Fireye PPC6000 Series User manual

PPC6000
SERIES
FUEL AIR
RATIO
CONTROLLER
DESCRIPTION
The Fireye PPC6000 is a state of the art stand-alone parallel positioning system for all types of
liquid or gaseous fuel fired combustion systems. When combined with a Fireye flame safeguard
system such as the Fireye BurnerLogix control, the PPC6000 offers the most compact and
advanced parallel positioning system available. Four fuel profiles allow the PPC6000 to
accommodate a variety of applications such as two fuels, with and without, the optional variable
speed drive (VSD). With each profile having up to 24 points entered to assure a smooth “curve”,
the microprocessor interpolates points between entered values and precisely positions fuel and
air to within +- .1 degree. This eliminates hysteresis for improved efficiency. The PPC6000 is
capable of powering up to ten 24volt servomotors supplied from the integral transformer. All
servomotors and displays operate on a secure CANbus communications protocol and can be
“daisy chained” together for simplified wiring. Two independent PID control loops for
temperature or pressure control provide precise, accurate control of firing rate for unmatched
response to load changes. Four safety rated user definable digital inputs are standard and can
be configured for functions such as lead lag, night setback, thermal shock warm up, etc. Digital
inputs can also be configured as analog inputs via the optional programmable function blocks
using Fireye Abacus software. Built in lead lag sequencing for up to four boilers is included in
every PPC6000. More elaborate lead lag schemes may be possible using the programmable
function blocks.
Two variations of multifunction displays are available:
NXTSD104 10.4” Color Touchscreen display with Ethernet, Modbus TCPIP, 4
programmable relays and backup.
NX610 display provides automatic storage of operating parameters and profiles for
upload/download to the PPC6000. In addition, three line voltage fully programmable relays
are mounted inside the display.
PPC-6001
JANUARY 18, 2016

2
Other options include, two Variable speed drive (VSD) outputs via daughter board, Oxygen Trim
using Fireye’s proven heated zirconia oxide probe and optional interface, a wide variety of
communications platforms such as Modbus is also available.
An optional internal freely programmable logic section of the PPC6000 means that external
PLC’s and expensive stand-alone sequencing controls may no longer be needed. Easy to
program and protect, this new feature will make the PPC6000 suitable for many unique or
unusual applications. Functions such as lead lag, sequencing, feedwater control and draft
control are just some of the ways this feature can be used.
Optional ComFire software allows the user to view and control all aspects of the burner system,
provides real time trending and logging, upload and download of profiles and options. The user
can build custom screens or import actual photographs of the combustion equipment for
animation.
Summary of PPC6000 Features
State of the art surface mount technology
Smallest footprint available: 7.0” x 4.5” x 2.5”
Capable up to ten servomotors powered from the control
Two PID loops for precise process control
Simple four wire CANbus wiring reduces time and mistakes
Optional VSD card provides two VSD’s and one Analog output
Re-transmittal of most data as 420mA output (requires NXDBVSD
option)
VSD encoder feedback available
Standby lag boiler on water temp.
Built in lead/lag sequencing for up to four boilers
Fully programmable function block programming allows for custom
applications such as draft control or feedwater control
Two levels of displays: 12 Key Keypad with Backup, 10.4” Color
Touchscreen
Unparalleled worldwide support

3
Safety information
WARNING
When this equipment is fitted to an appliance due regard must also be given to the requirements of that
appliance.
Before attempting to install, commission or operate this equipment all relevant sections of this
document must be read and fully understood. If in doubt about any requirements consult Fireye.
Installation, commissioning or adjustment of this product MUST be carried out by suitably trained
engineers or personnel qualified by training and experience.
After installation or modifications to the installation all functions of the equipment MUST be checked
to ensure safe and reliable operation of the control.
The manufacturer of this equipment accepts no liability for any consequences resulting from inappropriate,
negligent or incorrect installation, commissioning or adjustment of operating parameters of the equipment.
Control panels must not be left uncovered while power is on. If it is essential to do so while rectifying faults
only personnel qualified by training and experience should be involved.
The time any covers are off must be kept to a minimum and warning notices must be posted.
Before attempting any work on this equipment or any equipment controlled by or connected to this equipment,
all related electrical supplies must be isolated.
Safety interlocks must not be removed or over-ridden. Any faults once detected must be corrected before
the control is operated.
CAUTION – SOME VERSIONS OF THIS EQUIPMENT CONTAIN
A LITHIUM BATTERY IN THE DISPLAY UNIT
NOTE
The manufacturer of this equipment has a policy of continual product improvement and reserves the right to
change the specification of the equipment and the contents of this manual without notice.
The equipment described in this manual is capable of causing property damage, severe injury, or
death. It is the responsibility of the owner or user to ensure that the equipment described herein is
installed, operated and commissioned in compliance with the requirements of all national and local
legislation, which may prevail.

4
Table of contents
This manual describes the installation, commissioning, operation and maintenance of the PPC6000 series fuel
air ratio controls. It may be used in conjunction with the following other manuals:
NEX-1502 - ComFire combustion analysis tool user manual
Please read the safety information at the front of this manual before proceeding.
1Technical specification 11
1.1General 11
1.2Servo-motor control – IMPORTANT: See Section 3.2 11
1.3Digital outputs (PPC6000) 12
1.4Alarm output (PPC6000) 12
1.5Digital inputs (PPC6000) 13
1.6Pressure/Temperature Input (PPC6000) 13
1.7Communications interface (PPC6000) 13
1.8Optional Oxygen Probe Interface Unit (NXO2INT) - optional 14
1.9Optional Ambient Air Temperature Unit (NXIATS) - optional 14
1.10Variable Speed Drive (VSD) Daughter Board (NXDBVSD) - optional 14
1.11Fireye NXC04, NXC12, NXC20, NXC20A, NXC40 Servo Motors 15
1.12Fireye NXO2INT Oxygen Probe Interface Unit (optional) 15
1.13Fireye NXIATS Ambient Air Temperature Sensor (optional) 16
1.14Approvals 16
1.15Parts List with Description 16
2Installation 18
2.1Mounting details for the PPC6000 control 19
2.2Mounting details for the display module 20
2.3Mounting details for optional Oxygen Probe Interface unit, NX02INT 21
2.4The oxygen trim option 22
2.4.1Oxygen Probe description 22
2.4.2Installation of oxygen probe 22
2.4.3Mounting the oxygen probe 23
2.4.4Mounting arrangements for Temperature and Steam pressure sensors 24
2.4.5Boiler temperature sensors 24
2.4.6Steam pressure sensors 25
2.5Option link selection (PPC6000) 26
2.5.1General (Access to jumper’s and fuse’s is gained by removing the back cover of the PPC6000)
26
2.5.2Line supply voltage (LK1 - 4) (PPC6000) 26
2.5.3SENS IN and SENS SUPP (boiler temp/pressure sensor) (PPC6000) 27
2.5.4REMOTE SETPOINT (PPC6000) 27
2.5.5RS485 serial communications termination resistor (PPC6000) 27
2.5.6RS485 serial communications termination resistor (daughter board) 27
IN 27
IN 27
IN 27
IN 27
2.6Wiring 29
2.6.1General 29

5
2.6.2Grounding cable screens 32
2.6.3GROUND (EARTH) connection 32
2.6.4Ground (earth) Connection (display unit) 33
2.6.5Terminal Designation 33
2.6.6LINE and NEUTRAL supply (PPC6000) PE1 & PE2 35
2.6.7Safety Shutdown output (PPC6000) 36
2.6.8Controlled Shutdown Relay Output (PPC6000) 36
2.6.9Alarm Relay output – RELAY 4 (on the PPC6000) 36
2.6.10Auxiliary Relay Outputs (display) 37
2.6.11Fuel Select /Profile Select Input/Purge and Ignition Prove Outputs (PPC6000) 37
2.6.12Low Voltage Digital Inputs (PPC6000) – relevant Engineer’s Keys EK1-EK4 (Sec. 6.6.2) 38
2.6.13Servo-motor and Display Connection (PPC6000) 38
2.6.14Display Connection with PPC6000 and BurnerLogix YB110 39
2.6.15Oxygen Probe Interface Connection (PPC6000) 40
2.6.16Pressure/temperature sensor input (PPC6000) 40
2.6.17Remote Setpoint (Analog Input 5) (PPC6000) 41
2.6.18RS485 interface (PPC6000) 41
2.6.19Variable Speed Drive Selection: 42
2.6.20PPC6000 Variable Speed Drive Daughter Board P/N NXDBVSD 43
2.6.21LIVE and NEUTRAL supply (optional Oxygen Probe Interface unit) 44
2.6.22Oxygen probe connection (optional Oxygen Probe Interface unit), NX02INT 44
2.6.23Inlet temperature sensor (optional) 46
2.7Final checks 47
3Servo-motor selection and calibration 48
3.1Servo-motor selection 48
3.1.1Motor requirements 48
3.2IMPORTANT: Servo-motor direction warning 49
3.3Locking the servo-motor to the valve shaft 50
3.4Feedback potentiometer 50
3.5Adjusting microswitch positions 51
3.6Servomotor Replacement 52
4Description of operation 53
4.1The Display / Keypad 53
4.2Start-up sequence 54
4.3Non-volatile lockout 59
4.4Modulation 59
4.4.1Normal/Remote mode. 59
4.4.2Local mode. (LOC 1, LOC 2) 59
5Commissioning the control 60
5.1General 60
5.2Commissioning data 61
5.2.1Option parameters 61
5.2.2Setpoints 61
5.3The Commissioning process 61
5.3.1Navigation 61
5.4Description of Touchscreen operation. 63
5.4.1The Touchscreen 63
5.4.2Touchscreen Power on. 63
5.4.3The Operation Mode line and Status messages 63
5.4.4Touchscreen Overview display. 65

6
5.4.5Touchscreen Lockout Reset (Alarm Mute) Function. 66
5.4.6Touchscreen LED Indication. 66
5.4.7Touchscreen Fuel/Profile Select. 67
5.4.8Touchscreen ‘Control’ screen. 68
5.4.9Touchscreen ‘Menu’ button. 68
5.4.10Touchscreen ‘Burner Settings’ button. 68
5.4.11Touchscreen ‘Fault/Event Log’ button. 70
5.4.12Touchscreen ‘Screen Configuration’ button. 70
5.4.13Cleaning the Touchscreen 71
5.4.14Touchscreen Commission mode. 72
5.5Using option set mode 74
5.5.1Option parameter list 74
Option 00.1 - Site passcode (0 - 999) DEFAULT VALUE is 154. LV3 74
Option 00.2 - Serial communications control address (0 - 15) LV3 74
Option 00.3 - Reset hours run (0 - 1) LV3 75
Option 00.4 – User program select (0 / 1) LV1 75
Option 00.6 – Reserved 75
Option 00.7 – Modbus device address (1 – 99) LV3 75
Option 00.8 – Modbus communications speed (0 – 3) LV3 76
Option 01.0 – Power Up Option (0 - 30) LV3 76
Option 01.1 – Keyboard Auto/Manual enable (0 - 1) LV3 [Engineer’s Key 33] 76
Option 01.2 – Mute/Reset Input enable (0 - 2) LV3 76
Option 02.x – Drive Name LV3 77
Option 03.x – Drive Serial Number LV3 78
Option 04.x – Drive Usage Information LV3 78
Option 05.x – Drive Options LV3 79
Options 06.1-06.4 – Profile Naming LV3 80
Options 07.x, 08.x– RESERVED 80
Option 09.0 - Inverter control accuracy (0 / 1) LV3 80
Option 09.1 - Inverter error tolerance (0 / 1) LV3 80
Option 09.2 - Inverter closed loop gain (15 – 125%) LV3 81
Option 09.3 - Inverter stop time (0 – 100 seconds) LV3 81
Option 09.4 - Inverter acceleration time (0–100 seconds) (60 seconds max. recommended) LV381
Option 09.6 – VSD2 Speed Encoder Scaler (255 - 999) LV3 82
Option 09.7 – Reserved 82
Option 09.8 – Reserved 82
Option 14.1 – Limit Relay (0 - 8) LV3 83
Option 14.2 – Oxygen and Flue Temperature Limit Relay (0 - 8) LV3 83
Option 15.0 - Modulation sensor input type (0 - 3) LV3 84
Option 15.1 – Modulation input decimal places (0 to 2) 84
Option 15.2 – Modulation input zero value (-999 to +999 / -99.9 to +99.9 / -9.99 to
+9.99) LV3 85
Option 15.3 – Modulation input span value (-999 to +999 / -99.9 to +99.9 / -9.99 to
+9.99) LV3 85
Option 15.4 – Setpoint display units (0 – 3) LV3 85
Option 15.5 - Boiler high safety limit (0 - 999 / 0.0 - 99.9 / 0.00 – 9.99) LV3 85
Option 15.6 – Modulation Time (0 – 120 seconds) LV3 85
Option 15.7 – Bumpless Transfer (0 or 1) LV3 86
Option 15.8 – Low before Off (0 or 1) LV3 86
Option 15.9 - reserved 86
Option 16.2 – Allow profile swap (0 to 16) LV3 87
Option 18.1 to 18.4 – Low Voltage Fail-safe Alarm / Lockout Inputs (0 – 460) LV3 91

7
Option 19.1 to 19.4 – Fail-safe Alarm / Lockout Display Messages LV3 93
Option 20.0 – Set-point Select input (0 - 35) LV3 94
Option 20.1 – Boiler Shutdown input (0 - 35). LV3 95
Option 20.2 – Low Fire Hold input (0 - 35). LV3 95
Option 20.3 – Oxygen Trim Disable input (0 - 35). LV3 95
Option 20.4 – Ignition Wait input (0 - 35). LV3 96
Option 20.5 – Purge Hold input (0 - 35). LV3 96
Option 20.6 – Purge Time Start input (0 - 35). LV3 96
Option 20.7 – Analog Input 5 function (0 - 2). LV3 96
Option 20.8 – Digital Input - Lead Boiler Select (0 – 35) LV3 97
Option 21.0 – Set-point 1 enable (0 - 1) LV1 97
Option 21.1 – Set-point 1 control value (0 - 999 / 00.0 - 99.9 / 0.00 - 9.99) LV1 97
Option 21.2 – Set-point 1 proportional band (0 - 999 / 00.0 - 99.9 / 0.00 - 9.99) LV197
Option 21.3 – Set-point 1 integral time (0 – 999 seconds) LV1 97
Option 21.4 – Set-point 1 derivative time (0 – 999 seconds) LV1 98
Option 21.5 - Setpoint 1 control limit type (0 - 2) LV3 98
Option 21.6 - Setpoint 1 low limit control value (Cut In) (0 - 999 / 00.0 - 99.9 / 0.00 - 9.99) LV1 98
Option 21.7 - Setpoint 1 high limit control value (Cut Out) (0 - 999 / 00.0 - 99.9 / 0.00 - 9.99) LV198
Option 21.8 – Remote Setpoint 1 zero (4ma) value (0 - 999 / 00.0 - 99.9 / 0.00 - 9.99) LV1 98
Option 21.9 – Remote Setpoint 1 span (20mA) value (0 - 999 / 00.0 - 99.9 / 0.00 - 9.99) LV1 98
Option 22.0 – PID (set-point) 2 enable (0 - 1) LV1 98
Option 22.1 – Set-point 2 control value (0 - 999 / 00.0 - 99.9 / 0.00 - 9.99) LV1 99
Option 22.2 – Set-point 2 proportional band (0 - 999 / 00.0 - 99.9 / 0.00 - 9.99) LV1 99
Option 22.3 – Set-point 2 integral term (0 – 999 seconds) LV1 99
Option 22.4 – Set-point 2 derivative term (0 - 100) LV1 99
Option 22.5 - Setpoint 2 control limit type (0 - 2) LV3 99
Option 22.6 - Setpoint 2 low limit control value (0 - 999 / 00.0 - 99.9 / 0.00 - 9.99) LV1 100
Option 22.7 - Setpoint 2 high limit control value (0 - 999 / 00.0 - 99.9 / 0.00 - 9.99) LV1 100
Option 22.8 – Maximum modulation rate 100
Option 22.9 – Reserved 100
Option 23.0 – Warming Enable (0 or 1) LV1 100
Option 23.1 – Warming Limit (0 - 999 / 00.0 - 99.9 / 0.00 - 9.99) LV1 100
Option 23.2 – Warming Time (0 to 999 minutes) LV1 100
Options 24.x – Sequencing 101
Option 24.0 Sequence Slaves (number of boilers) (0-3) LV1 102
Option 24.1 -24.3 Priority Number(s) LV1 102
Option 24.4 – Lead OFF Time LV1 103
Option 24.5 – Lead (master) Boiler Select Method LV1 103
Option 24.6 – lag (slave) On Rate (0-100%) LV1 104
Option 24.7 – lag (slave) On Delay (0-999 minutes) LV1 104
Option 24.8 – lag (slave) Off Rate (0-100%) LV3 104
Option 24.9 – lag (slave) Off Delay (0-999 minutes) LV3 104
Option 25.0 – Banking based on temperature / water temperature standby for steam boiler LV3104
Option 25.1 – Water temperature zero value LV3 105
Option 25.2 – Water temperature span value LV3 105
Option 25.3 – Water temperature cut-in LV1 105
Option 25.4 – Water temperature cut-out LV1 105
Option 25.5 – Temperature based warming limit LV1 105
Option 25.6 – Lag wait time LV1 105
Option 28.0 – Analog Input decimals (0-2) LV3 105
Option 28.1 – Analog Input 1 zero (0-999) LV3 105
Option 28.2 – Analog Input 1 span (0-999) LV3 105
Option 28.3 – Analog Input 2 decimals (0-2) LV3 105
Option 28.4 – Analog Input 2 zero (0-999) LV3 105
Option 28.5 – Analog Input 2 span (0-999) LV3 105

8
Option 28.6 – Analog Input 3 decimals (0-2) LV3 105
Option 28.7 – Analog Input 3 zero (0-999) LV3 106
Option 28.8 – Analog Input 3 span (0-999) LV3 106
Option 29.0 – 4-20mA Output 1 function if not VSD LV3 106
Option 29.1 – Output1 zero value (4mA output) LV3 106
Option 29.2 – Output1 span value (20mA output) LV3 106
Option 29.3 – 4-20mA Output 2 function if not VSD LV3 107
Option 29.4 – Output2 zero value (4mA output) LV3 107
Option 29.5 – Output2 span value (20mA output) LV3 107
Option 29.6 – 4-20mA Output 3 function if not VSD LV3 107
Option 29.7 – Output3 zero value (4mA output) LV3 107
Option 29.8 – Output3 span value (20mA output) LV3 107
Option 30.0 – Oxygen probe interface serial number LV3 109
Option 30.1 - Oxygen probe calibration offset value (0 – 999) LV3 109
Option 30.2 - Oxygen probe calibration gain value (0 – 999) LV3 110
Option 30.4 – Flue and inlet sensor temperature units (0 – 1) LV3 110
Option 30.5 - Oxygen input function (0/1) LV3 110
Option 30.6 - Oxygen probe calibrate enable (0 – 2) LV3 110
Option 30.7 - Boiler transport delay (5 – 60 seconds) LV3111
Option 30.8 - Reset oxygen trim profile (0/1) LV3 111
Option 30.9 – Automatic trim commissioning (0 / 1) LV3 111
Options 31.1 to 31.4 - Trim Type for profiles 1 to 4 (0 to 2) LV3 113
Option 32.0 - Trim limit default (0/1) LV3 114
Options 33.1 to 33.4 - Trim integral gain (Default 10%) LV3 114
Option 34.0 - Trim proportional gain (0/1) LV3 115
Options 34.1 to 34.4 - Trim proportional gain (0.0 – 99.9%) LV3 115
Option 34.5 - Calculating and entering the flow values manually LV3 115
Option 35.0 – Inlet temperature sensor serial number LV3 118
Options 35.5 to 35.8-Calorific values of fuels/profiles 1 to 4 respectively (0.0 – 99.9) LV3 118
Option 35.9 - Boiler radiated heat loss (0.0 – 9.9%) LV3 119
Option 36.0 - Flue temperature alarm select (0/1) LV3 119
Options 36.1 to 36.4 - Flue temperature low alarm values (0 – 999) LV3 119
Option 38.0 - Oxygen alarm select (0 – 2) LV3 120
Options 38.1 to 38.4 - Oxygen low alarm values at low fire (0.0 – 99.9%) LV3 120
Options 39.1 to 39.4 - Oxygen low alarm values at high fire (0.0 – 99.9%) LV3 120
Options 40.1 to 40.4 - Oxygen high alarm values at low fire (0.0 – 99.9%) LV3 120
Options 41.1 to 41.4 - Oxygen high alarm values at high fire (0.0 – 99.9%) LV3 120
Option 42.0 – Second Oxygen probe interface serial number LV3 121
Option 42.1 – Second Oxygen probe calibration offset value (0 – 999) LV3 121
Option 42.2 – Second Oxygen probe calibration gain value (0 – 999) LV3 121
Option 42.3 – Second Oxygen probe calibrate enable (0 – 2) LV3 122
Option 42.4 – Max oxygen variation (0 – 9.9 %) LV3 122
Option 42.5 – Max flue temp variation (0 to 999 ºC) LV3 123
Option 42.7 – Air pressure monitoring* – input number LV3 123
Option 42.8 – Air pressure monitoring* – Span LV3 123
Option 42.9 – Air pressure monitoring* – max error LV3 123
Option 43.0 – Water level / expansion unit** LV3 - Reserved 123
Option 43.1 – Water level / expansion unit** LV3 - Reserved 123
Option 44.0 - Set real time clock (0/1) LV1 123
Option 44.1 – Set Year (00 – 99) LV1 123
Option 44.2 – Set Month (1 – 12) LV1 123
Option 44.3 – Set Day of Month (1 – 31) LV1 123
Option 44.4 – Set Day of Week (1 - 7) LV1 124
Option 44.5 – Set Hours (0 - 23) LV1 124
Option 44.6 – Set Minutes (0 - 59) LV1 124
Option 44.7 – Set Seconds (0 - 59) LV1 124

9
Option 44.9 – Reset Fault Log (0 - 1) LV3 124
Option 45.0 - Erase / Restore enable (0 - 1) LV3 124
Option 45.1 - Erase command (0 - 5) LV3 125
Option 45.2 - Restore command (0 - 999) LV3 125
5.6Commission ratio mode 126
5.6.1Description 126
5.6.2Using commission ratio mode 126
5.6.3Leaving commission ratio mode 128
5.7Adjust ratio mode 128
5.7.1Description 128
5.7.2Entering adjust ratio mode 128
5.7.3Using adjust ratio mode 129
5.7.4Leaving adjust ratio mode 130
5.8Interrogating the software issue 130
6Faults and fault finding 131
6.1The fault display 131
6.2What to do when a fault occurs 131
6.3Non-volatile lockout 132
6.4Fault subsets 132
6.5Fault listing 132
6.6The engineer's key 139
6.6.1Fault history 140
6.6.2Engineer’s key parameter list 140
6.7Troubleshooting 150
6.7.1Display / General 150
6.7.2Startup 151
6.7.3Commissioning 151
6.7.4Modulation 152
6.7.5Inverters 153
6.8YB110/TSD104 Fault Messages 155
7Inverter (variable speed) drives 157
7.1System configuration 157
7.2Description of control method 158
7.3Setting up the inverter for use with the PPC6000 series 158
7.4Setting up the PPC6000 series for use with a inverter drive 159
8The oxygen trim option 160
8.1Oxygen Pro probe description 160
8.1.1Installation of oxygen probe 160
8.1.2Mounting the oxygen probe 160
9Appendix 163
9.1Calibrating and servicing the oxygen probe 163
9.1.1Probe calibration 163
9.1.2Oxygen Probe Filter Testing 164
9.1.3Removing the oxygen probe from the flue 164
9.1.4Filter replacement 165
9.1.5Probe mounted flue thermocouple replacement. 165
9.2Troubleshooting inverter problems 167
9.3PID Tutorial 168

10
9.4Combustion Profile Setup Guideline 169
9.5Fireye PPC6000 Efficiency Calculations 170
9.6Typical Wiring Diagrams 172
9.7Operator’s Guide 179
9.7.1Introduction 179
9.7.2General 179
9.7.3Password 179
9.7.4Adjusting Cut IN and Cut OUT 180
9.7.5Manual Modulation 181
9.7.6Resetting the Control 181
9.7.7Fault and Fault Finding 182
9.7.8Fault subsets 182
9.7.9Fault listing 183
9.7.10PID Tutorial 183
9.7.11The startup / shutdown stages are as follows: 184
9.7.12Non-volatile lockout 187
9.8Fireye Nexus Combustion Curve 188
10Function Block Programming Details 189
Introduction to Fireye’s Abacus Programming Software 189
1.1.Introduction 189
1.4.The schematic toolbar 193
1.5.Place Function blocks 194
1.6.Moving and editing the link lines 194
11Circuit board connections 196
11.1Inlet Air Temperature Sensor (Optional) 196
11.2PPC6000 Variable Speed Drive Daughter Board P/N NXDBVSD 197
11.3Oxygen probe connection (optional Oxygen Probe Interface unit) 198
11.4PPC6000 199

11
1 Technical specification
1.1 General
Supply voltage
Power consumption
Supply frequency
Ambient temperature range
Control unit protection category
Unit dimensions
Weight
120/230Vac +10% - 15%
Approx. 60VA
50/60 Hz 5%
0 to 60C (32 to 140F)
IP20. The control must be situated in a clean environment
according to EN6730-1.
Indoor: Control must be mounted in an NEMA1 (IP40) enclosure
Outdoor: Control must be mounted in an NEMA3 (IP54) enclosure
Control unit 176 x 115 x 92mm (6.93 x 4.53 x 3.62 in) deep
Display 132 x132 x 36mm (5.20 x 5.20 x 1.42 in) deep
Control unit 1.55kg (3.42 lbs)
Display 0.90Kg (1.98 lbs)
Type of display
2 lines x 20 characters, vacuum fluorescent display with membrane
keypad.
1.2 Servo-motor control – IMPORTANT: See Section 3.2
Type
Maximum (total) number of servo-motors
Maximum number of fuel profiles
Max. number of setpoints per profile
Positioning accuracy
Response time to positioning error
Number of fuel motors
Number of air (non fuel) motors
CANbus
10 (see section 3 regarding servo-motors)
4
24 including close, purge and ignition
+/-0.1
15s for 1.0, 1s for 5.0
Not Limited by profile (e.g. 2 or 3 fuel motors). All
non-monotonic.
Not Limited by profile (e.g. 2 or 3 fuel motors). All
non-monotonic.
NOTE: Number of servomotors is limited in all
profiles by VA rating. See Section 3.1

12
Interface to PPC6000
Speed
Microswitches
Torque
CANbus
30 seconds for 90 degrees.
Open & close positions
Driving Holding
NXC04 4Nm/ 3 ft/lb 2Nm
NXC12 12Nm/ 9 ft/lb 18Nm
NXC20, NXC20A 20Nm/ 14.7 ft/lb 18Nm
NXC40 40Nm/ 29 ft/lb 20Nm
Voltage:
VA rating / Temperature
Protection Category
Typical accuracy
Accuracy (as specified by EN12067)
24-30Vac supplied from control only
NXC04 – 3VA NXC04 = 0°C – 60°C
NXC12 = 5VA NXC12 = 0°C – 60°C
NXC20 = 10VA NXC20 = 0°C – 60°C
NXC20A = 10VA NXC20A = -20°C – 60°C
NXC40 = 18VA NXC40 = -20°C – 60°C
NXC04 = IP40, NEMA 1
NXC12, NXC20, NXC20A = IP54, NEMA 3S
NXC40 = IP65, NEMA 4
+/-0.1
+/-0.5
1.3 Digital outputs (PPC6000)
Controlled Shutdown, Safety Shutdown
Type
Minimum current
Maximum current (per output)
Maximum voltage
On-off relay, de-energize for off.
200mA rms
8A rms
250Vac rms
1.4 Alarm output (PPC6000)
Alarm
Type
Minimum current
Maximum current (per output)
Maximum voltage
On-off relay, de-energize for off.
200mA rms
4A rms
250Vac rms

13
1.5 Digital inputs (PPC6000)
Low Voltage digital inputs 1 to 4, HIGH
input, AUTO input.
Digital, Switching 0V to 5V pulsed. Feed must be taken from
the correct terminal as indicted in this manual. Inputs 1-4
configurable for 4-20Ma. Via function block programming.
Less than 25mA
10V absolute maximum
Profile Select High voltage inputs
Digital, 0V for off, 90-264Vac for on.
1.6 Pressure/Temperature Input (PPC6000)
0-5V
Maximum current
Maximum voltage
Input accuracy (typical)
Input accuracy (as specified by EN12067)
Less than 2mA
0 to 5.0 volts maximum.
0.1%
0.3%
4-20mA
Maximum current
Burden (load) resistor
Input accuracy (typical)
Input accuracy (as specified by EN12067)
2 wire loop or ext. powered
0 to 25mA maximum
220 Ohm nominal
1.0%
1.1%
1.7 Communications interface (PPC6000)
2-wire RS485 plus ground, with termination resistor selected using a link. See Section 2.5.5.
An isolated 2-wire RS485 interface is available as an option. See Section 2.5.6.
See MOD-6101 (FIREYE serial communications protocol manual) for details.

14
1.8 Optional Oxygen Probe Interface Unit (NXO2INT) - optional
Supply voltage
Power consumption
Supply frequency
Ambient temperature range
Protection category
Unit dimensions
Weight
Interface to PPC6000 series.
Interface to oxygen probe.
115/230Vac 15%
Approximately 60VA
50/60Hz 5%
0 to 60C (32 to 140F)
NEMA4 (IP65).
160 x 98 x 63mm (6.30 x 3.86 x 2.48“) deep
1.34Kg (2.95 lbs)
FIREYE specific CANbus.
FIREYE specific or 4-20mA
1.9 Optional Ambient Air Temperature Unit (NXIATS) - optional
Type
Ambient temperature range
Protection category
Unit dimensions
Weight
Interface to PPC6000 series.
CANbus
0 to 60C (32 to 140F)
NEMA3 (IP54)
57 x 63 x 35 mm (2.25 x 2.5 x 1.37 inches)
0.15 kg (5.4 oz.)
FIREYE specific CANbus.
1.10 Variable Speed Drive (VSD) Daughter Board (NXDBVSD) - optional
Ambient temperature range
Protection category
Analog inputs (4 – 20mA)
Input impedance
Analog outputs (4 – 20mA)
Maximum loop resistance
Isolation voltage
RS485 communications.
0 to 60C (32 to 140F)
Not applicable (fits inside PPC6000 unit).
3 max (non-isolated)
120ohms
3 max (isolated)
250 ohms
50v
Modbus RTU

15
1.11 Fireye NXC04, NXC12, NXC20, NXC20A, NXC40 Servo Motors
Interface to PPC6000
Speed
Microswitches
Torque
CANbus
30 seconds for 90 degrees.
Open & close positions
Driving Holding
NXC04 4Nm/ 3 ft/lb 2Nm
NXC12 12Nm/ 9 ft/lb 18Nm
NXC20 20Nm/ 14.7 ft/lb 18Nm
NXC40 40Nm/ 29 ft/lb 20Nm
Voltage:
VA rating
Protection Category
Typical accuracy
Accuracy (as specified by EN12067)
24-30Vac supplied from control only
NXC04 = 3VA
NXC12 = 5VA
NXC20, NXC20A = 10VA
NXC40 = 18VA
NXC04 = IP40, NEMA 1
NXC12, NXC20, NXC20A = IP54, NEMA 3S
NXC40 = IP65, NEMA 4
+/-0.1
+/-0.5
1.12 Fireye NXO2INT Oxygen Probe Interface Unit (optional)
Supply voltage
Power consumption
Supply frequency
Ambient temperature range
Protection category
Unit dimensions
Weight
Interface to PPC6000 / NX6100
Interface to oxygen probe.
115/230Vac 15%
Approximately 60VA
50/60Hz 5%
0 to 60C (32 to 140F)
NEMA4 (IP65).
160 x 98 x 63mm (6.30 x 3.86 x 2.48“) deep
1.34Kg (2.95 lbs)
FIREYE specific CANbus.
FIREYE specific or 4-20mA

16
1.13 Fireye NXIATS Ambient Air Temperature Sensor (optional)
Type
Ambient temperature range
Protection category
Unit dimensions
Weight
Interface to PPC6000 / NX6100
CANbus
-29C to 60C (-20F to 140F)
NOTE: Accuracy below 0C (32F) may
vary slightly. Agency testing conducted to
0C only.
NEMA3 (IP54)
FIREYE specific CANbus.
1.14 Approvals
Tested in accordance with the Gas Appliance Directive (GAD 90/396 EEC), encompassing the following
standards:
SIL Level 3 – Kiwa Gastec Report #123836
ANSI/UL 462, Heat Reclaimers for Gas, Oil, or Solid Fuel-Fired Appliances
ANSI/UL 1995, Heating and Cooling Equipment
ANSI/UL 1998, Software in Programmable Components
CAN/CSA-C22.2 No. 236, Heating and Cooling Equipment
FM
ENV1954, Internal and external behavior of safety related electronic parts
EN60730-1, Automatic electrical controls for household and similar use
prEN12067, Gas/air ratio controls for gas burners as gas burning appliances
SIL level 3 per Kiwa report #123836
1.15 Parts List with Description
PART NO* DESCRIPTION
PPC6000 FUEL AIR RATIO CONTROLLER
PPC6000 Stand-alone parallel positioning controller, with up to ten (10) selectable function
CANbus servo-motor outputs. Includes user configurable function blocks for
custom applications. Display ordered separately.
DISPLAY MODULES FOR PPC6000
NX610 CANbus display for PPC6000 with upload/download of PPC6000 data and three
programmable relays
NXTSD104** 10.4” Touchscreen Display with upload/download, full commissioning, data log,
internet connection, four programmable relays, 10 line voltage Digital Inputs.
SERVO-MOTORS FOR PPC6000
NXC04 4 wire CANbus Servo-motor, 3 ft lbs. torque, 4 Nm, 50/60 Hz, 24 VAC.

17
PART NO* DESCRIPTION
NXC12 4 wire CANbus Servo-motor, 9 ft lbs. torque, 12 Nm, 50/60 Hz, 24 VAC.
NXC20, NXC20A 4 wire CANbus Servo-motor, 14.75 ft lbs. torque, 20 Nm, 50/60 Hz, 24 VAC.
NXC40 4 wire CANbus Servo-motor, 29.5 ft lbs. torque, 40 Nm, 50/60 Hz, 24 VAC.
EXPANSION INTERFACE MODULES FOR PPC6000
NXDBMB Modbus RTU communications card
NXDBVSD
VSD interface daughter board with two VSD channels, one analog output, two
counter inputs, two programmable relays, isolated RS485, Modbus RTU
communications
NXO2INT CANbus O2 interface module with Fireye and generic (4-20mA) probe inputs.
O2 PROBES FOR PPC6000
NXO2PK4 O2 probe assembly (for flues 300mm to 1000mm). Includes NXIATS CANbus
ambient temperature sensor, flange kit.
NXO2PK6 O2 probe assembly (for flues 600mm to 2000mm). Includes NXIATS CANbus
ambient temperature sensor, flange kit.
NXO2PK8 O2 probe assembly (for flues 1200mm to 4000mm). Includes NXIATS CANbus
ambient temperature sensor, flange kit.
NXIATS PPC6000 CANbus Inlet (ambient) Air Temperature Sensor Sensor -29C to
60C (-20F to 140F)
SENSORS FOR PPC6000
PXMS-15 Steam Pressure Sensor: 0 - 15 PSI, 0 - 1 bar, 4-20mA output, 1/2" NPT, non
self-check (for use with PPC6000).
PXMS-200 Steam Pressure Sensor: 0 - 200 PSI, 0 - 14 bar, 4-20mA output, 1/2" NPT, non
self-check (for use with PPC6000).
PXMS-300 Steam Pressure Sensor: 0 - 300 PSI, 0 - 21 bar, 4-20mA output, 1/2" NPT, non
self-check (for use with PPC6000).
BLPS-15 Steam Pressure Sensor: 0 - 15 PSI, 0 - 1 bar, 4-20mA output, 1/2" NPT, non
self-check (for use with PPC5000 / PPC6000 / NX3100 / NX4100 / NX6100).
BLPS-30 Steam Pressure Sensor: 0 - 30 PSI, 0 - 1 bar, 4-20mA output, 1/2" NPT, non
self-check (for use with PPC5000 / PPC6000 / NX3100 / NX4100 / NX6100).
BLPS-200 Steam Pressure Sensor: 0 - 200 PSI, 0 - 14 bar, 4-20mA output, 1/2" NPT, non
self-check (for use with PPC5000 / PPC6000 / NX3100 / NX4100 / NX6100).
BLPS-300 Steam Pressure Sensor: 0 - 300 PSI, 0 - 21 bar, 4-20mA output, 1/2" NPT, non
self-check (for use with PPC5000 / PPC6000 / NX3100 / NX4100 / NX6100).
TS350 (-2), (-4), (-8)
Temperature Sensor, Range 32oF-350oF (0-176oC), 4-20mA linear
output, includes 1/2 - 14 NPT well. See bulletin BLZPTS-1 for
complete description.
TS752 (-2), (-4), (-8)
Temperature Sensor, Range 32oF-752oF (0-400oC), 4-20mA linear
output, includes 1/2 - 14 NPT well. See bulletin BLZPTS-1 for
complete description.
SOFTWARE
NXAM ComFire communications software on CD for Nexus and PPC controls.
COMMUNICATION INTERFACE GATEWAY
NXDBVSD
VSD interface daughter board with two VSD channels, one analog output, two
counter inputs, two programmable relays, isolated RS485 – Modbus RTU
communications
NXMBIV2 Modbus RTU Communications daughter board.
* FOR ADDITIONAL PARTS SEE FIREYE PRICE BOOK CG-14
** SOME FEATURES INCLUDED ON NXTSD MANUFACTURED AFTER MAY 2011.

18
2 Installation
This section contains basic installation information concerning choice of control and servomotor environment,
wiring specification and connection details.
WHEN INSTALLING THIS PRODUCT:
Read these instructions carefully and ensure you fully understand the product requirements. Failure to
follow them could damage the product or cause a hazardous condition.
Check the ratings given in these instructions to ensure the product is suitable for your application.
After installation is complete, check the product operation is as described in these instructions
CAUTION
Disconnect the power supply before beginning installation to prevent electrical
shock, equipment and/or control damage. More than one power supply
disconnect may be involved.
Wiring must comply with all applicable codes, ordinances and regulations.
Loads connected to the PPC6000 series must not exceed those listed in the
specifications as given in this manual.
All external components connected to the control must be approved for the
specific purpose for which they are used.
WARNING
EXPLOSION OR FIRE HAZARD
CAN CAUSE PROPERTY DAMAGE,
SEVERE INJURY OR DEATH
To prevent possible hazardous burner operation, verification of safety
requirements must be performed each time a control is installed on a burner, or
the installation modified in any way.
This manual may cover more than one model in the PPC6000 controls. Check for
Additional Information at the end of this chapter.
This control must not be directly connected to any part of a Safety Extra Low
Voltage (SELV) circuit.

19
2.1 Mounting details for the PPC6000 control
A Template for mounting is provided at the end of this manual for convenience. See Section 8.
There are two versions of the control, one that is intended to be mounted inside of a burner control cabinet, the
other which has provision for conduit storage of field wiring etc. that can be mounted without the need for a
burner control cabinet. If the version which is designed to be fitted inside of a burner control cabinet is being
used the cabinet should have a minimum protection level of NEMA1 (IP40) for indoor use or NEMA3 (IP54) for
outdoor use.
The control can be mounted in any attitude; clearances of a least 2.36-inch (60mm) should be left around the
unit to allow sufficient space for wiring and to ensure reliable operation.
The ambient operating temperature range of the equipment is 0 to 60°C (32 to 140°F). Refer to section 7 for
more details.
0.75”
(19mm)
3.15”
(80mm)
6.26” (159mm)
6.93” (176mm)
4.65”
(118mm)
Terminal Block PA
Terminal Block PB
Terminal Block PE
Screen
Termination
Clamps

20
2.2 Mounting details for the display module
A Template for mounting is provided at the end of this manual for convenience. See Section 8.
NOTE: The four (4) M4 clearance holes are the mounting holes for the display. After removing the
back cover, carefully remove the four brass hex standoff’s to secure the display to the panel.
The display should be mounted on the front of the burner cabinet, or similar accessible location.
It extends for 31mm (1.22 inches) behind the panel, and 4mm (0.16 inches) in front of the panel.
The maximum allowable panel thickness is 7mm (0.275 inches).
8mm
The display is held in using the four brass standoffs. The panel is cut out inside the four mounting holes only.
Remove the four brass standoffs, insert the screw studs through the mounting holes, then re-install the brass
standoffs. Do not over tighten the standoffs.
A Template for mounting is provided at the end of this manual for convenience. See Section 8.
REMOVE AND REUSE
For Mounting
8mm
8mm
Other manuals for PPC6000 Series
2
Table of contents
Other Fireye Controllers manuals
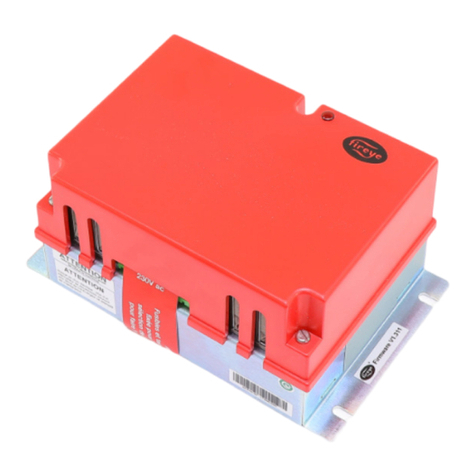
Fireye
Fireye NEXUS NX6100 series User manual
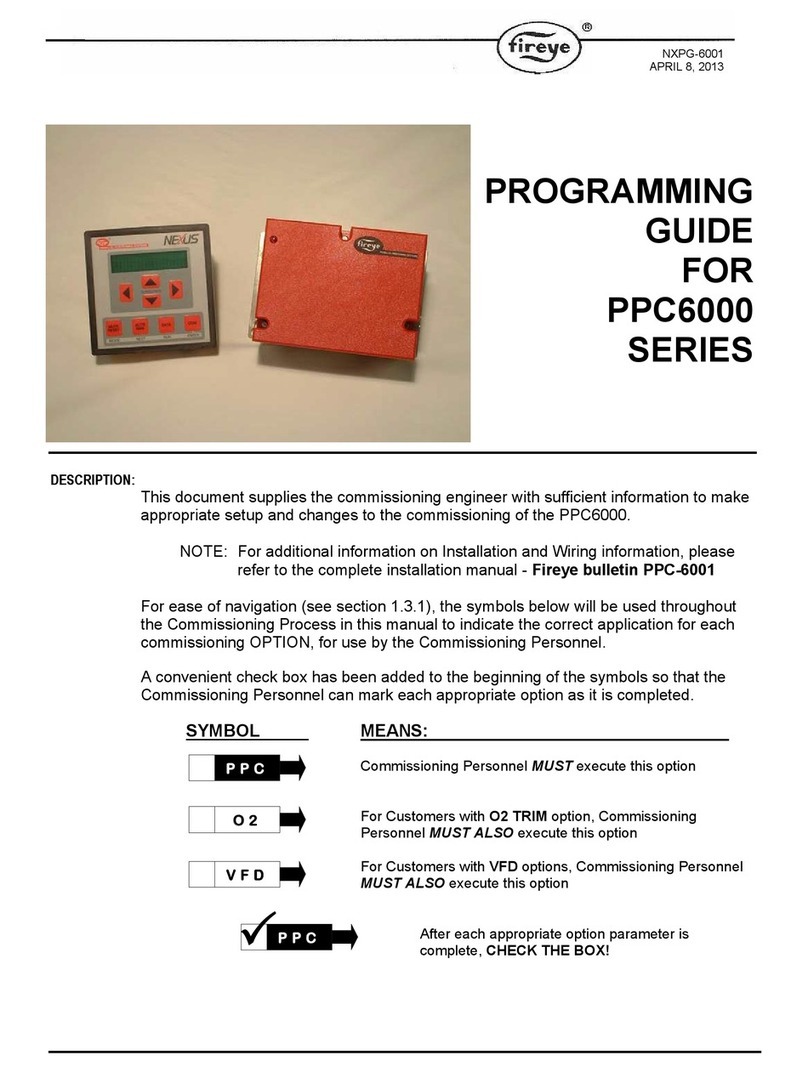
Fireye
Fireye PPC6000 Series Operating instructions
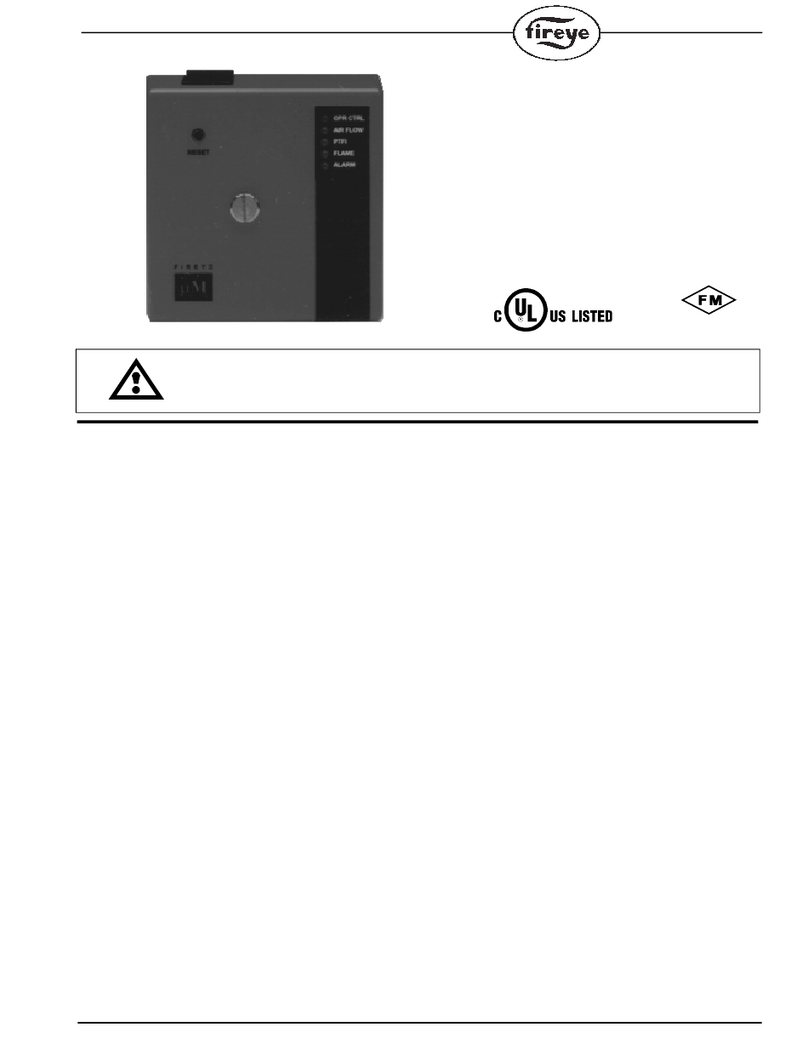
Fireye
Fireye MicroM Series User manual
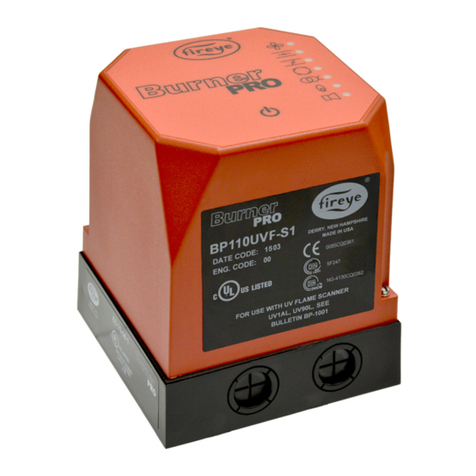
Fireye
Fireye BurnerPRO BP110 User manual
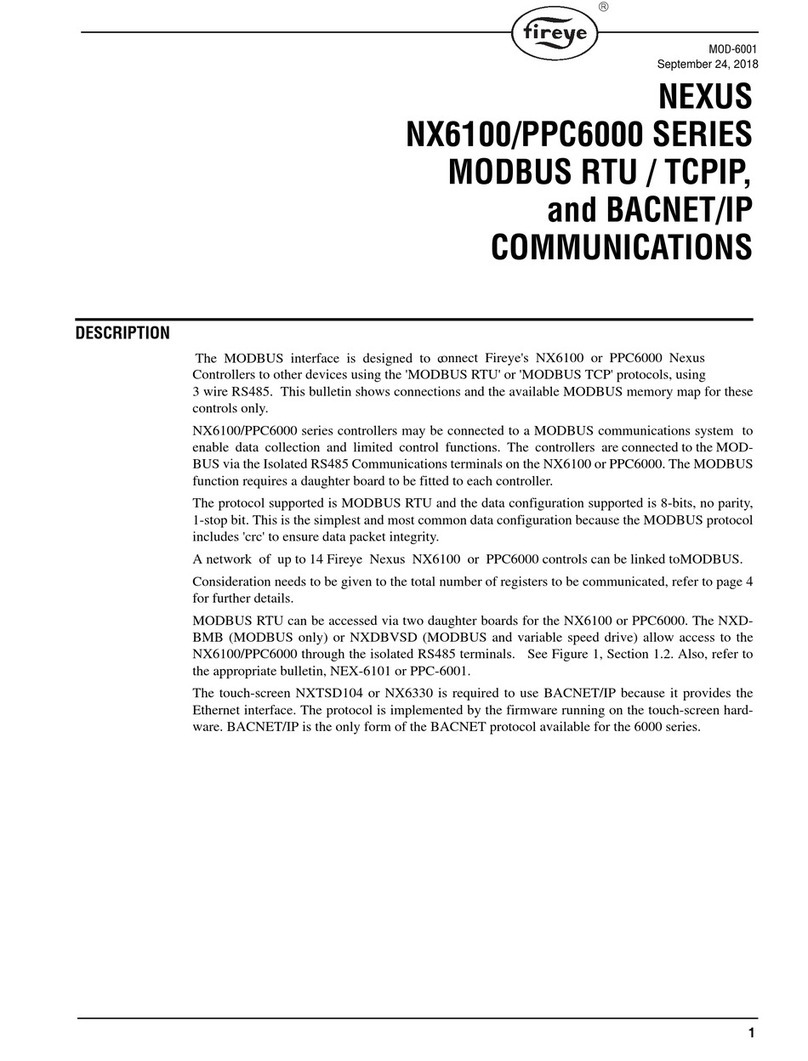
Fireye
Fireye NEXUS NX6100 series User manual
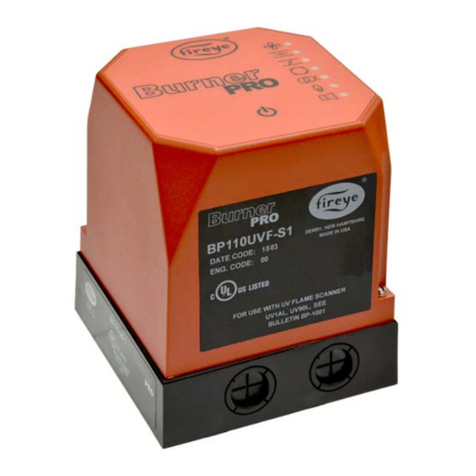
Fireye
Fireye BurnerPRO BP110 User manual
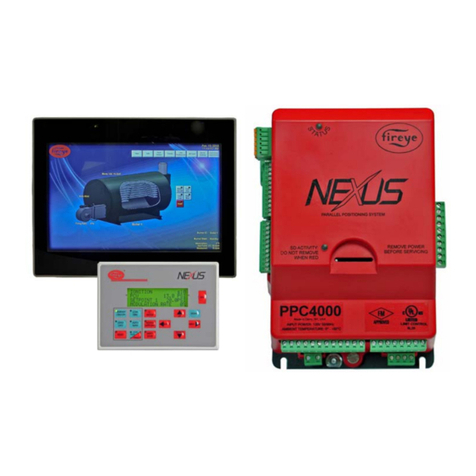
Fireye
Fireye PPC4000 SERIES User manual

Fireye
Fireye SB Series User manual
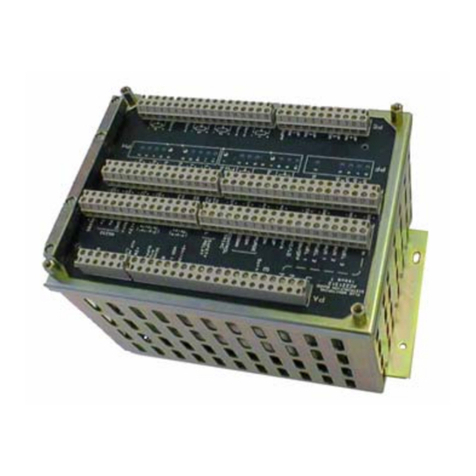
Fireye
Fireye PPC5000 User manual
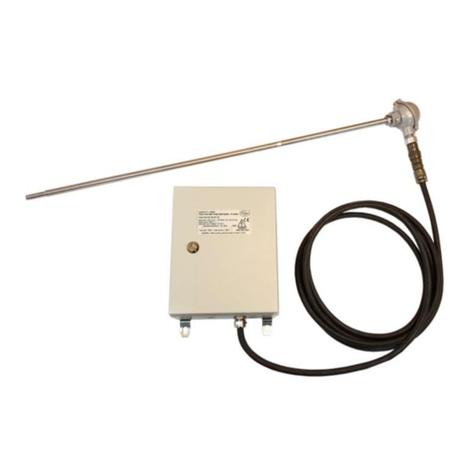
Fireye
Fireye SureFire II User manual