FUTABA T12Z Technical manual

- 1 -
1M23N16910
T12Z Software Update
(Editor Version:1.3.2, Encoder Version:1.39)
CAUTION
To support new features model memories must be updated to version 1.2.0. Once the 1.2.0 update is installed
into your transmitter, the model memory update will automatically occur when you select the model the first time.
After this update has been performed the model memory will no longer be compatible with software versions prior
to 1.2.0.
Changing the RF Modulation
The T12Z transmitter is compatible with Futaba's TM-14 Module FASST 2.4GHz system.
When switching from the existing MZ-FM module to the TM-14, the TM-14 to the MZ-FM module, or similar
situation, it is necessary to reset the band accordingly.
When using the TM-14 and Futaba FASST receiver, it is necessary to link the transmitter module to the
respective receiver prior to using them for the first time. This process will only be necessary the first time that
these items are used. The unique identification code will be stored in the receiver.
When using the TM-14 FASST system, the DSC function has been disabled as it is unnecessary. Futaba's
FASST system will prevent any RF interference issues which might have arisen in the previous RF
modulation.
The multiprop function cannot be used.
HowtoSettheBand
1. With the transmitter's power OFF, remove the
existing RF module and replace it with the TM-14
module.
2. Turn ON the transmitter's power switch. Since
the RF module was replaced by an RF module
that varies from the previous settings, an
on-screen warning is displayed. To change the
modulation settings, push the DATA button.
3. In the linkage menu, select the frequency setting
[FREQUENCY], and push the DATA button. A
message confirming the band change is displayed.
Press the DATA button once again.
Please note: This will automatically select
Futaba's FASST MULT setting. If, however, you
are using a receiver which employs the FASST
7-Channel settings, please see the section entitled
Channel Mode Selection which follows.
4. A channel mode selection screen is displayed.
Press the EDIT button.
5. A function channel relocation confirmation screen
is displayed. When [YES] is selected and the
DATA button is pressed, the function channel
assignment is changed to the optimum setting in
the FASST system. When [NO] is selected and the
DATA button is pressed, the setting is not
changed.
After the channels have been relocated you must
verify that the receiver connections are correct and
verify that all of the settings within the transmitter
are correct before flying.
In the FASST system, the optimum channel
assignment and optimum setting in the
conventional modulation mode are different.

- 2 -
6. The band setting changes accordingly to reflect
the selection of the 2.4GHz band. The display will
return to the frequency confirmation screen.
RangeCheckModeOperation
The 'range check mode' reduces the transmission
range of the radio waves to allow for a ground range
check.
The range check mode, when activated, will
continue for 90 seconds unless the user exits this
mode early. When the progress bar reaches 90s,
the RF transmission automatically returns to the
normal operating power.
WARNING
Do not fly in the range check mode.
Since the range of the radio waves is short, if the
model is too far from the transmitter, control will
be lost and the model will crash.
1. Turn ON the transmitter's power switch. Select
[NO] on the frequency confirmation screen.
For safety, the RANGE CHECK mode can not be
selected while the RF transmission is active.
2. With the system menu selected press the DATA
button, choose the [RANGE CHECK] selection
from the menu options and press the DATA
button.
3. The RANGE CHECK screen is displayed. To
activate the RANGE CHECK mode select [YES]
and then press the DATA button. During the
RANGE CHECK period, the RF power is reduced
to allow the ground range tests to be performed.
Operation can be cancelled by pressing the
“RETURN” or “HOME” button.
4. The Range Check function automatically exits
after the 90 second time limit has expired. Should
you complete the range check before the 90
seconds has passed, select [EXIT] and press the
DATA button.
When [RESTART] is selected and the DATA
button is pressed, the range check mode timer is
returned to 0.
Please note, upon expiration of the 90 seconds, or
when [EXIT] is selected, the transmitter will
automatically return to the normal RF operation
as noted on the display.
Once the 14MZ is transmitting at full power, it is
not possible to enter the Range Check mode
without first switching the transmitter Off and
back On. This has been designed to prevent a
modeler from inadvertently flying in the Range
Check mode.
5. When [EXIT] is selected and the DATA button is
pressed, the RANGE CHECK mode is disabled
and the 12Z will begin transmitting at full power.
After the RANGE CHECK mode was reset, it
cannot be selected again. To select the RANGE
CHECK mode again, turn on the power switch and
start from the beginning.

- 3 -
ChannelModeSelection
When using the TM-14 RF module with the T12Z,
there are two modes of operation available:
multi-channel mode (as utilized in conjunction with the
R6014FS receiver) and 7-channel mode (used for
receivers such as the R617FS). It is important to set
the channel mode selection to match the receiver being
utilized in the model. Please refer to the chart below
as a reference guide.
Receiver
Transmitter R606FS
R616FFM
R607FS
R617FS
R608FS
R6014FS
Multi-ch mode ——Compatible
TM-14
Module 7ch mode Compatible Compatible —
1. Access the frequency setting [FREQUENCY] in
the linkage menu and then press the DATA
button. The currently selected transmission
mode is displayed.
2. To change the mode selection, select the alternate
transmission mode.
[FASST MULT] : Multi channel mode
[FASST 7CH] : 7 channels mode
3. Press the DATA button, the display will return to
the confirmation screen.
4. A channel relocation screen will appear. If you
wish to relocate the channel assignments,
select the [Yes]. If not, select [No]. The channel
assignments will not be modified.
(Information pertaining to the 7 channel mode)
When the 7 channel mode is selected, the following
conditions are applicable:
While the setting items of channels 8 and above
may appear in the various menu options (e.g., sub
trims, servo reverse, etc.), the only settings which
are applicable are those of channels 1-7.
When using the 7 channel mode, fail safe is only
available for channel three (throttle). If/when the
fail safe for channel three has been activated, the
battery fail safe is also active. Unlike the multi
channel mode, the fail safe and the battery fail
safe can not be set independently.
ChannelAssignment
Servo connection
Below is a reference chart which has been created to
obtain the optimum performance from the FASST
system in conjunction with the channel mode and
various swash types. It is important to note and
adhere to this reference information in order to achieve
the maximum performance from the model. As such,
please connect the servos to the corresponding
channels in the chart below.
Multi channel mode 7 channels mode
CH Except
H-4, H4X H-4, H4X Except
H-4, H4X H-4, H4X
1
Ail
e
r
o
n
Ail
e
r
o
n
Ail
e
r
o
n
Ail
e
r
o
n
2 Elevator Elevator Elevator Elevator
3 Pitch Pitch Throttle Throttle
4 Rudder Elevator2 Pitch Pitch
5 G
y
ro Rudder G
y
ro G
y
ro
6 Throttle Throttle Rudder Rudder
7 Governor G
y
ro Governor Elevator2
8 Governor Governor AUX5 AUX5
9 Needle Governor AUX4 AUX4
10 AUX3 Needle AUX3 AUX3
11 AUX2 AUX2 AUX2 AUX2
12 AUX1 AUX1 AUX1 AUX1
VC1 AUX1 AUX1 AUX1 AUX1
VC2 AUX1 AUX1 AUX1 AUX1
VC3 AUX1 AUX1 AUX1 AUX1
VC4 AUX1 AUX1 AUX1 AUX1
It is important to note that these settings differ
from that used in the previous G3 receivers.
Utilizing the channel assignments from the G3
receivers will not allow you to obtain the ideal
performance from your model.
Please note that the settings in the chart above
are the default settings. As such, when the
data is reset, the channel assignments above
will be utilized.

- 4 -
Automaticchannelassignment
When using the TM-14 RF module, the T12Z channel
assignment function allows the automatic relocation of
the channels (servo output) to maximize performance
of the FASST system.
(Example) Change from the MZ-FM module to the
TM-14 module
1. Replace the RF module of the T12Z with the
TM-14.
2. Turn on the transmitter.
3. Select LINKAGE menu.
4. Select FREQUENCY menu.
5. A message is displayed. Push the DATA
button.
6. A CHANNEL RELOCATION message will
appear. If you wish to relocate the channel
assignments, select [YES] and press the DATA
button. If not, select [NO]. The channel
assignments will not be modified.
7. Band setting changes to 2.4GHz.
8. The channel assignment is changed to suitable
assignment of FASST.
9. After the channels have been relocated you
must verify that the receiver connections are
correct and verify that all of the settings within
the transmitter are correct before flying.
RangeChecktheRadio
It is extremely important to range check your models
prior to each flying session. This enables you to
ensure that everything is functioning as it should and
to obtain maximum enjoyment from your time flying.
The TM-14 transmitter module incorporates a system
that reduces its power output and allows you to
perform such a range check.
1. Turn on the transmitter and activate the
'RANGE CHECK' mode through the
transmitter's System menu. Please note: if
the RF is activated, the 'RANGE CHECK' mode
will not be available to utilize. As such, do
NOT activate the RF when the transmitter is
turned ON.
2. The LEDs on the rear of the TM-14 module will
indicate that a radio frequency link has been
established between the transmitter and
receiver. This is noted by a solid green LED
and a blinking red LED on the TM-14 module.
The solid green LED indicates that the radio
frequency link has been established. As
indicated by the blinking red LED, the radio
frequency power has been reduced to allow for
the range check. Note: the transmitter will
remain in the RANGE CHECK mode for a
maximum of 90 (ninety) seconds. This time
limit has been established to ensure that the
modeler not inadvertently forget to return to
the standard power output when flying his/her
model.
3. Walk away from the model while
simultaneously operating the controls. Have
an assistant stand by the model to confirm that
all controls are completely and correctly
operational. You should be able to walk
approximately 30-50 paces from the model
without losing control.
4. If everything operates correctly, return to the
model. Set the transmitter in a safe, yet
accessible, location so it will be within reach
after starting the engine or motor. Be certain
the throttle stick is in the low throttle position,
then start the engine or motor. Perform
another range check with your assistant
holding the aircraft with the engine running at
various speeds. If the servos jitter or move
inadvertently, there may be a problem. We
would strongly suggest you do not fly until the
source of the difficulty has been determined.
Look for loose servo connections or binding
pushrods. Also, be certain that the battery
has been fully charged.
AntennaofTM-14
1. As with all radio frequency transmissions, the
strongest area of signal transmission is from the
sides of the TM-14 transmitter module's antenna.
As such, the antenna should not be pointed directly
at the model. If your flying style creates this
situation, please pivot the antenna to correct this
situation.
2. Please do not grasp the transmitter's antenna
during flight. Doing so may degrade the quality of
the RF transmission to the model.

- 5 -
TM-14LEDindication
When the transmitter is powered up, the LEDs on
the rear of the module will begin to glow or blink
accordingly. The chart below provides you with an
easy reference as to the meaning of the LEDs.
Green Red Status
Solid Solid Initializing
Blink Off RF is off
Alternate Blink Check nearby RF condition
Solid Off RF power on
Solid Blink
RF power on (Power reduced to perform
the range check function)
R6014FS LED Indication
Green Red Status
Off Solid No signal received
Solid Off Signal received, normal operation
Blink Off
Receiver is receiving signals but the ID
is unmatched
Alternate Blink Unrecoverable error (EEPROM, etc.)
Othermodifications
Cumulative Model Timer
A cumulative model timer has been added to this
version of the software. To show this timer on the
home screen please follow the instructions below.
The Cumulative Model Timer and System Timer
values are maintained even if they are not displayed
on the home Screen.
1. Open [SYSTEM TIMER] of the System Menu.
2. Select “MODE” and turn the DATA dial and
switch the display to [TOTAL] or [MODEL].
※The display blinks.
[TOTAL] : Operation is the same as in the past.
[MODEL] : The elapsed time of each model is
recorded.
3. When the DATA button is pressed, the setting is
changed.
Automatic channel assignment
The 12Z will automatically relocate channel
assignments as necessary to achieve the highest
performance. This automatic channel relocation will
occur when you change the modulation type. To
minimize latencies and obtain the highest
performance you should allow the transmitter to
automatically relocate the channels when requested.
Once the channels have been relocated it will be
necessary to verify that the servos are plugged into
the proper channels on the receiver.
1. Change the modulation mode using the
[FREQUENCY] function of the Linkage Menu.
2. A channel relocation confirmation screen is
displayed. To change the channel allocation,
select [YES] and press the DATA button. To
maintain the current channel allocations, select
[NO] and press the DATA button.
Frequency setting
The frequency, modulation and receiver ID can be set
at same time from this version. It is not necessary to
return to the frequency setting screen for each setting.
1. Change the frequency, the modulation mode or
receiver ID using [FREQUENCY] function of the
Linkage Menu.
2. A confirmation screen is displayed.
3. If you want to change other setting, press the
frequency channel button, the modulation type
button or the receiver ID button.
Modeltype
2 ailerons + 4 flaps and 4 ailerons + 2 flaps have been
added to the glider model types which can be selected
in the PCM1024 mode and the PPM mode.
Motor gliders cannot be handled.

- 6 -
Data initialization after swash type switching
In the past when the swash type was changed, all of
the model data had to be initialized. Starting with
version 1.3.0 it is possible to change the swash type
and the software will automatically transfer the
settings. There are a few swash type conversions
that are not possible, please see the table below for
more information.
If the swash type data can be retained the
transmitter will prompt with “Initialize all data?”
Answer [No] if you would like to retain the swash
settings answer. Answer [Yes] if you would like
the data initialized then answer.
It may not be possible to continue the model data,
depending on the swash type before and after
modification.
Before
modification
After
modification Continuation
H-1,H-2,HE3,
HR3,HN3,H-3
H-1,H-2,HE3,
HR3,HN3,H-3 Possible
H-4,H-4X H-4,H-4X Possible
H-1,H-2,HE3,
HR3,HN3,H-3 H-4,H-4X Impossible
H-4,H-4X H-1,H-2,HE3,
HR3,HN3,H-3 Impossible
1. When the swash type is changed, and if the data
can be retained, a data initialization confirmation
screen is displayed. When [YES] is selected and
the DATA button is pressed, the data is initialized.
When [NO] is selected and the DATA button is
pressed, the data is retained.
Verify that all of the settings are correct before
operating your model.
Mixing switch NULL-ON/OFF setting
When the switch type “NULL” is selected, you can
toggle the On/Off option manually.
1. Open the mixing switch selection screen. Select
[NULL] and press the DATA button.
2. The on/off setup screen is displayed. Turn the
DATA dial and switch the display to [ON] or
[OFF].
※The display blinks.
[ON] : Mixing always on.
[OFF] : Mixing always off.
3. When the DATA button is pressed, the setting is
changed.
Function name
The function name can be changed for the full name
(10 characters) or for the abbreviated name (4
characters).
1. Select [FUNCTION NAME] of the Linkage Menu
and press the DATA button.
2. The FUNCTION NAME setup screen is
displayed.
3. Select the function to be renamed and select the
[Rename] and the DATA button is pressed. A
character input screen is displayed. Type in the
new function name and select [Enter] and press
the DATA button to store the new function name,
or press the RETURN button to cancel.
4. When [RESET] is selected and the DATA button
is held down, the function name is reset to the
initial state function name.

- 7 -
5. The function name may be displayed in 10
characters or 4 characters, depending on the
setup screen. For 4 characters display, input the
function name as required.
Timer
A timer can now be set to maintain its value even
when the power is turned off or the model is
switched.
1. Open [TIMER] of the Linkage Menu.
2. Select "MEMORY" and turn the DATA dial and
switch the display to [ON] or [OFF].
※The display blinks.
[ON] : Memory mode. The timer value is held
even after power off and model switching.
[OFF] : The timer is reset by power off and model
switching as in the past.
3. When the DATA button is pressed, the setting is
changed.
Trimdisplayunits
Percentage (%) display can be selected at trim.
1. Open [DIAL MONITOR] of the Linkage Menu.
2. Turn the DATA dial and switch “TRIM UNIT” to
[%] or [-].
※The display blinks.
[%] : Trim is displayed in % units.
[--] : Trim is displayed numerically the same as in
the past.
3. When the DATA button is pressed, the setting is
changed.
Volume modification
The volume can be set according to the type of sound.
The types of sound which can be selected are:
• Key operation sound
• Error/Warning sound
• Trim and center click sound
• Timer event sound
• Other sound
1. Select [SOUND] of the System Menu and press
the DATA button.
2. The volume setup screen opens.
3. Select the item whose volume is to be set. When
the DATA dial is turned clockwise, the volume
increases and when the dial is turned
counterclockwise, the volume decreases. When
the DATA button is held down, the volume is reset
to the initial value.
For safety, the error/alarm sound cannot be set to
below a certain volume.
Japanese/German display compatibility
The set has been made compatible with Japanese and
German display.
Display switching
1. Open [INFORMATION] of the System Menu.
2. Turn the DATA dial and select the display
language.
※The display blinks.
[ENGLISH] : English mode
[JAPANESE] : Japanese mode
[GERMAN] : German mode
3. When the DATA button is pressed, the setting is
changed.

- 8 -
Character input
Lower case alphabetic characters and katakana, etc.
can be used.
1. When the DATA dial is turned, the input
character field cursor moves left and right.
2. When the CURSOR lever is moved up, down, left,
or right, the candidate characters list moves.
When the DATA button is pressed, the character
on the cursor is input.
3. When the CURSOR lever is pressed, the
candidate characters list is switched alphabet,
numbers/symbols and katakana.
4. To enter the input, operate the CURSOR lever
and select [ENTER] and press the DATA button.
5. To cancel input, operate the CURSOR lever and
select [CANCEL] and press the DATA button.
Pitch angle display mode
The system has been made compatible with pitch angle
display.
1. Open [PITCH CURVE] of the Model Menu.
2. Move the cursor and display the page 4.
3. Select “UNIT” and turn the DATA dial and switch
the display to [DEG.] or [%].
※The display blinks.
[DEG.] : Angle display mode
[%] : % display mode
4. When the DATA button is pressed, the setting is
changed.
5. When [ANGLE] is selected and the DATA dial is
pressed, the angle setup screen is displayed.
6. Set high pitch. Move the pitch control to high
pitch and move the cursor to [HIGH]. Turn the
DATA dial and set the angle.
7. Set center pitch. Move the pitch control to the
hovering point and move the cursor to [CENTER].
Turn the DATA dial and set the angle.
8. Set low pitch. Move the pitch control to low pitch
and move the cursor to [LOW]. Turn the DATA
dial and set the angle.
AFR, D/R
The following functions cannot be selected at AFR and
D/R because they are not effective.
• Ailerons 2,3,4
• Flaps 2,4
• Rudder 2
• Throttle (helicopter only)
• Pitch
• Camber
• Gyro 1,2,3
• Governor 1,2
• Mixture
• Multiprop
Sticksetting
The adjustable range of the stick response is reduced
to 1-16.

- 9 -
Function channel initialization
PCM1024 mode and PPM mode function channel setting was changed as shown below.
If you want to see the function channel setting in other modulation modes, please see the manual.
Normal and V-tail
1Aileron 2Aileron 2Aileron + 1Flap
CH Airplane EP Glider Glider Airplane EP Glider Glider Airplane EP Glider Glider
1 Aileron Aileron Aileron Aileron Aileron Aileron Aileron Aileron Aileron
2 Elevator Elevator Elevator Elevator Elevator Elevator Elevator Elevator Elevator
3 Throttle Motor AUX1 Throttle Motor AUX1 Throttle Motor AUX7
4 Rudder Rudder Rudder Rudder Rudder Rudder Rudder Rudder Rudder
5 Gear AUX7 AUX7 Gear AUX7 AUX7 Gear AUX6 AUX6
6 Airbrake Airbrake Airbrake Aileron2 Aileron2 Aileron2 Flap Flap Flap
7 AUX6 AUX6 AUX6 AUX6 AUX6 AUX6 Aileron2 Aileron2 Aileron2
8 AUX5 AUX5 AUX5 AUX5 AUX5 AUX5 AUX5 AUX5 AUX5
VC1 AUX1 AUX1 AUX1 Camber Camber Camber Camber Camber Camber
VC2 AUX1 AUX1 AUX1 AUX1 Butterfly Butterfly AUX1 Butterfly Butterfly
VC3 AUX1 AUX1 AUX1 AUX1 AUX1 AUX1 AUX1 AUX1 AUX1
VC4 AUX1 AUX1 AUX1 AUX1 AUX1 AUX1 AUX1 AUX1 AUX1
2Aileron + 2Flap 2Aileron + 4Flap 4Aileron + 2Flap
CH Airplane EP Glider Glider Glider Glider
1 Aileron Aileron Aileron Aileron Aileron
2 Elevator Elevator Elevator Elevator Elevator
3 Throttle Motor AUX6 Rudder Rudder
4 Rudder Rudder Rudder Aileron2 Aileron2
5 Gear AUX5 AUX5 Flap Aileron3
6 Aileron2 Aileron2 Aileron2 Flap2 Aileron4
7 Flap Flap Flap Flap3 Flap
8 Flap2 Flap2 Flap2 Flap4 Flap2
VC1 Camber Camber Camber Camber Camber
VC2 AUX1 Butterfly Butterfly Butterfly Butterfly
VC3 AUX1 AUX1 AUX1 AUX1 AUX1
VC4 AUX1 AUX1 AUX1 AUX1 AUX1
Flying wing
2Aileron 2Aileron + 1Flap
CH Airplane EP Glider Glider Airplane EP Glider Glider
1 Aileron Aileron Aileron Aileron Aileron Aileron
2 Rudder2 Rudder2 Rudder2 Rudder2 Rudder2 Rudder2
3 Throttle Motor AUX1 Throttle Motor AUX7
4 Rudder Rudder Rudder Rudder Rudder Rudder
5 Gear AUX7 AUX7 Gear AUX6 AUX6
6 Aileron2 Aileron2 Aileron2 Flap Flap Flap
7 AUX6 AUX6 AUX6 Aileron2 Aileron2 Aileron2
8 AUX5 AUX5 AUX5 AUX5 AUX5 AUX5
VC1 Elevator Elevator Elevator Elevator Elevator Elevator
VC2 Camber Camber Camber Camber Camber Camber
VC3 AUX1 AUX1 AUX1 AUX1 Butterfly Butterfly
VC4 AUX1 AUX1 AUX1 AUX1 AUX1 AUX1
2Aileron + 2Flap 2Aileron + 4Flap 4Aileron + 2Flap
CH Airplane EP Glider Glider Glider Glider
1 Aileron Aileron Aileron Aileron Aileron
2 Rudder2 Rudder2 Rudder2 Aileron2 Aileron2
3 Throttle Motor AUX7 Rudder Aileron3
4 Rudder Rudder Rudder Rudder2 Aileron4
5 Gear AUX6 AUX6 Flap Rudder
6 Flap Flap Flap Flap2 Rudder2
7 Aileron2 Aileron2 Aileron2 Flap3 Flap
8 Flap2 Flap2 Flap2 Flap4 Flap2
VC1 Elevator Elevator Elevator Elevator Elevator
VC2 Camber Camber Camber Camber Camber
VC3 AUX1 Butterfly Butterfly Butterfly Butterfly
VC4 AUX1 AUX1 AUX1 AUX1 AUX1

- 10 -
Ailevator
1Aileron 2Aileron 2Aileron + 1Flap
CH Airplane EP Glider Glider Airplane EP Glider Glider Airplane EP Glider Glider
1 Aileron Aileron Aileron Aileron Aileron Aileron Aileron Aileron Aileron
2 Elevator Elevator Elevator Elevator Elevator Elevator Elevator Elevator Elevator
3 Throttle Motor AUX1 Throttle Motor AUX1 Throttle Motor AUX7
4 Rudder Rudder Rudder Rudder Rudder Rudder Rudder Rudder Rudder
5 Gear AUX7 AUX7 Gear AUX7 AUX7 Gear AUX6 AUX6
6 Airbrake Airbrake Airbrake Aileron2 Aileron2 Aileron2 Flap Flap Flap
7 Elevator2 Elevator2 Elevator2 Elevator2 Elevator2 Elevator2 Aileron2 Aileron2 Aileron2
8 AUX5 AUX5 AUX5 AUX5 AUX5 AUX5 Elevator2 Elevator2 Elevator2
VC1 AUX1 AUX1 AUX1 Camber Camber Camber Camber Camber Camber
VC2 AUX1 AUX1 AUX1 AUX1 Butterfly Butterfly AUX1 Butterfly Butterfly
VC3 AUX1 AUX1 AUX1 AUX1 AUX1 AUX1 AUX1 AUX1 AUX1
VC4 AUX1 AUX1 AUX1 AUX1 AUX1 AUX1 AUX1 AUX1 AUX1
2Aileron + 2Flap
CH Airplane EP Glider Glider
1 Aileron Aileron Aileron
2 Elevator Elevator Elevator
3 Throttle Motor AUX6
4 Rudder Rudder Rudder
5 Elevator2 Elevator2 Elevator2
6 Aileron2 Aileron2 Aileron2
7 Flap Flap Flap
8 Flap2 Flap2 Flap2
VC1 Camber Camber Camber
VC2 AUX1 Butterfly Butterfly
VC3 AUX1 AUX1 AUX1
VC4 AUX1 AUX1 AUX1
Helicopter
CH H-1,H-2,HE3,HR3,HN3,H-3 H4,H-4X
1 Aileron Aileron
2 Elevator Elevator
3 Throttle Throttle
4 Rudder Rudder
5 Gyro Gyro
6 Pitch Pitch
7 Governor Governor
8 Needle Elevator2
VC1 AUX1 AUX1
VC2 AUX1 AUX1
VC3 AUX1 AUX1
VC4 AUX1 AUX1

- 11 -
( Update Modification Contents in the past )
STICK SETTING [System Menu]
This function sets the servo response speed (response) and dead
band width (hysteresis) relative to stick operation for each
condition. The operation feel of the stick can be adjusted to
match the in-flight aerobatics.
Call the setting screen shown below by selecting [STICK
SETTING] from the System Menu.
Response adjustment
1. Use the cursor lever to move the cursor to the set value
display of the stick whose response you want to adjust.
2. Use the dial to set the response.
Initial value : 4
Adjustment range : 1~16 (The larger the adjustment
value, the slower the response.)
Hysteresis adjustment
1. Use the cursor lever to move the cursor to the set value
display of the stick whose hysteresis you want to adjust.
2. Use the dial to adjust the response.
Initial value : 1
Adjustment range : 0~32 (The larger the adjustment
value, the larger the hysteresis.)
MULTIPROP CHANNEL
[Linkage Menu]
One channel can be expanded to 8 channels by using an
MPDX-1 (Multiprop Decoder). Up to two MPDX-1 can be used
with the 12Z system.
Multiprop function assignment
1. Open the function setting screen of the Linkage Menu,
and set the function of the channel to which you want to
connect the MPDX-1 to MULTIPROP1 or MULTIPROP2.
Operation control setting method
1. After assigning the function as described above, use the
cursor lever to move the cursor to MP CH of the channel
you want to set to multiprop. Push the DATA button to
display the setting screen shown below.
2. Use the cursor lever to move the cursor to CH
CONTROL of the multiprop channel you want to set.
Push the DATA button to display the control selection
screen. Select control.
Reverse setting
*Use this function when you want to reverse the direction of servo
operation.
1. Open the servo reverse setting screen of the Linkage
Menu. Use the cursor lever to select MP CH of the
channel you want to set to multiprop. Push the DATA
button.
2. The multiprop channel reverse setting screen is
displayed. Use the cursor lever to move the cursor to the
channel whose direction of operation you want to reverse.
Use the dial to switch between NORM (normal) and REV
(reverse), and push the DATA button.
End point adjustment
1. Open the end point (ATV) setting screen of the Linkage
Menu. Use the cursor lever to select MP CH of the
channel you want to set to multiprop. Push the DATA
button.
2. The multiprop channel end point (ATV) setting screen is
displayed. Use the cursor lever to move the cursor to the
channel whose end point you want to adjust. Use the dial
to change the rate. (Left and right, up and down can be
adjusted individually.)
*When both MULTIPROP1 and MULTIPROP2 are set, pushing the
cursor lever switches the MULTIPROP1 and MULTIPROP2 displays.
Response
setting
Hysteresis setting
Condition
group/single
switching
Screen with MULTIPROP1 and MULTIPROP2 set

- 12 -
Servo monitor
1. When the cursor lever is pushed, the normal channel
display and multiprop channel display are switched.
<Normal channel display>
<Multiprop channel display>
LOGIC SWITCH [Model Menu]
The logic switch function lets you turn operation on and off by
combining multiple switches. For instance, “Turn on the
function when 2 switches are turned on simultaneously” can be
set.
·Up to 4 switches can be combined.
·Up to 10 circuits can be used with the condition switches and
up to 8 circuits can be used with the ON/OFF switch of each
mixing function, except airplane snap roll.
<Mixing ON/OFF switch display>
(example of program mixing)
Setting procedure
1. Use the cursor lever to move the cursor to the switch
display of the function you want to set. Push the DATA
button.
2. The switch selection screen shown below is displayed.
<Mixing ON/OFF switch display>
(example of program mixing)
3. Use the cursor lever to move the cursor to the switch
mode. Use the dial to select the single switch mode or
logic switch mode, and push the DATA button. The single
switch mode is used with individual switches, the same
as in the past. When switched to the logic switch mode,
the switch mode and switches are displayed as shown
below. ON/OFF is determined by the combination of the
switch and logic mode displayed at the top and bottom.
4. Use the cursor lever to move the cursor to the logic
mode. Use the dial to select the logic from the three
types AND, OR, and Ex-OR, and push the DATA button.
Logic operation is shown in the table at below right. For
AND, both switches are ON, for OR, either one of the
switches is ON, and for Ex-OR, when the two switches
are in different states, the result is ON.
5. Use the cursor lever to move the cursor to the top or
bottom switch mode. Use the dial to select the logic
switch mode, and push the DATA button. Switch display
is added to each. A combination of up to 4 switches can
be registered in this manner. When 3 or more switches
are registered, the left and right switch combinations
surrounded by the frame are judged first. Next, the
combination in the judged frame are judged by the logic
displayed at the far right side. Finally, ON/OFF is
decided.
*In the above example, first SW-A and SW-B are judged by AND
condition and then SW-C and SW-D are judged by AND condition.
Lastly, the result of judgment of the SW-A and SW-B judgment result
and SW-C and SW-D judgment result by OR condition becomes the
final result. In this case, when SW-A and SW-B are simultaneously ON
or SW-C and SW-D are simultaneously ON, the result is ON.
Restrictions:
1. Logic switches can be used in mixing the ON/OFF
setting with up to 8 circuits for each condition. In
condition switching, it can be used with up to 10 circuits.
When logic switches exceeding the maximum settable
value are selected, an error message is displayed.
Release the unnecessary logic switches and then
reselect.
Switch mode
Switch
Switch state display (INH, ON, OFF)
(Condition switch: ON and OFF)
Judgment(1) Judgment(2) Judgment(3)
Mode selection

- 13 -
2. Mixing using logic switches as ON/OFF switches is
forcibly switched to the condition single mode. Switching
to the condition group mode is impossible until the logic
switches are released.
PROGRAM MIXING [Model Menu]
Speed Mode
This function lets you set the operation switch at the program
mixing master side. The servo can be operated outside the set
curve by switch operation by using this function.
Setting method
1. Set program mixing to the curve mode. The ACT,
SWITCH, etc. setting screen shown above appears.
2. Use the cursor lever to move the cursor to speed mode
selection. Use the dial to select the master mode, and
push the DATA button.
3. Set the in speed and out speed.
4. Set the toggle switch to program mixing master.
5. When the switch set to master is operated, the master
position marker of the curve is shifted at the set servo
speed and the slave function operates along the curve
setting. In the below example, when SW-F is operated,
the slave auxiliary 1 function automatically operates
along the EXP1 curve.
MODEL TYPE [Linkage Menu]
The H-4X mode has been added to the swash types available.
The H-4X swash type is the same as the H-4 type, except the
control points are rotated 45 degrees.
MOTOR MIXING [Model Menu]
Motor mixing was added to airplane model. In addition, when
the power is turned on in the mixing on state, a warning
message is output.
SWASH RING [Model Menu]
This function limits the swash travel to within a fixed range to
prevent damaging of the swash ring by simultaneous operation
of the ailerons and elevators. It is effective in 3D aerobatics
which use a large travel.
Setting method
1. Open the swash ring setting screen by selecting
SWASH RING from the linkage menu.
2. The operating range display area mark shows the stick
position. The vertical direction shows the aileron travel.
When ACT is displayed by pushing the ACT/INH button,
the swash ring function is activated, and a circle is
displayed in the operating range display area. Stick
operation is limited to within the area of this circle.
3. Use the cursor lever to move the cursor to the rate
display. Use the dial to set the rate. The adjustment
range is 50~200%. Adjust the rate to maximum swash
tilt.
THROTTLE LIMITER [Model Menu]
This function sets the upper limit position of the throttle curve.
Limit position adjustment can be assigned to an arbitrary control.
Adjustment range upper and lower limits can be set.
Setting method
1. Open the throttle limiter setting screen by selecting THR
LIMITER from the Model Menu.
2. Use the cursor lever to move the cursor to the ACT/INH
display. Use the dial to select ACT, and push the DATA
button. ON or OFF is displayed.
3. Use the cursor lever to move the cursor to the SWITCH
display and push the DATA button. The switch selection
screen opens. Select the throttle limiter function ON/OFF
switch.
Switch Combination logic
SW1 SW2 AND OR Ex-OR
off off off off off
off on off on on
on off off on on
on on on on off
Speed mode selection
Switched to condition single mode
Logic mode
A
djustment range gauge
Throttle curve
Limit control
Limit control position
Master: SW-F
Operating range
display area
A
CT/INH Rate

- 14 -
4. Use the cursor lever to move the cursor to the
CONTROL display and push the DATA button. The
control selection screen opens. Select the control which
is to adjust the limit position.
5. Use the cursor lever to move the cursor to the HI
RANGE display. Use the dial to set the limit adjustment
range upper limit. An adjustment range gauge is
displayed.
6. Use the cursor lever to move the cursor to the LOW
RANGE display. Use the dial to set the limit adjustment
range lower limit. An adjustment range gauge is
displayed.
PCM-G3 COMMUNICATION MODE
Two types of PCM-G3 communication modes can be selected:
Mode A and Mode B. Mode A is the conventional mode. Mode
B is a mode with enhanced communication quality. Choose the
mode matched to the usage environment.
Setting method
1. Open the frequency setting screen from the Linkage
Menu.
2. Open the modulation type setting screen from the
frequency setting screen.
3. Use the cursor lever to move the cursor to PCM-G3
mode selection.
4. Use the dial to select the mode, and push the DATA
button.
5. Use the cursor lever to move the cursor to PCM G3, and
push the DATA button.
6. A change confirmation screen is displayed. When the
DATA button is pushed, the modulation type is changed
and the Startup screen appears.
Notes:
·When using communications mode B, a receiver
compatible with mode B is necessary. (The R5014DPS is
not mode B compatible.)
·In communication mode B, the servo response to stick
operation is approximately 20% lower than that of mode
A.
PCM1024 CH10
10th channel is added to the PCM1024 mode. DG2 is added on
the function menu at the PCM1024 mode. It is 10th channel
control selection.
Notes:
·The current 9ch receiver must be modified at the
servicing department to implement the 10th channel.
Modulation PPM mode
Added the modulation polarity selection at PPM mode.
Added 12 channels PPM mode.
Setting method
1. Open the frequency setting screen from the Linkage
Menu.
2. Open the modulation type setting screen from the
frequency setting screen.
3. Use the cursor lever to move the cursor to PPM setting
item.
4. Use the dial to select the mode, and push the DATA
button.
CH : 8CH or 12CH, POL : STD or INV, OFFS : N1.5 or
N1.3
OFFS is appeared at only selected 12CH.
5. Use the cursor lever to move the cursor to PPM, and
push the DATA button.
6.A change confirmation screen is displayed. When the
DATA button is pushed, the modulation type is changed
and the Startup screen appears.
Notes:
·The PPM setting of “8CH” and “STD” corresponds to
FUTABA receivers.
PITCH CURVE [Model Menu]
A function which copies a curve containing the pitch trim
(hovering pitch, low side pitch, high side pitch) when the curve
mode is LINE and SPLINE was added.
Setting method
1. Open the pitch curve setting screen.
2. Set the curve mode to LINE or SPLINE.
3. Set the pitch trim (hovering pitch, low side pitch, high
side pitch).
4. Operate the pitch trim (hovering pitch, low side pitch,
high side pitch).
5. Use the cursor lever to move the cursor to COPY, and
push the DATA button for at least 1 second.
Mode selection
Copy function added
Polarity selection
STD
or
INV
CH selection
8CH or 12CH Neutral pulse width selection.
N1.5 or N1.3
(
This a
pp
ears at onl
y
12CH.
)

- 15 -
6. The pitch curve becomes a curve containing the pitch
trim (hovering pitch, low side pitch, high side pitch). A
curve containing the pitch trim (hovering pitch, low pitch,
high pitch) is also displayed at the new pitch curve.
Notes:
·When the curve mode is only "LINE" and "SPLINE", the
COPY button is displayed.
·When the pitch trim is INH or the control of the pitch trim
is not set, the copy function doesn't work.
THROTTLE CURVE [Model Menu]
A function which copies a curve containing the hovering throttle
trim when the curve mode is LINE and SPLINE has been
added.
Setting method
1. Open the throttle curve setting screen.
2. Set the curve mode to LINE or SPLINE.
3. Set the hovering throttle trim.
4. Operate the hovering throttle trim.
5. Use the cursor lever to move the cursor to COPY, and
push the DATA button for at least 1 second.
6. The throttle curve becomes a curve containing the
hovering throttle trim. A curve containing the hovering
throttle trim is also displayed at the new throttle curve.
Notes:
·When the curve mode is only "LINE" and "SPLINE", the
COPY button is displayed.
·When the hovering throttle trim is INH or the control is not
set, the copy function doesn't work.
FUNCTION [Linkage Menu]
When the modulation is “PCM-G3”, the switch channel DG1
and DG2 are added to the function setting.
The control of DG1 and DG2 are able to select.
SERVO REVERSE [Linkage Menu]
When the modulation is “PCM-G3”, the switch channel DG1
and DG2 are added to the servo reverse setting.
Copy function added

- 16 -
Table of contents
Other FUTABA Remote Control manuals

FUTABA
FUTABA T16IZ Ver.2 Manual
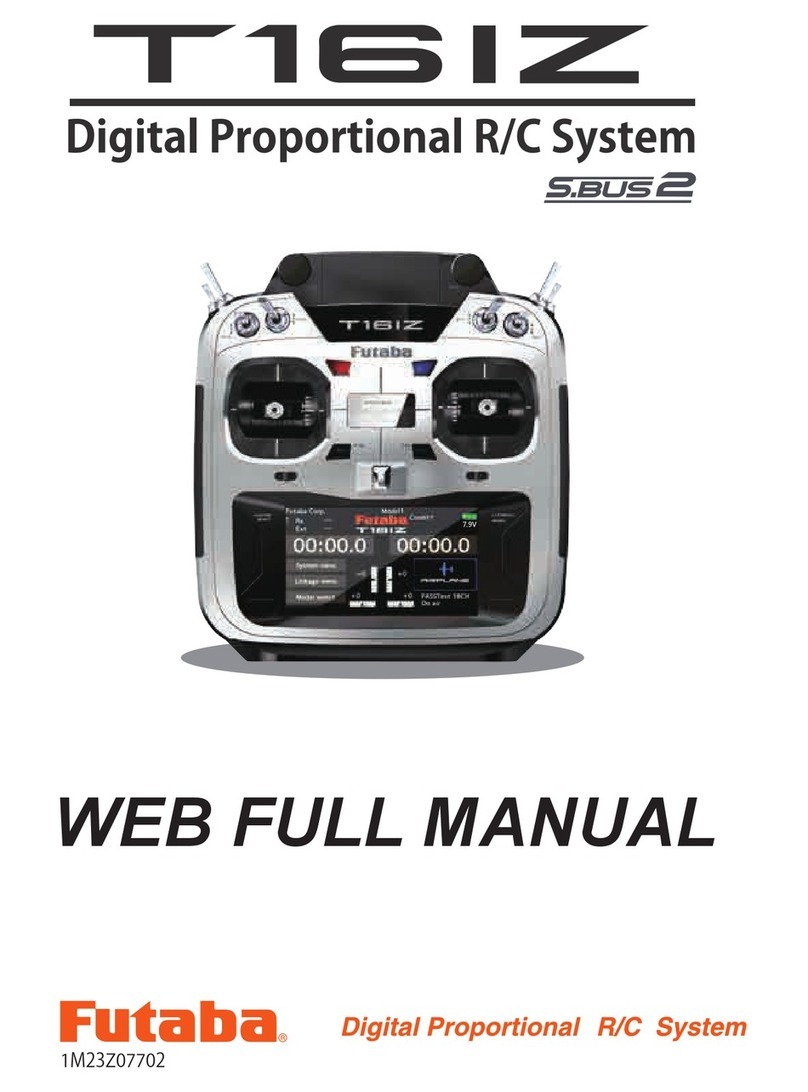
FUTABA
FUTABA 16IZS Installation instructions
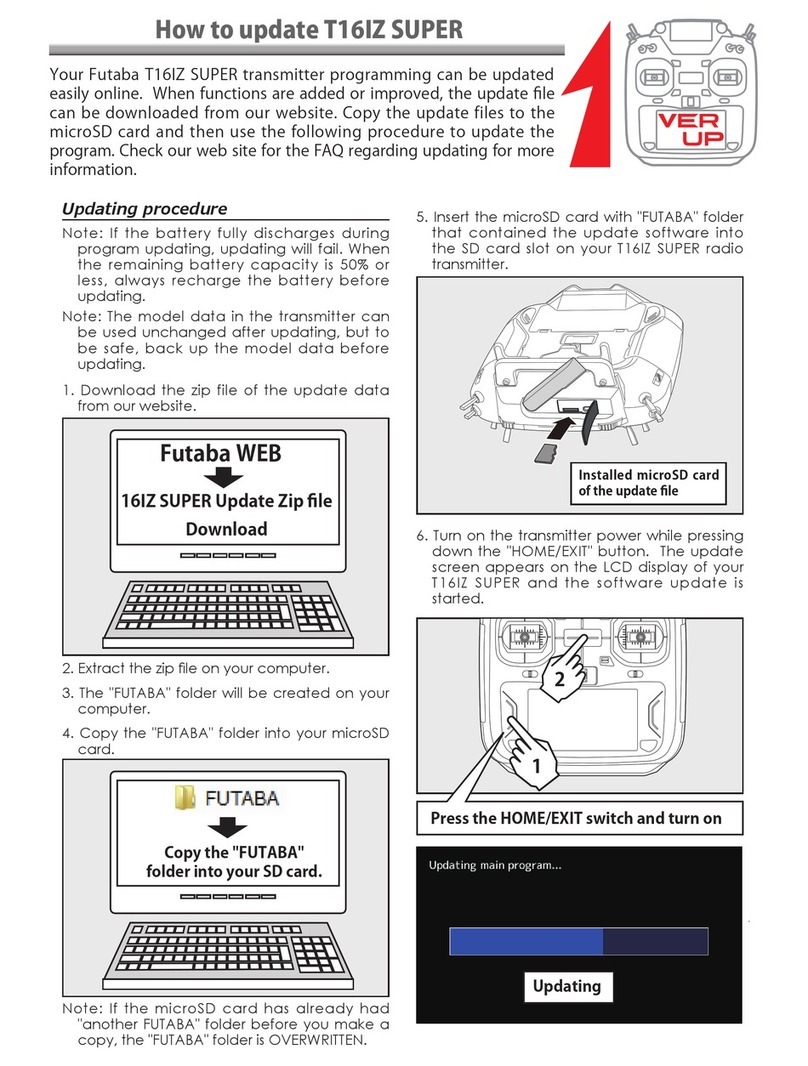
FUTABA
FUTABA T16IZ Installation and user guide
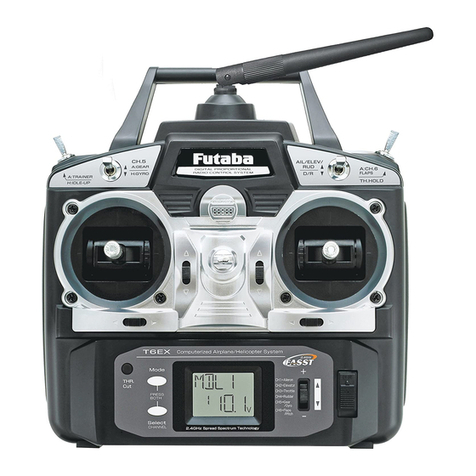
FUTABA
FUTABA 6EX-2.4GHZ User manual
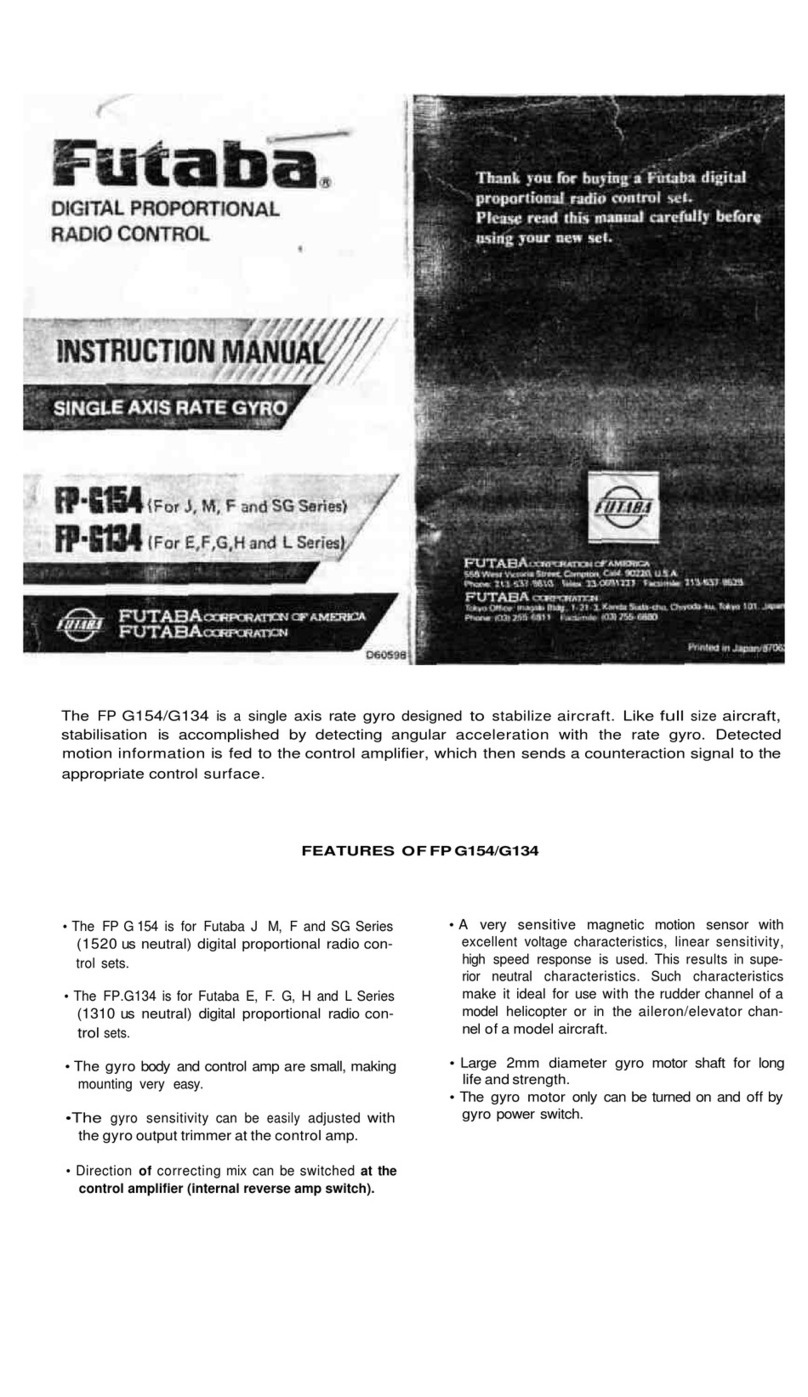
FUTABA
FUTABA FP-G134 User manual

FUTABA
FUTABA T10PX Installation instructions
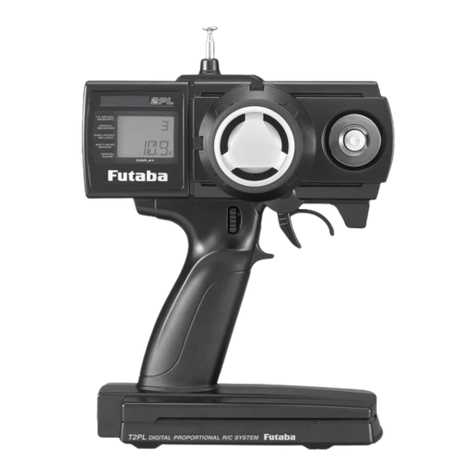
FUTABA
FUTABA 2PL User manual
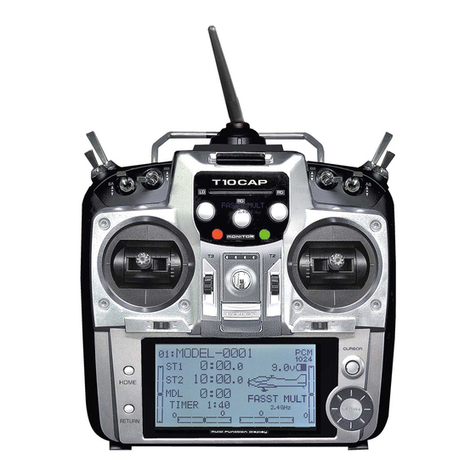
FUTABA
FUTABA 10CAP User manual
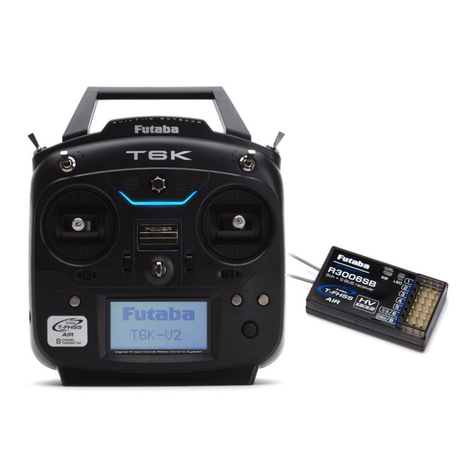
FUTABA
FUTABA T6K Technical manual

FUTABA
FUTABA GV T2PG User manual
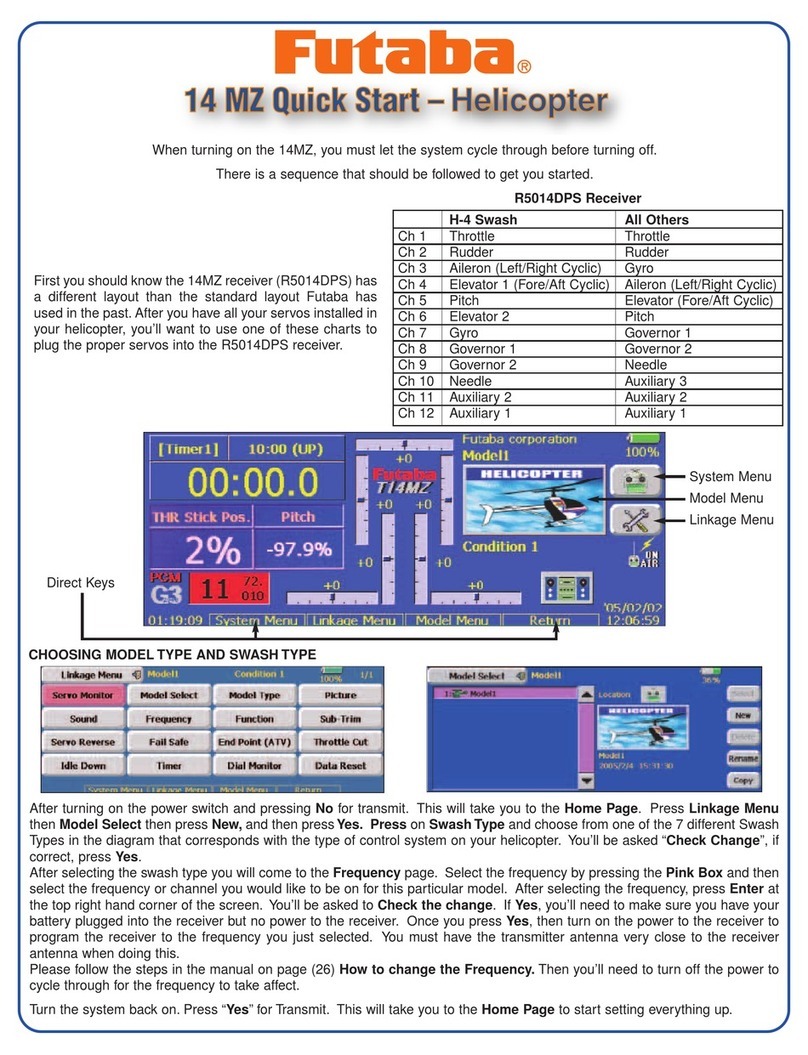
FUTABA
FUTABA 14MZ User manual
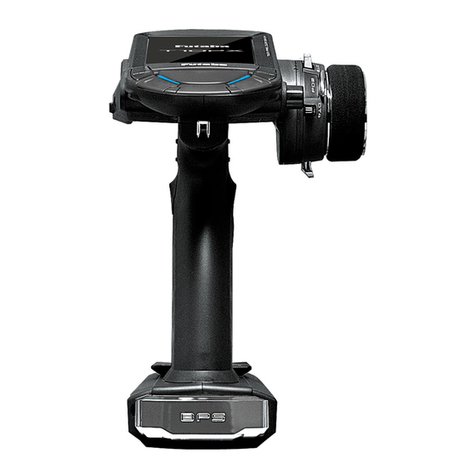
FUTABA
FUTABA T10PX How to use
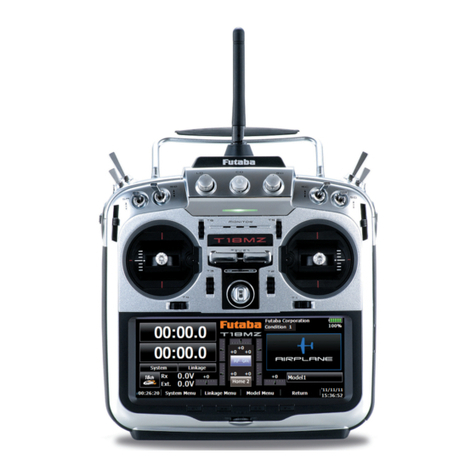
FUTABA
FUTABA T18MZ User manual
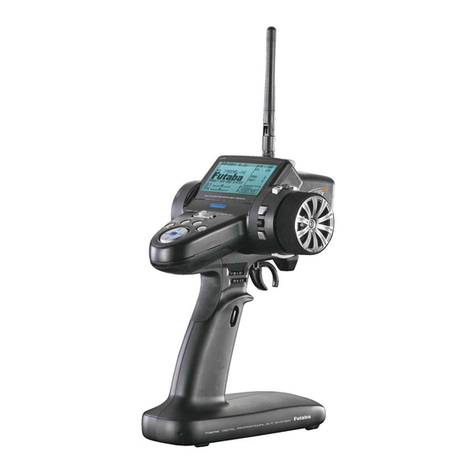
FUTABA
FUTABA 4PK-2.4GHZ User manual
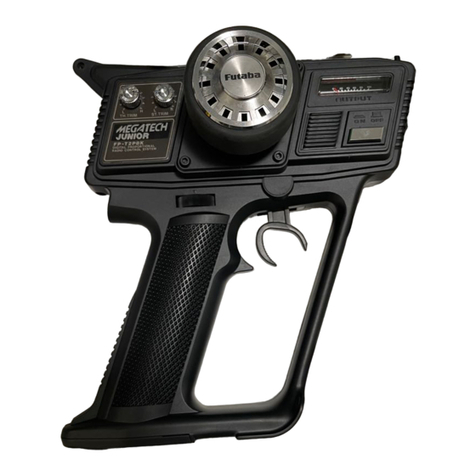
FUTABA
FUTABA FP-2PB User manual
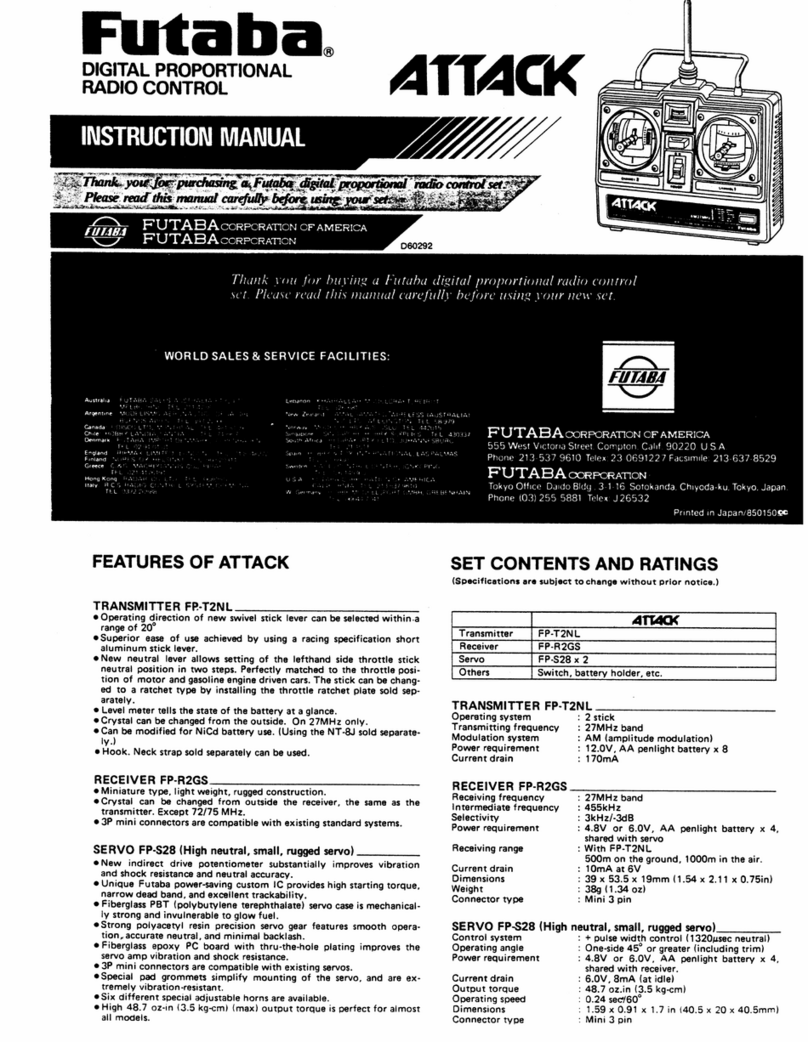
FUTABA
FUTABA Attack FP-R2GS User manual
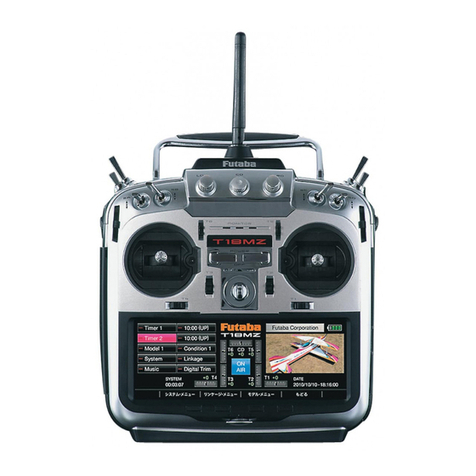
FUTABA
FUTABA T18MZ User manual
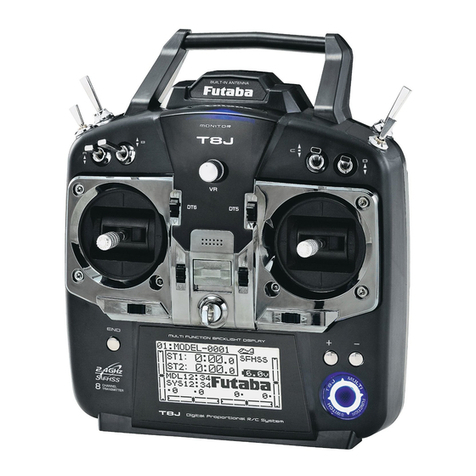
FUTABA
FUTABA T8J-2.4G User manual

FUTABA
FUTABA 2PH User manual
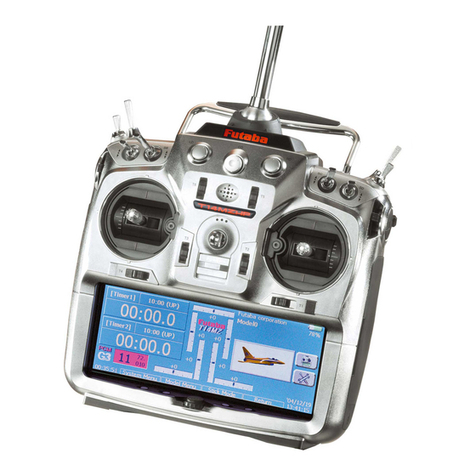
FUTABA
FUTABA 14MZ User manual