ENCARDIO RITE EDS-71V User manual

BOREHOLE EXTENSOMETER
SYSTEM (BHE) WITH VIBRATING
WIRE/ POTENTIOMETRIC SENSORS
MODEL EDS-71V/P
ENCARDIO-RITE ELECTRONICS PVT. LTD.
A-7, Industrial Estate, Talkatora Road Lucknow, UP - 226011, India | P: +91 522 2661039-42 | Email: geotech@encardio.com | www.encardio.com
International: UAE | Qatar | Bahrain | Bhutan | Europe | USA
India: Lucknow | Delhi | Kolkata | Mumbai | Chennai | Bangalore | Hyderabad | J&K
Doc. # WI 6002.99 R00 | Jun 2011
ONE STOP MONITORING SOLUTIONS | HYDROLOGY | GEOTECHNICAL | STRUCTURAL | GEODETIC
Over 50 years of excellence through ingenuity
USERS’ MANUAL

Users’ Manual EDS-71V/P Single point borehole extensometer
www.encardio.com
Contents
1INTRODUCTION 1
1.1 Applications 1
1.2 Measurement method 1
1.3 Conventions used in this manual 2
1.4 How to use this manual 2
2BOREHOLE EXTENSOMETER (BHE) 4
2.1 General Description 4
2.1.1 Reference head assembly 4
2.1.2 Displacement sensor 4
2.1.3 Connecting rod assembly 6
2.1.4 Anchor 7
2.2 Accessories 8
2.2.1 Junction box 8
2.2.2 Cable 8
3INSTALLATION OF SINGLE POINT BOREHOLE EXTENSOMETER 9
3.1 Site preparation before installation 9
3.2 Check sensor before installation 9
3.3 Procedure 12
3.4 Tools & accessories required for installation 17

Users’ Manual EDS-71V/P Single point borehole extensometer
Page | 1
1 INTRODUCTION
Encardio-rite model EDS-71V single point borehole extensometer using vibrating wire sensors is a
precision instrument designed to help civil engineers and geologists in measurement of deformation of rock
mass and adjacent or surrounding soil. Together with anchor bolt load cells and tape extensometer, it is
an essential piece of equipment for investigation and monitoring of foundations, slopes & embankments
and for studying behaviour of rock around underground cavities, tunnels and mines.
NOTE: Same manual to be used for model EDS-71P single point borehole extensometer using
potentiometric sensors. Make special note of the following:
Diameter of model EDE-PXX potentiometric sensor is 16 mm whereas diameter of Model EDE-VXX is
12.7 mm. This requires adaptor cum guide plate (6) and link plate (16) in figure 2.2 to be different in
the two assemblies.
Manual readout unit for EDE-PXX is model EDI-53P, whereas for model EDE-VXX is model EDI-51V.
For Sample test certificate of model EDE-PXX refer to page 3-3. Sample test certificate for model EDE-
VXX is given on page 3-2.
1.1 Applications
To determine how roof or wall of mine, underground cavity or tunnel behaves during excavation.
To study effectiveness of the roof/wall support system of a mine, underground cavity or tunnel.
To predict potential roof or wall falls before they actually occur. Roof or wall falls in underground cavities
are almost invariably preceded by measurable sags as the strata opens up and the movement usually
occurs at an increasing rate as fall conditions are approached. Unsuspected roof and wall falls may
result in serious accidents and may require costly patch-up and repair operations.
To measure and monitor movements in slopes and foundations due to excavation of underground
cavities or due to construction of heavy structures like concrete, rockfill, masonry or earth dams over
the foundation.
Suitable for upward or downward sloping hole using fibreglass or stainless steel AISI-410 connecting
rods.
Model EDS-71V/P has following options:
Required borehole for installation of single point extensometers is φ50 mm. Diameter at the mouth of
borehole is increased to 63 mm (300 mm depth for 50 mm displacement sensor or 430 mm depth for
100 mm displacement sensor and 560 mm for 150 mm displacement sensor).
The displacement is measured electronically by using a vibrating wire displacement transducer model
EDE-VXX and a readout system model EDI-51V or data acquisition system model EDAS-10. The
displacement is measured using potentiometric sensor model EDE-PXX with an indicator EDI- 53P
1.2 Measurement method
The displacement is measured electronically by using a vibrating wire displacement transducer model
EDE-VXX and Potentiometric displacement transducer model EDE-PXX with read out system model EDI-
51V and EDI-53P respectively or data acquisition system model EDAS-10.

Users’ Manual EDS-71V/P Single point borehole extensometer
Page | 2
Dimensional details of sensor
Displacement Overall length of VW sensor
(in closed position)
Overall length of Pot. sensor
(in closed position)
50 mm 290 mm 325 mm
100 mm 420 mm 425 mm
150 mm 550 mm 525 mm
The sensor shaft is fixed to female thread in connecting rod through a sensor lock nut (18), link plate (16),
sensor tightening nut (17) and a reference button (15) - refer to figures 2.1 and 2.2. The outside body of
sensor is fixed to a adopter cum guide plate (6) in the flanged housing at the face of the borehole. The
system is rugged and is protected by a protecting cover (19). Flange assembly (5) .Nipple is an integral
part of flanged housing (22) through which cable for sensors can be taken to a junction box (23) and then
through a multi-core cable to any distant location.
NOTE: Encardio-rite uses the convention that depth of anchor is calculated as the distance from the
mouth of hole to near end of anchor.
CAUTION: Never rotate shaft of displacement sensor in respect to the outside body. This will permanently
damage the sensor. During installation pull / push or pull shaft only axially. A pin has been
provided at the end of displacement sensor that sits flush in a groove in sensor body. During
assembly operation and while using spanners for tightening, keep sensor in closed position
with pin seated inside groove such that no torque is exerted on its shaft and there is no
rotational movement.
1.3 Conventions used in this manual
WARNING! Warning messages calls attention to a procedure or practice, that if not properly followed
could possibly cause personal injury.
CAUTION: Caution messages calls attention to a procedure or practice, that if not properly followed may
result in loss of data or damage to equipment.
NOTE: Note contains important information and is set off from regular text to draw the users’ attention.
1.4 How to use this manual
The users’ manual is intended to provide sufficient information for making optimum use of borehole
extensometers in different applications.
To make the manual more useful we invite valuable comments and suggestions regarding any additions
or enhancements. We also request to please let us know of any errors that are found while going through
this manual.
NOTE: The installation personnel must have a background of good installation practices and
knowledge of the fundamentals of geotechnics. Novices may find it very difficult to carry on
the installation work. The intricacies involved in installation are such that even if a single
essential but apparently minor requirement is ignored or overlooked, the most reliable of
instruments will be rendered useless.
A lot of effort has gone in preparing this instruction manual. However the best of instruction
manuals cannot provide for each and every condition in the field, which may affect the
performance of the instrument. Also, blindly following the instruction manual will not guarantee
success. Sometimes, depending upon field conditions, the installation personnel will have to
consciously depart from the written text and use their knowledge and common sense to find
the solution to a particular problem.

Users’ Manual EDS-71V/P Single point borehole extensometer
Page | 3
The manual is divided into a number of sections, each section containing a specific type of information.
The list given below tells you where to look for in this manual if you need some specific information. It is
however recommended that you read the manual from the beginning to the end to get a thorough grasp of
the subject. You will find a lot of unexpected information in the sections you feel you may skip.
For description of vibrating wire borehole extensometers manufactured by Encardio-rite: See § 2.1
“Borehole extensometers”.
For layout drawings of vibrating wire borehole extensometers: See figures 2.1 – 2.2.
For installation of single point borehole extensometers: See § 3 “Installation of single position borehole
extensometer”.
For tools & accessories required for installation: See § 3.4 “Tools & accessories required for installation”.

Users’ Manual EDS-71V/P Single point borehole extensometer
Page | 4
2 BOREHOLE EXTENSOMETER (BHE)
2.1 General Description
Borehole extensometer (BHE) measures extension (displacement) that takes place with time in a bored
hole or in several bored holes in a rock mass. The Encardio-rite BHE essentially consists of one anchor
and a reference plate. Anchor is set in same borehole or in different boreholes drilled adjacent to first
borehole. The BHE helps to accurately measure distance between anchor with respect to reference plate
and thus monitor with passage of time their relative displacement in respect to each other. It is usually
assumed anchor is in stable ground and so any change in anchor spacing is interpreted as sag of roof bed,
movement of side wall or slope, settlement of foundation etc.
Model EDS-71V/P BHE is specially designed to monitor a relative displacement of a single anchor
economically over any other borehole extensometer. At locations where access to mouth of borehole is
easily available, mechanical measurement of displacement by model EDS-64U/D is economical and
reliable. Displacement readings are taken by a micrometer depth gage by measuring depth of reference
button at near end of connecting rod from a reference plate.
Model EDS-71V/P borehole extensometer basically comprises following major sub-assemblies:
Reference head assembly
Vibrating wire displacement sensor/ potetiometric sensor
Connecting rod assembly (fibreglass or stainless steel AISI 410)
Anchor (reinforced bar or packer)
Grouting and vent tube as required
2.1.1 Reference head assembly
Refer to figures 2.1& 2.2 for details of single point BHE reference head assembly. Reference head
assembly is supplied packed from factory as per items listed in figure 2.1. The sensor is separately supplied
but it is very convenient to assemble it at site inside the reference head assembly along with the connecting
rod ends according to instructions given in § 3.
The reference head assembly consists of a flanged housing (5), an adaptor cum guide plate (6) is fixed to
the near end with help of M4x8 grub screws (8a). A grub screw M4x5 (8b) is provided in adopter cum guide
plate to fix the sensor. The reference plate (14) is fixed to guide plate with an allen head screw M5x12 and
one stainless steel centre pillar (13) in such a way that the holes marked (1,G.V )on reference plate is
aligned to the respective holes of guide plate. The holes 1,G,V are used for connecting rod, grout and vent
tube respectively. The removable cover (19) is threaded to the adopter cum guide plate (6) to protect the
entire assembly.
2.1.2 Displacement sensor
The Encardio-rite model EDE-VXX/PXX linear displacement sensor is used in model EDS-71V/P borehole
extensometer for transmitting the mechanical displacement to a remote observation room. It basically
consists of a vibrating wire sensor having a stroke of 50 , 100 or 150 mm.
The retractable shaft of the sensor having a male thread of M6x12 is connected to the connecting rod
through a link system. The sensor is provided with an integral 1 m long φ 4 mm four core cable with cores
in red, black, green and white. Red and black cores are for frequency signal while green and white are for
temperature monitoring through a thermistor.
Refer to data sheet 1085-03 P on model EDE-VXX vibrating wire linear displacement transducer (20) for
detailed description and specifications.
The potentiometric sensor model EDE-PXX is used in place of vibrating wire sensor if required.

Users’ Manual EDS-71V/P Single point borehole extensometer
Page | 5
Adaptor cum guide plate
6
Rubber bush
Allen head screw, M5x12
Hollow bolt
Long hollow bolt
Grub screw, M4x8
11
12
10
8.a
9
7
Washer
Vent tube
Connecting rod
Grout tube
Flanged housing
Description
Item
4
5
3
1
2
Anchor
Displacement sensor
Expandable anchor
Junction box assembly
Reference button
Reference plate
Sensor lock nut
Sensor tightening nut
Link plate
Center pillar
17
19
18
21
23
20
Cover
16
15
14
13
22 Nipple with chuck nut
Grub screw, M4x5
8.b
Figure 2.1 - Single point BHE
reference head assembly
Figure 2.2 - Single point BHE
detailed assembly
18
15
16
17
1
V
G
PLAN (without cover)
22
23
3, 4
20
Grout
1
2
Ø50
21
Displacement
100 mm
50 mm
A
378
248
B
225
185
150 mm 510 285
Ø65
Ø130
Ø52
AB
12
11
10
5
6
a plastic bag
Wrapped in
15,16
17,18
24 &
25
8.a
8.b
13
19
14
7
9

Users’ Manual EDS-71V/P Single point borehole extensometer
Page | 6
2.1.3 Connecting rod assembly
2.1.3.1 Fibreglass connecting rod assembly
Fibreglass connecting rod assembly (2) comprises of a fibreglass rod of specified length protected inside
an outer continuous nylon tube. The rod has two end connectors. One end connector has a male thread
and fits into anchor (1). Other end connector with a female thread is for connecting to reference button
(15). Displacement of connecting rod end is transferred through a link plate (16) to the displacement sensor
(20) with the help of a sensor-tightening nut (17) and a sensor lock nut (18). Components 15, 16, 17 and
18 are packed inside the reference head assembly in a plastic bag.
The fibreglass assembly is illustrated below in figure 2.3
Anchor end of nylon tube is firmly sealed with anchor to prevent any grout from leaking in. Other end of
nylon tube is firmly sealed in reference head assembly with help of rubber bush (10), washer (11) and
hollow bolt (12) and long hollow bolt
Proper sealing in reference head assembly is especially necessary for upwards to horizontally slanting
holes to prevent any grout leaking into reference head assembly during grouting.
The outer nylon tube allows free movement to fibreglass rod and reference button even after borehole is
grouted.
NOTE: Fibreglass rods are generally more suitable for vertically upward holes as compared to
downward holes. This is because in vertically upward holes the connecting rod is in tension;
whereas in downward holes it is in compression, resulting in sagging or buckling. Longer the
extensometer, greater may be the sagging or buckling.
Shorter the extensometer, better is accuracy of measurement of relative displacement
between anchors. In deeper boreholes, use of stainless steel connecting rods is
recommended, as they are more rigid.
Design Engineer should carefully consider what type of connecting rod to use taking into
consideration field conditions and accuracy of measurement required. Actual performance of
rods is determined by site conditions and it is recommended to conduct some field tests to
arrive at a proper conclusion.
2.1.3.2 Stainless steel AISI 410 connecting rod assembly
Stainless steel AISI 410 connecting rods of 8 mm diameter are available in standard lengths of 1m, 2 m
and 3 m with a M6 x 12 mm male thread at one end and a M6 x 15 mm female thread at other end. These
are connected together at site for positioning anchor at the correct depth from mouth of borehole. Thread
sealant Loctite 290 or equivalent is used between threads to firmly grip connecting rods to each other.
To give an example, in case depth of a particular anchor from the mouth is 14 m, use four connecting rods
of 3 m length and one of 2 m length. Similarly, in case depth of anchor from the mouth is 25 m, use eight
connecting rods of 3 m length and one connecting rod of 1 m.
Nylon Tube (OD - 10 x 1 thk)
Fibre glass rod assly.
Nylon Tube (OD - 12 x 1 thk)
Figure 2.3 – Fibreglass connecting rod assembly

Users’ Manual EDS-71V/P Single point borehole extensometer
Page | 7
On the near end of assembled connecting rods a standard 14 cm spacer with male thread on one side and
female on the other side is always provided. The reference button (15) is threaded into the female end of
this spacer. The male thread of connecting rod most distant from the mouth of the borehole fits into the
anchor (1).
PVC tubing 14 mm od x 10 mm id in 3 m length is provided for enclosing connecting rods at time of
assembly. One end of these tubes is swaged to form a male extender such that male and female ends of
successive PVC tubes can be conveniently assembled to each other using any PVC jointing compound in-
between. After jointing, the joint should always be checked by pulling and then wrapped with PVC tape to
make it leak proof. The outer PVC tubing allows free movement to connecting rods and reference button
even after borehole is grouted.
The furthest PVC tubing is firmly sealed to the anchor to prevent any leakage of grout into the PVC tube..
This 3 m long PVC tubing is cut by 50 mm from the plain end to make it convenient for successive
connecting rods and PVC tubings to be connected together.
The near end of the PVC tubing is firmly sealed in flanged housing (5) with help of rubber bush (10), washer
(11) and hollow bolt (12). The PVC tube should be cut such that when sealed in flanged housing, its face
extends around 20 mm beyond rubber bush (10). Proper sealing in reference head assembly is especially
necessary for upwards to horizontally slanting holes for preventing any grout for leaking into reference
head assembly during grouting.
2.1.4 Anchor
2.1.4.1 Following type of anchors are available from Encardio-rite:
Encardio-rite groutable anchors φ 20 mm x 500 mm long usually used for hard rocks. These are
lowered down or pushed in borehole along with connecting rod of appropriate length and fixed in
position by cement grout. The connecting rod is protected from cement grout by enclosing in plastic
tubing, thus allowing for its free movement. Groutable anchors may also be installed in vertical
boreholes or holes inclined upwards. Installation of groutable anchors in holes inclined upwards needs
special precautions to retain grout and prevent it from flowing out of borehole.
Encardio-rite packer anchors usually used for soft rocks and soil. These are lowered down or pushed
in borehole along with connecting rod of appropriate length and fixed in position by pumping cement
grout into the packer for taking a firm grip with the surroundings. Refer to consultant for use with
fibreglass connecting rods.
NOTE: Encardio-rite uses convention that depth of anchor is calculated as distance from mouth of
hole to near end of anchor.
2.1.4.2 Groutable anchor for fibreglass option
2.1.4.3 Groutable anchor for AISI 410 rod option (swaged end of PVC tube slides over it)
Figure 2.4
Figure 2.5
PVC pipe (od-14x2 thk., 30 long)
Pin Anchor

Users’ Manual EDS-71V/P Single point borehole extensometer
Page | 8
2.1.4.4 Packer anchor
Packer anchor with geotextile bladder inflated with grout is generally used in fractured rock or soil.
2.2 Accessories
2.2.1 Junction box
Cable can be extended from the sensor to the observation room. Alternatively a junction box is available
for termination of cable from sensor and transmitting the signal through a multi-core cable to the
observation room.
2.2.2 Cable
For range of cables available, refer to ‘Accessories’ in Consolidated Catalogue on
http://www.encardio.com.
Figure 2.7- Junction box
To grout pump
Grout tube
Hollow bolt
Washer
Rubber bush
Grout
Hose clamp
PVC tube
Extension rod
Tie rod
Soil
PCB # 14-05004
Figure 2-6

Users’ Manual EDS-71V/P Single point borehole extensometer
Page | 9
3 INSTALLATION OF SINGLE POINT BOREHOLE EXTENSOMETER
NOTE: Procedure described below is for installing single point borehole extensometer with fibreglass
connecting rods for in a downward sloping hole using groutable anchors. For installation in
an upward to horizontally sloping borehole, or for using packer anchors, modify procedure
suitably.
Due to many permutations and combinations in type of BHE required by users and widely
varying conditions encountered from site to site, the procedure described is suggestive and
may be used as a guide only. The installation personnel will have to use experience in
devising the best method of installation.
3.1 Site preparation before installation
3.1.1 Drill hole of 50 mm diameter to a depth of 0.8 m more than specified length.
NOTE: In case borehole extensometer is to be mounted horizontally and design permits, it is
desirable to provide a downward slope of 5oor more to borehole. This facilitates grouting of
anchors as grout can easily flow in.
3.1.2 At mouth of borehole, increase diameter of drilled hole to 63 mm up to a depth of 300 mm for 50
mm displacement sensor or 425 mm for 100 mm and 560 mm for 150 mm displacement sensor.
This is for wrapping outside of housing with rags or jute cloth strips soaked in cement during
installation.
3.1.3 Insert reference head assembly centralised in the 63 mm borehole. Taking holes on flange as
reference, drill four holes 12 mm diameter x 125 mm deep for fastening flange to borehole. Remove
reference head assembly from borehole.
3.1.4 Wash hole clean up to bottom by pumping in fresh water.
3.2 Check sensor before installation
The cable from Vibrating wire sensor is four wired. Red and black cores are for frequency signal while
green and white are for temperature monitoring through a thermistor. The cable from Potentiometric sensor
is also four wired. Red and black cores are for (+) and (-) excitation while green and white are for (+) and
(-) output. Check working of sensor as follows:
3.2.1 Connect sensor to portable indicator model EDI-51V (for vibrating wire sensor) and EDI 53P (for
Potentiometric sensor. With displacement shaft in retracted position enter sensor constants from
Test Certificate and set reading in engineering units at zero mm.
NOTE: Data entry of sensor constants in the EDI-51V/ EDI 53P will later on be used to set sensor in
flanged housing during installation process.
3.2.2 Using a scale, move the shaft by about 25 mm. The indicator should read around 25 mm. This
change in reading ensures proper functioning of displacement sensing system. The sensor can
now be installed in the housing assembly (5) when required.
Figure 3.1 – Displacement sensor
Displacement (mm)
V W sensor – L in mm.
Potentiometeric. sensor – L in mm.
50
290
325
100
420
425
150
550
525
L

Users’ Manual EDS-71V/P Single point borehole extensometer
Page | 10
TEST CERTIFICATE
Customer
ABC Corporation
PO #
PHP 050-05 October 28, 2005
Instrument
V.W Displacement sensor for Bore hole
Extensometer
Serial number
05508
Date
09.11.200
5
Range
50 mm
Temperatur
e
25°C
Input
Observed value
Average
End Point
Poly
Displacement
Up1
Down
Up2
Fit
Fit
(mm)
(Digit)
(Digit)
(Digit)
(Digit)
(mm)
(mm)
0.00
2297.4
2294.0
2294.0
2296
0.00
0.00
10.00
3437.8
3432.1
3432.1
3435
10.08
10.00
20.00
4570.7
4567.8
4567.8
4569
20.12
20.01
30.00
5700.8
5695.9
5695.9
5698
30.11
30.00
40.00
6824.1
6821.4
6821.4
6823
40.05
39.99
50.00
7947.7
7947.7
7946.0
7947
50.00
50.01
Error (% fs)
0.23
0.03
Digit
f ² X 10E-3
Linear gage factor (G)
8.848E-03
mm/digit
Thermal factor(K)
-0.003
mm/°C
Polynomial constants
A=
1.4276E-08
B=
8.7037E-03
C=
2.0061E+
01
Displacement "D" is calculated with the following equation:
Linear
D(mm) =G(R1-R0) - K(T1-T0)
Polynomial
D(mm) = A(R1)² + B(R1) + C - K(T1-T0) -D0
R1= current reading & R0 is initial reading in digit.
D0= Initial reading in mm
Zero reference (initial position) in the
field must be established by recording the initial reading R0(digit)
along with temperature T0(°C) just after installation.
Note
Zero displacement reading given in above calibration chart is taken at 3 mm
from mechanical
zero
Pin configuration/wiring code:
Red & black
Signal
Green & white
Thermistor

Users’ Manual EDS-71V/P Single point borehole extensometer
Page | 11
TEST CERTIFICATE
Date : 15.12.2008
Customer
:
P.O.no.
:
Instrument
:
Potentiometric displacement sensor
Model
:
EDE-P05
Serial number
:
XXXXX
Range
:
50 mm
Input Observed value Average Calculated
Error
Displacement Up1 Up2 displacement
(mm)
(Volts)
(Volts)
(Volts)
(mm)
% FS
0.00
0.0550
0.0580
0.0565
0.00
0.00
7.00
0.3250
0.3260
0.3255
6.95
0.11
17.00
0.7150
0.7140
0.7145
16.99
0.01
27.00
1.0990
1.0990
1.0990
26.92
0.16
37.00
1.4870
1.4870
1.4870
36.95
0.11
48.00
1.9150
1.9150
1.9150
48.00
0.00
Max error (%FS) :
0.16
Linear gage factor (G) :
25.83
mm/Volts
Displacement "D" is calculated with the following equation:
Linear
:
D(mm) =G(R1-R0)
R1 = current reading & R0 is initial reading in Volts
Zero reference (initial position) in the field must be established by recording the
initial reading R0 (Volts) just after installation.
Note : 1)
Zero displacement reading given in above calibration chart is taken
at around 3 mm from mechanical zero.(slider fully in).
2)
For best linearity use the displacement transducer only upto 3 mm
from its mechanical displacement limits (ends)
Pin configuration/wiring code:
Red :
Excitation '+ 5 V DC'
Black :
Excitation 0 V
white :
Output high (0 - 2 V DC)
Green :
Output 0 V
Checked by
Tested by

Users’ Manual EDS-71V/P Single point borehole extensometer
Page | 12
CAUTION: Never rotate shaft of displacement sensor in respect to the outside body. This will permanently
damage the sensor. During checking pull / push shaft only axially. A pin has been provided at
end of displacement sensor that sits flush in a groove in sensor body.
3.3 Procedure
3.3.1 Refer to figure 2-1 and 2.2. Remove cover (19) and take out polythene bag that contains requisite
quantity of reference buttons (15), link plates (16), sensor tightening nut (17), locknuts (18), M6 x
100 or 125 mm or 150 mm cheese head screw (24) depending upon type of housing and locking
nuts (25).
3.3.2 Remove guide plate (6) with 2 mm Allen key and hollow bolts (12) from holes marked 1, G and V
from flanged housing (5) and place latter flat on clean ground around 1 m away from borehole.
CAUTION: Always mark a line between flanged housing (5) and adopter cum guide plate (6) before
dismantling so that it can be aligned properly while assembling the sensor (20).
3.3.3 Cut grout and air vent tubes ( Φ12 mm outside dia.x 1 mm thick supplied in coil form) to required
length. Generally, lower end of grout tube is kept at a level higher than anchor. Grout should cover
anchor to mouth or be around 1 m from face of borehole whichever distance is less. To determine
length of grout tube, ensure that around 1.5 m is required outside the reference plate (14) for ease
in attaching it to grout pump. Air vent tube should be projected around 0.3 m is outside reference
plate (14). Lower end of air vent tube should always be at a higher level than lower end of grout
tube. While inserting anchor in borehole, lowest end of grout tube is tied with a cable tie to the
connecting rod
NOTE: In upward to horizontally sloping borehole, grout tube should be about 2 m longer than
specified depth of anchor and taped around 100 mm below far end of anchor. Tape grout tube
every 2 m with a PVC tape to plastic tube of connecting rod assembly to prevent it from
swinging loose.
NOTE: In upward to horizontally sloping borehole, air vent tube should be about 1.5 m longer than
specified depth of anchor and taped around 100 mm above far end of anchor. Tape air vent
tube every 2 m with a PVC tape to the nylon tube of connecting rod assembly to prevent it
from swinging loose. Top end of air vent tube should be at a level higher than anchor.
CAUTION: In upward to horizontally sloping borehole, care should be taken that air vent tube is taped
around 100 mm beyond rear end of anchor and should not get detached. This is very
necessary for the grout to fill in up to end of anchor.
3.3.4 Guide grout tube through hollow bolt (12), washer (11) and rubber bush (10) of hole marked G at
bottom of flanged housing and corresponding holes on guide plate (6) and reference plate (14),
the grout tube is around 1.5 m outside the reference plate. Similarly, guide the air vent tube through
hollow bolt of hole marked V at bottom of flanged housing; the vent tube is around 0.3 m outside
the reference plate (14).
3.3.5 Tighten corresponding hollow bolt (12) with spanner size 21 mm and long hollow bolt (7) to firmly
grip nylon grout and air vent tubes but not to squeeze them.
CAUTION: Always tight hollow bolts (12) 2 nos. firstly and then long hollow bolt (7) at the end.
CAUTION: In upward to horizontally sloping borehole, be particularly careful in tightening the hollow bolts
(12) properly as grout may leak through into the reference head assembly during the grouting

Users’ Manual EDS-71V/P Single point borehole extensometer
Page | 13
process.
3.3.6 Screw male end connector of fibreglass rod assembly (2) to groutable anchor (1). In the process,
the nylon tubing will also get firmly gripped to groutable anchor. A little grease may be used for
ease in assembly.
3.3.7 Lower groutable anchor into borehole till near end of fibreglass rod is remaining around 1 - 1.5 m
outside face of borehole. Trim nylon sleeve such that female connector and fibreglass rod is
exposed by around 100 mm from connector end.
WARNING! Fibreglass rod is supplied in coil form using cable ties. It is very stiff material and must be
carefully handled when unwinding as the end may snap back and cause personal injury.
3.3.8 Guide end of fibreglass rod through hollow bolt (12), washer (11) and rubber bush (10) of hole
marked ‘1’ at bottom of flanged housing (5) and corresponding holes on guide plate (6) with end
protruding around 80 mm from guide plate (6) face. To do this the fibreglass rod will have to be
bent. Tighten hollow bolt on connecting rod such that it does not slip into the borehole.
To Pump
25
24
4 holes Ø15
at 105 PCD.
Item
Description
24
M6 x 100 mm or 125 mm or 150 mm cheese head screw cheese
25
M6 lock nuts – 3 nos. per cheese head screw
Figure 3.2 – Setting arrangement for 1 point BHE

Users’ Manual EDS-71V/P Single point borehole extensometer
Page | 14
NOTE: Holes on top of flanged housing are marked
clockwise with identification numbers 1, G
respectively and V in middle. As an Encardio-rite
convention, serial number ‘1’ always
corresponds to anchor.
As an additional precaution, make a note in a
diary of orientation of serial number ‘1’ with
geographical North.
NOTE: When BHE is installed on a side wall or roof,
extension is generally expected. In such a case,
it may be desirable to set connecting rod end as
close as possible to reference plate (14).
Similarly, when BHE is installed in a vertically
down borehole settlement is generally expected.
In such cases, it may be desirable to set
connecting rod end as close as possible to guide
plate (6). In other cases, it may be necessary to
set connecting rod end in middle such that either
compression or tension can be monitored.
In other words, if only compression is expected,
set zero reading of sensor by extending shaft by
around 10 mm. If only extension is expected, set
zero reading of sensor by extending shaft by
around 10 mm less than sensor range. If
required, sensor may be set in mid position. As
a precaution, never set the sensor at the very
end.
A set of 100 mm or 125 mm or 150 mm long
cheese head screws (24) and lock nuts (25) is
provided for this purpose.
3.3.9 For any other required range, set distance ‘C’
accordingly. For example, Assemble cheese head
screw (24) and locking nuts (25) as shown in figure
3.2. Slightly loosen hollow bolts (12) related to hole
‘1’. Adjust end of connecting rod in required position
and tighten the lock nuts (25). To set connecting rod
ends, refer to table above.
Sensor range
(A)
Setting range
(B)
Shaft end from
guide plate top
(C)
50 mm ± 25 mm 45 mm
100 mm
± 50 mm
70 mm
150 mm ±75 mm 95 mm
Reference
plate
Guide plate
Downward borehole
+40
0
-10
~10
Tube face
30
Mid position borehole
+25
0
-25
~10
Tube face
45
Upward borehole
-40
0
+10
~10
Tube face
60

Users’ Manual EDS-71V/P Single point borehole extensometer
Page | 15
3.3.10 When installing a BHE with 50 mm displacement in a vertically downward borehole, settlement is
expected and setting range specified may be – 10/+ 40 mm. In such a case connecting rod end
distance from guide plate top (6) should be set at (45 – 15) i.e. 30 mm.
NOTE: If readout unit shows negative displacement reading, movement of structure is away from
borehole face and vice versa.
3.3.11 Re-assemble adopter cum guide plate (6) with grub (8.a) and (8.b) taking care that holes marked
‘1’ ‘G’ and ‘V’ are aligned in reference plate (14), adopter cum guide plate (6) and flange housing
(5).
3.3.12 Tighten hollow bolts (12) with spanner size 21 mm and long hollow bolt (12) to firmly grip nylon
tube but not to squeeze or hinder free movement of female end connector inside the nylon tube.
NOTE: In upward to horizontally sloping borehole, tighten hollow bolts (12) particularly carefully as
grout may leak through into the reference head assembly during the grouting process.
NOTE: Take care that extensometer assembly does not drop into borehole accidentally. It is
advisable to secure it properly by attaching a safety rope to the anchor.
3.3.13 Wrap rags or jute cloth strips soaked in quick setting cement water mix outside flanged housing
(5) to build up approximately 5 mm thick layer. Lift and insert housing in borehole using a to and
fro screwing motion sealing the annular space between housing and borehole.
3.3.14 Fix expandable anchors (21) in holes drilled earlier for securing flanged housing with the M12 nuts
and washers provided. Give enough time to let flanged housing set in borehole.
3.3.15 Connect grout pipe to grouting machine or pump, grout till the entire cavity is filled and grout flows
out of air vent pipe. Be very careful that grout flowing out of air vent tube does not get into the
flanged housing and makes the installation messy.
3.3.16 Pump clean water through the grout tube till clear water comes out of air vent tube. This will keep
the grout tube clean for topping up the grout later on.
NOTE: Give sufficient time for grout to set.
CAUTION: Clean up grout and air vent tubes with clean water after grouting operation is complete as in
§ 3.3.16 above
NOTE: Check Engineer for cement water proportion to be used in grout. Composition of grout to be
used depends upon site conditions. In case of hard rock, 50 kg of cement with 30 kg of water
has been successfully used at some project sites.
NOTE: Grout should cover anchor closest to the mouth or be around 1 m from the face of borehole
whichever distance is less. This can be checked by inserting a φ3 mm wire into borehole
through vent pipe.
CAUTION: Please ensure that no grout overflows into the flanged housing. In case it overflows, it may
get into the protective nylon tubing and jam the setting rods.
3.3.17 Again pump grout into the system after setting period of grout is over to ensure that all anchors
are properly grouted. During setting, heavier grout has a tendency to settle down leaving water at
top with a possibility that anchor is not properly grouted. Rule this possibility out by pumping in
grout again and ensuring that any such water at the top is pumped out through the air vent tube
and replaced by grout.
CAUTION: To get correct displacement readings, ensure that anchor is properly grouted. This problem
may be particularly faced in case of anchor in downward boreholes and in upward holes where
with cement in grout settling down, there may only be water around the anchor.

Users’ Manual EDS-71V/P Single point borehole extensometer
Page | 16
NOTE: For very deep hole, staged grouting may be necessary. It is always best to consult grouting
engineer at site and take his advice
NOTE: Packer anchor does not require the borehole to be fully grouted. It is recommended to use a
hand grout pump for better control. It is important to pump water first to water saturate packer
geotextile sufficiently. Pump grout until pressure builds up sufficiently to around 400 to 500
kPa. Let pressure dissipate for a few minutes and then pump again till a distinct pressure is
felt. Recommend grout mixture is 1 part cement and 1 part water by weight. Kink and tape
grout tube to retain pressure and disconnect pump. Clean pump thoroughly.
3.3.18 Remove screws (24) and lock nuts (25). Remove reference plate (14) and centre pillar (13) Cut
and remove grout and vent tubes. Round edges of grout and vent tube with a hand file. Clean
reference head assembly properly. Reassemble reference plate with centre pillar to guide plate.
3.3.19 Remove guide plate (6).
3.3.20 Insert sensor (20) in flanged housing (5) taking care that the cable is carefully routed out to be
eventually connected to the junction box (23). Secure sensor to adopter cum guide plate (6) with
grub screws (8a) ensuring that tube face (refer to figure 3.1) is around 10 mm extended from face
of adopter cum guide plate (6).
NOTE: Since only one sensor is being used therefore cable identification mark tagging is not required.
Pull shaft of sensor and assemble to connecting rod end with reference button (15), link plate
(16), sensor tightening nut (17) and locknut (18).
3.3.21 Screw in the sensor to connecting rod clearly noting position of extensometer ‘1’.
CAUTION: Never rotate shaft of displacement sensor in respect to the outside body. This will permanently
damage the sensor. During installation pull or push or pull shaft only axially. A pin has been
provided at the end of displacement sensor that sits flush in a groove in sensor body. During
assembly operation and while using spanners for tightening, keep sensor in closed position
with pin seated inside groove such that no torque is exerted on its shaft and there is no
rotational movement.
CAUTION: Do not use thread sealant on any thread while mounting the sensor as it may have to be
replaced at a later date.
3.3.22 Check displacement reading of sensor with model EDI-51V/EDI 53P read-out. Reading would be
around specified initial reading (refer to § 3.3.11). Set reading precisely by loosening respective
sensor with grub screws (8.a), repositioning sensor in adopter cum guide plate (6) and again
tightening grub screw.
3.3.23 Reset zero reading in EDI-51V/EDI 53P to final set position of sensor. Subsequent readings will
determine relative displacement between anchor and reference plate.
3.3.24 Take initial readings with help of depth micrometer. It is recommended to note date, time and
temperature while taking the initial reading.
NOTE: A proper record of depth readings with depth micrometer should be permanently maintained.
This is very important because sometimes it becomes necessary to verify the data from
electronic sensors.
3.3.25 Attach nipple (22) to socket of flanged housing and fix junction box assembly (23) with cable from
sensor routed to junction box.
3.3.26 Connect leads to respective connector pins in junction box.
NOTE: For transmitting signals to observation room, 4 core, 6 core, 12 core or 20 core cables are
available from Encardio-rite.

Users’ Manual EDS-71V/P Single point borehole extensometer
Page | 17
3.3.27 Replace cover (19) over guide plate (6).
NOTE: Model EDS-71V/P BHE can be used as a mechanical system in case electronic measurement
is not required. In such a case, BHE is installed without the electronic sensor. Later on, in
case in some of the installations continuous monitoring is required, the electronic sensor can
be installed at a later date.
3.4 Tools & accessories required for installation
The following tools and accessories are required for proper installation of the multi position borehole
extensometer:
3.4.1 Soldering iron 25 watt
3.4.2 Rosin 63/37 solder wire
3.4.3 Thread sealant (Loctite 290 or equivalent)
3.4.4 Cable jointing compound
3.4.5 Acetone (commercial)
3.4.6 Spanner 6, 8, 10, 18, 21,22,24, 30 and 25
3.4.7 Allen key 2, 4
3.4.8 Screw driver (tip size 6 x 0.8 and 3 x 0.5 mm)
3.4.9 Phillips head screw driver (tip size 2 mm)
3.4.10 Hacksaw with 150 mm blades
3.4.11 Cable cutter
3.4.12 Wire stripper
3.4.13 Insulated pliers 165 mm
3.4.14 150 mm flat file
3.4.15 Toothbrush
3.4.16 Wire brush
3.4.17 Cloth for cleaning (lint less)
3.4.18 Cello tape/Insulation tape
3.4.19 Micrometer depth gage 100 mm range
3.4.20 Digital indicator model EDI-51V
3.4.21 Digital multi-meter
This manual suits for next models
1
Table of contents
Other ENCARDIO RITE Measuring Instrument manuals
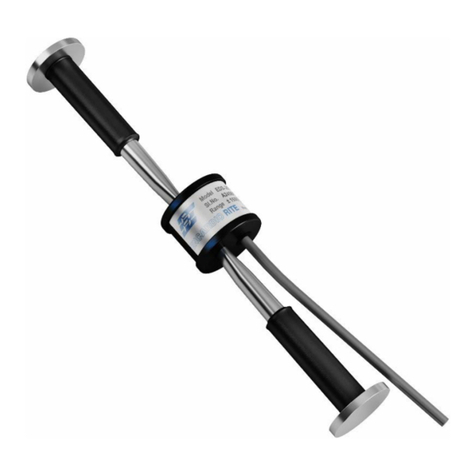
ENCARDIO RITE
ENCARDIO RITE EDS-20V-E User manual

ENCARDIO RITE
ENCARDIO RITE EAN-90M User manual
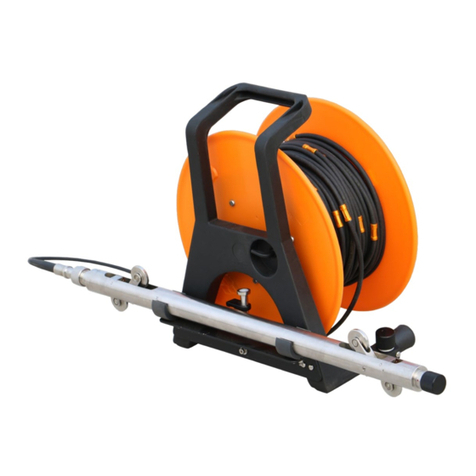
ENCARDIO RITE
ENCARDIO RITE EAN-26MH User manual

ENCARDIO RITE
ENCARDIO RITE ESM-12S User manual
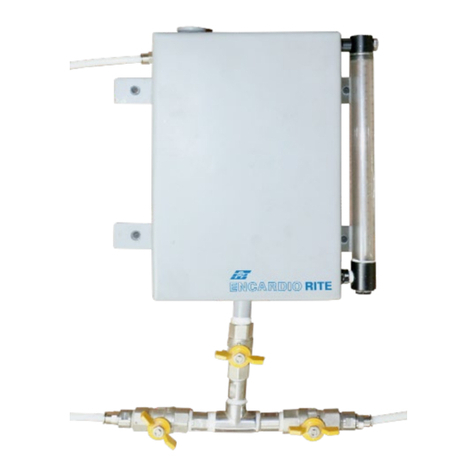
ENCARDIO RITE
ENCARDIO RITE ESM-40S User manual
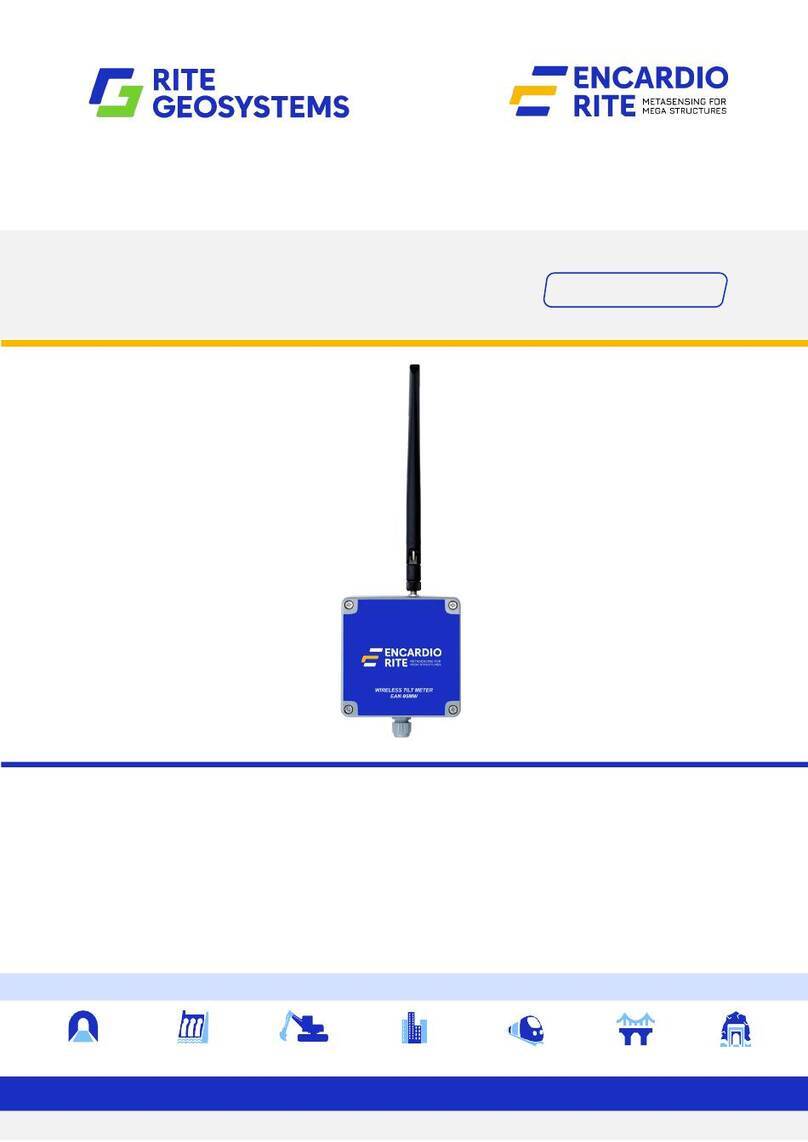
ENCARDIO RITE
ENCARDIO RITE EAN-95MW User manual
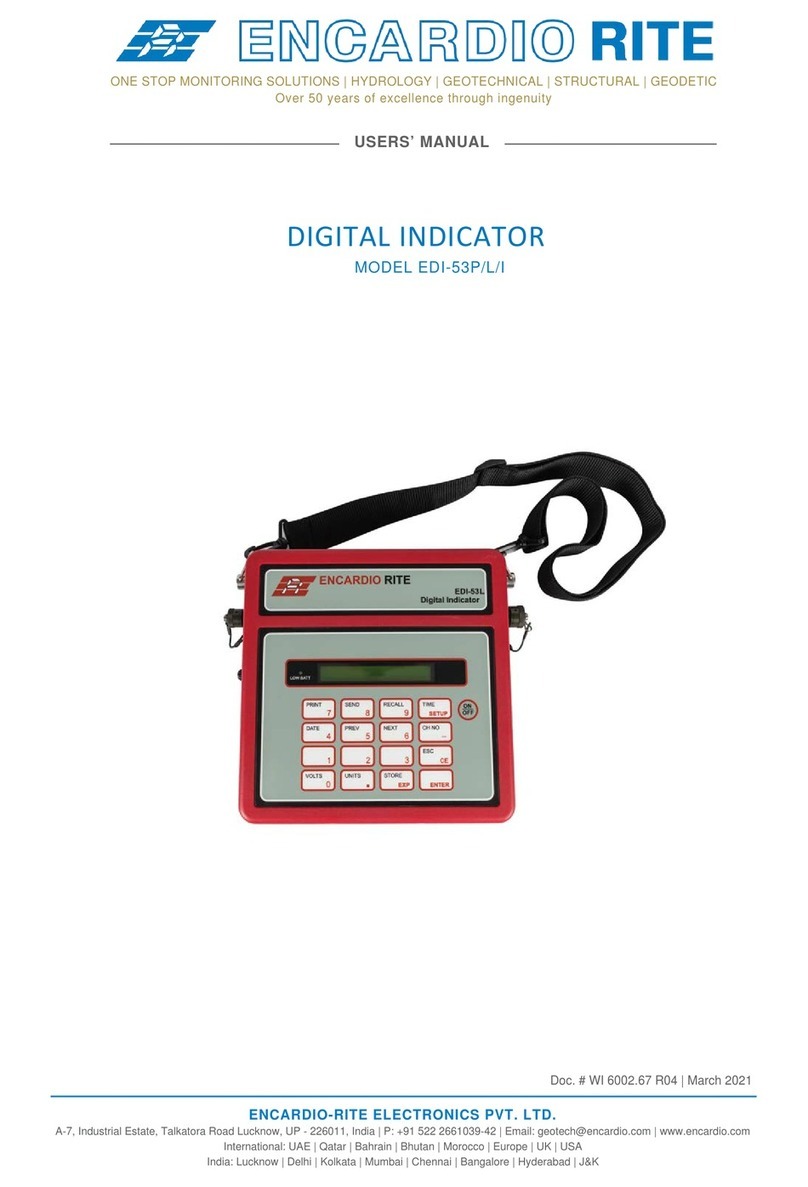
ENCARDIO RITE
ENCARDIO RITE EDI-53P/L/I User manual
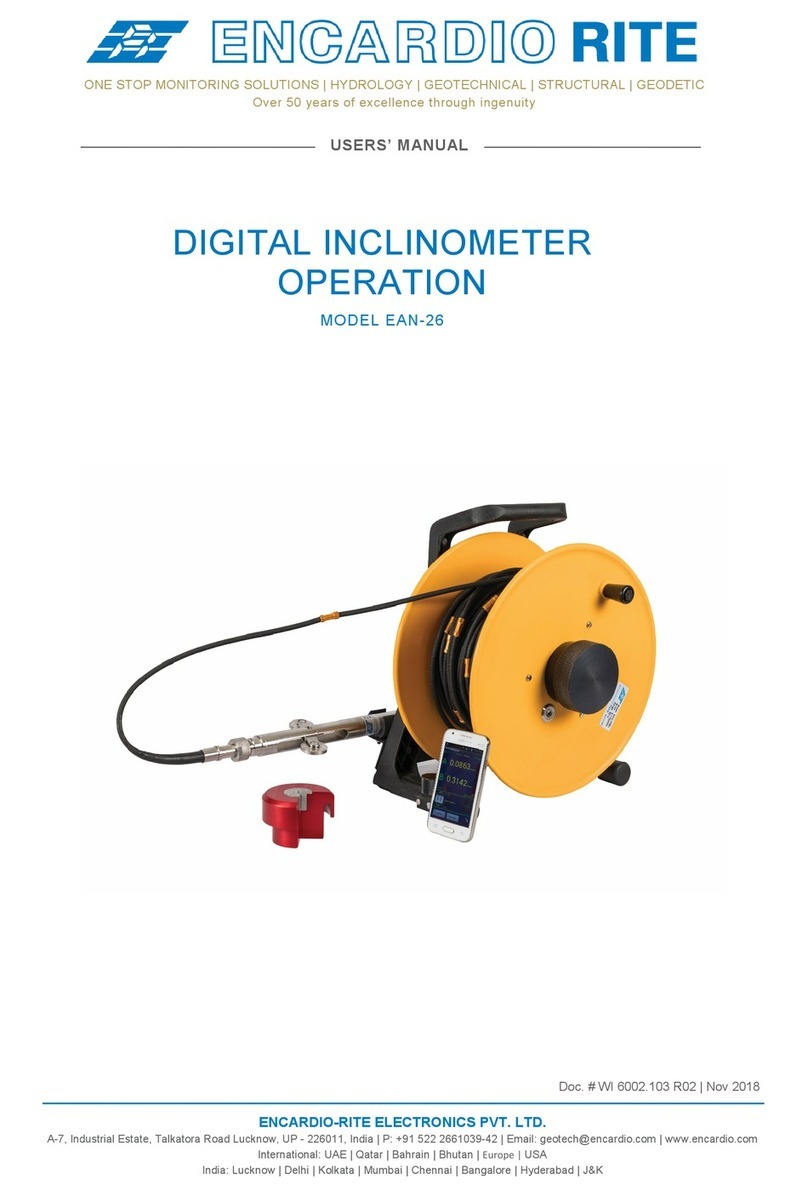
ENCARDIO RITE
ENCARDIO RITE EAN-26 User manual

ENCARDIO RITE
ENCARDIO RITE EAN-26CCJ User manual