GAC ACE295 Series User manual

1
Governors America Corp. © 2020 Copyright All Rights Reserved
ACE295 Series Actuator 3-2020-C PIB4160
ACE295 Series
Integrated Pump Mounted Electric Actuator
The GAC ACE295 Series Electric Actuator is designed
to mount directly on Bosch ‘P’ 9000 and 10000 series
fuel injection pumps in place of the mechanical governor.
The 295 Series actuators provide a high performance
integrated control system with no external linkages or
brackets.
The actuator is designed with two isolated chambers
that eliminates the possibility of any magnetic particles
collecting and jamming the actuator. One chamber
contains the oil and houses the actuator linkage while
the second chamber houses the electromagnetic
components.
The 295 Series typically outlasts the life of a diesel
engine. Camshaft bearing retainer kits and position
feedback sensor equipped versions are also available.
1
2
INTRODUCTION
SPECIFICATIONS
PERFORMANCE
Force 13.2 lbf (58.7 N)
Operating Stroke 0.79 in +/- 0.04 in (20 mm +/- 1 mm)
POWER INPUT
Operating Voltage 24 V DC
Normal Operating Current 2.4 A
Maximum Current Continuously Rated 4.5 A
ENVIRONMENT
Operating Temperature Range -40 °F to +185 °F (-40 °C to +85 °C)
Relative Humidity up to 100 %
All Surface Finishes Fungus Proof and Corrosion Resistant
PHYSICAL
Dimensions See Section 3, INSTALLATION DIAGRAM
Weight 11 lbf (4.9 kgf)
Mounting Directly on ‘P’ 9000 and ‘P’ 10000 Bosch fuel injection pumps in place of the
mechanical governor. Gasket supplied with kit.
MATING HARDWARE
Wiring Harness - ACE295 CH1215
Wiring Harness - ACE295F-24 CH1515

2
Governors America Corp. © 2020 Copyright All Rights Reserved
ACE295 Series Actuator 3-2020-C PIB4160
3INSTALLATION DIAGRAM
[X.X]
X.X
[mm]
in
Units
The following are general instructions for removing the existing governor and should not be used without a qualied professional.
Oil must be removed from the mechanical governor.
1. Remove the rear housing of the existing mechanical governor and disconnect the governor assembly from the fuel rack.
2. Remove the yweight assembly.
3. Remove the intermediate governor housing, this leaves only the rack and camshaft protruding from the housing.
4. Remove the oil hex plug located on the pump between the fuel rack and the camshaft to allow any oil which leaks from the fuel rack to
drain back into the pump.
4INSTALLATION
If the pump is equipped with a mechanical governor, it must be removed. GAC recommends that the modication be done
by a qualied fuel injection shop.
PREPARING THE FUEL PUMP
NOTE
1. Remove the four cap screws and carefully remove the gasket from the
cover on the actuator to access the lever assembly used to connect the
actuator to the fuel rack. Save the screws and gasket.
2. Remove the set screw from the bracket. DO NOT LOOSEN LEVER OR
REMOVE LEVER FROM THE SHAFT.
ACTUATOR LEVER
ASSEMBLY
CONNECTING ACTUATOR LINKAGE TO FUEL RACK
An overspeed shutdown device, independent of the governor system, should be used to prevent loss of engine control which
may cause personal injury or equipment damage. Do not rely exclusively on the governor system electric actuator to prevent
overspeed. A secondary shuto device, such as a fuel solenoid must be used.
NOTE:
Dimensions shown are nominal.
Final dimensions may vary slightly.

3
Governors America Corp. © 2020 Copyright All Rights Reserved
ACE295 Series Actuator 3-2020-C PIB4160
3. From the KT295 kit, select the P9 (15 mm) or P10 (14 mm) fuel rack adapter and
the socket head screw. Align the fuel rack adapter over the connecting screw
hole of the fuel control rack. Apply Loctite Thread Retention Compound to the
socket head screw. Using the socket head screw, connect adapter to fuel control
rack and torque to 7.8 - 8.4 N∙m (5.8 - 6.2 lbf∙ft).
4. Connect the linkage extension from kit KT295 to the end of the fuel rack adapter
using the M5-16 hex-head screw and washer, and torque to 4.6 - 5.1 N∙m (3.4 -
3.8 lbf∙ft).
NOTE The linkage is preset to a specic length and locked. Any adjustment
of rack travel must be made using the slot on the actuator lever. This
is completed after the actuator is mounted to the fuel pump.
5. Attach the actuator to the pump by rst cleaning the mounting surfaces of the
actuator and the pump. Remove the gasket and screws from kit KT296. The
gasket ts between the actuator and pump.
6. Apply a small amount of high temperature gasket sealant, such as RTV silicone,
to the pump side of the gasket. Align the gasket on the pump side to get the most
complete coverage.
7. Place the rear mounting side of actuator over the pump rack and linkage on the
bearing retainer plate. Attach the actuator to the pump using two of the four
screws and washers included with KT295, through the upper mounting holes.
Tighten screws securely to 9 N∙m (6.6 lbf∙ft) taking care to compress the gasket
evenly.
8. Push the lower mounting bar against the bearing retainer plate and tighten the
two bottom nuts onto the pump studs to 10 N∙m (7.3 lbf∙ft).
NOTE Make sure the linkage attached to the fuel rack moves freely when
moved from shut o to full fuel.
9. If necessary for access, loosen the two hex nuts that hold the front set screw
bracket to gain access to the lever area.
10. Pull the linkage fully away from the pump. Push the linkage 1 mm toward the
pump and attach it to the slot on the actuator lever using the M5x20 screw, two
at washers and the locking nut from kit KT295. Torque the lock nut to 4.6 - 5.1
N∙m (3.4 - 3.8 lbf∙ft).
11. The fuel rack should be 1 mm or less away from its internal physical stop. The
zero fuel stop of the system will now be provided by the actuator instead of inside
the fuel pump.
12. Manually move the actuator lever and linkage through its full range of motion. No
binding should be noticed. The stop plate on the linkage must not contact the
inside of the housing.
13. If loosened for access, torque the two screws holding the mounting bar to the
actuator to 20 N∙m.
14. Use the set screw and nut on the set screw bracket to adjust the maximum fuel
position on the actuator lever. The set screw and lock nut is adjusted to limit the
travel of the fuel rack.
15. After the maximum fuel delivery has been adjusted reinstall the saved gasket,
four cap screws and cover.
16. Access the set screw as required through the actuator cover.
4INSTALLATION (CONTINUED)
KT295 CONTENTS
KT296 CONTENTS
SET SCREW

4
Governors America Corp. © 2020 Copyright All Rights Reserved
ACE295 Series Actuator 3-2020-C PIB4160
Fabricate a cable harness to connect the speed control unit to the actuator. The
recommended wire size of the cable harness is 18 gauge (1 mm2) for a 24 V DC
system.
Larger gauge wire is necessary for cable lengths greater than 12 ft (4 m).
The engine should be equipped with an independent shut down device to prevent overspeed which can cause equipment damage or
personal injury.
If the governor system fails to operate, make the following tests at the actuator mounted connector while moving the actuator through
its stroke.
6TROUBLESHOOTING
5WIRING
The EC1000 or EC1010 electrical connector that mates with the actuator must be pre-wired in a conguration to match the system voltage.
Cable Harnesses CH1215, and CH1515 are available from GAC. Refer to MATING HARDWARE in section 2 ,SPECIFICATIONS.
The ACB295F-24 version of the actuator includes a rack position sensor. A GAC
speed control unit that includes fuel management electronics is required to interface
with this sensor. See your speed controller installation manual for wiring information.
HARNESS
PIN SIGNAL
1 + 5 V DC
2 GND
4 OUT
ACE295-24
ACE295F-24
CABLE HARNESS
TROUBLESHOOTING TEST
1. Energize the actuator to full fuel with the speed controller.
2. Manually move the actuator through its range using the stop lever. No binding or sticking should occur.
3. If the actuator passes these tests, the problem is elsewhere in the system. Refer to the troubleshooting section of the speed control unit’s
installation manual.
Other GAC Controllers manuals
Popular Controllers manuals by other brands
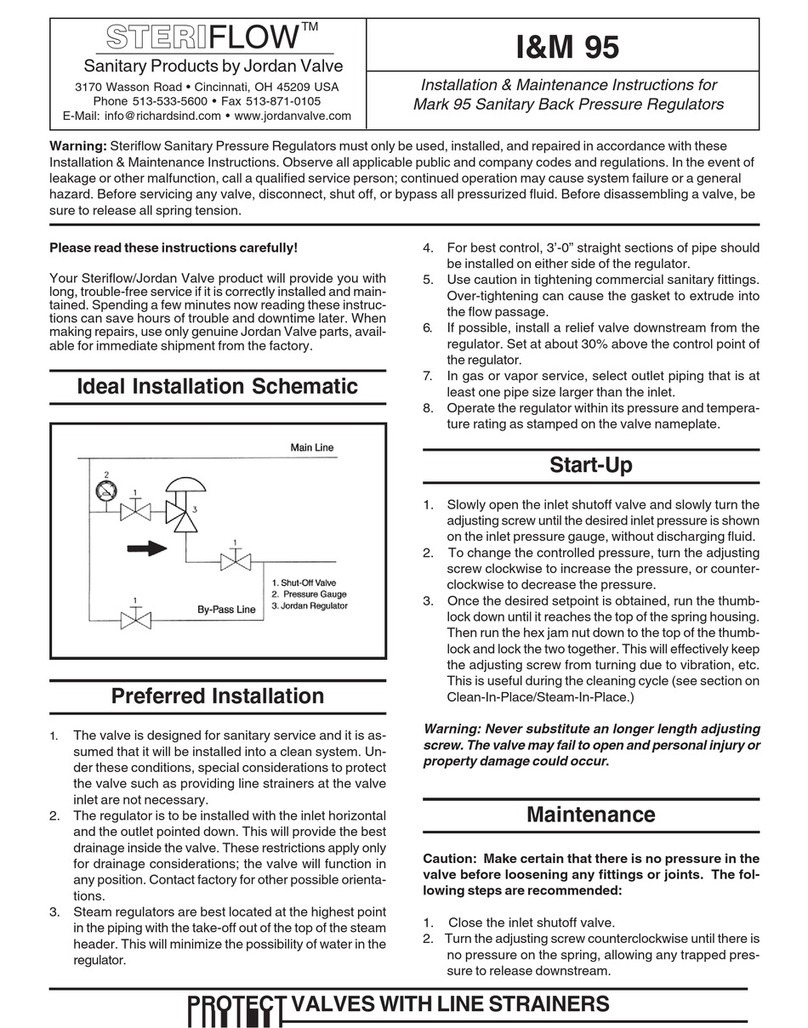
STERIFLOW
STERIFLOW Mark 95 Series Installation & maintenance instructions
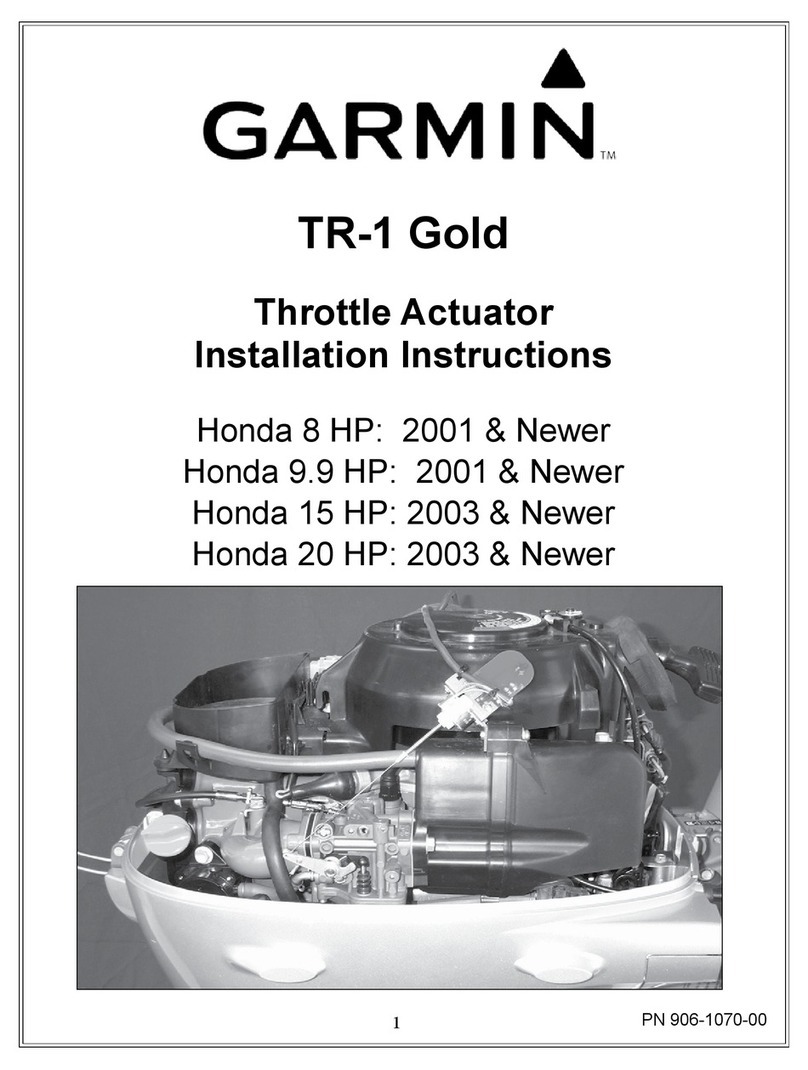
Garmin
Garmin TR-1 Gold installation instructions
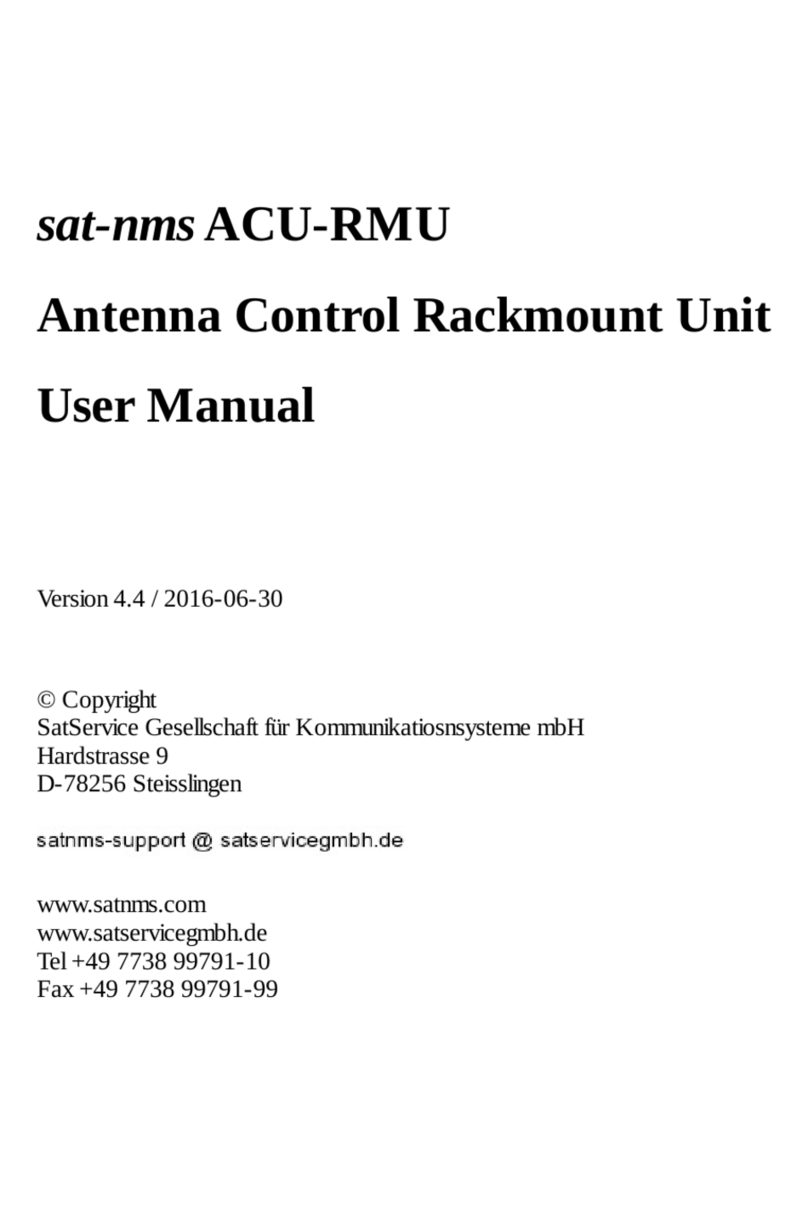
SatService
SatService sat-nms ACU-RMU user manual
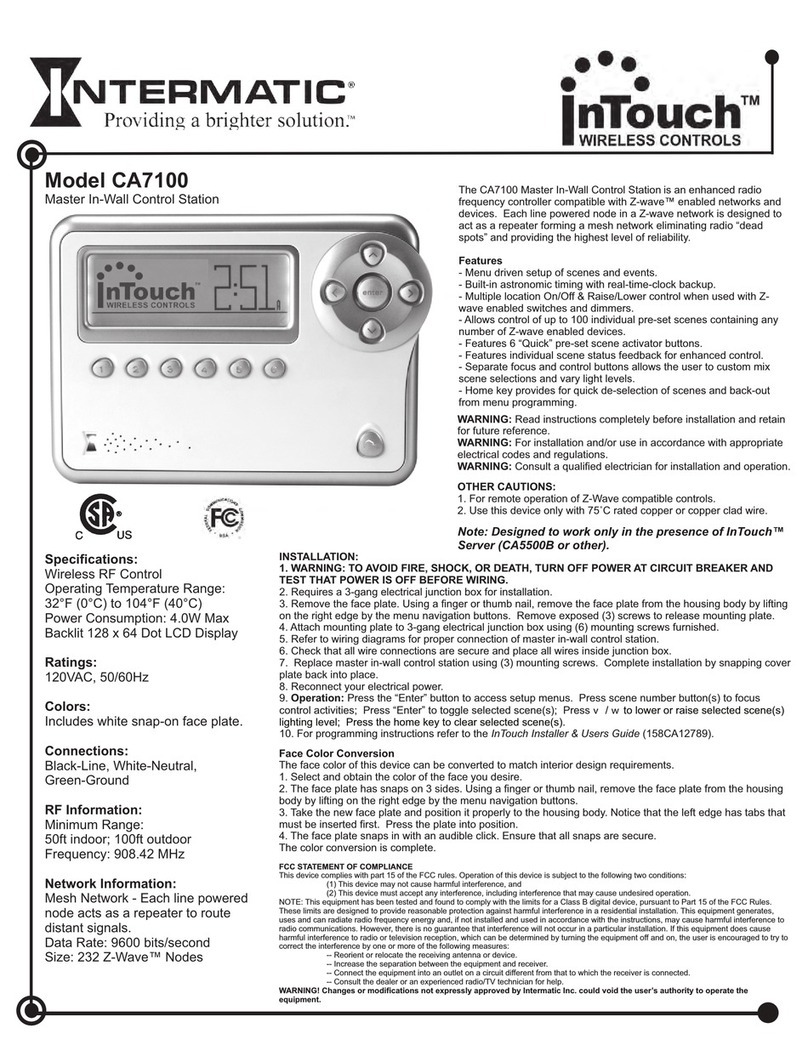
Intermatic
Intermatic InTouch CA7100 user guide

American Megatrends
American Megatrends MegaRAC MG9071 datasheet
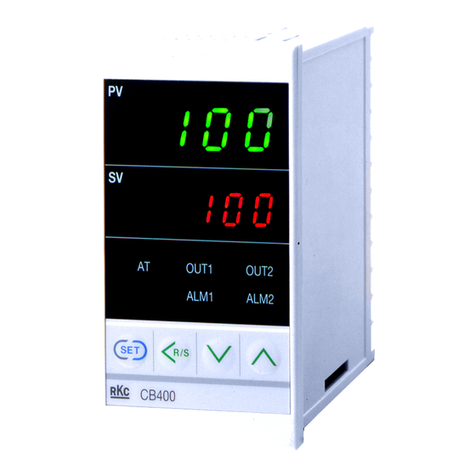
RKC INSTRUMENT
RKC INSTRUMENT CB100 Series Initial setup manual
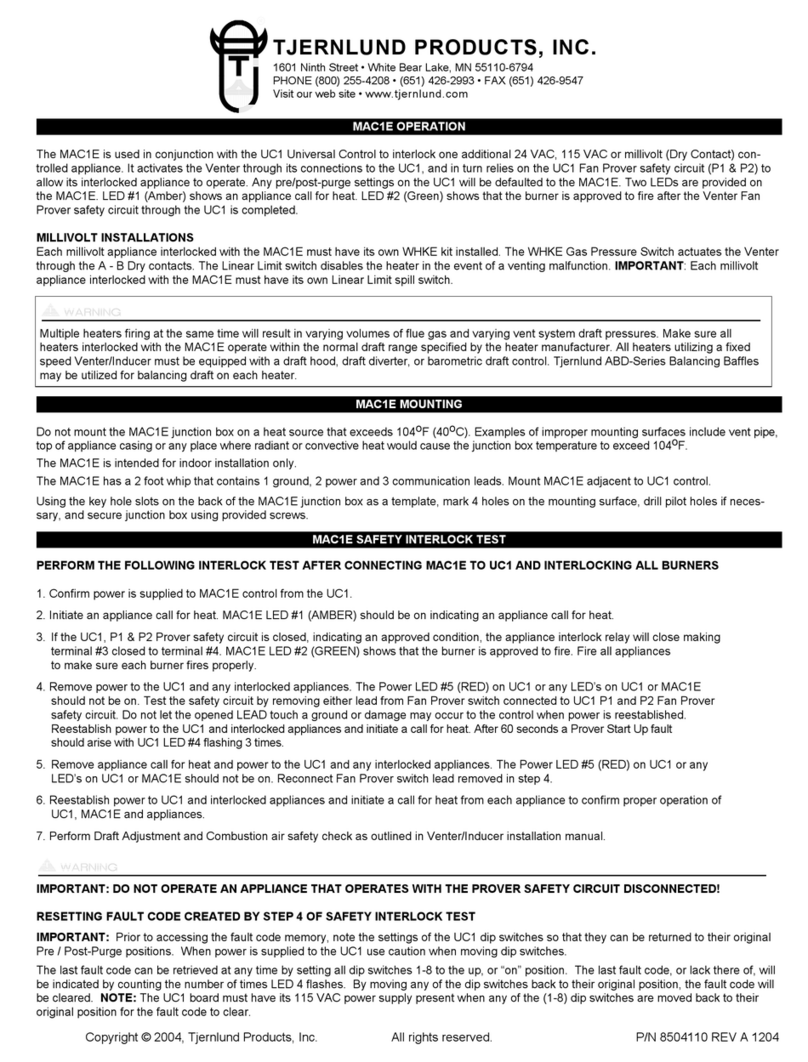
TJERNLUND
TJERNLUND MAC1E CONTROL (COMPATIBLE WITH UC1 CONTROL) 8504110 REV A... Operating and mounting instructions

STEINEL
STEINEL NightmatIQ manual
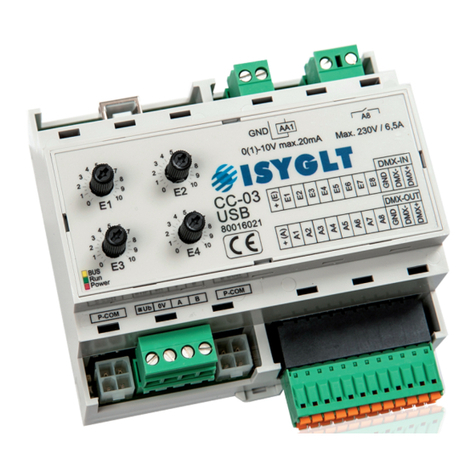
ISYGLT
ISYGLT CC-03-USB Technical Data/Instruction Manual
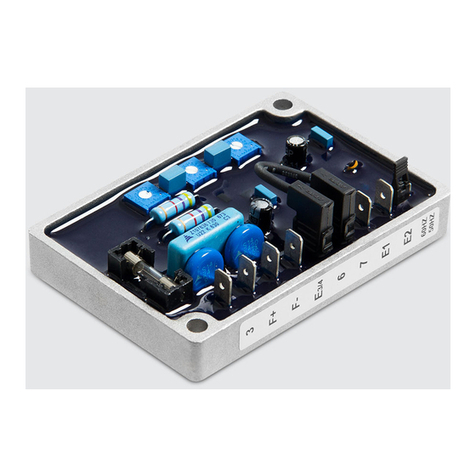
REACIONA
REACIONA AVR-A-OPT-02 Installation and operation manual

CLA-VAL
CLA-VAL 90G-21 Installation, operation & maintenance manual
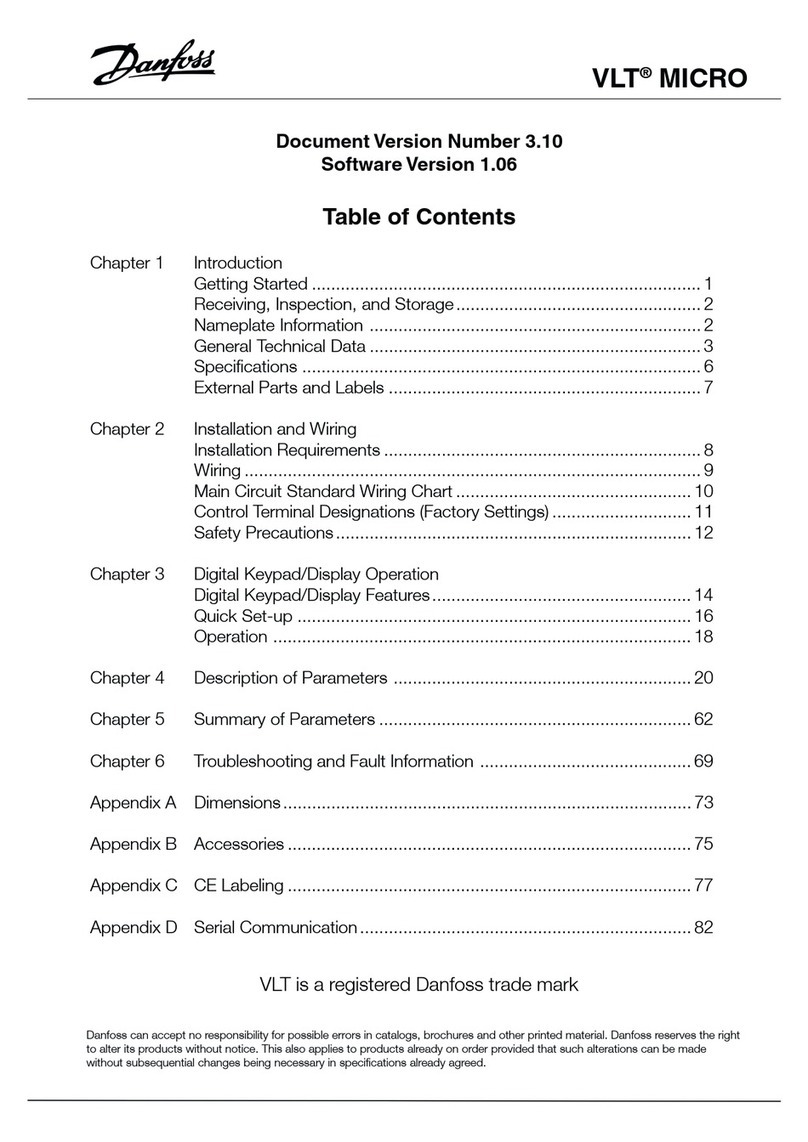
Danfoss
Danfoss 176F7300 manual