Echo CH8540 User manual

Before You Begin
DEAR ECHO Bear Cat®CUSTOMER
Thank you for purchasing an ECHO Bear Cat product. The ECHO Bear Cat line is designed, tested, and manufactured
to give years of dependable performance. To keep your machine operating at peak eciency, it is necessary to adjust
it correctly and make regular inspections. The following pages will assist you in the operation and maintenance of your
machine. Please read and understand this manual before operating your machine.
If you have any questions or comments about this manual, please call us toll-free at 888.625.4520.
If you have any questions or problems with your machine, please call or write your local authorized ECHO Bear Cat
dealer.
This document is based on information available at the time of its publication. ECHO Bear Cat is continually making
improvements and developing new equipment. In doing so, we reserve the right to make changes or add improvements
to our product without obligation for equipment previously sold.
PLEASE SEND US YOUR WARRANTY CARD
A warranty card is included in your owner’s kit packaged with your machine. Please take the time to ll in the information
requested on the card. When you send your completed card to us, we will register your machine and start your coverage
under our limited warranty or go to bearcatproducts.com/Product-Support/Product-Registration.
SERIAL NUMBER OR VIN
© 2017, CRARY®INDUSTRIES, ALL RIGHTS RESERVED. PRODUCED AND PRINTED IN THE U.S.A.
IDENTIFICATION NUMBER LOCATION
Your machine will have either a serial number or vehicle
identication number (VIN). VINs are located on the left
side of the trailer frame near the hitch. They are 17-digit
numbers of the format: 5VJAA001XXWXXXXXX. Serial
numbers are located on the machine body. They are
6-digit numbers.
Record your identication number in the space provided
and on the warranty registration card.
FOR MACHINE SERVICE OR PARTS
For service assistance, contact your nearest authorized
ECHO Bear Cat dealer or the factory. For parts, contact
your authorized dealer. The parts manual for your
machine is available at bearcatproducts.com/Product-
Support/Find-A-Product-Manual. Your dealer will need to
know the identication number of your machine to provide
the most ecient service. See below for information on
how to identify and record the identication number for
your machine.
FOR ENGINE SERVICE OR PARTS
For engine service or parts, contact your nearest
authorized engine dealer. ECHO Bear Cat does not
handle any parts, repairs or warranties for engines.
ORDERING PARTS
Only genuine ECHO Bear Cat replacement parts should
be used to repair the machine. Replacement parts
manufactured by others could present safety hazards,
even though they may t on this machine. Replacement
parts are available from your ECHO Bear Cat dealer.
Provide the following when ordering parts:
The SERIAL NUMBER or VIN of your machine.
The PART NUMBER of the part.
The PART DESCRIPTION.
The QUANTITY needed.
HOW TO CONTACT ECHO Bear Cat
ADDRESS PHONE E-MAIL HOURS
237 NW 12th Street
P.O. Box 849
West Fargo, ND 58078
888.625.4520
701.282.5520
Fax: 701.282.9522
Monday - Friday
8 a.m. to 5 p.m.
Central Time

LIMITED WARRANTY
This warranty applies to all ECHO Bear Cat®Outdoor Power Equipment manufactured by Crary®Industries, Inc. and does not
include gas engine or electric powered pressure washers under the ECHO Bear Cat brand. See ECHO Bear Cat Pressure Washer
Limited Warranty for complete warranty details on those products.
Crary Industries, Inc. warrants to the original owner each new ECHO Bear Cat product to be free from defects in material
and workmanship, under normal use and service. The warranty shall extend, from date of purchase, three years (U.S. and
Canada only [two years outside U.S. and Canada]) for Consumer use of the product, one year for Commercial applications and
six months for Rental applications. Replacement parts and accessories are warranted for 90 days from date of installation.
Batteries for Inverters and Generators are warranted for 90 days from the date of purchase.
“Consumer” dened as: complete unit for personal, residential or non-income producing use.
“Commercial” dened as: complete unit for commercial, institutional, property management, agricultural, horticultural or
income producing use.
“Rental” dened as: complete unit for rental purposes to produce income.
*Models SC2163, SC2170, SC3206 & SC3208 are classied as Consumer grade products and will not qualify for warranty
coverage if used for Commercial or Rental purposes.
The product is warranted to the original owner by either a completed warranty registration on le at Crary Industries, Inc. and/or
proof of sale. Warranty coverage begins on the date of purchase. The warranty registration can be registered on-line by visiting
bearcatproducts.com/Product-Support/Product-Registration or the paper card completed and returned to Crary Industries, Inc.
In the event of a failure, return the product, at your cost, along with proof of purchase to the selling ECHO Bear Cat dealer.
Crary Industries, Inc. will, at its option, repair or replace any parts found to be defective in material or workmanship. Warranty
on any repairs will not extend beyond the product warranty. Repair or attempted repair by anyone other than an authorized
ECHO Bear Cat dealer as well as subsequent failure or damage that may occur as a result of that work will not be paid under
this warranty. Crary Industries, Inc. does not warrant replacement components not manufactured or sold by Crary Industries,
Inc.
1. This warranty applies only to parts or components that are defective in material or workmanship.
2. This warranty does not cover normal wear items including, but not limited to: batteries, bearings, belts, pulleys, lters,
chipper blades, shredder ails or knives.
3. This warranty does not cover normal maintenance, service or adjustments.
4. This warranty does not cover depreciation or damage due to misuse, negligence, accident or improper maintenance.
5. This warranty does not cover damage due to improper setup, installation or adjustment.
6. This warranty does not cover damage due to unauthorized modications of the product.
7. Engines are warranted by the respective engine manufacturer and are not covered by this warranty.
ECHO Bear Cat’s Demo Fleet Warranty Program includes the following distributor guidelines. On the rst day the machine is
used for demonstration, all demo units must be registered to the distributor. A demo unit is under warranty to the distributor as
long as it is in the demo eet, a term which cannot exceed two years. If delivery date to the distributor is more than one year
prior to the date unit enters the demo eet, the warranty is expired. All units sold to customers within the demo period will
be granted a six month commercial warranty or one year consumer warranty. In order for these warranties to be effective, all
registrations must be changed to new owner once units are sold. Should unit be sold to customer outside of the demo period,
no warranty is offered by the manufacturer.
Crary Industries, Inc. is not liable for any property damage, personal injury or death resulting from the unauthorized
modication or alteration of an ECHO Bear Cat product or from the owner’s failure to assemble, install, maintain or operate the
product in accordance with the provisions of the Owner’s manual.
Crary Industries, Inc. is not liable for indirect, incidental or consequential damages or injuries including but not limited to loss
of crops, loss of prots, rental of substitute equipment or other commercial loss.
This warranty gives you specic legal rights. You may have other rights that may vary from area to area.
Crary Industries, Inc. makes no warranties, representations or promises, expressed or implied as to the performance of its
products other than those set forth in this warranty. Neither the dealer nor any other person has any authority to make any
representations, warranties or promises on behalf of Crary Industries, Inc. or to modify the terms or limitations of this warranty
in any way. Crary Industries, Inc., at its discretion, may periodically offer limited, written enhancements to this warranty.
CRARY INDUSTRIES, INC. RESERVES THE RIGHT TO CHANGE THE DESIGN AND/OR SPECIFICATIONS OF ITS PRODUCTS AT
ANY TIME WITHOUT OBLIGATION TO PREVIOUS PURCHASERS OF ITS PRODUCTS.
ENGLISH

TABLE OF CONTENTS
1 SAFETY ................................................................................................................................................................... 1
1.1 SAFETY ALERT SYMBOL.................................................................................................................................................... 1
1.2 BEFORE OPERATING.......................................................................................................................................................... 1
1.3 OPERATION SAFETY........................................................................................................................................................... 2
1.4 PTO SAFETY......................................................................................................................................................................... 3
1.5 MAINTENANCE/STORAGE SAFETY.................................................................................................................................. 3
1.6 SAFETY DECALS ................................................................................................................................................................. 4
1.7 SAFETY DECAL LOCATIONS ............................................................................................................................................. 5
2 ASSEMBLY.............................................................................................................................................................. 6
2.1 ATTACH CHUTE.................................................................................................................................................................... 6
2.2 ATTACH DISCHARGE TUBE ............................................................................................................................................... 7
2.3 CONNECT TO PTO DRIVELINE.......................................................................................................................................... 8
3 FEATURES & CONTROLS .................................................................................................................................... 9
4 OPERATION...........................................................................................................................................................11
4.1 STARTING THE CHIPPER ..................................................................................................................................................11
4.2 STOPPING THE CHIPPER .................................................................................................................................................11
4.3 CHIPPER OPERATION GUIDELINES .............................................................................................................................. 12
5 SERVICE & MAINTENANCE............................................................................................................................... 13
5.1 MAINTENANCE SCHEDULE ............................................................................................................................................. 13
5.2 ROTOR LOCK ..................................................................................................................................................................... 14
5.3 RAISE/LOWER ACCESS COVER ..................................................................................................................................... 14
5.4 CHIPPER BLADES MAINTENANCE................................................................................................................................. 14
5.5 REMOVING THE BLADES ................................................................................................................................................. 15
5.6 SHARPENING THE BLADES............................................................................................................................................. 15
5.7 INSTALLING THE BLADES................................................................................................................................................ 15
5.8 SETTING CHIPPER BLADE CLEARANCE ...................................................................................................................... 15
5.9 CLEARING A PLUGGED ROTOR...................................................................................................................................... 16
5.10 DRIVE BELTS.................................................................................................................................................................... 16
5.11 ROTOR BEARINGS .......................................................................................................................................................... 17
5.12 PTO DRIVELINE LUBRICATION ..................................................................................................................................... 17
5.13 LUBRICATION................................................................................................................................................................... 18
6 TROUBLESHOOTING.......................................................................................................................................... 19
7 SPECIFICATIONS ................................................................................................................................................ 20
7.1 BOLT TORQUE.................................................................................................................................................................... 21
8 OPTIONS............................................................................................................................................................... 22

18 INCH CHIPPER
ENGLISH
Section
1. Read and understand this owner’s manual. Be
completely familiar with the controls and the proper
use of this equipment.
2. Familiarize yourself with all of the safety and
operating decals on this equipment and on any of its
attachments or accessories.
3. Keep safety decals clean and legible. Replace
missing or illegible safety decals.
4. Obtain and wear safety glasses
and use hearing protection at all
times when operating this machine.
5. Avoid wearing loose tted clothing.
Never operate this machine while
wearing clothing with drawstrings that could wrap
around or get caught in the machine.
6. Do not operate this machine if you are under the
inuence of alcohol, medications, or substances that
can aect your vision, balance or judgement. Do not
operate if tired or ill. You must
be in good health to operate this
machine safely.
7. Do not operate this equipment in
the vicinity of bystanders. Keep
the area of operation clear of all persons, particularly
small children. It is recommended that bystanders
keep at least 50 feet (15 meters) away from the area
of operation.
8. Do not allow children to operate this equipment.
9. Use only in daylight or good articial light.
10. Do not run this equipment in an enclosed area. Engine
exhaust contains carbon monoxide gas, a deadly
poison that is odorless, colorless and tasteless.
Do not operate this equipment in or near buildings,
windows or air conditioners.
1 SAFETY
Indicates an imminently hazardous situation that, if not
avoided, will result in death or serious injury.
DANGER
Indicates a potentially hazardous situation that, if not
avoided, could result in death or serious injury.
WARNING
Indicates a potentially hazardous situation that, if not
avoided, may result in minor or moderate injury.
CAUTION
The Owner/Operator’s manual uses this symbol to alert
you of potential hazards. Whenever you see this symbol,
read and obey the safety message that follows it. Failure
to obey the safety message could result in personal injury,
death or property damage.
1.1 SAFETY ALERT SYMBOL 1.2 BEFORE OPERATING

28 INCH CHIPPER
SAFETY
1. Always stand clear of discharge area when operating
this machine. Keep face and body away from feed
and discharge openings.
2. Keep hands and feet out of feed and discharge
openings while machine is operating to avoid serious
personal injury. Stop and allow machine to come to
a complete stop before clearing
obstructions.
3. Set up your work site so you are
not endangering trac and the
public. Take great care to provide
adequate warnings.
4. Do not climb on machine when operating. Keep
proper balance and footing at all times.
1.3 OPERATION SAFETY
5. Check cutting chamber to verify it is empty before
starting the machine.
6. The rotor will continue to rotate after being disengaged.
Shut o the machine and make sure all moving parts
have come to a complete stop before inspecting or
servicing any part of the machine. Disconnect the
battery and remove the ignition key if applicable.
7. Do not insert branches with a diameter larger than
the max chipper capacity into machine or machine
damage may occur.
8. When feeding material into machine, do not allow
metal, rocks, bottles, cans or any other foreign
material to be fed into the machine.
9. Ensure debris does not blow into trac, parked cars,
or pedestrians.
10. Keep the machine clear of debris and other
accumulations.
11. Do not allow processed material to build up in the
discharge area. This may prevent proper discharge
and can result in kickback of material through the
feed opening.
12. If the machine becomes clogged, the cutting
mechanism strikes any foreign object, or the machine
starts vibrating or making an unusual noise, shut o
machine immediately and make sure all moving parts
have come to a complete stop. Disconnect the battery
and remove the ignition key if applicable. After the
machine stops: A) Inspect for damage, B) Replace
or repair any damaged parts, and C) Check for and
tighten any loose parts.
13. On electric start models, disconnect cables from
battery before doing any inspection or service.
Remove key.
14. Check blade bolts for proper torque after every 8 hours
of operation. Check blades and rotate or resharpen
daily or as required to keep blades sharp. Failure
to do so may cause poor performance, damage or
personal injury and will void the machine warranty.
11. Always use an approved fuel container. Do not
remove gas cap or add fuel when engine is running.
Add fuel to a cool engine only.
12. Do not ll fuel tank indoors. Keep open ames, sparks,
smoking materials and other sources of combustion
away from fuel.
13. Do not operate machine without shields in place.
Failure to do so may cause serious injury or death.
14. Keep all guards, deectors, and shields in good
working condition.
15. Before inspecting or servicing any part of this machine,
shut o the machine and make sure all moving parts
have come to a complete stop. Disconnect the battery
and remove the ignition key where applicable.
16. Check that all screws, nuts, bolts, and other fasteners
are secured, tightened and in proper working condition
before starting the machine.
17. Do not transport or move machine while it is operating
or running.

38 INCH CHIPPER
ENGLISH
SAFETY
1. Read and follow instructions on PTO safety decals.
2. Stay alert and pay attention when PTO is operating.
3. Keep bystanders, especially children, away from PTO
driveline.
4. Check the driveline to ensure it is attached securely
to the power supply.
5. Keep guards and shields in place at all times while
operating. Disengage PTO, shut o power source,
and make sure all moving parts have come to a
complete stop before removing guards or shields.
6. Clothing worn by operator must be fairly tight. Never
wear loose tted jackets, shirts, or pants when
working around the PTO. Tie long hair back or put
under a cap.
7. Keep hydraulic hoses, electric cords, chains and
other items from contacting the driveline.
8. Proper recommended PTO operating speed is 540
+/- 10 RPM.
9. Before inspecting or servicing the PTO drive area,
disengage the driveline, shut o power source,
remove ignition key, and make sure all moving parts
have come to a complete stop.
10. Keep hands, feet, and clothing away from all PTO
drive parts.
11. Do not clean, lubricate or adjust the PTO shaft when
it is running.
1. Before inspecting, servicing, storing, or changing
an accessory, shut o the machine and make sure
all moving parts have come to a complete stop.
Disconnect the battery and remove the ignition key
where applicable.
2. Replace any missing or unreadable safety decals.
Refer to the safety decal section for part numbers.
3. Allow machine to cool before storing in an enclosure.
4. Store the machine out of reach of children and where
fuel vapors will not reach an open ame or spark.
5. Never store this machine with fuel in the fuel tank
inside a building where fumes may be ignited by
an open ame or spark. Ignition sources can be hot
water and space heaters, furnaces, clothes dryers,
stoves, electric motors, etc.
6. Drain the fuel and dispose of it in a safe manner for
storage periods of three months or more.
1.4 PTO SAFETY 1.5 MAINTENANCE/STORAGE SAFETY

48 INCH CHIPPER
SAFETY
1.6 SAFETY DECALS
See Section 1.7 for decal locations. Familiarize yourself with all of the safety and operating decals on the machine
and the associated hazards. See the engine owner’s manual or contact the engine manufacturer for engine safety
instructions and decals.
Keep hands and feet out of inlet and discharge
openings while machine is operating to avoid serious
personal injury. Stop and allow machine to come to a
complete stop before clearing obstructions.
Read and understand this owner/operators
manual. Be completely familiar with the
controls and the proper use of this equipment
Obtain and wear safety glasses and use
hearing protection at all times when operating
this machine.
Before inspecting or servicing any part of this
machine, shut o power source, remove the
key, disconnect spark plug wire from spark
plug and make sure all moving parts have
come to a complete stop.
Do not operate this equipment in the vicinity of bystanders. Do not allow
children to operate this equipment. Always stand clear of discharge area
when operating this machine. Keep face and body away from discharge
areas.
Do not operate machine without shields in place.
Failure to do so may cause serious injury or
death.
Check blade bolts for proper torque
after every 8 hours of operation.
Check blades and rotate or
resharpen daily or as required to
keep blades sharp. Refer to owners
manual for instructions. Failure to do so may cause poor performance,
damage or personal injury and will void the machine warranty.
PN 12174
Keep hands and feet out of inlet and
discharge openings while machine
is operating to avoid serious
personal injury. Stop and allow
machine to come to a complete
stop before clearing obstructions.
2
1
3
7
4
5
6
PN 12169
PN 12172
PN 12173
PN 12174
PN 12175
PN 12250
PN 12168
Read and understand you owners manual before operating. If owners
manual was not included or you have any questions, please call
800.247.7335 or 701.282.5520 (U.S.A.).
Do not operate this equipment in the
vicinity of bystanders. Do not allow children
to operate this equipment. Always stand
clear of discharge area when operating
this machine. Keep face and body away
from discharge areas. Rotate the discharge
tube over the hitch before towing and lock
securely in place.
8PN 14942-00
Contact with rotating driveline
can cause death. Do not operate
without all driveline, tractor and
equipment shields in place.
Ensure the driveline is securely attached at both ends and driveline
shields that turn freely on the driveline are in place.
9PN 32109-00

58 INCH CHIPPER
ENGLISH
SAFETY
1.7 SAFETY DECAL LOCATIONS
The numbers below correspond to the decals in Section 1.6. Make certain that all safety and operating decals on this
machine are kept clean and in good condition. Decals that need replacement must be applied to their original locations.
1
2
3
4
5*
6
7
8
9
*Decal located under shield
CH8540XE MODEL SHOWN

68 INCH CHIPPER
Section
2 ASSEMBLY
1. Remove chipper from shipping crate. Place unit on
a level surface before assembling. See the Torque
Chart in Section 7 for the recommended torque for
tightening bolts and screws.
2. Mount the chipper chute to the frame mounting
bracket using eight 3/8" × 1-1/2" bolts and locknuts.
Use three bolts on each side and two on the bottom.
3. For models with extension trays: Attach the extension
tray to the chute with ve 3/8" × 1" bolts and nuts.
Figure 2.1, Attach Chute
If any bolts or nuts are dropped in the machine, be sure
to remove them before starting the machine.
WARNING
2.1 ATTACH CHUTE
Do not operate this unit without the chipper chute
correctly installed. Rotating cutting blades can cause
serious personal injury.
WARNING
CH8540XE MODEL SHOWN

78 INCH CHIPPER
ENGLISH
ASSEMBLY
1. Attach one clamping ring (1) and one spacer ring (2)
to discharge tube base (3) using three 3/8" × 1-1/4"
bolts (4) and nylock nuts (5). Tighten leaving 1/16"
gap to assist in mounting to ange. See Figure 2.2.
2. Slide the tube onto the mounting ange on the
chipper frame. The discharge clamp (1) should slide
underneath the lip of the ange. Tighten the bolts to
secure it.
3. Install the second half of the spacer (2) and clamp
ring (1) on the discharge tube with 3/8" × 1-1/4" bolts
(4) and nylock nuts (5).
4. Attach lanyard with discharge pin (6) as shown in
Figure 2.3. Loop on lanyard installed below nut
located under discharge handle.
Figure 2.2, Attach Clamp Ring and Spacer
1
2
3
4
5
Figure 2.3, Attach Discharge Tube
1
2
5
4
6
2.2 ATTACH DISCHARGE TUBE
5. Lubricate the tube by applying grease to the grease
zerk at the base of the tube. Rotate the tube and
apply grease until the tube rotates freely.
6. Rotate the tube 360 degrees and lock it in place with
the lock pin to make sure it is mounted correctly.
7. Attach the discharge deector (7) to the discharge
tube. Connect the deector with two 3/8" × 1-1/2"
bolts (8) through the lower hole in the discharge tube.
Run these bolts through the inside of the tube, 1/2"
washer (12), deector, 3/8" washer (13), and then
knob (9).
8. Finish bolting the deector to the tube with two 3/8"
× 1" bolts (10) through the end hole in the discharge
tube, 1/2" washer, deector, and 3/8 nut (11).
Keep nuts as tight as possible while allowing the
discharge chute to freely turn.
NOTE
Figure 2.5, Attach Discharge Deector
7
8
9
10
11
12
13

88 INCH CHIPPER
ASSEMBLY
6. Remove driveline pieces (for ease of cutting) and cut
ONLY the outer and inner plastic tubes.
7. After cutting plastic tubes, measure 1-9/16" (40 mm)
from the ends of both newly cut plastic tubes.
8. Mark the inner steel shafts and cut both shafts at
1-9/16" (40 mm) as shown in the photos.
9. File both shaft ends to remove sharp edges and slide
the driveline pieces back together.
10. When you have conrmed that the driveline is the
correct length for your tractor, connect the driveline to
the chipper rotor.
11. Connect the opposite end of the PTO shaft to the
tractor.
1-1/4" from Shield
Inner
Tube
Yoke
Shield
●The tractor must have a standard 540 RPM PTO
shaft.
●If the tractor has an electric PTO clutch, consult
your dealer for correct operating procedures.
●Consult the attached GKN Walterscheid driveline
manual for complete service and maintenance
recommendations.
IMPORTANT
1-9/16" (40 mm)
Outer
Tube
Steel
Shaft
Steel
Shaft Inner
Tube
1-1/4" from Shield
Outer
Tube
Yoke
Shield
The driveline supplied with this machine may need to be
cut to a shorter length for proper operation with the tractor
being used. To determine if driveline will need to be cut,
follow steps below or consult attached driveline manual.
1. BEFORE ATTACHING THE DRIVELINE: attach the
machine to the tractor with three-point hitch system.
2. Raise and lower machine on three-point hitch to
determine the shortest possible working distance
between the tractor PTO shaft and the drive shaft of
the machine.
3. Pull the driveline apart so the two pieces are
separated. Attach the 6-splined connector for the
outer tube to the tractor, and attach the connector for
the inner tube to the machine.
4. Position installed driveline halves parallel to one
another. (Photo below is example of driveline overlap.)
5. On larger outer tube, measure back 1-1/4" (32 mm)
from lower yoke shield and mark plastic tube. Repeat
this process for smaller inner plastic tube measuring
1-1/4" (32 mm) back from upper yoke shield.
2.3 CONNECT TO PTO DRIVELINE

98 INCH CHIPPER
ENGLISH
Section
3 FEATURES & CONTROLS
Understanding how your machine works will help you achieve the best results when using your chipper. The following
descriptions dene the features and controls of your machine.
1. CHUTE EXTENSION TRAY
CE compliant models. The feed chute has an extension tray that folds down.
2. DISCHARGE CAP
Directs the discharge of material vertically. Adjust the discharge cap by turning the knobs located on the side. Turn
knob counterclockwise to loosen discharge cap. Adjust to desired position. Turn knob clockwise to secure discharge
cap.
3. DISCHARGE TUBE
Directs the discharge of chipped material horizontally. The discharge tube can be rotated 360° horizontally by
removing the pin and rotating the discharge tube until the discharge faces the desired position. Replace the pin in
one of the holes on the base of the discharge.
4. ROTOR ACCESS COVER
Tilts up to expose rotor.
5. ROTOR LOCK
Use the rotor lock to hold the rotor in place when doing any maintenance work. See Section 5.2.
6. FEED CHUTE
Materials to be chipped are fed into the feed chute to the chipper blades.
7. MANUAL CONTAINER
Conveniently holds your manuals.
8. DRIVE BELT SHIELD
Never remove shields when in use.
9. CAT. I THREE-POINT CONNECTION
Mounts chipper to tractor three-point hitch.

10 8 INCH CHIPPER
FEATURES & CONTROLS
1
2
3
4
5
6
7
8
9
CH8540XE MODEL

118 INCH CHIPPER
ENGLISH
Section
4 OPERATION
Move machine to a clear, level area outdoors before
starting. Do not operate in the vicinity of bystanders.
Make sure cutting chamber is empty before starting.
WARNING
Before operating your machine, be sure you read
and understand all safety, controls and operating
instructions in this owner’s manual and on your
machine. Failure to follow these instructions can result
in serious injury or property damage.
WARNING
As with any other piece of outdoor equipment, getting the
feel for how your machine operates and getting to know
the best techniques for particular jobs are important to
overall good performance.
CHIPPING OPERATION
The chipping operation takes place in the middle of
the machine, where hardened steel chipper blades are
mounted on a rotating rotor assembly. Material fed into
the chipper chute is sliced into small chips and propelled
out through a discharge tube.
4.1 STARTING THE CHIPPER
1. Connect PTO driveline to tractor as described in
Section 2.3.
2. Adjust three-point top link so the chipper sits level.
3. Start tractor engine and engage PTO (refer to tractor
owner’s manual). Increase engine speed to rated
PTO RPM.
Do not inspect or work on PTO drive area without rst
disengaging PTO and shutting o tractor. Allow all
moving parts to come to a complete stop.
WARNING
1. Move tractor throttle to slowest position.
2. Disengage PTO lever and shut o tractor engine.
3. Allow machine to come to a complete stop.
The rotor will continue to turn for some time after the
engine has been shut o. Make sure rotor has stopped
completely before inspecting or servicing machine.
NOTE
4.2 STOPPING THE CHIPPER

12 8 INCH CHIPPER
OPERATION
●Never lean over the chipper chute to push objects
into the cutting device. Use a push stick or brush
paddle.
●Never use shovels or forks to feed brush. They
can cause extensive damage if they contact the
blades. In addition, metal pieces can be ejected
from the chipper chute and cause serious injury
or death.
●Never feed brush into the chute with your feet.
●Never use hands or feet to clear materials that
build up in the chute.
CAUTION
●Obtain and wear safety glasses at all times when
operating the machine.
● Do not wear loose tting clothing.
●The operator should always wear heavy boots,
gloves, pants and a long-sleeved shirt.
●Use common sense and practice safety to protect
yourself from branches, sharp objects, and other
harmful objects.
CAUTION
To prevent personal injury or property damage: shut
o engine and make sure that all moving parts have
come to a complete stop before servicing, adjusting,
or repairing machine.
WARNING
Read and follow all safety instructions in this manual.
Failure to operate the machine in accordance with
the safety instructions MAY RESULT IN PERSONAL
INJURY!
WARNING
The machine chips a variety of materials into a more
readily decomposed or handled condition. The following
guidelines will help you get started.
1. Gradually increase engine speed to rated PTO
RPM.
2. ALWAYS run engine at rated PTO RPM before
starting to chip material.
3. If the chipper rotor slows, stop feeding material
and allow the engine to recover. Feed material more
evenly.
4. If the chipper jams, remove the branch and rotate
it before reinserting into the chute. Alternately insert
and retract the limb or insert continuously at a rate
that will not kill the engine.
5. Sharpen the chipping blades periodically. Check
the sharpness of the blades every 5-15 hours. Refer to
the Service and Maintenance section for sharpening
instructions.
6. Limbs fed in to the chipper chute must be 8"
(20.3 cm) in diameter or less. Trim side branches
that cannot be bent enough to feed into the chipper
chute. Hold small diameter branches together in a
bundle and feed in simultaneously.
7. Alternate green or fresh cut material with dry
material to lubricate the chipping blades for
longer life and better performance. Chipping dead,
dry material will create heat and dull the chipping
blades quicker.
8. ALWAYS feed brush from the side of the chipper
chute, rather than from the front. Step aside to avoid
being hit by the brush moving into the chipper.
9. ALWAYS place limb, butt end rst, into the
chipper chute until it contacts the chipper blades.
The actual feed rate of the limb into the chipper will
depend on the type of material fed and sharpness of
the cutting blades.
4.3 CHIPPER OPERATION GUIDELINES
10. NEVER attempt to clear a plugged rotor or discharge
with the engine running. ALWAYS shut engine
OFF and remove the PTO shaft from tractor before
servicing any part of this machine.
11. NEVER attempt to chip pieces of metal, rock, bottles,
cans or other foreign objects.

138 INCH CHIPPER
ENGLISH
Section
5 SERVICE & MAINTENANCE
The items listed in this service and maintenance schedule are to be checked, and if necessary, corrective action taken.
This schedule is designed for units operating under normal conditions. If the unit is operating in adverse or severe
conditions, it may be necessary for the items to be checked and serviced more frequently.
SERVICE AND MAINTENANCE SCHEDULE
FREQUENCY
COMPONENT MAINTENANCE
REQUIRED
BEFORE
EACH USE
EVERY 8
HOURS
EVERY 25
HOURS
EVERY 50
HOURS
All internal and external
nuts and bolts Check tightness ●
Chipper anvil Check clearance and
retorque to 75 ft-lbs. (1) ●
Chipper blades Check sharpness and
retorque to 120 ft-lbs. (1) ●
Entire machine Clean ●
PTO cross journals Lube ●
PTO inner tubes Lube ●
PTO shield retaining
bearing Lube ●
Drive belt Check ●
Belt tension Check ●
Belt/pulley alignment Check ●
Grease zerks Lube ●
(1) Perform more frequently when chipping dry or dirty wood.
As the Limited Warranty states, failure by the Owner to perform normal maintenance will void the machine’s
warranty. The aggressive, high-speed nature of chipping REQUIRES THE OWNER TO PERFORM THE
ABOVE LISTED NORMAL MAINTENANCE. Special consideration to maintain and re-torque the CHIPPER
ANVIL, CHIPPER BLADES, and ALL INTERNAL AND EXTERNAL NUTS AND BOLTS is the sole responsibility
of the Owner. Failure by the Owner to do so shall be cause for denial of warranty.
5.1 MAINTENANCE SCHEDULE

14 8 INCH CHIPPER
SERVICE & MAINTENANCE
WARNING
BEFORE INSPECTING OR SERVICING ANY PART OF THIS MACHINE, SHUT OFF POWER SOURCE,
AND MAKE SURE ALL MOVING PARTS HAVE COME TO A COMPLETE STOP.
The chipper blades will eventually become dull, making
chipping dicult and adding extra strain on the machine.
CHECK THE SHARPNESS OF THE BLADES EVERY
5-15 HOURS OF OPERATION AND SHARPEN AS
NEEDED.
Your blades need to be sharpened if:
●Machine vibrates severely when material is fed into
the chipper.
●Chips discharge unevenly or have stringy tails,
especially when chipping green branches.
Before you sharpen the chipping blades, check for
permanent damage. Replace the blade if:
●There are cracks, broken corners or nicks greater
than 1/8" (see below).
●The base of the cutting edge is worn or has been
re-sharpened so that it no longer extends past the
chipping slot (see below).
5.2 ROTOR LOCK
Follow the steps below to install the rotor lock:
1. There is a hole in the shaft cap, the rotor shaft and
a matching hole in the bracket mounted to the rotor
bearing.
2. Rotate the rotor assembly until the hole on the rotor
shaft lines up with the holes in the rotor shaft cap and
bracket.
3. Install pin into the rotor shaft cap, bracket and shaft.
4. Remove pin when service and/or maintenance is
completed.
The rotor assembly has a lock mechanism. When
working on the rotor assembly, use the lock mechanism
at all times.
WARNING
MATCHING HOLE
ON ROTOR SHAFT
ROTOR
LOCK HOLE
ROTOR
ASSEMBLY
SHAFT CAP
PIN
Figure 5.1, Rotor Lock
Follow the steps below to raise or lower the access cover:
1. Rotate the discharge tube so it is parallel to the
access cover.
5.3 RAISE/LOWER ACCESS COVER
5.4 CHIPPER BLADES MAINTENANCE
2. To raise the access cover, remove the chipper housing
access weldment and nylock nuts that secure the
cover to the chipper housing.
3. Lower the cover and secure to the chipper housing
using the chipper housing access weldment and
nylock nuts.

158 INCH CHIPPER
ENGLISH
SERVICE & MAINTENANCE
WARNING
BEFORE INSPECTING OR SERVICING ANY PART OF THIS MACHINE, SHUT OFF POWER SOURCE,
AND MAKE SURE ALL MOVING PARTS HAVE COME TO A COMPLETE STOP.
The blades can be ground on a bench grinder or by a
professional.
1. Never sharpen or grind the mounting surfaces of
the blades. This will cause the edge to roll and the
blade will be damaged, resulting in poor chipping
performance.
2. Regrind the angled edge of the chopping blades to
45 degrees (Figure 5.2). Use the blade angle gauge
plate when sharpening the blades to achieve the
proper angle (see Figure 5.3).
3. Be careful when grinding so that the blade does
not become overheated and change color. This will
remove the heat-treated properties.
5.5 REMOVING THE BLADES
1. Open access cover to allow access to rotor (see
Section 5.3). Rotate the rotor so that the bolts holding
the chipper blades are accessible.
2. Install the rotor lock (Section 5.2). The rotor is now
restrained for removing the blades. To access the
remaining blades, remove pin and reposition rotor.
Return pin to the rotor lock hole.
3. Remove the two bolts that hold the blade to the
rotor. The hardware can be reused. Repeat for the
remaining blade.
4. The blades have two edges and can be reversed one
time before sharpening.
Chipping blades are sharp! Use caution when working
on machine to avoid injury.
WARNING
5.6 SHARPENING THE BLADES 5.7 INSTALLING THE BLADES
1. Install the rotor lock (Section 5.2). The rotor is now
restrained for installing the blades.
2. Place a blade on the rotor and attach using original
hardware. Torque the bolts to 120 ft-lbs. (162 Nm).
Repeat for the remaining blade.
3. Lower the access cover and secure to the chipper
housing (see Section 5.3).
4. Remove rotor lock.
Figure 5.2, Chipper Blade Surfaces
5.8 SETTING CHIPPER BLADE
CLEARANCE
The chipping blades should clear the anvil by 1/16 inch to
1/8 inch. Check the clearance every 8 hours of operation
and adjust if needed.
The chipping anvil is reversible. All four edges of the anvil
can be used for chipping.
To adjust the anvil:
1. Open the access cover (section 5.3) and expose
rotor.
4. Use short grinding times and cool with water or some
type of liquid coolant.
5. Remove an equal amount o each blade to maintain
rotor balance.
6. Small imperfections such as nicks and burrs on
the at side of the blade will not aect the chipping
performance of the machine.
7. For blades that have been repeatedly sharpened,
ensure that the sharpened surface extends past
the chipping slot opening. If it does not extend past
the opening, the blades should be replaced (see
Section 5.4).
Figure 5.3, Blade Angle Gauge Plate

16 8 INCH CHIPPER
SERVICE & MAINTENANCE
WARNING
BEFORE INSPECTING OR SERVICING ANY PART OF THIS MACHINE, SHUT OFF POWER SOURCE,
AND MAKE SURE ALL MOVING PARTS HAVE COME TO A COMPLETE STOP.
5.9 CLEARING A PLUGGED ROTOR
Feeding too large or too much material at once may plug
the chipper. To clear a plugged rotor, proceed as follows:
1. Turn o tractor. Allow all moving parts to come to a
complete stop.
2. Open access cover (see Section 5.3).
3. Clean the debris away from the chipper rotor. Turn
the rotor by hand to be sure it is free to rotate. Be
careful to avoid the chipper blades when cleaning out
the debris.
4. Close access cover and secure (see Section 5.3).
5. Follow start up procedures in Section 4.1.
If the machine becomes plugged, lift the engagement
handle, shut o the engine, disconnect the spark plug
wire and allow the machine to come to a complete stop
before clearing debris. Do not operate the machine
without proper guards and shields in place.
WARNING
ROTOR
CHIPPER
BLADE
ANVIL
ANVIL
SPACER
1/2" BOLT
1/16-1/8"
Figure 5.5, Chipper Blade/Anvil Clearance
2. Loosen the three 1/2 inch bolts that hold the chipper
anvil to the frame. See Figure 5.4 for anvil location.
3. Adjust anvil inward or outward to the correct clearance.
Check to make sure all blades clear the anvil.
4. Tighten bolts on chipping anvil to 75 ft-lbs. and close
access cover.
If the chipping anvil edge is damaged or worn unevenly,
remove the three bolts holding the anvil and use one of
the other three edges. Adjust for correct measurement.
5.10 DRIVE BELTS
Check the condition of the drive belt annually or after
every 25 hours of operation, whichever comes rst. If the
belt is cracked, worn, frayed, or stretched, replace it.
To replace the belt:
1. Disengage PTO and shut o tractor engine.
2. Remove PTO shaft from tractor; disconnect machine
from 3 pt. hitch.
3. Remove round shield connected to belt guard that
covers PTO shaft by removing two 5/16" nuts.
4. Remove belt guard covering pulleys and belts.
5. Remove spring loaded idler pulley o belts and
remove belt.
6. Install new belt and reverse above instructions to
complete belt replacement.
SPACER
CHIPPING ANVIL
ROTOR HOUSING
Figure 5.4, Chipping Anvil Location
Other manuals for CH8540
3
Table of contents
Other Echo Chipper manuals
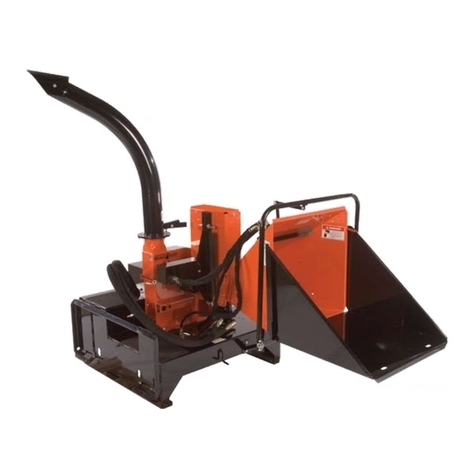
Echo
Echo Bear Cat CH500H(74500) User manual
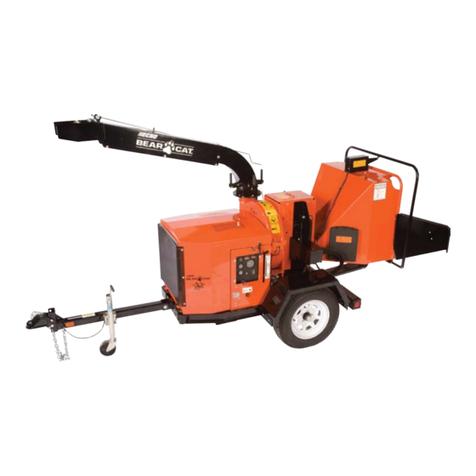
Echo
Echo CH611DH (76628) User manual
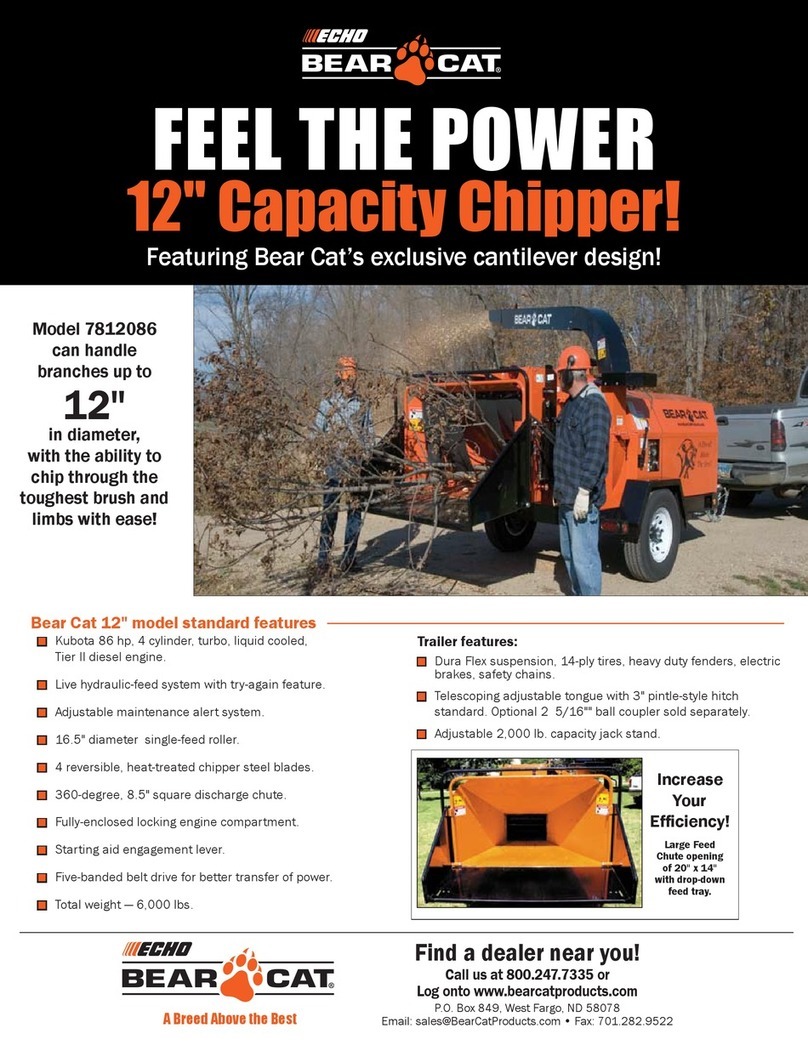
Echo
Echo Bear Cat 7812086 User manual
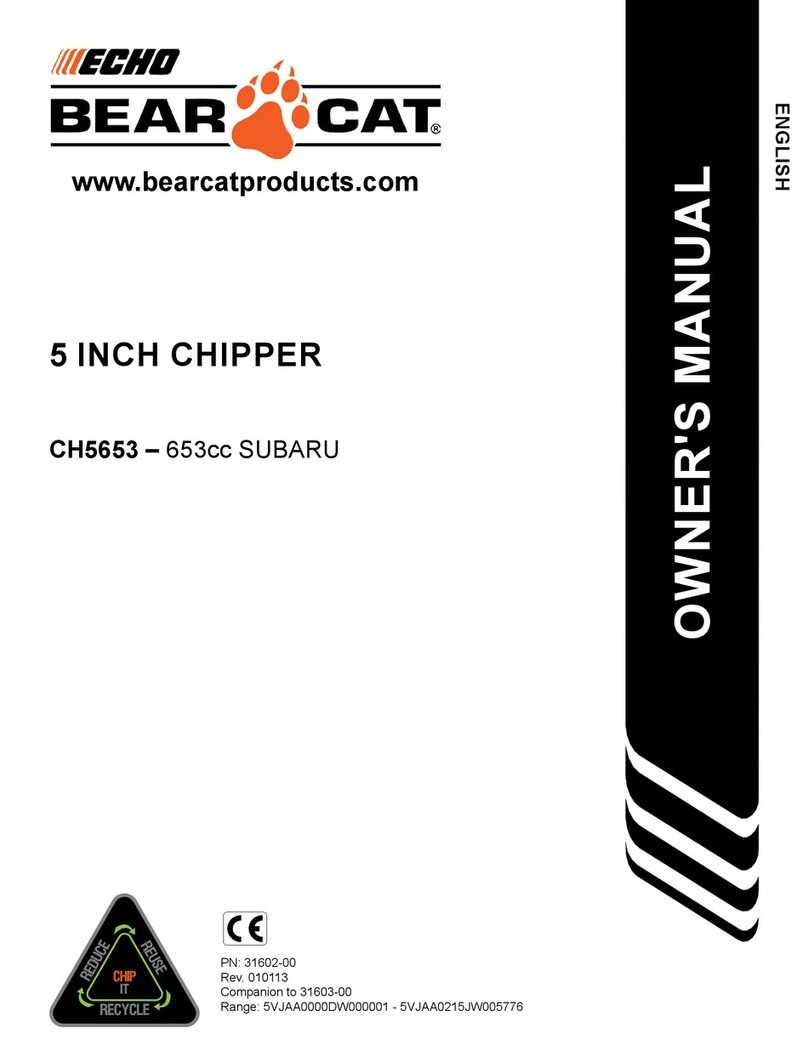
Echo
Echo BEAR CAT CH5653 User manual
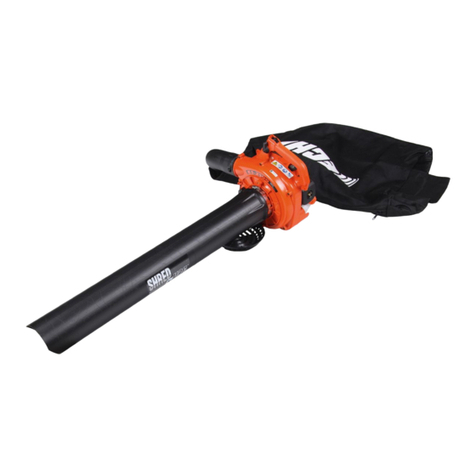
Echo
Echo Shred 'N' Vac ES-2100 User manual
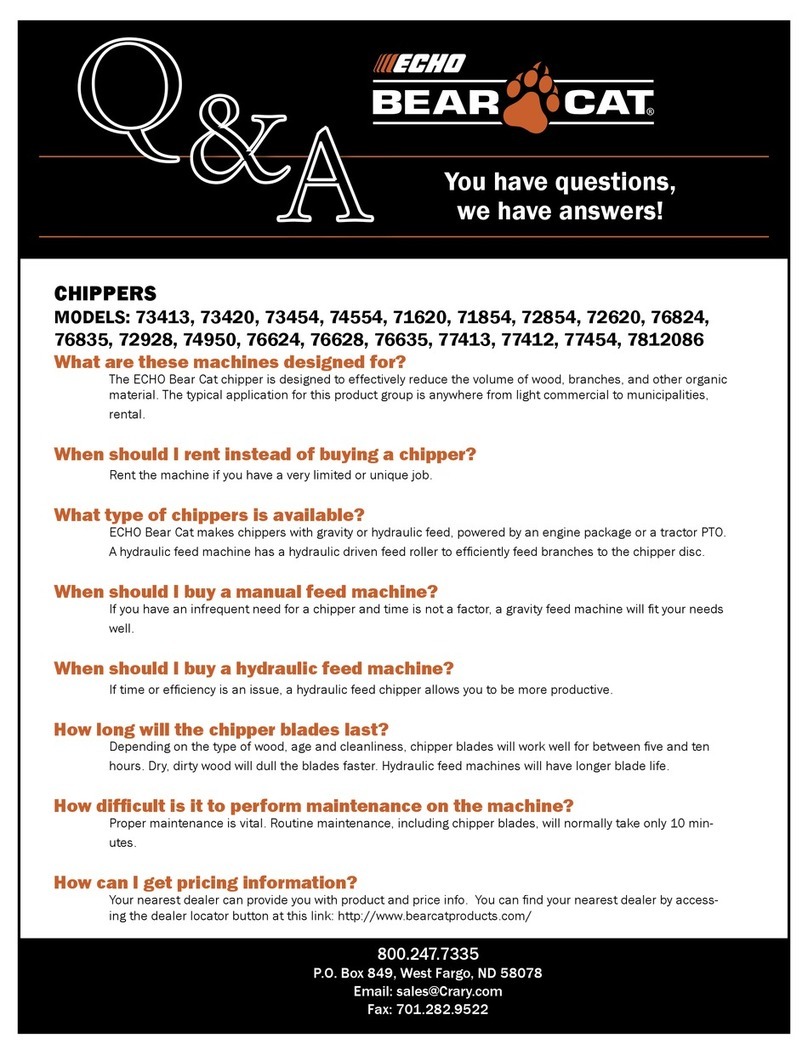
Echo
Echo Bear Cat 76824 Installation guide
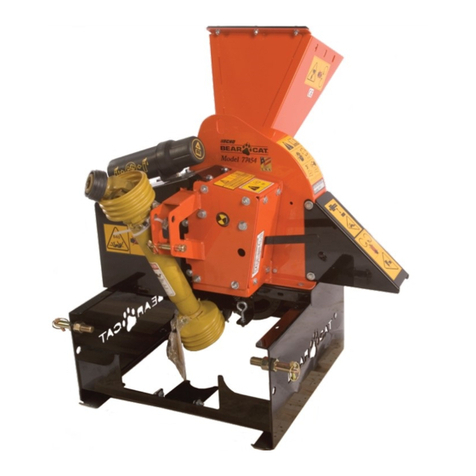
Echo
Echo Bear Car CH45342 (77412) User manual
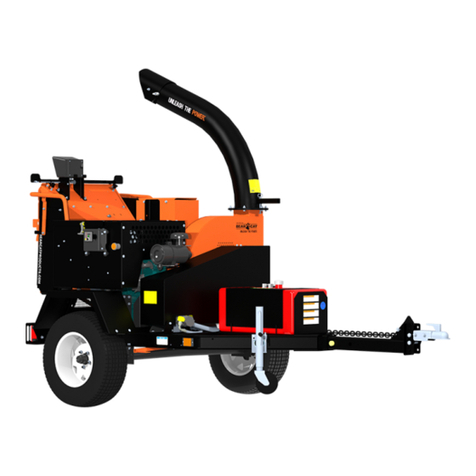
Echo
Echo Bear Cat CH922DH User manual
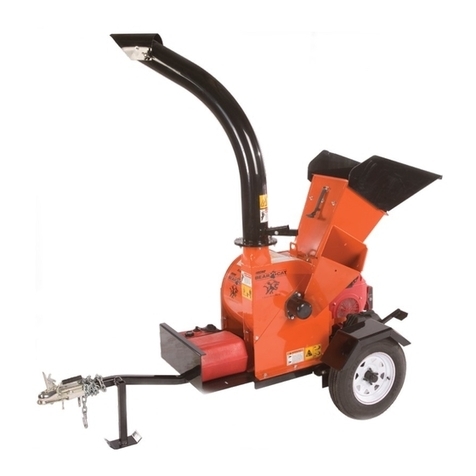
Echo
Echo SC5670B (75524) User manual

Echo
Echo Bear Cat CH6627H User manual