Festo SLG-8 Series User manual




















This manual suits for next models
2
Other Festo DC Drive manuals

Festo
Festo DGC-HD Series User manual

Festo
Festo DGOL-16 PPV-A B Series User manual
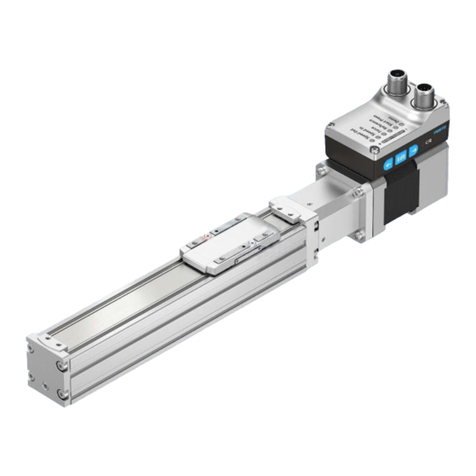
Festo
Festo EMCS-ST User manual
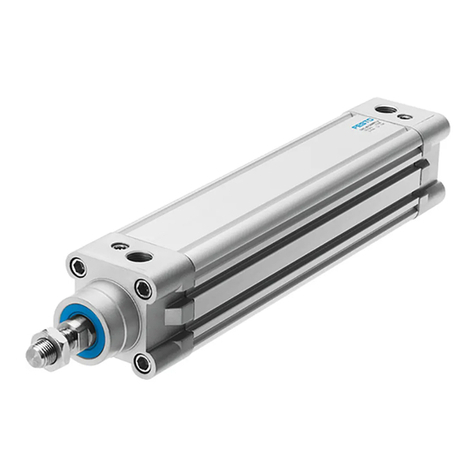
Festo
Festo DNCM POT Series User manual

Festo
Festo EMCS-ST User manual
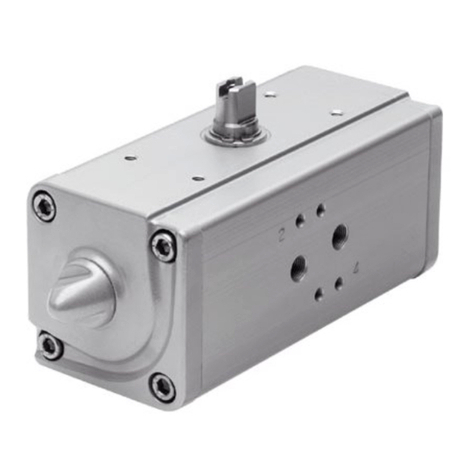
Festo
Festo DAPS Series User manual
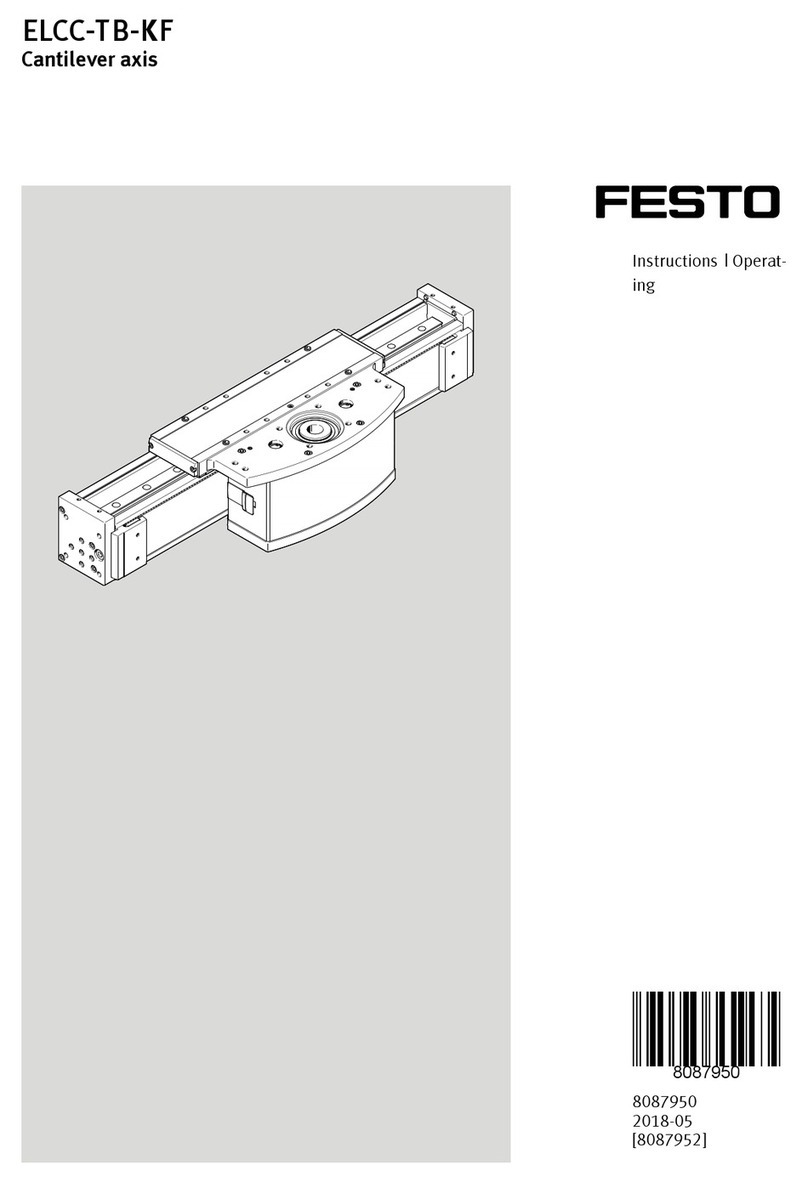
Festo
Festo ELCC-TB-KF Parts list manual
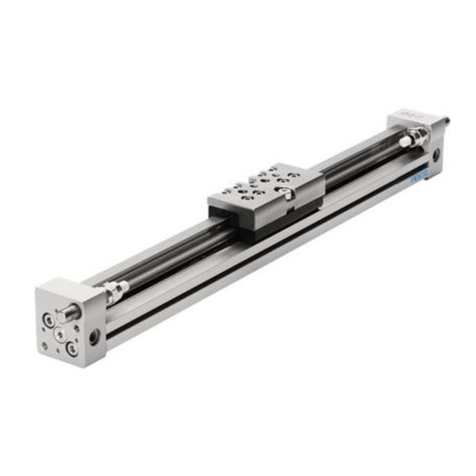
Festo
Festo DGC G Series Setup guide
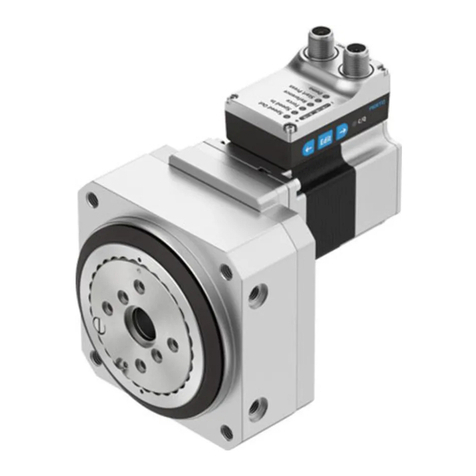
Festo
Festo ERMS Parts list manual
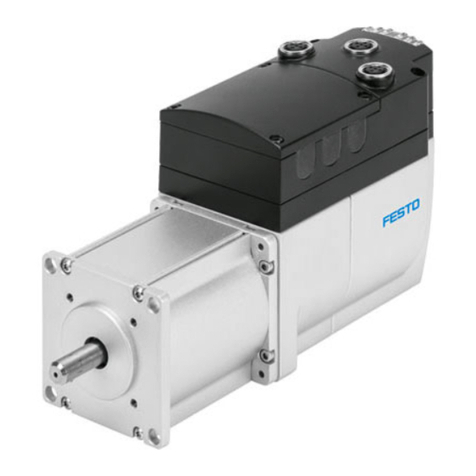
Festo
Festo EMCA-EC-67 CO Series Reference guide
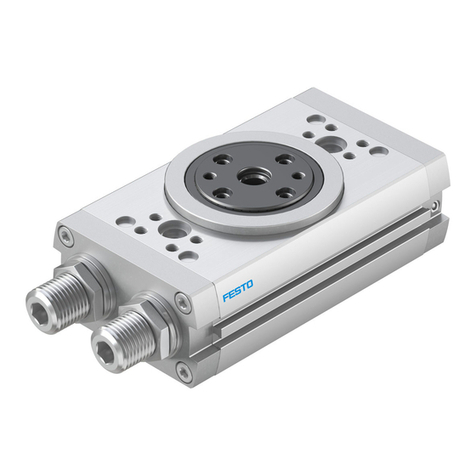
Festo
Festo DRRD Series User manual
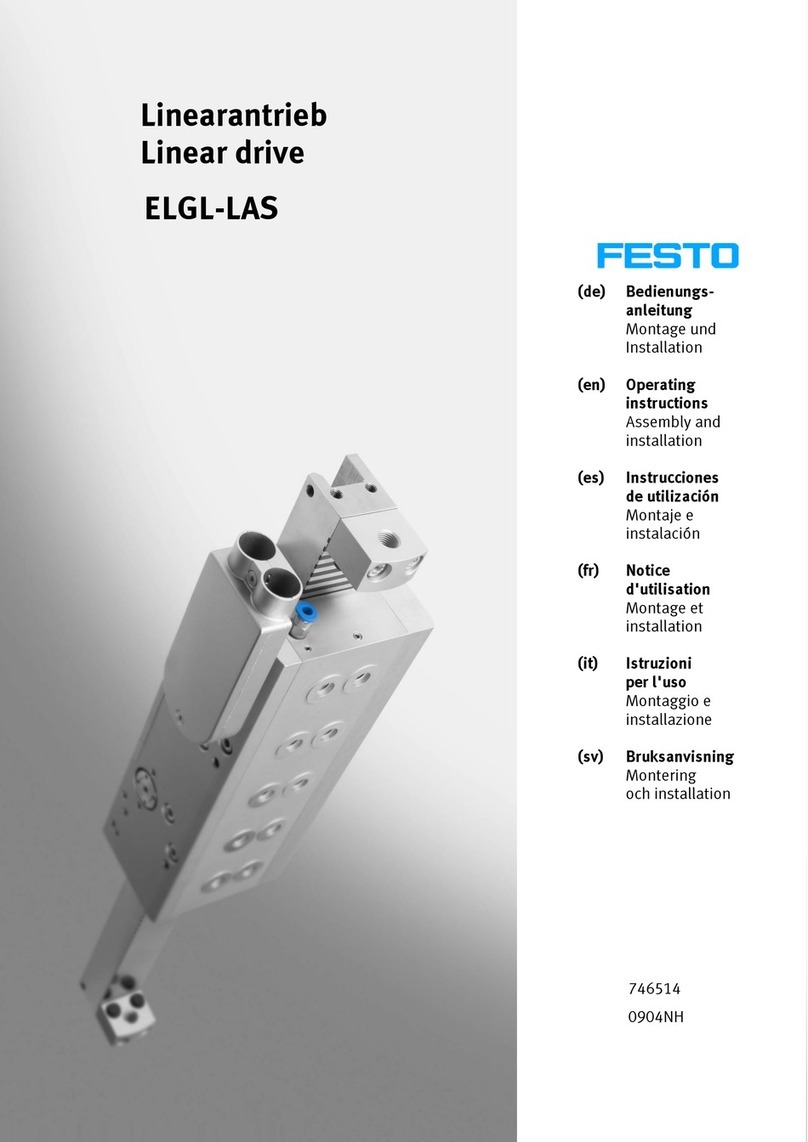
Festo
Festo ELGL-LAS User manual
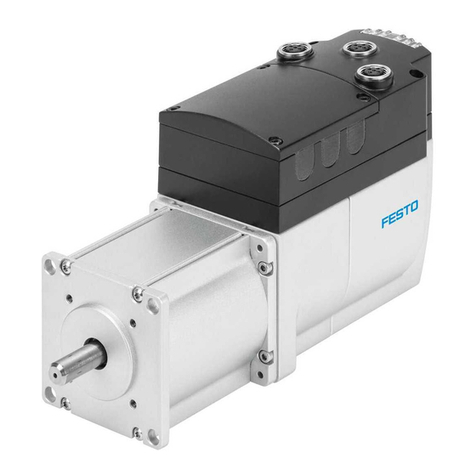
Festo
Festo EMCA-EC-67-DIO Series Parts list manual
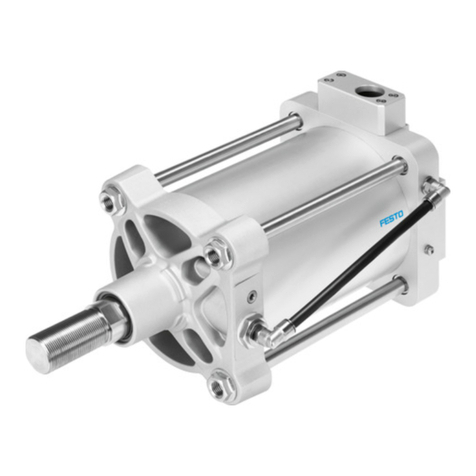
Festo
Festo DFPI ND2P-E-NB3P Series User manual
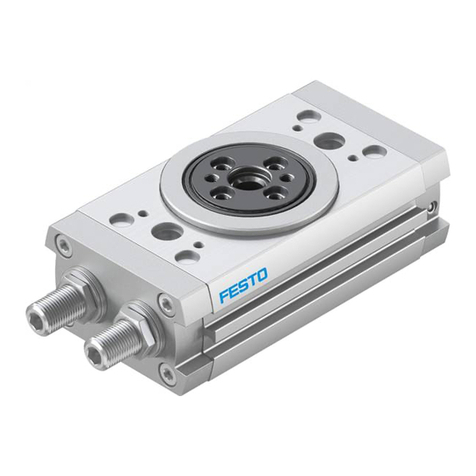
Festo
Festo DRRD-12 User manual
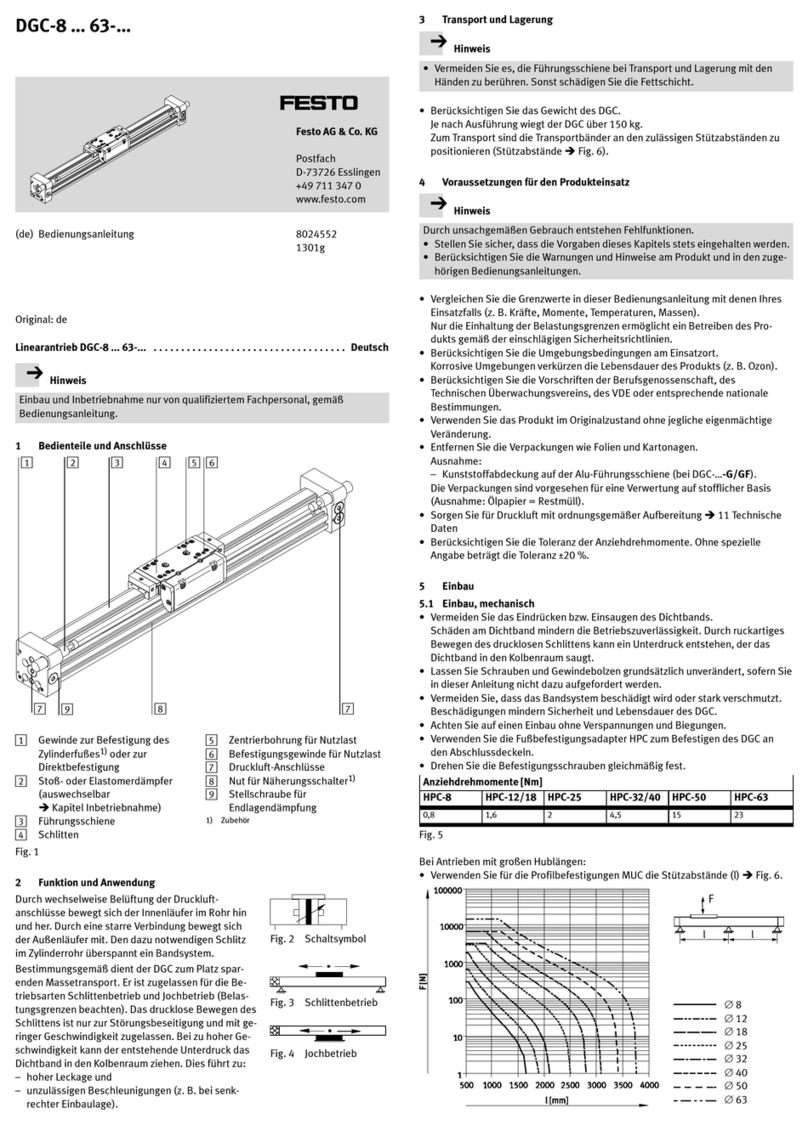
Festo
Festo DGC-8 Series User manual
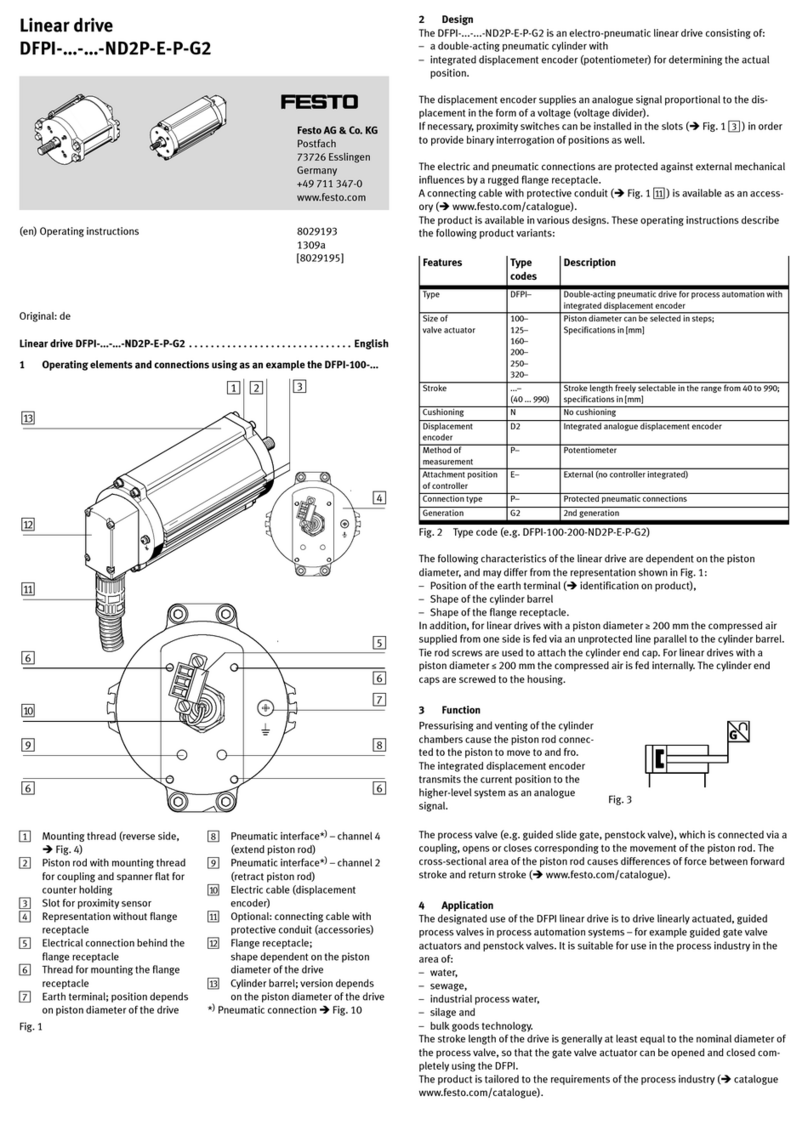
Festo
Festo DFPI-***-***-ND2P-E-P-G2 User manual

Festo
Festo DGCI Series User manual
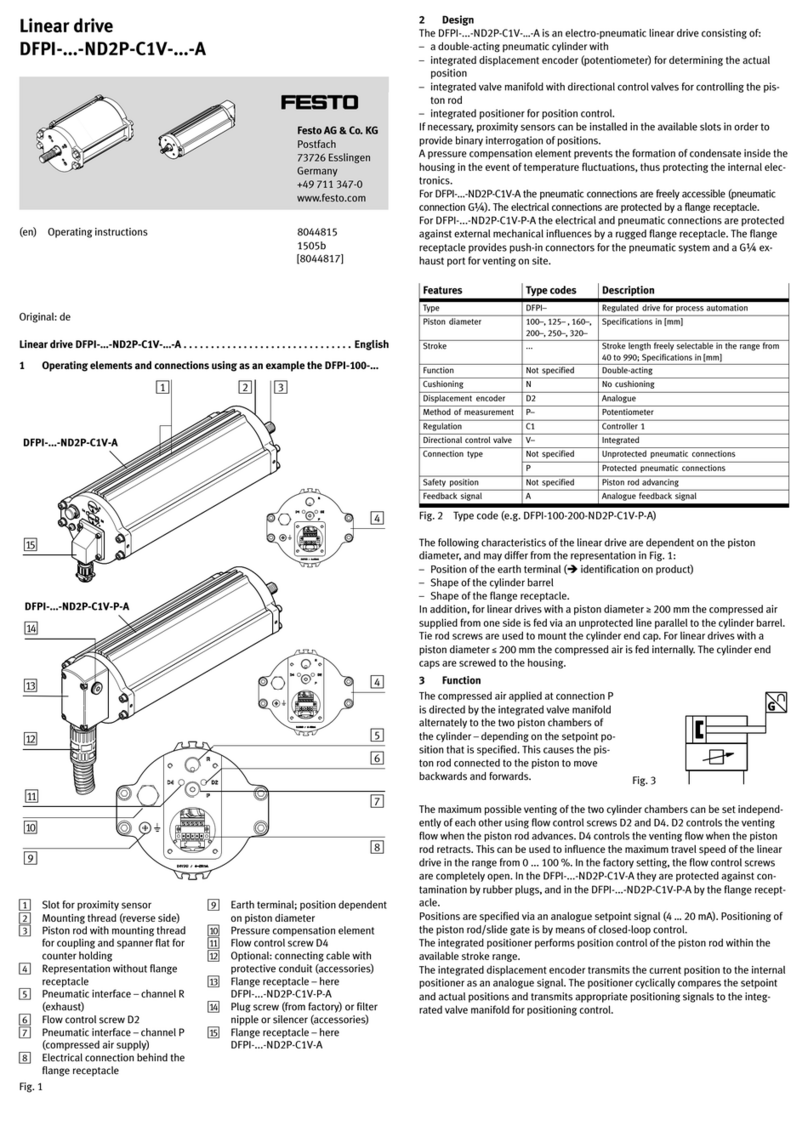
Festo
Festo DFPI-***-ND2P-C1V-***-A User manual
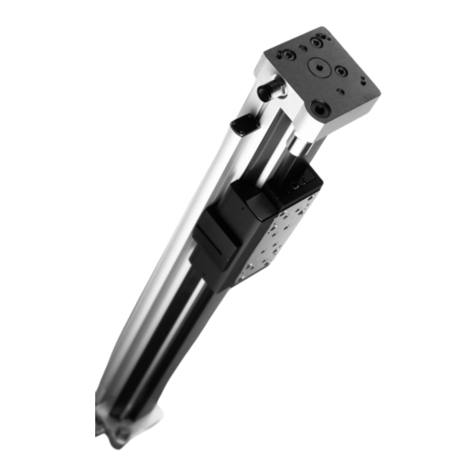
Festo
Festo DGCI Series User manual
Popular DC Drive manuals by other brands
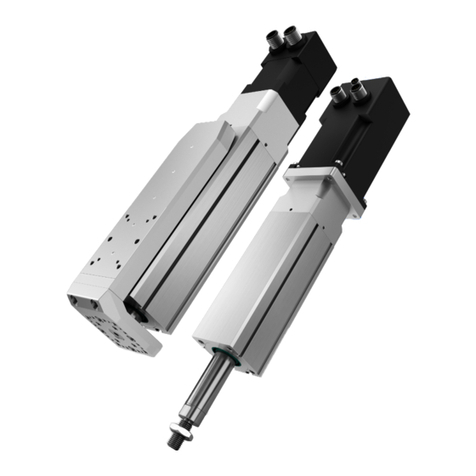
Unimotion
Unimotion MCE Assembly and maintenance instructions
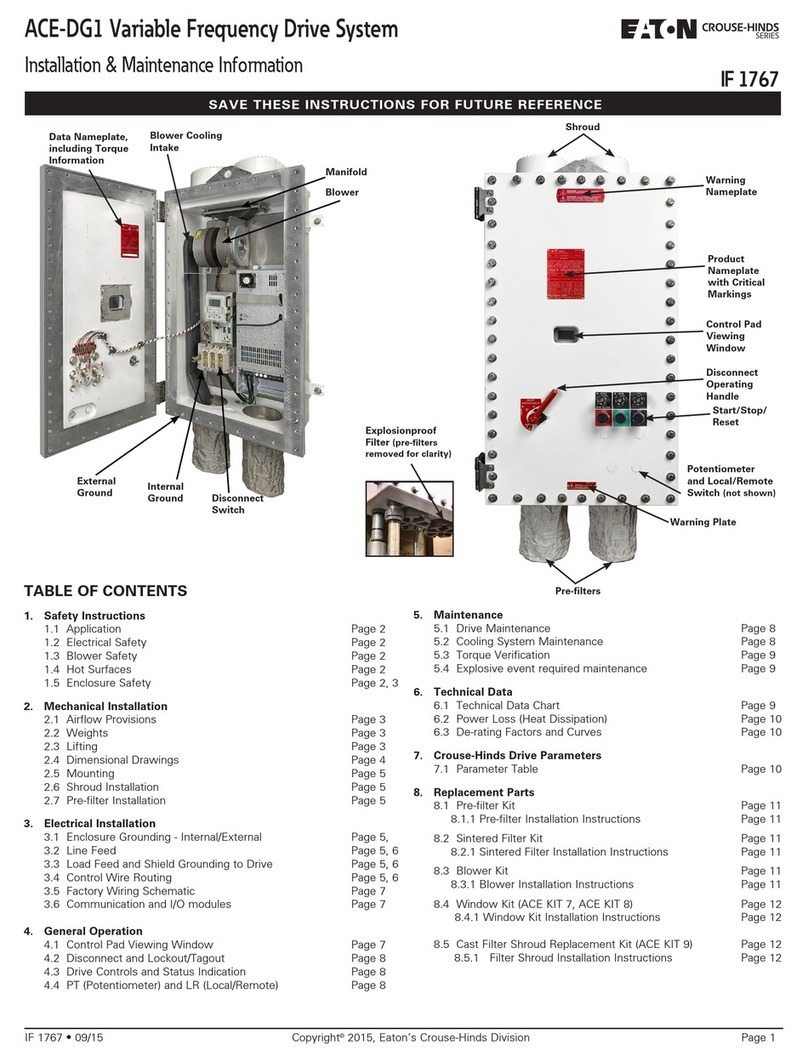
Eaton
Eaton Crouse-hinds series Installation & maintenance information
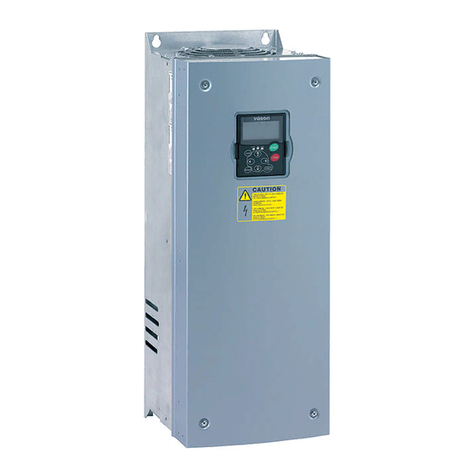
Vacon
Vacon NX user manual

Cerus Industrial
Cerus Industrial Titan GS Series Installation, operation & maintenance manual
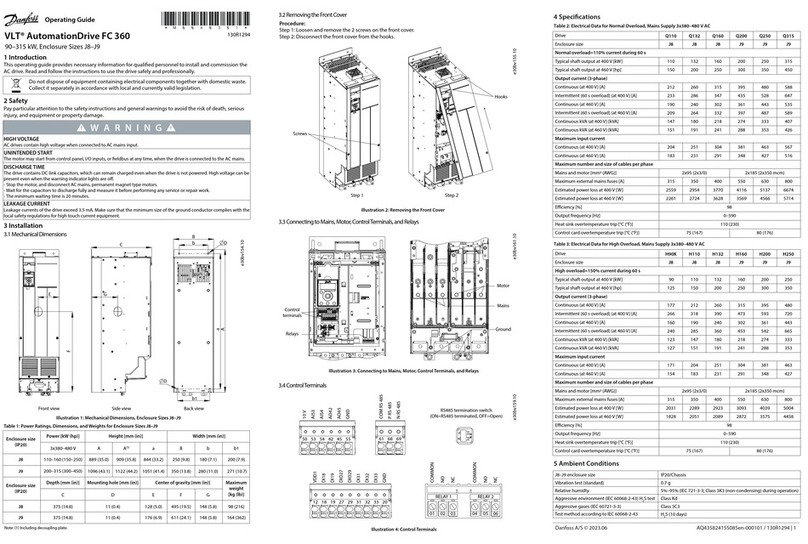
Danfoss
Danfoss VLT AutomationDrive FC 360 operating guide
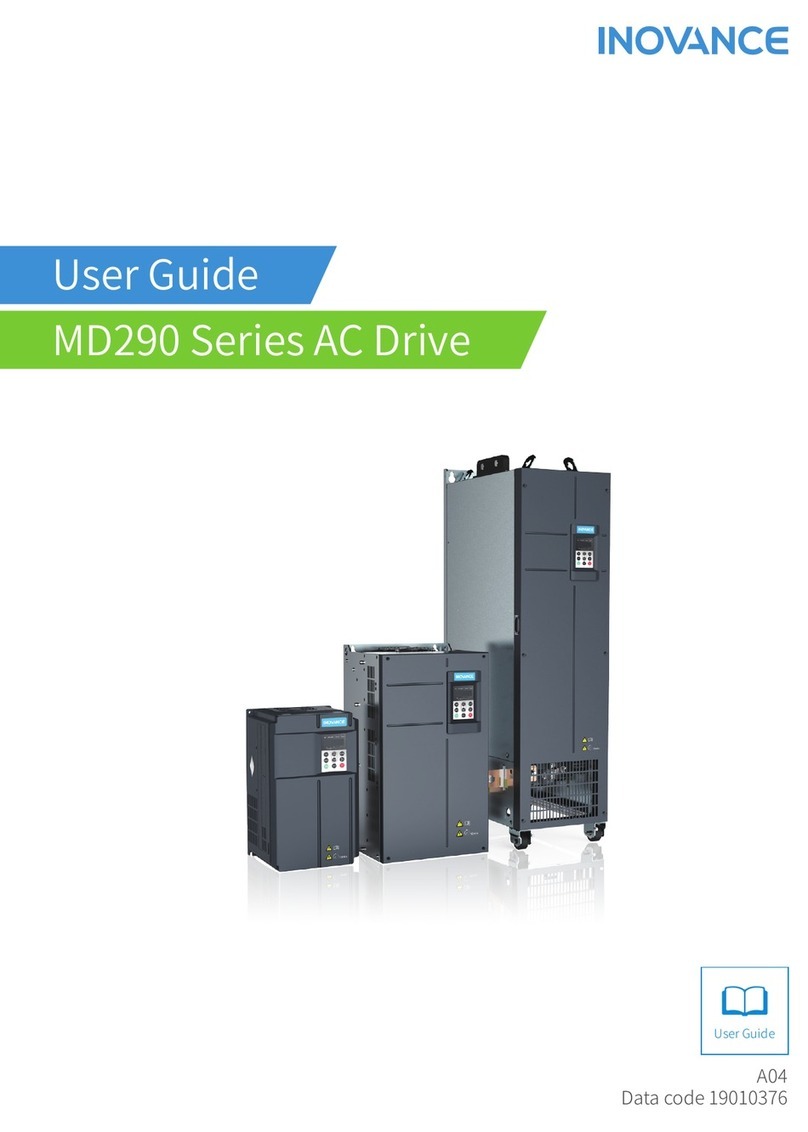
Inovance
Inovance MD290 Series user guide