APS Resource HTC Kit Installation instructions

6219 West Eastwood Court • Mequon, Wisconsin 53092 • TEL: (262) 518-1000 • FAX: 1-800-827-7491
AP4047 RA 11/10
©2010 4Front Engineered Solutions, Inc. - APS Resource
APS Resource
Your Aftermarket Solution
®

PAGE 1
©2010 4Front Engineered Solutions, Inc. - APS Resource AP4047 RA 11/10
APS Resource warrants that this HYDRAULIC CONVERSION KIT will be free from defects in material and workman-
ship under normal use for a period of one (1) year from the earlier of 1) 60 days after the date of initial shipment by
APS Resource, or 2) the date of installation of the HYDRAULIC CONVERSION KIT by the original purchaser, provided
that the owner maintains and operates the HYDRAULIC CONVERSION KIT in accordance with this Owner’s Manual.
In the event that this HYDRAULIC CONVERSION KIT proves defective in material or workmanship within the
applicable limited warranty period, APS Resource will, at its option:
1. Replace the HYDRAULIC CONVERSION KIT or the defective portion without charge to the owner, or
2. Alter or repair the HYDRAULIC CONVERSION KIT on site or elsewhere, without charge to the owner.
The limited warranty stated in the preceding paragraph IS EXCLUSIVE AND IT IS IN LIEU OF ANY OTHER
GUARANTEES AND WARRANTIES, EXPRESS OR IMPLIED. The limited warranty does not cover any failure
caused by improper installation, abuse, negligence or failure to maintain and adjust the Hydraulic Conversion Kit
properly. Parts requiring replacement due to damage resulting from vehicle impact, abuse or improper operation are
not covered by this warranty. APS Resource disclaims any responsibility or liability for any loss or damage (including,
without limitation, direct, indirect or consequential damages, or lost prots or production time) that results from the use
of unauthorized replacement parts or modication of the HYDRAULIC CONVERSION KIT. APS Resource’s sole ob-
ligation with regard to a HYDRAULIC CONVERSION KIT that proves to be defective in material or workmanship shall
be as set forth in its standard warranty above (i.e., APS Resource will, at its option, repair or replace the HYDRAULIC
CONVERSION KIT or portion thereof, without charge to the purchaser).
This limited warranty does not cover any failure caused by improper installation, abuse, negligence, or failure to prop-
erly maintain and adjust the HYDRAULIC CONVERSION KIT. This limited warranty will be void or of no effect if the
original purchaser does not notify APS Resource’s warranty department within ninety (90) days after the product defect
is discovered. Parts requiring replacement due to damage resulting from vehicle impact, abuse, or improper operation
are not covered by this warranty. APS Resource disclaims any responsibility or liability for any loss or damage that
results from the use of unauthorized replacement parts or modication of the HYDRAULIC CONVERSION KIT.
THERE ARE NO WARRANTIES, EXPRESS OR IMPLIED, WHICH EXTEND BEYOND THE DESCRIPTION ON THE
FACE HEREOF, AND THERE IS NO WARRANTY OF MERCHANTABILITY OR OF FITNESS FOR A PARTICULAR
PURPOSE.
APS Resource warranties extend only to the HYDRAULIC CONVERSION KIT itself, and not to the dock leveler to
which it is installed.
APS Resource DISCLAIMS all warranties, express or implied, responsibility or liability for loss or damage of any kind
associated with the installation or maintenance of the HYDRAULIC CONVERSION KIT, including any liability for premature
product wear, product failure, property damage or bodily injury arising from improper installation or maintenance of the
HYDRAULIC CONVERSION KIT.

PAGE 2
©2010 4Front Engineered Solutions, Inc. - APS Resource AP4047 RA 11/10
LIMITED WARRANTY ............................................................................................. 1
CONTENTS & SAFETY SIGNAL WORDS .............................................................. 2
SAFETY PRACTICES..................................................... ............................................. 3
TOOL LIST ............................................................................................................... 3
INSTALLATION ........................................................................................................ 4
PIT CHECK ........................................................................................................ 4
LEVELER CHECK .............................................................................................. 4
SITE PREPARATION ......................................................................................... 5
SECONDARY MAINTENANCE STRUT ............................................................. 6
LEVELER PREPARATION ................................................................................. 7
RAMP PLATFORM BRACKET INSTALLATION ................................................. 8
PIT FLOOR BRACKET ....................................................................................... 9
LIP CYLINDER INSTALLATION ......................................................................... 10
LIP SUPPORT INSTALLATION .......................................................................... 11
PLACARD INSTALLATION ................................................................................ 11
POWER SYSTEM INSTALLATION ..................................................................... 12
WIRING DIAGRAMS .......................................................................................... 13
ARTD SYSTEM INSTALLATION ........................................................................ 14
CONVERSION SYSTEM TEST .......................................................................... 17
OPERATION ............................................................................................................ 17
MAINTENANCE ....................................................................................................... 20
TROUBLESHOOTING GUIDE ................................................................................. 21
PARTS LIST ............................................................................................................. 22
You may find safety signal words such as DANGER, WARNING, CAUTION or NOTICE throughout the owners
manual. Their use is explained below.

PAGE 3
©2010 4Front Engineered Solutions, Inc. - APS Resource AP4047 RA 11/10
READ AND FOLLOW THE INSTRUCTIONS
CONTAINED IN THIS MANUAL BEFORE INSTALLING,
OPERATING OR SERVICING THE HYDRAULIC
CONVERSION KIT.
Place barricades on the dock floor around the dock
leveler pit and in the driveway in front of the pit while
installing, maintaining or repairing the dock leveler.
SAFELY SECURE MAINTENANCE STRUT before
climbing into the dock leveler pit or doing any
maintenance or repair under the dock leveler.
Disconnect the power and properly tag or lock off
before climbing into the dock leveler pit or doing any
maintenance or repair under the dock leveler.
All electrical troubleshooting or repair must be done by
a qualified technician and must meet applicable codes.
Disconnect the power and properly tag or lock off
before doing any electrical work. If it is necessary to
make troubleshooting checks inside the control box with
the power on, USE EXTREME CAUTION! Do not place
fingers or non-insulated tools inside the control box.
Touching wires or other parts inside the control box
could result in electrical shock, serious injury or death.
Do not operate the dock leveler with equipment,
material or people on the ramp or lip.
Do not operate the dock leveler when anyone is in front
of it unless they are securing the maintenance strut.
Stay clear of the dock leveler when it is moving.
KEEP HANDS CLEAR OF HINGES AT ALL TIMES.
Do not use hands to position dock leveler ramp or lip in
truck or to store dock leveler.
Always use full range toe guards on dock levelers
converted with hydraulic conversion. Failure to use toe
guards could result in serious shearing injuries from a
descending dock leveler.
Do not use the dock leveler if it looks broken or does
not seem to work right. Tell your supervisor it needs
repair right away.
Do not use a fork truck or other material handling
equipment to lower the ramp.
List of tools and equipment needed to field install the
HTC Kit. This job would typically require two service
technicians.
Service truck should be equipped with the following:
• Safety markers to secure work area around the dock
• “Boom” crane or hoist
• Cutting torch
• Welder
• Soap stone or paint marker
• Tape measure
• Drill and drill bit kit, magnet, & hammer
• Miscellaneous hand tools.
• 1-1.5 gallons of Mil H - 5606 hydraulic fluid
• Teflon plumbers tape
• Touch up paint
• Shim stock
• Electrical wire / conduit

PAGE 4
©2010 4Front Engineered Solutions, Inc. - APS Resource AP4047 RA 11/10
1. Check entire dock leveler pit for proper
construction according to certified pit drawings.
Concrete must be without excessive cracks and in
structurally sound condition.
2. Check electrical service running to the pit to assure
it agrees with the correct location and voltage for
the junction box.
1. Visually check that the dock leveler to be
converted is structurally sound and able to
be returned to extended service.
2. Visually check that the rear hinge pins and retaining
clips are in place. Movement of the rear hinge must
be limited to only rotational. If the rear hinge moves
vertically or horizontally, STOP, do not install the
Hydraulic conversion kit.
3. Visually check that the retaining clips for the lip rods
are in place.
4. Visually check that all cotter pins, hardware, and
other fasteners are not excessively worn, and are in
place to function properly.
5. Verify that all welds are intact and that all structural
members are in good working condition.
6. Thoroughly inspect the structural integrity of
the dock leveler to be sure it is suitable for
conversion.
7. Lay out the location of all the Hydraulic Conversion
Kit components. Check for any interference
between the Hydraulic Conversion Kit components
and any structural members on the leveler,
including the platform and subframe (except as
described in step 5A or 5B of the “Ramp Platform
Bracket Installation”). If there appear to be any
interference problems, STOP, do not install the
Hydraulic Conversion Kit.
8. Check the front of the subframe. Make sure the
front of the subframe is connected by structural
members to the rear subframe and can support the
full weight of the leveler and traffic. If not, STOP,
do not install the Hydraulic Conversion Kit.

PAGE 5
©2010 4Front Engineered Solutions, Inc. - APS Resource AP4047 RA 11/10
Place barricades around pit on dock floor and driveway
before installing, maintaining, or repairing dock leveler.
1. In this conversion you will be removing the ramp’s
lifting mechanism. After the ramp has been opened
into the “up” position, it must be safely secured with
the proper hoists and safety struts before work can
begin. Failure to do so could allow the ramp to fall
resulting in serious injury or death.
2. Mount and wire push-button station (See Figure 1)
and pit mounted receptacle (See Figure 2). See
wiring diagram located on the inside cover of the
control box or wiring diagrams in this manual for
wiring information. Follow the wiring instructions
to set control for proper voltage. Wires show in
dashed lines are field connections.
3. If conduit must be installed do so at this time. Refer
to the conduit requirements on the pit detail (See
Figure 2). Follow all applicable electrical codes and
standards.
Push-button
control station
48"

PAGE 6
©2010 4Front Engineered Solutions, Inc. - APS Resource AP4047 RA 11/10
1. Secure all areas around the dock leveler to be
converted. Both the front and rear areas around the
dock leveler should be blocked-off and secured.
2. Raise the ramp to the open position. Raise the lip to
its maximum open position and safely secure it.
3. Please the OEM safety bar in the factory
recommended position.
4. Weld the maintenance strut hanger to the underside
of the ramp per dimensions shown; or adjust
position as required for proper installation. Use
touch-up paint as required. See Figures 3 and 4.
5. Weld the subframe bracket to the inside of the
subframe as shown. Use touch-up paint as
required. See Figure 5.
6. Place the upper strut tube into the lower strut tube.
Make sure the decal on the lower tube, and the tab
on the upper tube, both face outward toward the
driveway as shown. See Figure 6.

PAGE 7
©2010 4Front Engineered Solutions, Inc. - APS Resource AP4047 RA 11/10
1. With the ramp properly secured by both
maintenance struts, carefully disassemble and
remove all parts of the ramp activation mechanism,
cross traffic leg mechanism, below dock chain
mechanism, lip extension mechanism, and holdown
assembly (if applicable).
2. Using the (2) 5/8” x 4” concrete anchor bolts
provided, anchor the rear frame of the dock leveler
to the pit floor. The anchor must penetrate at least
3” into the concrete. See Figure 8.
3. Install full range sliding toe guards if applicable. In
some applications, it may be necessary to create
holes in the stationary toe guards for clearance of
the pivot and slider bolts. See Figure 9.
7. Place the lower strut tube into the subframe bracket
and fasten securely as shown using the hardware
provided. See Figures 6 and 7.
8. While extending the upper strut tube, swing both
tubes together upward, placing the tab into the
slot of the maintenance strut hanger located on
the ramp. Telescope both tubes until the holes line
up in both tubes and fasten as shown using the
hardware provided. See Figures 6 and 7.
9. Secure the upper tube to the maintenance strut
hanger using the hardware provided. If desired, a
keyed lockout (by others) may be used in place of
the hardware in position “A” only. See Figure 6.

PAGE 8
©2010 4Front Engineered Solutions, Inc. - APS Resource AP4047 RA 11/10
1. Measurements to locate the ramp platform bracket
position are calculated from the rear face of the
ramp plate to the center of the hole in the ramp
platform bracket, See Figure 10.
2. A visible reference line should be drawn at the
above determined position, extending between both
deck support beams.
3. From the reference line towards the rear of the
leveler, measure and draw a line at 8⅜".
4. From the reference line in step 2 towards the front
of the leveler, measure and draw a line at 4¾". You
will now have located a combined area of approx.
13 ⅛". This marks the spot where the 2 angles
and ramp platform bracket will be positioned. See
Figure 10.
.
Serco dock levelers make use of a center deck
support channel. As a result, 20" pit levelers will
require additional main lifting cylinder clearance.
To provide the additional clearance needed, remove
the portion of the center support channel marked
off for the ramp platform bracket described in step
4. This 13⅛" area of the deck plate should be
ground flat enough to allow you to "flush mount" the
platform bracket assembly. See Figure 12.
Measure the height
of the center support channel and subtract ¼". In
the same 13⅛" area described in step 4, locate the
next (left and right of center) support channels and
mark this measurement to the inboard sides. This
is where the 2 support angles will be welded. See
Figure 12.
6. To evenly distribute the platform load when raising
the leveler, weld the 2 pieces of angle iron into the
marked off area along the support beams and deck.
The weld must be continuous and surround the
entire perimeter of the angles. See Figures 11 and
12.
7. After the angles have been completely welded in
position, center and align the flat base plate to the
angles with the holes closest to the front of the
ramp. Weld the plate into position on the angles.
See Figures 11 and 12.
A
B
C
D
- CRITICAL QUALITY DIMENSION
TOLERANCES ARE IN INCHES
UNLESS OTHERWISE SPECIFIED
MATERIAL SPECIFICATION
DRAWN
APPROVED
SHEET
DRAWN DATE
APPROVED DATE
SHEET SIZE
JOB/REF NUMBER
MATERIAL#/PO#
SCALE
.X : 0.030
.XX : 0.030
.XXX : 0.010
FRACTIONAL : 1/16
DIAMETER : +0.015 / -0.005
ANGULAR : 1 DEG 1 E10/25/2010 1FOekleuhcS.nosaJ
UOM
17"
DIMENSION "A"
4-3/4" 8-3/8"
LIP CYLINDER
LIP LUG
LIP CYLINDER
RAMP LUG
PIT FLOOR BRACKET
RAMP BRACKET
LEVELER LENGTH APPROX. PIT DEPTH DIMENSION "A"
8 FT. 20 IN. 36-1/8"

PAGE 9
©2010 4Front Engineered Solutions, Inc. - APS Resource AP4047 RA 11/10
8. Bolt the clevis bracket (with the two bolts provided)
to the flat base plate using the third and fifth
threaded holes. The holes referred to are counted
from the rear of the leveler.
9. If the gap between the side of the clevis bracket and
the side of the deck support channel is less than
6¼", you will not have enough clearance for the
cylinder pin. It will be necessary to install the ramp
cylinder into the clevis bracket before the clevis
bracket is bolted to the base plate.
10. Once bolted in place, weld the clevis bracket to
the base plate. The weld must be continuous and
surround the entire perimeter of the clevis bracket.
See Figure 11.
1. Attach main lifting cylinder to the ramp bracket with
the hose port upward towards the ramp.
2. Attach the clevis pit floor bracket assembly to the
cylinder rod with the hardware provided.
3. Full extend the cylinder rod and allow the clevis pit
floor bracket to lie flat on the pit floor. Mark the
location where the bracket makes contact with the
pit floor is the pit floor bracket mounting location.
4. Temporarily secure the pit floor bracket in place.
5. With a hoist, lower the ramp slowly to make sure the
cylinder will not bottom out at the full below dock
position. Adjust the pit floor bracket if needed.
6. Disassemble the pit floor clevis from the baseplate
by unscrewing the (2) bolts.
7. Place the baseplate in the marked off area.
Securely fasten the baseplate to the pit floor using
the (6) ¾" x 6" concrete anchors provided.
8. Reassemble the pit floor clevis to the baseplate,
using the (2) bolts from Step 6.
9. Weld the clevis to the baseplate. The weld must be
continuous and surround the entire perimeter of the
clevis bracket. See Figure 13.
20
ANCHOR HOLES
FOR 3/4" X 6" ANCHORS
BOLTS TO ASSEMBLE
PIT CLEVIS TO PIT
FLOOR PLATE BASE
1/4

PAGE 10
©2010 4Front Engineered Solutions, Inc. - APS Resource AP4047 RA 11/10
1. Extend the lip to its maximum position.
2. Secure the lip in the completely extended
position.
3. Find an area at the front of the leveler to install
the lip cylinder without interfering with the
operation of the leveler. If not already there, cut
an opening of 4½" wide by 5" tall into the front
header to make room for the lip cylinder. See
Figure 14.
4. Weld the lip cylinder lip lug (front cylinder lug) on
the underside of the lip, against the front of the lip
spool, or close to the lip rod. See Figures 10 and
14.
(IF APPLICABLE)
5. Position the lip cylinder ramp lug (rear cylinder
lug) beneath the deck plate so that it is in line with
the front cylinder lug. The distance between the
mounting holes from the front cylinder lug to the
rear cylinder lug should be approx. 17". See Figure
10.
6. Tack weld the rear cylinder lug in position and
attach the lip cylinder at both ends. See Parts List
for clevis pin information.
7. Weld on bridge bar clevis below the opening cut
in the header, allowing enough room for the front
cylinder lug movement (approximately 5” below
hinge). See Figure 14.
8. Carefully lower the lip to the pendant position.
The lip cylinder must not stroke out when the lip is
extended or bottom out when the lip is closed.
9. After making sure that the lip cylinder has
the proper range, weld the rear cylinder lug
permanently in position.

PAGE 11
©2010 4Front Engineered Solutions, Inc. - APS Resource AP4047 RA 11/10
1. Install lip supports if applicable.
2. Carefully lower the lip to the closed position.
3. With a hoist lower the ramp until it is perfectly even
with the loading dock floor. This step is important
to determine the resting or pendant position of the
leveler when it is not in use.
4. With the deck even to the dock floor level and the
lip closed in the pendant position, tack weld the
lip supports on to the front of the frame. The lip
supports must be positioned in such a way as to
allow the fully closed lip and deck to rest evenly on
both lip supports. See Figure 15.
5. With the hoist, raise the leveler and support it on
both maintenance struts, then fully weld the lip
supports in position.
1. Permanently mount the laminated dock leveler
WARNING and OPERATING INSTRUCTION
placard on the wall near the dock leveler control.
See Figures 1 and 16. Make sure the customer
gets the user's manual and is properly trained.
Warning and operating
instruction placard
OPERATIONS
567
1/4
WELD ALL AROUND
BOTH LIP KEEPERS.
SHIM AS REQUIRED.

PAGE 12
©2010 4Front Engineered Solutions, Inc. - APS Resource AP4047 RA 11/10
1. Find an open area near the rear of the subframe
that will allow for easy access to service and
maintain the motor/pump assembly.
2. Weld the motor support bracket to the subframe in
the above mentioned position.
3. Attach the motor to the motor support bracket.
4. Install all of the elbows onto the pump and
cylinders. See Figure 17 and Parts List.
5. Install the velocity fuse and adapter to the main
lifting cylinder.
6. Install the smaller hose from the lip cylinder to the
pump.
7. Install the larger hose from the pump to the velocity
fuse on the main lifting cylinder.
8. Install the breather to the cylinder.
9. With the ramp resting on the maintenance strut, and
the lip pendant, fill the oil reservoir near the top with
MIL 5606 oil.

PAGE 13
©2010 4Front Engineered Solutions, Inc. - APS Resource AP4047 RA 11/10
BLU BRN
ORG
RED
WHT
BLK
YEL
208-230V, SINGLE PHASE, 50/60HZ
LEVELER MOTOR WIRING DETAILS
DOUBLE POLE
CIRCUIT BREAKER
(BY OTHERS)
10 AMP MAX
L1
GRN
L2
208-230V
1 PHASE
50/60HZ
PIT WALL
JUNCTION BOX
(BY OTHERS)
3/4 HP MOTOR HAS
AUTOMATIC THERMAL
OVERLOAD
CONTROL
STATION
NOTE: VISUALLY CONFIRM MOTOR TAG
BLACK
GREEN
WHITE
MOTOR
WHT
BLK
GRN
INCOMING POWER AND MOTOR WIRES TO
BE STRANDED 14 GA 75°C COPPER.
(TORQUE TO 9 LBS. - IN)
GROUND WIRES TO BE STRANDED 14 GA
75°C COPPER )TORQUE TO 35 LB.- IN)
WIRING PROVIDED BY CUSTOMER
WIRING PROVIDED BY APS RESOURCE
M
GRN
SUPPLY LINE
GRN
NEUTRAL LINE
CIRCUIT BREAKER
(BY OTHERS)
20 AMP MAX
WHITE
GREEN
BLACK
PIT WALL
JUNCTION BOX
(BY OTHERS)
CONTROL
STATION
110-115V
1 PHASE
50/60HZ
LEVELER MOTOR WIRING DETAILS
110-115V, SINGLE PHASE, 60HZ
NOTE: VISUALLY CONFIRM MOTOR TAG
M
BLK
GRN
WHT
BRN
ORG
RED
BLU
WHT
YEL
BLK
INCOMING POWER AND MOTOR WIRES TO
BE STRANDED 14 GA 75°C COPPER.
(TORQUE TO 9 LBS. - IN)
GROUND WIRES TO BE STRANDED 14 GA
75°C COPPER )TORQUE TO 35 LB.- IN)
MOTOR
3/4HP MOTOR HAS AUTOMATIC
THERMAL OVERLOAD
WIRING PROVIDED BY CUSTOMER
WIRING PROVIDED BY APS RESOURCE
GRN
¾
¾

PAGE 14
©2010 4Front Engineered Solutions, Inc. - APS Resource AP4047 RA 11/10
1. Determine a good location for the ARTD sensor
brackets. Make sure the brackets and sensors will not
become damaged from normal operation of the dock
leveler.
2. Weld the ARTD ramp bracket to the underside of the
deck plate. Locate approximately 9" behind the front
edge of the ramp plate. The slot should be oriented
towards the front of the dock leveler. See Figure 18
and 19.
3. Weld the ARTD lip bracket to the underside of the lip
plate. Locate approximately 3" behind the lip hinge
area. See FIGURES 18 and 20.
4. Fasten junction box to the subframe. Mount
approximately 29" measured from the rear of the pit.
Use self tapping screws provided. See Figure 21.
5. Install a strain relief into each end of the junction box.
6. Install the power cord through the strain relief facing
the rear of the pit. Use a self tapping screw to secure
the green wire (ground) of the power cord to the frame
inside the junction box.
1
1
2
2
3
3
4
4
A A
B B
- CRITICAL QUALITY DIMENSION
TOLERANCES ARE IN INCHES
UNLESS OTHERWISE SPECIFIED
MATERIAL SPECIFICATION
DRAWN
MATERIAL#/PO#
PART DESCRIPTION
DRAWN DATE
JOB/REF NUMBERSCALE
ISSUE
PART NUMBER
.X :
0.060
.XX :
0.030
.XXX :
0.010
FRACTIONAL :
1/16
DIAMETER : +0.015 / -0.005
ANGULAR :
1 DEG
B6009078
PROXIMITY SWITCH INSTALLATION
KELLEY ARTD PROXY KIT
NTS.
jaime.pulido 7/11/2006
UOM
N/A
The information contained herein is proprietary and confidential to 4Front Engineered Solutions and is to be used solely for the
express purpose of consideration and development of the article described herein and may not be reproduced or disseminated without
the express written permission of 4Front.
EZIS TEEHSTEEHS
B2 OF2
Subframe
DETAIL - ARTD RAMP BRACKET WELD
DETAIL - ARTD LIP BRACKET WELD
RAMP PLATE
ARTD RAMP BRACKET
1/8
LIP PLATE
ARTD LIP BRACKET
LIP LUG
1/4
DETAIL - ARTD RAMP BRACKET WELD
DETAIL - ARTD LIP BRACKET WELD
RAMP PLATE
ARTD RAMP BRACKET
1/8
LIP PLATE
ARTD LIP BRACKET
LIP LUG
1/4
3"
9"
ARTD RAMP BRACKET
(ORIENT SLOT TOWARD
FRONT OF DOCK LEVELER)
ARTD
LIP BRACKET

PAGE 15
©2010 4Front Engineered Solutions, Inc. - APS Resource AP4047 RA 11/10
7. Attach the new lip and deck proximity switches and
brackets to the holes in the lip and deck brackets.
Fasted using hex nuts. See Figure 22.
8. At the LIP proximity switch, create a strain relief for
the switch cable. Use a black cable tie to make a
loop around the switch body. Leave a small amount
of slack in the switch cable and tighten cable tie. See
Figures 22 and 23.
9. At the DECK proximity switch, create a strain re-
lief for the switch cables. Use a black cable tie to
make a loop around the switch body. Route the LIP
and DECK sensor cable through this loop. Leave a
small amount of slack in the DECK sensor cable and
tighten cable tie. See Figures 22 and 24.
DETAIL F
1
1
2
2
3
3
4
4
A A
B B
- CRITICAL QUALITY DIMENSION
TOLERANCES ARE IN INCHES
UNLESS OTHERWISE SPECIFIED
MATERIAL SPECIFICATION
DRAWN
MATERIAL#/PO#
PART DESCRIPTION
DRAWN DATE
JOB/REF NUMBERSCALE
ISSUE
PART NUMBER
.X :
0.060
.XX :
0.030
.XXX :
0.010
FRACTIONAL :
1/16
DIAMETER : +0.015 / -0.005
ANGULAR :
1 DEG
B6009078
PROXIMITY SWITCH INSTALLATION
KELLEY ARTD PROXY KIT
NTS
jaime.pulido 7/11/2006
UOM
N/A
The information contained herein is proprietary and confidential to 4Front Engineered Solutions and is to be used solely for the
express purpose of consideration and development of the article described herein and may not be reproduced or disseminated without
the express written permission of 4Front.
EZIS TEEHSTEEHS
B2 OF1
COMMON PARTS KIT - PROXIMITY SWITCHES 6009078
QTY
DESCRIPTIONPART NUMBER
ITEM
4
HN-ANSI B18.2.2 - 1/4 - 20
2141611
2AC INDUCT PROX SWITCH, N/O, 18 MM6250402
1CAP, KELLEY ARTD60082893
2Wire Strain Relief5211104
4Cable Tie, Nylon - 8 1/4"131475
5
12" X 4" JUNCTION BOX60089826
1
2" X 4" J BOX COVER
60089877
2TEK #12-14 X 3/4" UNC Self Tapping Screw2157028
2ZIP TIE PANDUIT ANCHORS1314769
1Artd On Deck Bracket 600828610
1Artd On Deck Lip600828811
1CAP, MAINTAIN FLOAT/STORED SENSOR, V2600072112
1
Cord - Molded Plug
71202713
3Wire Nut16101114
4
LW 1/4 MED ZINC PLD BULK23428115
1) INSTALL PROXIMITY SWITCHES USING THE ARTD BRACKETS 10.1 & 11.1 AS SHOWN ON FIG. 1 & 2
2) FASTEN BRACKETS TO DECK AND LIP USING NYLON LOCK NUT 1.1
3) USE 5.1 CABLE TIES TO HOLD THE WIRES AND 9.1 PANDUIT ANCHORS, RUN ALL WIRES TO THE REAR,
4) "J" BOX FIG. 3 TO BE FASTENED 29" MEASURED FROM THE BACK OF THE BEAM USING 8.1 SELF TAPPING SCREWS ON
BEAM LEFT OF THE HYDRAULIC CYLINDER
5) SEE FIG. 4 FOR THE ELECTRICAL SCHEMATIC
REV. HISTORY:
ECO # DATE BY DESCRIPTION APPROVAL
09-185 04/06/2010 JP BREPLACED FASTENERS
2
2
Deck Bracket & Switch
Lip Bracket & Switch

PAGE 16
©2010 4Front Engineered Solutions, Inc. - APS Resource AP4047 RA 11/10
DETAIL F
1
1
2
2
3
3
4
4
A A
B B
- CRITICAL QUALITY DIMENSION
TOLERANCES ARE IN INCHES
UNLESS OTHERWISE SPECIFIED
MATERIAL SPECIFICATION
DRAWN
MATERIAL#/PO#
PART DESCRIPTION
DRAWN DATE
JOB/REF NUMBERSCALE
ISSUE
PART NUMBER
.X :
0.060
.XX :
0.030
.XXX :
0.010
FRACTIONAL :
1/16
DIAMETER : +0.015 / -0.005
ANGULAR :
1 DEG
B6009078
PROXIMITY SWITCH INSTALLATION
KELLEY ARTD PROXY KIT
NTS
jaime.pulido 7/11/2006
UOM
N/A
The information contained herein is proprietary and confidential to 4Front Engineered Solutions and is to be used solely for the
express purpose of consideration and development of the article described herein and may not be reproduced or disseminated without
the express written permission of 4Front.
EZIS TEEHSTEEHS
B2 OF1
COMMON PARTS KIT - PROXIMITY SWITCHES 6009078
QTY
DESCRIPTIONPART NUMBER
ITEM
4
HN-ANSI B18.2.2 - 1/4 - 20
2141611
2AC INDUCT PROX SWITCH, N/O, 18 MM6250402
1CAP, KELLEY ARTD60082893
2Wire Strain Relief5211104
4Cable Tie, Nylon - 8 1/4"131475
5
12" X 4" JUNCTION BOX60089826
1
2" X 4" J BOX COVER
60089877
2TEK #12-14 X 3/4" UNC Self Tapping Screw2157028
2ZIP TIE PANDUIT ANCHORS1314769
1Artd On Deck Bracket 600828610
1Artd On Deck Lip600828811
1CAP, MAINTAIN FLOAT/STORED SENSOR, V2600072112
1
Cord - Molded Plug
71202713
3Wire Nut16101114
4
LW 1/4 MED ZINC PLD BULK23428115
1) INSTALL PROXIMITY SWITCHES USING THE ARTD BRACKETS 10.1 & 11.1 AS SHOWN ON FIG. 1 & 2
2) FASTEN BRACKETS TO DECK AND LIP USING NYLON LOCK NUT 1.1
3) USE 5.1 CABLE TIES TO HOLD THE WIRES AND 9.1 PANDUIT ANCHORS, RUN ALL WIRES TO THE REAR,
4) "J" BOX FIG. 3 TO BE FASTENED 29" MEASURED FROM THE BACK OF THE BEAM USING 8.1 SELF TAPPING SCREWS ON
BEAM LEFT OF THE HYDRAULIC CYLINDER
5) SEE FIG. 4 FOR THE ELECTRICAL SCHEMATIC
REV. HISTORY:
ECO # DATE BY DESCRIPTION APPROVAL
09-185 04/06/2010 JP BREPLACED FASTENERS
2
2
10. Attach the adhesive backed cable tie mounts to the
underside of the deck. Clean the deck surface before
applying the mounts. Route and secure both sensor
cables through the cable tie mounts towards the junc-
tion box. See Figures 22 and 25.
11. Route the proximity switch cables through the remain-
ing strain relief and into the junction box. Shorten the
cables if necessary. See Figure 26.
12. Use wire nuts to connect the proximity cables to the
power cord leads. See Figure 27 for wiring diagram.
13. Install the junction box cover.
14. Connect the power cord to the control panel and wire
per the wiring diagram for the dock leveler control
panel. Install a receptacle at the rear of the pit; or
hardwire per local and national electrical codes.
PRS1: Closes 4° Below Dock,
Opens 4° Above Dock
PRS2: Closes When Lip is Pendant
Deck Sensor
625-040
Deck Position
(Below Dock)
PRS1
Lip Sensor
625-040
Lip Position
(Pendant)
PRS2
Power Cord
BRN BRN BLU BLU
BLK
WHT
J BOX
NEMA 5 15P
GRN
WHT
BLK

PAGE 17
©2010 4Front Engineered Solutions, Inc. - APS Resource AP4047 RA 11/10
1. With a hoist, slowly lower the ramp and lip to the
full below dock position. Check clearances to be
sure the cylinders do not bottom out and that the
power unit does not come in contact with the deck.
2. Disconnect and remove the hoist from the ramp.
3. Turn the "ON/OFF" switch to the "OFF" position.
4. Connect the electrical power to the dock leveler.
5. Turn the "ON/OFF" switch to the "ON" position.
Ramp will automatically return to the stored
position.
6. Press the "RAISE" Button. The ramp will rise
and the lip will extend once the ramp reaches the
highest position.
7. Release the "RAISE" button. Ramp will lower and
lip will remain extended.
8. Once the leveler reaches the full below dock
position, the lip will fall pendent. The ramp will then
automatically return to the stored position.
9. Repeat Steps 6-8 several times until all of the air
has been purged from the hydraulic system.
10. After the air has been purged from the hydraulic
system, raise the leveler and secure it using both
safety struts.
11. Check the entire hydraulic system for leaks or loose
fittings. Fix all leaks and make any necessary
repairs or adjustments.
12. Check to be sure that the hydraulic reservoir is filled
to the proper level. Add if required. See Figure 28.
13. Double check all welds and paint exposed metal to
prevent rust.
3"- 4"
Use Type 5606 (Low Temp.)
Hydraulic Oil.
Check Oil Level With Ramp
Resting on the Matienance Strut
And Lip Pendant.

PAGE 18
©2010 4Front Engineered Solutions, Inc. - APS Resource AP4047 RA 11/10
Lip extend
Ramp
Vehicle bed
OFF ON
PUSH
TO RAISE
Dock level
supports
1. Do not operate the dock leveler until a vehicle is in
position against the dock bumpers.
2. Tell vehicle driver “Your vehicle must stay at the dock.”
3. Chock or hitch vehicle.
4. If necessary, remove end loads with the ramp in the
dock level (stored) position. See Figure 29.
5. To extend the dock leveler lip into the vehicle:
5.1 Turn the “ON/OFF” switch to the “ON” position.
See Figure 30.
5.2 Push and hold the "RAISE" button. The ramp will
rise and the lip will extend once the ramp reaches
the highest position. See Figure 30.
5.3 Release the "RAISE" button once the lip is fully
extended.
5.4 Ramp and lip will lower until the lip rests on the
vehicle bed. See Figure 31.
6. Proceed with loading or unloading.

PAGE 19
©2010 4Front Engineered Solutions, Inc. - APS Resource AP4047 RA 11/10
7. To return the dock leveler to the stored position when
loading or unloading is complete.
7.1 Turn the “ON/OFF” switch to the “ON” position.
7.2 Push and hold the “RAISE” button. The ramp will
rise and the lip will lower.
7.3 Release the "RAISE" button when the lip is fully
retracted. The ramp will lower to the dock level
(stored) position.
7.4 Check that the lip is not extended and the ramp
is supported by both dock level supports before
driving or walking on the ramp. Ramp should be
level with dock oor.
7.5 Turn the “ON/OFF” switch to the “OFF” position.
8. Unchock or release vehicle.
9. Tell vehicle driver “Your vehicle may now leave the
dock.”
To lower the ramp without extending the lip for end loading
below dock level:
1. Turn the “ON/OFF” switch to the “ON” position.
2. Press the "RAISE" button and hold it until leveler is
fully raised and the lip starts to extend. When the lip
has extended 2 to 3 inches to clear the front of the lip
keepers, release the button.
3. Turn the “ON/OFF” switch to the “OFF” position as the
ramp begins to lower. Leveler will oat down for end
loading.
4. Load or unload end loads.
5. When loading or unloading is complete, return the
dock leveler to the stored position. Turn the “ON/
OFF” switch to the “ON” position. The dock leveler will
automatically return to the stored position.
6. Visually check that the lip is not extended and the
ramp is supported by both dock level supports before
driving or walking on the ramp. Ramp should be level
with dock oor.
7. Turn the “ON/OFF” switch to the “OFF” position.
8. Unchock or release vehicle.
9. Tell vehicle driver “Your vehicle may now leave the
dock”.
The A.R.T.D. automatically resets the leveler whenever a
vehicle just pulls away from the loading dock with the lip
resting on the vehicle. This is how it works.
1. If the vehicle pulls away, the leveler will oat down to
the lowest position and the lip will fall. The leveler will
automatically raise, retract the lip, then oat down to
the stored position.
Table of contents
Popular Lifting System manuals by other brands
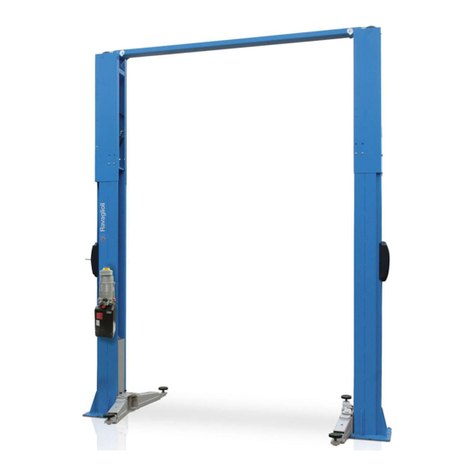
Ravaglioli
Ravaglioli KPH 370.32 Translation of the original instructions
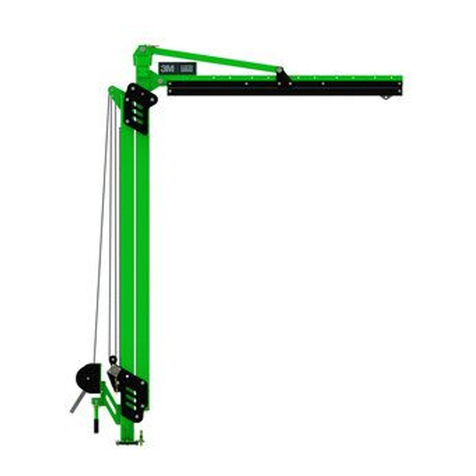
3M
3M DBI SALA Flexiguard M100 User instructions
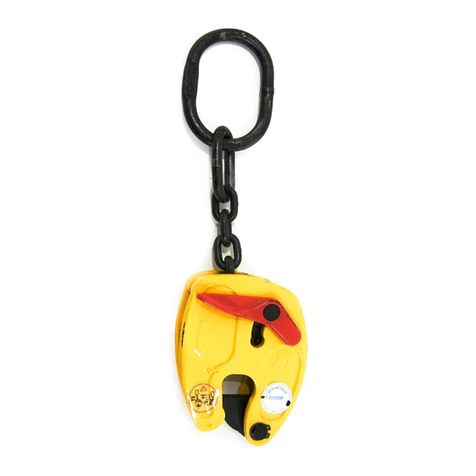
Tractel
Tractel KS USER OPERATING AND INSPECTION MANUAL
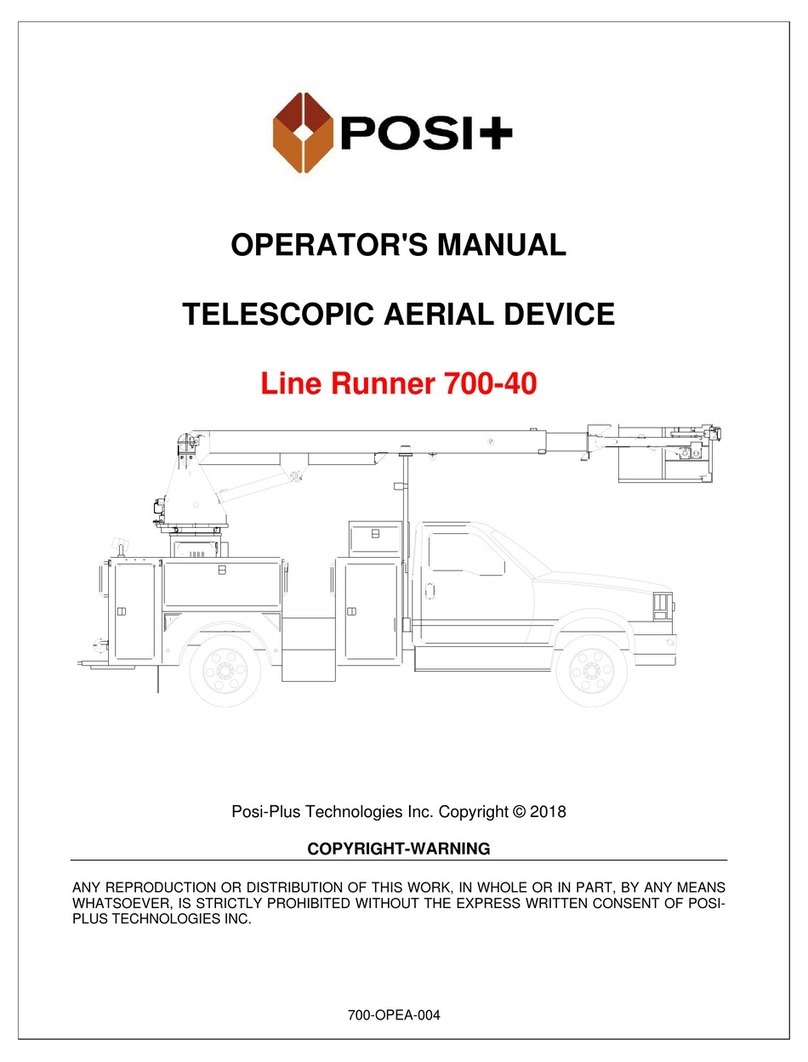
Posi-Plus
Posi-Plus Line Runner 700-40 Operator's manual
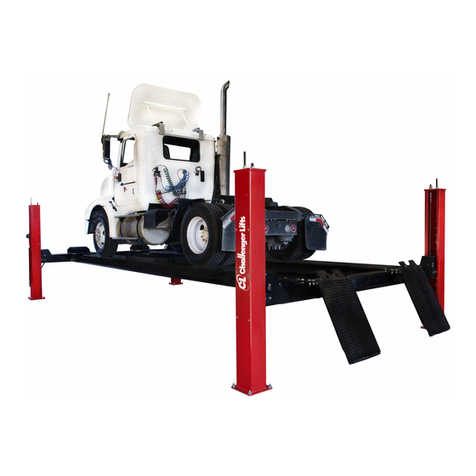
Challenger Lifts
Challenger Lifts 4030SFX Installation, operation & maintenance manual
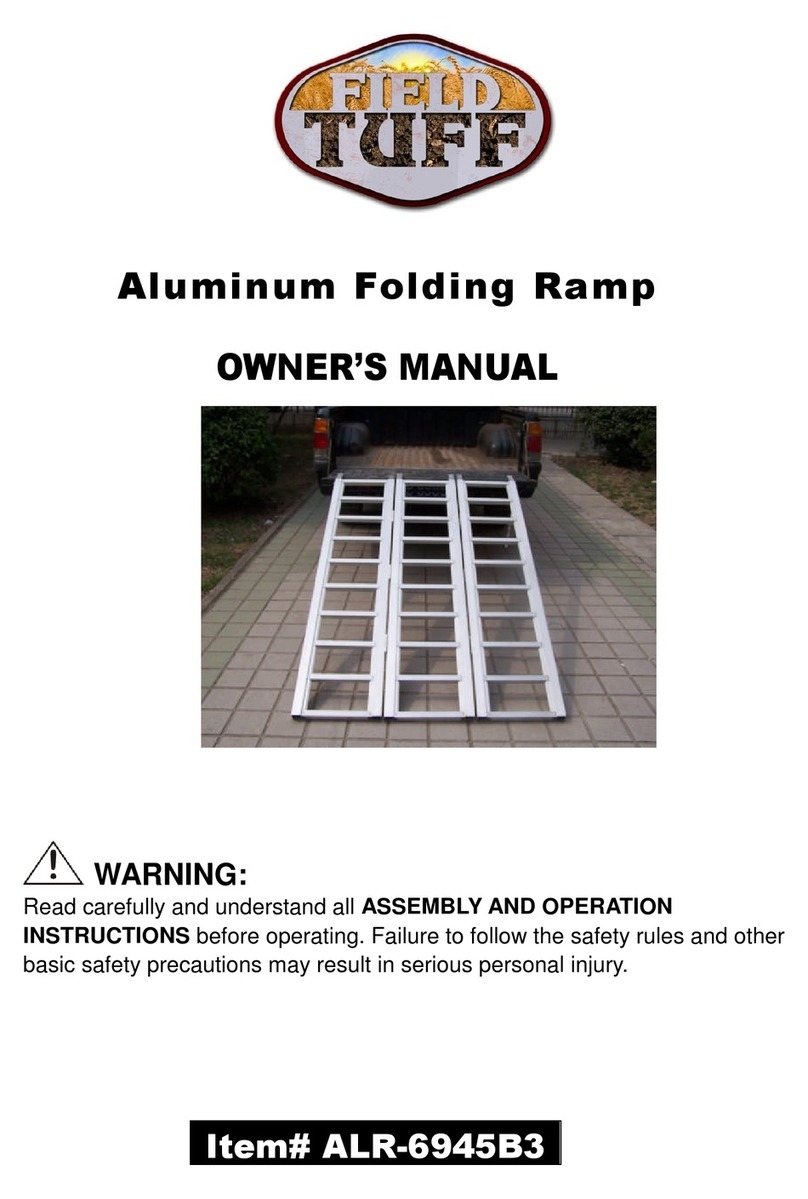
Field Tuff
Field Tuff ALR-6945B3 owner's manual