Check-line TI-25P User manual

– 1 –– 20 –
TABLE OF CONTENTS
01.0 Introduction . . . . . . . . . . . . . . . . . . . . . . . . . . . . . . . . . . . . . . . . . . . . . . . 02
02.0 Overview . . . . . . . . . . . . . . . . . . . . . . . . . . . . . . . . . . . . . . . . . . . . . . . . . 03
2.1 Gauge
2.2 Complete Kit
03.0 Operating Elements . . . . . . . . . . . . . . . . . . . . . . . . . . . . . . . . . . . . . . . . . 04
3.1 The Keypad
3.2 The Display
3.3 The Transducer
04.0 Condition and Preparation of Measuring Surface . . . . . . . . . . . . . . . . . . 07
05.0 Zeroing The Probe . . . . . . . . . . . . . . . . . . . . . . . . . . . . . . . . . . . . . . . . . . 08
0 6.0 Calibration Procedure. . . . . . . . . . . . . . . . . . . . . . . . . . . . . . . . . . . . . . . . 09
6.1 Programming The Sound Velocity
07.0 Transducer Selection . . . . . . . . . . . . . . . . . . . . . . . . . . . . . . . . . . . . . . . . 10
008.0 Taking Measurements . . . . . . . . . . . . . . . . . . . . . . . . . . . . . . . . . . . . . . . 12
09.0 Specifications . . . . . . . . . . . . . . . . . . . . . . . . . . . . . . . . . . . . . . . . . . . . . . 13
10.0 Appendix A, Applications Notes . . . . . . . . . . . . . . . . . . . . . . . . . . . . . . . 14
11.0 Appendix B, Sound Velocity Of Common Materials . . . . . . . . . . . . . . . 16
12.0 Material Safety Information. . . . . . . . . . . . . . . . . . . . . . . . . . . . . . . . . . . 17
13.0 Warranty . . . . . . . . . . . . . . . . . . . . . . . . . . . . . . . . . . . . . . . . . . . . . . . . . . 18
IMPORTANT NOTE:
Inherent in ultrasonic thickness measurement is the possibility that the
instrument will use the second rather than the first echo from the back
surface of the material being measured. This may result in a thickness
reading that is TWICE what it should be. Responsibility for proper use of
the instrument and recognition of this phenomenon rests solely with the
user of the instrument.
NOTES

– 2 –
1.0 INTRODUCTION
The TI-25P is a precision Ultrasonic Micrometer. Based on the same operating
principles as SONAR, the TI-25P is capable of measuring the thickness of
various materials with accuracy as high as ± 0.001 inches, or ± 0.01 millimeters.
The principle advantage of ultrasonic measurement over traditional methods is
that ultrasonic measurements can be performed with access to only one side of
the material being measured.
– 19 –
NOTES

– 3 –
2.0 OVERVIEW
2.1 Gauge
– 18 –
13.0 WARRANTY
ELECTROMATIC Equipment Co., Inc. (ELECTROMATIC) warrants to the
original purchaser that this product is of merchantable quality and confirms
in kind and quality with the descriptions and specifications thereof. Product
failure or malfunction arising out of any defect in workmanship or material in the
product existing at the time of delivery thereof which manifests itself within one
year from the sale of such product, shall be remedied by repair or replacement of
such product, at ELECTROMATIC’s option, except where unauthorized repair,
disassembly, tampering, abuse or misapplication has taken place, as determined
by ELECTROMATIC. All returns for warranty or non-warranty repairs and/or
replacement must be authorized by ELECTROMATIC, in advance, with all
repacking and shipping expenses to the address below to be borne by the
purchaser.
THE FOREGOING WARRANTY IS IN LIEU OF ALL OTHER
WARRANTIES, EXPRESSED OR IMPLIED, INCLUDING BUT NOT
LIMITED TO, THE WARRANTY OF MERCHANTABILITY AND FITNESS
FOR ANY PARTICULAR PURPOSE OR APPLICATION. ELECTROMATIC
SHALL NOT BE RESPONSIBLE NOR LIABLE FOR ANY CONSEQUEN-
TIAL DAMAGE, OF ANY KIND OR NATURE, RESULTING FROM THE
USE OF SUPPLIED EQUIPMENT, WHETHER SUCH DAMAGE OCCURS
OR IS DISCOVERED BEFORE, UPON OR AFTER REPLACEMENT OR
REPAIR, AND WHETHER OR NOT SUCH DAMAGE IS CAUSED BY
MANUFACTURER’S OR SUPPLIER’S NEGLIGENCE WITHIN ONE YEAR
FROM INVOICE DATE.
Some State jurisdictions or States do not allow the exclusion or limitation of
incidental or consequential damages, so the above limitation may not apply to
you. The duration of any implied warranty, including, without limitation, fitness
for any particular purpose and merchantability with respect to this product, is
limited to the duration of the foregoing warranty. Some states do not allow
limitations on how long an implied warranty lasts but, not withstanding, this
warranty, in the absence of such limitations, shall extend for one year from the
date of invoice.
ELECTROMACTIC Equipment Co., Inc.
600 Oakland Ave. Cedarhurst, NY 11516—USA
Tel: 1-800-645-4330/ Tel: 516-295-4300/ Fax: 516-295-4399
Every precaution has been taken in the preparation of this manual. Electromatic Equipment Co., Inc.,
assumes no responsibility for errors or omissions. Neither is any liability assumed for damages resulting
from the use of information contained herein. Any brand or product names mentioned herein are used for
identification purposes only, and are trademarks or registered trademarks of their respective holders.
2.2 Complete Kit
Probe
Receptacles
Probe Zero Test Plate and
Battery Compartment Cover
Backlit LCD
Display
Membrane
Keypad
Probe
a
d
c
e
g
The TI-25P is supplied as a
complete kit with the following:
a. Gauge
b. Two (2) AA batteries
(installed in gauge)
c. Probe/cable assembly
d. 4 oz. Bottle of coupling fluid
e. NIST-traceable calibration
certificate
f. Operating instruction manual
g. Foam-filled carrying case

– 4 –
3.0 OPERATING ELEMENTS
The TI-25P interacts with the operator through the membrane keypad and the
LCD display. The functions of the various keys on the keypad are detailed below,
followed by an explanation of the display and its various symbols.
3.1 The Keypad
This ON/OFF key is used to turn the TI-25P on and off. When the
gauge is turned ON, it will first perform a brief display test by illumi-
nating all of the segments in the display. After one second, the gauge
will display the internal software version number. After displaying the
version number, the display will show "0.000" (or "0.00" if using metric
units), indicating the gauge is ready for use.
The TI-25P is turned OFF by pressing the ON/OFF key. The gauge has
a special memory that retains all of its settings even when the power is
off. The gauge also features an auto-powerdown mode designed to con-
serve battery life. If the gauge is idle for 5 minutes, it will turn itself
off.
The PRB-0 key is used to “zero” the TI-25P in much the same way that
a mechanical micrometer is zeroed. If the gauge is not zeroed correctly,
all of the measurements that the gauge makes may be in error by some
fixed value. Refer to page 8 for an explanation of this important proce-
dure.
The IN/MM key is used to switch back and forth between English and
Metric units. This key may be used at any time, whether the gauge is
displaying a thickness (IN or MM) or a velocity value (IN/µs or M/s)
The BACKLIGHT key switches the display backlight between three
available settings. OFF will be displayed when the backlight is switched
off. AUTO will be displayed when the backlight is set to automatic
mode, and ON will be displayed when the backlight is set to stay on. In
the AUTO setting, the backlight will illuminate when the TI-25P is
actually making a measurement.
ON
OFF
IN
MM
PRB
0
– 17 –
Section 1— Product Identification
Product Name: TI-25M Generic Name: Ultrasonic Couplant
Manufacturer: Electromatic Equpt. Co. NFPA Hazardous Materials Identification System (est)
Health 0 Flammability 0 Reactivity 0
Section 2— Hazardous Ingredients
This material does not contain any ingredients having known health hazards in concentrations
greater than 1%. This material does not contain any known or suspected carcinogens.
Section 3 — Physical Data (nominal)
Boiling Point: >220°F Freezing Point: <20°F
Vapor Pressure: N/A Evaporation Rate: N/A
Specific Gravity: >1.0Z Solubility in Water: complete
pH: 7.35 – 7.9 Acoustic Imp.: 1.726x106
Vapor Density: N/A Appearance and Odor: water white, opaque gel; bland odor
Section 4 — Fire and Explosive Hazard Data
Flash Point: none Upper Exposure Limit: none Lower Exposure Limit: none
Special Fire Fighting Procedures: N/A Extinguishing media: N/A
Unusual Fire and Explosion Hazards: none
Section 5 — Reactive Data
Stability: Stable Conditions to Avoid: none
Incompatibility (Materials to Avoid): none known
Hazardous Polymerization: will not occur
Hazardous Decomposition or Byproducts: none known
Section 6 —- Health Hazard and First Aid Data
Routes of Entry1:
Skin: not likely Ingestion: not normally Eyes: not normally Inhalation: no
Effects of Overexposure:
Acute: May cause temporary eye irritation Chronic: none expected
First Aid Procedures:
Skin: Remove with water if desired. Eyes: Flush with water for 15 minutes.
Ingestion: For large quantities, induce vomiting and call a physician Inhalation: N/A
Section 7 - Storage and Handling Information
Precautions to be taken in handling and storage: Store between 20 °F and 120 °F. Spills are
slippery and should be cleaned up immediately. Steps to be taken in case material is released or
spilled: Pick up excess for disposal. Clean with water. Waste disposal method: Dispose of in
accordance with federal, state, and local regulations.
Section 8 — Control Measures
Respiratory Protection: not required Ventilation: not required
Protective Gloves: on individuals demonstrating sensitivity to TI-25M
Eye Protection: as required by working conditions Other Protective Equipment: not required
1. TI-25M contains only food grade and cosmetic grade ingredients.
12.0 MATERIAL SAFETY DATA SHEET (MSDA)

– 5 –
3.2 The Display
Numerals: The numeric portion of the
display consists of 4 complete digits
preceded by a leading "1", and is used
to display numeric values, as well as
occasional simple words, to indicate
the status of various settings. When
the TI-25P is displaying thickness
measurements, the display will hold the
last value measured, until a new meas-
urement is made. Additionally, when
the battery voltage is low, the entire
display will begin to flash. When this
occurs, the batteries should be replaced.
Stability Indicator: These 8 vertical
bars form the Stability Indicator. When
the TI-25P is idle, only the left-most bar
and the underline will be on. When the
gauge is making a measurement, six or
seven of the bars should be on. If fewer
than five bars are on, the TI-25P is
having difficulty achieving a stable
measurement, and the thickness value
displayed will most likely be erroneous.
IN Symbol: When the IN symbol is
on, the TI-25P is displaying a thickness
value in inches. The maximum
thickness that can be displayed is
19.999 inches.
MM Symbol: When the MM symbol is
on, the TI-25P is displaying a thickness
value in millimeters. If the displayed
thickness exceeds 199.99 millimeters,
the decimal point will shift automatical-
ly to the right, allowing values up to
1999.9 millimeters to be displayed.
IN/µs Symbol: When the IN symbol
is on, in conjunction with the /µs
symbol, the TI-25P is displaying a
sound-velocity value in inches-per-
microsecond.
1.8.8.8.8
+INMM/μs
1.8.8.8.8
+INMM/μs
1.8.8.8.8
+INMM/μs
1.8.8.8.8
+INMM/μs
1.8.8.8.8
+INMM/μs
– 16 –
11.0 APPENDIX B: SOUND VELOCITIES OF COMMON MATERIALS
Aluminum 0.2500 6350
Bismuth 0.8600 2184
Brass 0.1730 4394
Cadmium 0.1090 2769
Cast Iron 0.18000 4572
Constantan 0.2060 5232
Copper 0.1840 4674
Epoxy resin 0.1000 2540
German silver 0.1870 4750
Glass, crown 0.2230 5664
Glass, flint 0.1680 4267
Gold 0.1280 3251
Ice 0.1570 3988
Iron 0.2320 5898
Lead 0.8500 2159
Magnesium 0.2280 5791
Nickel 0.2220 5639
Nylon 0.1020 2591
Paraffin 0.0870 2210
Platinum 0.1560 3962
Plexiglass 0.1060 2692
Polystyrene 0.0920 2337
Porcelain 0.2300 5842
PVC 0.0940 2388
Quartz glass 0.2220 5639
Rubber, vulcanized 0.0910 2311
Silver 0.1420 3607
Steel, common 0.2330 5920
Steel, stainless 0.2230 5664
Stellite 0.2750 6985
Tin 0.1310 3327
Titanium 0.2400 6096
Tungsten 0.2100 5334
Zinc 0.1660 4216
Water 0.058 1473
Material Velocity Velocity
Type Inches/µs Meters/s
Notes: 1. These values are to be used only when a suitable sample of known
thickness is not available for calibrating, as slight variations in material
composition, finishing (hardening, polishing, etc.) or shape can affect the
acoustic velocity. ...
Notes: 2. “✔”denotes the factory default setting for acoustic velocity.
✔

– 6 –
M Symbol: When the M symbol is on,
in conjunction with the /s symbol, the
TI-25P is displaying a sound-velocity
value in meters-per-second.
3.3 The Transducer
The transducer is the “business end”of the TI-25P. It transmits and receives
the ultrasonic sound waves which the TI-25P uses to calculate the thickness
of the material being measured. The transducer connects to the TI-25P via
the attached cable and two coaxial connectors. When using the transducer,
the orientation of the dual coaxial connectors is not critical: either plug may
be fitted to either socket in the TI-25P.
The transducer must be used correctly in order for the TI-25P to produce
accurate, reliable measurements. Below is a short description of the trans-
ducer, followed by instructions for its use.
This is a bottom view of a typical transducer.
The two semicircles of the wearface are
visible, as is the barrier separating them.
One of the semicircles is responsible for
conducting ultrasonic sound into the material
being measured, and the other semicircle is
responsible for conducting the echoed sound
back into the transducer. When the transducer
is placed against the material being measured,
it is the area directly beneath the center of the
wearface that is being measured.
This is a top view of a typical transducer.
Press against the top with the thumb or index
finger to hold the transducer in place.
Moderate pressure is sufficient, as it is only
necessary to keep the transducer stationary,
and the wearface seated flat against the
surface of the material being measured.
1.8.8.8.8
+INMM/μs
– 15 –
An additional important consideration when measuring laminates is that
any included air gaps or pockets will cause an early reflection of the ultra-
sound beam. This effect will be noticed as a sudden decrease in thickness in
an otherwise regular surface. While this may impede accurate measurement
of total material thickness, it does provide the user with positive indication
of air gaps in the laminate.

– 7 –
4.0 CONDITION AND PREPARATION OF MEASURING SURFACE
In any ultrasonic measurement scenario, the shape and roughness of the test
surface are of paramount importance. Rough, uneven surfaces may limit the
penetration of ultrasound through the material, and result in unstable, and
therefore unreliable, measurements. The surface being measured should be clean,
and free of any small particulate matter, rust, or scale. The presence of such
obstructions will prevent the transducer from seating properly against the surface.
Often, a wire brush or scraper will be helpful in cleaning surfaces. In more
extreme cases, rotary sanders or grinding wheels may be used, though care
must be taken to prevent surface gouging, which will inhibit proper transducer
coupling.
Extremely rough surfaces, such as the pebble-like finish of some cast irons,
will prove most difficult to measure. These kinds of surfaces act on the sound
beam like frosted glass on light, the beam becomes diffused and scattered in all
directions.
In addition to posing obstacles to measurement, rough surfaces contribute to
excessive wear of the transducer, particularly in situations where the transducer is
“scrubbed” along the surface. Transducers should be inspected on a regular basis,
for signs of uneven wear of the wearface. If the wearface is worn on one side
more than another, the sound beam penetrating the test material may no longer be
perpendicular to the material surface. In this case, it will be difficult to exactly
locate tiny irregularities in the material being measured, as the focus of the
soundbeam no longer lies directly beneath the transducer.
– 14 –
10.0 APPENDIX A: APPLICATION NOTES
Measuring pipe and tubing
When measuring a piece of pipe to determine
the thickness of the pipe wall, orientation of
the transducers is important. If the diameter
of the pipe is larger than approximately four
inches, measurements should be made with the transducer oriented so that
the gap in the wearface is perpendicular (at right angle) to the long axis
of the pipe. For smaller pipe diameters, two measurements should be
performed, one with the wearface gap perpendicular, another with the gap
parallel to the long axis of the pipe. The smaller of the two displayed values
should then be taken as the thickness at that point.
Measuring hot surfaces
The velocity of sound through a substance is dependent upon its
temperature. As materials heat up, the velocity of sound through them
decreases. In most applications with surface temperatures less than about
200°F (100°C), no special procedures must be observed. At temperatures
above this point, the change in sound velocity of the material being
measured starts to have a noticeable effect upon ultrasonic measurement.
At such elevated temperatures, it is recommended that the user perform a
calibration procedure (refer to page 9) on a sample piece of known
thickness, which is at or near the temperature of the material to be
measured. This will allow the TI-25P to correctly calculate the velocity of
sound through the hot material.
When performing measurements on hot surfaces, it may also be necessary
to use a specially constructed high-temperature transducer. These transduc-
ers are built using materials which can withstand high temperatures. Even
so, it is recommended that the probe be left in contact with the surface for
as short a time as needed to acquire a stable measurement. While the
transducer is in contact with a hot surface, it will begin to heat up itself,
and through thermal expansion and other effects, may begin to adversely
affect the accuracy of measurements.
Measuring laminated materials
Laminated materials are unique in that their density (and therefore sound-
velocity) may vary considerably from one piece to another. Some laminated
materials may even exhibit noticeable changes in sound-velocity across a
single surface. The only way to reliably measure such materials is by
performing a calibration procedure on a sample piece of known thickness.
Ideally, this sample material should be a part of the same piece being
measured, or at least from the same lamination batch. By calibrating to
each test piece individually, the effects of variation of sound-velocity
will be minimized.
Perpendicular Parallel

– 8 –
5.0 ZEROING THE PROBE
Setting the Zero Point of the TI-25P is important for the same reason that setting
the zero on a mechanical micrometer is important. If the gauge is not "zeroed"
correctly, all of the measurements the gauge makes will be in error by some fixed
number. When the TI-25P is "zeroed", this fixed error value is measured and
automatically corrected for in all subsequent measurements. The TI-25P may be
"zeroed" by performing the following procedure:
1. Make sure the TI-25P is on.
2. Plug the transducer into the TI-25P. Make sure that the connectors are fully
engaged. Check that the wearface of the transducer is clean and free of any
debris.
3. On the top of the TI-25P, above the display, is the metal probe-disc. Apply a
single droplet of ultrasonic couplant to the face of this disc.
4. Press the transducer against the probe-disc, making sure that the transducer
sits flat against the surface of the probe-disc. The display should show some
thickness value, and the Stability Indicator should have nearly all its bars
illuminated.
5. While the transducer is firmly coupled to the probe-disc, press the PRB-0 key
on the keypad. The TI-25P will display "Prb0" while it is calculating its zero
point.
6. Remove the transducer from the probe-disc.
At this point, the TI-25P has successfully calculated it's internal error factor,
and will compensate for this value in any subsequent measurements. When
performing a "probe-zero", the TI-25P will always use the sound-velocity value
of the built-in probe-disc, even if some other velocity value has been entered for
making actual measurements. Though the TI-25P will remember the last "probe-
zero" performed, it is generally a good idea to perform a "probe-zero" whenever
the gauge is turned on, as well as any time a different transducer is used. This
will ensure that the instrument is always correctly zeroed.
– 13 –
9.0 SPECIFICATIONS
Measuring Range 0.025 to 19.999 inches (0.63 to 500 millimeters)
Resolution: 0.001 inch (0.01 millimeter)
Accuracy ±0.001 inch (0.01 millimeter), depends on
material and conditions
Sound Velocity
Range 0.0492 to 0.3930 in/µs (1250 to 10000µ/s)
Keypad Sealed membrane, resistant to water and
petroleum products.
Display Liquid-Crystal-Display, 4.5 digits,
0.500 inch high numerals. LED
Power Source Two AA size, 1.5 volt alkaline
or 1.2 volt NiCad cells.
Battery Life 200 hours typical operating time using alkaline,
120 hours typical operating time using NiCad.
Weight 10 ounces
Size 2.5W x 4.75H x 1.25D inches
(63.5W x 120.7H x 31.8D mm).
Operating
Temperature –20 to 120 °F (–20 to 50 °C)
Case Extruded aluminum body
nickel plated aluminum end caps.

– 9 –
6.0 CALIBRATION PROCEDURE
In order for the TI-25P to make accurate measurements, it must be set to the cor-
rect sound-velocity for the material being measured. Different types of material
have different inherent sound-velocities. For example, the velocity of sound
through steel is about 0.233 inches-per-microsecond, versus that of aluminum,
which is about 0.248 inches-per-microsecond. If the gauge is not set to the cor-
rect sound-velocity, all of the measurements the gauge makes will be erroneous
by some fixed percentage.
6.1 Programming the Sound Velocity
Since the TI-25P is a fixed velocity gauge, the correct sound velocity for
the material being measured must be programmed into the gauge via the
serial port on the bottom of the unit. Approximate sound velocities for com-
mon materials can be found in appendix C.
1. Connect the serial cable (Part No. N-306-0010) to a COM port on a
computer and to the RS232 connector located on the bottom of the
TI-25P. Remove and replace the rubber plug before and after
programming.
2. Assuming that DakView2 PC software is installed and running, select
the TI-25P icon from the DakView2 gauge selector icons. A window
will appear with the title “TI-25P Velocity Upload Utility”.
3. Under the Preset Velocity heading are two options. The first option is a
test box with a velocity number displayed. The text box is editable. To
change the velocity, click in the text field and type in the appropriate
velocity number. The second option is a list box with a material type
displayed. To change the material type, click the down arrow located to
the right of the list box. Use the arrows or slider bar to scroll through
the available material types. Click on a material to select it.
4. To select the units (english or metric), click on the radio button located
to the left of the units title. A black dot will appear in th button when
selected.
5. Click on the Program Gauge button located in the top right of the
window. A pop up window will be display with the following message
“Turn on gauge power”. Press the ON/OFF button on the TI-25P to
download the velocity. The TI-25P will display the new velocity.
– 12 –
8.0 TAKING MEASUREMENTS
In order for the transducer to do its job, there must be no air gaps between the
wear-face and the surface of the material being measured. This is accomplished
with the use of a “coupling” fluid, commonly called "couplant." This fluid serves
to “couple.” or transmit, the ultrasonic sound waves from the transducer, into the
material, and back again. Before attempting to make a measurement, a small
amount of couplant should be applied to the surface of the material being
measured. Typically, a single droplet of couplant is sufficient.
After applying couplant, press the transducer (wearface down) firmly against the
area to be measured. The Stability Indicator should have six or seven bars dark-
ened, and a number should appear in the display. If the TI-25P has been properly
“zeroed” (see page 8) and set to the correct sound velocity (see page 9), the num-
ber in the display will indicate the actual thickness of the material directly
beneath the transducer.
If the Stability Indicator has fewer than five bars darkened, or the numbers on the
display seem erratic, first check to make sure that there is an adequate film of
couplant beneath the transducer, and that the transducer is seated flat against the
material. If the condition persists, it may be necessary to select a different trans-
ducer (size or frequency) for the material being measured. See page 10 for infor-
mation on transducer selection.
While the transducer is in contact with the material being measured, the TI-25P
will perform four measurements every second, updating its display as it does so.
When the transducer is removed from the surface, the display will hold the last
measurement made.
IMPORTANT: Occasionally, a small film of couplant will be drawn out between
the transducer and the surface as the transducer is removed.
When this happens, the TI-25P may perform a measurement
through this couplant film, resulting in a measurement that is
larger or smaller than it should be. This phenomenon is obvious
when one thickness value is observed while the transducer is in
place, and another value is observed after the transducer is
removed.

– 10 –
7.0 TRANSDUCER SELECTION
The TI-25P is inherently capable of performing measurements on a wide range of
materials, from various metals to glass and plastics. Different types of material,
however, will require the use of different transducers. Choosing the correct
transducer for a job is critical to being able to easily perform accurate and reli-
able measurements. The following paragraphs highlight the important properties
of transducers, which should be considered when selecting a transducer for a
specific job.
Generally speaking, the best transducer for a job is one that sends sufficient ultra-
sonic energy into the material being measured such that a strong, stable echo is
received by the TI-25P. Several factors affect the strength of ultrasound as it trav-
els. These are outlined below:
Initial Signal Strength
The stronger a signal is to begin with, the stronger its return echo will be. Initial
signal strength is largely a factor of the size of the ultrasound emitter in the trans-
ducer. A large emitting area will send more energy into the material being meas-
ured than a small emitting area. Thus, a so-called "1/2-inch" transducer will emit
a stronger signal than a "1/4-inch" transducer.
Absorption and Scattering
As ultrasound travels through any material, it is partly absorbed. If the material
through which it travels has any grain structure, the sound waves will also
experience scattering. Both of these effects reduce the strength of the waves,
and thus, the TI-25P's ability to detect the returning echo.
Higher frequency ultrasound is absorbed and scattered more than ultrasound of
a lower frequency. While it may seem that using a lower frequency transducer
might be better in every instance, low frequencies are less directional than high
frequencies. Thus, a higher frequency transducer would be a better choice for
detecting the exact location of small pits or flaws in the material being measured.
Geometry of the Transducer
The physical constraints of the measuring environment sometimes determine a
transducer's suitability for a given job. Some transducers may simply be too large
to be used in tightly confined areas. Also, the surface area available for contact-
ing with the transducer may be limited, requiring the use of a transducer with a
small wearface. Measuring on a curved surface, such as an engine cylinder wall,
may require the use of a transducer with a matching curved wearface.
– 11 –
Temperature of the Material
When it is necessary to measure on surfaces that are exceedingly hot, high
temperature transducers must be used. These transducers are built using special
materials and techniques that allow them to withstand high temperatures without
damage. Additionally, care must be taken when performing a "Probe-Zero" or
"Calibration to Known Thickness" with a high temperature transducer. See
Appendix B for more information on measuring materials with a high tempera-
ture transducer.
NOTE: Selection of the proper transducer is often a matter of tradeoffs between
various characteristics. It may be necessary to experiment with a variety
of transducers in order to find one that works well for a given job.
Electromatic can provide assistance in choosing a transducer, and
offers a broad selection of transducers for evaluation in specialized
applications.

TI-25P
ULTRASONIC
THICKNESS GAUGE
Operating Instructions
CHECK
•LINE®
BY ELECTROMATIC
Distributed by: ABQ Industrial LP USA
Tel: +1 (281) 516-9292 / (888) 275-5772 eFax: +1 (866) 234-0451
Web: https://www.abqindustrial.net E-mail: [email protected]
Table of contents
Other Check-line Test Equipment manuals

Check-line
Check-line MiniTest 7200 FH Manual
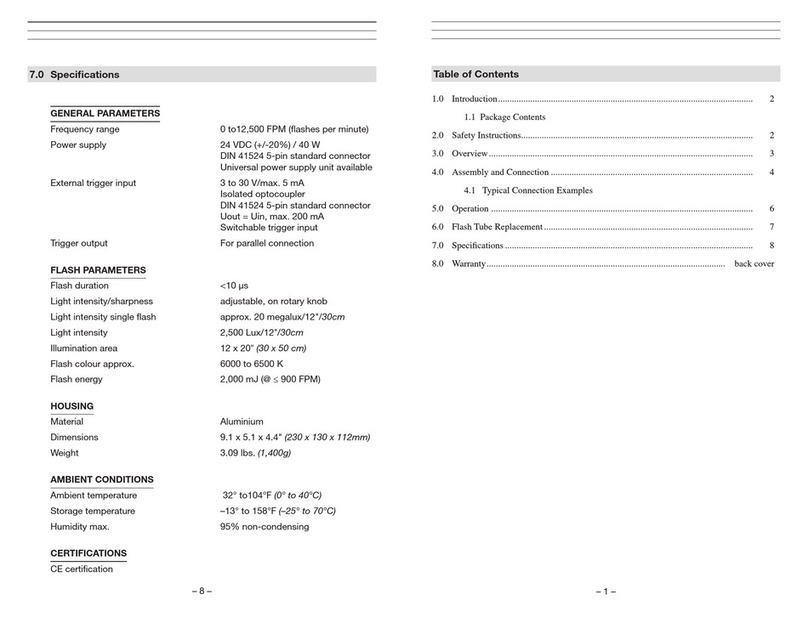
Check-line
Check-line LS-9-12000 User manual
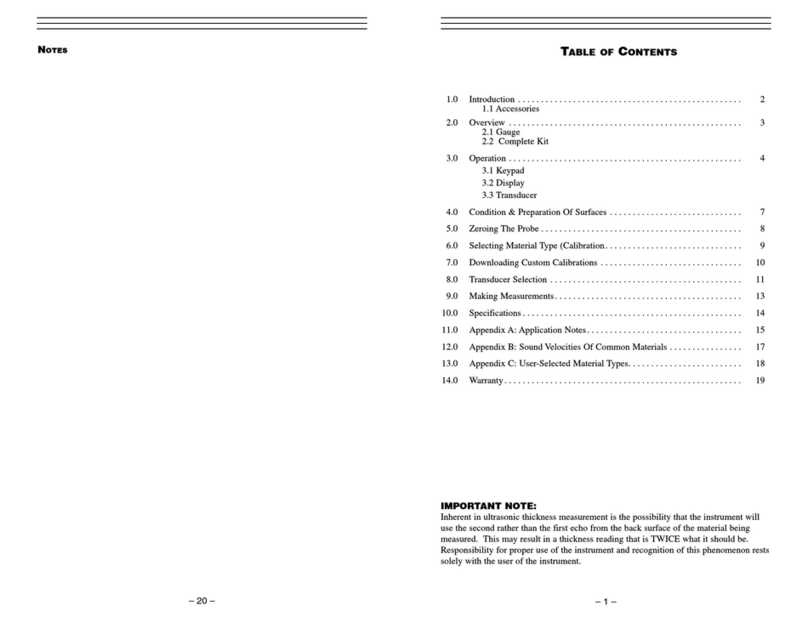
Check-line
Check-line TI-25S User manual
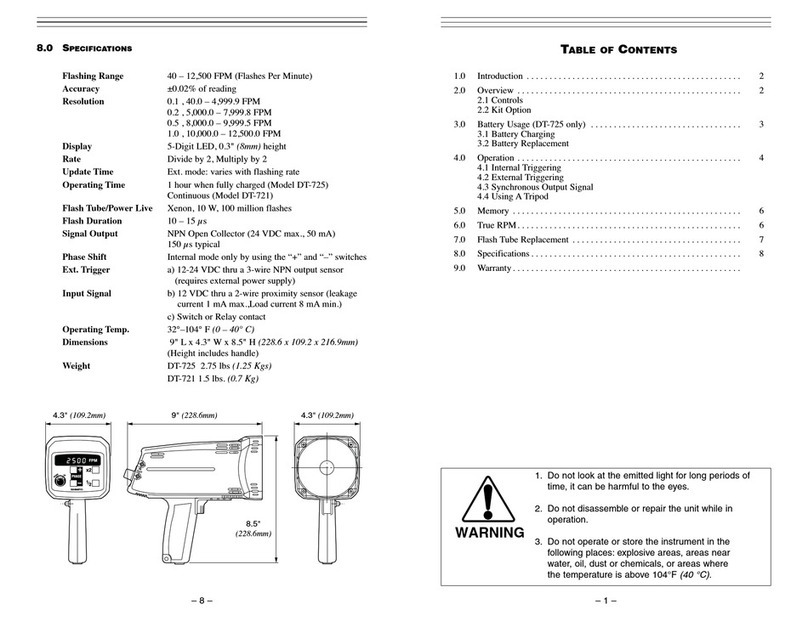
Check-line
Check-line DT-725 User manual

Check-line
Check-line TTC Series User manual
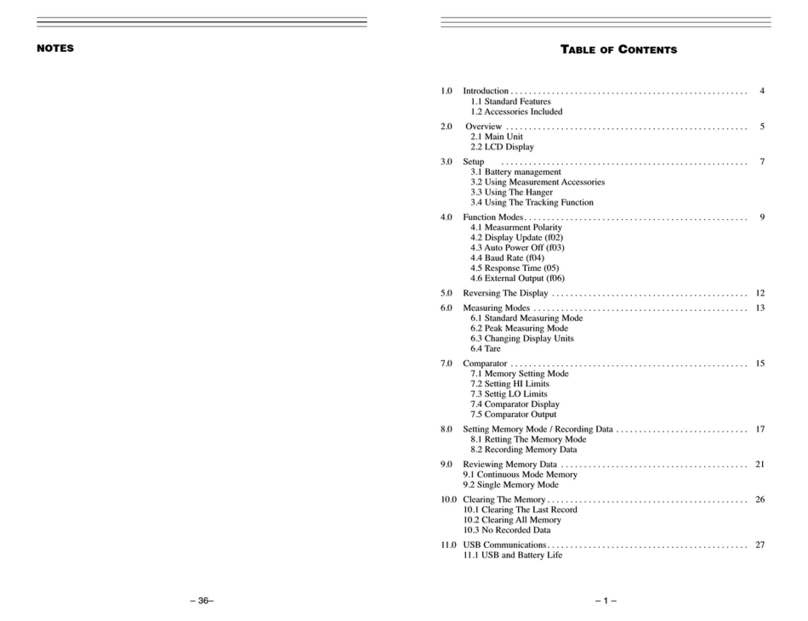
Check-line
Check-line FGV-XY User manual

Check-line
Check-line DT-311D User manual
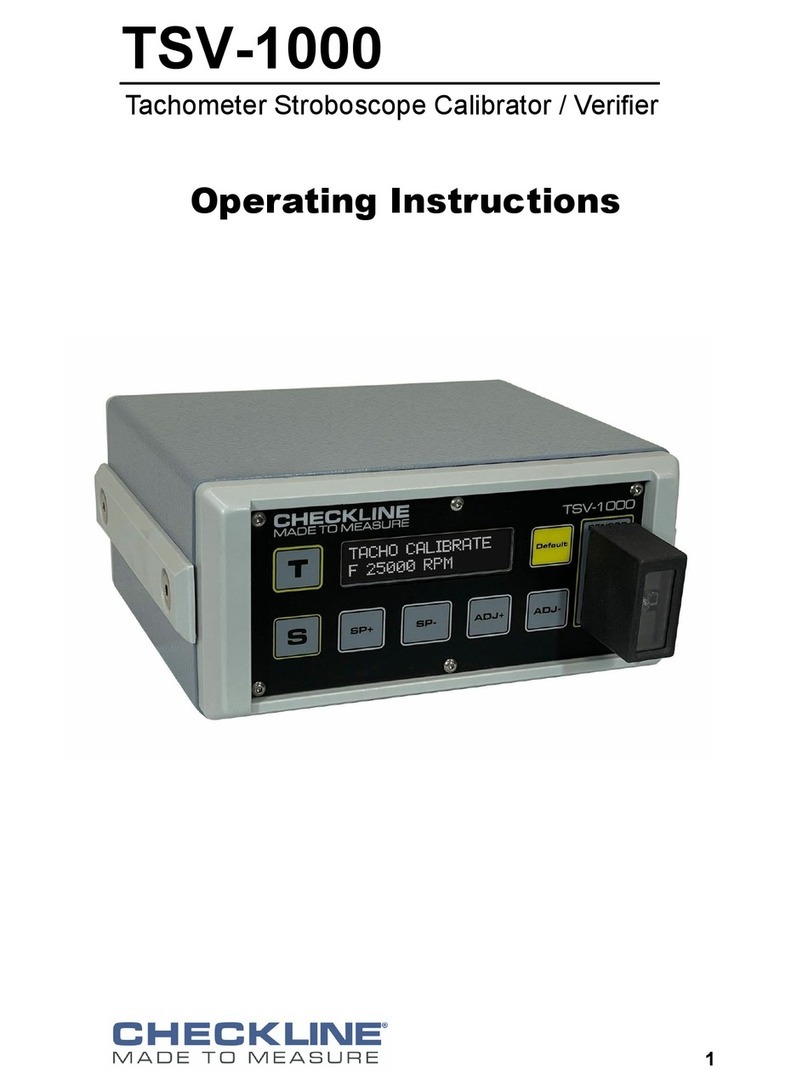
Check-line
Check-line TSV-1000 User manual
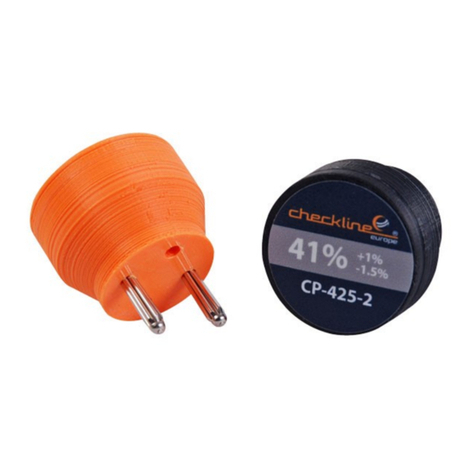
Check-line
Check-line CP-425-KIT User manual
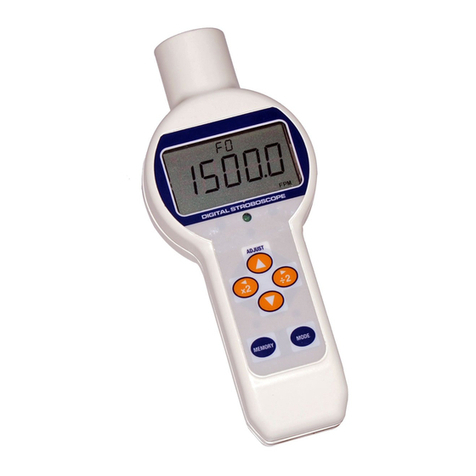
Check-line
Check-line NS-600 User manual