Adash A4900 - Vibrio M User manual

Adash 4900 - Vibrio M
Version 4.00 and later
Machine vibration diagnostics
Bearing diagnostics
Lubrication diagnostics
Route measurements (4MB memory)
Service activities
Product Inspection
Ex version available
Wideband RMS or PEAK measurements of acceleration, velocity and displacement
Velocity measurement from 10Hz, optionally from 1 Hz for low speed machines
Time signals measurement
Spectrum FFT analysis
Measurement in frequency bands for bearing diagnostics
Store data and perform route measurements
Built-in ISO 10816 limits
Fault Source Identification and Diagnostics Tool
Headphones for "listening to vibration"
Built-in Infrared Thermometer
Built-in stroboscope lamp
Built-in torch
Detection of machine and bearing conditions
Detection of machine speed
Overload indicator, sensor fault and cable fault indicators
User’s Manual
Applications and Key Features:
For USA Sales and Support: AdashAmerica 1-888-817-4335 [email protected]

Adash 4900 – Vibrio M
Contents
Why perform vibration diagnostics.................................................................................... 5
Why A4900 - Vibrio M?........................................................................................................ 6
The instrument memory...................................................................................................... 7
Two instrument versions................................................................................................... 7
Upgrade to advanced version........................................................................................... 7
Off-Route measurement ................................................................................................... 7
Route measurements........................................................................................................ 7
Vibration Diagnostics - Basic Information......................................................................... 8
Introduction....................................................................................................................... 8
Basic Rules....................................................................................................................... 8
Machine and bearing condition diagnostics....................................................................... 9
Methods for ball bearing condition diagnostics.................................................................. 9
The relation between gears and ball bearings................................................................... 9
Fault Source Identification and Diagnostics Tool..............................................................10
Measurement Points........................................................................................................10
Preparation of the measurement point ..............................................................................11
Listening to Vibration Using Headphones..........................................................................12
Relationship of Measurement in Acceleration and Speed ................................................12
Abbreviations used in the guide.......................................................................................12
What Will You Get with Your Instrument?..........................................................................13
Instrument and accessories.............................................................................................13
Before You Start.................................................................................................................14
Standards for vibration measurements............................................................................15
Adash Limit Values of Machine and Bearing Vibrations...................................................16
ISO 10816 limit values.....................................................................................................17
Classification according to machine type, nominal power or shaft height.................................. 17
ISO Groups 1-4 classifications define the following types of machinery:................................... 17
Classification according to foundation........................................................................................ 17
Evaluation ranges....................................................................................................................... 17
Classification of vibration values for machines groups 1 and 3 ................................................. 18
Classification of vibration values for machines groups 2 and 4 ................................................. 18
Values setting in A4900 - Vibrio M unit.............................................................................18
Quick Start..........................................................................................................................19
Preparation of Measurement Point...................................................................................19
Putting in Batteries...........................................................................................................19
Plugging in Vibration Sensor............................................................................................20
Connectors - top panel.....................................................................................................21
Vibration measurements ...................................................................................................22
Temperature measurement..............................................................................................22
Automatic detection of the machine speed.......................................................................23
Evaluation of the machine and bearing conditions...........................................................23
Fault Source Identification and Diagnostics Tool..............................................................23
The Stroboscope .............................................................................................................24
The Torch........................................................................................................................24
Using headphones.............................................................................................................25
Instrument Operation.........................................................................................................26
Switching on and off.........................................................................................................26
Standby mode....................................................................................................................27
Information line................................................................................................................27
For USA Sales and Support: AdashAmerica 1-888-817-4335 [email protected]

Adash 4900 – Vibrio M
Selection of Measurement ...............................................................................................28
Measurement Methods Screens ......................................................................................28
Speed detection and definition.........................................................................................32
Menu for functions selection ............................................................................................33
LIGHT - TORCH ......................................................................................................................... 34
LIGHT - STROBO....................................................................................................................... 34
MEMORY.................................................................................................................................... 35
ROUTE ....................................................................................................................................... 35
VIEW........................................................................................................................................... 35
CLRDATA................................................................................................................................... 35
MEMORY – CLR ALL................................................................................................................. 35
VOLUME..................................................................................................................................... 36
SETUP........................................................................................................................................ 37
SPEED........................................................................................................................................ 37
ALARMS..................................................................................................................................... 38
MEASURE - UNITS.................................................................................................................... 38
MEASURE - DISPLACEMENT VALUE...................................................................................... 39
TIME SETTING........................................................................................................................... 39
-ESC-.......................................................................................................................................... 40
Error Messages ...............................................................................................................40
Sensor connection Error............................................................................................................. 40
Display Value Overload.............................................................................................................. 40
Input Overload Error ................................................................................................................... 41
Measurement Error..................................................................................................................... 41
Using the memory..............................................................................................................42
Off-Route measurements.................................................................................................42
Measurement screen No.1 properties ........................................................................................ 43
Measurement screen No.2 properties ........................................................................................ 43
Measurement screen No.3 properties ........................................................................................ 44
Measurement screen No.4 properties ........................................................................................ 44
Measurement screen No.5 properties ........................................................................................ 44
Measurement screen No.6 properties ........................................................................................ 45
Measurement screen No.7 FASIT properties............................................................................. 45
Measurement screen No.8 properties ........................................................................................ 45
Route measurements.......................................................................................................46
How to evaluate the failure................................................................................................49
Overall RMS values.........................................................................................................49
Overall PEAK values........................................................................................................50
Spectrum 200 Hz– Detection of Looseness....................................................................50
Time signal for bearing condition evaluation ....................................................................51
Vibrations in frequency bands – gearboxes/bearings.......................................................53
Fault Source Identification and Diagnostics .....................................................................54
Adash 4900 – Vibrio M Specifications ..............................................................................55
Response specification....................................................................................................56
Calibration .......................................................................................................................56
Vibration velocity measurement frequency response.......................................................56
Vibration acceleration measurement frequency response................................................56
Velocity measurement amplitude response......................................................................57
Acceleration measurement amplitude response...............................................................57
Sensor sensitivity.............................................................................................................57
Basic test with A4801 Sensor Simulator...........................................................................57
Basic test with sensor and shaker....................................................................................57
Advanced tests of velocity measurement.........................................................................57
Advanced tests of acceleration measurement..................................................................58
Envelope demodulation test.............................................................................................58

Adash 4900 – Vibrio M
Adash 4900 - Vibrio Ex - The ATEX Appendix (option)................................................59
Specification according to 94/9/EC (ATEX) directive:.......................................................59
Zones categories.............................................................................................................59
Useof Instrument..............................................................................................................59
Certificated accessories...................................................................................................60
Accelerometer AC90x................................................................................................................. 60
Battery........................................................................................................................................ 60
Headphones ............................................................................................................................... 60
The unit sticker ................................................................................................................61
Adash 4900 - Vibrio MP (proximity option).......................................................................62
Switch On of Instrument...................................................................................................62
Screens ...........................................................................................................................63
Speed enter ................................................................................................................................ 63
DC offset..................................................................................................................................... 63
Displacement in 1-1000Hz range ............................................................................................... 63
Spectrum 1000Hz or 2500Hz ..................................................................................................... 64
Spectrum 200Hz......................................................................................................................... 64
Time waveform in 1-1000Hz.......................................................................................................64
Setup...............................................................................................................................65
RevCnt........................................................................................................................................ 65
CONFIG...................................................................................................................................... 65
EVAL........................................................................................................................................... 65
SENSOR..................................................................................................................................... 66
For USA Sales and Support: AdashAmerica 1-888-817-4335 [email protected]

Adash 4900 – Vibrio M
Why perform vibration diagnostics ?
Vibration diagnosticsallows you to check the health condition of all your machinery. By utilizing
vibration monitoring on a routine basis, you will be informed early about potential failure before the
machine gets damaged and you will be able to order only required maintenance (instead of
expensive overhauls).
For USA Sales and Support: AdashAmerica 1-888-817-4335 [email protected]

Adash 4900 – Vibrio M
Why A4900 - Vibrio M?
You always ask before you make a decision to buy anew instrument...what unit is the best for my
specific needs? Is it an instrument with a large amount of functions, including specialized software for
data processing (which you will not ever use), or is it an instrument which is easier to use and still
contains all required functions? You should pay only for the modules that you will actually use in the
field. The A4900 is just that. The instrument uses a standard external accelerometer with a magnetic
base and enables correct repeatable measurements. You should not equate our unit with "vibration
pens".
The Adash model A4900 is a multi-function portable meter and data-collector that bridges the gap
between the basic and advanced FFT data-collector/analyser. It is a complete machine condition
expert system than gives results without the use of a computer or laptop. It is designed for field
maintenance technicians, engineers, and consultantswho need to analyze a rotating machine on-
site without investing in or carrying expensive instruments.
This single meter can measure overall vibration, band graph, 800 lines spectrum, 2048 samples time
signals, temperature, and rotation speed. In addition,it incorporates a strobe scope, handy inspection
torch,and stethoscope.
The A4900 caters to ISO 10816-3 with expert rules covering vibration levels that identify the prime
machinery faults: Unbalance, Looseness and Misalignment. An anti-friction bearing health level
indication is also incorporated. Many informative screens are available.
Do your machines work under optimum conditions?
The A4900 will:
- Determine the condition of your bearings, including slow-turning ones.
- Identify insufficiently lubricated bearings.
- Indicates unbalance, looseness, misalignment.
- Check machine speed by built-in stroboscope.
- Check machine temperature by non-contact temperature meter.
- Measures in either Metric or English units.
Operation of A4900 is easy to use. The colors green, orange,and red display the machine status.
Determination of individual machine or bearing defect types is done directly during operation, without
the need for a computer or software. Despite the fact that the A4900 is very compact and rugged, it is
designed to fit in the palm of a hand and is big in performance.
The A4900 is supplied as a complete set with an accelerometer, coiled cable, magnetic base, transit
case,and headphones. You can connect headphones to listen to machinery noise related to
vibration and processes. When measuring transmissions or slow-running bearings, you will quickly
appreciate the benefits of the headphone accessory.

Adash 4900 – Vibrio M
The instrument memory
The model A4900 - Vibrio M has a4MB data memory.
Two instrument versions
You can buy two versions of this device. The basic, lower-priced version does not have memory. The
advanced version has a 4MB data memory. Both versions have the memory capability installed on
the board and only the firmware is different.
Upgrade to advanced version
If you want to upgrade the basic version to advanced version, ask your supplier.The firmware can
easily be rewritten to include memory without having to send your unit in.
Off-Route measurement
The instrument offers many kinds of measurement option. The results are displayed on specific
screens. Some screens contain more results (e.g. RMS and Peak), some screens contain only
one (e.g. spectrum). You can save each screen to the memory. Such data are labelled as OFF-
ROUTE.
Route measurements
A pre-defined list of required measurements can be prepare in the DDS2014 software on your
computer. Once the route is created, you load the list to the A4900 - Vibrio M instrument through a
USB connection. Then the standard route arrangement is available while in the field. You see the
name of sensor location on the screen (example Motor Outboard Horizontal -MOH), mount the sensor
to that point and take the measurement. Such data are labelled as ROUTE data. After data collection,
transfer the saved measurements back to your computer to further review the data within the software.

Adash 4900 – Vibrio M
Vibration Diagnostics - Basic Information
Introduction
What is vibration diagnostics? This chapter explains the basic steps you will need to be able to begin
practical measurements.
When we are talking about vibration diagnostics, we mean routine measurements (usually
every 2-4 weeks), whose primary objectives are:
1.
Finding changes in vibration, which in turn means a change of machine operational condition.
2.
Determining the reason for this change.
3. Recommending maintenance (repair, adjustment, lubrication etc.).
4.
Checking maintenance success (including revision of dismantled part to confirm the
analysis).
The machine vibration diagnostics solves two basic tasks:
1.
Diagnostics of machine mechanical failure (imbalance, misalignment, mechanical looseness etc.).
2. Diagnostics of rolling bearing condition.
Basic Rules
1.
If the measured value of vibration increases in time, it is anindicator of a degrading machine
condition.
2.
If the measured values do not change, the machine is in stable operating condition.
However, this doesn’t necessarily mean ideal condition. For example,if a bearing was installed
incorrectly, then there will be high signal value immediately. This value will remain stable for some time
(the bearing will be able to withstand it), but then there will be a fast increase and destruction of the
bearing. This short bearing life can take hours, days, weeks or even months.
3. Reliability of the diagnostics will never be 100%.
There will always be defects, which can develop quickly in between routine measurements and thus
are not caught by the analysis. The defects caused by material fatigue can develop in seconds
(cracks, breaks). The proof of the diagnostic performance is primarily a decrease in maintenance
costs (not to absolute zero) and a significant decrease in unexpected breakdowns (not their
complete elimination).
4.
Using standards is only possible for special machines, for which the special standards
exist.
It is not possible to simply define limit vibration values in general for a wide range of machines.
However, it is possible to create standards for special machines (e.g. turbines), and these
standards are a strong diagnostic tool.
General standards should be determined by comparing a unit with similar machines as well as
asking the machine manufacturer for any suggested vibration guidelines they have created for
their specific models. Once baseline data is established (several consecutive readings), it will
become easier to identify unusual spikes in vibration level and patterns.
5.
Shortening the interval between measurements means more successful prevention of
unexpected failures.

Adash 4900 – Vibrio M
Machine and bearing condition diagnostics
Basic defects:
- unbalance (heavy spot on the rotor causes vibrations),
- misalignment (machinery parts are not in alignment ),
- looseness (machine is not properly connected with its base - soft foot),
- bearing defect (wear of bearing, bad assembly, bad lubrication or overload).
The first three defects influence the whole machine (e.g. the vibration caused by unbalance can be
identified from any point on the machine). We use the velocity [mm/s] measurements for that.
Roller (ball) bearing condition we can detect only on the nearest point as this is alocal failure. For
bearing defect identification we measure with acceleration [g].
Methods for ball bearing condition diagnostics
We have to measure vibration in acceleration [g]
For correct data acquisition, all methods must satisfy the following conditions.
We can choose different procedures for evaluation of the acceleration signal. Measured signal can be
imagined as the level of a river. It flows with appropriate speed and there are little or big waves. If we
want to measure the stream we can measure the flow per hour or wave level. The value of the flow
will be stable and it will change slowly. But the wave levels are unstable because measurements
have avariety of values.
Similar effects occur for bearing condition measurements. You can measure RMS value (the total
energy in signal) or PEAK value (the highest peak in signal). We can use both types for evaluation,
but we just have to realize the advantages and disadvantages of each.
RMS measurement
- advantages
- disadvantages
- stable and repeatable, time trends are easy to read
- if wear increases the response is slower then PEAK, but sufficient for
maintenance.
PEAK measurement
- advantages
- disadvantages
- fast response for any condition change.
- not stable or easily repeatable (extremely sensitive), time trends are not well
readable.
From these two basic measurements further measurements are derived:
- gENV - envelope signal modulation. Advantages and disadvantages are in the middle
of RMS and PEAK measurements.
-gSE BCU, SEE, SPM - measurements are performed usually on the sensor resonance frequency.
These methods have the same advantages and disadvantages as the PEAK measurement.
The relation between gears and ball bearings
For gearbox diagnosis it is necessary to measure the acceleration signal like we do for ball bearings.
When the balls are rolling over the damagedtracks (pitting), shock pulses occur. Unfortunately similar
shocks are also found in the data from worn or damaged gears. So if we measure a gearbox with
roller bearings then higher vibration values can be caused by both sources.
More information for this type of analysis can be found in the chapter Vibrations in frequency range -
gearboxes/bearings.

Adash 4900 – Vibrio M
Fault Source Identification and Diagnostics Tool (FASIT)
This tool is included in the Adash 4900 - Vibrio M. This type of auto-analysis function is hard to find in
this price category. This tool displaysseveral bar graphs with traffic light colors. The two major
(largest) bars are allocated to general machine condition (on the left side) and ball bearing condition
(on the right side).
The next three bars are located in the middle, horizontally. They display the severity level of
UNBALANCE, LOOSENESS and MISALIGNMENT (from the top down).
Measurement Points
The measurement location must enable repeatable measurements under the same conditions as the
previous measurement. Also,the direction of the sensor ( radial, axial for rotated machines) is important.
For this reason, it is important to determine set measurement points on the machine. Atypical
machine with suggested measurement points can be seen in the image below.
For the measurement in radial direction, we are going to place the sensor perpendicularly to the axis
of rotation, for axial measurement along the axis. The radial measurement can be usually performed
horizontally, vertically or in another angle. The importance of the angle choice should not be
overstressed; choose any radial direction with easy access.
The measurement points need to be prepared prior to collecting data. The best method is to place
measuring pads on a machine (see next page).

Adash 4900 – Vibrio M
Preparation of the Measurement Location
For quality data collection, the measurement point location must be prepared in advance. For regular
measurements the sensor must always be fixed in the same way at the same point. For bearing
diagnostics it is necessary to fix the sensor with a magnetic base. Do not simply hold the sensor
against the machine by hand - high frequencies cannot be measured this way.
The magnetic base is firmly screwed to the sensor and then it is magnetically fixed to the metal
surface of the machine. Hence the sensor is fixed and a measurement is possible. Quality of fixation
markedly influences the result of your measurement. If the sensor swings or jumps about etc., your
measurement is pointless. A layer of paint is also a big obstacle for higher frequencies. The magnetic
base has a ground surface and the same surface quality must be created on the machine. Generally,
this is nearly impossible as the quality of the bearing’s housing steel is not high and such a surface
can quickly succumb to corrosion. Then it becomes unusable.
The solution to this problem is to use measurement pads. These are the cylinders with the diameter
approx. 26 mm and 10 mm high with a ground surface, made of a magnetic stainless steel. They are
fixed to chosen points with special glue, which ensures a perfect transmission of the high frequency
vibration. The pad is covered with a plastic cover, which is removed only for the measurement. Another
advantage of the cover is that when the machine is painted, your measurement point is preserved. The
paint would devalue the pad. It is sufficient to coarsely grind the machine’s surface and degrease it
before the pad is glued. Durability of the pads in time is unlimited. In general, the pad will last until it is
forcibly removed from the machine.
You will need the following items: angle grinder, set of files, sand paper, degreaser (ethanol,
solvent), measurement pads and glue.
Prepare the surface in the following way:
- remove paint, corrosion,or unevenness from the surface by grinding,
- degrease the surface.
The pad is affixed with glue. We typically use the METAL TECH SG cement, but other glues with
similar properties may be used.
The METAL TECH SG cement is a 2-component epoxy cement with properties best suited for this
task. The two components, after mechanical mixing, chemically react and after drying they form a hard
material resistant to pressure, temperature,and humidity.
In the case of the simple pad the procedure is as follows: cut-off a disc approx .3 mm thick from the
cement with a sharp knife. Wet your fingers and work the disc into a homogenous lump. Roll a cylinder
with the diameter approx. 2-3 mm from this lump and put it on the side, which is not roughened.
For USA Sales and Support: AdashAmerica 1-888-817-4335 [email protected]

Adash 4900 – Vibrio M
Push the pad with glue to the prepared place on the machine and while constantly pushing and
turning the pad with circular movements, observe that the cement is being evenly pushed out along
the circumference of the pad. The purpose is to make the layer between the pad and the surface as
thin as possible.
! ATTENTION. CEMENT MUST NOT BE PUSHED OUT COMPLETELY!
Pushed out cement may be removed or levelled out around the pad. In the end you put a cover on the
pad.
When using aTpad, the amount of the cement is dependent on the size of the gap between the motor
ribs and it is not so easy to determine the amount of the cement to process. As with the simple pad,
the surface between the ribs must be well cleaned and degreased. The space should be filled with the
necessary amount of the cement so that only the cylindrical part of the pad remains visible after drying
of the cement. In the end put the cover on the pad.
Listening to Vibration Using Headphones
A user can connect headphones to the Adash 4900 – Vibrio M instrument, since listening to a
measurement signal also enables a differentiation of the problem type. People think that this is an old
method, which does not have a place in this modern world. The opposite is true. Analysis of gears
and low speed bearings (e.g. in paper mills) gainsbetter quality by listening. Listening can easily be
done by any maintenance person without deep knowledge of diagnostics. If there is a defective
bearing, a distinct rumbling sound is audible in the headphones. If the bearing is OK, then you can
hear only a weak noise.
HEADPHONES WARNING!
Listen at moderate volumes to avoid hearing damage.
Always remove the headphones from the ears when you move the sensor or re-connect cable.
Relationship of Measuring in Acceleration and Speed
Maintenance staff usually measure vibrations in mm/s or inch/s (velocity) and not in g = 9.81 m/s2
(acceleration). This is a relic of the past, when old equipment enabled the vibration speed
measurement only. Bearing defects are not recognizable by using velocity measurements. If the
velocity value increases due to a bearing defect, then the defect is already serious and there is an
acute danger of unexpected breakdown. Measuring velocity vibration does not give an early enough
warning before failure of a rolling bearing.
For accurate bearing condition measurement you have to measure the acceleration vibration!
Abbreviations used in the guide
Abbreviations below are used in this User’s Manual
RPM – Revolutions per minute
CPS – Revolutions per second
RMS – RMS value of the measured signal
PEAK – Peak value of the measured signal
For USA Sales and Support: AdashAmerica 1-888-817-4335 info@adashamerica.com

Adash 4900 – Vibrio M
What the Instrument Includes
Instrument and accessories
The instrument case contains:
- A4900 – Vibrio M instrument
- vibration sensor - accelerometer
- magnetic base for vibration sensor
- coiled cable to connect vibration sensor
- headphones
- measuring tip for putting manual pressure on vibration sensor
- 1.5V alkaline batteries
- CD with the manual
Fig. Adash 4900 – Vibrio M with accessories
For USA Sales and Support: AdashAmerica 1-888-817-4335 info@adashamerica.com

Adash 4900 – Vibrio M
Before You Start
1.
Always connect only ICP type sensors into an ICP marked socket !
If unsure, consult your supplier.
2. Never plug this instrument into 230 V household voltage !
3. To power this instrument, use batteries with max. nominal voltage of 1.5 V!
4. To power this instrument, use only alkaline or rechargeable (NiCd, NiMH) batteries.
Regular carbon-zinc batteries are not suitable.
Ignoring any
of the
recommendations mentioned below may cause failure of the
instrument.
Handling voltage higher then 24 V can cause an accident.
WARNING!
Use correct battery polarity.
Incorrect polarity will cause destruction of the
instrument!
HEADPHONES WARNING!
Listen at moderate volumes to avoid hearing
damage.
Remove the headphones from your ears when
you move the sensor or re-connect cable.

Adash 4900 – Vibrio M
Standards for Vibration Measurements
Using standards is an occasional topic in vibration diagnostics. Because there are a lot of
different types of machines,it is impossible to determine the critical limits of vibrations for a wide
range of machines. If a standard were to encompass all types of machines, its reliability would be
low and as a result you could repair a machine which did not require any maintenance.
Therefore, the standards should be determined for a narrow range of machines.
The A4900 - Vibrio M contains Adash limit values and ISO 10816 limit values. Adash limits are not
rewritten from any existing standard. It’s a result of 20 years of Adash engineering team experiences.
It’s difficult to invent critical value definition which would be simple (that means not many parameters
such as speed, power, bearing type, machine type and so on) and reliable.
The following figures provide some detail on how we derived limit values. Three levels of machine
condition are defined: GOOD, ALERT (Machines in this range are not acceptable for long period
operation, but they could be operated till the time when they are repaired) and DANGER (Vibration
values in this range are considered as very dangerous andthey can cause damage to the machine).
The corresponding colors are taken from traffic lights: green, yellow,and red.
All limit values are related to the speed value. The low speed machine should generate lower vibration
then a higher speed machine.
In the graphs below, you can see three particular areas. The GOOD condition is the space up to the
yellow line that means operation without restriction. The space above yellow but under red line is an
ALERT condition. It is possible to operate the machine but more data should be collected and
analyzed to further pinpoint the concern. It’s necessary to determine the source of worsening condition
and plan repairs(for instance change the bearing) or maintenance (balancing, alignment). The space
above the red line is DANGER condition and the machine should not be operated. The first figure
contains the values for overall machine condition which are used for unbalance, misalignment, and
mechanical looseness. They are called “overall” values because we can measure them on most
measurement points. The second figure contains the limit values of a roller bearing condition. This
condition is local and can be measured only on the appropriate bearing house.
Working with the figures below is simple. It’s necessary to know the speed. The instrument determines
it automatically or the user can enter it manually. On the bottom horizontal axis you should find the
point which corresponds with speed. Above this point you will find an intersection with the orange and
red lines. Projections to the vertical axis will determine limit values for yellow or red state. If the
measured value is lower than yellow the condition is GOOD – green. If the value is above yellow but
under red then the condition is ALERT – yellow. If the value is higher then red graph then the condition
is DANGER – red.

Adash 4900 – Vibrio M
Adash Limit Values of Machine and Bearing Vibrations
Graphs, according to which the instrument determines acceptable vibration limits depending on
machine speed.
Unbalance, misalignment, and mechanical looseness:
0.0
1.0
2.0
3.0
4.0
5.0
6.0
0 500 1000 1500 2000 2500 3000 3500 4000
speed [RPM] ---->
Vel (10-1000Hz) [mm/s RMS] ---->
0
0.04
0.08
0.12
0.16
0.2
0.24
Vel (10-1000Hz) [ips RMS] ---->
0.0
0.5
1.0
1.5
2.0
2.5
3.0
3.5
0 1000 2000 3000 4000 5000 6000 7000 8000
speed [RPM] ---->
Acc (5k-16kHz) [g RMS] ---->
For USA Sales and Support: AdashAmerica 1-888-817-4335 info@adashamerica.com
Roller bearing condition

Adash 4900 – Vibrio M
ISO 10816 limit values
There are a wide range of valid standards but we would like to mention ISO 10816. It has several
sections and it also deals with procedures on how to gain limit values for particular machines. It
contains 3 tables of values, which are applicable for the A4900 - Vibrio M unit.
Classification according to machine type, nominal power or shaft height
Select the Group that best describes the general size, type, and speed of the machinery being
measured. Note that these machine group classifications are set forth in ISO 10816-3, which rates
overall velocity vibration levels for industrial machines with normal power above 15kW and nominal
speeds between 120 r/min and 15000 r/min when measured in situ.
ISO Groups 1-4 classifications define the following types of machinery:
Group 1
Large machines ( rated power above 300kW) with a shaft height greater than 315 mm. These
machines are normally equipped with sleeve bearings.
Group 2
Medium-sized machines (rated power from 15 kW to 300 kW) and electrical machines with a shaft
height between 160 and 315 mm.
These machines are normally equipped with rolling element bearings.
Group 3
Pumps with multi-vane impeller and with separate driver with rated power above 15 kW.
Group 4
Pumps with multi-vane impeller and with integrated driver with rated power above 15 kW.
Classification according to foundation
An additional setting allows the specification (when defining the overall alarm levels) of measurements
taken from machinery with Rigid or Flexible foundations.
Evaluation ranges
For evaluation of the machine health from vibration there are defined following evaluation ranges.
Range A: New machine vibrations should occasionally be in this range.
Range B: Machines in this range can be operated for unlimited period.
Range C: Machines in this range are not acceptable for a long period operation, they could be
operated till repair time only.
Range D: Vibration values in this range are considered as very dangerous an they can cause
damage of the machine.

Adash 4900 – Vibrio M
Classification of vibration values for machines groups 1 and 3
Foundation class RMS velocity values border zone
mm/s in/s
Rigid (R13) 2,3 0,09 A/B
4,5 0,18 B/C
7,1 0,28 C/D
Flexible (F13) 3,5 0,14 A/B
7,1 0,28 B/C
11,0 0,43 C/D
Classification of vibration values for machines groups 2 and 4
Foundation class RMS velocity values border zone
mm/s in/s
Rigid (R24) 1,4 0,06 A/B
2,8 0,11 B/C
4,5 0,18 C/D
Flexible (F24) 2,3 0,09 A/B
4,5 0,18 B/C
7,1 0,28 C/D
Setting values in the A4900 - Vibrio M unit
It’s possible to set up these values directly in the unit. Then the measured values are displayed in
traffic light colors as mentioned earlier.
You can choose to use the Adash limits (recommended) or 10-816 limits.
To change the values referenced, visit the menu under the mode SETUP (see instrument
operation).
Colored marks according to 10-816 are ranges A and B, displayed by green colour.
Range C is yellow and range D is red.
It’s necessary to choose a type of evaluation R13, F13, R24 or F24 (see table above).

Adash 4900 – Vibrio M
Quick Start
The aim of this chapter is to introduce you to theinstrument, and, without reading a complete User’s
Guide, enable you to measure vibration values. This chapter does not describe full and detailed
operation of this instrument or measurement methodology. Special chapters in this Guide are intended
for this purpose.
Preparation of the Measurement Point
We have to select a measurement point before the measurement itself. We want to choose it in such
way that transmission of vibration will not be attenuated. Usually this means as close to the source of
vibration as possible (for instance at a bearing housing). We always have to measure at a solid, firm
part of a machine. We should not be measuring on covers and so on. The place should be clean,
without corrosion and paint. It should also be flat so the sensor will not “wobble”. The best method is to
use a measurement base, which is glued onto the machine. It has a perfect surface, plastic cover, and
is made from magnetic stainless steel. This will enable you to perform the measurements on the
machine at any time under the same conditions. Measurement repeatability is critical for accurate data
collection and analysis.
Putting in Batteries
Batteries are accessible after opening a lid at the bottom part of the instrument. Open the lid by
pressing its lower edge (the edge with hinge), the lid upper part opens easily - see figure. Do not ever
use force! Proper polarity is shown on the picture.
Do not forget to switch the instrument off before opening the power battery lid!
Never handle the power batteries with the instrument switched on!
Fig. Opening of the lid
1. Press gently
2. Open

Adash 4900 – Vibrio M
Fig. Placement of power batteries Fig. Proper cell polarity
Plugging in Vibration Sensor
To measure a vibration signal we need to plug in the vibration sensor with ICP power. The plugged in
sensor must be a standard accelerometer with 100 mV/g sensitivity. The instrument is equipped
with its own source of ICP power for connected sensor. The sensor needs to be connected at the right
input plug with the supplied cable.
Fig. The instrument with a sensor connected
Other manuals for A4900 - Vibrio M
2
Table of contents
Other Adash Measuring Instrument manuals
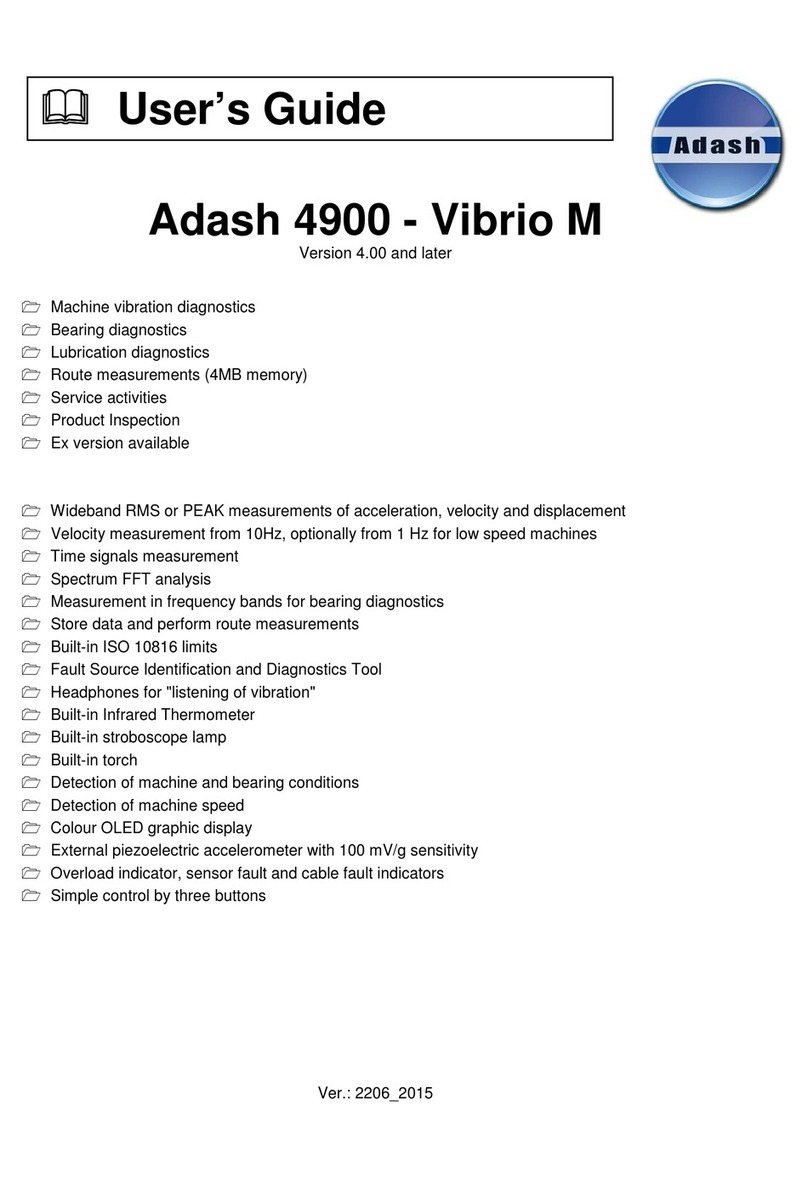
Adash
Adash 4900 Vibrio Ex User manual

Adash
Adash A3716 User manual
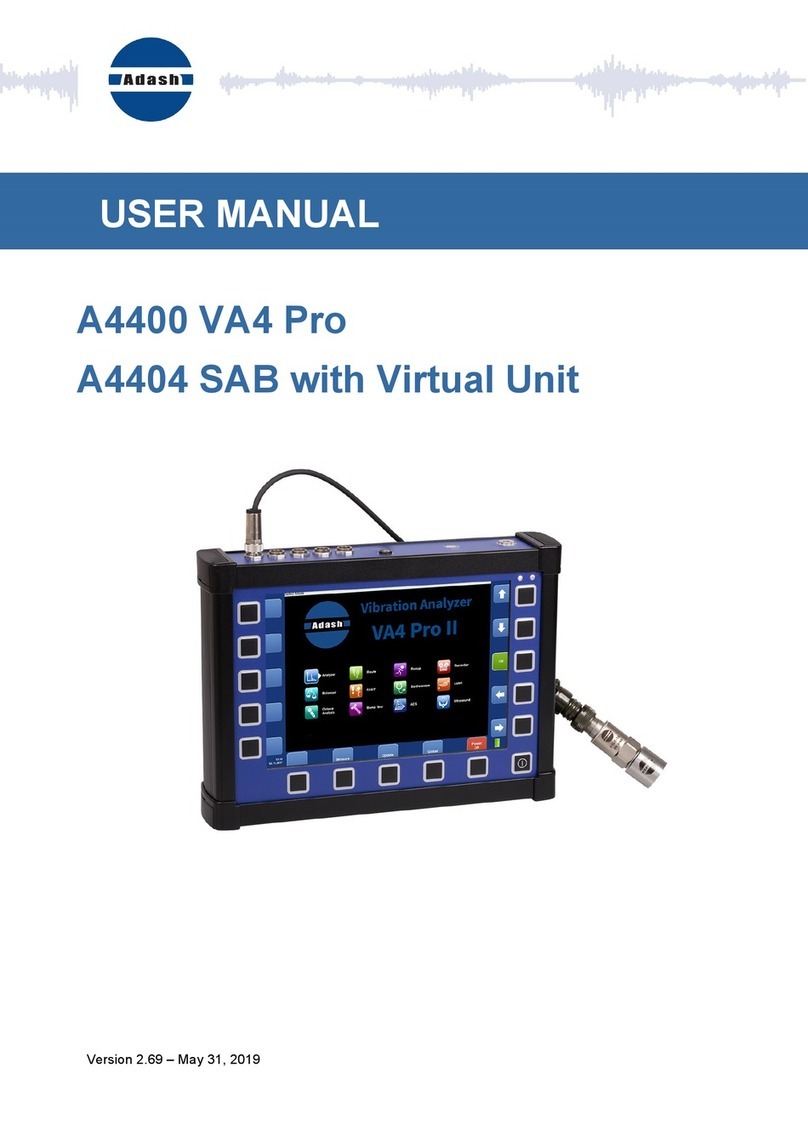
Adash
Adash VA4 Pro II User manual

Adash
Adash 4300 VA3Pro User manual
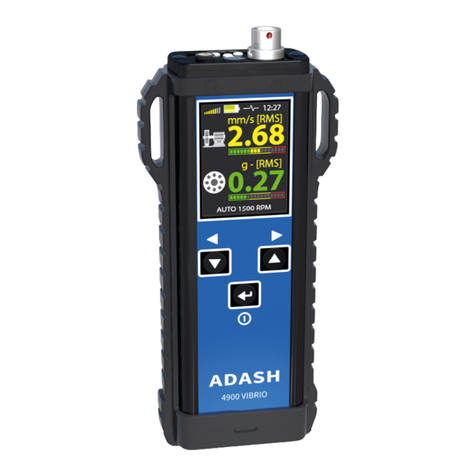
Adash
Adash A4900 - Vibrio M User manual
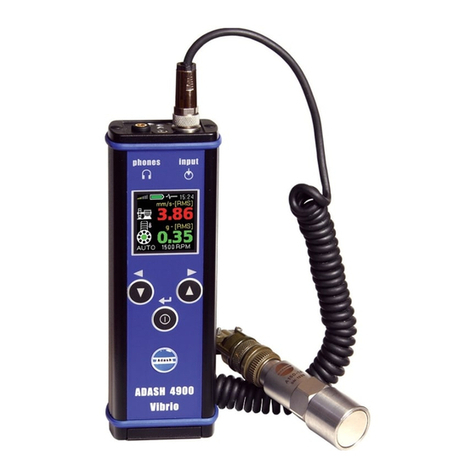
Adash
Adash A4900 - Vibrio M User manual
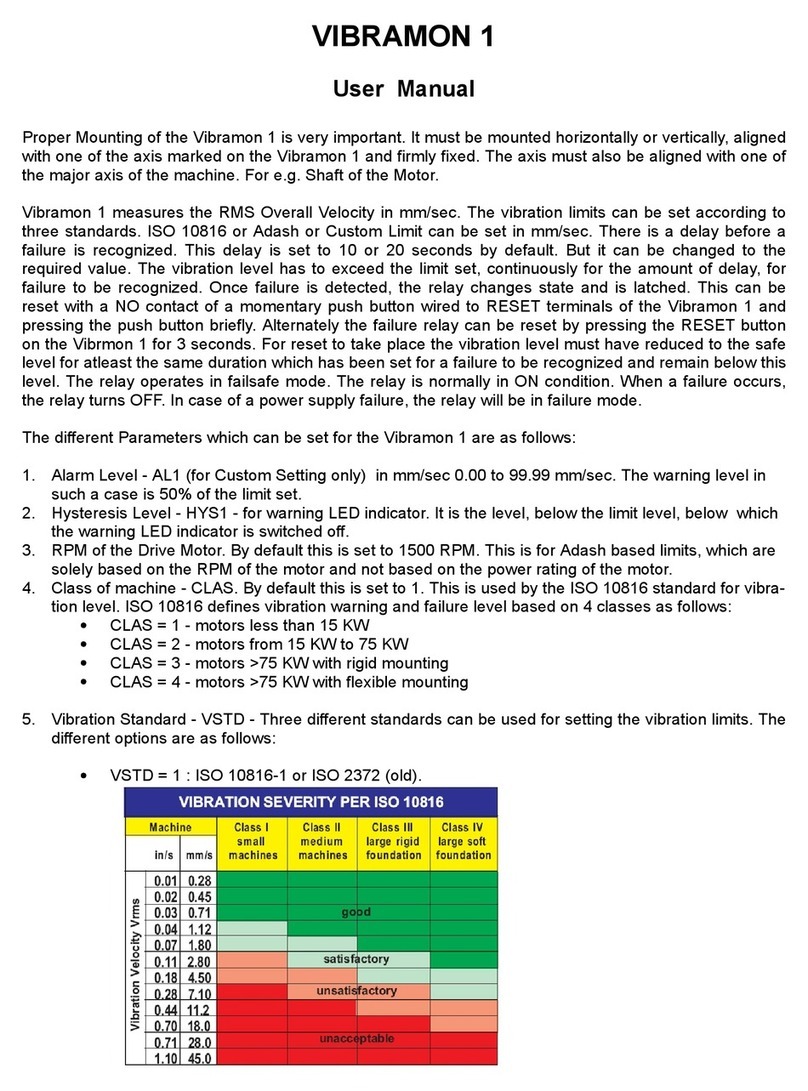
Adash
Adash VIBRAMON 1 User manual

Adash
Adash 4300 - VA3 User manual
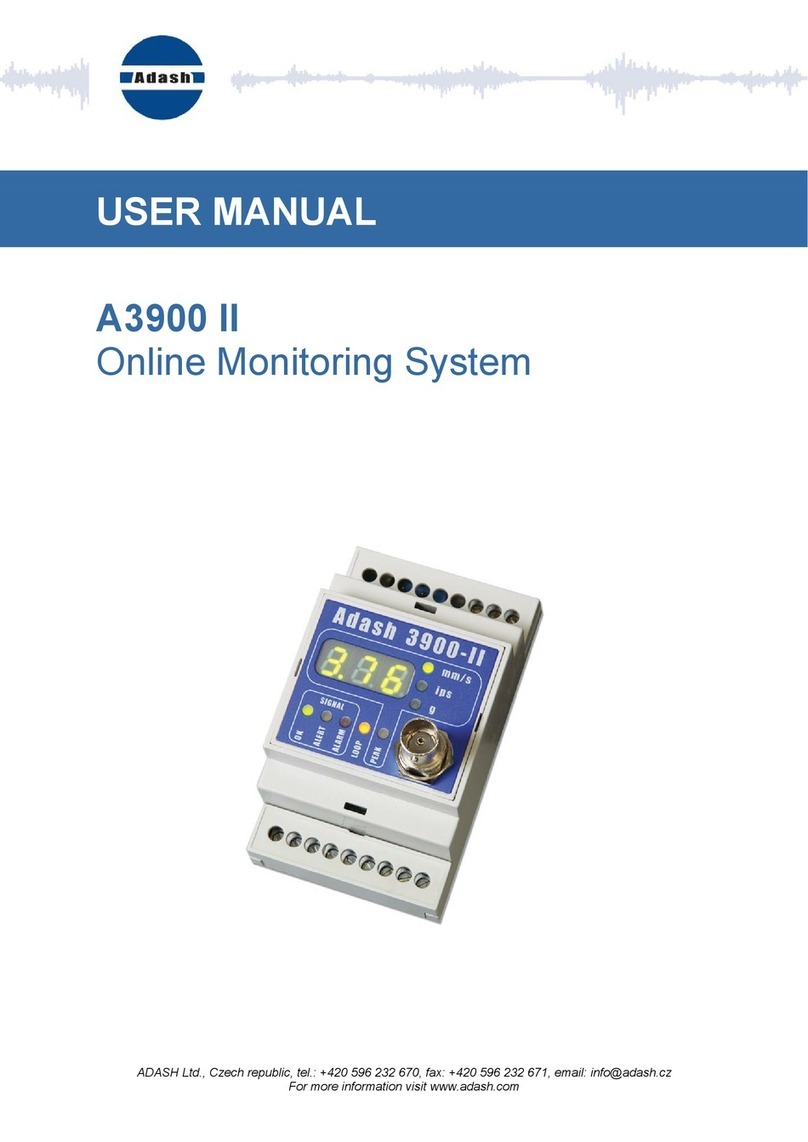
Adash
Adash A3900 II User manual
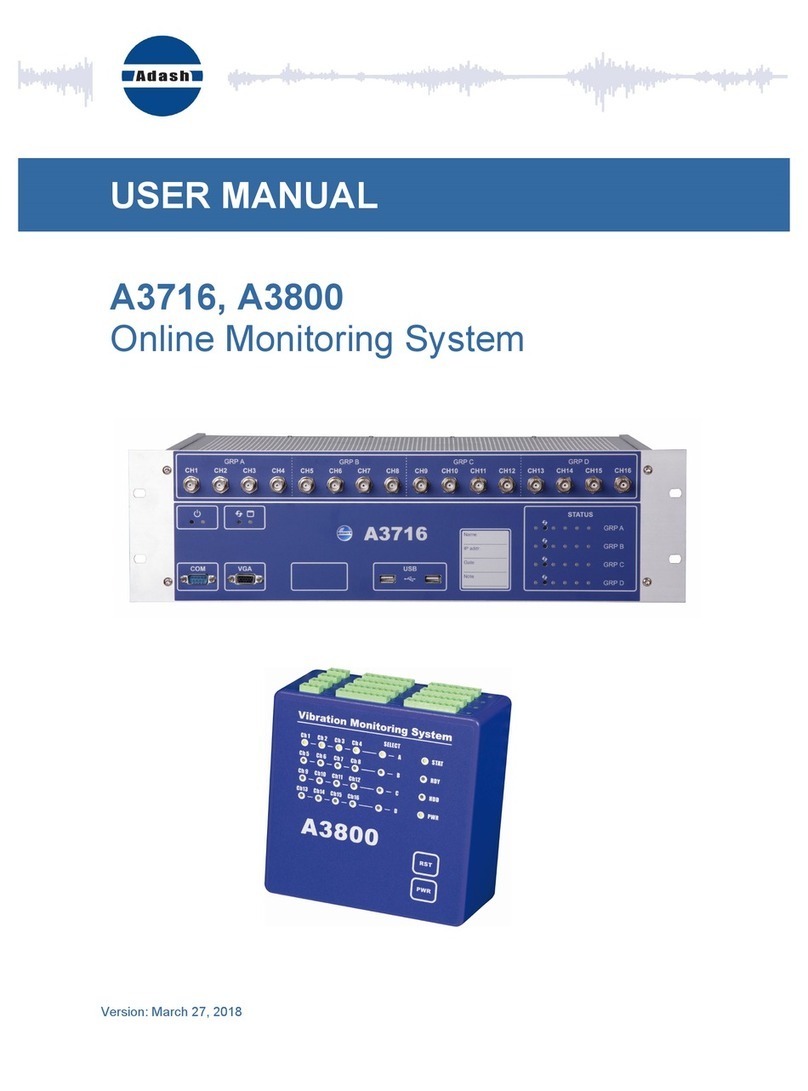
Adash
Adash A3716 User manual
Popular Measuring Instrument manuals by other brands
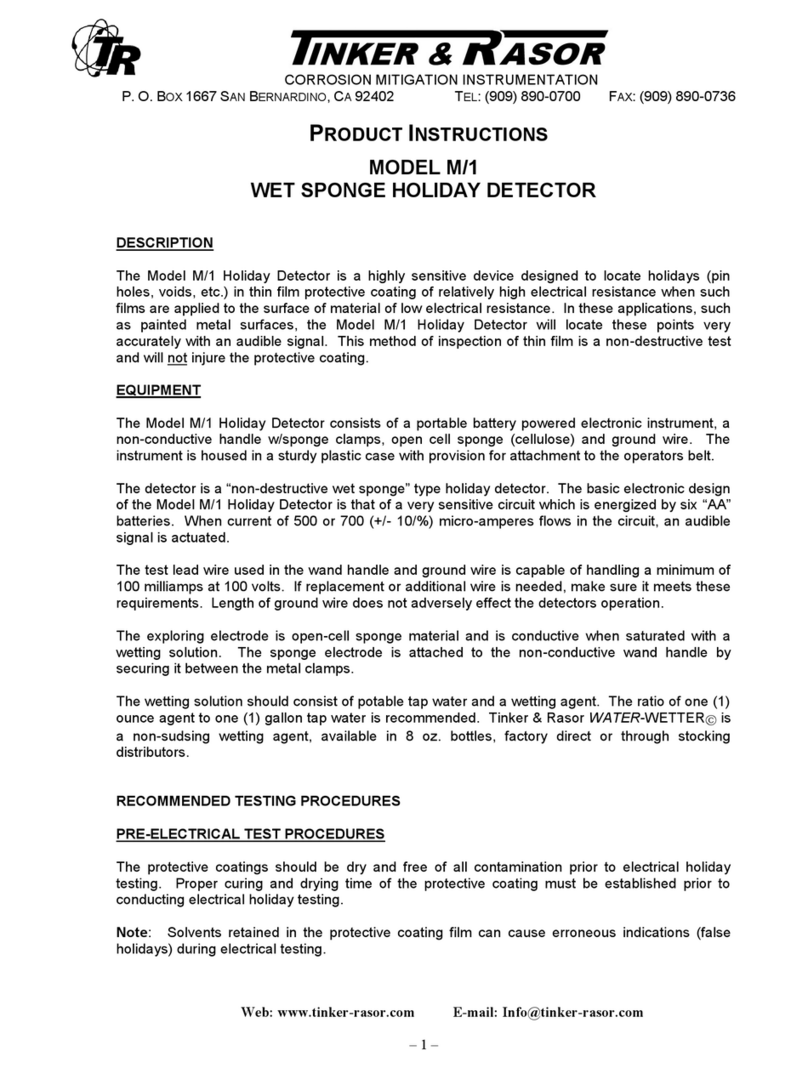
Tinker & Rasor
Tinker & Rasor M1/AC Product instructions

ABQINDUSTRIAL
ABQINDUSTRIAL Dakota Ultrasonics ZX-2 instruction manual

Blackline Safety
Blackline Safety G6 Dock Technical user's manual
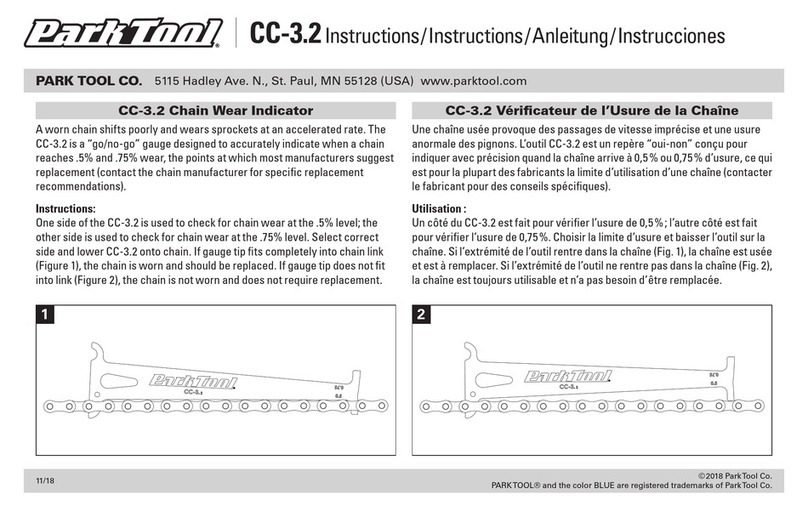
parktool
parktool CC-3.2 instructions
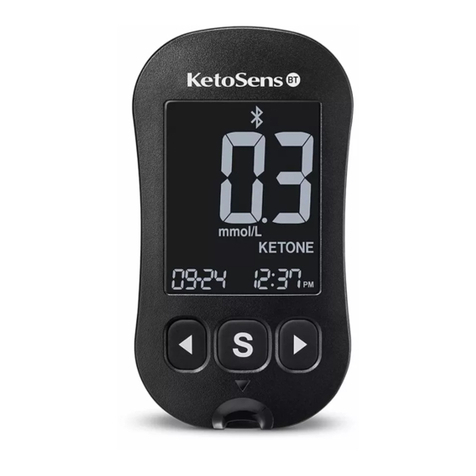
iSens
iSens KetoSens user manual
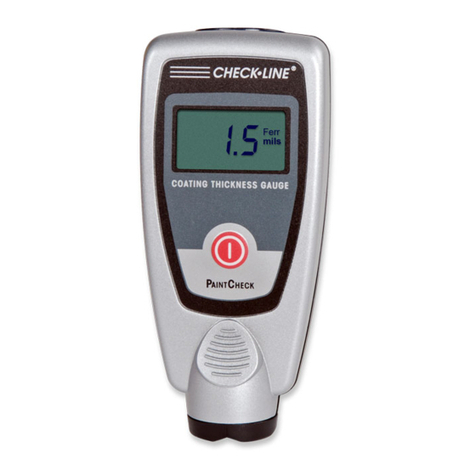
Check-line
Check-line PaintCheck operating instructions