FRONIUS RCU 2000 User manual

Operating
Instructions
RCU 2000
42,0410,0941 003-11012024
DE Bedienungsanleitung
EN Operating Instructions
FR Instructions de service
RCU 2000


Allgemeines
Gerätekonzept
RCU 2000
Fernbedienung RCU 2000
Die Fernbedienung RCU 2000
ermöglicht den Fernbetrieb einer
Stromquelle. Der Fernbetrieb kann
beispielsweise für Einrichtzwecke von
Stromquellen in Fertigungszellen die-
nen. Die Funktionen an der Fernbedie-
nung entsprechen dem Bedienpanel
der Stromquelle MagicWave
1700/2200.
Systemvoraus-
setzungen
Der Betrieb der Fernbedienung RCU 2000 ist in Verbindung mit folgenden
Stromquellen
-MagicWave 1700/2200
-MagicWave 2500/3000
-MagicWave 4000/5000
-TransTig 2200
-TransTig 2500/3000
-TransTig 4000/5000
-TransPocket 4000/5000
-TransSynergic 4000/5000
-TransPuls Synergic 2700/3200/4000/5000
WICHTIG! Wird die Stromquelle TransTig 2200 von der Fernbedienung RCU
2000 aus bedient, sind folgende Bedien- / Anzeigeelemente außer Funktion:
- Taste Verfahren
- Parameter Balance
WICHTIG! Sämtliche Bedien- und Anzeigeelemente für das HF-Zünden (Hoch-
frequenz-Zünden) sind außer Funktion wenn über die Fernbedienung RCU 2000
folgende Stromquellen bedient werden:
-TransPocket 4000/5000
-TransSynergic 4000/5000
-TransPuls Synergic 2700/3200/4000/5000
3
DE

Fernbedienung
anschliessen
Stecker des Fernbedienungskabels an der Anschluss LocalNet (A) anstecken
(A)
Vorderansicht MW/TT 1700/2200
(A)
Vorderansicht TPS 2700
(A)
Rückansicht TS/TPS 3200/4000/5000
(A)
Vorderansicht TPS 2700
Schlüsselschal-
ter
(B)(C)
WICHTIG! Bei Schlüsselschalter in
waagerechter Position (B) sind alle Tas-
ten am Bedienpanel gesperrt:
-Am Bedienpanel leuchtet das
Schlüssel-Symbol (C)
-Wird dennoch eine Taste gedrückt,
erscheint an den Anzeigen kurz die
Sperrmeldung „Clo|SEd“. Nur je-
ner Parameter, der zum Zeitpunkt
der Tastensperre angewählt war,
kann mittels Einstellrad geändert
werden.
4

Bedienpanel
Übersicht Wesentliches Merkmal des Bedienpanels ist die logische Anordnung der Bedien-
elemente. Alle für die tägliche Arbeit wesentlichen Parameter lassen sich einfach
-mit den Tasten anwählen
-mittels Einstellrad verändern
-während des Schweißens am Display anzeigen.
HINWEIS!
Aufgrund von Softwareupdates können Funktionen an Ihrem Gerät verfügbar
sein, die in dieser Bedienungsanleitung nicht beschrieben sind oder umgekehrt.
Zudem können sich einzelne Abbildungen geringfügig von den Bedienelemen-
ten an ihrem Gerät unterscheiden. Die Funktionsweise dieser Bedienelemente
ist jedoch identisch.
Nachfolgend dargestelltes Bild zeigt eine Übersicht der wesentlichen Einstellun-
gen für die tägliche Arbeit, am Beispiel des Bedienpanels MagicWave 1700/2200.
Eine ausführliche Beschreibung dieser Einstellungen befindet sich in dem nach-
folgenden Kapitel „Bedienpanel“.
4. Parameter ändern 1. Betriebsart anwählen:
Stabelektrode
Job-Betrieb
4-Takt Betrieb
2-Takt Betrieb
2. Verfahren anwählen:
(nur MagicWave 1700/2200)
DC+ Schweißen
(nur Stabelektrode)
DC- Schweißen
AC + Kalottenbildung
(nur WIG)
AC Schweißen
3. Parameter anwählen:
Startstrom I
S
Up-Slope t
up
Hauptstrom I
1
Down-Slope t
down
Endkraterstrom I
E
Balance (nur WIG-AC)
Elektroden-Durchmesser
Job-Nummer (nur Jobbetrieb)
5
DE

Bedienpanel
RCU 2000
Das Bedienpanel der Fernbedienung RCU 2000 entspricht dem Bedienpanel der
Stromquelle MW 1700/2200.
WARNUNG!
Gefahr durch Fehlbedienung und fehlerhaft durchgeführte Arbeiten.
Schwere Personen- und Sachschäden können die Folge sein.
▶Alle in diesem Dokument beschriebenen Arbeiten und Funktionen dürfen
nur von technisch geschultem Fachpersonal ausgeführt werden.
▶Dieses Dokument vollständig lesen und verstehen.
▶Sämtliche Sicherheitsvorschriften und Benutzerdokumentationen dieses
Gerätes und aller Systemkomponenten lesen und verstehen.
(6)(15) (12)(10) (11) (2)(3) (5)(4)
(1)(14)(9)(13)(8) (7)
(1) Taste Betriebsart
zur Anwahl der Betriebsart
(2) 2-Takt Betrieb
(3) 4-Takt Betrieb
(4) Job-Betrieb
(5) 2-Takt Betrieb
WICHTIG! Wird die Betriebsart Stabelektroden-Schweißen (5) an-
gewählt, steht die Schweißspannung erst nach einer Verzögerung von 3
Sekunden zur Verfügung.
6

(6) Taste Verfahren
zur Anwahl des Verfahrens, abhängig von der gewählten Betriebsart
Betriebsart 2-Takt Betrieb / 4-Takt Betrieb gewählt:
Verfahren:
WIG-DC- Schweißen
WIG-AC- Schweißen
WIG-AC Schweißen mit aktivierter Kalottenbildung
Bei gewählter Betriebsart Job-Betrieb (4) wird das für den aktuellen
Job gespeicherte Verfahren angezeigt.
Betriebsart Stabelektroden-Schweißen gewählt:
Verfahren:
Stabelektroden-DC+ Schweißen
Stabelektroden-DC- Schweißen
Stabelektroden-AC Schweißen
(7) Einstellrad
zum Ändern von Parametern. Leuchtet die Anzeige am Einstellrad,
kann der angewählte Parameter geändert werden.
(8) +
(9)
Tasten Parameteranwahl
zur Anwahl der Parameter. Ein Wechsel der Parameter mittels Tasten
Parameteranwahl (8) und (9) ist auch während des Schweißens möglich.
Parameter bei angewählter Betriebsart 2-Takt Betrieb (2):
Startstrom Is
0 bis 100 % vom Hauptstrom I1
Werkseinstellung: 35%
WICHTIG! Der Startstrom ISwird für die Betriebsarten WIG AC
Schweißen und WIG DC- Schweißen getrennt gespeichert.
Up-Slope tup
0,0 bis 9,9 s, Werkseinstellung: 0,1 s
WICHTIG! Der Up-Slope tup wird für die Betriebsarten 2-Takt Betrieb
und 4-Takt Betrieb getrennt gespeichert.
Hauptstrom I1
-MagicWave 1700: 3 bis 170 A
-MagicWave 2200: 3 bis 220 A
WICHTIG! Bei Schweißbrennern mit Up-/Down-Funktionalität kann
während des Geräte-Leerlaufes der volle Einstellbereich angewählt
werden. Während des Schweißvorganges ist eine Hauptstrom-Korrektur
von +/-20 A möglich.
Down-Slope tdown
0,0 bis 9,9 s, Werkseinstellung: 1 s
WICHTIG! Der Down-Slope tdown wird für die Betriebsarten 2-Takt Be-
trieb und 4-Takt Betrieb getrennt gespeichert.
7
DE

Endkrater-Strom IE
0 bis 100 % vom Hauptstrom,
Werkseinstellung: 30 %
Balance (nur WIG-AC)
-5 / +5, Werkseinstellung: 0
-5 höchste Aufschmelzleistung,
geringste Reinigungswirkung
+5 höchste Reinigungswirkung,
geringste Aufschmelzleistung
Elektroden-Durchmesser
0 bis 4,0 mm (0.158 in.)
Werkseinstellung: 2,4 mm (0.095 in.)
Parameter bei angewählter Betriebsart 4-Takt Betrieb (3):
Startstrom Is
0 bis 100 % vom Hauptstrom I1
Werkseinstellung: 35%
WICHTIG! Der Startstrom ISwird für die Betriebsarten WIG AC
Schweißen und WIG DC- Schweißen getrennt gespeichert.
Up-Slope tup
0,0 bis 9,9 s, Werkseinstellung: 0,1 s
WICHTIG! Der Up-Slope tup wird für die Betriebsarten 2-Takt Betrieb
und 4-Takt Betrieb getrennt gespeichert.
Hauptstrom I1
-MagicWave 1700: 3 bis 170 A
-MagicWave 2200: 3 bis 220 A
WICHTIG! Bei Schweißbrennern mit Up-/Down-Funktionalität kann
während des Geräte-Leerlaufes der volle Einstellbereich angewählt
werden. Während des Schweißvorganges ist eine Hauptstrom-Korrektur
von +/-20 A möglich.
Absenkstrom I2
0 bis 100 % vom Hauptstrom I1
Werkseinstellung: 50%
Down-Slope tdown
0,0 bis 9,9 s, Werkseinstellung: 1 s
WICHTIG! Der Down-Slope tdown wird für die Betriebsarten 2-Takt Be-
trieb und 4-Takt Betrieb getrennt gespeichert.
Endkrater-Strom IE
0 bis 100 % vom Hauptstrom,
Werkseinstellung: 30 %
Balance (nur WIG-AC)
-5 / +5, Werkseinstellung: 0
-5 höchste Aufschmelzleistung,
geringste Reinigungswirkung
+5 höchste Reinigungswirkung,
geringste Aufschmelzleistung
Elektroden-Durchmesser
0 bis 4,0 mm (0.158 in.)
Werkseinstellung: 2,4 mm (0.095 in.)
8

Parameter bei angewählter Betriebsart Job-Betrieb (4):
Im Job-Betrieb stehen die Parameter zur Verfügung, welche für die im
angewählten Job gespeicherte Betriebsart gelten. Zusätzlich ist folgen-
der Parameter verfügbar:
Job-Nummer
zur Anwahl des gewünschten Jobs
Parameter bei angewählter Betriebsart Stabelektroden-Schweißen (5):
Hauptstrom I1
-MagicWave 1700: 10 bis 140 A
-MagicWave 2200: 10 bis 180 A
WICHTIG! Bei Schweißbrennern mit Up-/Down-Funktionalität kann
während des Geräte-Leerlaufes der volle Einstellbereich angewählt
werden. Während des Schweißvorganges ist eine Hauptstrom-Korrektur
von +/-20 A möglich.
(10) Anzeige Schweißstrom
zur Anzeige des Schweißstromes für die Parameter
-Startstrom IS
-Hauptstrom I1
-Absenkstrom I2
-Endkraterstrom IE
Vor Schweißbeginn zeigt die linke Anzeige den Sollwert. Für IS, I2 und
IEzeigt das rechte Display zusätzlich den %-Anteil vom Hauptstrom I1.
Nach Schweißbeginn wird der Parameter I1automatisch angewählt. Das
linke Display zeigt den aktuellen Ist-Wert des Schweißstromes.
Das Bedienpanel verdeutlicht die entsprechende Position im
Schweißprozess mittels dunkel leuchtenden Anzeigen der Parameter
(IS, tup, ...).
WICHTIG! Ist der Parameter ACS (Kapitel „Das Setup-Menü: Ebene 2“)
auf OFF gestellt, bleibt während des Schweißens der zuletzt gewählte
Parameter angewählt. Es erfolgt keine automatische Anwahl des Para-
meters I1.
(11) Anzeige Schweißspannung
zur Anzeige des aktuellen Ist-Wertes der Schweißspannung an der
rechten Anzeige.
Vor dem Schweißen zeigt die rechte Anzeige bei angewählten Betriebs-
arten für das WIG-Schweißen „0.0“. Bei angewählter Betriebsart
„Stabelektroden-Schweißen“ wird nach einer Verzögerung von 3 Sekun-
den der Wert für die Leerlaufspannung „50V“ angezeigt.
WICHTIG! Die Anzeige „50 V“ bei angewähltem Verfahren „Stabelek-
troden-Schweißen“ bedeutet den Mittelwert der gepulsten Leerlauf-
spannung.
9
DE

(12) Anzeige HOLD
bei jedem Schweißende werden die aktuellen Ist-Werte von
Schweißstrom und -spannung gespeichert - die Hold-Anzeige leuchtet.
Die Hold-Anzeige bezieht sich auf den zuletzt erreichten Hauptstrom
I1. Werden andere Parameter angewählt, erlischt die Hold Anzeige. Die
Hold-Werte stehen jedoch bei erneuter Anwahl des Parameters I1wei-
terhin zur Verfügung.
Die Hold-Anzeige wird gelöscht durch
-Erneuten Schweißstart
-Einstellung des Hauptstromes I1
-Wechsel der Betriebsart
-Wechsel des Verfahrens
WICHTIG! Wurde die Hauptstromphase nie erreicht oder eine Fuß-
Fernbedienung verwendet, werden keine Hold-Werte ausgegeben.
(13) Taste Store
für das Speichern von Jobs. Dient auch zum Einstieg in das Setup-
Menü.
(14) Taste Gasprüfen
zum Einstellen der benötigten Schutzgasmenge am Druckminderer.
Nach Drücken der Taste Gasprüfen strömt für 30 s Schutzgas aus.
Durch erneutes Drücken wird der Vorgang vorzeitig beendet.
(15) Anzeige Übertemperatur
leuchtet auf, wenn sich die Stromquelle zu stark erwärmt (z.B. infolge
überschrittener Einschaltdauer). Weiterführende Informationen finden
Sie im Kapitel „Fehlerdiagnose- und Behebung“.
(38) (39) (40) (41) (42)
(43)(44)
Zusätzliche Anzeigen
Die dargestellten Anzeigen leuchten, so-
lange bestimmte Funktionen aktiviert sind.
Nachfolgende Beschreibung gibt Ihnen ei-
nen Überblick über diese Funktionen. Teil-
weise erfolgt eine noch genauere Be-
schreibung bei der Detailbehandlung der
jeweiligen Funktion / des entsprechenden
Parameters in den Kapiteln
-Das Setup-Menü: Ebene 1
-Das Setup-Menü: Ebene 2
-Sonderfunktionen
(38) Pulsen ist aktiviert
Setup-Parameter „F-P“ wurde auf eine Pulsfrequenz eingestellt
(39) Punktieren ist aktiviert
Setup-Parameter „SPt“ wurde auf eine Punktierzeit eingestellt
(40) Heften ist aktiviert
Setup-Parameter „tAC“ wurde auf eine Zeitdauer eingestellt
10

(41) Anzeige „Elektrode überlastet“
leuchtet bei einer Überbelastung der Kalotte an der Wolframnadel. Es
besteht die Gefahr des Ausbildens einer übergroßen Kalotte.
Ursache
-Wolfram-Elektrode mit zu geringem Durchmesser
-Hauptstrom I1auf einen zu hohen Wert eingestellt
-Balance zu weit in Richtung „+“ eingestellt
Abhilfe
-Wolfram-Elektrode mit größerem Durchmesser verwenden
-Den Hauptstrom reduzieren und/oder die Balance weiter in Rich-
tung „-“ einstellen
WICHTIG! Die Anzeige „Elektrode überlastet“ (41) ist exakt auf folgen-
de Wolfram-Elektroden abgestimmt:
-WIG-AC Schweißen: Reinwolfram-Elektroden
-WIG-DC Schweißen: Cerierte Elektroden
Für alle anderen Elektroden gilt die Anzeige „Elektrode überlastet“ (41)
als Richtwert
(42) Anzeige „Tastensperre aktiviert“
leuchtet bei aktivierter Tastensperre, gemäß Kapitel „Sonderfunktio-
nen“
(43) Kaltdraht-Vorschub ist angeschlossen
leuchtet bei angeschlossenem Kaltdraht-Vorschub
(44) HF-Zünden (Hochfrequenz-Zünden) ist aktiviert
Setup-Parameter „HFt“ wurde auf ein Intervall für die Hochfrequenz-
Impulse eingestellt
11
DE

General
Product concept
RCU 2000
RCU 2000 remote control unit
The RCU 2000 remote control unit al-
lows you to remote-operate a power
source which is located e.g. inside a
production cell - for set-up purposes,
for example. The functions available on
the remote control unit correspond to
those on the control panel of the Ma-
gicWave 1700/ 2200 power source.
System require-
ments
The RCU 2000 remote control unit can be operated in conjunction with the fol-
lowing power sources:
-MagicWave 1700/2200
-MagicWave 2500/3000
-MagicWave 4000/5000
-TransTig 2200
-TransTig 2500/3000
-TransTig 4000/5000
-TransPocket 4000/5000
-TransSynergic 4000/5000
-TransPuls Synergic 2700/3200/4000/5000
IMPORTANT! If the TransTig 2200 power source is operated by the RCU 2000
remote control unit, the following buttons and indicators will be disabled:
- “Process” button
- “Balance” parameter
IMPORTANT! All controls and display elements for HF ignition (high-frequency
ignition) are disabled, when one of the following power sources is controlled
using the RCU 2000 remote control unit.
-TransPocket 4000/5000
-TransSynergic 4000/5000
-TransPuls Synergic 2700/3200/4000/5000
12

Connecting up
the remote con-
trol unit
Insert the plug at the end of the remote-control cable into the LocalNet connec-
tion socket (A).
(A)
Front view MW/TT 1700/2200
(A)
Front view TPS 2700
(A)
Rear view TS/TPS 3200/4000/5000
(A)
Front view TP 4000/5000
Keylock switch
(B)(C)
IMPORTANT! When the keylock switch
is in the horizontal position (B), all the
buttons on the control panel are disab-
led:
-The “key” symbol (C) is lit up on
the control panel
-If you still press any of the but-
tons, the disabled message “Clo|
SEd” will briefly appear on the dis-
plays. The only parameter that it is
possible to alter (with the adjus-
ting dial) is the one that was alrea-
dy selected at the time the keylock
was activated.
13
EN

Control panel
Overview The key feature of the control panel is the logical way in which the controls are
arranged. All the main parameters needed for day-to-day working can easily be
-selected with the buttons
-altered with the adjusting dial
-shown on the display during welding.
NOTE!
Owing to software updates, you may find that your machine has certain func-
tions that are not described in these Operating Instructions, or vice-versa. Also,
certain illustrations may be very slightly different from the actual controls on
your machine. However, these controls function in exactly the same way.
The illustration below shows an overview of the main settings needed for day-to-
day working, based on the example of the MagicWave 1700/2200 control panel.
You will find a detailed description of these settings in the following section
(“Control panel”).
4. Alter the parameter 1. Select the operating mode:
Rod electrode (MMA)
Job mode
4-step mode
2-step mode
2. Choose which process:
(only on MagicWave 1700/2200)
DC+ welding
(only with rod electrode)
DC- welding
AC + cap-shaping
(only with TIG)
AC welding
3. Select the parameter:
Starting current I
S
Upslope t
up
Main current I
1
Downslope t
down
Final current I
E
Balance (only with TIG-AC)
Electrode diameter
Job number (only in Job Mode)
14

RCU 2000 con-
trol panel
The RCU 2000 control panel correspond to the control panel of the MagicWave
1700/2200 power source.
(6)(15) (12)(10) (11) (2)(3) (5)(4)
(1)(14)(9)(13)(8) (7)
(1) Mode button
for selecting the operating mode
(2) 2-step mode
(3) 4-step mode
(4) Job mode
(5) Rod electrode (MMA) welding
IMPORTANT! If you select the “Rod electrode (MMA) welding” mode
(5), the welding voltage will only be available after a 3-second time-lag.
(6) Process button
for selecting the process, depending upon which operating mode has
been selected
If 2-step / 4-step mode has been selected
Process:
TIG-DC- welding
WTIG-AC- welding
TIG-AC welding with activated cap-shaping function
15
EN

If “Job mode” (4) has been selected, the display shows the process that
was saved for the current job.
If “Rod electrode (MMA) welding mode” (5) has been selected:
Process:
Rod electrode DC+ welding
Rod electrode DC- welding
Rod electrode AC welding
(7) Adjusting dial
for altering parameters. If the indicator is lit up on the adjusting dial,
then the selected parameter can be altered.
(8) +
(9)
Parameter selection buttons
for selecting the parameters It is also possible to change parameters by
means of the parameter selection buttons (8) and (9) while the welding
operation is in progress.
Available parameters where 2-step mode (2) has been selected:
Starting current Is
0 to 100 % of main current I1
Factory setting:35%
IMPORTANT! The starting current ISis saved separately for the “TIG-
AC welding” and “TIG DC- welding” operating modes
Up-Slope tup
0.0 to 9.9 s, factory setting: 0.1 s
IMPORTANT! The upslope tup is saved separately for the 2-step and 4-
step operating modes.
Main current I1
-MagicWave 1700: 3 to 170 A
-MagicWave 2200: 3 to 220 A
IMPORTANT! On welding torches with Up/Down functionality, the enti-
re setting range is available for selection while the machine is idling. Du-
ring welding, the main current can be corrected by +/-20 A.
Downslope tdown
0.0 to 9.9 s, factory setting: 1 s
IMPORTANT! The downslope tdown is saved separately for the 2-step
and 4-step operating modes.
Final current IE
0 to 100 % of main current
Factory setting: 30 %
Balance (only with TIG-AC)
-5 / +5, factory setting: 0
-5 highest fusing power,
lowest cleaning action
+5 highest cleaning action,
lowest fusing power
16

Electrode diameter
0 to 4.0 mm (0.158 in.),
Factory setting: 2,4 mm (0.095 in.)
Available parameters where 4-step mode (3) has been selected:
Starting current Is
0 to 100 % of main current I1
Factory setting: 35%
IMPORTANT! The starting current IS is saved separately for the “TIG-
AC welding” and “TIG DC- welding” operating modes.
Upslope tup
0.0 to 9.9 s, factory setting: 0.1 s
IMPORTANT! The upslope tup is saved separately for the 2-step and 4-
step operating modes.
Main current I1
-MagicWave 1700: 3 to 170 A
-MagicWave 2200: 3 to 220 A
IMPORTANT! On welding torches with Up/Down functionality, the enti-
re setting range is available for selection while the machine is idling. Du-
ring welding, the main current can be corrected by +/-20 A.
Reduced current I2
0 to 100 % of main current I1
Factory setting: 50%
Downslope tdown
0.0 to 9.9 s, factory setting: 1 s
WICHTIG! The downslope tdown is saved separately for the 2-step and
4-step operating modes.
Final current IE
0 to 100 % of main current
Factory setting: 30 %
Balance (only with TIG-AC)
-5 / +5, factory setting: 0
-5 highest fusing power, lowest cleaning action
+5 highest cleaning action, lowest fusing power
Electrode diameter
0 to 4.0 mm, (0.158 in.)
Factory setting: 2.4 mm (0.095 in.)
Available parameters where “Job mode” (4) has been selected:
In “Job mode”, the parameters that apply to the operating mode that
has been stored in the selected job are made available. In addition, the
following parameter is also available:
Job number
for selecting the desired job
Available parameters where the “Rod electrode (MMA) welding” mode
(5) has been selected:
17
EN

Main current I1
-MagicWave 1700: 10 to 140 A
-MagicWave 2200: 10 to 180 A
IMPORTANT! On welding torches with Up/Down functionality, the enti-
re setting range is available for selection while the machine is idling. Du-
ring welding, the main current can be corrected by +/-20 A.
(10) Welding current display
for indicating the welding current for the parameters:
-IS (starting current)
-I1(main current)
-I2(reduced current)
-IE(final current)
Before the start of welding, the left-hand display shows the command
value. For IS, I2 and IEthe right-hand display also shows the respective
%-age of the main current I1.
After the start of welding, the parameter I1is automatically selected.
The left-hand display shows the present actual value of the welding cur-
rent.
The control panel indicates which position has been reached in the wel-
ding process by means of a dimmed display of the parameters (IS,
tup, ...).
IMPORTANT! If the parameter ACS (see the section headed “Set-up
menu: Level 2”) is set to OFF, then the most recently selected parame-
ter remains active during welding. No automatic selection of parameter
I1takes place.
(11) Welding voltage display
for indicating the actual welding-voltage value on the right-hand display.
Where one of the TIG-welding modes has been selected, the right-hand
display reads “0.0” before the start of welding. Where the “Rod electro-
de (MMA) welding” mode has been selected, there is first a 3-second
time-lag, after which the value for the open-circuit voltage “50V” is dis-
played.
IMPORTANT! The value of “50 V” indicated where the “Rod electrode
(MMA)” process has been selected refers to the mean value of the pul-
sed open-circuit voltage.
18

(12) HOLD indicator
every time you finish a welding operation, the actual values for welding
current and voltage are stored, and the “Hold” indicator lights up.
The “Hold” indicator refers to the last value reached by the Main cur-
rent I1. As soon as any other parameter is selected, the “Hold” indicator
goes out. The “Hold” values will continue to be available, however, if Pa-
rameter I1is selected once again.
The “Hold” indicator is cancelled whenever
-a new welding operation is started
-the Main current I1is adjusted
-the operating mode is changed
-the process is changed
IMPORTANT! If the main-current phase was never reached, or if a pe-
dal remotecontrol unit was being used, no “Hold” values are outputted.
(13) Store button
for storing jobs. Is also used for accessing the Set-up menu.
(14) Gas-test button
for setting the required gas-flow rate on the pressure regulator. After
you press this button, gas will flow out for 30 s. Press the button again
to stop the gas test-flow before the 30 seconds are up.
(15) Overtemperature indicator
lights up if the power source overheats (e.g. because the duty cycle has
been exceeded). For more information on this, see the “Troubleshoo-
ting” section.
(38) (39) (40) (41) (42)
(43)(44)
Additional indicators
The indicators shown glow for as long as
the respective functions remain activated.
The following description will give you an
overview of these functions. In some ca-
ses, they will be described in even greater
detail in the in-depth sections dealing with
the function or parameter in question, to
be found in:
-The set-up menu: Level 1
-The set-up menu: Level 2
-Special functions
(38) Pulsing is activated
Set-up parameter “F-P” has been set to a certain pulsing frequency
(39) Spot welding is activated
Set-up parameter “SPt” has been set to a certain spot-welding time
(40) Tacking is activated
Set-up parameter “tAC” has been set to a certain duration
19
EN

(41) “Electrode overload“ indicator“
lights up when the cap at the tip of the tungsten electrode is overloa-
ded. This means that there is a risk of an excessively large cap being for-
med.
Causes
-The tungsten electrode does not have a large enough diameter
-Main current I1has been set to too high a value
-“Balance” has been set too far towards “+”
Remedies
-Use a tungsten electrode with a bigger diameter
-Reduce the main current and/or set “Balance” further towards “-”
IMPORTANT! The “Electrode overload“ indicator (41) is fine-tuned to
work with the following tungsten electrodes:
-TIG-AC welding: Pure tungsten electrodes
-TIG-DC welding: Ceriated electrodes
For all other electrodes, the “Electrode overload” indicator (41) must
be taken as a guideline only
(42) “Keylock activated” indicator
lights up when the keylock is activated, as described in the section hea-
ded “Special functions”
(43) Cold-wire feeder is connect
This indicator lights up when a cold-wire feeder is connected
(44) HF (high-frequency) ignition is activated
Set-up parameter “HFt” has been set to a certain interval for the high-
frequency impulses
20
Other manuals for RCU 2000
1
Table of contents
Languages:
Other FRONIUS Controllers manuals
Popular Controllers manuals by other brands
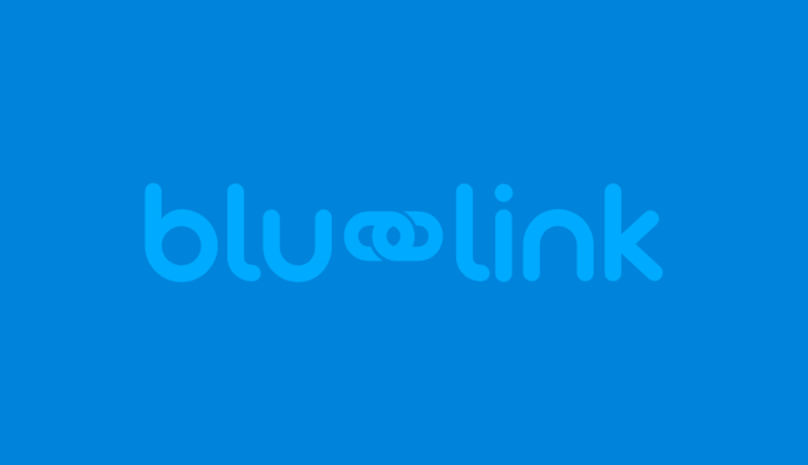
Gate
Gate Blu-Link BLU-L quick start
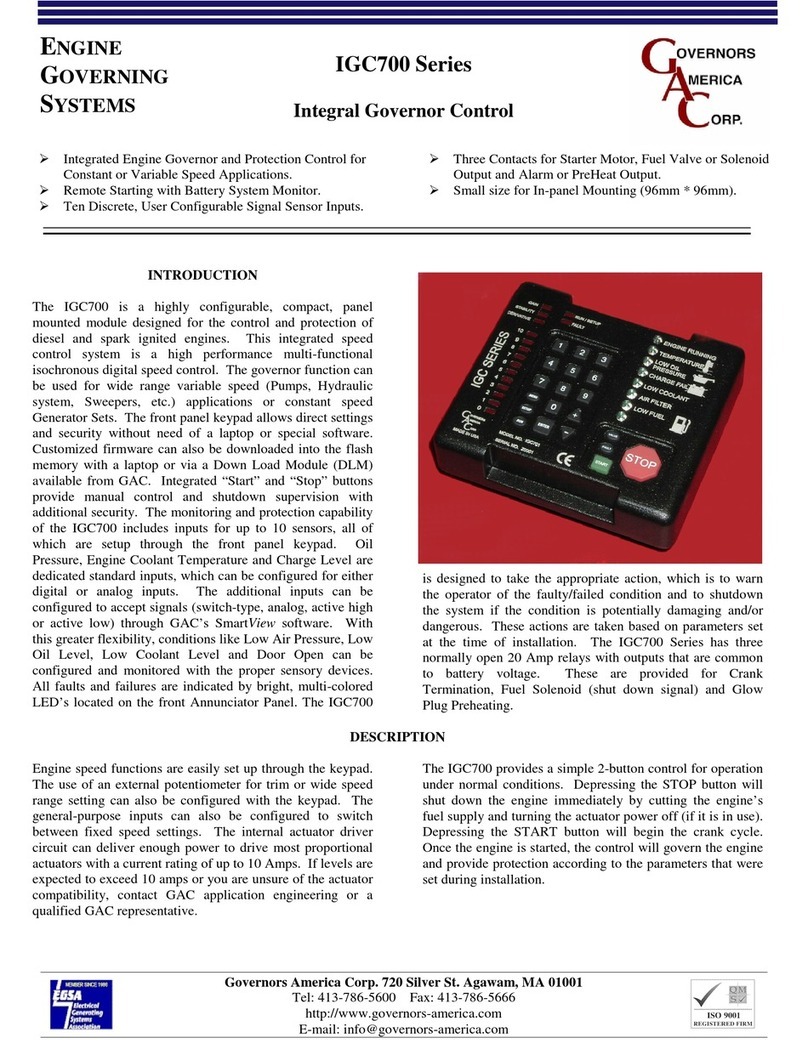
GAC
GAC IGC700 Series manual

MAGUIRE
MAGUIRE Weigh Scale Blender 4088 Installation operation & maintenance
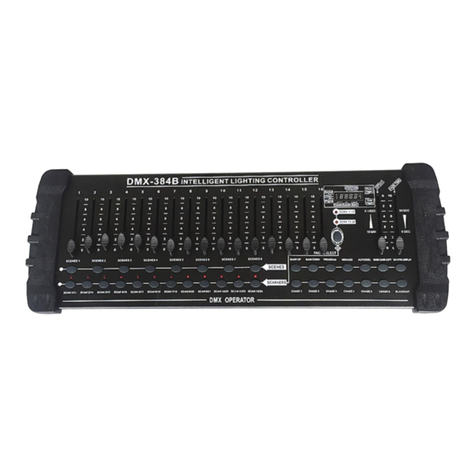
QTX Light
QTX Light DMX 512 Series user manual
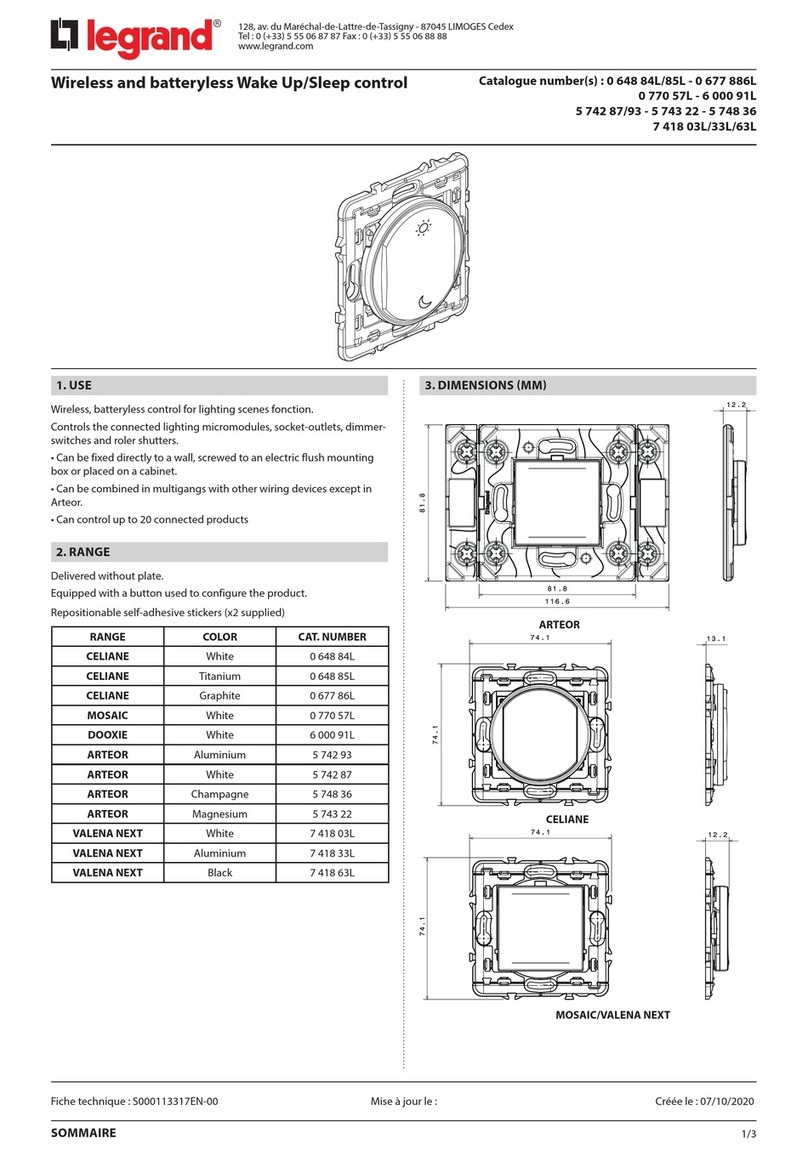
LEGRAND
LEGRAND 0 677 886L quick start guide

Siemens
Siemens RAJA+ 3TE7131-1HC14-1A Installation, Maintenance & Troubleshooting Guide