Audi A8 292 Assembly instructions

292
Service
292
Home study program 292
For internal company use only
All rights reserved, including the right to
make technical changes
Copyright* 2002 AUDI AG, Ingolstadt
Department I/VK-35
D-85045 Ingolstadt
Fax +49 (0)841/89-36367
000.2811.12.20
Technically correct as at 007/02
Printed in Germany
adaptive air suspension
in the Audi A8

The development of the running gear is subject to conflicting objectives. For now, besides
"classic" aims such as function, driving safety, strength and durability, requirements such as
weight reduction, driving comfort and acoustics are increasingly gaining in importance.
At first glance, many requirements appear to be in mutual opposition. A car designed to be
very comfortable will lose out in terms of driving safety when driven at the limit.
On the other hand, a car with very sporty tuning will achieve considerably higher cornering
speeds, and will reach its limit much later. However, this sporty tuning necessarily entails limi-
tations when it comes to comfort.
In the Audi A8 MY 2003, a newly developed, fully bearing air suspension system is used.
In conjunction with the CDC status-dependent electronic damping control, this ensures that
the main - and partly conflicting - requirements are satisfied in an optimum manner within the
limits of the laws of physics.

3
Contents
Page
Caution!
Note!
New!
The home study program informs you about designs and
functions.
The home study program is not a Repair Manual!
All values stated herein are purely intended to facilitate your
understanding of the program, and are based on the software
version valid at the time the SSP was compiled.
For service and repair work, it is important that you please use
the current technical literature.
Introduction
Basics . . . . . . . . . . . . . . . . . . . . . . . . . . . . . . . . . . . . . . . . . . . . . . . . . . . . . . . . . . . . . . 4
New technology. . . . . . . . . . . . . . . . . . . . . . . . . . . . . . . . . . . . . . . . . . . . . . . . . . . . . . 4
Operation and display
Vehicle levels . . . . . . . . . . . . . . . . . . . . . . . . . . . . . . . . . . . . . . . . . . . . . . . . . . . . . . . . 6
Operation and display system . . . . . . . . . . . . . . . . . . . . . . . . . . . . . . . . . . . . . . . . . . 9
System components
Vehicle overview . . . . . . . . . . . . . . . . . . . . . . . . . . . . . . . . . . . . . . . . . . . . . . . . . . . . 10
Control unit J197 . . . . . . . . . . . . . . . . . . . . . . . . . . . . . . . . . . . . . . . . . . . . . . . . . . . . 12
Suspension/shock absorber strut . . . . . . . . . . . . . . . . . . . . . . . . . . . . . . . . . . . . . . 13
Shock absorber . . . . . . . . . . . . . . . . . . . . . . . . . . . . . . . . . . . . . . . . . . . . . . . . . . . . . 14
Air supply unit . . . . . . . . . . . . . . . . . . . . . . . . . . . . . . . . . . . . . . . . . . . . . . . . . . . . . . 15
Solenoid valve block . . . . . . . . . . . . . . . . . . . . . . . . . . . . . . . . . . . . . . . . . . . . . . . . . 16
Accumulator. . . . . . . . . . . . . . . . . . . . . . . . . . . . . . . . . . . . . . . . . . . . . . . . . . . . . . . . 16
Pneumatic diagram . . . . . . . . . . . . . . . . . . . . . . . . . . . . . . . . . . . . . . . . . . . . . . . . . . 18
Pressure build-up. . . . . . . . . . . . . . . . . . . . . . . . . . . . . . . . . . . . . . . . . . . . . . . . . . . . 19
Pressure reduction . . . . . . . . . . . . . . . . . . . . . . . . . . . . . . . . . . . . . . . . . . . . . . . . . . 19
Senders (sensors) . . . . . . . . . . . . . . . . . . . . . . . . . . . . . . . . . . . . . . . . . . . . . . . . . . . 20
System functions
Control concept for standard running gear . . . . . . . . . . . . . . . . . . . . . . . . . . . . . . 26
Control concept for sporty running gear . . . . . . . . . . . . . . . . . . . . . . . . . . . . . . . . 28
Control concept for special operating conditions . . . . . . . . . . . . . . . . . . . . . . . . . 29
Interfaces
System overview of components with bus link (CAN, MOST) . . . . . . . . . . . . . . . 34
System overview of components without bus link . . . . . . . . . . . . . . . . . . . . . . . . 35
CAN information exchange . . . . . . . . . . . . . . . . . . . . . . . . . . . . . . . . . . . . . . . . . . . 36
Function diagram . . . . . . . . . . . . . . . . . . . . . . . . . . . . . . . . . . . . . . . . . . . . . . . . . . . 38
Other interfaces. . . . . . . . . . . . . . . . . . . . . . . . . . . . . . . . . . . . . . . . . . . . . . . . . . . . . 40
Service
Control unit code . . . . . . . . . . . . . . . . . . . . . . . . . . . . . . . . . . . . . . . . . . . . . . . . . . . . 42
System initialisation . . . . . . . . . . . . . . . . . . . . . . . . . . . . . . . . . . . . . . . . . . . . . . . . . 42
Final control diagnosis . . . . . . . . . . . . . . . . . . . . . . . . . . . . . . . . . . . . . . . . . . . . . . . 43
Measured value blocks . . . . . . . . . . . . . . . . . . . . . . . . . . . . . . . . . . . . . . . . . . . . . . . 43

4
Introduction
Basics
The basics for understanding air suspension
systems are contained in home study pro-
grams 242 and 243 and are of course also
valid for the system to be introduced in the
A8 from model year 2003.
New technology
The new A8 heralds a new system in terms of
technical content and range of functions. It
differs from the known system of the allroad
quattro in the following features:
CDC instead of PDC damping control:
The control takes account of the current driv-
ing status. The wheel movements (unsprung
masses) and body movements (sprung
masses) are recorded.
Within the choice of four programs (modes),
different damping characteristics are
implemented. In this process, each shock
absorber can be controlled independently.
292_001
Therefore, in each mode which is selected
(comfortable or sporty), the maximum degree
of comfort and driving safety is ensured (see
description "Shock absorber" in the "System
components" section).
The term "mode" can therefore be understood
to be the well-balanced combination of the
adaptive air suspension program and the
damping map.
292_025
Enhanced sensor system:
Three acceleration sensors are employed to
record the body movement.
(See description "Body acceleration sender"
in the "System components" section.)

5
Operation:
Integration in the MMI means that operation
is user-friendly, logical and easy to learn.
(See description in the "Operation and dis-
play" section.)
292_003
292_002
Residual pressure retaining valves:
Each suspension strut features residual pressure retaining valves directly at the air connec-
tion. This ensures that a minimum pressure of approx. 3.5 bar is maintained in the pneumatic
springs. This practically eliminates the risk of damage during storage and assembly to the
greatest possible extent.
Encased pneumatic springs:
The air bellows are encased in an aluminium
cylinder. The result is a considerable improve-
ment in the response characteristic.
(See description "Pneumatic springs" in the
"System components" section.)

6
Operation and display
Vehicle levels
The A8 comes either with a standard running gear (adaptive air suspension) or a sporty run-
ning gear (adaptive air suspension-sport).
Standard running gear:
The following programs can be selected either manually or automatically:
"automatic" mode:
Basic vehicle level, comfort-oriented suspension with appropriately adapted damper map. The
vehicle is lowered by 25 mm after 30 seconds at speeds of 75 mph (120 km/h) or more ("motor-
way lowering"). This lowered position improves aerodynamics and reduces fuel consumption.
"comfort" mode:
Vehicle height as in "automatic" mode, less damping at lower speeds than in "automatic"
mode, resulting in even greater driving comfort than in "automatic" mode.
There is no automatic motorway lowering.
292_005
"automatic" and "comfort" mode: Basic level
Basic level
of standard
running
gear

7
292_006
"lift" mode: + 25 mm
+ 25 mm
"lift" mode:
Vehicle level is 25 mm higher than in "automatic" mode, comfort-oriented suspension like
"automatic" mode.
292_004
"dynamic" mode: - 20 mm
- 20 mm
"dynamic" mode:
Vehicle level is 20 mm lower than in "automatic" mode. The damper map is automatically set to
sporty. After 30 seconds at speeds of 75 mph (120 km/h) or more, the car is lowered by another
5 mm ("motorway lowering").

8
Operation and display
"lift" mode:
Level 25 mm higher than "automatic" mode of sporty running gear, sporty suspension.
Sporty running gear:
"automatic" mode:
Basic vehicle level corresponds to "dynamic" mode in the standard running gear, sporty
suspension with appropriately adapted damper map (more comfortable than "dynamic"
mode). The vehicle is lowered by another 5 mm after 30 seconds at speeds of 75 mph
(120 km/h) or more ("motorway lowering").
292_049
"dynamic", "automatic" and "comfort" mode: Basic level for sporty running gear
Basic level of sporty
running gear (-20 mm)
Basic level
of standard
running
gear
292_006
"lift" mode: + 25 mm
+ 25 mm
"dynamic" mode:
Level as for "automatic" mode of sporty running gear, hard, sporty suspension with appropri-
ately adapted damper map. The vehicle is lowered by 5 mm after 30 seconds at speeds of 75
mph (120 km/h) or more ("motorway lowering").
"comfort" mode:
Level as for "automatic" mode of sporty running gear, less damping at lower speeds than in
"automatic" mode. There is no automatic motorway lowering.

9
Operation and display system
The process of switching from one mode to
another and the display/monitoring of the
system status all form part of the MMI operat-
ing system.
The adaptive air suspension menu is opened
directly in the MMI display in the centre con-
sole when the "CAR" button is pressed. This
ensures that adaptive air suspension has first
priority. This means that any other functions
already in the display are blanked out in
favour of the adaptive air suspension operat-
ing/status display.
Turning the control knob to a different mode
and then pressing the control knob activates
a new mode.
System status information can be requested
and special settings undertaken by pressing
the SETUP button.
(See current Owner’s Manual and "Control
strategy" in the "Special system states" sec-
tion.)
292_010
With the standard running gear, the
"dynamic" mode (low level) is additionally dis-
played as driver information by an indicator
lamp in the dash panel insert.
An extremely low or extremely high level is
displayed by the indicator lamp and the warn-
ing lamp in the dash panel insert.
(See "Control strategy" in "Special system
states".)
292_011
Warning
lamp
Indicator lamp for
extreme low level

10
Air supply unit
Solenoid valve block
with pressure sender
Pneumatic struts, FA
Adaptive air suspension
control unit
Vehicle level
sender, FA
Dash panel insert
Front operator/display unit
(MMI)
Body acceleration
sender
System components
Vehicle overview

11
Pneumatic struts, RA
Accumulator
Vehicle level sender, RA
Body acceleration sender
292_012

12
System components
292_013
Hardware
4E0 907 553 C * = Standard running gear
4E0 907 553 D * = Sporty running gear
Control unit J197
The control unit is the central element of the
system. It is installed in the vehicle in front of
the glove box.
It processes the relevant messages from the
other bus users, and the discreet input sig-
nals (see function diagram and CAN informa-
tion exchange).
The principal result of this processing work
are the signals to actuate the compressor, the
solenoid valves and the shock absorbers.
Because of the differences between the
standard and sporty running gears, the con-
trol unit had to be produced in two versions
(software application).
* These numbers are correct as at 06/2002. Changes may be made as a result of further
technical developments.
(See current Repair Manual.)
Software
4E0 910 553 C * = Standard running gear
4E0 910 553 D * = Sporty running gear

13
Pneumatic spring
Construction:
The pneumatic spring is encased in an alu-
minium cylinder. In order to prevent dirt from
getting between the cylinder and the air bel-
lows, the area between the piston and the cyl-
inder is sealed by a sleeve. The sleeve can be
replaced during servicing, but the air bellows
cannot be replaced separately. In the event of
a fault, the entire suspension/shock absorber
strut must be replaced.
In order to provide as much usable space and
loading width in the boot as possible, the
diameter of the rear axle pneumatic springs is
kept to a minimum. However, if demands for
comfort are to be met, a minimum air volume
is required. The solution to this conflict is pro-
vided in the form of a reservoir for additional
air, which is connected to the shock absorber.
Suspension/shock absorber strut
All four suspension/shock absorber struts are constructed in the same way.
292_015
Suspension/
shock absorber
strut, rear axle
Additional
air volume
292_014
Aluminium
cylinder
Pneumatic
spring
Suspension/
shock absorber
strut, front axle
Function:
The pneumatic spring not only replaces the
steel spring, it also offers considerable
advantages over the steel version (see
SSP 242). Encasing the pneumatic spring in
an aluminium cylinder enables the wall thick-
ness of the bellows to be reduced. This
results in an even more sensitive response to
bumpy roads.

14
292_016
System components
Shock absorber
Construction:
A twin-tube gas-filled shock absorber with
continuous electrical control is used (ccontin-
uous damping control =CDC shock absorber).
The main damping valve 3 in the piston 1 is
mechanically pre-tensioned by a spring 4. A
solenoid 5 is situated above the valve, and the
connecting cable is routed to the outside
through the hollow piston rod.
Function:
For general information on the function of a
twin-tube gas-filled shock absorber, see
SSP 242.
The damping force is determined to a consid-
erable extent by the flow resistance of the
valves. The greater the flow resistance for the
oil flowing through the valves, the higher the
damping force.
Basic method of operation using bump as an example (= bump absorption):
The entire piston unit 1 is moved downwards
inside the cylinder tube 2 at speed v.
The oil pressure in the chamber below the
main damping valve 3 increases.
Current flows to the solenoid 5. The magnetic
force FMcounteracts the spring force FFand
partially raises it.
If the sum of the magnetic force and the oil
pressure force (FM+FP) exceeds the spring
force FF
, the resulting force FRopens the
valve. The amount of magnetic force can be
regulated by adjusting the amount of electri-
cal current. The higher the electrical current,
the lower the flow resistance and thus the
damping force.
Info: The highest damping force is achieved when the solenoid is not electrically actuated.
For the lowest damping force, the solenoid must be receiving a current of approx.
1800 mA.
In emergency running mode, the solenoid is not electrically actuated. In this way, the
damping force is set to maximum, ensuring a dynamically stable driving condition.

15
Air supply unit
The air supply unit is installed at the front left of the engine compartment. This prevents any
impairment of the acoustics in the passenger compartment. Furthermore, more effective cool-
ing can be achieved. This increases the amount of time the compressor can be switched on,
and thus the quality of control.
292_017
1
2
3
4
5
67
8
9
10
11
Function:
It functions in an identical manner to the unit
used in the allroad quattro.
The unit is switched off when necessary to
prevent the compressor from overheating
(excessive cylinder head temperature). The
maximum static system pressure is 16 bar.
Components:
1. Bracket
2. Electric motor
3. Compressor
4. Air drier
5. Pneumatic exhaust solenoid valve
6. Temperature sensor
Pneumatic connections:
7. Air intake and exhaust line
8. Compressed air connection to solenoid
valve block
Electrical connections:
9. Connection to exhaust solenoid valve
10. Connection for battery voltage 12V
11. Connection for temperature sensor
Design:
The air supply unit is the same as the one
used in the allroad quattro (see SSP 243).

16
System components
Solenoid valve block
The solenoid valve block contains the pres-
sure sender and the valves for actuating the
pneumatic springs and the accumulator. It is
installed in the wheel housing between the
wheel housing liner and the left-hand
A-pillar.
Solenoid valves
Construction/function:
The construction and function of the solenoid
valves are largely the same as in the allroad
quattro (see SSP 243).
Accumulator
The accumulator is situated between the
floor of the boot and the rear silencer on the
left-hand side of the vehicle.
Construction:
The accumulator is made of aluminium.
It has a volume of 5.8l and a max. operating
pressure of 16 bar.
Function:
The objective in designing this system was to
reliably satisfy functional requirements
whilst keeping energy consumption to a min-
imum (so that the compressor is on as little
as possible). In order to enable controlled
pressure build-up to be effected solely with
the accumulator, there must be a minimum
difference in pressure of 3 bar between the
accumulator and the pneumatic springs.
Rear right 292_018
Accumulator
Front left
Pressure connection
for compressor
Front right Rear left
292_019

17
Notes

18
System components
Pneumatic diagram
292_020
Air supply unit
Solenoid valve block
1CompressorV66
2 Air drier
3a, 3b Non-return valves
4 Exhaust throttle
5 Electrical exhaust solenoid valve
N111
6 Pneumatic exhaust solenoid valve
7 Additional silencer
8Airfilter
9a Valve for strut FL N148
9b Valve for strut FR N149
9c Valve for strut RL N150
9d Valve for strut RR N151
10 Valve for accumulator N311
11 Pressure sender G291
12 Accumulator
13a Pneumatic spring FL
13b Pneumatic spring FR
13c Pneumatic spring RL
13d Pneumatic spring RR

19
Pressure build-up
Pressure reduction
The appropriate valves 9a, 9b and 9c, 9d and
the electrical exhaust solenoid valve 5 are
opened. The air can flow through the exhaust
solenoid 5 to open the pneumatic, pilot oper-
ated exhaust solenoid 6.
When the pneumatic springs are filled by the
accumulator, the valve 10 and the valves 9 for
the appropriate axle open.
The accumulator 12 is filled by the compres-
sor 1 forcing air through the open valve 10.
If the vehicle is on a sideways incline, valves
9a - 9d are also actuated individually.
The valves 9a, 9b and 9c, 9d are electrically
actuated in pairs (front axle and rear axle).
The compressor takes in the air through the
air filter 8 and the additional silencer 7.
The compressed air flows via the air drier 2,
the non-return valve 3a and the valves 9 to the
pneumatic springs.
The air leaves the system via exhaust sole-
noid 6, additional silencer 7 and air filter 8.
When air flows through the air drier 2, the
desiccant is regenerated.
292_022
292_021

20
System components
Senders (sensors)
Compressor temperature sender G290
Construction:
An NTC resistor is housed in a small glass
case.
Function:
The sender records the temperature of the
cylinder head compressor.
Its resistance decreases sharply as the tem-
perature rises (NTC: negative temperature
coefficient). This change in resistance is ana-
lysed by the control unit. The current temper-
ature calculated in each case determines the
maximum compressor running time. The
sender cannot be replaced separately during
servicing.
Pressure sender G291
Construction:
The sender is cast in the solenoid valve block
and is inaccessible from the outside.
Function:
The pressure sender measures the pressure
of the front and rear axle struts or the accu-
mulator (depending on how the solenoid
valves are actuated, see pneumatic diagram).
The G291 employs a capacitive measuring
technique:
The pressure (p) to be measured causes a
ceramic diaphragm to deflect. This deflection
changes the distance between an electrode
(1) attached to the diaphragm and a station-
ary counter-electrode (2) on the sender hous-
ing.
The electrodes together form a capacitor. The
smaller the distance between the electrodes,
the greater the capacitance of the capacitor.
This capacitance is measured by the inte-
grated electronics and converted to a linear
output signal.
292_017
Temperature sensor
292_024
P
21
This manual suits for next models
1
Table of contents
Other Audi Automobile manuals
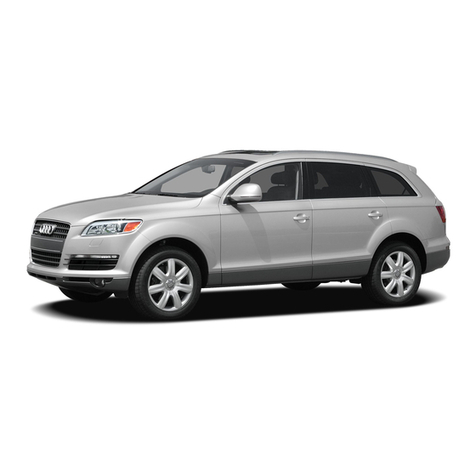
Audi
Audi Q7 2007 Operating instructions

Audi
Audi A3 Sportback g-tron User manual

Audi
Audi 2003 A8 Instruction manual

Audi
Audi RS 4 CABRIOLET User manual

Audi
Audi 1.8T User manual
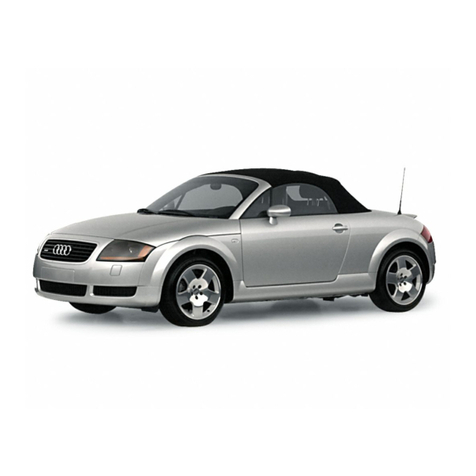
Audi
Audi TT Roadster User manual

Audi
Audi A3 CABRIOLET User manual
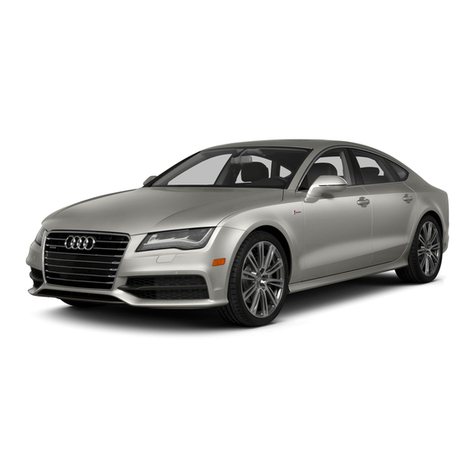
Audi
Audi A7 2013 Assembly instructions
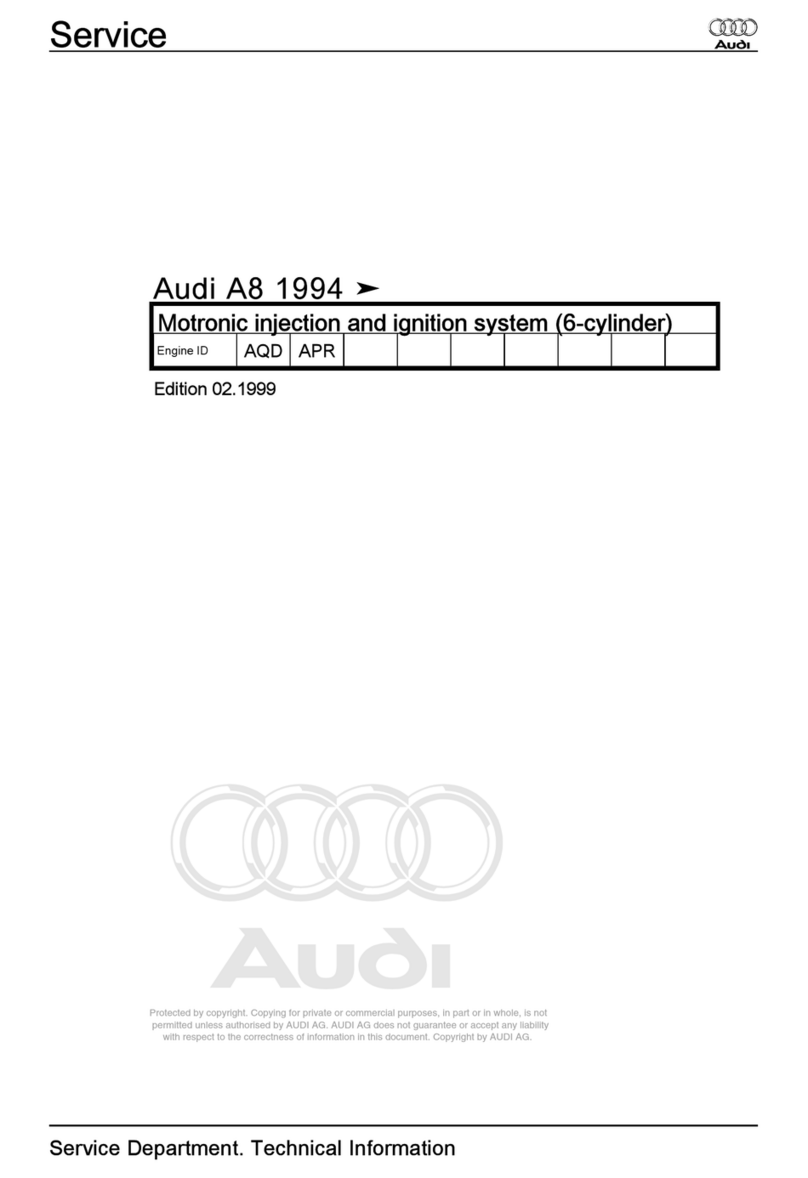
Audi
Audi A8 1994 User manual
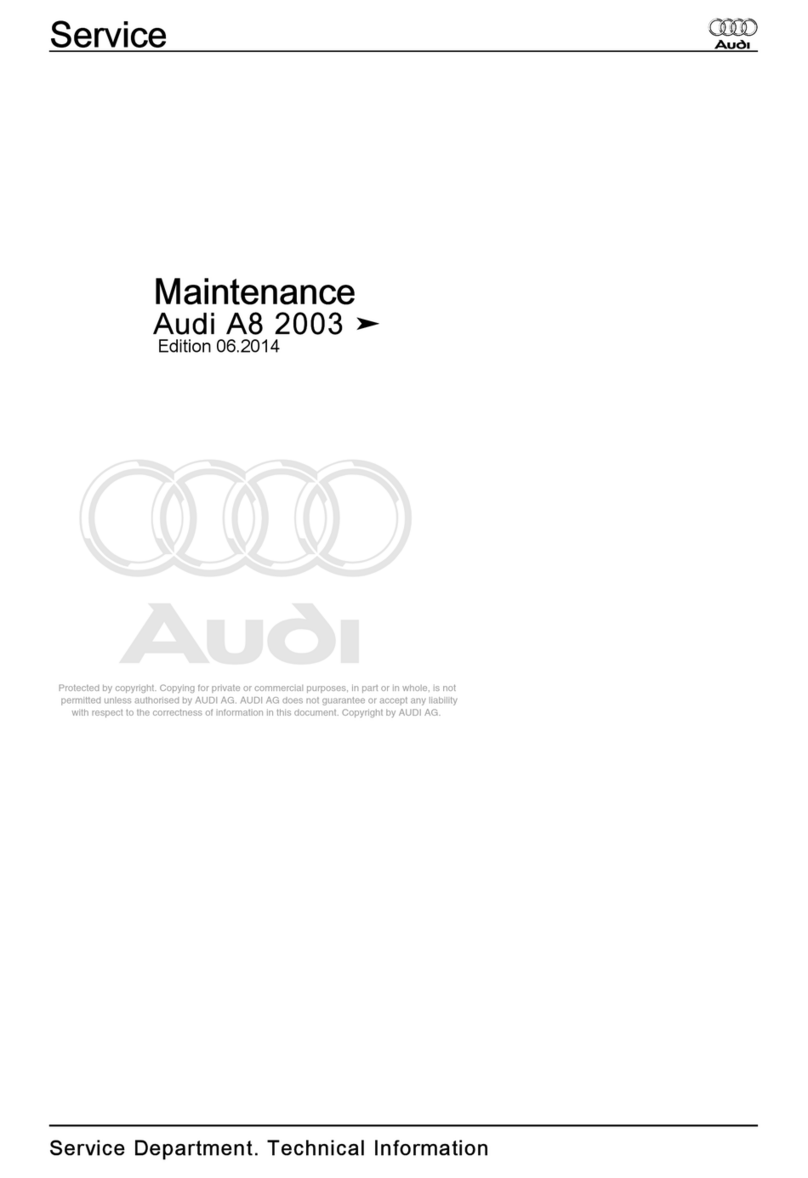
Audi
Audi 2003 A8 Guide

Audi
Audi A3 2010 User manual
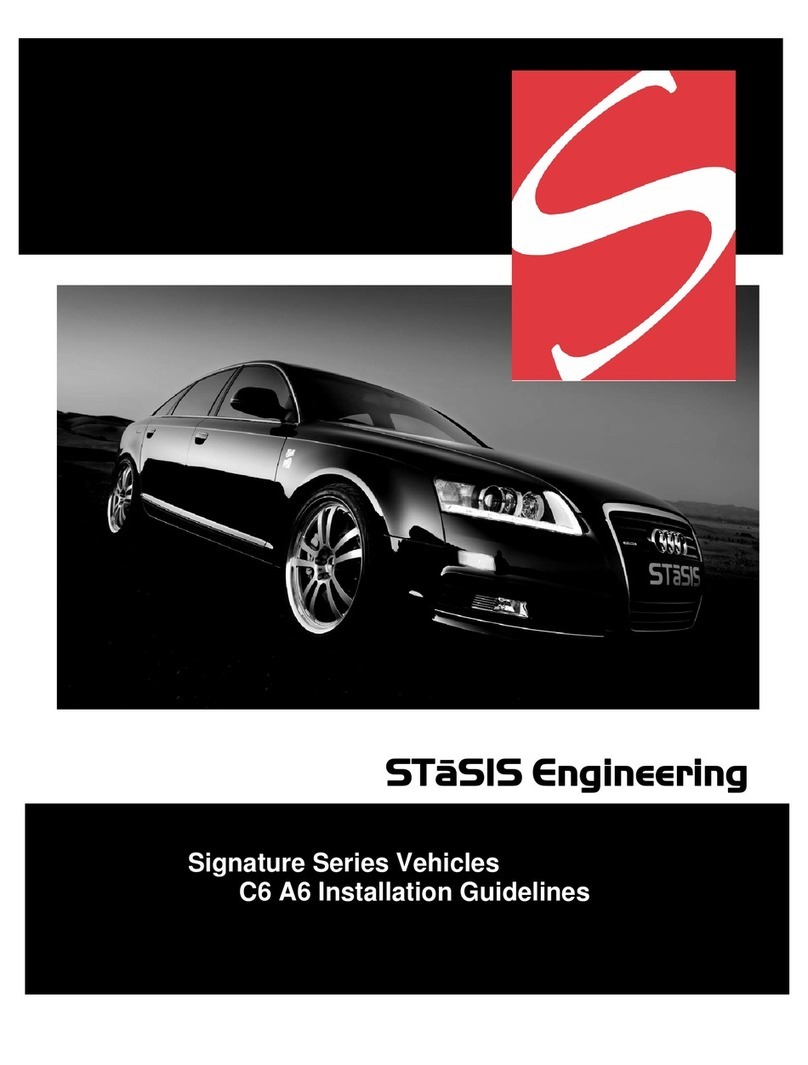
Audi
Audi ST?SIS Instruction sheet
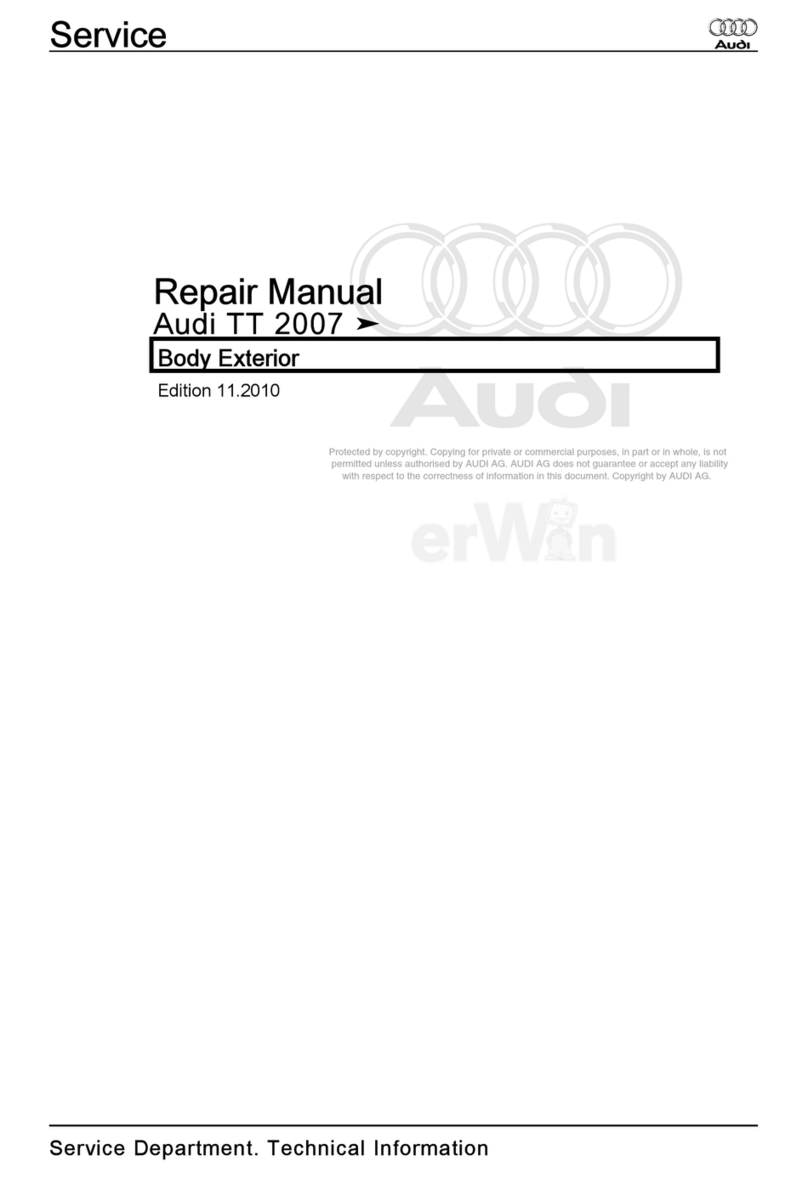
Audi
Audi TT 207 Operating instructions
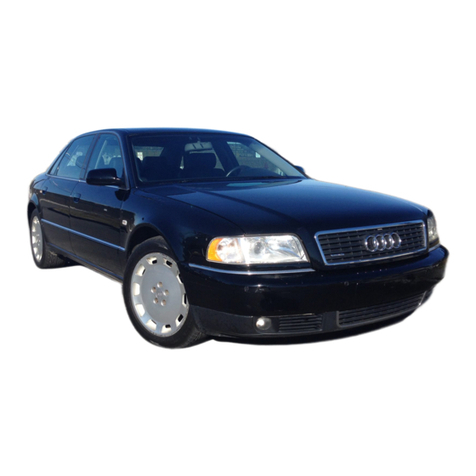
Audi
Audi A8 User manual

Audi
Audi S3 User manual
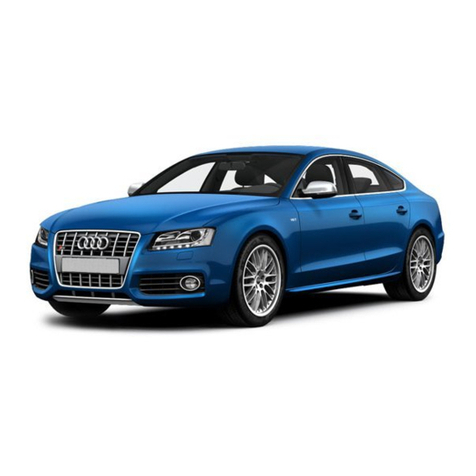
Audi
Audi S5 CABRIOLET User manual

Audi
Audi 1999 TT Operating instructions

Audi
Audi A7 Sportback 2011 Install guide
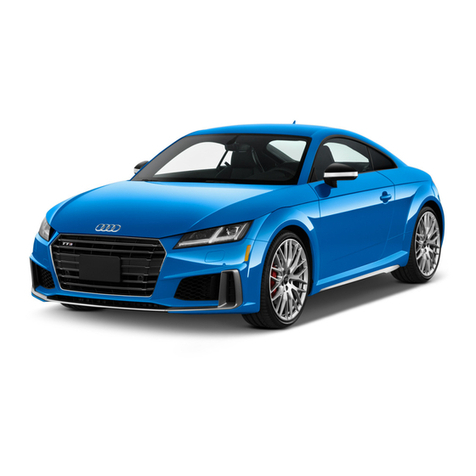
Audi
Audi TT 2019 User manual
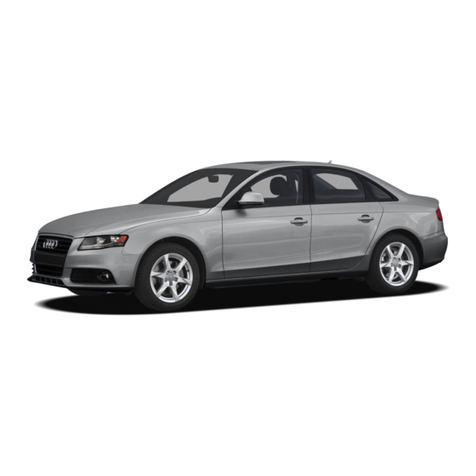
Audi
Audi A4 User manual