Buhler SCS 104 User manual

Gas Analysis
Installation and Operation Instructions
Original instructions
19" Sample Gas Conditioning System
SCS 104
BECS0031
02/2020
Bühler Technologies GmbH, Harkortstr. 29, D-40880 Ratingen
Tel. +49 (0) 21 02 / 49 89-0, Fax: +49 (0) 21 02 / 49 89-20
E-Mail: [email protected]
Internet: www.buehler-technologies.com

Bühler Technologies GmbH, Harkortstr. 29, D-40880 Ratingen
Tel. +49 (0) 21 02 / 49 89-0, Fax: +49 (0) 21 02 / 49 89-20
Internet: www.buehler-technologies.com
E-Mail: [email protected]
Read this instruction carefully prior to installation and/or use. Pay at-
tention particularly to all advises and safety instructions to prevent in-
juries. Bühler Technologies can not be held responsible for misusing
the product or unreliable function due to unauthorised modifications.
All rights reserved. Bühler Technologies GmbH 2020
Document information
Document No.......................................................... BECS0031
Version........................................................................ 02/2020
Part No...............................................................998BECS0031

SCS 104
Contents
1 Introduction..................................................................................................................................................................................................................... 3
1.1 Intended Use......................................................................................................................................................................................................... 3
1.2 System Description ............................................................................................................................................................................................. 3
1.2.1 Sample conditioning section ............................................................................................................................................................3
1.2.2 Calibration gas section .......................................................................................................................................................................3
1.2.3 Blowback air section ............................................................................................................................................................................3
1.2.4 Manual control..................................................................................................................................................................................... 4
1.2.5 External control and monitoring.................................................................................................................................................... 4
1.3 Scope of delivery..................................................................................................................................................................................................4
2 Safety instructions......................................................................................................................................................................................................... 5
2.1 Important advice ................................................................................................................................................................................................. 5
2.2 General hazard warnings .................................................................................................................................................................................6
3 Transport and storage .................................................................................................................................................................................................. 7
4 Installation and connection ........................................................................................................................................................................................8
4.1 Installation site requirements.........................................................................................................................................................................8
4.2 Gas Line Connections .........................................................................................................................................................................................8
4.3 Electrical connections ........................................................................................................................................................................................8
5 Operation and control ................................................................................................................................................................................................ 10
5.1 Start up................................................................................................................................................................................................................. 10
5.2 Using the device menu .................................................................................................................................................................................... 10
5.2.1 Use of menu functions......................................................................................................................................................................10
5.2.2 Lock Menu..............................................................................................................................................................................................11
5.2.3 Overview of the menu items............................................................................................................................................................11
5.2.4 Description of menu functions ...................................................................................................................................................... 13
5.3 Manual operation of the SCS (front panel module CM0191)................................................................................................................ 16
5.4 Monitoring system operation on the controller module (front panel module CM0191) ............................................................. 16
5.5 External control ................................................................................................................................................................................................. 16
5.6 External monitoring......................................................................................................................................................................................... 16
5.7 Flow Meter Operation.......................................................................................................................................................................................17
5.8 Pressure regulators and gauges ....................................................................................................................................................................17
6 Maintenance.................................................................................................................................................................................................................. 18
7 Service and repair......................................................................................................................................................................................................... 19
7.1 Troubleshooting ................................................................................................................................................................................................ 19
7.1.1 Error messages on the display.......................................................................................................................................................20
7.2 Safety instructions............................................................................................................................................................................................ 21
7.3 Replacing the Fuse in the Front Panel.........................................................................................................................................................22
7.4 Replacing the fuse (F1) from the gaspumps ..............................................................................................................................................22
7.5 Replacing the fuse (F2) from the peristaltic pumps................................................................................................................................22
7.6 Replacing the Peristaltic Pump Hose...........................................................................................................................................................22
7.7 Replacing the filter element...........................................................................................................................................................................23
7.8 Replace Flowmeter module............................................................................................................................................................................23
7.9 Install Extension module gaspump.............................................................................................................................................................23
7.10 Drying the Moisture Detector........................................................................................................................................................................24
7.11 Calibration of the moisture detector...........................................................................................................................................................24
7.12 Spare parts and accessories ...........................................................................................................................................................................24
7.12.1 Spare parts and accessories............................................................................................................................................................ 24
8 Disposal........................................................................................................................................................................................................................... 25
9 Appendices.....................................................................................................................................................................................................................26
9.1 Technical Data....................................................................................................................................................................................................26
9.2 Legend................................................................................................................................................................................................................... 27
9.3 Drawing 1: Flow chart.......................................................................................................................................................................................28
9.4 Drawing 2: Wiring diagrams .........................................................................................................................................................................29
9.5 Drawing 3: Front view......................................................................................................................................................................................30
iBühler Technologies GmbHBECS0031 ◦ 02/2020

SCS 104
9.6 Drawing 4: Back view.......................................................................................................................................................................................30
10 Attached documents....................................................................................................................................................................................................31
ii Bühler Technologies GmbH BECS0031 ◦ 02/2020

SCS 104
1 Introduction
1.1 Intended Use
The SCS104 is a gas sample conditioning system. The specifications and their limits given in the appendices are to be main-
tained during installation. The device is not to be used in hazardous areas.
1.2 System Description
Please consult the illustrations and the legend at the end of the operating manual. The components are numbered. The num-
bers are referenced in the text.
1.2.1 Sample conditioning section
The sample gas is pulled in at the sample inlet (1) and through the cooler (2) by the sample pump (6). The cooler (2) operates at
approximately 5°C (41°F). The moisture in the sample gas drops out inside the heat exchanger (integral to the cooler) and is de-
livered to the condensate outlet (10) by the condensate pump (3). The condensate pump is often referred to as a peristaltic
pump.
The heat exchanger temperature is shown in the display (30). In the event of a cooler (2) overload and temperature increase of
3K the sample pump (6) will turn off to avoid downstream moisture damage, and the temperature alarm LED (25) will turn red.
Additionally, a highly sensitive moisture sensor (4) is located downstream from the cooler (2) and before the filter (5). If the mois-
ture sensor (4) detects even the slightest amount of moisture in the sample gas stream, the pump will turn off, and the moisture
alarm (26) will illuminate and the display shows “h20.1”.
Downstream from the moisture sensor (4) the sample gas passes through the filter (5) to remove particulates. The filter element
is visible and accessible at the front panel.
From the outlet of the filter the sample gas is directed to a manual three way valve (7) located on the front panel that allows
either sample gas or calibration gas to enter the inlet of the sample pump (6). The manual valve provides calibration gas directly
to the analyzers, bypassing the probe when in the calibration position.
The sample pump output passes through an adjustable flowmeter with needle valve (8a) to the analyzer(s). The portion of the
sample gas or calibration gas not required by the analyzer(s) flows through a second flowmeter without needle valve (8b). The
amount of sample gas being used by the analyzer(s) is the difference between the two flowmeters. Both flowmeters are visible
and accessible from the front panel. If flow decreases the set limit at flowmeter (8a), the flow alarm LED (27) on the front panel
will turn red.
Condensate pump (3) and gas pump (6) are redundant. Switches (3c and 6c) on relay board RB0291 (23) can be used to change
the active pumps.
Whenever the SCS is powered up the sample conditioning system is operating.
1.2.2 Calibration gas section
Up to 6 calibration gases and 1 zero gas (span 1 – span 6 + zero gas) can be connected to the bulkhead fittings (11a..g + zero gas)
on the rear panel of the SCS. The flow of each calibration gas is controlled by an independent solenoid valve (12a..g) into a com-
mon, adjustable flowmeter with needle valve (13) located on the front panel. From the flowmeter (13) the selected calibration gas
flows to the span outlet bulkhead fitting (14) located on the rear panel and to the manual three way valve (7). A specific calibra-
tion gas is selected using the mode switch (28) and indicated by the system mode LEDs (29), all located on the front panel. Calib-
ration gases can also be controlled by an external controller when the mode switch (28) is in the sample (external control) posi-
tion.
1.2.3 Blowback air section
Instrument air for blowback is connected to the inlet bulkhead fitting (15) on the rear panel. The blowback air pressure is adjus-
ted with a regulator (16), displayed on a pressure gauge (19) and controlled by a solenoid valve (17). The blowback air passes
through the outlet bulkhead fitting (18) located on the rear panel. Operation of the blowback solenoid is selected with the mode
switch (28) and indicated by a system mode LED on the front panel. Blowback air can also be controlled by an external controller
(40) when the mode switch (28) is in the sample (external control) position.
3Bühler Technologies GmbHBECS0031 ◦ 02/2020

SCS 104
1.2.4 Manual control
Manual control is exercised using the rotary (mode) switch (28). The selectable system modes are: "Blow-back", “Zero Air”,
“Sample (external control)”, "Span 1", "Span 2", "Span 3", "Span 4", "Span 5", and "Span 6". The selected mode is indicated by the
system mode LEDs (29). Rotating the mode switch to any position other than sample (external control), will direct the selected
calibration gas or air to the corresponding outlet.
The valves are switched with a short time delay, so the correct mode can be selected before any change in gas flow takes effect.
1.2.5 External control and monitoring
The SCS can be externally controlled only if the mode switch (28) is in the exernal control (sample) position. Each mode is selec-
ted using the corresponding dry contacts at the external control terminal block (40) located on the rear panel. When no external
contact is closed the SCS is in the sample mode. The externally selected mode is shown by the system mode display LEDs on the
front panel (29) and can be monitored at the mode output terminal board (41) on the rear panel. LED and status output for ex-
ternal control (sample) position are also active.
Alarms for moisture, flow and temperature can be monitored at the status output terminal block (42) on the rear panel. An open
contact indicates status OK. A closed contact indicates an alarm. The normal status of the contacts may be changed on the con-
troller module from normally open to normally closed.
1.3 Scope of delivery
– SCS analysis gas conditioning system
– Product Documentation
4 Bühler Technologies GmbH BECS0031 ◦ 02/2020

SCS 104
2 Safety instructions
2.1 Important advice
Operation of the device is only valid if:
– the product is used under the conditions described in the installation- and operation instruction, the intended application
according to the type plate and the intended use. In case of unauthorized modifications done by the user Bühler Technolo-
gies GmbH can not be held responsible for any damage,
– when complying with the specifications and markings on the nameplates.
– the performance limits given in the datasheets and in the installation- and operation instruction are obeyed,
– monitoring devices and safety devices are installed properly,
– service and repair is carried out by Bühler Technologies GmbH,
– only original spare parts are used.
This manual is part of the equipment. The manufacturer keeps the right to modify specifications without advanced notice. Keep
this manual for later use.
Signal words for warnings
DANGER
Signal word for an imminent danger with high risk, resulting in severe injuries or death if not avoided.
WARNING
Signal word for a hazardous situation with medium risk, possibly resulting in severe injuries or death if not
avoided.
CAUTION
Signal word for a hazardous situation with low risk, resulting in damaged to the device or the property or
minor or medium injuries if not avoided.
NOTICE
Signal word for important information to the product.
Warning signs
In this manual, the following warning signs are used:
Warning against hazardous situations General notice
Warning against electrical voltage Disconnect from mains
Warning against respiration of toxic gases Wear respirator
Warning against acid and corrosive substances Wear eye/face protection
Warning against potentially explosive atmospheres Wear protection gloves
Warning against hot surface
5Bühler Technologies GmbHBECS0031 ◦ 02/2020

SCS 104
2.2 General hazard warnings
The equipment must be installed by a professional familiar with the safety requirements and risks.
Be sure to observe the safety regulations and generally applicable rules of technology relevant for the installation site. Prevent
malfunctions and avoid personal injuries and property damage.
The operator of the system must ensure:
– Safety notices and operating instructions are available and observed,
– The respective national accident prevention regulations are observed,
– The permissible data and operational conditions are maintained,
– Safety guards are used and mandatory maintenance is performed,
– Legal regulations are observed during disposal,
– compliance with national installation regulations.
– the device is protected from mechanical loads.
Maintenance, Repair
Please note during maintenance and repairs:
– Repairs to the unit must be performed by Bühler authorised personnel.
– Only perform conversion-, maintenance or installation work described in these operating and installation instructions.
– Always use genuine spare parts.
– Do not install damaged or defective spare part. If necessary, visually inspect prior to installation to determine any obvious
damage to the spare parts.
Always observe the applicable safety and operating regulations in the respective country of use when performing any type of
maintenance.
DANGER Electrical voltage
Electrocution hazard.
a) Disconnect the device from power supply.
b) Make sure that the equipment cannot be reconnected to mains unintentionally.
c) The device must be opened by trained staff only.
d) Regard correct mains voltage.
DANGER Toxic, corrosive gas/condensate
Sample gas/condensate may be hazardous to health.
a) If necessary, ensure a safe gas/condensate discharge.
b) Always disconnect the gas supply when performing maintenance or repairs.
c) Protect yourself from toxic/corrosive gasses/condensate when performing mainten-
ance. Wear appropriate protective equipment.
DANGER Potentially explosive atmosphere
Explosion hazard if used in hazardous areas.
The device is not suitable for operation in hazardous areas with potentially explosive at-
mospheres.
Do not expose the device to combustible or explosive gas mixtures.
6 Bühler Technologies GmbH BECS0031 ◦ 02/2020

SCS 104
3 Transport and storage
The device should be only transported in the original case or in appropriate packing.
If the device is not used for some time, protect it against heat and humidity. Store the device in a roofed, dry, and dust free
room. Temperature should be between –5 °C and 40 °C (23 °F and 104 °F).
7Bühler Technologies GmbHBECS0031 ◦ 02/2020

SCS 104
4 Installation and connection
4.1 Installation site requirements
The unit mounts in a 19 inch rack. Due to the weight the housing requires rails. These are available from the cabinet/rack manu-
facturer.
Please note, cooling generates waste heat inside the SCS. Adequate ventilation is therefore required (e.g. fan slot inside the cab-
inet).
The following requirements must be met during installation:
– Never install the system near sources of heat or vibration, in direct sunlight, or around high frequencies or magnetic fields.
The operator must install a lightning arrester.
– The system must be permanently installed in a location which can support the weight of the system.
– It must be protected from shock and impact.
– Never expose the display components to external forces.
– Never install the system outdoors.
4.2 Gas Line Connections
DANGER Toxic, acidic gasses
Sample gas can be harmful.
a) The gas lines and electric cables must be connected by a professional. Observe local
laws and regulations.
b) If necessary, ensure a safe gas discharge.
c) Switch off the gas supply before performing maintenance and secure against acci-
dental opening.
d) Protect yourself from toxic/corrosive gases. Wear suitable protective equipment.
The gas connections are 1/4” bulkhead fittings. Ensure the connections are tight.
4.3 Electrical connections
WARNING Hazardous electrical voltage
The device must be installed by trained staff only.
CAUTION Wrong mains voltage
Wrong mains voltage may damage the device.
Regard the correct mains voltage as given on the type plate.
Use the included M3 plug to connect to power. The plug insert can be installed turned to your liking. Please refer to the wiring
diagram in the appendix for the assignment.
The supply line diameters must be aligned with the rated current. Use a maximum line cross-section of 1.5mm2 and a cable dia-
meter of 8-10mm (0.31 – 0.39 inch).
CAUTION Same Voltage
The voltage at the clamps for the status must always be the same. Do not mix different
voltages at the clamps.
All other signals connect with the included connector.
8 Bühler Technologies GmbH BECS0031 ◦ 02/2020

SCS 104
CAUTION Supply cable
The power adapter must be suitable for the maximum power input of the device. It must
be heat-resistant and must not come into contact with hot surfaces. The power adapter
must meet IEC60227 or IEC60245. Or be approved by another recognised testing body.
Run the lines so the insulation will not be damaged. If necessary, secure the lines with suitable means and avoid excess line
lengths.
The power and voltage supply must be equipped with ELCB.
The ELCB (tripping current 30mA) must shut off the load within the specified period (200ms at 115VAC, 40ms at 230VAC). It
must be suitable for the maximum load.
9Bühler Technologies GmbHBECS0031 ◦ 02/2020

SCS 104
5 Operation and control
NOTICE
The device must not be operated beyond its specifications.
After switching on the system the block temperature will be displayed. The display will flash until the block temperature has
reached the set target value (± adjustable alarm range). The status contact is in the temperature alarm position.
Once the target temperature range has been reached, the temperature will continuously be displayed and the status contact
switches over.
If the display flashes during operation or an error message appears, please refer to item "Troubleshooting [> page19]”.
Please refer to the technical data for performance data and maximum ratings.
5.1 Start up
Confirm the SCS is correctly mounted and wired and perform the following procedure in order:
Verify the filter (5) cover is correctly closed (tighten clockwise by hand).
Switch on the SCS. The on/off switch (20a) is located on the PS0191 (20c) front panel.
– The cooler fan will turn on.
– The green power LED will illuminate.
– System mode LED (green) “Sample” will light.
– The cooler display (30) shows the system software version for some seconds (e.g. “d2,03”, “n1.13”)
– On initial power up the cooler display (30) will register approximately ambient temperature (blinking), and the temperature
alarm LED will be red.
The alarm LED will continue to stay red until the cooler temperature drops to 8°C (46°F). When the cooler temperature drops to
8°C (46°F), the sample pump will come on.
The condensate pump comes on any way.
The SCS is now ready for operation.
5.2 Using the device menu
The mode switch (28) can also be used for further settings, e.g. cooler temperature.
5.2.1 Use of menu functions
Turn/rotate mode switch (28) for menu interaction:
Key Section Function
Short push Display – No function
Menu – Select the menu item displayed
Enter – Applies an edited value or a selection
Long push Display – Keep switch pushed until display changes for seconds to enter device menu
Menu – Flip back to initial display
Enter – No function
Rotate clockwise Display – Set system mode
Menu – Move menu, see „Overview of the menu items“
Enter – Decrease parameter value
Rotate counter
clockwise
Display – Set system mode
Menu – Move menu, see „Overview of the menu items“
Enter – Increase parameter value
10 Bühler Technologies GmbH BECS0031 ◦ 02/2020

SCS 104
5.2.2 Lock Menu
Some menus can be locked to prevent inadvertently changing the settings of the unit. This requires setting a code. For informa-
tion on setting up or disabling the menu lock please refer to "Global Settings" (toP) under menu item toP>Loc.
The menu lock is not enabled at the time of delivery, all menu items can be accessed.
5.2.3 Overview of the menu items
When pressing the mode switch (28) in normal mode, the display will show the prompt code if the menu is locked. Enter the
right code by rotating the mode switch (28) and accept with a push.
If an incorrect code or no code is entered, the menu will not be unlocked and you will not be able to access all menu items.
If you forgot the password you can always enter master code 287 to access the menu; the menu will be unlocked.
The following image shows an overview of the menu structure.
Items with a dashed frame will only appear with the respective settings or with the respective status messages.
The factory defaults and settings ranges are specified in the overview as well as under the respective menu item. The factory de-
faults apply unless otherwise agreed.
Menu:
Top Settings top
Globale Einstellungen
3
21
1.
2.
3.
Menu designation
Display
Brief description
Parameter:
Eingabe 5'C
-20 . . . 60 'C
6
54
4.
5.
6.
Value input
Factory preset
Parameter range
Auswahl oP
op haLf Lo hi
9
87
7.
8.
9.
Selecting from the list of values
Factory preset
Parameter range/selection
Optional menu navigation:
10
10. dashed box = Optional
11Bühler Technologies GmbHBECS0031 ◦ 02/2020

SCS 104
OK
OK OK
OK
OK
OK
Selection unit
'C - 'F
SCS 104 ScS
Device designation
Display SLct
Temperature
Top Settings top
Global settings
Settings menu unit
Temperature unit
Temperature tEmP
Target temp. Cooling block
Exit E
Close submenu
OK
Display Main menu Submenu 1 Submenu 2 Parameter
Input 5'C
2 . . . 20 °'C
OK
OK Input 3'C
1 . . . 7 °'C
Settings menu A hi
Alarm hysteresis
Settings menu A Lo
Alarm hysteresis
Drop down menu h2o
Drop down menu sen
Moisture detector 1 sensitivity
OK Input -3'C
-1 . . . -3 'C
Calibrate moisture detector 1
Moisture detector 1 rst
OK
Input non
non - hi - Lo
OK
Confirm
Error Err
Status message
Login Loc
Enable menu lock
Input 0
0. . . . 9999
OK
Reset rSt
Factory settings
Exit E
Close submenu
Confirm rst
yes - no
OK
Exit E
Close submenu
Drop down menu hLtc
Humidity auto reset
Input no
yes - no
OK
Drop down menu bLtc
Cable break auto reset
Input YES
yes - no
OK
Restart rESt
Restart device
Confirm no
yes - no
OK
Drop down menu h.chn
Heat exchanger material selection
OK Drop down menu tS
(Steel)
tS (Glass)
t6 (PVDF)
tU
Fig.1: Menu overview
12 Bühler Technologies GmbH BECS0031 ◦ 02/2020

SCS 104
5.2.4 Description of menu functions
5.2.4.1 Main menu
Cooler of the SCS-system
Display → ScS
This will take you to the cooler target temperature and the tolerance range setting (alarm
threshold).
Global setting (ToP Settings)
Display → toP
This menu is used to configure the global cooler settings.
Heat exchanger material selection
Display → h.chn
Heat exchanger material selection
Parameter range: tS (Steel), t6 (Glass), tU (PVDF)
Factory setting: tS (cooler without heat exchanger), or respective material per configuration
Exit main menu
Display → E
Selecting this will return you to display mode.
5.2.4.2 Submenu 1
Target temperature (Temperature)
Display → Cooler → temp
This setting determines the nominal temperature for the cooler temperature.
Parameter range: 2 °C to 20 °C (35.6 °F to 68 °F)
Factory setting: 5 °C (41 °F)
Note: If the temperature is changed the indicator may blink, until the new operating range has been
reached.
This menu item is hidden if the keylock is enabled.
upper alarm limit (alarm high)
Display → Cooler → A hi
Here you can set the upper threshold for the visual signal and the alarm relay. The alarm limit is set
based on the cooler temperature setting.
Parameter range: 1 °C to 7 °C (1.8 °F to 12.6 °F)
Factory setting: 3 °C (5.4 °F)
Note: This menu item is hidden if the keylock is enabled.
13Bühler Technologies GmbHBECS0031 ◦ 02/2020

SCS 104
lower alarm limit (alarm low)
Display → Cooler → A Lo
Here you can set the lower threshold for the visual signal and the alarm relay. The alarm limit is set
based on the cooler temperature setting.
Parameter range: -1 °C to -3 °C (-1.8 °F to -5.4 °F)
Factory setting: -3 °C (-5.4 °F)
Note: This menu item is hidden if the keylock is enabled.
Exit submenu 1
Display → Submenu → E
Selecting this will return you to the main menu.
5.2.4.3 Submenu global settings
Temperature unit
Display → toP → unit
Used to select the temperature display unit.
Parameter range: °C, °F
Factory setting: °C
Calibrate moisture detector
Display → toP → h2o (h2o)
If a moisture detector is installed, calibration can now be performed. To do so, the unit must be
flushed with dry gas.
Note: Calibration was performed at the factory using ambient air. After replacing the moisture detector a
calibration is again required.
Calibrating the moisture detector will set the menu sEn to hi.
This menu will be hidden if the menu is locked.
If the unit has multiple moisture detectors built in, they will be numbered in the menu. In this case, h2o indicates the first, h2o2
the second moisture detector. The same applies to setting the sensor sensitivity in menu SEn.
Moisture detector sensitivity
Display → toP → SEn
If moisture detectors are installed, the sensitivity can be reduced here.
Parameter range: hi: high sensitivity
Lo: low sensitivity
non: no moisture detector
Factory setting: hi
Note: This menu will be hidden if the menu is locked.
14 Bühler Technologies GmbH BECS0031 ◦ 02/2020

SCS 104
Moisture detector: automatic reset following moisture ingress
Display → toP → hLtc
(hLtc = humidity latch). The setting applies to all connected moisture detectors.
Specifies whether the moisture ingress message must be reset manually or will automatically be re-
set after the sensor dries.
Parameter range: YES: The status will be indicated until the user restarts the device and the pumps will be deactivated.
no: The status message will automatically be cleared. The pumps will be reactivated again once
moisture is no longer detected.
Factory setting: no
Note: This menu will be hidden if the menu is locked.
Moisture detector: error cleared automatically after cable break
Display → toP → bLtc
(bLtc = broken wire latch). The setting applies to all connected moisture detectors.
Determines whether the cable break alarm must be reset manually or will automatically clear on
valid measuring signal.
Parameter range: YES: The status will be indicated until the user restarts the device. Clears the error, and the pumps
will be deactivated.
no: The error message will disappear. The pumps will be switched on again once the moisture de-
tector is reactivated again.
Factory setting: YES
Note: This menu will be hidden if the menu is locked.
Lock Menu
To protect the menu from unauthorised use, enter a value for the lock code. Menu items can then only be accessed after enter-
ing the correct code.
Display → toP → Loc
This setting will cancel/enable the menu lock.
Parameter range: 0 to 9999
Factory setting: 0 (keylock cancelled)
Note: This menu will be hidden if the menu is locked.
Restart
Display → toP → rESt
(rESt = restart)
The device will restart, all settings are saved. All error messages will be reset.
The moisture detector will be reset, irrespective of the settings in menus h.Itc and h.Moi.
Parameter range: YES: Restart. The display will show the software version for the device and returns to measurement
display.
no: Exit menu without restarting.
Note: The user settings will be saved.
15Bühler Technologies GmbHBECS0031 ◦ 02/2020

SCS 104
Factory settings
Display → toP → rst
This setting restores the factory settings.
Parameter range: Yes: factory settings restored.
No: Exit menu without making changes.
Factory setting: No
Note: This menu will be hidden if the menu is locked.
Exit submenu 1
Display → Submenu → E
Selecting this will return you to the main menu.
5.3 Manual operation of the SCS (front panel module CM0191)
The active gas path is selected with the mode switch (28). Calibration gas flow is selected by rotating the mode switch to the de-
sired span position as indicated by the system mode LED (29). The condition "Sample" starts active after start of the system.
To enter device menu push mode switch (28) for some seconds until dispay (30) shows “SCS”.
5.4 Monitoring system operation on the controller module (front panel module
CM0191)
The controller module (24) contains the display (30) for the current cooler temperature. The temperature shown in the display is
that of the cooling block which is nearly identical to the cooler gas outlet temperature and therefore, the outlet dew point. If the
cooler temperature rises above 8°C (46°F), the sample gas pump will stop.
On the left side of the CM0191 panel are the alarm LEDs for temperature moisture and flow.
If moisture is detected by the moisture sensor (4), the moisture alarm LED is illuminated, and the sample gas pump is turned off.
The Flow LED turns red, if the flow at flowmeter 8a is below the alarm level. For correct monitoring the flow has to cross the level
once.
5.5 External control
To enable external control of the SCS the mode switch must be in the sample (external control) position. If the mode switch is in
any other position, external control is disabled.
To activate external selection of any of the modes the corresponding terminals on the external control terminal block (40) must
be wired to an external contact. When an external contact is closed, that operational mode is engaged. If the mode switch is in
the sample (external control) position and NO external contacts are closed, the SCS is in the sample mode.
Multiple modes can be selected at the same time.
5.6 External monitoring
The mode and status of the SCS can be monitored by external devices. All outputs are dry contact and are available during both
manual and sample (external control).
The system mode contacts are available at the mode output terminal block (41). A closed contact indicates the corresponding
mode is activated. If no contacts are closed and the mode switch is in the sample (external control) position, the SCS is in the
sample mode.
The status output contacts are available at the status output terminal block (42). The sample gas path activity is defined by the
status of the cooler, flow and moisture detector. In normal operation the alarm status contacts for the cooler and moisture de-
tector are open. Contact closure indicates moisture has been detected, or the cooler has failed.
16 Bühler Technologies GmbH BECS0031 ◦ 02/2020

SCS 104
5.7 Flow Meter Operation
The flow meters have a range of 50..500L/h. The flow can be controlled with the built-in valves.
The flow meters are calibrated for air at 20 °C (68 °F) and 1.2 bar (17.4 psi) abs. Actual values may therefore vary when using other
calibrating and sample gases.
5.8 Pressure regulators and gauges
Blowback air pressure is controlled by a regulator (18) on the front panel. To adjust the pressure pull the regulator knob out to
unlock it and turn counter clockwise to decrease the pressure or clockwise to increase the pressure. When the desired pressure
has been obtained, push the knob in to lock it.
The set value is shown on a gauge (19).
17Bühler Technologies GmbHBECS0031 ◦ 02/2020

SCS 104
6 Maintenance
The following routine maintenance is required:
–Peristaltic pump: Check hoses
–Filter: Check filter element
–Moisture detector: Calibrate moisture detector
During maintenance, remember:
– The equipment must be maintained by a professional familiar with the safety requirements and risks.
– Only perform maintenance work described in these operating and installation instructions.
– When performing maintenance of any type, observe the respective safety and operation regulations.
DANGER Electrical voltage
Electrocution hazard.
a) Disconnect the device from power supply.
b) Make sure that the equipment cannot be reconnected to mains unintentionally.
c) The device must be opened by trained staff only.
d) Regard correct mains voltage.
DANGER Toxic, corrosive gas/condensate
Sample gas/condensate may be hazardous to health.
a) If necessary, ensure a safe gas/condensate discharge.
b) Always disconnect the gas supply when performing maintenance or repairs.
c) Protect yourself from toxic/corrosive gasses/condensate when performing mainten-
ance. Wear appropriate protective equipment.
18 Bühler Technologies GmbH BECS0031 ◦ 02/2020
Table of contents
Other Buhler Measuring Instrument manuals

Buhler
Buhler GAS 222.15 Reference guide

Buhler
Buhler APO User manual
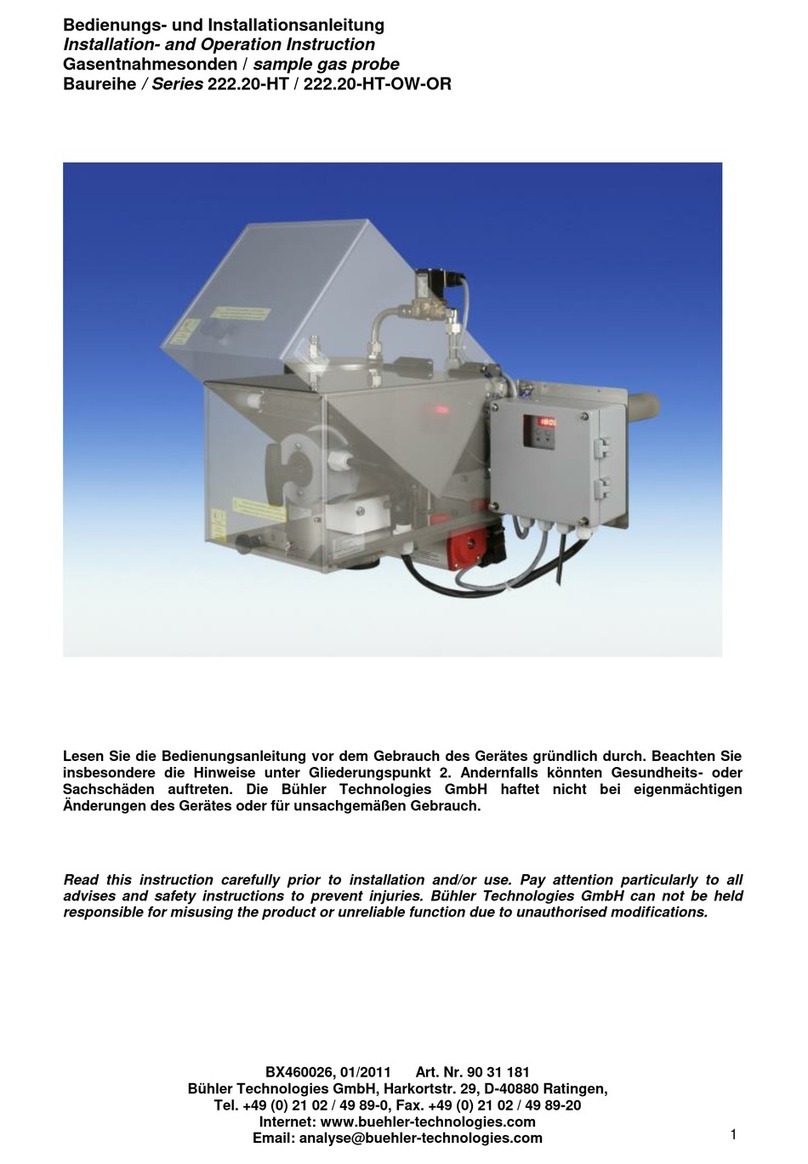
Buhler
Buhler GAS 222 Series Owner's manual
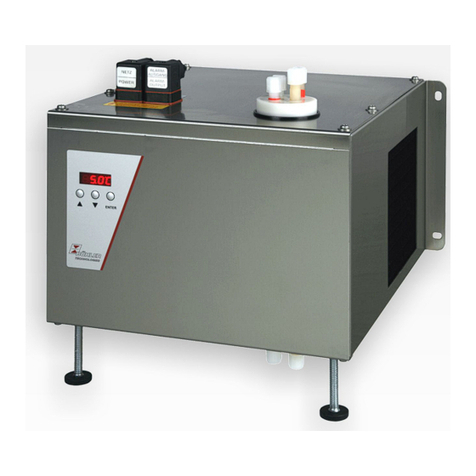
Buhler
Buhler EGK 1SD User manual

Buhler
Buhler SM-6 User manual
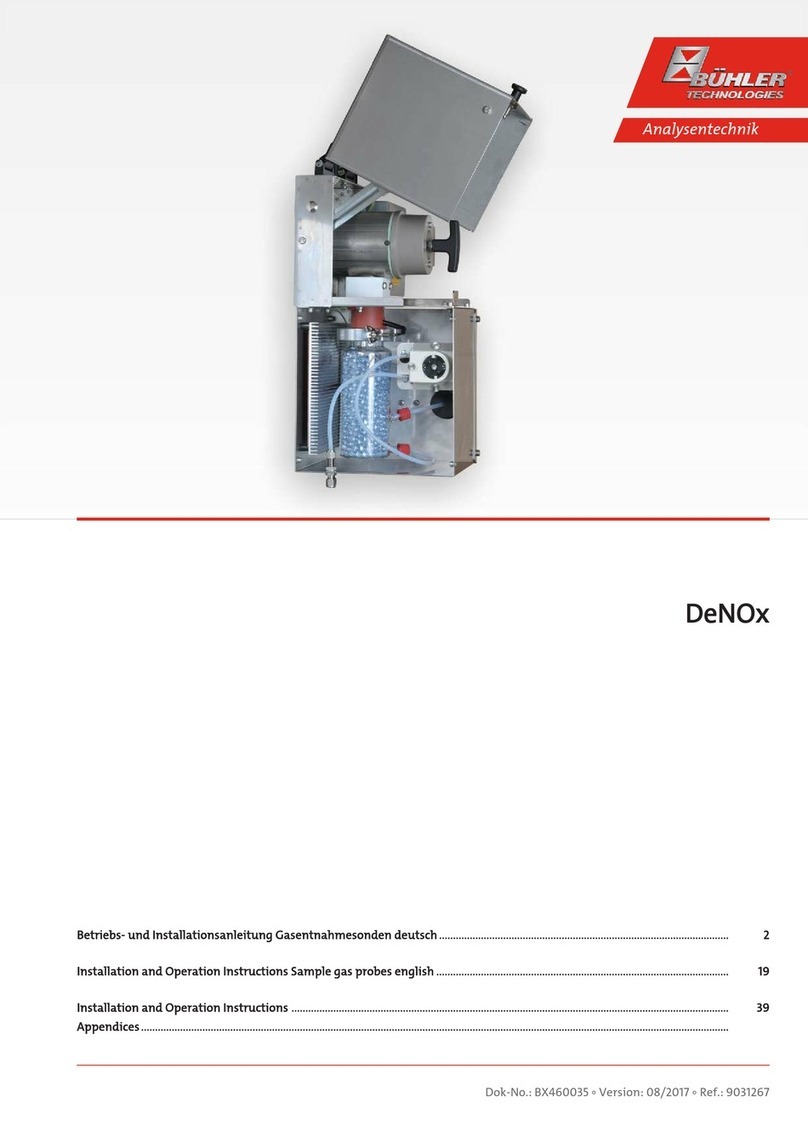
Buhler
Buhler DeNOx User manual

Buhler
Buhler GAS 222.20 Denox User manual

Buhler
Buhler BA 4000 Inj. GV User manual

Buhler
Buhler Nivotemp NT M-XP Series User manual
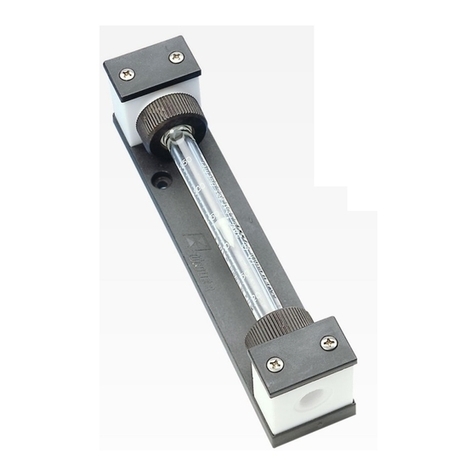
Buhler
Buhler SM-6 Reference guide
Popular Measuring Instrument manuals by other brands
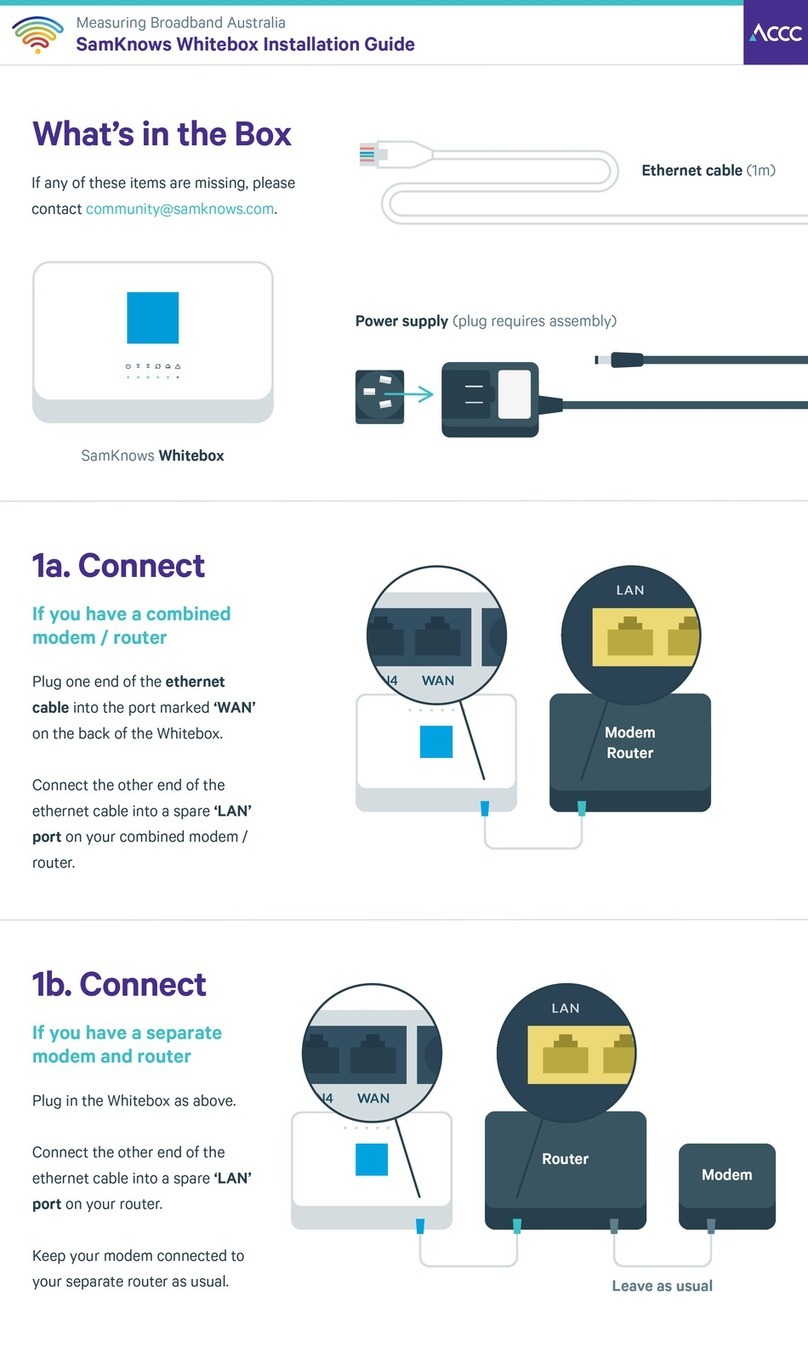
SamKnows
SamKnows Whitebox installation guide
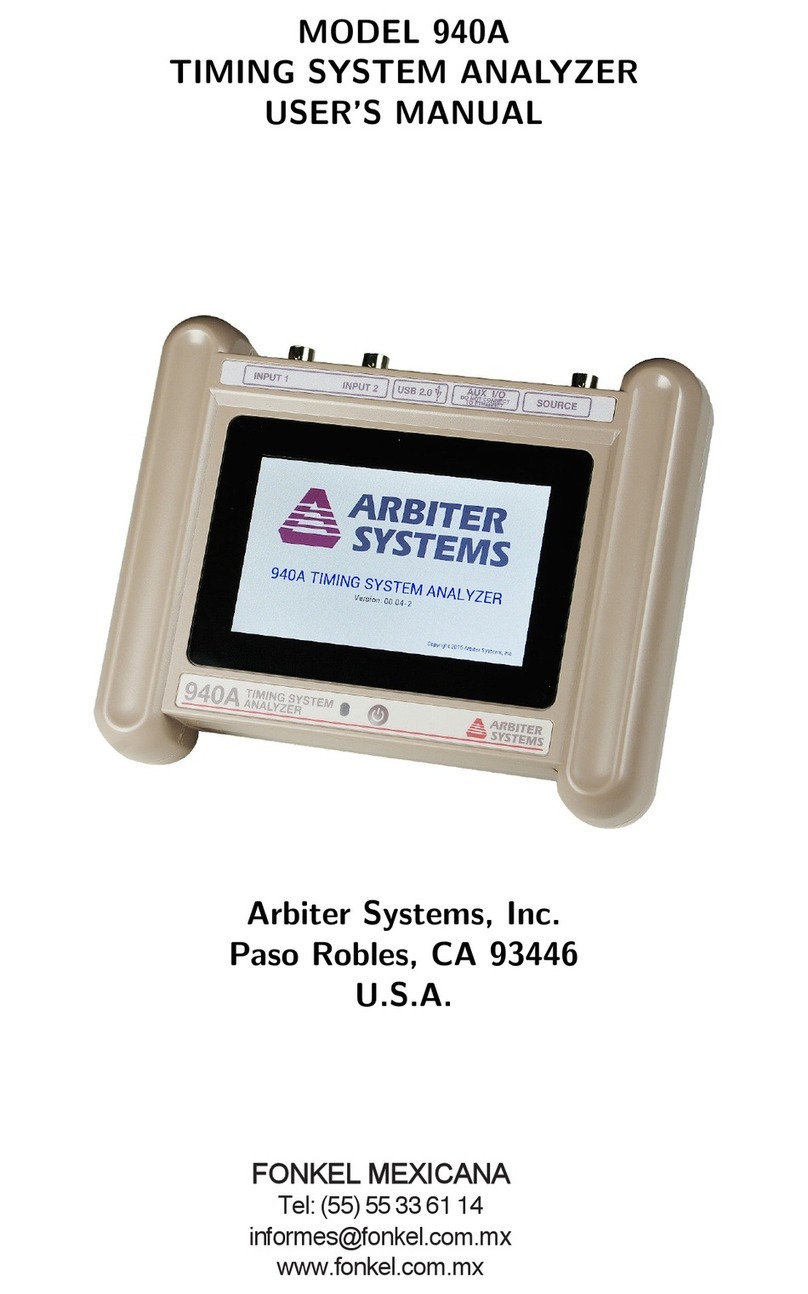
Arbiter Systems
Arbiter Systems 940A user manual

ZURN
ZURN ZEG6003EV Installation, operation, maintenance and parts manual
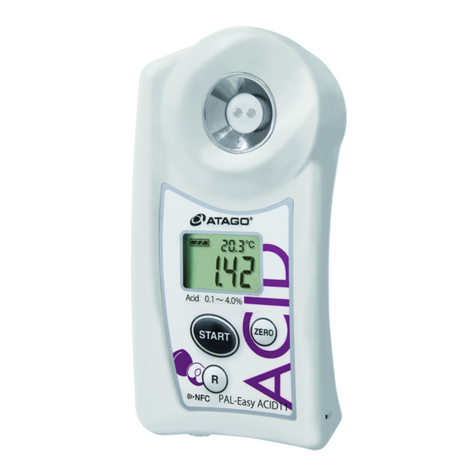
ATAGO
ATAGO PAL-Easy ACID11 instruction manual

Simex
Simex SPI-638 user manual

Bacharach
Bacharach Monoxor Plus Configuration and operation manual