Edwards IW10002 Mounting instructions

1General
Operator and Supervisor Information
Signal Word Denition
Signal Word Panel
2 Signal Word Panel - Machine Front
3 Signal Word Panel - Machine Back
4 Signal Word Panel - Machine Right
5 Signal Word Panel - Machine Left
6Signal Words
Danger Panel
Warning Panel
Notice Panel
Additional Graphic Information
Safety Manual Table of Contents
Operator and Supervisor Information
This is one of four manuals supplied with your machine.
• Installation Manual
• Safety Instructions Manual
• Operations Manual
• Maintenance Manual
READ ALL MANUALS BEFORE OPERATING MACHINERY. Operating
machinery before reading and understanding the contents of all four
manuals greatly increases the risk of injury.
Each of the four machine manuals describes ‘best practices’ in han-
dling, installing, operating and maintaining your machine. The contents
of each manual is subject to change without notice due to improvements
in the machinery or changes in National or International standards.
All rights reserved. Reproduction of this manual in any form, in whole or
in part, is not permitted without the written consent of Edwards Manu-
facturing Company.
Keep all manuals close to the machine to allow for easy reference when
necessary.
Provide operators with sufcient training and education in the basic
functions of the machine prior to machine operation.
Do not allow for operation of the machine by unqualied personnel. Ed-
wards Manufacturing Company is not liable for accidents arising from
unskilled, untrained operation.
Do not modify or change the machine without written authorization from
Edwards Manufacturing Company. Unauthorized modication to a ma-
chine may result in serious operator injury, machine damage and will
void your machine warranty.
Never leave a powered machine unattended. Turn machinery OFF be-
fore walking away.
This machine is manufactured for use by able bodied and able minded
operators only. Never operate machinery when tired or under the inu-
ence of drugs or alcohol.
Do not resell, relocate or export to a destination other than to the original
point of sale. Edwards has designed this machine to meet the stan-
dards of the original receiving country and is not liable for meeting any
governing body or performance standards beyond those of the original
receiving country.

1
Signal Word Definition
Indicates a hazardous situation that, if not avoided,
will result in death or serious injury.
Indicates a hazardous situation that, if not avoided,
could result in death or serious injury.
Indicates a hazardous situation that, if not avoided,
could result in mild or moderate injury.
Indicates information considered important, but not
hazard related.
Signal Word Panel on Machine
Critical machine safety information is identied on signal word labels.
Labels are attached adjacent to the potentially hazardous locations of the
machine. Reference the Safety Instruction Manual for additional informa-
tion regarding the potentially hazardous condition identied on the label.
Review ALL labels on the machinery, reference the operational pre-
cautions and safe operations sections within this manual before any
operation activity is initiated.
Failure to read and understand the signal word labels afxed to the
machinery may result in operator death or injury.
WARNING: This product can expose you to chemicals
including Methyl Isobutyl Ketone which is known to the State of
California to cause cancer and birth defects or other reproduc-
tive harm. For more information go to http://www.p65warnings.
ca.gov.
WARNING: Some dust, fumes and gases created by
power sanding, sawing, grinding, drilling, welding and other
construction activities contain chemicals known to the State of
California to cause cancer and birth defects or other reproduc-
tive harm. Some examples of these chemicals are:
• lead from lead based paint
• crystalline silica from bricks, cement and other masonry
products
• arsenic and chromium from chemically treated lumber
Your risk of exposure varies, depending on how often you do
this type of work. To reduce your exposure to these chemicals,
work in a well-ventilated area and work with approved safety
equipment, such as dust masks that are specically designed
to lter out microscopic particles. For more information go to
http://www.p65warnings.ca.gov/ and http://www.p65warnings.
ca.gov/wood.

2
Signal Word Panel • Machine Front
Recommended Clearance
For Punches and Dies
Material Thickness Die Clearance
1/4” through 15/32”
1/2” through 23/32”
3/4” and over
1/32”
1/16”
3/32”
ACCESSORY AUTO
CUT
IRON
WORKER
Read, understand, and follow
all labels shown on the machine
and described in the:
• Safety Instructions Manual
• Installation Manual
• Operations Manual
• Maintenance Manual
Keep all manuals close for easy
reference.
Trained and authorized
personnel are to install, operate
and service this machinery. Do
not allow for operation of the
machine by unqualified
personnel.
Personal protective equipment
must be worn at all times
during machinery operation.
DO NOT REMOVE, DESTROYOR
COVER THIS LABEL.
HYDRAULIC /ACCESSORY CONTROLS
POWERED BYIRONWORKER.
OPERATIONS CONTROL
KEEPOUT
Lockout
power before
servicing.
Hazardous
voltage inside.

3
Signal Word Panel • Machine Back

4
Signal Word Panel • Machine Right
Keep
guards
in place.
Moving
parts can
cut and
crush.
SHEAR/
CRUSH
HAZARD

5
Signal Word Panel • Machine Left
PUSH BUTTON LIMIT SWITCH
FLUID
INJECTION
HAZARD
Fluid under
pressure.
P.P.E.
Required
Hydraulic
accessory
controls
powered by
ironworker.
AUTO CUT AUX LIGHT
Keep
guards
in place.
Moving
parts can
cut and
crush.
SHEAR/
CRUSH
HAZARD
Optional Hydraulic Accesory Pack
NOTICE
When adjusting
Electric Stroke
Control confirm red
light is illuminated
at top of stroke.

6
Danger Panel Warning Panel
Electrical Hazard
This is the electrical hazard symbol. It
indicates there are dangerous high volt-
ages present inside the enclosure of this
product. ONLY qualied, authorized, main-
tenance, service or Certied Electricians
should gain access to electrical panel. Do
not operate this equipment from any power
source that does not match the voltage
rating stamped on the equipment. Refer to
the Manufacturer’s Identication Label for
operational requirements.
Lockout Power
Danger circuits are live. Lockout/Tagout the
upstream power source. Lockout/Tagout
machinery according to Employer proce-
dures.
Voltage (Varies by consumer requirement)
Indication of operating power requirements.
This product should be operated only from
the type of source indicated on the manu-
facturer’s identication label Installation
should be in compliance with applicable
sections of the National Electric Code.
Consult your local building code before
installing.
Phase (Varies by consumer requirement)
Indication of electrical phase requirements.
This product should be operated only from
the type of source indicated on the manu-
facturer’s identication label Installation
should be in compliance with applicable
sections of the National Electric Code.
Consult your local building code before
installing.
Horsepower (Varies by model)
Indication of horsepower requirements. This
product should be operated only from the
type of source indicated on the manufactur-
er’s identication label Installation should
be in compliance with applicable sections
of the National Electric Code. Consult your
local building code before installing.
Hertz (Varies by consumer requirement)
Indication of electrical cycles per second.
This product should be operated only from
the type of source indicated on the manu-
facturer’s identication label Installation
should be in compliance with applicable
sections of the National Electric Code.
Consult your local building code before
installing.
Shear/Crush Hazard
Moving parts can cut and crush. Keep
hands clear while operating. Lockout
power before servicing. Immediately
replace guards after adjustment, repair or
service.
Wear Personal Protective
Equipment
To avoid physical hazard, always wear per-
sonal protective equipment. Wear protec-
tive eyewear, clothing, gloves, footwear,
head-gear and hearing protection while
operating or servicing this machinery.
Fluid Injection Hazard
Hydraulic hoses and cylinders are under
pressure. Pressurized uid can pierce skin
and cause severe injury. To avoid physical
hazard, always wear personal protective
equipment. Keep hands clear while oper-
ating. Lockout power before servicing.
Immediately replace guards after adjust-
ment, repair or service.
Do Not Operate With Guard
Removed
Physical barriers and guards have been
designed and installed to protect the oper-
ator from moving parts that can pinch, cut
and crush. Keep hands clear while oper-
ating. Lockout power before servicing.
Immediately replace guards after adjust-
ment, repair or service to moving parts.
Heat Hazard
To avoid physical burn hazard, always
wear personal protective equipment. Wear
protective clothing and gloves while work-
ing adjacent to or on the affected surface.

7
Notice Panel
Ironworker Operation
This manual outlines the basic functions
associated with typical Ironworker opera-
tions and is neither intended to create a
comprehensive list of, nor describe every
operation possible with an Ironworker
tool. Ironworker machines are designed to
punch, shear and notch mild steel (A36)
plate, barstock and angle. A wide range of
accessories are available to fabricate rod,
square stock, sheet metal and pipe. DO NOT
USE THIS EQUIPMENT FOR ANY PURPOSE
NOT DESCRIBED IN THE MANUALS.
Ironworker machines are dangerous
and require extreme care and caution
in the safe installation, operation and
maintenance of the machinery. Edwards
Manufacturing Company strongly sug-
gests reading and understanding all
manuals associated with the machinery
as well as obtaining certied, techni-
cal, industrial machinery operations
and maintenance training to reduce the
risk of injury. Regardless of the contents
of the machinery manuals Edwards
Manufacturing Company will not be held
liable for accidents caused by lack of
training.
Wear Personal Protective
Equipment
To avoid physical hazard, always wear per-
sonal protective equipment. Wear protec-
tive eyewear, clothing, gloves, footwear,
head-gear and hearing protection while
operating or servicing this machinery.
Forklift Location
This machine is equiped with rated fork-
lift movement points. Do not attempt to
lift the machinery by any other means.
Inappropriate movement of the machin-
ery may result in serious operator injury,
machine damage and will void machine
warranty. Consult the installation manual
for equipment weight ratings. Provide
rated forklift and certied forklift operator
to move machinery to appropriate location.
Refer to Manuals:
Safety, Installation, Operations
and Maintenance
Manuals contain critical instructions
regarding proper procedures for your
machinery. Understand the contents of all
manuals thoroughly. Failure to follow proper
procedures may result in serious operator
injury, machine damage and will void your
machine warranty. Keep manuals close to
the machine for easy reference.
Safety Ground
Safety earth ground location.
Do Not Use Non-Approved
Lubricants
This machine requires lubrication of
moving mechanical parts (grease) and the
maintenance of hydraulic uids. Consult
maintenance manual for specic lubrication
requirements and application or mainte-
nance schedules.
PE
‘Protective earth’, electrical grounding
location.
Additional Graphic
Information
Electric Motor Rotation (Above)
Identication of proper electrical motor
rotation.
Hydraulics
Hydraulic uids must be recycled as
required by local environmental law. Do not
dispose of by adding to the municipal waste
stream.

Installation Manual
07-2018
Original Instructions - IW1001
EDWARDS

1 General
Operator and Supervisor Information
Signal Word Denition
Signal Word Panel
2 Installation Requirements
Environmental Requirements at Work Station
Electrical Requirements at Work Station
Electrical Performance Specication
3 Installing the Ironworker
Receiving the Ironworker
Unpacking/Moving the Ironworker
Anchoring the Ironworker
Electrical Connection of the Ironworker
Installing the Ironworker
Starting Box Wiring
Powering Up the Ironworker
Installation Manual Table of Contents
Operator and Supervisor Information
This is one of four manuals supplied with your machine.
• Installation Manual
• Safety Instructions Manual
• Operations Manual
• Maintenance Manual
READ ALL MANUALS BEFORE OPERATING MACHINERY. Operating
machinery before reading and understanding the contents of all four
manuals greatly increases the risk of injury.
Each of the four machine manuals describes ‘best practices’ in
handling, installing, operating and maintaining your machine. The
contents of each manual is subject to change without notice due to
improvements in the machinery or changes in National or International
standards.
All rights reserved. Reproduction of this manual in any form, in whole
or in part, is not permitted without the written consent of Edwards
Manufacturing Company.
Keep all manuals close to the machine to allow for easy reference
when necessary.
Provide operators with sufcient training and education in the basic
functions of the machine prior to machine operation.
Do not allow for operation of the machine by unqualied personnel.
Edwards Manufacturing Company is not liable for accidents arising
from unskilled, untrained operation.
Do not modify or change the machine without written authorization
from Edwards Manufacturing Company. Unauthorized modication to
a machine may result in serious operator injury, machine damage and
will void your machine warranty.
Never leave a powered machine unattended. Turn machinery OFF
before walking away.
This machine is manufactured for use by able bodied and able minded
operators only. Never operate machinery when tired or under the inu-
ence of drugs or alcohol.
Do not resell, relocate or export to a destination other than to the
original point of sale. Edwards has designed this machine to meet the
standards of the original receiving country and is not liable for meeting
any governing body or performance standards beyond those of the
original receiving country.

1
Signal Word Definition
Indicates a hazardous situation that, if not avoided,
will result in death or serious injury.
Indicates a hazardous situation that, if not avoided,
could result in death or serious injury.
Indicates a hazardous situation that, if not avoided,
could result in mild or moderate injury.
Indicates information considered important, but not
hazard related.
Signal Word Panel on Machine
Critical machine safety information is identied on signal word labels.
Labels are attached adjacent to the potentially hazardous locations of the
machine. Reference the Safety Instruction Manual for additional informa-
tion regarding the potentially hazardous condition identied on the label.
Review ALL labels on the machinery, reference the operational
precautions and safe operations sections within this manual before
any operation activity is initiated.
Failure to read and understand the signal word labels afxed to the
machinery may result in operator death or injury.
WARNING: This product can expose you to chemicals
including Methyl Isobutyl Ketone which is known to the State of
California to cause cancer and birth defects or other reproduc-
tive harm. For more information go to http://www.p65warnings.
ca.gov.
WARNING: Some dust, fumes and gases created by
power sanding, sawing, grinding, drilling, welding and other
construction activities contain chemicals known to the State of
California to cause cancer and birth defects or other reproduc-
tive harm. Some examples of these chemicals are:
• lead from lead based paint
• crystalline silica from bricks, cement and other masonry
products
• arsenic and chromium from chemically treated lumber
Your risk of exposure varies, depending on how often you do
this type of work. To reduce your exposure to these chemicals,
work in a well-ventilated area and work with approved safety
equipment, such as dust masks that are specically designed
to lter out microscopic particles. For more information go to
http://www.p65warnings.ca.gov/ and http://www.p65warnings.
ca.gov/wood.

2
This manual provides installation information for the following
Edwards Ironworkers:
25 Ton 40 Ton 50 Ton
55 Ton 60 Ton 65 Ton
75 Ton 100 Ton 100 Ton DX
120 Ton Elite 110 Elite 110/65 D.O.
Environmental Requirements at Work Station
The work station environment for your Edwards Ironworker must meet
the following minimum requirements:
• Floor area: Assure that the machinery work area provides
for a stable, adequately sized and load rated oor area for
material movement to and from the machinery work stations.
• Shelter: Edwards Ironworkers are designed for indoor use
only. Protect your Ironworking machinery from water, salts
and corrosive elements.
• Lighting: 500LUX (50 footcandles) minimum.
• Operating Temperature: This equipment will operate
correctly in its intended ambient, at a minimum between
+5° C and +40°C.
• Relative Humidity: This equipment will operate correctly
within an environment at 50% RH, +40°C. Higher RH may
be allowed at lower temperatures. Measures shall be taken
by the Purchaser to avoid the harmful effects of occasional
condensation.
• Altitude: This equipment will operate correctly up to 1000m
above mean sea level.
• Transportation and Storage: This equipment will withstand,
or has been protected against, transportation and storage
temperatures of -25°C to +55°C and for short periods up to
+70°C. It has been packaged to prevent damage from the
effects of normal humidity, vibration and shock.
Electrical Requirements at Work Station
Locate your Ironworker directly adjacent to your power supply. Conrm
that power supply is not connected in series with other machinery. Pro-
vide dedicated electrical socket and circuit breaker for each Ironworker
installed. Edwards Ironworkers are protected from voltage variations
provided the variation does not exceed +/- 10% machine rating.
Installation Requirements
Electrical Performance Specication
Machine Motor # Type Brand 60Hz/V FLA 50Hz/V FLA
25 Ton 116676 1Hp 1~ Leeson 60 Hz 115/208-230 12/6 50 Hz 110/220 13/6
40, 50, 55, 60 Ton, 132089 5Hp 1~ Leeson 60 Hz 230 19 50 Hz 208-220 23-22
Porta-Power 132077 5Hp 3~ Leeson 60 Hz 208-230/460 14/7 50 Hz 190/380 16/8
CEM3615T-5 5Hp 3~ Baldor 60 Hz 575 5
65, 75, 100 Ton, 132089 5Hp 1~ Leeson 60 Hz 230 19 50 Hz 208-220 23-22
Elite 110, 140809 7.5Hp 3~ Leeson 60 Hz 208-230/460 22-21/10 50 Hz 190/380 24/12
Elite 110/65 D.O. CEM3710T-5 7.5Hp 3~ Baldor 60 Hz 575 8
141140 7.5Hp 1~ Leeson 60 Hz 230 36
100DX, 120 Ton CEM3714T 10Hp 3~ Baldor 60 Hz 208-230/460 25-24/12
EM3714T-5 10Hp 3~ Baldor 60 Hz 575 10
CEM3714T-50 10Hp 3~ Baldor 50 Hz 220/380/440 28/16/14
CL3712T 10Hp 1~ Baldor 60 Hz 208-230 38

3
Receiving the Ironworker
Edwards Ironworking machinery is fully assembled and is shipped ei-
ther by palletized custom wooden crate or by shrink–wrapped wooden
pallet for ease of transport and receiving.
Inspect the packaging for damage and follow shipping/receiving instruc-
tions as listed on the packaging prior to receiving the Ironworker into
your facility.
When receiving your Ironworker, be prepared to safely move your ma-
chinery with a fork-lift rated for the following equipment weights:
Minimum Machinery Weights
25 Ton 453.6 kg / 1000 lb
40 Ton 861.8 kg / 1900 lb
50 Ton 916.3 kg / 2020 lb
55 Ton 1124.9 kg / 2480 lb
60 Ton 1156.7 kg / 2550 lb
65 Ton 2154.6 kg / 4750 lb
75 Ton 1859.7 kg / 4100 lb
100 Ton 2109.2 kg / 4650 lb
100 Ton DX 2349.6 kg / 5180 lb
120 Ton 2494.8 kg / 5500 lb
ELITE 110 2440.3 kg / 5380 lb
ELITE 110/65 3891.8 kg / 8580 lb
Utilize best practices for fork-lift operation. Handle material as close
to the drive surface as possible with the widest spread and deepest pen-
etration of forks effective to service the pallet. Forks should be adjusted
and locked into the safety detent closest to the maximum available fork
spread.
Unpacking/Moving the Ironworker
Your Edwards Ironworker includes surface and remotely mounted
electrical cabling and hydraulic lines. Exercise caution when removing
the factory supplied packaging. Do not cut electrical wires or hydraulic
hoses.
1. Unbolt/unpack Ironworker from its pallet using a 3/4” (19.05mm)
socket. Wear appropriate personal protective equipment.
2. Lift Edwards machinery using the designated fork lift locations and
appropriately rated lifting equipment.
3. Move the Ironworker to the prepared workstation.
Anchoring Ironworker
Anchor the base of the Ironworker to the workstation oor using four
1/2” (12.7mm) wedge anchor bolts. Anchorage points are the front and
rear of the fork-lift tubes. Secure the machinery with lock-nuts.
In the event the machinery needs to be relocated, reverse procedure.
Electrical Connection
Conrm with a certied electrician that the electrical supply to the
terminal location powering your Ironworker meet the operating speci-
cations (page 2) of the machine prior to electrical connection.
Conrm your electrical supply with the electrical specications of the
machine or accessory listed (page 2), and located on the Ironworker
starter box. It is critical that a qualied electrician install your
machinery as your Warranty protection does not cover incorrect
wiring of electrical components at your site.
Prior to connecting your machine to the dedicated, protected power
supply, match work station wiring to the power supply cable (Owner
supplied) and the starter-box/motor specications on the machinery.
Install connections appropriately. Check for stability of connections.
If wiring through a plug/socket connection at the work station,
match work station wiring to the socket (Owner supplied), plug
(Owner supplied) and the power supply cable (Owner supplied) to the
starter-box / motor specications on the machinery. Install connec-
tions appropriately. Check for stability of connections.
Wire according to the electrical diagrams located within the control
box.
Installing the Ironworker

4
Starting Box Wiring
Provide the electrical schematic wiring diagram (located within
the Ironworker control box) to your Electrician prior to initiating the
electrical hookup of the machine.
Power up the Ironworker
With all stations clear of tools, tooling or debris, power up the Ironworker
by pressing the green button on the starter box. With the power on, your
machine will return to a neutral position.
Cycle the machinery by pressing the foot pedal. If pressure is released
at the foot pedal prior to completing a full stroke, the operating center of
the machinery will return to a neutral position.
If the machinery fails to cycle the motor may be rotating incorrectly. To
ensure the machinery cycles properly simply reverse two of the phase
wires on the machine starter box.
If the machine fails to cycle, power down the Ironworker by pressing the
red button on the starter box, Lockout / Tagout the upstream power and
consult the trouble shooting section of the Operator Manual.

Operations Manual
Serial Number:
07-2018
Original Instructions - IW10003
EDWARDS

1 General
Company Prole
Warranty
Machine Identication
Operator and Supervisor Information
Signal Word Denition
Signal Word Panel
Operational Precautions
Machine Operations
Foreseeable Misuse
Machine Life Cycle
4Operations Diagrams
8 Control Panel
9 Angle Shear Station
Safe Operation
Angle Shear Operation
10 Bar Shear Station
Safe Operation
Bar Shear Operation
11 Electric Stroke Control
Setup
Safe Operation
Electric Stroke Control Operation
12 Punch Station
Setup
Safe Operation
Punch Operation
Punch and Die Operating Clearances
Punch Capacities
Material Multiplier
Punch Tonnage Requirements (Figure 1)
14 Notcher Station
(50/60/65/75/100DX/120 Ton Ironworkers)
Safe Operation
Notcher Operation
Optional Tooling
15 Angle Notcher
16 Auto-Cut Tool
17 Brake
18 Notcher (25/40/55/100Ton)
20 Oversize Punch
21 Pipe Notcher
22 Rod Shear/Multi-Shear
23 241 Punch
24 Accessory Light
25 Hydraulic Accessory Package
26 Troubleshooting
Operations Manual Table of Contents

1
Company Profile
Edwards Manufacturing Company
manufactures a full line of high
quality, low maintenance hydraulic
ironworking machines, associated
tooling and accessories that are
used in the steel fabrication industry.
With proper operation, care, and
maintenance, your Edwards
Ironworker or Hydraulic Accessory
Tool will provide consistent, long-term service. Please take time
to study this Operator’s Manual carefully to fully understand
Ironworker and Hydraulic Accessory Tool safety procedures,
set-up, operation, care, maintenance, troubleshooting and
warranty coverage prior to putting the machine into production.
Any questions not answered within this manual can be directed
to your local Edwards Ironworker dealer or factory representative.
Contact the factory:
Edwards Manufacturing
Company
1107 Sykes Street
Albert Lea, MN 56007
507 373 8206 PHONE
507 373 9433 FAX
www.edwardsironworkers.com
General Questions:
sales@edwardsmfg.us
Service Questions:
service@edwardsmfg.us
Contact your dealer:
Warranty
Edwards Manufacturing Company will, within one (1) year
of date of original purchase (proof of purchase required),
replace F.O.B. the factory, any goods, excluding punches,
dies and shear blades, which are defective in materials or
workmanship provided that the buyer return the defective
goods, freight pre-paid, to the seller, which shall be the
buyer’s sole and exclusive remedy for the defective goods.
Hydraulic components are subject to their manufacturer’s
warranty.
Edwards Manufacturing Company will, within thirty (30) days
of date of original purchase (proof of purchase required),
replace F.O.B. the factory, any punches, dies and/or shear
blades, which are defective in materials or workmanship.
This warranty does not apply to machines and/or components
which have been altered, changed or modified in any way,
or subjected to abusive and abnormal use, inadequate
maintenance and lubrication, or subjected to use beyond
seller recommended capacities and specifications. Edwards
Manufacturing Company shall not be liable for labor costs
expended on such goods or consequential damages.
Edwards Manufacturing Company shall not be liable to
the purchaser or any other person for loss, down-time, or
damage directly or indirectly arising from the use of the
goods or from any other cause. No officer, employee, or
agent of Edwards Manufacturing Company is authorized to
make any oral representations or warranty of fitness or to
waive any of the foregoing terms and none shall be binding
on Edwards Manufacturing Company.
NOTE: Edwards Manufacturing is a division of JPW Industries,
Inc. References in this document to Edwards also apply to
JPW Industries, Inc., or any of its successors in interest to
the Edwards brand.
Machine Identification
Your Edwards Ironworker has been serialized for quality control, product
traceability and warranty enforcement. Please refer to the aluminum
identification tag with engraved serial number, electrical and power
specifications when ordering parts or filing a warranty claim.
EDWARDS

2
This is one of four manuals supplied with your machine.
• Installation Manual
• Safety Instructions Manual
• Operations Manual
• Maintenance Manual
READ ALL MANUALS BEFORE OPERATING MACHINERY. Operating
machinery before reading and understanding the contents of all four
manuals greatly increases the risk of injury.
Each of the four machine manuals describes‘best practices’ in han-
dling, installing, operating and maintaining your machine. The contents
of each manual is subject to change without notice due to improvements
in the machinery or changes in National or International standards.
All rights reserved. Reproduction of this manual in any form, in whole or
in part, is not permitted without the written consent of Edwards Manu-
facturing Company.
Keep all manuals close to the machine to allow for easy reference when
necessary.
Provide operators with sufcient training and education in the basic
functions of the machine prior to machine operation.
Do not allow for operation of the machine by unqualied personnel.
Edwards Manufacturing Company is not liable for accidents arising from
unskilled, untrained operation.
Do not modify or change the machine without written authorization from
Edwards Manufacturing Company. Unauthorized modication to a ma-
chine may result in serious operator injury, machine damage and will
void your machine warranty.
Never leave a powered machine unattended. Turn machinery OFF be-
fore walking away.
This machine is manufactured for use by able bodied and able minded
operators only. Never operate machinery when tired or under the inu-
ence of drugs or alcohol.
Do not resell, relocate or export to a destination other than to the original
point of sale. Edwards has designed this machine to meet the stan-
dards of the original receiving country and is not liable for meeting any
governing body or performance standards beyond those of the original
receiving country.
WARNING: This product can expose you to chemicals includ-
ing Methyl Isobutyl Ketone which is known to the State of California to
cause cancer and birth defects or other reproductive harm. For more
information go to http://www.p65warnings.ca.gov.
WARNING: Some dust, fumes and gases created by power sand-
ing, sawing, grinding, drilling, welding and other construction activities
contain chemicals known to the State of California to cause cancer and
birth defects or other reproductive harm. Some examples of these
chemicals are:
Indicates a hazardous situation that, if not avoided,
will result in death or serious injury.
Indicates a hazardous situation that, if not avoided,
could result in death or serious injury.
Indicates a hazardous situation that, if not avoided,
could result in mild or moderate injury.
Indicates information considered important, but not
hazard related.
Signal Word Panel on Machine
Critical machine safety information is identied on signal word labels. La-
bels are attached adjacent to the potentially hazardous locations of the
machine. Reference the Safety Instruction Manual for additional informa-
tion regarding the potentially hazardous condition identied on the label.
Review ALL labels on the machinery, reference the Safety Instruc-
tions Manual, the operational precautions and the safe operations
sections within this manual before any operation activity is initiated.
Failure to read and understand the signal word labels afxed to the
machinery may result in operator death or injury.
Signal Word Definition
Operator and Supervisor
Information
• lead from lead based paint
• crystalline silica from bricks, cement and other masonry products
• arsenic and chromium from chemically treated lumber
Your risk of exposure varies, depending on how often you do this type
of work. To reduce your exposure to these chemicals, work in a well-
ventilated area and work with approved safety equipment, such as dust
masks that are specically designed to lter out microscopic particles.
For more information go to http://www.p65warnings.ca.gov/ and http://
www.p65warnings.ca.gov/wood.

3
Edwards Ironworkers are designed to punch, shear and notch mild
steel plate, barstock and angle. A wide range of accessories are avail-
able to fabricate rod and square stock, sheet metal and pipe. Edwards
Ironworkers operate by applying hydraulic force to a moving center.
The center moves within a frame in a simple, vertical path and exerts
force through shear blades, punch and dies, notchers, brake dies
or bump-die tooling upon A36 mild steel. Edwards Ironworkers are
designed for single operator use only; unless otherwise identied with
a D.O./Dual Operator designation.
The following pages detail the proper operations procedures for
setting up and safely operating the standard and optional tooling
of your Edwards Ironworker.
Foreseeable Misuse
Do not use this equipment for any purpose not described in this
manual. Using this equipment in ways not described in this manual
could result in death or serious injury to the operator.
Machine Life Cycle
Edwards Ironworkers are designed to be generally free from risk
throughout their life cycle from installation to dismantling and dis-
posal. Consult your local governmental agency for guidelines and pro-
cedures to ensure the safe disposal and recycling of system hydrau-
lics, electronics and metals.
Reasonable, common sense safety precautions should be observed when
operating the Ironworker or hydraulic accessory tool. The following pre-
cautions are described in order of their hazard.
Electrical Hazard
Dangerous high voltages are present inside the electrical enclosure
of this product. Only qualied, authorized, maintenance or service
personnel should gain access to the electrical panel.
Lockout Power
Danger, circuits are live. Lockout / tagout upstream power source
before any maintenance activity is performed.
Shear / Crush Hazard
Moving parts can cut and crush. Keep hands clear when servicing
and maintaining the Ironworker.
Hydraulic Fluid Hazard
Hydraulic hoses are under pressure. Pressurized uid can pierce
skin and cause severe injury. To avoid physical hazard, always wear
personal protective equipment when servicing / maintaining the
Ironworker.
Do Not Operate With Guard Removed
Physical barriers and guards have been designed and installed to
protect the operator from moving parts that can pinch, cut and
crush. If it is necessary to remove guarding when servicing the
Ironworker, immediately replace guards after service and prior to
power being restored to the machinery.
Refer to Manuals
For safe installation, operation and maintenance of the machine,
read:
Installation Manual
Safety Instructions Manual
Operations Manual
Maintenance Manual
Wear Personal Protective Equipment
To avoid physical hazard wear protective eyewear, clothing, gloves,
footwear, head-gear and hearing protection.
Operational Precautions Machine Operations
Table of contents
Other Edwards Power Tools manuals
Popular Power Tools manuals by other brands
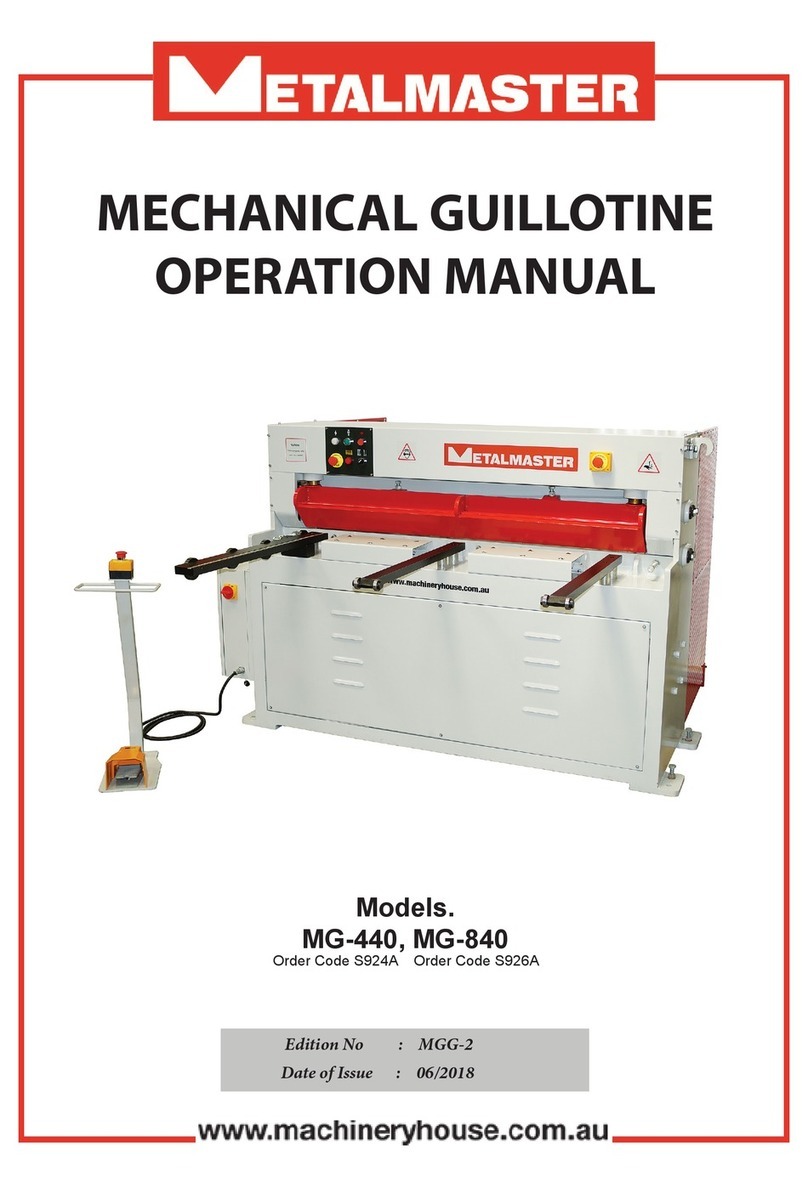
MetalMaster
MetalMaster S924A Operation manual
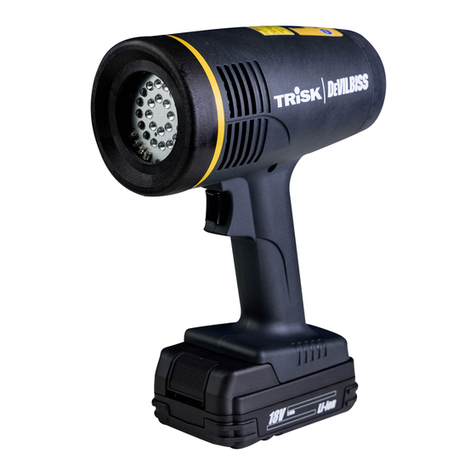
Carlisle Fluid Technologies
Carlisle Fluid Technologies Trisk DeVILBISS Tru-Cure UV-LED Service manual
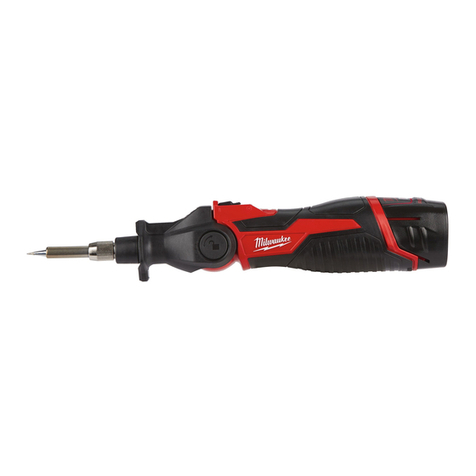
Milwaukee
Milwaukee M12 SI Original instructions
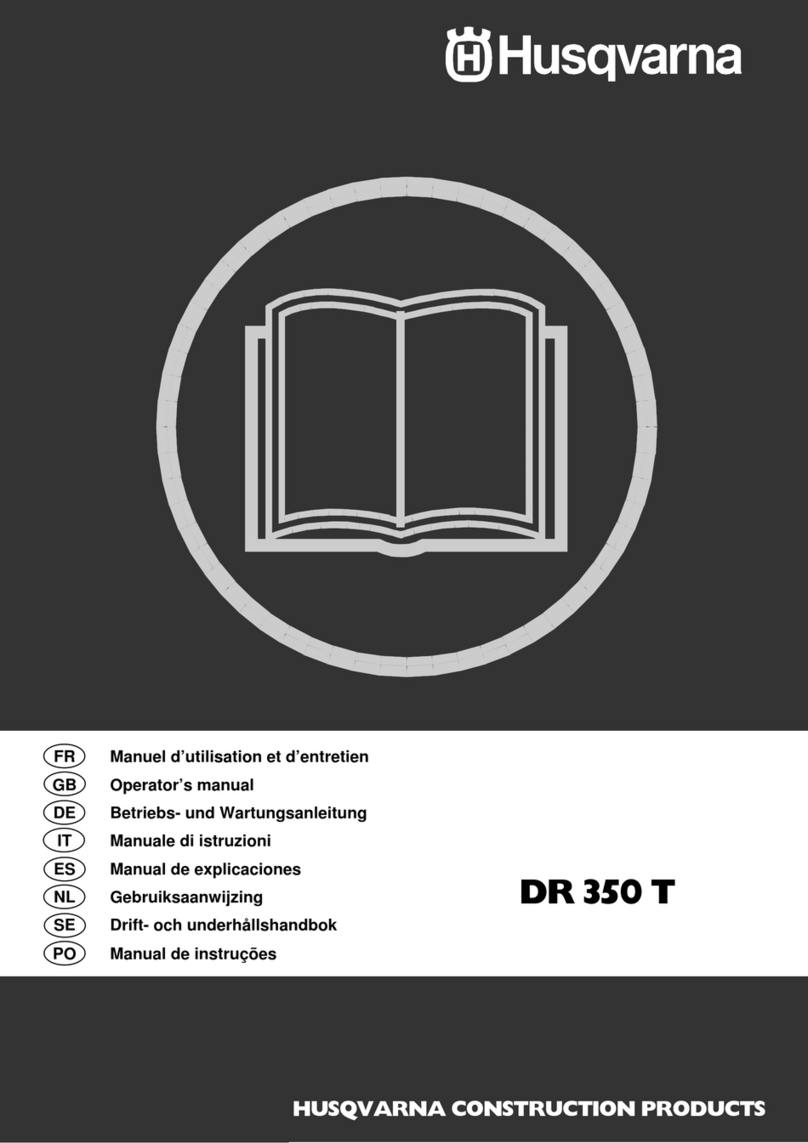
Husqvarna
Husqvarna DR 350 T Operator's manual
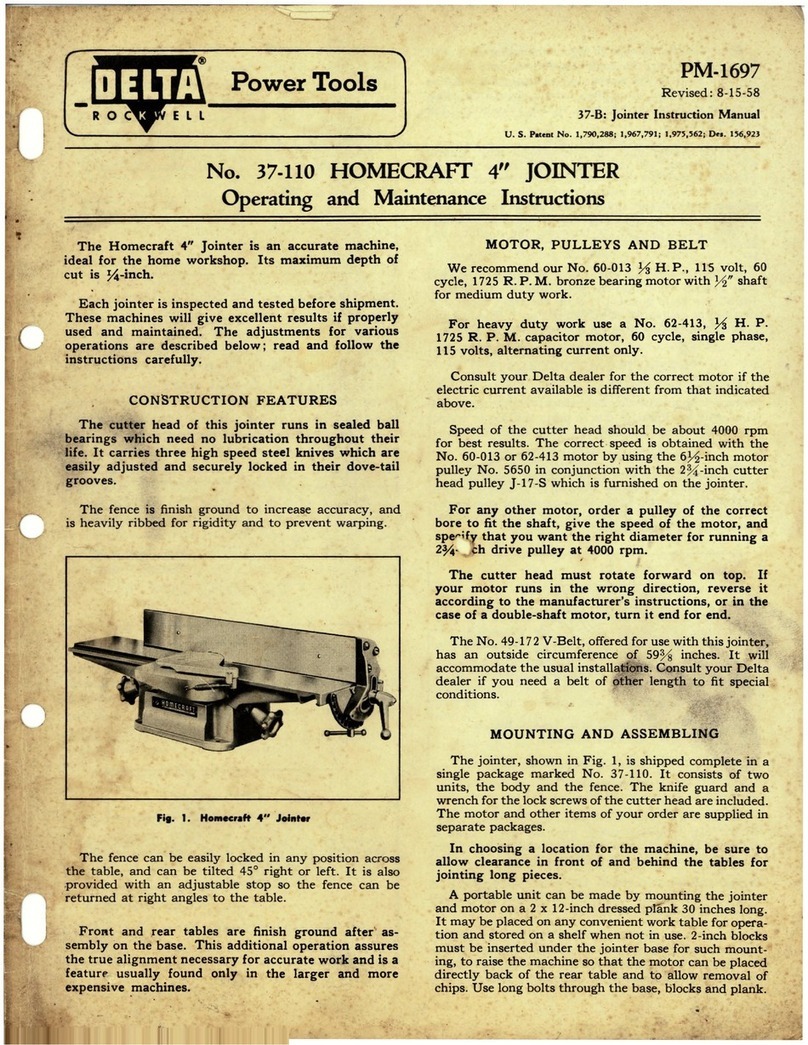
Delta Rockwell
Delta Rockwell 37-110 Operating and maintenance instructions
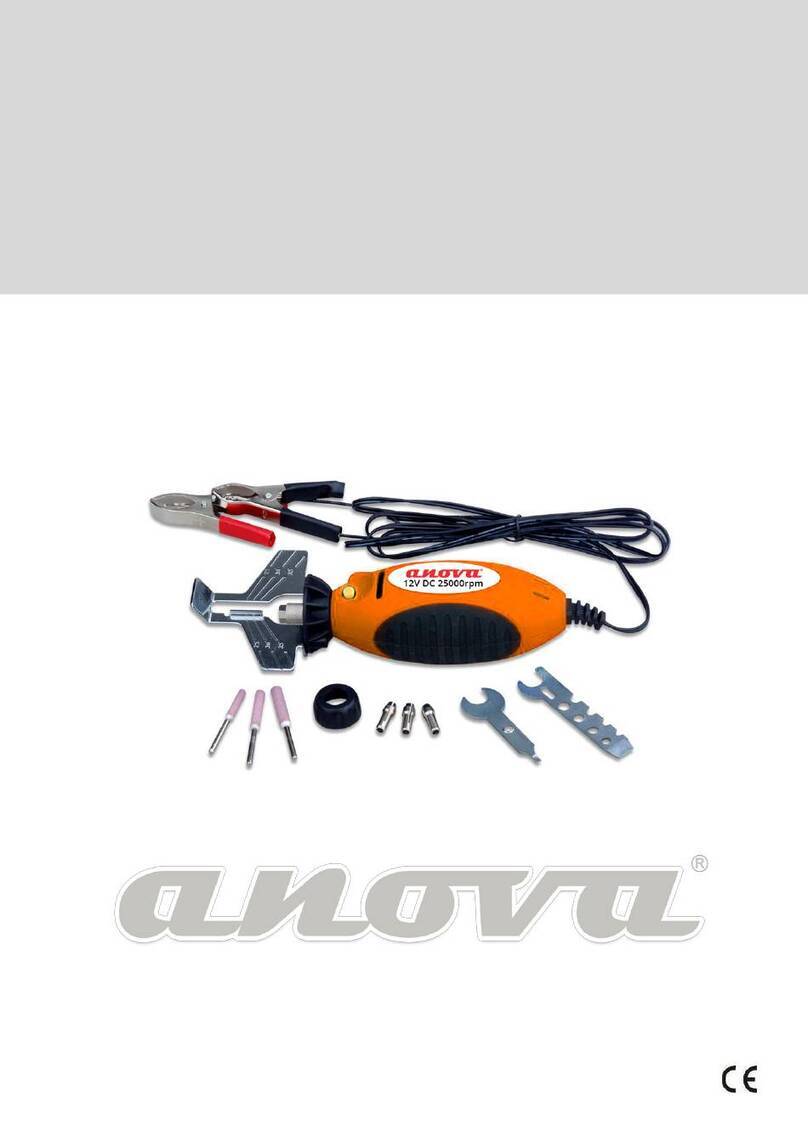
Anova
Anova AF1333 manual