AUMA PROFOX PF-M100X User manual

PROFOX actuators
PF-M25(X) –PF-M100(X)
PF-Q80(X) –PF-Q600(X)
Profibus DP
Device integrationManual

Read operation instructions first.
●Observe safety instructions.
Purpose of the document:
This document contains information for the commissioning staff of the distributed control system and DCS software
engineers.This document is intended to support the actuator integration into the DCS via fieldbus interface.
Reference documents:
●Operation instructions (Assembly and commissioning) for the actuator
●Manual (Operation and setting)
Reference documents can be downloaded from the Internet (www.auma.com) or ordered directly from AUMA
(refer to <Addresses>).
Table of contents Page
41. Safety instructions................................................................................................................. 41.1. Prerequisites for the safe handling of the product 51.2. Range of application 51.3. Warnings and notes 51.4. References and symbols
62. General information about Profibus DP............................................................................... 62.1. Basic characteristics 62.2. Basic functions of Profibus DP 62.3. Transfer mode 62.4. Bus access 62.5. Functionality 72.6. Protective functions 72.7. Device types
83. Commissioning...................................................................................................................... 83.1. Introduction 83.2. Parameter setting 83.3. Bus address (slave address) 93.4. Configuration of Profibus DP interface 103.5. Communication start-up 103.6. Adaptation options 103.7. Communication monitoring 103.7.1. Connection monitoring of the Profibus DP communication 103.7.2. Fail Safe and Global Control ClearTelegrams 113.8. I & M functions
124. Description of the data interface ......................................................................................... 124.1. Input data (process representation input) –signals 124.1.1. Process representation input (default process representation) 144.1.2. Description of the bytes in the process representation input 244.2. Output data (process representation output) 254.2.1. Process representation output arrangement 264.2.2. Description of the output data 284.3. Profibus DP-V1 services
2
PROFOX actuators
Table of contents Profibus DP

305. Corrective action.................................................................................................................... 305.1. Troubleshooting 305.2. Diagnostics
336. Technical data......................................................................................................................... 336.1. PROFOX Profibus DP
34Index........................................................................................................................................
3
PROFOX actuators
Profibus DP Table of contents

1. Safety instructions
1.1. Prerequisites for the safe handling of the product
Standards/directives The end user or the contractor must ensure that all legal requirements, directives,
guidelines, national regulations and recommendations with respect to assembly,
electrical connection, commissioning and operation are met at the place of installation.
They include among others:
●Standards and directives such as IEC 60079 “Explosive atmospheres":
- Part 14: Electrical installations design, selection and erection.
- Part 17: Electrical installations inspection and maintenance.
●Applicable configuration guidelines for fieldbus applications.
Safety instructions/
warnings All personnel working with this device must be familiar with the safety and warning
instructions in this manual and observe the instructions given. Safety instructions
and warning signs on the device must be observed to avoid personal injury or property
damage.
Qualification of staff Assembly, electrical connection, commissioning, operation, and maintenance must
be carried out by suitably qualified personnel authorised by the end user or contractor
of the plant only.
Prior to working on this product, the staff must have thoroughly read and understood
these instructions and, furthermore, know and observe officially recognised rules
regarding occupational health and safety.
Work performed in potentially explosive atmospheres is subject to special regulations
which have to be observed.The end user or contractor of the plant is responsible
for respect and control of these regulations, standards, and laws.
Electrostatic charging Highly efficient charge generating processes (processes more efficient than manual
friction) on the device surface must be excluded at any time, since they will lead to
propagating brush discharges and therefore to ignition of a potentially explosive
atmosphere.
This also applies to fireproof coatings or covers available as an option.
Ignition dangers Gearboxes were subjected to an ignition hazard assessment in compliance with the
currently applicable standard according to ISO 80079-36/ -37.Hot surfaces,
mechanically generated sparks as well as static electricity and stray electric currents
were identified and assessed as major potential ignition sources.Protective measures
to prevent the likelihood that ignition sources arise were applied to the gearboxes.
This includes in particular lubrication of the gearbox, the IP protection codes and the
warnings and notes contained in these operation instructions.
Commissioning Prior to commissioning, imperatively check that all settings meet the requirements
of the application. Incorrect settings might present a danger to the application, e.g.
cause damage to the valve or the installation.The manufacturer will not be held
liable for any consequential damage.Such risk lies entirely with the user.
Operation Prerequisites for safe and smooth operation:
●Correct transport, proper storage, mounting and installation, as well as careful
commissioning.
●Only operate the device if it is in perfect condition while observing these instruc-
tions.
●Immediately report any faults and damage and allow for corrective measures.
●Observe recognised rules for occupational health and safety.
●Observe national regulations.
●During operation,thehousingwarms upandsurfacetemperatures> 60 °C may
occur.To prevent possible burns, we recommend checking the surface temper-
ature prior to working on the device using an appropriate thermometer and
wearing protective gloves.
4
PROFOX actuators
Safety instructions Profibus DP

Protective measures The end user or the contractor are responsible for implementing required protective
measures on site, such as enclosures, barriers, or personal protective equipment
for the staff.
Maintenance To ensure safe device operation, the maintenance instructions included in this manual
must be observed.
Any device modification requires prior written consent of the manufacturer.
1.2. Range of application
AUMA actuators are designed for the operation of industrial valves.
Other applications require explicit (written) confirmation by the manufacturer.
No liability can be assumed for inappropriate or unintended use.
Observance of these instructions and the operation instructions is considered as
part of the device's designated use.
1.3. Warnings and notes
The following warnings draw special attention to safety-relevant procedures in these
operation instructions, each marked by the appropriate signal word (DANGER,
WARNING, CAUTION, NOTICE).
Indicates an imminently hazardous situation with a high level of risk. Failure
to observe this warning results in death or serious injury.
Indicates a potentially hazardous situation with a medium level of risk.Failure
to observe this warning could result in death or serious injury.
Indicates a potentially hazardous situation with a low level of risk. Failure to
observe this warning could result in minor or moderate injury. May also be
used with property damage.
Potentially hazardous situation. Failure to observe this warning could result
in property damage. Is not used for personal injury.
Safety alert symbol warns of a potential personal injury hazard.
The signal word (here: DANGER) indicates the level of hazard.
1.4. References and symbols
The following references and symbols are used in these instructions:
Information The term Information preceding the text indicates important notes and information.
Symbol for CLOSED (valve closed)
Symbol for OPEN (valve open)
➥Result of a process step
Describes the result of a preceding process step.
5
PROFOX actuators
Profibus DP Safety instructions

2. General information about Profibus DP
For exchange of information among automation systems and between automation
systems and the connected distributed field devices, the use of serial fieldbus systems
for communication is state-of-the-art.Thousands of applications have proved
impressively that, in comparison with conventional technology, cost savings of up to
40 % in wiring, commissioning, and maintenance are achieved by using fieldbus
technology.While in the past the fieldbus systems used were often manufacturer
specific and incompatible with other bus systems, the systems employed today are
almost exclusively open and standardized.This means that the user does not depend
on individual suppliers and can choose within a large product range the most suitable
product at the most competitive price.
Profibus DP is the leading open fieldbus system in Europe and is also used
successfully throughout the world.The application range includes automation in the
areas of manufacturing, processing, and building.Profibus DP is an international,
open fieldbus protocol which has been standardized in the fieldbus standards IEC
61158 and IEC 61784.This standardization ensures that the investments by
manufacturers and users are protected to the best possible degree and the
independence of the manufacturer is guaranteed.
2.1. Basic characteristics
Profibus DP defines the technical and functional features of a serial fieldbus system
allowing interconnection of distributed, digital automation devices. Profibus DP
distinguishes between master and slave devices.
Profibus DP is designed for fast data transmission on the field level.Here, central
control devices, such as a PLC or PC, communicate via a fast serial connection with
peripheral field devices such as input/output devices, valves, and actuators.
Data exchange among these field devices is based on cyclic communication.The
respectively necessary communication functions are defined by the Profibus DP
basic functions according to IEC 61158 and IEC 61784.
Master devices Master devices control data traffic on the bus.A master is allowed to send messages
without an external request.Within the Profibus protocol, masters are also called
‘active devices’.
Slave device Slave devices such as AUMA Profibus DP actuators are peripheral devices.Typical
slave devices are input/output devices, valves, actuators, and measuring transducers.
They do not have bus access rights, i.e. they may only acknowledge received
messages or, at the request of a master, transmit messages to that master. Slaves
are also called ‘passive devices’.
2.2. Basic functions of Profibus DP
On a cyclic basis, the master reads the input information from the slaves and writes
the output information to the slaves. In addition to this cyclic data transfer of the
processrepresentation,ProfibusDP also providespowerfulfunctionsfordiagnostics
and commissioning. Data traffic is monitored through the monitoring functions on
the master and slave side.
2.3. Transfer mode
●RS-485 twisted pair cable or fibre optic cable
●AUMA actuators support baud rates up to 1.5 Mbits/s.
2.4. Bus access
●Token-passing between the masters and polling between master and slave
●Mono-master or multi-master systems are possible.
●Master and slave devices: max. 126 devices at a bus
2.5. Functionality
●Peer-to-peer (process data exchange [DATA EX]) or Multicast (control com-
mands to all slaves)
6
PROFOX actuators
General information about Profibus DP Profibus DP

●Cyclic process data exchange between DP master and DP slaves.
●Additional acyclic data exchange between DP master and DP slaves for
Profibus DP withV1 services.
●Checking the configuration of the DP slaves
●Synchronisation of inputs and/or outputs
2.6. Protective functions
●All messages are transmitted with Hamming Distance HD=4.
●Watchdog timer at DP slaves
●Access protection for the inputs/outputs of DP slaves (Sync and Freeze)
●Process data exchange monitoring with configurable timer interval at the master
●Adjustable failure behaviour
2.7. Device types
●DP master class 2 (DPM2), e.g.programming/configuration tools
●DP master class 1 (DPM1), e.g.central controllers such as PLC, PC
●DP slave, e.g.AUMA Profibus DP devices. Devices with binary or analogue
inputs/outputs, actuators, plug valves
7
PROFOX actuators
Profibus DP General information about Profibus DP

3. Commissioning
3.1. Introduction
When commissioning a Profibus DP network, the devices on the Profibus DP must
be parametrised and configured using the programming software at the controls
(Profibus configurator).
The programming software first reads the GSD file (GeneralStationData) of the
individual actuators.The GSD file contains information about the device properties
needed by the master.
Afterwards, the user can configure and parametrise the device at the Profibus DP
for the programming software of the process control system.
This information is then stored in the controls (DP master) and sent to the actuators
(DP slaves) each time cyclic communication is started.
The process representation input and output bytes are used to control the actuator
and to supply the feedback signals.If a configuration with consistent data is selected,
certain PLCs require special function blocksforthe control of the ProfibusDPslaves.
Certification AUMA actuators with Profibus DP are certified by the Profibus user organisation
(PNO).
ID number Each DP slave and each DP master have individual ID numbers.The ID number is
requiredforthe DP master to identify the type of deviceconnected without significant
protocol overhead.The master compares the ID numbers of the connected DP
devices to the ID number in the specified configuration data.The process data transfer
will only be started if the correct device types with the correct station addresses were
connected to the fieldbus.This ensures a high security against configuration errors.
The PNO manages the ID numbers together with the device master data (GSD).
PROFOX actuators are listed with the following Ident number at PNO:
●Ident number of the standard version: 0x1146 with functions for:
- Single channel Profibus DP interface (not redundant)
- Optional Profibus DP-V1 services
Device Master Data
(GSD) For Profibus DP, the performance features of the devices are documented by the
manufacturer and made available to the users as device data sheet and device
master data file.Structure, contents and coding of the General Station Description
(GSD) are standardised.They enable comfortable configuration of any DP slaves
with configuration devices by different manufacturers.
The following GSD files are available for PROFOX actuators:
●Standard version: AUMA1146.GSD with functions for:
- Single channel Profibus DP interface (not redundant)
- Optional Profibus DP-V1 services
Information GSD files can be downloaded from our website: www.auma.com.
3.2. Parameter setting
The parameter setting is partly defined in the Profibus standard, e.g. one bit for
switching bus monitoring on and off (watchdog).
3.3. Bus address (slave address)
Each participant at the bus is addressed via its specific bus address (slave address).
The bus address may be assigned only once per fieldbus network.
Bus address storage is non-volatile.
On delivery, address 126 (default value) is set for all devices.
The bus address (slave address) can be set in the following ways:
8
PROFOX actuators
Commissioning Profibus DP

●Locally via the display
For details on setting refer to the Operation Instructions to the actuator or
Manual (Operation and Setting).
●Using AUMA CDT service software (via PC or laptop with Bluetooth).
The latest version of AUMA CDT can be downloaded from our website:
www.auma.com.
●Via fieldbus, please note that only one device with the address 126 (default
value) is be connected to Profibus DP. A new bus address may be assigned
to the actuator using the SAP 55 (Service-Access-Point Set Slave Address).
3.4. Configuration of Profibus DP interface
During configuration, the number of input and output bytes reserved for each device
in the controls’memory is selected. Additionally, the method of data processing is
defined: consistent or non-consistent.
Information Only the number of bytes defined in the configuration are transmitted between DP
master and DP slave.
The following configurations are possible with AUMA Profibus DP actuators:
Number of output bytesNumber of input bytes
11
41
81
12
42
82
162
14
44
84
164
86
166
48
88
128
412
812
1212
1612
420
820
1220
432
832
1232
1632
2640
All these configurations (except 1 In, 1 Out) can be selected as consistent or
non-consistent.
The number of input bytes indicates how many of the maximum 40 bytes are sent
to the DP master by the DP slave.
9
PROFOX actuators
Profibus DP Commissioning

The number of output bytes indicates how many of the maximum 26 bytes are sent
to the DP slave by the DP master.
If, for example, a configuration with 8 input bytes is selected, only the first 8 bytes
are sent by the DP slave to the DP master during data exchange. In this case, the
master does not have access to bytes 9 to 40.This way, the DP master saves memory
space since only 8 input bytes are reserved for the actuator.
Data issued by AUMA actuators shall be consistently processed by the DP master.
This ensures that the value of a 2-byte variable (position transmitter, analogue
customer input) does not change after reading out the first byte and, thus, does not
distort the value. If a master does not offer the option of consistent configuration
because of the DCS, configuration without consistency can be selected.
3.5. Communication start-up
Whenswitchingon the DP master, it first sends oneparameterand one configuration
telegram to each DP slave.If parameters and configuration are correct, the DP slave
enters the ‘Data Exchange’mode to exchange process data between controls and
slave.Then, the DP master can control the DP slave and read its current state via
the process representation.
If communication is interrupted (e.g.when switching the slave off or in the event of
Profibuscablerupture), it is automatically resumed bythe DP master once the cause
of the fault is eliminated.
3.6. Adaptation options
The actuator provides the option to adapt to existing DCS configurations of actuator
controls ranges AC 01.2/ACExC 01.2 as well as AC 01.1/ACExC 01.1.For this, the
actuator can be set as to support the standard arrangement of Profibus DP-V0
process representation input of AC 01.2/ACExC 01.2 without changing the Profibus
configuration of the DCS.
Information ●Only the Profibus DP-V0 standard arrangement of the process representation
input of AC 01.2/ACExC 01.2 is supported, deviating arrangements of the
Profibus DP-V0 process data input require use/installation of the
AUMA1144D.gsd file in the DCS.
3.7. Communication monitoring
3.7.1. Connection monitoring of the Profibus DP communication
The connection monitoring within the master has to be activated to monitor both
master and cable connection between master and actuator (parameter telegram
byte 1 bit 3 WD_ON = 1).
Only if the connection monitoring is active can the actuator react in the even of loss
of communication once the monitoring time also set in the master has elapsed.
The reaction of the actuator also depends on the settings for failure behaviour or
EMERGENCY behaviour.
3.7.2. Fail Safe and Global Control ClearTelegrams
Another possibility to set the slave to a safe state in the event of a fault are the fail
safe telegrams (telegrams with data length = 0).If fail safe telegrams are received,
the actuator remains in the Data Exchange state;depending on the respective setting,
the actuator may initiate the failure behaviour or the EMERGENCY behaviour.The
actuator quits the fail safe state as soon as valid telegrams with data length ≠0 are
received.
Furthermore, the Global Control Clear (GC Clear) master telegrams can also be
used to initiate the failure behaviour or the EMERGENCY behaviour.This state can
be disabled using a Global Control Operate telegram (GC Operate).
10
PROFOX actuators
Commissioning Profibus DP

For activated EMERGENCY behaviour:
Risk of actuator operation due to an EMERGENCY signal or a loss of commu-
nication!
Risk of personal injuries or damage to the valve.
→Forcommissioningandmaintenancework:Select position OFF via ApporCDT.
Motor operation can only be interrupted in this operation mode.
→If the actuator starts unexpectedly:immediately disconnect from mains.
3.8. I & M functions
The actuator supports the I & M function according to PNO guideline 3.502.
With the term Identification & Maintenance (I & M) functions, the Profibus user
organisation e.V. (PNO) introduced a new functionality for all Profibus devices with
acyclic communication channel that may prove very useful for plant operators.The
I & M functions define how certain device-describing data (according to name plate)
is to be uniformly stored in the Profibus devices.Engineering tools may then read
and interpret the data according to a code which can be accessed on the PNO server.
This provides uniform and powerful access to all important and current device data,
one of the major requirements for asset management.
Partof the device-specificI & M information is the unambiguous (asset) identification
using a manufacturer ID (MANUFACTURER_ID, for AUMA actuators = 319), the
order number (ORDER_ID) of the actuator as and well as the individual serial number
(SERIAL_NUMBER). Further data supplements the asset information.
SizeContent
Header
10 OctetsManufacturer specific
I&M Block
2 OctetsMANUFACTURER_ID
20 OctetsORDER_ID
16 OctetsSERIAL_NUMBER
2 OctetsHARDWARE_REVISION
4 OctetsSOFTWARE_REVISION
2 OctetsREVISION_COUNTER
2 OctetsPROFILE_ID
2 OctetsPROFILE_SPECIFIC_TYPE
2 OctetsIM_VERSION
2 OctetsIM_SUPPORTED
11
PROFOX actuators
Profibus DP Commissioning

4. Description of the data interface
4.1. Input data (process representation input) –signals
The process representation input allows the master (controls) to read the state of
the slave (actuator).
4.1.1. Process representation input (default process representation)
Grey bits are collective signals.They contain the results of a disjunction (OR
operation) of other information.
12
PROFOX actuators
Description of the data interface Profibus DP

13
PROFOX actuators
Profibus DP Description of the data interface

4.1.2. Description of the bytes in the process representation input
Byte 1: Logic signals
Bits 3, 6, and 7 are collective signals.
Bits 5 and 4 of the logical signals (byte1) indicate a logical operation of the actuator,
i.e.they are set when the actuator has received the command for an electrical
operation (also active when e.g.the actuator is in a stepping pause during stepping
mode or waiting for the end of the dead time).
Table 1:Byte 1: Logic signals
DescriptionValuePrm-Text-Def GSD fileDesignation
(process representation)
Bit
For limit seating: Limit switch operated in direction
OPEN.
For torque seating:Torque switch and limit switch oper-
ated in direction OPEN.
1(2) = "Bit: End p. OPEN"
End position OPEN
0
No signal.0 For limit seating: Limit switch operated in direction
CLOSE.
For torque seating:Torque switch and limit switch oper-
ated in direction CLOSE.
1(1) = "Bit: End p. CLOSED"
End position CLOSED
1
No signal.0 The position setpoint is within max.error variable (outer
dead band). Is only signalled if Profibus DP master has
set the Fieldbus SETPOINT bit (process representation
output).
1(5) = "Bit:Setpoint reached"
Setpoint pos.reached
2
No signal.0 Collective signal 04:
Contains the result of a disjunction (OR-operation) of all
bits comprised in bytes 13 and 14 (Not ready REMOTE
1 and Not ready REMOTE 2).
The actuator cannot be operated from REMOTE.
Theactuator can only be operatedvia the localcontrols.
1(22) = "Bit: Not ready RE-
MOTE"
Not ready REMOTE
3
In bytes 13 and 14, no signals are active (all bits are set
to 0).
0
An operation command via the local controls or via
fieldbus in direction OPEN is performed:Fieldbus OPEN
or Fieldbus SETPOINT (process representation output).
This bit remains also set during operation pauses (e.g.
due to the dead time or the reversing prevention time).
1(7) = "Bit: Running OPEN"
Running OPEN
4
Operation in direction OPEN via fieldbus is not executed.0An operation command via the local controls or via
fieldbus in direction CLOSE is performed: Fieldbus
CLOSE or Fieldbus SETPOINT (process representation
output).This bit remains also set during operation
pauses (e.g.due to the dead time or the reversing pre-
vention time).
1(6) = "Bit: Running CLOSE"
Running CLOSE
5
Operation in direction CLOSE via fieldbus is not ex-
ecuted.
0
Collective signal 02:
Contains the result of a disjunction (OR-operation) of all
bits of bytes 17 to 20 (Warning 1 to Warning 4).
1(21) = "Bit:Warnings"
Warning
6
In bytes 17 and 20, no warnings are active (all bits are
set to 0).
0
Collective signal 03:
Contains the result of a disjunction (OR-operation) of all
bits of bytes 15 and 16 (Fault 1 and Fault 2).
The actuator cannot be operated.
1(20) = "Bit: Fault"
Fault
7
In bytes 15 and 16, no faults are active (all bits are set
to 0).
0
14
PROFOX actuators
Description of the data interface Profibus DP

Byte 2: Actuator signals
Table 2:Byte 2: Actuator signals
DescriptionValuePrm-Text-Def GSD fileDesignation
(process representation)
Bit
Motor protection tripped.1(56) = "Bit:Thermal fault"
Thermal fault
0No signal.0
●When connecting to a 3-phase AC system and with
internal 24 V DC supply of the electronics:Phase 2
is missing.
●Whenconnecting to a 3-phaseor 1-phase ACsystem
and with external 24V DC supply of the electronics:
One of the phases L1, L2 or L3 is missing.
1(57) = "Bit: Phase fault"
Phase fault
1
All phases are available.0 Select in position REMOTE.1(9) = "Bit: Sel. sw. RE-
MOTE"
Select REMOTE
2Select not in position REMOTE.0 Select in position LOCAL.1(8) = "Bit: Selector sw.
LOCAL"
Select LOCAL
3Select not in position LOCAL.0 Limit switch in end position OPEN active.1(12) = "Bit: Limit sw. OPEN"
Limit switch OPEN
4No signal.0 Limit switch in end position CLOSED active.1(11) = "Bit: Limit sw.
CLOSED"
Limit switch CLOSED
5No signal.0 Torque switch operated in direction OPEN.1(14) = "Bit:Torque sw.
OPEN"
Torque sw. OPEN
6No signal.0 Torque switch operated in direction CLOSE.1(13) = "Bit:Torque sw.
CLOSE"
Torque sw. CLOSED
7No signal.0
Bytes 3 and 4: Actual position
Byte 3 = high byte, byte 4 = low byte.
If a position transmitter is installed in the actuator, bytes 3 and 4 are used to transmit
the current actuator position.The value is transmitted in per mil (value: 0 –1,000).
Byte 5: Device status
Table 3:Byte 5: Device status
DescriptionValuePrm-Text-Def GSD fileDesignation
(process representation)
Bit
Collective signal 04:
Contains the result of a disjunction (OR-operation) of all
bits comprised in bytes 13 and 14 (Not ready REMOTE
1 and Not ready REMOTE 2).
The actuator cannot be operated from REMOTE.
The actuator can only be operated via the local controls.
1(22) = "Bit: Not ready RE-
MOTE"
Not ready REMOTE
0
In bytes 13 and 14, no signals are active (all bits are set
to 0).
0
Collective signal 02:
Contains the result of a disjunction (OR-operation) of all
bits of bytes 17 to 20 (Warning 1 to Warning 4).
1(21) = "Bit:Warnings"
Warning
1
In bytes 17 and 20, no warnings are active (all bits are
set to 0).
0
Collective signal 03:
Contains the result of a disjunction (OR-operation) of all
bits of bytes 15 and 16 (Fault 1 and Fault 2).
The actuator cannot be operated.
1(20) = "Bit: Fault"
Fault
2
In bytes 15 and 16, no faults are active (all bits are set to
0).
0
15
PROFOX actuators
Profibus DP Description of the data interface

DescriptionValuePrm-Text-Def GSD fileDesignation
(process representation)
Bit
Collective signal 09:
Indication according to NAMUR recommendation NE 107
Recommendation to perform maintenance.
Contains the result of a disjunction (OR-operation) of all
bits of byte 24 (Maintenance required).
1(19) = "Bit: Maintenance
requ."
NAMUR mainten. req.
3
In all bits of byte 24, no signals are active (all bits are set
to 0).
0
Collective signal 07:
Indication according to NAMUR recommendation NE 107
Actuator is operated outside the normal operation condi-
tions.
Contains the result of a disjunction (OR-operation) of all
bits of bytes 25 to 28 (Out of specification 1 to 4).
1(18) = "Bit: Out of spec."
NAMUR out of spec.
4
In bytes 25 and 28, no signals are active (all bits are set
to 0).
0
Collective signal 08:
Indication according to NAMUR recommendation NE 107
The actuator is being worked on;output signals are tem-
porarily invalid.
Contains the result of a disjunction (OR-operation) of all
bits of bytes 29 and 30 (Function check 1 and 2).
1(17) = "Bit:Function check"
NAMUR funct. check
5
In bytes 29 and 30, no signals are active (all bits are set
to 0).
0
Collective signal 10:
Indication according to NAMUR recommendation NE 107
Actuator function failure, output signals are invalid.
Contains the result of a disjunction (OR-operation) of all
bits of byte 23 (Failure).
1(16) = "Bit: Failure"
NAMUR failure
6
In all bits of byte 23, no signals are active (all bits are set
to 0).
0
Collective signal 05:
The device is ready for remote control.
No AUMA warnings, AUMA faults or signals according to
NAMUR are present.
Bit 7 is set if bits 0 to 6 are deleted.
1(15) = "Bit: Device ok"
Device ok
7
Contains the result of a disjunction (OR-operation) of bits
0 to 6 (device status).
0
Byte 6: Operation status
They include information about the actuator movement.
Table 4:Byte 6: Operation status
DescriptionValuePrm-Text-Def GSD fileDesignation
(process representation)
Bit
The actuator is in off-time (e.g.reversing prevention time).1(23) = "Bit: Op. pause act-
ive"
Operation pause active
0No signal.0 The actuator is in an intermediate position e.g. neither in
end position OPEN nor in end position CLOSED.
1(29) = "Bit: In interm. posi-
tion"
In intermediate pos.
1
No signal.0 No signal (reserved).——2No signal (reserved).——3Actuator is running (output drive is moving)
Hard wired collective signal consisting of signals:
●(26) Running LOCAL
●(27) Running REMOTE
●(28) Handwheel oper.
1(25) = "Bit: Actuator run-
ning"
Actuator running
4
No signal.0
16
PROFOX actuators
Description of the data interface Profibus DP

DescriptionValuePrm-Text-Def GSD fileDesignation
(process representation)
Bit
Output drive rotates without electric operation command.1(28) = "Bit: Running via
handw."
Handwheel oper.
5No signal.0 Output drive rotates due to operation command from
REMOTE.
1(27) = "Bit: Running RE-
MOTE"
Running REMOTE
6
No signal.0 Output drive rotates due to operation command from
LOCAL.
1(26) = "Bit: Running LOC-
AL"
Running LOCAL
7
No signal.0
Byte 7: Intermediate positions
Table 5:Byte 7: Intermediate positions
DescriptionValuePrm-Text-Def GSD fileDesignation
(process representation)
Bit
Intermediate position 1 reached.1(31) = "Bit: Intermediate
pos. 1"
Intermediate pos. 1
0No signal.0 Intermediate position 2 reached.1(32) = "Bit: Intermediate
pos. 2"
Intermediate pos. 2
1No signal.0 Intermediate position 3 reached.1(33) = "Bit: Intermediate
pos. 3"
Intermediate pos. 3
2No signal.0 Intermediate position 4 reached.1(34) = "Bit: Intermediate
pos. 4"
Intermediate pos. 4
3No signal.0 Intermediate position 5 reached.1(35) = "Bit: Intermediate
pos. 5"
Intermediate pos. 5
4No signal.0 Intermediate position 6 reached.1(36) = "Bit: Intermediate
pos. 6"
Intermediate pos. 6
5No signal.0 Intermediate position 7 reached.1(37) = "Bit: Intermediate
pos. 7"
Intermediate pos. 7
6No signal.0 Intermediate position 8 reached.1(38) = "Bit: Intermediate
pos. 8"
Intermediate pos. 8
7No signal.0
Byte 8: Discrete inputs
Table 6:Byte 8: Discrete inputs
DescriptionValuePrm-Text-Def GSD fileDesignation
(process representation)
Bit
A high signal (+24 V DC) is present at digital input 1.1(39) = "Bit: Input DIN 1"
Input DIN 1
0No signal.0 A high signal (+24 V DC) is present at digital input 2.1(40) = "Bit: Input DIN 2"
Input DIN 2
1No signal.0 A high signal (+24 V DC) is present at digital input 3.1(41) = "Bit: Input DIN 3"
Input DIN 3
2No signal.0 No signal (reserved).——3No signal (reserved).——4No signal (reserved).——5No signal (reserved).——6The Bluetooth interface is connected.1(46) = "Bit: Input DIN 7"
Bluetooth connected
7No signal.0
Bytes 9 and 10: Input AIN 1
Byte 9 = high byte, byte 10 = low byte.
17
PROFOX actuators
Profibus DP Description of the data interface

Bytes 9 and 10 transmit the value of the first additional free analogue current input
of the Profibus DP interface.The start and end values can be set via the display.
(For operation, please refer to the respective operation instructions for the actuator.)
If the measuring values are 0.3 mA below the initial value, a signal loss is indicated.
The value is transmitted in per mil (value: 0 –1,000).
Bytes 11 and 12:Torque
Byte 11 = high byte, byte 12 = low byte.
The current actuator torque is transmitted in byte 11 and byte 12.
The value transmitted is the current torque in percent or per mil of the nominal actuator
torque.
The value is transmitted in per mil (value: 0 –1,000).
●The value 1,000 corresponds to 127,0 % torque in direction OPEN.
●The value 500 is the torque zero point.
●The value 0 corresponds to 127,0 % torque in direction CLOSE.
Byte 13: Not ready REMOTE 1
Table 7:Byte 13: Not ready REMOTE 1
DescriptionValuePrm-Text-Def GSD fileDesignation
(process representation)
Bit
Wrong operation command
Indicates that several operation commands were received
simultaneously via Profibus DP (e.g.Remote OPEN and
Remote CLOSE simultaneously or Remote CLOSE/Re-
mote OPEN and Remote SETPOINT simultaneously) or
that the max. value for a setpoint position has been ex-
ceeded (setpoint position > 1,000).
1(98) = "Bit:Wrong opera-
tion cmd"
Wrong oper. cmd
0
Operation commands are ok.0 Select in position LOCAL or in position OFF.1(53) = "Bit: Sel. sw. not
REMOTE""
Select n. REMOTE
1Select in position REMOTE.0 Actuator is locked.1(52) = "Bit:Interlock active"
Interlock active
2No signal.0 No signal (reserved).——3Operation mode EMERGENCY stop is active (EMER-
GENCY stop button has been pressed).
1(50) = "Bit: EMCY stop
active"
EMCY stop active
4
EMERGENCYstopbuttonnot pressed(normaloperation).0Operation mode EMERGENCY behaviour is active
(EMERGENCY signal was sent).
1(49) = "Bit: EMCY be-
hav.act."
EMCY behav. active
5
No signal.0 No valid communication via fieldbus (despite available
connection)
1(47) = "Bit: FailState field-
bus"
FailState fieldbus
6
Communication via fieldbus is OK.0 The actuator is controlled via the I/O interface (parallel).1(48) = "Bit: I/O interface"
I/O interface
7The actuator is controlled via the fieldbus.0
Byte 14: Not ready REMOTE 2
Table 8:Byte 14: Not ready REMOTE 2
DescriptionValuePrm-Text-Def GSD fileDesignation
(process representation)
Bit
No signal (reserved).——0No signal (reserved).——1No signal (reserved).——2No signal (reserved).——3No signal (reserved).——4
18
PROFOX actuators
Description of the data interface Profibus DP

DescriptionValuePrm-Text-Def GSD fileDesignation
(process representation)
Bit
PVST or torque profile operation (reference or comparat-
ive operation) active.
1(116) = "Bit:Valve test act-
ive"
PVST / valve test active
5
No signal.0 Operation mode Service is active.1(51) = "Bit: Service active"
Service active
6No signal.0 Manual operation is active (handwheel is engaged); op-
tional signal
1(54) = "Bit: Handwheel
active"
Handwheel active
7
No signal.0
Byte 15: Fault 1
The fault signals contain the causes why the actuator cannot be operated.
Table 9:Byte 15: Fault 1
DescriptionValuePrm-Text-Def GSD fileDesignation
(process representation)
Bit
Incorrect configuration, i.e.the current setting of the is
invalid.
1(72) = "Bit: Configuration
error"
Configuration error
0
Configuration is OK.0 No signal (reserved).——1Motor protection tripped.1(56) = "Bit:Thermal fault"
Thermal fault
2No signal.0
●When connecting to a 3-phase AC system and with
internal 24 V DC supply of the electronics:Phase 2
is missing.
●When connecting to a 3-phase or 1-phase AC system
and with external 24 V DC supply of the electronics:
One of the phases L1, L2 or L3 is missing.
1(57) = "Bit: Phase fault"
Phase fault
3
No signal.0 Torque fault in direction OPEN1(61) = "Bit:Torque fault
OPEN"
Torque fault OPEN
4No signal.0 Torque fault in direction CLOSE1(60) = "Bit:Torque fault
CLOSE"
Torque fault CLOSE
5No signal.0 Collective signal 14:Internal error.1(69) = "Bit: Internal fault"
Internal error
6No internal fault0 No actuator reaction to operation commands within the
set reaction time.
1(71) = "Bit: No reaction"
Wrn no reaction
7
No signal.0
Byte 16: Fault 2
The fault signals contain the causes why the actuator cannot be operated.
Table 10:Byte 16: Fault 2
DescriptionValuePrm-Text-Def GSD fileDesignation
(process representation)
Bit
No signal (reserved).——0No signal (reserved).——1No signal (reserved).——2No signal (reserved).——3No signal (reserved).——4No signal (reserved).——5Config. error of REMOTE interface active.1(123) = "Bit: Config error
remote"
Config. error REMOTE
6No signal.0 No signal (reserved).——7
19
PROFOX actuators
Profibus DP Description of the data interface

Byte 17:Warnings 1
The warning signals are for information only and do not interrupt or disable an
operation (as opposed to faults).
Table 11:Byte 17:Warnings 1
DescriptionValuePrm-Text-Def GSD fileDesignation
(process representation)
Bit
No signal (reserved).——0No signal (reserved).——1No signal (reserved).——2No signal (reserved).——3Warning: Limit value for torque warning in direction
CLOSE exceeded.
1(125) = "Bit:Torque wrn
CLOSE"
Torque wrn CLOSE
4
No signal.0 Warning:Limit value for torque warning in direction OPEN
exceeded.
1(124) = "Bit:Torque wrn
OPEN"
Torque wrn OPEN
5
No signal.0 No signal (reserved).——6Warning: No actuator reaction to operation commands
within the set reaction time.
1(71) = "Bit: No reaction"
Wrn no reaction
7
No signal.0
Byte 18:Warnings 2
Table 12:Byte 18:Warnings 2
DescriptionValuePrm-Text-Def GSD fileDesignation
(process representation)
Bit
Warning:Temperature within actuator controls housing
too high.
1(88) = "Bit:WrnControl-
sTemp"
Wrn controls temp.
0
No signal.0 No signal (reserved).——1No signal (reserved).——2The external 24 V DC voltage supply of the controls has
exceeded the power supply limits.
1(68)= "Bit:24V DC,extern-
al"
24 V DC external
3
No signal.0 No signal (reserved).——4Warning:Voltage of RTC button cell too low.1(126) = "Bit: RTC button
cell"
RTC voltage
5No signal.0 The real time clock has not yet been set on the basis of
valid values.
1(77) = "Bit: RTC not set"
Time not set
6
No signal.0 Warning: Configuration setting is incorrect.
The device can still be operated with restrictions.
1(108) = “Bit: Config.Warn-
ing”
Config. warning
7
No signal.0
Byte 19:Warnings 3
Table 13:Byte 19:Warnings 3
DescriptionValuePrm-Text-Def GSD fileDesignation
(process representation)
Bit
No signal (reserved).——0No signal (reserved).——1No signal (reserved).——2Warning: Loss of signal analogue input 11(91) = "Bit:Wrn input AIN
1"
Wrn input AIN 1
3No signal.0
20
PROFOX actuators
Description of the data interface Profibus DP
This manual suits for next models
3
Table of contents
Other AUMA Controllers manuals
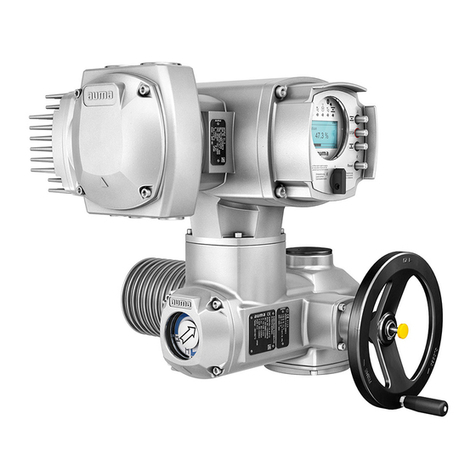
AUMA
AUMA SAVEx Series User manual
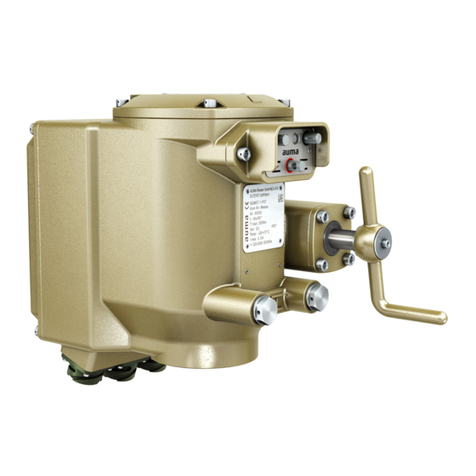
AUMA
AUMA SGM Series User manual

AUMA
AUMA SA 25.1-UW User manual
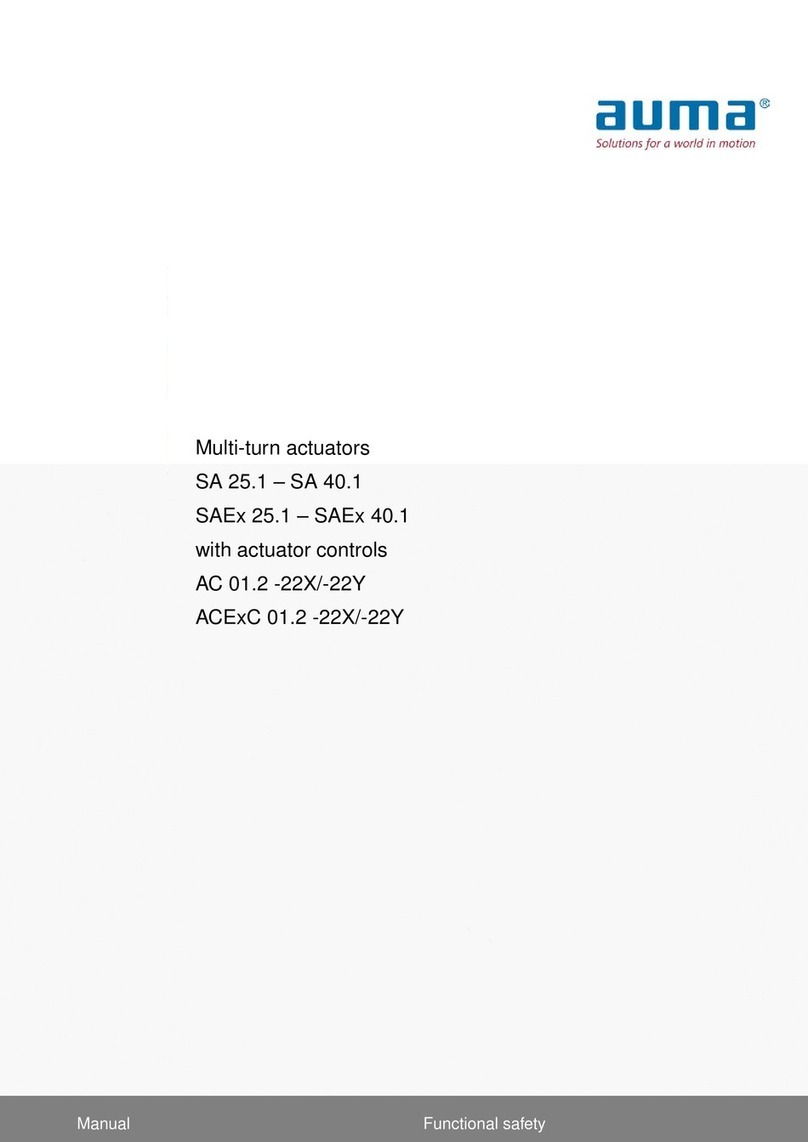
AUMA
AUMA AC 01.2-22X User manual
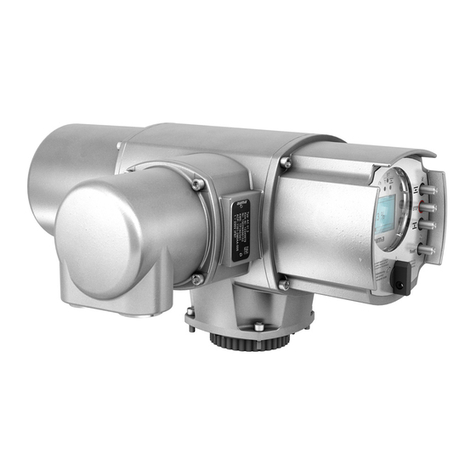
AUMA
AUMA Aumatic AC 01.1 User manual
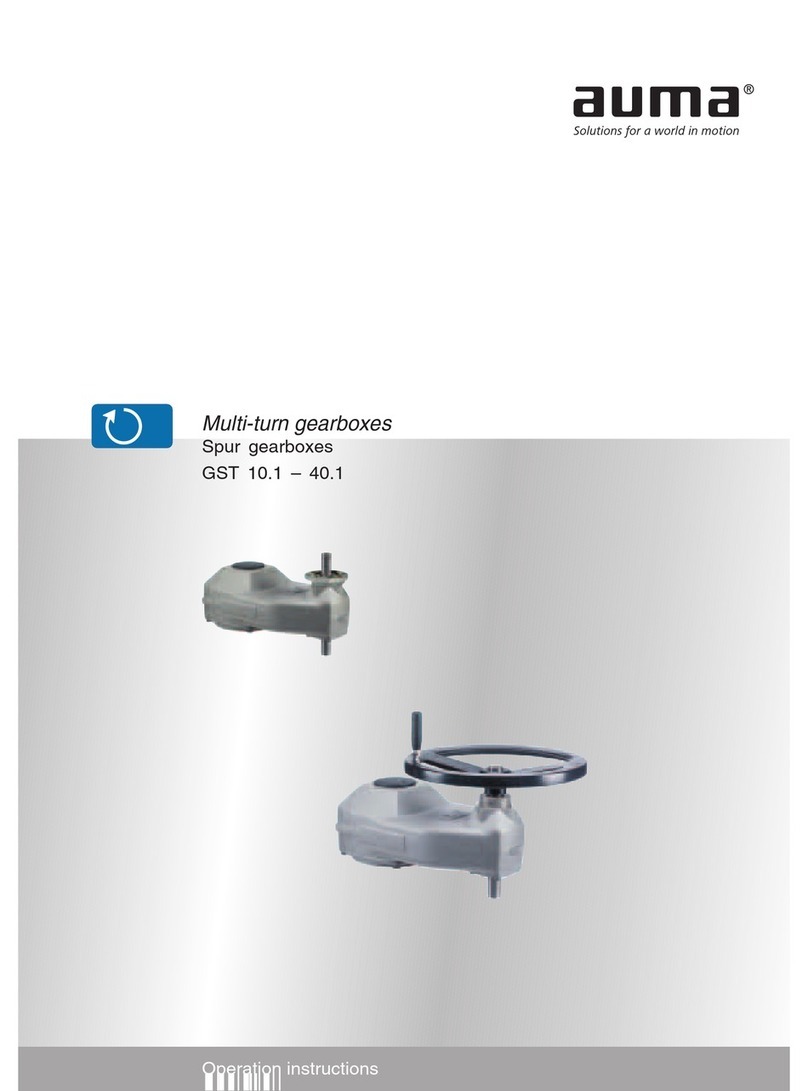
AUMA
AUMA GST 10.1 Administrator Guide
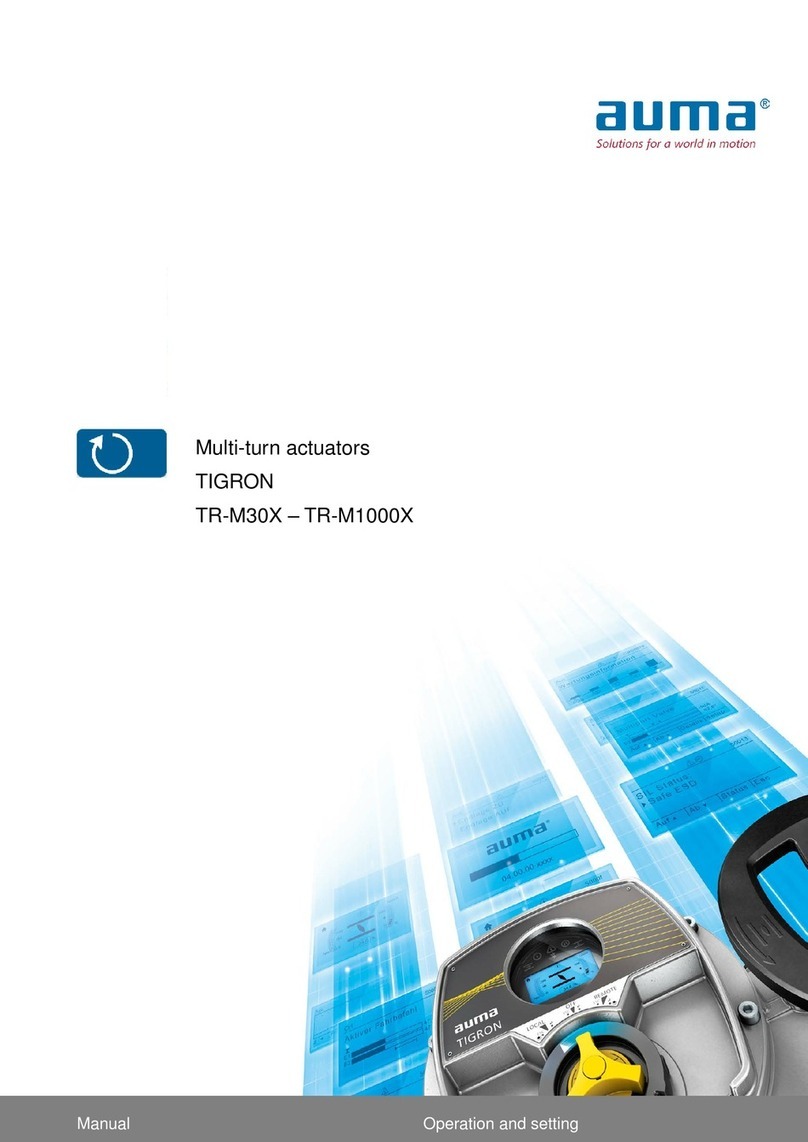
AUMA
AUMA TIGRON TR-M30X User manual
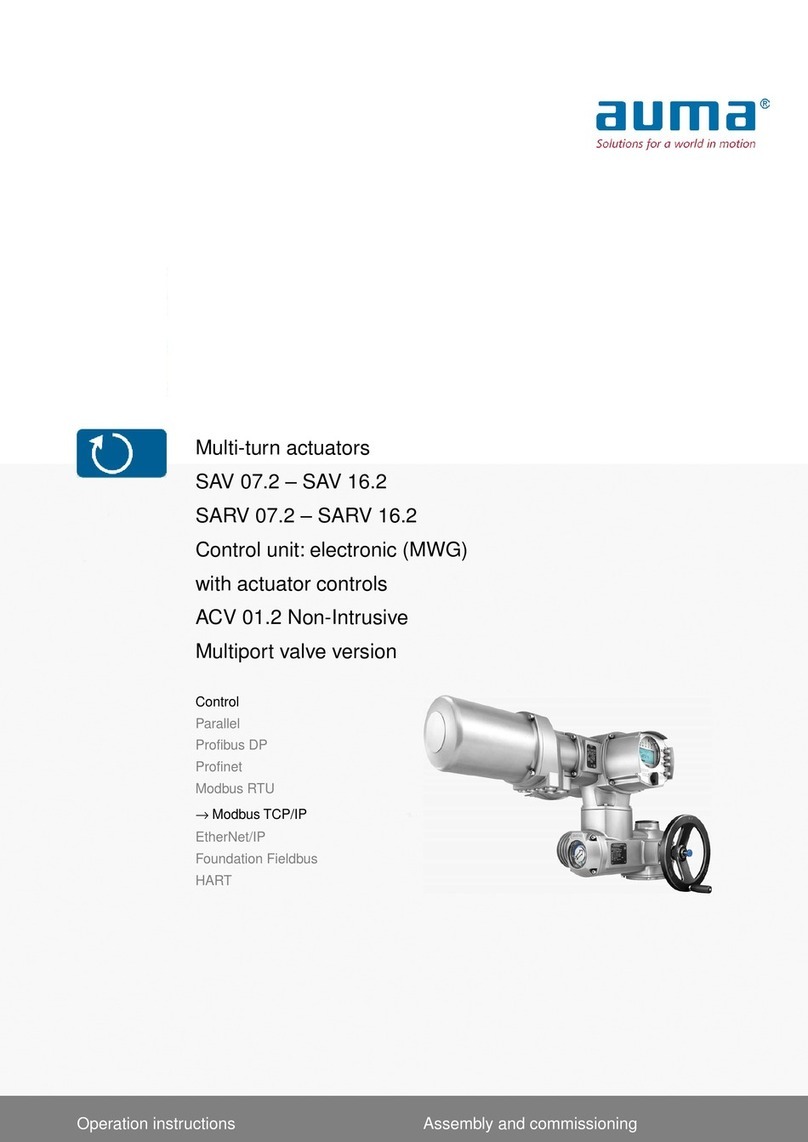
AUMA
AUMA SAV 07.2 User manual
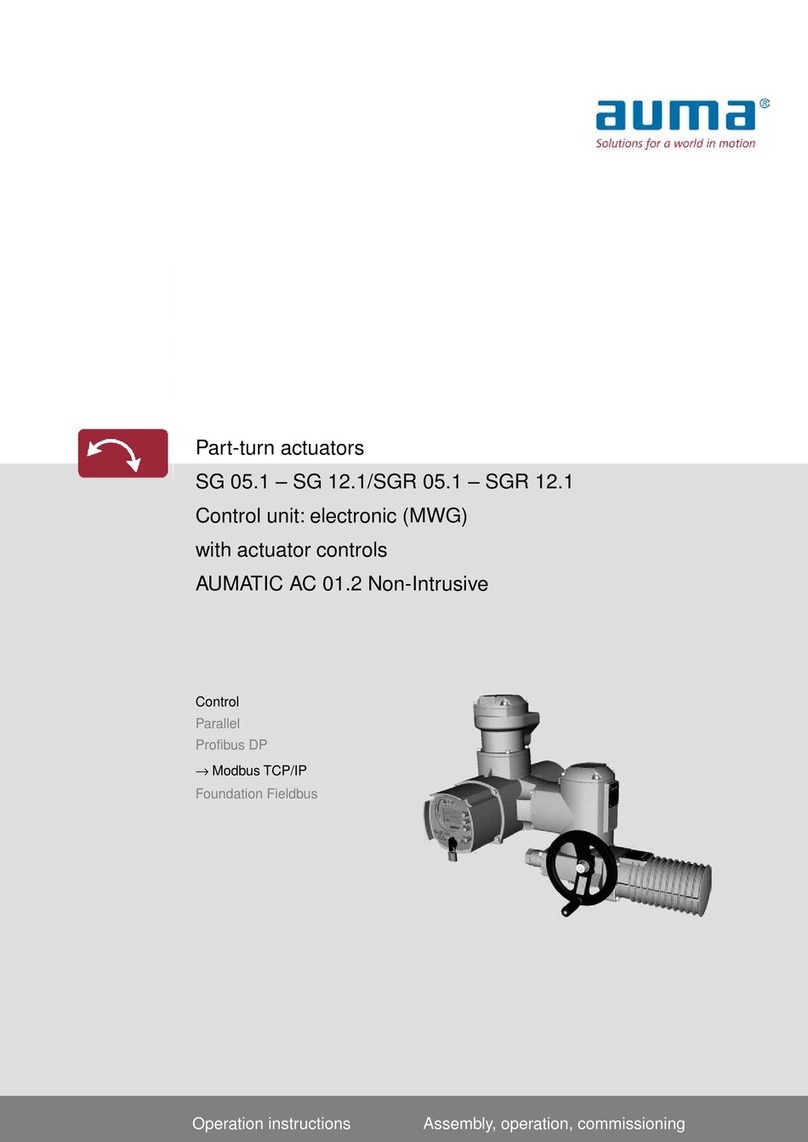
AUMA
AUMA SGR 05.1 User manual
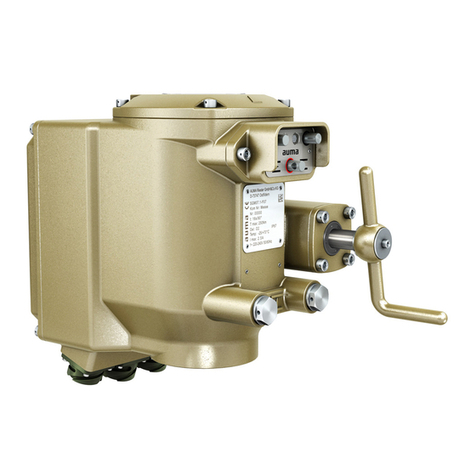
AUMA
AUMA SGM 04.1 User manual
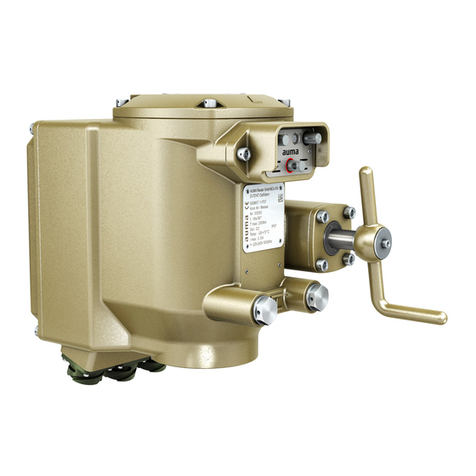
AUMA
AUMA SGM 04.1 User manual
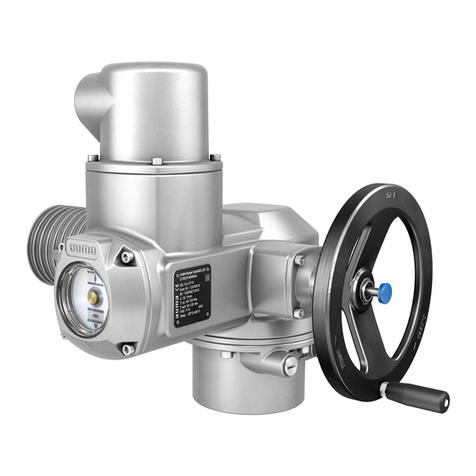
AUMA
AUMA FQM 05.1 User manual
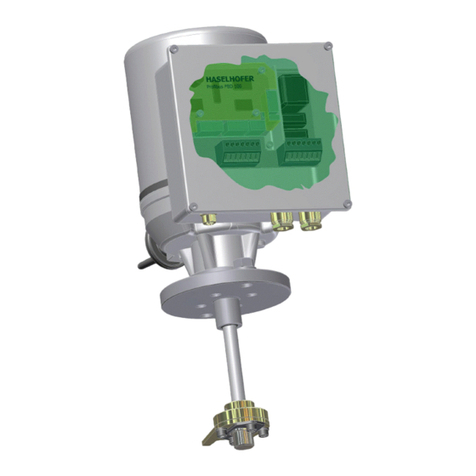
AUMA
AUMA Profibus PBD 100 User manual
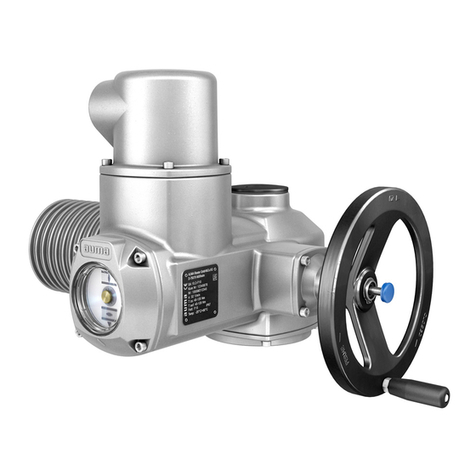
AUMA
AUMA SA 07.2 User manual
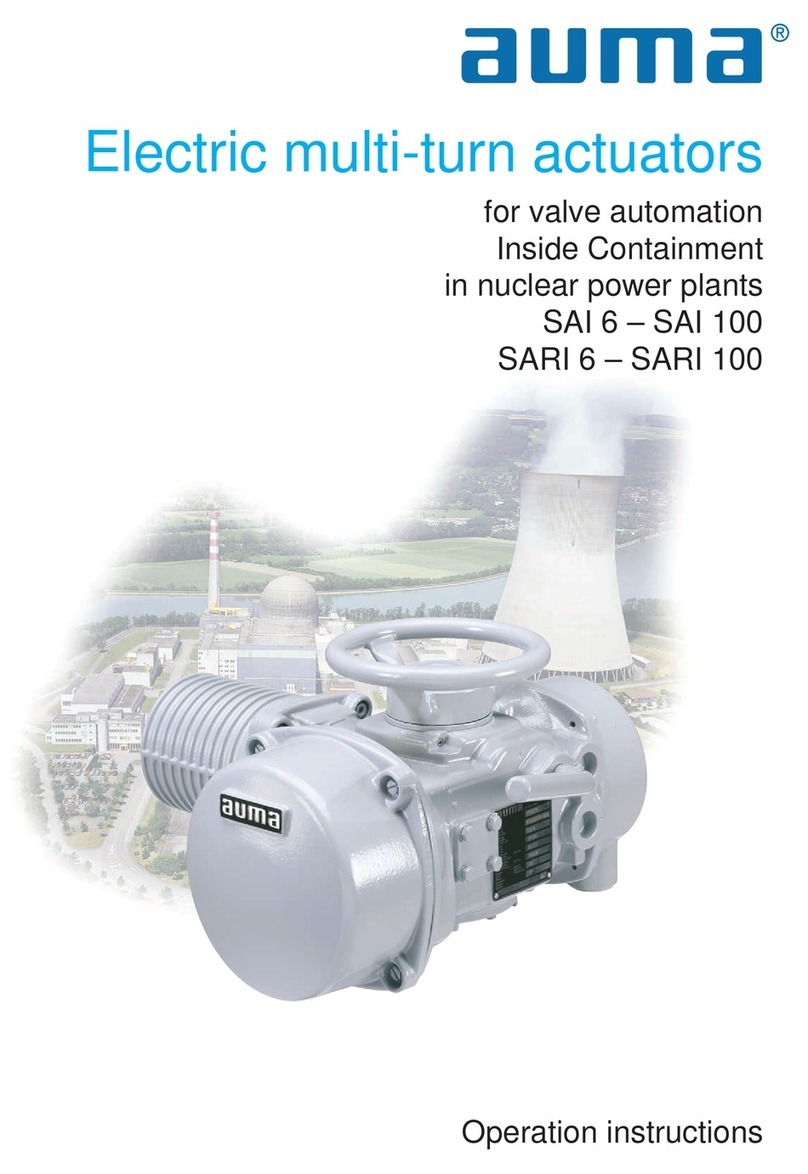
AUMA
AUMA SAI 6 User manual
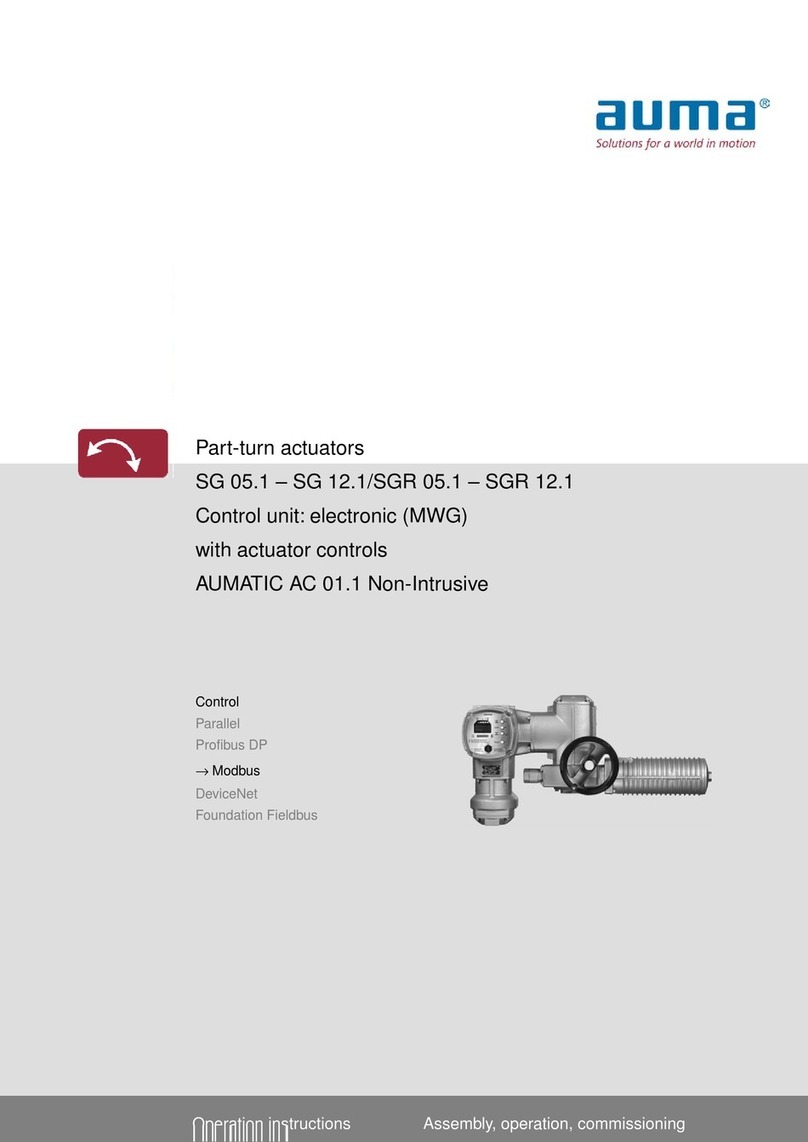
AUMA
AUMA SG 05.1 User manual
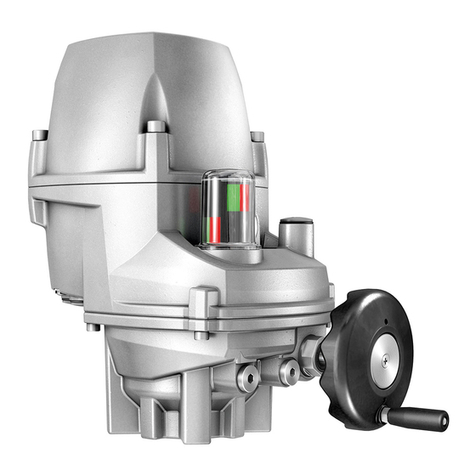
AUMA
AUMA PROFOX PF-Q80 User manual
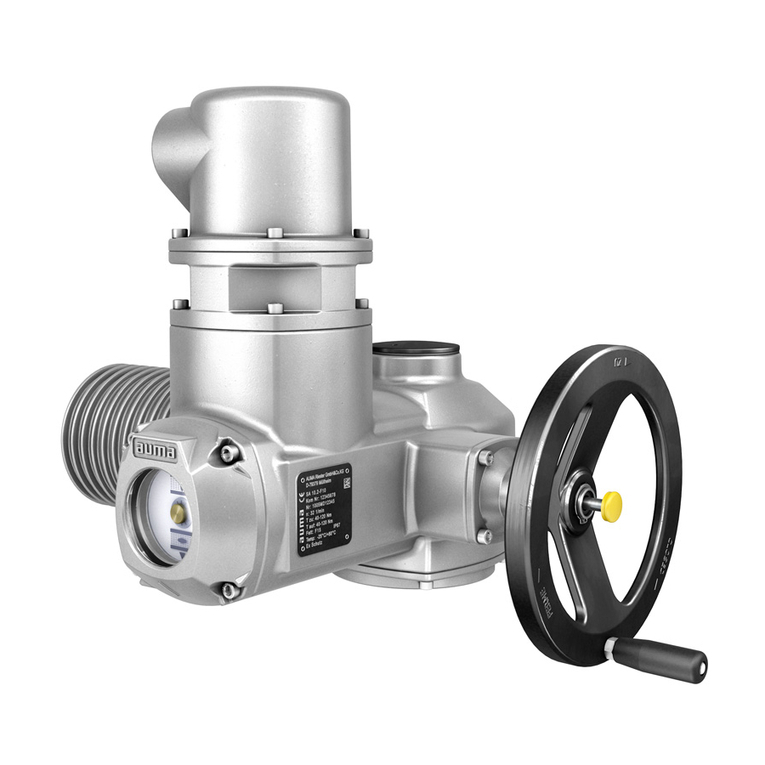
AUMA
AUMA SAEx 07.2 User manual
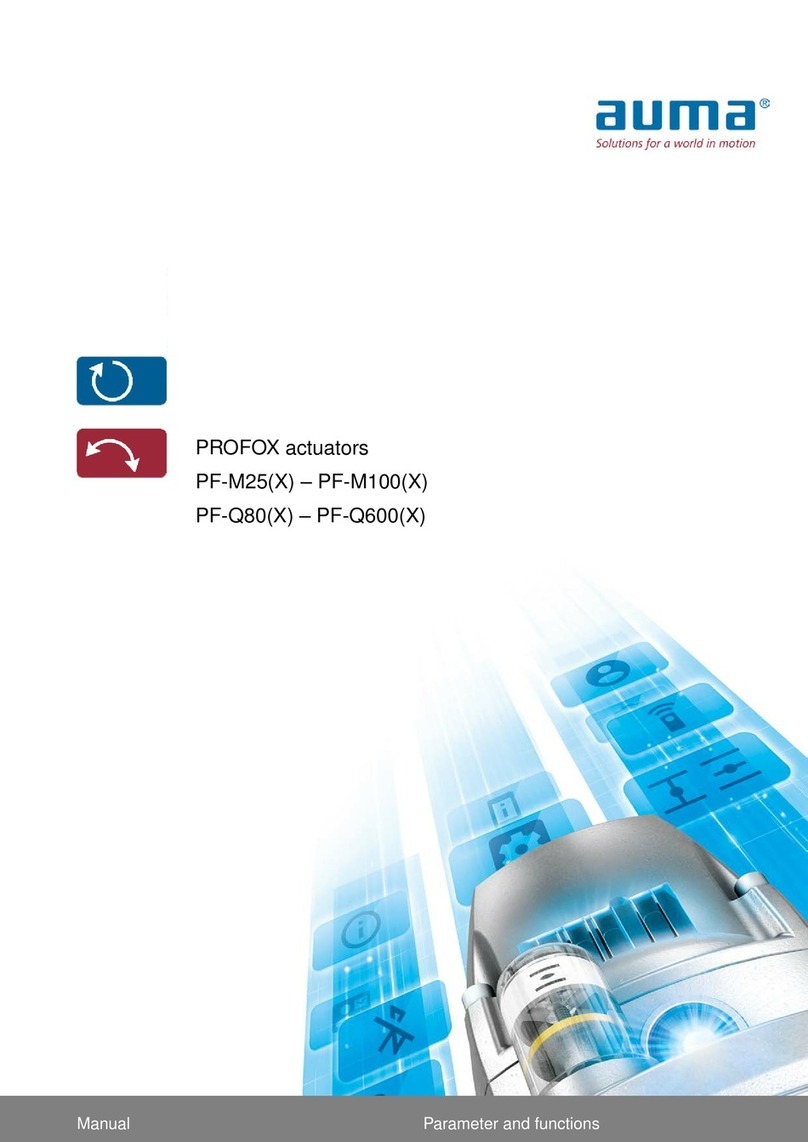
AUMA
AUMA PROFOX PF-M25X User manual
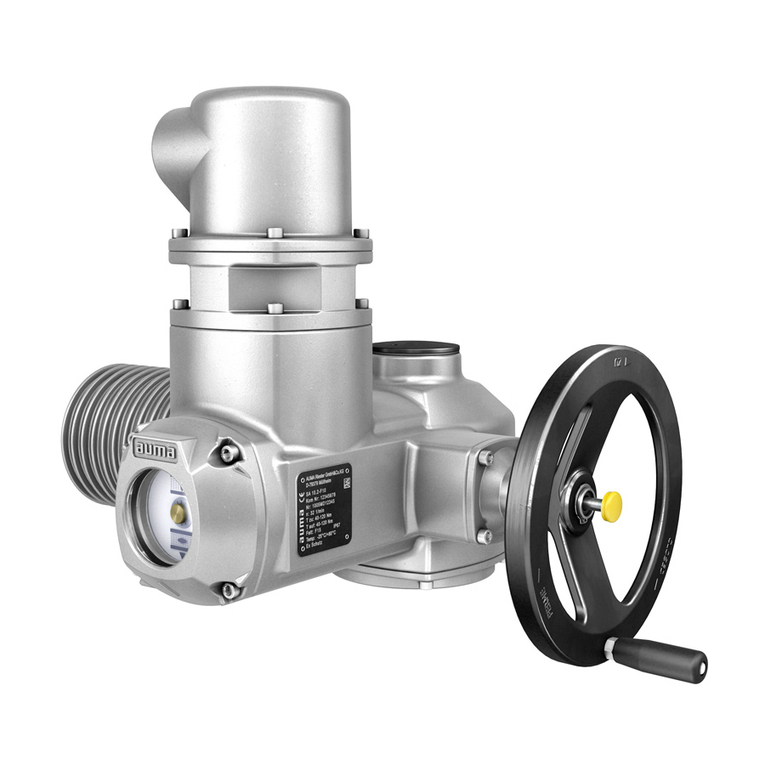
AUMA
AUMA SAEx 07.2 User manual