Distech Controls SC-ARES User manual

Installation Guide
SC-ARES
Analog Resistance Module
Figure 1: SC-ARES Analog Resistance Module
Product Description
This document describes the hardware installation procedures for the SC-ARES Analog Resistance Module.
The analog resistance module is an interface that accepts an analog signal input (voltage or current) and uses that signal to proportionally control a variable
resistance output. The device output simulates a 3 wire slide wire or rotary potentiometer. The resistive output is electrically isolated from the input control
signal.
The input signal type is DIP switch selectable to one of several factory calibrated standard ranges and the output has both ends of the potentiometer and
the wiper available on the terminal connectors. The output resistance simulates a potentiometer and does not wrap around at the end points.
The resistance module includes a regulated power output that can be used to power a current-loop transducer and also features a failsafe input that will
connect to the output terminals in case of power loss or for manual output control. There is also an LED power indicator and a manual override jumper for
failsafe operation.
The product comes with standard snap-track for easy mounting or is available with various resistance values. The potentiometer may be ordered with no
offset value such as 0-135 Ω, or may be configured with an offset resistance such as 20-30K Ω.
General Installation Requirements
For proper installation and subsequent operation of each device, pay special attention to the following recommendations:
- Upon unpacking the product, inspect the contents of the carton for shipping damages. Do not install damaged device.
- Avoid areas where corroding, deteriorating or explosive vapors, fumes or gases may be present.
- Ensure that all equipment is installed according to local, regional, and national regulations.
Personal injury or loss of life may occur if you do not follow a procedure as specified.
Equipment damage or loss of data may occur if you do not follow a procedure as specified.
Take reasonable precautions to prevent electrostatic discharges to the controller when installing, servicing or operating
the controller. Discharge accumulated static electricity by touching one’s hand to a well-grounded object before working
with the controller.

2/5
Mounting Instructions
The snap-track device may be mounted in any position. Use only fingers to remove the PCB from the snap-track, do not pry on the PCB with tools. Do not
flex the PCB during removal or installation. Slide the PCB out of the snap-track or push against one side of the snap-track and lift the PCB out.
See Figure 2. Ensure any metallic mounting hardware does not contact the underside of the PCB.
Figure 2: Transmitter PCB.
Avoid mounting in areas where the device is exposed to vibrations or rapid temperature changes. Mount the snap track with the PCB removed using two
screws as shown in Figure 3.
Figure 3: Mounting Snap Track.
Once the snap track is mounted, place the bottom edge of the PCB into the bottom slot on the snap track and then gently press the top edge in both
corners until the PCB snaps into the top slot of the snap track. See Figure 4.
Figure 4 Mounting PCB onto Snap Track.

3/5
Wiring
- Deactivate the 24 Vac power supply until all connections are made to the device to prevent electrical shock or equipment damage. Follow proper
electrostatic discharge handling procedures when installing the device or equipment damage may occur.
- Use 22 AWG shielded wiring for all connections and do not locate the device wires in the same conduit with wiring used to supply inductive loads
such as motors. Make all connections in accordance with national and local codes.
Wiring – Power Input
- Connect the plus DC or the AC voltage hot side to the PWR terminal. The supply common is connected to the COM terminal. The device is reverse
voltage protected and will not operate if connected backward. It has a half-wave power supply so the supply common is the same as the input signal
common.
- Several devices may be connected to one power supply and the input signals all share the same common.
- Ensure the supplied power is within the device ratings. Power supply voltages outside the ratings may cause over-heating, device damage or
unreliable operation.
Wiring – Input Signal
- The analog input signal is connected to the IN terminal. The input signal is referenced to the COM terminal.
- Ensure the INPUT SELECT switches are set for the correct signal type, either voltage or current. The input signal will typically come from a DDC or
BAS analog output.
Wiring – Power Output
- The 20V terminal is a regulated power supply output which provides a 20 Vdc power supply at 30 mA maximum that can be used to operate an
external sensor.
Wiring – Resistance Output
- The signal interface output stimulates a potentiometer.
- Terminal R is the wiper, terminal W is the low end (minimum) of the pot and terminal.
- Terminal B is the high end (maximum) of the pot.
Figure 5 Wiring Diagram.

4/5
Operation – Input and Output Signals
The input signal type is selected with the 4 position DIP switch labeled INPUT SELECT. The available input signal types and DIP switch positions are
shown in the chart below.
Figure 6 Input and Output Signals
Figure 7 Applications of Operation Input Output Signals
The ranges shown in the chart are all pre-calibrated such that 0-100% of the input signal will cause the output resistance from W to R to change from the
pot minimum to the maximum value.
Upon power up, the wiper will start at the W position but will immediately sample the input signal and move to the resistance value proportional to the input
signal and the selected input range.
For example, for a 0-5 Vdc input signal and a 0-135 Ω pot, the resistance between W (min) and R (wiper) will be 0 Ω for 0 Vdc input and the resistance
between B (max) and R (wiper) will be 135 Ω. As the input signal increases from 0 to 5 Vdc, the resistance between W and R will increase and the
resistance between B and R will decrease until the input signal is 5 Vdc. At 5 Vdc the W-R resistance will be 135 Ω and the B-R resistance will be 0 .
The resistance output has a minimum and maximum value and does not wrap around. In the above example with 0-5 Vdc input signal, the W-R resistance
will increase to 135 Ω and will stay at 135 Ω even in 6 Vdc is applied to the input.
Voltage input signals are referenced to the COM terminal and have an input impedance of >10 KΩ.
Current input signals are also referenced to COM and have an input impedance of 250 Ω. The current input is a sinking type signal, the controller must
source the 0-20 mA signal.
The signal interface features a micro-controller for highest accuracy and includes input filtering and hysteresis to prevent relay chatter or hunting for the
correct output resistance value. The output resistance is controlled with a 256 bit resolution.
Operation – Failsafe Input
The signal interface OUTPUT terminals are connected to the resistance values through a DPDT relay that is used to control the failsafe function. During
normal operation with power applied to the signal interface, the pot resistance is connected to the OUTPUT terminals.
In the event of a power loss, the failsafe relay will disconnect the OUTPUT terminals from the pot value and instead connect the OUTPUT terminals directly
to the FAILSAFE terminals.
This is useful in several ways, for example, discreet resistor may be connected to the W (min) and R (wiper) terminals of the FAILSAFE connector to set
a minimum resistance value on power failure. If the signal interface is controlling a damper actuator, then the resistance would set a minimum open position
on power failure.
To failsafe to the minimum signal interface resistance value, connect a wire jumper between the W and R terminals of the FAILSAFE connector.
To failsafe the maximum signal interface resistance value, connect a wire jumper between the B and R terminals of the FAILSAFE connector.
A manual potentiometer may also be connected to the FAILSAFE connector to allow manual control. The PCB has a MAN / AUTO jumper that can be
used to force the failsafe mode. For normal operation the jumper is placed in the AUTO position. To test the system, place the jumper in the MAN position
and the OUTPUT terminals will immediately connect to the FAILSAFE terminals so an external pot can be used to manually control the device connected
to the signal interface output.
Return the jumper to the AUTO position for normal operation.

©, Distech Controls 2020 All rights reserved.
While all efforts have been made to verify the accuracy of information in this manual, Distech Controls is not responsible for damages or claims arising from the use of this
manual. Persons using this manual are assumed to be trained HVAC specialist / installers and are responsible for using the correct wiring procedures and maintaining safe
working conditions with fail-safe environments. Distech Controls reserves the right to change, delete or add to the information in this manual at any time without notice.
Distech Controls, the Distech Controls logo, and Innovative Solutions for Greener Buildings are trademarks of Distech Controls. All other trademarks are property of their
respective owners.
5/5 SC-ARES_IG_10_EN
Dimensions
Table of contents
Other Distech Controls Control Unit manuals
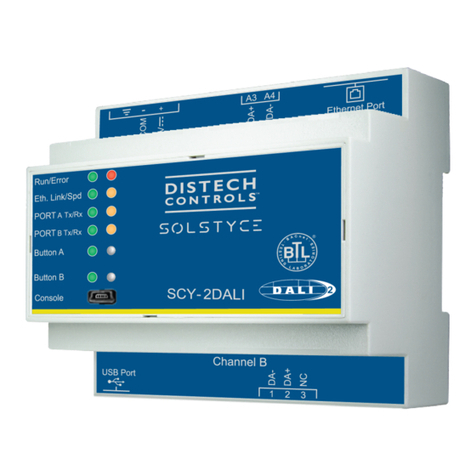
Distech Controls
Distech Controls SOLSTYCE Series User manual
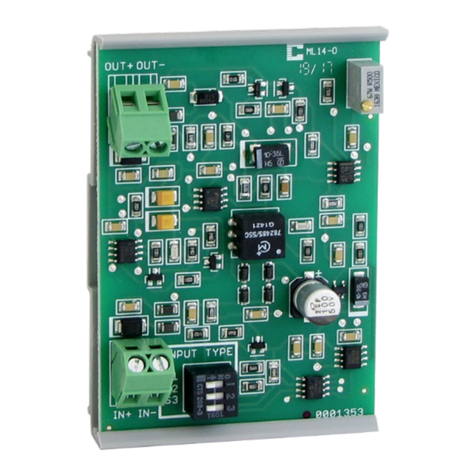
Distech Controls
Distech Controls SC-AI-420 User manual

Distech Controls
Distech Controls Allure UNITOUCH User manual
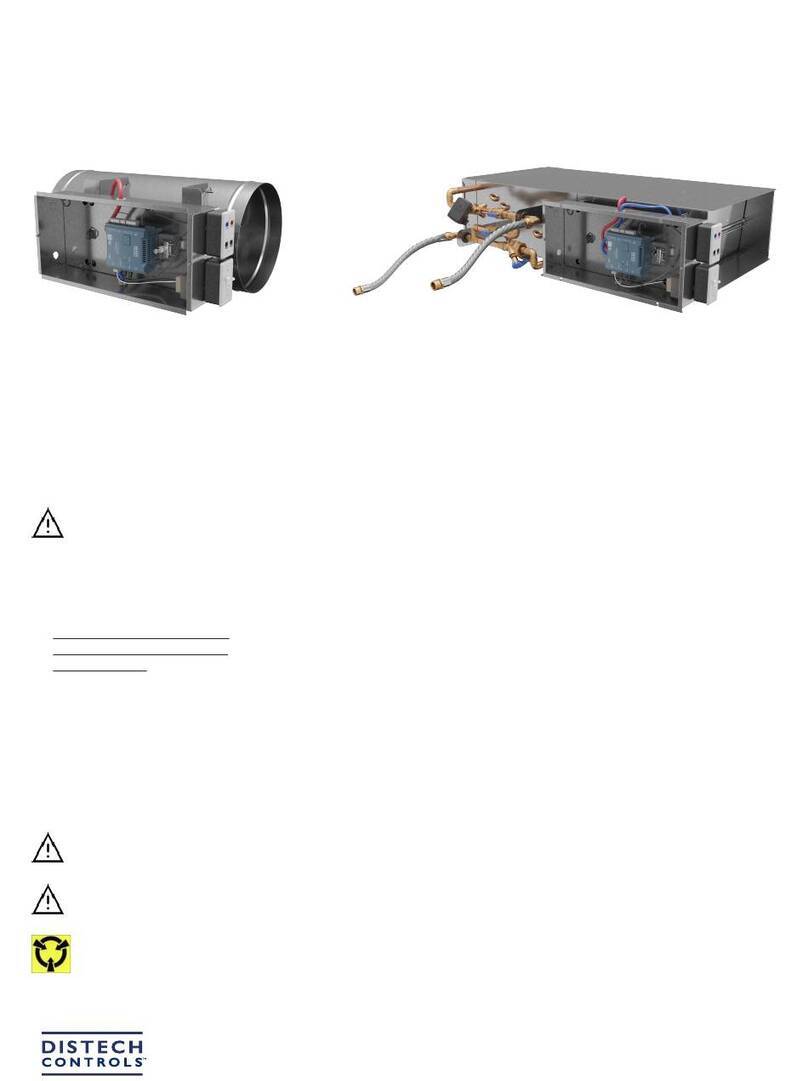
Distech Controls
Distech Controls Smart Air Control Valve User manual
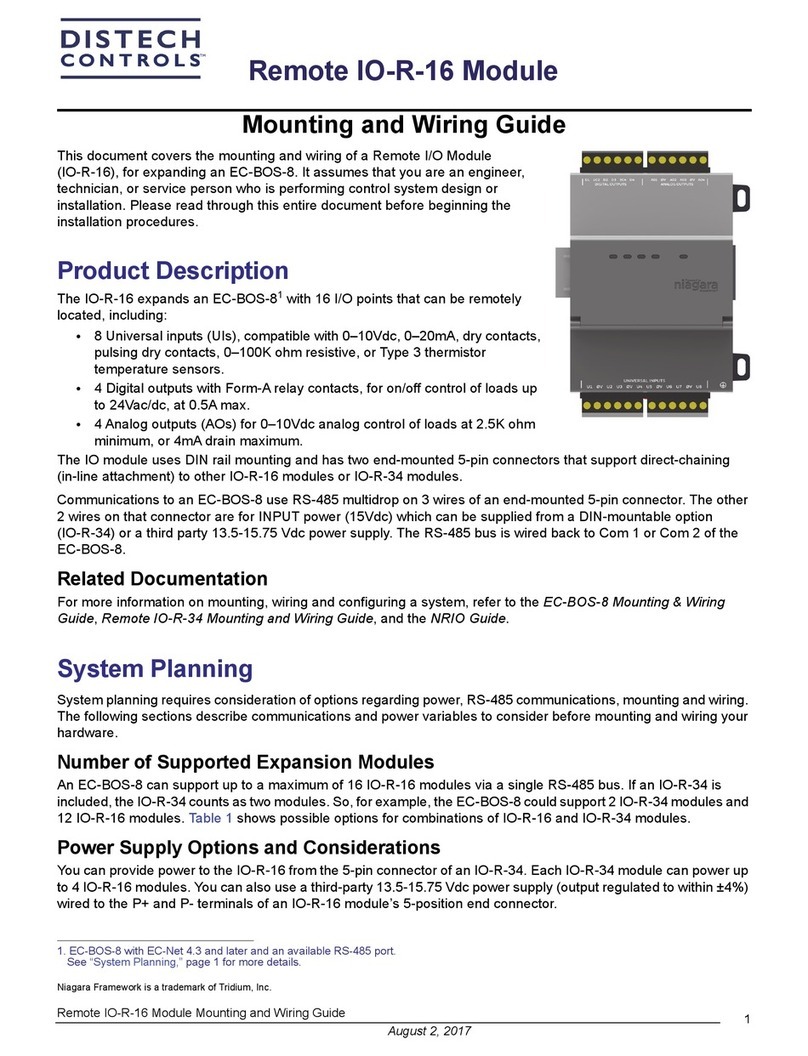
Distech Controls
Distech Controls IO-R-16 User manual
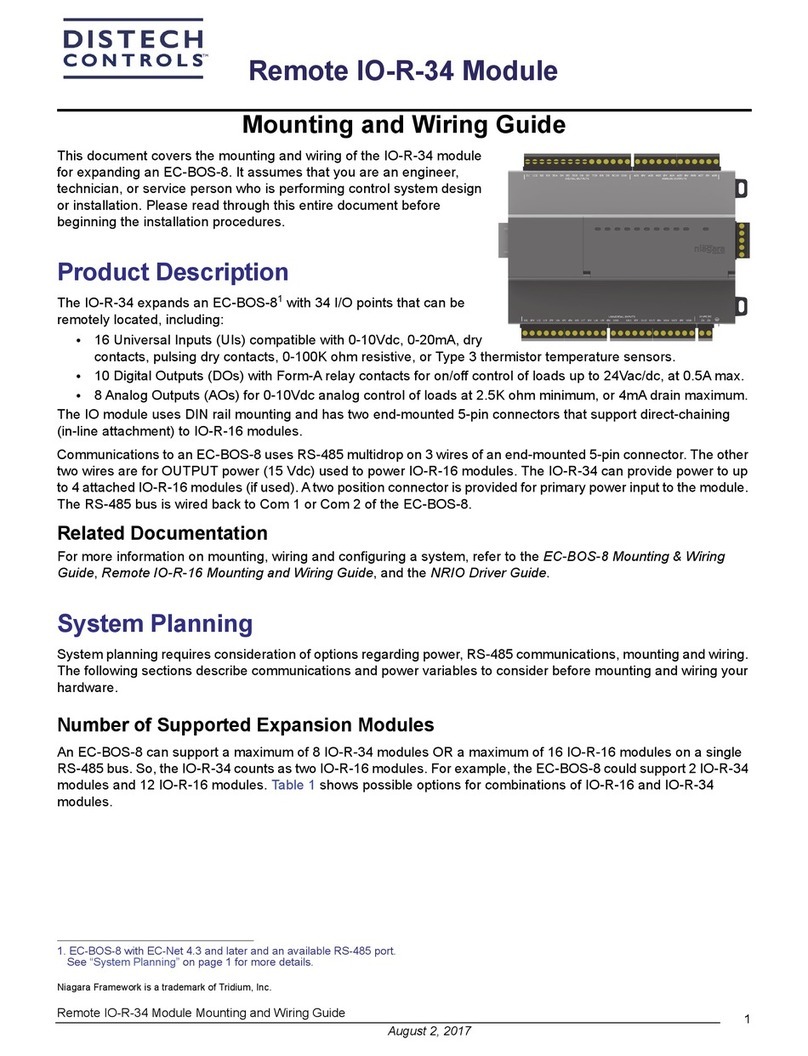
Distech Controls
Distech Controls IO-R-16 User manual
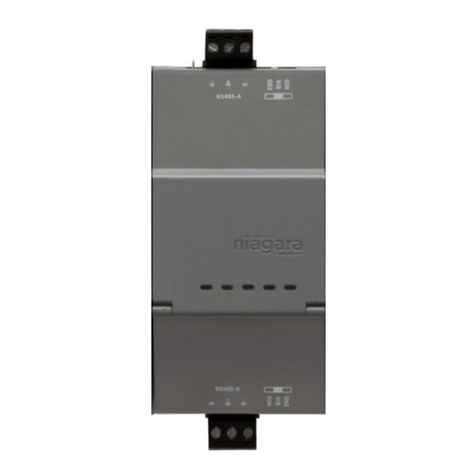
Distech Controls
Distech Controls RS485 UUKL User manual