Emotron EMX-R Series User manual

Emotron EMX™- R
DRIVE SYSTEM
Instruction manual
English

Valid for the following models:
EMX-R-15S
EMX-R-15E
EMX-R-25S
EMX-R-25E
EMX-R-35S
EMX-R-35E
Software version 2.x
Emotron EMX-R
DRIVE SYSTEM
INSTRUCTION MANUAL - English
Document number: 01-3333-01
Edition: r3
Date of release: 2010-08-01
© Copyright Emotron AB 2005 - 2010
Emotron retain the right to change specifications and
illustrations in the text, without prior notification. The
contents of this document may not be copied without the
explicit permission of Emotron AB.

The product is protected as follows:
Patents: US 6 628 100; SE 9902821-9
SE 0100814-3; SE 0100814-3; EP 1 366 346; US 7 083 544
Registered design: US 462 937; DE 400 05 393.4; SE 66 630

Emotron AB 01-3333-01r3
Safety instructions
During installation
• Read the instruction manual completely before installation and commis-
sioning.
• The installation must be carried out by qualified personnel.
• General conditions and regulations for the installation and operation of
electrical machinery must be observed.
• Measures to protect against personal injury and damage to the machine
must be taken following local rules and regulations.
• The drive system EMX-R is intended for permanent installation.
• Cables may not be connected or disconnected while the supply voltage is
on.
• Check that the equipment is correctly connected before it is taken into use,
see the instructions in the chapter on Mounting/Connection.
• Faults that arise due to faulty installation or operation are not covered by the
guarantee.
During operation
• Measurements in the control unit, during operation, must only be carried
out on the terminals and only by authorized personnel. NOTE! Great care
must be taken.
• The units may not be opened or disassembled during operation.
During disassembly and scrapping
• The product is designed to comply with the RoHS directive, and shall be
handled and recycled in accordance with local legislations.

Emotron AB 01-3333-01r3

Emotron AB 01-3333-01r3 1
Contents
1. Description.................................................................................. 3
1.1 Introduction................................................................................................. 3
1.2 Product range ............................................................................................. 4
1.3 Operating indicators / built-in functions ................................................... 5
1.3.1 Automatic purging mode / holding torque................................................ 6
1.3.2 Rotation monitor (DIP switch 4)................................................................. 7
1.3.3 Protection of the control unit ..................................................................... 8
2. Mounting/connection.............................................................. 11
2.1 Mounting .................................................................................................. 11
2.1.1 External sensor for rotation monitor (option) ........................................ 12
2.2 Connection ............................................................................................... 12
2.2.1 When switching off .................................................................................. 13
2.2.2 Recommendations with respect to EMC................................................ 13
2.2.3 Priority switch / defrosting / manual control......................................... 14
2.2.4 Manual control using a 10 kOhm potentiometer .................................. 14
2.2.5 Test switch ............................................................................................... 14
2.2.6 Choice of maximum speed ..................................................................... 16
2.2.7 Setting DIP switches................................................................................ 17
2.2.8 Speed controller ...................................................................................... 18
2.2.9 Parallel connection.................................................................................. 18
2.2.10 Heat recovery on cooling – summer/winter switch............................... 19
2.2.11 Analogue output signal (only available on Model E) ............................. 19
2.2.12 Potentiometer with low resistance, 100 Ohm to 5 kOhm
(only available on Model E)..................................................................... 19
3. Maintenance/troubleshooting................................................ 21
3.1 Maintenance ............................................................................................ 21
3.2 Motor diagnosis ....................................................................................... 21
3.3 Troubleshooting ....................................................................................... 22
4. Technical data ......................................................................... 25

2Emotron AB 01-3333-01r3
4.1 The drive system’s operation using different control signals................ 26
4.2 Choice for sizes of drive system and belt pulley .................................... 29
4.3 Accessories and documentation ............................................................ 30
5. Appendix ................................................................................... 31

Emotron AB 01-3333-01r3 Description 3
1. Description
1.1 Introduction
Emotron EMX-R is a series of speed controlled drive systems specially designed
for driving rotary heat exchangers. The drive system consist of a motor and its
associated control unit.
EMX-R completely replaces drive systems EMS-VVX 1, 2-4N, 2-4N/ET and
2-4EM as well as the drive systems EMS-VVX 15, 25 and 35. All mentioned
drive systems have completely been replaced by EMX-R.
The drive system Emotron EMX-R is based, like its predecessor, on the
SR-motors (SR=Switched Reluctance). These motors make it possible to drive
heat exchanger rotors up to 3.5 metres in diameter without gears.
Fig. 1 Emotron Motor and Control unit for rotary heat exchangers.
10-F0810-F08
Control unit
Motor
Heat exchanger rotor

4Description Emotron AB 01-3333-01r3
1.2 Product range
EMX-R is available in three sizes for heat exchanger rotors up to around 3.5 m.
They come in sizes 15, 25 and 35 (for other rotor sizes, please contact the local
distributor or Emotron AB). The control unit sizes are dedicated to the motor
sizes. Control unit EMX-R-15S(or E) could only work with motor
EMX-R-15M and so on.
The control unit is available in two versions, S and E, where Model E has an
extra circuit board for increased functionality.
Built-in functions included in the Model S are:
• Automatic purging operation
• Rotation monitor - integrated electronics or with external rotation sensor
• Alarm relay
•Testswitch
• Priority switch/defrosting
• Heat recovery on cooling with external differential thermostat
In addition to the functions included in Model S, the Model E includes:
• Display of the rotor speed in rpm when the external rotation sensor is con-
nected.
• Analogue output signal proportional to the speed of the motor.
• Heat recovery on cooling with external temperature sensors.
• Input for potentiometer with low resistance, 100 Ohm to 5 kOhm.
• Prepared for serial communication.
Model Operating Indicator Max heat exchanger
rotor diameter (mm)
EMX-R- 15S Two LEDs indicating red or green 1500
EMX-R- 15E LED display
EMX-R- 25S Two LEDs indicating red or green 2500
EMX-R- 25E LED display
EMX-R- 35S Two LEDs indicating red or green 3500
EMX-R- 35E LED display

Emotron AB 01-3333-01r3 Description 5
1.3 Operating indicators / built-in functions
Two LEDs, one red and one green, are used on the Model S for indication,
while the Model E has an LED display as follows:
Table 1 Operating indication – Model S
Green
Slow flashing – Purging mode/Low control signal
Rapid flashing – Operation, the motor rotates continuously
Lit for two seconds – Magnet passing rotation sensor
Lit - RotoSens measures the load on the motor during acceleration
Red Lit or flashing LED indicates alarm, see also the chapter on trou-
bleshooting
Table 2 Operating indication – Model E
Purging mode. Low control signal
The speed of the rotor in rpm. At start a speed is displayed according to
the gear ratio rotor/motor = 1:25. After 2 pulses from the rotation
monitor, the correct speed of the rotor is displayed. Range 0.2–99 rpm.
RotoSens is selected using the DIP-switch (4) and with no rotation
sensor connected
Lit for two seconds when the magnet passes the rotation sensor
RotoSens measures the load on the motor during acceleration
Summer operation/heat recovery on cooling
No rotation monitor - DIP 4 in the OFF position and jumper between
terminal 31-32
An alarm is indicated by the letter F followed by a number. See also the
chapter on troubleshooting.

6Description Emotron AB 01-3333-01r3
1.3.1 Automatic purging mode / holding torque
When the control signal is low, <1.5 V at 0–10 V, the drive system switches to
purging mode. In purging mode the motor shaft turns two revolutions every 10
minutes, which is equivalent to around 30 degrees of rotation by the heat
exchanger rotor. This slow rotation does not provide any significant heat
transfer, but simply serves to keep the heat exchanger rotor clean.
Most of the time the heat exchanger rotor seals keep the rotor stationary, but if
the rotor seals are not touching the rotor and the air flow is not perpendicular to
the rotor, the air flow may cause the rotor to rotate. To prevent unintentional
heat recovery in this situation the motor is automatically used to provide a
holding torque to keep the rotor stationary.
The first time the drive system goes into purging mode after the power is
switched on this holding torque is not activated, since many heat exchanger
rotors do not require an active holding torque to keep them stationary. A rotor
that does require a holding torque will then begin to turn slowly. The drive
system immediately brakes this motion, reducing the speed to zero, and then
applies a constant holding torque to keep the rotor stationary. The drive system
has now learned which rotors require a holding torque, and which do not. The
holding torque is at least 50% higher than the torque required for operation just
before stand still.
If a holding torque has been applied and you grasp the drive belt and try to turn
the heat exchanger rotor by hand, the torque will progressively increase.
The holding torque is generated by passing a current through one of the motor
phases. The higher the torque that is required, the higher the current. This
current produces a noise that gets louder as the current increases. Integrated in
the control unit are three motor protection breakers, one for each motor phase.
The motor protection also protects the motor when the holding torque is
activated.

Emotron AB 01-3333-01r3 Description 7
1.3.2 Rotation monitor (DIP switch 4)
Two different rotation monitors can be selected. The first, RotoSens, which is
an integrated electronic rotation monitor, and secondly a rotation monitor
using an external rotation sensor.
RotoSens uses the motor as the sensor. By allowing the control unit to measure
the load on the motor, you can determine whether the drive belt has broken.
When the drive belt has broken, the motor load will be low. As the heat
exchanger rotors which rotate very easily also give a low load on the motor, it is
necessary to also measure the load during acceleration - you then get a
measurement of the rotor’s torque of inertia. After 2 minutes of operation at a
low load, a load measurement is made during acceleration. If the drive belt is
broken an alarm is given, if it is undamaged the load measurement during
acceleration is repeated again after 24 hours. In cleaning mode, measurement
during acceleration is made once every 24 hours.
The rotation monitor with external rotation sensor requires a magnet fitted on
the periphery of the rotor. The magnet activates the external rotation sensor
once every revolution. Should, for example, a belt break and the rotor stops, the
pulses cease and an alarm is given. The time until the alarm is given is speed
dependent and is 24 seconds at max. speed, 20 minutes at min. speed and about
8 hours in purge mode.
The rotation monitors give alarms through operating indications (display or
LED) and via the alarm relay (external signal). The motor does not stop with
this alarm.
Following rotation monitor functions are available:
• DIP switch 4( see chapter 2.2.7 page 17)in position “OFF” (downwards),
NOTE: In order to use RotoSens the load on the motor should not be too low.
The minimum diameter for the heat exchanger rotor and belt pulley for each
size of the drive system must be:
EMX-R-15: Belt pulley 63 mm, heat exchanger rotor diameter 630 mm
EMX-R-25: Belt pulley 63 mm, heat exchanger rotor diameter 1200 mm
EMX-R-35: Belt pulley 100 mm, heat exchanger rotor diameter 2000
mm
If the belt pulley or heat exchanger rotor are smaller, RotoSens can not be
used, however, the rotation monitor with sensor can always be used.

8Description Emotron AB 01-3333-01r3
means the built-in electronic rotation monitor RotoSens is connected.
• DIP switch 4 in position “ON”(uppwards), means rotation monitor uses an
external rotation sensor.
• No rotation monitoring, DIP-switch 4 also must be set in position “OFF”,
and a jumper must be fitted between terminals 31 and 32 (“oF” is now indi-
cated in the display on Model E).
1.3.3 Protection of the control unit
The control unit is protected by monitoring for both over-voltage and under-
voltage. If the supply voltage goes over or under the allowed limits, an alarm is
triggered and the motor stops. The motor starts again automatically when the
supply voltage returns to its normal value. The alarm is automatically reset.
The control unit has built-in motor protection that protects against
overloading, and external motor protection is not required. Power supply to the
motor is cut in the event of overload. In order to restart the drive system, the
supply voltage to the control unit must be temporarily disconnected for at least
5 seconds.
Built-in short circuit protection protects against short circuits between the
phases of the motor and between the phases and earth.
Table 3 Protection and alarm functions
Protective
function
External alarm
with alarm relay Restart Alarm reset
Supply fault, over-
voltage Yes, immediately Automatic
Automatic
Supply fault,
under-voltage
Pre-alarm, rotation
monitor No Motor not stop-
ped
Rotation
monitor Yes 1)
Pre-alarm, motor
protection/over-
load
No
The system tries
to reset three
times
Automatic

Emotron AB 01-3333-01r3 Description 9
Motor protection/
overload Yes, immediately
Manual, discon-
nect and recon-
nect power
supply
Manual, discon-
nect and recon-
nect power
supply
Short circuit
1) RotoSens - manual, disconnect and reconnect the power supply.
Rotation monitor with sensor - automatic.
Table 3 Protection and alarm functions
Protective
function
External alarm
with alarm relay Restart Alarm reset

10 Description Emotron AB 01-3333-01r3

Emotron AB 01-3333-01r3 Mounting/connection 11
2. Mounting/connection
2.1 Mounting
Both the motor and the control unit are usually mounted in the heat exchanger
housing. In this way, they do not occupy any space outside of the heat
exchanger housing and are well protected during transport. Furthermore, it is
often advantageous from the point of view of interference (EMC) to place the
motor and control unit in the rotor housing. The motor is usually mounted on
a sprung motor support when a V-belt is used. In this way, problems arising if
non-circular rotors are used can be prevented. Vibration dampers should be
mounted between the motor and the motor support so that any vibration from
the motor is not transmitted to the rotor housing.
Fig. 2 Heat exchanger rotor and drive system
10-F0810-F08
Control unit
Motor
Heat exchanger

12 Mounting/connection Emotron AB 01-3333-01r3
2.1.1 External sensor for rotation monitor (option)
The magnet for the rotation sensor is mounted onto the periphery of the heat
exchanger. If the heat exchanger rotor cover is magnetic, the magnet must be
insulated from the cover. The rotation sensor is mounted such that the magnet
passes at a distance of 5–8 mm, see below.
Fig. 3 Mounting of the rotation sensor
2.2 Connection
The motor is delivered with a fixed connected motor cable to simplify
installation of the drive system. The length of the cable is 2.0 m for EMX-R
15M and 2.5 m for EMX-R 25M and EMX-R 35M.
In order to secure the function of the EMX drive system, do not change the
length of the motor cable. This could interfere with the electronic tachometer
that is built into the system.
An external slow-blow fuse rated at <10 A must always be installed. The drive
system does not contain a fuse. Electronic motor protection is built into the
control unit, and monitors the motor at all times. The control unit is protected
from short circuit within the motor.
WARNING! Residual voltage remains for up to 1 minute after
disconnection of the supply voltage.
Rotation sensor
Magnet
5-8 mm
Heat exchanger rotor

Emotron AB 01-3333-01r3 Mounting/connection 13
A safety switch is to be installed between the mains supply and the control unit.
An alarm for loss of power is given if the mains supply is disconnected.
2.2.1 When switching off
When it is desired to switch off the heat exchanger, for example at night, this
can be done using a relay connected in series with the control signal. This relay
interrupts the signal to control signal terminal number 33. In this way, no alarm
about interruption of power supply is given. The control signal can of course
also be reduced to its minimum value, in order to achieve the same result. If the
control signal is low or absent the drive system switches to purging mode.
2.2.2 Recommendations with respect to EMC
In order to fulfil the European EMC Directive 89/336/ECC regarding
electromagnetic compatibility, the following precautions must be taken:
• The motor cable must be mounted as close to the heat exchanger housing as
possible. If the cable is too long, the excess should be collected together in
the form of, for example, a figure “8”. The area enclosed by the cable should
be as small as possible. Electrical tape or cable ties can be used to achieve
this.
Fig. 4 Excess motor cable should be arranged such that the area enclosed is as
small as possible
Special EMC couplings/glands are not necessary. An EMC filter is built into all
EMX-R models.
WARNING! No switch is allowed between the motor and the control
unit.
WRONG
RIGHT

14 Mounting/connection Emotron AB 01-3333-01r3
2.2.3 Priority switch / defrosting / manual control
A preselected speed of rotation can be specified by a potential-free connection
between the priority inputs 34–35. When terminal 34 is connected to terminal
35, the speed is determined by the priority potentiometer, which is located next
to the DIP switches in the control unit. The priority switch has higher priority
than the summer/winter switch (only available on Model E) and the control
signal.
The switch can be used, for example, when cleaning the rotor, defrosting using
an external differential pressostat or for manual control of the speed of rotation.
2.2.4 Manual control using a 10 kOhm potentiometer
It is simple to control the drive system manually by using a 10 kOhm
potentiometer connected as shown in the figure.
2.2.5 Test switch
The control unit is equipped with a test switch, placed under the cover between
terminals 37 and 41. When this switch is in the “ON” position, the motor soft-
starts and the speed increases to the maximum, independently of other signal
sources. When in the “OFF” position (down), the test switch is not operational.
The test switch can also be used to run the motor at maximum speed if, for
example, an external control signal is missing.
Control unit
33
34
37
10 kOhm

Emotron AB 01-3333-01r3 Mounting/connection 15
Fig. 5 Location of terminals, etc.
No. Designation
1 Supply terminal
2Motorterminal
3 Priority potentiometer
4 Control signal terminal
5 DIP switch
6Testswitch
7Alarmterminal
8 Operating indicator for Model S, two LEDS
10-F05
12345678
ON
31
51
LN32 33 34 35 36 37 41 42 43654321
52 53 54 55 56 57 58
J1
IU
1234 56 7
8
Extra circuit board in
the Model E with LED-
display,
E-terminals 51-58
and jumper J1
ON
This manual suits for next models
6
Table of contents
Languages:
Other Emotron DC Drive manuals
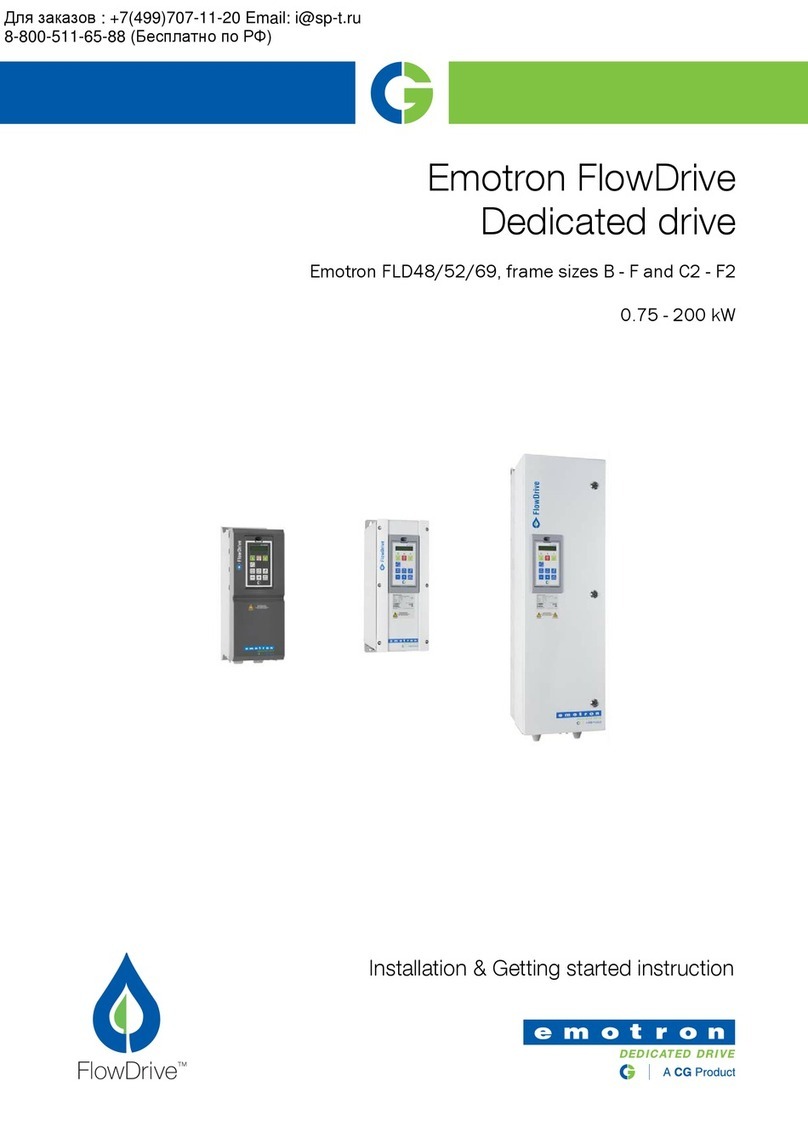
Emotron
Emotron FlowDrive Emotron FLD48 User manual
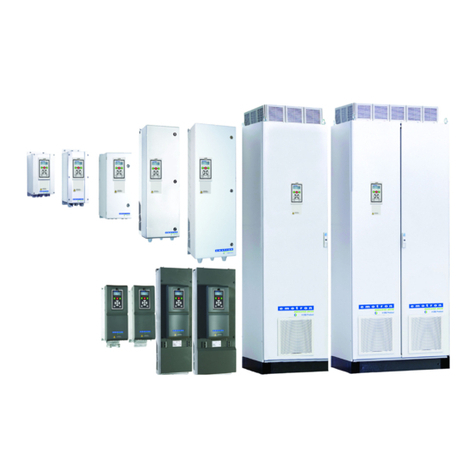
Emotron
Emotron FDU Series User manual
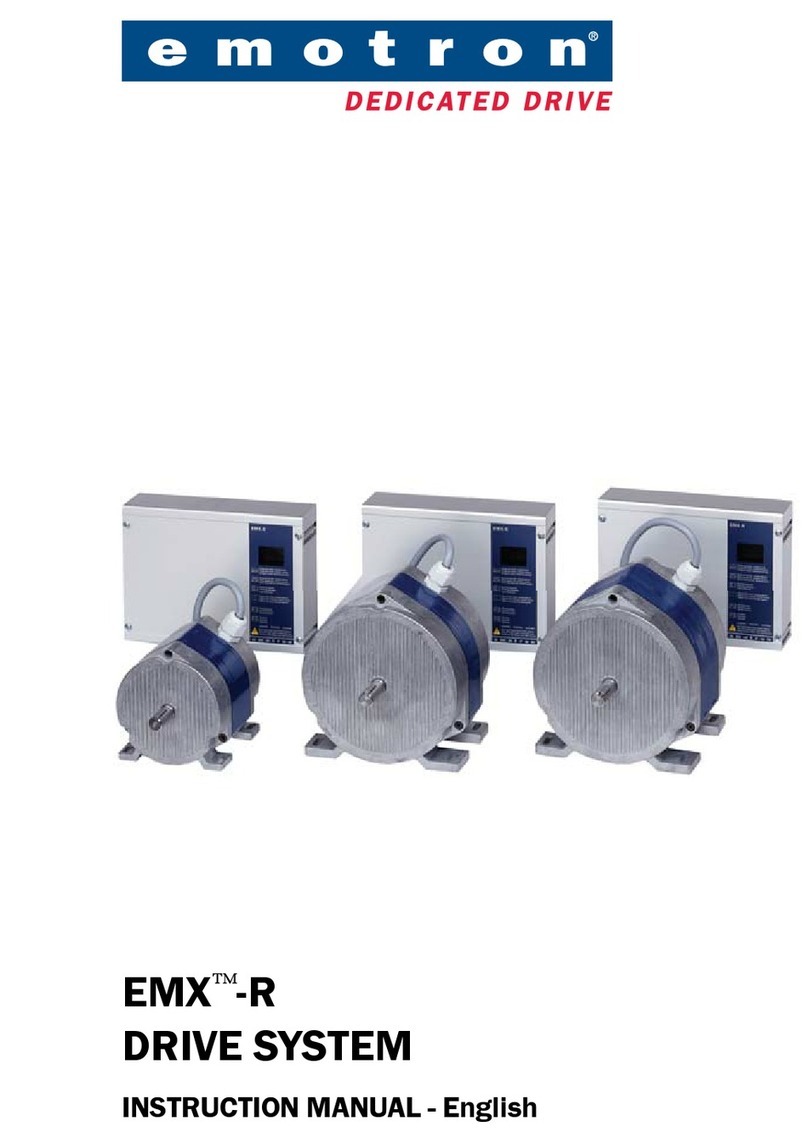
Emotron
Emotron EMX-R-15S User manual
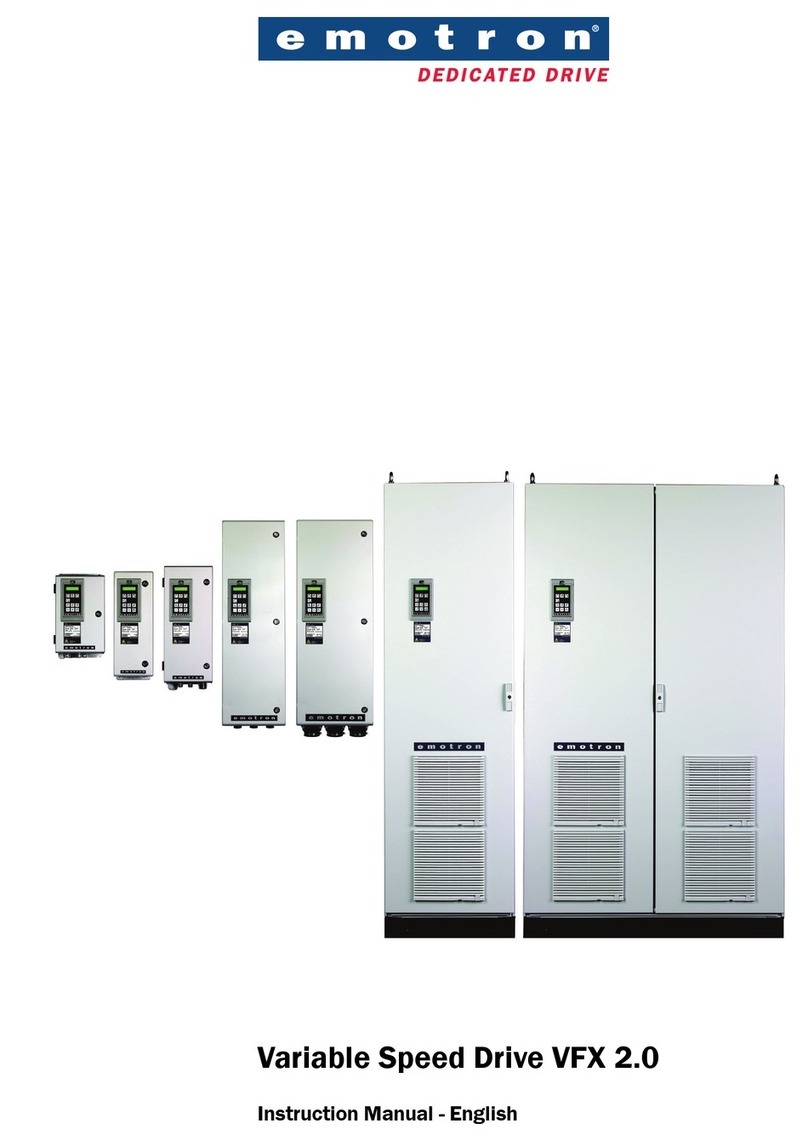
Emotron
Emotron VFX 2.0 User manual
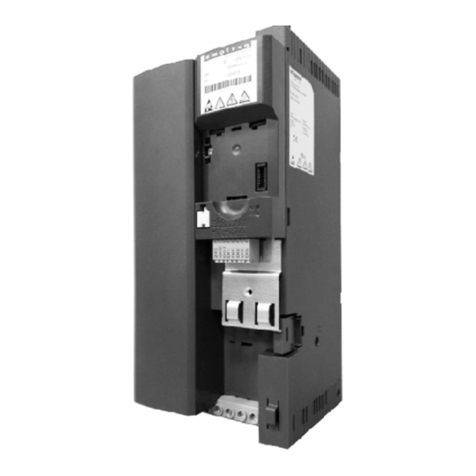
Emotron
Emotron VS30 Guide
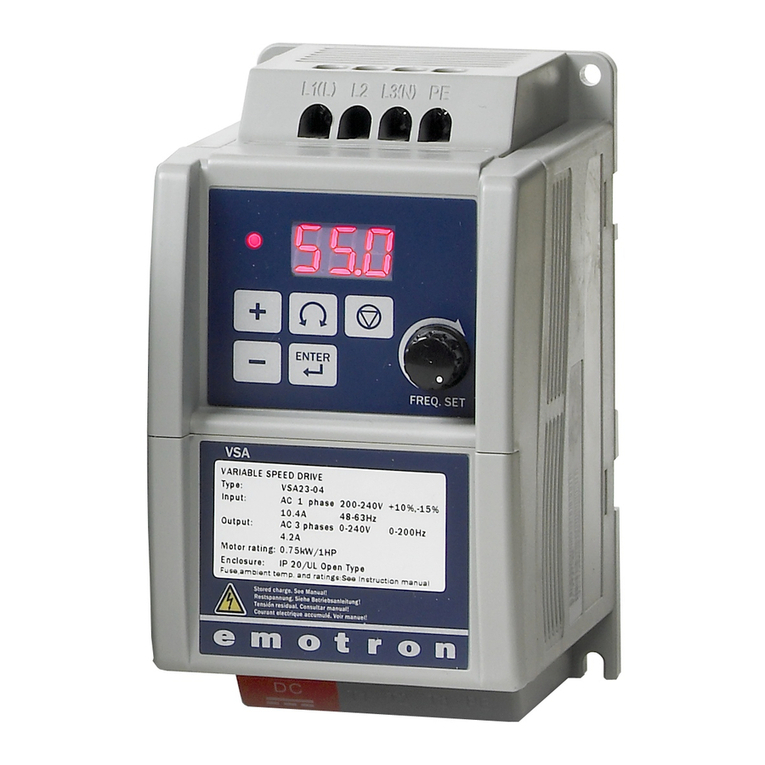
Emotron
Emotron VSA Series User manual
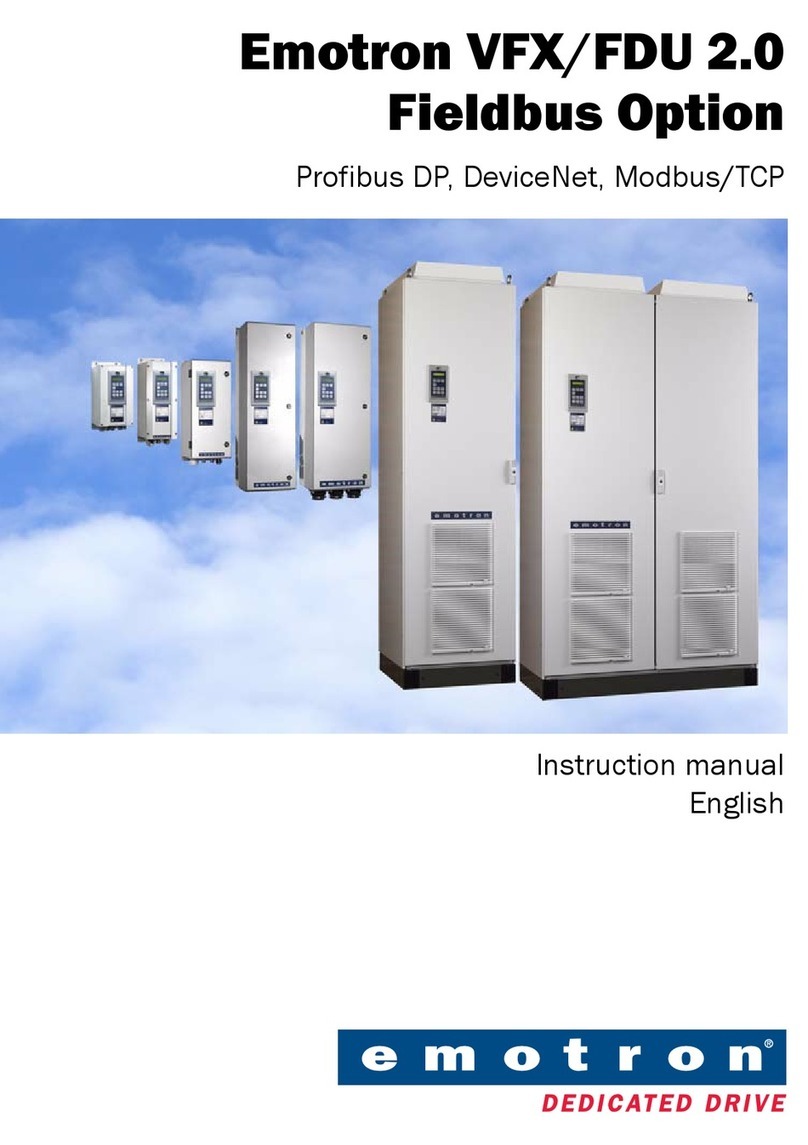
Emotron
Emotron VFX 2.0 User manual
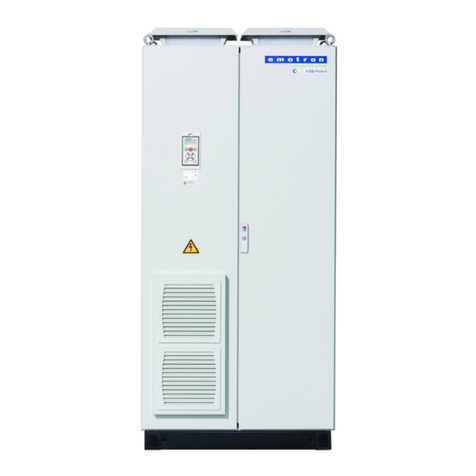
Emotron
Emotron VFX 2.1 User manual

Emotron
Emotron EMX-D User manual
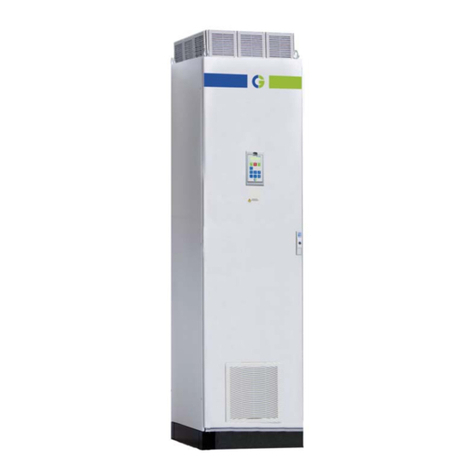
Emotron
Emotron FDU 2.0 User manual