GMP EXCELMASTER-1600 User manual

USER'S GUIDE
EXCELMASTER-1600
Before operating the unit, please read this manual thoroughly and retain it for future reference.

2
TABLE OF CONTENT
Cover 1
Table of Content 2
Important Safety Instructions 3
Specifications 4
Pre-Installation 5
Installation 6
ControlGuide 7
Power ON/ OFF 7
ControlPanelDisplay 7
ControlPanel 7
Rewinder Selection Switch 8
Upper Rewinder Direction Switch 9
Lower Rewinder Direction Switch 9
Rear Control Switch 9
FootSWEnable 9
Features Guide
E-Stop 10
Safety Shield Interlock Latch 10
Safety Shield 10
FeedTable 10
HeatRollers 10
PullRollers 10
RollerHandle 11
Idler Bar 11
ChillIdler 11
CoolingFans 11
FilmShaft 11
Lower Shaft Lock 11
Rewind Shaft 12
Rewind Tube 12
Unwind/ Rewind Tension 12
Core Adaptors 12
Rewind Adaptors 12
Rear Table 12
Rear Slitter 12
FilmWeb 12
NipPoint 12
Foot Switch 12
Print Unwind Basket 12
Options 12
Separator Bar 12
Rewind Kit 12
Film Loading and Threading 13
Load a Roll of Film 13
LoadingTopThermalFilm 14
LoadingTopPSAFilm 14
Loading Top Mount Adhesive 15
LoadingBottomThermalFilm 15
LoadingBottomPSAFilm 16
Loading Bottom Mount Adhesive 16
Threading Card Procedure 17
StartLaminating 18
Tacking New Film To Existing Film 19
To Unweb The Laminator 20
ClearingAFilmJam 20
Applications 21
Pre-Coating Boards 21
Using Rear Rollers 21
Mounting Pre-Coated Boards 21
SingleSidedLamination 22
Creating a Decal 22
Mounting a Decal 22
PSAEncapsulation 23
ThermalEncapsulation 23
Micronex 23
The Art Of Lamination 24
Basic Rules 24
FilmTension 24
Heat 25
Output 25
Maintenance 26
Troubleshooting Guide 27

3
IMPORTANT SAFETY INSTRUCTIONS
YOUR SAFETY AS WELL AS THE SAFETY OF
OTHERS IS IMPORTANT TO GBC. IN THIS
INSTRUCTION MANUAL AND ON THE
PRODUCT, YOU WILL FIND IMPORTANT
SAFETYMESSAGES REGARDINGTHE
PRODUCT. READTHESE MESSAGES
CAREFULLY. READ ALL OF THE INSTRUC-
TIONSAND SAVE THESE INSTRUCTIONS FOR
LATER USE.
THE SAFETY ALERT SYMBOL PRE-
CEDESEACH SAFETY MESSAGEIN
THIS INSTRUCTION MANUAL. THE SYMBOL
INDICATES A POTENTIAL PERSONAL
SAFETY HAZARD TO YOU OR OTHERS, AS
WELL AS PRODUCT OR PROPERTY DAMAGE.
THEFOLLOWING WARNINGSARE FOUND
UPONTHIS PRODUCT.
ADVERTENCIA
!
Ries
g
o de cho
q
ue
eléctrico
No abra:
Adentro no ha
y
piezas reparables
por el usuario.
Mantenimiento
solamente por
personal
calificado
A TTE N TI ON
!
Ris
q
ue de
secousse
électri
q
ue.
Ne pas ouvrir.
Pas de pièces
réparables par
l'utilisateur.
Entretien
seulement par
personnel
q
ualifié.
WARNING
!
Electrical shock
hazard.
Do not open.
No user
serviceable
parts inside.
Refer servicin
g
to
q
ualified service
personnel.
THIS SAFETY MESSAGE MEANS THAT YOU
COULDBE SERIOUSLYHURT OR KILLEDIF
YOUOPEN THEPRODUCT ANDEXPOSE
YOURSELF TO HAZARDOUS VOLTAGE.
ADVERTENCIA
!ATTENTION
!CAUTION
!
RODILLOS
CALIENTES.
PUNT O DE
PINCHAMIENTO.
Mantener manos
y
ropa a distancia.
ROULEAUX
CHAUDS.
POINT DE
PINCEMENT.
Tenir mains et
vêtements àl'écart.
HOT ROLLS.
PINCH POINT.
Keep hands and
clothin
g
awa
y
.
THIS SAFETY MESSAGE MEANS THAT YOU
COULDBEBURNED ANDYOURFINGERS AND
HANDSCOULD BETRAPPED AND CRUSHED
INTHE HOT ROLLERS. CLOTHING,JEWELRY
AND LONG HAIR COULD BE CAUGHT IN THE
ROLLERS AND PULL YOU INTO THEM.
ADVERTENCIA
!ATTENTION
!CAUTION
!
NAVAJA FILOSA.
Mantener manos y
dedos a distancia.
LAME COUPANTE.
Tenir mains et
doigts àl'écart.
SHARP BLADE.
Keep hands and
clothing away.
THIS SAFETY MESSAGE MEANS THAT YOU
COULD CUT YOURSELF IF YOU ARE NOT
CAREFUL.
WARNING: THE SAFETY ALERT
SYMBOLPRECEDES EACH SAFETY
MESSAGE IN THIS INSTRUCTION MANUAL.
THE SYMBOL INDICATES A POTENTIAL
PERSONAL SAFETY HAZARD TO YOU OR
OTHERS, AS WELL AS PRODUCT OR
PROPERTYDAMAGE.
WARNING: DO NOT ATTEMPT TO
SERVICE OR REPAIR THE LAMINATOR.
WARNING: DO NOT CONNECT THE
LAMINATOR TO AN ELECTRICAL
SUPPLY OR ATTEMPT TO OPERATE THE
LAMINATOR UNTIL YOU HAVE COMPLETELY
READ THESE INSTRUCTIONS. MAINTAIN
THESEINSTRUCTIONS IN ACONVENIENT
LOCATIONFOR FUTUREREFERENCE.
INJURY, THE FOLLOWING SAFETY
PRECAUTIONSMUST BE OBSERVEDIN THE
INSTALLATION AND USE OF THE LAMINATOR.
General
Keep hands, long hair, loose clothing, and articles such
as necklaces or ties away from the front of the heat
and pull rollers to avoid entanglement and entrapment.
The heat rollers can reach temperatures over 300°F.
Avoid contact with the heat rollers during operation or
shortly after power has been removed from the
laminator.
Keep hands and fingers away from the path of the
sharp film cutter blade located at the film exit.
Do not use the laminator for other than its intended
purpose.
Avoid moving the laminator on uneven floor surfaces.
Never tilt the laminator.
Do not defeat or remove electrical and mechanical
safety equipment such as interlocks, shields and
guards.
Do not insert objects unsuitable for lamination or
expose the equipment to liquids.
Electrical
The laminator should be connected only to a source of
power as indicated in these instructions and on the
serial plate located on the rear of the laminator.
Contact an electrician should the attachment plug
provided with the laminator not match the receptacles
at your location.
CAUTION: The receptacle must be
located near the equipment and
easily accessible.
Do not operate the laminator with a damaged power
supply cord or attachment plug, upon occurrence of a
malfunction, or after the laminator has been damaged.
Contact GMP’s Technical Service Department or your
dealer/distributor for assistance.
Service
Perform only the routine maintenance procedures
referred to in these instructions.
WARNING: Do not attempt to service
or repair the laminator.
Disconnect the plug from the receptacle and contact
GMP's Technical Department or your dealer/distributor
when one or more of the following has occurred.
- The power supply cord or attachment plug is
damaged.
- Liquid has been spilled into the laminator.
- The laminator is malfunctioning after being
mishandled.
- The laminator does not operate as described in
these instructions.
WARRANTY
GMP warrants to the original purchaser for a
period of ninety (90) days after installation that
this laminator is free from defects in workman-
ship and material under normal use and service.
GMP's obligation under this warranty is limited to
replacement or repair, at GMP's option, of any
part found defective by GMP without charge for
material or labor.
This warranty is in lieu of all other warranties
expressed or implied. WARRANTIES OF
MERCHANTABILITY OR FITNESS FOR A
PARTICULAR PURPOSEARE EXPRESSLY
EXCLUDED. Any representations or promises
inconsistent with, or in addition to, this warranty
are unauthorized and shall not be binding upon
GMP. In no event shall GMP be liable for any
special, incidental or consequential damages,
whether or not foreseeable.
This warranty shall be void if the product has
been misused; mishandled; damaged by
negligence, by accident, during shipment, or
due to exposure to extreme conditions;
repaired, altered, moved, or installed by anyone
other than GMP or its authorized agents; or if
incompatible film was used. GMP's obligation
under this warranty does not include routine
maintenance, cleaning, adjustment, normal
cosmetic or mechanical wear, nor freight
charges.
Without limiting the generality of the previous
paragraph, GMP's obligation under this
warranty does not include:
•damage to the pressure rollers or pull rollers
caused by knives, razors, or other sharp
tool; by any object falling into the working
area of the laminator; or by cleaning the
rollers with solutions or materials that harm
their surfaces;
•damage to Lucite panels or manometer glass
caused by mechanical action or by cleaning
with solutions or materials that harm those
surfaces; nor
•damage to the outer finish caused by
mechanical action or by cleaning with
solutions or materials that harm the outer
finish.
For proper cleaning procedures, see the
“
CARING FOR YOUR LAMINATOR
”chapter.
For European Union Residents Only: This
guarantee does not affect the legal rights which
consumers have under applicable national
legislation governing the sale of consumer
goods.

4
SPECIFICATIONS - EXCELMASTER-1600
Operating Speed:
Up to 5m/min
Temperature range:
0OC - 150 OC
Max. Mounting Thickness:
1.3 cm
Max. Film Width:
EXCELMASTER :165cm
Dimensions (W x D x H):
Unit alone: (Figure 2)
211 cm x 102 cm x 131 cm
Shipping:
216 cm x 109 cm x 159 cm
Weight:
Unit alone:
1030 lb. (467 kg.)
Shipping:
1250 lb. (567 kg.)
Electrical Requirements:
Refer to the serial plate located on
the rear of the laminator for the
specific electrical rating applicable
to the unit.
Voltage:
400V/50~60 Hz
Current:
8.3A
Power:
4000 W
Phase:
Single
Fig. 1
211 cm
131 cm
102 cm
EXCELMASTER-1600

5
PRE-INSTALLATION
Before a Laminator
can be installed, ensure the
following requirements are met;
1. Are door ways and hallways
wide enough for the laminator to
be moved to the installation site?
2. Is there ample room for the
laminator?
–A work area must be
established that allows for
operation in both the front and
rear of the laminator and
provides space for efficient
material flow. (Figure 3)
3. Is the environment appropriate
for the laminator?
–The laminator requires a clean,
dust and vapor free environment
to operate properly.
–Avoid locating the laminator
near sources of heat or cold.
Avoid locating the laminator in
the direct path of forced, heated
or cooled air.
CAUTION: Air flow can cause
uneven heating/ cooling of the
rollers and result in poor
output quality.
4. Have you contacted a certified
electrician to wire the receptacle
and ensure that adequate
power is being supplied, having
the appropriate capacity, over
current protection and safety
lockouts available?
EXCELMASTER requires:
°© 400V at 50/60hz with 15 amp
service. Use a Nema 6-20R.
Fig. 2
508 cm
330 cm
91 cm
220 cm
220 cm
101.6 x 152 cm
Work table on wheels
Electrical cord
drop
Front
Back
101.6 x 152 cm
Work table on wheels

6
INSTALLATION
1. Shipping damage should be
brought to the immediate
attention of the delivering
carrier.
2. With assistance, carefully roll
the laminator into position over
flat and even surfaces.
3. The laminator should be
positioned to allow exiting film to
flow freely to the floor or a work
table (Figure 4). Accumulation of
laminateimmediatelybehindthe
laminator as it exits the equip-
ment may cause the film to wrap
around the pull rollers, resulting
in a “jammed”condition.
4. Avoid locating the laminator near
sources of heat or cold. Avoid
locating the laminator in the
direct path of forced, heated or
cooled air.
5. Once the laminator has been
properly positioned, lock the
castors in place. Locking the
castors prevent the machine
from rolling during set up,
operation or servicing.
6.Connect the attachment plug
provided with the laminator to a
suitably grounded outlet. Avoid
connecting other equipment
to the same branch circuit to
which the laminator is
connected, as this may
result in nuisance tripping
of circuit breakers or
blowing fuses.
Fig. 3

7
CONTROLGUIDE
Located at the back left of the
machine applies power to the
laminator. The control panel display
will illuminate when position
marked “l”is pushed. The off
position, marked “O”, removes
power from the laminator.
B. CONTROL PANEL DISPLAY:
(Figure 4) Illuminates when the
laminator is plugged in and POWER
ON/ OFF is in the on, (I), position.
Displays settings for top heater,
bottom heater, speed, Job, mode
and ready/wait/ positioning
indicator.
ROLLER POSITION INDICATOR:
Displays the current main roller
position. In figure 7, the roller is
shown in the “Release”position.
Refer to Roller Handle for more
information.
READY/ WAIT INDICATOR:
“READY”appears when actual
temperature is equal to (+/- 5) set
temperature. “WAIT“appears
when actual temperature is lower
than the set temperature. “WAIT”
appears when actual temperature
is higher than the set temperature.
POSITIONING INDICATOR:
“Positioning...”appears in place
of the ready/ wait indicator any
time the main rollers are traveling in
an upward or downward motion.
C. CONTROL PANEL: (Figure 6)
MASTER DIAL :
Increases (+)
or decreases (-) the numeric value
for the selected setting when
display actual temperature of top
and bottom main rollers.
Top Temp. :
When pressed,
permits increasing or decreasing of
the top temperature by turning the
MASTER DIAL
and is
indicated on the control panel
display. Range is 0OC
- 150OC).
Bottom Temp. :
When
pressed, permits increasing or
decreasing of the bottom tempera-
ture by turning the
MASTER DIAL
and is indicated on the control
panel display. Range is 32oF -
0OC - 150OC.
Fig. 4
Fig. 5
Fig. 6
Release
WAIT
TOP
JOB
SPEED0℃
BOT0℃
03
01
Release
WAIT
TOP
JOB
SPEED0℃
BOT0℃
03
01
Top Temp.
Rev. Stop Run
Bottom Temp.
Speed
Job
Press/Release Cooling

8
Press/ Release :
When
pressed, raises the upper main
roller over riding the pull roller
handle setting. When pressed
again, reverts to current pull roller
handle setting.
Cooling :
(Figure 7) When
pressed, turns on the cooling fans.
When pressed again, turns off the
cooling fans.
JOB :
When pressed, permits
scrolling of job numbers by turning
the
MASTER DIAL
and is
indicated on the control panel
display. Range is 1 - 10. Job 10 is
reserved for running Accushield
material.
To store parameters for a particular
job number, select the desired job
number location, enter the upper
and lower temperatures and
speed, then press
JOB
.
SPEED :
When pressed,
permits increasing or decreasing of
speed by turning the
MASTER
DIAL
and is indicated on the
control panel display. Range is 1 -
10.
REV :
When pressed and held,
reverses roller movement to clear
film jams and wrap-ups.
STOP :
Stops the movement of
the rollers.
RUN :
When pressed, activates
rollers for normal operation.
D.REWINDERSELECTION
SWITCH: (Figure 8) This switch
enables the operator to control the
function of the upper rewind/
unwind shafts.
I: In this position, turns the power
on to the upper front rewind/
unwind shaft.
:
In this position, neither the
upper front or upper rear rewind/
unwind shaft is selected for motor
power.
II : In this position, turns the power
on to the upper rear rewind/
unwind shaft.
Fig. 7
Fig. 8
REWINDER
I
II
III
(D)

REWINDER
FWD.
(E) (F)
REV.
STOP
FWD.
REV.
FWD.
FWD.
REV.
REV.
REVERSESTOPRUN
"RUN"
"REVERSE"
(G)
9
E.UPPERREWINDERDIRECTION
SWITCH: (Figure 9) This switch
enables the operator to control the
direction of the upper rewind/
unwind shafts.
“FWD.” : In this position, the motor
runs in a forward direction.
“STOP” : Stops the rewinder motor
for the rewind/ unwind shaft
selected.
“REV.” : In this position, the motor
runs in a reverse direction.
F.LOWER REWINDERDIRECTION
SWITCH: (Figure 9) This switch
enables the operator to control the
direction of the Lower rewind/
unwind shaft.
“FWD.” : In this position, the motor
runs in a forward direction.
“STOP” : Stops the rewinder motor
for the rewind/ unwind shaft
selected.
“REV.” : In this position, the motor
runs in a reverse direction.
G.REAR CONTROL SWITCH:
(Figure 10) This switch enables the
operator to run jobs from the rear
operating position of the laminator
when rear controls are enabled.
“REVERSE” : In this position, the
rollers turn from the front operating
position towards the rear operating
position.
“STOP” : Stops the movement of
the rollers.
“RUN” : In this position, the rollers
turn from the rear operating position
towards the front operating position.
ENABLEREARCONTROL SWITCH:
To enable the rear control switch,
press and hold
JOB
until you
hear a beep, approximately 3
seconds. REAR CONTROL
replaces READY/ WAIT on the
control panel display.
Replace the rear slitter with the
safety shield properly installed and
latched.
DISABLEREARCONTROLSWITCH:
Press and hold
JOB
again to
disable the rear control switch.
H. FOOT SW ENABLE: (Figure11)
In this mode permits operation using
the footswitch.
To enable the foot switch, press
and hold
STOP
until you hear a
beep, approximately 3 seconds.
FOOT SW ENABLE flashes where
READY/ WAIT is indicated.
Press and hold
STOP
again to
disable the foot switch.
Fig. 9
Fig. 10
Fig. 11
Release
FootSWEnable
TOP
JOB
SPEED0℃
BOT0℃
03
01

10
Fig. 12
Fig. 13
Fig. 14
FEATURES GUIDE
A. E-STOP: (Figure 12) Two E-
STOP buttons exist on the
laminator. One on each side of the
upper cabinet.
To engage (1), press either push
button, roller movement is stopped.
To disengage (2), turn the push
button clockwise once the
emergency condition has been
resolved.
B.SAFETY SHIELD INTERLOCK
LATCH: (Figure 13) Used to lock
the safety shield into position and
activate an interlock switch. The
interlock latch is located on the left
side of the safety shield. When
pushed to the full left (1), the
safety shield is locked. When
pushed to the full right (2), the
safety shield is unlocked.
C. SAFETY SHIELD: (Figure 13)
Prevents entanglement, entrapment
and inadvertent contact with the
heat rollers. The laminator will
operate only when the Safety
Shield is located in the fully
locked position.
To remove the safety shield, unlock
the safety shield interlock latch and
lift the safety shield (1) up and
away from the safety shield
mounting pins (2).
D. FEED TABLE: (Figure14)The
Feed Table is used to position items
for lamination. The laminator will
operate only when the Feed
Table and Feed Table Latch are
properly installed.
E. HEAT ROLLERS: (Figure14)
Silicone rubber coated steel tubes
heat the laminating film and
compress the heated film to the
items being laminated. Heat is
provided by an internal heating
element. The heat rollers are motor
driven for ease of loading new film.
F. PULL ROLLERS: (Figure 14) The
pull rollers, located at the back of
the laminator, are motor driven.
They simultaneously pull the film
and improve the quality of the
laminateditem.
(1) (2)
(B)
(1)
(2)
(C)
(1) (2)
(A)
(F)
(E)
(D)

Release
15mm Mounting
10mm Mounting
5mm Mounting
3mm Mounting
Low-Prs Laminating
Mid-Prs Laminating
High-Prs Laminating
(G)
(H)
(I)
(J)
(2)
(1)
(N)
(1)
(2)
+
-
(1)
(2)
(M)
(L)
(K)
11
G. ROLLER HANDLE: (Figure15)
The roller handle manually sets the
position of the pull rollers while
simultaneously electronically setting
the main rollers.
Available settings are;
–Release
–15mm Mounting
–10mm Mounting
–5mm Mounting
–3mm Mounting
–Low-Prs Laminating
–Mid-PrsLaminating
–High-PrsLaminating
(Prs = pressure)
H. IDLER BAR: (Figure 16) The idler
bars, located near each heat roller,
are used to direct the film to the
heat roller nip.
I. CHILL IDLER: (Figure 16) Assist
in the cooling process of the web
material as it exits the heat rollers.
To engage the chill idler, grip the
chill idler handles located on each
side of the chill idler and lower to
the web position (1). To disengage
the chill idler, move the chill idler to
it’s rest position (2).
J. COOLING FANS: (Figure 16)
Assist in the cooling process by
pushing unheated air onto the web
material as it exits the heated
rollers. This feature can be
controlled from the control panel.
K. FILM SHAFT:(Figure 17) The
film shaft holds the film supply on
the machine.
To remove the film shaft, lift up on
the round end (1) of the unwind/
rewind shaft then pull the hex end
(2) of the shaft out and away from
thelaminator.
L. CORE ADAPTORS: (Figure 17)
Hold and lock the rolls of film on the
shafts to prevent side to side
shifting.
M. LOWER SHAFT LOCK: (Figure
17) Secures the left side of the
lower shafts. To remove a shaft,
turn the outer dial (1) opening so it
aligns with the inner u-channel (2)
opening and lift up and out.
N.UNWIND/REWIND TENSION:
(Figure 17) Used to apply resis-
tance to the film shaft.
To increase film shaft tension, turn
the film shaft tension knob
clockwise. Counter clockwise will
decrease film shaft tension.
Fig. 15
Fig. 16
Fig. 17

12
O. REWIND SHAFT:(Figure 18) The
rewind shaft holds the rewind tube
on the machine.
P. REWIND TUBE: (Figure 18) The
two rewind tubes located at the
front of the machine are used to
rewind release liners. The one
located at the rear of the machine
is used to rewind the finished
product.
Q. REWIND ADAPTORS: (Figure
18) Hold and lock the rewind tube
on the rewind shafts to prevent
side to side shifting.
R. REAR TABLE: (Figure 19)
Provides a working surface when
operating the machine from the
rear. This table may also be
lowered when webbing for roll to
roll applications.
To lower, slide the left and right
side rear table latches (1) to the
unlatched position and lower the
rear table.
S. REAR SLITTER: (Figure 19)
Used to cut the film web where it
exits the rear of the laminator.
To make a cut, push down on the
blade engage lever and slide to the
apposite side.
T. FILM WEB: Laminating film
loaded into the machine.
U. NIP POINT: The point at which
the top and bottom rollers come into
contact. The Nip Point of the heat
rollers is the place at which the
items for lamination are introduced
into the laminator.
V. FOOTSWITCH: (Figure 20) Used
to assist in webbing of the machine
and initial feeding of material.
W. PRINT UNWIND BASKET:
(Figure 20) Holds a rolled image.
Prevents the image from touching
the floor.
X. SEPARATOR BAR OPTION:
(Figure 18) Required if running
Micronext®material.
To install, replace the rear slitter
with the separator bar.
Y. REWIND KIT OPTION: Enables
roll to roll webbing of material. This
kit must be installed by a qualified
GMP service representative.
Fig. 18
Fig. 19
Fig. 20
(P)
(O)
(Q)
(1)
(2)
(1)
(S)
(R)
(W)
(V)

13
OPERATING INSTRUCTIONS
FILM LOADING & THREADING
The top and bottom rolls of
laminating film must be of the same
width and be present simulta-
neously. A small amount of
adhesive will “squeeze out”during
lamination. Hardened adhesive
deposits can damage the heat
rollers. To avoid any damage,
select “Low-Prs Laminating”on the
roller handle, rotate the rollers at
slowest speed with heat on. Refer
to the section entitled
CARING
FOR THE LAMINATOR
for instructions regarding
removal of the accumulated
adhesive.
Adhesive will deposit on the rollers
if:
- Only one roll is used.
- Different widths of rolls are
loaded together.
- Either roll is loaded adhesive
side against a heat roller.
- One or both rolls of film are
allowed to run completely off its
core.
The adhesive side of the film is on
the inner side of the web (Figure
21). The shiny side of clear film
must contact the heat rollers. The
dull side of the film contains the
adhesive. Use extreme caution
when loading delustered (matte)
film as both sides appear dull.
Always change the top and bottom
supply rolls at the same time. Near
the end of each roll of GMP
laminating film is a label stating
“Warning-End of Roll”. The appear-
ance of this label on either the top or
bottom roll requires that new rolls of
film be installed as soon as the item
presently being laminated completely
exits the rear of the laminator. Do not
introduce any additional items into the
laminator when the warning label is
visible.
To load a roll of film; (Figure 22)
1. Lift up on the round end, left
side (1), of the unwind/ rewind
shaft.
2. Pull the hex end, right side (2), of
the shaft out and away from the
laminator.
3. Slide the roll of film onto the film
shaft ensuring adhesive side is
out.
4. Replace the shaft with the hex
end in first then the round end.
5. Center the roll of film.
Fig. 21
Fig. 22
Poly-in
Adhesive
surface
Pol
y
ester surface
Poly-out
Adhesive
surface
Pol
y
ester surface
(2)
(1)

14
LOADING TOP THERMAL FILM
This procedure describes how to
load the upper roll of film onto the
laminator. Figure 23 uses poly-in
film and the upper rear unwind/
rewind position for illustration
purpose.
1. Turn the Power ON/OFF to on
(I). Set top heat temperature for
the film type you are using.
2. Ensure no brake tension is
applied to the film shaft.
3. Remove the safety shield and
pivot the feed table down.
4. Pull the top roll of film down
under the idler bar and allow to
drape over the top heat roller
(Figure 23).
5. Reference one of the loading
bottom material procedures.
LOADING TOP PSA FILM
This procedure describes how to
load the upper roll of film onto the
laminator. Figure 24uses PSA film
and the upper rear unwind/ rewind
position for illustration purpose.
1. Turn the Power ON/OFF to on
(I). If the laminator is already
hot, turn POWER ON/OFF to the
off (O) position and allow the
unit to cool. Once cool, turn the
laminator back on.
2. Ensure no brake tension is
applied to the film shaft.
3. Remove the safety shield and
pivot the feed table down.
4. Set the roll of film in the rear
unwind/ rewind position and the
rewind tube in the front unwind/
rewind position.
5. Pull the top roll of film down
under the idler bar and up the
upper front rewind tube.
6. Place one piece of masking tape
in the center of the film and
secure to the rewind tube.
7. Make two full wraps around the
rewind tube, then carefully
score the laminate without
cutting the release liner.
8. Pull the laminate down allowing it
to drape over the upper main
roller.
9. Reference one of the loading
bottom material procedures.
Fig. 23
Fig. 24

15
LOADING TOP MOUNT ADHESIVE
This procedure describes how to
load a roll of mount adhesive using
the upper position for pre-coating
(Figure 25).
1. Turn the Power ON/OFF to on
(I). If the laminator is already
hot, turn POWER ON/OFF to the
off (O) position and allow the
unit to cool. Once cool, turn the
laminator back on.
2. Ensure no brake tension is
applied to the film shaft.
3. Remove the safety shield.
4. Set the roll of mount adhesive in
the upper rear unwind/ rewind
position.
5. Pull the mount adhesive over the
upper idler and upper main roller
allowing the material to rest on
the top of the feed table.
6. Reference
THREADING CARD
PROCEDURE
next.
LOADING BOTTOM THERMAL
FILM
This procedure describes how to
load a roll of thermal film using the
lower unwind position for encap-
sulation (Figure 26).
1. At this point you should have an
upper roll of thermal film loaded
onto the laminator.
2. Ensure no brake tension is
applied to the film shaft.
3. Guide the bottom film around the
lower idler.
3. Adhere the film to the loaded
upper roll of thermal film by
pulling the film up towards the
existing draped thermal film over
the main rollers.
NOTE: You may follow this
procedure to load a roll of Kraft
Paper for single side lamination.
4. Reference
THREADING CARD
PROCEDURE
next.
Fig. 25
Fig. 26

16
LOADING BOTTOM PSA FILM
This procedure describes how to
load a roll of mount adhesive using
the lower unwind position for
decaling (Figure 27).
1. At this point you should have an
upper roll of PSA film loaded
onto the laminator.
2. Ensure no brake tension is
applied to the film shaft.
3. Pull the lower roll of film around
the lower idler bar and towards
the lower rewind.
4. Place one piece of masking tape
in the center of the film and
secure to the rewind tube.
5. Make two full wraps around the
rewind tube, then carefully
score the laminate without
cutting the release liner.
6. Adhere the lower PSA film to the
loaded upper roll of film by
pulling the film straight up
towards the main rollers.
7. Reference
THREADING CARD
PROCEDURE
next.
LOADING BOTTOM MOUNT
ADHESIVE
This procedure describes how to
load a roll of mount adhesive using
the lower unwind position for
decaling (Figure 28).
1. At this point you should have an
upper roll of film loaded onto the
laminator.
2. Ensure no brake tension is
applied to the film shaft.
3. Adhere the mount adhesive to
the loaded upper roll of film by
pulling the mount adhesive
straight up towards the main
rollers. Do not web around the
lower idler.
4. Reference
THREADING CARD
PROCEDURE
next.
Fig. 27
Fig. 28

17
THREADINGCARDPROCEDURE
This procedure describes how to
feed two loaded films through the
main rollers (Figure 29).
1. At this point you should have an
upper roll of film and lower roller
roll of film loaded onto the
laminator with the appropriate
material for your application.
2. The table and safety shield must
be properly installed.
3. Push the threading card into the
main roller nip. The threading
card becomes sandwiched
between the upper and lower
loaded films.
4. Set the roller handle to a
laminating position, press the
RUN
button.
5. Once the threading card has
exited the laminator, press the
STOP
button.
6. Use the rear slitter to cut the
threading card from the web.
7. If you are not running the
laminator, set the roller handle to
the“RELEASE”position.
8. Now refer to the section entitled
START LAMINATING
.
Fig. 29
Threading card

18
START LAMINATING
1. The safety shield and feed table
must be in the normal operating
position.
2. Select a job mode ( ) and
ensure the proper speed and
temperatures are set. Refer to
the section entitled
SPEED/
TEMPERATURE GUIDE.
3. Set the roller handle to one of
the laminating positions.
4. Press the PRESS/ RELEASE ( )
button. The main rollers gap.
5. Press the RUN ( ) button.
6. Press thePRESS/ RELEASE
() button. The main rollers
close.
7. Adjust unwind and rewind
tensions as necessary.
8. Align the leading edge of the
item square to the heat roller nip
(Figure 30).
9. With both hands and an outward
force push the image slower
than the speed of the rollers into
the nip of the heat rollers (Figure
31).
CAUTION: Avoid forcing the
image into the main roller nip
as this action will cause the
corners of the leading edge to
buckle and create a wave.
Fig. 30
Fig. 31

19
METHODFOR TACKING NEW
FILM TO EXISTING FILM
The following describes a method
for loading film whereby the
existing film present on the heat
rollers may be used in place of the
threading card to draw the new
film through the laminator. The
adhesive of the existing film must
be tacky or liquefied. Leading
edges of the new film will be
overlapped onto the tacky adhesive
of the old film. The existing film and
the new film will be pulled through
the laminator together.
1. Cut remaining top and bottom film
webs between the idler bar and
heat rollers (Figure 32).
CAUTION: DO NOT CUT THE HEAT
ROLLERSWHEN CUTTING THE
FILM WEB.
2. Remove the safety shield and tilt
the feed table down.
3. Do not allow the adhesive side
of the film to contact the heat or
pull rollers. Liquefied or tacky
adhesive deposited on heat
rollers will require the rollers to
be cleaned per the section
entitled
CARING FOR THE
LAMINATOR
.
4. Replace both the top and bottom
rolls of film with new rolls.
Ensure the adhesive side is
facing out.
5. Pull the film around the idler
bars, with the exception of PSA
mounting adhesives without a
release liner.
6. Tack the new film to the existing
film on the heat rollers. For PSA
film, attach the release liner to
the rewind tube (Figure 33).
7. Replace the safety shield and
feed table.
8. Use the footswitch to advance
the film into the heat roller nip.
9. Observe the film being pulled
through the laminator to assure
that the remaining existing film
and the new film are advancing
concurrently. Any separation
between the films will require
stopping the motor immediately
and the situation corrected.
10. Press STOP () once the
newly threaded film has
completely exited the pull rollers.
Fig. 32
Fig. 33
Cut here
Cut here
New film
New film

20
TO UNWEB THE LAMINATOR
Unweb the laminator if you are
changing film widths, cleaning the
rollers or have finished using the
machine for the day.
1. Using the rear slitter, cut the
output from the web (Figure 34).
2. Set the roller handle to the
“Release”position.
3. Remove the safety shield and tilt
the feed table.
4. Cut remaining top and bottom film
webs between supply rolls and
heat rollers (Figure 34). Be
careful not to cut any of the
rollers!
5. Carefully grab hold of the web
(top and bottom film), from the
front operating position and pull
towards you (Figure 35).
6. Do not allow the adhesive side
of the film to contact the heat or
pull rollers.
CLEARING A FILM JAM (Wrap-
up)
Film jams (wrap-ups) may occur if
the film is loaded backwards or if
the area at which film exits the
equipment is blocked. The film,
when jammed, wraps around the
heat rollers during webbing if a
threading card is not used or pull
rollers during operation.
To clear a jam:
1. Immediately stop the laminator by
pressing STOP ().
2. Remove the safety shield and tilt
the feed table.
3. Press and hold REVERSE ( )
until the jam has cleared the heat
rollers or pull rollers
4. Set the roller handle to the
“Release”position.
5. Manually assist the material
through the main rollers and/ or
pull rollers.
6. Once the jam has been cleared,
set the roller handle to one of
the laminating positions.
7. You can now resume laminating.
Fig. 34
Cut web
Cut web
Cut web
Pull web
Fig. 35
Table of contents
Other GMP Laminator manuals
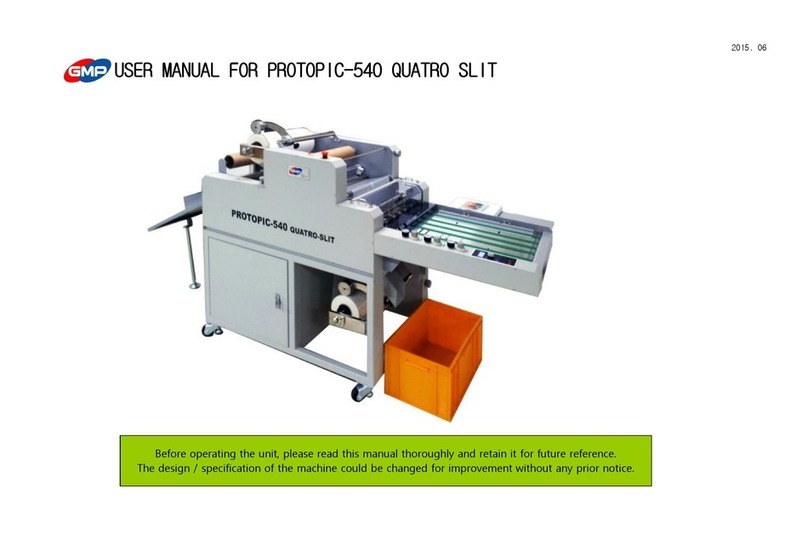
GMP
GMP PROTOPIC-540 QUATRO SLIT User manual
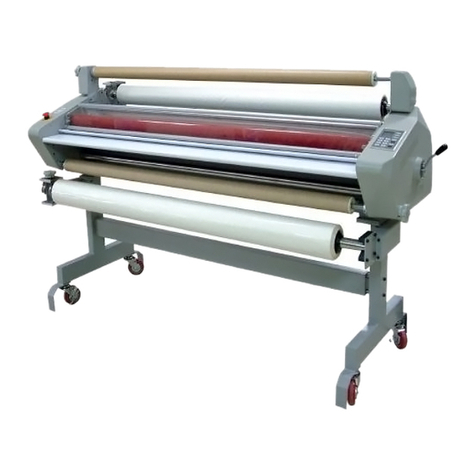
GMP
GMP EXCELAM-1100SWING User manual
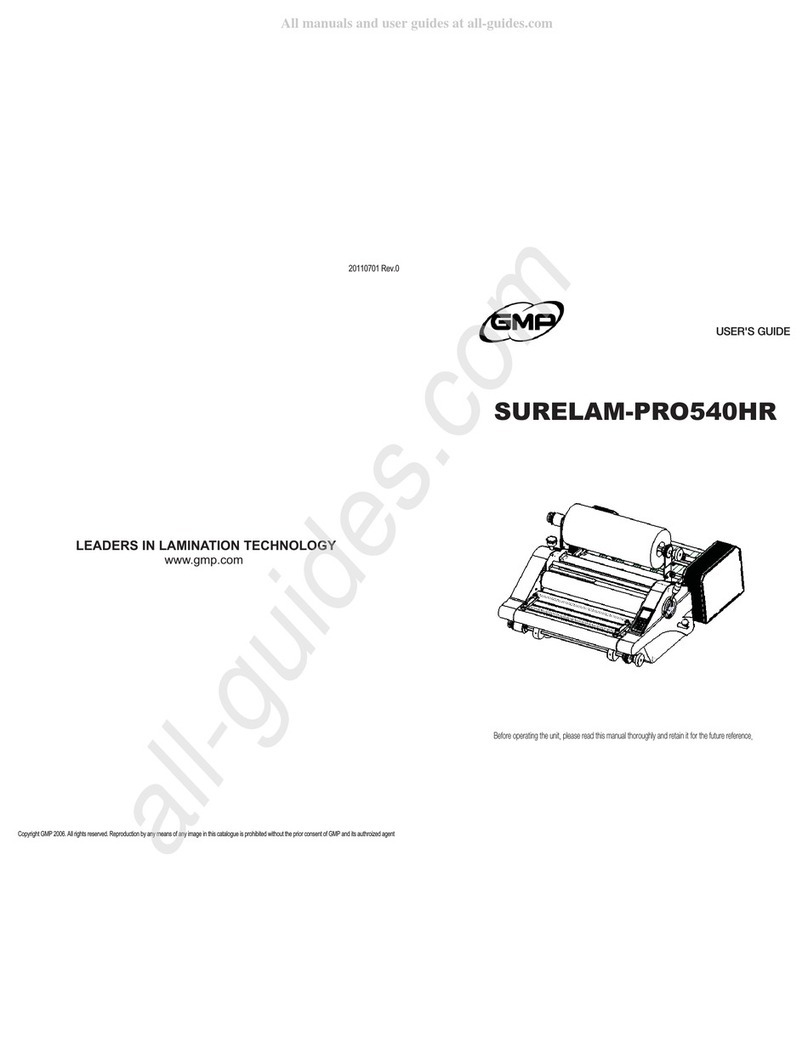
GMP
GMP SURELAM-PRO540HR User manual

GMP
GMP GraphicMaster 1600HR User manual
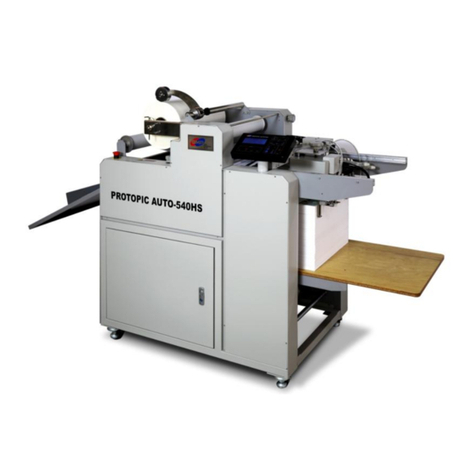
GMP
GMP PROTOPIC AUTO-540 HS User manual
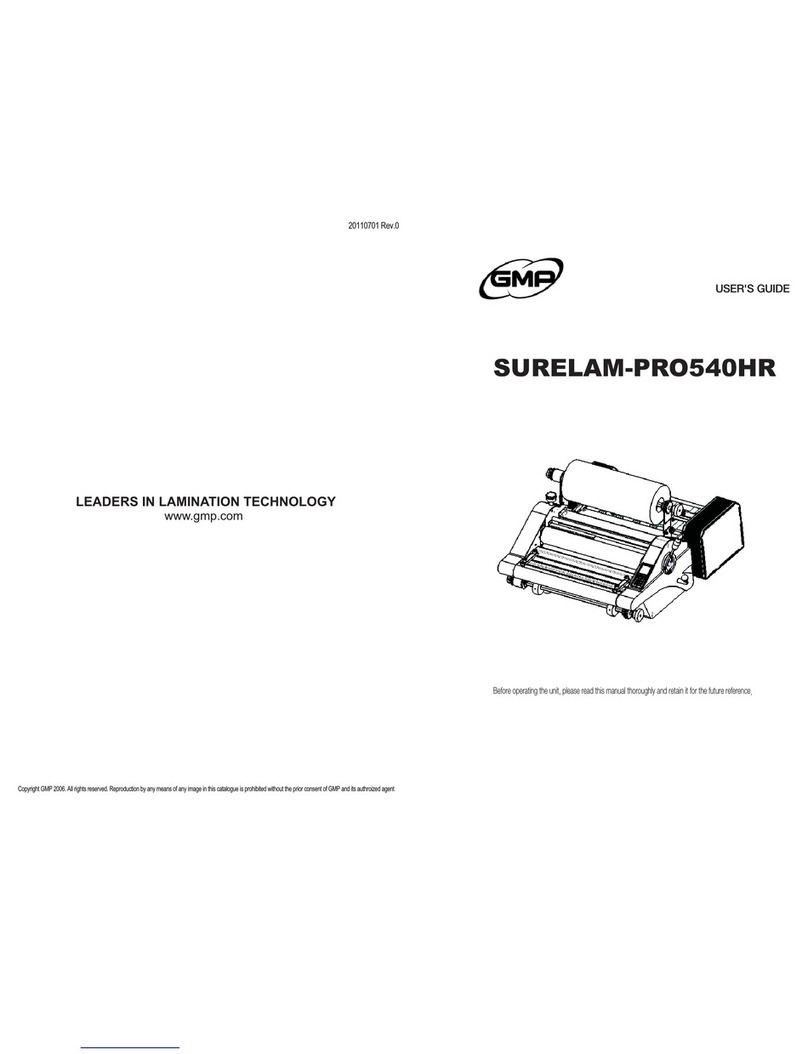
GMP
GMP SURELAM-PRO540HR User manual
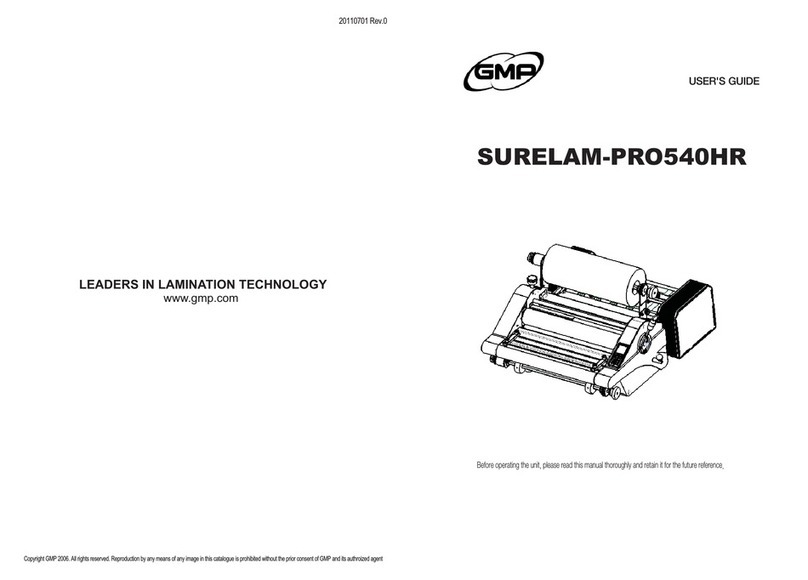
GMP
GMP SURELAM-PRO540HR User manual

GMP
GMP ELECTRO ULTRA LAMITRIM-1800 User manual
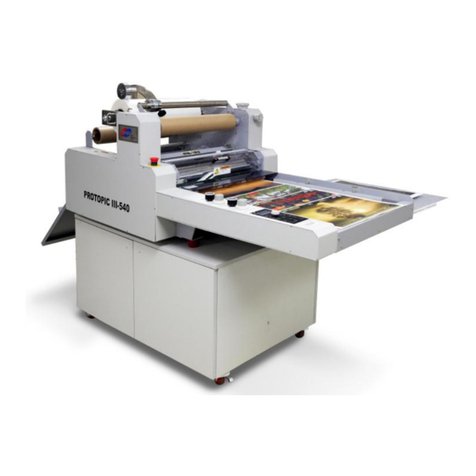
GMP
GMP PROTOPIC III-540 User manual
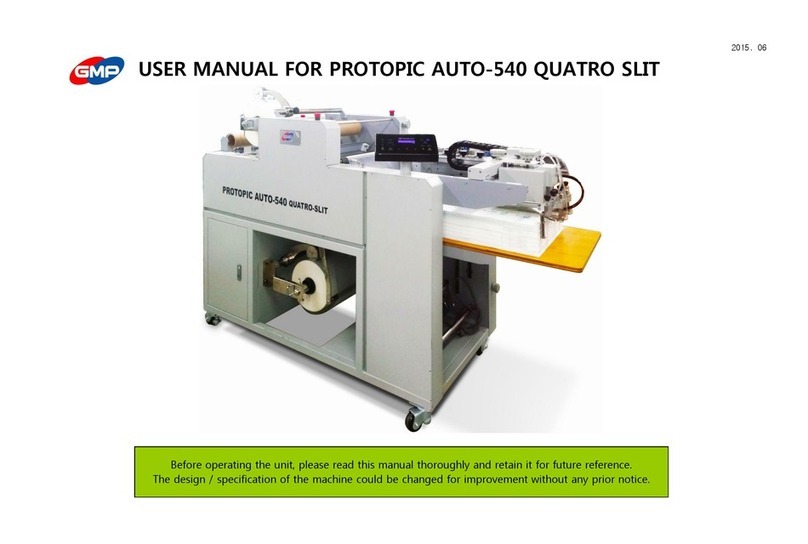
GMP
GMP PROTOPIC AUTO-540 HS User manual