FLIR Alpha Nir User manual

INDIGO OPERATIONS
A
Al
lp
ph
ha
a
N
NI
IR
R
™
™
D
Di
ig
gi
it
ta
al
l
I
Im
ma
ag
ge
e
A
Ac
cq
qu
ui
is
si
it
ti
io
on
n
S
Sy
ys
st
te
em
m
User’s Guide
Version 150
412-0007-10

Alpha NIR User’s Guide 412-0007-10 Ver 150
INDIGO OPERATIONS
If You Need Help – Technical Support
If you need help at any time with the installation or use of the Alpha NIR camera or
the IRvista software, please call Technical Support at Indigo Systems Corp. in
Goleta, CA.
805-964-9797
Disclaimer
In no event shall Indigo Systems Corporation or their representatives be liable for
any consequential damages whatsoever (including, without limitation, damages for
loss of business profits, business interruption, loss of business information, or other
loss), arising out of the use of or inability to use the Alpha NIR camera or IRvista
software even if Indigo Systems Corporation has been advised of the possibility for
such damages.
Copyright
Copyright ©2002 Indigo Systems Corp. All rights reserved. No part of this
document may be reproduced, stored in a retrieval system, or transmitted, in any
form or by any means, electronic, mechanical, photocopying, recording, or
otherwise, without prior written consent of Indigo Systems Corporation.
i

Alpha NIR User’s Guide 412-0007-10 Ver 150
INDIGO OPERATIONS
Table of Contents
1INTRODUCTION 4
1.1 IRVISTA INSTALLATION INSTRUCTIONS ............................................................................5
1.2 INSTALLING ALPHA NIR HARDWARE................................................................................8
1.3 ALPHA NIR SYSTEM HARDWARE SETUP.........................................................................10
2ALPHA NIR EXTERNAL SYNC OPERATION 12
2.1 PROCEDURE FOR ACTIVATING EXTERNAL SYNC WITH IRVISTA...................................12
3ALPHA™ NIR CALIBRATION LIGHT SOURCE NUC PROCEDURE 16
3.1 RECOMMENDED EQUIPMENT & SOFTWARE.....................................................16
3.2 PROCEDURE ...................................................................................................................16
3.3 SHORT INTEGRATION TIMES ............................................................................................20
3.4 HIGH GAIN MODE..............................................................................................................20
4APPLICATION NOTE ON TIME STAMPS IN IRVISTA 2.51 21
ii

Alpha NIR User’s Guide 412-0007-10 Ver 150
INDIGO OPERATIONS
Cautions and Warnings:
• The camera is not sealed, so avoid dust and moisture exposure, and replace lens
cap when not in use.
• Do not exceed 7 volts DC input power, or reverse the polarity of input power.
• Do not apply DC input power to both the DC input and the Auxiliary I/O
connector simultaneously.
• This is a precision optical instrument, and should be protected from shock and
vibration. Keep the camera stored in the manufacturer’s shipping container.
• This camera contains static-sensitive electronics and should be handled
appropriately.
• Do not open the camera body, as doing so will void the warranty.
• Do not insert any objects inside the camera housing, as the window AR coating
can be damaged.
• If you have questions that are not covered in this manual, or need service, contact
Customer Support at 805-964-9797 for additional information (prior to returning
cameras).
3

Alpha NIR User’s Guide 412-0007-10 Ver 150
INDIGO OPERATIONS
1 Introduction
• Alpha NIR is a digital infrared imaging sensor based on indium gallium arsenide
(InGaAs) photodetectors in a 320 by 256 pixel focal-plane staring array. The
Alpha NIR focal plane contains the Indigo Systems ISC9809 Readout Integrated
Circuit (ROIC) that is hybridized to the detector array using indium bump bond
technology. InGaAs material is sensitive in the 900-1680 nm waveband, a region
of the spectrum that encompasses many near-infrared laser wavelengths,
including the wavelengths used for fiber optics communication. Indigo also
offers a special version of the Alpha NIR with a VisGaAs sensor. The VisGaAs
material is sensitive from 400 to 1700 nm. In all other respects, the VisGaAs
cameras are identical to the standard InGaAs cameras. Alpha NIR produces 12-
bit image data at a 30 Hz frame rate, and accepts standard C-mount lenses for
imaging applications.
• We have found that conventional video camera optics designed for visible-light
imaging work fairly well with the Alpha NIR system. There are also several
vendors of NIR lenses specifically designed to work in the InGaAs and VisGaAs
spectral ranges, although we do not stock their lenses at this time. However, laser
beam profiling applications often require direct illumination of the sensor. Unlike
lead-oxysulfide vidicon cameras, InGaAs sensors are highly resistant to damage
from intense laser beams and do not suffer from image retention, making
microsecond-level exposure times achievable. The ability to control exposure
times over six orders of magnitude gives an effective dynamic range span of 20
bits in addition to the 12-bit instantaneous dynamic range of the digitizer for a
total of 32 bits. In addition, the gain state of the sensor can be changed from low
to high. This changes the responsivity of the camera by a factor of 21, further
increasing the dynamic range capability of the camera by ~4 bits, for a total of 36
bits! Note: some cameras for the export market have high-gain mode disabled
per instructions from the U.S. government. Very weak and very bright laser light
can be imaged without the need for neutral density filters or beamsplitters, a
distinct advantage in many applications.
• Alpha NIR is not a conventional video camera in and of itself – it does not
produce analog video, nor does it have external switches or controls – it is really
just a sensor head. To acquire images, one connects Alpha NIR to a host
computer via a digital framegrabber board that is installed into the computer’s
PCI bus. Indigo supports two framegrabber boards from National Instruments,
the PCI-1422 LVDS and the PCI-1424 LVDS. Additionally, the computer
controls the camera through an RS-232 interface.
There are three versions of Alpha NIR available to users, ranging from a full
imaging solution to bare sensor heads for OEM applications. They are described
below:
4

Alpha NIR User’s Guide 412-0007-10 Ver 150
INDIGO OPERATIONS
• Users can purchase Alpha NIR as a turn-key imaging systems complete with
sensor head with power supply, digital interface cable, frame grabber board and
driver software, host PC, and custom software based on National Instruments
LabVIEW. The software, called IRvista, is a real-time image acquisition and
analysis application that provides the user with acquisition, storage, retrieval,
display, processing, and analysis of still images and video in a flexible,
convenient Windows interface. IRvista allows the user to control the sensor via
an integrated RS-232 interface. Operation of IRvista is described in detail in the
IRvista user’s manual (Indigo p/n 321.0028.10).
• LabVIEW programmers can purchase an Alpha NIR developer’s kit from Indigo
Systems Corporation. This kit includes Alpha NIR sensor head and power
supply, digital interface cable, and National Instruments PCI-1422 frame grabber,
a board which contains 16 Megabytes of on-board RAM, and which is capable of
acquiring images at the full 30-Hz frame rate that the sensor head is capable of
delivering.
• Advanced users can design their own interface to Alpha NIR using their own
digital frame grabber and camera control software. They need only purchase the
sensor head from Indigo Systems Corporation. We provide all necessary
interface documentation, including timing diagrams, connector pin-outs, and
command syntaxes in the Alpha NIR Interface Control Document (Indigo p/n
102.0003.10).
1.1 IRvista Installation Instructions
These are instructions for installing IRvista 2.51 or later revisions onto a
personal computer running Windows NT 4.0, Windows 2000, or Windows XP.
The recommended operating systems are Windows 2000 or Windows XP. The
recommended computer should have a P4 2.0 GHz or faster processor, at least 1
Gig of RAM, and a high-speed disk drive (7500 rpm or faster). These are
recommendations, not requirements.
PROCEDURE:
1. Open the folder called Disk 1 on the IRvista installation CD and find the folder
NI-IMAQ. The CD is Indigo part number 321-0028-00.
2. Install NI-IMAQ Version 2.5.1 from the IRvista CD only. Do not use the NI-
IMAQ CD that comes with the board! Open the folder NI-IMAQ and find
install.exe. Run install.exe.
3. Shut down the computer and install the PCI-1422 frame grabber into an unused
PCI slot. Install the PCI-1422 board using standard ESD and safety procedures.
5

Alpha NIR User’s Guide 412-0007-10 Ver 150
INDIGO OPERATIONS
4. Ensure that the board has had the correct threaded standoffs installed into it. The
threads should be 4-40, and the digital interface cable for the camera that will be
connected to the system should mate with the connector on the board and be
retained by the thumbscrews.
5. Power up the computer. It should show you a message that the IMAQ hardware
is initializing.
6. Run the Upgrade to IMAQ 2.5.3 executable on the Alpha NIR Setup CD. The
computer will reboot again.
7. Open the folder Disk 2 on the CD and run setup.exe. Use of default settings for
installation locations is strongly recommended. Do not restart until all
components have been installed and the message “IRvista INSTALLATION IS
COMPLETE” appears. In other words, hit the CANCEL button when prompted
about whether to restart after individual components are installed.
8. Restart the computer.
9. Open the folder called DLL Patch which is located in the Disk 2 folder on the CD.
Replace the two installed .DLL files with the same names with these two new
files. To do this, copy the two dll files in the DLL patch folder and paste them in
the folder called Indigo Data which is located at C:\Program Files\IRvista\Indigo
Data. When the “confirm file replacement” window pops up hit the Yes to All
button.
10. Find the folder “IMAQ Vision Deployment 6.0.3”, execute “autorun”, select
“IMAQ Vision 6.0 Run-Time Engine” – this installs the NI IMAQ Vision license.
Once it has finished installing, click on “Exit”. Do not install the first choice on
the list, which is the IMAQ Vision Deployment License.
11. Connect your IMAQ cable to the PCI-1422’s 100-pin SCSI connector. Connect
the other cable end to the camera that is being integrated with IRvista. All screw
threads should be fully engaged.
12. From your desktop, run “Measurement and Automation” – the installed NI utility.
Select OK, then double-click “Devices and Interfaces”, double-click IMAQ PCI-
1422: img 0, then right-click channel 0 – select Indigo Systems, then Alpha
NIR.icd. This configures the frame grabber to use the proper camera driver.
13. To confirm everything is working properly at this point, click “grab”. This should
result in the display of a dark box in the center of the window – this is the output
of the camera without non-uniformity correction or gain control. If the camera
type is a NIR sensor, then make sure the sensor head lens aperture is open and
6

Alpha NIR User’s Guide 412-0007-10 Ver 150
INDIGO OPERATIONS
shine a flashlight or an incandescent (fluorescent lights have low intensity in this
waveband) light into the opening. This should result in a change in intensity in the
displayed window. You should see something on the screen, albeit a low contrast
image. Close the Measurement and Automation utility.
14. Run IRvista. During the program loading, the system checks to see that a camera
is connected and communicating. Refer to the IRvista manual for help during the
next phase of testing. The manual is Indigo part number 321.0028.10.
15. Try acquiring a burst of images. The message flashed on the screen during
acquisition should show that IRvista has acquired 50 of 50 frames. The default is
50 frames, but that can be changed on the front panel. It should not drop frames –
it should always say that the number of frames acquired matches the number of
buffers (frames) received by the IMAQ card.
16. Next, try recording images direct to disc. Save the images to a .bin file on the
desktop. You will delete that file after viewing it. Record to Disc will run at >50
Hz with a 2.8 GHz Pentium 4 processor. You can verify this by acquiring 500
frames and using a stopwatch to time the acquisition. We typically see times of
less than 10 seconds with a host PC like the one described above.
17. Test the serial communications with the camera by launching the camera control
window. You can vary the gain state of the camera, as well as many other low-
level sensor functions.
Uninstall Procedure:
To uninstall IRvista and supporting software, run install.exe in Disk 1 and
setup.exe in Disk 2. You will be prompted to modify, repair, or remove most of
the components. Select remove in each case. Two supporting applications, NI-
Serial and NI Visa, must be uninstalled from the Windows control panel.
7

Alpha NIR User’s Guide 412-0007-10 Ver 150
INDIGO OPERATIONS
1.2 Installing Alpha NIR Hardware
Note: This instruction set is pertinent to users that purchased the developer’s kit for
installation on their own computer. If you purchased a turn-key system complete with
computer, please skip this section.
The Alpha NIR Imaging kit you have purchased should include:
1) Alpha NIR sensor head
2) 25mm C-mount lens
3) Tripod adapter plate
4) Connector Support
5) Tripod Mounting Screws
6) Power cord and AC/DC converter
7) Alpha NIR Setup disc
8) Settings file CD for the camera enclosed
9) IMAQ PCI-1422 frame grabber board
10)NI IMAQ Version 2.5.1 CD and documentation
11)IMAQ cable assembly for Alpha NIR
12)Carrying case
Available optional accessories:
1) Lens, 25mm, 50mm, Zoom
2) Computer System
3) LabVIEW Tool Kit
4) External Sync Cable
5) NIR Calibration Light Box
6) Internal Filter Holder (see figure 1 on p.14)
The Alpha NIR Imaging Kit has been tested and can be expected to work properly on a
computer that is configured as follows:
• Windows NT 4.0 w/ Service Pack 6 or Windows 2000 Service Pack 2
• Pentium IV 1.5 GHz or faster recommended
• 250 Mb RAM, 512 Mb recommended
• Available PCI slot
• High Resolution Graphics Adapter and Monitor
To install the Alpha NIR Imaging Kit, perform the following steps:
1) Insert Alpha NIR Setup disc 412.0007.35
2) Using MS Explorer, find the CD folder “NI-IMAQ”
8

Alpha NIR User’s Guide 412-0007-10 Ver 150
INDIGO OPERATIONS
3) Execute “autorun”
4) Select “Install NI-IMAQ 2.5.1”, click through default options, restart ok – this
installs the NI frame grabber software. (The NI CD included in your shipment is
not required)
5) Run the Upgrade to IMAQ 2.5.3 executable on the Alpha NIR Setup CD. The
computer will reboot again.
6) Shut down the computer completely.
7) Install the IMAQ 1422 board using standard ESD and safety procedures.
8) Restart the computer.
9) Connect your IMAQ cable to the NI 1422 100-pin connector. Connect the other
cable end to the Alpha NIR sensor head – all screw threads should be fully
engaged. For added support a connector support is included which is installed in
between the camera and the tripod adapter. When using the tripod adapter alone,
use the shorter 4-40 X 3/8” long socket head cap screws. When using the tripod
adapter and connector support together, use the longer 4-40 X 7/16” long socket
head cap screws.
10)Connect your Alpha NIR power adapter to the sensor head, which will now be
energized.
11)From your desktop, run “Measurement and Automation” – the installed NI utility.
Select OK, then double-click “Devices and Interfaces”, double-click IMAQ PCI-
1422:img 0, then right-click channel 0 – select Indigo Systems, then select Alpha
NIR. This configures the frame grabber to use the proper camera driver.
12) To confirm everything is working properly at this point, click “grab”. This
should result in display of a dark box in the center of the window – this is the
output of the camera without correction or gain control. Make sure the sensor
head lens aperture is open and shine a flashlight or an incandescent (fluorescent
lights have low intensity in this waveband) light into the opening. This should
result in a change in intensity in the displayed window. Close the Measurement
and Automation utility.
13) Find the folder “IMAQ Vision Deployment 6.0.3”, execute “autorun”, select
“IMAQ Vision 6.0 Run-Time Engine” – this installs the NI Labview
environment.
14) Find the folder “IRvista” on the Setup CD, execute “setup” – this installs the
IRvista software.
15) Create a shortcut to IRvista.exe form the folder C:\Program Files\IRvista. Drag
and drop this “IRvista.exe” shortcut onto the desktop.
16) Find the folder “settings” on the setting files CD – this folder contains the Non-
Uniformity Correction and Bad Pixel Replacement (NUC and BPR, or camera
settings) files for your camera. You should find 11 files that correspond to NUC
and BPR conditions found at various integration times from 5 microseconds to
500 msec and both high and low gain states.
17)Copy all of the camera settings files into the folder “C:\Program
Files\IRvista\Indigo Data\NUC and BPR”
18) Since writing these files onto the CD automatically changes the attributes to
“read only”, once we get them copied onto your disk drive, we must change them
9

Alpha NIR User’s Guide 412-0007-10 Ver 150
INDIGO OPERATIONS
back to “not read only”. So, for each camera settings file, right click on the file,
select properties, unclick “read only”, click “apply” and “ok”. Repeat until all
camera settings files are not “read only”.
19) Run IRvista. During the program loading, the system checks to see that a camera
is connected and communicating. After the IRvista splash screen, you should see
a warning to select a settings file immediately.
20) Click the button in the upper left hand corner of the display that looks like a
crossed wrench and hammer – tool tips should confirm this is the “Change
Preferences” utility. Using this tool, we must indicate what camera settings files
should be used for this camera.
21) In the section, “Non-uniformity and BPR files”, select the file open icon. This
should result in the file open dialog box that defaults to the “C:\Program
Files\IRvista\Indigo Data\NUC and BPR” folder. Select the settings file that
corresponds to the integration time and gain state you want to run (generally, one
would use 16 ms, low gain for imaging around a laboratory, 5 µs and 100 µs for
laser beam (or high intensity) applications, and 500 msec, high gain for very low-
light imaging). Click “make new default settings” to insure the system reboots to
the new settings files.
22)The imaging system should now display a corrected image.
23) For more detailed documentation, please see the user’s manual for IRvista
(Indigo p/n 321.0028.10).
1.3 Alpha NIR System Hardware Setup
Users that purchased a complete turn-key system should follow the setup instructions
given below.
1. Set up the host computer following the manufacturer’s instructions. The
computer has Windows NT installed on it already. The password for the
computer is “password”, all in lower case letters. We recommend that you
change the password to something else of your choosing for security reasons.
2. Connect the Alpha NIR interface cable to the National Instruments PCI card
connector on the back of the host computer. This is a 100-pin, very-high-density
connector located in one of the PCI slots.
3. Connect the other end of the interface cable to the Digital Interface Connector on
the side of the Alpha NIR sensor head.
4. Insert the power jack of the 6-volt Alpha NIR power supply into the Alpha NIR
sensor head’s DC Power Input on the back.
5. Plug the power supply into a wall socket.
10

Alpha NIR User’s Guide 412-0007-10 Ver 150
INDIGO OPERATIONS
6. The sensor head should immediately being streaming images to the computer.
7. Launch the IRvista application by double clicking on the IRvista icon on the host
computer’s Desktop.
8. The IRvista window will appear with a corrected live digital video image
displayed at about 10 frames per second.
Note: The Factory Test Interface Connector is generally for factory use. Please do not
attempt to communicate through the camera using this connector while simultaneously
connected to the framegrabber. The only time a user should use this connector is with
the external sync cable provided as an optional accessory.
Digital
Interface
Connector
Su
pp
ort
DC Power
In
p
ut
Factor
y
Test
Interface
Connector Tripod
Ada
p
ter
11

Alpha NIR User’s Guide 412-0007-10 Ver 150
INDIGO OPERATIONS
2 Alpha NIR External Sync Operation
2.1 Procedure for Activating External Sync with IRvista
1) Connect the interface cable between the Alpha NIR and the host computer.
2) Connect the Alpha NIR external sync cable to the back of the Alpha NIR sensor
head.
3) Connect a pulse generator or other trigger source to the external sync cable. The
signal level should be a CMOS level (3.3 volts), with a zero-volt ground level.
4) Power up camera by connecting power supply to it.
5) Open IRvista software.
6) Open the camera control panel.
7) Select external sync mode. The default value is internal sync mode. If the
software is exited, you will have to repeat 6 and 7.
8) Exit from the camera control panel if you are done. The camera should be
triggering off the external sync source. Vary the source frequency to confirm
external sync operation.
Notes:
The EXT_SYNC command is used to put the camera into External Sync Mode. When the
camera is in External Sync Mode, integration and digital data output is initiated by the
ext_sync input pin. A rising edge on the ext_sync pin will cause the camera to begin
integration within a 33.46ms frame, and begin to output the previous frame’s data on the
digital port. Note that there is a one-frame pipeline delay for the output data.
The purpose of External Sync Mode is to control the start of integration for
synchronization to an external event, or to synchronize multiple cameras. The ext_sync
signal must remain high for greater than 100ns to be recognized as a valid rising edge.
The ext_sync signal must be low for a minimum of 100ns before rising.
Integration modes “Normal” and “Special Short” are the only supported modes when
using the external sync; “Extended” and “Manual” modes are not supported.
The relationship between the ext_sync rising edge and the actual frame integration is
shown in Figure 2. Note that the end of integration is fixed; the start of integration varies
based upon the integration time that is defined. The oscillator used in the camera has a
tolerance of 100ppm. At a frame time of 33.46ms, the oscillator tolerance introduces an
uncertainty of 3.346µs in the “end of integration” prediction.
12

Alpha NIR User’s Guide 412-0007-10 Ver 150
INDIGO OPERATIONS
The ext_sync period (time between rising edges) must be greater than 33.47ms (29.87 Hz
frame rate max), in both Normal and Short modes. There is no maximum period. Periods
less than the specified limit will result in the camera ignoring ext_sync inputs.
When the camera is not in External Sync mode, the ext_sync input is unused.
Integration
Ext Sync
TEND
TSTART
TPER
TWID
TWID Minimum width of pulse = 100ns
TPER Minimum period of ext_sync = 33460µs
TWID
Normal Mode Timing
TEND Delay from Rising edge of Ext Sync to End of Integration
822076 ± 8.5 clocks (33492 ± 3.7us)
TSTART Delay from Rising edge of Ext Sync to Start of Integration
36 + (count*16) ± 8.5 clocks (where count is from Normal Integration Counter)
TEND Delay from Rising edge of Ext Sync to End of Integration
419.5 ± 8.5 clocks (17.09 ± 0.35us)
TSTART Delay from Rising edge of Ext Sync to Start of Integration
11.5 + (count*16) ± 8.5 clocks (where count is from Short integration counter)
Special Short Mode Timing
Clock = 1/24545450Hz = 40.74075ns
13

Alpha NIR User’s Guide 412-0007-10 Ver 150
INDIGO OPERATIONS
14

Alpha NIR User’s Guide 412-0007-10 Ver 150
INDIGO OPERATIONS
F
F
Fi
i
ig
g
gu
u
ur
re
e
e
1
1
1
r
S
A
Al
lp
ph
ha
a™
™
N
NI
IR
R
C
Ca
al
li
ib
br
ra
at
ti
io
on
n
L
Li
ig
gh
ht
t
S
So
ou
ur
rc
ce
e
N
NU
UC
C
P
Pr
ro
oc
ce
ed
du
ur
re
e
N
N
NI
I
IR
R
R
C
C
Ca
a
al
l
li
i
ib
b
br
r
ra
a
at
t
ti
i
io
o
on
n
n
L
L
Li
i
ig
g
gh
h
ht
t
t
S
So
o
ou
u
ur
r
rc
c
ce
e
e
15

Alpha NIR User’s Guide 412-0007-10 Ver 150
INDIGO OPERATIONS
3 Alpha™ NIR Calibration Light Source NUC Procedure
3.1 RECOMMENDED EQUIPMENT & SOFTWARE
3.1.1. National Instrument Framer Grabber (P/N 216-0001-03)
3.1.2. IRvista software (321-0028-00) and Indigo Alpha NIR Camera Interface
software (110-0064)
3.1.3. 0 to 12V Adjustable DC Power Supply for Light Source.
3.1.4. Indigo Adjustable Light Source Box
3.1.5. Lens tissue and lens cleaner solution
3.1.6. Black cloth for blocking ambient room light
3.2 PROCEDURE
3.2.1. Verify that the FPA window is very clean.
3.2.2. Set up the light box against the front of the camera lens, or the front of the
camera itself. If a lens is used, it is best to set the lens aperture and focus to
the desired values before performing the non-uniformity correction. In
actual practice, aperture and focus adjustments are made constantly. We
tend to perform generic corrections with the aperture wide open and the
focus set to infinity. One can perform a one-point correction one the lens is
set properly to minimize spatial non-uniformity.
3.2.3. Set the power supply to 0 VDC for the light box. WARNING: The lamp
inside the light box is rated for a maximum drive voltage of 12 VDC. Set
power supply voltage to 0 VDC before connecting power cable to light box.
Verify that the power supply is set to voltage readout and not amps readout.
3.2.4. Mount lens on camera and open the lens aperture to wide open (f /1.4).
Focus the lens to infinity.
3.2.5. Attach Digital Interface cable to camera.
3.2.6. Raise height of camera lens to center it to the light box. The camera lens
should be pushed against the light box’s diffusion filter.
3.2.7. Power up the camera (6 VDC) and open “IRvista.exe” on PC desktop. If
IRvista does not open, check that the “File Path for Camera Settings”
window shows NOFILE in capital letters.
3.2.8. Place the black cloth over the camera and light box.
16

Alpha NIR User’s Guide 412-0007-10 Ver 150
INDIGO OPERATIONS
3.2.9. Open “IRvista” on PC desktop. Go to “Setup” menu, then pull down to
“Preferences”. Name the file in the “File path for camera settings” box.
Select “Apply and Save Preferences”. Select “Change”.
3.2.10. Select “Camera” at the top tool bar.
3.2.11. Select “Camera Control” at the top tool bar.
3.2.12. Select “Skimming on” or “Skimming off.”
3.2.13. Select “Low Gain” mode or “High Gain” mode.
3.2.14. Set “Integration Time” in microseconds (i.e. 16 msec is 16000 usec)
3.2.15. Set VDetCom to the minimum voltage for the integration time using the
“Camera Control” selection under the “Camera” menu on the upper tool bar.
IMPORTANT NOTE: If the NUC looks bad because it appears that a large
area of pixels are not turned on, try a higher VDetCom voltage.
INTEGRATION TIME MINIMUM VDETCOM
VOLTAGE
33.2 msec lens on, f/ 1.4, skimming on Low Gain 4.70V
16 msec lens on, f/ 1.4, skimming on Low Gain 4.70V
500 usec no lens, skimming on Low Gain 4.75V
100 usec no lens, skimming on Low Gain 4.80V
25 usec no lens, skimming on Low Gain 5.0V
*5 usec no lens, skimming off Low Gain 5.1V
16 msec lens on, f /1.4, skimming off High Gain 4.70V
33.2 msec lens on, f /1.4, skimming off High Gain 4.70V
100 msec lens on, f /1.4, skimming off High Gain 4.70V
200 msec lens on, f /1.4, skimming off High Gain 4.70V
500 msec lens on, f /1.4, skimming off High Gain 4.70V
*Note integration times shorter than 25 usec may need a brighter light
source.
3.2.16. Select “Camera” at the upper tool bar.
3.2.17. Select “Calibrate Camera”.
3.2.18. Or select “Generate New NUC and BPR tables” icon on top tool bar. Icon
has camera with arrow on it.
3.2.19. Create a camera folder.
3.2.20. Create an integration time folder. Highlight the new folder.
17

Alpha NIR User’s Guide 412-0007-10 Ver 150
INDIGO OPERATIONS
3.2.21. Push the “Select Cur Dir button”.
3.2.22. Note the IRvista histogram mean count value of the pixels in the array with
the light off. This “light off” mean count value will typically be around 350-
450 counts at 16 msec, low gain mode with skim enabled. It may be as high
as 1000 counts in high gain mode with skim enabled.
3.2.23. Adjust light box voltage so that the histogram mean is approximately 100
counts over the minimum “light off” mean count value. This is the DARK
level used in the NUC.
3.2.24. When the image’s mean count value reaches 100 counts above the light off
counts and stabilizes, push the “GO” button. The light box can sometimes
take a few moments to stabilize. Once you press GO, the system acquires 64
frames of image data and averages them. Do not touch the camera, light
box, or light box power supply controls during the collection process.
3.2.25. When prompted by IRvista to set the MEDIUM source intensity, adjust the
lamp voltage until the mean value is about 400 counts above the “light off”
mean count value. Push the GO button when the light box has stabilized at
the desired mean value.
3.2.26. When prompted by IRvista to set the BRIGHT source intensity, adjust the
lamp voltage until the mean value is about 950 counts above the “light off”
mean count value. Push the GO button when the light box has stabilized at
the desired mean count value.
3.2.27. At Bad Gains Pixel Map window, note the sizes of clusters with the limits
set to 50% and 150% of the mean gain. Adjust the gain limits so that the
clusters stay within spec. We will quantitatively measure these clusters after
the NUC process is complete. The Minimum Allowed Gain number is
usually increased until too many bad pixels are found in the corner of the
image or until a cluster is too big (out of spec). The Maximum Allowed
Gain number is decreased until too many bad pixels are found in the center
of the image or until a cluster is too big. The target number of bad pixels
failed on gain should not exceed 400, which is approximately 0.5% of the
total number of pixels. Try not to grow a cluster such that it fails the spec.
Cluster spec is less than 6 for the inner zone and less than 10 for the outer
zone.
3.2.28. “Accept”, Bad Gains Pixel Map.
3.2.29. Adjust the limits for the Bad Noise Pixel Map to be the same as for the Bad
Gain Pixel Map. Be careful to not overcorrect for Pixels with bad noise.
The number of bad noise pixels should not exceed 400 minus the number of
Bad Gain pixels. For example, there may be only 100 pixels marked as
having bad gains.
3.2.30. “Accept”, Bad Noise Pixel Map.
3.2.31. “OK” at warning message.
18

Alpha NIR User’s Guide 412-0007-10 Ver 150
INDIGO OPERATIONS
3.2.32. Save in the camera’s folder. “Save”.
3.2.33. Apply now, but don’t change default settings. Push the “GO” button.
3.2.34. Look at the camera’s image with lens on. If the image is good, continue if
another NUC is to be made. If there is a large area of bad pixels in the
image, try increasing VDetCom voltage and re-NUC the camera.
3.2.35. Do a NUC for each integration time. Set the integration time and VDetCom
by selecting the “Camera” and “Control Camera” options from the pull
down menu or at the “Control System Camera Directly” option on the upper
tool bar. IMPORTANT NOTE : If the NUC looks bad because it
appears that a large area of pixels are not turned on, try a higher
VDetCom voltage. Set the Camera Integration Time, skimming mode, and
VDetCom voltage to;
INTEGRATION TIME MINIMUM VDETCOM
VOLTAGE
33.2 msec lens on, f/ 1.4, skimming on Low Gain 4.70V
16 msec lens on, f /1.4, skimming on Low Gain 4.70V
500 usec no lens, skimming on Low Gain 4.75V
100 usec no lens, skimming on Low Gain 4.80V
25 usec no lens, skimming on Low Gain 5.0V
*5 usec no lens, skimming off Low Gain 5.1V
16 msec lens on, f /1.4, skimming off High Gain 4.70V
33.2 msec lens on, f /1.4, skimming off High Gain 4.70V
100 msec lens on, f /1.4, skimming off High Gain 4.70V
200 msec lens on, f /1.4, skimming off High Gain 4.70V
500 msec lens on, f/ 1.4, skimming off High Gain 4.70V
*Note integration times shorter than 25 usec may need a brighter light
source. Also, some sensors may not image very well in high gain mode
and at long integration times (200 msec or 500 msec in high gain mode).
3.2.36. Open the “Generate New NUC and BPR tables” icon on top tool bar. Icon
has camera with arrow on it.
3.2.37. Open camera’s folder.
3.2.38. Create an integration time folder and highlight the folder.
3.2.39. Push the “Select Cur Dir” button.
3.2.40. Repeat 2.11. to 2.35. for each NUC.
19
Table of contents
Other FLIR Digital Camera manuals
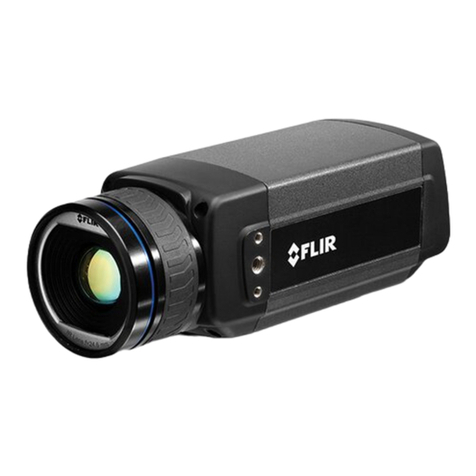
FLIR
FLIR A6 Series User manual
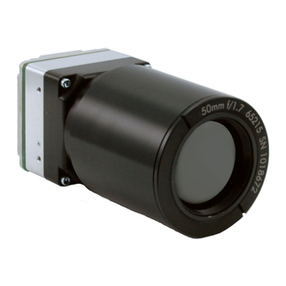
FLIR
FLIR Tau Camera TAU-0035-00-10 User manual
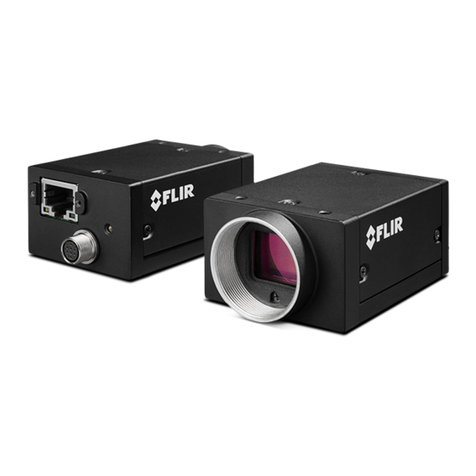
FLIR
FLIR GRASSHOPPER 3 Series Use and care manual

FLIR
FLIR A3 PT series User manual
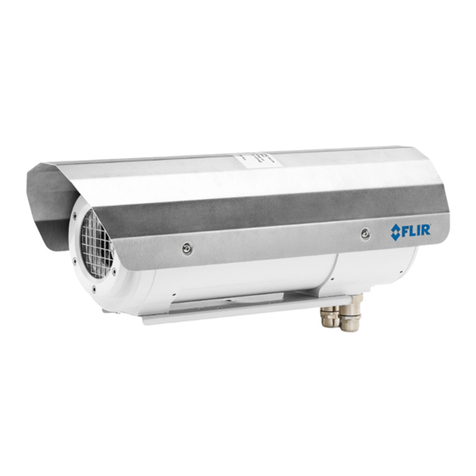
FLIR
FLIR A310 ex Series User manual
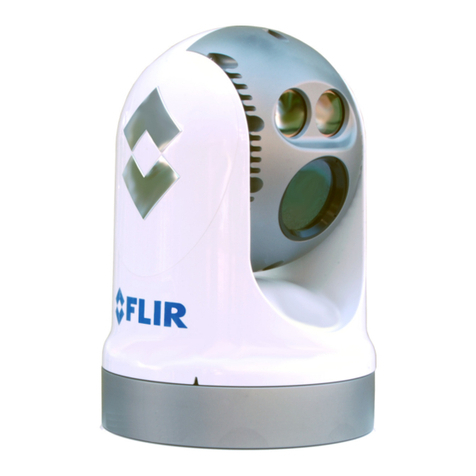
FLIR
FLIR M500 User manual

FLIR
FLIR ThermaCAM QuickView User manual
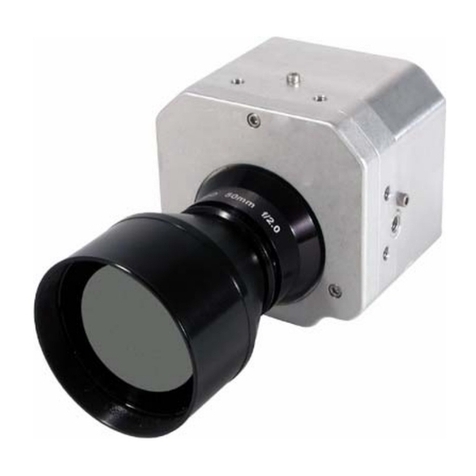
FLIR
FLIR Photon Block 2 User manual
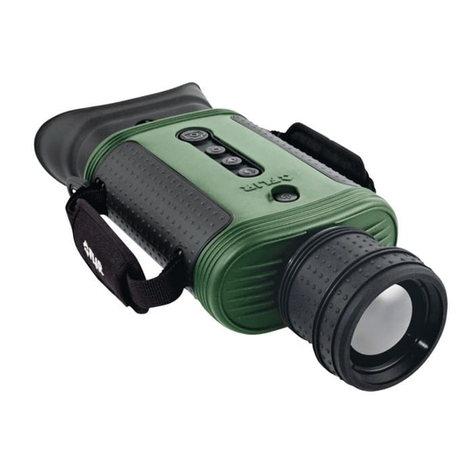
FLIR
FLIR Scout Bi-Ocular User manual
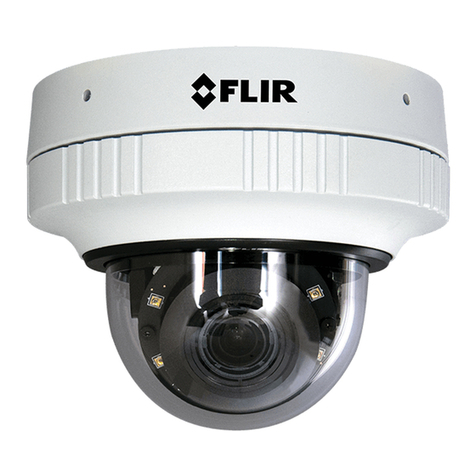
FLIR
FLIR Quasar CM-6405 User manual
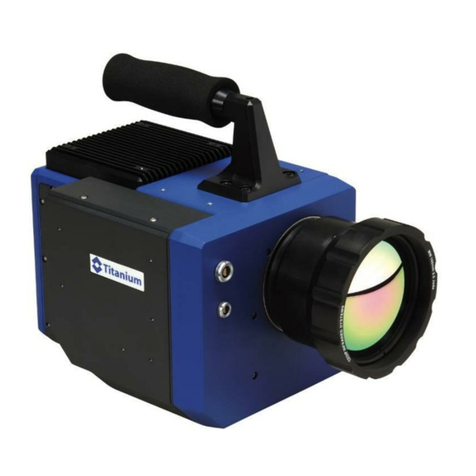
FLIR
FLIR ORION SC7000 User manual
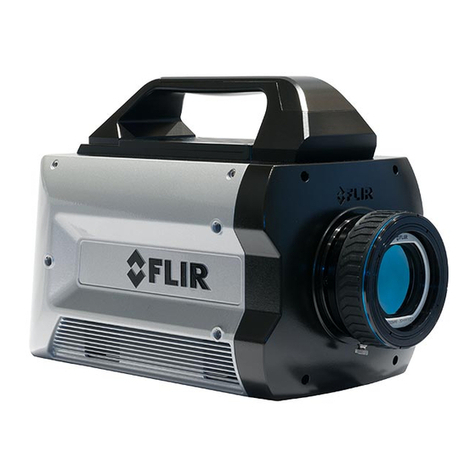
FLIR
FLIR X-Series User manual
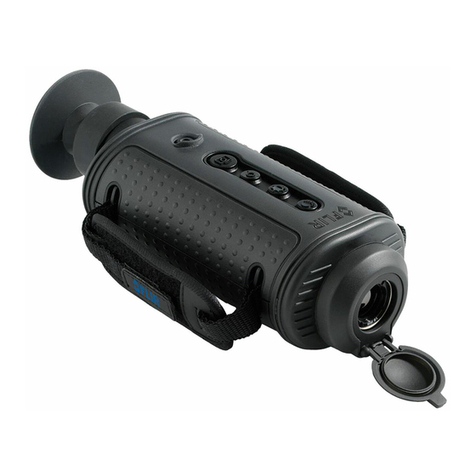
FLIR
FLIR HS-324 User manual
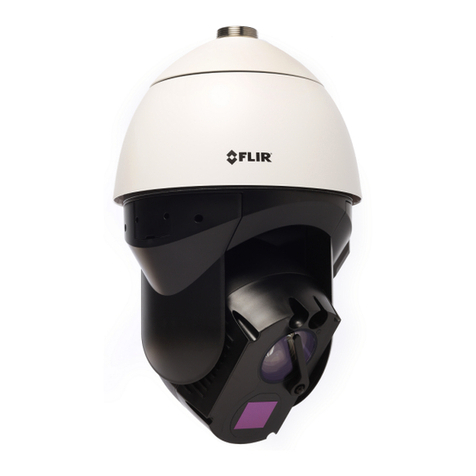
FLIR
FLIR Elara DX Series User manual
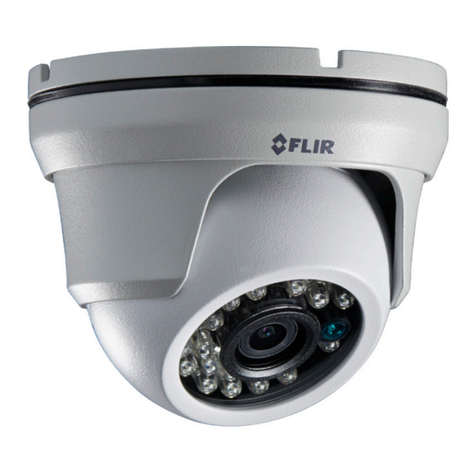
FLIR
FLIR Flir MPX User manual
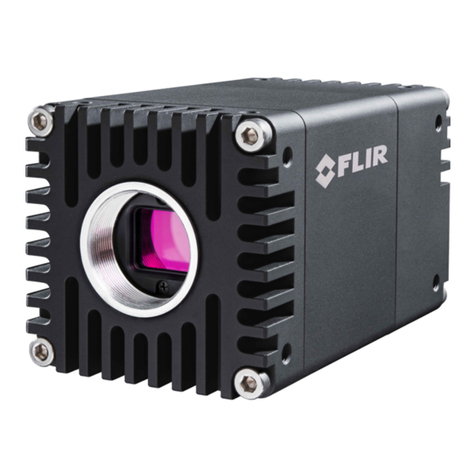
FLIR
FLIR ORYX R User manual
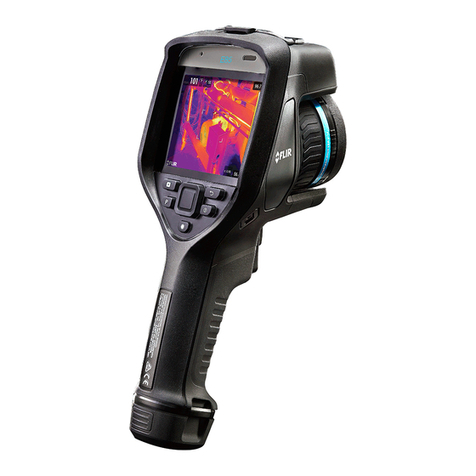
FLIR
FLIR Exx series User manual

FLIR
FLIR FC S Series Assembly instructions

FLIR
FLIR Tau CNV User manual
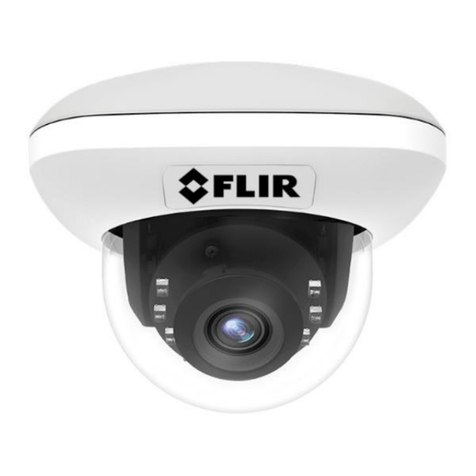
FLIR
FLIR Ariel CM-3102 Manual