Challenge SPARTAN 120 Technical reference manual

The
Challenge Machinery Company provides owner's
manuals on its products solely as a courtesy to its customers.
See the information below before using this manual.
These manuals are for reference only. These manuals include products which are non-
current, unsupported or no longer produced by The Challenge Machinery Company, and are
provided solely as an accomodation to our customers. By providing these manuals, The
Challenge Machinery Company makes no representation or warranty as to the products,
their current condition, or their suitability or fitness for use in any particular application, which
are the sole and independent responsibility of the product owner and user.
Older products may not comply with current safety procedures, guidelines or regulations,
and it is the product owner's and user's responsibility to evaluate the suitability and fitness of
the products in their current use and application. The Challenge Machinery Company makes
no representation, warranty or recommendation regarding any modifications which may be
required on non-current or unsupported products. The Challenge Machinery Company
assumes no liability for any modification or alteration to any Challenge product, and any such
modification or alteration to any Challenge product is not authorized by The Challenge
Machinery Company. The availability of these manuals is solely for the purpose of providing
reference information for the products.
This
manual
may not be
complete
in all aspects of
product
maintenance
and
repair.
All
products should be used only by qualified and properly trained personnel, following proper
safety procedures. All products should be regularly inspected and maintained, and their condition,
application and use should be periodically evaluated by qualified personnel. Only qualified and
properly trained technicians should perform maintenance,
repair
and replacement
procedures. Attempting
t
hese procedures without proper training
may
cause
machine
damage or
operator
injury!
Products
may be
unsupported by The Challenge Machinery Company
due to age or the
unavailability
of parts from their
original manufacturer.
No parts or
product support
will be
available
to repair or
maintain unsupported
products.
Older
products
may not be UL
listed (if
the product does not have a UL label it is not a listed product), and may not comply with
applicable installation or other regulations or requirements if
relocated
to a new
facility.
Many
municipalities require
a
product
to be UL
listed
before
an
electrician
will
connect
power
to them. Often the cost of updating an older product to comply with current safety regulations is
greater than the value of the product.

SPARTAN 120
SPARTAN 120SPARTAN 120
SPARTAN 120
BENCH TOP CUTTER
Sold and Serviced by
The Challenge Machinery Company
6125 Norton Center Drive
Norton Shores, MI 49441-6081 USA
ChallengeMachinery.com
Serial Numbers 99100 & Up
INSTRUCTION AND
PARTS MANUAL
NOTICE: UNSUPPORTED PRODUCT!
NO TECHNICAL SUPPORT AVAILABLE!
NO REPAIR PARTS AVAILABLE!

1.0 Introduction
2
1.0 Introduction
This manual is designed to help you get the most from your Challenge equipment. Keep this manual
in a safe, convenient place for quick reference by operators and service personnel.
SAFETY ALERT! This symbol means CAUTION: Personal safety
instructions! Pay special attention to the instructions in bold type.
Personal injury may result if the precautions are not read and followed.
READ THIS MANUAL BEFORE OPERATING! If you follow precautions and instructions, you should
have years of trouble-free operation. Contact your Authorized Challenge Dealer.
FOR PARTS AND SERVICE, contact the Authorized Challenge Dealer from whom you purchased
your machine. Use the illustrations and parts lists at the back of this manual to identify the correct
parts needed. Always give the SERIAL NUMBER and MODEL of your machine to insure the correct
parts are sent as soon as possible.
Take a few minutes right now to RECORD YOUR MACHINE SERIAL NUMBER in the space
provided on the front cover of this manual. Also be sure to fill out the warranty card accompanying
this manual and return it DIRECTLY TO CHALLENGE.
If you bought a used machine, it is important to have the following information on record at Challenge.
Copy this page, fill in the information and send it care of The Challenge Service Department, 6125
Norton Center Drive •Norton Shores •MI 49441-6081.
CHALLENGE MODEL Spartan 120 SERIAL NUMBER
ATTN COMPANY
ADDRESS
CITY STATE/PROVINCE ZIP
PHONE DATE INSTALLED
DEALER NAME & CITY
* WARRANTY INFORMATION *
PLEASE REVIEW THE ENCLOSED WARRANTY INFORMATION SHEET
It is very important that you read and understand the conditions outlined in the Warranty Information
Sheet attached to the outside of the shipping container of your machine.
The Warranty Information Sheet must be filled out completely and returned to THE CHALLENGE
MACHINERY COMPANY in order for the warranty to be issued for this machine.
Challenge® is a registered trademark of
The Challenge Machinery Company•6125 Norton Center Drive•Norton Shores•MI 49441-6081
Copyright© 2000-2006 by The Challenge Machinery Company. All rights reserved. Printed in the USA.
NOTICE: UNSUPPORTED PRODUCT!
NO TECHNICAL SUPPORT AVAILABLE!
NO REPAIR PARTS AVAILABLE!

1.0 Introduction
3
TABLE OF CONTENTS
1.0 Introduction ...................................................................................................................................... 2
2.0 Safety............................................................................................................................................... 5
2.1 Precautions...................................................................................................................................5
2.2 Power Lockout Procedure ............................................................................................................5
3.0 Packing List...................................................................................................................................... 7
4.0 Specifications................................................................................................................................... 8
5.0 Installation Guide ............................................................................................................................. 9
5.1 Inspecting Shipment.....................................................................................................................9
5.2 Unpacking.....................................................................................................................................9
5.3 Moving ..........................................................................................................................................9
5.4 Setup.............................................................................................................................................9
5.5 Cleaning........................................................................................................................................9
6.0 User’s Guide .................................................................................................................................. 10
6.1 Preset the Backgauge ................................................................................................................10
6.2 Set the Cutting Dimension..........................................................................................................10
6.3 Load Paper .................................................................................................................................10
6.4 Make the Cut ..............................................................................................................................10
6.5 Emergency Power Shut-Off Switch ............................................................................................10
6.6 Cut Stick Rotation and Replacement..........................................................................................11
7.0 Appendix A - Maintenance Guide.................................................................................................. 12
7.1 Mechanical System.....................................................................................................................13
7.1.1 Lubrication...........................................................................................................................13
7.1.2 Changing the Knife..............................................................................................................14
7.1.3 Knife Disposal......................................................................................................................15
7.1.4 Hood Switch Adjustment.....................................................................................................15
7.1.5 Hood Plunger Adjustment ...................................................................................................16
7.1.6 Backgauge Preset Position Adjustment..............................................................................16
7.2 Hydraulic System........................................................................................................................16
7.2.1 Hydraulic Fluid Check .........................................................................................................16
7.2.2 Replacing Hydraulic Fluid....................................................................................................17
7.2.3 Hydraulic Fluid Compatibility List ........................................................................................18
7.2.4 Oil Absorber Replacement..................................................................................................18
7.3 Electrical System........................................................................................................................18
7.3.1 Fuse Check and Replacement............................................................................................18
8.0 Appendix B - Parts List................................................................................................................... 20
8.1 Mechanical..................................................................................................................................20
8.1.1 Main Assembly- Arch Cover/Hood......................................................................................20
8.1.2 Main Assembly- Arch Cover/Hood Parts List......................................................................21
8.1.3 Main Assembly- Frame, Front View....................................................................................22
8.1.4 Main Assembly- Frame, Front View Parts List....................................................................23
8.1.5 Main Assembly- Frame, Rear View.....................................................................................24
8.1.6 Main Assembly- Frame, Rear View Parts List.....................................................................25
8.1.7 Main Assembly- Base..........................................................................................................26
8.1.8 Main Assembly- Base Parts List..........................................................................................27
8.1.9 Main Assembly- Lead-screw and Table..............................................................................28
8.1.10 Main Assembly- Lead-screw and Table Parts List............................................................29
NOTICE: UNSUPPORTED PRODUCT!
NO TECHNICAL SUPPORT AVAILABLE!
NO REPAIR PARTS AVAILABLE!

1.0 Introduction
4
8.1.11 Main Assembly- Finish and Parts List...............................................................................30
8.1.12 Main Assembly- Controls..................................................................................................31
8.1.13 50025 Bell-Crank Assembly..............................................................................................32
8.1.14 50025 Bell-Crank Assembly Parts List .............................................................................33
8.2 Electrical.....................................................................................................................................35
8.2.1 E-2896 Basic Machine Schematic......................................................................................35
8.2.2 EE-2895 Rev. B Panel Assembly- Electrical Controls....................................................36
8.2.3 EE 2895 Panel Assembly- Electrical Controls Parts List....................................................37
8.2.4 S-1781-85 Fuse Replacement Label..................................................................................38
8.3 Hydraulic ....................................................................................................................................39
8.3.1 H-549 Hydraulic Schematic ................................................................................................39
8.3.2 H-549 and H-549-1 Hydraulic Power Unit ..........................................................................40
9.0 Appendix C- Troubleshooting.........................................................................................................41
10.0 Appendix D- Safety System Tests................................................................................................42
NOTICE: UNSUPPORTED PRODUCT!
NO TECHNICAL SUPPORT AVAILABLE!
NO REPAIR PARTS AVAILABLE!

2.0 Safety
5
2.0 Safety
2.1 Precautions
•This machine is designed for one-person operation. Never operate the machine with more than
one person.
•Safe use of this machine is the responsibility of the operator. Use good judgment and common
sense when working with and around this machine.
•Read and understand all instructions thoroughly before using the machine. If questions remain,
contact your Authorized Challenge Dealer. Failure to understand the operating instructions may
result in personal injury.
•Only trained and authorized people should operate this machine.
•Do not alter safety guards or devices. They are there for your protection. Severe laceration or
dismemberment may result.
•Disconnect power before cleaning or performing maintenance. See Section 2.2 , Power Lockout
Procedure.
•Observe all caution labels on this machine.
•Be extremely careful when handling knives. Always use the guarded knife lifter provided in the
toolkit. Severe lacerations or dismemberment may result from careless handling procedures.
•Never place your hands under the knife/clamp.
•When replacing hydraulic parts, loosen the connections slowly to relieve pressure. Never loosen
connections while the machine is running. Allow hydraulic fluid to cool before performing
maintenance on the hydraulic system.
•If the machine operates abnormally, consult Appendix C- Troubleshooting.
2.2 Power Lockout Procedure
For maximum safety while making adjustments or repairs to your machine, be sure to disconnect
power to the machine. Disconnect the power plug from its socket.
Figure 1 – Main Power Disconnect
NOTICE: UNSUPPORTED PRODUCT!
NO TECHNICAL SUPPORT AVAILABLE!
NO REPAIR PARTS AVAILABLE!

2.0 Safety
6
Warning Label Definitions
The following warning label is found on the front cover of the machine. Read and understand the
meaning of this symbol. If this label is lost from the machine, it should be replaced. The item number
and location of this label can be found in section 8.1.11 Main Assembly- Finish and Parts List.
SHOCK HAZARD
Disconnect power before removing cover. Replace cover before operation.
NOTICE: UNSUPPORTED PRODUCT!
NO TECHNICAL SUPPORT AVAILABLE!
NO REPAIR PARTS AVAILABLE!

3.0 Packing List
7
3.0 Packing List
Part No. Description Qty.
CMC-120 Basic Machine 1
50042 Jogging Aid 1
50056 Cut Stick 4
50051 Knife Lifter 1
K-50043 Tool Kit 1
Tool Kit Includes:
41121 Felt Washer 4
5064 Cut Stick Hook 1
W-107 7/32 Hex “T” Wrench 1
W-137 5/32 Hex Wrench 1
W-141 1/8 Hex Wrench 1
36134 Pocket Pull Handle 4
E-889-35 1 Amp Slo-Blo Fuse 1
E-889-32 10 Amp Slo-Blo Fuse 1
H-6918-406 1/4-20 X 3/4 socket head cap screw
for use with optional stand P/N 35470 4
NOTICE: UNSUPPORTED PRODUCT!
NO TECHNICAL SUPPORT AVAILABLE!
NO REPAIR PARTS AVAILABLE!

4.0 Specifications
8
4.0 Specifications
Description US Units Metric Units
Cutting Width 12 in. 30.5 cm
Clamp Opening 1.5 in. 3.8 cm
Table Behind Knife 17.25 in. 43.8 cm
Table In Front of Knife 8.5 in. 21.6 cm
Minimum Cut 1.25 in. 3.2 cm
Cutting Force 1767 lbs. 7.86 kN
Clamping Force 785 lbs. 3.5 kN
Overall Height 22.4 in. 56.8 cm
Overall Width 23.5 in. 59.7 cm
Overall Length 34.4 in. 87.4 cm
Net Weight 230 lbs. 104 kg
Shipping Weight 250 lbs. 113 kg
Miscellaneous Specifications
Current 11 Amps
Voltage Requirements 120 VAC / 60Hz
or
220 VAC / 50 Hz
Power Consumption 0.75 HP 0.56 kW
Operating Pressure 1000 PSI 6895 kPa
Oil Capacity 1.5 qt. 1.4 L
NOTICE: UNSUPPORTED PRODUCT!
NO TECHNICAL SUPPORT AVAILABLE!
NO REPAIR PARTS AVAILABLE!

5.0 Installation Guide
9
5.0 Installation Guide
5.1 Inspecting Shipment
Your Spartan cutter has been carefully packed to prevent damage during shipment. However, claims
for damage or loss are the responsibility of the recipient. Inspect all shipments as soon as they are
received. If there is any noticeable damage, note it on the freight bill. Visual and/or hidden damage
must be reported to the claims department of the carrier within 15 days. Contact your dealer if you
need any assistance. Check the contents of the crate against the packing list on page 7. Make sure
there are no missing items.
5.2 Unpacking
Remove the packing materials and braces from the top portion of the skid and discard. Use a safe,
material-handling device, such as a pallet jack, to move the cutter with skid next to the installation
location. Note that the installation location must have a 120 VAC (or 220 VAC) wall outlet nearby.
The machine may be lifted from 4 handle locations around the cutter. These handle locations may be
used with appropriate lifting devices.
5.3 Moving
The machine should only be moved using a stable material-handling device that is low to the ground.
Do not place the machine on a cart. A cart will raise the center of gravity and create a tipping hazard.
If a stand is required, purchase a Challenge stand, P/N 35470. Make sure to install the (4) screws
from the tool kit into the top of the stand to prevent the machine from being pushed off the stand.
5.4 Setup
Once the machine has been placed in its permanent location, simply plug it into a nearby 120 VAC
wall outlet. A knife has been shipped pre-installed. Remove the packing materials. Insert the four
pocket pull handles into the rectangular cutouts in the sides of the cutter. The machine is ready to
use.
If you purchased the optional stand, P/N 35470, assemble the stand and place the machine on top.
Align (4) holes in the top of the stand with (4) holes in the underside of the cutter. The tool kit
contains (4) 1/4-20 x 3/4" cap screws. Run these through the underside of the holes on the stand.
Make sure they enter the clearance holes on the underside of the machine. These screws will
prevent the cutter from being pushed off the stand.
5.5 Cleaning
It may be necessary to clean the cutter after installation. It may be cleaned with a solution of dish
soap and water. Do not use a dripping wet cloth. The cloth should be squeezed out prior to wiping.
Free running liquid may damage the digital display on the right hand side of the table surface. Do not
use petroleum or acid based solvents to clean the machine. Damage may result.
NOTICE: UNSUPPORTED PRODUCT!
NO TECHNICAL SUPPORT AVAILABLE!
NO REPAIR PARTS AVAILABLE!

6.0 User’s Guide
10
6.0 User’s Guide
6.1 Preset the Backgauge
The backgauge must be preset whenever power has been off and should be done occasionally if the
machine is being used frequently. The machine should be preset at least once every eight hours for
average use. A graphical representation of the instructions for presetting is found on the indicator
label on the right-hand side of the front tabletop. The machine will cut more accurately if the
backgauge is preset on a regular basis.
To preset the machine:
•Bring the backgauge to its forward position by turning the hand wheel clockwise until the
backgauge stops.
•If the machine is on, turn off the power and then turn it on again. Only dashes will be
displayed. Press the Preset button on the tabletop until the appropriate units are displayed
(inches or millimeters). During normal operation, this button switches between English and
Metric measurement mode. This can be done at any time. A test cut should measure 1.31
inches (1-5/16") or 3.3 cm.
6.2 Set the Cutting Dimension
Turn the hand wheel until your cutting dimension is displayed on the digital indicator. The indicator
may be switched between inches and millimeters by pressing the button to the left of the indicator.
This is also the preset button. When moving to a longer cut dimension, the backgauge should be
moved past the cut dimension then brought forward to the cut position. Use the thumb wheel lock on
the front face of the machine base to lock the backgauge in position.
6.3 Load Paper
Lift the front hood and jog the stock against the backgauge. Challenge recommends centering the
stock on the backgauge to ensure square cutting. The side-guides may not be precisely square to
the backgauge and knife although the backgauge and knife are parallel. A jogging aid has been
provided in the toolkit. The jogging aid is used to tap the pile flush against the backgauge without
reaching under the knife and clamp.
6.4 Make the Cut
To make the cut, close the front hood then press the two cut buttons simultaneously. The cut buttons
are located on each side of the machine. The hood must be closed in order to cut, and the cut
buttons must be pressed within ½ second of each other. It will take a moment for the machine to
begin its cycle after the cut buttons have been pressed. Hold in the cut buttons until the knife has
made a full stop into the cut stick. Release the cut buttons. The knife and clamp will return to their
original position. If you release the cut buttons before the cut is completed, the knife and clamp will
return to their original position. Open the hood, discard the any trimmings or remove the cut stock. If
the machine will not execute a cut cycle see Section 9.0 Appendix C- Troubleshooting.
6.5 Emergency Power Shut-Off Switch
The front face of the machine has a red mushroom button with a yellow backer. Pressing this button
at any time will cut-off all power to the machine. The knife and clamp will stop. If the machine will
not cycle, first check to make sure the emergency power shut-off switch is on.
NOTICE: UNSUPPORTED PRODUCT!
NO TECHNICAL SUPPORT AVAILABLE!
NO REPAIR PARTS AVAILABLE!

6.0 User’s Guide
11
6.6 Cut Stick Rotation and Replacement
Through time the cut stick will become worn, affecting the quality of cut on the lower sheets of a pile.
Rotating or replacing the cut stick will provide a fresh surface for cutting.
Disconnect main power.
See Section 2.2 Power Lockout Procedure.
1. Use the cut stick hook from the toolkit to remove either end of the cut stick.
2. Once an end of the stick has been freed from the slot, pull the remaining portion out of the
slot by hand.
3. Rotate or flip the stick until a new surface is oriented such that it would lie under the knife
when reinserted into the slot.
4. If all surfaces (2 on each side, 4 total) have been used, replace it with a new cut stick.
5. Insert the cut stick
•Place one end into the end of the slot.
•Press down on the stick with one hand while wiggling the stick back and forth with the
other. This is necessary because the stick has a wavy shape and will not simply fall
into the slot.
Figure 2- Removing the Cut Stick
NOTICE: UNSUPPORTED PRODUCT!
NO TECHNICAL SUPPORT AVAILABLE!
NO REPAIR PARTS AVAILABLE!

7.0 Appendix A - Maintenance Guide
12
7.0 Appendix A - Maintenance Guide
NOTICE
The instructions on the following
pages are for the use of trained
service personnel only!
Attempting to perform repair and
replacement procedures without
proper training may cause
machine damage or operator
injury!
PARTS CUSTOMERS: The Challenge Machinery Company provides parts with the express
understanding that they are to replace parts found missing or no longer serviceable on
equipment designed and/or manufactured at Challenge. The Challenge Machinery
Company assumes no liability for any modification or alteration to any Challenge products,
and any such modification or alteration to any Challenge product is not authorized by The
Challenge Machinery Company. Any modification or alteration of any Challenge product
will void any remaining warranty.
NOTICE: UNSUPPORTED PRODUCT!
NO TECHNICAL SUPPORT AVAILABLE!
NO REPAIR PARTS AVAILABLE!

7.0 Appendix A - Maintenance Guide
13
7.1 Mechanical System
The machine should be lubricated every 6 months, and the knife should be changed when cut quality
becomes unacceptable.
7.1.1 Lubrication
Grease
Disconnect main power.
See Section 2.2 Power Lockout Procedure.
1. Remove the top cover by removing the four screws that mount it to the machine base.
Two are located in the rear, and two are located in the front. The hood must be in the up
position in order to remove the two front screws.
2. After removing the mounting screws, lift the top cover straight up until it clears the frame
plate inside. Set aside the top cover and mounting screws.
3. Brush high-pressure grease onto the exposed knife bar and knife bar bearing surfaces.
4. Brush high-pressure grease onto the exposed surfaces of the guide blocks on each end
of the clamp as shown in Figure 3.
5. Apply light machine oil to the clamp cylinder mounting pin and pull down bar mounting
screws on the clamp as shown in Figure 3.
Figure 3- Rear Gib Lubrication
6. Apply light machine oil to all four knife link pins as shown in Figure 4- Front Gib
Lubrication on page 14.
7. Remove left rear panel.
Oil
NOTICE: UNSUPPORTED PRODUCT!
NO TECHNICAL SUPPORT AVAILABLE!
NO REPAIR PARTS AVAILABLE!

7.0 Appendix A - Maintenance Guide
14
8. Apply light machine oil to all six bell-crank pins under the table as shown in Figure 4-
Front Gib Lubrication and Figure 5- Bell-Crank Lubrication.
9. Brush high-pressure grease along the backgauge guide shaft and lead-screw as in
Figure 5- Bell-Crank Lubrication
10. Brush high-pressure grease into the hole in which the lead-screw enters the rear pillow
block as shown in Figure 6.
Figure 6- Grease Rear Pillow Block
11. Replace the left panel and top cover.
7.1.2 Changing the Knife
As the knife wears, the quality of cut decreases. The knife cannot be reground. It must be replaced
with a new one.
Disconnect main power.
See Section 2.2 Power Lockout Procedure
Even worn knives are very sharp! Never touch an exposed blade.
Knife changing is a one person operation. Failure to follow
instructions could result in severe lacerations or dismemberment.
Knife Removal:
1. Lift the hood and remove the two knife bolts in the center of the knife (the bolts in the
slotted portion of the knife bar). A hex wrench is provided in the toolkit.
Figure 4- Front Gib Lubrication Figure 5- Bell-Crank Lubrication
NOTICE: UNSUPPORTED PRODUCT!
NO TECHNICAL SUPPORT AVAILABLE!
NO REPAIR PARTS AVAILABLE!

7.0 Appendix A - Maintenance Guide
15
2. Fasten the knife lifter to the knife. The knife lifter should be angled into the machine, right
end first. It can then be slid up into place. Thread the handles into the knife and firmly
tighten them by hand.
3. Place a 12” or longer piece of chipboard directly underneath the knife.
4. Place an empty scabbard on the tabletop.
5. Remove the two remaining screws from the knife.
6. While holding the knife lifter up, loosen the the knife lifter handles from the knife just
enough to release the knife from the knife bar.
7. Lower the knife to clear the knife bar. Move it to the far right and pull the left-end of the
knife out of the machine.
8. Carefully place the knife and lifter onto the scabbard.
9. Remove the lifter from the knife.
10. Place both thumbs on the bottom protected portion of the scabbard and use all fingers on
the top portion of the knife to position it over the screw holes in the scabbard.
11. Thread the scabbard screws into the scabbard to secure the knife.
Disconnect main power.
See Section 2.2 Power Lockout Procedure.
Even worn knives are very sharp! Never touch an exposed blade.
Knife changing is a one person operation. Failure to follow
instructions could result in severe lacerations or dismemberment.
Knife Installation:
1. Place a 12” or longer piece of chipboard directly underneath the knife.
2. Lift the hood and place the new knife and scabbard on the tabletop. The top of the knife
should face the knife bar.
3. Remove the scabbard screws.
4. Place all fingers on the top edge of the scabbard and thumbs in the tapped holes in the
knife.
5. Slide the knife up the scabbard far enough to expose the sharp edge.
6. Thread the handles of the knife lifter all the way into the knife, then back them out ½ turn.
7. Angle the knife and lifter into the machine right-end first.
8. Raise the handles into the slots of the knife bar.
9. Firmly hand-tighten the handles of the knife lifter locking the knife in place. Make sure
the knife is all the way up in the slots on both ends.
10. Insert and tighten the two outside knife screws.
11. Loosen the knife lifter handles and remove the knife lifter from the machine.
12. Insert the scabbard screws into the scabbard and store the scabbard and lifter for later
use.
7.1.3 Knife Disposal
The used knife must be mounted to the scabbard. It should be properly discarded. Check with the
appropriate authorities (local code or waste-management company) for proper disposal. You may
also check with your regrind shop or Authorized Challenge Dealer for disposal options.
7.1.4 Hood Switch Adjustment
The hood switch mechanism was designed to disable the machine from operation if the hood is
rotated beyond 2o. The machine should not be operated if the hood switch is improperly adjusted.
To adjust the hood switch:
Disconnect main power.
See Section 2.2 Power Lockout Procedure.
NOTICE: UNSUPPORTED PRODUCT!
NO TECHNICAL SUPPORT AVAILABLE!
NO REPAIR PARTS AVAILABLE!

7.0 Appendix A - Maintenance Guide
16
1. Remove the right arch side panel.
2. Lift hood and place 5/8” (15.9 mm) thick material on the front edge of the table.
3. Loosen hood switch mounting screws.
4. Adjust the hood switch plunger to touch the steel actuator flap.
5. Tighten hood switch mounting screws.
6. Replace arch side panel.
7. Test according to instructions in Appendix D- Safety System Tests.
8. Fine-tune the actuator switch as required.
Figure 7- Hood Switch Adjustment
7.1.5 Hood Plunger Adjustment
1. Locate the spring plunger in the left hood pivot block.
2. Use a hex wrench to adjust the plunger until the hood remains in the up position.
Do not over-tighten the plunger. Over-tightening the plunger will cause undue wear.
7.1.6 Backgauge Preset Position Adjustment
Use the following instructions to set the forward backgauge limit to the preset position, 1.31” (3.3 cm):
1. Remove the rear Lexan™ cover.
2. Loosen the jam nut on the preset adjustment setscrew.
3. Adjust the setscrew until the test cuts result in a cut of 1.31” (3.3 cm).
4. Re-tighten jam nut.
5. Replace rear Lexan™ cover.
7.2 Hydraulic System
7.2.1 Hydraulic Fluid Check
The hydraulic fluid should be checked every six months and topped off as necessary. Depending on
usage, it may need to be checked more frequently.
To check the hydraulic fluid level:
Disconnect main power.
See Section 2.2 Power Lockout Procedure.
NOTICE: UNSUPPORTED PRODUCT!
NO TECHNICAL SUPPORT AVAILABLE!
NO REPAIR PARTS AVAILABLE!

7.0 Appendix A - Maintenance Guide
17
1. Remove the right side panel using a hex wrench provided in the toolkit.
2. View the hydraulic reservoir through the open panel. The fluid level should be 75-90%
full as shown in Figure 8- Recommended Hydraulic Fluid Level.
Figure 8- Recommended Hydraulic Fluid Level
3. As necessary, add fluid to the reservoir as described in the following steps.
4. Remove the rear panel and unscrew the filler cap.
5. Using a long funnel, add fluid until the recommended level is reached. Only use 100-
weight hydraulic fluid. This can be ordered from Challenge in five-gallon containers, part
number S-1991-3. See Section 7.2.3 for a compatibility list. DO NOT OVERFILL!
6. Screw the filler cap back into the reservoir and replace all covers.
7.2.2 Replacing Hydraulic Fluid
The hydraulic fluid should be replaced annually.
Do not replace the hydraulic fluid while it is hot. Severe burns may
result.
Use the following procedure to replace the hydraulic fluid:
Disconnect the main power.
See Section 2.2 Power Lockout Procedure.
1. Remove the rear panel.
2. Remove the filler cap from the reservoir.
3. Use a transfer pump or syphoning tool to remove the used fluid from the reservoir.
These can be found at most hardware stores.
Refill tank to the level illustrated in
4. Figure 8- Recommended Hydraulic Fluid Level.
5. Replace the rear panel.
NOTICE: UNSUPPORTED PRODUCT!
NO TECHNICAL SUPPORT AVAILABLE!
NO REPAIR PARTS AVAILABLE!

7.0 Appendix A - Maintenance Guide
18
7.2.3 Hydraulic Fluid Compatibility List
Any of the following hydraulic fluids may be used.
Product Name Distributor
Rykon No. 100 AMOCO
Energol HLP 100 BP
AW 100 Chevron
Pacemaker XD 100 Citgo
Super Hydraulic 100 Conoco
Univis N100 Exxon
Security AW 100 Gulf
Knoil R&O AW 100 Kendall
Tellus 100 Shell
7.2.4 Oil Absorber Replacement
Each hydraulic cylinder has two felt washers P/N 41121 to absorb normal rod seal leakage from the
hydraulic cylinders. The felt washers should be replaced when they become saturated with oil. If the
felt is saturated, drips of oil will be seen at the center of the knife bar or clamp.
Use the following procedure to replace the felt, oil absorbers:
Disconnect the main power.
See Section 2.2 Power Lockout Procedure.
1. Remove the top cover by removing the four screws that secure it to the base.
2. Lift the top cover straight up until it clears the main frame plate.
3. Remove the saturated absorbers from around the knife and clamp cylinder rods.
4. If the replacement washers do not have a cut in them, then cut through one side of each
allowing them to be opened and fit onto the cylinder rod.
5. Wipe any obvious leakage from the cylinder and knife bar.
6. Place two new oil absorbers on each cylinder rod.
7. Replace the top cover.
7.3 Electrical System
7.3.1 Fuse Check and Replacement
If the machine is plugged in and either the digital display does not light or the hydraulics will not turn
on, a fuse may be blown. The fuse labeled F1 (10 Amp) is used in the hydraulic circuit, and the fuse
labeled F2 (1 Amp) is used in the LED display circuit.
To check and replace fuses:
Disconnect the main power.
See Section 2.2 Power Lockout Procedure.
1. Remove the front panel.
2. A label on the inside of the front panel includes a diagram showing the location of each
fuse on the power panel.
3. Locate each fuse F1 and F2.
4. Pull each fuse holder up and remove the fuse by pushing it with the tip of a screwdriver.
5. Inspect the fuses for damage.
6. Replace damaged fuses. One set of fuses is provided with the toolkit.
7. Push fuse holders back into the power panel.
8. Replace the front panel.
NOTICE: UNSUPPORTED PRODUCT!
NO TECHNICAL SUPPORT AVAILABLE!
NO REPAIR PARTS AVAILABLE!

7.0 Appendix A - Maintenance Guide
19
NOTICE: UNSUPPORTED PRODUCT!
NO TECHNICAL SUPPORT AVAILABLE!
NO REPAIR PARTS AVAILABLE!
This manual suits for next models
1
Table of contents
Other Challenge Cutter manuals
Popular Cutter manuals by other brands
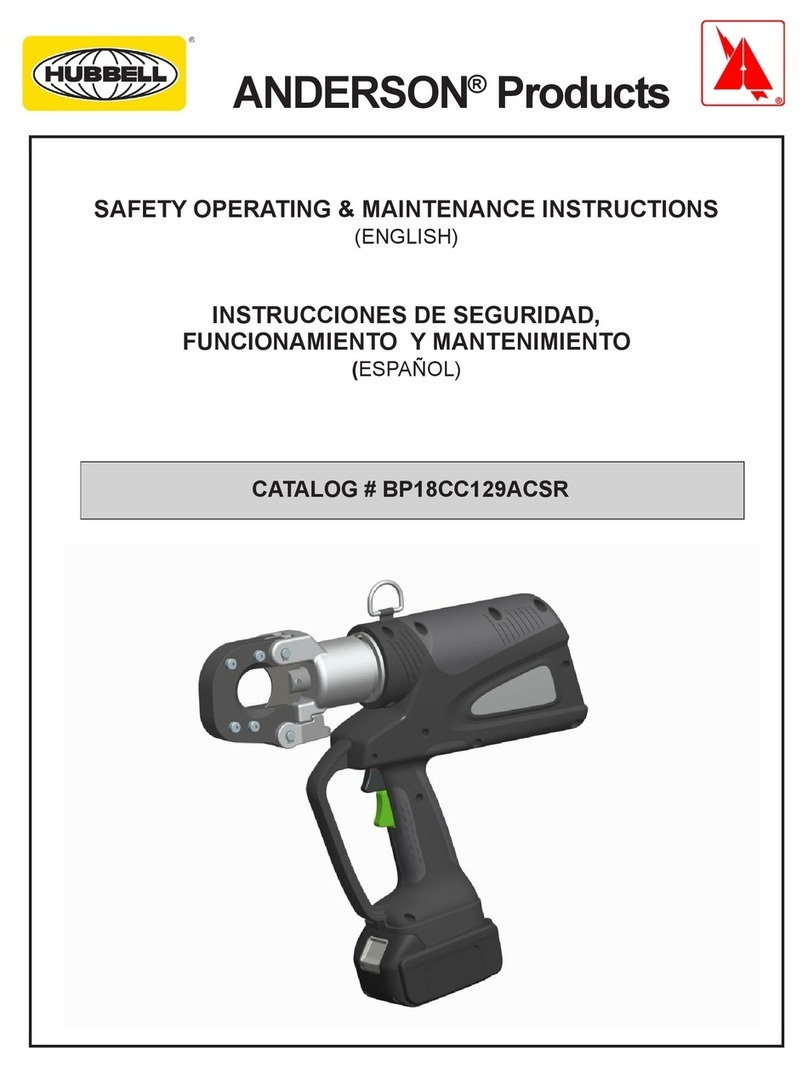
Hubbell
Hubbell ANDERSON BP18CC129ACSR SAFETY OPERATING & MAINTENANCE INSTRUCTIONS

Maruyama
Maruyama QC-E owner's manual
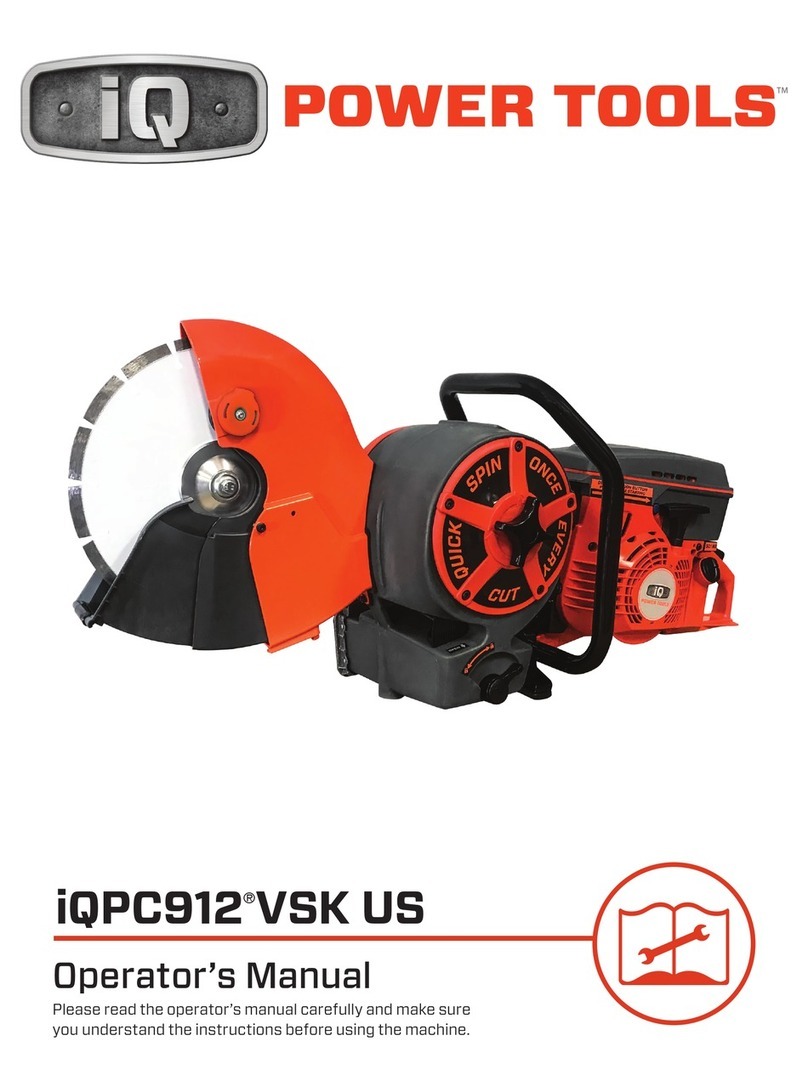
IQ Power Tools
IQ Power Tools iQPC912VSK Operator's manual
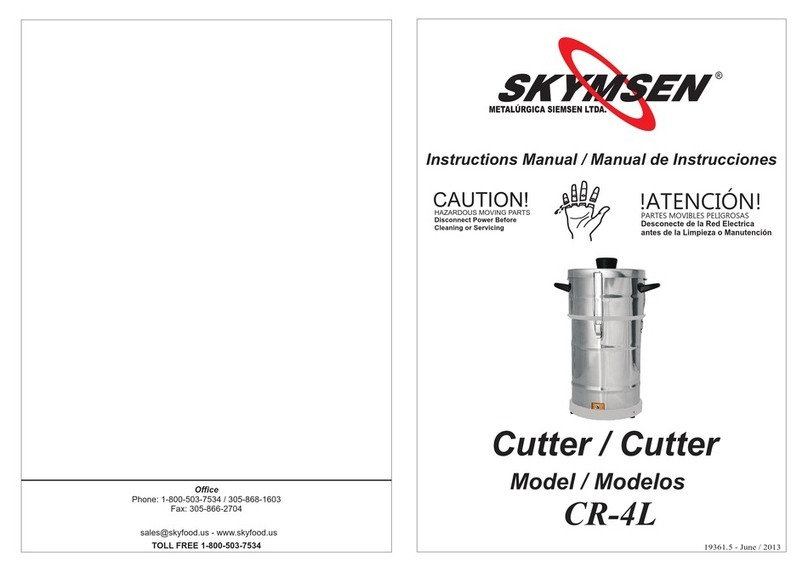
Skymsen
Skymsen CR-4L instruction manual
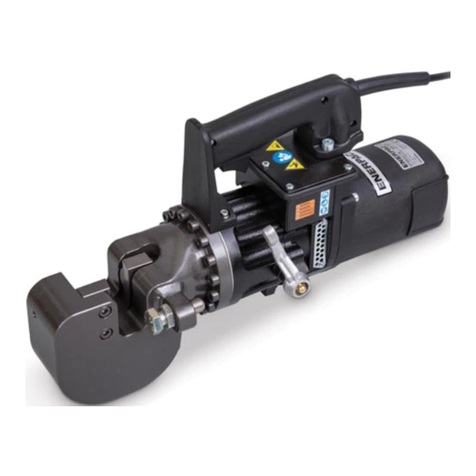
Enerpac
Enerpac EFBE5017 instruction sheet
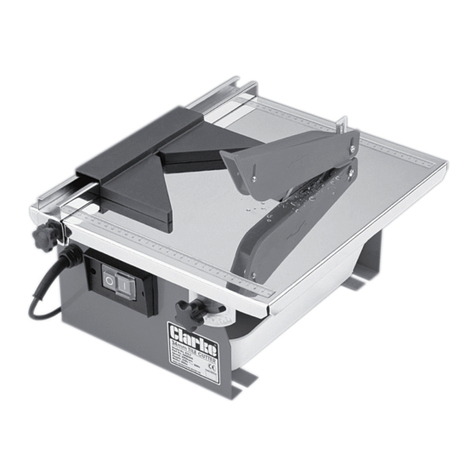
Clarke
Clarke ETC7 Operating & maintenance instructions