GHM Delta OHM HD404 Series User manual

Operating manual
Low pressure transmitters
H
D404… series
www.deltaohm.com
English
Keep for future reference.

HD404… - 2-V1.2
TABLE OF CONTENTS
1INTRODUCTION.................................................................................................... 3
2TECHNICAL CHARACTERISTICS ............................................................................ 5
3INSTALLATION ..................................................................................................... 8
3.1 ELECTRICAL CONNECTIONS ................................................................................... 10
3.2 EXAMPLE OF CONNECTION TO A PITOT TUBE................................................................ 11
3.3 EXAMPLES OF CONNECTION WITH HD9022 INDICATOR/REGULATOR ................................... 12
4CONFIGURATION................................................................................................ 13
4.1 CONFIGURATION OF THE MODELS WITH ANALOG OUTPUT (HD404T…) ................................ 13
4.2 CONFIGURATION OF THE MODELS WITH RS485 OUTPUT (HD404ST…)............................... 15
4.3 NOTES ON THE CONFIGURATION OF THE MODELS WITH SR OPTION..................................... 17
4.4 ERROR MESSAGES ON DISPLAY............................................................................... 17
5MODBUS-RTU PROTOCOL (HD404ST…) .............................................................. 18
6INSTRUMENT STORAGE ...................................................................................... 20
7SAFETY INSTRUCTION........................................................................................ 20
8ACCESSORIES ORDERING CODES ....................................................................... 21

HD404… - 3-V1.2
1INTRODUCTION
The series of HD404…transmitters is able to measure relative pressures with refer-
ence to the atmosphere or differential in the range:
•from 50 to 1000 Pa (from 0.2” H2O to 4” H2O) for the versions with analog output;
•250 Pa / 1000 Pa / 100 mbar for the versions with RS485 Modbus RTU output.
The transmitters use a “micromachined” temperature compensated silicon sensor that
has an excellent linearity, repeatability and stability over time.
The sensor signal is amplified and converted, depending on the model, into a standard
current (4-20 mA) or voltage (0-10 V) analog output, or into a digital RS485 Modbus
RTU output, and can therefore be transmitted over long distances with a high noise
immunity.
In the models with analog output it is possible to choose, via a dip switch, between
two measurement ranges in order to select the optimal scale for each application.
An optional auto-zero circuit (AZ) periodically equalizes the differential pressure at the
sensor input and corrects the offset; the transmitters equipped with this circuit are in-
sensitive to the mounting position. In addition, the auto zero circuit compensates the
sensor aging and deviation of the zero with temperature changes, eliminating the
maintenance.
The display option (L) is available, in which the pressure is visualized on a 4-digit dis-
play in the chosen measurement unit.
The “square root” version (SR) is especially useful if the transmitter is connected to a
Pitot or Darcy tube, as the output is directly proportional to the speed of airflow. The
SR version with L option also allows displaying, in addition to the pressure measured,
the calculated airflow speed. It is possible to set the coefficient of the Pitot or Darcy
tube used and the parameters for the calculation of the speed (air flow temperature,
barometric pressure, differential static pressure in the duct). In the models with ana-
log output it is possible to set the full scale speed for the output.
The instruments are factory calibrated and ready for use.

HD404… - 4-V1.2
Models with analog output
HD404T
“” = pressure output
SR = speed output (only Gversions)
“” = without LCD
L= with LCD
“” = without auto-zero circuit (only HD404T3… and HD404T4…)
AZ = with auto-zero circuit
D = differential pressure –f.s.…+f.s.
G = relative pressure with respect to the atmosphere 0…+f.s.
Nominal full scale (f.s.)
1P = 100 Pa
2P = 250 Pa
3P = 500 Pa
4P = 1000 Pa
1M = 10 mmH
2
O
2M = 25 mmH2O
3M = 50 mmH2O
4M = 100 mmH2O
1I = 0.4” H
2
O
2I = 0.8” H2O
3I = 2” H2O
4I = 4” H2O
Models with RS485 Modbus-RTU output
HD404ST
“” = pressure output
SR = speed output
“” = without LCD
L= with LCD
“” = without auto-zero circuit (only HD404ST4… and HD404ST5…)
AZ = with auto-zero circuit
Nominal full scale (f.s.)
2 = -250 … +250 Pa
4 = -1000 … +1000 Pa
5 = -100 … +100 mbar

HD404… - 5-V1.2
2TECHNICAL CHARACTERISTICS
Sensor Piezoresistive
Measuring range See tables 2.1 and 2.2
Resolution 0.1 Pa for HD404ST2…
0.5 Pa for f.s. up to 500 Pa (except Hd404ST2…)
1 Pa for f.s. 1000 Pa
0.1 mbar for HD404ST5…
0.05 mmH2O for f.s. up to 50 mmH2O
0.1 mmH2O for f.s. 100 mmH2O
0.002” H2O for f.s. up to 4” H2O
0.01 m/s (only SR versions)
Accuracy See table 2.1
Long-term stability See table 2.1
Output •HD404T…: Active analog 0…10 Vdc (RLmin = 10 kΩ
) or 4…20 mA
(RLmax = 500 Ω)
•HD404ST…: Digital RS485 Modbus-RTU
Response time •HD404T… with dip-switch set to FAST:
0.125 s in pressure mode
1 s in speed mode (only SR versions)
•HD404T… with dip-switch set to LOW:
Configurable 1, 2 or 4 s (default 2 s)
•HD404ST…:
Configurable 0.125, 1, 2 or 4 s (default 2 s)
Overpressure limit 50 kPa
Connection to PC •HD404T…:
RS232 serial port
Can be connect to a USB port by using the optional CP27 adapter
•HD404ST…:
Can be connect to a USB port by using the optional RS48 adapter
Zero calibration Automatic for the versions with AZ option
Compatible media Only air and non-aggressive dry gases
Power supply •HD404T…: 24 Vac ±10% o 18…40 Vdc
•HD404ST…: 12…30 Vdc
Absorption •HD404T…: < 1 W @ 24 Vdc
•HD404ST…: < 100 mW @ 12 Vdc
Pressure connection Nickel-plated brass, Ø 6 mm
Electrical connections Screw terminal block, max 1.5 mm2 , PG9 cable gland
Operating conditions -10...+60 °C (-5…+50 °C for the models with AZ option), 0…95% RH
Storage temperature -20...+70 °C
Housing dimensions 80 x 84 x 44 mm
Protection degree IP65

HD404… - 6-V1.2
TAB. 2.1: pressure measuring ranges, accuracy and long term stability
MODEL MEASURING RANGE ACCURACY (1)
(@ 0…+50 °C) LONG-TERM
STABILITY (2)
LOW HIGH AZ NO AZ AZ NO AZ
MODELS WITH ANALOG OUTPUT (HD404T…)
Pa (HD404TxP…)
HD404T1PGAZ… 0...50 0...100
±(0.8% measure
+ 0.5)
-
≤±0.2
-
HD404T2PGAZ… 0...100 0...250
HD404T3PG… 0...250 0...500 ±1% f.s. nom. ≤±8
HD404T4PG… 0...500 0...1000
HD404T1PDAZ… ±50 ±100 - -
HD404T2PDAZ… ±100 ±250
HD404T3PD… ±250 ±500 ±1% f.s. nom. ≤±8
HD404T4PD… ±500 ±1000
mmH2O(HD404TxM…)
HD404T1MGAZ… 0...5 0...10
±(0.8% measure
+ 0.05)
-
≤±0.02
-
HD404T2MGAZ… 0...10 0...25
HD404T3MG… 0...25 0...50 ±1% f.s. nom. ≤±0.8
HD404T4MG… 0...50 0...100
HD404T1MDAZ… ±5 ±10 - -
HD404T2MDAZ… ±10 ±25
HD404T3MD… ±25 ±50 ±1% f.s. nom. ≤±0.8
HD404T4MD… ±50 ±100
inchH2O(HD404TxI…)
HD404T1IGAZ… 0...0.2 0...0.4
±(0.8% measure
+ 0.002)
-
≤±0.0008
-
HD404T2IGAZ… 0...0.4 0...1
HD404T3IG… 0...1 0...2 ±1% f.s. nom. ≤±0.04
HD404T4IG… 0...2 0...4
HD404T1IDAZ… ±0.2 ±0.4 - -
HD404T2IDAZ… ±0.4 ±1
HD404T3ID… ±1 ±2 ±1% f.s. nom. ≤±0.04
HD404T4ID… ±2 ±4
MODELS WITH RS485 MODBUS-RTU OUTPUT (HD404ST…)
HD404ST2AZ… ±250 Pa ±(0.8% measure
+ 0.5) Pa ≤±0.2 Pa
HD404ST4… ±1000 Pa ±1% f.s. ≤±8 Pa
HD404ST5… ±100 mbar ±(0.8% measure
+ 0.005) mbar ±1% f.s. ≤±0.002
mbar ≤±0.08
mbar
(1) f.s. nom. (nominal) = full scale of “HIGH” measuring range.
(2) Long-term stability refers to 1 year.

HD404… - 7-V1.2
TAB.2.2: Speed full scale in the models with SR option
MODEL MAX SPEED MEASURABLE (3)
(m/s)
ANALOG OUTPUT
DEFAULT FULL SCALE
(m/s)
LOW HIGH
HD404TxP…SR
HD404T1PGAZ…SR 9.06 12.82 10
HD404T2PGAZ…SR 12.82 20.27 20
HD404T3PG…SR 20.27 28.67 25
HD404T4PG…SR 28.67 40.55 40
HD404TxM…SR
HD404T1MGAZ…SR 8.98 12.70 10
HD404T2MGAZ…SR 12.70 20.08 20
HD404T3MG…SR 20.08 28.39 25
HD404T4MG…SR 28.39 40.16 40
HD404TxI…SR
HD404T1IGAZ…SR 9.05 12.80 10
HD404T2IGAZ…SR 12.80 20.24 20
HD404T3IG…SR 20.24 28.62 25
HD404T4IG…SR 28.62 40.48 40
(3) The maximum speed measurable depends on various parameters. Table 2.2 shows the maxi-
mum speed measurable with the factory default values:
oK = 1.0 Tube coefficient
oT = 16.0 °C Air flow temperature
oPatm = 1013.25 mbar Barometric pressure
oPs = 0 Differential static pressure, equal to the difference between the absolute static
pressure inside the duct and the barometric pressure. Ps is zero if the duct is open (in
contact with the atmosphere); Ps can be different from zero if the duct is closed.
In the models HD404T…, the serial command SV provides the maximum speed measurable as
a function of the parameters setting, while the command CS allows setting the full scale
speed of the analog output.
The following graphs show the change of the maximum measurable speed value
(normalized to 1 for T=16.0 °C and Patm=1013.25 mbar) with the change of the
temperature and barometric pressure.
Change of the max. speed with the temperature at constant barometric pressure

HD404… - 8-V1.2
Change of the max. speed with the barometric pressure at constant temperature
DIMENSIONS (mm)

HD404… - 9-V1.2
3INSTALLATION
By opening the lid, 3 mm diameter holes are available so to allow securing the base of
the instrument directly to a panel or to the wall.
Internally there are:
•the terminal header for connecting the power supply and the output;
•the RS232 serial connector (COM AUX, except HD404ST…);
•the dip switches for quick configuration.
•The CAL ZERO button.
Models with active analog output
(HD404T…)
Models with digital RS485 output
(HD404ST…)

HD404… - 10 -V1.2
The instruments can be mounted in any position, but typically they are fixed on a ver-
tical wall with the pressure inputs facing down.
The deviation of the zero due to the mounting position can be corrected by using the
CAL ZERO button.In the models with AZ option, an auto-zero circuit periodically au-
tomatically equalizes the differential pressure at the input of the sensor and corrects
the offset due to the mounting position or sensor aging.
To manually calibrate the zero, disconnect both the tubes from the + and – pressure
inputs, then proceed as follows:
•press CAL ZERO until the red LED starts flashing;
•when the red LED turns off, the zeroing procedure is completed: reconnect the
tubes to the pressure inputs.
In the models without AZ option, it is recommended to follow the auto zero procedure
at least once a year under normal operating conditions.
In models with AZ option, the zeroing is performed hourly. During the zeroing, which
takes about 4 seconds, the output and the display remain frozen at the last measured
value.
3.1 ELECTRICAL CONNECTIONS
Current analog output
Voltage analog output
RS485 connection
In the RS485 connection, the instruments are connected in a sequence through a
shielded cable with twisted pair for signals and a third wire for the common. Line ter-
mination must be set at the two network ends.
The maximum number of devices that can be connected to the RS485 line (Bus) de-
pends on the load characteristics of the devices to be connected. The RS485 standard
requires that the total load does not exceed 32 unit loads. The load of an HD404ST…
transmitter is equal to ¼ of unit load. If the total load is greater than 32 unit loads,
Power supply
Power supply
Power supply
Other sensors with
RS485 output
Termination
Termination
PLC, data logger or
RS485/USB or RS485/RS232
converter for PC

HD404… - 11 -V1.2
divide the network into segments and add a signal repeater between a segment and
the successive one. Line termination should be applied at both ends of each segment.
The instrument has a built-in line termination that can be connected or removed
through a short jumper placed next to the terminal block. If the instrument is the last
or the first device of a network group, connect the termination placing the short
jumper between the “RT” and “120 ohm” indications. If the instrument is not at the
end of a network group, remove the termination placing the short jumper between the
“RT” and “OPEN” indications.
The cable shield must be connected to both line ends. The cable should have the fol-
lowing features:
•Characteristic impedance: 120 ohm
•Capacity: less than 50pF/m
•Resistance: less than 100 ohm/km
•Gauge: 0.22 mm2(AWG24) at least
The cable maximum length depends on baud rate and cable characteristics. Typically,
the maximum length is 1200 m. The data line must be kept separated from any power
lines in order to prevent interferences on the transmitted signal.
3.2 EXAMPLE OF CONNECTION TO A PITOT TUBE
Transmitter with SR option connected to a Pitot tube

HD404… - 12 -V1.2
3.3 EXAMPLES OF CONNECTION WITH HD9022 INDICATOR/REGULATOR
4…20 mA current output
0…10 Vdc voltage output
Power supply
Power supply

HD404… - 13 -V1.2
4CONFIGURATION
4.1 CONFIGURATION OF THE MODELS WITH ANALOG OUTPUT (HD404T…)
The transmitter can be configured by using the dip switches on the circuit board and
via the serial communication port COM AUX.
Configuration via dip switches:
Dip switches RANGE: selection of the LOW or HIGH range for the analog output.
Dip switches FAST/SLOW: selection of the response time for the analog output. In
FAST mode the response time is 0.125 s in pressure measurement mode and about 1 s
in speed measurement mode, while in SLOW mode the response time is selectable to 1,
2 or 4 s by means of the S1, S2 or S4 serial commands respectively. SLOW mode is rec-
ommended if there are conditions of turbulence or disruption of air flow.
Configuration via the serial port COM AUX:
In order to modify the settings, please proceed as follows:
•Connect the serial COM AUX output of the transmitter to the RS232 port (via the
RS27 cable) or USB (via the cable CP27) of the PC. If you use the CP27 cable,
install the USB drivers on your PC.
•On the PC, run a serial communication software, set the baud rate to 115200
and the communication parameters to 8N1.
•To change the display configuration or the operating mode (commands O3E,
O3D, O4E, O4D, O5E, O5D, O6E, O6D, O7E, O7D, O8E, O8D) it is necessary to
send the CAL START command to enter the configuration mode. It is not neces-
sary to send the CAL START command to change the parameters related to the
speed measurement (tube coefficient, temperature, pressure, full scale for the
analog output).
•Send the commands given in table 4.1 to set or read the configuration parame-
ters of the transmitter (the commands that affect the speed or the flow have effect
only in the versions with SR option).
TAB. 4.1: serial commands (models with analog output)
Command
Response
Description
Sn
&n sec
Set the response time of index n for the analog outputs:
n=1 ⇒1 s, n=2 ⇒2 s, n=4 ⇒4 s
S?
n sec
Reads the response time set for the analog outputs.
O3E
&
Shows alternately speed (or flow) and pressure on display .
O3D
&
Disables the alternating display of speed (or flow) and pressure.
O4E
&
Automatic change of speed resolution on display (0.1 ⇔0.01) de-
pending on the measured value.
O4D
&
Fixed centesimal speed resolution on display.
O5E
&
Sets ft/s as speed unit of measurement on display.
Note: the symbol ft/s does not appear on display.
O5D
&
Sets m/s as speed unit of measurement on display (default).
O6E
Model
description
Enables “Debimo” sensor.
O6D
Model
description
Enables Pitot or Darcy sensor (default).

HD404… - 14 -V1.2
Command
Response
Description
O7E
Model
description
Enables flow mode.
O7D
Model
description
Enables speed mode (default).
O8E
Model
description
Sets m3/min as flow unit of measurement .
O8D
Model
description
Sets L/s as flow unit of measurement.
CK n.n…
&
Sets the Pitot or Darcy tube coefficient to the value n.n…
The value must be between 0.6 and 1.2 (default = 1).
RK
n.nnnnn|
Reads the value of the Pitot or Darcy tube coefficient set in the
transmitter.
D nnnn
nnnn mmq |
Sets and reads the duct section in mm2.
CD n.n
&
Sets the “Debimo” blades coefficient to the value n.n (default=0.8).
CB
nnnn.nn…
&
Sets the barometric pressure to the value nnnn.nn… mbar. The val-
ue must be between 500 and 1500 mbar (default = 1013.25 mbar).
RB
nnnn.nnn|
Reads the value of the barometric pressure in mbar set in the
transmitter.
CT n…
&
Sets the airflow temperature in tenths of °C (default = 160 ⇒16.0
°C).
The value must be between -999 (⇒-99.9°C) and 2000 (⇒200.0°C).
RT
n…|
Reads the value of the temperature, in tenths of °C, set in the
transmitter.
CP nnnn…
&
Sets the differential static pressure (see note 2) in mbar (default = 0).
RP
nnnn…|
Reads the value of the differential static pressure set in the
transmitter.
CS nnnn
&
In speed mode, sets the full scale speed, in hundredths of m/s, for
the analog output (default = see table). The m
ax settable value is
10000 (⇒100.00m/s). In flow mode, sets the full scale flow in L/s
or m3/min.
RS
nn.nn|
In speed mode, reads the speed full scale value, in m/s, for the
analog output. In flow mode, reads the flow full scale value, in L/s
or m3/min, for the analog output.
SV
nn.nn|
In speed mode, prints the max measurable speed as a function of
the transmitter full scale pressure and values set for the parame-
ters. The value is in the speed unit of measurement set in the
transmitter. In flow mode, prints the max measurable flow in L/s or
m3/min.
Note: To exit the configuration mode after sending the CAL START command, send
the CAL END command (the transmitter automatically exits the configuration mode af-
ter 5 minutes from the last command sent).

HD404… - 15 -V1.2
4.2 CONFIGURATION OF THE MODELS WITH RS485 OUTPUT (HD404ST…)
RS485 Modbus address: each transmitter of the network is univocally identified by
an address between 1 and 247. Transmitters having the same address shall not
be present in the network. The transmitter Modbus address is equal to the sum of
the value set with the dip-switches 2…6 (value settable from 0 to 31) and the value set
with the serial command WA (value settable from 1 to 216, default = 1). By setting a
dip-switch to ON (upwards), the following values are added to the address:
Dip-switch 2 Dip-switch 3 Dip-switch 4 Dip-switch 5 Dip-switch 6
ON 16 8 4 2 1
OFF 0 0 0 0 0
Example: if the dip-switches 2 and 4 are set to ON, and the dip-switches 3,5 and 6
are set to OFF, the value set with the dip-switches is 16+4=20. If the value set with
the serial command WA is 1 (default value), the transmitter Modbus address is
20+1=21.
The dip-switches can be set even if the transmitter is powered, and the change is ef-
fective immediately.
Configuration via the RS485 serial port:
In order to change the settings, proceed as follows:
•Connect the transmitter RS485 output to the PC RS232 (through a RS485/RS232
converter) or USB (through a RS485/USB converter, for example the RS48 ca-
ble) port. If a RS485/USB converter is used, install in the PC the related USB
drivers.
•To enable the configuration mode, set the dip-switch 1 (the one closest to the
terminal block) to ON (upwards), then power the transmitter.
Note: the dip-switch 1 can be changed from OFF to ON even when the instru-
ment is powered; in this case it is however necessary, after setting the dip-
switch to ON, to press briefly (less than 0.5 seconds) the CAL ZERO button to
enable the configuration mode (the transmitter model information appears on
display, if present). Alternatively, power cycle the transmitter.
•On the PC, run a serial communication software, set the baud rate to 57600 and
the communication parameters to 8N1.
•Send the CAL START command (the command is required to change the config-
uration; to read the value of the parameters, the command is not required).
•Send the commands given in table 4.2 to set or read the configuration parame-
ters of the transmitter (the commands that affect the speed or the flow have effect
only in the versions with SR option.
TAB. 4.2: serial commands (models with RS485 Modbus-RTU output)
Command
Description
AVGn
Set the response time of index n for the measurement:
n=0 ⇒0.125 s, n=1 ⇒1 s, n=2 ⇒2 s, n=4 ⇒4 s
AVG?
Reads the response time set for the measurement.
DU0
Shows pressure in Pa on display.
DUF
Shows flow in l/min on display (only in the versions with SR option).
DUV
Shows speed in m/s on display (only in the versions with SR option).
OPT3E
Shows alternately speed (or flow) and pressure on display.

HD404… - 16 -V1.2
Command
Description
OPT3D
Disables the alternating display of speed (or flow) and pressure.
OPT4E
Automatic change of speed resolution on display (0,1 ⇔0,01) depending on the
measured value.
OPT4D
Fixed centesimal speed resolution on display.
OPT6E
Enables “Debimo” sensor.
OPT6D
Enables Pitot sensor (default).
WK n.n…
Sets the Pitot or Darcy tube coefficient to the value n.n…
The value must be between 0.6 and 1.2 (default = 1).
RK
Reads the value of the Pitot or Darcy tube coefficient set in the transmitter.
WD n.n…
Sets the “Debimo” sensor coefficient to the value n.n…
The value must be between 0.6 and 1.2 (default = 1).
RD
Reads the value of the “Debimo” sensor coefficient set in the transmitter.
WS nnnn
Sets the duct section in mm2.
RS
Reads the duct section in mm2.
WB nnnn.nn…
Sets the barometric pressure to the value nnnn.nn… hPa.
The value must be between 100 and 2000 hPa (default = 1013.25 hPa).
RB
Reads the value of the barometric pressure in hPa set in the transmitter.
WT nn.n
Sets the airflow temperature in °C.
The value must be between -20.0°C and +60.0°C.
RT
Reads the value of the temperature in °C set in the transmitter.
WP nnnn…
Sets the differential static pressure (see note 2) in Pa (default = 0).
RP
Reads the value of the differential static pressure set in the transmitter.
Auto-zero
ZFn
Sets the auto-zero interval of index n (only in the versions with AZ option):
n=0 ⇒disabled n=1 ⇒5 min n=2 ⇒10 min n=3 ⇒20 minn=4 ⇒30 min
n=5 ⇒60 min
Default = 60 min
ZF?
Reads the auto-zero interval set (only in the versions with AZ option)
Modbus parameters
WA n...n
Sets the Modbus base address to the value n...n.
The value must be between 1 and 216 (default = 1).
Warning: the actual Modbus address of the transmitter is equal to the
base address set with this command plus the value set with the dip-
switches.
Note: in the reply to the command, the previous actual address appears; the new
address will appear in the replies to the next commands.
BAUD r...r
Sets the Modbus Baud Rate to the value r...r.
The acceptable values are 9600 and 19200 (default = 19200).
If the command is sent without the parameter r…r, the current setting is obtained.
PAR p
Sets the Modbus communication parameters of index p:
p=O ⇒8O1 p=N ⇒8N2 p=E ⇒8E1
If the command is sent without the index p, the current setting is obtained
(default = 8E1).
Note: the replies of the HD404ST… transmitters always start with the address of the
connected transmitter. For example, sending the RB command to a transmitter with
Modbus address 1, the reply is “001: ATM pressure = 1013.250 hPa”.

HD404… - 17 -V1.2
Note: To exit the configuration mode after sending the CAL START command, send
the CAL END command (the transmitter automatically exits the configuration mode af-
ter 5 minutes from the last command sent).
4.3 NOTES ON THE CONFIGURATION OF THE MODELS WITH SR OPTION
Resolution of the speed measurement: The speed is calculated from the pressure
measure through a quadratic relationship. For this reason, the speed resolution is
lower for low pressure values measured, and the change of the speed measurement
on the display appears rather discontinuous if the fixed centesimal resolution is used.
If a more uniform speed change on display is desired, enable the automatic speed
resolution change as a function of the measured value (serial command O4E in the
models HD404T…, serial command OPT4E in the models HD404ST…).
Flow measurement: the transmitter can be set in flow measurement mode (serial
command O7E in the models HD404T…, serial command DUF in the models
HD404ST…). The flow is calculated from the speed measurement and the duct section
set. The flow mode is available both with Pitot and "Debimo" sensors.
4.4 ERROR MESSAGES ON DISPLAY
Undr: The measured value is less than the minimum measurable value.
OvEr: The measured value exceeds the maximum measurable value.
CAL Error: It appears at the end of the zero calibration if the maximum offset value
possible to be corrected is exceeded.

HD404… - 18 -V1.2
5MODBUS-RTU PROTOCOL (HD404ST…)
To operate with the Modbus-RTU protocol be sure that the dip-switch 1 (the one
closest to the terminal block) is set to OFF (downwards). The dip-switch can be set to
OFF even if the transmitter is powered, and the change is effective immediately.
Below is the list of registers:
TAB. 5.1: Input Registers
Address Description Format
3 Pressure in tenths of Pa (only HD404ST2...) 16-bit integer
4 Pressure in Pa (only HD404ST2... and HD404ST4...) 16-bit integer
5 Pressure in daPa (only HD404ST4... and HD404ST5AZ...) 16-bit integer
6 Pressure in hPa (only HD404ST4 without AZ option and
HD404ST5...) 16-bit integer
7 Pressure in kPa (only HD404ST5...) 16-bit integer
8 Pressure in hundredths of mmH2O (only HD404ST2... and
HD404ST4AZ...) 16-bit integer
9 Pressure in tenths of mmH2O (only HD404ST2... and HD404ST4...) 16-bit integer
10 Pressure in mmH2O (only HD404ST4... and HD404ST5AZ...) 16-bit integer
11 Pressure in thousandths of inchH2O (only HD404ST2... and
HD404ST4AZ...) 16-bit integer
12 Pressure in hundredths of inchH2O (only HD404ST4...) 16-bit integer
13 Pressure in tenths of inchH2O (only HD404ST4 without AZ option
and HD404ST5...) 16-bit integer
14 Pressure in inchH2O (only HD404ST5...) 16-bit integer
15 Pressure in thousandths of mmHg (only HD404ST4AZ...) 16-bit integer
16 Pressure in hundredths of mmHg (only HD404ST4...) 16-bit integer
17 Pressure in tenths of mmHg (only HD404ST4 without AZ option
and HD404ST5AZ...) 16-bit integer
18 Pressure in mmHg (only HD404ST5...) 16-bit integer
19 Pressure in thousandths of PSI (only HD404ST4 without AZ option) 16-bit integer
20 Pressure in hundredths of PSI (only HD404ST4 without AZ op-
tion and HD404ST5...) 16-bit integer
21 Speed in hundredths of m/s (only models with SR option) 16-bit integer
22 Speed in hundredths of ft/s (only models with SR option) 16-bit integer
23 Flow in l/s (only models with SR option) 16-bit integer
24 Flow in l/min (only models with SR option) 16-bit integer
25 Flow in m3/min (only models with SR option) 16-bit integer
26 Error register 16-bit integer
Note: Reading a register not available for a particular model returns the value -32768
(0x8000).
Note: If the pressure measurement is negative, the speed and flow registers return
zero.

HD404… - 19 -V1.2
Error register
The bits of the error register signal, if set to 1, anomalies in the measurement. The bit
0 (the less significant one) indicates a measurement over-range of the transmitter.
The bit 1 indicates whether the measurement is less than the minimum measurable
(under-range). The bits 2 and 3 indicate sensor errors.
TAB. 5.2: Holding Registers
Address Description Format
100 Modbus base address (from 1 to 216)
Warning: the actual Modbus address of the transmitter is
equal to the base address set in this register plus the val-
ue set with the dip-switches.
16-bit integer
101 Modbus Baud Rate
Acceptable values: 3 (
⇒
9600) and 4 (
⇒
19200)
16-bit integer
102 Modbus communication parameters
Acceptable values: 1 (
⇒
8N2), 2 (
⇒
8E1) and 4 (
⇒
8O1)
16-bit integer
The Modbus Holding Registers allow setting the same Modbus parameters that can be
set via the serial commands WA, BAUD and PAR. Use the 06h (Write Single Register)
and 03h (Read Holding Registers) function codes to write and read respectively the con-
tent of the registers.
To make the changes of the Holding Registers content active and permanent,
write the hexadecimal value FF00 in the Coil Register with address 2 by using
the 05h function code (Write Single Coil).
TAB. 5.3: Coils
Address Description
2 Activation and permanent storage of the Holding Registers content changes.

HD404… - 20 -V1.2
6INSTRUMENT STORAGE
Instrument storage conditions:
•Temperature: -20...+70 °C.
•Humidity: less than 90 %RH no condensation.
•In storage, avoid places where:
•humidity is high;
•the instrument is exposed to direct sun radiation;
•the instrument is exposed to a high temperature source;
•high vibration levels are present;
•the instrument may be exposed to vapor, salt and/or corrosive gas.
7SAFETY INSTRUCTION
General safety instructions
The instrument has been manufactured and tested in accordance with the safety
standard EN61010-1:2010 “Safety requirements for electrical equipment for meas-
urement, control and laboratory use” and has left the factory in perfect safety tech-
nical conditions.
The instrument proper operation and operating safety can be ensured only if all
standard safety measures as well as the specific measures described in this manual
are followed.
The instrument proper operation and operating safety can be ensured only in the cli-
matic conditions specified in this manual.
Do not use the instruments in places where there are:
•Corrosive or flammable gases.
•Direct vibrations or shocks to the instrument.
•High-intensity electromagnetic fields, static electricity.
User obligations
The instrument operator shall follow the directives and regulations below that refer to
the treatment of dangerous materials:
•EEC directives on workplace safety.
•National law regulations on workplace safety.
•Accident prevention regulations.
Table of contents
Other GHM Transmitter manuals
Popular Transmitter manuals by other brands
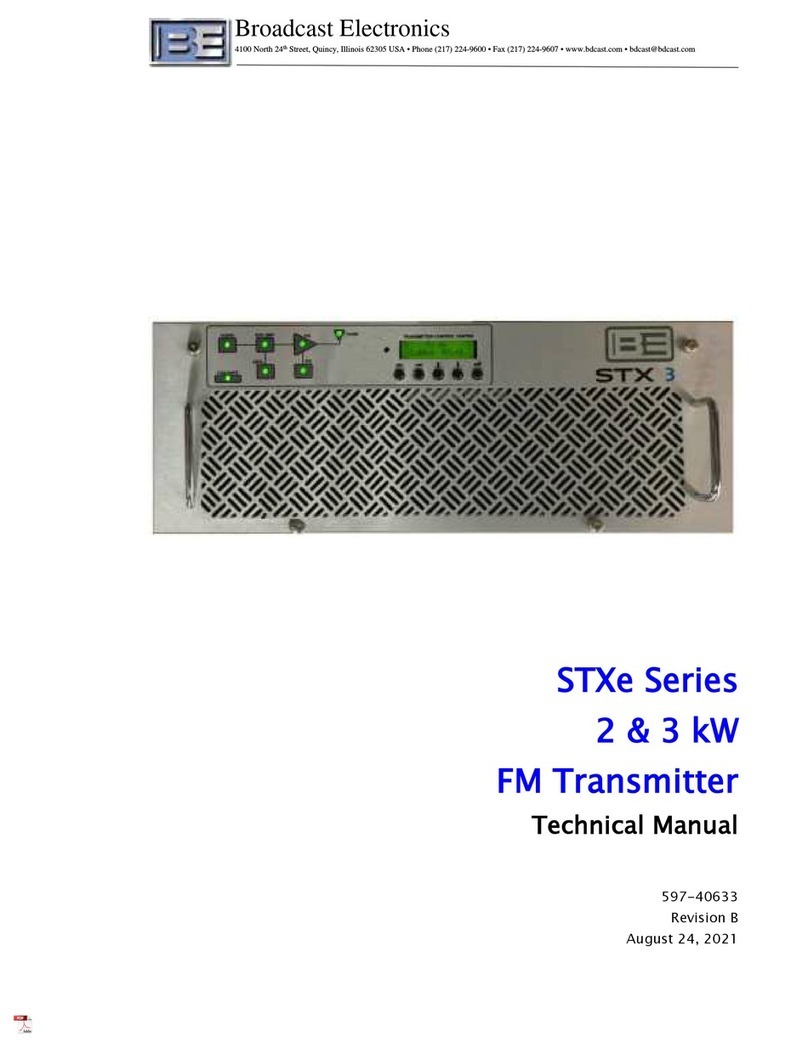
Broadcast Electronics
Broadcast Electronics STXe Series Technical manual

Hollyland
Hollyland Mars 4K quick guide
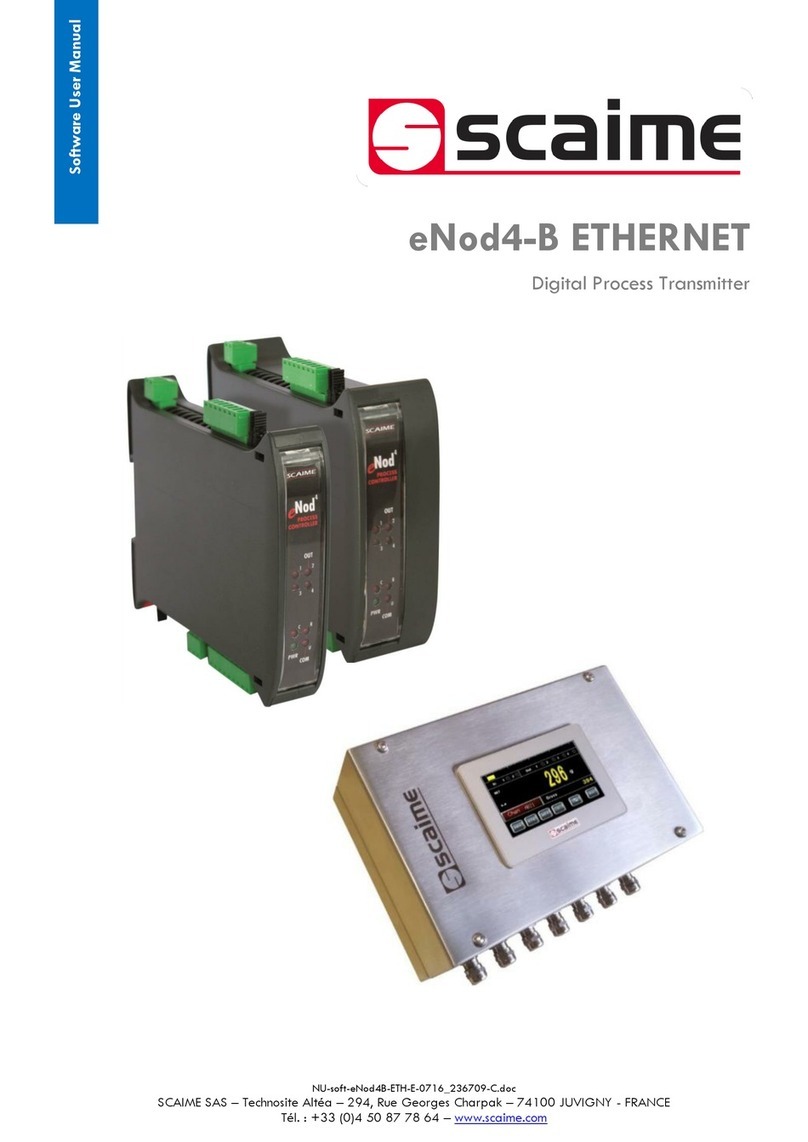
Scaime
Scaime eNod4-B user manual
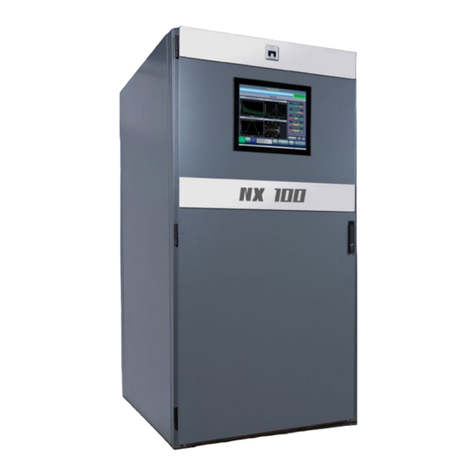
Nautel
Nautel NX100 installation manual
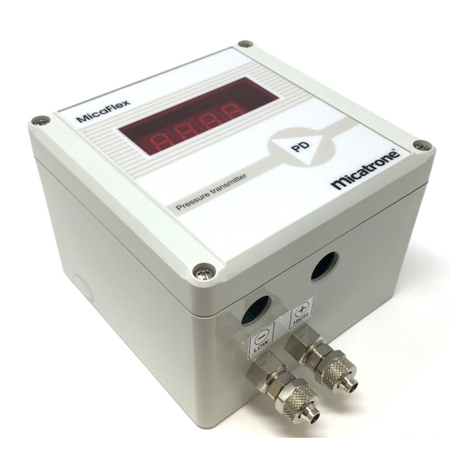
Micatrone
Micatrone Micaflex PD ver 4 Installation & operation manual

Endress+Hauser
Endress+Hauser Proline 500 PROFIBUS PA Brief operating instructions