DriSteem Vapor-logic 4 User manual

Vapor-logic®4
Humidifier Control System
Installation and
Operation Manual
Important: Read and save these instructions.


%3*45&&.7BQPSMPHJD*OTUBMMBUJPOBOE0QFSBUJPO.BOVBMt1BHFJ
Contents
Overview. . . . . . . . . . . . . . . . . . . . . . . . . . . . . . . . . 1–11
Vapor-logic4 capabilities. . . . . . . . . . . . . . . . . . . . . . . . . . . . . . . . . . . . 1
Humidificationsystemoverview ............................3
Operatingconditions ......................................3
Vapor-logic4 control board:
Three-dimensionalview................................4
Connectionpoints.....................................5
Usingthekeypad/display...................................6
UsingtheWebinterface....................................7
Pre-installationChecklistandinstructions ...................8
Installation . . . . . . . . . . . . . . . . . . . . . . . . . . . . . . 12–33
Step1:Fieldwiring .......................................12
Step2:Setup.............................................24
Step3:Startup ...........................................33
Operation . . . . . . . . . . . . . . . . . . . . . . . . . . . . . . . 34-85
Menusandscreens........................................34
Homescreen.........................................35
Statusscreen.........................................36
Diagnosticsscreen....................................39
Alarmsscreen........................................44
Setupscreen ......................................24,46
PIDtuning .............................................47
Waterlevelcontrol........................................51
Ducthighlimitoptions ...................................53
Temperaturesensor/transmitter............................54
Tankpreheating..........................................55
Aquastat .............................................55
Freezeprotection.........................................56
Fan-baseddispersionoperation ............................56
Sensoroffsets ............................................56
Automaticdrainsequence.................................57
Skimming .............................................58
Endofseasondraining....................................58
Serviceinterval...........................................59
Settingdateandtime .....................................59
Battery,nonvolatilememory...............................59
Security/password........................................60
Downloadinghistoricaldata...............................60
Databackupandrestore...................................60
Firmwareupdates ........................................61
Testoutputs,testrun......................................63
Modbus,BACnet,LonTalkinteroperability..................64
Multi-tankoperation......................................70
Troubleshooting........................................74
Replacementparts........................................86
Warranty .....................................Backcover
Appendices . . . . . . . . . . . . . A-1–A-4
Controlinputsignals..............A-1
Sensorplacement.................A-3
GTS model-specific default setup values
....................A-4

1BHFJJt%3*45&&.7BQPSMPHJD*OTUBMMBUJPOBOE0QFSBUJPO.BOVBM

%3*45&&.7BQPSMPHJD*OTUBMMBUJPOBOE0QFSBUJPO.BOVBMt1BHF
Overview
Vapor-logic4 capabilities
Accurate, responsive control
Vapor-logic®, DRI-STEEM’s humidification
system controller, has been setting the standard
for exceptional functionality and accurate RH
control since 1992. The fourth generation
controller, Vapor-logic4, retains the qualities
that established the Vapor-logic reputation,
plus offers several new capabilities, including:
Web interface, a standard feature, enables remote,
simultaneous, secure access from anywhere, at any time.
Modbus®, BACnet®, and LonTalk® allow interoperability with
multiple building automation systems (BAS).
Up-time optimizer keeps humidifiers operating through system
faults, as long as safety conditions are met, minimizing production
down-time.
USB port on Vapor-logic4 allows easy firmware updates, and data
backup and restore capability.
PID control provides accurate, responsive, and adjustable relative
humidity control.
Real-time clock allows time-stamped alarm and message tracking,
and accurate drain and flush scheduling.
Tank temperature sensor, mounted on the evaporating chamber,
provides over-temperature protection, freeze protection, and tank
preheating, allowing rapid response to a call for humidity.
Auxiliary temperature sensor/transmitter allows temperature
compensation control to prevent window condensation, or air
temperature monitoring, such as in a duct.
Programmable outputs allow remote signaling or device
activation, and are easily configured during the setup process.
Multiple-humidifier control allows staged control of up to 16
humidifiers with one controller.
More capabilities on the next page ▶

1BHFt%3*45&&.7BQPSMPHJD*OTUBMMBUJPOBOE0QFSBUJPO.BOVBM
Overview
Use the
Vapor-logic4
keypad/display or the standard Web
interface, shown here, to control your
humidification system.
Insert a USB
flash drive into
the Vapor-logic4
board’s USB port
to perform
firmware
updates, or
to back up and
restore data.
Vapor-logic4 capabilities
Enhanced diagnostics include:
rTe st outputs function, using the keypad/display or Web interface
to verify component operation
rTest humidifier function, by simulating demand to validate
performance
rData collection of RH, air temperature, water use, energy use,
alarms, and service messages
Factory commissioning of humidifier and control board
guarantees a reliable, fast installation, minimizing field installation
requirements.
Preconfigured but easily changed. Just go into the Setup menu to
change a factory setting if, for example, a control signal changes.

%3*45&&.7BQPSMPHJD*OTUBMMBUJPOBOE0QFSBUJPO.BOVBMt1BHF
Overview
Humidification system overview
Figure 3-1:
Typical humidification system layout (GTS humidifier shown)
Vapor-logic4
keypad/display
Humidifier
OM-1220
Dispersion assembly
Every humidification system with a Vapor-logic4 controller has a keypad/display connection and an Ethernet connection for
connecting to a Web interface on a computer. A GTS humidifier is shown here, with keypad/display mounted on the cabinet. Other
types of DRI-STEEM humidifiers can have the keypad/display contained within a control cabinet or mounted remotely.
Connect a computer directly to the
Vapor-logic4 board, or through a
network, to use the Web interface
Operating conditions
The Vapor-logic4 main board and keypad/display must be operated
and stored within the limits listed below. Exceeding these limits
can result in poor display performance and/or damage to the unit.
Main board
Operating temperature: 32 °F to 158 °F (0 °C to 70 °C)
Storage temperate: -40 °F to 185 °F (-40 °C to 85 °C)
Operating humidity range: <95% noncondensing
Keypad/display
Operating temperature: 32 °F to 158 °F (0 °C to 70 °C)
Storage temperate: -22 °F to 176 °F (-30 °C to 80 °C)
Operating humidity range: <95% noncondensing
CAUTION! The keypad/display is not rated for plenum operation.

1BHFt%3*45&&.7BQPSMPHJD*OTUBMMBUJPOBOE0QFSBUJPO.BOVBM
Overview
Vapor-logic4 control board
The Vapor-logic4 control board is
mounted to the subpanel located inside
the humidifier control compartment or
cabinet.
Note: Control board is shown here
mounted on a GTS humidifier subpanel.
Location of control board on subpanel
will vary with humidifier type.
Vapor-logic4 control board
The photo above shows key components of the Vapor-logic4 control board. See the illustration on the next page for more detail.
Figure 4-1:
Vapor-logic4 control board
Power to board connection
Factory connection points
for drain, steam valve, etc.
USB connection
Field connection points for
transmitters, power vent, etc.
Field connection terminal labels
have a white border.
Optional LonTalk
module location
Ethernet connection
for computer
Keypad/display
connection
BACnet or Modbus
connection
Factory connection points
for water level control,
gas valves, etc.
DRI-STEEM RS485
connection
Figure 4-2:
Control board mounted on GTS subpanel

%3*45&&.7BQPSMPHJD*OTUBMMBUJPOBOE0QFSBUJPO.BOVBMt1BHF
Overview
Vapor-logic4 board connections
P9:
Ethernet connection to
laptop computer or network
P10:
Vapor-logic4 keypad/
display connection
Figure 5-1:
Vapor-logic4 control board connections
P4:
Isw = Interlock switch (24VAC input)
TT = Tank temp sensor (RTD input)
= Ground for tank temp sensor
AI2 = Analog input (0-10VDC typical)
P3:
GV1 = Gas valve 1 (24VAC input)
BT1 = Blower tach 1 (pulse tach input)
LW = Low water (24VAC input)
FPsw = Flue pressure switch
(24VAC input)
Notes:
*CAUTION! Programmable dry contact (P12) is rated for 10 Amp maximum; programmable triac (P16) is rated for 4 Amp maximum. Exceeding these
maximum ratings can cause the triac or relay components on the Vapor-logic4 board to fail.
t 5SJBDBOEESZDPOUBDUGVODUJPOTBSFEFGJOFEVTJOHUIFLFZQBEEJTQMBZPS8FCJOUFSGBDFEVSJOHUIF4FUVQQSPDFTT
t 'PSNPTUBQQMJDBUJPOTGJFMEDPOOFDUJPOTBSFNBEFBUUFSNJOBMTPOUIFCPBSEUIBUBSFTVSSPVOEFEXJUIBXIJUFCPSEFS11
t 5IJTDPOUSPMCPBSEJTVTFEGPSTFWFSBMUZQFTPGIVNJEJGJFSTZTUFNTGPSFYBNQMFHBTIVNJEJGJFSTBTXFMMBTFMFDUSJDIVNJEJGJFST:PVSBQQMJDBUJPOXJMMOPUIBWF
connections at all terminals.
P1
P2
P3
P4
P5
P6
P7
P8
P9
P10
P11
P12 P13 P14 P15
P16
P17
P18
P19
SSR/BL Steam
Fill Drain
SDU
Triac PV/CA24VAC CAsw 24VAC PVsw
TS24VDC
DHL
24VDC 24VAC AFsw
N.O. C N.C.24VDC RH CT/I1CT/I2CT/I3CT/I4
Ethernet Display
GV1
AI2
Fieldbus 24VACTop Mid Low
BT1
LWFPsw
lsw
TT
GV2
BT2GV3
BT3
GV4
BT4
AI1
DSTEEM
SW1
Optional LonTalk®card location
P20
USB
P2:
Low = Low water probe
Mid = Mid water probe
Top = Top water probe
= Ground for water probe
P1:
24VAC = Power to board
= Ground for power return
P5:
GV2 = Gas valve 2 (24VAC input)
BT2 = Blower tach 2 (pulse tach input)
GV3 = Gas valve 3 (24VAC input)
BT3 = Blower tach 3 (pulse tach input)
P6:
GV4 = Gas valve 4 (24VAC input)
BT4 = Blower tach 4 (pulse tach input)
= Ground for AI
AI1 = Analog input (RTD input)
P7:
Fieldbus = Modbus or BACnet
(RS485)
P8:
DSTEEM = Multi-tank (RS485)
SW1:
RS485 termination for multi-tank
P19:
Steam = Steam or hot water valve
=Ground for blower and P16 triac
SSR/BL = SSR (electric systems)/or
Blower (gas systems)
P18: (all are triacs)
CT/I4= Contactor 4 (electric systems)/or
Ignition module 4 (gas systems)
CT/I3= Contactor 3/Ignition module 3
CT/I2= Contactor 2/Ignition module 2
P17: (all are triacs)
CT/I1= Contactor 1/Ignition module 1
Drain = Drain valve (24 VAC output)
Fill = Fill valve (24 VAC output)
P16: (all are triacs)
PV/CA = Power vent/combustion air
control signal (24 VAC output)
SDU = Space Distribution Unit
(24 VAC output)
Triac = Programmable output, 4AMP*
max. (Note: Connect ground at P19)
P15:
PVsw = Power vent switch (24VAC input)
24VAC = Power to power-vent switch
CAsw = Combust. air sw. (24VAC input)
24VAC = Power to combustion air switch
P14:
TS = Aux. temp. sensor or temp. comp.
sensor (4-20 mA input)
24VDC = Power to aux. temp. sensor or
temp. comp. sensor
P13:
AFsw = Airflow proving switch
(24VAC input)
24VAC = Power to airflow proving switch
DHL = Duct high limit switch/transm.
(4-20 mA input)
24VDC = Power to duct high limit switch
or transmitter
P12:
Programmable dry contact (10 AMP*max.)
N.C. = Normally closed
C = Common
N.O. = Normally open
P11:
= Ground for demand signal by others
RH = Space RH input (RH transmitter,
dew point transmitter, humidistat,
or demand signal by others input
(4-20 mA or 0-10VDC typical)
24VDC = Power to space RH sensor
LED-1 (power indicator)
LED-2

1BHFt%3*45&&.7BQPSMPHJD*OTUBMMBUJPOBOE0QFSBUJPO.BOVBM
Overview
Using the keypad/display
Figure 6-1:
Using the Vapor-logic4 keypad/display
Press Main softkey to
go to Main menu
Press Up
or Down
arrow to move
through menus
and screens Press
Enter
to select or
confirm
Alarm
label flashes
when there is a
system alarm
Fill icon
shows water level
status (see Page 35)
Typical Home screen
One of three softkeys;
functions vary by screen
Tank temperature
Tank status
Change set point from the Home
screen by pressing the Up or
Down arrow keys until set point is
highlighted (as shown here), press
Enter, press Up or Down arrow
keys to change value, press Enter
to confirm
Message
label becomes
highlighted when
there is a system
message
Change Mode from the Home
screen by pressing the Up or
Down arrow keys until Mode is
highlighted, press Enter, press Up
or Down arrow keys to change,
press Enter to confirm

%3*45&&.7BQPSMPHJD*OTUBMMBUJPOBOE0QFSBUJPO.BOVBMt1BHF
Overview
Using the Web interface
Figure 7-1:
Using the Vapor-logic4 Web interface (Setup screen shown)
Click on a tab label to move to another screen
Click here to
view alarms
Click here to
view messages
To change value:
Highlight value;
type in new value;
DMJDLPO"11-:
Click on CHANGE
to change value
Drag scroll bar
to view more of
the window
Click on label
to expand (+)
or contract (-)
menu item

1BHFt%3*45&&.7BQPSMPHJD*OTUBMMBUJPOBOE0QFSBUJPO.BOVBM
Installation
1SFJOTUBMMBUJPO$IFDLMJTU
See Figure 8-1 for field terminal block locations. Note that
field wiring connection locations on the Vapor-logic4 board are
surrounded with a white border.
See the figure on the next page for instructions on how to make
wiring connections.
See the wiring drawings and manuals that shipped with your
humidifier.
When making field connections, do not route low voltage wires
near the line voltage area in the humidifier control cabinet. Do
not route low voltage wires in the same conduit as line voltage
wires.
Humidistat, room/duct transmitter, temperature sensor, and
airflow proving switch wiring must be minimum 18-gauge
(1 mm2) plenum rated, shielded (screened), twisted pair wire
with a bare drain wire for grounding.
Connect the shield (screen) wire [with a length less than 2"
(50 mm)] to the shield (screen) ground terminal on the electric
subpanel. Do not ground the shield (screen) wire on the
humidistat or transmitter end.
More Checklist on the next page ▶
Figure 8-1:
Vapor-logic4 control board detail
Board detail showing white border
Terminals P-11
through P-16
have a white
border on the
Vapor-logic4
board. This
is where you
will make
most of your
field wiring
connections.
Full board
Field
connection
terminals have
labels printed
on a white
border.

%3*45&&.7BQPSMPHJD*OTUBMMBUJPOBOE0QFSBUJPO.BOVBMt1BHF
Installation
[
1SFJOTUBMMBUJPO$IFDLMJTUDPOUJOVFE
Figure 9-1:
Vapor-logic4 terminal block detail and connection instructions
Terminal block plug.
Make connections
when the plug is
attached to the
board, or remove for
easier access. Pull
plug straight up to
remove.
Tighten screw after
wire is inserted.
Maximum torque is
3 in-lb (0.34 N-m)
Remove insulation
from end of wire
and insert wire here.
P11
P12 P13 P14 P15
P16
SDU
Triac PV/CA24VAC CAsw 24VAC PVsw
TS24VDC
DHL
24VDC 24VAC AFsw
N.O. C N.C.24VDC RH
Vapor-logic4 board detail
(see also Figure 5-1)
If you have a remote-mounted control cabinet, the water
level control device, thermal trip, safety interlock, fill valve,
and drain valve wiring must be minimum 18-gauge (1 mm2)
stranded wire run in a conduit separate from power wires.
Do not use shielded (screened) cable for water level control
devices.
When the control cabinet is mounted remotely from the
humidifier, connect a ground wire from the machine ground
lug on the humidifier to the machine ground lug in the control
cabinet. The bonding machine ground wire should be the same
AWG (mm2) as the largest heater wire (electric humidifiers) or
sized per NEC or IEC 60364 requirements.

1BHFt%3*45&&.7BQPSMPHJD*OTUBMMBUJPOBOE0QFSBUJPO.BOVBM
Installation
The Vapor-logic4 board is designed to make installation very easy:
r 5FSNJOBMCMPDLTUIBUSFRVJSFGJFMEDPOOFDUJPOTBSFPVUMJOFEJO
white.
r 5FSNJOBMQMVHTDBOCFSFNPWFEUPBMMPXFBTZBDDFTTXIFO
inserting wires and tightening screws.
r 'PSNPTUBQQMJDBUJPOTIVNJEJGJFSTTIJQXJUIUIFDPOUSPM
board fully configured, with drain, fill, and other humidifier
components factory-wired to the board, and the keypad/display
attached to the humidifier and connected to the Vapor-logic4
board.
Installing Vapor-logic4 is a three-step process:
1. Connect field wiring from device to Vapor-logic4 board.
See instructions beginning on Page 12. Note that some
connections listed here may not apply to your system.
r $POUSPMJOQVU (one required)
– RH or dew point transmitter
– Demand signal by others (4-20 mA or 0-10 VDC typical)
– Room or duct humidistat
– Demand signal by BACnet, Modbus, or LonTalk
r -JNJUDPOUSPMT
– Airflow switch (duct or SDU)
– Duct high limit on-off switch or transmitter
– Temperature compensation transmitter (or auxiliary
temperature sensor connected to same terminal)
Continued on the next page ▶
Installation process

%3*45&&.7BQPSMPHJD*OTUBMMBUJPOBOE0QFSBUJPO.BOVBMt1BHF
Installation
r $PNNVOJDBUJPODPOOFDUJPOT
– Vapor-logic4 keypad
– Ethernet
– Modbus
– BACnet
– LonTalk
– Multiple-tank communication
r 1SPHSBNNBCMFUSJBDBOEPSSFMBZ
r "SFBUZQFPS4%6EJTQFSTJPOGBOT
r (54DPNCVTUJPOBJSTXJUDIBOEQPXFSWFOU
2. Complete the Setup process.
See instructions beginning on Page 24.
3. Start up humidifier(s).
See instructions beginning on Page 33.
Refer to the Pre-installation Checklist and drawings on the
previous pages, and then make the field wiring connections as
described on the following pages.
Installation process

1BHFt%3*45&&.7BQPSMPHJD*OTUBMMBUJPOBOE0QFSBUJPO.BOVBM
Installation
Field wiring:
Control input
Connect control input signal wiring by inserting wires into
Terminal P11 (labeled 24, RH, and ground) per the wiring
diagram on the next page. Tighten screws; maximum torque is
3 in-lb (0.34 N-m).
Allowed inputs at Terminal P11 include:
r 3)USBOTNJUUFSPSEFXQPJOUUSBOTNJUUFS
Transmitters provide a signal proportional to the RH or dew
point being measured. All transmitters provided by
DRI-STEEM are two-wire devices using a 4 to 20 mA signal.
r %FNBOETJHOBMCZPUIFST
Demand signals are sent to the Vapor-logic4 board from another
control system such as a building automation system. These
systems have their own RH or dew point transmitters, calculate
required humidifier output, and send a demand signal to the
humidifier to create steam at a percentage of that humidifier’s
capacity. Demand signals are typically 0-10 VDC or 4-20 mA,
but may also come from a DDC signal via Modbus, BACnet, or
LonTalk.
A humidistat also delivers a demand signal to the humidifier,
but it is not typically used with Vapor-logic4.
Humidistats provide either on-off control or modulating control.
DRI-STEEM humidistats are powered by a 24 VDC supply
provided by the Vapor-logic4 control board.
When using modulating control, the signal from a humidistat
directly controls the amount of output from the humidifier.
Notes:
r 4FFUIFXJSJOHEJBHSBNTPOUIFOFYUQBHF
r 'PSNPSFJOGPSNBUJPOBCPVUDPOUSPMJOQVUTJHOBMUZQFTBOE
operation, see the control input signals section in the Appendix.
r 4FFUIFJOUFSPQFSBCJMJUZTFDUJPOPGUIJTNBOVBMGPSNPSF
information about LonTalk, BACnet, or Modbus control input
signals.
Figure 12-1:
Terminal P11
Terminal P11:
24VDC = Power to space RH sensor
RH = Space RH input (RH transmitter, dew point
transmitter, humidistat, or demand signal by
others) (4-20 mA or 0-16 (typ. 0-10) VDC input
= Ground for demand signal by others
Terminal P11
Note:
If you do not know which control
components were ordered with your system,
contact DRI-STEEM or connect your keypad/
display to the Vapor-logic4 board per the
instructions on Page 17. Go to the Setup
menu per the instructions on Page 24 to
view system parameters that were factory
configured as ordered.

%3*45&&.7BQPSMPHJD*OTUBMMBUJPOBOE0QFSBUJPO.BOVBMt1BHF
Installation
Figure 13-1:
Vapor-logic4 control input wiring connections
Field wiring:
Control input
Signal by others
Transmitter
On-off RH humidistat
Key

1BHFt%3*45&&.7BQPSMPHJD*OTUBMMBUJPOBOE0QFSBUJPO.BOVBM
Installation
Field wiring:
Limit controls
Duct or SDU airflow proving switch
Connect wiring for a duct or Space Distribution Unit (SDU)
airflow proving switch by inserting wires into the terminal block
plug at P13 (labeled AFsw and 24) per the wiring diagram on
the next page. Tighten screws; maximum torque is 3 in-lb
(0.34 N-m). (An SDU is a cabinet fan dispersion assembly.)
See also the sensor placement section in the Appendix.
Duct high limit switch or transmitter
Connect wiring for a duct high limit switch or transmitter by
inserting wires into the terminal block plug at P13 (labeled DHL
and 24) per the wiring diagram on the previous page. Tighten
screws; maximum torque is 3 in-lb (0.34 N-m).
Note: The duct high limit sensor connected at this location can
be an on-off high limit switch, or it can be a duct high limit
transmitter with an adjustable high limit set point (4-20 mA input).
See also the sensor placement section in the Appendix.
Terminal P13
Figure 14-1:
Terminal P13
Terminal P13:
24VDC = Power to duct high limit switch or transmitter
DHL = Duct high limit switch/transm. (4-20 mA input)
24VAC = Power to airflow proving switch
AFsw = Airflow proving switch (24 VAC Input)

%3*45&&.7BQPSMPHJD*OTUBMMBUJPOBOE0QFSBUJPO.BOVBMt1BHF
Installation
Figure 15-1:
Vapor-logic4 limit controls wiring connections
Field wiring:
Limit controls
Airflow switch
Duct high limit (not used on SDU or Area-type)
Temperature compensation transmitter or auxiliary temperature sensor
Key
In a duct When using an SDU

1BHFt%3*45&&.7BQPSMPHJD*OTUBMMBUJPOBOE0QFSBUJPO.BOVBM
Installation
Temperature compensation transmitter
or auxiliary temperature sensor
Connect wiring for a temperature compensation transmitter or an
auxiliary temperature sensor by inserting wires into the terminal
block plug at P14 (labeled 24 and TS) per the wiring diagram
on the previous page. Tighten screws; maximum torque is 3 in-lb
(0.34 N-m).
Note: Only one device can be connected at P14. You will identify
the connected device during Step 2 of the installation process.
An auxiliary temperature sensor typically monitors duct or space
air temperature. Mount the auxiliary temperature sensor wherever
you want to monitor temperature.
A temperature compensation transmitter allows Vapor-logic4
to reduce humidifier output on cold days, reducing window
condensation. Mount the temperature compensation transmitter
on the inside of an outside-wall window.
To mount the temperature compensation sensor:
1. See Figure 16-2. Position the temperature compensation
sensor control box on a wall adjacent to a window frame facing
north or northeast.
2. Place the flat surface of the temperature sensor tip on the lower
corner of glass surface.
3. Temporarily hold the sensor tip in place with strips of masking
tape.
4. Apply a small amount of clear RTV silicone adhesive over and
around the sensor tip (making sure the sensor tip is in contact
with the window glass).
5. After adhesive cures, remove masking tape.
6. See the operation section of this manual for more information
about the temperature compensation sensor.
Field wiring:
Limit controls
Terminal P14
Figure 16-1:
Terminal P14
Terminal P14:
24VDC = Power to auxiliary temperature sensor or
temperature compensation sensor (transmitter)
TS = Auxiliary temperature sensor or temperature
compensation sensor (transmitter) (4-20 mA input)
Figure 16-2:
Temp. comp. transmitter installation
OM-337
Thermostat
control wires
Surface-mounted
thermostat
temperature
control box on
wall
Typical
sensor
cord
routing
Secure temperature
sensor tip to inside
surface of window
glass using clear RTV
silicone adhesive
Double-
pane
window
glass
Window frame
Other manuals for Vapor-logic 4
2
Table of contents
Other DriSteem Control System manuals
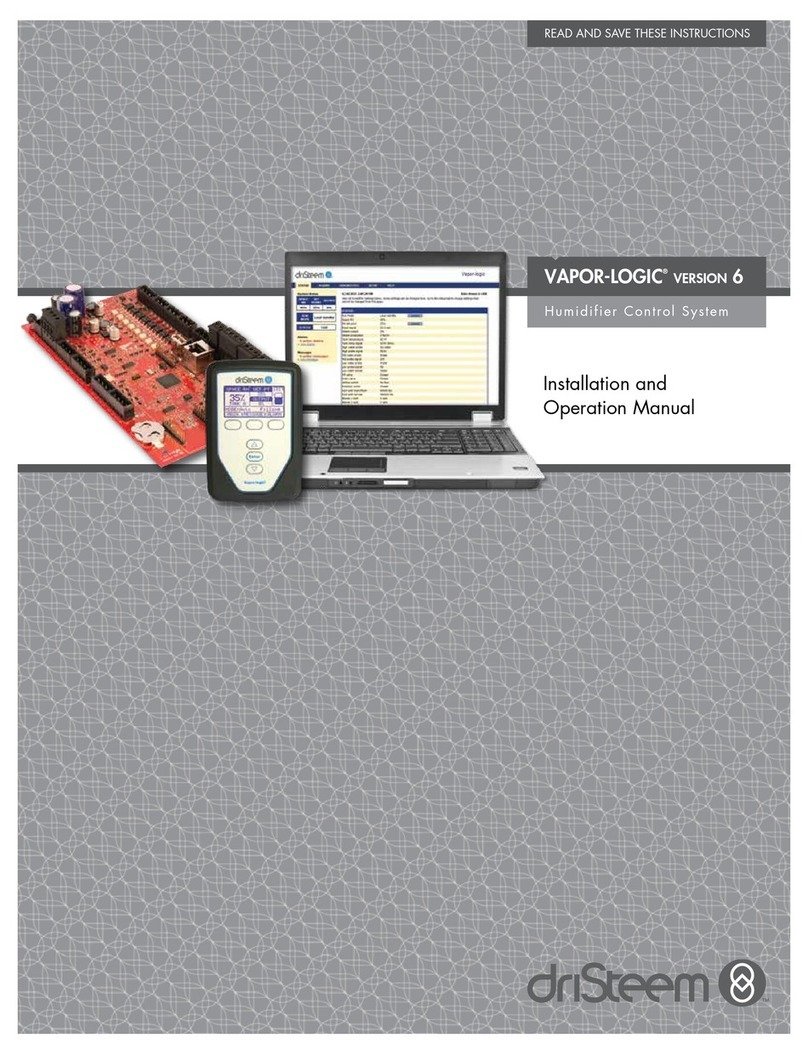
DriSteem
DriSteem Vapor-Logic User manual
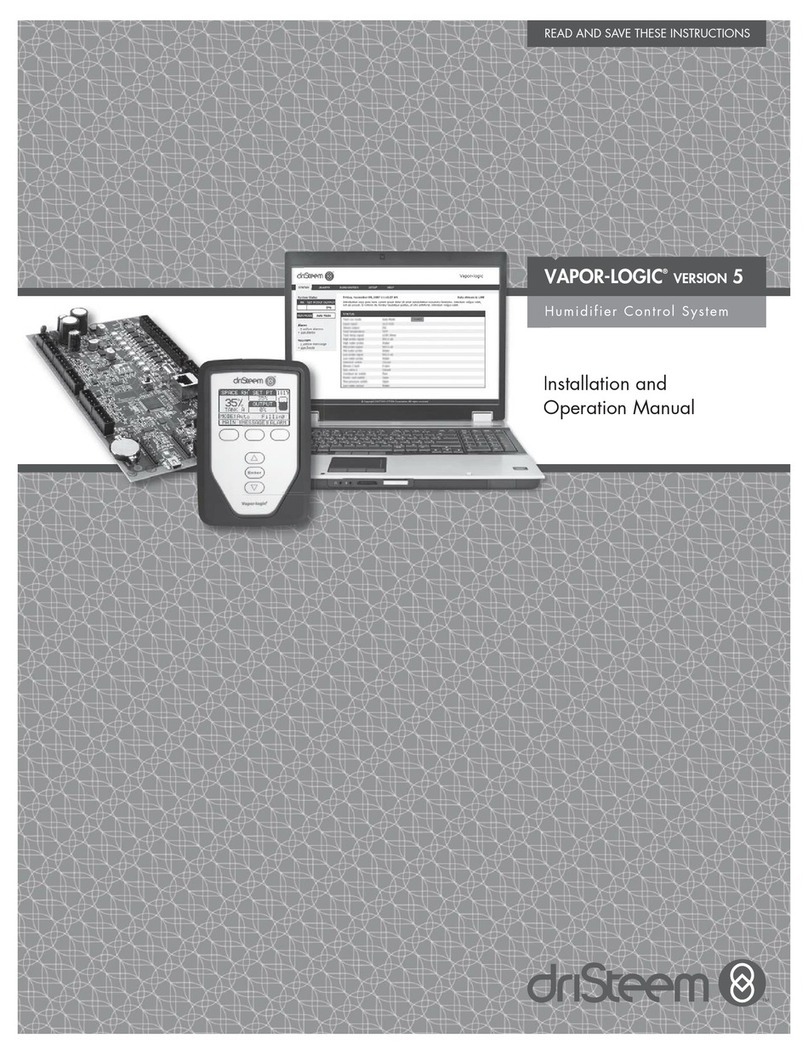
DriSteem
DriSteem Vapor-Logic User manual
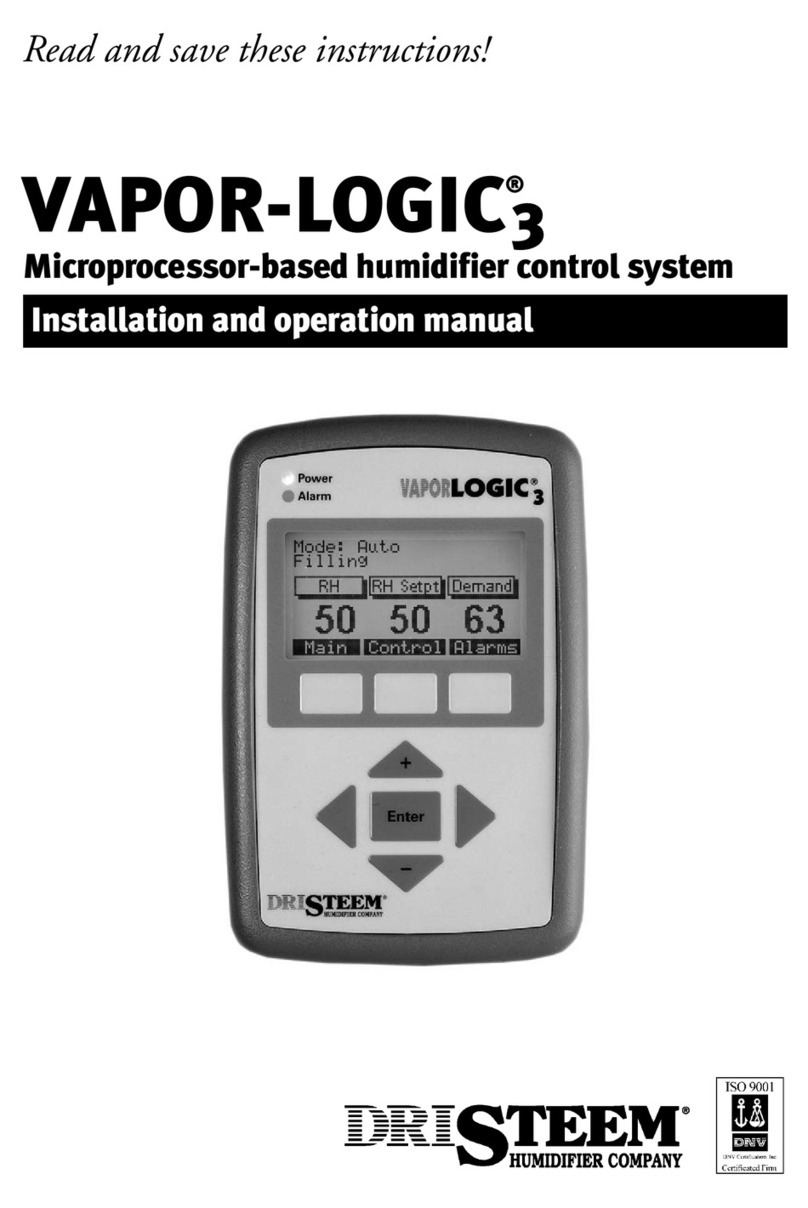
DriSteem
DriSteem Vapor-logic3 User manual
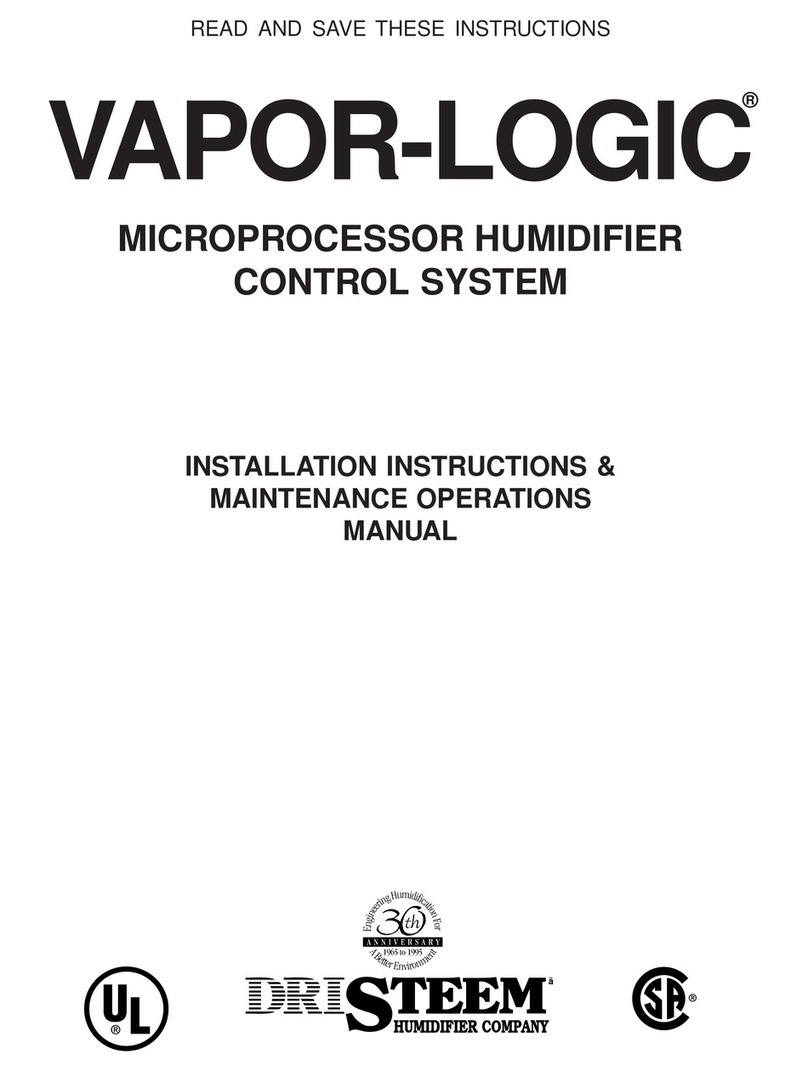
DriSteem
DriSteem Vapor-Logic User manual

DriSteem
DriSteem VAPOR-LOGIC 3 User manual
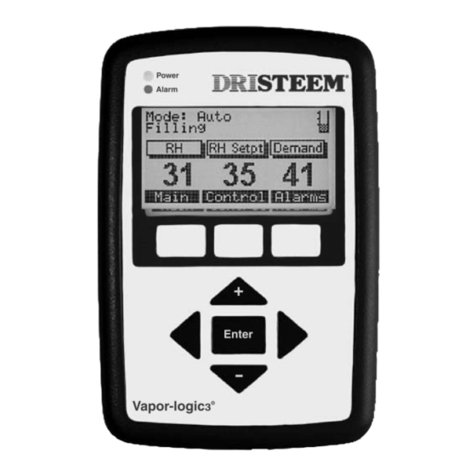
DriSteem
DriSteem Vapor-logic3 User manual
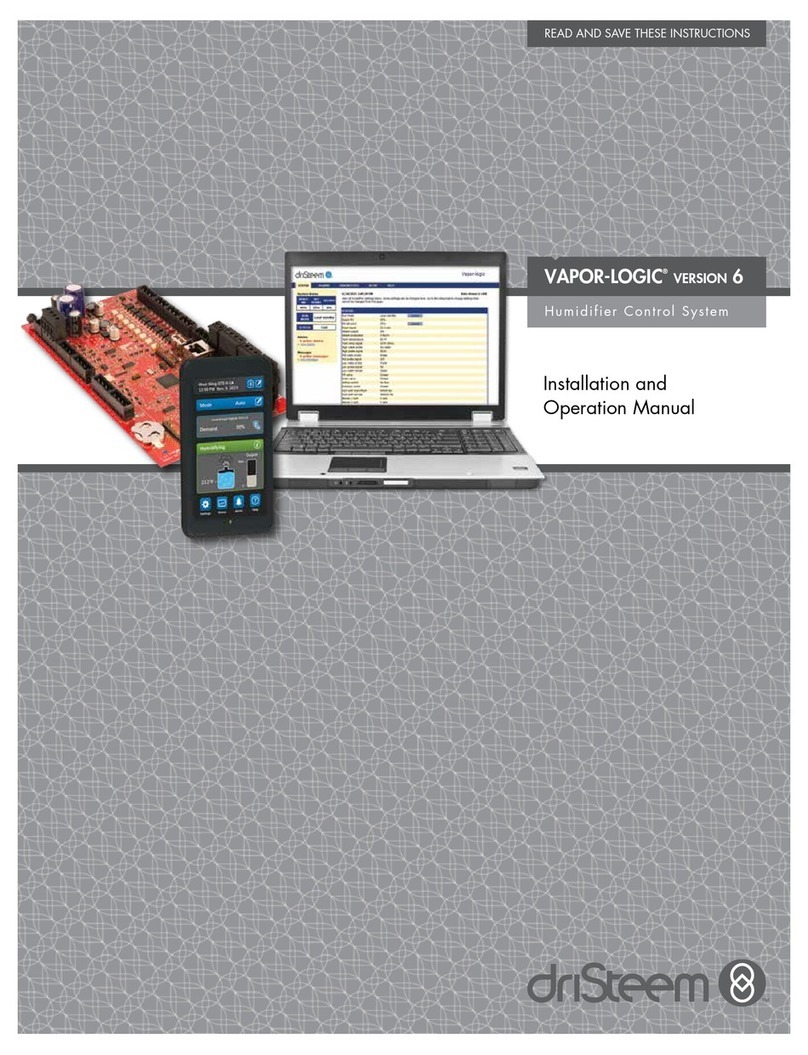
DriSteem
DriSteem Vapor-logic 6 User manual

DriSteem
DriSteem Vapor-Logic User manual