AXIOMATIC UMAXTC4CO User manual

USER MANUAL UMAXTC4CO
THERMOCOUPLE SCANNER,
FOUR CHANNEL
With CANopen®
USER MANUAL
P/N: AXTC4CO

Version 1.1.0 Preliminary Documentation – May be Subject to Change ii
VERSION HISTORY
Version Date Author Modifications
1.0.0 August 18, 2010 Anna Murray Initial Draft
1.1.0 January 26, 2011 Anna Murray Added new object 5555h. Updated object 1029h
defaults.
1.1.1 March 25, 2015 Amanda
Wilkins
Updated power supply spec to 12V or 24Vdc.
- July 29, 2015 Amanda
Wilkins
Added vibration compliance
ACRONYMS
AVG Average
CAN Controller Area Network
CANopen® CANopen® is a registered community trademark of CAN in Automation e.V.
CAN-ID CAN 11-bit Identifier
CJ Cold Junction
COB Communication Object
EDS Electronic Data Sheet
EMCY Emergency
LSB Least Significant Byte (or Bit)
LSS Layer Settling Service
MSB Most Significant Byte (or Bit)
MEMS Micro-electromechanical system
NMT Network Management
RO Read Only Object
RPDO Received Process Data Object
RW Read/Write Object
SDO Service Data Object
TC Thermocouple
TPDO Transmitted Process Data Object
WO Write Only Object
REFERENCES
[DS-301] CiA DS-301 V4.1 – CANopen Application Layer and Communication Profile.
CAN in Automation 2005
[DS-305] CiA DS-305 V2.0 – Layer Setting Service (LSS) and Protocols. CAN in
Automation 2006
[DS-404] CiA DS-404 V1.2 – CANopen profile for Measurement Devices and Closed
Loop Controllers. CAN in Automation 2002

Version 1.1.0 Preliminary Documentation – May be Subject to Change iii
These documents are available from the CAN in Automation e.V. website http://www.can-cia.org/.

Version 1.1.0 Preliminary Documentation – May be Subject to Change iv
TABLE OF CONTENTS
1. OVERVIEW OF THERMOCOUPLE SCANNER…………………………………..………………………… 5
1.1. Description of Thermocouple Scanner…..………………………………………..…………………. 5
1.2. Thermocouple Measurements………….……………………………………………………………... 6
1.3. Average Measurements…………………..……………………………………………………………. 8
1.4. Cold Junction Measurement..…………………………………………………………………………. 9
2. INSTALLATION INSTRUCTIONS…………………………………………………………………................ 10
2.1. Dimensions and Pinout………………………………………………………………………………… 10
2.2. Installation Instructions ……………………………………………………………………...….…….. 11
3. CANOPEN ® OBJECT DICTIONARY………………....…………………………………………………….. 14
3.1. NODE ID and BAUDRATE……………….………………………………………………………….… 14
3.1.1. LSS Protocol to Update………………..…………………………………………………………... 14
3.2. COMMUNICATION OBJECTS (DS-301 and DS-404)…….………………………………..……… 18
3.2.1. Object 1000h: Device Type…….………………………………..………………………..…........ 19
3.2.2. Object 1001h: Error Register………………..…………………..………………………..…........ 20
3.2.3. Object 1002h: Manufacturer Status Register…………………………………….….…..…........ 20
3.2.4. Object 1003h: Pre-Defined Error Field………..………………………..………………….......... 20
3.2.5. Object 100Ch: Guard Time…….………………………………..…………….…………..…........ 22
3.2.6. Object 100Dh: Lifetime Factor……………………………..……………………………..…........ 22
3.2.7. Object 1010h: Store Parameters…………………………..……………………………..…........ 23
3.2.8. Object 1011h: Restore Parameters……………………..………………………..…………........ 24
3.2.9. Object 1016h: Consumer Heartbeat Time………..………………………..….......................... 26
3.2.10. Object 1017h: Producer Heartbeat Time………..……………………………………....…........ 27
3.2.11. Object 1018h: Identity Object……………………………..……………………………..….......... 27
3.2.12. Object 1020h: Verify Configuration………………..………………………..….......................... 28
3.2.13. Object 1029h: Error Behaviour……………………………..………………………..………........ 29
3.2.14. RPDO Behaviour …………………………...……………………………..………………………. 30
3.2.15. TPDO Behaviour……………...……………………………..………………………..………........ 32
3.3. APPLICATION OBJECTS (DS-404)……..………………………………..………………………..… 34
3.3.1. Object 6100h: Thermocouple Input Field Value………………………………………………… 34
3.3.2. Object 6110h: Thermocouple Sensor Type………………….………………….……………… 35
3.3.3. Object 6112h: Thermocouple Operating Mode………………….………………….………….. 35
3.3.4. Object 6114h: ADC Sample Rate………...……………..…….………………….……………… 36
3.3.5. Object 6126h: Thermocouple Scaling Factor………………….………………….……………. 37
3.3.6. Object 6127h: Thermocouple Scaling Offset………………….………………….…………….. 37
3.3.7. Object 7130h: Thermocouple Input Process Value………………….………………….……… 38
3.3.8. Object 6150h: Thermocouple Status……….………………….………………….……………… 38

Version 1.1.0 Preliminary Documentation – May be Subject to Change v
3.4. MANUFACTURER OBJECTS……..………………………………..………………………..……….. 40
3.4.1. Object 2000h: Cold Junction Auto-Correct…..………………………………..………………… 40
3.4.2. Object 2010h: Thermocouple Microvolts……………………..…..……………………………... 41
3.4.3. Object 2100h: Average Input Field Value……………………..…..…………………………….. 41
3.4.4. Object 2112h: Average Operating Mode………………….………………….………………….. 42
3.4.5. Object 2126h: Average Scaling Factor………………….………………….……………………. 43
3.4.6. Object 2127h: Average Scaling Offset………………….………………….…………………….. 44
3.4.7. Object 2130h: Average Input Process Value………………….………………….…………….. 45
3.4.8. Object 3100h: Cold Junction Input Field Value……………………..…..…………………….… 46
3.4.9. Object 3126h: Cold Junction Scaling Factor………………….………………….……………… 46
3.4.10. Object 3127h: Cold Junction Scaling Offset………………….………………….……………… 46
3.4.11. Object 3130h: Cold Junction Input Process Value………………….………………….………. 47
3.4.12. Object 4000h: Low Temperature Warning Threshold………………………………………….. 47
3.4.13. Object 4010h: High Temperature Warning Threshold………………………………………….. 48
3.4.14. Object 4020h: High Temperature Shutdown Threshold……………………………………….. 49
3.4.15. Object 4030h: Error React Delay………………….………………….………………………….. 49
3.4.16. Object 5000h: Power Supply Measured………………….………………….………………….. 50
3.4.17. Object 5010h: ADC Filter Frequency….………………….………………….………………….. 50
3.4.18. Object 5555h: Start in Operational……..………………….………………….………………….. 51
4. USING RS-232 WITH TERA TERM ………………………………………………………………………….. 52
4.1. Main Menu Options………….……………………………………………………………..….….……. 53
4.1.1. V – View Object Dictionary………………………………………………………………………... 54
4.1.2. D – Default Object Dictionary…………………………………………………………………….. 55
4.1.3. T – Toggle RS-232 Stream Off/On………………………………………………………………. 55
4.1.4. S – Show/Stop Diagnostics……………………………………………………………………….. 56
4.1.5. L – Load New Software………………………………………………………………………........ 56
APPENDIX A – Technical Specifications………………………………………………………………..….…. A
LIST OF FIGURES
1. Thermocouple Input Block Diagram…………………………………………………………………………… 6
2. Average Measurement Block Diagram………………………………………………………………………... 8
3. Cold Junction Measurement Block Diagram………………………………………………………………….. 9
LIST OF TABLES
1. LSS Baudrate Indexes…………………………………………………………………………........................ 16
2. Error Descriptions…………………………………………………………………………............................... 21
3. EMCY Error Codes…………………………………………………………………………............................. 21
4. Supported Thermocouple Types…………………………………………………………………………........ 35
5. Thermocouple Status Values………………………………………………………………………….............. 38

UMAXTC20CO V1.1.1 Preliminary Documentation – May be Subject to Change 6-59
1. OVERVIEW OF THERMOCOUPLE SCANNER
1.1. Description of Thermocouple Scanner
The following User Manual describes the architecture and functionality of a four channel CANopen
® thermocouple scanner.
There are four channels on the TC4, each with three pins at the connector for +ve, -ve and shield
connections. All channels are fully isolated from each other, the CAN lines, and from the power
supply. All channels are sampled simultaneously at a rate of 5 scans/second (200ms update rate).
The power supply was designed for a wide range of nominal inputs of 12V or 24V and will provide
proper operation from 9 to 36Vdc.
Temperature is measured in ºC, with up to a 0.001ºC resolution. Each channel can be individually
configured to measure J, K or T type thermocouples. When installed properly, as described in
section 2.2, the scanner will send temperatures with +/- 1ºC accuracy.
A very precise analog-to-digital converter, with a programmable gain, measures the thermocouple
input voltage. As the voltage changes, the controller will adjust the gain accordingly to get the best
resolution and accuracy of the signal. For rapid changes at the input, such as an open-circuit, it
may take a couple of scans before the appropriate range is found. Since there are 8 possible
gains, an open-circuit (measured using the lowest gain) can take up to 1.6 seconds to be flagged,
if the last 'good' input was in the highest gain range.
Another feature of the ADC is that it has a programmable rejection mode for either 50Hz or 60Hz. It
provides better than 110dB normal mode rejection of the line frequency and all its harmonics.
The scanner has a built in sensor for measuring the cold junction temperature and automatically
applies the correction to the reported thermocouple temperature. The operator has the option of
disabling the automatic cold-junction compensation.
If desired, the average temperature of all the active channels, or all channels from a block of two,
can be broadcasted to the network using the Average Input function block. This feature is
described in detail in section 1.3.
On power-up, the AXTC4CO will immediately send the bootup message to the network. However,
in ordered to prevent erroneous readings before all the data from all channels have been read
correctly, the unit will only start broadcasting diagnostic data after 3 seconds have elapsed, and
will not enter “Operational” mode during this period.
The scanner can be used to flag low temperature warnings, high temperature warnings, or high
temperature shutdowns. It will also detect and flag open circuits on the sensor wires.

UMAXTC20CO V1.1.1 Preliminary Documentation – May be Subject to Change 7-59
1.2. Thermocouple Measurements
Figure 1 – Thermocouple Input Block Diagram
The block diagram shown in Figure 1 capture the objects associated with each thermocouple
channel. Each channel, 1 through 4, operates in the same fashion as described below.
Objects $2000 Cold Junction Auto Correct, $6110 Thermocouple Sensor Type and $6112
Thermocouple Operating Mode determine how the scanner processes the raw microvolt reading
and converts it into a temperature value in degrees Celsius, which is written to read-only object
$6100 Thermocouple Input Field Value.
Objects $6126 Thermocouple Scaling Factor and $6127 Thermocouple Scaling Offset are
used to convert the field value to read-only object $7130 Thermocouple Input Process Value,
which is mapped to TPDO1 by default.
The formula to convert the field value (FV) to process value (PV) is:
Process Value = (Field Value * Scaling Factor) + Scaling Offset
While the FV is a real number, containing the temperature in °C, the PV is a 16-bit integer value.
The default scaling has been selected such that the PV will send the temperature with a resolution
of 0.0625 °C/bit and a offset of -273°C. [Scaling Factor = 16, Offset = 4368] Since the maximum
temperature the scanner can measure for a thermocouple is 1735°C, this means the range of the
PV data will be 0 to 32123 (-273°C to 1735°C.)
Alternatively, it may be desired to send the temperature in Fahrenheit with a 0.1°F resolution per
bit. In this case, the Scaling Factor would be set to 18, and the Offset to 320. Other scaling can be
selected as desired by the user.

UMAXTC20CO V1.1.1 Preliminary Documentation – May be Subject to Change 8-59
In all cases, certain values will be ‘plugged’ into the PV object to indicate various conditions.
Should the associated thermocouple be disabled by object $6112, then the value in the PV will
always be -1 (0xFFFF). Alternatively, should the scanner detect an open circuit on the sensor, then
the PV value will be set to -512 (0xFE00).
In the open-circuit error condition mentioned above, the associated object $6150 Thermocouple
Status will also be updated to reflect the problem. Other faults that the scanner can detect and flag
are determined by the values in objects $4000 Low Temperature Warning Threshold, $4010
High Temperature Warning Threshold and $4020 High Temperature Shutdown Threshold.
The threshold values are always measured with respect to the field value, and have a fixed
resolution of 0.1°C/bit. For example, a value of 1250 in object $4010 means that any measured
temperature greater than or equal to 125°C will flag a high temperature warning. The fault
detection thresholds also have a fixed 1°C built-in hysteresis to clear them. In the example above,
the temperature would have to drop below 124°C to clear the fault once it has been set.
Finally, in order to prevent flooding the network with emergency messages when the temperature
hovers around a warning threshold, the object $4030 Error React Delay allows the user to select
how long the fault condition must be present before the status object is updated and the error
reaction is triggered.
Once the status object shows that the FV value is not longer valid, the object $1003 Pre-Defined
Error Field is updated to reflect the appropriate emergency error code and additional information.
Since both a high temperature warning and shutdown could be active at the same time, object
$1003 could have up to 40 entries at any given time. Also, when a sensor error is activated, the
controller will react as specified in object $1029 Error Behaviour.
The error values loaded in the status object $6150 are described in Table 5, while the associated
emergency fields that are loaded into object $1003 are outlined in Table 3.
A couple of other miscellaneous objects associated with the thermocouple channels are two read-
only objects $2010 Thermocouple Microvolts and $6114h ADC Sampling Rate. Both of these
objects are associated directly with the ADC chip used to measure the thermocouples and cold
junction voltages. As channels are disabled, object $6114 is automatically updated by the
controller to reflect approximately how many milliseconds will elapse between each scan of a
particular channel. Object $2010 is available for debugging purposes.
Lastly, object $5010 ADC Filter Frequency is a single value (non-array) that sets the rejection
filter frequency used by the analog-to-digital converter. The only permissible values in this case are
either 50Hz (i.e. Europe) or 60Hz (i.e. North America.)

UMAXTC20CO V1.1.1 Preliminary Documentation – May be Subject to Change 9-59
1.3. Average Measurements
Figure 2 – Average Measurement Block Diagram
There are three types of average values that can be measured and broadcasted on a TPDO.
a) Average of Bank 1 sensors (thermocouples 1 and 2, active only)
b) Average of Bank 2 sensors (thermocouples 3 and 4, active only)
c) Average of all sensors (active only)
Object $2112 Average Operating Mode determines if the average value of any of the above will
be enabled. When enabled by selecting “Normal Operation”, the average of all active channels is
calculated and written to read-only object $2100 Average Input Field Value in degrees Celsius. If
a thermocouple channel is disabled or open circuited then the value in the FV object is not counted
in the average calculation.
As with the thermocouple inputs, the average FV can be converted to a process value using
scaling objects $2126 Average Scaling Factor and $2127 Average Scaling Offset. The formula
to convert to read-only object $2130 Average Input Process Value is the same as describe in
section 1.2.
By default, all averages are enabled and the calculated PVs can be sent on TPDO2.

UMAXTC20CO V1.1.1 Preliminary Documentation – May be Subject to Change 10-59
1.4. Cold Junction Measurements
Figure 3 – Cold Junction Measurement Block Diagram
The cold junction value is measured from an on-board temperature sensor and used in the
thermocouple temperature calculations. By default, the value measured can be broadcasted on
TPDO2.
The measured cold junction temperature is written to read-only object $3100 Cold Junction Input
Field Value in degrees Celsius. As with the thermocouple inputs, the average FV can be
converted to a process value using scaling objects $3126 Cold Junction Scaling Factor and
$3127 Cold Junction Scaling Offset. The formula to convert to read-only object $3130 Cold
Junction Input Process Value is the same as describe in section 1.2.
The supply voltage powering the scanner is written to read-only object $5000 Power Supply
Measured, which can be mapped to a TPDO object, but by default it is not.

UMAXTC20CO V1.1.1 Preliminary Documentation – May be Subject to Change 11-59
2. INSTALLATION INSTRUCTIONS
2.1. Dimensions and Pinout
Grey Connector Black Connector
Pin # Function Pin # Function
1 RS-232 GND 1 Thermocouple 1 +
2 RS-232 TXD 2 Thermocouple 1 -
3 RS-232 RXD 3 Thermocouple 1 Shield
4 Not Used (plug) 4 Thermocouple 2 +
5 Frame GND 5 Thermocouple 2 -
6 Batt - 6 Thermocouple 2 Shield
7 Batt + 7 Thermocouple 3 Shield
8 Not Used (plug) 8 Thermocouple 3 -
9 Not Used (plug) 9 Thermocouple 3 +
10 CAN_L 10 Thermocouple 4 Shield
11 CAN_H 11 Thermocouple 4 -
12 CAN Shield 12 Thermocouple 4 +
Note: The Frame GND must be connected to the machine chassis.

UMAXTC20CO V1.1.1 Preliminary Documentation – May be Subject to Change 12-59
2.2. Installation Instructions
NOTES & WARNINGS
Do not install near high-voltage or high-current devices.
Ground the chassis for safety purposes and proper EMI shielding.
Note the operating temperature range. All field wiring must be suitable for that temperature
range.
Install the unit with appropriate space available for servicing and for adequate wire harness
access (15 cm) and strain relief (30 cm).
Do not connect or disconnect the unit while the circuit is live, unless the area is known to be
non-hazardous.
MOUNTING
The module is designed for mounting on the engine. If it is mounted without an enclosure, the
Thermocouple Scanner should be mounted horizontally with connectors facing left or right, or with
the connectors facing down, to reduce likelihood of moisture entry.
The thermocouple wires and CAN communication cable are considered intrinsically safe. The
power wires are not considered intrinsically safe.
Mask all labels if the unit is to be repainted, so label information remains visible.
Mounting legs include holes sized for M6 or ¼ inch bolts. The bolt length will be determined by the
end-user’s mounting plate thickness. Typically 20 mm (3/4 inch) is adequate.
If the module is mounted off-engine, no wire or cable in the harness should exceed 30 meters in
length. The power input wiring should be limited to 10 meters.
CONNECTIONS
Use the following Deutsch IPD mating plugs to connect to the integral receptacles. Wiring to these
mating plugs must be in accordance with all applicable local codes. Suitable field wiring for the
rated voltage and current must be used. The rating of the connecting cables must be at least
85°C. For ambient temperatures below –10°C and above +70°C, use field wiring suitable for both
minimum and maximum ambient temperature.
Receptacle
Mating Sockets as appropriate
(Refer to www.laddinc.com for more information on the
contacts available for this mating plug.)
Power and CAN bus: DTM06-12SA and wedge WM12S
Thermocouple Interface Receptacle: DTM06-12SB and wedge WM12S

UMAXTC20CO V1.1.1 Preliminary Documentation – May be Subject to Change 13-59
NOISE – ELECTRICAL CONNECTIONS
To reduce noise, separate all thermocouple wires from power wires. Shielded thermocouple wires
will protect against ignition and injector noise.
GROUNDING
To improve the scanners immunity to EMI noise, the Frame GND pin on the grey receptacle should
be connected to a chassis ground. All chassis grounding should go to a single ground point
designated for the engine and all related equipment.
The ground strap that provides a low impedance path for EMI should be a ½ inch wide, flat, hollow
braid, no more than 12 inches long with a suitable sized ring lug for the module’s grounding lug.
SHIELDING
The thermocouple and CAN wiring should be shielded using a twisted conductor pair. All
thermocouple wire shields should be terminated to the associated Shield GND pin on the black
connector. The thermocouple wires should not be exposed for more than 50 m (2 inches) without
shielding. The shield may be cut off at the thermocouple end as it does not require termination at
that end.
Shields can be AC grounded at one end and hard grounded at the opposite end to improve
shielding effectiveness.
If the module is installed in a cabinet, shielded wiring can be terminated at the cabinet (earth
ground), at the entry to the cabinet or at the Thermocouple Scanner.
INPUT POWER
The main input to the power supply must be of low-impedance type for proper operation. If
batteries are used, an alternator or other battery-charging device is necessary to maintain a stable
supply voltage.
Central suppression of any surge events should be provided at the system level.
The installation of the equipment must include overcurrent protection between the power source
and the Thermocouple Scanner by means of a series connection of properly rated fuses or circuit
breakers. Input power switches must be arranged external to the Thermocouple Scanner.
The power input wiring should be limited to 10 meters.
Note the operating temperature range. All field wiring must be suitable for that temperature range.
THERMOCOUPLE INPUT WIRING
Wiring for the thermocouple input must be shielded cable, 16 or 18 AWG. Cable lengths should be
less than 30 meters. Shielding should be unbroken.

UMAXTC20CO V1.1.1 Preliminary Documentation – May be Subject to Change 14-59
CAN WIRING
The CAN port is electrically isolated from all other circuits. The isolation is SELV rated with respect
to product safety requirements. Refer to the CAN 2.0B specification for more information.
Shielded CAN cable is required. The Thermocouple Scanner provides the CAN port shield
connection ac coupled to the Frame Ground pin on the connector.
NETWORK CONSTRUCTION
Axiomatic recommends that multi-drop networks be constructed using a “daisy chain” or
“backbone” configuration with short drop lines.
TERMINATION
It is necessary to terminate the network; therefore an external CAN termination is required. No
more than two network terminators should be used on any one single network. A terminator is a
121Ω, 0.25 W, 1% metal film resistor placed between CAN_H and CAN_L terminals at the end two
nodes on a network.

UMAXTC20CO V1.1.1 Preliminary Documentation – May be Subject to Change 15-59
3. CANOPEN ® OBJECT DICTIONARY
The CANopen object dictionary of the Thermocouple Scanner is based on CiA device profile DS-
404 V1.2 (device profile for Thermocouple Scanners). The object dictionary includes
Communication Objects beyond the minimum requirements in the profile, as well as several
manufacturer-specific objects for extended functionality.
3.1. NODE ID and BAUDRATE
By default, the Thermocouple Scanner ships factory programmed with a Node ID = 127 (0x7F) and
with Baudrate = 125 kbps.
3.1.1. LSS Protocol to Update
The only means by which the Node-ID and Baudrate can be changed is to use Layer Settling
Services (LSS) and protocols as defined by CANopen ® standard DS-305.
Follow the steps below to configure either variable using LSS protocol. If required, please refer to
the standard for more detailed information about how to use the protocol.
3.1.1.1. Setting Node-ID
Set the module state to LSS-configuration by sending the following message:
Item Value
COB-ID 0x7E5
Length 2
Data 0 0x04 (cs=4 for switch state global)
Data 1 0x01 (switches to configuration state)
Set the Node-ID by sending the following message:
Item Value
COB-ID 0x7E5
Length 2
Data 0 0x11 (cs=17 for configure node-id)
Data 1 Node-ID (set new Node-ID as a hexadecimal number)
The module will send the following response (any other response is a failure):
Item Value
COB-ID 0x7E4
Length 3
Data 0 0x11 (cs=17 for configure node-id)
Data 1 0x00
Data 2 0x00

UMAXTC20CO V1.1.1 Preliminary Documentation – May be Subject to Change 16-59
Save the configuration by sending the following message:
Item Value
COB-ID 0x7E5
Length 1
Data 0 0x17 (cs=23 for store configuration)
The module will send the following response (any other response is a failure):
Item Value
COB-ID 0x7E4
Length 3
Data 0 0x17 (cs=23 for store configuration)
Data 1 0x00
Data 2 0x00
Set the module state to LSS-operation by sending the following message:
(Note, the module will reset itself back to the pre-operational state)
Item Value
COB-ID 0x7E5
Length 2
Data 0 0x04 (cs=4 for switch state global)
Data 1 0x00 (switches to waiting state)
3.1.1.2. Setting Baudrate
Set the module state to LSS-configuration by sending the following message:
Item Value
COB-ID 0x7E5
Length 2
Data 0 0x04 (cs=4 for switch state global)
Data 1 0x01 (switches to configuration state)
Set the baudrate by sending the following message:
Item Value
COB-ID 0x7E5
Length 3
Data 0 0x13 (cs=19 for configure bit timing parameters)
Data 1 0x00 (switches to waiting state)
Data 2 Index (select baudrate index per table 4)

UMAXTC20CO V1.1.1 Preliminary Documentation – May be Subject to Change 17-59
Index Bit Rate
0 1 Mbit/s
1 800 kbit/s
2 500 kbit/s
3 250 kbit/s
4 125 kbit/s (default)
5 reserved (100 kbit/s)
6 50 kbit/s
7 20 kbit/s
8 10 kbit/s
Table 1 – LSS Baudrate Indexes
The module will send the following response (any other response is a failure):
Item Value
COB-ID 0x7E4
Length 3
Data 0 0x13 (cs=19 for configure bit timing parameters)
Data 1 0x00
Data 2 0x00
Activate bit timing parameters by sending the following message:
Item Value
COB-ID 0x7E5
Length 3
Data 0 0x15 (cs=19 for activate bit timing parameters)
Data 1 <delay_lsb>
Data 2 <delay_msb>
The delay individually defines the duration of the two periods of time to wait until the bit timing
parameters switch is done (first period) and before transmitting any CAN message with the new bit
timing parameters after performing the switch (second period). The time unit of switch delay is 1
ms.
Save the configuration by sending the following message (on the NEW baudrate):
Item Value
COB-ID 0x7E5
Length 1
Data 0 0x17 (cs=23 for store configuration)

UMAXTC20CO V1.1.1 Preliminary Documentation – May be Subject to Change 18-59
The module will send the following response (any other response is a failure):
Item Value
COB-ID 0x7E4
Length 3
Data 0 0x17 (cs=23 for store configuration)
Data 1 0x00
Data 2 0x00
Set the module state to LSS-operation by sending the following message:
(Note, the module will reset itself back to the pre-operational state)
Item Value
COB-ID 0x7E5
Length 2
Data 0 0x04 (cs=4 for switch state global)
Data 1 0x00 (switches to waiting state)
The following screen capture (left) shows the CAN data was sent (7E5h) and received (7E4h) by
the tool when the baudrate was changed to 250 kbps using the LSS protocol. The other image
(right) shows what was printed on the debug RS-232 menu while the operation took place.
Between CAN Frame 98 and 99, the baudrate on the CAN Scope tool was changed from 125 to
250 kbps.

UMAXTC20CO V1.1.1 Preliminary Documentation – May be Subject to Change 19-59
3.2. COMMUNICATION OBJECTS (DS-301 and DS-404)
The communication objects supported by the Thermocouple Scanner are listed in the following
table. A more detailed description of some of the objects is given in the following subchapters.
Only those objects that have device-profile specific information are described. For more
information on the other objects, refer to the generic CANopen protocol specification DS-301.
Index
(hex) Object Object Type Data Type Access PDO
Mapping
1000 Device Type VAR UNSIGNED32 RO No
1001 Error Register VAR UNSIGNED8 RO No
1002 Manufacturer Status Register VAR UNSIGNED32 RO No
1003 Pre-Defined Error Field ARRAY UNSIGNED32 RO No
100C Guard Time VAR UNSIGNED16 RW No
100D Life Time Factor VAR UNSIGNED8 RW No
1010 Store Parameters ARRAY UNSIGNED32 RW No
1011 Restore Default Parameters ARRAY UNSIGNED32 RW No
1016 Consumer Heartbeat Time ARRAY UNSIGNED32 RW No
1017 Producer Heartbeat Time VAR UNSIGNED16 RW No
1018 Identity Object RECORD RO No
1020 Verify Configuration ARRAY UNSIGNED32 RW No
1029 Error Behaviour ARRAY UNSIGNED8 RW No
1400 RPDO1 Communication Parameter RECORD RW No
1401 RPDO2 Communication Parameter RECORD RW No
1402 RPDO3 Communication Parameter RECORD RW No
1403 RPDO4 Communication Parameter RECORD RW No
1600 RPDO1 Mapping Parameter RECORD RO No
1601 RPDO2 Mapping Parameter RECORD RO No
1602 RPDO3 Mapping Parameter RECORD RO No
1603 RPDO4 Mapping Parameter RECORD RO No
1800 TPDO1 Communication Parameter RECORD RW No
1801 TPDO2 Communication Parameter RECORD RW No
1802 TPDO3 Communication Parameter RECORD RW No
1803 TPDO4 Communication Parameter RECORD RW No
1A00 TPDO1 Mapping Parameter RECORD RW No
1A01 TPDO2 Mapping Parameter RECORD RW No
1A02 TPDO3 Mapping Parameter RECORD RW No
1A03 TPDO4 Mapping Parameter RECORD RW No
Per the CANopen ® standard DS-301, the following procedure shall be used for re-mapping, and is
the same for both RPDOs and TPDOs.
a) Destroy the PDO by setting bit exists (most significant bit) of sub-index 01h of the according
PDO communication parameter to 1b
b) Disable mapping by setting sub-index 00h of the corresponding mapping object to 0
c) Modify the mapping by changing the values of the corresponding sub-indices
d) Enable mapping by setting sub-index 00h to the number of mapped objects
e) Create the PDO by setting bit exists (most significant bit) of sub-index 01h of the according
PDO communication parameter to 0b

UMAXTC20CO V1.1.1 Preliminary Documentation – May be Subject to Change 20-59
3.2.1. Object 1000h: Device Type
This object contains information about the device type as per device profile DS-404. The 32-bit
parameter is divided into two 16-bit values, showing General and Additional information as shown
below.
MSB LSB
Additional Information = 0x1002 General Information = 0x0194 (404)
DS-404 defines the Additional Information field in the following manner:
0000h = reserved
0001h = digital input block
0002h = analog input block
0004h = digital output block
0008h = analog output block
0010h = controller block
0020h = alarm block
0040h … 0800h = reserved
1000h ... 8000h = manufacturer-specific
The 0x10 in the MSB of the additional information indicates that this is the first CANopen ®
Thermocouple Scanner that has been manufactured by Axiomatic. The 0x02 in the LSB indicates
that this module supports analog input blocks.
Object Description
Index 1000h
Name Device Type
Object Type VAR
Data Type UNSIGNED32
Entry Description
Access RO
PDO Mapping No
Value Range 0x10020194
Default Value 0x10020194
This manual suits for next models
1
Table of contents
Other AXIOMATIC Measuring Instrument manuals
Popular Measuring Instrument manuals by other brands
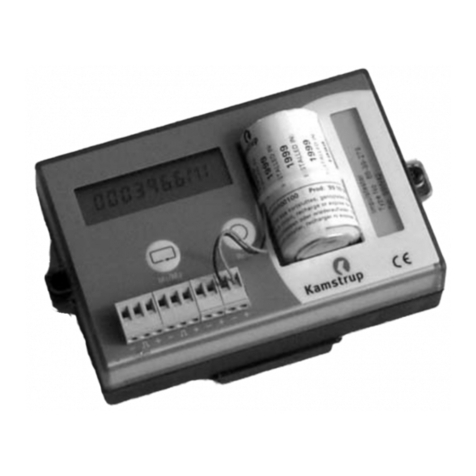
Kamstrup
Kamstrup 66-99-279 Operator's guide
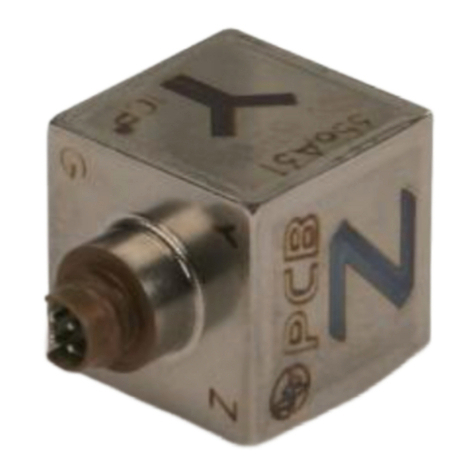
PCB Piezotronics
PCB Piezotronics TLD356A32 Installation and operating manual
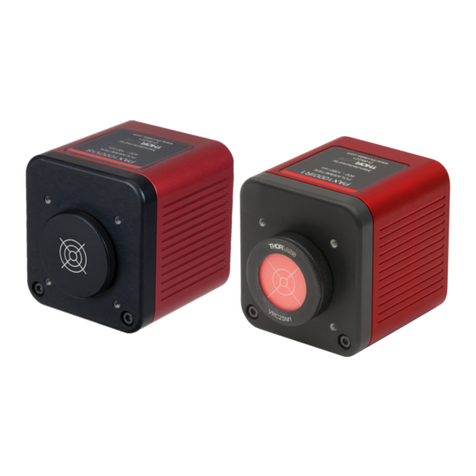
THORLABS
THORLABS PAX1000 Operation manual
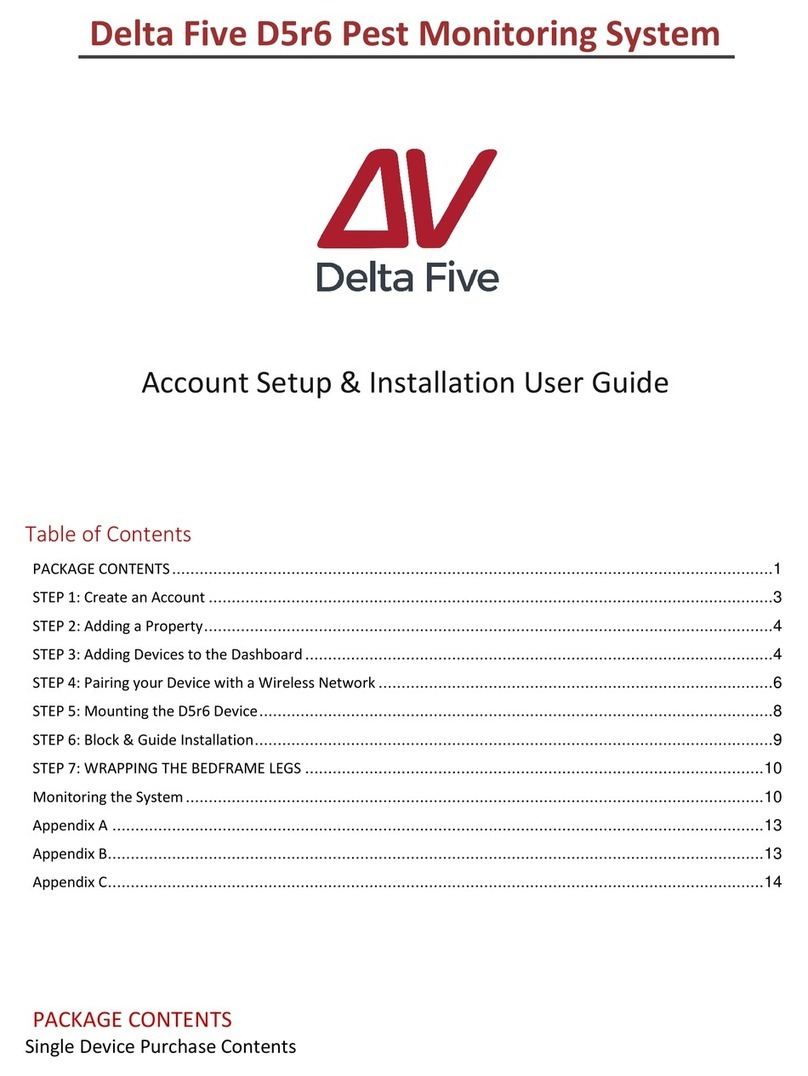
Delta Five
Delta Five D5r6 Account Setup & Installation User Guide
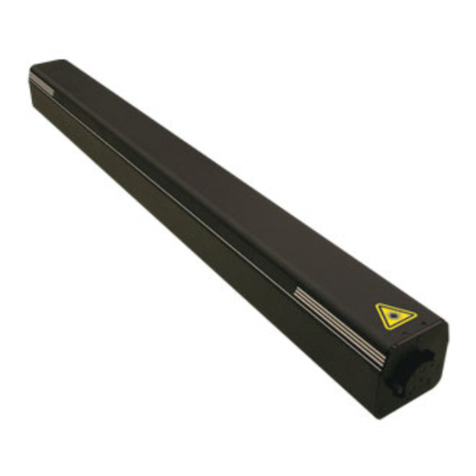
THORLABS
THORLABS HRP350 operating manual
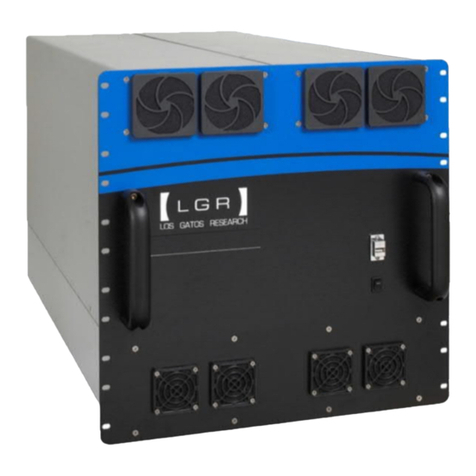
ABB
ABB LGR GLA351 Series user manual
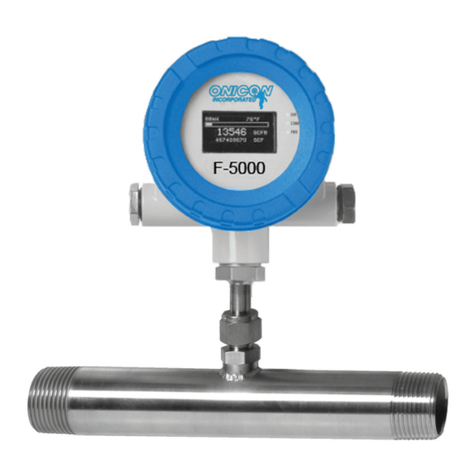
Onicon
Onicon F-5100 Inline Installation and operation guide

Inepro
Inepro PRO380-S user manual
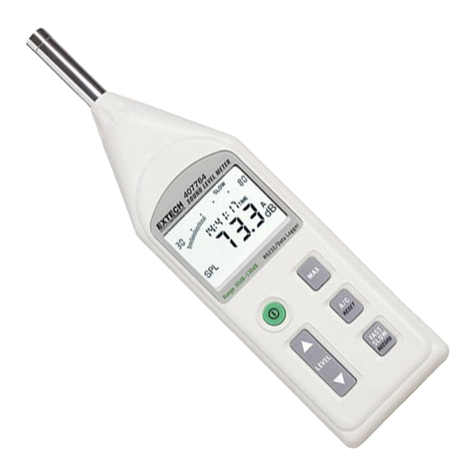
Extech Instruments
Extech Instruments 407764 user manual
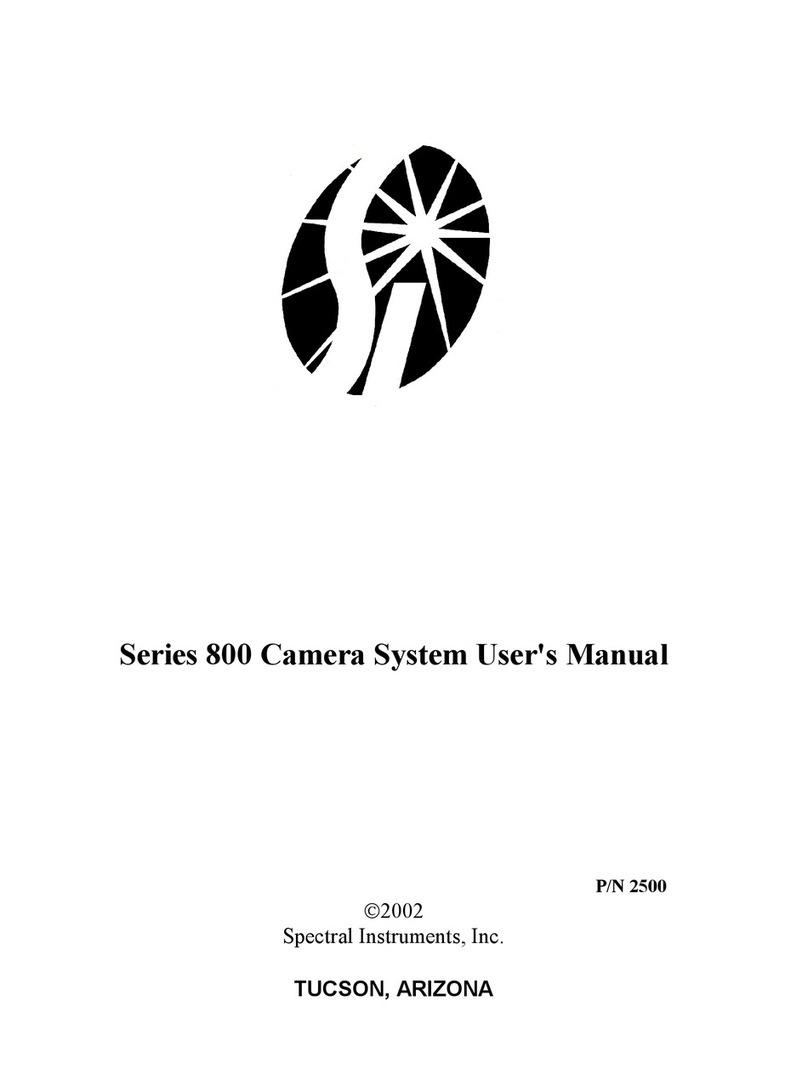
Spectral Instruments
Spectral Instruments Series 800 user manual
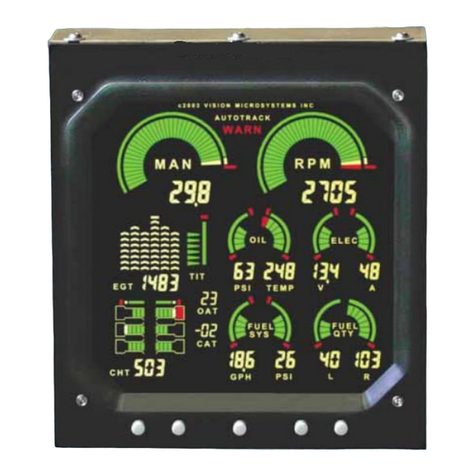
vision microsystems
vision microsystems VM1000C pilot's guide
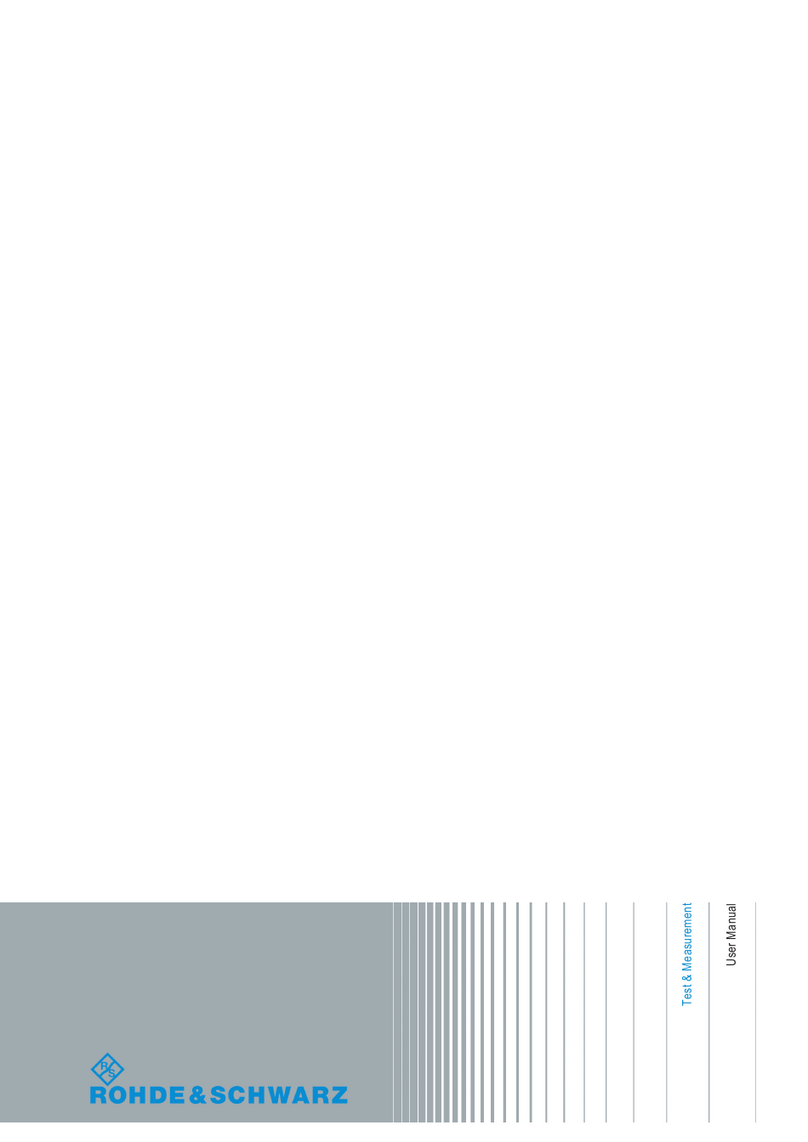
Rohde & Schwarz
Rohde & Schwarz CMW-B400B user manual