AUMA SG 03.3 Series User manual

Electric part-turn actuators
SG 03.3 – SG 04.3
with AUMATIC AC 01.1
Operation instructions

2
Part-turn actuators SG 03.3 – SG 04.3
with AUMATIC AC 01.1 Operation instructions
Scope of these instructions: These instructions are valid for part-turn actuators of the type range
SG 03.3 – SG 04.3 mounted with controls AUMATIC.
These instructions are only valid for “clockwise closing”, i.e. driven shaft
turns clockwise to close the valve.
Table of contents Page
1. Safety instructions 4
1.1 Range of application 4
1.2 Commissioning (electrical connection) 4
1.3 Maintenance 4
1.4 Warnings and notes 4
1.5 Further notes 4
2. Short description 4
3. Technical data 5
4. Transport and storage 7
5. Packaging 8
6. Fitting the ball handle/manual operation 8
6.1 Fitting the ball handle 8
6.2 Manual operation 8
7. Mounting to valve 8
8. Checking the end stops 9
8.1 Setting of end stop CLOSED 9
8.2 Setting of end stop OPEN 10
8.3 Setting values for mechanical end stops 10
9. Electrical connection 11
9.1 Connection with AUMA plug/socket connector 11
9.2 Heater 12
9.3 Motor protection 12
9.4 Remote position transmitter 12
9.5 Subsequent mounting of the controls 12
9.6 Type of seating 12
9.7 Fitting of the cover 12
10. Setting the limit switching 13
10.1 Setting for end position CLOSED (black section) 13
10.2 Setting for end position OPEN (white section) 14
11. Setting of mechanical position indicator 14
12. Test run 15
12.1 Check whether type of seating is set correctly 15
13. Setting of the potentiometer (option) 16
14. Setting of electronic position transmitter RWG (option) 16
14.1 Setting of 4-wire system 4 – 20 mA 17
15. Indication, operation and setting of the AUMATIC 18
15.1 Change settings 18
15.2 Password protection 18
15.3 Factory setting 18
15.4 Control and display elements 18
15.4.1 The local controls 18
15.4.2 LED indications 18

3
Part-turn actuators SG 03.3 – SG 04.3
Operation instructions with AUMATIC AC 01.1
Page
15.5 General information about the menu design 19
15.5.1 LCD contrast setting 19
15.5.2 Navigation through the indications 19
15.5.3 Group S: Status indications 20
15.5.4 Group M: Menu indications 21
15.5.5 Group D: Diagnosis indications 24
15.6 Checking for software version 24
15.7 Fieldbus interface 24
15.8 Display indications and software parameters 25
15.8.1 Status indications 25
15.8.2 Menu indications 27
15.8.3 Diagnosis indications 48
16. Operation modes and functions of the AUMATIC 51
16.1 Operation mode OFF 51
16.2 Operation mode LOCAL 52
16.3 Operation mode REMOTE 52
16.4 Operation mode EMERGENCY 52
16.5 Operation mode SAFETY 53
16.6 Signal relays 54
16.7 Stepping mode 54
16.8 Analogue position feedback 55
16.9 Type of seating 55
16.10 Push-to-run operation or self-retaining 55
16.11 Intermediate positions 56
16.12 Monitoring functions 57
16.12.1 Motor protection (thermo monitoring) 57
16.12.2 Exceeding the max. permissible number of starts or running time per hour 57
16.12.3 Operating time monitoring 58
16.12.4 Reaction monitoring 58
16.13 Running indication (blinker) 58
16.14 Logging of operating data 58
16.15 Electronic name plate 58
16.16 Release of the local controls (option) 59
17. Faults and warnings 59
17.1 Faults 59
17.2 Warnings 59
17.3 Problems with position feedback/indication E2 (from actuator) 59
17.4 LCD badly or not readable 59
17.5 Actuator does not run 59
17.6 Actuator does only operate from Local 60
17.7 Actuator is not switched off by limit seating in direction CLOSE or OPEN 60
18. Fuses 60
19. Maintenance 61
20. Disposal and recycling 61
21. Service 61
22. Part-turn actuators SG 03.3 – SG 04.3 62
23. Spare parts list AUMATIC AC 01.1 64
24. Declaration of Conformity and Declaration of Incorporation 66
Index 67
Addresses AUMA offices and representatives 68

1. Safety instructions
1.1 Range of application AUMA part-turn actuators are designed for the operation of industrial valves,
e.g. butterfly valves and ball valves.
For other applications, please consult us. The manufacturer is not liable for
any possible damage resulting from use in other than the designated
applications. Such risk lies entirely with the user.
Observance of these operation instructions is considered as part of the
controls'/actuator's designated use.
1.2 Commissioning
(electrical connection)
During electrical operation certain parts inevitably carry lethal voltages.
Work on the electrical system or equipment must only be carried out by a
skilled electrician himself or by specially instructed personnel under the
control and supervision of such an electrician and in accordance with the
applicable electrical engineering rules.
1.3 Maintenance The maintenance instructions (refer to page 61) must be observed,
otherwise a safe operation of the actuator is no longer guaranteed.
1.4 Warnings and notes Non-observance of the warnings and notes may lead to serious injuries or
damage. Qualified personnel must be thoroughly familiar with all warnings
and notes in these operation instructions.
Correct transport, proper storage, mounting and installation, as well as
careful commissioning are essential to ensure a trouble-free and safe
operation.
The following references draw special attention to safety-relevant
procedures in these operation instructions. Each is marked by the
appropriate pictograph.
This pictograph means: Note!
"Note" marks activities or procedures which have major influence on the
correct operation. Non-observance of these notes may lead to
consequential damage.
This pictograph means: Electrostatically endangered parts!
The printed circuit boards are equipped with parts which may be damaged
or destroyed by electrostatic discharges. If the boards need to be touched
during setting, measurement or for exchange, it must be assured that
immediately before a discharge through contact with an earthed metallic
surface (e.g. the housing) has taken place.
This pictograph means: Warning!
"Warning" marks activities or procedures which, if not carried out correctly,
can affect the safety of persons or material.
1.5 Further notes This pictograph means: Procedure may have been performed by valve
manufacturer!
If actuators are delivered mounted to a valve, this step has been done in the
valve manufacturer's plant.
Setting must be checked during commissioning!
2. Short description AUMA part-turn actuators type SG 03.3 – SG 04.3. have a modular design.
The actuators are driven by an electric motor and controlled with the
electronic controls AUMATIC, which are included in the scope of supply.
Manual operation is possible without change-over.
The limitation of travel is realised via limit switches in both end positions.
4
Part-turn actuators SG 03.3 – SG 04.3
with AUMATIC AC 01.1 Operation instructions
MOV
M

3. Technical data
5
Part-turn actuators SG 03.3 – SG 04.3
Operation instructions with AUMATIC AC 01.1
Application
Part-turn actuator Electrical operation of valves (e.g. butterfly valves and ball valves).
Features and functions
Type of duty (according to IEC 34-1) Short time duty S2 - 15 min
Motors Standard: 1-phase AC motor
Option: 3-phase AC motor
Insulation class F, tropicalized
Motor protection Standard: Thermoswitches
Option: PTC-thermistors
Self-locking yes
Operating times see table
Swing angle 90° (adjustable from 82° to 98°)
Type of seating by limit switching
Limit switching Counter gear mechanism for end positions OPEN and CLOSED
Standard: Single switch (1 NC and 1 NO) for each end position
Option: Tandem switch (2 NC and 2 NO) for each end position, switches galvanically
isolated
Torque switching not available
Intermediate positions (option) Electronic intermediate position switches, max. 2 switching points, adjustable
(only in combination with electronic position transmitter RWG 6020)
Position feedback signal
(options)
Precision potentiometer
Electronic position transmitter RWG 6020, 0/4 – 20 mA, voltage supply 24 V DC
Mechanical position indicator Adjustable indicator disc with symbols OPEN and CLOSED, continuous indication
Running indication (option) in combination with blinker transmitter possible
Heater in switch compartment Standard: Resistance type heater, 5 W, 24 V DC, internal supply
Manual operation Manual drive for setting and emergency operation, handwheel does not rotate during
electric operation
Handwheel lockable (option) Yes
Electrical connection
Electrical connection Standard: AUMA plug/socket connector with screw type connection
Option: Double sealed (double sealed plug/socket connector)
Threads for cable glands Standard: 1 x M20x1.5, 2 x M25x1.5
Options: Pg-threads
NPT-threads
Terminal plan 1-phase AC motor: KMS B10101100 (basic version)
3-phase AC motor: KMS A10101100 (basic version)
Valve attachment
Valve attachment Dimensions according to EN ISO 5211
Coupling Splined coupling for connection to the valve shaft,
part-turn actuator can be repositioned 4 x 90° on coupling
Standard: Coupling without bore
Options: Machined coupling with bore and keyway, square bore or bore with two-flats
Service conditions
Enclosure protection according
to EN 60 529
Standard: IP 67
Option: IP 68
Corrosion protection Standard: KN Suitable for installation in industrial units, in water- or power plants
with a low pollutant concentration4)
Options: KS Suitable for installation in occasionally or permanently aggressive
atmosphere with a moderate pollutant concentration (e.g. in
wastewater treatment plants, chemical industry)
KX Suitable for installation in extremely aggressive atmosphere with
high humidity and high pollutant concentration
Ambient temperature Standard: –25 °C to +70 °C
Finish coating Standard: two-component iron-mica combination
Standard colour AUMA silver-grey (similar to RAL 7037)
Other information
Reference documents Brochure SG 03.3 – SG 04.3
Dimension sheet SG 03.3 – SG 05.3
Electrical data SG 03.3 – SG 04.3
Table 1: Part-turn actuator SG 03.3 – SG 04.3

6
Part-turn actuators SG 03.3 – SG 04.3
with AUMATIC AC 01.1 Operation instructions
Electrical connection See page 11
Supply voltage Refer to name plate
Weight approx. 7 kg
Motor controls Reversing contactors
External supply of the AUMATIC (option) 24 V DC +20 %/–15 %,
Basic version requires approx. 200 mA/with options max. 500 mA
Voltage output 24 V DC, max. 100 mA (option: 115 V AC, max. 30 mA) (galvanically isolated from
internal voltage supply)
Digital inputs
(input signals)
OPEN - STOP - CLOSE - EMERGENCY, RELEASE 2)
Nominal voltage:
Standard: 24 V DC, current consumption: approx. 10 mA per input
Option: 115 V AC, current consumption: approx. 15 mA per input
Galvanic isolation:
Opto-isolators
Relay outputs
(signals)
see also page 30 ff
– Programmable signal relay for collective fault signal;
Standard configuration:
Phase failure (only for 3-ph AC), motor protection tripped
– 5 programmable signal relays;
Standard configuration:
End position CLOSED/end position OPEN/selector switch REMOTE
Further possible signals:
Operation CLOSE/operation OPEN/actuator runs/motor protection tripped/
selector switch LOCAL/selector switch OFF/intermediate position 1 to 4/
fault signal/not ready REMOTE/phase failure (only for 3-ph AC)
Rating of signal contacts – Signal relay for collective fault signal:
NO/NC contact max. 250 V AC, 5 A (resistive load)
– Signal relays:
Standard: potential-free NO contacts with one common:
max. 250 V AC, 1 A (resistive load)
Option: potential-free NO/NC contacts:
per relay max. 250 V AC, 5 A (resistive load)
Analogue outputs – Actual position value 3) (galvanically isolated) E2 = 0/4 – 20 mA (load max. 500 Ω)
Electronic timer 3) Start and end of stepping mode as well as ON and OFF time (1 up to 300
seconds) can be programmed individually for the directions OPEN and CLOSE.
EMERGENCY operation command Programmable for selector switch position LOCAL and REMOTE or REMOTE only:
– End position OPEN, end position CLOSED, intermediate position, stop
– By-pass of thermal protection 4)
4 electronic intermediate
positions 3) Each intermediate position can be between 0 and 100 % .
Behaviour of actuator and signal behaviour when reaching an intermediate
position adjustable.
Logging of operating data
via a resettable counter and a lifetime
counter.
– Total motor running time
– Total number of cycles
– Number of motor protection faults
Electronic name plate Order info
– Commission number
– KKS number (definition system for power plants)
– Valve number
– Plant number
Product data
– Product type
– Works number of actuator
– Works number of AUMATIC
– Software version logic, hardware version logic
–Date of final test
–Wiring diagram, terminal plan
Project data
–Project name
–2 customer fields, definable as required
1) Distance between actuator and AUMATIC max. 100 m
2) Release of the local controls (option)
3) Requires position transmitter (potentiometer or RWG) in actuator
4) Not in combination with thermistors; for thermoswitches possible on request.
Table 2: Actuator controls AUMATIC type AC 01.1
Integral controls AUMATIC type AC 01.1, for direct mounting to:
Part-turn actuators AUMA NORM SG 03.3 – SG 04.3

4. Transport and storage .Transport to place of installation in sturdy packing.
.Do not attach ropes or hooks to the handwheel for the purpose of lifting by
hoist.
.If part-turn actuator is mounted on valve, attach ropes or hooks for the
purpose of lifting by hoist to valve and not to part-turn actuator.
.Store in well-ventilated, dry room.
.Protect against floor dampness by storage on a shelf or on a wooden
pallet.
.Cover to protect against dust and dirt.
.Apply suitable corrosion protection agent to bright surfaces.
If part-turn actuators are to be stored for a long time (more than 6 months),
the following points must be observed additionally:
.Prior to storage: Protect bright surfaces, in particular the output drive parts
and mounting surface, with long-term corrosion protection agent.
.Check for corrosion approximately every 6 months. If first signs of
corrosion show, apply new corrosion protection.
After mounting, connect part-turn actuator immediately to electrical mains,
so that condensation is prevented by the heater.
7
Part-turn actuators SG 03.3 – SG 04.3
Operation instructions with AUMATIC AC 01.1
Service data
–Service phone
–Internet address
–Service text
Monitoring and safety
functions
–Monitoring of the motor temperature (motor protection)
–Reaction monitoring (programmable)3)
–Operating time (programmable)
–Max. running time per hour (programmable)
– Max. cycles per hour (programmable)
– Internal diagnosis:
- Control of motor controls
- Sub-assembly monitoring
Profibus DP interface (option) Profibus DP according to EN 50170
– 2 analogue and 4 digital customer inputs, internal supply (24 V DC/max.
100 mA) via power supply unit of the AUMATIC possible (see "voltage output")
– Programmable process representation
– Profibus DP (V1) (option)
– Fibre optic connection (option)
– Redundant fibre optic connection (option)
– Overvoltage protection (option)
– Redundancy: 2 separate bus interfaces in the AUMATIC (option)
For complete description see "Technical data actuator controls AUMATIC with
Profibus DP interface".
Modbus interface (option) – 2 analogue and 4 digital customer inputs, internal supply (24 V DC/max.
100 mA) via power supply unit of the AUMATIC possible (see "voltage output")
– Overvoltage protection (option)
– Redundancy: 2 separate bus interfaces in the AUMATIC (option)
– For complete description see "Technical data actuator controls AUMATIC with
Modbus interface".
Setting/programming – Via menu and the push buttons and display of the local controls
(password-protected)
– Via the programming software COM-AC (option)
– Illuminated LC display, 4 lines with 20 characters each, plain text display
Local controls – Selector switch LOCAL-OFF-REMOTE, lockable
– Push buttons OPEN-STOP-CLOSE-RESET
– Illuminated LC display, 4 lines with 20 characters each, plain text display
– Indication lights (programmable):
Standard configuration:
End position CLOSED (yellow), torque fault CLOSE5) (red), motor protection
tripped (red), torque fault OPEN5) (red), end position OPEN (green)
– Running indication: Blinking indication lights OPEN/CLOSE
Ambient temperature Refer to Technical Data Part-turn actuator
Enclosure protection acc. to EN 60529 Standard IP 67; Option: IP 68
3) Requires position transmitter (potentiometer or RWG) in actuator.
5) Not available

5. Packaging Our products are protected by special packaging for the transport ex works.
The packaging consists of environmentally friendly materials which can
easily be separated and recycled.
For the disposal of the packaging material we recommend recycling and
collection centres.
We use the following packaging materials:
Wooden material boards (OSB)/cardboard/paper/PE film
6. Fitting the ball handle/manual operation
To avoid damage during transport, the ball handles are fitted to the inside of
the handwheel. Prior to commissioning, the ball handle has to be fitted in
the correct position.
6.1 Fitting the ball handle .Remove cap nut.
.Pull out ball handle and re-insert in
correct position.
.Fasten with cap nut.
.Remove sticker from the hand wheel for
fitting the ball handle.
6.2 Manual operation Manual operation is activated by turning the handwheel. A change-over is
not required. The handwheel does not rotate during motor operation.
Turning the handwheel during motor operation results in
an extension or reduction of the operating time, depending
on the direction of rotation.
7. Mounting to valve .Prior to mounting the part-turn actuator must be checked
for any damage.
.Damaged parts must be replaced by original spare parts.
.After mounting to valve, touch up any possible damages
to paint finish.
.For butterfly valves the recommended mounting position is end position
CLOSED.
(Prior to mounting, bring the part-turn actuator to the mechanical end stop
CLOSED by turning the handwheel clockwise).
.For ball valves the recommended mounting position is end position
OPEN. (Prior to mounting, bring the part-turn actuator to the mechanical
end stop OPEN by turning the handwheel counter-clockwise).
.Thoroughly degrease mounting faces of part-turn actuator and valve.
.Place coupling sleeve on to valve shaft and secure
(refer to figure A2, detail A or B), ensure that dimensions X, Y and Z are
observed (refer to table 3).
.Apply non-acidic grease at splines of coupling.
.Fit actuator so that fixing holes in actuator and valve mounting flange are
in alignment.
If necessary, move actuator up or down one tooth on the coupling.
If required, turn handwheel a little in direction OPEN or CLOSE until holes
align to the threads.
.Ensure that the spigot (if provided) mates uniformly in the recess and that
the mounting faces are in complete contact.
.Fasten the actuator with bolts of minimum quality 8.8 using lock washers.
Fasten bolts crosswise to the appropriate torque according to table 3.
8
Part-turn actuators SG 03.3 – SG 04.3
with AUMATIC AC 01.1 Operation instructions
2
1
3
4
Figure A1
Ball handle
Cap nut
MOV
M

8. Checking the end stops
This check can only be performed on valves which are not yet mounted into
a pipeline.
8.1 Setting of end stop CLOSED .Check whether mechanical end position of the valve corresponds to the
mechanical end stop of actuator by turning at handwheel (clockwise for
end position CLOSED)
.If necessary, remove screw plug (22.1, figure B1) and adjust mechanical
end stop at hex. socket head cap screw (21.1, figure B3). Turning
clockwise results in smaller, turning counter-clockwise results in larger
swing angles.
.Never remove the screws (21.2, figure B2 and 21.1,
figure B3) completely, because this will cause oil leakage.
.Observe dimension Tmin. (subclause 8.3).
.Check O-ring in screw plug and replace if damaged.
.Replace and fasten screw plug (22.1, figure B1).
9
Part-turn actuators SG 03.3 – SG 04.3
Operation instructions with AUMATIC AC 01.1
Figure B1
22.2 22.1
Type X max Y max Z max 8.8 TA[Nm]
SG 03.3/04.3-F04 10 0 37 4 x M 5 6
SG 03.3/04.3-F05 8 2 35 4 x M 6 11
SG 03.3/04.3-F07 8 2 35 4 x M 8 25
Table 3
MOV
M
A
X
B
Z
Y
Figure A2
Coupling
Valve
Grub screw

8.2 Setting of end stop OPEN The swing angle has been set in the factory to approx. 90° or to the swing
angle stated in the order. An adjustment might be necessary if the end stop
CLOSED has been re-adjusted.
.Check whether mechanical end position of the valve corresponds to the
mechanical end stop of actuator by turning at handwheel
(counter-clockwise for end position OPEN)
.If necessary, remove screw plug (22.2, figure B2) and adjust mechanical
end stop at hex. socket head cap screw (21.2, figure B2).
.Check O-ring in screw plug and replace if damaged.
.Replace and fasten screw plug (22.2).
8.3 Setting values for mechanical end stops
10
Part-turn actuators SG 03.3 – SG 04.3
with AUMATIC AC 01.1 Operation instructions
TT min.
Tmin.
T
Fig. B4: (top view) Fig. B5: (top view)
MOV
M
Fig. B2: Setting end position OPEN Fig. B3: Setting end position CLOSED
(top view) (top view)
21.2
22.2 22.1
21.1

The limitation of travel is realised via limit switches
(page 13) in both end positions. For this reason the end
stops of the actuator have to be set to a slightly larger swing
angle (approx. by 2° larger) than the swing angle actually
required by the valve.
9. Electrical connection Work on the electrical system or equipment must only be
carried out by a skilled electrician himself or by specially
instructed personnel under the control and supervision of
such an electrician and in accordance with the applicable
electrical engineering rules.
AUMA part-turn actuators SG are operated via the controls AUMATIC
AC 01.1. The controls may either be mounted directly to the actuator or to a
separate wall bracket.
When installing the AUMATIC on a wall bracket, observe the following points:
.For the connection of actuator and AUMATIC on wall bracket, use suitable
flexible and screened connecting cables.
(Connecting cables are available on request, see address list page 68).
.The max. permissible cable length between actuator and the controls
AUMATIC is 100 m.
9.1 Connection with AUMA plug/socket connector
.Check whether type of current, supply voltage and frequency correspond
to motor data (refer to name plate at motor/AUMATIC).
.Loosen bolts (26.01) (figure C2) and remove plug cover (26.0).
.Loosen screws (26.2.5) and remove socket carrier (26.2) from plug cover
(26.0).
.Insert cable glands suitable for connecting cables.
.Enclosure protection IP 67 or IP 68 is only ensured if
suitable cable glands are used.
.Seal cable entries which are not used with suitable plugs.
11
Part-turn actuators SG 03.3 – SG 04.3
Operation instructions with AUMATIC AC 01.1
Fig.C1 Wall bracket (accessory)
Connecting cables to actuator
Fig. C2: Connection
26.0
26.01
26.2
26.2.5
Basic factory setting for 90° swing angle:
Swing angle 1) SG 03.3/SG 04.3
Dimension T (factory setting) mm 13.5
Dimension Tmin.2) mm 9
1) By turning at the hex. socket head cap screw for end stop CLOSED or OPEN the end
position changes accordingly.
The swing angle can be checked and set by using the dimension T.
2) If Tmin. is not reached, the gearing might be damaged.
For each turn of the hex. socket head cap screw, the setting of the end
position changes by:
for clockwise turn approx.: 3.3°
for counter-clockwise turn approx.: 2.4°

.Connect cables according to order related wiring diagram ACP . . . . The
wiring diagram applicable to the actuator is attached to the handwheel in
a weather-proof bag, together with the operation instructions. In case the
wiring diagram is not available, it can be obtained from AUMA (state
commission no., refer to name plate) or downloaded directly from the
Internet (see page 67).
A special parking frame for protection against touching the bare contacts
and against environmental influences is available (see address list page 68).
9.2 Heater AUMA part-turn actuators have a heater installed as standard. Unless
ordered otherwise, the heater is internally supplied.
9.3 Motor protection In order to protect the motor against overheating a thermoswitch is
embedded in the motor windings. The controls AUMATIC switch off the
motor as soon as the max. permissible windings temperature is reached.
The switch is connected again automatically after the motor has cooled
down to a temperature of approx. 90 °C Afterwards the actuator can be
switched on again.
9.4 Remote position transmitter For the connection of position transmitters (potentiometer, RWG) screened
cables must be used.
9.5 Subsequent mounting of the controls
To avoid malfunctions we recommend that in case of
subsequent mounting of the AUMATIC on the actuator the
electrical interfaces are checked for compatibility.
9.6 Type of seating The limitation of travel is realised via limit switches in both end positions.
A torque sensor is not available.
A torque seating is not permissible. The set type of seating
can be checked via the parameters "OPEN POSITION" and
"CLOSED POSITION" (page 27).
For further information regarding the type of seating see also page 55,
subclause 16.9.
9.7 Fitting of the cover .After completion of the power supply connection, insert the socket carrier
(26.2), see figure C2, page 11, into the plug cover (26.0) and fasten it with
screws (26.2.5).
.Clean sealing faces at plug cover (26.0) and check whether O-ring is in
good condition. Apply a thin film of non-acidic grease (e.g. Vaseline) to the
sealing faces.
.Replace plug cover (26.0) and fasten 4 bolts (26.01) evenly crosswise.
12
Part-turn actuators SG 03.3 – SG 04.3
with AUMATIC AC 01.1 Operation instructions
MOV
M
Technical data Motor power connections1) Protective earth Control pins
No. of contacts max. 6 (3 are used) 1 (leading contact) 50 pins/sockets
Marking U1, V1, W1, U2, V2, W2 according to VDE 1 to 50
Voltage max. 750 V – 250 V
Current max. 25 A – 16 A
Type of customer connection Screws Screw for ring lug Screws
Cross section max. 6 mm26 mm22.5 mm2
Material:Pin/socket carrier Polyamide Polyamide Polyamide
Contacts Brass (Ms) Brass (Ms) Brass, tin plated or gold plated
(option)
1) Suitable for copper wires. For aluminium wires contact AUMA.
Table 4: Technical data AUMA plug/socket connector
Fig. C3: Parking frame (accessory)
Parking frame

.Fasten cable glands firmly to ensure required enclosure protection.
10. Setting the limit switching .Take off cover at switch compartment.
.Pull off indicator disc (figure D). Open end spanner (approx. 14 mm) may
be used as lever.
These operation instructions are only valid for "clockwise closing", i.e. driven
shaft turns clockwise to close the valve.
10.1 Setting for end position CLOSED (black section)
.Turn handwheel clockwise until valve is closed.
.Turn handwheel approx. 1 turn in direction OPEN and then half a turn in
direction CLOSED.
.Press down and turn setting spindle A (figure E1) with screw driver
(5 mm) in direction of arrow, thereby observe switch cam B. While a
ratchet is felt and heard, the switch cam B moves 90° every time. When
switch cam B is 90° from the switch, continue turning slowly.
When the switch cam B snaps and trips the switch, stop turning and
release setting spindle.
If you override the tripping point inadvertently (ratchet is heard after the
switch cam has snapped), continue turning the setting spindle in the same
direction and repeat the setting process.
13
Part-turn actuators SG 03.3 – SG 04.3
Operation instructions with AUMATIC AC 01.1
Figure D: Removing the indicator disc
Indicator disc
MOV
M
Fig. E1
AD
E
B

10.2 Setting for end position OPEN (white section)
.Turn handwheel counter-clockwise until valve is open.
.Turn handwheel approx. 1 turn in direction CLOSE and then half a turn in
direction OPEN.
.Press down and turn setting spindle D (figure E1) with screw driver (5
mm) in direction of arrow, thereby observe switch cam E. While a ratchet
is felt and heard, the switch cam E moves 90° every time. When switch
cam E is 90° from the switch, continue turning slowly.
When the switch cam E snaps and trips the switch, stop turning and
release setting spindle.
If you override the tripping point inadvertently (ratchet is heard after the
switch cam has snapped), continue turning the setting spindle in the same
direction and repeat the setting process.
11. Setting of mechanical position indicator
.Place indicator disc on shaft.
.Move valve to end position CLOSED.
.Turn lower indicator disc (figure E2) until symbol CLOSED is in
alignment with the mark on the cover (figure E3).
.Move actuator to end position OPEN.
.Hold lower indicator disc in position and turn upper disc with symbol
OPEN until it is in alignment with the mark on the cover.
Indicator disc rotates approximately 90° at full travel from OPEN to CLOSED
or vice versa.
If no optional components (clauses 13. to 15.) require setting:
.Clean sealing faces at cover and housing; check whether O-ring is in good
condition. Apply a thin film of non-acidic grease to the sealing faces.
.Replace cover on switch compartment and fasten bolts evenly crosswise.
14
Part-turn actuators SG 03.3 – SG 04.3
with AUMATIC AC 01.1 Operation instructions
Fig. E2
Indicator disc
Fig. E3: Switch compartment cover
Mark

12. Test run
12.1 Check whether type of seating is set correctly (see page 55, subclause 16.9)
Switching off in the end positions must be by limit seating.
The type of seating can be set separately for direction CLOSE and
direction OPEN.
.Set selector switch to position OFF (0), figure G1.
.Select status indication S0:
Press push button briefly, if necessary several times.
Push x times briefly
until S0 appears
Check if end positions of the limit switching are set correctly:
.Engage manual operation as described under clause 6.2 on page 8.
.Move actuator manually to the respective end position.
End position CLOSED reached: LED yellow: illuminated
Indication in display: CLOSED POSITION
End position OPEN reached: LED green: illuminated
Indication in display: OPEN POSITION
The LED signals described here are standard settings. Deviating from this,
individual LED's can also signal another information (see page 18)
.If the end positions are not set correctly, the limit switching must be set
anew, as described on page 13.
When end positions are set correctly, perform a test run in motor operation,
as described below.
.Set selector switch (figure G3) to position LOCAL (I).
.Operate actuator with push buttons
OPEN - STOP - CLOSE
.
Actuator runs in direction CLOSE: LED yellow: blinking
Indication in display: RUNNING CLOSE
End position CLOSED reached: LED yellow: illuminated
Indication in display: CLOSED POSITION
Actuator runs in direction OPEN: LED green: blinking
Indication in display: RUNNING OPEN
End position OPEN reached: LED green: illuminated
Indication in display: OPEN POSITION
15
Part-turn actuators SG 03.3 – SG 04.3
Operation instructions with AUMATIC AC 01.1
C
Figure G1
CLOSED (yellow) OPEN (green)
OFF
Figure G2
Figure G3

13. Setting of the potentiometer (option)
For a position feedback from the actuator a potentiometer is
required.
.Move valve to end position CLOSED.
.Take off cover at switch compartment.
.Pull off indicator disc.
.Turn potentiometer (R) counter-clockwise until stop is felt. End position
CLOSED corresponds to 0 %, end position OPEN to 100 %.
.Turn potentiometer (R) slightly back from the stop.
.Perform fine-tuning of the zero point at external setting potentiometer (for
remote indication).
.Press indicator disc on shaft and perform setting as described on page
14, clause 11.
.Clean sealing faces at cover and housing; check whether O-ring is in good
condition. Apply a thin film of non-acidic grease to the sealing faces.
.Fit and fasten switch compartment cover.
14. Setting of electronic position transmitter RWG (option)
– For an AUMATIC on wall bracket –
After mounting the part-turn actuator to the valve, check setting by
measuring the output current (see subclause 14.1) and re-adjust, if
necessary.
16
Part-turn actuators SG 03.3 – SG 04.3
with AUMATIC AC 01.1 Operation instructions
Figure H
R
Terminal plans KMS _ _ _ _ R _/_ _
4-wire system
Output current Ia4 – 20 mA
Supply voltage Uv24 V DC, ± 15 %
smoothed
Max. input current I 25 mA at 20 mA
output current
Max. load RB600 Ω
Table 5: Technical data RWG 6020
MOV
M

14.1 Setting of 4-wire system 4 – 20 mA .Connect voltage for electronic position transmitter.
.Move valve to end position CLOSED.
.Take off cover at switch compartment.
.Pull off indicator disc.
.Connect ammeter for 0 – 20 mA to measuring points
(MP1/MP2) (figure J).
The circuit (external load) must be connected (observe
max. ext. load RB), or the appropriate poles at the AUMA
plug/socket connector must be linked (refer to terminal
plan), otherwise no value can be measured.
.Turn potentiometer (R, figure H) counter-clockwise until stop is felt.
.Turn potentiometer (R) slightly back from the stop.
.Turn trimmer potentiometer (R6 - "0") clockwise until output current starts
to increase.
.Turn back potentiometer (R6 - "0") until a residual current of approx.
0.1 mA is reached.
.Move valve to end position OPEN.
.Set trimmer potentiometer (R5 - "max.") to end value 16 mA.
.Move valve to end position CLOSED.
.Set potentiometer (R5 - "max.") from 0.1 mA to initial value 4 mA.
This results in a simultaneous shift of the end value by 4 mA, so that the
range is now 4 – 20 mA.
.Approach both end positions anew and check setting. If necessary, correct
the setting.
.Press indicator disc on shaft and perform setting as described on page
14, clause 11.
.Clean sealing faces at cover and housing; check whether O-ring is in good
condition. Apply a thin film of non-acidic grease to the sealing faces.
.Replace cover on switch compartment and fasten bolts evenly crosswise.
17
Part-turn actuators SG 03.3 – SG 04.3
Operation instructions with AUMATIC AC 01.1
Figure J
R6 “0”
MP1 (–)
R5 “max”
MP2 (+)

15. Indication, operation and setting of the AUMATIC
The setting of the AUMATIC is done with the push buttons of the local
controls (figure Q1).
15.1 Change settings To change the settings, the following steps are required:
1) Set selector switch (figure Q1) to position OFF.
2) Press push button and hold it for approx. 2 seconds until the group M0
appears (see also page 21).
3) Make selection: e.g. M0 "LANGUAGE/CONTRAST" and confirm selection
with .
15.2 Password protection The settings of the AUMATIC are password-protected. In the factory, the
following password is set: 0000. If necessary, the password can be changed
(enter password: page 22; change password: page 36).
15.3 Factory setting During the function test the AUMATIC is set according to the customer's
requirements and its details (comm. no., date of final test....) are stored in
the EEPROM (non-volatile memory) as factory settings. The AUMATIC can
always be reset to these factory settings (see "FACTORY SETTING",
page 47).
15.4 Control and display elements
15.4.1 The local controls The push buttons on the local controls (figure Q1) have two functions,
depending on the selector switch position:
.Selector switch in position LOCAL:
Run commands OPEN - STOP - CLOSE and Reset
.Selector switch in position OFF:
Indication and change of parameters,
indication of status and diagnosis information
.Selector switch in position REMOTE :
Indication of parameters,
indication of status and diagnosis information
15.4.2 LED indications Five local LEDs (figure Q2) indicate different signals (see page 28,
Parameter LED1 to LED 5 LOCAL CONTROLS.).
18
Part-turn actuators SG 03.3 – SG 04.3
with AUMATIC AC 01.1 Operation instructions
C
Selector switch: LOCAL-OFF-REMOTE
Push-buttons:
Function for Function
selector switch for selector switch
in position LOCAL: in position OFF and REMOTE:
OPEN scroll/ change values
STOP scroll/ change values
CLOSE confirm selection
Reset C Escape
Figure Q1: Local controls
LED V1
(yellow)
is illuminated Actuator is in end position CLOSED
is blinking Actuator runs in direction CLOSE (can be swit-
ched on or off via parameter “BLINKER” page 28)
LED V2
(red)
is illuminated Torque fault CLOSED1) (max. set torque was ex-
ceeded before reaching the end position)
LED V3
(red)
is illuminated Motor protection tripped
LED V4
(red)
is illuminated Torque fault OPEN1) (max. set torque was excee-
ded before reaching the end position)
LED V5
(green)
is illuminated Actuator is in end position OPEN
is blinking Actuator runs in direction OPEN (can be switched
on or off via parameter “BLINKER” page 28)
1) not available
Figure Q2

Lamp test After the supply voltage is connected a function test of the LEDs is
automatically performed. All 5 LEDs must be illuminated for at least
3 seconds.
15.5 General information about
the menu design
The indications on the display are divided into 3 main groups:
1) group S= Status indications, 15.5.3
2) group M= Menu indications, see 15.5.4
3) group D= Diagnosis indications, see 15.5.5
In the upper right corner of the display the group in which one is moving is
indicated. See example figure S1, page 20: Group S= Status indications
15.5.1 LCD contrast setting .Either: Change setting via menu "LANGUAGE/CONTRAST" (see "Change
settings" below)
.Or: Press button in the status page S0 and hold it. After approx. 10 s
(the above mentioned menus - groups S,M,D- are hereby skipped) the
brightness of the LCD display continuously changes from bright to dark
and vice versa. When the button is released, the current brightness level
is saved under "CONTRAST".
15.5.2 Navigation through the indications
(Selector switch in position OFF or REMOTE)
Scrolling within a group: .To scroll within a group (see subclause 15.5):
Press push button "scroll" , . The triangles in the display show
the direction of the scrolling.
Confirm selection: .To reach a new menu or a subgroup:
Load the new selection with the push button "Confirm selection" .
Select group S,Mor D: After the AUMATIC is switched on, the status indication S0 is shown on the
display.
.Change from the group S(Status indications S0,S1,S2,S3) to the
group M(Menu indications):
Press and hold it for approx. 2 seconds until the group M0 appears.
.Change from the group S(Status indications S0,S1,S2,S3) to the
group D(Diagnosis indications):
Press and hold it until the group D0 appears (menu indications M are
skipped).
.Change from any group Mor Dback to the group S0:
Press push button briefly.
Show settings: .Set selector switch to position OFF or REMOTE.
.Select group M0.
.Make selection: e.g. M0 "LANGUAGE/CONTRAST" and
confirm selection with .
."Select "VIEW" and confirm with .
Change settings: .Set selector switch to position OFF.
.Select group M0.
.Make selection: e.g. M0 "LANGUAGE/CONTRAST" and
confirm selection with .
."Select "EDIT" and confirm with .
.Enter password (see page 22 ).
.Change value.
Cancel process/back: .To cancel a process or to go back to the previous indication:
Press push button .
19
Part-turn actuators SG 03.3 – SG 04.3
Operation instructions with AUMATIC AC 01.1
C
C
C
C
C

15.5.3 Group S: Status indications The status indications (group S) show the current operation mode
(see also page 51, clause 16.).
Status page S0 (figure S1-0): .Line 1 shows the current operation mode (page 51, clause 16.).
.Line 2 shows the current run commands which are transmitted to the
actuator via the local controls (push buttons) or via REMOTE.
.Line 3 shows the actuator position in % of the travel (0 % = actuator is in
end position CLOSED, 100 % = Actuator is in end position OPEN). Is only
indicated if a position transmitter (potentiometer or RWG) is installed in
the actuator.
.Line 4 shows the current status of the actuator, example: "OPEN
POSITION" = Actuator is in end position OPEN, "RUNNING OPEN" =
Actuator runs in position OPEN.
For further information regarding status
page S0 see page 25.
Status page S1 (figure S1-1): .Faults are indicated here.
For further information
regarding status page S1 see
page 26.
Faults interrupt or prevent an operation
(see pages 25,26 and 59).
20
Part-turn actuators SG 03.3 – SG 04.3
with AUMATIC AC 01.1 Operation instructions
OFF S0
RUNNING OPEN
S1
S2
FAULT IND.
NO FAULT
WARNING IND.
NO WARNING
E2 100%
S3NOT READY IND.
READY
Figure S1: Overview status indications
OFF S0
RUNNING OPEN
E2 100%
Line 3: Actuator position
Line 1:
O
peration mode
Line 4: Actuator status
Line 2: Run commands
Figure S1-0
S1FAULT IND.
NO FAULT
Other manuals for SG 03.3 Series
1
This manual suits for next models
1
Table of contents
Other AUMA Controllers manuals
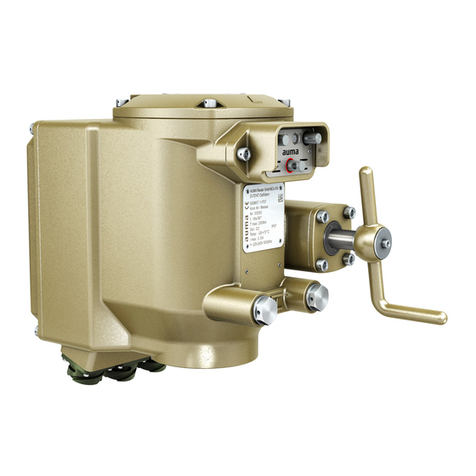
AUMA
AUMA SGM 04.1 User manual
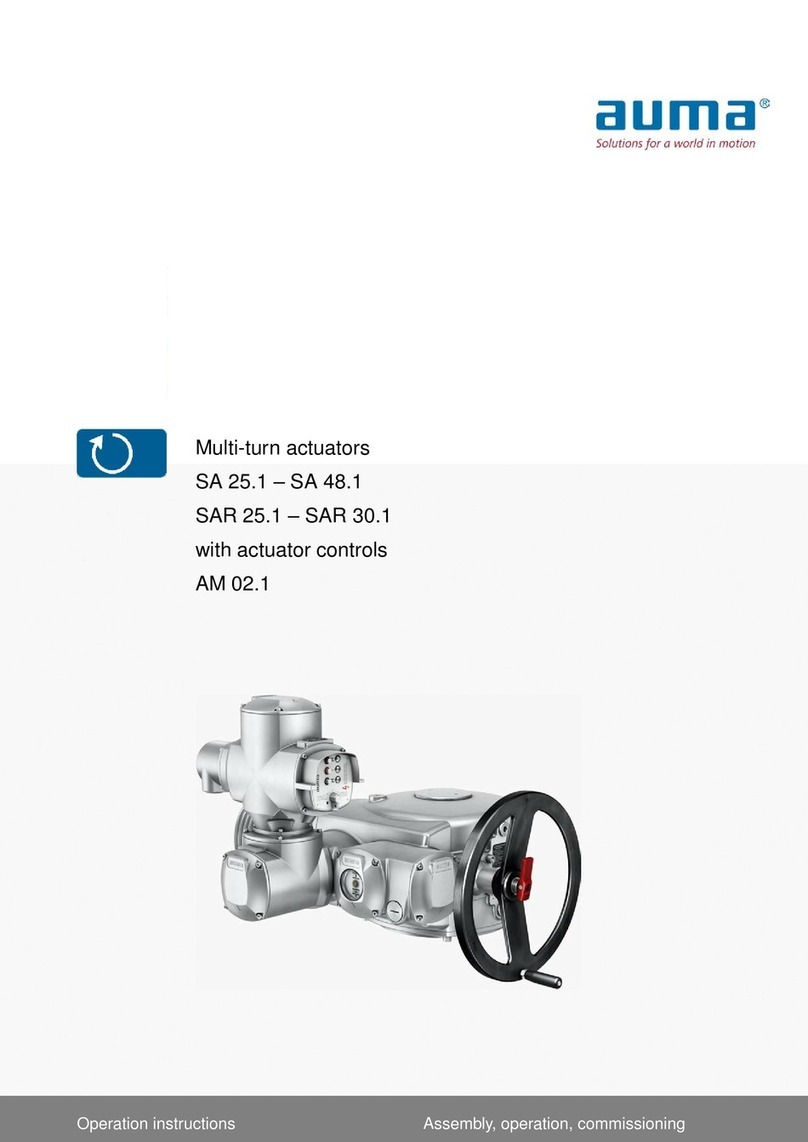
AUMA
AUMA SA 48.1 SAR 25.1 User manual
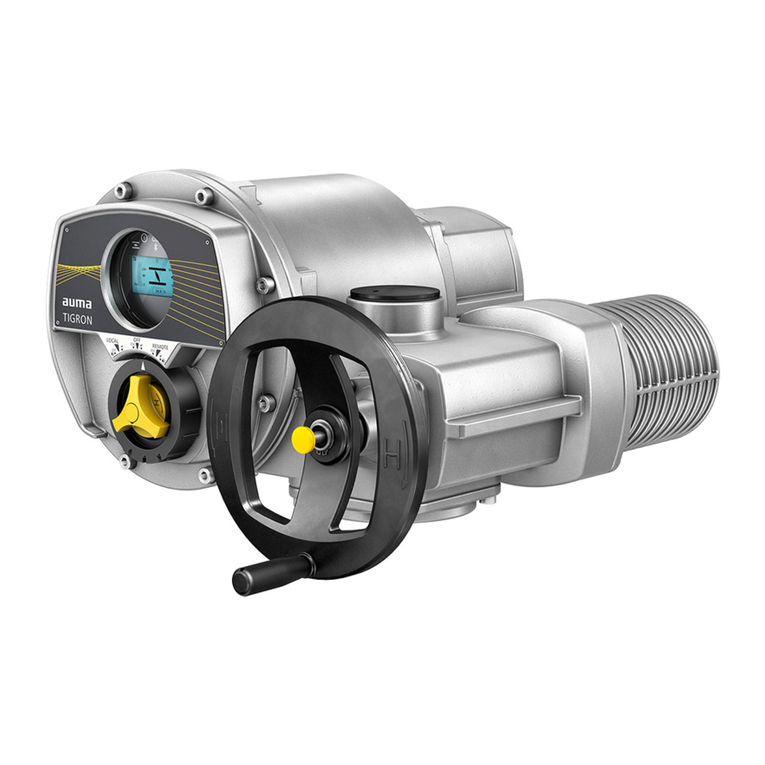
AUMA
AUMA TIGRON TR-M30X Manual
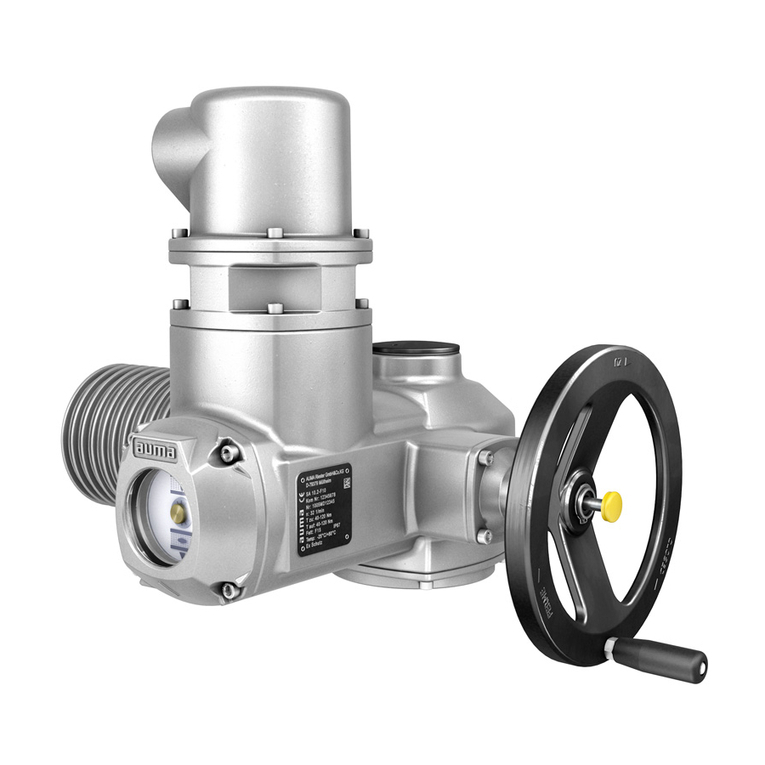
AUMA
AUMA SAEx 07.2 User manual
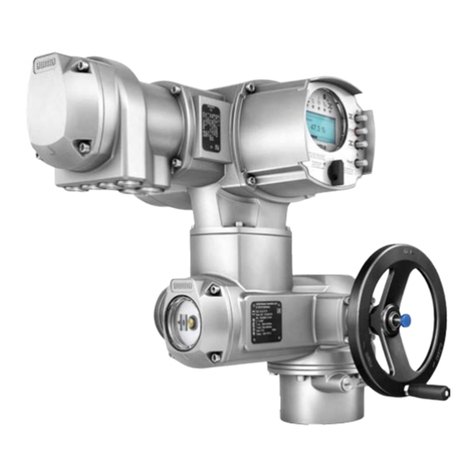
AUMA
AUMA SQ 05.2 User manual
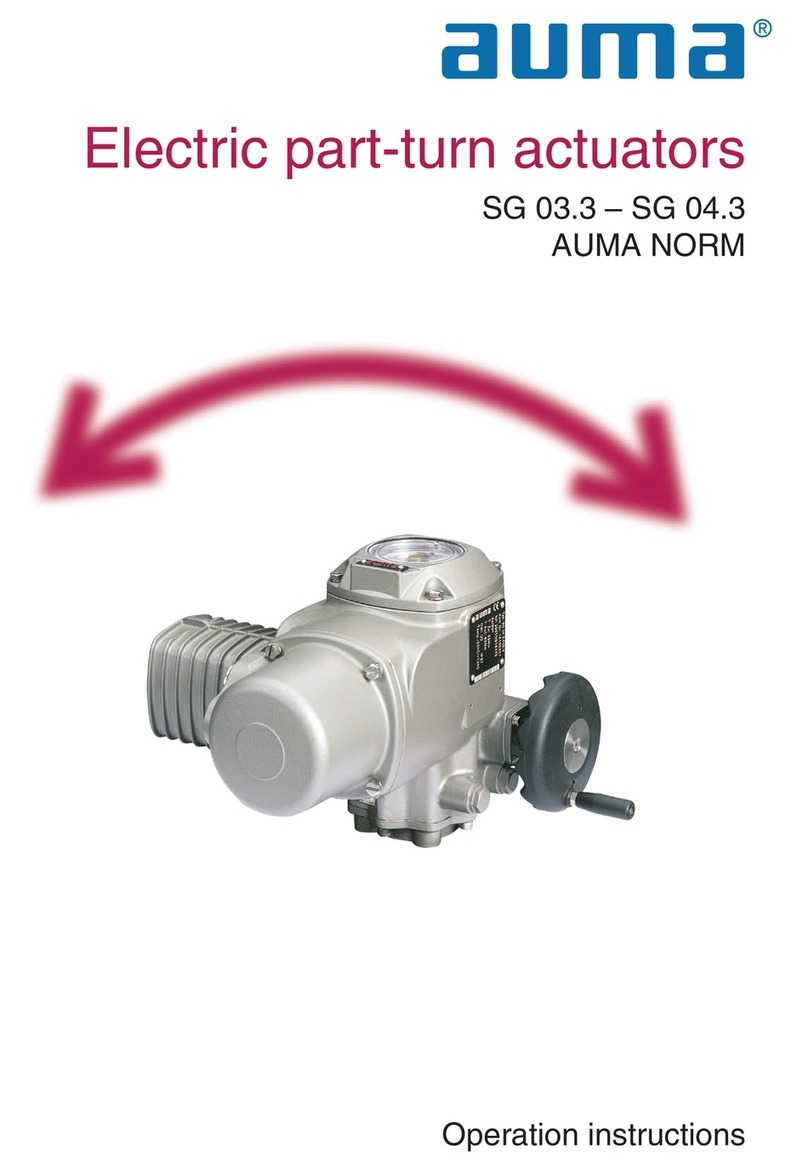
AUMA
AUMA NORM Series User manual
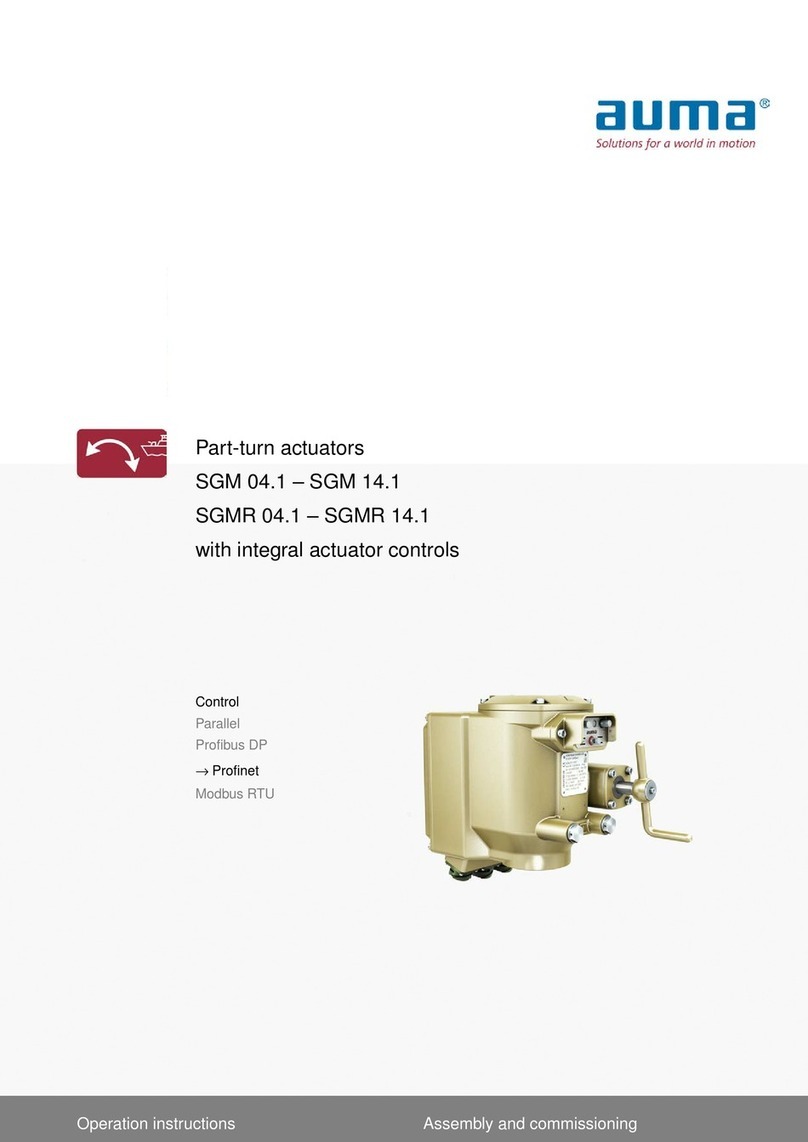
AUMA
AUMA SGM 04.1 User manual
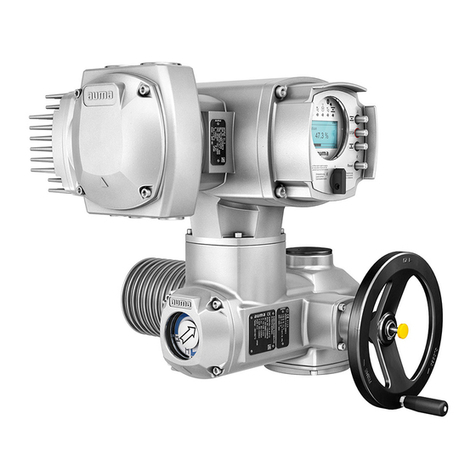
AUMA
AUMA SAVEx Series User manual
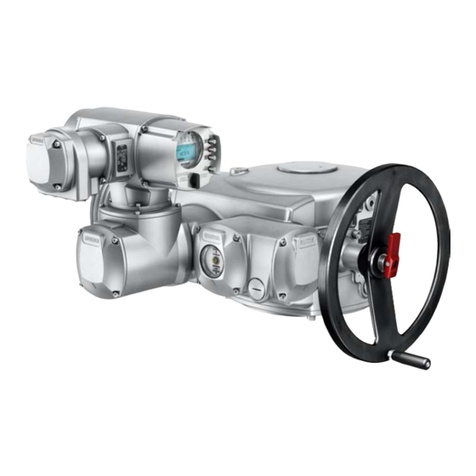
AUMA
AUMA SA 25.1 User manual
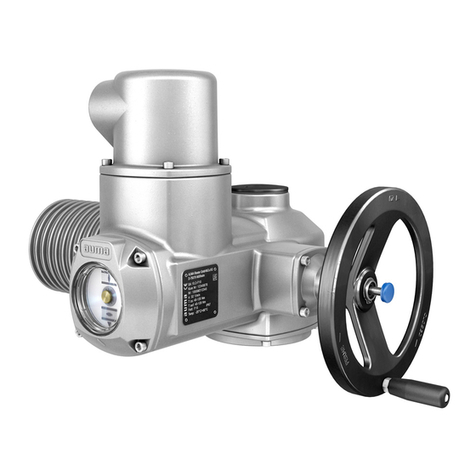
AUMA
AUMA SA 07.2 User manual
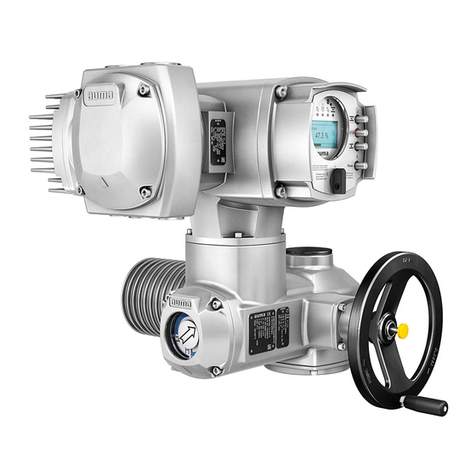
AUMA
AUMA SAVEx 07.2 User manual
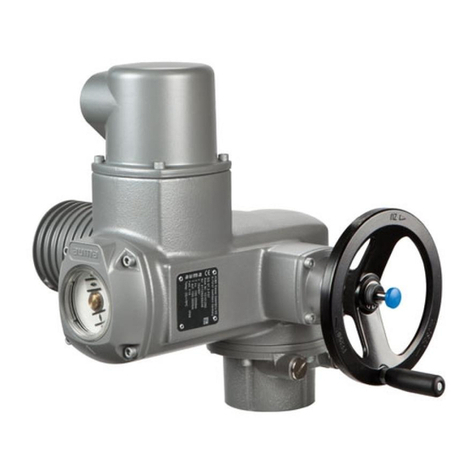
AUMA
AUMA SG 05.1-F05 User manual
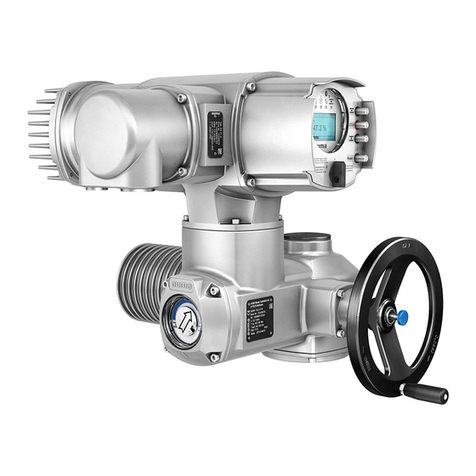
AUMA
AUMA SA 07.1 User manual
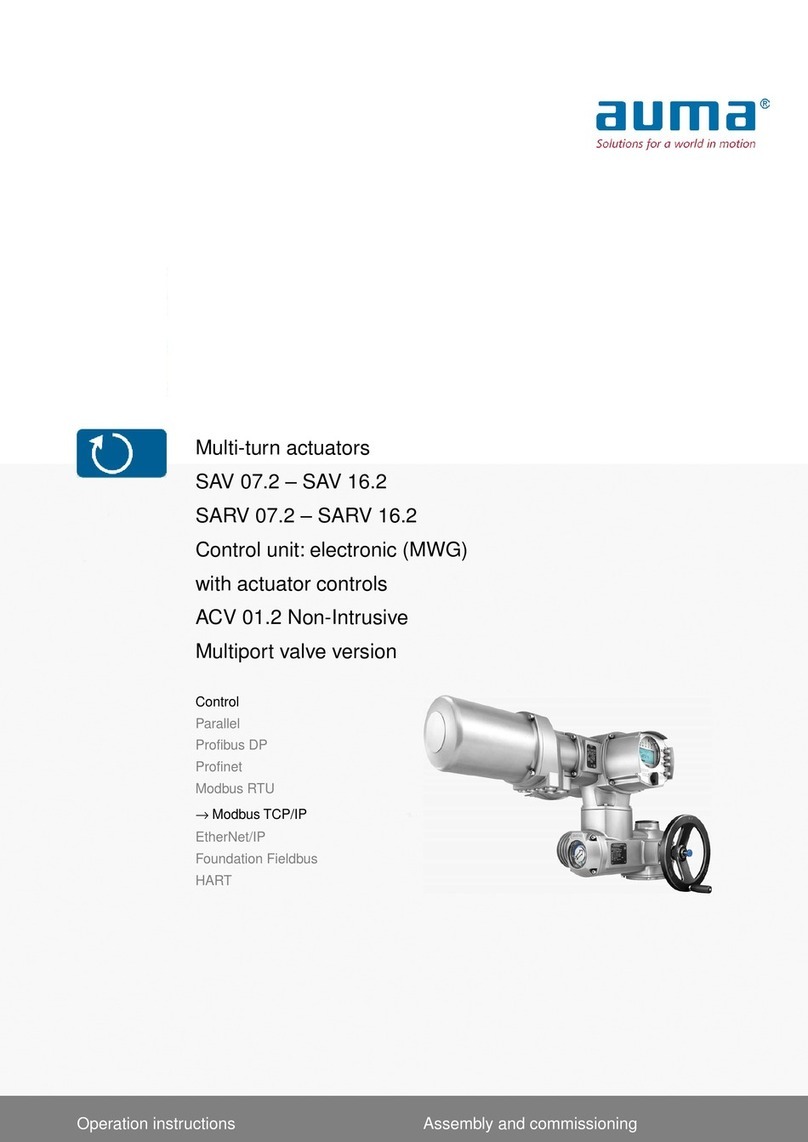
AUMA
AUMA SAV 07.2 User manual
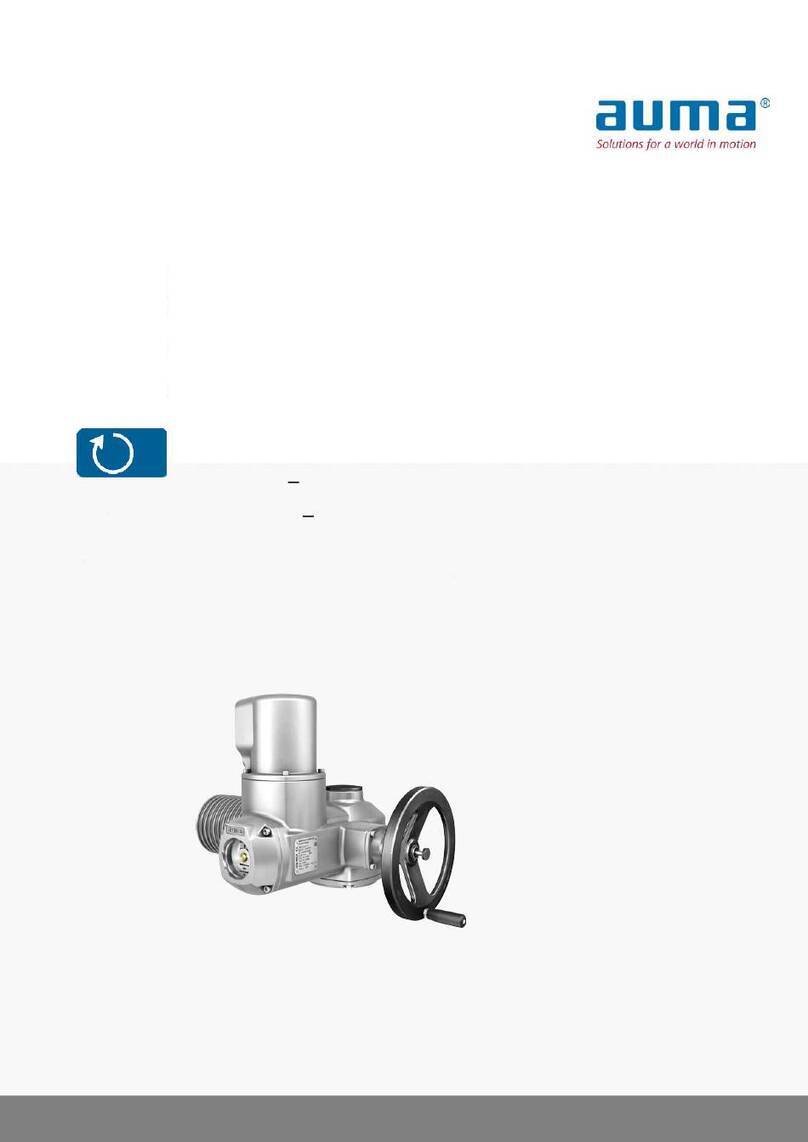
AUMA
AUMA SAN 07.2 User manual
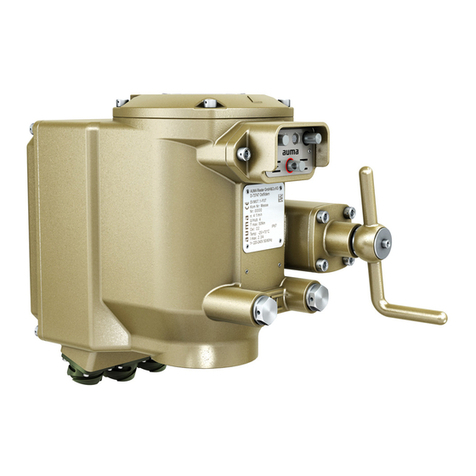
AUMA
AUMA SVM Series User manual
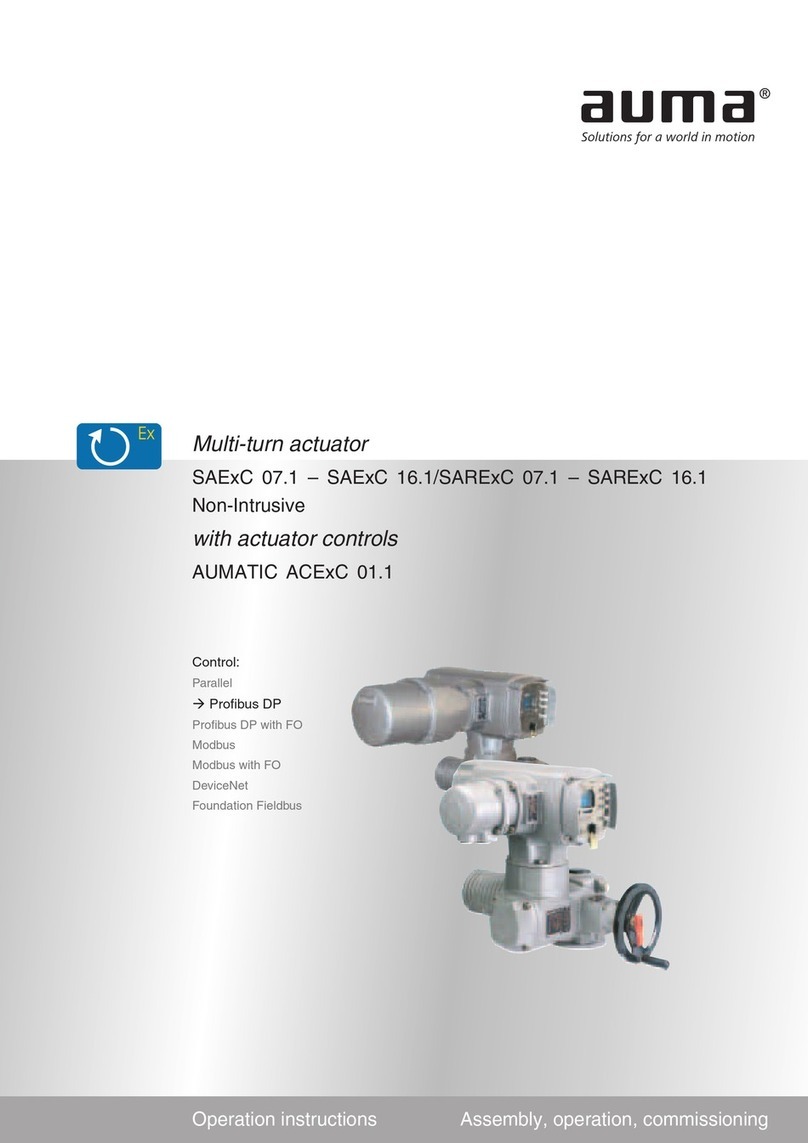
AUMA
AUMA SAExC 07.1 User manual
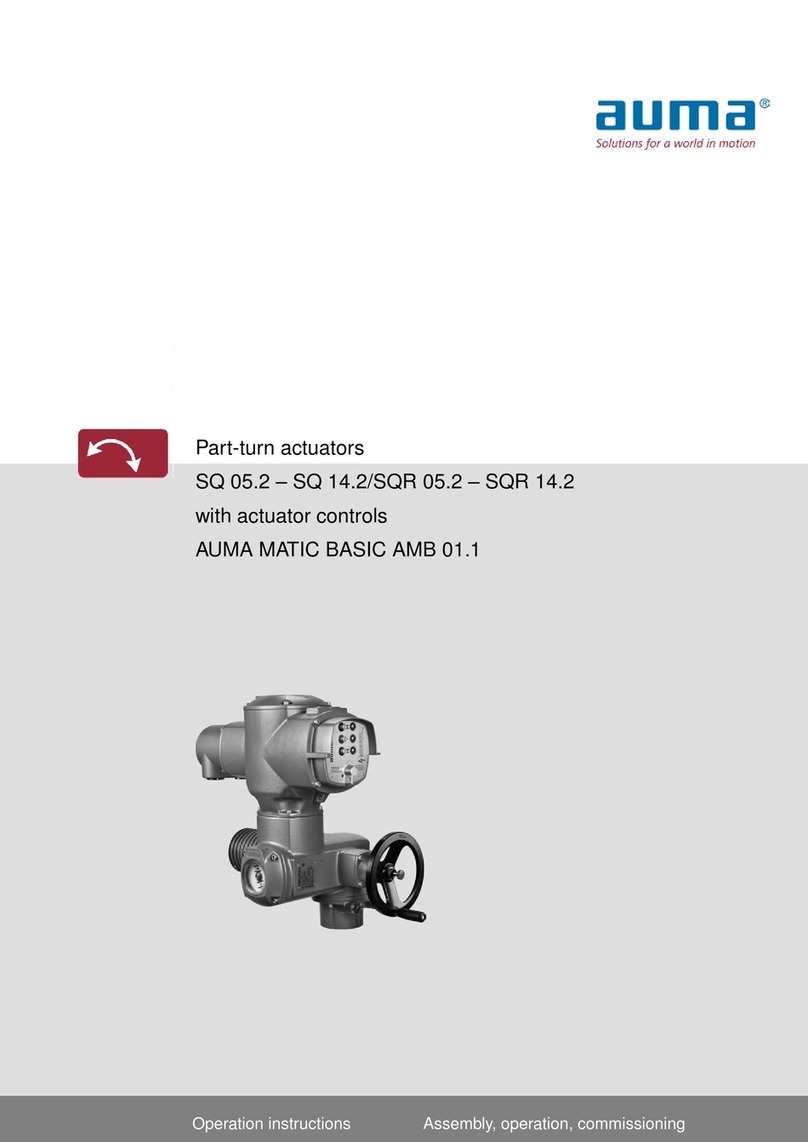
AUMA
AUMA AMB 01.1 User manual
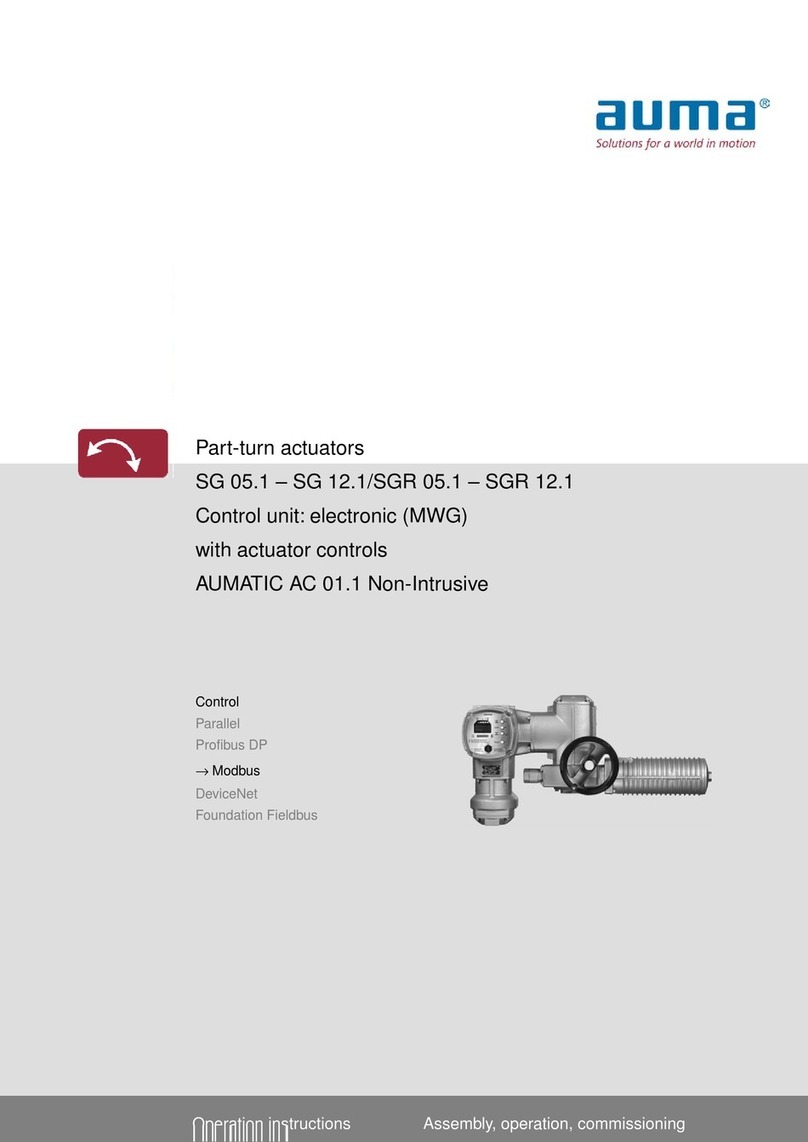
AUMA
AUMA SG 05.1 User manual
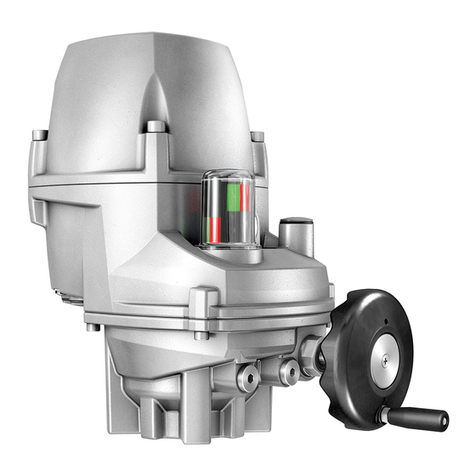
AUMA
AUMA PROFOX PF-Q80 User manual