Hawle HAWIDO 1403 User manual

manual
Pressure relief and pressure retention valve DAV for electrical control - open without current®

HAWIDO - REGULATING VALVES
Instruction for
Pressure relief and pressure retention valve
for electric control
Type 1403/04
ND 40 to DN200
Keep this instruction manual at the location of the valve!

Example of rating plate
After the commissioning, enter the following data and make use of this additional information regarding the
valve type, pressure and flow ratios when consulting the manufacturer or the supplier or asking them questions:
Serial number: ................................................... DN ……………… PN: …………………..
Year of manufacture:...................................................
Anleitung Stand September 2018 - 1/plü Subject to technical changes!

-1-
CONTENTS
A. DESCRIPTION 2
1. FUNCTION 2
2. GENERAL SAFETY INSTRUCTIONS 2
3. RECOMMENDED INSTALLATION 3
B. COMMISSIONING 4
1. FUNCTIONAL DIAGRAM (1403) 4
2. FUNCTIONAL DIAGRAM (1404) 4
3. PREPARATORY WORK 5
4. VENTING 5
5. ADJUSTMENTS 5
6. SETTING THE REACTION SPEED 6
7. CHECKING FOR LEAKAGE 6
C. FAULT FINDING 7
D. PUTTING OUT OF SERVICE AND MAINTENANCE 8
1. PUTTING OUT OF SERVICE 8
2. MAINTENANCE AND SERVICE 8
2.1 GENERAL INFORMATION 8
2.2 ANNUAL FUNCTIONAL CHECKS 8
2.3 4TO 5-YEAR MAINTENANCE 9
3. REPAIR KITS AND SPARE PARTS 10
3.1 BASE VALVE DN 40 TO DN 200 (DRAWING)11
3.2 MAIN VALVE (PARTS LIST)12
3.3 DAV STAINLESS STEEL CONTROL VALVE DN 3/8" PN 10/16/25 (DRAWING)14
3.4 DAV STAINLESS STEEL CONTROL VALVE DN 3/8" PN 10/16/25 (PARTS LIST)15
3.5 CONTROL LINE INDIVIDUAL PARTS AND ACCESSORIES 16
3.6 2/2-WAY SOLENOID VALVE.21
3.7 OPTICAL POSITION INDICATOR (DRAWING)22
3.8 OPTICAL POSITION INDICATOR (PARTS LIST)23
E. ANNEX 24
1. TORQUES 24
F. HAWLE IN EUROPE 25

-2-
A. Description
1. Function
The pressure relief valve maintains constant a pre-set inlet pressure (p1). Any excess system pressure is
relieved by fast opening of the valve. The closing procedure is slow in order to avoid shock pressure loads.
Variable flow rates have no effect on the maintained pressure which is regulated by the control valve. The
overpressure or maintained pressure of the standard version can be set within the range of 1.5 bar to 12 bar.
The valve is opened (started up) or closed via the electric solenoid valve.
Technical features:
Medium: Drinking water
Pressure stages: PN 10 (from DN 200 Standard)
PN16 (up to DN150 Standard)
PN25
Flanges: Connection dimensions according to DIN EN 1092 - -2
Pressure gauge EN 837-1, Accuracy class 1.6
Main valve material: EN-GJS-400-15
Temperature range: 2 –40 °C
2. General safety instructions
These instructions must be read through carefully and understood before starting the commissioning.
Damage to property and injuries to persons could occur as a result of improper installation, commissioning,
operation and maintenance.
The Hawle regulating valve (HAWIDO) has been designed for use in drinking and process water supplies.
Other application media only after consultation with the manufacturer.
The technical regulations (e.g. SVGW, ÖVGW, DVGW...) and codes of practice (e.g. VDE, VDI ...), laws and
standards are taken as a minimum standard, and must be adhered to and applied.
Work on electrical installations (e.g. installation of magnetic position switches, solenoid valves, etc.) may only
be carried out by personnel authorised for this work.
In principle, the responsibility for the layout, the installation position, the installation and the commissioning of
the fittings in the pipe work lies with the designer, the installation company and/or the operator. Design or
installation errors can adversely affect the safe operation of the regulating valve, and can represent a
significant risk. Please consult us in case of doubt.

-3-
3. Recommended installation
Before the installation of the fitting, the pipe lines must be carefully blown or flushed through to prevent any
foreign material, such as pieces of wood, stones etc., from entering the regulating valve.
The HAWIDO must be installed horizontally with the valve cover upwards (other models available on
request). We recommend that a gate valve and a dirt trap be fitted in front of the valve, as well as the
mounting of an gate valve at the outlet.
If the HAWIDO 1400 is used as a safety valve the shut-off gate valve on the outlet side can be omitted.
Before the installation, check that no coarse foreign objects can penetrate into the HAWIDO.
Please contact us for other types of installation.

-4-
B. Commissioning
1. Functional diagram (1403)
Components
1 Main valve
2 Ball valve (A, B, C)
3 Filter
4 Orifice plate
5 One-way flow restrictor
6 Control valve
7 Pressure gauge
8 Optical position indicator
Electrical position indicator (optional)
Valve opening limiter (optional)
9 Solenoid valve
2. Functional diagram (1404)
Components
1 Main valve
2 Ball valve (A, B, C)
3 Filter
4 Orifice plate
5 One-way flow restrictor
6 Control valve
7 Pressure gauge
8 Optical position indicator
Electrical position indicator (optional)
Valve opening limiter (optional)
9 Solenoid valve
3 4
p1p2
1
2A 2C
5
8
7
69
L
2B
3 4
p1p2
1
2A 2C
5
8
7
69
L
2B

-5-
3. Preparatory work
Before commissioning the valve, check that the gate valves on the inlet and outlet sides of the valve (or the
slider on the inlet side) are/is closed and that the flange connections have been correctly tightened and
sealed.
On the valve:
•Open ball valves (2A and 2B) and loosen the set screw lock nut on the one-way flow restrictor (5)
•Unscrew the adjusting screw on the one-way flow restrictor (5) by approximately 10 turns. (The line
to the control chamber is open).
•Close the ball valve (2C)
•Loosen the threaded pin in the central plug on the position indicator by a few turns.
•Loosen the threaded pin in the venting elbow by a few turns.
Threaded screw in the venting elbow
Vent hole
•Lower the adjusting lever on the pressure reduction control valve (6) and turn the lever to the right
until a very high resistance is felt from the spring.
•1403 Solenoid valve (9) inactive (➔solenoid valve has no flow).
•1404 Solenoid valve (9) inactive (➔solenoid valve has flow).
4. Venting
Procedure:
Slowly open the inlet gate valve on the inlet side until water flows into the valve. The valve fills with water
and the air escapes through the open vent holes.
When all the air has been expelled by venting the valve in the control line, re-tighten the threaded pin. Check
that all the screw connections are properly sealed, and re-tighten if necessary.
Slowly open the inlet gate valve completely.
Check: If the shut-off gate valve on the outlet side is slightly opened, the valve should close or remain
closed. Then close the shut-off gate valve again.
If the valve does not close, the commissioning procedure must be repeated from the previous chapter.
Particular care must then be taken to ensure that the upper valve chamber and control lines are properly
vented.
5. Adjustments
Prepare the valve according to Chapters 2 and 3. The gate valves on the inlet and outlet side are closed.
Procedure:
•Slowly open the ball valve (2C)
•Gradually and slowly open the gate valve on the outlet side (if present) (according to previous
chapter, the slider on the inlet side is already open).
•Valve 1403: Apply power to the solenoid valve (9) (➔solenoid valve has flow, opens).
•Valve 1404: Leave solenoid valve (9) inactive (➔solenoid valve has flow, is open).
•Slowly turn the adjusting lever of the control valve (6) to the left until the valve opens (audible sound
of water flowing).
•Check the inlet pressure on the pressure gauge.

-6-
•Gradually turn the adjusting lever of the control valve (6) (½ turn) according to the table below.
•1403. Remove power from solenoid valve (9) (➔solenoid valve closes), the base valve close and
remains closed.
•Valve 1404: Apply power to the solenoid valve (9) (➔solenoid valve closes), the base valve close
and remains closed.
Note:
Wait for the hydraulic system to stabilise between each half turn of the hand wheel. If the required relief
pressure has been set, tighten the screw on the hand wheel of the control valve (6).
6. Setting the reaction speed
If the HAWIDO does not operate quietly, or if pressure shocks occur in the supply network, this can be
corrected by the corresponding adjustment of the one-way flow restrictor (5).
Procedure:
Loosen the locknut. Screw in the set screw clockwise with a screwdriver until the valve operates quietly.
Then retighten the locknut.
Caution
The setting screw must always remain at least 3 - 5 turns open, otherwise the valve can no longer close or
does not open after the closing sequence. A special setting is necessary for very high inlet pressures.
7. Checking for leakage
The HAWIDO's are tested at the factory for both leakage and function before delivery. When checking for
leakage under operational conditions, particular attention must therefore be given to the seals of the flange
connections, the control line and the central plug screw on the valve cover. Where necessary, ensure the
seal by retightening the connections.
Notes:
Spring
type
Article
number
Marking
Regulati
ng
pressur
e
Pressure
change
for 1 turn
[bar]
Number of
spindle
turns for
Δp = 1bar
Standard
1145 200 000
NONE
1.5 –
12bar
0.4
2.5
Strong
1145 200 002
yellow
1118 000 000
10 –
22bar
0.9
1.1
Weak
1145 000 001
blue
1118 000 001
0.2 –
5bar
0.08
12.6

-7-
C. Fault finding
Symptoms
Possible cause
Action
Valve does not open
One-way flow restrictor blocked
Replace or unscrew the set
screw several times until the
valve functions properly
One-way flow restrictor closed
too far
Unscrew the set screw until the
valve functions properly
Valve does not open
(Pressure retention)
Control valve screw over-
tightened (pressure set too
high)
Loosen the set screw. Reset the
pressure
Valve does not close
One-way flow restrictor blocked
Replace, or screw the set screw
fully in and out several times
and then re-set
Filter in the control line blocked
Clean the filter
Air in the control line / upper
valve chamber
Vent
Foreign matter in the main valve
Carry out service and remove
any foreign matter
Diaphragm defective
Carry out a service.
Replace the diaphragm
Valve spindle jammed by
encrustation
Carry out service and remove
any encrustation
Loud noise
Unfavourable operating
conditions
Change pressure by approx. 0.1
to 0.2 bar. Slightly open or close
the one-way flow restrictor.
Contact the Hawle Customer
Service department.
Wrong valve size
Have the correct valve size
calculated (contact Hawle)
Erratic operation
One-way flow restrictor
incorrectly set
reset (according to chapter:
Setting the reaction speed)
Original pressure values not
reached
Pressure gauge faulty
Check or replace pressure
gauge
Changed operating conditions
Reset (see Setting-up
paragraph)
EWS coating damaged
Transportation damage,
installation damage
Repair with Hawle two-
component repair set for
coatings

-8-
D. Putting out of service and maintenance
1. Putting out of service
The operating valve must first be shut off hydraulically by proceeding as follows:
•Slowly close the gate valves before and after the valve
•Slowly close the ball valves (2A, 2B, 2C).
In order to be able to carry out maintenance work on the valve, the solenoid valve must be disconnected
from the power. The electrical supply must be disconnected.
Caution: Electrical work may only be carried out by qualified specialist personnel!
The valve has now been taken out of operation, and a service can be carried out.
2. Maintenance and service
2.1 General information
Through our many years of experience with diaphragm valves that are controlled by the flow medium, we
know that our HAWIDOs normally function trouble-free for many years. Regular maintenance is a
precondition for this, however.
Under normal operating conditions, the following should be carried out:
•The valve should be checked for correct operation once a year (functional check)
•The dirt trap upstream of the valve and the filter in the control line should be cleaned once a year
•The inner working components should be checked and worn parts be replaced every four to five
years (maintenance).
Under unusual operating conditions (e.g. with water that contains quantities of suspended matter, very high
pressure reduction, small flow rates etc.), the functional checks and the service work should be carried out
more frequently.
Maintenance sign:
xx stands for the respective year.
2.2 Annual functional checks
Cleaning the dirt trap in the main line
•Unscrew the lid
•Clean the filter with a brush or cloth etc., or replace it
•Install the filter and screw the lid back on
Cleaning the filter in the control line
•Unscrew the lid of the filter

-9-
•Clean the filter with a brush or cloth, or replace it
•Re-install the filter and screw the filter lid back on
Checking the valve
•Remove the vent plug from the valve cover.
•Check that the valve spindle moves easily by raising and lowering it with the threaded rod.
Putting back into service
•according to Commissioning paragraph
Functional check of the valve
The pressure retention valve must be set for the check to allow the inlet pressure to open the valve (please
refer to chapter Regulation of pressure retention)
•Valve 1403: Apply power to the solenoid valve (9) (➔solenoid valve has flow, opens).
•Valve 1404: Leave solenoid valve (9) inactive (➔solenoid valve has flow, is open).
•Slowly close the ball valve (2C); the valve must close.
•Slowly open the ball valve (2C); the valve must open.
2.3 4 to 5-year maintenance
Dirt trap (main line)
•Unscrew the lid
•Clean or replace the filter
•Install the filter and screw the lid back on
Filter (control line)
•Unscrew the lid of the filter
•Clean or replace the filter mesh
•Re-install the filter and screw the filter lid back on
Base valve (see chapter: Repair kits and spare parts)
•Loosen the screw connections and remove the complete control line.
•Dismantle the optical position indicator or assembled accessories and replace the gaskets.
•Undo the screws of the valve cover and remove the cover.
•Visually inspect all inner components for wear, dirt and scaling
•Clean the inner components, the seat and the inner surfaces, including the cover
•Dismantle the spindle guide in the body, flush the body interior.
For valves DN 40 to DN 100 (from 2012 on) and DN 125 to DN 200 (from 2014 on) the spindle guide
is dismantled from the inside. Here the thread of the spindle guide and the base valve must be
extremely clean. Grease the thread thoroughly (e.g. Foodgrease Aqua, Art. no. 5292, see chapter
“Control line individual parts and accessories”).
•Replace the diaphragm, the O-ring and the seat seal.
•Grease the spindle guide area with a grease suitable for contact with food (e.g. Foodgrease Aqua).
Check the easy movement of the spindle by lifting and lowering with the spindle lifting tool (article
number 1199, see chapter “Control line individual parts and accessories”).
•Reassemble the base valve (see table in the annex for torques). During the assembly, the easy
movement of the spindle must be checked with the spindle lifting tool by lifting and lowering several
times.
Disassembling the control valve (see chapter: Repair kits and spare parts)
•Switch over the clamping and adjusting lever
•Turn the adjusting lever to the left until no resistance can be felt from the spring
•Undo the housing screw
•Loosen the guide pin and the sealing plate
•Replace the diaphragm, the O-ring and, if necessary, the seal support
•Visually inspect the inner surfaces of the housing, and clean if necessary, including the cover

-10-
•Reassemble the control valve (see table in the annex for torques).
Functional check of the one-way flow restrictor
•Undo the locknut
•Screw in the throttle screw, and then unscrew it as far as it goes
•Screw in again a few turns. This process must be easy and meet little resistance
Putting back into operation and functional check
•In accordance with the Putting into Operation and Functional Check chapter and the previous
chapter
3. Repair kits and spare parts
Several replacement parts are required for the 4 or 5 - year service. These can be obtained as a repair kit
for:
•the main valve
•the control valve
•the control line
•the optical position indicator
The article numbers can be found in the part lists and the lists of spare parts.
Caution:
When ordering replacement parts, always specify the valve type, serial number and year of construction!
Important:
Replacement parts made of EPDM (diaphragms, seals) and NBR (O-rings) must be stored in a dark place,
protected from UV radiation!
Shelf-life when stored in the dark:
EPDM 8 years from date of manufacture
NBR 5 years from date of manufacture

-11-
3.1 Base valve DN 40 to DN 200 (drawing)
08.12.2011/plü

-12-
3.2 Main valve (Parts list)
Item.
Description
Material
Article number
DN 40
DN 50
DN 65
DN 80
DN 100
1
Body
GGG 40
1004 040 000
1004 050 000
1004 065 000
1004 080 000
1004 100 000
2
Valve cover
GGG 40
1014 050 000
1014 050 000
1014 065 000
1014 080 000
1014 100 000
3
Spindle guide cover
INOX
1024 900 000
1024 900 001
1024 900 002
1024 900 003
1024 900 004
4
Spindle
INOX
1026 050 000
1026 050 000
1026 065 000
1026 080 000
1026 100 000
5
Seat
INOX
*
*
*
*
*
6
Counter seat
INOX
1044 040 001
1044 050 001
1044 065 001
1044 080 001
1044 100 001
7
Seal
EPDM
1022 040 000
1022 050 000
1022 065 000
1022 080 000
1022 100 000
8
Seal carrier
INOX
1027 040 200
1027 050 200
1027 065 200
1027 080 200
1027 100 200
9
Diaphragm PN10/16
EPDM
1020 050 000
1020 050 000
1020 065 000
1020 080 000
1020 100 000
Diaphragm PN25
EPDM
1020 050 000
1020 050 000
1021 065 000
1021 080 000
1021 100 000
10
Pressure disc
INOX
1047 050 000
1047 050 000
1047 065 000
1047 080 000
1047 100 000
11
Nut
INOX
0007 710 080
0007 710 080
0007 712 080
0007 716 080
0007 716 080
12
Spring
INOX
1049 050 000
1049 050 000
1049 065 000
1049 080 000
1049 100 000
Spring for valves installed
upright position
INOX
1050 050 000
1050 050 000
1050 065 000
1050 080 000
1050 100 000
13
Spindle guide cover
INOX
1042 900 000
1042 900 000
1042 900 001
1042 900 002
1042 900 002
14
Hexagonal screw
INOX
0006 608 020
0006 608 020
0006 610 025
0006 610 025
0006 612 025
15
O-ring
NBR
0180 012 020
0180 012 020
0180 012 020
0180 016 020
0180 016 020
16
Washer
INOX
0008 208 000
0008 208 000
0008 210 000
0008 210 000
0008 212 000
17
GSK-sticker
1099 900 000
1099 900 000
1099 900 000
1099 900 000
1099 900 000
18
Maintenance sticker
9691 0xx 000
9691 0xx 000
9691 0xx 000
9691 0xx 000
9691 0xx 000
Main valve complete
PN10/16
1201 040 000
1201 050 000
1201 065 000
1201 080 000
1201 100 000
Main valve complete
PN25
--
--
1201 065 025
1201 080 025
1201 100 025
Repair kit for main valve
with stainless steel
connection, comprising
item 7, 9, 15, 18
PN10/16
1080 040 000
1080 050 000
1080 065 000
1080 080 000
1080 100 000
PN25
1080 040 000
1080 050 000
1081 065 000
1081 080 000
1081 100 000

-13-
Item
Description
Material
Article number
DN 125
DN 150
DN 200°
DN 200^
1
Body
GGG 40
1004 125 000
1004 151 000
1004 200 000
1004 200 016
2
Valve cover
GGG 40
1014 125 000
1014 151 000
1014 200 000
1014 200 000
3
Spindle guide cover
INOX
1024 900 005
1024 900 005
1024 900 006
1024 900 006
4
Spindle
INOX
1026 125 000
1026 151 000
1026 200 000
1026 200 000
5
Seat
INOX
*
*
*
*
6
Counter seat
INOX
1044 125 001
1044 150 001
1044 200 001
1044 200 001
7
Seal
EPDM
1022 125 150
1022 151 000
1022 200 000
1022 200 000
8
Seal carrier
INOX
1027 125 200
1027 151 200
1027 200 200
1027 200 200
9
Diaphragm PN10/16
EPDM
1020 125 150
1020 151 000
1020 200 000
1020 200 000
Diaphragm PN25
CR
1051 125 150
1051 151 000
--
1034 200 000
10
Pressure disc
INOX
1047 125 150
1047 151 000
1047 200 000
1047 200 000
11
Nut
INOX
0007 720 080
0007 720 080
0007 724 080
0007 724 080
12
Spring
INOX
1049 125 150
1049 151 150
1049 200 000
1049 200 000
Spring for valves
installed upright position
INOX
1050 125 150
1050 151 000
1050 200 000
1050 200 000
13
Spindle guide cover
INOX
1042 900 003
1042 900 003
1042 900 004
1042 900 004
14
Hexagonal screw
INOX
0006 616 035
0006 616 035
0006 620 045
0006 620 045
15
O-ring
NBR
0180 018 020
0180 018 020
0180 021 020
0180 021 020
16
Washer
INOX
0008 216 000
0008 216 000
0008 220 000
0008 220 000
17
GSK-sticker
1099 900 000
1099 900 000
1099 900 000
1099 900 000
18
Maintenance sticker
9691 0xx 000
9691 0xx 000
9691 0xx 000
9691 0xx 000
21
Retaining bracket
INOX
--
--
1200 900 020
1200 900 020
Main valve complete
PN10/16
1201 125 000
1201 151 000
1201 200 000
1201 200 016
Main valve complete
PN25
1201 125 025
1201 151 025
1201 200 025
Repair kit for main valve
with stainless steel
connection, comprising
item 7, 9, 15, 18
PN10/16
1080 125 150
1080 151 000
1080 200 000
1080 200 000
PN25
1081 125 150
1081 151 000
1081 200 000
° PN10
^ PN16
* not interchangeable
16.03.2018/plü

-14-
3.3 DAV stainless steel control valve DN 3/8" PN 10/16/25 (drawing)
01.09.2017/plü

-15-
3.4 DAV stainless steel control valve DN 3/8" PN 10/16/25 (parts list)
Item
Description
Material
Article number
1
Control casing
Stainless steel
1100 200 000
2
Cover
Stainless steel
1108 200 000
3
O-ring
NBR70
0180 020 025
4
Diaphragm DN3/8
EPDM (W270)
1121 000 000
5
Seat Compact Form 1.0, blank
Stainless steel
1117 200 000
6
Seat Compact Form 1.0, 9 mm
Stainless steel
1117 200 002
7
DAV Sealing plate
stainless
steel/EPDM
1120 200 001
8
Pressure screw
Stainless steel
1133 200 000
9
Fibre seal
Rubber
0132 024 015
10
Pressure spring standard
Stainless steel
1145 200 000
11
Spacer sleeve for spring
Stainless steel
1133 300 000
12
Spring guide
Stainless steel
1133 400 000
13
M6 x 10 Cap bolt
Stainless steel
0004 506 010
14
M8 x 0.5d Hexagon nut
Stainless steel
0007 208 050
15
M6 x 45 Cap bolt
Stainless steel
0004 506 045
16
O-ring
NBR70
0180 048 015
17
O-ring
NBR70
0180 016 015
18
Intermediate housing for DAV long
Stainless steel
1115 016 030
19
Sleeve for DAV
Stainless steel
1140 500 000
20
O-ring
NBR70
0180 011 015
21
U-washer
STAINLESS STEEL
0008 206 000
22
Clamping and adjusting lever
Kst –PA6.6
1135 000 001
23
Load washer for clamping lever
Kst –PA6.6
1135 000 010
24
Axle with IG to the clamping lever
Stainless steel
1135 000 011
25
M4 x 16 Cap bolt
Stainless steel
0004 804 016
26
O-ring
EPDM
0180 010 015
27
Pressure disc DN 3/8”
Stainless steel
1129 012 000
28
Pressure nut for control valve
Rg
1134 000 010
29
Guide pins (for DRV/MBV)
Stainless steel
1137 000 000
REGULATING
RANGE:
Complete control valve (standard)
1.5 –12 bar
1920 001 000
Complete control valve, identification
blue
0.2 –5 bar
1920 001 001
Complete control valve, identification
yellow
10 –22 bar
1920 001 002
Repair kit consisting of:
Pos. 3, 4, 7, 9, 16, 17, 20, 26
1181 000 001
01.09.2017/plü

-16-
3.5 Control line individual parts and accessories
Master number
Designation
Picture
Size
further sizes possibly available
Art. number
0130
Compound seal
stainless steel/NBR 3/8“
stainless steel/NBR 1/2"
stainless steel/NBR 3/4"
Stahl/NBR 1“
0130 012 000
0130 016 000
0130 025 000
0130 032 000
0273
Individual parts
Fitting connection (consisting of:
connector nut and clamping ring)
DN 12 stainless steel
connector nut only
0273 012 000
0274 xxx xxx
0275 Support
sleeve
stainless steel d4 –6
stainless steel d12 –9
stainless steel d12 –10
0275 006 004
0275 012 009
0275 012 010
0283
Clamping ring
d6 stainless steel
d12 stainless steel
d18 stainless steel
d8 - 6 stainless steel
0283 006 000
0283 012 000
0283 018 000
0283 008 006
0284
Orifice plate
(Old orifice plate
number
0281.
d12 stainless steel Ø 0.6 mm
d12 stainless steel Ø 0.9 mm
d12 stainless steel Ø 1.2 mm
d12 stainless steel Ø 1.5 mm
d12 stainless steel Ø 1.9 mm
d12 stainless steel Ø 2.4 mm
d12 stainless steel Ø 3.1 mm
d18 stainless steel Ø 3.5 mm
d18 stainless steel Ø 4.0 mm
0284 006 000
0284 009 000
0284 012 000
0284 015 000
0284 019 000
0284 024 000
0284 031 000
0284 035 010
0284 040 010
0311
Screw connection
with screw-in nipple
d 12 - 3/8" stainless steel
d 12 - 1/2" stainless steel
d 6 - 1/8" stainless steel
d 6 - 1/4" stainless steel
d 6 - 3/8" stainless steel
d18 –1/2“ stainless steel
0311 012 012
0311 012 016
0311 006 004
0311 006 008
0311 006 012
0311 018 016
0323
Straight fitting
d 6 stainless steel
d 12 stainless steel
0323 006 000
0323 012 000
0324
Straight socket
end fitting
d12 - 3/8"
0324 012 012
0351
Reduction
fitting
d6 –d12 stainless steel
0351 012 006
0361
Transition sleeve
d 10 - 3/8" stainless steel
d 12 - 3/8" stainless steel
d 12 - 1/2" stainless steel
d 18 –1/2” stainless steel
0361 010 012
0361 012 012
0361 012 016
0361 018 016
0371
Reduction nipple
IG d 12 –AG 3/8" stainless steel
0371 012 012

-17-
0401
Sleeve
3/8" stainless steel
1/2" stainless steel
3/4" stainless steel
1" stainless steel
0401 012 000
0401 016 000
0401 025 000
0401 032 000
0411
Adjuster nipple
DN 6 - 1/8" stainless steel
DN12 - 3/8" stainless steel
0411 006 004
0411 012 012
0431
Screw-in elbow
DN 6 - 1/8" stainless steel
DN6 - 1/4" stainless steel
DN12 - 3/8" stainless steel
DN18 - 1/2" stainless steel
0431 006 004
0431 006 008
0431 012 012
0431 018 016
0431
Screw-in elbow with
vent
DN 123/8" Stainless steel
0431 012 013
0451
Angled fitting
DN6 stainless steel
DN12 stainless steel
DN18 stainless steel
0451 006 000
0451 012 000
0451 018 000
0452
90° Adjuster elbow
DN12
0452 012 000
0455
Connector elbow
IG 3/8" stainless steel
IG 1/2" stainless steel
IG 3/4“ stainless steel
IG 1“ stainless steel
0455 012 000
0455 016 000
0455 025 000
0455 032 000
0456
Connector elbow
IG 3/8" - AG 3/8" stainless steel
IG 1/2" - AG 1/2" stainless steel
IG 3/4" - AG 3/4" stainless steel
IG 1“ – AG 1“ stainless steel
0456 012 000
0456 016 000
0456 025 000
0456 032 000
0461
T-piece
d6 stainless steel
d12 stainless steel
d12 - 6 - 12 stainless steel
d18 stainless steel
0461 006 000
0461 012 000
0461 012 006
0461 018 000
0510
Plug
AG 3/8" conical stainless steel
AG 1/2" conical stainless steel
0510 012 000
0510 016 000
0511
Vent plug,
lock screw
AG 1/2" stainless steel
AG 3/4" stainless steel
AG 1” stainless steel with hexagon
socket
0511 016 000
0511 025 000
0511 032 001
0520
hexagon double nipple
d 1/8" stainless steel
d 1/4" stainless steel
d 3/8" stainless steel
d 1/2" stainless steel
d 3/4" stainless steel
0520 004 000
0520 008 000
0520 012 000
0520 016 000
0520 025 000
0541
Ball valve
DN 3/8" stainless steel
DN 1/2" stainless steel
DN 3/4" stainless steel
0541 012 001
0541 016 000
0541 016 010
This manual suits for next models
1
Table of contents
Other Hawle Control Unit manuals
Popular Control Unit manuals by other brands
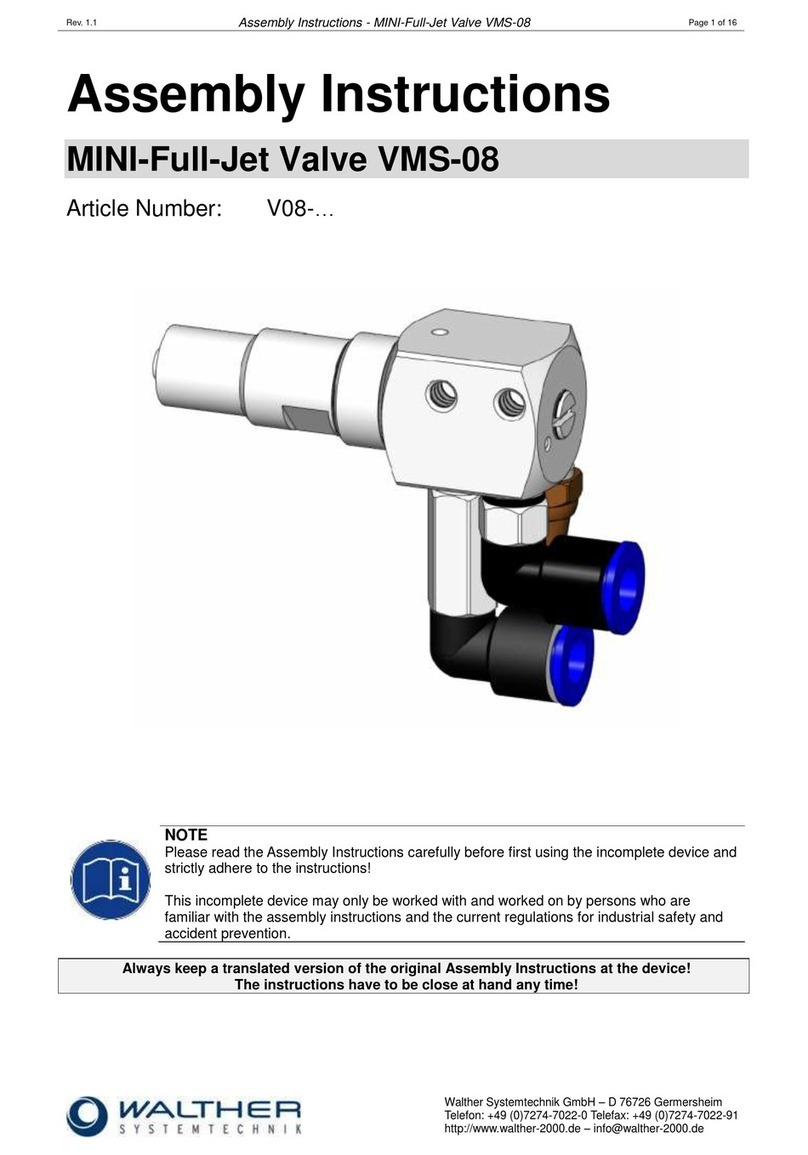
Walther Systemtechnik
Walther Systemtechnik VMS-08 Assembly instructions
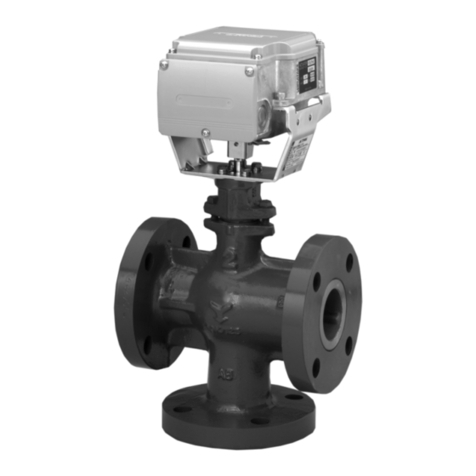
Azbil
Azbil ACTIVAL VY54X0F Series Specifications & instructions
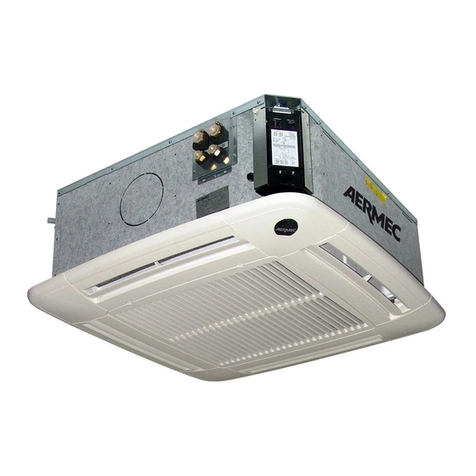
AERMEC
AERMEC VHL22 installation manual

Mitsubishi Electric
Mitsubishi Electric AJ65BT-D62 user manual
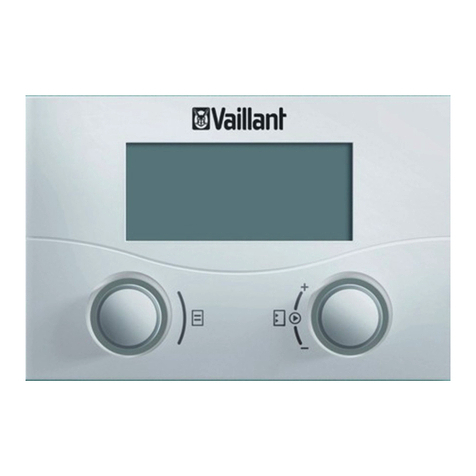
Vaillant
Vaillant VR 90 OPERATING AND INSTALLATION Manual
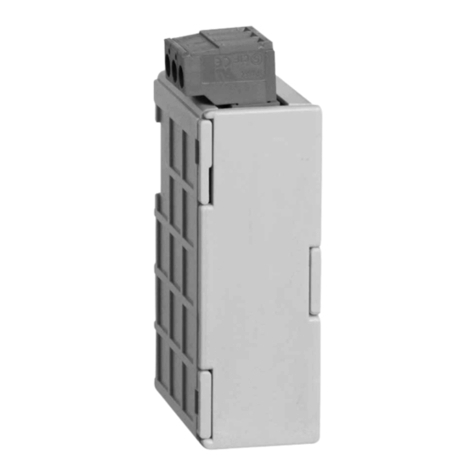
Bticino
Bticino F4N400 installation manual