ABB CRB 15000 User manual

ROBOTICS
Product manual
CRB 15000

Trace back information:
Workspace 22A version a16
Checked in 2022-03-11
Skribenta version 5.4.005

Product manual
CRB 15000
OmniCore
Document ID: 3HAC077389-001
Revision: E
© Copyright 20212022 ABB. All rights reserved.
Specifications subject to change without notice.

The information in this manual is subject to change without notice and should not
be construed as a commitment by ABB. ABB assumes no responsibility for any errors
that may appear in this manual.
Except as may be expressly stated anywhere in this manual, nothing herein shall be
construed as any kind of guarantee or warranty by ABB for losses, damage to persons
or property, fitness for a specific purpose or the like.
In no event shall ABB be liable for incidental or consequential damages arising from
use of this manual and products described herein.
This manual and parts thereof must not be reproduced or copied without ABB's
written permission.
Keep for future reference.
Additional copies of this manual may be obtained from ABB.
Original instructions.
© Copyright 20212022 ABB. All rights reserved.
Specifications subject to change without notice.

Table of contents
9Overview of this manual ...................................................................................................................
12Product documentation ....................................................................................................................
14How to read the product manual ......................................................................................................
151 Safety
151.1 Safety information .............................................................................................
151.1.1 Limitation of liability .................................................................................
161.1.2 Requirements on personnel ......................................................................
171.2 Safety signals and symbols .................................................................................
171.2.1 Safety signals in the manual ......................................................................
191.2.2 Safety symbols on manipulator labels .........................................................
251.3 Robot stopping functions ....................................................................................
261.4 Safety during installation and commissioning .........................................................
281.5 Safety during operation ......................................................................................
291.6 Safety during maintenance and repair ...................................................................
291.6.1 Safety during maintenance and repair .........................................................
301.6.2 Emergency release of the robot axes ..........................................................
311.6.3 Brake testing ..........................................................................................
321.7 Safety during troubleshooting ..............................................................................
331.8 Safety during decommissioning ...........................................................................
352 Manipulator description
352.1 About CRB 15000 ..............................................................................................
362.2 Technical data ..................................................................................................
402.3 Safety data .......................................................................................................
422.4 Working range .................................................................................................
442.5 The unit is sensitive to ESD .................................................................................
453 Installation and commissioning
453.1 Introduction to installation and commissioning .......................................................
463.2 Unpacking .......................................................................................................
463.2.1 Pre-installation procedure .........................................................................
473.2.2 Risk of tipping/stability .............................................................................
483.3 On-site installation ............................................................................................
483.3.1 Brief installation procedure .......................................................................
493.3.2 Lifting the robot ......................................................................................
493.3.2.1 Orienting and securing the robot ...................................................
523.3.3 Manually releasing the brakes ...................................................................
553.3.4 Installation of brake release tool .................................................................
573.3.5 Setting the system parameters for an inverted or a tilted robot .........................
603.3.6 Loads fitted to the robot, stopping time and braking distances .........................
613.3.7 Fitting equipment on the robot (robot dimensions) .........................................
633.3.8 Test run after installation, maintenance, or repair ..........................................
643.3.9 Installation of laser scanner ......................................................................
693.4 Electrical connections ........................................................................................
693.4.1 Robot cabling and connection points ..........................................................
713.4.2 Customer connections on the manipulator ...................................................
743.5 Arm-side interface .............................................................................................
743.5.1 Configuring the arm-side interface ..............................................................
783.5.2 Using the arm-side interface ......................................................................
793.5.3 Working closely with the robot in a safe way ................................................
823.6 Configuring the software .....................................................................................
823.6.1 Information about software for the CRB 15000 ..............................................
843.6.2 Lead-through ..........................................................................................
863.6.3 The SafeMove configurator app on FlexPendant ...........................................
973.6.4 Guidelines for transient and quasi-static contact, CRB 15000 ..........................
Product manual - CRB 15000 5
3HAC077389-001 Revision: E
© Copyright 20212022 ABB. All rights reserved.
Table of contents

1003.6.5 Information about Collaborative Speed Control add-in ....................................
1013.6.6 Speed control .........................................................................................
101
3.6.6.1 Configuration of one PROFINET-base laser scanner (RobotWare 7.5 or
earlier) .......................................................................................
107
3.6.6.2 Configuration of one PROFINET-base laser scanner (RobotWare 7.6 or
later) .........................................................................................
111
3.6.6.3 Configuration of two PROFINET-base laser scanners (RobotWare 7.6 or
later) .........................................................................................
115
3.6.6.4 Configuration of one SafetyIO-base laser scanner (RobotWare 7.6 or
later) .........................................................................................
119
3.6.6.5 Configuration of two SafetyIO-base laser scanners (RobotWare 7.6 or
later) .........................................................................................
1233.6.6.6 Speed control strategies ...............................................................
1263.6.7 Use cases of safety configurations .............................................................
1314 Maintenance
1314.1 Introduction ......................................................................................................
1324.2 Maintenance schedule and expected component life ...............................................
1324.2.1 Specification of maintenance intervals ........................................................
1334.2.2 Maintenance schedule .............................................................................
1344.3 Inspection activities ...........................................................................................
1344.3.1 Inspecting the robot .................................................................................
1374.3.2 Inspecting the cable harness ....................................................................
1404.4 Cleaning activities .............................................................................................
1404.4.1 Cleaning the CRB 15000 ...........................................................................
1414.5 Testing activities ...............................................................................................
1414.5.1 Testing the brake release functionality ........................................................
1424.5.2 Running the Cyclic Brake Check routine ......................................................
1434.5.3 Testing the functionality of the joint electronics .............................................
1455 Repair
1455.1 Introduction ......................................................................................................
1465.2 General procedures ...........................................................................................
1465.2.1 Mounting instructions for sealings ..............................................................
1495.3 Cable harness ..................................................................................................
1495.3.1 Replacing the base cabling ......................................................................
1595.3.2 Replacing the axis-1 cabling .....................................................................
1935.3.3 Replacing the axis-2 cabling .....................................................................
2215.3.4 Replacing the axis-3 cabling .....................................................................
2475.3.5 Replacing the axis-4 cabling .....................................................................
2775.3.6 Replacing the axis-5 cabling .....................................................................
3175.3.7 Replacing the axis-6 cabling .....................................................................
3395.3.8 Replacing the axis-5 to axis-6 transition cabling ...........................................
3405.3.9 Replacing the brake release unit ...............................................................
3575.4 Upper and lower arms ........................................................................................
3575.4.1 Replacing the lower arm ..........................................................................
3725.4.2 Replacing the housing .............................................................................
3995.4.3 Replacing the tubular ..............................................................................
4265.4.4 Replacing the wrist housing ......................................................................
4615.4.5 Replacing the tool flange and axis-6 inner flange ..........................................
4695.4.6 Replacing the arm-side interface ...............................................................
4735.5 Swing and base ................................................................................................
4735.5.1 Replacing the base .................................................................................
5085.5.2 Replacing the swing ................................................................................
5325.6 Joint units ........................................................................................................
5325.6.1 Replacing the axis-1 joint unit ...................................................................
5705.6.2 Replacing the axis-2 joint unit ...................................................................
5985.6.3 Replacing the axis-3 joint unit ...................................................................
6245.6.4 Replacing the axis-4 joint unit ...................................................................
6 Product manual - CRB 15000
3HAC077389-001 Revision: E
© Copyright 20212022 ABB. All rights reserved.
Table of contents

6545.6.5 Replacing the axis-5 joint unit and the axis-5 to axis-6 transition cabling ...........
6965.6.6 Replacing the axis-6 joint unit ...................................................................
7196 Calibration
7196.1 Calibration method and when to calibrate .............................................................
7206.2 Calibrating the robot .........................................................................................
7226.3 Jogging directions ............................................................................................
7237 Troubleshooting
7237.1 Introduction to troubleshooting ............................................................................
7257.2 Mechanical noise or dissonance ..........................................................................
7277.3 Manipulator collapses on power down ...................................................................
7287.4 Brake release tool does not work .........................................................................
7307.5 Communication failure between PROFINET-based laser scanner, PLC, and controller ....
7317.6 Communication failure between PLC and controller .................................................
7337.7 Communication failure between scalable I/O device and controller .............................
7347.8 Movement in Safe area not in full speed or at zero speed .........................................
7357.9 Unable to remove or change installed options in Collaborative Speed Control add-in .....
7367.10 RED flashing status on Scalable I/O device and unable to move the robot ...................
7377.11 Unexpected robot movement when starting the program in Protecting Area .................
7398 Decommissioning
7398.1 Environmental information ..................................................................................
7418.2 Scrapping of robot .............................................................................................
7439 Reference information
7439.1 Introduction ......................................................................................................
7449.2 Applicable standards .........................................................................................
7469.3 Unit conversion .................................................................................................
7479.4 Screw joints ....................................................................................................
7489.5 Weight specifications .........................................................................................
7499.6 Standard toolkit ................................................................................................
7509.7 Special tools ....................................................................................................
753Index
Product manual - CRB 15000 7
3HAC077389-001 Revision: E
© Copyright 20212022 ABB. All rights reserved.
Table of contents

This page is intentionally left blank

Overview of this manual
About this manual
This manual contains instructions for:
• mechanical and electrical installation of the CRB 15000
• maintenance of the CRB 15000
• mechanical and electrical repair of the CRB 15000
The robot described in this manual has the following protection types:
•Standard
Product manual scope
The manual covers all variants and designs of the CRB 15000. Some variants and
designs may have been removed from the business offer and are no longer available
for purchase.
Usage
This manual should be used during:
• installation and commissioning, from lifting the product to its work site and
securing it to the foundation, to making it ready for operation
• maintenance work
• repair work
• decommissioning work
Note
It is the responsibility of the integrator to conduct a risk assessment of the final
application.
It is the responsibility of the integrator to provide safety and user guides for the
robot system.
Who should read this manual?
This manual is intended for:
• installation personnel
• maintenance personnel
• repair personnel.
Prerequisites
A maintenance/repair/installation craftsman working with an ABB robot must:
• be trained by ABB and have the required knowledge of mechanical and
electrical installation/repair/maintenance work.
• be trained to respond to emergencies or abnormal situations.
Continues on next page
Product manual - CRB 15000 9
3HAC077389-001 Revision: E
© Copyright 20212022 ABB. All rights reserved.
Overview of this manual

References
Documentation referred to in the manual, is listed in the table below.
Document IDDocument name
3HAC079469-001Product manual, spare parts - CRB 15000
3HAC077390-001Product specification - CRB 15000
3HAC060860-001Product manual - OmniCore C30
3HAC074304-003Circuit diagram - CRB 15000
3HAC065037-001Operating manual - Integrator's guide OmniCore
3HAC065041-001Technical reference manual - System parameters
3HAC066559-001Application manual - Functional safety and SafeMove
3HAC083267-001Application manual - Force Control Standard for GoFa
3HAC066553-001Technical reference manual - Event logs for RobotWare 7
Tip
All documents can be found via myABB Business Portal, www.abb.com/myABB.
Revisions
DescriptionRevision
First edition.A
Published in release 21B. The following updates are made in this revision:
• Added procedure for refitting the axis-4 cover in the replacement
procedure for the axis-5 joint unit.
• Changed the tightening torque for the axis-4 and axis-5 covers.
•Added procedure for refitting the swing in the replacement proced-
ure for the base.
•Added step for removing and refitting cable bracket in replacement
procedure for the lower arm.
• Corrected safety data.
• Updated information about SafeMove for the CRB 15000.
• Updated information about the arm-side interface, see Working
closely with the robot in a safe way on page 79.
•Added information about how to calibrate the robot, see Calibration
on page 719.
• Updated spare part number for axis-3 joint unit.
B
Published in release 21C. The following updates are made in this revision:
• Updated information related to the safety data, and the brake
closing time is updated.
• Updated how to initiate the calibration service routine.
•Updated information about Cyclic Brake Check in the maintenance
section.
• Updated article number for brake release tool.
• Added information about rotating connector at the manipulator
base, see Connectors at the base on page 71.
C
Continues on next page
10 Product manual - CRB 15000
3HAC077389-001 Revision: E
© Copyright 20212022 ABB. All rights reserved.
Overview of this manual
Continued

DescriptionRevision
Published in release 21D. The following updates are made in this revision:
• Added information about laser scanner.
• Added tip in section Calibration method and when to calibrate on
page 719.
• Updated working range for axis 6, see Working range on page 43.
D
Published in release 22A. The following updates are made in this revision:
• Updated information about ASI buttons.
• Added tips about the calibration features, see Features in the
routine on page 720.
• Updated information for the SafeMove function Human Contact
Supervision.
• Updated information for lead-through, see Lead-through on
page 84.
• Added information about length of thread engagement for attach-
ment screws.
• Added foundation material yield strength data.
• Updated information about response times in section Safety data
on page 40.
• Updated information about Gleitmo treated screws, see Screw
joints on page 747.
• Updated replacement procedures for axis-2, axis-3, axis-4, axis-
5 and axis-6 cabling.
• Information about online user guide added in section The Safe-
Move configurator app on FlexPendant on page 86.
• Added more information for laser scanners.
E
Product manual - CRB 15000 11
3HAC077389-001 Revision: E
© Copyright 20212022 ABB. All rights reserved.
Overview of this manual
Continued

Product documentation
Categories for user documentation from ABB Robotics
The user documentation from ABB Robotics is divided into a number of categories.
This listing is based on the type of information in the documents, regardless of
whether the products are standard or optional.
Tip
All documents can be found via myABB Business Portal, www.abb.com/myABB.
Product manuals
Manipulators, controllers, DressPack/SpotPack, and most other hardware is
delivered with a Product manual that generally contains:
• Safety information.
• Installation and commissioning (descriptions of mechanical installation or
electrical connections).
•Maintenance (descriptions of all required preventive maintenance procedures
including intervals and expected life time of parts).
• Repair (descriptions of all recommended repair procedures including spare
parts).
• Calibration.
• Decommissioning.
•Reference information (safety standards, unit conversions, screw joints, lists
of tools).
• Spare parts list with corresponding figures (or references to separate spare
parts lists).
• References to circuit diagrams.
Technical reference manuals
The technical reference manuals describe reference information for robotics
products, for example lubrication, the RAPID language, and system parameters.
Application manuals
Specific applications (for example software or hardware options) are described in
Application manuals. An application manual can describe one or several
applications.
An application manual generally contains information about:
• The purpose of the application (what it does and when it is useful).
•What is included (for example cables, I/O boards, RAPID instructions, system
parameters, software).
• How to install included or required hardware.
• How to use the application.
• Examples of how to use the application.
Continues on next page
12 Product manual - CRB 15000
3HAC077389-001 Revision: E
© Copyright 20212022 ABB. All rights reserved.
Product documentation

Operating manuals
The operating manuals describe hands-on handling of the products. The manuals
are aimed at those having first-hand operational contact with the product, that is
production cell operators, programmers, and troubleshooters.
Product manual - CRB 15000 13
3HAC077389-001 Revision: E
© Copyright 20212022 ABB. All rights reserved.
Product documentation
Continued

How to read the product manual
Reading the procedures
The procedures contain all information required for the installation or service activity
and can be printed out separately when needed for a certain service procedure.
Safety information
The manual includes a separate safety chapter that must be read through before
proceeding with any service or installation procedures. All procedures also include
specific safety information when dangerous steps are to be performed.
Read more in the chapter Safety on page 15.
Illustrations
The product is illustrated with general figures that does not take painting or
protection type in consideration.
Likewise, certain work methods or general information that is valid for several
product models, can be illustrated with illustrations that show a different product
model than the one that is described in the current manual.
14 Product manual - CRB 15000
3HAC077389-001 Revision: E
© Copyright 20212022 ABB. All rights reserved.
How to read the product manual

1 Safety
1.1 Safety information
1.1.1 Limitation of liability
Limitation of liability
Any information given in this manual regarding safety must not be construed as a
warranty by ABB that the industrial robot will not cause injury or damage even if
all safety instructions are complied with.
The information does not cover how to design, install and operate a robot system,
nor does it cover all peripheral equipment that can influence the safety of the robot
system.
In particular, liability cannot be accepted if injury or damage has been caused for
any of the following reasons:
• Use of the robot in other ways than intended.
• Incorrect operation or maintenance.
• Operation of the robot when the safety devices are defective, not in their
intended location or in any other way not working.
• When instructions for operation and maintenance are not followed.
• Non-authorized design modifications of the robot.
• Repairs on the robot and its spare parts carried out by in-experienced or
non-qualified personnel.
• Foreign objects.
• Force majeure.
Intended use
The ABB robot is intended for automation of different tasks including
moving/handling parts and production equipment or carrying sensors etc.
Application ranges from traditional manufacturing to services.
The integrator of the robot system is required to perform an assessment of the
hazards and risks.
The CRB 15000 manipulator is only intended for use with the ABB OmniCore C30
controller.
Spare parts and equipment
ABB supplies original spare parts and equipment which have been tested and
approved. The installation and/or use of non-original spare parts and equipment
can negatively affect the safety, function, performance, and structural properties
of the robot. ABB is not liable for damages caused by the use of non-original spare
parts and equipment.
Product manual - CRB 15000 15
3HAC077389-001 Revision: E
© Copyright 20212022 ABB. All rights reserved.
1 Safety
1.1.1 Limitation of liability

1.1.2 Requirements on personnel
General
Only personnel with appropriate training are allowed to install, maintain, service,
repair, and use the robot. This includes electrical, mechanical, hydraulics,
pneumatics, and other hazards identified in the risk assessment.
Persons who are under the influence of alcohol, drugs or any other intoxicating
substances are not allowed to install, maintain, service, repair, or use the robot.
The plant liable must make sure that the personnel is trained on the robot, and on
responding to emergency or abnormal situations.
Personal protective equipment
Use personal protective equipment, as stated in the instructions.
Risk of entanglement
Loose clothing should not be worn and long hair should be tied up to reduce the
risk for entanglement.
16 Product manual - CRB 15000
3HAC077389-001 Revision: E
© Copyright 20212022 ABB. All rights reserved.
1 Safety
1.1.2 Requirements on personnel

1.2 Safety signals and symbols
1.2.1 Safety signals in the manual
Introduction to safety signals
This section specifies all safety signals used in the user manuals. Each signal
consists of:
• A caption specifying the hazard level (DANGER, WARNING, or CAUTION)
and the type of hazard.
• Instruction about how to reduce the hazard to an acceptable level.
• A brief description of remaining hazards, if not adequately reduced.
Hazard levels
The table below defines the captions specifying the hazard levels used throughout
this manual.
SignificanceDesignationSymbol
Signal word used to indicate an imminently hazard-
ous situation which, if not avoided, will result in ser-
ious injury.
DANGER
Signal word used to indicate a potentially hazardous
situation which, if not avoided, could result in serious
injury.
WARNING
Signal word used to indicate a potentially hazardous
situation related to electrical hazards which, if not
avoided, could result in serious injury.
ELECTRICAL
SHOCK
Signal word used to indicate a potentially hazardous
situation which, if not avoided, could result in slight
injury.
CAUTION
Signal word used to indicate a potentially hazardous
situation which, if not avoided, could result in severe
damage to the product.
ELECTROSTATIC
DISCHARGE (ESD)
Signal word used to indicate important facts and
conditions.
NOTE
Continues on next page
Product manual - CRB 15000 17
3HAC077389-001 Revision: E
© Copyright 20212022 ABB. All rights reserved.
1 Safety
1.2.1 Safety signals in the manual

SignificanceDesignationSymbol
Signal word used to indicate where to find additional
information or how to do an operation in an easier
way.
TIP
18 Product manual - CRB 15000
3HAC077389-001 Revision: E
© Copyright 20212022 ABB. All rights reserved.
1 Safety
1.2.1 Safety signals in the manual
Continued

1.2.2 Safety symbols on manipulator labels
Introduction to symbols
This section describes safety symbols used on labels (stickers) on the manipulator.
Symbols are used in combinations on the labels, describing each specific warning.
The descriptions in this section are generic, the labels can contain additional
information such as values.
Note
The symbols on the labels on the product must be observed. Additional symbols
added by the integrator must also be observed.
Types of symbols
Both the manipulator and the controller are marked with symbols, containing
important information about the product. This is important for all personnel handling
the robot, for example during installation, service, or operation.
The safety labels are language independent, they only use graphics. See Symbols
on safety labels on page 19.
The information labels can contain information in text.
Symbols on safety labels
DescriptionSymbol
Warning!
xx0900000812
Warns that an accident may occur if the instructions are not
followed that can lead to serious injury, possibly fatal, and/or
great damage to the product. It applies to warnings that apply
to danger with, for example, contact with high voltage electrical
units, explosion or fire risk, risk of poisonous gases, risk of
crushing, impact, fall from height, etc.
Caution!
xx0900000811
Warns that an accident may occur if the instructions are not
followed that can result in injury and/or damage to the product.
It also applies to warnings of risks that include burns, eye injury,
skin injury, hearing damage, crushing or slipping, tripping, im-
pact, fall from height, etc. Furthermore, it applies to warnings
that include function requirements when fitting and removing
equipment where there is a risk of damaging the product or
causing a breakdown.
Prohibition
xx0900000839
Used in combinations with other symbols.
Continues on next page
Product manual - CRB 15000 19
3HAC077389-001 Revision: E
© Copyright 20212022 ABB. All rights reserved.
1 Safety
1.2.2 Safety symbols on manipulator labels

DescriptionSymbol
See user documentation
xx0900000813
Read user documentation for details.
Which manual to read is defined by the symbol:
• No text: Product manual.
Before disassembly, see product manual
xx0900000816
Do not disassemble
xx0900000815
Disassembling this part can cause injury.
Extended rotation
xx0900000814
This axis has extended rotation (working area) compared to
standard.
Brake release
xx0900000808
Using the brake release tool will release the brakes. This means
that the robot arm can fall down.
Continues on next page
20 Product manual - CRB 15000
3HAC077389-001 Revision: E
© Copyright 20212022 ABB. All rights reserved.
1 Safety
1.2.2 Safety symbols on manipulator labels
Continued
Other manuals for CRB 15000
5
Table of contents
Other ABB Robotics manuals
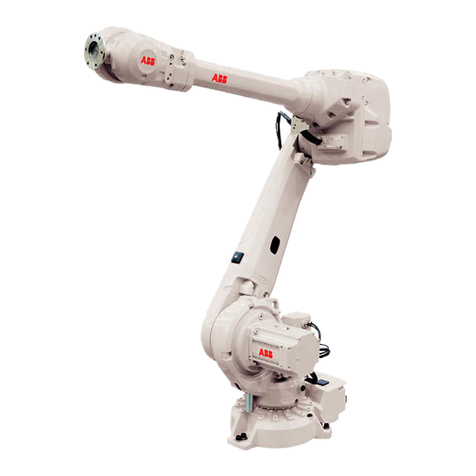
ABB
ABB IRB 4600 - 40/2.55 User manual
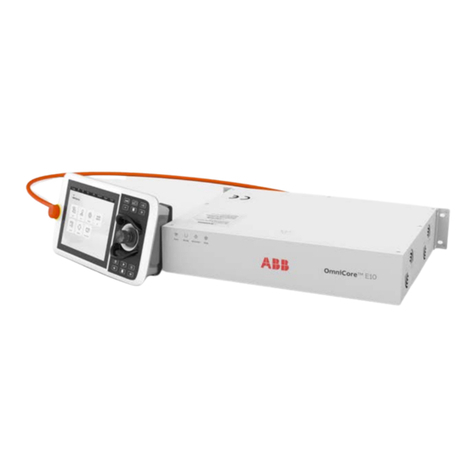
ABB
ABB OmniCore E10 User manual
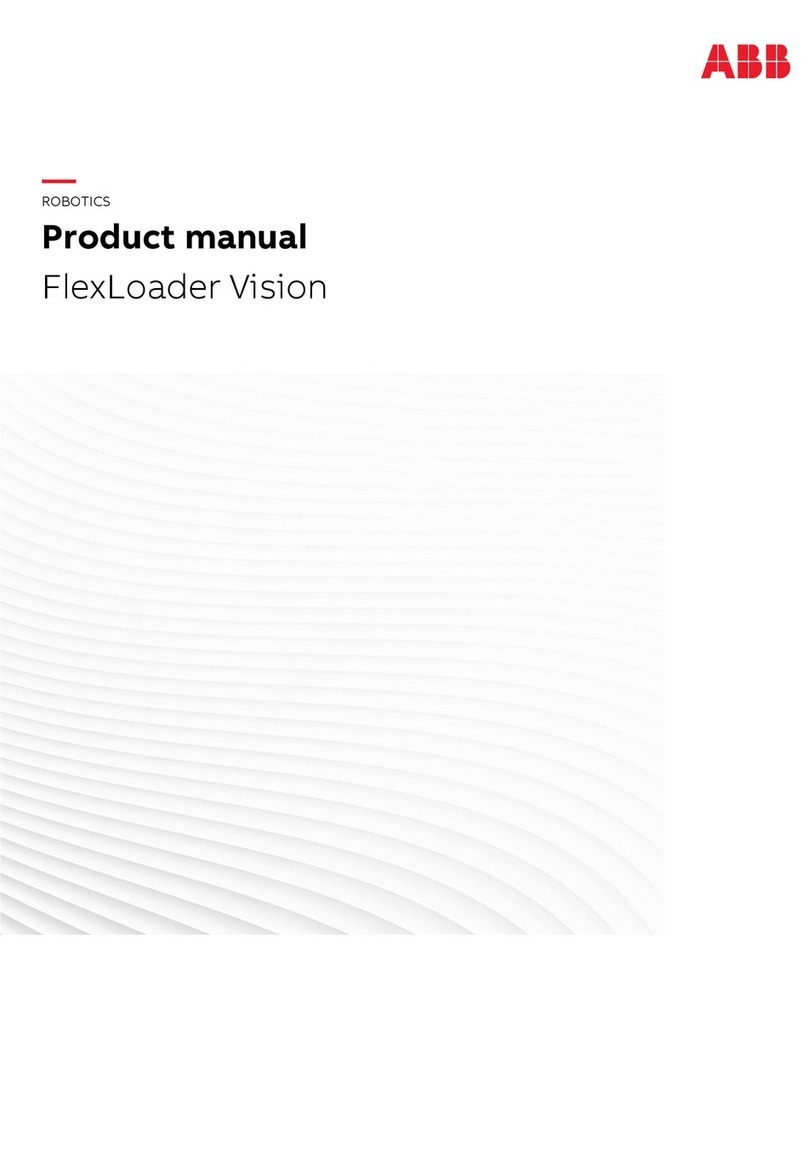
ABB
ABB FlexLoader Vision User manual
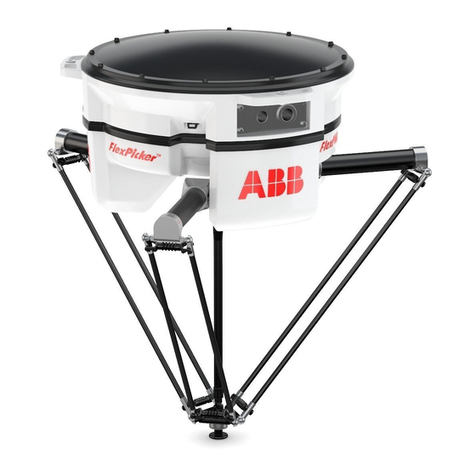
ABB
ABB IRB 360/3 User manual

ABB
ABB IRB 360-1/800 User manual
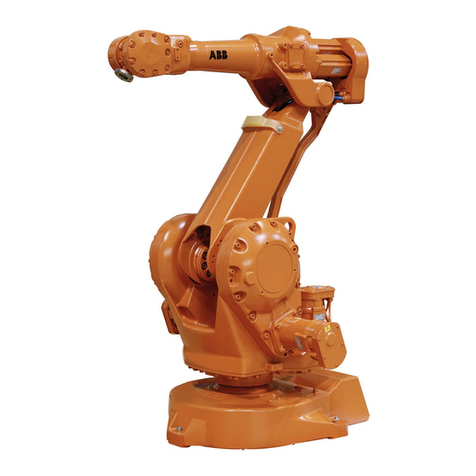
ABB
ABB IRB 2400/10 Owner's manual

ABB
ABB IRT 710 User manual
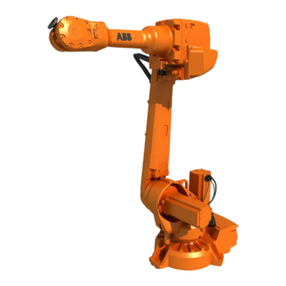
ABB
ABB IRB 2600 Series User manual
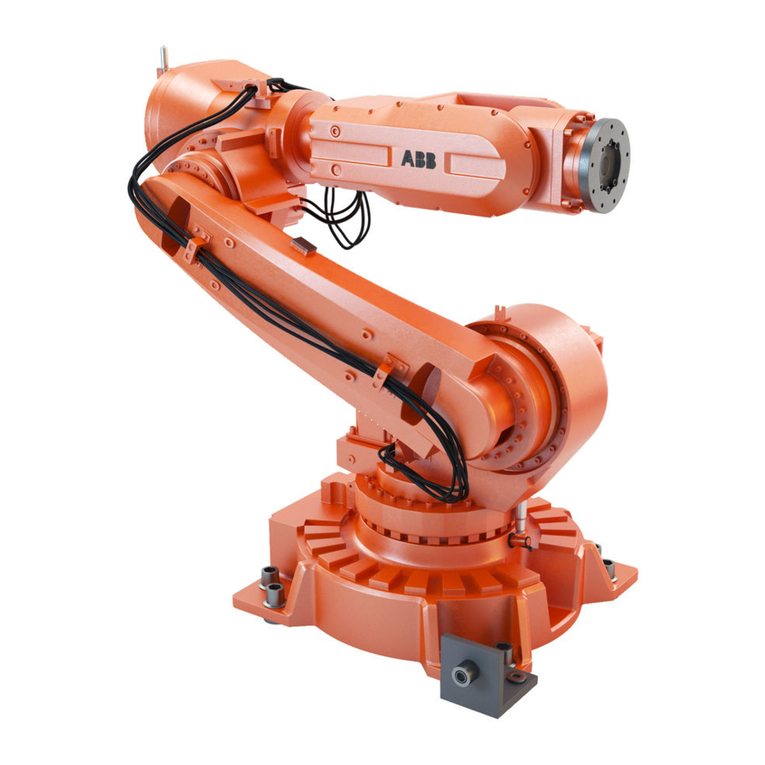
ABB
ABB IRB 6620 Owner's manual
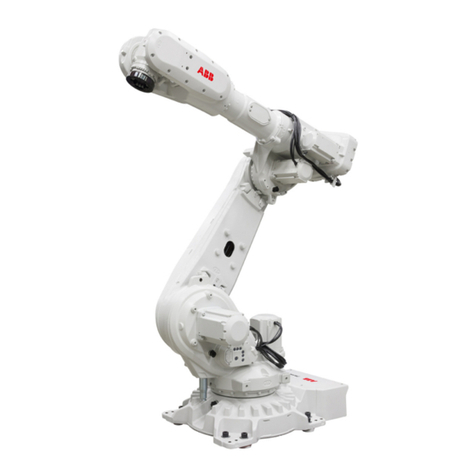
ABB
ABB IRB 5720 User manual
Popular Robotics manuals by other brands
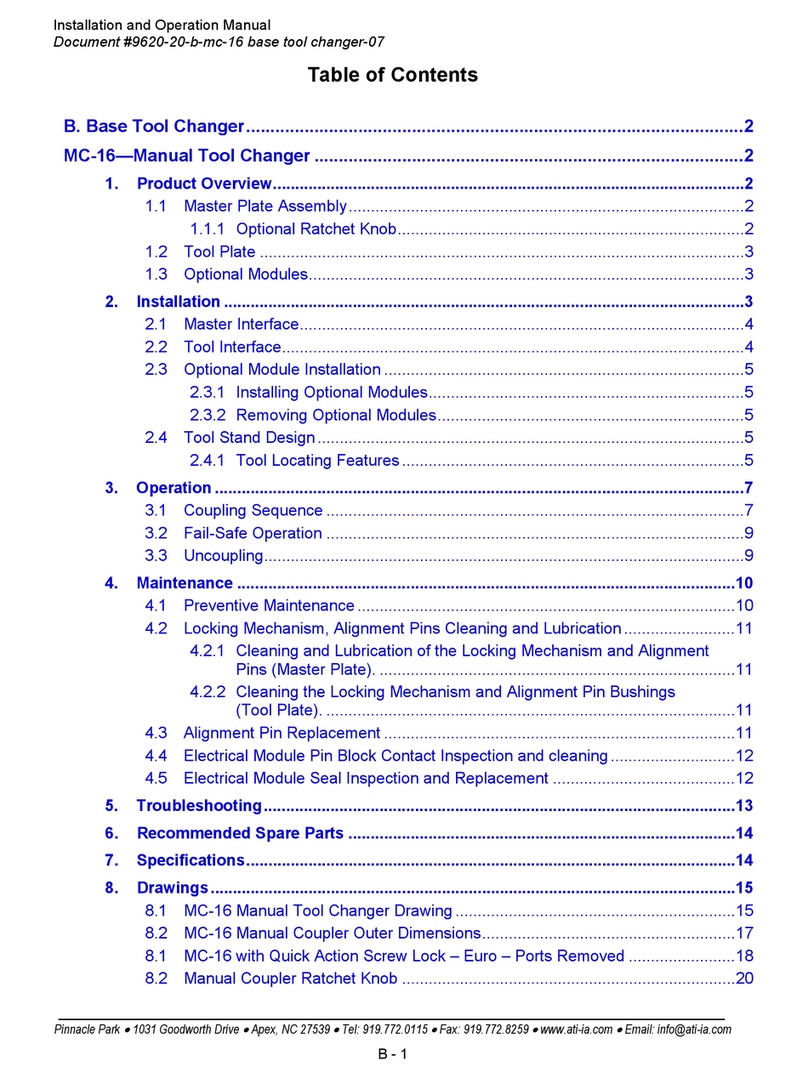
ATI Technologies
ATI Technologies MC-16 Installation and operation manual
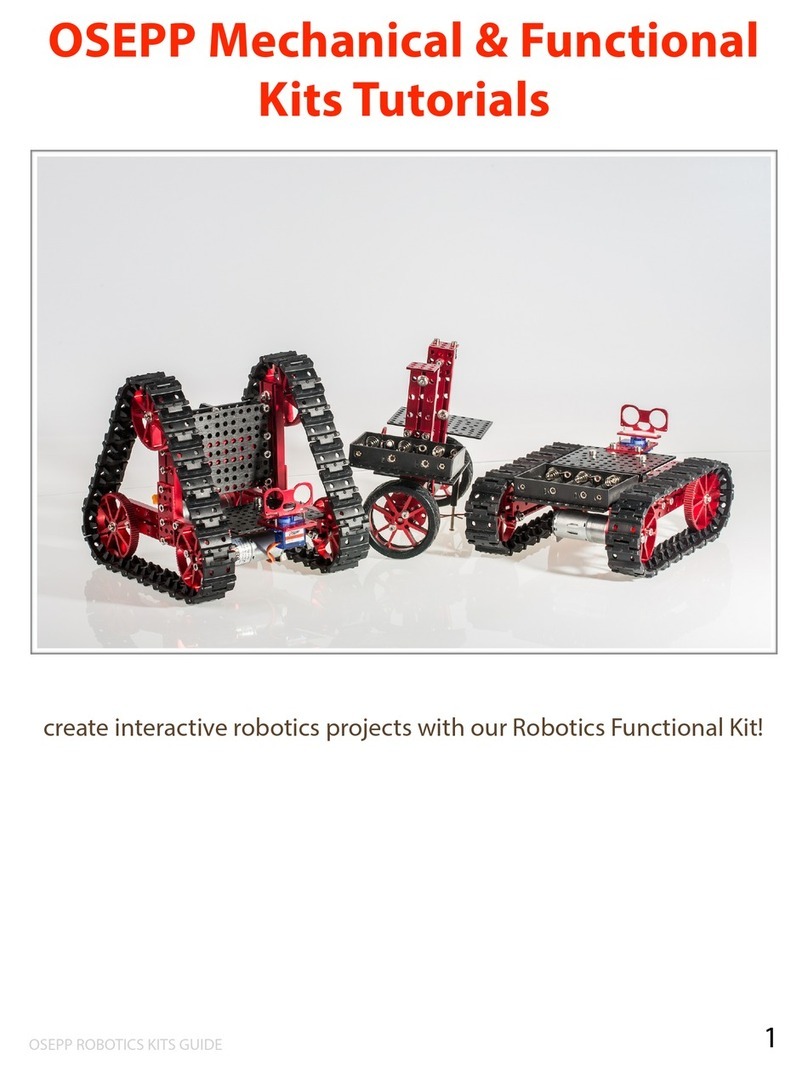
OSEPP
OSEPP Tank Mechanical Kit manual
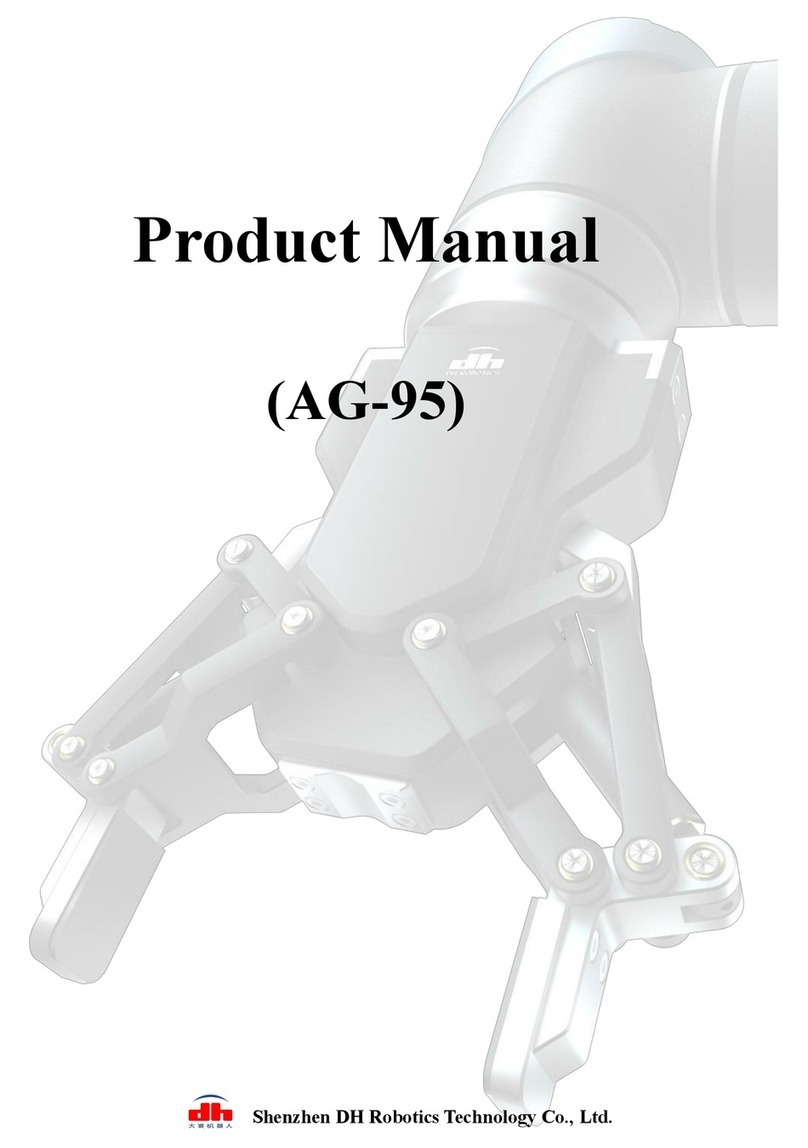
DH Robotics Technology
DH Robotics Technology AG-95 product manual
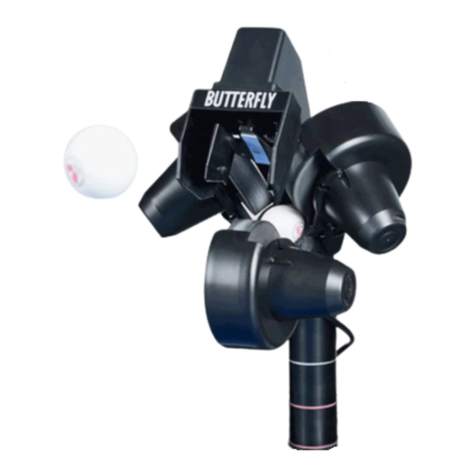
Butterfly
Butterfly AMICUS PRIME owner's manual
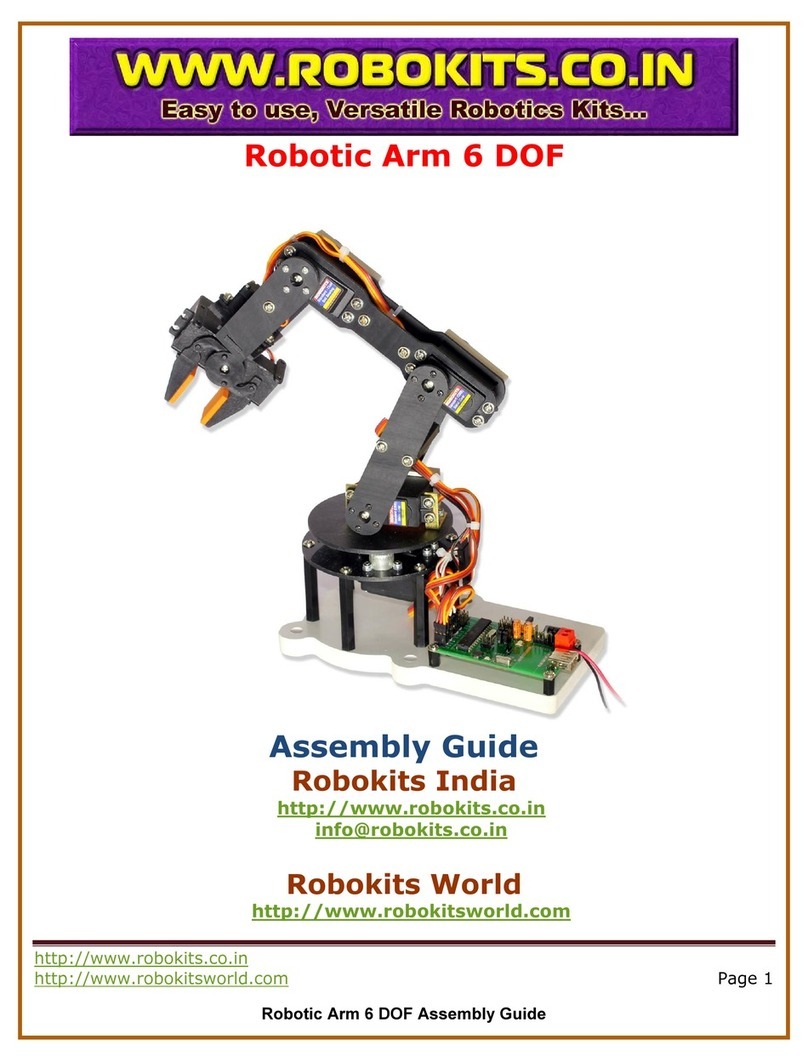
Robokits
Robokits Robotic Arm 6 DOF Assembly guide
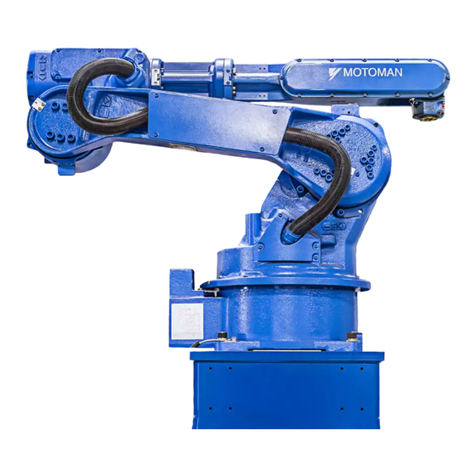
YASKAWA
YASKAWA MOTOMAN-HP20 instructions