AMA Instruments The GC 5000 BTX User manual

OPERATING MANUAL
Gas chromatograph – GC 5000 BTX

Address of manufacturer:
AMA Instruments GmbH
Soeinger Straße 100
89077 Ulm, Germany
Tel +49 731 933-2100
Fax +49 731 933-2110
Imprint:
Operating Manual GC 5000 BTX
Version 5.0; English
Date: 11/2010

Operating Manual GC 5000 BTX; Version 5 – 11/2010 1
Table of Contents
Page
1.0 Information for the owner …………………………………………………........... 5
1.1 How to use the manual ……………………………………………………………… 5
1.2 Specific normal operation …………………………………………………………… 5
1.3 Delivery information …………………………………………………………………. 6
1.4 Standard and regulations …………………………………………………………… 7
1.5 Declaration of conformity …………………………………………………………… 7
1.6 Copyright ……………………………………………………………………………… 8
1.7 Service address ……………………………………………………………………… 8
2.0 Hazard Information ………………………………………………………………… 9
2.1 General hazard information ………………………………………………………… 9
2.2 Responsibility of the operator ………………………………………………………. 10
3.0 Product description - technical specifications ……………………………….. 11
3.1 Normal use of GC 5000 BTX ……………………………………………………….. 11
3.2 Hardware description ……………………………………………………………….. 12
3.3 Description of GC components .…………………………….……………………… 14
3.3.1 System control and watchdog.…………………………………………………….. 14
3.3.2 GC oven ………………..…………………………………………………………….. 14
3.3.3 Columns………………………………………………………………………... ……. 14
3.3.4 Detector……………………………………………………………………………….. 14
3.3.5 Setup of parameters….……………………………………………………………… 14
3.4 Technical data (GC 5000 BTX)..…………………………………………………... 15
3.5 Options……………………………………………………………………………….. 17
3.5.1 Calibration gas selector (optional)………………………………………………….. 17
3.5.2 Ozone precursor monitoring system (optional) ...………………..……..………… 17
3.5.3 Optional modules……………………………………. ….…………..………………. 18
3.5.3.1 Dilution module DIM 200……………………………………. ….…………..………. 18
3.5.3.2 Sample stream selector SSM 600…………………………. ….…………..………. 19
4.0 Installation …………………………………………………………………………… 21
4.1 Safety instructions…………………………………………………………………… 21
4.2 Installation condition ………………………………………………………………… 22
4.3 Gas connections …………………………………………………………………….. 22
4.4 Electrical connections ………………………………………………………………. 23
5.0 Start up and shut down ..……..…………………………………………………… 24
5.1 Safety instructions …………………………………………………………………… 24
5.2 Start up instructions …………………………………………………………………. 25
5.3 Decommissioning…….. …………………………………………………………….. 27
6.0 Setting up the GC 5000 Software ……………..…………………………………. 28
6.1 Status screen ……………………………………..………………………..………… 28
6.2 How to unlock – password protection ………….………………………………….. 30
6.3 How to select operation modes………………….…………………………………. 31
6.4 How to select master modes .……………………………………………………… 31
6.5 How to select communication parameters… …………………………………….. 32
6.5.1 Analog outputs configuration……………………………………………..…………. 32
6.5.2 Alarm configuration…………………………………………………..…..………….. 34
6.5.3 Gesytec specifications………………………………………………..…..………….. 35
6.5.4 Modifying parameters under “Gesytec specifications”..………………………….. 35

Operating Manual GC 5000 BTX; Version 5 – 11/2010 2
Page
7.0 Starting operation …..…………………………………………………………… 38
7.1 How to start measurement………………………………………………………….. 38
7.2 How to adjust the retention time windows………………………………………… 41
7.3 How to zoom / zoom out the chromatogram……………………………………… 45
7.4 How to optimize integration parameters…………………………………………... 47
8.0 Using LCD display and buttons on the front panel …………..….………… 48
9.0 Calibrating and validating ……………………………………………………… 51
9.1 Calibration……………………..……………………………………………………... 51
9.1.1 Calibration intervals..……..………………………………………………….……….51
9.2 How to enter the data of calibration gas concentrations..……………….…….. 52
9.2.1 Enter data - without a calibration gas module..…….………………………..…… 52
9.2.2 How to disable concentration levels ……………….……………………………… 52
9.2.3 Enter data - with a calibration gas module .……………………………………… 53
9.3 How to start a calibration…………………………….……………………………... 55
9.3.1 Calibration of one level……………………………………………………………….55
9.3.2 Calibration of sequence (without calibration module or cal. valves) .………… 56
9.4 Auto-calibration………………………………………………………………………. 57
9.5 Validation………………………..……………………………………………………. 58
9.5.1 Principle of validation……..…………………………………………………………. 58
9.5.2 Types of validation……………………………….………………………………….. 58
9.5.3 How to start validation……………………………….……………………………….59
10.0 Functional description ……………………………………………………………. 64
10.1 Measuring principle …………………………………………………………………. 64
10.2 Definition of the program step …………………………………………………….. 65
10.3 Program example …………………………………………………………………… 67
11.0 Software reference ………………………..……………………………………… 68
11.1 Basic software design ..…………………………………………………………...... 68
11.1.1 Software architecture ..…………………………………………………………....... 68
11.1.2 Configuration files …………………………………………………………………… 68
11.1.3 Main window: Program……………………………………………………………… 69
11.1.4 Menu items…………………………………………………………………………… 71
11.2 Unlock………………………………………………………………………………….72
11.3 Parameters……………………………………………………………………………73
11.3.1 Change password…………………………………………………………………….73
11.3.2 Operation mode……………………………………………………………………… 73
11.3.3 Remote control………………………………………………………………………..74
11.3.4 Master mode………………………………………………………………………… 77
11.3.5 Method…………………………………………………………………………………77
11.3.6 Analysis……………………………………………………………………………… 78
11.3.7 GC Oven……………………………………………………………………………. 79
11.3.8 Calibration…………………………………………………………………………… 81
11.3.9 Validation set up…………………………………………………………………… 84

Operating Manual GC 5000 BTX; Version 5 – 11/2010 3
Page
11.0 Software reference continuing
11.3.10 Analog output configuration………………………………………………………… 85
11.3.11 Alarm configuration…………………………………………………..…..………….. 86
11.3.12 CP Analysis……………………………………………………………………………87
11.3.13 CP File Editor……………….……………………………………………………...... 88
11.3.14 Module setup………………..……………………………………………………...... 97
11.4 Program steps……………………………………………………………………….. 98
11.4.1 Standard BTX …………………………………………………………………………98
11.4.2 BTX with stripper Column ………………………………………………………….. 101
11.5 View…………………………..……………………………………………………….. 104
11.6 Run calibration (manual and auto-calibration)……………………………………. 107
11.7 Run validation ……………………………………………………………………….. 109
11.8 Help functions …………….………………………………………………………… 110
11.8.1 Remote support….………….………………………………………………………. 110
11.8.2 About (current Software Version)………………………………………………….. 110
12.0 Miscellaneous procedures ……………………………………………………… 111
12.1 Programming and editing values ………………………………………………….. 111
12.2 Programming GC oven parameters …………………………………………….. 112
12.2.1 How to display the running temperature program …………..…………………… 112
12.2.2 Select the parameters for the running temperature program ………………….. 113
12.3 Start and stop ……………………………………………………………………… 114
12.4 Subsequent data processing………………..……………………………………… 116
13.0 Maintenance ………………………………………………………………………. 119
13.1 Security instructions ………………………………………………………………… 119
13.2 Maintenance schedule ……………………………………………………………… 120
13.3 Maintenance work ……………………………………………………………….. 121
13.3.1 Exchange the enrichment tube ……………………………………………………..121
13.3.2 Maintenance of the pump ………………………………………………………….. 122
13.3.3 Exchange the input filter of the MFC ……………………………………………… 122
13.3.4 Exchange or repair the capillary column ………………………………............... 123
13.3.5 Adjust the detector signal ………………………………………………………….. 125
13.3.6 Check the glow plug ………………………………………………………………… 125
13.3.7 Check the thermocouples ………………………………………………………….. 126
13.3.8 Check the heating units of detector and valve oven ……………………………. 126
13.3.9 Exchange of the PID lamp ………………………………………………............... 127
13.3.10 Clean the PID lamp window ………………………………….……………………. 128
13.3.11 Exchange the rotor of the rotary valve …………………………………………… 128
13.3.12 Exchange the GC oven motor …………………………………………………….. 130
13.3.13 Exchange the back panel fan ……………………………………………..………. 130
13.3.14 Exchange the Peltier cooler fan …………………………………………………… 131
13.3.15 FID maintenance …………………………………………………………............... 131
14.0 Troubleshooting …………………………………………………………………. 132
14.1 General faults ……………………………………………………………………… 132
14.2 Alarm messages …………………………………………………………………….. 134
14.3 Warning messages………………………………………………………………… 136
14.4 Error messages ..……………………………………………………………………. 139
15.0 Spare parts list ……………………………………………………………………. 140

Operating Manual GC 5000 BTX; Version 5 – 11/2010 4
Page
16.0 Warranty ……………………………………………………………………………. 140
17.0 GESYTEC-II protocol ……………………………………………………………. 141
17.1 Telegram definitions…………………………………………………………………. 142
17.2 Status request MZ…………………………………………………………………… 142
17.3 Status response ZM…………………………………………………………………. 142
17.4 Data request DA ..…………………………………………………………………… 143
17.5 Data response AD…………………………………………………………………… 144
17.6 Control command ST ………………………………………………………………. 144
17.7 Control response TS ………………………………………………………………... 146
17.8 Appendix ………..……………………………………………………………………. 146
18.0 Digital I/O ……………………………………………………………………………. 148
18.1 General ………..……………………………………………………………………. 148
18.2 Digital outputs…..……………………………………………………………………. 149
18.3 Digital inputs…..……………………………………………………………………. 150

Operating Manual GC 5000 BTX; Version 5 – 11/2010 5
1 Information for the owner
1.1 How to use the manual
Caution!
Please read this manual carefully before starting with operation.
The manual will provide you with information on using, installing, operating
and maintaining this unit. It ensures proper functioning and helps you to
operate the device more easily and efficiently.
Symbols:
Caution!
Pay particular attention to all kind of warnings and notes. Information of this
type is set apart from the rest of the text and specially identified by
appropriate symbols and pictograms
1.2 Specified normal operation
Before the system left the factory, it has been inspected and found to be in
perfect condition as regards safety. To ensure a safe and problem-free
operation, the product should only be used in the manner described by the
manufacturer. In addition, proper transportation, storage and initial
installation are vital to ensure a correct and safe operation as well.
This manual provides the information you will need to use the described
product in the proper manner for which it is intended. This manual includes
several safety information (including warnings). The knowledge of this
information is essential for hazard-free installation and operation as well as
maintenance.
Therefore the manual refers to technically qualified personnel especially
trained and authorized for maintenance and service of analyzer and
monitoring devices. Moreover they possess the knowledge of correct
interpretation of the safety information and warnings provided in this
manual. This ensures as well to put it properly into practice.
Note
The GC 5000 is configured and calibrated ex factory with your required
application. In particular you intend to use the analyzer for new applications,
we recommend you to contact your local supplier to discuss the application
in question. (See chapter 2.2 and 3.1as well)

Operating Manual GC 5000 BTX; Version 5 – 11/2010 6
1.3 Delivery information
When you receive the shipment, please check the following:
1. The packaging is not damaged.
2. Both indicators labels which are fixed on the package should display
the white color as a sign for proper transportation.
The package of the analyzer is posted with one so-called
“shockwatch” indicator label and one “tilt watch” indicator label. Both
labels change their color from white to red in case of improper
handling by the forwarder regarding tilts and shocks.
Note!
In case one of the indicator labels is red or both, note it on bill of lading,
inspect the shipment for damage and inform AMA Instruments within 10
days after arrival at latest.
The scope of delivery is corresponding to the relevant purchase contract
and is shown on the documents enclosed with the shipment:
3. Open the packaging and check whether the shipment is complete.
4. Check the serial number on the type plate with the serial number
specified in the shipping documents.
5. The operating manual is delivered on CD-ROM and recorded on the PC
of the analyzer as well.
Note!
Do not throw the original packaging away: A saver shipment is guaranteed
while using the original purpose-made packaging (it contains foamed
plastic inserts which are adapted to the size of the analyzer). Therefore we
recommend the storage of the original packaging.
6. First visual check-up of the analyzer:
When unpacking the system, remove the cover and have a closer look
to the interior of the analyzer. The following checklist may be of help:
All parts are fixed
Check additionally if the plug in card and the riser card are fixed
properly (optional installation)
Remove the cover of the GC oven and make a sight check of the
column
In case the column is broken, follow the instruction of chapter 13.3.4
- how to cut and repair a capillary column in the right way.

Operating Manual GC 5000 BTX; Version 5 – 11/2010 7
1.4 Standards and regulations
As far as possible the specifications and manufacture of this unit are based
on the harmonized European standards.
If this product is used outside the area of validity of these standards and
regulations, the standards and regulations valid in the owner’s country
should be observed.
1.5 Declaration of conformity
Our product GC 5000 BTX
is manufactured in compliance with the following standard(s) or documents:
Low-Voltage Equipment Directive 2006/95/EG
EMC Directive 2004/108/EG
Harmonized standards EN 61326 and EN 61010
In accordance with the named above EC directives, the EC Declarations of
Conformity are kept available for the relevant Authorities by
AMA Instruments GmbH
Soeflinger Strasse 100
D-89077 Ulm / Germany
If this product is used outside the European Union, the standards and
regulations valid in the owner’s country must be observed.

Operating Manual GC 5000 BTX; Version 5 – 11/2010 8
1.6 Copyright
The reproduction, transmission or use of this document or its contents is
not permitted without express written authority. Technical data are subject
to change. All rights are reserved by AMA Instruments GmbH, Ulm,
Germany.
1.7 Service address
If you require further information, which are not treated in sufficient depth in
this document or in case of malfunction, please contact your local supplier.
The responsible service engineer will provide you with the required
information.
In case of malfunction, it is recommended to have the following information
on hand:
•Detailed description of the failure
•Serial number of the system (on the back side of the analyzer)
Note!
In case of a repair, we would welcome your detailed information about the
failure in order to assure an efficient handling for a fast return shipment of
your system.
Note
For a saver shipment we recommend the use of the original packaging of
the analyzer which is purpose-made. (It contains foamed plastic inserts
which are adapted to the size of the analyzer.). For proper shipment the
system should be transported on a pallet.

Operating Manual GC 5000 BTX; Version 5 – 11/2010 9
2 Hazard information
2.1 General hazard information
Please observe the following notes to safeguard against damage to the
system described as well as to any systems which may be connected to it.
Safety information and warnings are given particular emphasis in this
manual by means of various symbol terms defined below. They apply to
both, users and service / electrical technicians. They intend to help
preventing dangers to life and health as well as preventing damages to
properties. These notes are also marked by warning symbols which reflect
the meaning of the accompanying text. Within the context of this manual
and information on the product itself, the terms used are defined as follows:
Danger!
This means that death or severe injury or considerable damage to property
will result if the corresponding precautions are not taken.
Warning!
This means that death or severe injury or considerable damage to property
could occur if the corresponding precautions are not taken.
Caution!
This means that damages to property may result if the corresponding
precautions are not taken.
Note
Provides important information about the product, about using it or about a
corresponding part of the manual to which special attention has to be
shown.

Operating Manual GC 5000 BTX; Version 5 – 11/2010 10
2.2 Responsibility of the operator
The analyzer described can only be used for applications which are
described in chapter 3.1. For operation of the system, the technical data
described in chapter 3.4 must be observed.
The analyzer described in this manual has been designed, manufactured,
inspected and documented in compliance with the relevant safety
standards. The design of the GC 5000 BTX ensures a safe operation. If the
operator follows the handling requirements and observes safety instructions
which are described for installation, operation and maintenance, then the
system will be not a source of danger to individual health and safety or to
property.
Warning!
In case you open the unit, certain parts which apply hazardous voltage
become accessible. Only qualified and accredited technicians in the field of
electricity are permitted to have access.
Only qualified and trained personnel with a thorough knowledge of all
sources of danger are permitted to have access to this system. Regarding
the safety information in this manual, qualified personnel is defined as
follows:
•The operating personnel – They are trained in operating the system
and observing its safety requirements. As well they are familiar with the
operation-related content of this manual. This means they are able to
fully understand the English written safety instructions.
•The commissioning or maintenance personnel – They are authorized to
install, operate, maintain and repair this kind of systems and electrical
circuits in accordance with accepted technical safety standards. They
possess the authorization and appropriate training to putting into
operation, maintain and repair this system. Furthermore they are able
to fully understand the English written safety instructions and
maintenance requirements as well.

Operating Manual GC 5000 BTX; Version 5 – 11/2010 11
3 Product description - technical specifications
3.1 Normal use of GC 5000 BTX
The AMA GC 5000 BTX has been developed for the continuous monitoring
of emission and immission levels of organic compounds in ambient air and
gas streams in the range of C4– C12. The instrument is characterized by its
compact design and its outstanding detection sensitivity in the ppt- range.
The analyzer is type approved according to DIN EN 14662-3 (August 2005)
and can be used for the legally obliged monitoring of benzene in ambient
air according to the guideline 2000/69/EC of the European parliament and
the council from November 16th 2000.
At the same time often concentrations of other aromatic hydrocarbons are
monitored as well.
According to the EU guideline 2002/3/EC from February 12th 2002, the VDI
guideline 2100 and the guidelines of the Technical Assistance Document
EPA/600-R-98/161 of the American environmental protection agency EPA
from September 30th 1998 the analysis system is also suitable for the
continuous monitoring of ozone precursors in the range of C4-C12.
A system for continuous monitoring of the complete range of ozone
precursor from C2-C12 can be configured by combining the GC 5000 BTX
and the GC 5000 VOC.
General range of applications:
•Ambient air monitoring, immissions and emissions control
•Aromatic hydrocarbons (BTEX, styrene, trimethylbenzene, ethyltoluene)
•Aliphatic hydrocarbons (1,3-butadiene, methylcyclopentane,
methylhexane)
•Chlorinated hydrocarbons (vinyl chloride, tri-chloroethene, tetra-
chloroethene)
The GC 5000 BTX analyzer is configured and calibrated ex factory with
your required standard application. This means that the equipment of the
system is adapted specifically to the required measuring task.
Application
ex factory

Operating Manual GC 5000 BTX; Version 5 – 11/2010 12
3.2 Hardware description - Overview
The GC 5000 BTX analyzer is constructed as a 19” plug in case. All
necessary parts are integrated as there are
•electronic control unit,
•PC, heater controller,
•gas regulation etc. and
•optional equipment as output requirements, calibration gas selector or
controller for external devices as permeation modules etc.
A 10” monitor is available optionally as well. Otherwise a monitor can be
connected to the external VGA interface.
Fig. 1: Front view of the GC 5000 Analyzer

Operating Manual GC 5000 BTX; Version 5 – 11/2010 13
Fig. 2: Rear view
Fig. 3: Gas regulation inside the analyzer

Operating Manual GC 5000 BTX; Version 5 – 11/2010 14
3. 3 Description of GC components
3.3.1 System control and watchdog
System control is realized via a built-in PC board with Windows XP and the
AMA control software.
Note
The GC 5000 features a hardware watchdog. In case of a software crash
or an operating system crash, the watchdog resets the internal PC. Then
the operating system and the AMA control software are started again
automatically and the GC 5000 is operating properly again. The
automated restart of the analyzer helps your service personnel: No extra
visits to the monitoring station are necessary.
3.3.2 GC oven
The GC module features a three step temperature program. It enables to
work with high end temperatures without having long cooling down-times as
construction and used materials of the GC components are characterized
by preventing from thermal inertia.
The dimensions of the oven are 21cm * 21cm * 8cm which makes app.
3500 cm3. The geometry of the oven allows the use of columns with their
own cages.
The maximum linear heating rate for the range between 40 -200°C is
25°C/min, adjustable in steps of 1°C/min.
3.3.3 Columns
The dimensions of the oven allow the use of commercial capillary columns.
This helps to exchange a column in a few minutes.
The GC can be equipped with capillary columns with an internal diameter of
0.32mm, 0.45mm or 0.53 mm and up to 60m length. For standard
applications use a 0.32mm column.
3.3.4 Detector
The standard detector is a FID (Flame Ionization Detector) or a PID (Photo
Ionization Detector). The output of the detector is an analog signal of 0-5 V.
The signal is digitized and analyzed by chromatography software.
3.3.5 Setup of parameters
The control software allows to enter and to modify all analysis parameters.
Unauthorized access is avoided due to password protection.

Operating Manual GC 5000 BTX; Version 5 – 11/2010 15
3.4 Technical data GC 5000 BTX
General
Case 19” plug-in case
Height 6 height units
Depth 600 mm
Weight approx. 40 kg
Ambient temperature 5°C to 35°C (if temp. exceeds this range, air conditioning is required)
Humidity 5% to 95% relative humidity, non-condensing
EMC CE-marking, conformity with EMC guideline 2004/108/EG
Instrument supply
Voltage 220-240 VAC; 110-120 VAC (optional)
Line frequency 50 to 60 Hz
Power consumption max. 800 W
Carrier gas Nitrogen GC grade (5.0 = 99.999%), 3 bar
Supply gases (for FID
only)
Combustion air, GC grade 2 bar;
H2 , GC grade, 2 bar
Gas connections 1/8” Swagelok
Pressure control Integrated pressure regulators, electronic readout of carrier gas
pressure, manometers for indication of supply gas pressures (for
FID only)
Flow control MFC for precise flow control of hydrogen supply (for FID only)
Sampling
Sampling Maintenance-free membrane pump for automated air sampling
Volume measurement Mass flow controller with flow sensor for precise measurement and
control of sample volume irrespective of fluctuations in atmospheric
pressure and temperature
Sampling time 0-99 min (adjustable)
Flow rate MFC, 5-50 sccm/min (adjustable)
Sample volume Typical 200-800 sccm (adjustable)
MFC inlet filter Sintered metal filter, stainless steel 2µm
Enrichment
Enrichment module Single-stage enrichment module with integrated thermal desorption
unit for pre-concentration of organic components ≥ C4
Enrichment temperature Typical 30°C (adjustable)
Desorption temperature max. 350°C (adjustable)
Heating-up rate Up to 40°C/s providing high-speed sample introduction, which
results in optimized peak separation
Valve oven
Oven liner Stainless steel
Internal dimensions H 70 mm x D 80 mm x W 210 mm
Heated valve block Temperature controlled, adjustable from 40-150°C
Sample valve 6-port VALCO valve, electrically actuated

Operating Manual GC 5000 BTX; Version 5 – 11/2010 16
GC oven
Oven liner Stainless steel
Internal dimensions H 55 mm x W210 mm x D 210 mm
Analytical column Fused silica capillary, length up to 60 m
Heating Forced air
Temperature range 40°C to 210 °C
Temperature control Closed loop PID, set point resolution 1°C
Temperature program 3 linear heating ramps, 4 isothermal holds
Heating rate 1°C/min to 25°C/min, set point resolution 1°C/min
Oven cooling Fast cooling down due to forced air cooling
Computer
specifications
Hardware Intel Atom 1.6GHz dual core, 1 GB RAM, 2,5” hard disk
Communication ports 2x Ethernet, RS232 / RS 485, 4x USB, PS2, VGA
Protocols GESYTEC II, other protocols on request
Operating system Windows XP Professional
Protection Password protection
Watchdog Hardware watchdog for an automated restart of the analyzer in case
of a software crash or an operating system crash.
Detector (select one
type)
FID – Flame Ionization
Detector
- Stable signal output due to temperature controlled detector block
- Make-up gas connection provides enhanced detection sensitivity
- Amplifier output 0-5 VDC
- Requires H2 and combustion air supply
PID – Photo Ionization
Detector
- Electrode-less, radio frequency excited UC lamp provides
increased UV intensity and extended lifetime of lamp
Options for GC 5000
Display 10” Touch screen
Communication Various I/O modules, analog outputs and digital I/O
Calibration Calibration gas selector (Sample, Cal1, Cal 2)
Accessories Developed for optimized connection with GC 5000
Sample stream selector SSM 600, Art.-No. 00001327
Dilution module DIM 200, Art.-No. 00000980
Combustion air supply
for FID
Dry-running compressor with exchangeable charcoal filter;
Art-No. 00000256

Operating Manual GC 5000 BTX; Version 5 – 11/2010 17
3.5 Options
3.5.1 Calibration gas selector (optional)
The AMA GC 5000 BTX can be equipped with two different calibration gas
supplies.
1. Calibration gas generator:
The analyzer is equipped with a communication interface to external
gas generators.
2. Calibration gas cylinders:
Fig. 4: Gas flow scheme of the calibration gas selector
Optionally the analyzer can be equipped with a valve array for the selection
of different sources of sampling. The array consists of 3 valves and can be
used for one ambient source and two calibration sources. The needle
valves of the calibration gas cylinders have to be adjusted to 70ml/min or
more.
3.5.2 Ozone precursor monitoring system (optional)
For the on-line monitoring of hydrocarbons C2-C11 (ozone precursor) in
one system, the AMA BTX analyzer can be synchronized with a AMA VOC
analyzer.
You have to select “Master mode on” in the BTX analyzer parameters and
“Slave mode on” in the VOC analyzer parameters. Then each cycle and
each calibration is started by the BTX analyzer.

Operating Manual GC 5000 BTX; Version 5 – 11/2010 18
3.5.3 Optional Modules
3.5.3.1Dilution module – DIM 200
The DIM 200 provides calibration gas at specified concentration levels for
precise calibration of monitoring devices. The calibration gas is generated
by diluting a source calibration gas with zero gas (e.g. nitrogen or purified
air).
The DIM 200 can be controlled manually or remotely via bus
communication by any AMA monitoring device or via digital I/O’s. This
allows for periodic validation and/or calibration of monitoring devices even
while running in unattended operation mode.
If the DIM 200 is controlled remotely by any AMA GC system, also setup of
the module is fully integrated into the analyzer software.
Technical data DIM 200:
General
Case 19” plug-in case
Height 3 height units
Depth 400 mm
Weight 8 kg
Mounting designed for cabinet / rack mounting
Ambient temperature 5°C to 40°C (if temp. exceeds this range, air conditioning is required)
Humidity 5% to 95% relative humidity, non-condensing
EMC CE-marking, conformity with EMC guideline 2004/108/EG
Instrument supply
Voltage 100-240 VAC
Line frequency 50 to 60 Hz
Power consumption max. 200 W
Supply gases Zero air (purified air or N2) 3 bar;
Source calibration gas, 3 bar
Sample gas
Supply connections 1/8” Bulkhead union for calibration gas and sample in/out
1/4” bulkhead union for zero gas and bypass
Gas flow control
Source calibration gas Mass flow controller, 2 to 100 sccm/min, accuracy +/- 0.5% of
reading
Zero gas Mass flow controller, 100 to 5000 sccm/min, accuracy +/- 0.5% of
reading
Dilution range 1 to 2500
Concentration levels Up to 5 levels (manual operation or remote control via digital I/O’s)
Up to 20 levels (remote control by AMA monitoring devices)
Gas flow concentrations Certification of the DIM 200 optionally available by factory-set
correction of flow rates determined by an independent and
accredited body for gas certification
Supplied gases Digitally controlled solenoid valves to supply either sample gas, zero
gas or calibration gas at sample out port
Microprocessor
controlled gas
calibration
Automated
calibration of
monitoring
devices
Table of contents
Other AMA Instruments Laboratory Equipment manuals
Popular Laboratory Equipment manuals by other brands
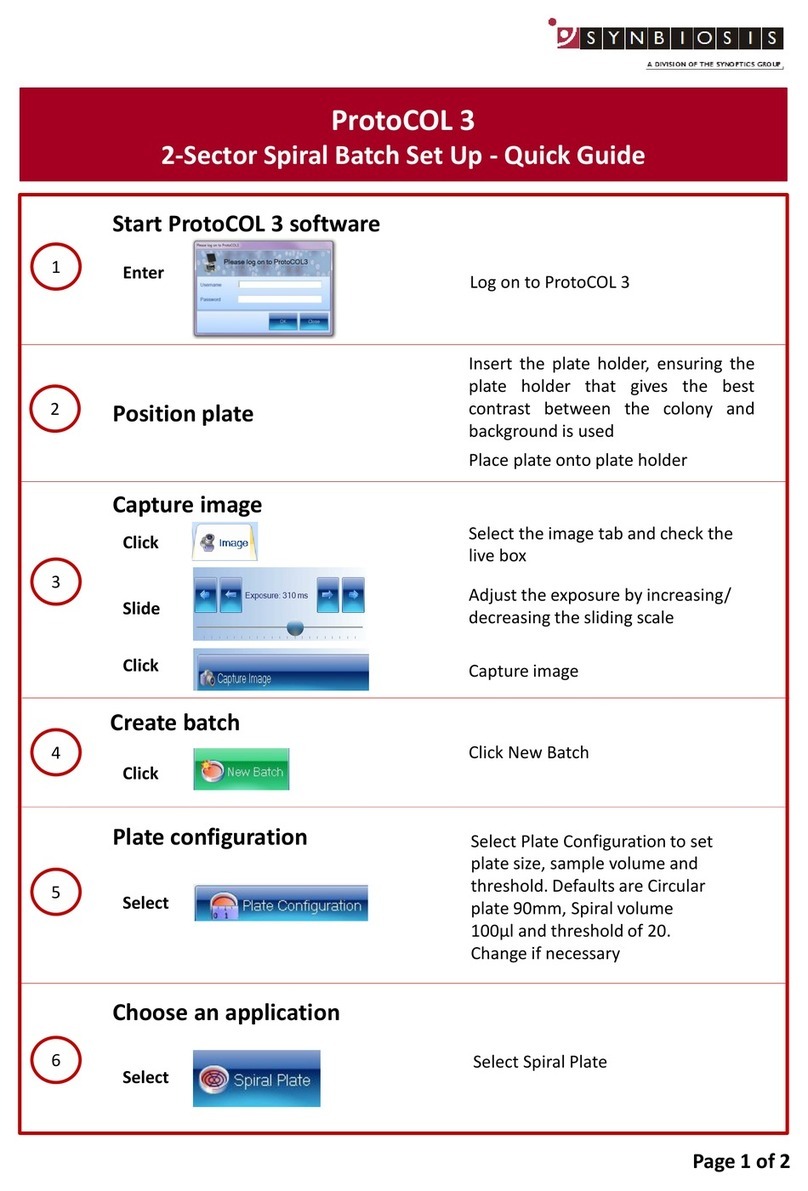
SynOptics
SynOptics SYNBIOSIS ProtoCOL 3 quick guide
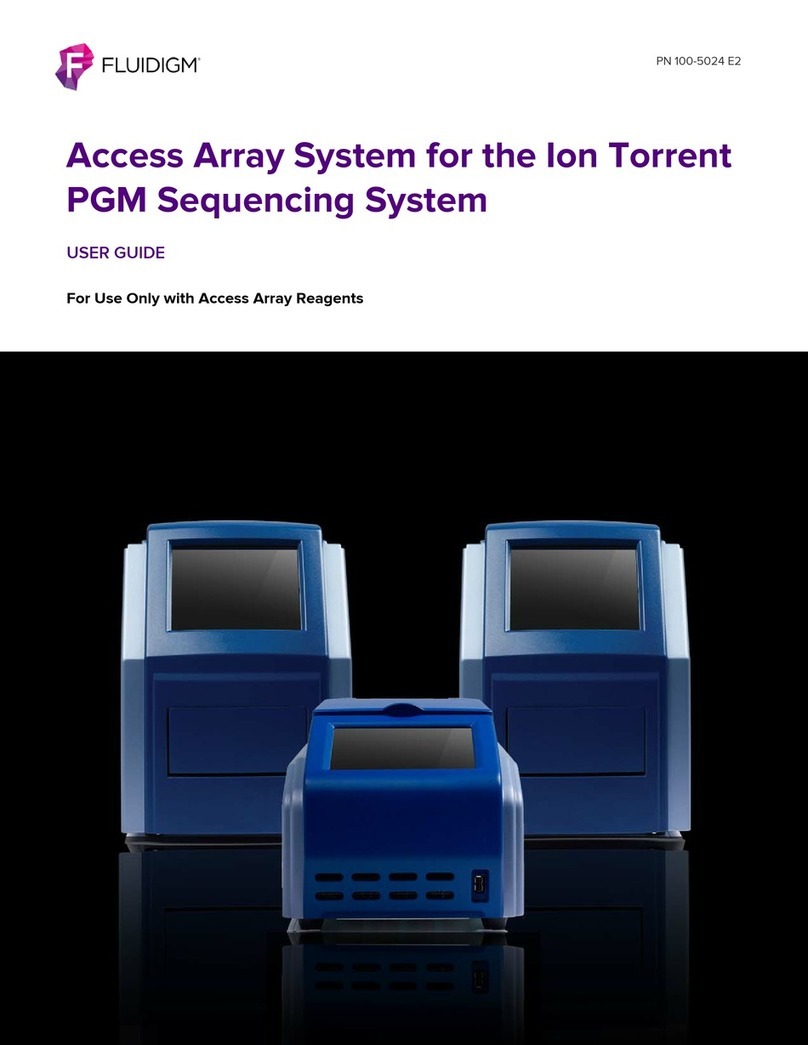
Fluidigm
Fluidigm Access Array user guide
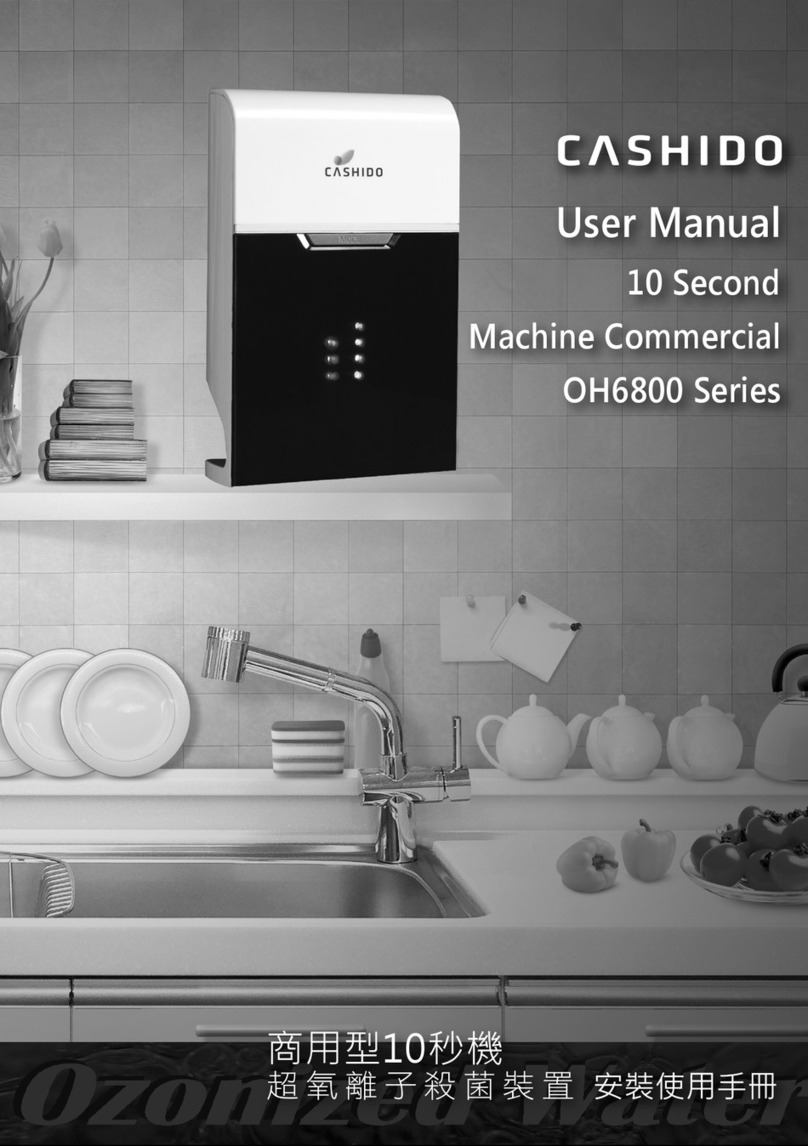
CASHIDO
CASHIDO 10 Second Machine Commercial XW2 user manual
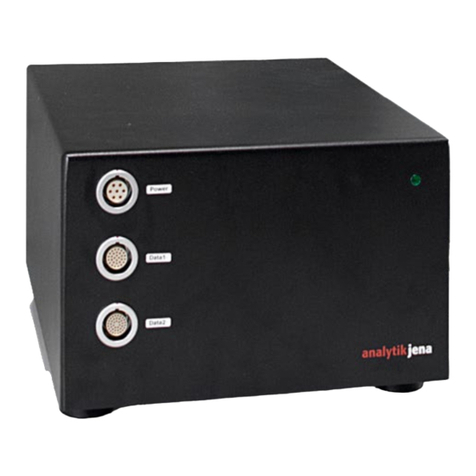
Endress+Hauser
Endress+Hauser analytikjena qTOWER3auto Series Service manual
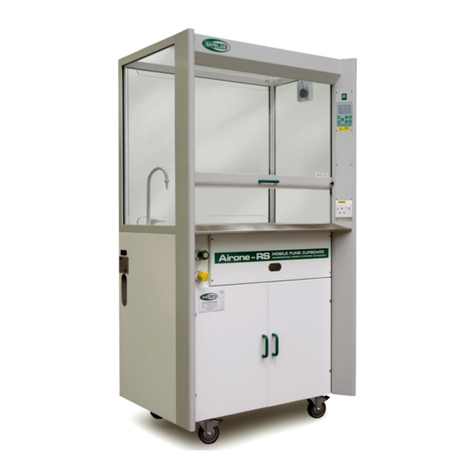
Safelab
Safelab Airone 1000RS/E instruction manual

Steinberg Systems
Steinberg Systems SBS-LZ-3000SLS user manual