Aybey Elektronik ALC Series User manual

ALC SERIES LIFT CONTROL SYSTEM
USER MANUAL
Document Version: E 1.12b
Based on the ALC Software Version 3.04r

F/7.5.5.02102 R:1 2 ALC
INDEX
CHAPTER 1 - DESCRIPTION OF THE SYSTEM......................................................................................................................5
1.1) SERIAL COMMUNICATION AND CONFIGURATIONS..................................................................................5
1.2) CALL REGISTERS................................................................................................................................................5
1.3) DOORS...................................................................................................................................................................5
1.4) CAN PORTS...........................................................................................................................................................5
1.5) ELECTRONIC BOARDS IN THE SYSTEM.........................................................................................................6
1.6) SAFETY LINE .......................................................................................................................................................7
1.7) PANEL VOLTAGE..............................................................................................................................................10
1.8) INPUTS ................................................................................................................................................................10
1.9) OUTPUTS ............................................................................................................................................................10
1.10) UNINTENTED CAR MOTION (UCM).............................................................................................................10
1.11) CAR POSITION INFORMATION.....................................................................................................................10
1.12) DISTANCE BASED OPERATION....................................................................................................................11
1.13) GROUP OPERATION .......................................................................................................................................11
1.14) FIRE FUNCTIONS.............................................................................................................................................11
1.15) VIP TRAVEL .....................................................................................................................................................11
1.16) PRIORITY FUNCTION.....................................................................................................................................12
1.17) ACCESS CONTROL SYSTEM .........................................................................................................................12
1.18) HANDTERMINAL ............................................................................................................................................12
1.19) DATA TRANSFER............................................................................................................................................12
1.20 MAINTENANCE CONTROL.............................................................................................................................13
1.21) TEST MENU ......................................................................................................................................................13
1.22) ELECTRONIC RESCUE SYSTEM...................................................................................................................13
1.23) EN81-21 LOW PIT/LOW HEADROOM APPLICATIONS ..............................................................................13
CHAPTER 2 - LCD SCREEN AND KEYPAD...........................................................................................................................14
2.1) STARTUP SCREENS ..........................................................................................................................................15
2.2) MAIN SCREEN....................................................................................................................................................15
2.3) BUTTON FUNCTIONS IN MAIN SCREEN.......................................................................................................19
2.4) TEST MENU ........................................................................................................................................................21
2.5) USER DEFINABLE MENU.................................................................................................................................22
2.6) MENU TREE........................................................................................................................................................22
CHAPTER 3 - INPUTS.........................................................................................................................................................23
3.1) HARDWARE .......................................................................................................................................................23
3.2) INPUT FUNCTIONS ...........................................................................................................................................23
3.3) MONITORING OF THE STATES OF THE INPUTS..........................................................................................31
3.4) DEFINITION OF INPUTS...................................................................................................................................31
3.5) SETTING OF INPUT TERMINALS....................................................................................................................32
3.6) SETTING ALL INPUTS BY ACOMMAND.......................................................................................................33
CHAPTER 4 - OUTPUTS .....................................................................................................................................................33
4.1) HARDWARE .......................................................................................................................................................33
4.2) LOCATION AND SPECIFICATION OF OUTPUTS..........................................................................................34
4.3) OUTPUT FUNCTIONS .......................................................................................................................................34
4.4) DEFINING OUTPUTS.........................................................................................................................................38
CHAPTER 5- PARAMETERS ...............................................................................................................................................39
5.1) P1-MAIN PARAMETERS...................................................................................................................................40
5.3) P3-TIMER PARAMETERS .................................................................................................................................58
CHAPTER 6 - FLOOR PARAMETERS ..................................................................................................................................64
6.1) K1-SET DISPLAYS .............................................................................................................................................64
6.2) K2-SET DOOR AAND K3-SET DOOR B............................................................................................................65
6.3) K4-CAR CALLS...................................................................................................................................................66
6.4) HALL CALLS ......................................................................................................................................................66
6.5) K6-ENCODER PULSE OF FLOORS ..................................................................................................................67
6.6) K7-GENERAL PULSE.........................................................................................................................................68
6.7) K8-CALL REGISTER PERIODS.........................................................................................................................68

F/7.5.5.02102 R:1 3 ALC
CHAPTER 7 - SYSTEM SETTINGS.......................................................................................................................................69
7.1) SETTING DATE &TIME....................................................................................................................................69
7.2) R4-MODEM SETTINGS......................................................................................................................................69
7.3) SETTING PASSWORD .......................................................................................................................................69
CHAPTER 8 - LIFT FUNCTIONS ..........................................................................................................................................70
8.1) GROUP OPERATIONS .......................................................................................................................................70
8.2) PRIORITY FUNCTION.......................................................................................................................................71
8.3) ACCESS CONTROL SYSTEM...........................................................................................................................72
8.4) MAINTENANCE CONTROL..............................................................................................................................75
CHAPTER 9 - UTILITIES......................................................................................................................................................76
9.1) FACTORY DEFAULTS.......................................................................................................................................76
9.2) BACKUP OF PARAMETERS.............................................................................................................................76
9.3) DISPLAY UTILITIES..........................................................................................................................................77
9.4) R5-RESET PULSES.............................................................................................................................................78
9.5) RB-ENCODER DIRECTION (ABSOLUTE ENCODER)..........................................................................................78
9.6) PA-LIFT NUMBER..............................................................................................................................................78
CHAPTER 10 - ENCODER OPERATIONS ............................................................................................................................78
10.1) INCREMENTAL ENCODER ............................................................................................................................78
10.2) ABSOLUTE ENCODER....................................................................................................................................80
10.3) DISTANCE BASED OPERATION....................................................................................................................86
CHAPTER 11 - ERROR LOG AND ERROR CODES ...............................................................................................................87
11.1) ALC SERIES ERROR CODES ..........................................................................................................................88
CHAPTER 12 - UCM SERVICES ..........................................................................................................................................94
12.1) UCM...................................................................................................................................................................94
12.2) UCM IN ELECTRIC LIFTS WITH ASYNCHRONOUS MOTOR ...................................................................................95
12.3) UCM IN ELECTRIC LIFTS WITH SYNCHRONOUS MOTOR (GEARLESS MACHINE) .................................................96
12.4) UCM IN HYDRAULIC LIFTS .................................................................................................................................97
12.5) MANUAL UCM TEST...........................................................................................................................................98
12.6) SHAFT LIMIT TEST...............................................................................................................................................99
CHAPTER 13 - ELECTRONIC RESCUE SYSTEM.................................................................................................................100
13.1) ELECTRONIC RESCUE TYPES..............................................................................................................................100
13.2) DEFINITIONS AND PARAMETERS USED WITH RESCUE APPLICATION ..................................................................102
13.3) RESCUE PROCEDURE .........................................................................................................................................102
CHAPTER 14 –EN81-21 LOW PIT/LOW HEADROOM APPLICATIONS ...........................................................................104
14.1) AMI-100 DEVICE............................................................................................................................................104
14.2) CHECKING OF MANUAL OPENING OF SHAFT DOORS WITH TRIANGULAR KEY ...........................105
CHAPTER 15- VARIABLES AND LANGUAGE....................................................................................................................106

F/7.5.5.02102 R:1 4 ALC
PREFACE
ALC Series Lift Control System is designed to fulfil the requirements of the new EN81-20 / 50
standards for electric and hydraulic lifts. It supports a wide range of lift applications for up to 64
floors. ALC makes use of intelligent electronic units communicating via CAN-BUS in the overall lift
system. The system comes with three CAN ports which provide flexibility in connecting CAN-units.
The communication hardware between car and controller is designed to be a fault tolerant CAN to
increase the robustness to against any electronic disturbances in the connection.
ALC supports parallel and serial communications for landing panels and group operations for up to
8 lifts. There are various function boards in ALC system to support specific functions and increase
flexibility. It also has integrated lift access control system and VIP travel facilities in its software to
restrict the use of the lift.
ALC series has advanced data communication facilities. There are interfaces for ethernet, USB, and
Bluetooth connections in ALC series to enable any user to edit the parameters in the controller or
observe the motion of the lift either by a computer or a mobile device locally or via the internet.
In this manual, you will find detailed information about ALC Series Lift Control System. However,
since there are continuous developments in software it is possible that the software version you are
using may not be fully compatible with this manual. If this is the case, you can download the most
recent manual in from www.aybey.com.
You can send a mail to support@aybey.com either to get more technical information about ALC or
to send any comments. Please feel free to contact us for any problems or suggestions. Bear in mind
that all these systems have been developed mainly by benefiting from the criticism of customers
and users.
Aybey Elektronik

F/7.5.5.02102 R:1 5 ALC
CHAPTER 1 - DESCRIPTION OF THE SYSTEM
1.1) SERIAL COMMUNICATION AND CONFIGURATIONS
The communication between car and controller in ALC series is always serial. However, the landing
panels can be connected both in serial and in parallel. The communication system is CAN. When
landings are parallel then the configuration is called as “car serial” and when landings are serial
then the configuration is called “full serial”. The serial interfaces between car and controller are
always in low speed and fault tolerant mode where the interface for landings can be selected as
low speed fault tolerant or high speed. The terminal board used in the controller depends on the
serial configuration. In full serial configuration ALSK terminal boards and in car serial configuration
ALPK terminal boards should be used.
1.2) CALL REGISTERS
1.2.1) CAR CALLS:
i) Not prewired systems: Car calls are collected by the car controller board SCB for up
to 16 stops. For more than 16 stops CAN-IO boards must be connected to the car
circuit to collect car calls. Each CAN-IO board has a 16-stop capacity.
ii) Prewired systems: Car calls are collected by the car controller board PWS for up to
16 stops. For more than 16 stops APE boards must be connected to the car circuit to
collect car calls. Each APE board has a 16-stop capacity.
1.2.2) LANDING CALLS:
i) Car Serial Systems: The terminal board ALPK has 8 call registers onboard. An I/O
board can be plugged onto ALPK to increase the number of call registers to 16. For
greater numbers, CAN-IO boards must be added to increase number of landing call
registers. Each CAN-IO board has 16 call registers.
iii) Full serial systems: CAN landing units collect and send calls at the landings. No
additional board is required for any number of stops.
1.3) DOORS
ALC lift controller system supports two car doors separately. There is separate door open, door
close, photocell and door limit inputs for two doors. There are also various timers associated with
doors. Adequate door open checking tests in conformity to the lift standard EN81-20/50 have
been developed for one and two doors as well as full and semi-automatic doors. The door bridging
board SDB is always required to test the doors at arrival. Therefore, it must be plugged always
onto ICM mainboard even when no relevelling and door pre-opening are requested if EN81-20/50
standard is obeyed.
1.4) CAN PORTS
There are three CAN ports on ALC mainboard. One is built-in on the main board (C0) for low speed
fault tolerant mode and is used as default connection for the car. C1 and C2 ports require an add-
on CAN interface board (CSI or CCI) to be plugged onto the mainboard to become active. However,
any CAN port can be configured for any circuit (landing, car, group, absolute encoder, etc.). Please
note that the landing circuit will be low speed fault tolerant if CSI is used and high speed if CCI is
used.

F/7.5.5.02.102 R:1 6 ALC
1.5) ELECTRONIC BOARDS IN THE SYSTEM
The electronic boards used in ALC system and their descriptions are listed below.
ALC: It is the main controller board of ALC system. It contains a microcontroller, an LCD display and
a keypad, to manage the system. This board is common in electric and hydraulic lifts. It has 8
programmable inputs and 9 programmable relay outputs on it.
SCB: This board is used in the inspection box and works as the car controller board. It collects car
calls and detector inputs in car circuit. It contains 5 programmable relay outputs and 12
programmable inputs, 16 call registers, a battery charger for emergency power supply, and
hardware for other lift functions in car. It also supports announce system when AFM (Announce
Board) board is plugged.
SDB: It is the door bridging board plugged onto ALC.
SGD: It controls the activation of the coil on speed governor.
OUT: This board contains 4 programmable output relays.
INPS: This board contains 4 programmable inputs.
CSI: This is the CAN interface board in fault tolerant mode. It can be used for lift group operation to
communicate with other lifts or to have a separate CAN bus for landing panels.
CCI: This is the CAN interface board in high speed mode. It can be used to have a separate CAN bus
for landing panels when landing panels have high speed CAN interfaces.
ETN: It is the ethernet interface board and is used to connect a PC to the controller either in with a
local area network (LAN) or via the internet.
ETW: It is the Wi-Fi ethernet interface board and is used to connect a PC to the controller either
with a local area network (LAN) or via the internet.
USN:USB interface board for local PC connection.
RS232: RS232 interface board.
IDC: ERS connection interface board.
IO: It has 8 call registers on it. It is used to increase the number of call registers on ALPK.
CAN-IO: This board communicates via CAN-BUS and serves as a call register. One CAN-IO board has
16 call registers. It is used to expand the number of call registers in car circuit above 16 floors or
above 16 call registers in systems where landing panels are not serial.
ALSK: This board is used in systems where landing panels are serial and serves as a terminal board
for programmable inputs and outputs in controller and PTC. It contains 8 (12) programmable inputs.

F/7.5.5.02.102 R:1 7 ALC
ALPK: This board is used in systems where landing panels are parallel and serves as a call register
well as a terminal board for programmable inputs and outputs in controller and PTC. It contains 8
(12) programmable inputs.
SPB: This board serves as a pit controller in shaft pit. It communicates via low speed fault tolerant
CAN-BUS.
SPT: This board serves as a pit controller in shaft pit. It communicates via high speed CAN-BUS.
PWH: This board is used only in prewired systems in the inspection box. It serves as the terminal
connection board of flexible cable in car.
PWL: This board is used only in prewired systems in the inspection box. It serves as the car
controller. It collects car calls and detector inputs in the car top circuit. It contains 5
programmable relay outputs and 14 programmable inputs, a battery charger for emergency power
supply, and hardware for other lift functions in car.
AFM: This board is a pluggable module and contains only memory for announcement data. It is used
together with SCD, PWS and PWSC boards.
PWS (PWF): This board has been designed to drive only prewired Aybey APQB series car buttons
in prewired systems. It is usually placed into the car operating panel. It collects car calls, drives
indicator signals and displays in car panel and carries on in-cabin announcement. Its code is PWF
when AFM has been already plugged onto it.
PWSC (PWFC): This board has been designed to drive car buttons in prewired systems. It is usually
placed into the car operating panel. It collects car calls, drives indicator signals and displays in car
panel and carries on in-cabin announcement. Its code is PWFC when AFM has been already plugged
onto it.
APE: This board is used only in prewired systems as an extension to PWS. It has 16 car call registers
on it and increases the number of car calls.
1.6) SAFETY LINE
1.6.1) Safety line voltage:
The power supply of the safety circuit is labelled as 110 and 150, where 110 is the starting terminal
and 150 is the return terminal. Safety Circuit Voltage can be selected by the customer. The voltages
to be selected for safety circuit are 48Vdc, 60Vdc, 110Vac, 230Vac.
The coil voltages of contactors and valves must be exactly the same as the safety line voltage. When
this is not possible in the application then the coils of the contactors and /or valves cannot be driven
directly by the safety line. They must be driven by two contactors or safety relays which are in
conformity to the standard as shown in Figure 1.1 These additional relays or contactors must be
driven by the safety line and have the same coil voltages as the safety line. See Figure 1.1 as an
example of such an application where the safety line voltage and contactor (or valves) coil voltages
are not the same.

F/7.5.5.02.102 R:1 8 ALC
Figure 1.1
1.6.2) Safety line structure:
Safety line starts to flow from the terminal 110 into the shaft devices. All devices, through which
the safety line must passes except lift doors, are to be between 110 and 120. 120 is the starting
point of the door safety contacts. The door circuit ends at the terminal 140. 140 is the end of the
safety line and the power source for the contactor and valve coils. When any door or any safety
contact in the shaft is open then there must be no voltage present at terminal 140. If it is present
then this means a wrong wiring or any fault in the devices.
The connection terminals of the shaft and the door contacts are found in wiring diagrams of the
related application. There are various connection diagrams for specific lift applications, door types
and number of doors. Please check first if the given electric diagram matches your application
exactly. Otherwise consult our support department to get the appropriate wiring diagram before
starting.
You can see the status of the safety line on the main screen indicated by letters ranging from A to
G, where G means that the safety line is closed. The LEDs labelled from 113 to 140 on the left side
of the ALC board show the closed terminals of the safety line directly.

F/7.5.5.02.102 R:1 9 ALC

F/7.5.5.02.102 R:1 10 ALC
1.7) PANEL VOLTAGE
Except for the safety line, there is only one power supply in the system which is 24V dc. It is the
power source in the controller to supply all electronic boards, signals and detectors. The current
rating (power) of the supply must be selected by taking into consideration the current consumption
of the panels.
1.8) INPUTS
All inputs are 100% galvanically isolated from the microcontroller circuit since they are connected
via optocouplers to this circuit. Input functions and input terminal assignment procedure are
explained in chapter 3.
1.9) OUTPUTS
All inputs and outputs are 100% galvanically isolated from the microcontroller circuit since they are
connected via optocouplers to this circuit. Mainly relays are used as outputs. Some output terminals
are assigned to a specific function as default, such as RU, RH, RF whereas the others are
programmable. The user can assign any function to these programmable output terminals.
Output functions and output terminal assignment procedure are explained in chapter 4.
1.10) UNINTENTED CAR MOTION (UCM)
ALC controller system supports numerous UCM test and control facilities for geared, gearless
and hydraulic lift systems. There are a variety of manual and automatic UCM test routines built
in in the software. The UCM tests can be executed at any time manually as well as automatically
(periodically according to time (daily) or starting of the lift). This option can be selected in
parameter B37. UCM facilities are explained in detail in chapter 12.
1.11) CAR POSITION INFORMATION
In ALC car position information can be collected with magnet switches or encoders.
1.11.1) MAGNETIC SWITCHES
In this mode counter method is used and a reset is required after each powering up. If the lift is
not at the top or base floor during any power up then it travels immediately to the base floor to
reset itself. Normally open magnet switches (KPM206) are used in ALC. You can only get two
types of information in this method. One is current floor number and the other is whether the
lift is at the door zone. These are all. This method is recommended only for low speed simple lift
applications. To select this method, adjust parameter A05 to 0.
1.11.2) INCREMENTAL ENCODER
An incremental encoder can be used to get car position information. To implement this Pulse A
and Pulse B outputs of the encoder should be connected to the ENC terminals on ALC
mainboard. When incremental encoder method is used then the position of the car can be
obtained by the controller in mm accuracy. This information helps the controller in managing
speed paths, especially in slowing down and stopping. Incremental encoder method also needs
to be reset after each start-up. Therefore, the lift always travels to the base floor or top floor
after start-up in order to calibrate itself. To select this method, adjust parameter A05 to 2. You
should also define a number of path lengths in section 6.6.

F/7.5.5.02102 R:2 11 ALC
1.11.3) ABSOLUTE ENCODER
The best way to get car position information is to use an absolute encoder. An absolute encoder
always gives the exact car position information to the controller. It does not need resetting after
start-up. An absolute encoder in ALC system is connected via CAN bus. It gives information about
car position in mm accuracy. This information helps the controller in managing speed paths,
especially in slowing down and stopping. To select absolute encoder, adjust parameter A05 to 3.
You should also define a number of path lengths in section 6.6.
1.12) DISTANCE BASED OPERATION
When an incremental encoder or an absolute encoder has been selected as the car position
collecting system then ALC offers a distance-based operation system. In distance-based
operation the distance to the target floor in mm is used in motion rather than floor. Distance
based operation has significant advantages in high speed lifts. There are no intermediate speeds
for high speed lifts. The lift can slow down directly from any speed to the target floor. A very
important point to know is that this process is totally managed by the ALC software and any
inverter can be used to drive the lift motor. The detailed explanation of this system is in section
10.4.
1.13) GROUP OPERATION
ALC controller can work in lift groups up to eight lifts. The communication between controllers is
implemented via CAN-BUS. The system is very flexible. There is no dedicated master. When a lift
in the group is switched off or cannot function properly then a new lift starts working as master,
and the group operation goes on without any interruption. The group connections and operation
are explained in details in section 8.1.
1.14) FIRE FUNCTIONS
ALC supports two lift standards related to fire event, EN81-72 and EN81-73. The standard which
will be used in lift operation should be defined in parameter B46. In case where EN81-73 has
been selected then there are two fire floors which are defined in parameters B05 and B40.
Depending on the activation of the fire inputs functions FR1 and FR2, one of the floors defined in
parameter B05 and B40 will be selected as the target floor (fire floor) for the lift. If FR1 and FR2
are both active then fire floor 1 will be selected as the target floor.
1.15) VIP TRAVEL
ALC has a VIP Travel function. When any of the VIP related input functions VP1 (62), VP2 (63) or
VP3 (64) is activated then the lift immediately moves to the floor defined in related parameters
B33, B34 and B35, respectively. If the lift is in motion in the same direction with the new target
then it continues its travel until reaching the VIP floor. If the motion and the new target
directions are opposite then the lift stops at the first floor and reverses its direction towards to
the VIP floor and starts its travel again. VP1 has the highest priority, VP2 medium and VP3 the
lowest. That means when there are more than one active VIP terminals then the one with the
highest priority is selected (VP1 >VP2 > VP3).

F/7.5.5.02102 R:2 12 ALC
1.16) PRIORITY FUNCTION
ALC software has a priority function. This function is very useful in buildings where public lifts are
working. In case of emergency these lifts can be called and used as a private lift by inhibiting
normal usage. This system works only in full serial systems where landings are serial and requires
access control readers (RFID or i-Button) in all landings and cars.
Priority function is explained in section 8.2.
1.17) ACCESS CONTROL SYSTEM
Access control utility permits only the users with appropriate permission to use the lift, in other
words, it restricts any person who is not allowed to use the lift for a specific floor or time interval.
For this purpose, each lift user should have a RFID card or i-Button key with a unique user ID. This
utility is present in ALC software. You do not need any access control system to implement it. You
only need access control readers in landing and car panels.
Access control system is explained in section 8.3.
1.18) HANDTERMINAL
The screen and the keypad on ALC mainboard can be accessed with a hand terminal HTC.It can
be used anywhere in the shaft, at floors or in machine room by connecting its terminals to CAN
bus. When hand terminal is active then the keypad on the mainboard becomes inactive.
1.19) DATA TRANSFER
ALC series controller supports computer connection via USB or Ethernet by means of Aybeynet
software. By using Aybeynet a computer can be connected directly, via a local network (LAN) or
via the Internet. Aybeynet computer interface program supports everything that you can do with
the keypad on the mainboard. Using Aybeynet in adjusting and monitoring the controller improves
the man-machine interface to a very high level when compared to a two-lines screen and 6 keys
in the keypad.
Aybeynet has the following features:
Lift motion and calls can be observed in real time
All timings and the status of the inputs and the outputs can be observed in real time
Error log can be obtained as digital data
All parameters can be checked and modified.
All input and output settings can be checked and modified.
All Parameters can be saved, loaded, transferred and printed.
You can download Aybeynet software and related drivers from the link
http://www.aybey.com/en/support/lift-control-system-application-software You can find detailed
information to install and use the software in “Aybeynet Installation Manual”.

F/7.5.5.02102 R:2 13 ALC
1.19.1) USB
In order to connect any PC to a lift controller with Aybeynet via USB it is necessary to have a USN
add-on board plugged onto the ALC mainboard. So, the controller can be monitored by a PC in
the machine room to adjust the parameters and timers or to detect an error.
1.19.2) Ethernet
In order to connect a PC to a local network (LAN) or to the internet it is necessary to plug the
ETN add-on board onto the ALC board. ETN board is the ethernet interface. This way the
controller can be monitored by a PC anywhere in the world where internet connection is present
to adjust the parameters and timers or to detect an error.
1.20 MAINTENANCE CONTROL
There are two independent control systems for maintenance mode activation. The first one is by
setting a maintenance time in the future and the second is by specifying a maximum number of
starts for the lift. If the adjusted maintenance time or number of starts is exceeded then the lift
switches to maintenance mode and does not accept calls anymore. Maintenance control is
explained in section 8.5.
1.21) TEST MENU
There is a special utility in ALC system for testing the lift in normal operation. The doors or calls
can be easily cancelled. A call to the top or bottom floor can be created and any number of
random lift travels can be executed automatically. Test menu is explained in section 2.4.
1.22) ELECTRONIC RESCUE SYSTEM
There is an automatic electronic rescue system that Detects power loss immediately and
provides uninterrupted power for the controller. It is described in detail in Section 13.
1.23) EN81-21 LOW PIT/LOW HEADROOM APPLICATIONS
EN81-21 standard sets the basic rules to design lifts which do not satisfy shaft requirements of
EN81-20/50. ALC supports some special equipment designed for EN81-21 applications.
Furthermore, it offers some very general functions. See Chapter 14 for more detailed explanation.

F/7.5.5.02102 R:2 14 ALC
CHAPTER 2 - LCD SCREEN AND KEYPAD
ALC Series have an LCD screen with two lines and sixteen characters per line and a keypad with six
buttons.
Buttons are located as below:
LEFT
UP
RIGHT
ESC
DOWN
ENT
Figure 2.1 Keypad layout
There are arrows in four directions as UP, DOWN, LEFT and RIGHT on the glass of the ALC
mainboard. However, we will denote them with as UP, DOWN, LEFT and RIGHT rather than
indicating with arrows with the same directions throughout this document.
The arrow buttons have various functions depending on the screen or menu they are used.
However, ESC and ENT buttons usually have the same functions where pressing ESC button exits
from current menu or application and ENT button usually confirms anything asked or selects the
indicated line. UP and DOWN arrow buttons are used in list type screens to move up and down
on the screen, respectively. Please be aware that there are some screens where a special button
is asked to be pressed to continue or to do a specific task.
One important use of the key panel is entering certain numbers as input. This is done mainly as
in the following example where you are asked to enter number of stops in parameter A01.
You can see the value of the parameter as 6 on the screen. When you are asked to enter a number
then cursor is always located under left most digit at the beginning. You can increase or decrease
value of the digit under which cursor is located by using UP and DOWN buttons respectively. In
order to change the digit in other positions you can move cursor to left and right by using LEFT
and RIGHT buttons.
On the screen above the value of the parameter is 6 and the cursor is located under the digit 6.
Now let us see how this number changes after the indicated button is pressed.
?000006
pressing DOWN
?000005
pressing DOWN
?000004
pressing LEFT
?000004
pressing UP
?000014
FLR: 6
A01 ?000006

F/7.5.5.02102 R:2 15 ALC
After setting the parameter, if you press ENT the new value on the screen is saved. However, if
you press ESC, changes are cancelled. In both cases, you return to the previous screen and will see
value of the parameter.
Here we press ENT and see the following screen.
2.1) STARTUP SCREENS
In start up you see the following screens one by one:
a) The number in the first line on this screen shows the software version number (bold) and
the second line indicates that the parameters have been loaded from EPROM.
b) This screen shows the current date and time. It is called “info screen”.
c) This screen shows the serial number of the controller board.
d) At the end of the start-up period you will see system ready message
e) Then the main screen is displayed. Now the system is ready to start to serve as a lift
controller.
2.2) MAIN SCREEN
After start-up period is completed main screen is displayed on LCD screen. Main screen displays
the most important state variables of the lift with some letters and symbols. Understanding this
screen will help you in operation significantly. Moreover, access to all menus and applications
starts through the main menu which is activated when ENT button is pressed on the main
screen.
AYBEY ALC 1.08c
12/08/2017 13:04
AYBEY ALC 1.08c
starting
AYBEY ALC 1.08c
System Ready
AYBEY ALC 1.08c
SNO: 14024
G 01=t--STOP 1
.......

F/7.5.5.02102 R:2 16 ALC
The meaning of the characters on the main screen is explained in the following screens. Please
note that the background of the explained positions is in grey and characters are in red.
a) The first character gives information about the safety line. The characters and their
corresponding safety line status are as follows:
terminal
character
113
A
114
B
120
C
125
D
130
E
135
F
140
G
When G is displayed here then the safety line is closed and the lift can move. C
represents STOP circuit.
b) The second character shows the direction of motion. There can be an up or down arrow
depending on the direction. This position will be blank when there is no direction.
c) The 3rd and 4th Characters indicate together the car position (floor number).
d) The fifth position shows if the car is at door zone. An equal sign (=) here means that the
car is at floor level namely at door zone. No character here means that the car is between
floors, so the doors cannot be opened.
e) The character group in positions 6, 7 and 8 shows the target floor with a ‘t’ in front them
in normal mode.
f) In inspection mode “INS” string will be displayed there.
G↑01=INSSLOW 1
.......
G 01=t--STOP 1
.......
G 01=t--STOP 1
.......
G 01=t--STOP 1
.......
G↑01=t04FAST 1
.......

F/7.5.5.02102 R:2 17 ALC
g) The positions 9 and 10 show the status of the doors.
If there is only one car door then there are two arrows in these positions. When the
arrows point toward each other it means the doors are closing or closed otherwise
opening or open.
Doors are closed or closing. Doors are open or opening.
If there are two car doors then there are two characters “ab” in these positions. “a”
represents the door A and “b” the door B.
When “a” is present then it means that the door A is closed or closing. When “a” is not
present then it means that the door A is open or opening. Similarly, when “b” is not
present then it means that the door B is open or opening.
Doors A and B are closed or closing. Doors A and B are open or opening.
Doors A is open or opening where door B is closed or closing
Doors B is open or opening where door A is closed or closing
h) The positions 11,12,13,14 and 15 shows as a group the motion status.
G 01=t--STOP 1
.......
G 01=INSSTOP 1
.......
G 01=t--STOP 1
.......
G 01=t--STOP 1
.......
G 03=t-- a b STOP
1 .......
G 03=t-- STOP 1
.......
G 03=t-- b STOP 1
.......
G 03=t-- a STOP 1
.......

F/7.5.5.02102 R:2 18 ALC
The speed words at these positions and their meanings are shown below.
STOP
Lift is at rest
START
Lift is executing a start command but motion has not started
yet.
LEVEL
Lift is relevelling
SLOW
Lift is in slow motion
FAST
Lift is in fast motion.
HIGH
Lift is in higher fast motion.
ULTRA
Lift is in highest fast motion.
i) The last character in first line gives two pieces of information in time division.
The number that we see gives information about the door tests completed. The meaning
of this number is shown below:
0
No doors have been checked.
1
Door A has been checked.
2
Door B has been checked.
3
Both, door A and B have been checked.
The “-“ or “+” signs at this position gives information about group connections.
-
No group communication
+
Group communication has been established.
j) The second line of the main screen shows the calls. When there is an error or message
then this second line is used as a message screen, too.
There are as many characters there as the number of floors. If there are more than 16 floors
then only the calls of the first sixteen floors are shown here. The meanings of the characters
used here are listed in the table below.
.
No call
▼
Down call
▲
Up call
-
Car call
When there is more than one call at one floor then the combination of the symbols are displayed
at this floor.
G 01=t--STOP -
.......
G 01=t--STOP 1
.......
G 01=t--STOP -
.......

F/7.5.5.02102 R:2 19 ALC
2.3) BUTTON FUNCTIONS IN MAIN SCREEN
The functions of the buttons when pressed while main screen is being displayed are as follows:
2.3.1) Pressing ENT Button -> MAIN MENU
When ENT button is pressed then the menu system is activated. Main menu appears as
below:
This is the starting point of the menu tree. From this menu you can reach submenus for
all parameters, variables and application menus in the system. You can use UP and
DOWN buttons to scroll up and down the lines, respectively and ENT button to select the
function denoted by ‘>’ arrow.
2.3.2) Pressing ESC Button -> INFO SCREEN
When ESC button is pressed while main screen is being displayed then info screen comes
as in starting period.
>M2-PARAMETERS
M3-ERROR LOG
AYBEY ALC 1.08c
12/08/2017 13:04

F/7.5.5.02102 R:2 20 ALC
When you do not press any button then the system will return to the main screen after a
certain number of seconds. But if you press ENT button here then you will enter into info
menu.
This is a menu showing some of the system variables such as number of starts,
temperature, pulse per mm, etc. You can go through the lines by pressing UP and DOWN
buttons.
When you are finished with the menu, you can exit by pressing ESC button.
2.3.3) Pressing RIGHT Button -> GIVING CAR CALLS
When RIGHT button is pressed then you will be asked for a floor number. When you
enter a number and press ENT then a car call for this floor is registered.
This is the facility of giving car call from keypad.
2.3.4) Pressing UP Button -> USER DEFINED MENU
When UP button is pressed while main screen is being displayed then the system
switches to the user-defined menu.
User defined menu is explained in section 2.5.
2.3.5) Pressing LEFT Button -> MONITORING OF THE STATES OF THE INPUTS
When LEFT button is pressed while main screen is being displayed then the system
switches to the monitoring inputs menu.
12/08/2017 13:04
1-DATE TIME
NUMBER OF STARTS
3- 1128
SERIAL NO
2- 1314
113*114*120*125*
130*135 140 141
Cabin Button
Floor No ?000002
I1: - (2) 870
MR INSPECTION
Table of contents
Other Aybey Elektronik Control System manuals
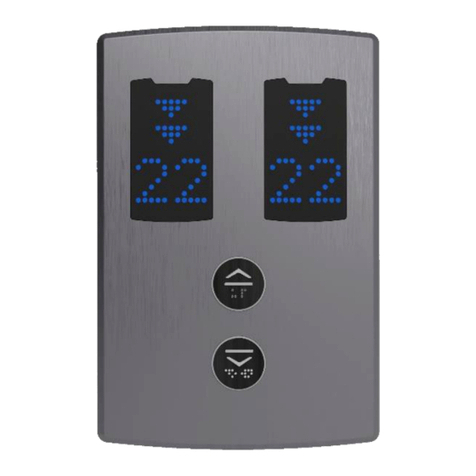
Aybey Elektronik
Aybey Elektronik ALYA User manual

Aybey Elektronik
Aybey Elektronik AE-SMART User manual

Aybey Elektronik
Aybey Elektronik SWLINE Series User manual

Aybey Elektronik
Aybey Elektronik EVOS Series User manual
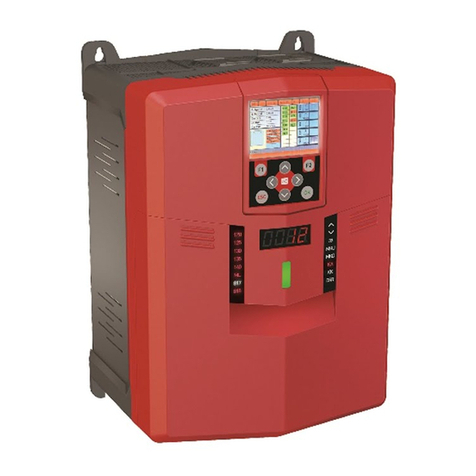
Aybey Elektronik
Aybey Elektronik AE-MAESTRO User manual
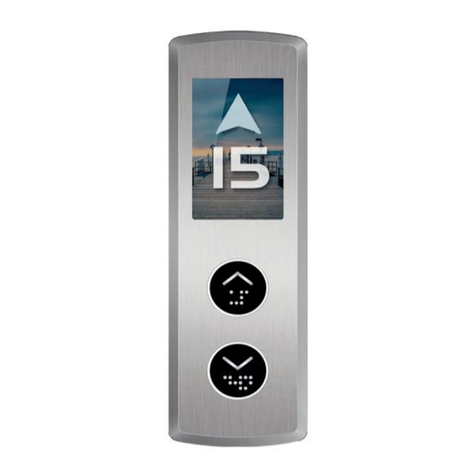
Aybey Elektronik
Aybey Elektronik ALYA Series User manual