Dynatech SD-BOX Specification sheet

SISTEMA DE CONTROL DEL MOVIMIENTO
INCONTROLADO DE LA CABINA
UNINTENDED CAR MOVEMENT CONTROL SYSTEM
SYSTÈME DE CONTRÔLE DU MOUVEMENT
INCONTRÔLÉ DE LA CABINE
KONTROLLSYSTEM FÜR UNBEABSICHTIGTE
FAHRKORBBEWEGUNGEN
SD-BOX
INSTRUCCIONES DE USO Y MANUTENCIÓN/
INSTRUCTIONS FOR USE AND MAINTENANCE/
INSTRUCTIONS D’USAGE ET ENTRETIEN/
GEBRAUCHS- UND WARTUNGSANLEITUNG/


SD-BOX INSTRUCTION MANUAL, CODE: DYN 81.01.00
Date: 03/03/2020 Version 00
-2 -
CONTENTS
1. INTRODUCTION.............................................................................................................- 3 -
1.1.DESCRIPTION............................................................................................................- 3 -
2. RISKS AND SAFETY WARNINGS.................................................................................- 4 -
2.1.ELECTRICAL RISK.....................................................................................................- 4 -
3. USE.................................................................................................................................- 4 -
3.1.TYPE OF LIFTS...........................................................................................................- 4 -
3.2.EXCLUSION OF LIABILITY.........................................................................................- 4 -
4. MAIN FEATURES...........................................................................................................- 5 -
4.1.TECHNICAL FEATURES ............................................................................................- 5 -
4.2.ENVIRONMENTAL OPERATING CONDITIONS.........................................................- 5 -
4.3.GENERAL DESCRIPTION..........................................................................................- 6 -
4.4.OPERATION DESCRIPTION ......................................................................................- 8 -
4.5.DESCRIPTION OF FAULTS........................................................................................- 8 -
5. ASSEMBLY..................................................................................................................- 13 -
5.1.GENERAL .................................................................................................................- 13 -
5.2.ELECTRICAL CONNECTION....................................................................................- 13 -
5.3.ELECTRICAL DIAGRAMS.........................................................................................- 17 -
6. OPERATING REQUIREMENTS ...................................................................................- 20 -
6.1.FIRST START UP......................................................................................................- 20 -
6.2.SETTING THE COIL DE-ENERGISATION WAIT TIME WITH THE CAR AT LEVEL.- 20 -
6.3.SETTING THE FAILURE OUTPUT RELAY...............................................................- 20 -
6.4.AUTOCHECK TEST FUNCTION...............................................................................- 20 -
6.5.VERIFICATION TESTS.............................................................................................- 20 -
7. MAINTENANCE............................................................................................................- 26 -
7.1.GENERAL .................................................................................................................- 26 -
7.2.CLEANING................................................................................................................- 26 -
7.3.STORAGE CONDITIONS AND USEFUL LIFE..........................................................- 26 -
7.4.INSPECTIONS ..........................................................................................................- 26 -
7.5.SPARE PARTS..........................................................................................................- 26 -
8. OPTIONS......................................................................................................................- 27 -
8.1.BATTERIES...............................................................................................................- 27 -
Note: This manual displays partial information on the instructions for use and maintenance of this product. Please refer to the customer
area in Dynatech’s website in order to consult the full manual; http://customers.dynatech-elevation.com/

SD-BOX INSTRUCTION MANUAL, CODE: DYN 81.01.00
Date: 03/03/2020 Version 00
- 3 -
1. INTRODUCTION
1.1. DESCRIPTION
This equipment is to detect any type of unintended movement of the car (UCM) with the doors open.
If there is unintended movement, it opens the safety line output connected to the safety chain and
locks the overspeed governor by deenergizing the associated rotation coil and engaging the safety
gear. This corresponds to the following device in table A.1 in the standard EN 81-20: 2017.
•“Detection of unintended car movement with open doors”, with a minimum SIL of 2.
This device must be used in combination with an overspeed governor equipped with a governor
rotation locking coil. When energised, the coil allows the governor to turn and locks it when it is de-
energised. The coil must be designed to be powered continuously (100% duty cycle) at 24 VDC and
consume a current of 150-800 mA while energised.
This system compares the car door status with the unlocking zone at all times. If it detects that the
car has left the unlocking zone with open doors, it locks the overspeed governor.
Facing the appearance of an UCM, a competent technician is needed to make the installation
operational again. Once the problem causing the UCM is resolved, the "RESET" button on the SD-
BOX is pressed to re-establish the safety line and make the system operational again.
No intervention of the lift control is
needed to make the overspeed
governor coil act, as the system
described acts directly on it.
If a fault occurs in this contact or in the
coil that may pose a risk, a system
failure signal is activated to inform the
controller. When this signal is received
it prevents the lift from starting the
following travel.
If batteries are used as an auxiliary
power supply, an external charger
between the batteries and the SD-BOX must not be connected under any circumstances. The SD-
BOX is capable of charging the batteries itself.
Important
note
Do not connect a charger between the batteries and SD-BOX, it may
burn. For further details on how to connect the SD-BOX to your control
panel, please refer to “5.3 ELECTRICAL DIAGRAMS” in this manual.
Note: This manual displays partial information on the instructions for use and maintenance of this product. Please refer to the customer
area in Dynatech’s website in order to consult the full manual; http://customers.dynatech-elevation.com/

SD-BOX INSTRUCTION MANUAL, CODE: DYN 81.01.00
Date: 03/03/2020 Version 00
- 4 -
2. RISKS AND SAFETY WARNINGS
2.1. ELECTRICAL RISK
Electrical
risk Do not handle or open the box when its terminals are connected to
the power supply system.
3. USE
3.1. TYPE OF LIFTS
It can be used in the following lifts:
•With or without a machine room.
•With or without re-levelling.
•With or without pre-opening doors.
Important
note
Lifts with a pre-opening door system must be certified according to the
EN 81-20 standard, table A.1, section 5.12.1.4.a) Control of levelling,
re-levelling and preliminary controls or section 5.12.1.8.2 Device for
bridging the landing door and car contacts
3.2. EXCLUSION OF LIABILITY
DYNATECH DYNAMICS & TECHNOLOGY, SL will not be held responsible for damages caused
by not observing any of the points in this document.
Strictly prohibited:
Intervening on any component within the box.
Note: This manual displays partial information on the instructions for use and maintenance of this product. Please refer to the customer
area in Dynatech’s website in order to consult the full manual; http://customers.dynatech-elevation.com/

SD-BOX INSTRUCTION MANUAL, CODE: DYN 81.01.00
Date: 03/03/2020 Version 00
- 5 -
4. MAIN FEATURES
4.1. TECHNICAL FEATURES
Important note
The response time is the interval from the SD-BOX receiving the
signal to performing the relevant action. It does NOT include the
lift unlocking zone sensor detection time, the coil activation time
or the drift control sensor state change.
Important note
The batteries are rechargeable and are charged by the SD-BOX
itself. Under no circumstances should any extra charger be
connected between the batteries and the SD-BOX.
Important note The coil is overexcited to 30 VDC for a brief period of time to
prevent possible failures in the overspeed unlocking.
4.2. ENVIRONMENTAL OPERATING CONDITIONS
Temperature 5 - 40ºC
Humidity 15 - 85% without condensation
1The battery charger has been optimised for Ni-Cd batteries. If you use other types of batteries their life will
be reduced. Dynatech is not responsible for the use of batteries other than the Ni-Cd type.
21A protection fuse is required
3If the SD-BOX is placed in locations 2000-4000m above sea level, the maximum voltage at the door input is
limited to 160VAC/DC.
4If the SD-BOX is placed in locations 2000-4000m above sea level, the maximum voltage at the motor input
is limited to 160VAC/DC.
Power supply INPUT 24 VDC (1.5A max.) SELV/PELV
Rechargeable battery power INPUT 12 VDC, 1,5 Ah1
Power supply for the governor
unlocking electric coil OUTPUT 24 VDC; max 800 mA
Power supply for the governor
unlocking sensor OUTPUT 24 VDC
10mA max.
Max. safety line current OUTPUT 1A max.2
Control system response time - 30ms
Door signal3INPUT 24 - 230 VDC, 24 - 230 VAC (±10%)
50mA @ 24 V, 20mA @ 230 V
Motor signal4INPUT 24 - 230 VDC, 24 - 230 VAC (±10%)
50mA @ 24 V, 20mA @ 230 V
Level 1 signal INPUT 24 VDC
Level 2 signal INPUT 24 VDC
External manual rescue signal INPUT 24 VDC
External reset signal INPUT 24 VDC
Box IP protection index - SD-BOX: IP20
Note: This manual displays partial information on the instructions for use and maintenance of this product. Please refer to the customer
area in Dynatech’s website in order to consult the full manual; http://customers.dynatech-elevation.com/

SD-BOX INSTRUCTION MANUAL, CODE: DYN 81.01.00
Date: 03/03/2020 Version 00
- 6 -
4.3. GENERAL DESCRIPTION
The control button functions and the general information supplied by the LEDs and the display are
described below.
Control buttons
•RESET5:Enables the system after the following: the first start-up, an UCM, a bypass action,
manual locking of the overspeed governor (MANUAL TRIPPING) or a fault/error.
•MANUAL RESCUE/BYPASS: This button must be held down for more than 3 seconds to be
activated. It can be used in maintenance work and for a manual rescue if the lift has no power.
A periodic warning beep will sound while the bypass is activated. The bypass function can be
turned off by pressing the “MANUAL RESCUE/BYPASS” button again or by pressing the
“RESET” button. The maximum duration of this mode when the SD-BOX is powered by batteries
is 10 minutes, whereupon it automatically returns to a resting state. As many rescues as
necessary can be performed by pressing the button again as long as the battery has enough
charge. The maximum duration of this mode with an external power supply is not established.
MAX. 10 minutes
The maximum duration of this mode when the SD-BOX is
powered by batteries is 10 minutes, whereupon the SD-BOX
automatically returns to a resting state. To warn of the
automatic disconnection, the beep frequency increases
during the final minute.
Application of bypass
during the process of
disengaging the safety
gear
After an UCM or a manual lock (MANUAL TRIPPING), the
bypass must be applied to prevent the overspeed governor
from locking in the opposite direction when the car is moved
to disengage the safety gear.
•MANUAL TRIPPING: This is to lock the governor during maintenance work. It is used in
combination with the “MODE” button and with an indication on the display to prevent the
governor from being locked accidentally or by mistake.
•MODE6: This enables the use of the manual lock (MANUAL TRIPPING), the setting of the de-
energisation wait time at floor level and the output relay FAILURE.
5The RESET function will not work when the “MOTOR” input is activated.
6If the “MOTOR” input is activated, no configuration can be made.
Note: This manual displays partial information on the instructions for use and maintenance of this product. Please refer to the customer
area in Dynatech’s website in order to consult the full manual; http://customers.dynatech-elevation.com/

SD-BOX INSTRUCTION MANUAL, CODE: DYN 81.01.00
Date: 03/03/2020 Version 00
- 7 -
The following steps are needed to activate the MANUAL TRIPPING mode:
oPress the “MODE” and “MANUAL TRIPPING” buttons simultaneously for 3 seconds until the
number 55 appears on the display.
oPress (▲) 20 times until the number 75 appears. Press “MODE” and the MANUAL
TRIPPING LED lights up indicating this option is activated.
oWhen the “MANUAL TRIPPING” button is pressed, the overspeed governor is locked.
oWhen the “MANUAL TRIPPING” button is released, the overspeed governor is unlocked.
oTo disable the MANUAL TRIPPING mode and return to normal status, press the “MODE”
and “MANUAL TRIPPING” buttons at the same time. It can also be disabled by pressing the
“RESET” button.
To configure the de-energisation wait time at the floor level, follow the instructions in section “6.2
SETTING THE COIL DE-ENERGISATION WAIT TIME WITH THE CAR AT LEVEL”.
To configure the FAILURE output relay, follow the instructions in section “6.3 SETTING THE
FAILURE OUTPUT RELAY”.
LED indicators
•POWER: Flashes when the SD-BOX is receiving power externally or from the batteries.
•STAND-BY: When the SD-BOX is in low consumption mode with the display and LEDs off.
•BATTERY CHARGING: Indicates the battery charging status: “Off” if it is charged, “on” if it
is charging and flashing when checking the battery status.
•BATTERY FAILURE: “Flasing” indicates a battery fault (damaged and impossible to charge)
or battery disconnection.
•FAILURE CONFIG.: Indicates the FAILURE output relay setting: “Off” indicates the SD-BOX
will act on the relay if it detects any fault or error, and “on” indicates the SD-BOX will act on
the relay according to the coil status. FAILURE output is a non-safety related signal.
•MANUAL RESCUE/BY PASS: “On” indicates the coil is being powered manually by
performing a rescue manoeuvre.
•MANUAL TRIPPING: “On” indicates the manual locking function is active and will manually
lock the overspeed governor when the “MANUAL TRIPPING” button is pressed.
•UCM DETECTED: “Flasing” indicates the system has detected unintended movement of the
car (UCM). The safety line contact will open and the fault “F2” will appear on the display.
•DOORS: “On” indicates the door series is closed. If it is flashing, there is a discrepancy in
the internal DOORS1/DOORS2 signals.
•MOTOR: “On” indicates the motor is running.
•LEVEL1: “On” indicates the car is at floor level.
•LEVEL2: “On” indicates the car is at floor level.
•INDUCTOR/μSWITCH: “On” indicates the unlocking sensor detects the overspeed governor
is unlocked.
Note: This manual displays partial information on the instructions for use and maintenance of this product. Please refer to the customer
area in Dynatech’s website in order to consult the full manual; http://customers.dynatech-elevation.com/

SD-BOX INSTRUCTION MANUAL, CODE: DYN 81.01.00
Date: 03/03/2020 Version 00
- 8 -
•COIL STATUS: “On” indicates the governor coil is powered and the governor is unlocked.
DISPLAY:The figures appearing on the display indicate the following:
•F1 – F9: Lift faults. See “4.5 DESCRIPTION OF FAULTS” for more detailed information on
each.
•A1: The batteries are not connected or have discharged.
•A2: Failure in the external power supply.
•E1 – E9: Internal SD-BOX errors. See “4.5 DESCRIPTION OF FAULTS” for more detailed
information on each.
•63: Access to the coil de-energisation time setting. For more information see “6.2 SETTING
THE COIL DE-ENERGISATION WAIT TIME WITH THE CAR AT LEVEL”.
•75: The manual lock function (MANUAL TRIPPING) and “MANUAL TRIPPING” button are
enabled, when the button is pressed with the car in movement the overspeed governor will
be locked and safety gear engaged on further movement of the car.
•81: Access to the FAILURE output relay setting. For further information, please see “6.3
SETTING THE FAILURE OUTPUT RELAY”.
4.4. OPERATION DESCRIPTION
Depending on the input signals the controller receives, the SD-BOX is able to detect unintended car
movement and lock the overspeed governor only when this happens; and not during normal stops.
The basic operation is as follows:
The following input signals are needed from the lift:
•Doors closed (DOORS).
•2 independent unlocking zone sensors (LEVEL1 and LEVEL2).
•Motor contactor (MOTOR).
When the car reaches a floor, the level inputs are activated and the coil remains energised keeping
the overspeed governor unlocked. The doors open, the closed doors signal is lost and, if UCM
occurs, the level inputs will be lost. At that moment, the safety line contact opens, the coil de-
energises and the overspeed governor is locked. If UCM does not occur, the doors will be closed
and a travel made.
4.5. DESCRIPTION OF FAULTS
Once an error has occurred, the SD-BOX will inform the user through the LEDs and the display
showing the status in which the error occurred and will remain in safe mode until it is restarted.
A list of possible failures that can occur during the operation of the SD-BOX, with their possible
causes and solutions, appear in the following table.
FAULT ACTION LEDs ACTION CAUSE
F0
DOORS signal
loss while
traveling
LED COIL ON
LED INDUCTOR ON
LED MOTOR ON
SAFETY LINE
OPENS Check the DOORS
connection
Note: This manual displays partial information on the instructions for use and maintenance of this product. Please refer to the customer
area in Dynatech’s website in order to consult the full manual; http://customers.dynatech-elevation.com/

SD-BOX INSTRUCTION MANUAL, CODE: DYN 81.01.00
Date: 03/03/2020 Version 00
- 9 -
7Check the coil connection on terminals 42-43 by loosening them and checking the continuity of the circuit
from the SD-Box to the overspeed governor coil (for Dynatech parking systems, the resistance between
terminals must be 42-52 Ω).
LED DOORS
CLOSED OFF
COIL DE-
ENERGISES
F1
Incorrect
detection of the
coil at start of
travel
LED COIL ON
LED INDUCTOR OFF
LED MOTOR ON
LED DOORS
CLOSED ON
SAFETY LINE
OPENS AFTER
7 MORE
ATTEMPTS
COIL DE-
ENERGISES IF
THERE IS AN
ERROR
Check the drift system
control sensor works
properly
The coil cannot
release the
overspeed
governor at start
of travel
LED COIL ON
LED INDUCTOR OFF
LED MOTOR OFF
LED DOORS
CLOSED ON
Check the coil terminals
output voltage (40-41)
is 20-30 VDC.
F2 UCM detected LED UCM ON
SAFETY LINE
OPENS
COIL DE-
ENERGISES
Notify a competent
person to check the
system
F3
Coil
disconnection or
failure at start of
travel
LED COIL OFF
LED INDUCTOR OFF
LED MOTOR OFF
LED DOORS
CLOSED ON
SAFETY LINE
OPENS
COIL DE-
ENERGISES
Check the coil
connection7
Coil
disconnection or
failure during
travel
LED COIL OFF
LED INDUCTOR OFF
LED MOTOR ON
LED DOORS
CLOSED ON
SAFETY LINE
OPENS
COIL DE-
ENERGISES
Check the coil
connection7
F4
Incorrect
detection of coil
when going to
rest situation
LED COIL OFF
LED INDUCTOR ON
LED MOTOR OFF
LED DOORS
CLOSED ON/OFF
SAFETY LINE
OPENS
COIL DE-
ENERGISES
Check there is no
component preventing
the fall of the parking
system cam. Check the
correct functioning of
the drift system control
sensor
Incorrect
detection of coil
LED COIL OFF
LED INDUCTOR ON
LED MOTOR OFF
LED DOORS
CLOSED ON/OFF
SAFETY LINE
OPENS
COIL DE-
ENERGISES
Check the correct
functioning of the drift
system control sensor
The coil is not
able to lock the
overspeed
governor after
LED COIL OFF
LED INDUCTOR ON
LED MOTOR OFF
SAFETY LINE
OPENS
Check there is no
component preventing
the fall of the parking
system cam. Check the
Note: This manual displays partial information on the instructions for use and maintenance of this product. Please refer to the customer
area in Dynatech’s website in order to consult the full manual; http://customers.dynatech-elevation.com/

SD-BOX INSTRUCTION MANUAL, CODE: DYN 81.01.00
Date: 03/03/2020 Version 00
- 10 -
deactivating
MANUAL
RESCUE
LED DOORS
CLOSED ON/OFF
LED MANUAL
RESCUE OFF
COIL DE-
ENERGISES
correct functioning of
the drift system control
sensor
F5
The coil cannot
release the
overspeed
governor after
pressing
MANUAL
RESCUE
LED COIL ON
LED INDUCTOR OFF
LED MOTOR OFF
LED DOORS
CLOSED ON/OFF
LED MANUAL
RESCUE ON
SAFETY LINE
CLOSED
COIL
ENERGIZED
Check there is no
component preventing
the fall of the parking
system cam. Check the
correct functioning of
the drift system control
sensor
F6
The coil cannot
release the
overspeed
governor after
pressing
MANUAL
RESCUE after
an engagement
LED COIL ON
LED INDUCTOR OFF
LED MANUAL
RESCUE ON
SAFETY LINE
CLOSED
COIL
ENERGIZED
Disengage the safety
gear. Push the
“RESET” button and
make a call. If the
failure persists, act in
the same way as for a
“F1” fault if the
overspeed governor is
not released, or as fault
“F4” if the overspeed
governor does not lock.
F7
The coil cannot
release the
overspeed
governor after
pressing the
“MANUAL
TRIPPING”
button
LED COIL ON
LED INDUCTOR OFF
LED MOTOR OFF
LED DOORS
CLOSED ON
LED MANUAL
TRIPPING ON
SAFETY LINE
OPENS
COIL
ENERGISES
Disengage the safety
gear. Push the
“RESET” button and
make a call. If the
failure persists, act in
the same way as for a
“F1” fault if the
overspeed governor is
not released, or as fault
“F4” if the overspeed
governor does not lock.
F8
The coil cannot
lock the
overspeed
governor after
pressing the
“MANUAL
TRIPPING”
button
LED COIL OFF
LED INDUCTOR ON
LED MOTOR ON
LED DOORS
CLOSED ON
LED MANUAL
TRIPPING ON
SAFETY LINE
OPENS
COIL
ENERGISES
Check there is no
component preventing
the fall of the parking
system cam. Check the
correct functioning of
the drift system control
sensor
F9 Short circuit at
the coil output LED COIL OFF
LED INDUCTOR OFF
SAFETY LINE
OPENS
COIL DE-
ENERGISES
Check the coil
connection7
A1
Batteries are
not connected
or have
discharged
NO ACTION Proceed as verification
test 3, “Checking the
battery charge”.
Note: This manual displays partial information on the instructions for use and maintenance of this product. Please refer to the customer
area in Dynatech’s website in order to consult the full manual; http://customers.dynatech-elevation.com/

SD-BOX INSTRUCTION MANUAL, CODE: DYN 81.01.00
Date: 03/03/2020 Version 00
- 11 -
A2 External power
supply failure LED BATTERY
FAILURE ON NO ACTION
Check the D-Box power
supply is properly
connected and the
voltage at its power
terminals (32-33) is 24
VDC
E0 Internal signals
short-circuited -
SAFETY LINE
OPENS
COIL DE-
ENERGISES
Contact Dynatech
E1
Reading
discrepancy in
LEVEL1 and
LEVEL2 signals
LED LEVEL1 and
LEVEL2 do not
match
SAFETY LINE
OPENS
COIL DE-
ENERGISES
Check the LEVEL1 and
LEVEL2 connections
(terminals 22-23 and
24-25) and voltages (24
VDC) match. If the
problem persists,
contact Dynatech.
E2
Reading
discrepancy in
internal
DOORS1 and
DOORS2
signals
LED DOORS flashes
SAFETY LINE
OPENS
COIL DE-
ENERGISES
Check the DOORS
connections (terminals
49-50) and voltages
(24/230 VAC/DC) are
acceptable. If the
problem persists,
contact Dynatech.
E3 Lift SEPIC
operation error -
SAFETY LINE
OPENS
COIL DE-
ENERGISES
Contact Dynatech
E4 PWM control
operation error -
SAFETY LINE
OPENS
COIL DE-
ENERGISES
Contact Dynatech
E5 SAFETY LINE
output relay 1
operation error -
SAFETY LINE
OPENS
COIL DE-
ENERGISES
Contact Dynatech
E6 SAFETY LINE
output relay 2
operation error -
SAFETY LINE
OPENS
COIL DE-
ENERGISES
Contact Dynatech
E7
Safety
processes
synchronisation
error
-
SAFETY LINE
OPENS
COIL DE-
ENERGISES
Contact Dynatech
E8 Flash memory
read/write error - SAFETY LINE
OPENS Contact Dynatech
Note: This manual displays partial information on the instructions for use and maintenance of this product. Please refer to the customer
area in Dynatech’s website in order to consult the full manual; http://customers.dynatech-elevation.com/

SD-BOX INSTRUCTION MANUAL, CODE: DYN 81.01.00
Date: 03/03/2020 Version 00
- 12 -
COIL DE-
ENERGISES
E9 RAM read/write
error -
SAFETY LINE
OPENS
COIL DE-
ENERGISES
Contact Dynatech
L0 EEPROM
read/write error -
SAFETY LINE
OPENS
COIL DE-
ENERGISES
Contact Dynatech
Note: This manual displays partial information on the instructions for use and maintenance of this product. Please refer to the customer
area in Dynatech’s website in order to consult the full manual; http://customers.dynatech-elevation.com/

SD-BOX INSTRUCTION MANUAL, CODE: DYN 81.01.00
Date: 03/03/2020 Version 00
- 13 -
5. ASSEMBLY
5.1. GENERAL
The assembly electrical connection and commissioning must be performed by properly trained,
specialist personnel.
The various connection terminals operate at different voltages, e.g. some are at 24 VDC and others
at 230 VDC/AC. If the 230V is connected to a 24V input, the SD-BOX will be destroyed.
Protect the box and connection terminals from dust and humidity.
The system is contained inside an electrical box for easy placement. On its lower side, it has some
tabs so it can be easily installed on a 35mm DIN rail. In its final position, the box must be properly
secured.
Before assembly, it must be verified that the box has not been damaged during transport.
The box dimensions are:
•Length: 157 mm
•Width: 90 mm
•Height: 71 mm
5.2. ELECTRICAL CONNECTION
Before the electrical connection, check there is no safety risk for the installer.
Before connecting the batteries, check the voltage at the battery’s terminals is
11-13 V.
Having an UCM control can affect the lift maintenance work.
During lift maintenance procedures, it must be taken into account that the UCM
control is connected. The operator must consider that any action to open the
doors from outside floor level will result in the safety line opening and the
overspeed governor being locked.
Note: This manual displays partial information on the instructions for use and maintenance of this product. Please refer to the customer
area in Dynatech’s website in order to consult the full manual; http://customers.dynatech-elevation.com/

SD-BOX INSTRUCTION MANUAL, CODE: DYN 81.01.00
Date: 03/03/2020 Version 00
- 14 -
Diagram 1: Main electrical connections
EXTERNAL MANUAL RESCUE
LEVEL 2
LEVEL 1
EXTERNAL RESET
24V
24V
24V
FAILURE
NC
1 2 3 4 5 6 7 8 9 10 11 12 13 14 15 16 17 18 19 20 21 22 23 24 25 26 27
28 29 30 31 32 33 34 35 36 37 38 39 40 41 42 43 44 45 46 47 48 49 50 51 52 53 54
NO
CM
SAFETY LINE
SAFETY LINE
EXTERNAL RESET
LEVEL 1
LEVEL 2
EXTERNAL MANUAL RESCUE
0V
0V
0V
0V
24V
0V
24V
POWER
BATTERY
+
-
IND. SENSOR
-
+
IN
COIL
0V
0V
24/230
AC/DC
24/230
AC/DC
DOORS
DOORS
MOTOR
MOTOR
POWER
BATTERY
Note: This manual displays partial information on the instructions for use and maintenance of this product. Please refer to the customer
area in Dynatech’s website in order to consult the full manual; http://customers.dynatech-elevation.com/

SD-BOX INSTRUCTION MANUAL, CODE: DYN 81.01.00
Date: 03/03/2020 Version 00
- 15 -
Electrical power supply
•The electrical power of the system, terminals 32-33, must be connected to a 24 VDC
SELV/PELV source.
•Terminals 34-35 are used for battery power, when the main power fails, to prevent the safety
gear from engaging. These same terminals are also used for charging the battery, so no
intermediate charger need be connected.
External battery
charger Do not connect a charger between the batteries and the SD-
BOX, as it may burn.
Necessary input signals from the lift
•DOORS, terminals 49-50, to indicate the doors are closed. The car door must be connected
in series with the floor doors. The input allows the use voltages from 24 to 230 VDC/AC.
•MOTOR, terminals 53-54, to indicate the motor is running. A lack of voltage means the
machine is not working. The input allows the use voltages from 24 to 230 VDC/AC.
•Unlocking zone (LEVEL1/LEVEL2), terminals 22-23 LEVEL1 and 24-25 LEVEL2. This
indicates the car is at floor level. The input must be connected to a 24 VDC signal.
Floor level
information Two unlocking zone sensors must be used: one for LEVEL1 and
another for LEVEL2.
Optional installation inputs
In addition to the physical MANUAL RESCUE and RESET buttons, the SD-BOX can be used for
the optional inputs discussed below for a manual rescue or remote reset from the control panel or
another controller.
•Remote manual rescue signal (EXTERNAL MANUAL RESCUE), terminals 26-27, to
implement a manual rescue or bypass command. If there is a voltage applied for more than
3 seconds, the overspeed governor will be unlocked. The input requires a 24 VDC signal,
whose use is optional. The bypass can be performed using the “MANUAL
RESCUE/BYPASS” button on the SD-BOX.
•Remote reset signal (EXTERNAL RESET)8, terminals 20-21, to implement the reset
command from the control panel. If there is a voltage applied, the reset function must be
performed. The input requires a 24 VDC signal, whose use is optional. The bypass can be
performed using the “RESET” button on the SD-BOX.
8The RESET function will not work when the “MOTOR” input is activated
Note: This manual displays partial information on the instructions for use and maintenance of this product. Please refer to the customer
area in Dynatech’s website in order to consult the full manual; http://customers.dynatech-elevation.com/

SD-BOX INSTRUCTION MANUAL, CODE: DYN 81.01.00
Date: 03/03/2020 Version 00
- 16 -
Outputs
•The output connected into the SAFETY chain, terminals 4 and 6, is part of two relays in
series which open when an UCM or fault is detected as described above, causing the safety
line to open. If there is no UCM or failure, these contacts will remain closed. If there is a
power cut, the contacts open, thus opening the safety line. If the coil has a fault, the contacts
will also open, once the motor input is deactivated, so the car can complete the travel being
taken when the fault occurs. If the motor is deactivated, it opens immediately if a fault is
found in the coil.
•SYSTEM FAILURE information, terminals 1-2-3, is a non-safety related signal with a
configurable output to inform the control panel of 2 different options:
A. The relay will change status when one ofthe aforementioned faults/errors isdetected
in “4.5 DESCRIPTION OF FAULTS”. The normally open (NO) 1-3 FAILURE relay
contact will be closed and the normally closed contact (NC) 2-3 will open.
B. The relay will change status according to the coil status: when this is powered, the
normally open (NO) 1-3 FAILURE relay contact will be closed and the normally
closed contact (NC) 2-3 will open.
Overspeed governor connection components
•The action of the coil releases the overspeed governor and allows its free rotation. If the coil
is not powered, a spring activated system locks the overspeed governor. If there is no power
reaching the coil with the car in motion, the overspeed governor will lock which could engage
the safety gear. This is why batteries must be used to prevent unwanted engagement of the
safety gear if there is a power failure in the lift.
•An inductive sensor or μSwitch (IND SENSOR), terminal 38 (inductive sensor supply 0 VDC),
terminal 49 (detection), terminal 40 (inductive sensor power supply 24 VDC). The inductive
sensor/μSwitch is a control sensor on the overspeed governor to check the proper operation
of the coil. This signal indicates the overspeed governor is unlocked; the absence of voltage
indicates the overspeed governor is locked.
Important note The batteries must be connected for proper operation.
Note: This manual displays partial information on the instructions for use and maintenance of this product. Please refer to the customer
area in Dynatech’s website in order to consult the full manual; http://customers.dynatech-elevation.com/

SD-BOX INSTRUCTION MANUAL, CODE: DYN 81.01.00
Date: 03/03/2020 Version 00
- 17 -
5.3. ELECTRICAL DIAGRAMS
1 OUTPUT. Normally open (NO) for fault indicator/coil status. This contact is closed if there is
a fault or the coil is activated.
2 OUTPUT. Normally closed (NC) for fault indicator/coil status. This contact is open if there is
a fault or the coil is activated.
3 OUTPUT. Common for fault indicator.
4 OUTPUT. SAFETY LINE: Common safety contact to connect to safety line.
5 No connection.
6 OUTPUT. SAFETY LINE: Normally open contact to connect to safety line.
7-19 No connection.
20 INPUT. External reset. 0 V
21 INPUT. External reset, 24 V. If there is voltage, the reset action is performed.
22 INPUT. Level 1. 0 V
23 INPUT. Level 1. 24 V.
24 INPUT. Level 2. 0 V
25 INPUT. Level 2. 24 V.
26 INPUT. Remote manual rescue, 0 V.
27 INPUT. Remote manual rescue, 24 V. If there is voltage for more than 3 seconds, the manual
or bypass rescue action is performed.
28-31 No connection.
32 INPUT. 24 VDC power supply.
33 INPUT. 0 V power supply.
34 INPUT. Batteries +
35 INPUT. Batteries -
36 No connection.
37 No connection.
38 OUTPUT. Inductive sensor, 0 V power supply.
39 INPUT. Inductive sensor, Detection.
40 OUTPUT. Inductive sensor, 24 VDC power supply.
41 No connection.
42 OUTPUT. Coil, 24 VDC
43 OUTPUT. Coil, 0 VDC
44-48 No connection.
49 INPUT. Doors, 0 V
Note: This manual displays partial information on the instructions for use and maintenance of this product. Please refer to the customer
area in Dynatech’s website in order to consult the full manual; http://customers.dynatech-elevation.com/

SD-BOX INSTRUCTION MANUAL, CODE: DYN 81.01.00
Date: 03/03/2020 Version 00
- 18 -
50 INPUT. Doors, 24-230 VDC or 24-230 VAC. If there is voltage, the door safety line is closed.
51 No connection.
52 No connection.
53 INPUT. Motor. 0 V
54 INPUT. Motor, 24-230 VDC or 24-230 VAC. If there is voltage, the motor is running.
Note: This manual displays partial information on the instructions for use and maintenance of this product. Please refer to the customer
area in Dynatech’s website in order to consult the full manual; http://customers.dynatech-elevation.com/

SD-BOX INSTRUCTION MANUAL, CODE: DYN 81.01.00
Date: 03/03/2020 Version 00
- 19 -
Electrical connections
Figure 2: Internal relays electrical connection
Note: This manual displays partial information on the instructions for use and maintenance of this product. Please refer to the customer
area in Dynatech’s website in order to consult the full manual; http://customers.dynatech-elevation.com/
Other manuals for SD-BOX
1
Table of contents
Popular Control System manuals by other brands
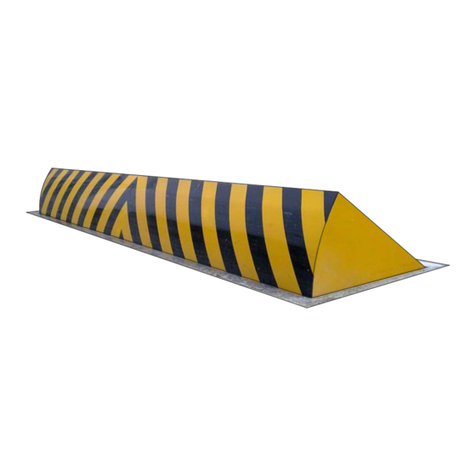
Parking Facilities
Parking Facilities PF8000 manual
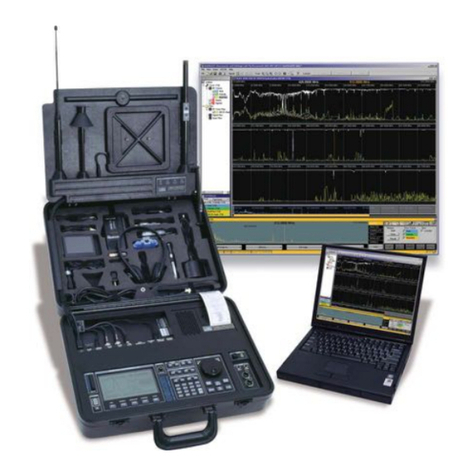
OSCOR
OSCOR OSC 5000 owner's guide
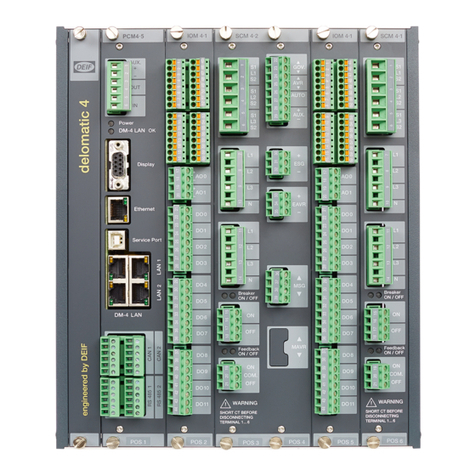
Deif
Deif DELOMATIC 4 Series Replacement instructions

Air Lift Performance
Air Lift Performance 3H user guide

Eventide
Eventide BD600+ Operator's manual
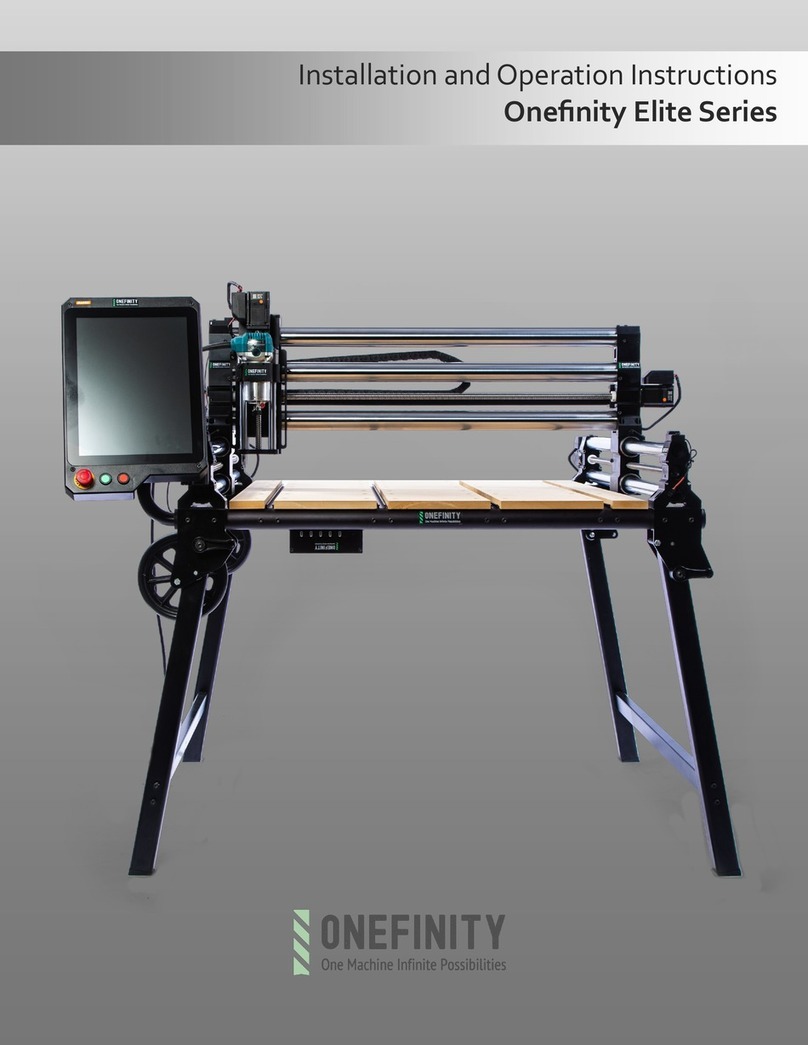
ONEFINITY
ONEFINITY Elite Series Installation and operation instruction