Apeks ATX Second Stage User manual

Authorized Technician
TECHNICAL MAINTENANCE MANUAL
ATX SECOND STAGE

Contents
COPYRIGHT NOTICE...............................................................................................................................................3
INTRODUCTION .......................................................................................................................................................3
WARNINGS, CAUTIONS, & NOTES.........................................................................................................................3
SCHEDULED SERVICE............................................................................................................................................3
GENERAL GUIDELINES..........................................................................................................................................3
GENERAL CONVENTIONS......................................................................................................................................4
DISASSEMBLY PROCEDURES...............................................................................................................................4
REASSEMBLY PROCEDURES................................................................................................................................7
FINAL TESTING......................................................................................................................................................10
Second Stage Opening Effort Test.................................................................................................................................................... 10
Second Stage Air Flow Test............................................................................................................................................................... 10
Second Stage Purge Flow Test ......................................................................................................................................................... 10
External Leak Test .............................................................................................................................................................................. 10
Subjective Breathing Test.................................................................................................................................................................. 10
TABLE 1 - FIRST-STAGE TROUBLESHOOTING GUIDE ......................................................................................11
TABLE 2 - RECOMMENDED TOOL LIST ..............................................................................................................12
TABLE 3 - RECOMMENDED LUBRICANTS AND CLEANERS...........................................................................13
PROCEDURE A - CLEANING AND LUBRICATION..............................................................................................14
TABLE 4 -TORQUE SPECIFICATIONS..................................................................................................................15
TABLE 5 - TEST BENCH SPECIFICATIONS .........................................................................................................15
EXPLODED PARTS DIAGRAM ..............................................................................................................................16

COPYRIGHT NOTICE
This manual is copyrighted, all rights reserved. It may not, in
whole or in part, be copied, photocopied, reproduced, translated,
or reduced to any electronic medium or machine readable form
without prior consent in writing from Aqua Lung America. It may
not be distributed through the internet or computer bulletin board
systems without prior consent in writing from Aqua Lung America.
©2002 Aqua Lung America, Inc.
ATX Second-Stage Service Manual
INTRODUCTION
This manual provides factory prescribed procedures for the cor-
rect service and repair of the Apeks ATX second-stage regula-
tor. It is not intended to be used as an instructional manual for
untrained personnel. The procedures outlined within this manual
are to be performed only by personnel who have received factory
authorized training through an Aqua Lung Service & Repair Sem-
inar. If you do not completely understand all of the procedures
outlined in this manual, contact Aqua Lung to speak directly with
a Technical Advisor before proceeding any further.
WARNINGS, CAUTIONS, & NOTES
Pay special attention to information provided in warnings, cau-
tions, and notes that are accompanied by one of these symbols:
WARNINGS indicate a procedure or situation that
may result in serious injury or death if instructions
are not followed correctly.
CAUTIONS indicate any situation or technique
that will result in potential damage to the prod-
uct, or render the product unsafe if instructions
are not followed correctly.
NOTES are used to emphasize important points, tips, and
reminders.
SCHEDULED SERVICE
If the regulator is subjected to less than 50 dives per year, it is
permissible to overhaul it every other year with an inspection
procedure being performed on the “off” years. For example:
Year #1: Inspection
Year #2: Overhaul
Year #3: Inspection
Year #4: Overhaul
and so on.
Both Inspections and Overhauls need to be documented in the
Annual Service & Inspection Record in the back of the Owner’s
Manual to keep the Limited Lifetime Warranty in effect.
If a regulator is subjected to more than 50 dives per year, it
should receive the complete overhaul.
An Ofcial Inspection consists of:
1. A pressurized immersion test of the entire unit to check for
air leakage.
2. Checking for stable intermediate pressure that is within the
acceptable range.
3. Checking for opening effort that is within the acceptable
range.
4. Checking for smooth operation of the control knob and
venturi switch.
5. A visual inspection of the lter for debris or discoloration.
6. A visual inspection of the exhaust valve to see that it is in
good shape and that it’s resting against a clean surface.
7. A visual inspection of the mouthpiece looking for tears or
holes.
8. Pulling back hose protectors and checking that the hoses
are secure in the hose crimps.
If a regulator fails item #1,2,3 or 4 the entire regulator should
be overhauled. If a regulator fails 4,5,6 or 7 it will be up to the
technician’s discretion whether or not a full overhaul is required.
GENERAL GUIDELINES
1. In order to correctly perform the procedures outlined in this
manual, it is important to follow each step exactly in the or-
der given. Read over the entire manual to become familiar
with all procedures before attempting to disassemble the
rst-stage, and to learn which specialty tools and replace-
ment parts will be required. Keep the manual open beside
you for reference while performing each procedure. Do not
rely on memory.
2. All service and repair should be carried out in a work area
specically set up and equipped for the task. Adequate
lighting, cleanliness, and easy access to all required tools
are essential for an efcient repair facility.
3. As the regulator is disassembled, reusable components
should be segregated and not allowed to intermix with
nonreusable parts or parts from other units. Delicate parts,
including inlet ttings and crowns which contain critical
sealing surfaces, must be protected and isolated from other
parts to prevent damage during the cleaning procedure.
4. Use only genuine Apeks parts provided in the ATX second-
stage overhaul parts kit (p/n AP0219/AA). DO NOT attempt
to substitute an Apeks part with another manufacturer’s,
regardless of any similarity in shape or size.
5. Do not attempt to reuse mandatory replacement parts
under any circumstances, regardless of the amount of use
the product has received since it was manufactured or last
serviced.
6. When reassembling, it is important to follow every torque
specication prescribed in this manual, using a calibrated
torque wrench. Most parts are made of either marine brass
or plastic, and can be permanently damaged by undue
stress.

4
Apeks ATX Second Stage Service Manual 5
GENERAL CONVENTIONS
Unless otherwise instructed, the following terminology and tech-
niques are assumed:
1. When instructed to remove, unscrew, or loosen a threaded
part, turn the part counterclockwise.
2. When instructed to install, screw in, or tighten a threaded
part, turn the part clockwise.
3. When instructed to remove an O-ring, use the pinch method
(see gure) if possible, or use a brass or plastic O-ring
removal tool. Avoid using hardened steel picks, as they may
damage the o-ring sealing surface. All o-rings that are re-
moved are discarded and replaced with brand new o-rings.
1. Using two ¹¹₁₆” wrenches, hold the retaining nut (11) station-
ary while turn the hose swivel counterclockwise. Remove
the o-ring from inside the hose swivel. Exercise caution not
to scratch the o-ring groove. Remove the o-ring from the
male end of the hose.
2. Pull back the two hose
protectors and inspect
the hose crimps. The
crimps should be free
from damage and the
hose should not be
pulling out of the crimp.
If it is, the hose must be
replaced.
3. Using the Apeks front cover tool (see note on page 13
regarding the modication of the front cover tool), unscrew
the case cover (4). To remove the purge button and spring
(2 & 3), squeeze two adjacent tabs inward.
4. Lift out the diaphragm
cover (5) and diaphragm
(6).
4. The following acronyms are used throughout the manual:
MP is Medium Pressure; HP is High Pressure; IP is Inter-
mediate Pressure.
5. Numbers in parentheses reference the key numbers on the
exploded parts schematics. For example, in the statement,
“...remove the o-ring (20) from the...”, the number 20 is the
key number to the crown o-ring.
DISASSEMBLY PROCEDURES
Note: Before performing any disassembly, refer to the
exploded parts drawing, which references all mandatory
replacement parts. These parts should be replaced with
new, and must not be reused under any circumstances
- regardless of the age of the regulator or how much use it
has received since it was last serviced.
CAUTION: Use only a plastic or brass o-ring
removal tool (p/n 944022) when removing o-rings
to prevent damage to the sealing surface. Even
a small scratch across an o-ring sealing surface
could result in leakage. Once an o-ring sealing
surface has been damaged, the part must be
replaced with new. DO NOT use a dental pick, or
any other steel instrument.
Pinch Method
Press upwardson sides
of O-ring to create a
protrusion. Grab O-
ring or insert O-ring
tool at protrusion.

4
Apeks ATX Second Stage Service Manual 5
5. Using an ¹¹₁₆” wrench, re-
move the heat exchanger
(11).
9. Unscrew the adjustment
knob (18) and completely
remove it from the valve
body.
6. Turn the adjustment knob counterclockwise until it stops.
Press the lever (28) against the valve body (25). While
keeping the lever depressed, grasp the knob and pull the
valve body assembly out of the case (7). Remove the valve
body o-ring (12) that will probably be left behind in the left
side of the box bottom as you look at it.
7. Grasp the venturi lever (14) and pull it out of the box bottom.
Remove the o-ring (13) from the venturi lever.
NOTE: The venturi lever may have come out with the
valve body in step 6. If this is the case, depress the lever
and slide the lever off from right to left.
8. Turn the knob clockwise
(inward) one turn. The
pin (29) should drop out.
If the pin remains in the
valve body, use a 1/16”
dowel or punch to push
it partially out, then use
needlenose pliers to
completely remove it from
the valve body.
10. Remove the o-ring (19) from the adjustment knob. Using
the Spring Adjuster Tool (p/n AT45), unscrew the spring
adjuster (15). Remove the two o-rings (16 & 17) from the
spring adjuster.
11. Remove the o-ring (12)
from the valve body.
13. Insert a small 1/8” wooden dowel into the threaded end of
the valve body and push out the shuttle valve assembly (20-
24). Separate the shuttle valve assembly by pulling on each
end.

6
Apeks ATX Second Stage Service Manual 7
14. Using a ngernail, remove the LP seat (24) and small o-ring
(22) from the shuttle valve.
17. Fold back the edges of
the exhaust valve (30)
and inspect underneath.
The seating surface
should be clean and free
of damage. Inspect the
exhaust valve. It should
be supple and have well
dened edges. If it looks
good, there is no need
to remove it and it may
be reused. If there is any
sign of deterioration, it
should be replaced.
15. Using a medium blade screwdriver, turn the crown (27)
six to seven full turns counterclockwise. Since the crown
is o-ring sealed, it will not completely unscrew from the
valve body. Insert the pin end of the seat extractor tool
(p/n 109436) into the valve body, grasp the pin and pull the
crown completely out of the valve body. Remove the o-ring
(26) from the crown.
Note: The exhaust tee is a molded part of the case and
cannot be removed. Only the exhaust cover can be re-
moved (see next step)
16. To remove the exhaust cover (31), locate the retaining
tab located inside the exhaust port (see picture). Using a
wooden dowel, press in on the upper ledge of the tab at an
angle and pop out the exhaust cover.
18. Using side cutters, snip the mouthpiece clamp (8). Remove
the mouthpiece (9).
This Ends Disassembly
Before starting reassembly, perform parts
cleaning and lubrication according to the
procedures outlined in Procedure A, titled
Cleaning & Lubrication, on page 15.

6
Apeks ATX Second Stage Service Manual 7
REASSEMBLY PROCEDURES
1. If the exhaust valve (30) was removed, thread the tail
through the retaining hole on the outside of the box bottom
until the barb engages on the inside. Align the rib so it is
horizontal. If it is a new valve, cut the excess stem with side
cutters leaving approximately 5mm of the tail behind.
2. Orient the exhaust cover (31) with the logo facing outward
(the side with two tabs pointing to the left). Slide the two
tabs into the exhaust port, then press down on the right
side of the exhaust cover to snap it into place.
3. Install a new, lubricated
o-ring (12) onto the valve
body (25).
4. Install a new, lubricated o-ring (22) onto the stem of the
shuttle valve (23). Press a new low pressure seat (24) into
the front of the shuttle valve.
5. Fit the valve spring (21) onto the leading edge of the coun-
terbalance cylinder (20). Carefully guide the stem of the
shuttle valve through the spring and into the counterbalance
cylinder.
6. If you removed the lever, replace it so that the lever is on
the side opposite the two pin holes. (The air outlet hole
should point to the left with the threaded end facing you.)
7. With the “feet” of the shuttle valve pointing downward (away
from the lever) and the lever pointing straight up (perpen-
dicular to the valve body), insert the valve assembly into
the valve body. Using your nger, press the shuttle valve
assembly all the way into the valve body.

8
Apeks ATX Second Stage Service Manual 9
8. Install a new, lubricated o-ring (19) onto the adjustment
knob. Install a new, lubricated o-rings (16 & 17) onto the
spring adjuster (15). Using the spring adjuster tool (p/n
AT45), thread the spring adjuster into the adjustment knob
(18) until it is ush with the end of the adjustment knob,
then turn in one additional revolution
10. Install the adjustment knob into the valve body. There
should now be spring tension on the lever. Continue to
screw clockwise until the holes for the locking pin are clear.
Install the locking pin (29). Be sure that it sits evenly in the
hole. Back the adjustment knob out counterclockwise to ap-
ply tension on the pin and keep it from falling out.
11. Install a new, lubricated o-ring (13) onto the venturi lever
(14). Point the venturi lever upward and insert it into the
case. Press it against the case so the o-ring is captured.
12. While depressing the lever, insert the valve body through
the venturi lever and into the box bottom. Be sure that
the two index ats and the two lever feet engage the tabs
molded into the box bottom.
13. Slide a new, lubricated o-ring (12) down the threaded end
of the valve body, into the box bottom. Screw the heat
exchanger (11), wrench ats facing outward, onto the valve
body until nger tight. Using an ¹¹₁₆” crows foot or deep
socket, tighten the nut to a torque of 45 ±2 inch-lbs.

8
Apeks ATX Second Stage Service Manual 9
14. Fit a new, lubricated o-ring (26) onto the adjustable crown
(27). Press the adjustable crown, threaded end rst, into the
valve body. Using blunt end of the seat extractor tool, push
the adjustable crown into the valve body as far as it will go.
15. While holding the rim of the box bottom at eye level, turn
the adjustable crown orice in (clockwise) until the lever
drops about 4mm below the case rim. Then, turn the crown
counterclockwise until the lever is even with the case rim.
16. Add a new o-ring to the male end of the medium pressure
hose. Install a new, lubricated o-ring into the swivel end of
the hose
17. Adjust the lever height
NOTE: The inline adjustment tool can be use with crowns
with a screwdriver slot or a hex hole. Make sure the inline
tool is set to use the appropriate tting.
a. Attach the Aqua
Lung in-line tool
(p/n 100190) to the
second stage. It can
accommodate both
the crown orice with
the 5mm hex and the
crown orice with the
slot. The tool is shown
with the optional in-line medium pressure gauge (p/n
111605).
b. Attach the swivel end of the medium pressure hose
to the other end of the inline tool. Attach the male end
of the hose to a properly adjusted rst-stage regula-
tor (135±5). Attach the rst-stage to a fully charged
cylinder. Slowly open the cylinder valve to pressurize
the regulator.
c. Press inward on the adjustment wheel of the inline
tool. Slowly rotate the adjustment wheel until the inline
tool engages the crown orice. Turn the crown in until
the lever drops approximately ¹₄”. This will “coin” the
rubber seat to help achieve a better seal. Now back
the crown orice out (counterclockwise). The lever will
raise. Continue until the lever is even with the rim of
the box bottom.
18. Position the diaphragm (6) into the box bottom (7). Using
your nger, work the edges of the diaphragm into place so it
sits evenly in the box bottom. Install the diaphragm cover (5)
into the case, over the diaphragm.
19. Place the small diameter
end of the purge spring
(3) onto the purge but-
ton (2). Orient the case
cover with the slotted
openings pointing to the
right. Properly align the
purge button and press
it into the case cover
until it snaps into place.

10 Apeks ATX Second Stage Service Manual 11
20. Screw the case cover
onto the case. Using the
cover tool (p/n AT31)
tighten the cover until it
stops. Conrm that the
purge button is properly
aligned. If air ows au-
dibly, the lever is set too
high. To lower the lever,
turn in the crown until
the ow stops.
21. Perform the purge test:
Slowly press the purge button unti air ows. The button
should not travel more than 2mm. Excessive travel indicates
that the lever is set too low. Adjust the crown out slightly
until the purge is satisfactory.
22. Screw the hose onto the
second stage. Using an
11/16” crows-foot and
torque wrench, tight the
hose to 40 inch pounds.
FINAL TESTING
Second Stage Opening Effort Test
1. Connect the rst stage regulator to a calibrated test bench
and pressurize the system to 3000 (±100) psi. Slowly open
the owmeter control knob (start vacuum) while watching
both the magnahelic gauge and the intermediate pressure
gauge.
2. When the intermediate pressure begins to drop, indicat-
ing the second-stage valve is open, the magnahelic gauge
should indicate an opening effort of +0.8” to +1.4” . If the
reading exceeds these specications, refer to refer to “Table
1 - Troubleshooting” for corrective actions.
External Leak Test
1. After disconnecting the regulator from the ow bench, con-
nect it to a scuba cylinder lled to approximately 3,000 psi.
Open the cylinder valve to repressurize the regulator, and
submerge the entire system in a test tank of clean water.
2. Observe any bubbles arising from the submerged regula-
tor over a one minute period. The recommended time is
necessary due to slower bubble formation that occurs in
smaller leaks. Bubbles indicate a leak, which requires that
the system must be disassembled at the source to check
sealing surfaces, assembly sequence and component posi-
tioning in order to correct the problem(s).
NOTE: Extremely small leaks may be better detected
by applying a soap solution or Snoop™ to the leak area.
Bubble streams will indicate the source of the leak. Before
disassembling to correct any leaks, rinse the entire regula-
tor thoroughly with fresh water and blow out all residual
moisture with ltered, low-pressure (50 psi) air. Disassem-
ble and remedy the problem, referring to “Table 1 - Trouble-
shooting.”
Subjective Breathing Test
1. Depress the purge cover fully to ensure that an adequate
volume of air needed to clear the second stage ows
through the mouthpiece. Then, inhale slowly but deeply
from the mouthpiece. A properly serviced and adjusted
regulator should deliver air upon deep inhalation without
excessive inhalation effort, freeow, or “uttering” of the
second-stage diaphragm. When exhaling, there should be
no uttering or sticking of the exhalation valve. If any of
these problems occur, refer to Table 1 - Troubleshooting.
This Ends Reassembly
NOTE: If your facility is equipped with a test bench, per-
form the tests before installing the mouthpiece. General
instructions for performing bench tests are located in the
next section, “Final Testing.”
23. If equipped with a Comfo-
bite mouthpiece, make sure
the ‘bridge’ of the mouth-
piece (9) is facing upward.
Stretch the mouthpiece over
the second-stage mouth-
piece boss. At the base of
the mouthpiece is a groove
for the clamp (8). Wrap the
clamp around the mouthpiece so that the buckle points to-
ward the hose. Tighten the clamp and snip the excess strap
with side cutters.

10 Apeks ATX Second Stage Service Manual 11
Table 1 - Troubleshooting Guide
SYMPTOM POSSIBLE CAUSE TREATMENT
Leakage or freeow from second stage
1. High rst-stage intermediate pres-
sure. (should be 135±5 psi)
1. Refer to rst-stage Troubleshoot-
ing Guide.
2. LP seat (24) damaged or worn. 2. Replace LP seat.
3. Crown (27) adjusted incorrectly,
lever set too high
3. Reset crown preliminary set-
tings, and repeat Adjustment
Procedures.
4. Lever (28) bent 4. Replace lever.
5. Crown (27) sealing surface dam-
aged. 5. Replace crown.
6. Poppet spring (21) damaged. 6. Replace spring.
Low purge or excessive work of breath-
ing (full cylinder)
1. Low rst-stage intermediate pres-
sure. (should be 135±5 psi)
1. Refer to rst-stage Troubleshoot-
ing Guide.
2. Crown (27) adjusted incorrectly,
lever set too low.
2. Reset crown to preliminary
settings and repeat Adjustment
Procedures .
3. Intermediate pressure hose clogged
or obstructed. 3. Clean or replace hose.
4. Lever (28) bent 4. Replace lever.
Water entering second-stage
1. Hole in mouthpiece (9). 1. Replace mouthpiece.
2. Demand diaphragm (6) damaged. 2. Replace diaphragm.
3. Exhaust valve (30) damaged. 3. Replace valve.
4. Venturi lever o-ring (13) dirty, dam-
aged, or worn. 4. Disassemble and replace o-ring.
5. Diaphragm improperly seated in box
bottom (7).
5. Remove front cover (3) and
properly reassemble sealing ring
with diaphragm (check for distor-
tion).
6. Box bottom damaged. (Check ex-
haust valve sealing surface.)
6. Disassemble and replace box
bottom
7. Inlet o-ring (12) damaged. 7. Replace o-ring.
8. Valve spindle o-ring (12) worn or
damaged 8. Replace o-ring.

12
Apeks ATX Second Stage Service Manual 13
Table 2 - Recommended Tool List
PART NO. DESCRIPTION APPLICATION
111610 I.P. test gauge Intermediate pressure testing
944022 O-ring tool, set O-ring removal and installation
AT31 Front Cover Tool* Front cover removal and installation
109436 Seat extract/install tool Crown removal and installation
100190 Inline Adjustment Tool 2nd-stage adjustment
n/a Torque wrench, inch-pound Retaining nut, hose
n/a 11/16” crows-foot Heat exchanger, hose (used with torque wrench)
n/a Medium blade screwdriver Crown
n/a 11/16” wrench (x2) Retaining nut, hose
AT45 Spring adjuster Spring adjuster
n/a 1/16” wooden dowel Shuttle valve removal
*NOTE: The front cover tool must be modied by removing one of the pins.

12
Apeks ATX Second Stage Service Manual 13
Table 3 - Recommended Lubricants & Cleaners
LUBRICANT / CLEANER APPLICATION SOURCE
Christo-Lube® MCG-111 All O-rings seals Aqua Lung, PN 820466, or
Lubrication Technologies
310 Morton Street
Jackson, OH 45640
(800) 477-8704
Oakite #31 Acid bath for reusable stainless
steel and brass parts.
Oakite Products, Inc.
50 Valley Road
Berkeley Heights, NJ 07922
White distilled vinegar (100 gr.) Acid bath for reusable stainless
steel and brass parts.
“Household” grade
Liquid dishwashing detergent
(diluted with warm water)
Degreaser for brass and stainless
steel parts; general cleaning solu-
tion for plastic and rubber
“Household” grade
CAUTION: Silicone rubber requires no lubrication or preservative treatment. DO
NOT apply grease or spray to silicone rubber parts. Doing so may cause a chemical
breakdown and premature deterioration of the material.
CAUTION: Do not use muriatic acid for the cleaning of any parts. Even if strongly di-
luted, muriatic acid can harm chrome plating and may leave a residue that is harmful
to O-ring seals and other parts.

14
Apeks ATX Second Stage Service Manual 15
Procedure A
Cleaning & Lubrication
The ATX Regulator and Nitrox
When it comes to issues of nitrox safety and compatibility, the concerns lie primarily with the rst stage as it is subjected to high inlet
pressures. High inlet pressures lead to adiabatic compression or heating of the gas. The ATX rst stage, when properly cleaned and
assembled, is authorized for use with enriched air nitrox (EAN) that does not exceed 40% (EAN 40). It is authorized because it has
undergone adiabatic compression testing and the authorized service kit components and lubricants are compatible in elevated oxygen
environments. During cleaning, a mild detergent must be used to remove condensed hydrocarbons (compressor oils) from the inside
passageways of the rst stage. For the rst stage to remain EAN40 compatible, only use hyperltered compressed gas (hydrocarbons <
0.1 mg/m3). Ordinary compressed breathing air (Grade E) usually does not meet this criterion. Once ordinary breathing air is used, the
rst stage is no longer EAN40 compatible until it is cleaned and serviced again.
Although regulator second stage components are not exposed to high pressure EAN, Aqua Lung recommends that the same cleaning
procedures be followed for the complete regulator. This prevents the possibility of cross contamination and guarantees the cleanliness
of the entire regulator.
Cleaning Brass and Stainless Steel Parts
1. Preclean in warm, soapy water* using a nylon bristle tooth brush.
2. Thoroughly clean parts in an ultrasonic cleaner lled with soapy water. If there are stubborn deposits, household white distilled
vinegar (acetic acid) in an ultrasonic cleaner will work well. DO NOT place plastic, rubber, silicone or anodized aluminum parts in
vinegar.
3. Remove parts from the ultrasonic cleaner and rinse with fresh water. If tap water is extremely “hard,” place the parts in a bath of
distilled water to prevent any mineral residue. Agitate lightly, and allow to soak for 5-10 minutes. Remove and blow dry with low
pressure (25 psi) ltered air, and inspect closely to ensure proper cleaning and like-new condition.
Cleaning Anodized Aluminum, Plastic & Rubber Parts
Anodized aluminum parts and parts made of plastic or rubber, such as box bottoms, box tops, dust caps, etc., may be soaked and
cleaned in a solution of warm water mixed with mild dish soap. Use only a soft nylon toothbrush to scrub away any deposits. Rinse in
fresh water and thoroughly blow dry, using low pressure ltered air.
CAUTION: Do not place plastic and rubber parts in acid solutions. Doing so my alter the physical properties
of the component, causing it to prematurely degrade and/or break.
Cleaning Hoses
1. Hose ttings: Ultrasonically clean with soapy water; vinegar OK on tough corrosion
2. Run soapy water through hose if need
3. Thoroughly rinse with fresh water
4. Blow out hose before install
Lubrication and Dressing
Wear powderless, latex gloves when handling and lubricating o-rings. Keeping internal parts free from skin oils and other contaminates
is important when running enriched air nitrox through a rst stage. All o-rings should be lubricated with Christo-Lube® MCG-111. Dress
the o-rings with a very light lm of grease, and remove any visible excess by running the o-ring between thumb and forenger. Avoid
applying excessive amounts of Christo-Lube grease, as this will attract particulate matter that may cause damage to the o-ring.
*Soapy water is dened as “household” grade liquid dishwashing detergent diluted in warm water.

14
Apeks ATX Second Stage Service Manual 15
Table 5 - Test Bench Specications
TEST CONDITION ACCEPTABLE RANGE
Leak Test Inlet 2,500-3,000 (±100) psig No leaks allowed
Intermediate Pressure Inlet 2,500-3,000 (±100) psig 135±5 psi
Intermediate Pressure
Creep Inlet 2,500-3,000 (±100) psig 5 psi max between 5 to 15 seconds after
cycling (purging) regulator
Opening Effort Inlet 2,500-3,000 (±100) psig
Intermediate pressure 135±5 psi +0.8 to +1.4 in. H20
Table 4 - Torque Specications
PART NUMBER DESCRIPTION / KEY NUMBER TORQUE
AP2031 Heat Exchanger / 11 45±2 inch-lbs
APF124563 Hose 40±2 inch-lbs

16
Apeks ATX Second Stage Service Manual 17
AP0219/AA Universal 2nd-Stage Repair Kit
1 AP5819 Decal, ATX200
AP5820 Decal, ATX50
2 AP5805 Purge Button
3 AP2020 Spring
4 AP5804 Case Cover, ATX200
AP5807 Case Cover, ATX50
AP5807/Y Case Cover, ATX50 Octopus
5 AP5802/C Diaphragm Cover, ATX200
AP5802 Diaphragm Cover, ATX50
6 AP5803 Diaphragm
7 AP5800 Case
8 104913 Mouthpiece Clip
9 109438 Mouthpiece, Comfobite
104138 Mouthpiece, Standard, Octopus
10 AP2037 Deector
11 AP5013/S Heat Exchanger, ATX200
AP5002 Heat Excahnger, ATX50
12 AP1267 O-ring
13 AP1438 O-ring
14 AP5339 Venturi Lever, ATX200
AP2039 Venturi Lever, ATX50
AP2039/Y Venturi Lever, Yellow, ATX50 Octopus
15 AP6578 Adjuster Spring
16 AP1159 O-ring
17 AP5711 O-ring
18 AP6577/S Adjusting Screw, ATX200
AP6577/1 Adjusting Screw, ATX50
19 AP1409 O-ring
20 AP2038 Counter Balance Cylinder
21 AP2021 Spring
22 AP2041 O-ring
23 AP2036 Shuttle Valve
24 AP2034 Rubber Seat
25 AP2028/S Valve Spindle, ATX200
AP2028 Valve Spindle, ATX50
26 AP1154 O-ring
27 AP2033 Seat
28 AP2035 Lever
29 AP1151 Spring Pin
30 AP1429 Exhaust Valve
31 AP5801 Cover, Exhaust Valve
AP5801/Y Cover, Exhaust Valve, Yellow
Exploded Parts Diagram
1
2
34
5
6
31
7
12
10
11
13
14
27 26
25
29
12
24 23 22
21 20 19 18 1716
15
8
9
30
28

16
Apeks ATX Second Stage Service Manual 17

Authorized Technician
TECHNICAL MAINTENANCE MANUAL
ATX SECOND STAGE
Aqua Lung America
2340 Cousteau Court, Vista CA 92083
Table of contents
Other Apeks Controllers manuals
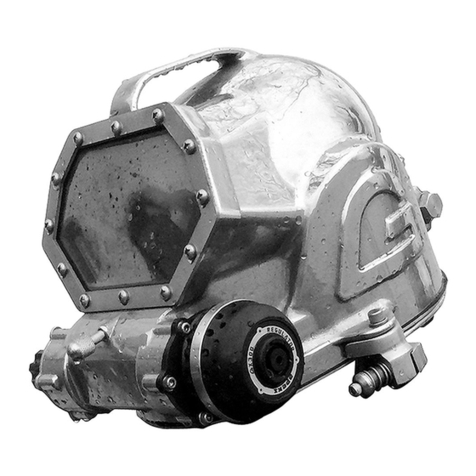
Apeks
Apeks GX300 User manual
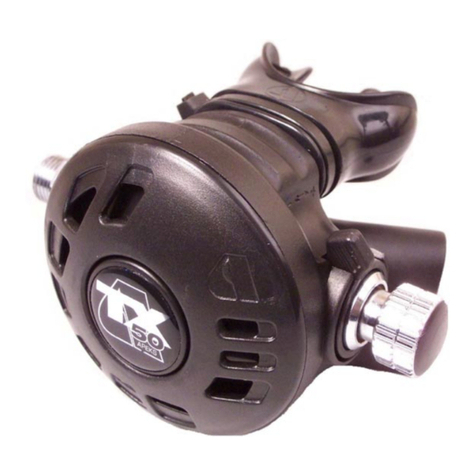
Apeks
Apeks TX100 User manual
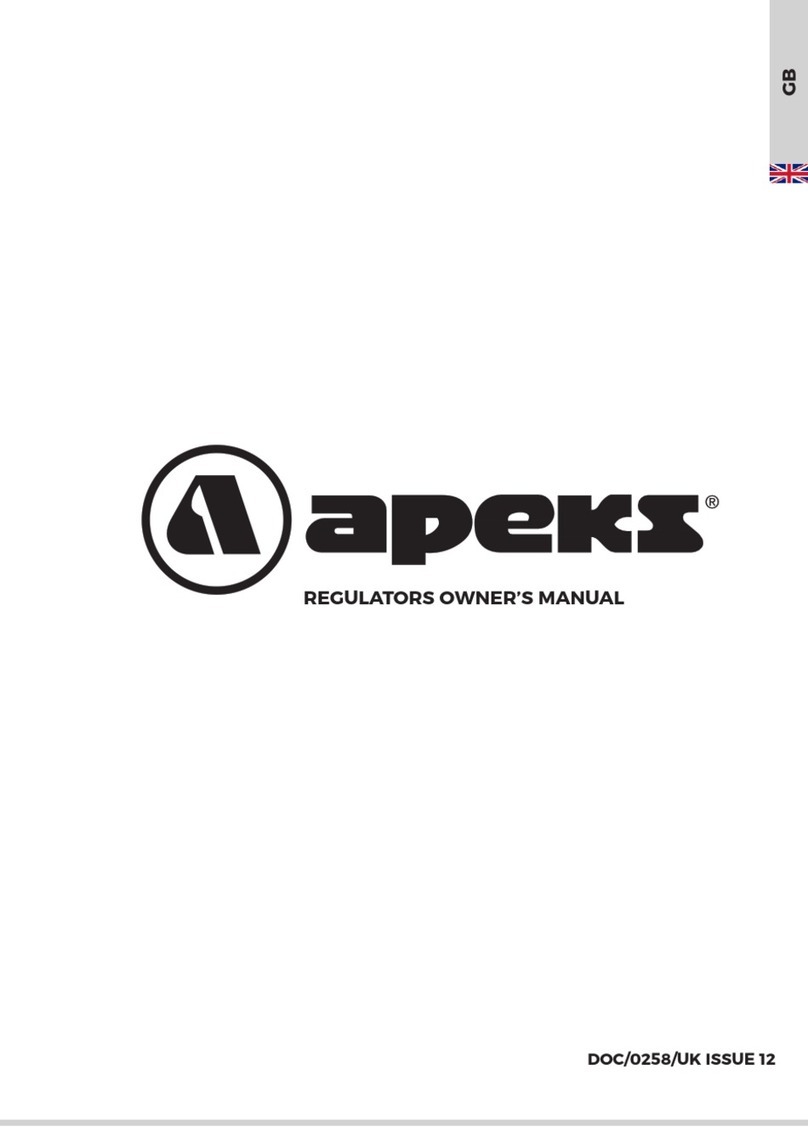
Apeks
Apeks TEK3/XTX50 User manual
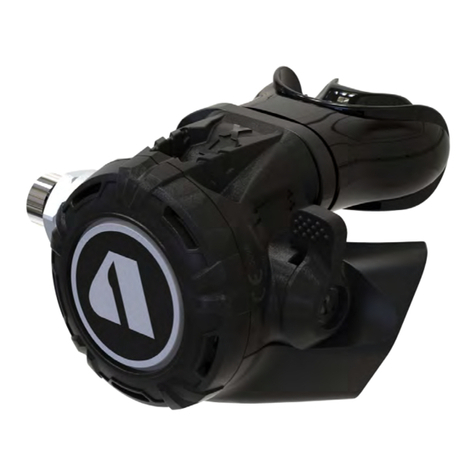
Apeks
Apeks XL4 SECOND STAGE User manual
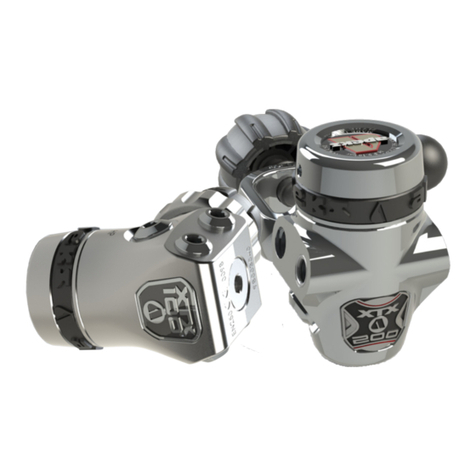
Apeks
Apeks XTX FSR User manual
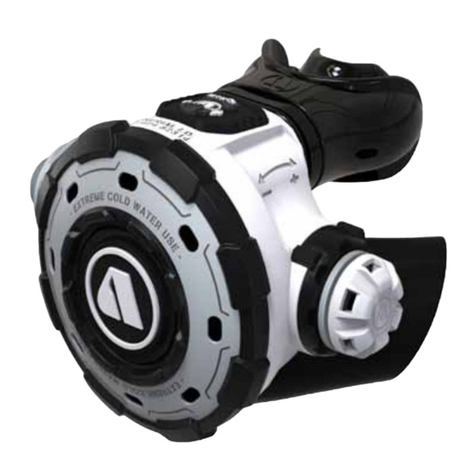
Apeks
Apeks MTX-R User manual
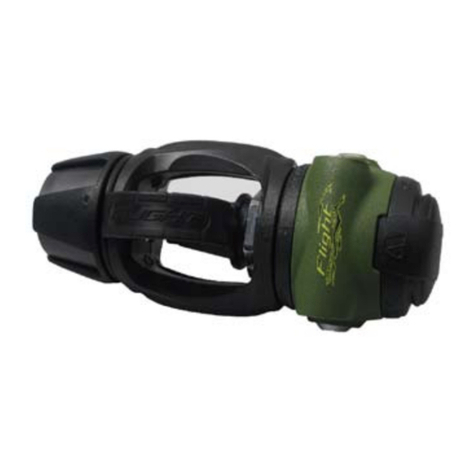
Apeks
Apeks Flight User manual
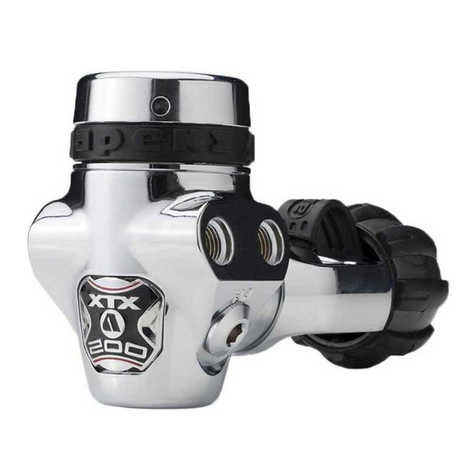
Apeks
Apeks FSR Series User manual
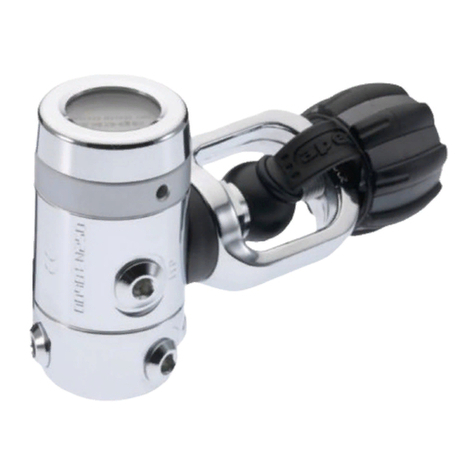
Apeks
Apeks DST User manual
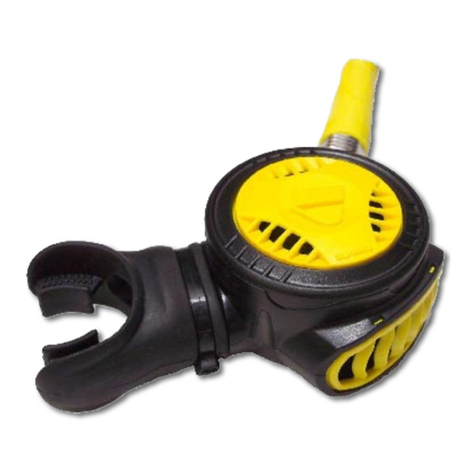
Apeks
Apeks Egress User manual
Popular Controllers manuals by other brands
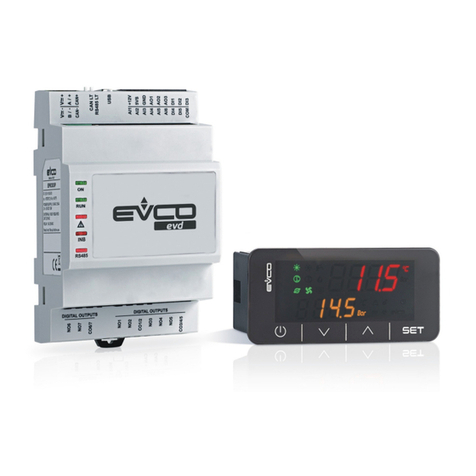
Evco
Evco EV3 HP Installer manual
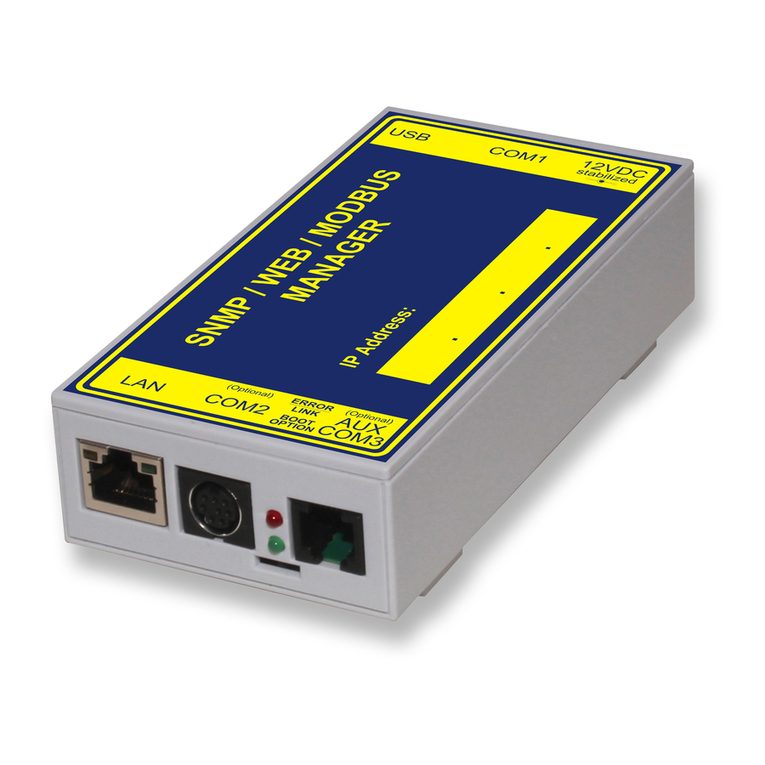
Generex
Generex CS141 Series Quick start manual
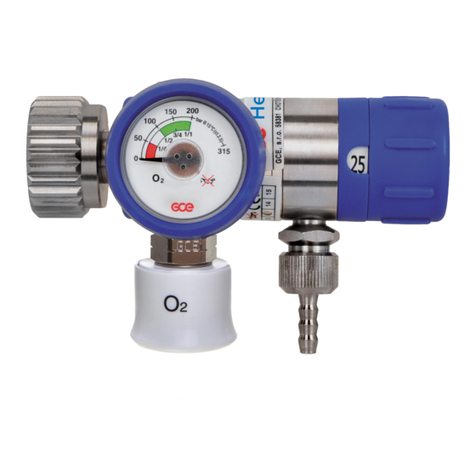
GCE
GCE mediline MEDIREG II Instructions for use
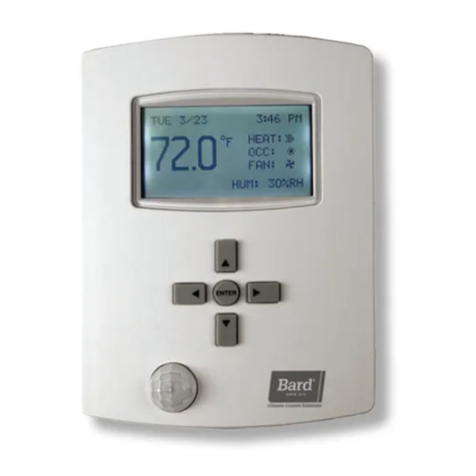
Bard
Bard CompleteStat-Series CS9B-THO Product guide
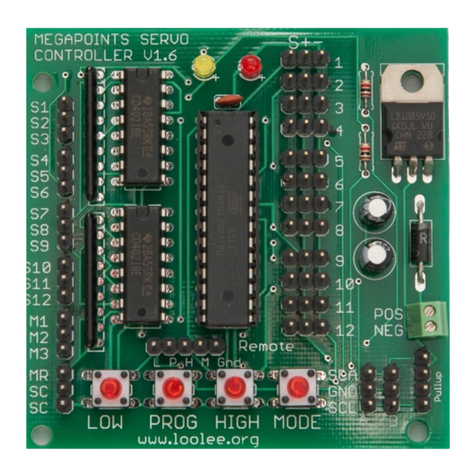
MegaPoints Controllers
MegaPoints Controllers Servo Controller user guide

White Rodgers
White Rodgers 50M56-743 installation instructions