Campbell CS451 User manual

CS451/CS456
Submersible Pressure Transducer
Revision: 8/19
Copyright © 2009 – 2019
Campbell Scientific


Guarantee
This equipment is guaranteed against defects in materials and workmanship.
We will repair or replace products which prove to be defective during the
guarantee period as detailed on your invoice, provided they are returned to us
prepaid. The guarantee will not apply to:
Equipment which has been modified or altered in any way without the
written permission of Campbell Scientific
Batteries
Any product which has been subjected to misuse, neglect, acts of God or
damage in transit.
Campbell Scientific will return guaranteed equipment by surface carrier
prepaid. Campbell Scientific will not reimburse the claimant for costs incurred
in removing and/or reinstalling equipment. This guarantee and the Company’s
obligation thereunder is in lieu of all other guarantees, expressed or implied,
including those of suitability and fitness for a particular purpose. Campbell
Scientific is not liable for consequential damage.
Please inform us before returning equipment and obtain a Repair Reference
Number whether the repair is under guarantee or not. Please state the faults as
clearly as possible, and if the product is out of the guarantee period it should
be accompanied by a purchase order. Quotations for repairs can be given on
request. It is the policy of Campbell Scientific to protect the health of its
employees and provide a safe working environment, in support of this policy a
“Declaration of Hazardous Material and Decontamination” form will be
issued for completion.
When returning equipment, the Repair Reference Number must be clearly
marked on the outside of the package. Complete the “Declaration of
Hazardous Material and Decontamination” form and ensure a completed copy
is returned with your goods. Please note your Repair may not be processed if
you do not include a copy of this form and Campbell Scientific Ltd reserves
the right to return goods at the customers’ expense.
Note that goods sent air freight are subject to Customs clearance fees which
Campbell Scientific will charge to customers. In many cases, these charges are
greater than the cost of the repair.
Campbell Scientific Ltd,
80 Hathern Road,
Shepshed, Loughborough, LE12 9GX, UK
Tel: +44 (0) 1509 601141
Fax: +44 (0) 1509 270924
Email: support@campbellsci.co.uk
www.campbellsci.co.uk


PLEASE READ FIRST
About this manual
Please note that this manual was originally produced by Campbell Scientific Inc. primarily for the North
American market. Some spellings, weights and measures may reflect this origin.
Some useful conversion factors:
Area: 1 in2(square inch) = 645 mm2
Length: 1 in. (inch) = 25.4 mm
1 ft (foot) = 304.8 mm
1 yard = 0.914 m
1 mile = 1.609 km
Mass: 1 oz. (ounce) = 28.35 g
1 lb (pound weight) = 0.454 kg
Pressure: 1 psi (lb/in2) = 68.95 mb
Volume: 1 UK pint = 568.3 ml
1 UK gallon = 4.546 litres
1 US gallon = 3.785 litres
In addition, while most of the information in the manual is correct for all countries, certain information
is specific to the North American market and so may not be applicable to European users.
Differences include the U.S standard external power supply details where some information (for
example the AC transformer input voltage) will not be applicable for British/European use. Please note,
however, that when a power supply adapter is ordered it will be suitable for use in your country.
Reference to some radio transmitters, digital cell phones and aerials may also not be applicable
according to your locality.
Some brackets, shields and enclosure options, including wiring, are not sold as standard items in the
European market; in some cases alternatives are offered. Details of the alternatives will be covered in
separate manuals.
Part numbers prefixed with a “#” symbol are special order parts for use with non-EU variants or for
special installations. Please quote the full part number with the # when ordering.
Recycling information
At the end of this product’s life it should not be put in commercial or domestic refuse but
sent for recycling. Any batteries contained within the product or used during the
products life should be removed from the product and also be sent to an appropriate
recycling facility.
Campbell Scientific Ltd can advise on the recycling of the equipment and in some cases
arrange collection and the correct disposal of it, although charges may apply for some
items or territories.
For further advice or support, please contact Campbell Scientific Ltd, or your local agent.
Campbell Scientific Ltd, 80 Hathern Road, Shepshed, Loughborough, LE12 9GX,
UK Tel: +44 (0) 1509 601141 Fax: +44 (0) 1509 270924
Email: support@campbellsci.co.uk
www.campbellsci.co.uk


Safety
DANGER —MANY HAZARDS ARE ASSOCIATED WITH INSTALLING, USING, MAINTAINING, AND WORKING ON
OR AROUND TRIPODS, TOWERS, AND ANY ATTACHMENTS TO TRIPODS AND TOWERS SUCH AS SENSORS,
CROSSARMS, ENCLOSURES, ANTENNAS, ETC. FAILURE TO PROPERLY AND COMPLETELY ASSEMBLE,
INSTALL, OPERATE, USE, AND MAINTAIN TRIPODS, TOWERS, AND ATTACHMENTS, AND FAILURE TO HEED
WARNINGS, INCREASES THE RISK OF DEATH, ACCIDENT, SERIOUS INJURY, PROPERTY DAMAGE, AND
PRODUCT FAILURE. TAKE ALL REASONABLE PRECAUTIONS TO AVOID THESE HAZARDS. CHECK WITH YOUR
ORGANIZATION'S SAFETY COORDINATOR (OR POLICY) FOR PROCEDURES AND REQUIRED PROTECTIVE
EQUIPMENT PRIOR TO PERFORMING ANY WORK.
Use tripods, towers, and attachments to tripods and towers only for purposes for which they are designed. Do not
exceed design limits. Be familiar and comply with all instructions provided in product manuals. Manuals are
available at www.campbellsci.eu or by telephoning +44(0) 1509 828 888 (UK). You are responsible for conformance
with governing codes and regulations, including safety regulations, and the integrity and location of structures or land
to which towers, tripods, and any attachments are attached. Installation sites should be evaluated and approved by a
qualified engineer. If questions or concerns arise regarding installation, use, or maintenance of tripods, towers,
attachments, or electrical connections, consult with a licensed and qualified engineer or electrician.
General
•Prior to performing site or installation work, obtain required approvals and permits. Comply with all
governing structure-height regulations, such as those of the FAA in the USA.
•Use only qualified personnel for installation, use, and maintenance of tripods and towers, and any
attachments to tripods and towers. The use of licensed and qualified contractors is highly recommended.
•Read all applicable instructions carefully and understand procedures thoroughly before beginning work.
•Wear a hardhat and eye protection, and take other appropriate safety precautions while working on or
around tripods and towers.
•Do not climb tripods or towers at any time, and prohibit climbing by other persons. Take reasonable
precautions to secure tripod and tower sites from trespassers.
•Use only manufacturer recommended parts, materials, and tools.
Utility and Electrical
•You can be killed or sustain serious bodily injury if the tripod, tower, or attachments you are installing,
constructing, using, or maintaining, or a tool, stake, or anchor, come in contact with overhead or
underground utility lines.
•Maintain a distance of at least one-and-one-half times structure height, or 20 feet, or the distance
required by applicable law, whichever is greater, between overhead utility lines and the structure (tripod,
tower, attachments, or tools).
•Prior to performing site or installation work, inform all utility companies and have all underground utilities
marked.
•Comply with all electrical codes. Electrical equipment and related grounding devices should be installed
by a licensed and qualified electrician.
Elevated Work and Weather
•Exercise extreme caution when performing elevated work.
•Use appropriate equipment and safety practices.
•During installation and maintenance, keep tower and tripod sites clear of un-trained or non-essential
personnel. Take precautions to prevent elevated tools and objects from dropping.
•Do not perform any work in inclement weather, including wind, rain, snow, lightning, etc.
Maintenance
•Periodically (at least yearly) check for wear and damage, including corrosion, stress cracks, frayed cables,
loose cable clamps, cable tightness, etc. and take necessary corrective actions.
•Periodically (at least yearly) check electrical ground connections.
WHILE EVERY ATTEMPT IS MADE TO EMBODY THE HIGHEST DEGREE OF SAFETY IN ALL CAMPBELL
SCIENTIFIC PRODUCTS, THE CUSTOMER ASSUMES ALL RISK FROM ANY INJURY RESULTING FROM IMPROPER
INSTALLATION, USE, OR MAINTENANCE OF TRIPODS, TOWERS, OR ATTACHMENTS TO TRIPODS AND TOWERS
SUCH AS SENSORS, CROSSARMS, ENCLOSURES, ANTENNAS, ETC.


i
Table of Contents
PDF viewers: These page numbers refer to the printed version of this document. Use the
PDF reader bookmarks tab for links to specific sections.
1. Introduction................................................................ 1
2. Precautions ................................................................ 1
3. Initial Inspection ........................................................ 1
4. QuickStart .................................................................. 2
5. Overview .................................................................... 4
6. Specifications ............................................................ 6
7. Installation ................................................................. 8
7.1 Installation Considerations...................................................................8
7.1.1 Vent Tube......................................................................................8
7.1.2 Appropriate Water Depth..............................................................8
7.1.3 Dislodging Bubbles.......................................................................9
7.2 Installation Procedure...........................................................................9
7.2.1 Lower to Depth .............................................................................9
7.2.2 Secure the Transducer...................................................................9
7.2.2.1 Tie Wrap/Tape....................................................................9
7.2.2.2 Split Mesh Cable Grip ........................................................9
7.2.2.3 Heyco Cable Grip.............................................................10
7.2.3 Measure the Initial Elevation ......................................................11
7.2.4 Offset Calculation .......................................................................11
7.3 Wiring ................................................................................................11
7.3.1 SDI-12 Data Logger Connections ...............................................12
7.3.2 RS-232 Connections ...................................................................12
7.4 Programming......................................................................................12
7.5 Changing Nose Cones ........................................................................13
8. Operation ................................................................. 14
8.1 Configuration .....................................................................................14
8.1.1 Computer Connection Using the A200 .......................................14
8.1.1.1 Driver Installation.............................................................14
8.1.1.2A200 Wiring.....................................................................15
8.1.1.3 Powering the Sensor .........................................................15
8.1.1.4 Determining which COM Port the A200 has been
Assigned .......................................................................16
8.1.2 Device Configuration Utility (version 2.03 or higher) ................16
8.2 SDI-12 Commands.............................................................................17
8.3 Measuring Multiple SDI-12 Sensors..................................................19
8.4 Unit Command ...................................................................................19
8.5 Sample Number Command ................................................................20

Table of Contents
ii
9. Maintenance............................................................. 20
9.1 Every Visit .........................................................................................20
9.2 Every Two Years................................................................................21
10. Troubleshooting ...................................................... 21
Appendices
A. Importing Short Cut Code into CRBasic Editor... A-1
B. Example Programs ................................................ B-1
C. Calibration Certificate ........................................... C-1
D. SDI-12 Sensor Support.......................................... D-1
D.1 Introduction..................................................................................... D-1
D.2 SDI-12 Command Basics ................................................................ D-1
D.2.1 Acknowledge Active Command (a!)........................................ D-2
D.2.2 Send Identification Command (aI!) ......................................... D-2
D.2.3 Start Verification Command (aV!)........................................... D-2
D.2.4 Address Query Command (?!) ................................................. D-3
D.2.5 Change Address Command (aAb!) .......................................... D-3
D.2.6 Start Measurement Commands (aM!…aM9!) ......................... D-3
D.2.7 Start Concurrent Measurement Commands (aC!…aC9!) ........ D-4
D.2.8 Start Measurement Commands with Cyclic Redundancy
Check (aMC! and aCC!)....................................................... D-5
D.2.9 Stopping a Measurement Command ........................................ D-5
D.2.10 Send Data Command (aD0! … aD9!) ...................................... D-5
D.2.11 Extended Commands ............................................................... D-6
D.3 SDI-12 Transparent Mode............................................................... D-6
D.3.1 Changing an SDI-12 Address................................................... D-7
D.3.2 Changing an SDI-12 Address – CR200(X) Series ................... D-7
D.4 References....................................................................................... D-8
E. RS-232 Connection Via Computer Terminal
Software ................................................................E-1
Figures
5-1. CS451 nose cone options .....................................................................5
7-1. Transducer suspended with split mesh cable grip ..............................10
7-2. Heyco Cable Grip...............................................................................10
7-3. Transducer mounted in PVC pipe using the Heyco cable grip...........11
7-4. Screws on the standard nose cone (top), NPT nose cone (middle),
and weighted nose cone (bottom) ...................................................14
8-1. A200 Sensor-to-Computer Interface ..................................................15
8-2. Connect screen ...................................................................................16

Table of Contents
iii
Tables
7-1.Wire Colour, Function, and Data Logger Connection for SDI-12
Measurements.................................................................................12
7-2. Wire Colour, Function, Data Logger Connection, and RS-232 Pin .....12
8-1. Factory Settings..................................................................................14
8-2. Wire Colour, Function, and A200 Connection...................................15
8-3. CS451/CS456 SDI-12 Commands .....................................................17
D-1. Campbell Scientific Sensor SDI-12 Command and Response Set.. D-1
D-2. Example aM! Sequence................................................................... D-3
D-3. Example aC! Sequence ................................................................... D-4
E-1. RS-232 Settings................................................................................E-1
E-2. RS-232 Terminal Commands...........................................................E-2
CRBasic Examples
B-1. CS451 SDI-12 Program for CR1000X Data Logger........................B-1
B-2. CS451 SDI-12 Program for CR200(X)-Series Data Logger ............B-2


1
CS451/CS456 Submersible Pressure
Transducer
1. Introduction
The CS451/CS456 Submersible Pressure Transducer provides pressure and
temperature measurements. It uses the SDI-12 or RS-232 communications
protocols to communicate with an SDI-12 or RS-232 recorder simplifying
installation and programming.
This manual provides information only for CRBasic data loggers.
For retired Edlog data logger support, access a retired manual at
www.campbellsci.com/old-manuals.
2. Precautions
•READ AND UNDERSTAND the Safety section at the front of this
manual.
•Sensor will be damaged if it is encased in frozen liquid.
•Although the CS451/CS456 is rugged, it is also a highly precise scientific
instrument and should be handled as such. There are no user-serviceable
parts and any attempt to disassemble the device will void the warranty.
•Dropping the instrument or allowing it to “free fall” down a well may
damage the transducer.
•Never suspend the CS451/CS456 from the connections at the top end of
the cable. Sharp bends or excessive pinching of the cable can cause
damage and may pinch off the vent tube causing measurement errors.
•Confirm the compatibility of the sensor and cable to non-water
environments before installation.
•The CS456, instead of the CS451, should be used in harsh water
applications, including salt water.
3. Initial Inspection
•Upon receipt of the CS451/CS456, inspect the packaging for any signs of
shipping damage and, if found, report the damage to the carrier in
accordance with policy. Also inspect the contents of the package and file a
claim if shipping related damage is discovered.
•The model number and pressure range is etched on the housing, and the
cable length is printed on the label near the connection end of the cable.
Check this information against the shipping documentation to ensure that
the expected product was received.
•Ensure the desiccant tube is attached to the vent tube on the cable.
Desiccant should be orange or blue. Replace it if the desiccant is green or
pale pink.
NOTE

CS451/CS456 Submersible Pressure Transducer
2
4. QuickStart
Avideo that describes data logger programming using Short Cut is available
at: www.campbellsci.eu/videos/cr1000x-datalogger-getting-started-program-
part-3. Short Cut is an easy way toprogram your data logger to measure the
sensor and assign data logger wiring terminals. Short Cut is available as a
download on www.campbellsci.eu.It is included in installations ofLoggerNet,
PC200W, PC400, or RTDAQ.
The following procedure also describes programming with Short Cut.
1. Open Short Cut and click Create New Program.
2. Double-click the data logger model.
3. In the Available Sensors and Devices box, type CS451 (1). You can also
locate the sensor in the Sensors | Water | Level & Flow folder. Double-
click CS450/CS451/CS455/CS456 Pressure Transducer (2). Water level
defaults to feet and temperature defaults to degrees Celsius. These can be
changed by clicking the Water Level (3) or Temperature (4) box and
selecting a different option. Type the correct SDI-12 Address (5) for the
CS451. After entering the Properties, click on the Wiring (6) tab to see
how the sensor is to be wired to the data logger.

CS451/CS456 Submersible Pressure Transducer
3
4. In the Available Sensors and Devices box, type Offset (1) and double-
click the Offset Calculation (2) under the Sensors | Water | Level &
Flow folder. For the Linked Level parameter (3), select the variable that
stores the level measurement (typically Lvl_ft or Lvl_m). Type the initial
water level in the Observed Level Reading box (4).
5. Repeat step three for other sensors being measured.

CS451/CS456 Submersible Pressure Transducer
4
6. In Output Setup, enter the scan rate (1), Data Output Storage Intervals
(2), and meaningful table names (3).
7. Select the measurement and its associated output options.
8. Click Finish and save the program. Send the program to the data logger if
the data logger is connected to the computer.
9. If the sensor is connected to the data logger, check the output of the sensor
in the data display in LoggerNet, PC400, RTDAQ, or PC200W to make
sure it is making reasonable measurements.
5. Overview
The CS451/CS456 pressure transducer provides a reliable, accurate
pressure/level measurement that is fully temperature compensated. Its 24-bit
A/D has simultaneous 50/60 Hz rejection and automatic calibration for each
measurement.
A number of additional advanced measurement techniques are employed to
harness the best possible performance available from today’s state-of-the-art
pressure transducer technology. The transducer reverts to a low power sleep

CS451/CS456 Submersible Pressure Transducer
5
state between measurements. Aseries ofmeasurements are performed yielding
a temperature and pressure value. This measurement cycle takes less than 1.5 s.
The transducer can also be configured to output pressure onlyinless than 1 s.
The measurement cycle is activated using SDI-12 or RS-232 commands.
The transducer consists ofa piezoresistive sensor housed in a 316L stainless-
steel (CS451) ortitanium (CS456) package to enhance reliability. The rugged
construction makes the CS451/CS456 suitable for water level measurement in
irrigation applications, water wells, lakes, streams, and tanks. The titanium
package of the CS456 makes itideal for salt water orother harsh environments.
The cable incorporates a vent tube to compensate for atmospheric pressure
fluctuations and the jacket ismade ofrugged Hytrel®, designed toremain
flexible and tough, even under harsh environmental conditions.
The CS451/CS456 has two communication options: SDI-12 and RS-232. The
CS451/CS456 is shipped from the factory with both communications options
enabled. As an SDI-12 sensor, the CS451/CS456 is shipped with an address of 0.
Two values are output bythe CS451/CS456—pressure/level andtemperature.
By default, the sensor outputs pressure in pounds per square inch gauge (psig),
which isthe pressure relative to atmospheric pressure. Bydefault, the sensor
outputs temperature in degrees Celsius.
The CS451/CS456 has three nosecone options. FIGURE 5-1 shows the nose
cone options. The weighted nose cone makes the transducer easier tosubmerge
to depth. The 1/4-inch NPT nose cone allows the transducer tobe used in
closed-pipe applications. Nose cones can be switched out later. The nose cones
are available separately from Campbell Scientific, allowing the nose cone to be
changed toa different style at a later date, ifdesired.
FIGURE 5-1. CS451 nose cone options
Weighted Nose Cone
Standard Nose Cone
1/4 inch NPT Nose Cone

CS451/CS456 Submersible Pressure Transducer
6
6. Specifications
Features:
•Output acceptable for recording devices with SDI-12 or RS-232
capability including Campbell Scientific data loggers
•Quality construction ensures product reliability
•Rugged stainless steel or titanium case protects piezoresistive sensor
•Fully temperature compensated
•Low power sleep state between measurements reduces power
consumption
•Weighted nose cone offered adds 0.2 kg (7.4 oz) to the transducer
weight. Additional weight makes submersion of the transducer easier
•Compatible with Campbell Scientific CRBasic data loggers:
CR1000X, CR300 series, CR6, CR200(X) series, CR800 series,
CR1000, CR3000, and CR5000
Power Requirements: 5 to 18 VDC
Power Consumption: Quiescent current < 50 µA
Measurement/Communication Current: 8 mA
for 1-s measurement
Maximum Peak Current: 40 mA
Measurement Time: Less than 1.5 s
Outputs: SDI-12 (version 1.3) 1200 bps
RS-232 9600 bps, 8 data bits, no parity,
1 stop bit, no flow control
Measurement Ranges:
Pressure (psig) Pressure (kPa)
Depth of fresh water
0 to 2.9 0 to 20 0 to 2 m (6.7 ft)
0 to 7.25 0 to 50 0 to 5.1 m (16.7 ft)
0 to 14.5 0 to 100 0 to 10.2 m (33.4 ft)
0 to 29 0 to 200 0 to 20.4 m (67 ft)
0 to 72.5 0 to 500 0 to 50.9 m (167 ft)
0 to 145 0 to 1000 0 to 102 m (334.5 ft)
Accuracy: ±0.1% full scale range TEB1or
±0.05% full scale range TEB2
Water-Level Resolution: 0.0035% full scale range
Worst-Case
Temperature Resolution: 0.006 °C
Overpressure: Twice the pressure range
Dry Storage Temperature: –10 to 80 °C
Sensor will be damaged if it is encased in frozen liquid.
Operating Temperature: 0 to 60 °C
CAUTION

CS451/CS456 Submersible Pressure Transducer
7
Temperature Accuracy: ±0.2 °C
Maximum Cable Length:
SDI-12 (one transducer
connected to a single
terminal): ~475 m (1500 ft)
SDI-12 (10 transducers
connected to a single
terminal3): 60 m (200 ft)
RS-232: 60 m (200 ft)
Cable Type: 5 Conductor, 26 AWG
Hytrel Jacket
Body Material: CS451 – 316L Stainless Steel
CS456 – Titanium
Element Material: CS451 – 316L Stainless Steel
CS456 – Hastelloy
Standard Nose Cone Material: Delrin
Length: 213.36 mm (6.875 in)
Diameter: 21.34 mm (0.84 in)
Cable Outer Diameter: 0.589 cm (0.232 in) nominal
0.599 cm (0.236 in) maximum
Distance from pressure sensor
interface (black line etched on
housing) to:
End of NPT fitting: 2.54 cm (1 in)
End of standard nose cone: 2.3 cm (0.9 in)
End of weighted nose cone: 9.9 cm (3.9 in)
Air Gap
Standard and weighted
nose cone:
NPT fitting:
Weight:
Compliance:
0.653 cm(0.257 in)
2.72 cm (1.07 in)
CS451: 0.17 kg (0.37 lb)
CS456: 0.10 kg (0.23 lb)
Cable: 0.421 kg/m (0.283 lb/ft)
View the EUDeclaration ofConformity at:
www.campbellsci.eu/cs451
www.campbellsci.eu/cs456
1Total Error Band (TEB) includes the combined errors due to nonlinearity, hysteresis,
nonrepeatability, and thermal effects over the compensated temperature range, per
ISA S51.1.
20.05% full scale range accuracy not available in the 0 to 2.9 psig range.
3Campbell Scientific recommends using separate terminals when possible.

CS451/CS456 Submersible Pressure Transducer
8
7. Installation
If using Short Cut to program the data logger, skip Section 7.3, Wiring (p. 11),
and Section 7.4, Programming (p. 12). Short Cut automatically performs these
steps. See Section 4, QuickStart (p. 2), for a Short Cut tutorial.
7.1 Installation Considerations
7.1.1 Vent Tube
The CS451/CS456 is designed for water level measurements. Typical
applications include agricultural water level/flow, water wells, lakes, streams,
and tanks. If the device isto beinstalled in a liquid other than water orin
contaminated water, check the compatibility ofthe wetted material. The CS456
should beused in harsh water applications, including salt water.
Avent tube incorporated inthe cable vents the sensor diaphragm tothe
atmosphere. This eliminates the need tocompensate for changes inbarometric
pressure. To prevent water vapourfrom entering the inner cavity ofthe sensor,
the vent tube opening terminates inside a desiccant tube.
The desiccant tube is shipped with a black cap to cover the
vent hole. This cap MUST be removed prior to installation.
Before installing the sensor, check the desiccant and replace it if the desiccant
is green instead of orange.
Until August 2019, the CS451/CS456 used blue desiccant that
turned pink when it became saturated.
The desiccant tube must always be attached to the CS451/CS456.
7.1.2 Appropriate Water Depth
The CS451/CS456 must be installed below the water at a fixed depth. This
depth should be chosen so the water pressure will never exceed the transducer
overpressure range (twice the pressure range).
The output reading will not be correct, and the transducer
can be damaged if pressure is excessive (twice the pressure
range).
Pressure can be converted to feet of fresh water using the following
conversion:
1 psi = 2.31 feet of water
For example, the maximum depth with a pressure range of 0 to 7.25 psig is
16.748 feet of water.
CAUTION
NOTE
CAUTION
Other manuals for CS451
4
This manual suits for next models
1
Table of contents
Other Campbell Transducer manuals
Popular Transducer manuals by other brands
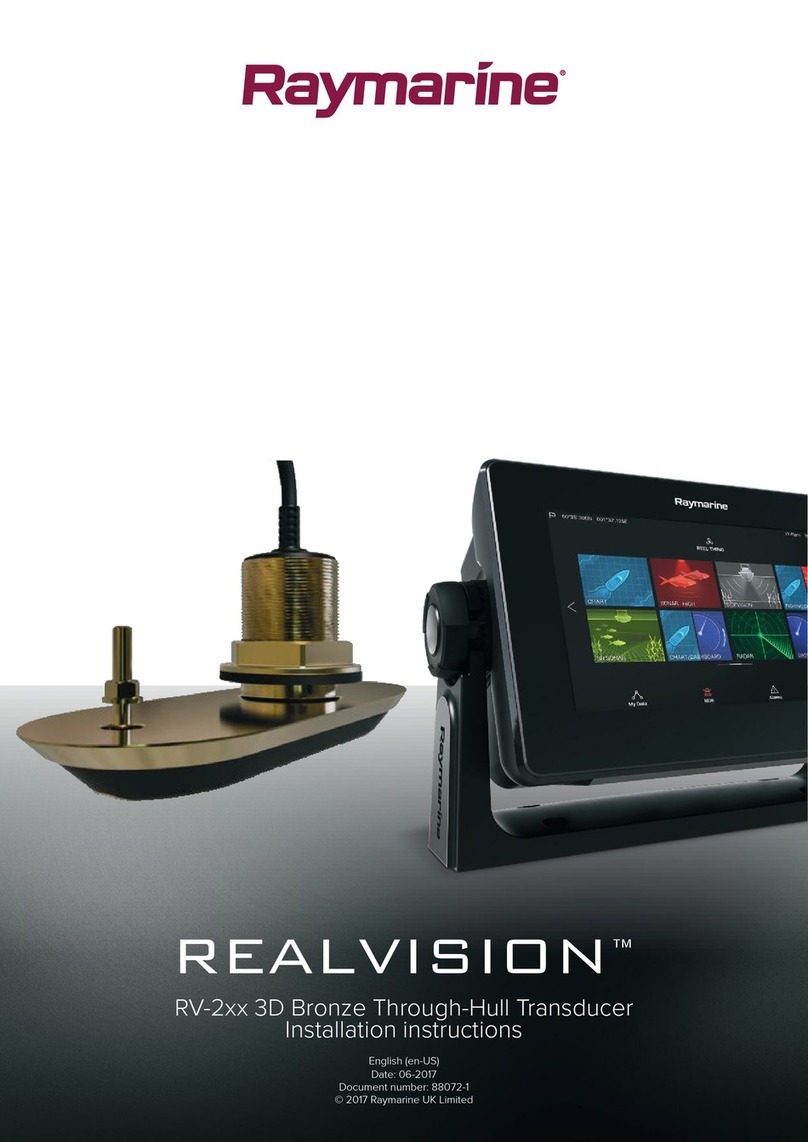
Raymarine
Raymarine Realvision RV-220P installation instructions
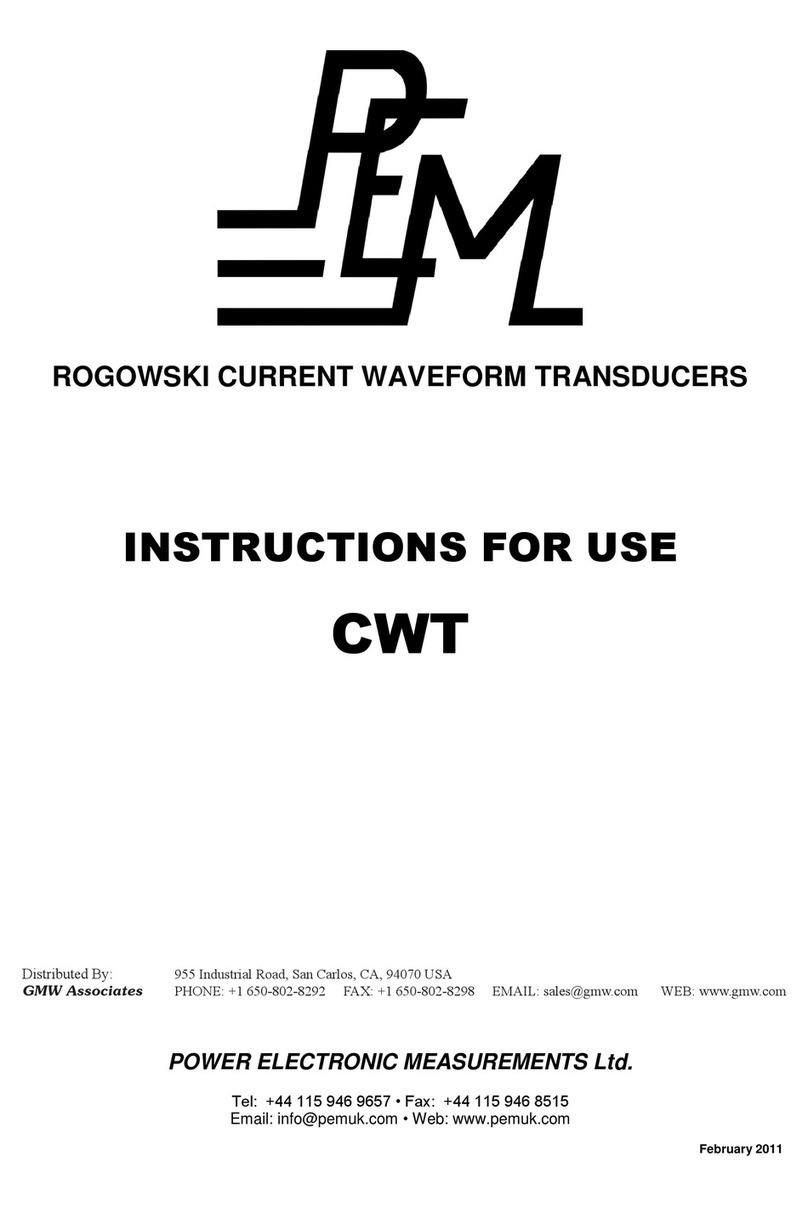
PEM
PEM CWT Instructions for use
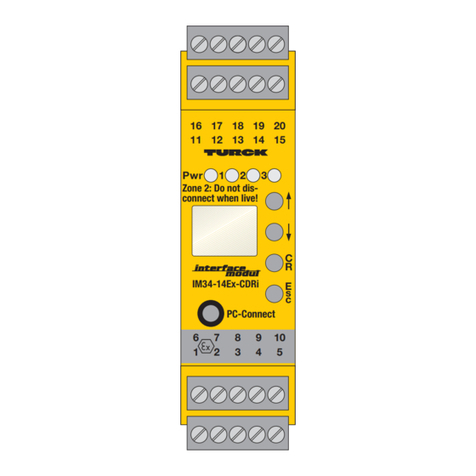
turck
turck IM34-14Ex-CDRi manual

BIOPAC Systems, Inc.
BIOPAC Systems, Inc. MP150 Hardware guide
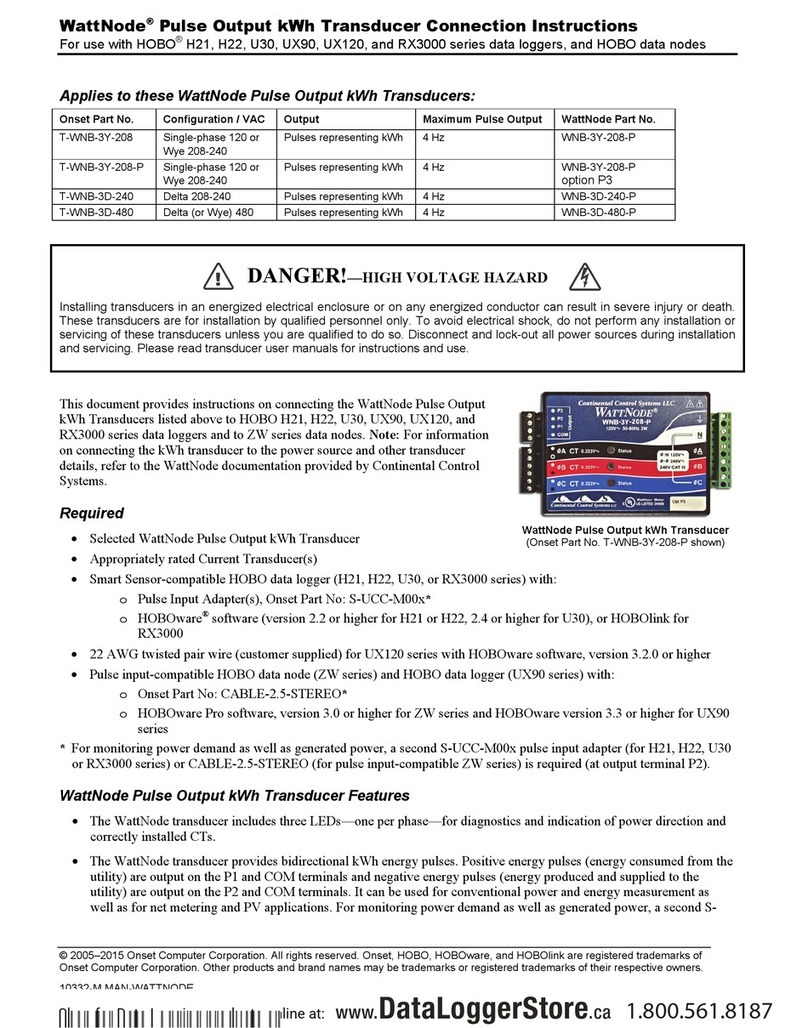
WattNode
WattNode T-WNB-3Y-208 Connection instructions

S+S Regeltechnik
S+S Regeltechnik THERMASGARD ALTM Operating Instructions, Mounting & Installation