Entron EN6001 User manual

700230 Rev 2.2
Entron Controls, LLC.
1402 S. Batesville Road
Greer, SC 29650
Phone: 864.416.0190
fax: 864.416.0195
www.EntronControls.com

2
700230 2Rev 2.2
READ THIS MANUAL COMPLETELY
BEFORE ATTEMPTING TO INSTALL OR OPERATE THE CONTROL.
STORE THIS TECHNICAL INFORMATION IN A PLACE
TO WHICH ALL USERS HAVE ACCESS AT ANY TIME
ENTRON Controls follows the practices of the RWMA for precautionary labeling. See RWMA Bulle-
tins #1 and #5 for a complete description. Observe the WARNING, DANGER, and CAUTION labels
affixed to control to maintain safe operation. ENTRON Controls, LLC. and its affiliates are not re-
sponsible for any harm caused by non-compliance of instructions associated with the aforemen-
tioned labels or signal words to follow.
The signal word DANGER is used to call attention to immediate or imminent hazards which if not
avoided will result in immediate, serious, or personal injury or loss of life. Examples are: exposed
high voltage; exposed fan blades.
The signal word WARNING is used to call attention to potential hazards which could result in
personal injury or loss of life. Examples are: not using proper personal protection; removal of guards.
The signal word CAUTION is used to call attention to hazards which could result in non-life
threatening personal injury or damage to equipment. CAUTION may also be used to alert against
unsafe practices.
The term NOTICE is used for making recommendations on use, supplementary information, or
helpful suggestions. Non-compliance with these recommendations may result in damage to control,
welding machine, or workpiece. ENTRON Controls, LLC. and its affiliates are not responsible for
damage caused by such non-compliance, and warranties may be voided accordingly at the discre-
tion of ENTRON Controls.
WARNING: Individuals with cardiac devices should maintain a safe distance due to strong magnetic
fields arising from resistance welding. The function of cardiac pacemakers and defibrillators may be
disturbed, which may cause death or considerable health damages to persons concerned! These
persons should avoid the welding system unless authorized by a licensed physician.
Important Safety Instructions

3
700230 3Rev 2.2
Filling out the following information (and keeping it readily available) may allow for future technical service of equipment
to be conducted more efficiently:
Model #: EN6001
Serial #:
OEM/Distributer:
Contact #:
Purchase Date:
Hardware Connections
P1—2, Foot Switch #1
P1—3, Foot Switch #2
P1—4, Emergency Stop
P1—5, No Weld Signal
P1—6, Programmable Input #1
P1—7, Programmable Input #2
P1—8, Programmable Input #3
P1—9, Programmable Input #4
P1—10, Programmable Input #5
P1—11, Programmable Input #6
P2—2, Solenoid Valve #1
P2—3, Solenoid Valve #2
P2—4, Solenoid Valve #3
P2—5, Programmable Output #1
P2—6, Programmable Output #2
P2—7, Programmable Output #3
P2—8, Programmable Output #4
P3 Sensing Coil
My Control Information
Primary SecondaryNot Used

4
700230 4Rev 2.2
Filling out the following information (and keeping it readily available) may allow for future technical service of equipment to
be conducted more efficiently. Please duplicate and complete this page for each utilized schedule:
SCHEDULE #:
Squeeze Delay: cycles KVA or %
Squeeze: cycles Valves:
Weld 1: cycles KVA or %
Cool 1: cycles
Slope: cycles
Weld 2: cycles KVA or %
Cool 2: cycles
Impulses: cycles
Hold: cycles
Off: cycles
Cycle Mode:
Comments:
Tap Setting: Pressure: Machine:
Weld Schedule Worksheet

5
700230 5Rev 2.2
Functions ………………………................................................................. 6
Specifications ……….……………………………………………………... 7
Wiring Diagrams .....................................................………………………. 8
Menu Navigation ....................................................................................... 9
Saving Weld Schedules ……..……………………………………………….. 10
Loading Weld Schedules ……..……………………………………………….. 11
Updating Firmware ………………………………………………………………. 12
User Connections ………………………………………………………………. 13
Weld Timing Cycles .…………………………….………………………… 15
Programming Parameters List .………………………………….…………… 16
I/O Map ……………………………………………………………………….. 23
Error List ……………………………………………………………………….. 24
Warranty and Service Policy …………………………………….…………. 27
Table of Contents

6
700230 6Rev 2.2
• Constant current regulation
• Primary or Secondary feedback
• Current Monitoring with high, low, and pre-limits
• Up to 64 programs (internal or external selection)
• On Timer Membrane Keyboard with backlit 128x64 (8 lines) LCD graphic display
• Six (6) inputs and four (4) outputs with output protection on CPU
• Electrode management functions; including stepping, current counting, tip-dressing, and preset
curves
• Welding programs may be linked together for complex spot schedules (chained or successive)
• USB-capable firmware refresh
• AC 60/50 Hz welding support
• Spot / Pulsation / Seam welding / Flash or Butt welding / Brazing
• Multiple weld intervals plus pulsation, upslope and downslope
• Air-over-oil gun operation
• Water Saver (contactor timer)
• Head lock function
• Program lockout (key switch) function
• Operation mode switch (program lockout and Weld/No Weld)
• Error reset switch
• Optional plug-in Ethernet card provides PLC compatibility with Modbus and EtherNet/IP
Functions

7
700230 7Rev 2.2
Environmental Conditions:
Operating Temperature 0°C to 60°C
Storage/Transport Temperature -25°C to 70°C
Air pressure 0 to 2000m above sea level
Humidity no dew point excursion allowed
Enclosure Ratings NEMA 1 and NEMA 12
Electronics Ratings:
CPU operating voltage (without I/O) 24 VDC +5% at 220 mA
Rated current (without I/O) at 24V SV1-SV3: ~500 mA
PO1-PO4: ~500 mA
Discrete I/O:
Input +24V +15%
DC Output 24 VDC, 0.5A max
AC Output 120 VAC, 1A max
Supply I/O: 24 VDC +5%
General Operating:
Operating Voltage 240VAC or
(see wiring diagram for details) 380VAC or
480VAC or
575VAC
Specifications

8
700230 8Rev 2.2
Wiring and Connectivity

9
700230 9Rev 2.2
Status Page List (Default)
Main Menu
1. Use Schedule
2. Edit Schedule
3. Copy Schedule
4. Reset Error
5. Edit counter
6. About
AND
Setup Menu
Menu Navigation
Schedule Select

10
700230 10 Rev 2.2
Step 1: Insert a formatted USB drive into USB port on the
control panel
Step 2: From the ‘Setup Menu’ (see Menu Navigation for de-
tails) select “Utility”.
Step 3: Select “Backup data”
Step 4: Rename file (desired) using and
Step 5: Set “Confirm” to “YES” using and
Step 6: Press and verify that “DONE!!!” appears in the
top left corner of the title bar.
Saving Weld Schedules

11
700230 11 Rev 2.2
Step 1: Insert USB drive with a previously saved backup file*
into the USB port on the control panel.
Step 2: From the ‘Setup Menu’ (see Menu Navigation for de-
tails) select “Utility”.
Step 3: Select “Restore data”
Step 4: Select the desired filename* using and
Step 5: Set “Confirm” to “YES” using and
Step 6: Press and verify that “DONE!!!” appears in the
top left corner of the title bar.
*Note: The backup file must be on the root directory of the
USB drive. And the filename must be
EN600100.EN6 to EN600199.EN6
Loading Weld Schedules

12
700230 12 Rev 2.2
Step 1: Ensure the control is completely powered down.
Step 2: Insert USB drive with EN6001 firmware file into USB
port on the control panel.
Step 3: Press and hold and
Step 4: Power on the control. Once the Bootloader Menu
(shown right) appears, release and
Step 5: Select “Refresh firmware”
Step 6: Select the desired filename* using and
Step 7: Set “Confirm” to “YES” using and
Step 8: Press and the control will begin updating.
Step 9: In order to return to the “Main Menu”, either
1. Temporarily power down the control
2. Go back to “Bootloader Menu” by pressing
Then, select “Execute firmware”, then select
“YES”.
*Note: The firmware file must be on the root directory of the
USB drive, and the filename will be
E0611001.BIN to E0619999.BIN
(this may requiring the extraction of a zip file)
Updating Firmware

13
700230 13 Rev 2.2
User Connections (DC)
Port Designation Switch
P1—1Foot Switch Common 24VDC
P1—2Foot Switch #1 N.O.
P1—3Foot Switch #2 N.O.
P1—4Emergency Stop N.C.
P1—5No Weld Signal N.C.
P1—6Programmable Input #1 N.O.
P1—7Programmable Input #2 N.O.
P1—8Programmable Input #3 N.O.
P1—9Programmable Input #4 N.O.
P1—10 Programmable Input #5 N.O.
P1—11 Programmable Input #6 N.O.
P1—12 Foot Switch Common 24VDC
P2—1Solenoid Valve Common 0VDC
P2—2Solenoid Valve #1 24V Digital
P2—3Solenoid Valve #2 24V Digital
P2—4Solenoid Valve #3 24V Digital
P2—5Programmable Output #1 24V Digital
P2—6Programmable Output #2 24V Digital
P2—7Programmable Output #3 24V Digital
P2—8Programmable Output #4 24V Digital

14
700230 14 Rev 2.2
User ConnectionsUser Connections (AC option)
Port Designation Switch
TS1 - SV1 Solenoid Valve #1 AC Analog
TS1 - SV2 Solenoid Valve #1 Common 0VAC
TS1 - SV3 Solenoid Valve #2 AC Analog
TS1 - SV4 Solenoid Valve #2 Common 0VAC
TS1 - SV5 Solenoid Valve #3 AC Analog
TS1 - SV6 Solenoid Valve #3 Common 0VAC
TS4 - TIMER
V3 OUT Output from P2 - 4 (Valve #3 control signal) 24V Digital
TS4 - V3IN Optional connection to replace “P2 - 4” signal
from timer module with an alternatively desired
24VDC signal. (For example, “P2 - 5” pro-
grammed to “Retraction” could be connected
when using an AC retraction valve.)
Default -
Jumper Connected to TS4 - TIMER
V3 OUT
TS7 - B Bypass Solenoid Valve #3 Safety Relay Default - JW6 Disconnected
TS7 - R Solenoid Valve #3 Safety Relay Default - JW6 Connected
WARNING Bypassing the safety relay will result in the valve 3 control being independent of FS1 or FS2 after initiation.
This should NOT be done with valves connected to pinch points such as the primary welding force valve.

15
700230 15 Rev 2.2
Weld Timing Cycle
PARAMETER SETTING
Squeeze Delay 0 cycles
Squeeze 3 cycles
Weld 1 0 cycles
Cool 1 0 cycles
Slope 0 cycles
Weld 2 2 cycles
>Mode Phase Shift
>Heat 50 %
Cool 2 1 cycle
Hold 2 cycles
Off 2 cycles
Impulses 2 cycles
The diagram above is intended to demonstrate a resulting weld-
ing timing cycle using the attached parameters; it is not recom-
mended as part of a functional weld schedule.
Pressure Curve
Squeeze
(3 cycles) Weld 2
(2 cycles) Hold
(2 cycles)
Weld 2
Cool 2
(1 cycle)
~50% Phase
Shi
Cool 2 O
(2 cycles)
First Impulse Second Impulse
Sequence
Iniaon
Sequence
Terminaon

16
700230 16 Rev 2.2
Parameter List
Sub Menu Parameter Input Range Description
1. Use Schedule
Schedule [0-63] Default = 0
2. Edit Schedule
Advance [0-99] cycles Default = 0
This option only appears when ‘air-over-oil’ configuration is
selected.
Intensify [0-99] cycles Default = 0
This option only appears when ‘air-over-oil’ configuration is
selected.
Block Delay [0-99] cycles Default = 0
This option only appears when ‘air-over-oil’ configuration is
selected.
Schedule Number [0-63]
Default = 0
In order to accept changes made to any field, the
button must pressed. It is important to make sure that the
correct schedule number is selected AND accepted BEFORE
completing all of the corresponding settings to follow.
Squeeze Delay [0-99] cycles
Default = 0
Additional time delay to be added to 'Squeeze'. This is usu-
ally utilized when 'Cycle Mode' is set to repeat. The squeeze
delay will only be applied to the first weld of the repeating
cycle.
Squeeze [0-99] cycles Default = 0
Time delay between the signal to the programmed valve(s)
and weld initiation.
>Valve
None
1 2 3
1+2 1+3 2+3
1+2+3
Selection of valve(s) to be activated
Weld 1 [0-99] cycles Default = 0
Also referred to as "pre-heat"
>Mode Phase Shift
Const Current
>Heat [0-99] % Phase shift %; does not apply when ‘Mode’ is set to Const
Current
or
>Current [0.00-60.00] kA Weld current setting does not apply when Mode is set to
Phase Shift
>I1 Monitor On
Off Must be enabled in order to track/report current errors
>PW1 Monitor On
Off Must be enabled in order to track/report phase shift abnor-
malities.
Cool 1 [0-99] cycles Default = 0
Time delay between ‘Weld 1’ and ‘Weld 2’. Designed to
give an impulse effect.
Main Menu

17
700230 17 Rev 2.2
Parameter List
Sub Menu Parameter Input Range Description
2. Edit Schedule
(continued)
Slope [0-99] cycles
Default = 0
The number of additional cycles between 'Weld 1' and 'Weld
2' in order to transition between the two gradually. A larger
'Weld 1' will result in a downslope; whereas a larger 'Weld 2'
will result in an upslope.
Weld 2 [0-99] cycles Default = 0
>Mode Phase Shift
Const Current
>Heat [0-99] % Phase shift %; does not apply when '>Mode' is set to Const
Current
or
>Current [0.00-60.00] kA Weld current setting does not apply when Mode is set to
Phase Shift
>I2 Monitor On
Off Must be enabled in order to track/report current errors
>PW2 Monitor On
Off Must be enabled in order to track/report phase shift abnor-
malities.
Cool 2 [0-99] cycles Default = 0
Primarily used when applying multiple impulses; time delay
following each 'Weld 2' impulse.
Hold [0-99] cycles Default = 0
Time delay during which the electrodes remain in contact
with the part being welded to allow weld nugget to congeal.
Off [0-99] cycles
Default = 0
Time delay following 'Hold' cycle in which the valve(s) re-
lease; the next schedule/sequence will not begin until the
'Off' cycle is complete.
Impulses [1-99] cycles Default = 1
Number of times to deliver Weld 2, Cool 2.
(Impulses do NOT apply to Weld 1, Cool 1)
I offset -1 %
0 %
+1 %
Adjustable increase or decrease to total current delivered by
a sequence. This is one of the few adjustable parameters
when control is locked.
Parameter is only visible when 'Max I offset' is not "0".
>Change all No
Yes No – 'I offset' will be applied to the current schedule
Yes – 'I offset' will be applied to all schedules'
Block Delay [0-99] cycles Default = 0
This option only appears when ‘air-over-oil’ configuration is
selected.
Main Menu (continued)

18
700230 18 Rev 2.2
Parameter List
Sub Menu Parameter Input Range Description
2. Edit Schedule
(continued)
Cycle Mode
Non-Repeat
Repeat
Chained
Successive
Wait Here
Non-repeat – Control can be initiated for only one sequence/
schedule even if initiation remains closed.
Repeat – Sequences/ schedules will continue if initiation re-
mains closed.
Chained – Schedules are chained together so that consecu-
tive schedules can be sequenced from one initiation.
Successive – Schedules are chained together so that consecu-
tive schedules will be sequenced from separate initiations.
Wait-Here – only applies when 'Weld2' is set to 99 cycles.
This allows infinite Weld 2 duration until Escape is trig-
gered. 'Beat_Mode' is authorized to "Wait-Here" if desired.
3. Copy Schedule
Copy From [0-63] Schedule # to be copied
Copy To [0-63] Schedule # to be replaced
Confirm Yes
No
Must select "Yes" and press the key to complete the
above copy/replace. "DONE!!!" will appear in the title bar
once complete.
4. Reset Error
Confirm Yes
No
Must select "Yes" and press the key to complete the
above copy/replace. "DONE!!!" will appear in the title bar
once complete.
5. Edit Counter
Counter Enable
Disable
Enable – 'Weld count done' will increment with each weld
delivered. Error "ER25" will be reported when 'Max part
count' = 'Part count done'
Max part Count [0-60,000] Default = 60,000
Number at which the 'part count done' reports error "ER25"
Weld per part [1-9,999] Default = 1
The number of welds to increment 'part count done' by one.
RST Counter
None
PCTR
WCTR
Both
Resets counter
PCTR – part counter
WCTR – weld counter
Main Menu (continued)

19
700230 19 Rev 2.2
Parameter List
Setup Menu
Sub Menu Parameter Input Range Description
1. Config
Weld Mode Spot
Seam1
Seam2
Spot – Standard squeeze, weld, hold and off sequence.
Seam1 – When FS1 or FS2 input is toggled, control will run
'schedule' from 'Squeeze Delay' through 'Cool 2'. If FS1 or
FS2 input is held, control will repeat 'Weld 2' and 'Cool 2'.
Seam2–FS1 initiation implements same function as in
Seam1. FS2, schedule 20, schedule 40 and schedule 60 will
always initiate "Spot" Weld Mode
Retraction Off
Maintained
Momentary
Maintained – Retraction output directly reflects retraction
input
Momentary – Retraction output changes state with a toggled
impulse to the retraction input.
This parameter is ignored if 'Beat_Mode' is enabled.
On Error Continue
Head Lock
Stop
Continue – Further welds are permitted regardless of previ-
ous weld status
Head Lock – On error, valve signal(s) are held on. Addi-
tional welds are not permitted until Error Reset occurs.
Stop – On error, valve signal(s) turn off as normal. Addi-
tional welds are not permitted until Error Reset occurs.
Sch Select Internal
External
Internal – FS1 will initiate the programmed weld schedule
number
External – FS1 will initiate the weld schedule number ac-
cording to the binary value represented by PI3, PI4, PI5, and
PI6.
(FS2 will always initiate weld schedule 20.)
I-Feedback Primary
Secondary This setting should correspond to the physical location of the
sensing coil.
Air-over-oil Off
Mode 1
Mode 2
Mode 1: air-over-oil setting without retraction
Mode 2: air-over-oil setting with retraction enabled using
'Retract Open' and 'Retract Close' settings
Retract Open [0-99] cycles
Default = 0
Time delay to allow for retraction from "pre-weld" position
to "fully open" position
Sub Menu only appears when 'air-over-oil' is set to "Mode 2"
Retract Close [0-99] cycles
Default = 0
Time delay to allow for closure from "fully open" position to
"pre-weld" position
Sub Menu only appears when 'air-over-oil' is set to "Mode 2"

20
700230 20 Rev 2.2
Parameter List
Setup Menu (continued)
Sub Menu Parameter Input Range Description
1. Config
(continued)
Beat mode
Off
Squeeze
Sqz. + Weld
Wait-Here
Off – Sequence/Schedule will complete with a momentary
activation of FS1 or FS2
Squeeze – Sequence/Schedule requires continuous activation
of FS1 or FS2 until the squeeze sequence is complete, other-
wise the sequence will terminate.
Sqz. + Weld – Welding sequence requires continuous activa-
tion of FS1 or FS2 until the weld sequence is complete, oth-
erwise the sequence will terminate.
Wait-Here – Welding sequence requires continuous activa-
tion of FS1 or FS2 until the weld sequence is complete, oth-
erwise the sequence will temporarily pause (retraction will
not occur). This setting requires the active schedule's 'Cycle
Mode' to also be set to "Wait-Here".
AVC Disabled
Max [1-10] %
Automatic Voltage Compensation – Will add additional per-
centage to phase shift in order to compensate for diminished
supply voltage. (only works with schedules using "Phase
Shift" Mode to regulate current)
AVC nom. [187-633] volts Default = 480
Supply voltage on which the control is designed to operate.
Parameter is only visible when 'AVC' is enabled.
Voltage monitor Off
On On – High and Low Voltage errors are enabled using the
following parameters.
>High [160-690] volts
Default = 690
Error "ER23" will be triggered if supply voltage is above the
set value
Parameter is only visible when 'Voltage Monitor' is "On"
>Low [160-690] volts
Default = 160
Error "ER24" will be triggered if supply voltage is below the
set value
Parameter is only visible when 'Voltage Monitor' is "On"
Max I offset [0-15] % Determines the input range for 'I offset' parameter. For ex-
ample, if 'Max I offset' is 6%, 'I offset' input range is -6% to
+6%
Water Saver [0-199] sec Default = 0
Time duration that the water flow signal will remain on fol-
lowing a weld. Feature available on PO4
87° delay Off
On
On – The first half cycle is delayed 87degrees (51.6% max)
phase shift in order to minimize saturation of the weld trans-
former
Half Cycle
Off
+
-
AC
+ – Only the positive half cycle is output
- – Only the positive half cycle is output
AC – Alternating positive/negative half cycles are output
Other manuals for EN6001
2
Table of contents
Other Entron Control Unit manuals
Popular Control Unit manuals by other brands
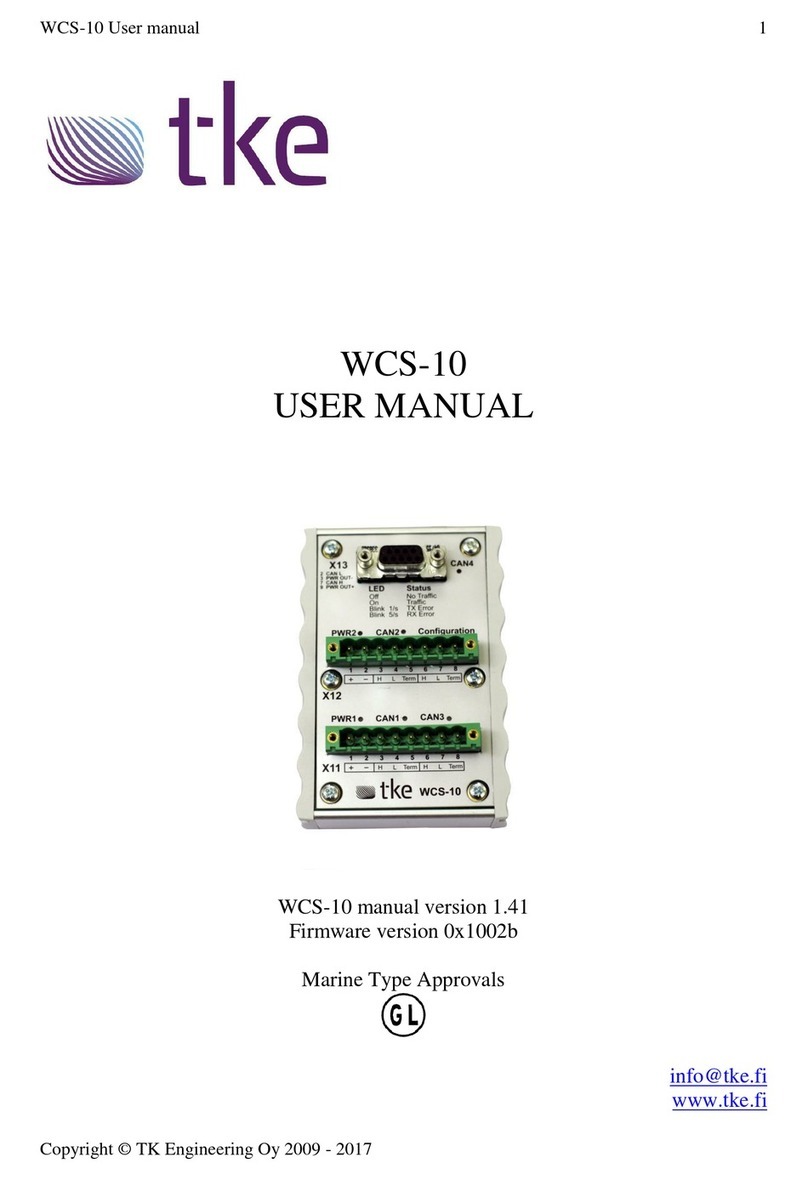
TKE
TKE WCS-10 user manual
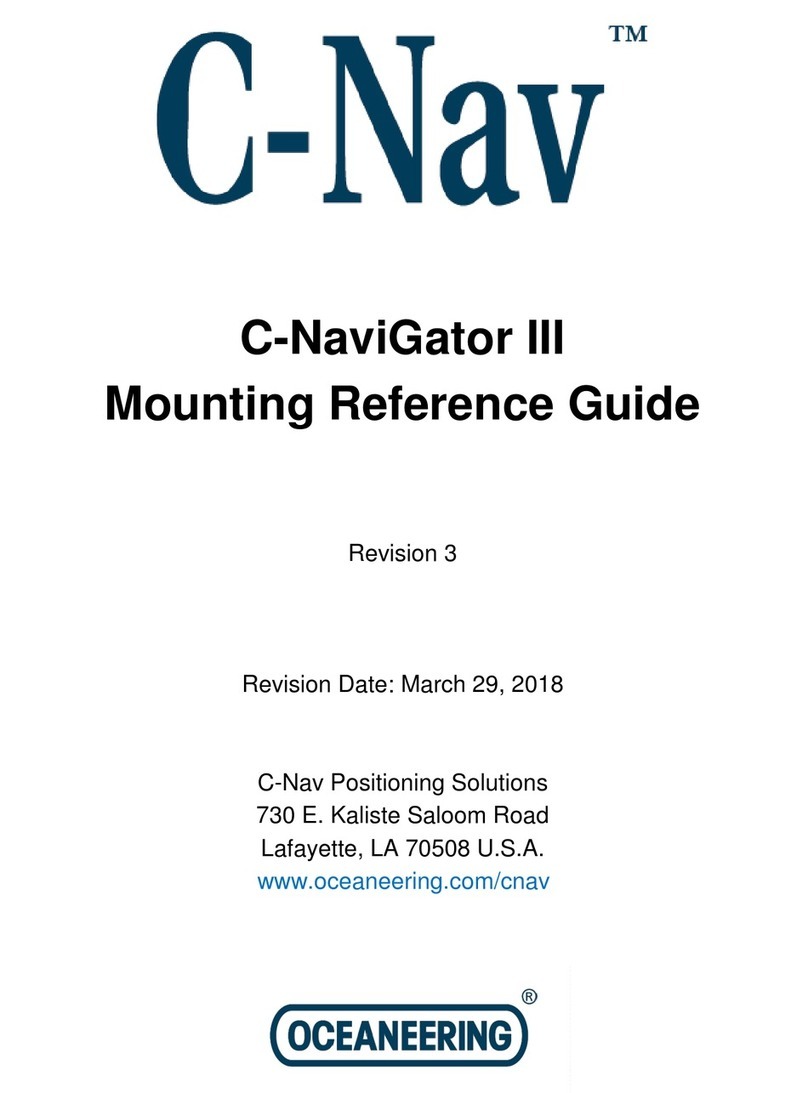
C-Nav
C-Nav C-NaviGator III reference guide

Festo
Festo VZXA Series Repair instructions
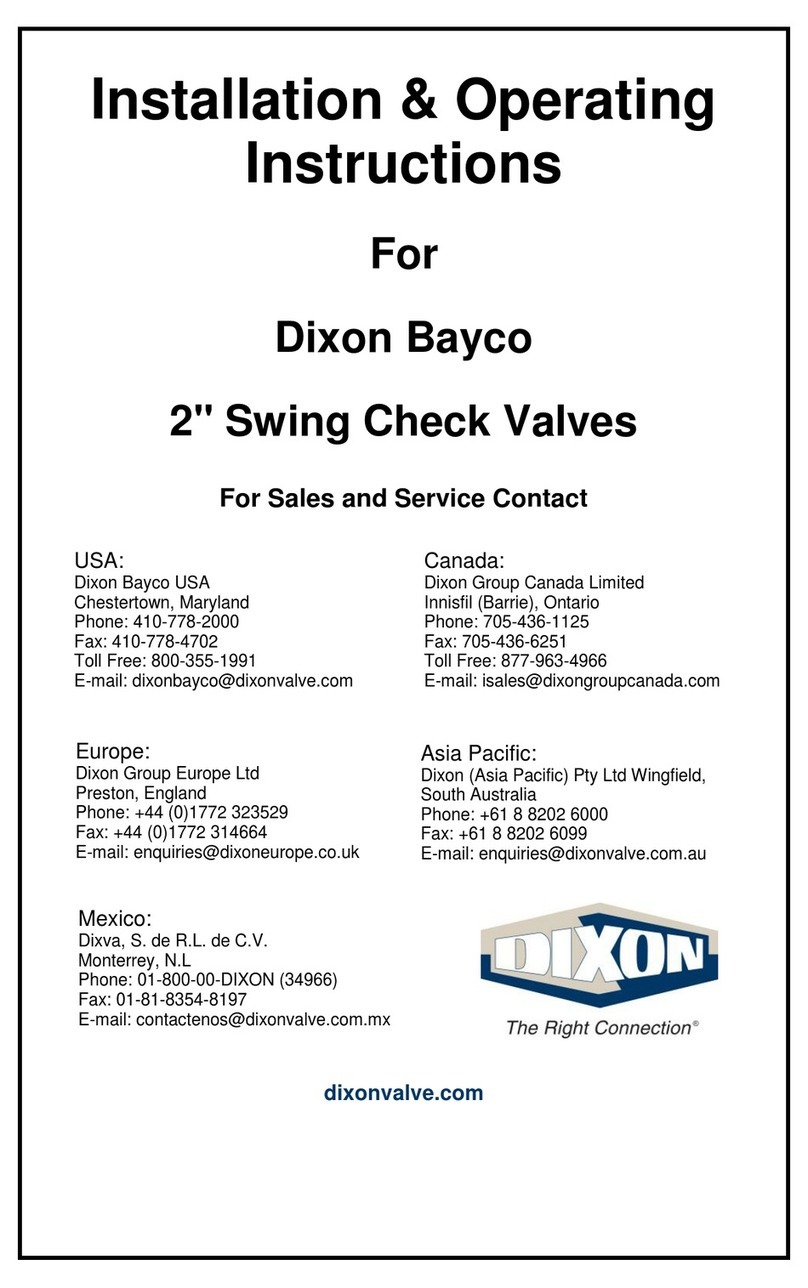
Dixon Bayco
Dixon Bayco 3020 Series Installation & operating instructions
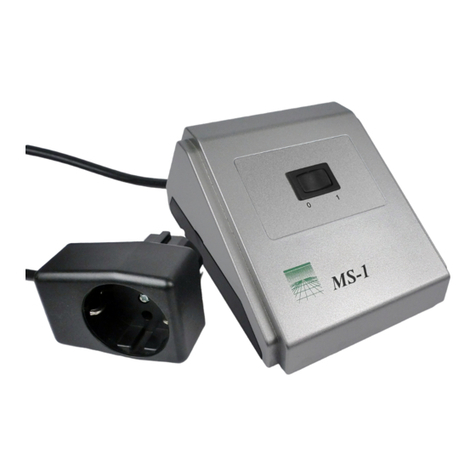
HumanTechnik
HumanTechnik MS-1 operating instructions
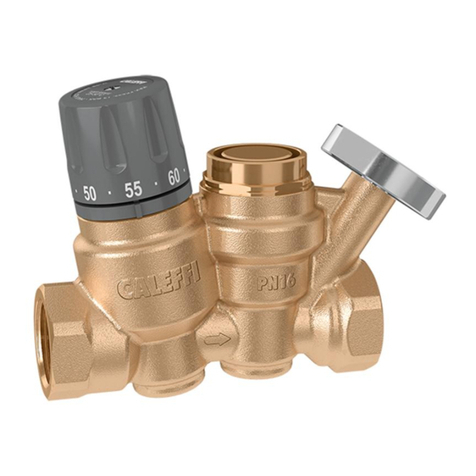
CALEFFI
CALEFFI ThermoSetter 116 Series Installation, commissioning and servicing instructions