E+E Elektronik EE895 User manual

User Manual EE895
Miniature Sensor Module for CO2, Temperature and Barometric Pressure | 2
Content
1 General Information...................................................................................................................................... 3
1.1 Explanation of Warning Notices and Symbols ....................................................................................... 3
1.2 Safety Instructions ................................................................................................................................ 4
1.2.1. General Safety Instructions ......................................................................................................................... 4
1.2.2. Intended Use............................................................................................................................................... 4
1.2.3. Mounting, Start-up and Operation................................................................................................................ 4
1.3 Environmental Aspects.......................................................................................................................... 5
1.4 ESD Protection .................................................................................................................................... 5
1.5 Product Description............................................................................................................................... 5
1.6 Operating Principle CO2Measurement ................................................................................................. 5
2 Handling Instructions................................................................................................................................... 6
3 Hardware ....................................................................................................................................................... 6
3.1 Dimensions ........................................................................................................................................... 6
3.2 Mounting Recommendation .................................................................................................................. 7
3.2.1. Mounting via Solder Pads............................................................................................................................ 7
3.2.2. Mounting via Side Plated Contacts .............................................................................................................. 7
3.3 EE895 Block Diagram ........................................................................................................................... 8
3.5 Pin Description...................................................................................................................................... 9
3.6 Electrical Characteristics..................................................................................................................... 11
3.7 Typical Applications............................................................................................................................. 12
3.7.1. EE895 Connected to USB Interface........................................................................................................... 12
3.7.2. EE895 in Battery Powered Devices ........................................................................................................... 12
3.7.3. EE895 Connected to a KNX Bus ............................................................................................................... 13
4 Digital Interface........................................................................................................................................... 13
4.1 I2C Interface........................................................................................................................................ 13
4.1.1. Modbus Protocol Over I2C Interface .......................................................................................................... 13
4.1.2. I2C Simplified Protocol............................................................................................................................... 14
4.2 UART Interface ................................................................................................................................... 16
4.2.1. Modbus Protocol Over UART Interface...................................................................................................... 16
4.3 Modbus Register Map ......................................................................................................................... 17
4.4 General Purpose Registers for Individiual Use.................................................................................... 17
4.5 EE895 Commands .............................................................................................................................. 18
4.5.1. Information ................................................................................................................................................ 18
4.5.2. General Settings........................................................................................................................................ 18
4.5.3. CO2Parameter Settings ............................................................................................................................ 20
5 Technical Data ............................................................................................................................................ 21

User Manual EE895
Miniature Sensor Module for CO2, Temperature and Barometric Pressure | 3
1 General Information
This user manual serves for ensuring proper handling and optimal functioning of the device. The user manual
shall be read before commissioning the equipment and it shall be provided to all staff involved in transport,
installation, operation, maintenance and repair. E+E Elektronik Ges.m.b.H. does not accept warranty and liability
claims neither upon this publication nor in case of improper treatment of the described products.
This document may contain technical inaccuracies and typographical errors. The content will be revised on a
regular basis. These changes will be implemented in later versions. The described product(s) can be improved
and changed at any time without prior notice.
The user manual may not be used for the purposes of competition without the written consent of E+E Elektronik
Ges.m.b.H. and may not be forwarded to third parties. Copies may be made for internal purposes. All information,
technical data and diagrams included in these instructions are based on the information available at the time of
writing.
PLEASE NOTE
Find this document and further product information on our website at www.epluse.com/ee895.
1.1 Explanation of Warning Notices and Symbols
Safety precautions
Precautionary statements warn of hazards in handling the device and provide information on their prevention.
The safety instruction labeling is classified by hazard severity and is divided into the following groups:
DANGER
Danger indicates hazards for persons. If the safety instruction marked in this way is not followed, the hazard
will verly likely result in severe injury or death.
WARNING
Warning indicates hazards for persons. If the safety instruction marked in this way is not followed, there is a
risk of injury or death.
CAUTION
Caution indicates hazards for persons. If the safety instruction marked in this way is not followed, minor or
moderate injuries may occur.
NOTICE
Notice signals danger to objects or data. If the notice is not observed, damage to property or data may
occur.
Informational notes
Informational notes provide important information which stands out due to its relevance.
INFO
The information symbol indicates tips on handling the device or provides additional information on it. The
information is useful for reaching optimal performance of the device.
The title field can deviate from “INFO” depending on the context. For instance, it may also read “PLEASE
NOTE”.

User Manual EE895
Miniature Sensor Module for CO2, Temperature and Barometric Pressure | 4
1.2 Safety Instructions
1.2.1. General Safety Instructions
NOTICE
Improper handling of the device may result in its damage.
▪ The EE895 housing and the circuit board shall not be exposed to unneccessary mechanical stress during
installation and operation. The forces exerted shall not exceed 50 N.
▪ The EE895 electronics is sensitive to electrostatic discharge (ESD), appropriate protective measures shall
be taken when touching it.
▪ Use the EE895 only as intended and observe all technical specifications.
1.2.2. Intended Use
The EE895 miniature sensor module measures the CO2concentration, the temperature (T) and the absolute
barometric pressure (p). It is intended to be used as sensor module in devices for diverse uses in non-condensing
environments. Applications can be , e.g., in building automation, demand controlled ventilation and process
control.
WARNING
Non-compliance with the product documentation may cause safety risk for people and the entire
measurement installation.
The manufacturer cannot be held responsible for damages as a result of incorrect handling, installation and
maintenance of the device.
▪ Do not use EE895 in explosive atmosphere or for measurement of aggressive gases.
▪ This device is not appropriate for safety, emergency stop or other critical applications where device
malfunction or failure could cause injury to human beings.
NOTICE
Failing to follow the instructions in this user manual may lead to measurement inaccuracy and device
failures.
▪ The EE895 may only be operated under the conditions described in this user manual and within the
specification included in chapter 5 Technical Data.
▪ The device may only be powered with safety extra-low voltage (SELV).
▪ Unauthorized product modification leads to loss of all warranty claims.
1.2.3. Mounting, Start-up and Operation
The EE895 has been produced under state of the art manufacturing conditions, has been thoroughly tested and
has left the factory after fulfilling all safety criteria. The manufacturer has taken all precautions to ensure safe
operation of the device. The user must ensure that the device is set up and installed in a way that does not impair
its safe use. The user is responsible for observing all applicable local and international safety guidelines for
safe installation and operation of the device. This user manual contains information and warnings that must be
observed by the user in order to ensure safe operation.
PLEASE NOTE
The manufacturer or his authorized agent can be only be held liable in case of willful or gross negligence.
In any case, the scope of liability is limited to the corresponding amount of the order issued to the
manufacturer. The manufacturer assumes no liability for damages incurred due to failure to comply with the
applicable regulations, operating instructions or the specified operating conditions. Consequential damages
are excluded from the liability.

User Manual EE895
Miniature Sensor Module for CO2, Temperature and Barometric Pressure | 5
WARNING
Non-compliance with the product documentation may cause accidents, personal injury or property damage.
▪ Mounting, installation, commissioning, start-up, operation and maintenance of the device may be
performed by qualified staff only. Such staff must be authorized by the operator of the facility to carry out
the mentioned activities.
▪ The qualified staff must have read and understood this user manual and must follow the instructions
contained within.
▪ All process and electrical connections shall be thoroughly checked by authorized staff before putting the
device into operation.
▪ Do not install or start-up a device supposed to be faulty. Make sure that such devices are not accidentally
used by marking them clearly as faulty.
▪ A faulty device shall be removed from the process.
▪ Service operations other than described in this user manual may only be performed by the manufacturer.
1.3 Environmental Aspects
PLEASE NOTE
Products from E+E Elektronik Ges.m.b.H. are developed and manufactured in compliance with all relevant
environmental protection requirements. Please observe local regulations for the disposal of the device.
For disposal, the individual components of the device must be separated according to local recycling
regulations. The electronics shall be disposed of correctly as electronics waste.
1.4 ESD Protection
The sensing elements and the electronics board are ESD (electrostatic discharge) sensitive components
of the device and must be handled as such. The failure to do so may damage the device by
electrostatic discharges when touching exposed sensitive components.
1.5 Product Description
Beside CO2concentrationupto10 000ppm,theEE895measurestemperature(T)andabsolutebarometric
pressure (p). The active pressure and temperature compensation minimizes the impact of altitude and ambient
conditions on the CO2measured data.
The CO2, T and p measured data is available on I²C or UART digital interfaces. The solder pads, the plated half-
holes and the through-holes allow for various mounting options.
1.6 Operating Principle CO2Measurement
The CO2measurement is based on the dual wavelength Non Dispersive Infra-Red (NDIR) technology which
compensates for ageing effects, is highly insensitive to pollution and offers outstanding long term stability.
Theinfrareddetector1(IR-1)istunedto4.2μm,whichisthewavelenghtabsorbedbyCO2, the infrared detector
2(IR-2)istunedto3.9μm,whichisnotaffectedbyanygas.Foreverysingleflashoftheinfraredlamp(IR-L),the
device calculates the CO2concentration from the outputs of both infrared detectors IR-1 and IR-2. The measuring
interval is user selectable (factory default: 15 s).

User Manual EE895
Miniature Sensor Module for CO2, Temperature and Barometric Pressure | 6
2 Handling Instructions
EE895 is an ESD sensitive device and must be handled with corresponding precautions. Protect the
sensor outside the EPA (Electrostatic Protected Area) using ESD protective packaging.
The EE895 is packed in stacks of ESD trays with 50 pieces each. The tray dimension is 354.2 x 278.6 x
23.8 mm (13.94 x 10.97 x 0.94 inch)
Operating and storage conditions: -40…60 °C (-40…140 °F)
0…95 % RH (non-condensing)
700...1 100mbar(10.15...15.95psi)
NOTICE
Failing to follow the instructions in this user manual may lead to measurement inaccuracy and device
failures.
▪ The EE895 housing and the circuit board shall not be exposed to unneccessary mechanical stress during
installation and operation. The forces exerted shall not exceed 50 N.
▪ The sensor module deploys a fine dust filter for sensing element protection. If the EE895 is deployed in a
device which is designed for harsh environments, the device shall deploy a filter as well.
3 Hardware
3.1 Dimensions
Valuesinmm / inch
Side view Bottom view
19.5 (0.8)
5.4
(0.2)
7.0 (0.3)
27.2 (1.1)
Air inlet through dust filter
towards CO2sensing cell
T / p sensor CO2sensing cell
35.0 (1.4)
15.0 (0.6)
2.54 (0.1)
1.50 (0.06“)
Ø 1.0 (0.04)
T / p sensorThrough-holesPlated half-holes
Recommended PCB footprint

User Manual EE895
Miniature Sensor Module for CO2, Temperature and Barometric Pressure | 7
3.2 Mounting Recommendation
NOTICE
The EE895 is not intended for reflow soldering and consequently it does not feature a moisture sensitivity
level rate (MSL). Nevertheless, for storage and handling it shall be regarded as compatible with MSL 1.
CAUTION
EE895 may only be soldered manually. A max. temperature of 360 °C may be applied for max. 10 s per
solder point.
ESD precautions shall be observed while manually soldering the EE895.
The EE895 can be mounted facing either upwards or downwards.
3.2.1. Mounting via Solder Pads
The EE895 module can be mounted onto a pluggable female header or directly onto the electronics board by
using a pin-header with 2.54 mm (0.1 inch) pitch.
The minimum clearance of 2 mm (0.08 inch) shall be strictly observed. This is necessary for free air flow around
the CO2sensing cell and around the T/p sensor.
T/p sensor
T/p sensor
h>2 mm (0.08")
h>2 mm (0.08")
Air inlet through dust filter
towards CO2sensing cell
male pins
female header
Pluggable
Soldered single pin header
male pins
Fig. 1 Mounting with soldered pin header
3.2.2. Mounting via Side Plated Contacts
The EE895 can be mounted by manually soldering the plated half-holes onto the host board.
T/p sensor
8 mm (0.32")
Air inlet through dust filter
towards CO2sensing cell
Solder
Solder
T/p sensor
Fig. 2 Mounting by soldering at the side plated contacts

User Manual EE895
Miniature Sensor Module for CO2, Temperature and Barometric Pressure | 8
3.3 EE895 Block Diagram
Fig. 3 Block diagram
3.4 Pin Assignment
Bottom view
Fig. 4 Pin assignment
Pin no. Name Type Comment
1VCC_EM Power supply Power supply emitter infra-red lamp (IR-L)
2VCC_IO Power supply Power supply for the microcontroller
3EN Input Enable the module. Tie to Vcc_IO for normal operation
4GND Power supply Ground1)
5GND Power supply Ground1)
6RDY Output Data ready (open drain output)
7ISEL Input Interface selection
8TX / SCL I/O Transmission line (TX) / Serial Clock (SCL)
9RX / SDA I/O Receive line (RX) / Serial Data (SDA)
1) Pins 4 and 5 shall be connected to the same potential.
Tab. 1 Pin assignment

User Manual EE895
Miniature Sensor Module for CO2, Temperature and Barometric Pressure | 9
3.5 Pin Description
Pin 1 - VCC_EM
Power supply for the infrared lamp (IR-L). For optimizing of the energy consumption such as in battery-powered
devices, the IR-L can be powered separately.
The IR-L does not have to be powered continuously, as it needs power supply during the measurement cycle tmeas
only, see Fig. 7. Between the measurement cycles the current consumption of IR-L is approx. 0.1 µA.
Pin 2 - VCC_IO
Power supply for the microcontroller and the digital functional blocks.
Pin 3 – EN (Enable)
For battery-powered devices the user can optimize the energy consumption controlling the status of the EN pin by
an external host controller.
WhentheENpinispulled-downtothelogicLow0(≤0.4V),theinternalvoltageregulatorofEE895isswitched
off and the current consumption is typically 1 µA (max 2 µA).
Whenpulled-uptothelogicstateHigh(≥0.9V),theEE895operatesnormally.
If the energy consumption of EE895 is not relevant, the EN pin shall be connected to VCC_IO.
The EN pin may not be left open.
Pin 6 – RDY (Data ready)
During the measurement cycle (tmeas), when CO2, T and p are measured and processed, the pin RDY is in logic
state High. As soon as data is available for read out, the pin RDY goes to logic state Low. The falling edge at this
pin indicates that measured data is available for reading, see Fig. 5.
If used, an external pull-up resistor is required. If not used, the RDY pin may be left open.
Fig. 5 Timing details (see also chapter 4.5.3. CO2Parameter Settings)

User Manual EE895
Miniature Sensor Module for CO2, Temperature and Barometric Pressure | 10
Pin 7 – ISEL (Interface selection)
The EE895 features I2C and UART interfaces.
Interface selection:
ISEL logic state EE895 interface
Low (0…0.9 V) I2C
High (2.1…5.5 V) or not connected UART
Tab. 2 Interface selection
Serial interface pins:
Pin 8 – TX_SCL Transmission data / Serial clock
Pin 9 – RX_SDA Receiving data / Serial data
The function of pins 8 and 9 depends on the interface selected with pin 7 ISEL.
Pin 7 – ISEL connected to ground: EE895 features I2C interface:
Pin no. Mode Comment
8SCL (serial clock) External pull-up resistor to V+ (bus high voltage level) is required.
9SDA (serial data) External pull-up resistor to V+ (bus high voltage level) is required.
Tab. 3 Pin assignement I2C interface
Example:
Fig. 6 Example I2C interface
Pin 7 – ISEL connected to VCC or left open: EE895 features UART interface:
Pin no. Mode Comment
8TX (transmission line) CMOS compatible (VOutLowMax 0.4 V; VOutHighMin 2.6 V)
9RX (receive line) CMOS compatible (VInputLowMax 0.9 V; VInputHighMin 2.1 V)
Tab. 4 Pin assignment UART interface

User Manual EE895
Miniature Sensor Module for CO2, Temperature and Barometric Pressure | 11
Example:
Fig. 7 Example UART interface
3.6 Electrical Characteristics
A DC/DC converter is used to flash the lamp (VCC_EM). Therefore, the supply current is reduced with higher
voltage and vice versa. The microcontroller (VCC_IO) is supplied via a linear reglator, hence the supply current is
constant.
The average current consumption at a sampling interval of 15 s (factory default) is 1.6 mA. Tab. 5 lists the typical
and maximum current values in each individual state during the sampling interval, which is shown in the current
profile in Fig. 8.
Power Supply VCC_IO VCC_EM
Status 3.3 V 5 V
Idle measurement 6.2 (9.9) mA <0.1 µA <0.1 µA
IR lamp pulse 6.2 (9.9) mA 85 (95) mA 60 (66) mA
Standby 190 (300) µA <0.1 µA <0.1 µA
Power off <2 µA <0.1 µA <0.1 µA
Tab. 5 Current values in the individual measurement states, typ. (max.)
0
IR lamp pulse
Standby / power off
300 ms 300 ms
Idle
measurement
Sampling intervall 15 s (configurable 10 s ... 1 h)
Fig. 8 States during a CO2sampling interval
Further electrical characteristics:
Signal Unit Min Max Note
Clock frequency Hz 500 100 000
Pull-up resistor kΩ 4.7 100 Typical10kΩ
Tab. 6 Electrical characteristics

User Manual EE895
Miniature Sensor Module for CO2, Temperature and Barometric Pressure | 12
3.7 Typical Applications
3.7.1. EE895 Connected to USB Interface
Fig. 9 Example USB Interface
Pin7-ISELisnotconnected→theEE895featuresUARTinterface.
VCC_EM is connected to the nominal 5 V from USB, the VCC_IO and EN are connected to 3.3 V voltage
regulator.
The host can read the values at any time, pin 6 - RDY is not used.
3.7.2. EE895 in Battery Powered Devices
Fig. 10 Example battery powerd devices
Pin7-ISELisconnectedtotheground→theEE895featuresI2C interface.
VCC_EM is supplied by a low ESR super-capacitor and VCC_IO is connected to a typical low drop
3.3 V regulator.
The I2C host enables the EE895 with pin 3 - EN.
By checking the status of pin 6 - RDY (pulled up), the host can read the data as soon as available. After reading
the data, EE895 can be disabled with pin 3.

User Manual EE895
Miniature Sensor Module for CO2, Temperature and Barometric Pressure | 13
3.7.3. EE895 Connected to a KNX Bus
Fig. 11 Example KNX Bus
Pin7-ISELisconnectedtotheground→theEE895featuresI2C interface.
The VCC_EM and the VCC_IO are connected to the typical 5 V bus voltage.
The I2C host keeps the EE895 enabled with the pin 3 – EN and can read the values at any time, pin 6 - RDY is
not used.
4 Digital Interface
The EE895 features standard I2C and UART interfaces. The interface selection is made with pin 7 – ISEL, see
Tab. 2 Interface selection. On both interfaces, I2C and UART, the data is encapsulated in Modbus Protocol Data
Units (Modbus PDUs).
PLEASE NOTE
Modbus implementation details and request/response examples are described in detail in the Modbus
Application Note AN0103 (available at www.epluse.com/ee895).
4.1 I2C Interface
The EE895 supports the standard I2C specification. For detailed information about the I2C interface, please refer
to NXP document „I2C-bus specification and user manual“, Rev. 6, 4 April 2014:
https://www.nxp.com/docs/en/user-guide/UM10204.pdf
The I2C interface simultaneously supports two protocols on two different slave addresses:
▪ Modbus over I2C address 0x5F
▪ I2C simplified address 0x5E
These addresses are fixed, they cannot be changed by the user.
4.1.1. Modbus Protocol Over I2C Interface
I2C slave address: 0x5F
The I2C interface encapsulates the data according Modbus PDU packets, including CRC:
SSlave Address W A Request: Modbus PDU + Modbus CRC P
SSlave Address R A Response: Modbus PDU + Modbus CRC P
Every byte of the Modbus PDU and the Modbus CRC must be acknowledged (according to I2C specification, not
shown above).

User Manual EE895
Miniature Sensor Module for CO2, Temperature and Barometric Pressure | 14
The EE895 module supports repeated START or STOP conditions between the request packet and the response
packet. If a START condition and an address match are detected, the EE895 will stay active until a STOP
condition is received or an idle timeout of 500 ms occurs. This might increase the power consumption and self-
heating. The I2C master shall ensure that the data is retrieved as soon as possible in case of a repeated START.
For the Modbus register map please refer to chapter 4.3 Modbus Register Map.
NOTICE
The CRC16 shall be calculated including the unshifted slave address.
Example of command reading the temperature (floating point value) T = 25.30 °C from the register 0x3EA:
EE895
Request [Hex]: S BE 03 03 EA 00 02 E8 C5 P
Start Slave address
7-bit shifted
Function
code
Starting
address Hi
Starting
address Lo
Qty. of
registers Hi
Qty. of
registers Lo CRC Stop
SBE 03 03 EA 00 02 E8 C5 P
Response [Hex]: S BF 03 04 00 00 41 DC 74 3F P
Start Slave address
7-bit shifted
Function
code
Byte
count
Register 1
value Hi
Register 1
value Lo
Register 2
value Hi
Register 2
value Lo CRC Stop
SBF 03 04 00 00 41 DC 74 3F P
For decoding of float values stored according standard IEEE 754, please refer also to the Modbus Application
Note AN0103.
Example of Decoding:
Modbus response [Hex]
Byte 1 Byte 2 Byte 3 Byte 4 Decimal value
41 DC 00 00 27.50
PLEASE NOTE
For obtaining the correct value, both registers have to be read with a single request. The measured value
can change between two Modbus requests. Exponent and mantissa may get inconsistent in this case.
4.1.2. I2C Simplified Protocol
I2C slave address: 0x5E
This I²C protocol is intended for I2C master reading the measured values from EE895 in “EEPROM-like-mode”.
The simplified I2C does not support any error detection (such as CRC) and provides the measured data in 8
subsequent registers, as 16 bit integers.
Slave
address 0x00 0x01 0x02 0x03 0x04 0x05 0x06 0x07
0x5E CO2
high byte
CO2
low byte
T
high byte
T
low byte
reserved*)
high byte
reserved*)
low byte
p
high byte
p
low byte
*) Reserved for future use
The read pointer is the first register to be set. Additional bytes are answered by the EE895 module
with NACK. If more bytes are read than the 8 registers, the EE895 answers with 0xFF (i.e. the SDA line is not
pulled down). If a START condition and an address match are detected, the EE895 will stay active until a STOP
condition is received or an idle timeout of 500 ms occurs.

User Manual EE895
Miniature Sensor Module for CO2, Temperature and Barometric Pressure | 15
The measured data is available as a 16 bit integer and is expressed in SI units:
Measurand Register pointer Unit Scale
CO2average, pc1) 0x00 ppm 1:1
T0x02 °C 1:100 *)
p0x06 mbar 1:10 **)
CO2average, npc2) 0x08 ppm 1:1
CO2raw, pc1) 0x0A ppm 1:1
CO2raw, npc2) 0x0C ppm 1:1
1) pc ... pressure compensated
2) npc ... not pressure compensated
*)Example:2 575means25.75°C
**)Example:10 130means1 013mbar
Tab. 7 Data availability from the EE895 Miniature Sensor Module
Example for reading all measurands (7-bit address shifted):
EE895
Request [Hex]: S BC 00 P
Start Slave address
7-bit shifted
Register
pointer Stop
SBC 00 P
Response [Hex]: S BD 03 B0 0A B7 8D 00 26 70 P
Start Slave address
7-bit shifted
CO2
high byte
CO2
low byte
T
high byte
T
low byte
res.*)
high byte
res.*)
low byte
p
high byte
p
low byte Stop
SBD 03 B0 0A B7 80 00 26 70 P
*) Reserved for future use
Conversion:
Measurand Response [Hex] Response [Dec] Value
CO20x03B0 944 944 ppm
T0x0AB7 2743 27.43 °C
p0x2670 9840 984.0 mbar
Tab. 8 Interpretation of data from the response

User Manual EE895
Miniature Sensor Module for CO2, Temperature and Barometric Pressure | 16
Example for reading the air pressure value (7-bit address shifted):
EE895
Request [Hex]: S BC 06 P
Start Slave address
7-bit shifted
Register
pointer Stop
SBC 06 P
Response [Hex]: S BD 26 70 P
Start Slave address
7-bit shifted
p
high byte
p
low byte Stop
SBD 26 70 P
*) Reserved for future use
Conversion:
Measurand Response [Hex] Response [Dec] Value
p0x2670 9840 984.0 mbar
Tab. 9 Interpretation of data from the response
4.2 UART Interface
4.2.1. Modbus Protocol Over UART Interface
Modbus slave address: 0x5F
The interface settings are: Baud rate 9600, 8 Data, No parity, 1 Stop bit (9600 8 N 1)
The slave address and the interface settings are fixed, they cannot be changed by the user.
The EE895 module shall be addressed according to the specification “Modbus over serial line V1.02”, see
https://modbus.org/docs/Modbus_over_serial_line_V1_02.pdf.
Modbus frame description (screenshot taken from the “Modbus over Serial Line Specification and Implementation
Guide V1.02” mentioned above):

User Manual EE895
Miniature Sensor Module for CO2, Temperature and Barometric Pressure | 17
4.3 Modbus Register Map
Following Modbus register map is valid for both, the I2C and the UART interface. The measured data is saved as
32 bit floating point values (data type FLOAT) and as 16 bit signed integer values (data type INTEGER), please
refer to Tab. 10 and Tab. 11 below:
FLOAT 32
Parameter Unit Register number1) [DEC] Register address2) [HEX]
Read register: function code 0x03
Temperature T °C 1003 0x3EA
Temperature T °F 1005 0x3EC
Temperature T K1009 0x3F0
CO2(average), pc3) ppm 1061 0x424
CO2(raw), pc3) ppm 1063 0x426
CO2(average), npc4) ppm 1065 0x428
CO2(raw), npc4) ppm 1067 0x42A
Pressure p mbar 1201 0x4B0
Pressure p psi 1203 0x4B2
1) Register number starts from 1
2) Register address starts from 0
3) pc ... pressure compensated
4) npc ... not pressure compensated
Tab. 10 I2C and UART Modbus register map for 32 bit floating point values
INT16
Parameter Unit Scale3) Register number1) [DEC] Protocol address2) [HEX]
Read register: function code 0x03
Temperature T °C 100 4002 0xFA1
Temperature T °F 50 4003 0xFA2
Temperature T K50 4005 0xFA4
CO2(average), pc4) ppm 14031 0xFBE
CO2(raw), pc4) ppm 14032 0xFBF
CO2(average), npc5) ppm 14033 0xFC0
CO2(raw), npc5) ppm 14034 0xFC1
Pressure p mbar 10 4101 0x1004
Pressure p psi 100 4102 0x1005
1) Register number starts from 1
2) Register address starts from 0
3) Examples: For scale 100, the reading of 2550 means a value of 25.5. For scale 50, the reading of 2550 means a value of 51.
4) pc ... pressure compensated
5) npc ... not pressure compensated
Tab. 11 I2C and UART Modbus register map for 16 bit signed integer values
4.4 General Purpose Registers for Individiual Use
There are two registers reserved for any customer use, e.g. serial number, traceability, etc.
Register number1) [DEC] Register address2) [HEX] Space (standard Modbus register)
Write register: function code 0x06 / Read register: function code 0x03
5801 0x16A8 16 bits / 2x8 bits / 2 bytes
5802 0x16A9 16 bits / 2x8 bits / 2 bytes
1) Register number starts from 1
2) Register address starts from 0
Tab. 12 Registers for special customer purpose

User Manual EE895
Miniature Sensor Module for CO2, Temperature and Barometric Pressure | 18
4.5 EE895 Commands
The following commands are available via Modbus over I2C and Modbus over UART.
PLEASE NOTE
I2C simplified does not support Modbus encapsulation. Therefore, no Modbus communication and no
settings are possible.
4.5.1. Information
Function
code
Register
address1)
[HEX]
Description Note
0x03
0x00 Serial number EE895 serial number, ASCII, 0 terminated
0x08 FW-Version (Major, Minor)
High-Byte = Major Version
Low-Byte = Minor Version
Example: 0x011A = 1.26 [01=1; 1A=26]
0x09 Sensor name 2 ASCII characters for each Register (“EE895”)
String is 0-terminated
1) Register address starts from 0
Tab. 13 Available commands for I2C and UART
PLEASE NOTE
When reading the serial number or the sensor name, it is always necessary to read all 8 registers, even if the
desired information requires less.
4.5.2. General Settings
The following functions allow for EE895 settings. These are stored in the RAM, therefore they are volatile.
Measuring mode: continuous or single shot
Function
code
Register
address1)
[HEX]
Note
Read 0x03
Write 0x06 0x1F8
[Bit 0] Default status = 0
0 = continuous. The EE895 measures at the regular interval set with the
command “CO2measuring interval”, see chapter 4.5.3.
1 = single shot. The EE895 measures only with the command
“Measuring trigger”, see below.
[Bit 1..15] reserved (must be written as 0)
1) Register address starts from 0
Tab. 14 Continuous or single shot measurement

User Manual EE895
Miniature Sensor Module for CO2, Temperature and Barometric Pressure | 19
Measuring status: indicates when new single shot measurement is possible.
Function
code
Register
address1)
[HEX]
Note
0x03 0x1F9
[Bit 0]: Data ready. The data are available for read out.
0 = busy, 1 = ready
[Bit 1]: Trigger ready. The EE895 is ready for new measurement cycle.
The minimum time interval between two triggers is 10 s.
0 = trigger not possible
1 = ready for new trigger
[Bit 2..15]
reserved (do not use)
1) Register address starts from 0
Tab. 15 Single shot measurement possible
Measuring trigger: command for the single shot measurement. For accurate measurement results, there are
recommended six single shot measurements under stable temperature conditions.
Function
code
Register
address1)
[HEX]
Note
0x06 0x1FA
[Bit 0]: Measurement Trigger
0 = don’t care
1 = Start new measurement cycle
[Bit 1..15]
reserved (must be written as 0)
1) Register address starts from 0
Tab. 16 Command single shot measurement
EE895 detailed status
Function
code
Register
address1)
[HEX]
Note
0x03 0x258
[Bit 0]: CO2measurement too high
[Bit 1]: CO2measurement too low
[Bit 2]: T measurement too high
[Bit 3]: T measurement too low
[Bit 6]: p measurement too high
[Bit 7]: p measurement too low
[Bit 8…15]: reserved (do not use)
1) Register address starts from 0
Tab. 17 Status details

User Manual EE895
Miniature Sensor Module for CO2, Temperature and Barometric Pressure | 20
4.5.3. CO2Parameter Settings
The CO2parameter settings are non-volatile since they are stored in the flash memory.
Function
code
Register
address1)
[HEX]
Description Unit Note
0x06
0x1450 CO2measuring interval S
16 bit integer unsigned
Scale 1:10. Example: 150 = 15 seconds
Range100…36 000
Default 15 s
0x1451 CO2filter coefficient*) -
16 bit integer unsigned
Range 1…20
Default: 4
0x1452 CO2customer offset ppm
16 bit integer signed
Range-32 786…32 785
Default: 0 ppm
1) Register address starts from 0
Tab. 18 CO2parameter settings
*) The EE895 features an exponential moving average filter which to a certain degree suppresses the influence
of short-term CO2variations onto the output CO2data. The filter coefficient is user selectable and affects the
response time of the EE895. A higher filter coefficient leads to smoother output data and to longer response time,
see figure Fig. 12. Fig. 13 shows the number of samples required to reach 63% or 90% of a CO2step as function
of the filter coefficient.
Fig. 12 Step response vs. samples
Other manuals for EE895
2
Table of contents
Other E+E Elektronik Control Unit manuals
Popular Control Unit manuals by other brands
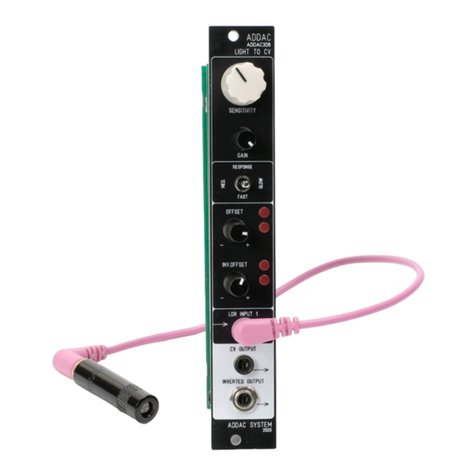
ADDAC System
ADDAC System ADDAC308 LIGHT TO CV user guide

oventrop
oventrop AQ Installation and operating instructions
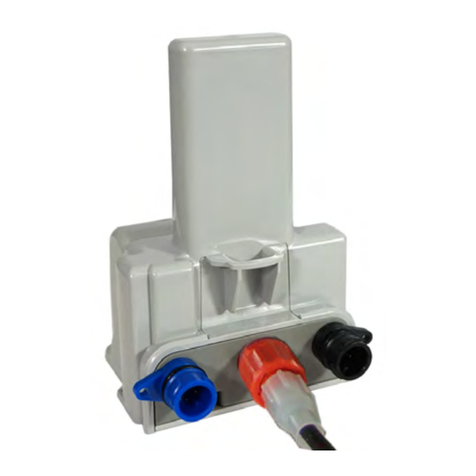
ITRON
ITRON OpenWay Riva installation guide
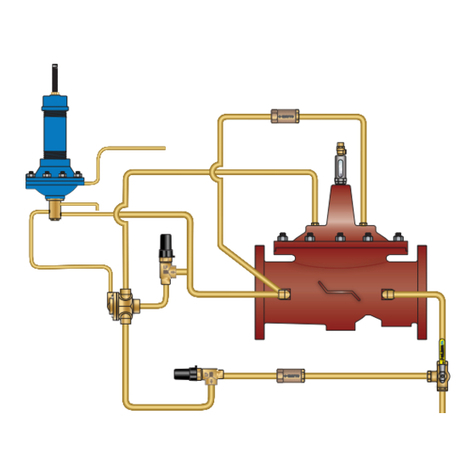
Watts
Watts LFM127-2 Series Installation, operation and maintenance
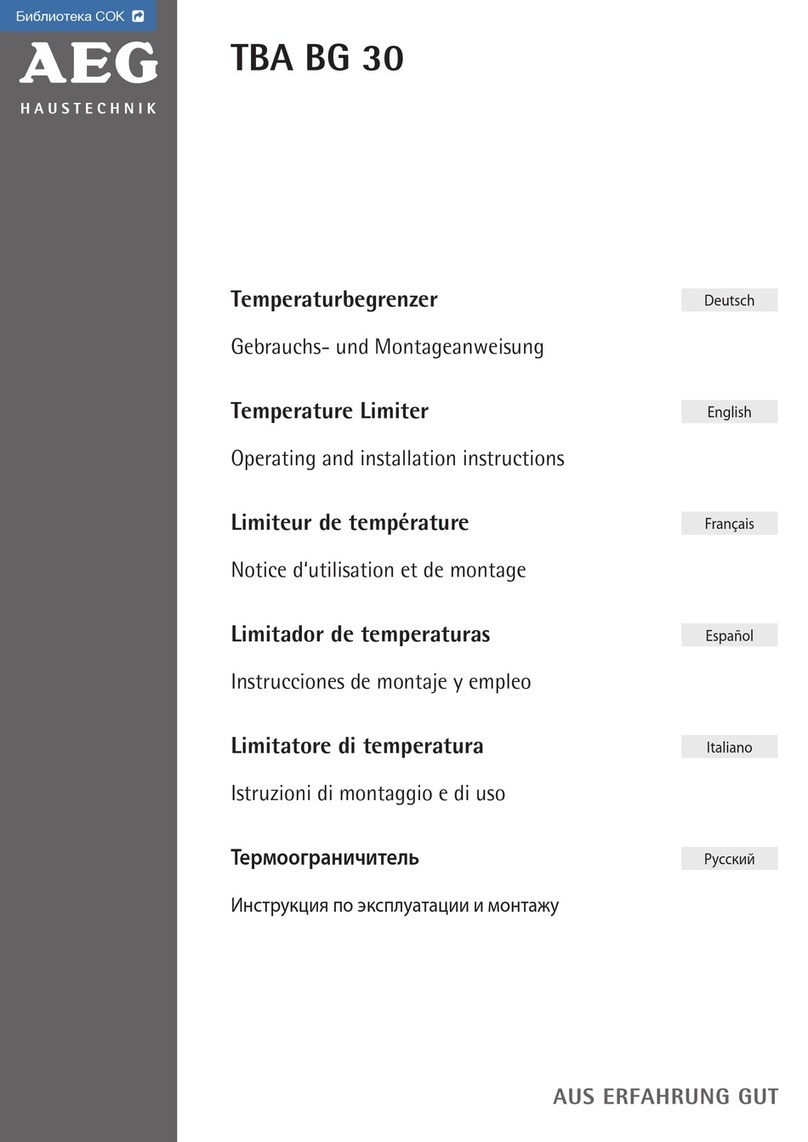
AEG
AEG TBA BG 30 Operating and installation instructions
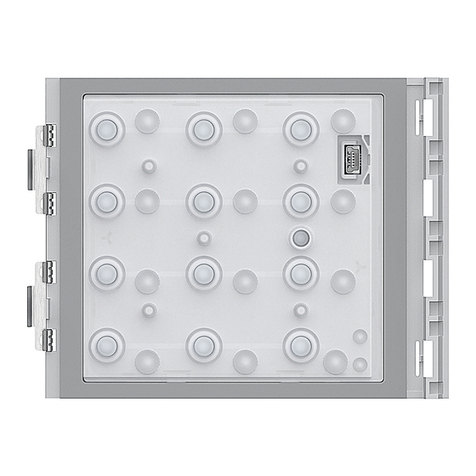
Bticino
Bticino Sfera video kit User and installation manual
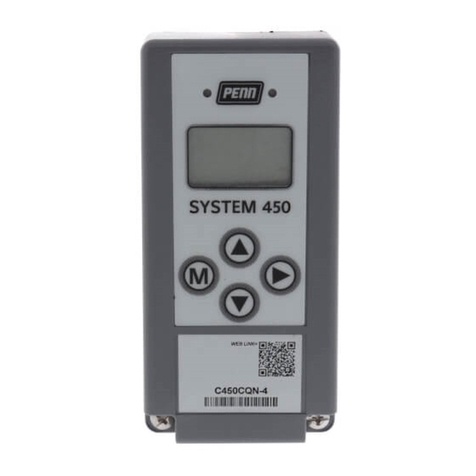
Johnson Controls
Johnson Controls System 450 Series Installation instructions and operators manual
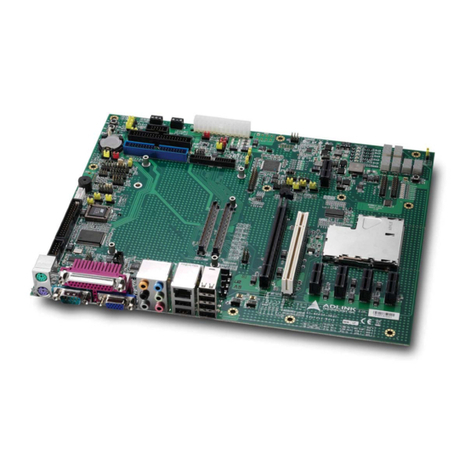
ADLINK Technology
ADLINK Technology com express user manual
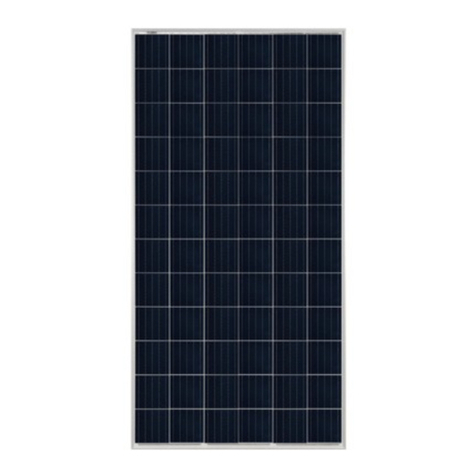
Sharp
Sharp ND-AH330H installation manual
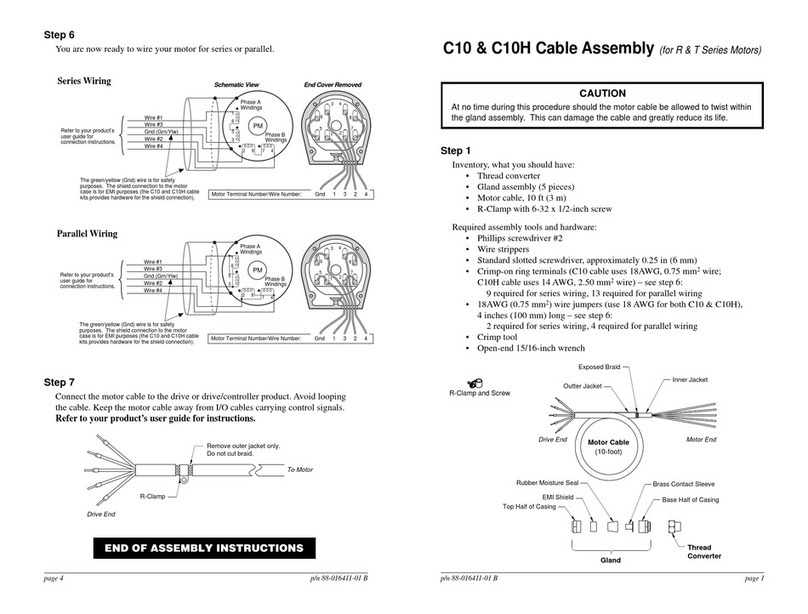
Parker
Parker C10 Cable Assembly
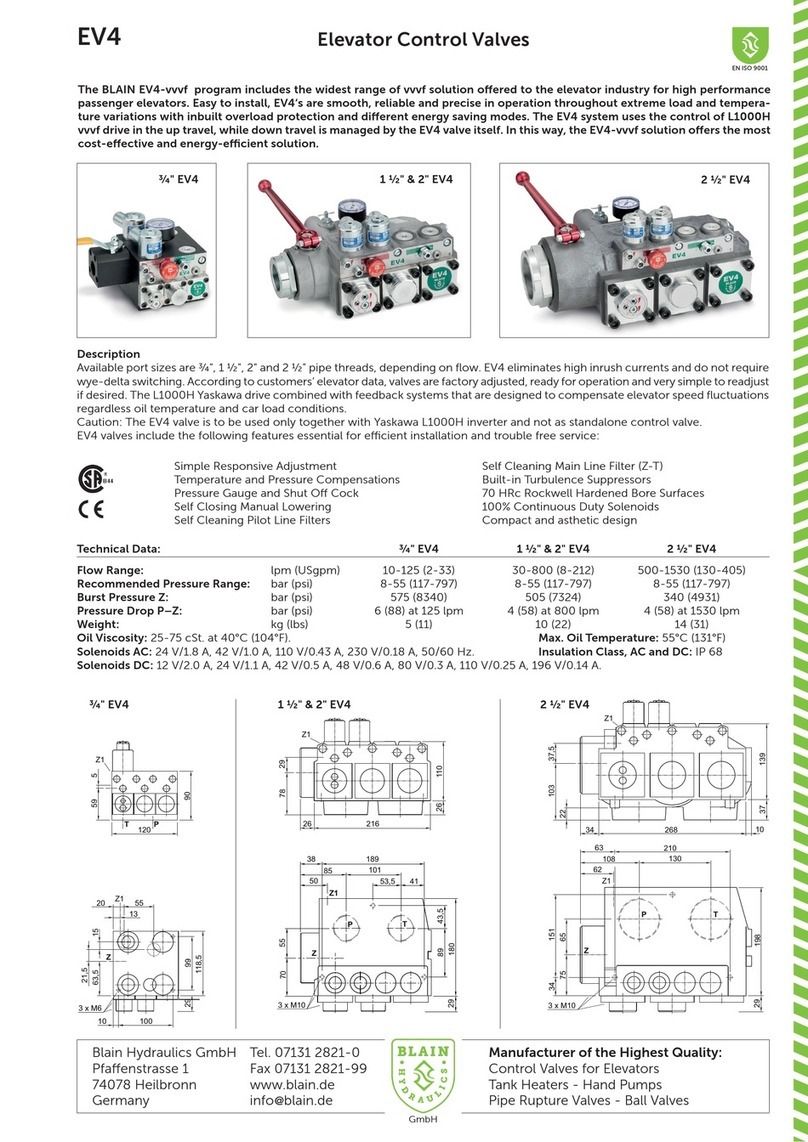
Blain Hydraulics
Blain Hydraulics EV4 manual
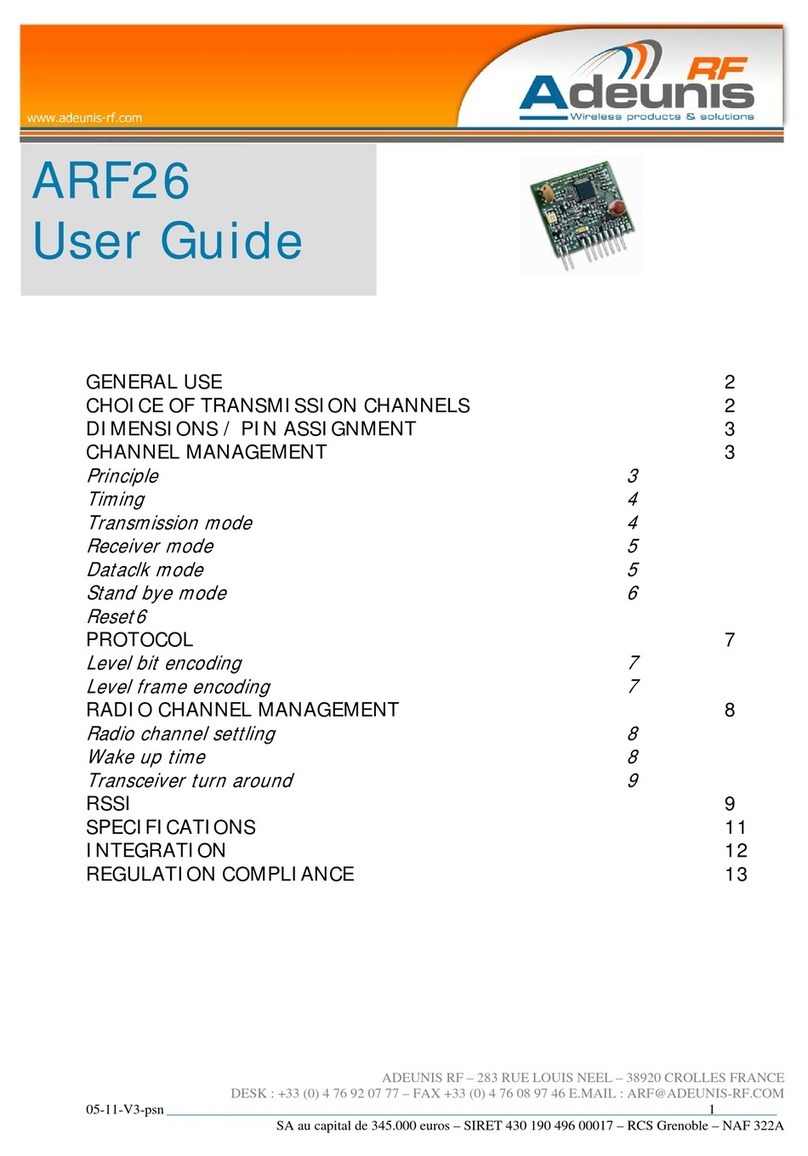
Adeunis RF
Adeunis RF ARF26 user guide