Fourgroup DUPLEX-UP Technical manual

DUPLEX-UP
USE AND INSTALLATION HANDBOOK
DUPLEX-UP
CONTROL PANEL FOR 2 ELECTRIC PUMPS WITH CURRENT CONTROL .
PR .T : FG006172
Date : 10/02/14
Rev . 01
Via Enrico Fermi 8 - 35020 Polverara PD
Tel.049/9772407 Fax.049/9772289
www.fourgroup.it E-mail : [email protected]

2
1. Warnings
page………3
2. Overview
page ………4
3. Handling
page ………4
4. Application and working limits
page ……….5
5. Standard operations
page ……….6
6. Installation
page ……….7-8
7. Electrical connection
page ……….9-10
8. Regulation and calibration
page ……….11
9. Stop of the pumps
page ……….12
10. Lights and push-buttons
page ……….12
11. Maintenance
page ……….13
12. Waste disposal
page ……….13
13. Warranty
page ……….14
14. Spare parts
page ……….14
15. Conformity declaration
page ……….15
16. Connection diagrams
page ……….16
INDEX

3
The following symbols, accompanied by the words: “Danger”, “Warning”,
indicate the potential hazard resulting from failure to observe the associated
warning, as specified below:
Failure to observe this warning may result in
electric shock
Failure to observe this warning may cause
personal injury and/or damage to property
Failure to observe this warning may cause
damage to the pump, the unit or the system
-CAUTION:
Make sure the pumps are fully primed before you start them.
-CAUTION:
The control panel must be connected by a qualified electrician in compliance
with the electrical regulations in force.
-CAUTION:
The electric pump or the motor and the panel must be connected to an efficient
grounding system in compliance with the electrical regulations locally in force.
-CAUTION:
Ground the unit before carrying out any other operation.
-CAUTION:
The electric pump or the motor can start up automatically.
-CAUTION:
As a general rule, always disconnect the power supply before proceeding to
carry out any operation on the electrical or mechanical components of the unit
or system.
1. WARNINGS
DANGER
RISK OF ELECTRIC
SHOCK
DANGER
WARNING

4
The purpose of this manual is to provide the necessary information for the proper
installation, use and maintenance of DUPLEX-UP. The user should read this manual
before operating the unit. Improper use may cause damage to the machine and lead
to the forfeiture of the warranty coverage. Always specify the model identification
code and the construction number when requesting technical information or spare
parts from our Sales and Service department. The instruction and warnings given
below concern the standard version; refer to the sale contract documentation for
modifications and special version characteristics. For instructions, situations and
events not considered in this manual or in the sale documents, please contact our
customer service.
Our units must be installed in sheltered, well-ventilated, non-hazardous environments
and must be used at a maximum temperature of +40°C and minimum of -5°C.
DANGER
WARNING
The panel must be handled with care, as falls and knocks can cause damage without
any visible external signs.
If for any reason the unit is not installed and starter immediately after it has reached
its destination it must be stored properly. The external packaging and the separately
packed accessories must remain intact, and the whole must be protected from the
weather, especially from freezing temperatures, and from any knocks or falls.
PRELIMINARY INSPECTION: after you have removed the external packaging,
visually inspect the control panel to make sure it has suffered no damage during
shipping.
If any damage is visible, inform a FOURGROUP dealer as soon as possible, no later
than five days from the delivery date.
2. OVERVIEW
3. HANDLING

5
DANGER
RISK OF ELECTRIC
SHOCK
WARNING
The DUPLEX-UP is designed for controlling two motors or electric pumps used
in pressurization systems or in applications for emptying wells or water tanks
with multi-contact float switches.
FOURGROUP S.r.l. shall not be liable for any damage caused or suffered by
the unit as a result of its unauthorised or improper use.
TECHNICAL FEATURES :
• Electronic control panel;
• Input voltage 1~50/60 Hz 230V ±10% (single-phase model DUPLEX-UP-M);
• Input voltage 3~50/60 Hz 400V ±10% (three-phase model DUPLEX-UP-T);
• Very low voltage input for float switch of stop;
• Very low voltage input for n.2 float switches of start;
• Very low voltage input for max level alarm float switch;
• Very low voltage input for n.2 motors Klixon;
• Pumps’ exchanger circuit with 4” delay between the starts of the 2 pumps;
• Possibility to exclude a damaged pump;
• Internal selector for exclusion of pumps exchanger;
• Push-buttons for AUTO-OFF-MANUAL motor operation (MANUAL temporary);
• Green led for power on;
• N.2 green led for motors operating;
• N.2 green led for auto operation;
• Red led for water level alarm;
• N.2 red led for overload motors protection alarm;
• N.2 red led for alarm: motor’s Klixon active;
• N.2 push button for restoration from protection;
• Adjustable electronic protection for motors overload;
• Time for activation of protection: 5”;
• Auxiliary circuits protection fuse;
• Motors protection fuses;
• Alarm output with exchangeable contacts 5 A 250V (resistive load);
• Main switch with door interlock;
• Single-phase model adapted for the insertion of a capacitor (not included);
• Box in ABS;
• Output with cable holder;
• Protection IP55;
• Ambient temperature: -5/+40 °C;
• Relative humidity 50% at 40 °C (not condensed).
Do not use the product in environments where dust, acids, corrosive and/or
flammable gases etc. are present.
4. APPLICATION AND WORKING

6
DANGER
RISK OF ELECTRIC
SHOCK
DANGER
WARNING
The “Mains power on” LED comes on to indicate that the board is functioning properly.
The motor can be governed directly by the operator with man present (Manual) or by remote
signals (Automatic) by means of the “Automatic – Off – Manual” buttons; (when the
automatic button is pushed the related LED above the button lights and the control panel is
ready to receive remote signals from the sensors and floats).
- G.MIN input can have double function:
With “AUTORITENUTA” jumper ON: G.MIN is used as STOP LEVEL (The 2 pumps continue
to run, after G1 and G2 command, until the G.MIN float switch is no longer tilted);
Without “AUTORITENUTA” jumper : G.MIN is used as MINIMUM LEVEL FLOAT SWITCH and
all the pumps can only work when the minimal level is exceeded.
With “EXC ALLAR.” Jumper it is possible to exclude the “LEVEL ALARM” red light
and the OUTPUT ALARM RELAY when G. MIN float switch is switches off.
This function is used when “AUTORITENUTA” Jumper is ON.
-G1 input is used as EXCHANGER function (it can be any free voltage contact – float switch)
- G2 input is used as EMERGENCY function (the second pump starts after 4-5 second)
- G.A. input is used as LEVEL ALARM function (when switches-on the 12Vcc SIREN output is
ON with a MAXIMUM absorption 30 mA)
The green pilot lights “Motor ON” indicate the functioning of the motors.
If the Overload protections are tripped, the motors stop and the red “MOTOR PROTECTION
ENABLED” and the red “LEVEL ALARM” LED lights on. Push RESET to reset the alarm;
Check for the cause of the malfunction before restoring the motor to operation.
If the motor has 2 wires for the thermal protection of the motor winding, connect them to the
“THERMAL T1” input terminal. If the protection cuts in, the motor is cut out when the contacts
open. If the motor does not have a built-in protection, then it is necessary to make a jumper
on THERMAL T1 input in order to enable the motor.
- The ammetric protection tripping current can be adjusted by means of the
“CORRENTE MOTORE” (MOTOR CURRENT) Trimmer, based on the rated absorption of
the motor; the adjustment can be made from a minimum of 2A to a maximum of 22A.
The cut-in delay time is fixed at 5 seconds and can be overridden during setting by
bridging the “ESCL.TIM.TA” Jumpers;
GENERAL NOTES :
During the calibration for Over-Load Protection, start the motor 2-3 times to check the
correct operating.
5. STANDARD OPERATIONS

7
DANGER
RISK OF ELECTRIC
SHOCK
DANGER
WARNING
Line of supply current
Connect the unit at ground before carrying out any other operation.
The voltage input corresponds to the data written on the panel and on the pump.
( 400V ± 10% 50/60Hz x DUPLEX-UP-T )
( 230V ± 10% 50/60Hz x DUPLEX-UP-M ).
Make sure that the power-supply-cable can bear the nominal current and connect it to
the terminals of the general switch of the control panel.
If the cables are exposed, they must be appropriately protected.
The line must be protected with a differential magnetotermic switch measured in
accordance with the regulations locally in force.
Line of motor power supply
Connect the unit at ground before carrying out any other operation.
The voltage input corresponds to the data written on the motors.
(400V±10% 50/60Hz three-phase)
(230V±10% 50/60Hz single-phase).
Doing some starting make sure that the motors respect the right direction of rotation
usually indicated by an arrow printed on the motors.
Line of external control
It is possible to control the motor in “Automatic” using a free voltage contact
normally open as a float switch or a pressure switch.
It is a line in very low voltage and not a power line. Connect anyway with the control
panel switched off and with the circuit breaker disconnected.
6a. INSTALLATION

8
-TO FIX THE CABLES IN THEIR TERMINALS USE A TOOL OF THE PROPER SIZE TO AVOID
THE DAMAGING OF THE SCREWS OR OF THEIR SEAT. If use an electric screwier pay
attention not to spoil the thread or the screws.
-FIX THE CONTROL PANEL TO A WALL AS IN PICTURE N.1 WITH SCREWS AND SCREW
ANCHOR USING THE HOLES ARRANGED IN THE BOX OR THE FIXING BRACKET IF
PRESENT.
AFTER THE FIXING, REMOVE EVERY PLASTIC OR METALLIC SURPLUS (ex. Pieces of copper of
the cables or plastic shavings of the box) INSIDE THE BOX BEFORE SUPPLING POWER.
WALL
Fig.1
N.B. : DO NOT INSTALL THE CONTROL PANEL CLOSE TO OBJECTS IN CONTACT WITH
FLAMMABLE LIQUIDS, WATER OR GAS.
6b. INSTALLATION

9
DANGER
RISK OF ELECTRIC
SHOCK
DANGER
WARNING
7a. ELECTRICAL CONNECTION DUPLEX-UP-T
OVERLOAD TRIMMERS AMPEROMETRIC
TRANSFORMERS
MOTOR COMMAND
LINE PROTECTION
FUSES
-
MOTORE 1 -
MOTORE 2
AMPEROMETRIC PROTECTION CUT-
IN DELAY TIME OVERRIDE JUMPERS
- WITH JUMPER CONNECTED:
DELAY
O
VERRIDDEN
PRIMARY LINE
PROTECTION
FUSE
(
400
V
)
PUMPS EXCHANGER JUMPERS
-WITH JUMPER IN “ ON “POSITION
PUMPS EXCHANGE IS ACTIVES
-WITH JUMPER IN “ OFF “POSITION :
PUMPS EXCHANGE IS NOT ACTIVES;
G1 IS ONLY THE FLOAT SWITCH FOR PUMP 1
G2 IS ONLY THE FLOAT SWICTH FOR PUMP 2
JP1 : JUMPER AUTORIT.
- WITH JUMPER CONNECTED: AUTORITENUTA IS ACTIVE (G.MIN IS USED AS STOP LEVEL FLOAT)
- WITH JUMPER DISCONNECTED: AUTORITENUTA IS NOT ACTIVE
( G.MIN IS USED AS MINIMUM LEVEL FLOAT ).
SENSORS ALARM OVERRIDE JUMPER
- WITH JUMPER CONNECTED:
ALARMS ACTIVE ( LED ON)
N° 2 CONNECTORS
FOR ALARM SIREN
12Vcc MAX 30 mA
CLICSON MOTOR
PROTECTION
CONNECTIONS
(T1, T2)

10
DANGER
RISK OF ELECTRIC
SHOCK
DANGER
WARNING
7b. ELECTRICAL CONNECTION DUPLEX-UP-M
START
CAPACITOR
CONNECTIONS
MOTOR
PROTECTION
FUSES
PRIMARY LINE
PROTECTION
FUSE
(
230
V
)
PUMPS EXCHANGER JUMPERS
-WITH JUMPER IN “ ON “POSITION
PUMPS EXCHANGE IS ACTIVES
-WITH JUMPER IN “ OFF “POSITION :
PUMPS EXCHANGE IS NOT ACTIVES;
G1 IS ONLY THE FLOAT SWITCH FOR PUMP 1
G2 IS ONLY THE FLOAT SWICTH FOR PUMP 2
JP1 : JUMPER AUTORIT.
- WITH JUMPER CONNECTED: AUTORITENUTA IS ACTIVE (G.MIN IS USED AS STOP LEVEL FLOAT)
- WITH JUMPER DISCONNECTED: AUTORITENUTA IS NOT ACTIVE
( G.MIN IS USED AS MINIMUM LEVEL FLOAT ).
SENSORS ALARM OVERRIDE JUMPER
- WITH JUMPER CONNECTED:
ALARMS ACTIVE ( LED ON)
N° 2 CONNECTORS
FOR ALARM SIREN
12Vcc MAX 30 mA
CLICSON MOTOR
PROTECTION
CONNECTIONS
(T1, T2)
OVERLOAD TRIMMERS AMPEROMETRIC
TRANSFORMERS
AMPEROMETRIC PROTECTION CUT-
IN DELAY TIME OVERRIDE JUMPERS
- WITH JUMPER CONNECTED:
DELAY
O
VERRIDDEN

11
Before the ignition the “System of Motor Protection from Overload” has to be calibrated
setting the Current Protection on the internal regulator of the Board.
The Protection Delay is set at a fix time of 4 seconds.
During the calibration close the JUMPER “E.T.TA“ to disable the delay protection;
The Regulator of Current Protection depends of the value of calibration set on the
board;
Trimmer “CORRENTE MOTORE”
NOTE : When the setting is complete, reset the protection tripping current delay time
by removing the “ESCL.TIM.TA” JUMPER;
EXAMPLE OF CURRENT PROTECTION FOR A THREE PHASE MOTOR:
Suppose that we want to set the Protection from Overload for a three phase motor of
5,5kW (7,5Hp) with a Nominal Supply Current of about 12 A.
CALIBRATION STEPS:
Override the current protection cut-in delay time by CONNECTING the E.T.TA
JUMPER;
Set the maximum value with the internal regulator on the “Protection tripping
current” panel (turn clockwise)
Turn the motor on and, with the “Protection tripping current” regulator, reduce
until the red “Motor Protection” LED comes on and the motor stops; (THIS SHOULD
CORRESPOND APPROXIMATELY TO THE RATED CURRENT… 12A);
Increase the “Protection tripping current” adjustment by approximately 10-20% of
the previously set value. (AT APPROX. 15a)
Reset the Protection Cut-in Delay by REMOVING ESCL.TIM.TA JUMPER; (the delay
is used to allow for the initial inrush currents);
8a. REGULATION AND CALIBRATION
EXAMPLE OF CALIBRATION OF MOTORS
- Current protection regulator
Set the current protection of the motor at
a value superior of about 10-20% of the
nominal current.
Example: for a motor with nominal
electrical input of 10A set it at about 12A
22A
2A
19A3A
12A6A
5A 15A
9A
8b. REGULATION AND CALIBRATION

12
WARNING
The MOTORS can be switched off in the following ways:
- In “manual”, the motors stop when the “MANUAL” button is released;
- In “automatic”, the motors stop when the FLOAT SWITCH are no longer
enabled or when the current protection is actives, or by pushing the “0 –
RESET” button;
- Turning the general switch with door interlock to “0”.
INDICATES THAT THE MAIN POWER IS ON ( GREEN LIGHT )
INDICATES THAT THE ALARM LEVEL IS ON ( RED LIGHT )
INDICATES THAT THE MOTOR IS RUNNING ( GREEN LIGHT )
CONTEMPORARY LIGHTING INDICATES THAT THE OVERLOAD
PROTECTION IS ON ( RED LIGHTS )
INDICATES THAT THE CLICSON THERMAL PROTECTIONS IS ON ( RED LIGHT )
KEEPING IT SWITCHED, THE MOTOR STARTS, EVERY ALARM IS BY-PASSED.
WHEN IT IS RELEASED THE MOTOR GET DISCONNECTED.
PUSH TO DISCONNECT THE MOTOR AND RESET THE ACTIVE PROTECTIONS.
WHEN PUSHED, THE AUTOMATIC MODE IS ACTIVATED WHICH IS INDICATED BY
THE GREEN LED; THE BOARD IS READY TO RECEIVE SIGNALS FROM THE
FLOATS SWITCHES or PRESSURE SWITCHES.
9. STOP OF THE PUMPS
10. LIGHTS and PUSH-BUTTONS ON THE FRONT-PANEL

13
DANGER
WARNING
DUPLEX-UP does not require any routine maintenance provided that their working
limits are observed. Any maintenance operations must be performed by qualified and
experienced personnel, in compliance with the safety regulations in force.
DANGER!
Make sure that DUPLEX-UP is disconnected from the power supply before
performing any maintenance operations.
After the control panel has been installed and started, the customer must provide for
the appropriate elimination/disposal of the waste materials according to the legislation
locally in force.
If the control panel or parts of it must be taken out of service and dismantled, follow
local regulations regarding sorted waste disposal. Refer to the appropriate recycling
centres.
CAUTION: Contamination of the environment with hazardous substances such as
battery acid, fuel, oil, plastic, copper, etc., may cause serious damage to the
environment and endanger people’s health.
11. MAINTENANCE
12. WASTE DISPOSAL

14
Our products are guaranteed for a year from the date of commissioning; this applies
only to products purchased from our offices or from our authorized retailers. The
warranty does not extend beyond 15 months from the date of shipping. If the
shipping documentation is missing, the date of manufacture is given in the code on
the nameplate or fused into the interior of the terminal box. The warranty covers all
manufacturing defects of material manufactured by us; it covers replacement and
repair only, at our premises and by our staff, of the defective panel or part. The
warranty does not provide for any claims by the customer. The warranty does not
cover damage caused by faulty electrical connections, lack of adequate protection,
incorrect assembly, incorrect use or any negligence in installing and operating the
plant.
The WARRANTY is also void in the following circumstances:
- damage due to corrosion or abrasion of any type or nature;
- malfunction due to improper installation;
- repair, disassembly or tampering by unauthorized persons;
- failure by the customer to pay due amounts.
The defective product must be returned to our factory carriage paid. We reserve the
sole right to determine the cause of the defect and whether it is covered by the
warranty or not. After the repair, the goods will be returned to the Customer carriage
forward.
WE DECLINE all liability for damages and injury caused by our products.
Fourgroup S.r.l. reserves the right to modify its products without notifications. Any
controversy arising from the terms of this warranty shall be resolved in the Padua
Court, even if payment is agreed by bank’s draft.
For any further information, refer to the sales contract.
Always state the exact model identification number and construction number when
requesting technical information or spare parts from our sales and service centre.
Use only original spare parts when replacing any faulty components.
The use of unsuitable spare parts can cause malfunctions, personal injury
and damage to property.
13. WARRANTY
14. SPARE PARTS

15
FOURGROUP S.r.l. with centre in Polverara via Enrico Fermi 8 – Padova – Italy,
declare that the products
DUPLEX-UP-T , DUPLEX-UP-M
is in compliance with the following European directives and with the national directives
of actuation :
Machine 2006/42/CEE
European Directive 2006/95/CE
Electromagnetic compatibility 2004/108/CEE
and the following technical rules:
EN 60439-1, EN 55014-1, EN 55014-2, EN 61000-3-2, EN 61000-3-3
Polverara – Italy, 05/08/2009
LEGAL REPRESENTATIVE
(Grigoletto Per. Ind. Walter)
15. CONFORMITY DECLARATION

16
16. CONNECTION DIAGRAMS
CONNECTIONS DUPLE
X
-UP-M
CONNECTIONS DUPLE
X
-UP-T
Table of contents
Other Fourgroup Control Panel manuals
Popular Control Panel manuals by other brands
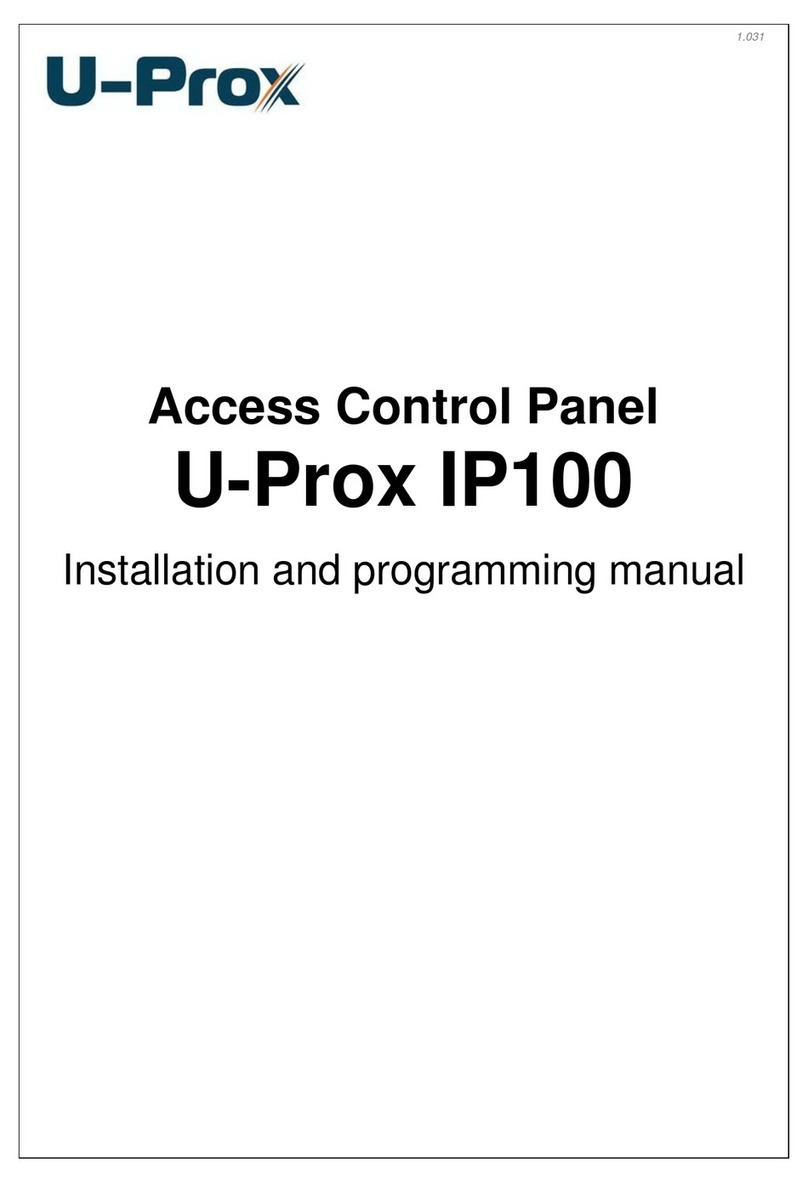
U-Prox
U-Prox IP100 Installation and programming manual
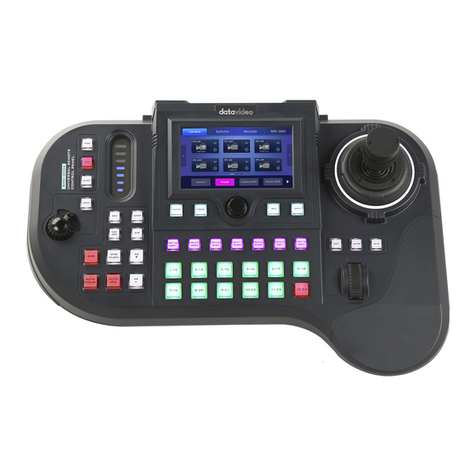
Data Video
Data Video RMC-300A instruction manual
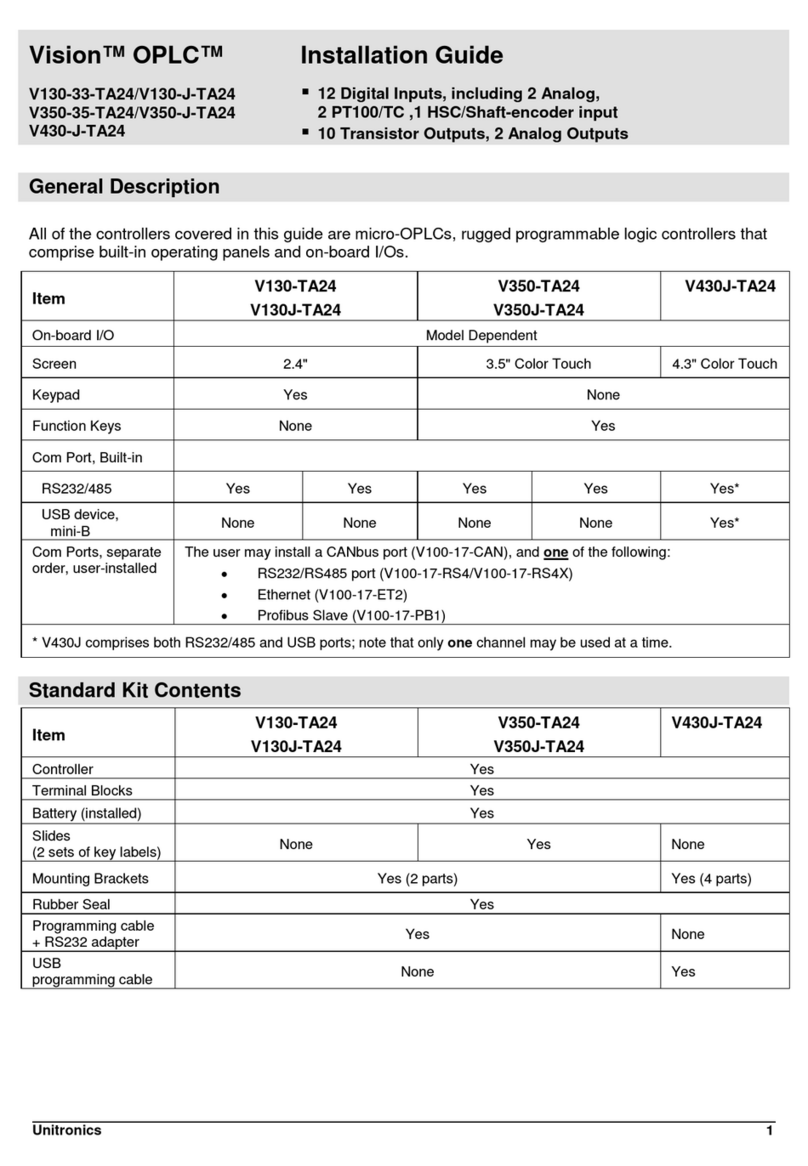
Vision
Vision OPLC V130-33-TA24 installation guide
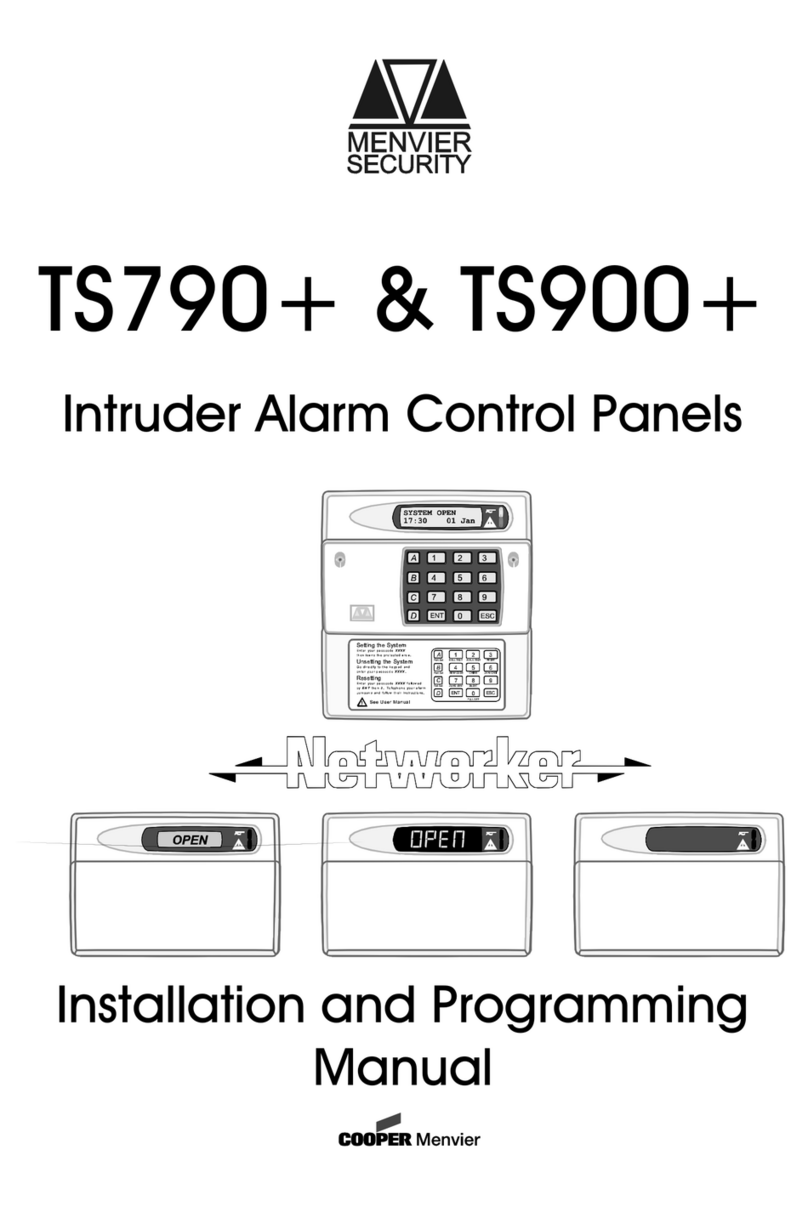
Menvier Security
Menvier Security TS790+ Installation and programming manual
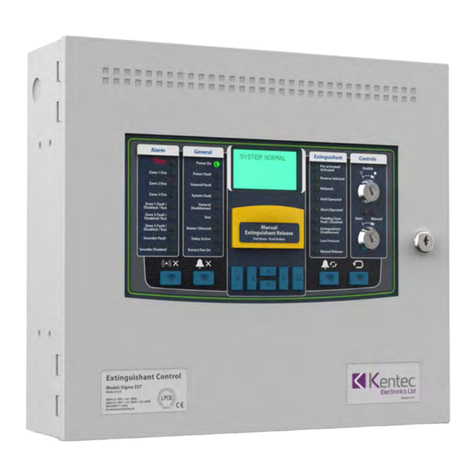
Kentec Electronics
Kentec Electronics Sigma ZXT installation manual
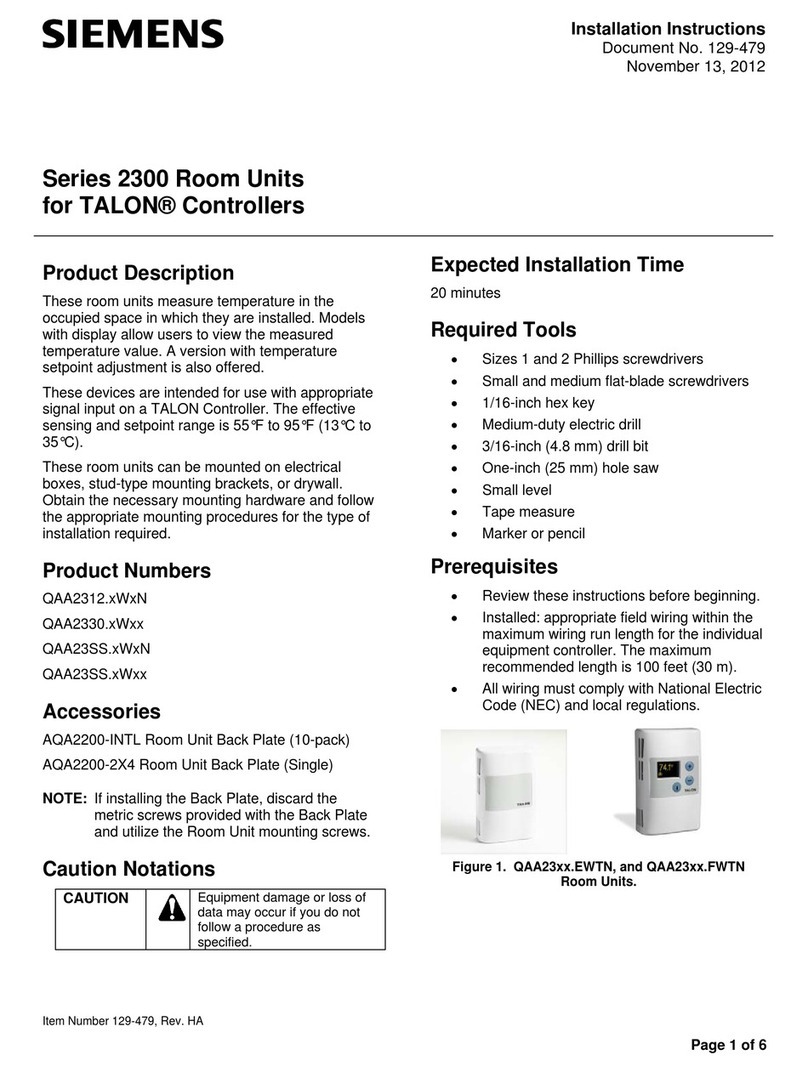
Siemens
Siemens Series 2300 installation instructions