FIRETRACE Direct Systems User manual

Firetrace® “Direct” Automatic Fixed
Fire Suppression Systems
For Mobility Drive from Chair Applications
Please read instructions carefully
prior to starting installation
Issue 5 Nov 2017

Contents
•System Overview
•System Layout
•Cylinder Installation
•Trace Detection tube routing
•Trace Detection tube installation
•Trace Detection tube fixings
•Trace Detection tube bend radius
•Connecting the Trace Detection Tube
•Commissioning Instructions
•Optional Pressure Switch
•Servicing and Maintenance

System Overview.
The Fixed Firetrace® system is a simple self-actuating device that is designed to suppress fires
within an identified risk area. The cylinder is not intended for portable use.
The system works by using pressurised Firetrace® linear detection tubing that is installed
throughout the risk area. This tubing is heat sensitive and when subjected to a temperature
above 120 Degrees centigrade, or when touched by flame, the Firetrace® tubing will rupture
and form a diffuser.
Tube burst forming diffuser
The FE-36 extinguishant is then deployed via this diffuser directly into the heart of the fire.
The Firetrace® system requires no external power source or separate detectors and owing to
its simple design ensures that all of the extinguishant is always deployed in the risk area.
The system can be fitted with a volt free single pressure switch (FT0124) or volt free twin
pressure switch (FT0124/T75) which, when connected to the cylinder, not only provides
constant monitoring of the system but can also send a signal to indicate a discharge via a Self
contained Alarm Sounder (FT0178).
It is important that both the cylinder & Firetrace® tubing are correctly installed and that the
system is subjected to a regular maintenance regime in line with BS5306-3 by a competent
engineer.
FT0178 Self-Contained Alarm Sounder

System Layout
Optional Monitoring Pressure Switch
FT0124
Twin Contact Monitoring Switch also
available
FT0124/T75
All our standard low pressure Firetrace® systems are supplied with all the necessary fixings for
the Trace detection tube.
End of Line Charging adapter –
FT0118
Shall be located in a suitable
position on the dash board
Red trace detection tube –FT0115*
Isolate
Valve
behind
pressure
gauge
Optional Self-Contained Audible Sounder
FT0178
Self-Contained Strobe Sounder also
available
FT0178/SS

Firetrace® Installation Instructions.
Cylinder
When installing the Firetrace® system it is important that a suitable cylinder location is
selected and that the cylinder is orientated correctly.
The cylinder location shall be in a clean area away from direct heat. The cylinder
must not be placed in a location where the ambient temperature is above 80 Degrees
centigrade.
The cylinder shall be readily accessible to allow future servicing / inspections and as close as
practicable to the risk area.
The cylinder shall be adequately fixed to a suitable load bearing surface.
Wherever possible the cylinder shall be mounted vertically and in exceptional circumstances
the cylinder can positioned at an angle of no more than 80 Degrees from vertical. (see cylinder label
for clarity)
It is recommended wherever possible that Firetrace® cylinders be mounted vertically.
Where vertical locating is not possible the systems can be mounted within 80° of
vertical.
As indicated in the above drawing when cylinders are fitted at an angle the
gauge must face uppermost.
THIS FIRETRACE® SYSTEM IS SUITABLE FOR HORIZONTAL
MOUNTING.
✓
✓
X
Cylinder Gauge
80° Max

Firetrace® Automatic Detection Tubing
The Firetrace® Automatic Detection tubing is the key part of the system and acts not only as the
detector but also as the delivery method for the FE-36.
The correct installation of the tubing is important to achieve optimum performance from the system.
The tubing must be mechanically protected outside the identified risk area and shall remain
accessible to allow future servicing.
As heat rises, the Firetrace® tubing is most efficient when mounted directly above the risk.
The tubing will activate at approximately 120 Degrees Centigrade and care must be taken to avoid
attaching the tubing where temperatures above this are achieved during normal operation.
It is recommended that the tube is a minimum of 150mm away from exceptionally hot surfaces or
fitted with additional sleeving to avoid false activation.
Tube Routing
As the Firetrace® detection tube is flexible the exact tube route can vary from vehicle to vehicle. The
basis of the system design is to circumnavigate the engine and dashboard area so that any potential
risks are covered. (Please see tube bending radius guide)
Trace Detection Tube installed around
the engine compartment
Trace Detection Tube located behind the
dashboard for extra protection
terminated at an End of Line Gauge
Firetrace® Cylinder
(Suitable for mounting up to 80° from vertical option)

Tube Fixings
The Firetrace® Automatic Detection tubing is the key part of the system and acts not only as the
detector but as the delivery method for the extinguishant as well.
The correct installation of the tubing is important to achieve optimum performance from the
system.
The detection tubing must be adequately fixed to retain its position and withstand the
vibration.
The tubing is a soft polymer and is susceptible to wear / chaffing when repeatedly rubbed
against a hard or sharp surface. The tubing shall be protected using nylon Kopex at all fixing
points and where it passes through holes.
The following photographs show both “Tyrap” and “P clip” fixings all of which are acceptable.
The Detection tubing shall be supported at maximum intervals of 150mm.
Always leave a small loop of tubing adjacent to the cylinder. Whilst this shall also be secured it
must be releasable to allow future servicing of the cylinder.
Where the tubing is installed with a group of other cables/pipes it must be positioned on the
underside of the loom and must never be located within the center of the loom.
The tubing must be physically protected outside the identified risk area using Kopex or
another flexible conduit and shall remain accessible to allow future servicing.
✓

Tube bending radius
The Firetrace® tubing acts as the detector and provides the delivery of the extinguishant. It is
imperative that the tubing is not kinked or crushed and the following minimum bending radius
must be adhered to.
Should the tubing be kinked or damaged in anyway then the Firetrace® tubing must be
replaced:
FT0115 Firetrace® tubing 6mm Minimum bending radius 60mm
Minimum Bend Radius
6mm tube = 60mm
Optimum Bend Radius
150mm

All compression fittings must be secured in the following manner:
a) Cut the tube end ensuring the cut is clean and free from burrs. Check that no debris/ swarf is
left in the tube.
b) Place the nut over the end of the tube with its threaded section towards the end of the tube.
c) Push the tube fully home into the body.
d) The nut shall be tightened finger tight and then using a 12mm Spanner pinched up to firm
hand tightness
e) Slacken off the assembly and inspect end to ensure flange has formed correctly then
reconnect and tighten down to ensure an effective seal.
Method of Assembly
1. Tubing must be cut off square.
2. Insert tubing into tubing nut.
3. Offer the tubing to the fitting so that the tubing bottoms on the tubing stop.
(this requires a firm push if cold)
4. Hold the tubing in contact with the tubing stop and screw the tubing nut down to
the recommended torque. (torque = 5.7 Nm)
5. Slacken off the assembly and inspect end to ensure flange has formed correctly then
reconnect to fitting and tighten down to ensure an effective seal.
✓
x
The use of a tube cutter (FT0127) is
recommended for an accurate cut of the
Trace Detection Tube.

Closed
Open
Commissioning the System
Warning Firetrace® cylinders contain 12 bar pressure
This procedure shall be read in conjunction with system layout earlier in this booklet.
Do not turn integrated isolate valve until system is fully commissioned (pressurised)
Locate cylinder and firmly secure with bracket provided
Remove black cap from the top of the cylinder. Connect red Trace detection tube, tighten silver nuts and
secure with appropriate clips
Remove blank plug from pressure switch port
Fit Schrader adapter FT0172 and pressurise to 12 Bar / 175 psi using a nitrogen bottle
or air pump.
Remove Schrader adapter FT0172, remove gauge from gauge
port and fit into pressure switch port. (Fit blanking plug into
Gauge port to keep dust and debris out)
Using tape, mark the location of the needle on the pressure gauge (Mid Green) and leave system for a
minimum of ten minutes per metre of Trace detection tube to check for any leaks on the detection
tube.
When satisfied pressure is good and no leaks have occurred, remove blank plug and open isolate valve
slowly using the key provided. Remove gauge from pressure switch port and fit into gauge port.
System is now live
Optional FT0124 pressure switch can be fitted in gauge adapter
on head assembly or if not pressure switch supplied, replace the blank
plug
Please note system will not operate with isolate
valve in closed position

Firetrace® Pressure switch (FT0124 & FT0124/T75) Optional
The optional Firetrace® pressure switch is used to monitor the system pressure and will activate
in the event of a pressure drop.
The switch can be introduced and removed from the cylinder whilst it is under pressure. This
allows its operation to be proven both during commissioning and future servicing.
The Pressure switch is fitted with a black rubber “o ring” which provides the air tight seal. This
“o ring”must be lubricated with silicone grease and free of any dirt or debris. Failure to ensure
the “o ring”is clean can lead to a leak which will require the system needing replacement.
The switch shall be screwed into the cylinder hand tight ONLY.
The switch contains both normally open & normally closed contacts.
When connecting the pressure switch to the (FT0178) Firetrace Self-Contained Alarm Sounder
the BROWN & GREY wires are used. The unused wires must be sleeved / insulated.
Always leave a small loop of spare cable adjacent to the pressure switch to allow future
removal.
FT0124 Monitoring Switch
Set at 5 bar falling.
Common Brown
Normally open Grey
Normally closed Black
Earth Green/yellow
FT0124/T75 Twin Monitoring Switch.
Switch 1 Set at 5 bar falling.
Switch 2 Set at 7 bar falling.
Common Brown
Normally open Grey
Normally closed Black
Earth Green/yellow

Service & Maintenance
The Firetrace® systems can operate in a harsh environment and are occasionally subjected to
high temperatures and extreme vibration. It is essential that the systems are regularly serviced
to ensure their correct operation.
In order to comply with British Standard BS 5306 (section three) the following maintenance
tasks shall be carried out periodically.
The British standard recommends that each system is visually inspected every 3 months and
then fully serviced at maximum intervals of 12 Months by a competent engineer.
All FE-36 systems require discharge testing at maximum 10 Year intervals.
Firetrace® Limited recommends a visual inspection of a Firetrace® system at
least every three months.
The following checks shall be carried out on this inspection.
•Check the pressure gauge is reading mid-green.
•Carry out a visual check of the trace detection tube.
•Check all detection tube fittings for soundness.
•Check external surface of the cylinder for evidence of rust or corrosion.
•Report any potential problems immediately.

Firetrace® Limited recommend that all systems are fully serviced every
12 Months by a competent engineer
If there’s no visible sign of pressure drop then;
✓Check date of manufacture and record when discharge test is required.(10 years from New
Date)
✓Check external condition of cylinder. Replace if there is any sign of damage or wear.
✓Check gauge is facing upwards (if applicable) and that cylinder is installed as upright as
possible. Where necessary reposition cylinder.
✓Remove cylinder gauge and ensure correct operation. Clean and lubricate O ring and
refit.
✓*Remove pressure switch (if applicable) and ensure correct operation. Clean and
lubricate pressure switch O ring and refit switch.
✓Record details and date of service on cylinder label. Replace cylinder into bracket and
ensure it is secured by clamp / Tyrap.
If there is visible sign of pressure drop then replace the cylinder and trace
detection tubing.

Address:
Unit 22, Knightsdale Road,
Ipswich,
Suffolk.
IP1 4JJ
Telephone:
01473 744090
Facsimile:
01473 744901
Email:
Website:
www.firetrace.co.uk
Twitter:
@firetrace_uk
Table of contents
Other FIRETRACE Firefighting Equipment manuals
Popular Firefighting Equipment manuals by other brands
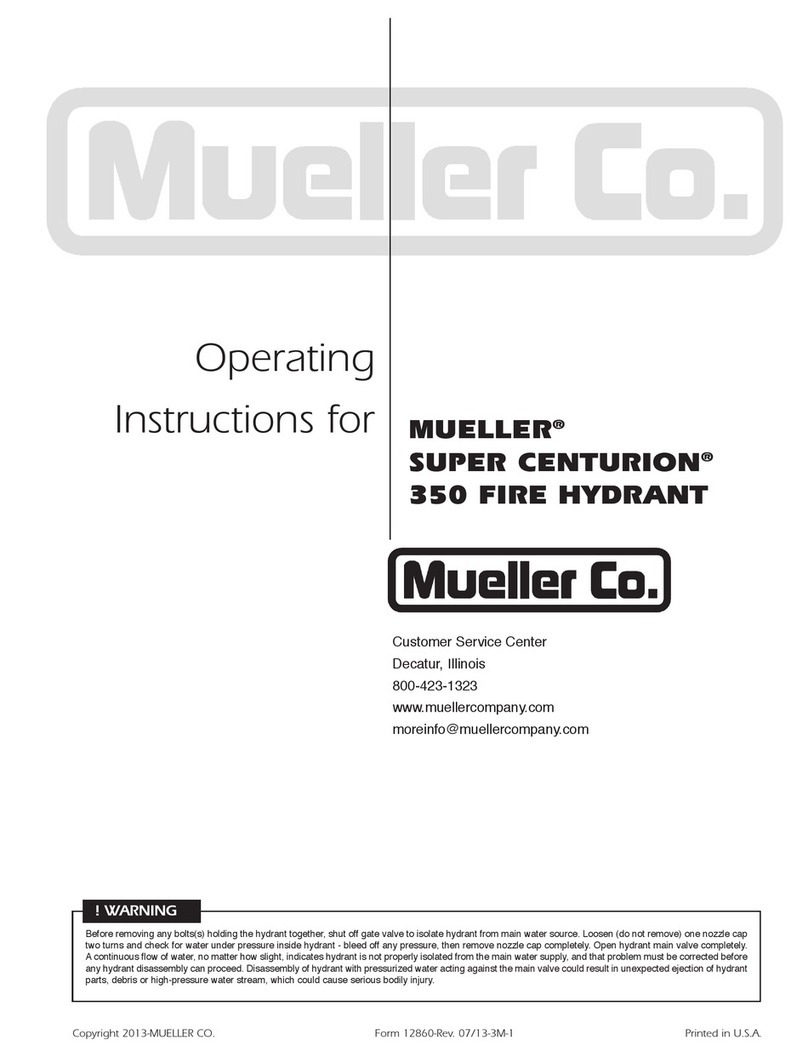
Mueller
Mueller Super Centurion 350 operating instructions

Amerex
Amerex 630 Installation, operating & servicing instructions

Tyco
Tyco TY-FRB Series quick start guide

Tyco
Tyco FSC 80 K-factor Flush Sprinkler quick start guide
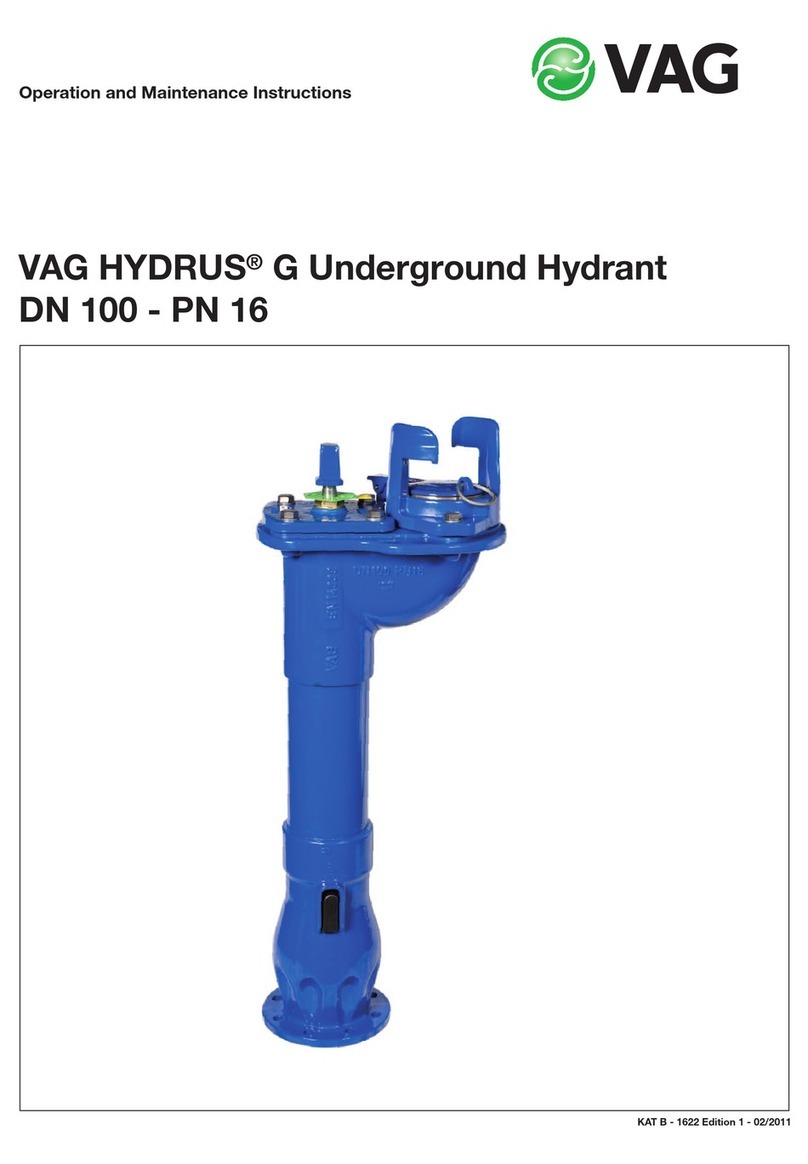
Vag
Vag HYDRUS G Operation & maintenance instructions
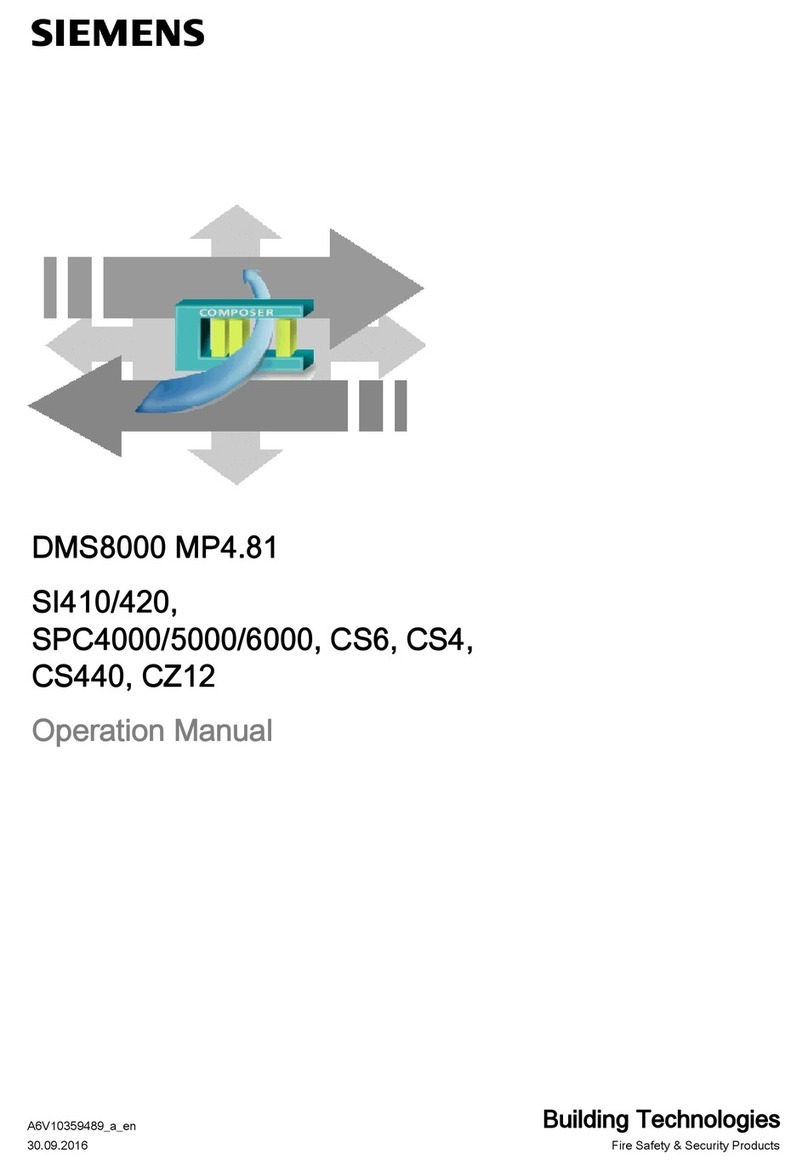
Siemens
Siemens DMS8000 Operation manual
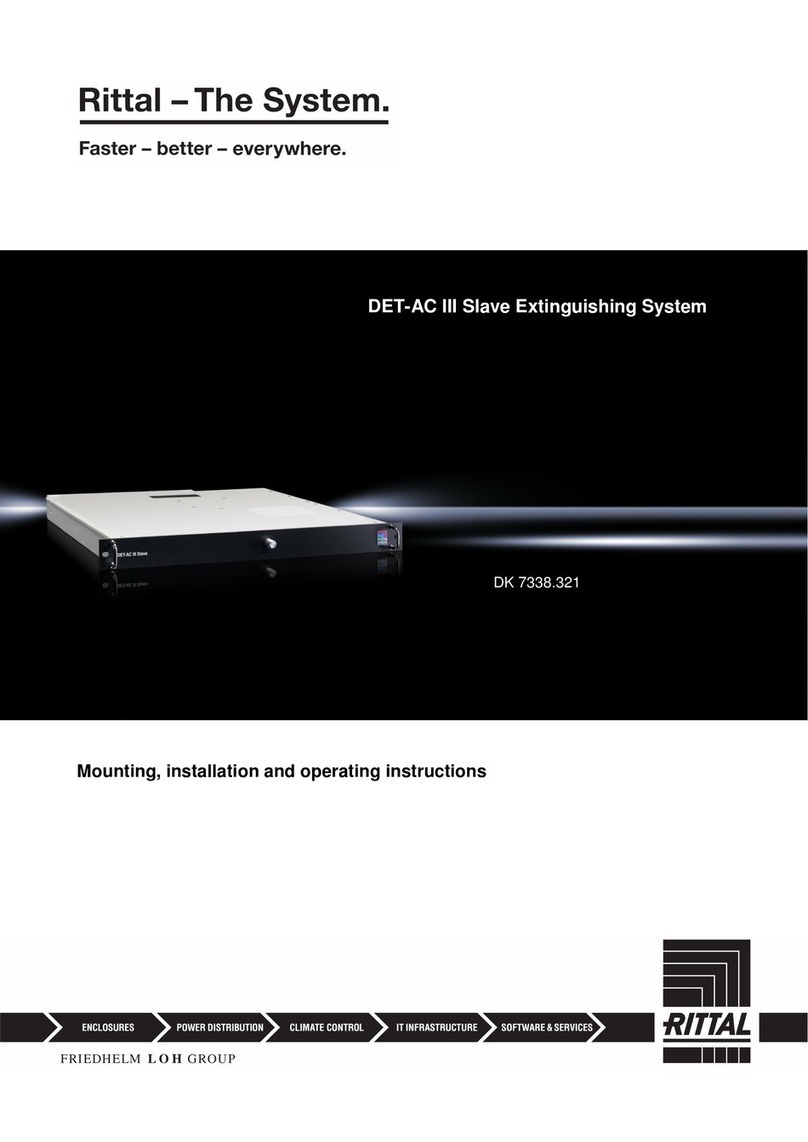
FRIEDHELM LOH
FRIEDHELM LOH RITTAL DET-AC III Slave Mounting, installation and operating instructions
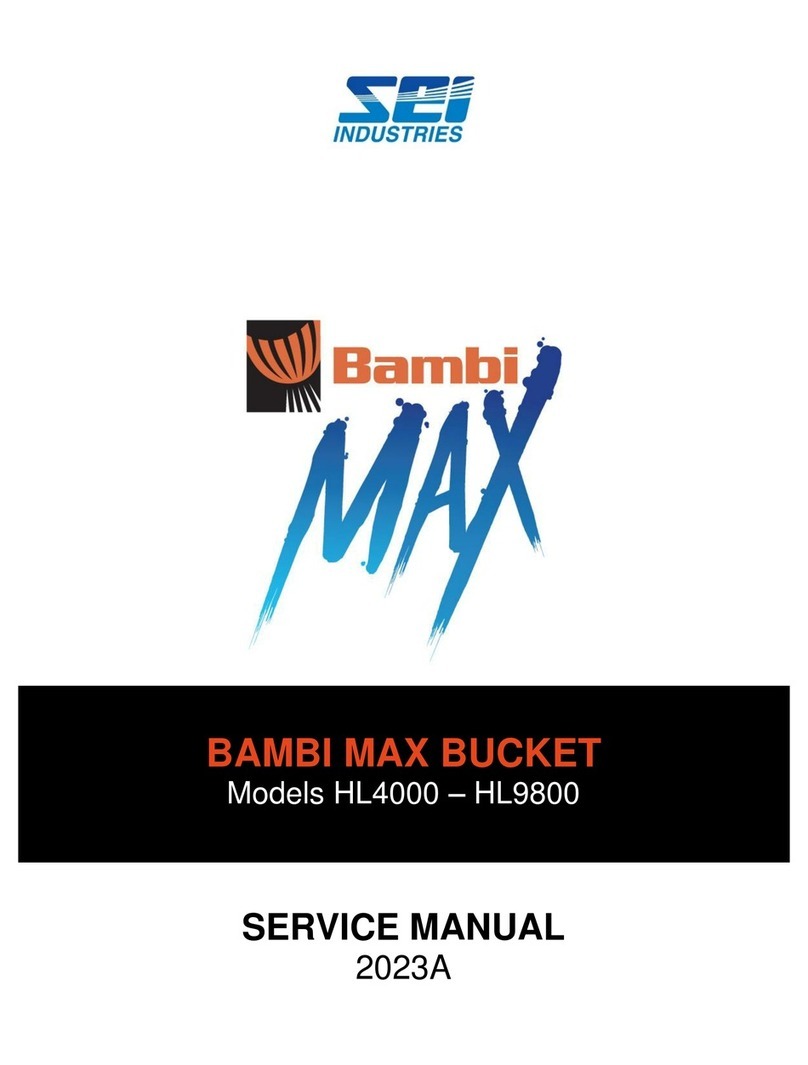
Bambi
Bambi MAX BBXHL4000 Service manual
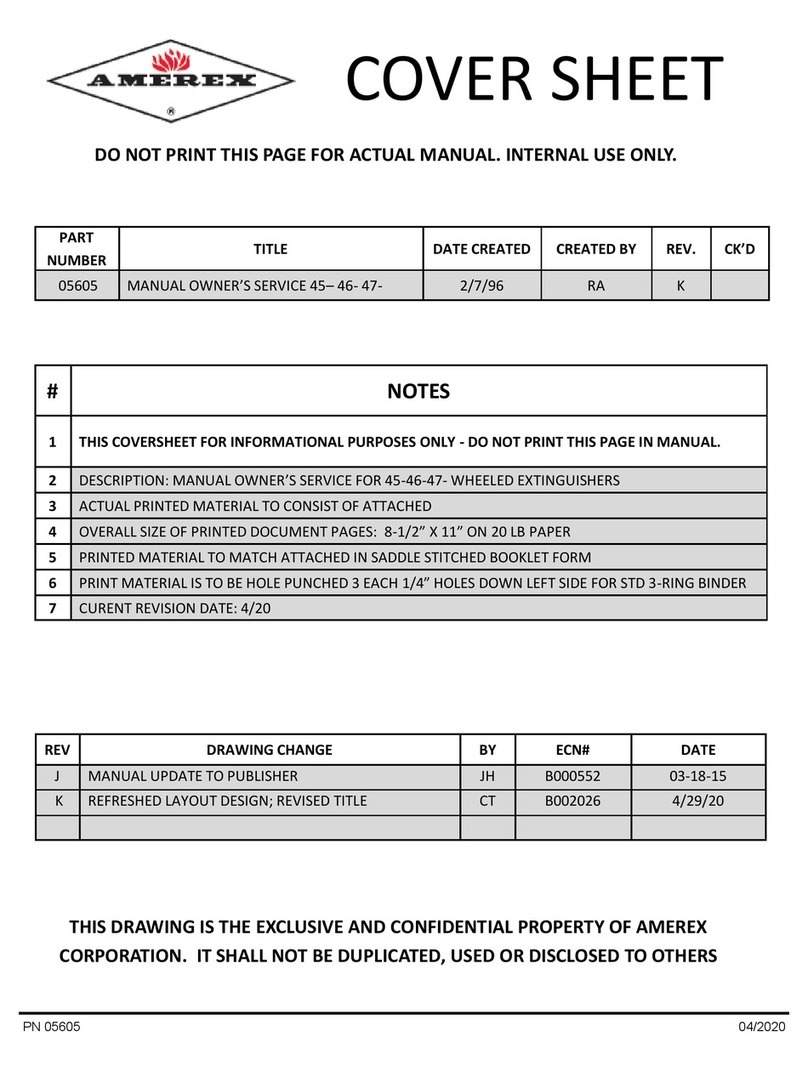
Amerex
Amerex 450 Installation, operating & servicing instructions

Bullard
Bullard Bullard FXE User's information guide
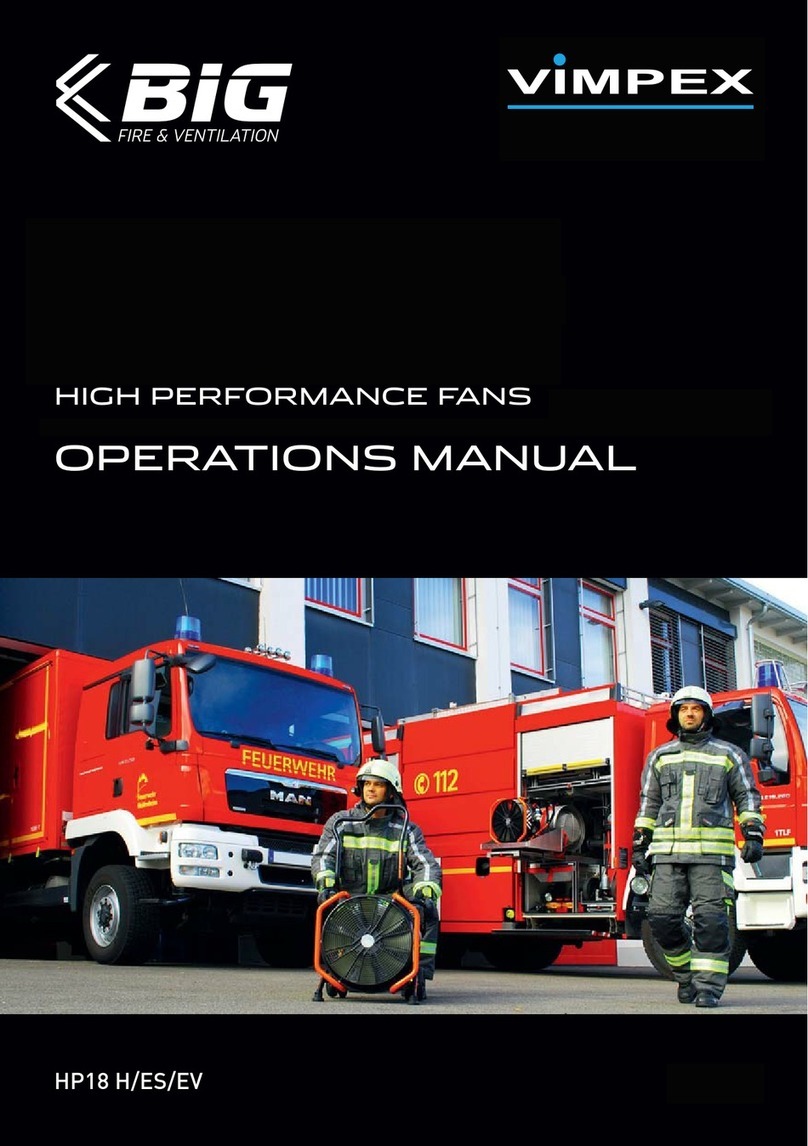
Vimpex
Vimpex BIG HP18-H200-B1 Operation manual
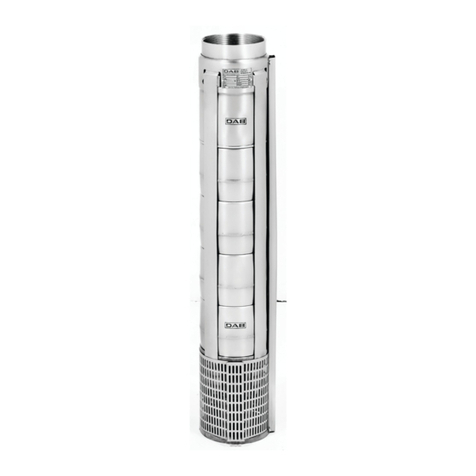
DAB
DAB SS6 Instruction for installation and maintenance