usually used, e.g., M20 x 1.5 or 1/2" NPT thread. The device being used to test the pressure is
then attached to this gland. The user is responsible for ensuring that the device is sealed and
installed correctly.
Re-insert the gland following the pressure test.
Before the supply power is switched on again, the housing, seals, thread, and cable entries
must be subjected to a visual inspection. There must be no signs of any damage.
Notice - Potential damage to parts!
When selecting the installation site, ensure that the housing will not be exposed to direct
sunlight. The ambient temperature limits must be observed. If direct sunlight cannot be
avoided, appropriate sun protection equipment must be installed.
For FNICO or FISCO installations, the number of devices must be limited as per the
applicable standard.
Other manuals for CoriolisMaster FCM2000
4
Table of contents
Other ABB Measuring Instrument manuals

ABB
ABB Aztec 600 User manual
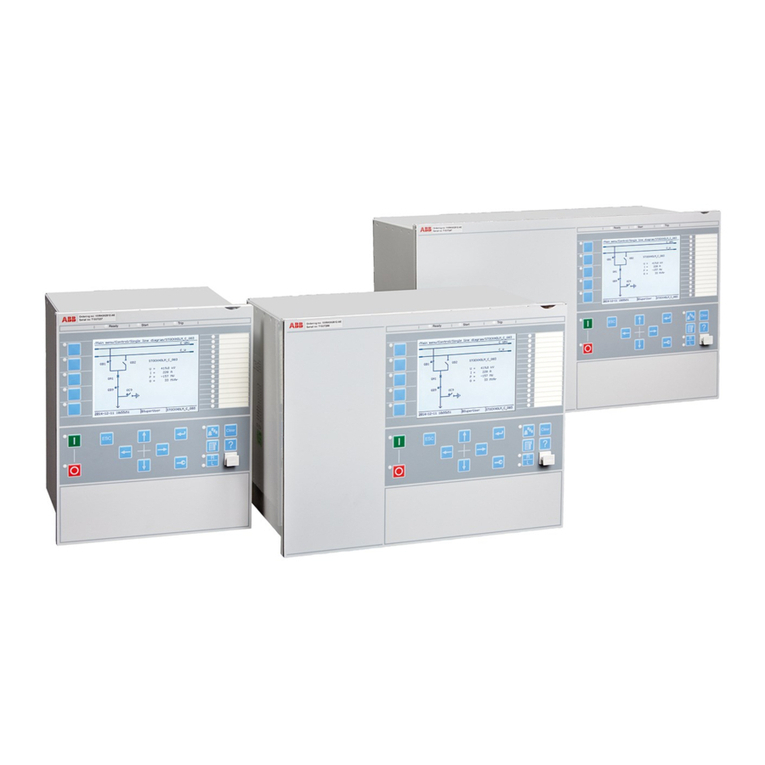
ABB
ABB Relion 670 series User manual

ABB
ABB AO2000-LS25 User manual
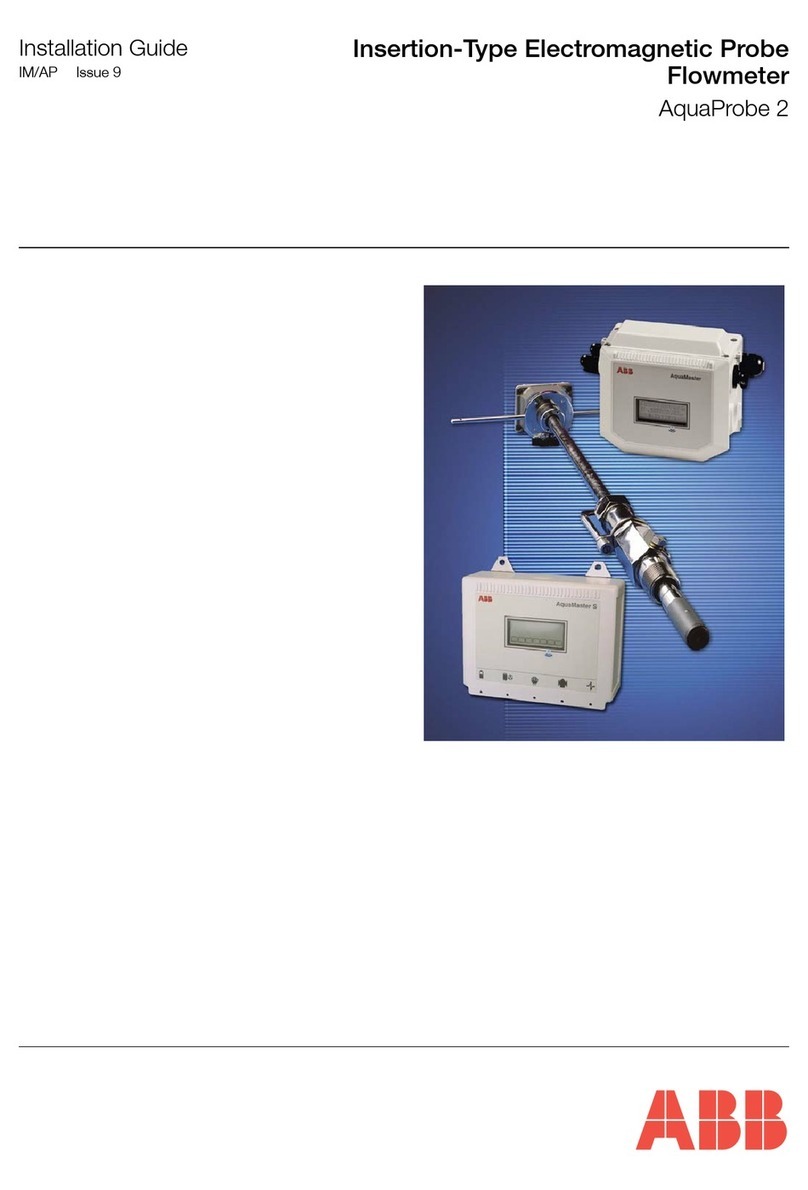
ABB
ABB AquaProbe 2 User manual

ABB
ABB VA Master FAM540 User manual
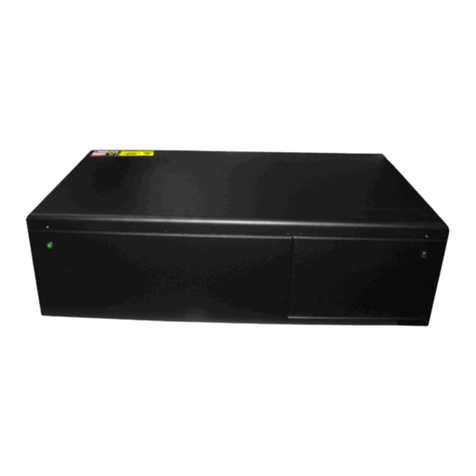
ABB
ABB ICOS GLA431-MCIA User manual
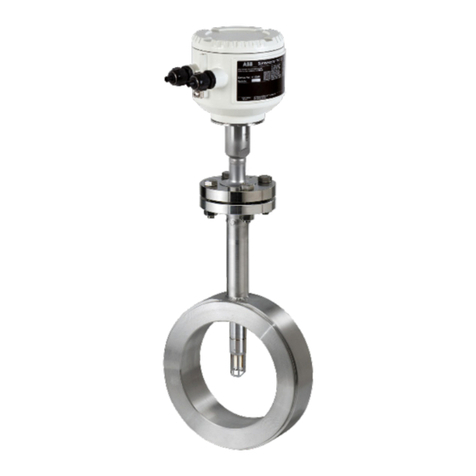
ABB
ABB SensyMaster FMT230 Installation and operation manual
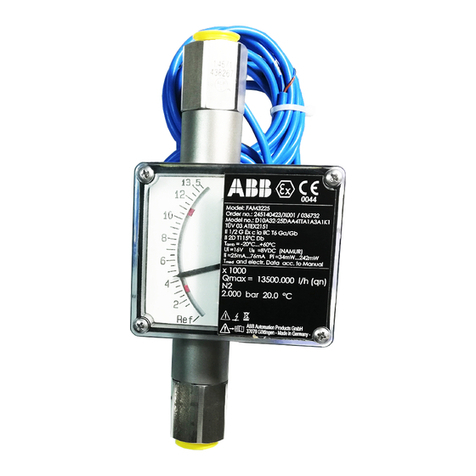
ABB
ABB FAM3200 Series User manual
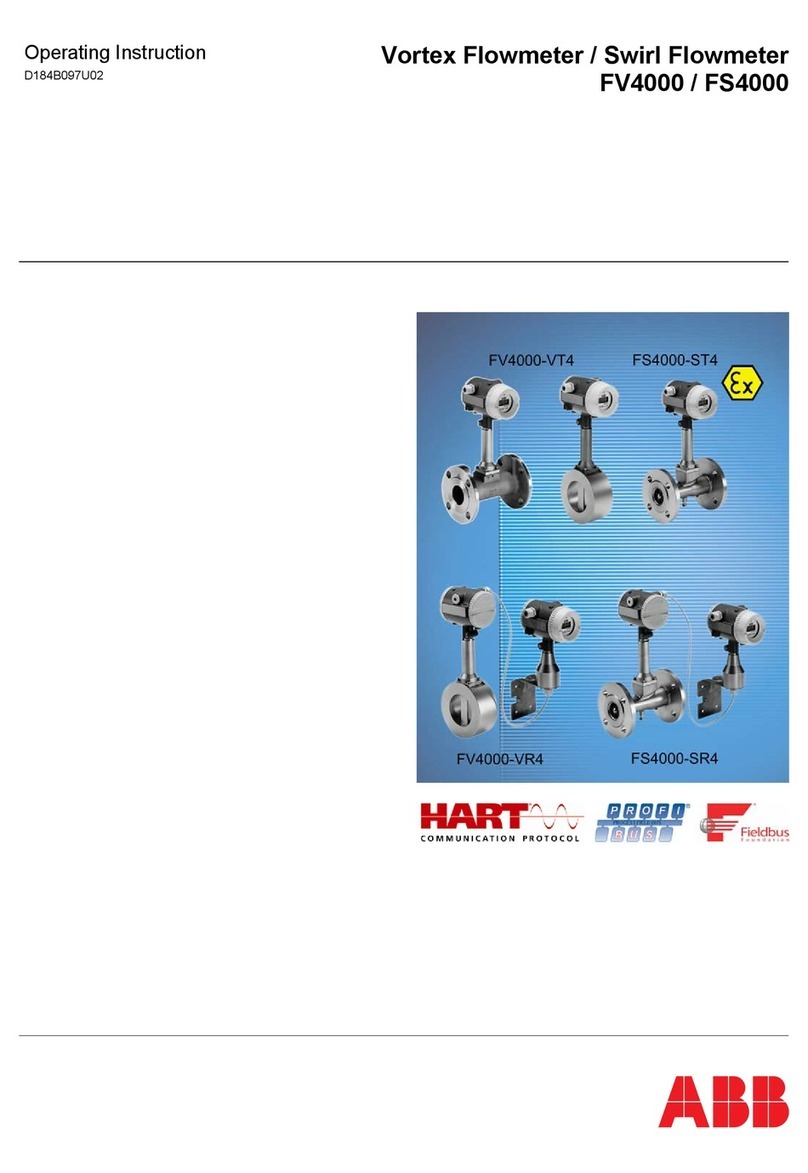
ABB
ABB FV4000 User manual
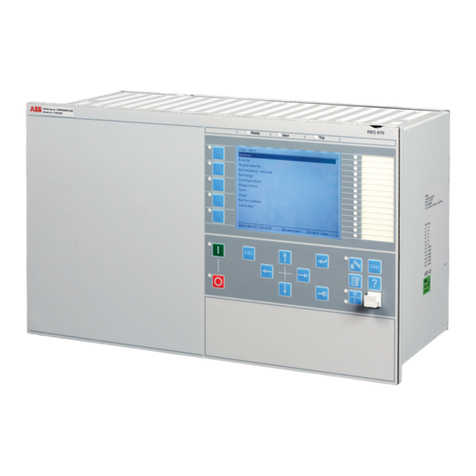
ABB
ABB Relion 670 series User manual