Adast Systems MINOR V-line 899 Series Operation and maintenance manual

Adast Systems, a.s., 679 04 Adamov No. 496, Czech Republic
T+420 516 519 201, F+420 516 519 102, [email protected]
www.adastsystems.cz
OÚ/001/2005/MSS/A
XI/2018
USER´S MANUAL
Instructions for Operation, Maintenance
and Installation
Fuel Dispenser with Suction or Pressure
Pumping System
POPULAR
MINOR
V-line 899x.xxx


USER’S MANUAL V-line 899x.xxx
I
CONTENT
1. INTRODUCTION ......................................................................................................... 1
1.1. Used symbols ....................................................................................................1
1.2. Marking of important information ...........................................................................1
1.3. Operating, maintenance and installation instructions ...................................................2
2. IMPORTANT NOTICE ................................................................................................... 2
3. USE ........................................................................................................................ 4
3.1. The environment of use .......................................................................................4
3.2. Marking of liquid fuels .........................................................................................4
4. INSTRUCTIONS FOR THE SAFETY OF WORK ...................................................................... 6
4.1. Safety of the equipment design..............................................................................6
4.2. Operation safety ................................................................................................7
4.3. Ecological safety ................................................................................................7
4.4. Hygiene ...........................................................................................................8
5. DESCRIPTION ............................................................................................................ 9
5.1. Skeleton ........................................................................................................ 10
5.2. Hydraulic system of the fuel dispenser ................................................................... 11
Hydraulic system of the fuel dispenser V-line 899x.4x2 ........................................................ 12
Hydraulic system of the fuel dispenser V-line 899x.6x2 ........................................................ 13
5.3. Electronics ..................................................................................................... 15
5.4. Vapour recovery system ..................................................................................... 16
5.5. Signalling of dispenser conditions (SO) ................................................................... 30
5.6. SOPA design.................................................................................................... 30
5.7. Design with heating of the electronic case .............................................................. 30
6. TECHNICAL DATA......................................................................................................30
6.1. Basic parameters for the classical and alternative fuels with dynamic viscosity up to 20 mPa.s30
6.2. Basic parameters for the vegetable and mineral oils with dynamic viscosity up to 1000 mPa.s36
7. IDENTIFICATION .......................................................................................................38
8. OPERATION .............................................................................................................39
8.1. putting the dispenser into operation...................................................................... 39
8.2. Attendance..................................................................................................... 40
8.3. Dispenser operation .......................................................................................... 40
8.4. Functions of KL-MANINF Manager and KL-SERINF service keyboardS ................................ 41
9. MAINTENANCE OF A DISPENSER AND ITS INDIVIDUAL OPERATING UNITS .................................43
9.1. Pumping monoblock .......................................................................................... 44
9.2. Piston flowmeter.............................................................................................. 45
9.3. Electromagnetic two-stage valve .......................................................................... 45
9.4. Sight glass of the dispenser ................................................................................. 45

V-line 899x.xxx USER’S MANUAL
II
9.5. Dispensing hose ............................................................................................... 45
9.6. Dispensing nozzle ............................................................................................. 45
9.7. V-belt of the pump ........................................................................................... 46
9.8. Dismantling of covers ........................................................................................ 46
9.9. Maintenance instructions for dispenser body parts..................................................... 47
9.10. Electronic counter............................................................................................ 48
10. DISASSEMBLY AND DISPOSAL ....................................................................................... 48
11. SUMMARY OF BASIC PRINCIPLES FOR DISPENSER MAINTENANCE ........................................... 48
12. TRANSPORT ............................................................................................................ 49
13. INSTALLATION OF THE FUEL DISPENSER......................................................................... 49
13.1. Hydraulic part ................................................................................................. 50
13.2. Mounting of spring of the spring hinge.................................................................... 53
13.3. Wiring........................................................................................................... 54
14. PACKING AND STORAGE ............................................................................................. 55
14.1. Packing ......................................................................................................... 55
14.2. Storag ........................................................................................................... 55
15. GUARANTEE AND CLAIMING......................................................................................... 55
16. SPARE PARTS CATALOGUE .......................................................................................... 56
17. ACCESSORIES........................................................................................................... 56
18. DOCUMENTATION DELIVERED ...................................................................................... 56
19. ENCLOSURES ........................................................................................................... 57

USER’S MANUAL V-line 899x.xxx
1
1. INTRODUCTION
The instructions for attendance, maintenance and installation serve the user to gain information on the
design, correct attendance, maintenance and safe installation.
The information included in the present instructions are mandatory and the manufacturer does not
accept any responsibility for any damage due to their non-observance.
The manufacturer reserves the right to make technical modifications without further notice due to
constant product development and improvement.
Keep the instructions accessible to users throughout the dispenser operation!
1.1. Used symbols
Smoking forbidden
Open flame use
forbidden
Use of mobile phones
forbidden
Warning
Attention!
Electrical device
Explosion hazard
Toxic substances
Forklift
Recyclable packaging
Recyclable material -
steel
Recyclable material -
aluminum
1.2. Marking of important information
ATTENTION!
Failure to comply with the requirements in this table may result in personal injury or
death, or extensive property damage.
WARNING!
Failure to meet the requirements in this table may result in personal injury or damage
to the dispenser.

V-line 899x.xxx USER’S MANUAL
2
NOTICE!
The requirements in this table are based on laws, standards and regulations that deal
with the design, installation and operation of dispensers. Failure to meet these
requirements may cause a dangerous situation or cause damage to the dispenser.
NOTE
Best practices, techniques, and methods to ensure correct installation, maintenance and
operation of the dispenser. Failure to do so may cause damage or poor performance of
the dispenser.
1.3. Operating, maintenance and installation instructions
Before installing, putting the dispenser into service or servicing, read this manual. Instructions must be
carefully read and understood before any manipulation of the product begins.
Pay special attention to warnings!
This document is a guideline compiled by the manufacturer of the dispenser for users, service personnel
and designers.
The information contained in this manual is binding and the manufacturer is not liable for any damages
caused by non-compliance.
The manufacturer reserves the right to make technical modifications without further notice due to
constant product development and improvement.
NOTICE!
Instructions are an integral part of the product and must be accessible to users
throughout the service life of the dispenser!
2. IMPORTANT NOTICE
ATTENTION!
The dispenser is a complex device that has to provide a variety of demanding
functions.
Prior to commissioning, clean the tanks, piping and clean the fuel. A clogged filter can
not be considered as a reason for warranty service.
Must be revised electrical distribution and control correct wiring to prevent electrical
shock and ensure the safety of explosion - fuels are flammable liquids I. and II. hazard
classes!
The instructions for attendance, maintenance and installation serve the user to gain information on the
design, correct attendance, maintenance and safe installation.

USER’S MANUAL V-line 899x.xxx
3
The information included in the present instructions are mandatory and the manufacturer does not
accept any responsibility for any damage due to their non-observance.
The dispenser is complicated equipment providing many important functions.
Prior to putting into operation tanks and the piping system shall be cleaned and fuel purity shall be
checked. Also el. power distribution and correct wiring shall be inspected to prevent injury by el.
current and to provide explosion proofness –fuels are flammable liquids of the 1st and 2nd danger
class!
The manufacturer tests each dispenser considering the function, safety and metrology. Each delivery
shall include the instructions for attendance, maintenance and installation, EC declaration of conformity
and a service book identifying dispenser components. The dispenser, produced with high precision and
care, secures reliable and safe operation. Principal safety regulations protecting the user against injury
shall be kept during operation and maintenance and the dispenser shall be prevented from damage.
ATTENTION!
No modifications of the dispenser equipment are allowed without producer’s written
approval!
Important instructions for installation and operation:
a) Study the instructions for attendance, maintenance and installation and other manufacturer’s
documents included within dispenser accessories before you start to handle the equipment.
b) Check the dispenser delivery completeness and inform the manufacturer immediately in case of any
discrepancies or damage.
c) The dispenser shall be stored in a dry and protected room before it is installed at the filling station.
d) Prior to dispenser installation check the completeness of the filling station technology according to
the valid design, check the connecting dimensions of the foundation frame including the piping
system outlet.
e) Rinse the process equipment (piping) through the filtration equipment until impurities are removed.
f) The dispenser requires the connection of the vapour return piping of min. DIN 16 –we recommend
DN 25.
g) Wiring and inspection of the dispenser shall be carried out.
h) When putting the dispenser into operation, proceed according to the point 7 of the present
instructions.
i) A metrology authority specialist shall perform function test and metrology checking.
j) Being these conditions fulfilled, after the approval of a state supervision authority and the
verification of a metrological office representative, usual operation can be started.
k) Only qualified and trained staff of a service company can perform service and installation. Service
procedures shall be performed in compliance with the operation regulations of the filling station. The
manufacturer is not responsible for damages due to the incompetence of the staff.
l) The owner can only start dispensing when the filling station inspection is finished and a
metrology authority carries out metrological verification of the dispensers.
m) When fuels are pumped, basic hygienical precautions shall be adhered. The owner shall enable
the customer to use protective gloves.
SAVE FOR FUTHER USE!

V-line 899x.xxx USER’S MANUAL
4
3. USE
Fuel dispensers type series V-line 899x.xxx with electronic counter used for the dispensing of
liquid petroleum products - automotive petrol, diesel, kerosene, etc., of alternative liquid fuels
(biofuels) - biodiesel (B 10 - B 100) - a mixture of diesel fuel with FAME (Fatty Acid Methyl Ester)
and a mixture of automotive petrol with bioethanol (E10 - E 85) (flammable liquids I. to IV. hazard
class and group explosivity IIA) with dynamic viscosity up to 20 mPa.s and with flow rate optional
40, 60, 70, 80, 110, 120, 130, 150 dm3. min-1.
Special modification dispensers type series V-line 89xx.xxx/OIL are determined to dispensing liquid
fuels on the base of vegetable oil (rape oil, sunflower oil, soya oil, which are modified for internal
combustion in diesel engines) and mineral oils with maximum dynamic viscosity up to 1000 mPa.s
and with flow rate optional 40, 60, 70, 80 dm3. min -1.
They have been designed for the installation at road filling stations and a fleet of vehicles, etc.
By means of a communication line the dispensers are connected to the control system of self-service
operation or serviced operation.
The dispensers are equipment with special requirements concerning safety, metrology and ecology.
The dispensers are equipped to exhaust vapours; thus ecological operation of filling stations is provided,
i.e. the prevention of harmful petrol vapours leakage into atmosphere.
ATTENTION!
The V-line 899x.xxx dispensers and their hydraulic system must not be used to dispense
other than the manufacturer's specified liquid fuels without the manufacturer's approval!
ATTENTION!
The dispenser shall not be installed in an explosion danger zone 0, 1, 2 in compliance
with zones specified in the EN 60079-10-1!
3.1. The environment of use
The dispenser has been designed for outdoor installation
Environmental class
H3 according to OIML D11 - outdoor - stationary (natural
environment with the exception of those which are in extreme
climatic zone conditions such as polar and desert environment.
Machanical class
M 2 –with ADPxxx electronic calculator
M 1 –with CDC electronic calculator
Elektromagnetická třída
E 2 - with ADPxxx electronic calculator
E 1 –with CDC electronic calculator
Humidity
Condensing
3.2. Marking of liquid fuels
Marking of liquid fuels on fuel dispensers according to EN 16942 "Fuels - Identification of vehicle
compatibility - Graphical expression of information for consumers".

USER’S MANUAL V-line 899x.xxx
5
3.2.1. Gasoline-type fuels
“E” stands for specific biocomponents (ethanol) present in petrol (5 % bio-components - bioethanol):
“E” stands for specific biocomponents (ethanol) present in petrol (10 % bio-components - bioethanol):
“E” stands for specific biocomponents (ethanol) present in petrol (85 % bio-components - bioethanol):
3.2.2. Diesel-type fuels
Diesel fuel according to EN 590 + A1:2018 (7 % of bio-components –FAME):
Diesel fuel according to EN 590 + A1:2018 (10 % of bio-components –FAME):
Diesel fuel according to EN 590 + A1:2018 (20 % of bio-components –FAME)
Diesel fuel according to EN 590 + A1:2018 (30 % of bio-components –FAME):

V-line 899x.xxx USER’S MANUAL
6
FAME according to EN 14214+A1:2014 (100 % bio-components - FAME):
4. INSTRUCTIONS FOR THE SAFETY OF WORK
ATTENTION!
Any handling open flame is prohibited during fuel filling and smoking is prohibited even
in vehicles interior. Also filling vehicle tanks with running motor and any other activities
possibly initiating explosion are prohibited!
4.1. Safety of the equipment design
The manufacturer guarantees safety of the equipment design.
The dispenser design complies with the EN 13617-1 requirements and it is homologated for the
operation in environment specified by II2G IIAT3 symbols shown on the dispenser plate.
Considering operation safety in environs with explosion danger the dispensers have been EC –type
examination (certification) according to the Annex III of the Directive 2014/34/EU –ATEX by an
authorised body FTZÚ, Pikartská 7, 716 07 Ostrava –Radvanice –Notified body no. 1026.
EC - Type Examination Certificate: No. FTZÚ 05 ATEX 0185
Regular inspection of production quality assurance according to Annexes IV and VII of the Directive
2014/34/EU executes FTZÚ, s.p., Ostrava –Radvanice, Notified body no. 1026.
Notification of quality assurance: No. FTZÚ 02 ATEX Q 020.
Considering legal metrology the dispensers have been EC –type examination (certification)
according to the Annex B of the Directive 2014/32/EU –MID by an authorised body Český
metrologický institut, Okružní 31, 638 00 Brno – Notified body no. 1383.
EC - Type Examination Certificate: No. TCM 141/07 - 4505
The producer performed a conformity examination for the fuel dispenser with the type described
in EC –Type Examination Certificate No. TCM 141/07 –4505 and technical requirements according
to the Directive of European Parliament and the Council 2014/32/EU.
The producer is competent for “The Declaration of Conformity” with the type based on production
quality assurance of measuring units according to the Directive Supplement D of European
Parliament and the Council 2014/32/EU.
Certificate of the Quality Management System for production, check-out and testing:
No. 0119-SJ-C007-07.
Regular inspection of production quality assurance, check-out and testing according to the
Directive Supplement D of European Parliament and the Council 2014/32/EU executes authorised
body Český metrologický institut, Okružní 31, 638 00 Brno – Notified body no. 1383.

USER’S MANUAL V-line 899x.xxx
7
4.2. Operation safety
NOTICE!
The owner is responsible for the filling station operation and is obliged to follow the
course of fuel pumping. In case a customer uses the dispenser incorrectly, the owner
shall instruct him about proper use.
The owner shall also identify the hazard zone of the filling station by warning symbols
(smoking prohibited, open flame prohibited, direction of arrival to dispensers, etc.).
Operation regulations of the filling station shall be accessible for the customer, which
enables him to get information on principal obligations.
Operator’s obligation:
–Keep the equipment in safe and proper condition.
–Follow the operation regulations and attendance instructions of the filling station.
–Report immediately any failure to the owner and put the equipment out of operation in case of
delay.
–Keep order permanently.
–The dispenser and storage tank operators are not allowed to repair the equipment and to reset any
safety valves.
Performance of service work is a special case. Servicemen are not allowed to break operation safety
during repairs and other activities. When dispenser covers are removed, they shall be very careful to
protect both them and customers against injury.
El. current supply shall be disconnected when handling el. components. Only approved components
shall be used to replace any parts.
All parts subject to approval shall be always in conditions required by the technical documentation
(leakproofness, earthing, electrostatic belts, electrostatically conductive filling hoses, etc.).
4.3. Ecological safety
In accordance with the „DIRECTIVE 2009/126/EC OF THE EUROPEAN PARLIAMENT AND OF THE
COUNCIL of 21 October 2009 on Stage II petrol vapour recovery during refuelling of motor vehicles
at service stations“must be filling station for dispensing gasoline equipped according to the national
legislative regulations of the country of destination (installation and operation of fuel dispensers)
Decree recovery system (reverse drain stage II petrol vapor - Equipment recuperate (consultation draft)
petrol vapor displaced from the fuel tank of a motor vehicle during refueling and carrying gasoline
vapors to the storage tank at the service station.
IMPORTANT NOTICE!
Terms of service stations and control petrol vapor recovery system stage II is drived by
the "Directive 2009/126/EC of the European Parliament and Council" and the relevant
national legal regulations in force in the countries of destination (installation and
operation of fuel dispensers).
Fuel dispensers ADAST V-line 899x.xxx for dispensing of petrol are equipped with an
efficient recovery system (reverse exhaust vapor) that meets the requirements of the
"Directive 2009/126/EC of the European Parliament and Council”: Volumetric efficiency
of vapor recovery shall be between 95-105% - the rate of the volume of recovered vapor
at atmospheric pressure to total dispensed gasoline into the fuel tank of a motor vehicle
is equal to or greater than 0,95 but less than or equal to 1,05.

V-line 899x.xxx USER’S MANUAL
8
4.3.1. Check of petrol vapor control system –by the Directive 2009/126/EC
Check of petrol vapor recovery system Stage II at the dispenser shall be in accordance with
Directive 2009/126/ES under the relevant national legislation and regulations applicable in the
countries of destination (installation and operation of fuel dispensers).
Regular checks under Directive 2009/126/EC
1. Checking the operating efficiency of petrol vapor recovery system Stage II must be
performed at least once per year. Checks whether the ratio is the ratio of the volume of
paid vapor at atmospheric pressure to the total volume of gasoline fished into the fuel tank
of a motor vehicle is equal to or greater than 0,95 but less than or equal to 1,05.
2. If the dispensers installed automatic monitoring system, the efficacy of petrol vapor
recovery stage II tested at least once every three years. Any such automatic monitoring
system shall automatically detect faults in the proper function of petrol vapor recovery
system Stage II and in the automatic monitoring system, indicate faults to the service
station and automatically stop the flow of petrol from the faulty dispenser if the fault is not
rectified within seven days.
IMPORTANT NOTICE!
All fuel dispensers used for dispensing gasoline must be equipped with clearly labeled,
indicating the need for customers to fully insert the nozzle into the filler neck of the
vehicle tank.
Check of petrol vapor recovery system Stage II at fuel dispensers
ADAST POPULAR V-line 899x.xxx.
To check the operating efficiency of petrol vapor recovery system Stage II are two procedures:
1. Procedure for dispensers where the pump driven by an electric pump without electronic
control system vapor recovery:
The test is performed for pumping petrol into a suitable volumetric container at 50% and 100%
of the nominal flow of petrol. Measuring the effectiveness of this system is carried out solely
for the purpose meter designated as a special meter Bürkert G4-RF1 connected to the suction
nozzle attachment with a universal connector UMAX 2 companies ELAFLEX).
2. Procedure for dispensers with electronically controlled petrol vapor recovery system Stage
II, which allows to perform the test without using gasoline:
The test is carried out so-called "dry way" apparatus approved for this purpose - eg special
meter Bürkert G4-RF1 connected to the suction nozzle attachment with a universal connector
UMAX 2 companies ELAFLEX). Gas meter Bürkert G4-RF1 is via pulse output is connected
through a special cable to enter the electronic counter. Linking meter counter and must be
done at a gas station through the reduction of RP/M/EX, which contains zener barrier for
intrinsic safety.
4.4. Hygiene
The dispensers are hygienically harmless for customers and the owner. But protective gloves are advised
to be used during maintenance or filling fuel. In case skin comes to contact with fuel or impurities, wash
the spot with water and soap as soon as possible. When eyes come to contact, medical treatment is
necessary. Do not inhale harmful vapours when filling fuel.

USER’S MANUAL V-line 899x.xxx
9
5. DESCRIPTION
The fuel dispensers V-line 899x.xxx with electronic counter are used to the dispensing of liquid oil
products (inflammable liquids the I. to IV. of danger class.
These dispensers enable one-sided or two-sided simultaneous output of 1 or 2 kinds of products.
With respect to the application the dispensers of the V-line 899x.xxx type series are supposed to be
installed at the following filling stations:
-V-line 899x.xxx/S –for filling stations with the suction system of pumping
-V-line 899x.xxx/P –for filling stations with central pressure distribution system
Fuel dispensers V-line 899x.xxx/S are in the suction design with own pumping aggregate in the fuel
dispenser for each product.
Fuel dispensers V-line 899x.xxx/P are in the pressure design for central pressure system which is made
by the help of submersible pump in the storage tank of the filling station.
The dispensers have been designed for the installation at road filling stations and a fleet of vehicles,
etc. By means of a communication line the dispensers are connected to the control system of self-
service operation or serviced operation (V-line 899x.614 dispensers fitted with mechanical counter can
only be operated in service mode).
V-line 899x.xxx/S, V-line 899x.xxx/P fuel dispensers are designed as self-contained sectional
contruction.
Two-space body is designed in the 3 styl variants –with one column for one product or with two columns
for two products, 3. modification is two-space body without column. A special modification with one-
space body is determinated for metering unit with the mechanical counter.
Construction of V-line 899x.xxx fuel dispensers consist from following basic modules:
Position number
Name of the part of dispenser V-line 899x.xxx
1
Skeleton
2
Integrated hydraulic unit
3
Vapour recovery system
4
Control electronic
5
Dispensing hose ADAST, ELAFLEX, GOODYEAR, ТRELLEBORG
6
Dispensing nozzle ELAFLEX, OPW , ABR, RAKORD
7
Safety Swivel Break ELAFLEX, OPW
8
Sight glass ADAST, ELAFLEX
9
Reducer
10
Transit socket
11
Safety socket
12
Spring
13
Spring

V-line 899x.xxx USER’S MANUAL
10
5.1. Skeleton
Skeleton –a self-supporting structure consisting of parts with high anticorrosive resistance. The base of
the dispenser is made of steel sheet, zinc-coated and varnished. Internal parts of the skeleton are made
of galvanised sheet. Parts of the body with the exception of the door of the hydraulic module and the
electronic counter case are made of stainless brushed sheet as a standard.
High resistance acrylurethane enamel is applied on the hydraulic module door and the electronic
counter case. The colour shade of the door including the logo can be optional.
Both doors are lockable; being unlocked, swing out and with earth wire disconnected they can be
removed and thus the hydraulic part is accessible. Connect the earth wires when the door is fitted back.
A junction box is built-in into the supporting column and is accessible after dismounting the side cover
of the column.
5.1.1. Case of the electronic counter
A case of the electronic counter or ADAMAT electronics is bolted to the column. The counter case space
is closed with lockable covers. The covers are provided with transparent glass. Indicators with
integrated large-area display of dispensed volume, total price, price for one unit and unresetable
electromechanical total counters (totalizers) are connected from the case interior to the covers. The set
of these elements represents all necessary information for the customer.

USER’S MANUAL V-line 899x.xxx
11
The covers of the case are hung up on hinges enabling tilting upwards after unlocking and thereby easy
access in the case interior. The user’s local preselection keyboard (if required) is located on the case
cover as well - an independent keyboard for each dispensing point.
5.1.2. Case of the electronic counter –design 2017 (see fig.)
A case (1) of the electronic counter or ADAMAT
electronics is bolted to the hose module
column. The counter case space is closed with
lockable covers (2). The covers are provided
with transparent glass.
On the inside cover of the case is mounted
under glass large-area display (3) issued volume
and total price, which displays all necessary
information for the customer.
Above the display is placed IR sensor (5) for
controlling and adjusting the dispenser
calculator manager or servicing keyboard.
On the outer side of the case cover is placed
(optional) keyboard local user preferences (4) -
an independent keyboard for each dispensing
point.
On request they can be built in a case
unresetable electromechanical total counters –
totalizers (6), which are accessed by opening the cover.
The dispensing nozzles are seated in covers in the „V“ form pressed shape of the column. When the
dispenser is out of operation the dispensing nozzles in covers can be locked.
5.2. Hydraulic system of the fuel dispenser
The integrated hydraulic unit consists from following basic modules:
Position
number
Name of the part of the integrated hydraulic unit - dispenser V-line 899x.xxx/S
1
Pumping monoblock ADAST P64x.50 or P64x.100
2
Filter
3
Four-piston all-aluminium meter and an integrated magnetic pulse transmitter ADAST
M 403.25P, M 403.32P, M 403.25EP, M 403.32EP, 403.25P/1, M 403.32P/1,
M 403.25EP/1, M 403.32EP/1
4
Magnetic pulse transmitter Eltomatic ME 01-05 or ME 01-05-05 or METRA MTX 075 or
ADAST 40
5
Electromagnetic proportional valve or ON/OFF valve
6
Connection piece 250-CP
7
Vacuum pump
8
Tree-weldment - joining piece
9
Monoblock bracket
10
Vacuum pump bracket
ATTENTION !
Before opening the covers, it is always necessary to disconnect power to the dispenser
and perform a reliable hedge against its re-connection.

V-line 899x.xxx USER’S MANUAL
12
11
V-belt ELECTROOIL of Pumping monoblock
12
V-belt ELECTROOIL of Vacuum pump
13
Electric motor Motor bracket
14
Motor bracket
15
Blind flange
16
Flange PS G 1 ½“
17
Ring NBR 70 50 x 3
18
Belt pulley
19
Valve flange
20
Safety ring
21
ELAFLEX Gasket VD 33/24
22
Tube –assy MONO
23
ELAFLEX Gasket VD 42/29
24
Deaeration tube
25
Deaeration tube
26
Coupling DN 8
Hydraulic system of the fuel dispenser V-line 899x.4x2

USER’S MANUAL V-line 899x.xxx
13
Hydraulic system of the fuel dispenser V-line 899x.6x2
The integrated hydraulic unit consists of a pumping monoblok (pos. 1) with an integrated large-surface
filter (pos. 2), a meter (pos. 3) with integrated magnetic pulse transmitter (pos. 4) connected with the
pumping monoblok (pos. 1) through a special joining piece (pos. 8) and a driving el. motor (pos. 13) of
the pump.
Pumping monoblock type series P 64x.xxx/x (pos. 1) –is an independent unit for one kind of the
pumped fuel. An integrated compact structure contains an efficient filter (pos. 2), sliding vane pump,
control and non-return valves, safety relief valve with continual control of the operating pressure,
cyclone (centrifugal) gas separator and a venting chamber with a float valve. Progressive design provides
100 % separation of gaseous components and automatic blocking of filling when excessive amount is
identified in the product pumped.
The large-surface filter with an integrated non-return valve and standard filtration efficiency 30 µm
for petrol and optional 30 µm or 60 µm for Diesel oil (winter operation in extreme low
temperatures).
The pumped liquid passes through the filter (pos. 2) and the non-return valve to the pump and the
separator where gases and vapours are separated and pass to the float chamber. Condensed liquid is
discharged to the suction part of the pump and gases are exhausted to the vented part of the dispenser
base. The liquid is discharged from the non-return valve to the meter (pos. 3), then through an
electromagnetic valve (pos. 5) into the dispensing hose with a dispensing nozzle at its end. The
dispensing nozzle lever controls the rate flow. A tube sight glass can be installed between the dispensing
hose and the nozzle for visual checking.
A three-phase asynchronous motor (pos. 13) drives the pump by means of an antistatic V-belt (pos. 11).
Special modifications of the pumping monoblok of P 64x.xxx/x/BIO series is intended to measure
the volume of biofuel - a mixture of automotive petrol with bioethanol (E10 - E 85).
It has a special surface protection, which ensures their high resistance against aggressive biofuels.
Dispensers V - line 899x.xxx/P series (pressure design) differ from suction dispensers because they are
not equipped with the pumping monoblock. A safety breaking valve shall be fitted in the connection.
The valve prevents fuel leakage in case of the dispenser damage. This valve is not a part of the
dispenser, as well as the pump, which is located in the underground tank. The pressure dispensers are
equipped with an inlet spherical valve for closing the liquid input in case of repairs.

V-line 899x.xxx USER’S MANUAL
14
The pumped liquid is supplied from the central submerged pump located directly in the fuel storage
tank through the safety breaking valve, spherical check valve and the filter with filtering property of 30
µm for petrol and 30 or 60 µm for Diesel oil. Liquid is discharged from the filter through the meter and
the electromagnetic valve to the dispensing hose with the dispensing nozzle at its end. The dispensing
nozzle lever controls the rate of flow. The tube sight glass can be fitted between the dispensing hose
and the nozzle for visual checking.
Meter type series M 403xxxx/x is composed of a four-piston all-aluminium meter and an integrated
magnetic pulse transmitter. The original meter ensures metering accuracy within a wide range of
flow rates 4 - 150 dm3.min-1 and fuel operating temperatures -20 °C to +50°C (-10 °C to +50°C for
biodisel B 70 to B 100) and ambient temperatures -40 °C to +60°C for nominal pressure up to 0,32
MPa. The new design made of special materials considerably improves the accuracy and reliability. The
universal design for both mechanical and electronic calibration is an advantage. A two-channel
integrating impulse generator is a part of the meter. The number of impulses is proportional to the
swivelling angle of the shaft and the runoff volume of fuel.
The impulser generates 2 x 100 impulses per 1 dm3. The meter is electronic calibrated by an el. meter
processor with the help of the service keyboard.
Meters are supplied with optional integrated magnetic pulse transmitter Eltomatic ME 01-05 or ME
01-05-05 - type designation M 403.25P, M 403.32P, M 403.25EP, M 403.32EP or with a magnetic
pulse transmitter METRA MTX 075 or ADAST 40 - type designation M 403.25P/1, M 403.32P/1, M
403.25EP/1, M 403.32EP/1.
Special modifications to the type of meters M 403.25хP/B, M 403.25хP/B/1, M 403.32хP/B,
M 403.32хP/B/1 is intended to measure the volume of biofuel - a mixture of automotive petrol with
bioethanol (E10 - E 85).
Meters with the designation /В have special surface protection, which ensures their high resistance
against aggressive biofuels.
Meters with the designation of EP in electronic calibration, indicating P mechanical calibration
For the pumping of biodiesel (B 10 - B 100) - a mixture of diesel fuel with FAME (Fatty Acid Methyl
Ester) fully complies with standard hydraulic system of the dispenser!
Electric motors –el. motors 0,75 kW, 1,1 kW are used in the V-line 899x.xxx/S suction dispensers.
El. motors 0,37 kW, or 0,18 kW h for vapour exhaustion are used in the V-line 899x.xxx/P pressure
dispensers.
The number of the pumping monoblocks, meters and el. motors is specified according to the dispenser
type.
Dispensing hoses –single and coaxial dispensing hoses meet the requirements of the EN 1360. The
dispensing hose is located in a cover, which ensures the safekeeping of the hose when the dispenser is
out of operation. Depending on the dispenser type the dispensing hose is anchored either in a spring
hinge or in a special angle piece at the dispenser side.
For pumping biodiesel (B 10 - B 100) - a mixture of diesel fuel with FAME (Fatty Acid Methyl Ester)
must use a special hose for biodiesel - Elaflex Slimline BIO!!
Dispensing nozzles –are supplied according to the Client’s option. The nozzles are automatic, fitted
with a swivelling joint and an effective STOP system used in case of the tank overfilling or in emergency
situation. The nozzles can be fitted with safety disconnecting joints according to the Client’s option.
The dispensing nozzle is hung in the nozzle cover and it is lockable when the dispenser is out of
operation. Dispensing nozzles meet the requirements of the EN 13012.
For the dispensing of vegetable and mineral oils are used nozzles without the "STOP" function of the
main valve.
The dispensers are equipped with electromagnetic (solenoid) valves ON/OFF (double stage), or
electromagnetic proportional valves as a standard.

USER’S MANUAL V-line 899x.xxx
15
5.3. Electronics
The dispenser control shall meet the exacting requirements of simplicity and convenience and depends
on the hanging up and lifting of the dispensing nozzle.
ADP1/T, ADP2/T, ADP1/L electronic counter of an up-to-date design with central processor board
equipped with a high efficient microprocessor. The configuration of the counter and its modes of
operation are adjusted by more than seventy parameters. The counter is provided with a self-diagnostic
system. The counter outlets control the motors, valves, signalling circuits and vapours exhaustion. The
electronic counter processes the impulses coming from the impulse sensor and transmits them to the
display, which displays the dispensed volume, its price and a price per a volume unit. In case of power
failure or voltage drop the data displayed remain for 30 minutes at least.
Counters ADP1/T, ADP2/T, ADP1/L are standardly equipped for electronic meter calibration (Electronic
Calibration of Meters –EC) and per request by ATC –(Automatic Temperature Compensation)
Electronic Calibration of Meters (EC) enable to correct measured volume by designed declination in
operation range -5,00 % to +5,00 % of recognised meter non accurancy by step of 0,05 %.
Automatic Temperature Compensation (ATC) is designed to compensate temperature expandity of
dispensed medium based on measured temperature during dispensing. For temperature measuring is
used approved certified temperature sensor –resistance temperature sensor PT 100, in fuel dispensers
V-line 899x.xxx/S build in entering angle to pumping monoblock and in fuel dispensers V-line 899x.xxx/P
build in pipeline after the filter unit.
Calibration tablets for ATC on designed medium (type of fuel) can be integrated into SW of electronic
counter by customer request. Setting of calibration EC or ATC is provided by using of service keyboard
KL-SERINF and setting of proper calibrating switches DIP on body of electronics counter as per
instructions described in manual of electronic counters ADP1/T, ADP2/T, ADP1/L.
Providing of calibration is allowed to authorised person, only. The DIP calibration switches must be fixed
by plomb after calibration finish.
Displays: LCD type with BACK LIGHT illumination
LCD displays with BACK LIGHT DISPLAY (BLD) illumination are used especially for their good
readability. The duration of data holding on the display after supply voltage failure is 30 minutes at
least. Decimal point on BLD display devices is represented automatically in accordance with the setting
of parameters.
Lighting
LED diodes are used for the illumination of displays at dispensers.
ON / OFF switching of the illumination is automatically carried out with the activation of electronics.
Totalizer: non-resetable electronic counter of dispensed volume and its price –11 digits –or non-
resetable electromechanical counter of dispensed volume –7 digits.
Electronic counter of ADP1/T, ADP2/T, ADP1/L series operates with a 2-channel impulse generator
producing 2x 100 impulses per 1 dm3. The HW and SW counters of the ADP1/T, ADP2/T, ADP1/L series
enable high metering accuracy and the application of the electronic calibration using the 2-channel
impulse generator.
The local electronic preselection system in IP67 design is integrated into the cover of the counter
case. The preselection enables the Customer’s preselection of the exact volume or the price of the
product to be dispensed. The two-stage or proportional electromagnetic valves ensure the closing of
flow and exact dispensing of the preselected volume and smooth initiation of dispensing.
The fuel dispensers can be equipped with ADAMAT filling automatic equipment –payment terminal. This
equipment enables dispensing and payment of the product by means of contactless, magnetic and chip
cards including receipt printing and this equipment undertakes simultaneously all functions of the
dispenser electronic counter for non-public and public dispensing. The electronics of the filling
automatic equipment can be complemented by the ADP1/T, ADP2/T, ADP1/L electronic counter with
public dispensing.
The fuel dispenser is connected through a communication line to the control system, which controls the
operation of the whole filling station (releasing of dispensers, volume preselection, unit price variation,
self-diagnosis, etc.). The dispensers can be operated even at the filling stations without any control
system –i.e. in serviced operation.

V-line 899x.xxx USER’S MANUAL
16
Circuit diagrams for the connection of individual dispenser types to the switchboard of the filling station
–see enclosures.
5.3.1. Communication to the control system
The dispensers are equipped with ADP1/T, ADP2/T, ADP1/L electronic counters, which are able to
communicate to POS Win control systems. A communication serial interface RS 485 or a communication
standard IFSF LON are used for the communication of electronic counters to the superior control system.
Communication to different control systems shall be consulted with the manufacturer of the dispensers
in advance.
The fuel dispensers connected to the control system can be operated in the mode of volume
preselection or the financial sum preselection from the control system (the dispensers have to be
equipped with two-stage or proportional electromagnetic valves).
The POSWIN control system (POS Win EURO) enables the process control and the sale of goods
according to stock cards (999 999 items in 99 groups) including storage facilities. The control systems
communicate with the dispenser on the principle of the bus interface RS 485. They combine the basic
functions of the filling station, i.e. sale of fuels, sale of dry goods and their filing. The POS system is
also able to operate even as a multi-cash one, i.e. its individual parts can be interconnected in the
communication SW network, two backoffices and three tills, if more than five backoffices or tills are
connected, a server has to be included.
5.4. Vapour recovery system
Fuel dispensers ADAST POPULAR type line V-line 899x.xxx are supplied in the following modifications of
petrol vapor recovery systems :
1
System VRC-M
Vapour Recovery Control –Mechanical - control the flow of vapor by
hydromechanical proportional valve integrated into nozzle (Elaflex).
2
System VRC-E
Vapour Recovery Control –Electronic –control the flow of vapor through the
proportional solenoid valve directly controlled by an electronic control unit
dispenser (single-chip microcontroller electronic counter).
3
System VRC-M
+ VRMS
System VRC-M with automatic control system –VRMS (Vapour Recovery
Monitoring System).
VRMS system independently monitors system VRC-M - detect faults in the
proper function recovery system Stage II petrol vapor and VRMS system
itself, indicate faults to the service station and automatically stops the
flow of petrol from the faulty dispenser (dispensing areas), if the fault is
not rectified within seven days.
4
System VRC-E
+ VRMS
System VRC-E with automatic control system –VRMS (Vapour Recovery
Monitoring System).
VRMS system independently monitors system VRC-E - detect faults in the
proper function recovery system Stage II petrol vapor and VRMS system
itself, indicate faults to the service station and automatically stops the
flow of petrol from the faulty dispenser (dispensing areas), if the fault is
not rectified within seven days.
This manual suits for next models
4
Table of contents
Other Adast Systems Dispenser manuals
Popular Dispenser manuals by other brands

AMERICAN SPECIALTIES
AMERICAN SPECIALTIES EZ FILL 0394 Series quick start guide
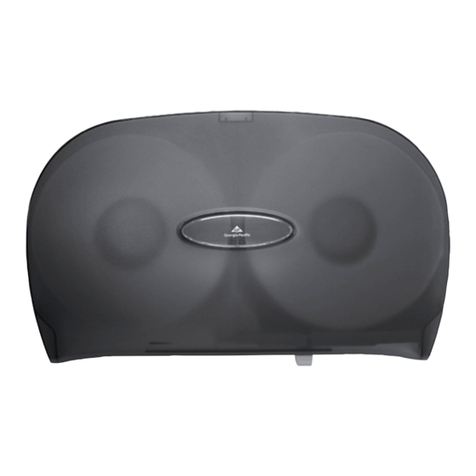
Georgia Pacific
Georgia Pacific Jumbo Jr. installation instructions
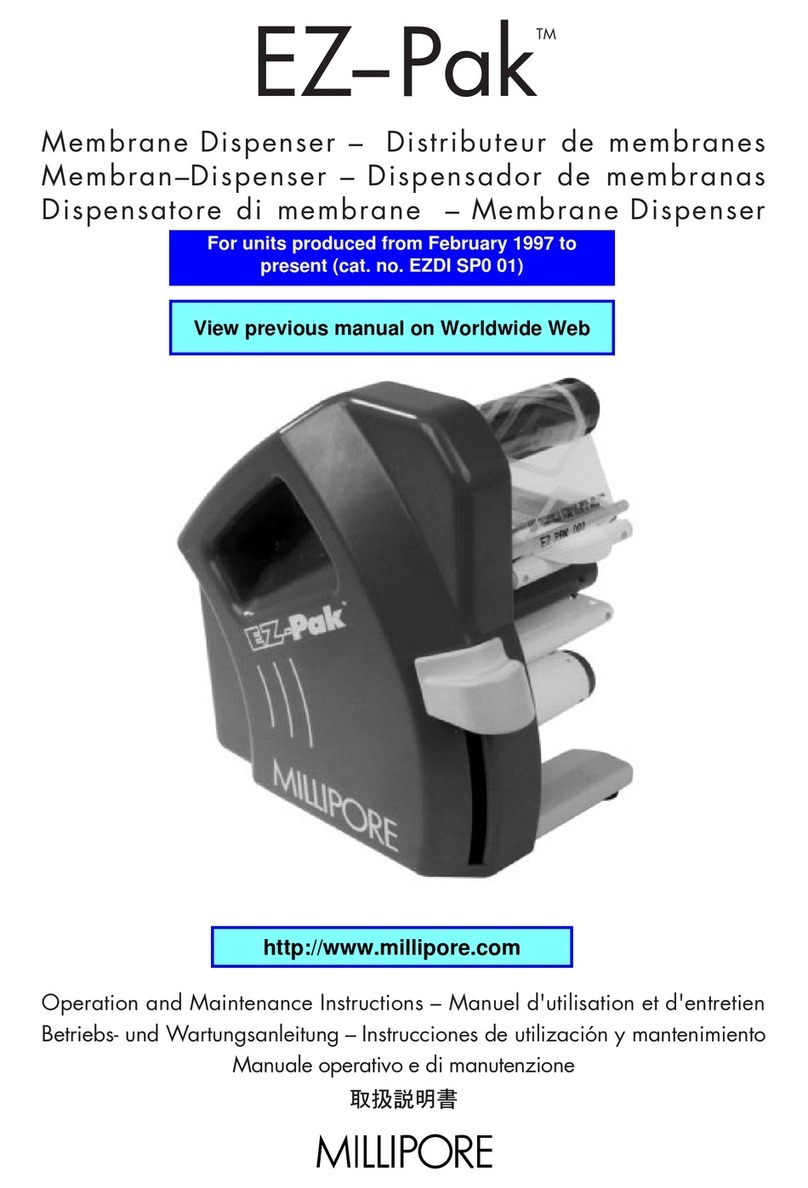
Millipore
Millipore EZ-Pak Operation and maintenance instructions
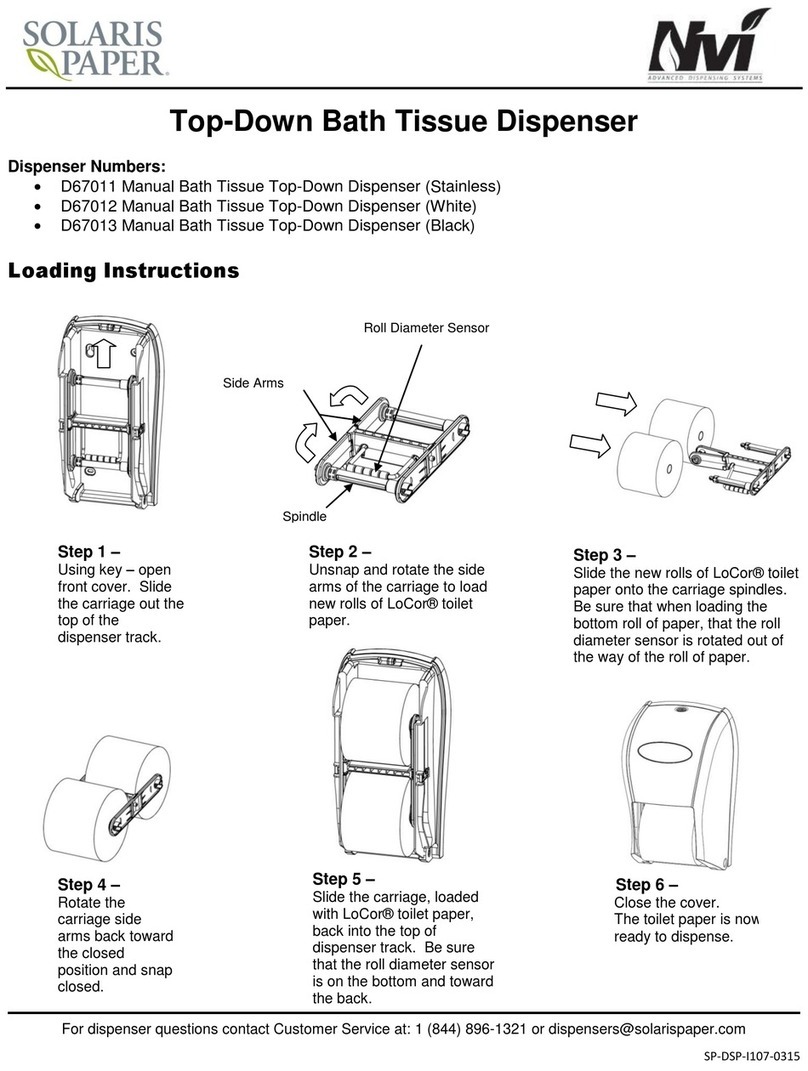
NVI
NVI SOLARIS PAPER D67011 quick start guide
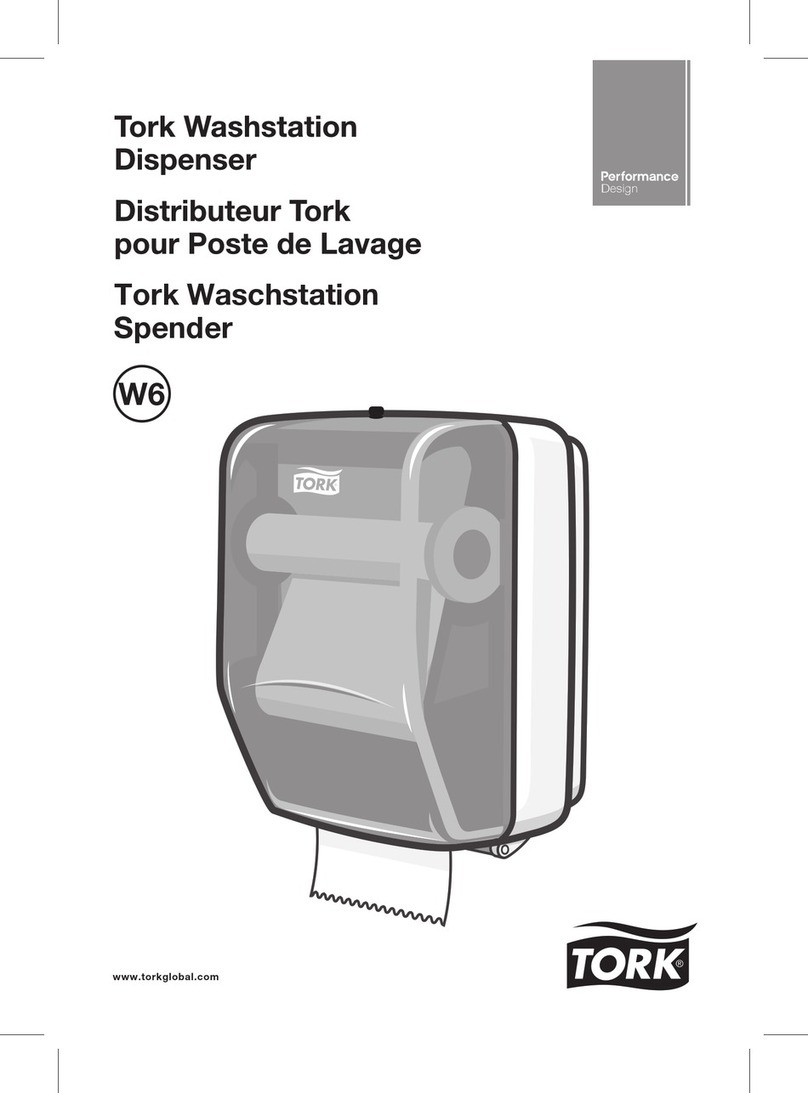
Essity
Essity TORK W6 manual
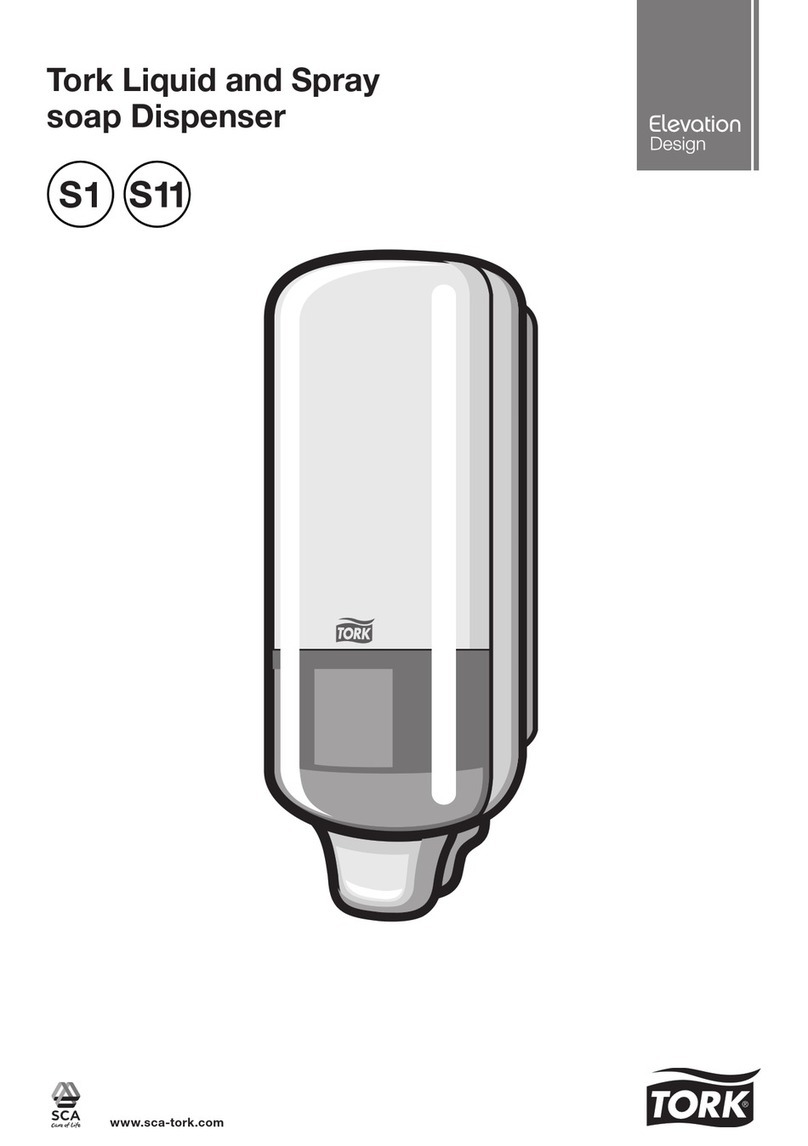
NSI
NSI Tork S1 manual