FUTABA ATTACK-4 User manual

Futaba
DIGITAL PROPORTIONAL
RADIO CONTROL
AM
Thank you for purchasing a Futaba digital proportional radio control set.
Please read this manual carefully before using your set.
FEATURES OFFP-4NBL
The FP-4NBL is a 4 channel AM proportional radio control
set
with
an
ergonomic
case
created
as
a
result of the exhaustive
pursuit of easier operation, newly designed sticks for smooth
and positive operation, servo reversing switch for each chan-
nel, and other innovations based on the opinions and needs of
many RC modelers.
Please read this manual before using your new set.
TRANSMITTER FP-T4NBL______________
•Servo reversingswitch foreach channel.Servos are reversed
byusing thisswitch.
•Newly designed sticks operate smoothlyandpositively.
Spring tension mechanismallowsadjustment of the operat-
ingfeelof the sticklever.
•Nonslip adjustablelever headallows adjustment of the stick
lengthasdesired.
•Functionalcase, createdas a result of theexhaustivepursuit
of easieroperation,hasevolved a thick case which fitsinto
the palm of the hand.
•Easy to read transmitterbattery voltage/output level meter.
•Neck strapbracket providedas standard. Operationiseasier
ifthe transmitteris hungfromyour neck byusing the neck
strap.
•Nicad operation as standard.
RECEIVERFP-R114H
•HighperformanceAM 4 channel receiver inwhich miniature
sizeand light weighthavebeen achievedby using thePC
board spaceto the maximum.
•Narrowband ceramicfilterimproves rejection of adjacent
channel interference.
FEATURES OF MCR-4A RECEIVER
•Narrow band design using a narrow bandceramic filter.
FEATURESOF MCR-4A AMP
•Built-inheat protectorpreventsoverheating ofthe amplifier
bya continuous overcurrent.
•Motor idle or maximum slow can bearbitrarilyset atthe
transmitterthrottlestick maximum slow position by built-in
idle point trimmer.
SERVO FP-S148 RUGGED, LOW-PROFILESERVO
•Vibration andshock resistance have been improved further
byusing a directwiringsystemwhich directlyconnects the
servoamp, motor and potentiometer.
•
The height of the
servo
has
been
reducedand
high
torque,
high speed, and smooth movement equal to thatof the core-
less servo have been realizedbyusing a new small, high-
performancemotor. (Output torque 3kg.cm,operating
speed 0.22 sec/60°).
SERVO FP-S133HIGH-QUALITY MICROSERVO_
•Futaba hybridcustom 1Cprovideshigh startingoutput
torque, narrowdead-band, and excellenttrackability.
•Thick filmgoldplatedconnector pinsinsurepositivecontact
connectorshapeincreasereliabilityagainstshock and vibra-
tion.The connector housing has a reverse insertion preven-
tionmechanism.
•Adjustable(splined)horn permits arbitrarysetting ofthe
neutral position.
•Despite being a microservo, operating speed is a fast 0.21
sec/ 60°and output torque isa high2.2 kg/cm.
SET CONTENTS AND RATINGS
(Specificationsare subjecttochange withoutprior notice.)
RECEIVERWITHLINEARCONTROLLERMCR-4A
•FET amplifierwith miniaturelightweight AM 4-channel re-
ceiverand motor controllerinone pack.
•Since the drivemotor power supply (7.2V NiCd battery
pack,etc.)can alsobeused to power the receiverand servos,
troublesome wiring isunnecessary and the model can be
made lighter.
•Built-inhigh performance low voltage "autocut" circuit pre-
ventsloss of control dueto power supply voltage drop
during flight.
•Since the motor speed can becontrolledsteplesslyfrom
maximum alowto high, acrobaticsequal to those of engine
aircraftcan bereproducedevenwitha motoraircraft.
Transmitter
Receiver
Servo
Charger
Nicad Battery
Switch
Accessories
FP-4NBL
For engine
powered plane
FP-T4NBL x 1
FP-R114H x 1
FP-S148 x 3
FBC-8B(4) x 1
NR-4QBx1| NR-4Kx1
SSW-J x 1
Servo tray ——
Extension cord. Neck strap. Frequency flag,
Spare horn. Screws
For glider
FP-S133x2
For electric
powered plane
MCR-4A x 1
—

TRANSMITTER FP-T4NBL
Operating system : 2 stick,all channels
servoreverse
Transmittingfrequency : 72 MHz bands
Modulation system: AM
(amplitude modulation)
Power requirement : 9.6V 500 mAHNicad
Battery
Current drain: 150mA
RECEIVER
FP-R114H___________
Receivingfrequency: 72 MHz bands
Crystalreplacementsystem:Frequencycan be
Intermediate frequency455 kHz
Power requirement 4.8V Nicd Battery
(sharedwithservo)
Currentdrain 18mA (at4.8 V)
Dimensions1.3x1.87x0.78 in
(33x47.4x19.8mm)
Weight 0.95 oz (27.5 g)
Receiving range500monthe ground
SERVOFP-S148
Control system
Operatingangle
Power requirement
Currentdrain
Output torque
Operatingspeed
Dimensions
Weight
+putse width control
1520 us neutral
One side45° or more
4.8V-6V
6.0V,12mA (at idle)
42 oz-in(3kg.cm)
0.22 sec/60°
1.59x0.77x1.4 in
(40.4x19.8x36mm)
1.5oz
(44.4
g)
changed withinthe
same frequencyband
by changingthe pre-
cisioncrystal.
1000mintheair
withthe FP-T4NBL
(under best conditions)
RECEIVERWITH LINEAR CONTROLLER MCR-4A
Dimensions
Weight
RECEIVER
Receivingfrequency
Intermediatefrequency
Current drain
Receiving range
AMP
Operating system
Voltage
Continuousmaximumcurrent
Momentary maximum current
Resistance loss
1.24x2.92x0.63 in (31.6x74.2x16.1mm)
(excludingprotrusionat top)
1.5oz (44.0 g) (excludingswitches and
connectors)
72 MHz bands
455
kHz
26mA
500mon theground 1000mintheair
with the FP-T4NBL
(under best conditions)
:idle tomaximum speed, no brake, idle
pointtrimmer
:
6.0
to
8.4
V
:
100
A
:
450
A
:0.01ohm
SERVO FPS133
Controlsystem
Operatingangle
Power supply
Power consumption
Outputtorque
Operatingspeed
Dimensions
Weight
+pulse width control1520usneutral
One side 40°orgreater(includingtrim)
trim)
4.8V
or
6.0V
(shared
with
receiver)
6.0V, 8mA (atidle)
30.6 oz/in(2.2kg.cm)
0.21 sec/60°
1.10 x 051x 1.14in(28 x 13x29mm)
0.67
oz
(19g)
Antenna
Fig.
2
Neckstrap bracket
Elevator trim lever
Power switch
Ailerontrimlever
Transmitter
crystal
Servo
reversing
switches
Battery cover
Nonslip adjustable
leverhead
TRANSMITTER FP-T4NBL
CONTROLS
Fig.1 and Fig.2 show the name
of each part ofthe transmitter.
Memorize the position and oper-
ation of each switch andcontrol.
Level meter
Throttle
trim
lever
Handle
Rudder trim lever
Throttle
MODE II
Aileron
Elevator
Fig.1
Charging
jack
Rudder
Inthe following descriptions, alltheservo reversing switches
are assumed to beinthe normal position. When they are inthe
reverse position, operation isthe opposite ofthat described.
Rudder Rudder operation
Aileron trim lever Ailerontrimmer
Elevator trim leverElevatortrimmer
Throttle trim lever Throttletrimmer
Rudder trim lever Rudder trimmer
Power switch ON inthe upposition
Level meter
Elevatorand Engine throttle
are opposite those showninthe
fiqureinMode-l.
MODEI
•This meter indicatesthetransmitterbatteryvoltage.
•When the antenna isextendedfullyand the power switchis
set to ON, the pointer should deflecttothe silverzone.
Aileron Aileronoperation
Elevator Elevatoroperation
Throttle Throttleoperation

Neck strap bracket
Bracketforneck strap. (Neck strap issold separately.)
Antenna
Strong
telescoping
antenna. Extend
it
to
its
full
length
when using the transmitter.
Handle
Use thisbarto carrythe transmitter.
Nonslipadjustable lever head
Thelengthof the lever head can beadjusted to suit the
operator.
inthe arrow direction,and adjust the head to
the most comfortablelength, then lock it by
turning it inthe direction opposite the arrows. Fig.3
and
,byturning them
Lever head
Leverhead
Unlock lever heads
Charging jack
Use thisjackforcharging.
Transmitter crystal
Batterycover
18Servo reversingswitches
Using the servoreversingswitches
•The left sideofeach switchis the normal position.
•The servoreversingswitchesreversethe direction of opera-
tion of the servos.
Adjust to the lengthof your hand.
Charging of transmitter and receiver Nicad batteries
Recharge the receiver and transmitterNicad batteries as
shown inFig.4.
Fig.
5
Aileron servo
reversing switch
NORM-> Normal
REV->Reverse
Afterlinkage iscomplete, inspect theservos. Ifthe direction of
operationof thestickleverand the directionof operationof a
servoare opposite, switchthe appropriate servoreversing switch.
Rudder servo
reversingswitch
Throttleservo
reversing switch
Elevator servo
reversing switch
•Connect the charging plug of the dual charger to the trans-
mitter charging jack.Connect the Rx-connectorofthe dual
charger to the receiverNicad batteryplug, and AC-plugthe
dual chargerto AC-outtetsocketas shown inthe figure.
•The receiverbatterycan beused about 10times at10min-
utesperflightbetweenrechargings.
•Charge the batteries forabout 15 hours.When the set is not
inuse forsome time,repeat discharge and chargetwoto
threetimesbeforeuse. (Ifthe batteriesarenot used fora
long time,theircapacitywillgo down).
•The dual charger transmitterand receiver Nicad batteries
independently or simultaneously.
Notes
1)First connect thecharger tothe transmittercharge jack.
The LED on the chargerwillglow RED.
2) Next connect to the receiverswitchharnesscharge cord.
TheLEDwillchangetoGREENISH-RED(ORANGE).
3) Inthe casewhereonly one battery pack is connected, the
LED color willbe:
TXonly:GREEN
RXonly:RED
NicadBattery
Connector
Caution
Donotpullthe Nicadbattery
connector when the backcover
isremoved. The power switch
maybedamagedifthe battery
connector isstrongly pulled.
Usea small Phillips
screwdriver
Charger PBC-8B
LED
Chargingplug
fortransmitter.
AC-plug.
Rx
Tx
Transmitter
Nicad battery
NT-8JY
Battery cover
NR-4QB
Fig.
4
Elevator
Aileron
Rudder
Thetensionof thestick lever spring can beadjusted.
When these screws are
removed, the back cover
canberemoved.
•Thetensionof the
spring can bead-
justedby removing
the transmitterback
coverand turning
the screwforeach
stick.Set the springs
for the beststickfeel.
Fig.
6

RECEIVER FP-R114H, SERVO FP-S1480R FP-S133(IN CASE OFENGINEPOWERED PLANE ORGLIDER)
RECEIVER WITH LINEAR CONTROLLER MCR-4A,SERVO FP-S133(INCASE OF ELECTRIC POWERED PLANE)
Receiver, servos, switches, and
battery holder connections
SSW-J
Power switch
Chargingplug
Incaseof glider
Aileron
servo
Elevator
servo
Extension
cord
Three servos are
suppliedasstand-
ard. (In caseof
glider,two servos
aresuppliedas
standard.)
Incase of engine
powered plane
Antenna wire
Theparts en-
closed by the
dotted lines must
bepurchased
separately.
Rudder
servo
Throttle
servo
Pay carefulattentionto thepolarity
oftheconnector.
Fig.
7
MCR-4A, servo, andbattery connection
Idle point trimmer
Power switch
Motor terminal
Antenna wire
Receiver crystal
•TheMCR-4A cancontrol 280class to 540class motors.
•6V(5batteries),7.2 V (6 batteries),or 8.4 V (7batteries)NiCd
batterypack can beused withthe MCR-4A.(Whenusing a 540
class,etc.motor,purchase an NiCd batterypack connectoroffthe
market. Besure thatthe (+)and (—)polaritiesarecorrect.If the
(+) and(—)connections are reversed, the MCR-4A may bedam-
aged beyond repair.)
Aileron servo (CH1)
Elevator servo (CH2)
Rudder servo (CH4)
Extension cord
Start switch NiCd
battery pack
The parts inside the dotted
lines are notincluded.
Alwaysusea noisekiller
capacitor on the electricmotor.
Drive motor
Fig.
8
The
idle
point
trimmer
sets
the
drive
motor
idling
point.
•Set the transmitterthrottle
servoreversingswitchto the
normal position.
•Setthe transmit throttle
stickto the slowest position
(stickallthe way back ),
turn on the MCR-4Apower
switch, pressthe startswitch,
and setthe idle point trim-
mer to the pointatwhich
the motor idles.
•Ifthe startswitch is not
pressed, the drive motor will
not
run.
•Turn the idlepointtrimmerslowly andwithouttoomuch
force.
•Ifthe drivemotor rotates inthe reverse direction, change
the connection ofthe lead wirefromthe MCR-4Aat the
motor terminals.
•Before pressing the MCR-4A start switch, check that the
transmitterthrottlestickis in the slowestposition. Starting
the drivemotor suddenly is dangerous. This also applies
when the idle point trimmeris changed. Be verycareful.
•Ifan overcurrentflowscontinuously in the motor forsome
reason, the heat protector willoperateand stop the motor.
When the temperaturedrops aftera short time, the motor
can becontrolledonce more.
Correct the cause of the continuous overcurrent before using
the
set.
•The heat protectordoes not protect the set againstmomen-
taryovercurrentcaused byshorting of the drive motor lead
wires,etc.
•Ifthe drivemotor is stopped bythe "autocut" function dur-
ing flight, land the aircraftimmediately and safely.

PRECAUTIONS
•Connect the receiver(orMCR-4A),servos, switches, and
battery firmlyas shown inFig. 7 (Fig. 8). Then extend the
transmitterand receiver antennas fully.
•Setthe transmitterpower switch toON. Then setthe receiv-
er(orMCR-4A)power switchtoON. The servosstop near
the neutralposition.Operate the transmittersticksand
check that each servofollowsthe movement of the stick.
•Connect the pushrod to each servohorn,then check if the
directionof travelof each servomatchesthe direction of
operationof its transmitterstick.To reversethe direction of
servotravel,switchthe servoreversingswitch.
•Operate each servooveritsfulltravel,and check if the push-
rod binds or is too loose. Applyingunreasonableforceto the
servohorn willadverselyaffectthe servoand quickly drain
the battery.Alwaysmake the travelof each control mecha-
nism somewhat larger than the fulltravel(includingtrim)of
the servohorn. Adjust the servohorns sothat they move
smoothly even when the trimleverand stickare operated
simultaneouslyinthe same direction.
•Bealertfornoise.
This set is noise-resistant,butis not completely immune to
noise. We recommend the use of noiseless parts and noise
killercapacitor.
•When installingthe switch harness, cut a rectangular hole
somewhat largerthanthe fullstrokeof the switchand install
the switchso thatit moves smoothly fromON to OFF. This
also appliesto the switchmount when the switch is install-
ed inside the fuselage and is turnedon and offfromthe out-
side
with
a
piece of wire,etc. Install
the
switchwhere
it
will
not beexposedto engine oil,dust,etc.
•Eventhough the receiverantennais long, donotcutor
bundle it.
•Installthe servos securely.Tighten the mounting screws un-
til the rubber grommet iscrushedslightly.If the screwsare
too tight, the cushioning effectwill beadversely affected.
SERVO MOUNTING
Fig.
10
•Spare servo horns are supplied. Use them as needed.
•Wrapthe receiverinsponge rubber. Waterproofand dust-
proof the receiverbyplacing itin a plasticbag and wrapping
arubber band around the open end of the bag.Dothe same
withthe receiver/servobattery.
•Use therubber bands wrappedaround the receiver to hold
the servoand switchleads.
•Aftermounting iscomplete,recheck eachpart, then check
the range bymaking the transmitterantenna as short as
possible, extendingthe receiverantenna fully,and operating
the set froma distanceof20m to 30m. The movement of
each servoshould followthe movement of each stickof the
transmitter.
•The motor controller connects to channel 3 inthe MCR-4A.
•
Motor
aircraftvibrate
less
thanengine aircraft,butthe
receiver and servoshould bevibrationproofed.
•Ifthe NiCdbattery pack is connected inreverse,
the MCR-4Amay bedamaged beyond repair.Be
surethatthe (+)and (—)connectionsarecorrect.
Blacklead wire0
Red lead wire +
Fig.
11
•Aftermounting and checking are complete, takeyour model
to the shop where you purchased the set, or to an experienc-
ed radio controlmodeler, and ask them to teach youhow to
handle your radiocontrolsetinthe proper manner and to
inspect your set-up carefully.
•
To
enjoyradio
control
models
fully,
be
sure
to
observe
all
safety standards.
USINGTHE ANTENNA FREQUENCY FLAG
Attachthe frequencyflagto
the flagholder asshown inthe
figure.
Fig.
12
The flag can beattachedto.
andremoved from, the
antenna withonetouch.
Fig.
13
Thishornpermitsshiftingofthe
servo neutralpositionattheservo
horn. Settingand shiftingthe neu-
tralposition.
a) Angle divisions
1)The splined horn has 25 seg-
ments. The amount ofchange per
segment is;360-25=14.4°.
2) The minimum adjustableangle
is determinedbythenumber of
arms or number oftheholes.For
four arms,the minimum adjust-
able angleis:
Fig.14
b) Effect
To shiftthe holes center lineto
the right(clockwise)relativeto
baselineA,shiftarm 2 tothepo-
sitionof arm1 and set it tothe
positionclosesttobaselineA.
[Example]For a fourarmhorn,
theangular shiftpersegment is
14.4". The shifttotherightis90°
-(14.4x6)=3.6°.
To shiftby thesame angle inthe
oppositedirection,usethe oppo-
sitearm number.
Fig.
15
For a sixarmhorn, turnthe arm
counterclockwiseand set arm2
tothepositionofarm1.The ad-
justableangle is60°- (14.4x 4)
=2.4°.
Arm3 shift4.8°totheright,arm
6shifts2.4° to theleft,and arm4
shifts7.2° tothe rightand left.
Fig.
16

No.
1
2
3
4
5
6
7
8
9
10
11
12
13
14
15
16
17
18
19
20
21
22
Part name
Uppercase
Middle
case
Motor
Motor pinion
1stgear
2ndgear
3rd gear
4th gear
Final gear
Output shaft
Intermediate shaft
VRjoint
VR drive plate
Potentiometer
SplinedhornF
Horn mounting screw
Bottom case
Case mountingscrew
Printed wiring board
Grommet
3PCcord170
Nameplate
Part No.
S05850
S05860
S91241
S02781
S02782
S02783
S02784
S02785
S02786
S05880
S04285
S05872
S05626
i39600
S01241
J55171
S05870
S40070
AS
1259
S90045
AT2213
S60122
No.
1
2
3
4
5
6
7
8
9
10
11
12
13
14
15
16
17
18
19
20
21
22
23
Partname
Uppercase
Middle case
Bottom case
Metalbearing-
Metal bearing
Potentiometer
Potentiometer driveplate
Motor
Motor pinion
Screw
1st gear
2ndgear
3rdgear
Finalgear
Intermediate shaft
2ndshaft
ServohornD
Bindinghead tappingscrew 2.6x8
Printed wiring board
3PB-WRB300G
w/gum bush
Pan head truss screw
Nameplate
PartNo.
VCS-48
FCS-48
FCS-48
S04137
S04136
139668
S02753
S91239
S02461
J50002
FGS-48
FGS-48
FGS-48
FGS-48
S02495
S02494
PSH-6W
FSH-41
ASH
57
AT2453
S90045
S50360
S60099
FUTABA CORPORATION
Makuhari
Techno
Garden
Bidg.,
B6F
1-3
Nakase,
Mihama-ku,
Chiba
261-01,
Japan
Overseas Marketing& SalesRadio Control Systems
Phone:(043)296-5119Facsimile: (043)296-5124
FUTABA CORPORATION OF AMERICA
4Studebaker, IrvineCalifornia92718, U.S.A.
Phone:714-455-9888
Telex:
23-0691227
Facsimile:
714-455-9899
This manual suits for next models
1
Table of contents
Other FUTABA Remote Control manuals
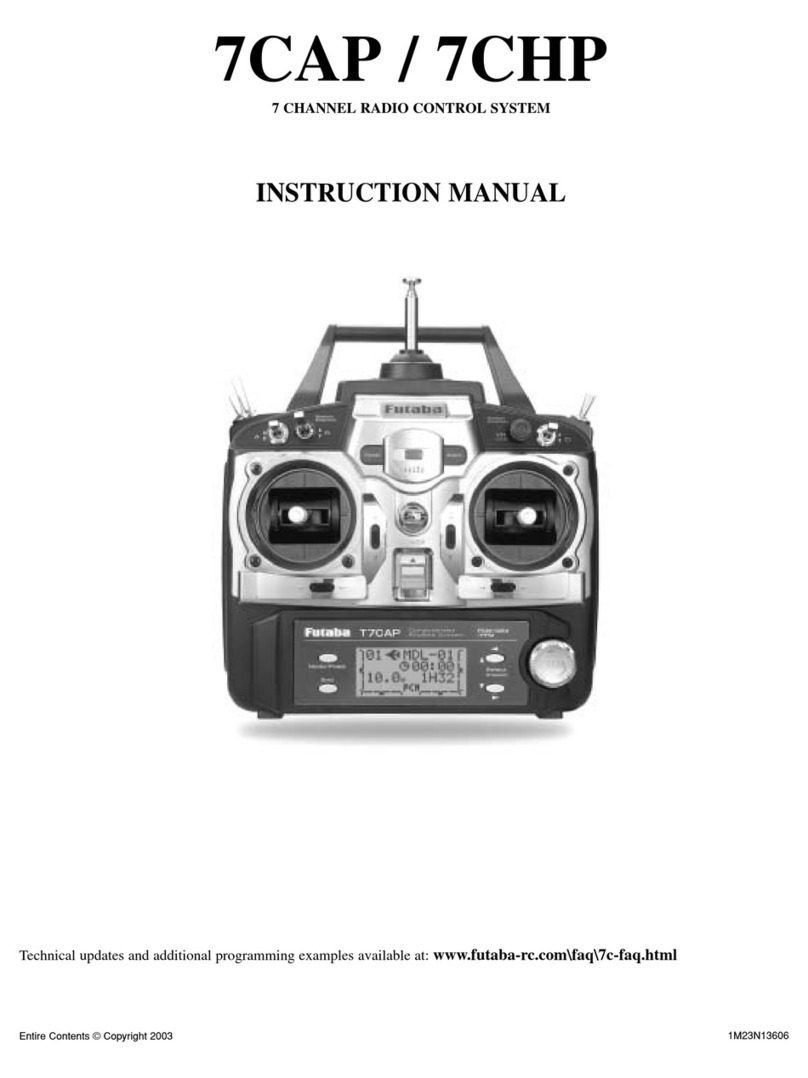
FUTABA
FUTABA 7CAP User manual

FUTABA
FUTABA 7XC User manual
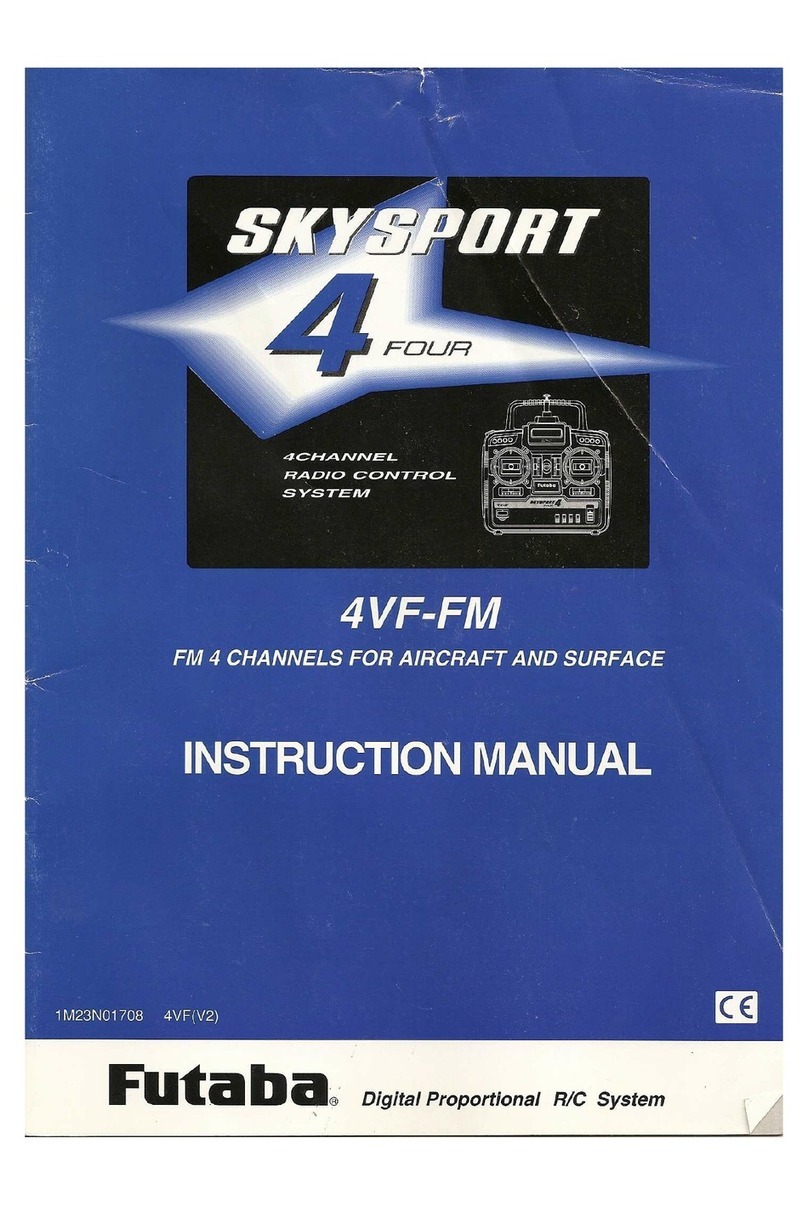
FUTABA
FUTABA 4VF-FM User manual
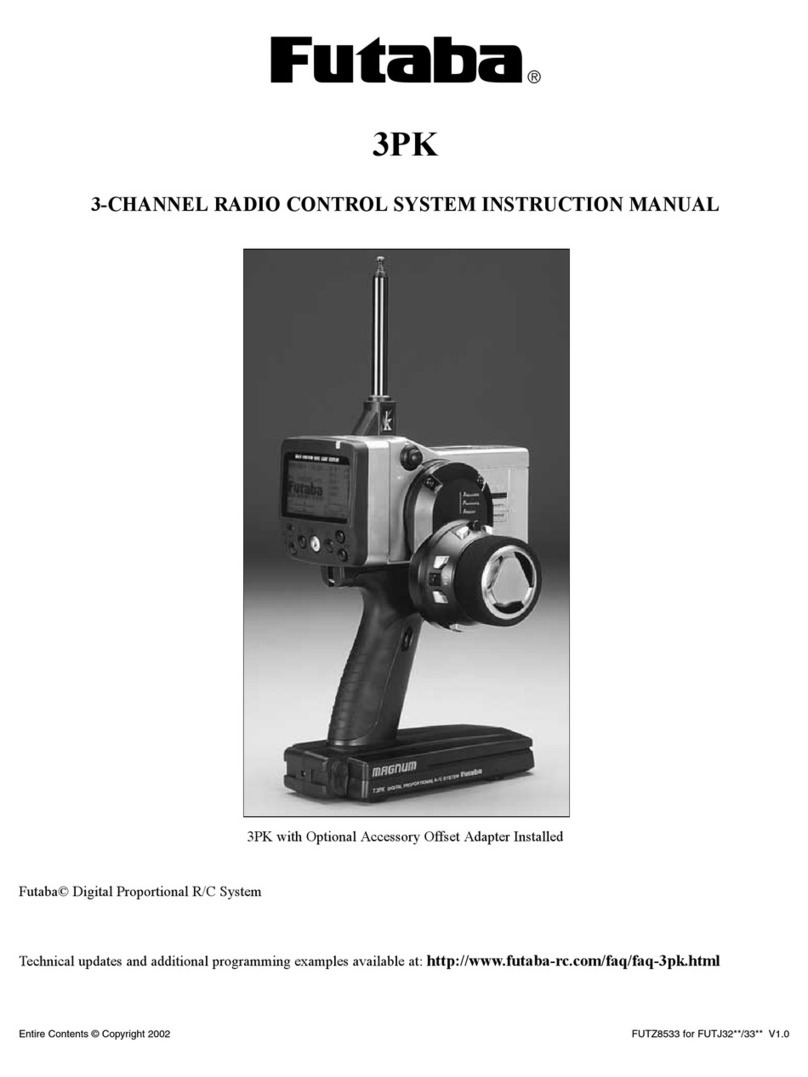
FUTABA
FUTABA Magnum 3PK Super User manual
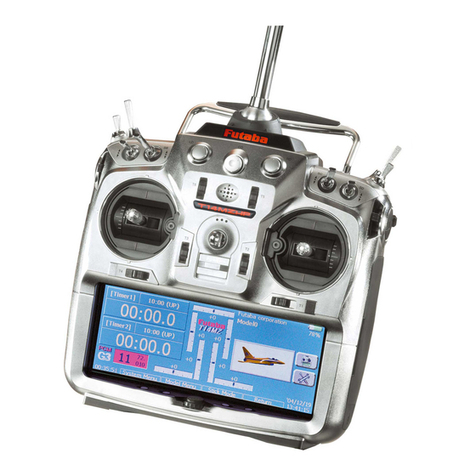
FUTABA
FUTABA 14MZ User manual
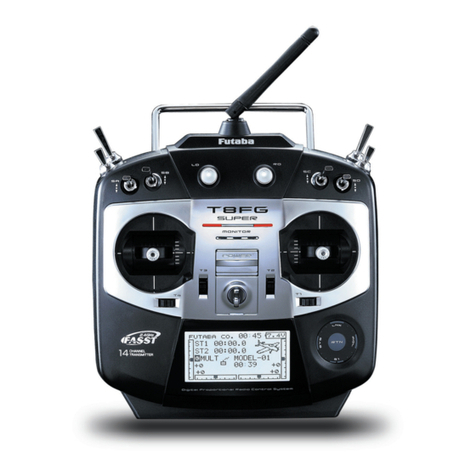
FUTABA
FUTABA 8FG User manual
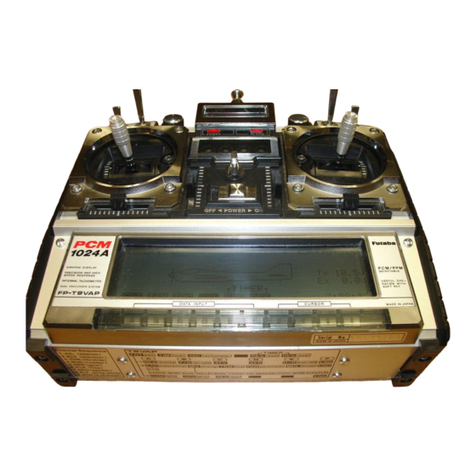
FUTABA
FUTABA 9VAP User manual
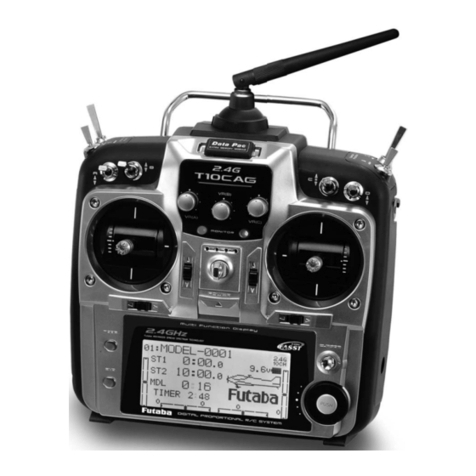
FUTABA
FUTABA 10CAG User manual
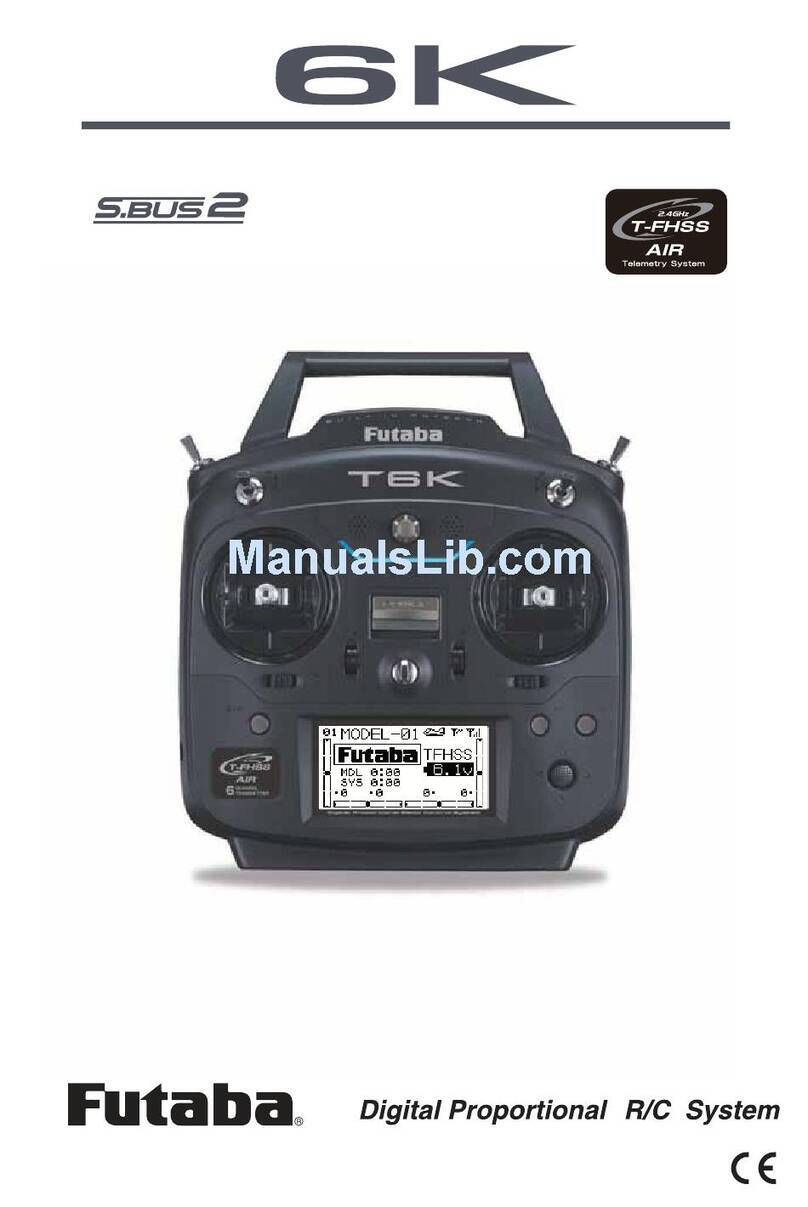
FUTABA
FUTABA 6k User manual
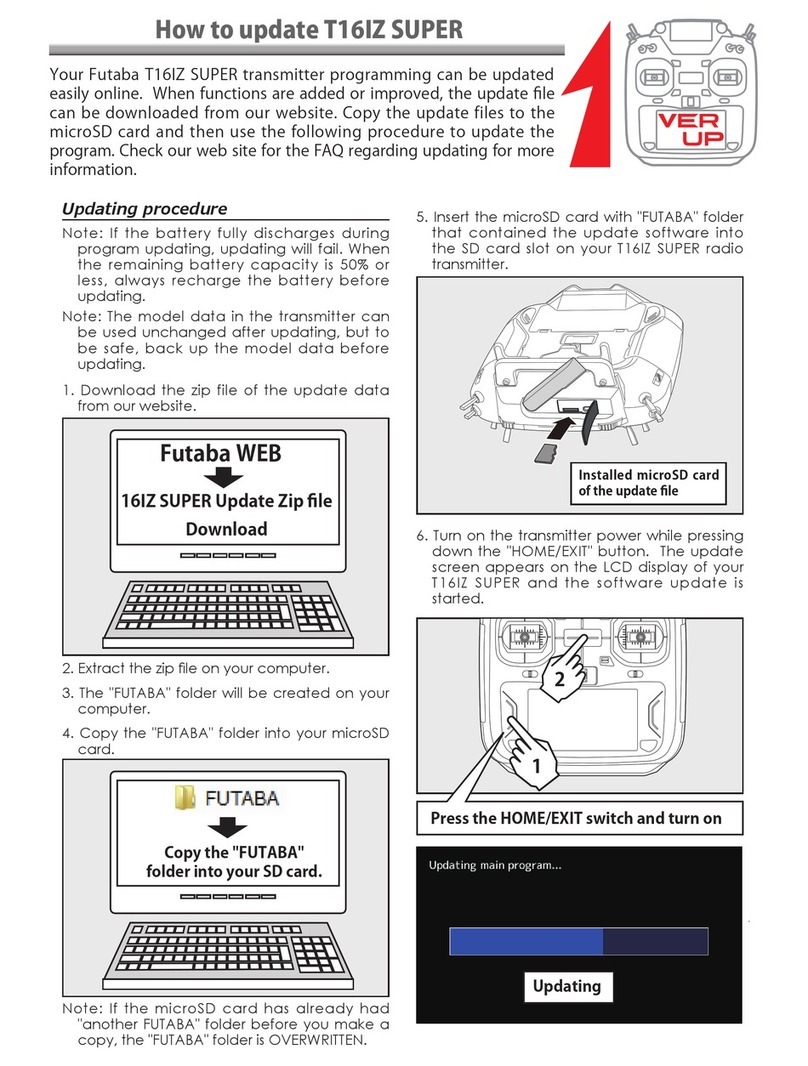
FUTABA
FUTABA T16IZ Installation and user guide
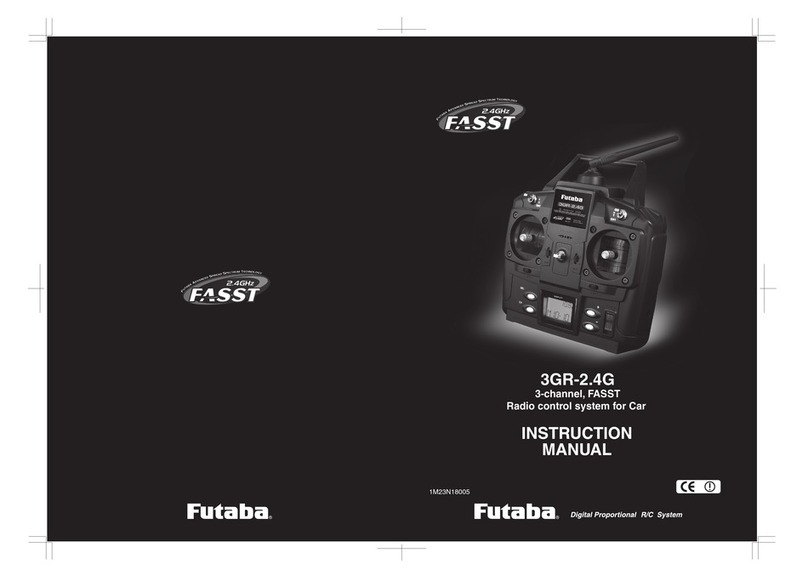
FUTABA
FUTABA 3GR-2.4G User manual
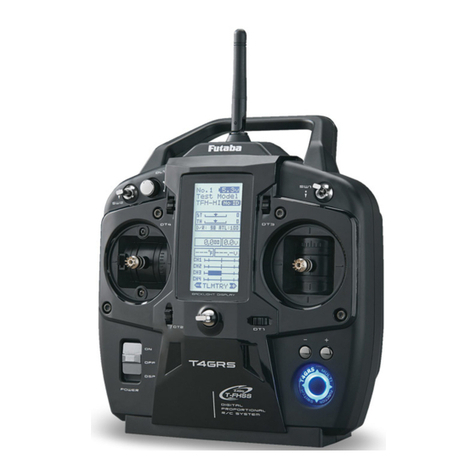
FUTABA
FUTABA T4GRS-24G User manual
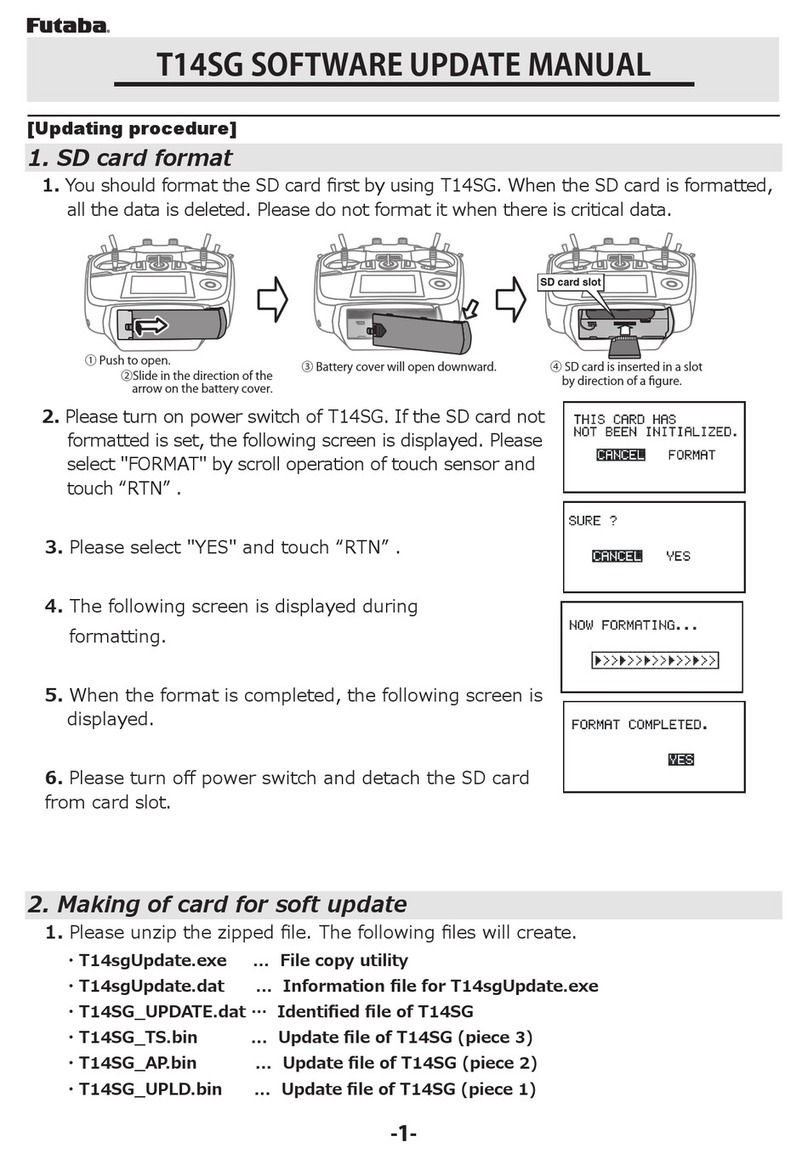
FUTABA
FUTABA T14SG Technical manual
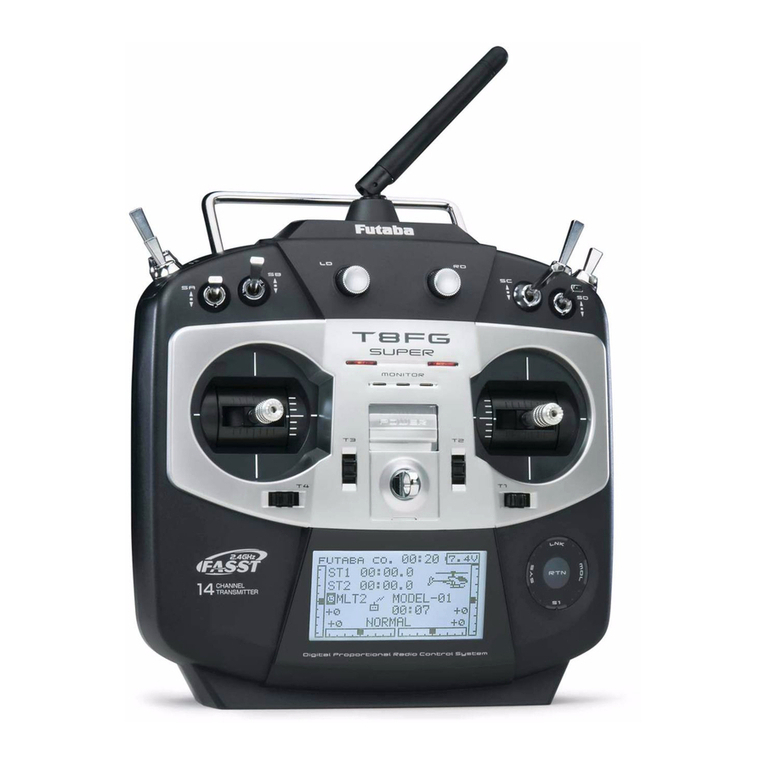
FUTABA
FUTABA 8FG Operating instructions
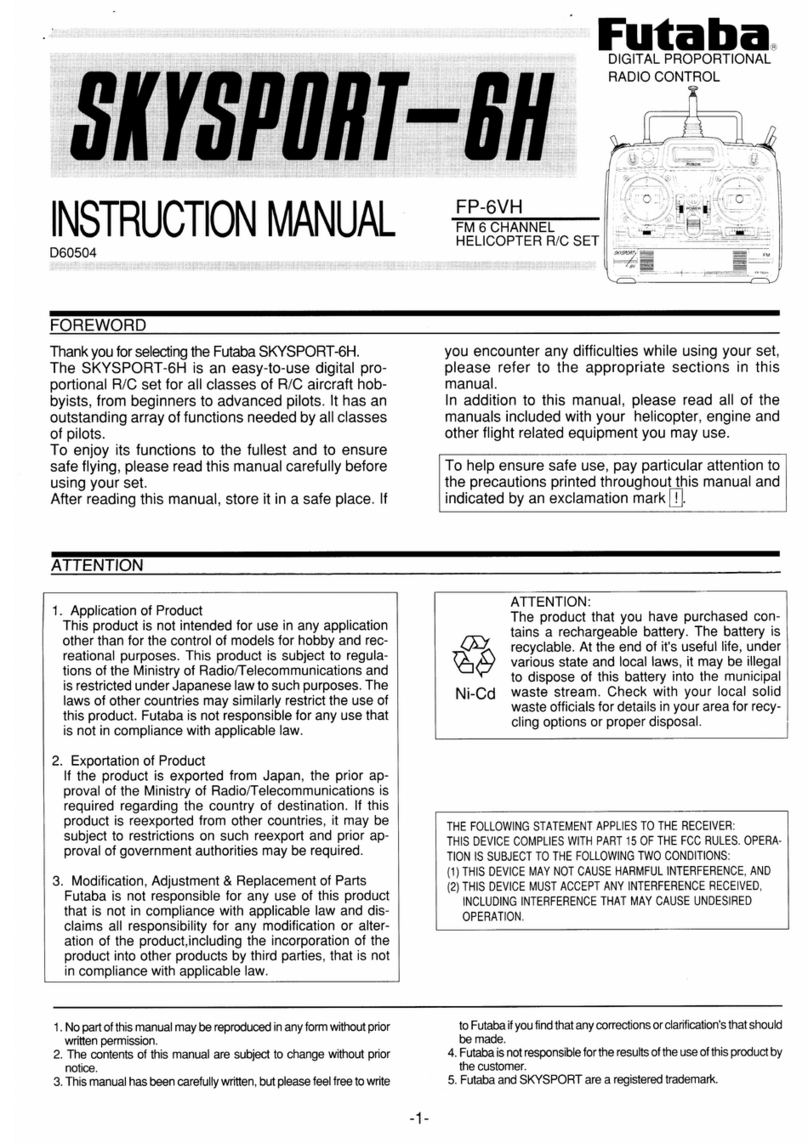
FUTABA
FUTABA FP-6VH User manual
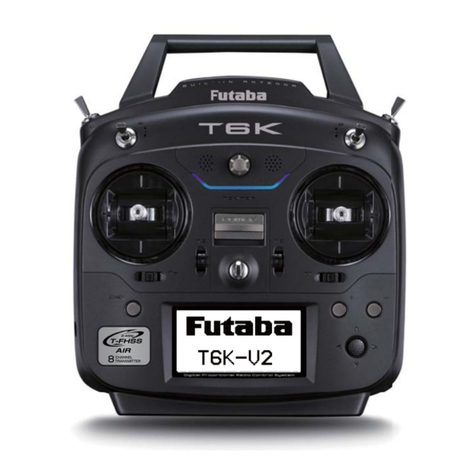
FUTABA
FUTABA T6K-V2 User manual

FUTABA
FUTABA ATTACK-II User manual
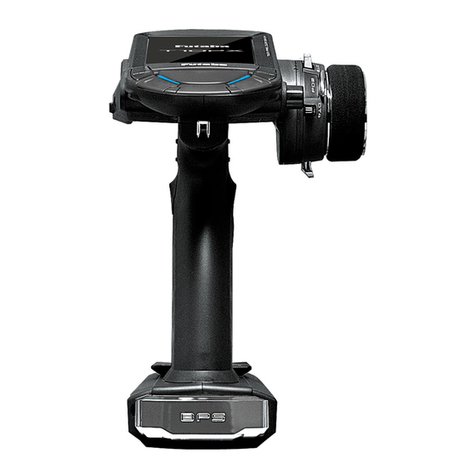
FUTABA
FUTABA T10PX How to use
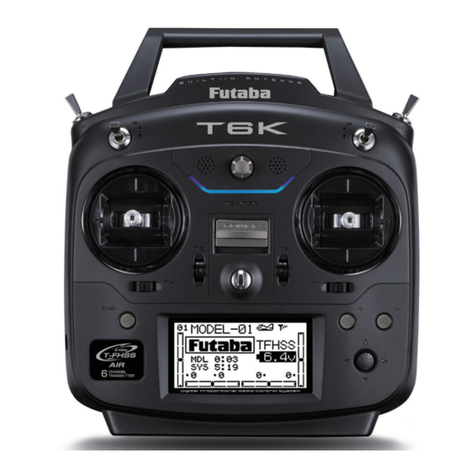
FUTABA
FUTABA 6k User manual
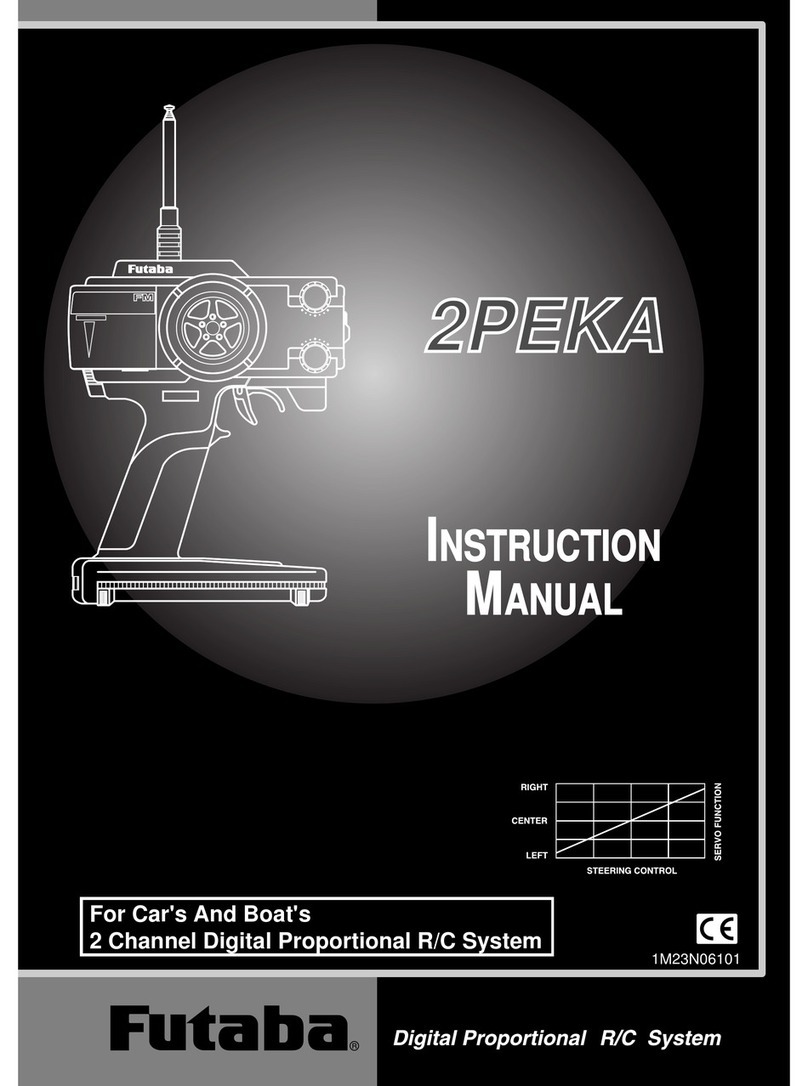
FUTABA
FUTABA 2PEKA User manual