Coldelite UC 511 G Installation and operating instructions

39
UC 511 G
Soft Serve Freezer
SINGLE FLAVOR COUNTER MODEL
OPERATION & SERVICE
MANUAL
COLDELITE CORPORATION OF AMERICA
3760 INDUSTRIAL DR. * WINSTON-SALEM, N.C.27105 * TEL.(910) 661-9893 * FAX (910) 661-9895

1
FOREWORD
ThankyouforselectingCOLDELITEtomeettoday’sfastgrowingdemands.
Your COLDELITE freezer has been manufactured at one of the most
modernmanufacturingplants,utilizingthemostadvancedequipmentand
technologyavailableintheindustry.WeatCOLDELITE,takegreatpride
and care in the manufacture of each and every freezer, using only the
finest components available, to provide you with years of trouble-free
operation.
Over thirty years of experience in the manufacturing of dispensing
equipment have guided us in the preparation of this Operation and
Service Manual. PLEASE READ IT CAREFULLY. Keep it for future
reference and most of all, follow the instructions from the very time your
machine is put into service.
Onthefollowingpages,youwillfindimportantinformationandprocedures
which describe the proper installation, sanitizing, operation, and
maintenance of your COLDELITE machine. We feel certain that your full
compliancewiththeseinstructionswillassureyouofexcellentperformance,
trouble-free operation and profitable business for years to come.
Alltechnicaldata,picturesanddrawingscontainedinthismanualarenotbindingonthemanufacturer,norcanthe
manufacturer be held liable for any modification of the machine in part or completely.
CODE: 5543360/5

2

3
INDEX
Page
FOREWORD 1
PART I INSTALLATION 5
A) Uncrating 5
B) Positioning the Machine 5
C) Electrical Requirements 6
D) Completing the installation 6
PART II EXPLANATION OF CONTROLS 7
A) Electronic Control Panel 7
B) The Dispense Handle 8
C) Proximity Switch 8
D) Safety Switch 8
E) Electric Control Panel 8
F) Other Controls 9
PART III INITIAL CLEANING PROCEDURE 10
PART IV ASSEMBLING THE FREEZER 14
A) Assembling the Beater/Augers 14
B) Assembling the Dispensing Head 15
C) Assembling the Gravity Feed Tubes 17
PARTV SANITIZING THE FREEZER 18
PARTVI STARTING THE FREEZER 21
PARTVII OPERATING THE FREEZER 23
PARTVIII ROUTINE, PERIODIC CLEANING 25
PROCEDURES
PART IX TECHNICAL INFORMATION 26
A) Refrigeration 26
B) Beater Motor 26
C) Overload 26
D) Proximity Switch 27
PART X MAINTENANCE 27
A) Trouble Shooting Guide 28
B) Parts Identification 29
C) Wiring Guide 35
D) Spare Parts List 37

4

5
Important
Failuretocloselyfollowoperationalandmaintenanceprocedures
may result in damage to the unit and/or void your warranty.
Coldelite Corporation will not be responsible for any machine
not properly maintained.
In the event this unit should malfunction, please contact your
Coldelite Distributor or an authorized service agency.
PART I
INSTALLATION
Before starting this procedure, make sure the shipping case
doesnotshowanyevidenceofhavingbeendropped,tampered
withorabusedinsuchawayastoindicatethatitscontentsmay
have been damaged in transit.
IMPORTANT:Shouldtheoutsideoftheshippingcasegiveany
indication of possible hidden damage, state this on the bill of
lading before signing. Contact the carrier immediately and
requestaninspectionofdamage.Ifthisprocedureisnotadhere
to,youwillforfeityourrighttofiledamageclaimandberesponsible
for subsequent repair costs.
A)Uncrating
Proceed, as follows:
1) The case is secured to the skid with plastic strapping.
When you cut this strapping, do it with caution, as it may
spring out. Remove case by lifting it straight up and away
from the machine.
2) Thefreezerisalsosecuredtotheskidwithplasticstrapping.
Exercise caution and cut this strapping to free the machine
from the skid.
3) Remove the single screw at the bottom of each side panel.
Remove the panels by sliding upward slightly, then
pull outwardatthebottomandallowthepaneltoslide
down. The protective plastic coating which is
laminated to the panels can now be removed by
simply peeling off.
B)Positioning the Machine
1) The freezer is shipped without legs installed. To install
the legs, lift the freezer and screw the four legs into the
bottom of the frame at each corner. When the freezer is
placed in the desired location, it must stand level. Level
the freezer by turning the bottom part of each leg in or
out. Check for level condition by placing level on the top
of the freezer at each corner.
NOTE: Accurate leveling is necessary for correct drainage of
freezer barrel and to insure correct over-run.
Figure 1
Clearances Required for
Air Cooled Models
2) The freezer is now ready to be positioned onto your
counter. The counter must be capable of supporting 180
lbs. and should be vibration free. Reinforce it, if necessary.
Remember when choosing a location, if your unit is air
cooled, proper air flow will need to be maintained. Allow
at least 8 inches on left side and a minimum of 6 inches
between the right side of the machine and any obstruction.
(Ref. Fig. 1).
Note: If these clearances are not maintained, the production
capacitywillbereduced,cyclingwillincreaseandthepotential
will exist that the machine will stop completely.
3) It is necessary to clean the condenser each month to
eliminate dust, paper, etc. which may obstruct it, damaging
the proper functioning of the machine.
4) The machine should also be within six feet of the power
supply (a plug and receptacle or unfused disconnected).
5) Position the machine for easy accessibility for cleaning,
servicing and maintenance.
6) Position the machine away from direct sunlight. For every
2°F over 68°F, the machine’s performance will decrease
by approximately 1%.
7) Once the machine is set in position, it should be leveled
as accurately as possible.
Air
Flow
8" 6"
Rear View

6
C) Electrical Requirements
Allwiringinstalledtooperatethisfreezermustbeinaccordance
with the National Electrical Code and/or local electrical codes,
rulesandregulations.Themachinemustbeproperlygrounded.
Itis recommendedthe powersupply beinstalled bya licensed
electrician.
Voltage UC 511: 115 Volts
Total Running Amperage FLA: 18 Amps.
Fuse Size: 20 Amp. Max.
Wire Size (50 Ft. Max.): # 10
Power Supply must be adequate to meet requirements at all
times.Voltagefluctuations,withthemachineinoperation,should
not exceed ± 5% of the normal or rated voltage.
Adequate Wiring must beprovided with respectto wire sizeor
gauge.Unless otherwiserequiredbythelocalElectricalCode,
thesamesizewiregaugeatthemachinejunctionboxshouldbe
used for direct power line. A separate circuit breaker with
adequate fuse protection should be employed.
An unfused disconnected switch or a properly sized plug and
receptacle within 6 feet of the freezer, is recommended.
Coldelite freezers are equipped with protection for the beater
motor. Should the line voltage drop, or in the unlikely event a
short circuit occurs, the overload protector will automatically
disconnectthestarterandthemachinewillstopimmediatelyso
that no permanent damage can be caused to the motor.
Torestartthefreezer,depresstheSTOP/RESETbuttonlocated
on the front switch pad.
Theheaterprotectionmustcooldownforseveralminutesbefore
the RESET will operate. See Fig. 4.
Thecompressorisalsointernallyprotected.IftheKlixonprotector
tripsduetoanoverload,againtheprotectormustfirstcooldown
for several minutes before the compressor can be restarted.
Electrical Connections (Ref. Fig. 5)
Having removed the right side panel, the machine’s wiring
connection box can be found on the bottom of the frame and is
labelled “Connect Power Line Here”.
The power line is first passed through the access hole located
atthebottomdeckdirectlybelowthewiringconnectionbox.The
powerlinemaythenbeconnectedtothemachine’spowerlines
and wiring connection box. Upon completion, the power line
shouldbefastenedtothewiringconnectionboxwithappropriate
electrical hardware.
In all installations, the machine must be properly grounded.
Since all high voltage components (controls are 24 volts) are
connected by means of flexible conduit, or cord, adequate
groundcontinuityisassuredbyrunningandfasteningaground
line to the machine junction box ground lug. (Ref. Fig. 5).
Beater Rotation
Afterelectricalconnectionsarecompleted,checktherotationof
thebeater.Itshouldbecounterclockwisewhenfacingthefront
of the machine.
D) Completing the Installation
Onthe following pages,you will findimportant information and
procedures which describe the proper installation, sanitizing,
operation and maintenance of your COLDELITE machine. We
feelcertainthatyourfullcompliancewiththeseinstructionswill
assureyouofexcellentperformance,trouble-freeoperationand
a profitable business for years to come.
NOTICE: Failure to closely follow set-up and maintenance
procedures can void your warranty. Coldelite Corporation will
not be responsible for any machine not properly maintained.
In the event this unit should malfunction, please contact your
Coldelite Distributor or an authorized service agency.
WARNING:EXTREME CARE MUST BE TAKEN WHEN
REMOVING SIDE, REAR OR CONTROL BOX PANELS.
ALWAYSTURNTHEMACHINETOTHEOFFPOSITION.ALSO
TURN OFF THE DISCONNECT SWITCH ON ELECTRICAL
SUPPLY LINE BEFORE EXPOSING ANY ELECTRICAL
CONNECTIONSAND/ORMOVINGPARTS,SUCHASBELTS,
PULLEYS, FAN BLADES AND BEATER.
Figure 5
Figure 4

7
Stand-by function
This position is used during prolonged idle periods. The
temperatureoftheproductinboththemixtank(s)andfreezer
cylinder (s) is held at a safe temperature and controlled
automatically by the thermostats. Product should never be
servedwheninthispositionasthe “storage” temperature is
higher than normal serving temperatures.
In this position the beater motor is ON when the system is
coolingthecylinder,beatermotorisOFFwhenthesystemis
cooling the hopper which will allow significant ENERGY
CONSERVATION.
Beater function
With this function on, pilot light pos. L4 on, only the beater
turns while the refrigeration system is cut out. This function
is timed and ends automatically when the settime is over.
About 15 minutes.
Hopper Mix level indicator
This pilot light pos. L5 indicates that the level of the mix
in the hopper has reached the minimum allowed, and that
more mix must be added.
Whenilluminated,dispensingofproductshouldbestoppedand
thetank refilled with mix. Eachtank has a total capacityof 6 qts
each when full.
The MIX LEVEL SWITCH is located within the stainless steel/
plastic rod attached to the bottom of each mix tank.
L1
L2
L3
L5
L4
570
571.1
571.2
PART II
EXPLANATION OF CONTROLS
A) Electronic Control Panel
Positions L1/L5 Lighted function indicators
These indicators illuminate to show that the function
corresponding to the signal next to the indicator itself is
on.
Monitor pos. 570
Thisnumericalmonitordisplaystheconsistencyoftheproduct
when the machine is turned on and while it is operating in
AUTOMATIC.
Stop/Reset button pos. 571.1
With the Stop/Reset function on, pilot light pos. L1 lit, the
machine is ready to receive the command for any of the
main functions.
Select button pos. 571.2
By pushing this button you can select the functions:
-Automatic
-Stand-by
-Beater
Indicatorsilluminatetoshownthatthefunctioncorresponding
to the signal next to the indicator itself is on.
Automatic function
When this function is on, pilot light pos. L2 lit, the product
is processed until it reaches the proper consistency (pre-
set HOT setting). During this function, The Monitor displays
a number indicating the consistency of the product in the
cylinder until it reaches the set value, then it indicates the
temperature of the mix in the hopper tank.

8
B) THE DISPENSE HANDLE
The Dispense Handle controls the flow, or extraction rate of
finished, soft serve product.
Pullingthehandleinadownwarddirectionwillopenthedispense
orifice.Whentheunitisinthe“AUTOMATIC”mode,thiswillallow
finished product to be extracted and served.
C) PROXIMITY SWITCH
D) SAFETY SWITCH
Machineisequippedwithamagnetmoldedintothespigothead.
If the spigot head is removed the magnet deactivates a safety
switchbehindthefrontpanel.Themachinewillnotoperatewith
the spigot head removed. A message "MIP" will appear on the
display.
E) ELECTRIC CONTROL PANEL
TheElectricControlPanellocatedbehindtheupperrearpanel
of the unit, contains the controlling circuit to the components of
the machine. This panel is to be accessed only by trained,
experienced technicians.
Warning
Disconnect freezer from the source of electrical supply before
attempting to service.
InAUTOMATICfunctiontheproximityswitchpos.152startsthe
motorwhenthehand,handlingcuporcone,isintherangeofthe
sensitivity preset by Coldelite.
Note: Keep the sensor always clear and clean.
Adjusting Proximity Switch
Theproximityswitchpos.152hasbeenpresetatthefactoryand
its range is approximately 9 inches.
Ifmodificationisrequired,contactauthorizedserviceagencyas
this operation must be carried out by specialized technicians.
1 2 3 4 5
6789
152

9
The following is an explanation of the control panel controls:
1) BEATER MOTOR STARTER - activates the beater/auger
drive motor. In the "BEATER" mode, the starter is energized by
thefrontswitchpad.Inthe"AUTO"mode,thestarterisactivated
by either the proximity switch or timer.
2) COMPRESSOR CONTACTOR - activates the refrigeration
compressor.Whentheunitisinthe"AUTO"mode,thecompressor
contactor can be energized by the electronic H.O.M., timer, or
"TEV"thermostat.Inthe"ENERGYCONS."mode,thecontactor
will be energized by the electronic board.
3)The OVERLOAD PROTECTORsensesthe currentsupplied
tothebeatermotorandwillstoptheentiremachineintheevent
of an overload. This device also houses the overload reset
mechanism.
4)ThemainTRANSFORMERstepsdownthelinevoltage(115
Volts) to 24 Volts for the control circuit.
5) ELECTRONIC BOARD - controls all the functions of the
machine.
- Temperature of the product in hopper.
- Consistency of the product.
- Timer.
-Instand-by controls temperatureofthe product inhopperand
cylinder.
- Controls and or energizes all the information or messages
displayed on the monitor.
6) FUSE - protects 115 voltage line.
7) The CURRENT TRANSFORMER monitors beater motor
current for the electronic H.O.M.
8)TRANSFORMER -Steps downthe 24volt lineto 11volts for
the electronic board.
9)The24voltTERMINALBLOCKservesastheinter-connection
point for all 24 volt controlling circuit components.
F) OTHER CONTROLS
1)RefrigerationSOLENOIDVALVESarelocatedbehindtheleft
sidepanel.Thesevalvesarenormallyclosedandwhenenergized
by the electronic board, direct refrigerant flow to either the
freezingcylinderormixtank.Themixtanksolenoidisidentified
as "EVV" and the cylinder solenoid as "EVC".
2)TheHIGHPRESSURECUT-OUTislocatedontherightside
ofthefreezerandistiedintodischargeorhighsidelinenearthe
compressor. In the event of high pressure situation, it will shut
downthecompressor.Resetisautomaticwhenthehighpressure
subsides.Commoncausesforcut-outorshutdownarerestricted
air flow on air cooled models, unusually high ambient (room)
temperatures, and restricted or excessively hot water flow on
water cooled models.

10
PART III
INITIAL CLEANING
PROCEDURE
Thisisanewmachineanditmustbecompletelydisassembled,
washed, and sanitized before starting. Proceed, as follows:
1) Remove the mix tank cover and items packed in the tank
(spare parts, sanitizer, lubricant).
Thesparepartsorstart-upkitwillinclude:1)aspatula,2)spare
o-rings and rubber seals, 3) an o-ring extractor, 4) a tube of
sanitary lubricant, 5) three various sized cleaning brushes, 6)
severalpackets of sanitizerandthe OPERATIONALMANUAL.
HELPFUL SUGGESTION: Before proceeding with the
disassemblyofthefreezer,werecommendaplasticdishpanbe
usedinwhichtoplacetheparts.Thiswillminimizethepossibility
of misplacing or damaging the various component parts.
2) Proceed with the disassembly process by removing the
gravityfeedtubelocatedinthemixtank.Snugfitting,thetube
can be removed by pulling straight up and out.
Onceremoved,thetubemustbedisassembled.Todisassemble,
first remove the “SPLASH GUARD” by pulling it out of the tube.
Next,removethegravitytube“SLEEVE”bypullingitstraightoff
the tube.

11
Finally, remove the o-rings using the O-RING EXTRACTOR
included in the “start-up kit”.
Warning!
Never use anything other than the O-RING EXTRACTOR to
remove o-rings as damage to the o-ring and/or part can result.
3) Clean carefully the mix level device.
4) Loosen and remove the two (2) dispensing head retaining
knobs. The knobs are removed by turning in a counter-
clockwise direction.
5) Remove the dispensing head by pulling it straight towards
you and away from the machine.

12
6) Disassemble the dispensing head by first opening the
dispense handle.
Pull the handle retaining rod out far enough to allow the first
handle to disengage.
Returntheretainingrodtoitsoriginalposition.Usingtherodas
afulcrum,leverthedispensepistonoutofthedispenseheadwith
the handle.
Using the O-RING EXTRACTOR, remove the piston o-rings.
Eachpistono-ringgrooveisnotchedforeasyinsertionoftheo-
ring extractor.
Turnthedispensingheadoverandremovethelargeo-ringfrom
the back of the head.
7) Remove the beater/auger from the freezer cylinder. Pull
the beater STRAIGHT out towards you. Should it became
jammed, DO NOT FORCE. Tap the front of the beater back
into the cylinder with the palm of your hand.

13
8) Disassemble the beater/auger by first removing the rubber
beater shaft (lip) seal, simply slide it off the shaft.
Continue disassembly by removing the beater IDLER. Pull
forward until the grooved portion of the shaft lines up with the
opening at the front of the beater/auger.
Finally, remove the beater/auger END PUSHER by pulling
straight and away from the beater. Dismount the scraper by
pulling it away from its housings.
9) The machine is now completely disassembled. The parts
should now be washed, rinsed and sanitized.
10)Washallthepartsinlukewarmwater(80-85F)usingamild
detergentandthecleaningbrushesprovidedintheSTART-
UP KIT.
DONOTUSEHOTWATERONANYOFTHEPLASTICPARTS
AS DAMAGE TO THE PARTS CAN RESULT.
Rinse the parts in luke warm water (80-85 F).
Place the parts in luke warm, sanitized water for 2 to 5
minutes. Use the sanitizer provided in the START-UP KIT
following the manufacturers directions.
11)Placethepartsonaclean,sanitizedcounterareaandallow
to air dry or disassemble wet. DO NOT TOWEL DRY OR
RINSE SANITIZED PARTS.
Figure 10
2) Rinse
3) Sanitize
4) Air Dry
1) Wash

14
Mount the idler back.
When installed correctly, the idler (when turned) should rotate
freely. If the idler does not rotate, it is incorrectly installed and
must not be installed into the machine. Repeat the above
instructions.
5) Next,lubricateandinstallthebeaterlipsealbyfirstlubricating
the beater/auger shaft with the lubricant included in the
START-UP KIT. Place three, 1/4" beads in equal distances
around the shaft as shown below.
Slide the rubber, beater lip seal onto the shaft.
Lubricatetheendofthebeaterlipsealwhichisnotlubricatedby
placing three, 1/4" beads in equal distances around the seal
surface as shown below.
PART IV
ASSEMBLING THE FREEZER
Once the parts have been washed, rinsed and sanitized, the
freezer is ready to be re-assembled. Prior to beginning the re-
assemblyprocedure,sanitizeyourhandsbysubmerginginthe
sanitizing solution. Begin to re-assemble as follows:
A) Assembling the Beater/Auger
1) First, re-assemble the beater/auger assembly. Begin by
gatheringthefivepartsneededtocompleteeachassembly:
A) plastic “END PUSHER”, B) BEATER/AUGER, C) IDLER,
D) rubber, beater LIP SEAL, E) BLADE.
2) Mounttherubbersealontothescraperbykeepingthehead
opposite to the groove.
3) Insert the scraper into the beater pins. Fasten the end
pusher. When installed correctly, the scraper should move
freely up and down, but should not come out away from
its seat.
BA
C
E
D

15
6) Finally, insert the beater/auger into the freezer cylinder.
Holdingthebeater/augerhorizontally,slideitstraightintothe
cylinder until it can go no further.
IMPORTANT:Beforeinstallingthebeater/auger,makecertain
thebeaterlipsealisinplaceandtheidlerisproperlyinstalled.
Rotatethebeater/augeruntilyoufeelthedriveshaftengageand
push the beater/auger further back to properly seat.
B) ASSEMBLING THE DISPENSING HEAD
1) Begin by gathering the parts necessary to assemble the
dispensinghead.Thesepartsinclude:A)one(1),4"diameter
O-ring, B) the dispensing head body, C) two (2), 13/8"
diameter end piston O-rings, D) one (1) piston, E) handle
retaining rod, F) one (1) dispense handle.
ABED
C
F

16
4) Insert the piston into the chamber of the dispensing head
body making certain to align the square notch of the piston
withtherectangular notch atthefront of thedispensehead.
5) Turn the dispense head over and install the 4" diameter
O-ring into O-ring groove located in the back of the head.
Lightly lubricate the O-ring with the sanitary lubricant.
2) First, remount the end piston O-rings onto the end pistons.
Simply roll onto the piston until they drop into the O-ring
notches.
3) OncetheO-ringshavebeenmounted,liberallylubricatethe
area between the two O-rings. Place a bead of lubricant
around the entire piston as shown.
Spread the lubricant on the surface area between the two O-
ringsandtheO-ringsaswell.Thiswillensurefreemovementof
thedispense handlesoncetheheadiscompletelyassembled.

17
6) Affix the dispensing head to the machine and fasten it onto
thetwo mounting studs.
7) Fasten the dispense head to the machine using the two (2)
stainlesssteelretainingknobs.
8) HAND TIGHTEN the knobs.
B
D
C) ASSEMBLING THE GRAVITY FEED
TUBES
1) Beginbygatheringthepartsneededtoassemblethegravity
feed tube. These parts include: A) the SPLASH GUARD, B)
two(2)3/4"diameterO-rings,C)theTUBESLEEVE,andD)
the GRAVITY FEED TUBE.
2) Slide the two (2) 3/4" O-rings onto the bottom of the gravity
feed tube until they drop in the O-rings grooves.
CA

18
3) Slide the sleeve onto the tube. Please note that the slots in
the sleeve should be at the top of the tube when installed.
4) Slide the splash guard into the tube.
5) Lubricate the two O-rings with sanitary lubricant.
6) Insert the assembled tube into the hole at the bottom of the
mixtank. Pressthetubedownuntilitseatsand theflangeat
thebase ofthetuberestsagainstthebottomof themixtank.
Themachineisnowcompletelyassembledandreadytobe
sanitized.
PART V
SANITIZING THE FREEZER
Prior to install the machine with your soft serve product, the
machine must be sanitized. The frequency of cleaning and
sanitizing cycles must comply with local health regulations.
If uncertain about local regulations, contact your local Board of
Health.
Sanitizing the machine is most important. This procedure will
retardthegrowthofbacteriaandinsureexcellenttestresultson
yourproductwhenexaminedbylocalHealthand/orAgriculture
Departments.
To begin, you will need a clean pail, sanitizer (sample packets
includedinthestart-upkit),spatula(includedinstart-upkit),and
brush (plastic bristle).
Lubricate

19
1) Mix the sanitizer (2 ounces of Steera Sheen green label or
equivalent)into a cleanpail containing onegallon of warm
water.Thissolutionwillmakea200P.P.M.(partspermillion)
concentrationofchlorinesanitizingsolution.Pourthesolution
into the mix tank.
IMPORTANT:Do notexceed theformula recommendedby the
sanitizer manufacturer as it will not add to its effectiveness.
2) Pull the gravity feed tube out of the mix tank hole and lay it
down in the tank. This will allow the cylinder to completely
fillwith thesanitizing solution.
3) Push selector button 571.2 to select the BEATER position.
Let the machine run for 30 seconds.
4) Push selector button 571.1 to turn “OFF” the machine.
5) Usingasanitizedsoftbristlebrush,brushthesidesofthemix
tank,andallotherproductcontactareas.Allowthesanitizing
solutiontoremainincontactwithallproductcontactareasfor
three to five minutes.
6) Placetheclean,sanitizedpailunderthedispensingheadand
open the handles by pulling them in a downward direction.
571.1
571.2
Table of contents
Other Coldelite Freezer manuals
Popular Freezer manuals by other brands
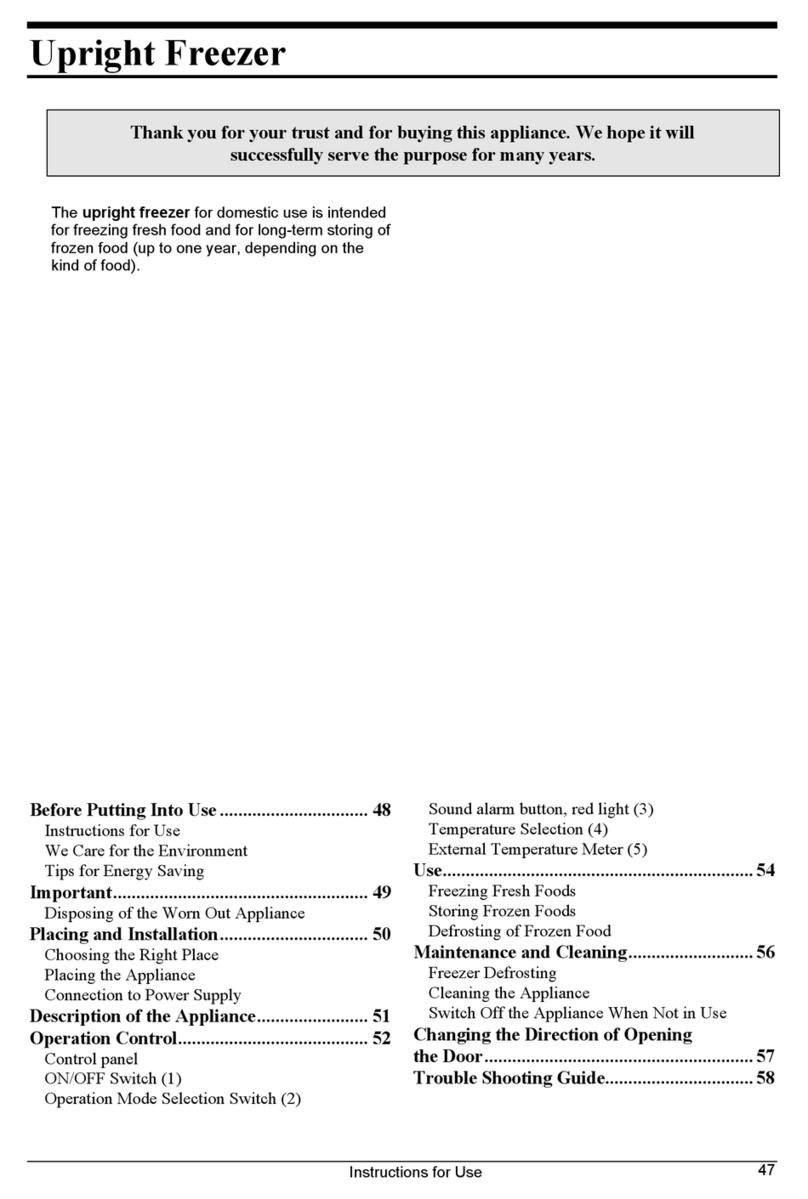
Smeg
Smeg CV24A Instructions for use
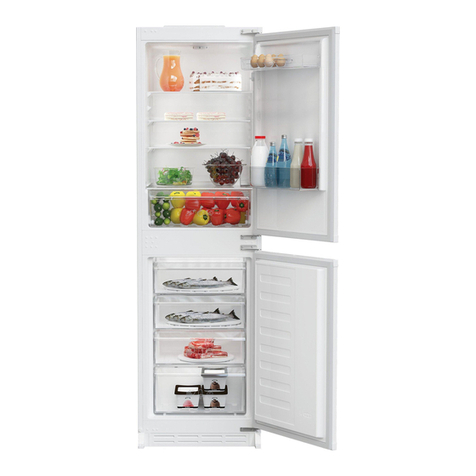
Zenith
Zenith ZICSD355 Installation instructions manual

Duke
Duke GES-102 OPERATOR’S MANUAL WITH ILLUSTRATED PARTS LIST

Miele
Miele KWFN 8706 SE ED-1 Operating and installation instructions
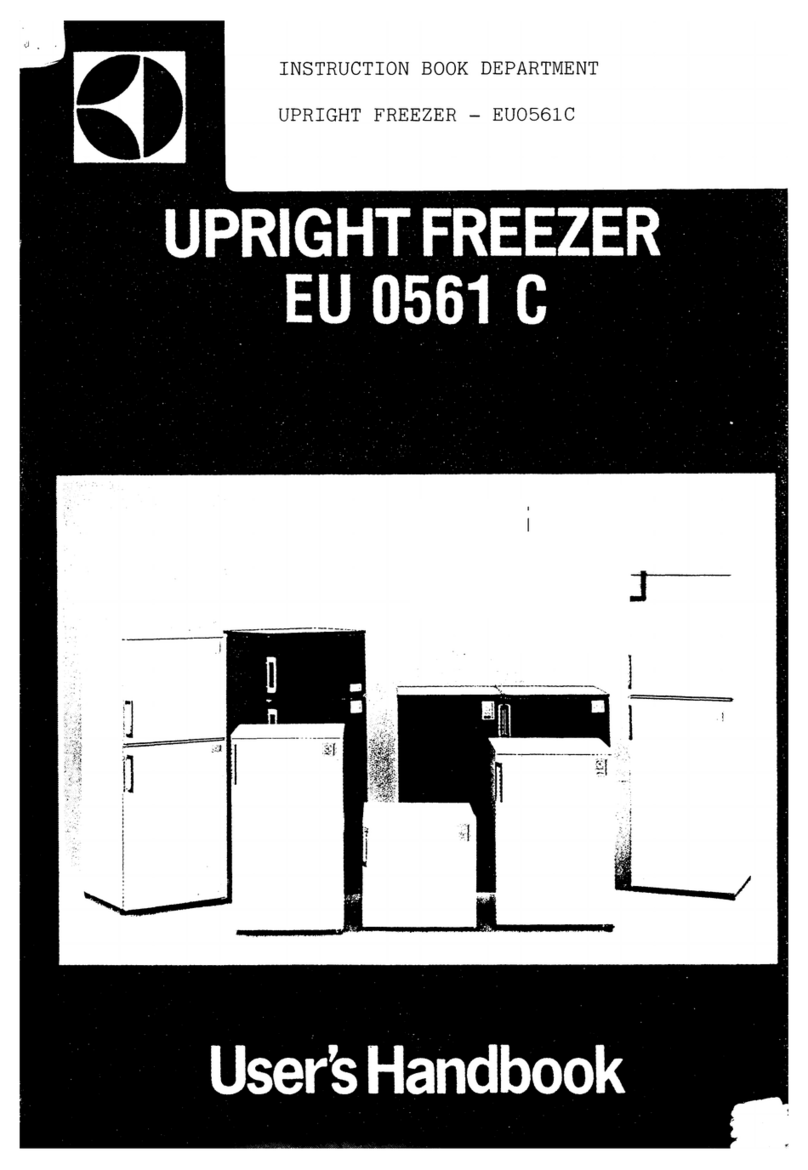
Electrolux
Electrolux EU 0561 C User handbook
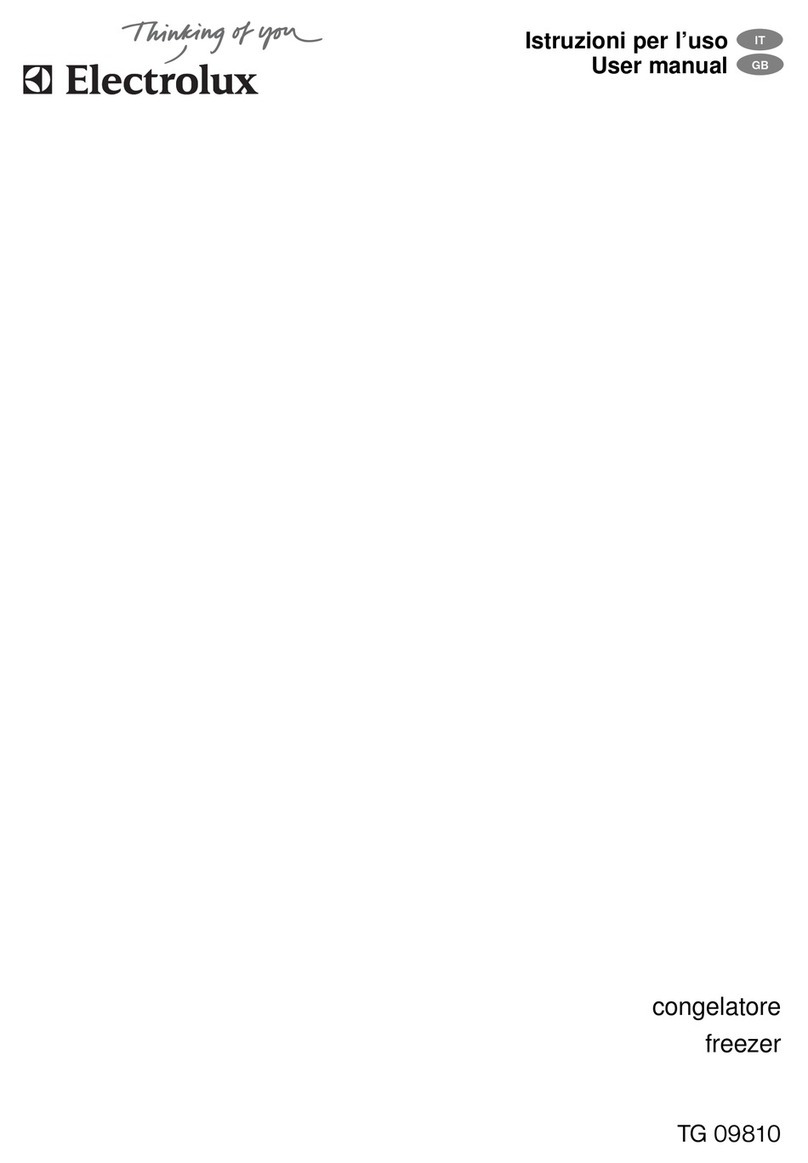
Electrolux
Electrolux TG 09810 user manual