HP 400D Quick start guide

@
MODELS 400D, 400H, AND 400L
VACUUM TUBE VOLTMETERS
TEST, ADJUSTMENT, AND CERTIFICATTON METHODS
These Service Notes have been prepared as an aid in
testing and adjusting all
@
Model 400D, 400H, and
400L Vacuum Tube Voltmeters. The procedures that
follow supersede those in other ServiceNotes or Op-
erating and Servicing Manuals for these instruments.
All
circuit
references apply to one of the three
ref-
erence schematic diagrams in these Service Notes.
No attempt should be made to make an instrument
agree completely
with
any one of these schematics.
All
recommended circuit changes are described in
Section
I
of these Service Notes.
Voltages mentioned herein are measured between
the indicated points and the chassis
unless
specified
otherwise. The voltmeter power supply should al-
ways be tested before undertaking repair and adjust-
ment of any other section of the instrument.
These Service Notes are divided into
five
sections
as follows:
Section Page
I
MODIFICATIONS
1
I1
TUBE
&
CRYSTAL DIODE REPLACEMENT 2
111
TEST EQUIPMENT REQUIRED 3
IV
TEST
&
CALIBRATION PROCEDURE
3
A.
Setting Mechanical in Models 400D
or 400H 3
B. Setting Mechanical Zero in Model 400L 3
C. Check Regulated Power Supply
4
D. Set dc Heater Voltage 4
E. Input Divider Circuit Identification 4
F. Input Circuit Preliminary Frequency
Response Adjustment
5
G. Basic Calibration (Setting Amplifier Gain)
5
H.
Basic Calibration (Setting Input Divider)
5
I. Miscellaneous Checks
5
J.
Recheck dc Heater Voltage 6
K.
Check Calibration and Tracking 6
L.
Check Effect of Line Voltage Change 6
M. Frequency Response Adjustment 6
V
TESTS FOR INSTRUMENT CERTIFICATION
8
N.
Final Check and Adjustment 7
SECTION
I
-
MODIFICATIONS
Modifications in certain serials of
($9
Model
400D,
400H, and 400L Voltmeterscan simplifytesting.Speci-
fications have not been changed, Modernization
of
instruments
will
simplify repair and testing and
will
add to instrument reliability. The changes that follow
apply only to those 400D, 400H, and 400L instruments
having the specified serial numbers.
A.
MODEL 400D SERIAL
NO.
2221 AND BELOW
Change V2 plate load resistor R23 from an 8200
ohm,
*5%,
1
watt, composition resistor to a metallic
oxide film-type having thesameresistance, tolerance,
and wattage rating. This Corning Glass Works style
N25 resistor
is
availableunder@StockNo. 0761-0001.
This change
is
particularly recommended for those
instruments in which the residual noise reading
is
too
high and/or unstable. Mount the new resistor as
nearly
as
possible in the same location as the old
resistor.
‘b
distribution abcfg
B.
MODEL 400D SERIAL NO, 3944 AND BELOW
Add resistor R67 in
series
with the control grid
of the
series
regulator tube V7. Transfer
the
wire
(usually green) from V7 pin
1
to vacant pin 6 on the
sametube socket. Connect a 470 ohm
f
lo%, 1/2 watt
composition resistor
(@
Stock No. 0687-4711)between
V7 socket pins
1
and 6.
This resistor prevents parasitic oscillation in the
power supply. Such oscillation can cause the meter
to be deflected
full
scale against the right hand stop.
C. MODEL 400D SERIAL NO.
4344
AND BELOW
I
Add 10 ohm
*lo%
1
watt, composition resistor
(@
Stock No. 0690-1001) R68 in parallel with heater
voltage adjustment control R66. Thisresistor reduces
power dissipation in R66 and extends the
life
of the
control. Readjust the dc heater voltage after
in-
stalling R68.
00665-4
COMPLETE
COJERAGE
IN
H
E
T-PACKARD
C
RUE
DU
Vft
QINCVA,
WLII
“WCWIACN
LLECTRONK
MEASURING
kQUIPMENT
I
5
0
8
+
A
4
8
Y
I
L
L
R
o
A
D
FALO
AbTOp
CALIIORWIA,
1.5.A.
CAILI:
“UlW;*CW*
UY~WORT
*-I000
r(Mc.0
*db..,A.
E*

Page 2
v-
400D-2C
D.
MODEL 400D SERIAL NO. 5130 AND BELOW
Transpose the connections to electrolytic capa-
citor C30
so
that C30B
is
20 pf and C3OC
is
40 pf.
This transposition
will
reduce power supply ripple.
E. MODEL 400D SERIAL NO. 14770 AND BELOW
MODEL 400H
S
ERIAL NO. 1137 AND BELOW
Replacement of control R29 or three-section resistor
R28 in the amplifier feedback
circuit
will
necessitate
revising and rewiring the feedback circuit.
The parts for this
circuit
revision
are
supplied as a
kit with complete instructions under
@
Stock No.
400D-95A.
The revised feedback
circuit
is
recommended for all
400D and 400H instruments whenever repair of the
feedback circuit
is
necessary. The revised circuit
is
superior to earlier circuitry but doesnot offer suf-
ficient
advantages to warrant modification merely to
include the new circuit in an instrument. The problem
of adjusting frequency response following anychanges
in the feedback circuit would also make
it
advisable
to avoid making unnecessary changes,
F. MODEL 400D SERIAL NO. 16371 AND ABOVE
The regulated power supply was changed. Series
regulator tube V7 was changed from
a
6AU5 toa
12B4A. Control tube V8 was changed from a 6CB6
to a 6U8 and reference tube V9 was changed from an
OB2 to a type 5651. The circuit differences can be
determined by referring to the schematic diagrams
included in these Service Notes.
Field modification to incorporate this change
is
im-
practical and
is
not recommended.
SECTION
II
-
TUBE
&
Tubes with standard JEDEC characteristics can be
used for replacement.
In
a great number of cases,
instrument trouble can betraced toadefectiveor weak
tube, Replace only those tubes proven to be defective
orweak. Check tubesby substitution. Results obtained
through the use of a “tube checker” canbe erroneous
and misleading. Mark original tubes to insure that
they are returned to the samesocket
if
not replaced.
The power supply should be checked according to the
instructions in these Service Notes
after
replacing
V6, V7, V8, orV9 in
the
power supply.
Heater voltage must be checked and adjustedafter
re-
placing
V1,
V2,
V3,
or V4. Factory selected tubes
are
available for
V1
and V2. These tubes aretested
for low noise and microphonics. Contactyour@ Sales
Office for the
@
Stock Numbers and prices on these
tubes.
G.
MODEL 400H SERIAL NO. 1338 THROUGH 1537
Resistor R83 should be changed in value and
location. The
new
value
is
470,000 ohms
*lo%,
1/2
,‘-
watt instead of 100,000ohms.
A
second
resistor
with
a value of 470,000 ohms
&lo%,
1/2 watt and a sche-
matic
reference
of R85
is
connected in
series
with
R83. The
series
combination of R83 and R85
is
then
connected between the regulated B+ output atthecath-
ode of the regulator tube and chassis ground. The
transformer winding supplying heater voltage for V6,
V7, and V8
is
connected
to
thejunction of R83 and R85.
These connections can be made by mounting both
re-
sistors between terminals on the socket for V7.
4
H. MODEL 400D SERIAL NO. 17970 AND BELgW
MODEL 400H SERIAL NO. 2237 AND,BELaW
Residual noise as indicated by the meters in these
instruments can be reduced by a modification of the
input attenuator.
A
higher degree of residual noise
reduction
is
obtained on the upper voltmeter ranges
by this modification.
The input attenuator
is
changedfroma capacitydivider
to a
resistive
divider system by the addition of a kit
of parts available under
@
Stock No. 400D-95B. The
instructions supplied with thekit giveallnecessary de-
tails
for changing the InputAttenuator ResistorBoard.
Basic calibration and frequency responseadjustments
will
be required after this modification has been
completed.
IC
L/
I.
MODEL 400D SERIAL NO. 25970 AND BELOW
MODEL 400H/L SERIAL NO. 5225 AND BELOW
The value of resistor R45 can bevaried to control low
frequency response
if
cathode resistors R38, R47, and
R53 are changed from 120 ohms to 100ohms
&lo%,
1
watt.See SectionIV stepM1-d. Thevtvm performance
will
be the same after changing the resistors but low
frequency response adjustments aresimplified.
CRYSTAL
DIODE
REPLACEMENT
Special high-performance junction type silicon diodes
areavailable for replacement of diodes CR1 andCR2.
These special diodes aremanufactured by
@
and are
available under
@
Stock No. G-29B-5. Orderdirectly
from the factory or from your
@
Sales Office.
The
@
Stock No, 212-1N82S diodes once specified for
CR1 and CR2 have been superseded by the superior
G-29B-5 diodes. The cathode end of the diode has
a
gold plated
wire.
The anode end of this diode has a
silver
plated
wire.
The G-29B-5 diodes have a junction that
is
less
than
1/2 mil in diameter. If the diodes aredropped, a
mechanical failure may occur at the junction.
After
installation the diodes
will
withstand any shock that
the entire instrument can withstand.
Voltage calibration and frequency response should be
checked and adjusted after replacing
V1,
V2, V3,
V4,
V5, CR1, or CR2.
4
00665-3

*.
4OOD-2C Page 3
SECTION
111
-
TEST EQUIPMENT REQUIRED
The following equipment
is
required to test and cali-
brate
@
Vacuum Tube Voltmeter Models 4WD, 400H,
and 400L.
A.
A
dc voltmeter capable of measuring
250,
6.3,
12.6 volts. This voltmeter musthave a
sensitivity
of 1000 ohms/volt or better.
A
vtvm such as the
@
Model 410B
is
satisfactory,
B.
An
@
Model 738AR (formerly
@
Spec. 23678)
Voltmeter Calibration Generator or equivalent.
Model 738AR generator will deliver a 400-cps output
voltage from 0.3 millivolt rms to 300 volts
rms
with
an accuracy of &0.25%and not more than 0.2%
hum
and distortion. This generator will also supply
+
dc
or -dc voltages from 0.3 millivolt to 300 volts for
calibration of dc voltmeters.
C. An
@
Model 739AR (formerly
@
Spec. 23679)
VTVM Frequency Response Generator. Thisgen-
erator has an internal signal source to cover
the
fre-
quency range from 350 kc to
11
mc.
Up
to a 3-volt
output signal can be obtained. The internalattenuator
and reference voltmeter are designed for frequencies
from 10 cps to
11
mc. Internal impedance
is
50
ohms.
D.
An
@
Model 200s (formerly
@
Spec. 23680) Wide
Range Oscillator. This oscillator has aninternal
impedance of
50
ohms and will deliver a 3-volt signal
from 5 cps to
600
kc. Use
with
Model 739AR VTVM
Frequency Response Generator.
b
E.
A
battery operated oscillator covering 60 and 120
cps with an output of at least
1
volt and not more
than
1%
distortion.
F.
A
square wave generator capable of delivering a
2-volt peak-to-peak
1
kc signal, $The@Model
211A
Square Wave Generator ortheinternal calibrator
in
the
@
Model 150A High Frequency Oscilloscopecan
be used.
G.
A
high frequency oscilloscope such as the
@
Model 150A.
H.
The
@
Model 739AR VTVM Frequency Response
Gen-
erator and the
@
Model 200s Wide Range Oscillator
aredesigned to
be
operated together
when
ma
quency response measurements. These
tw
ments greatly increase the speed and accuracy of
frequency response measurement.
The frequency response adjustment procedure given
in Section
IV
is
particularly suited for use
with
Model 739AR and Model
2005
instruments. Theinstru-
ments
in
the following list are suitable alternates.
--
A
low distortion oscillator covering the frequency
range from 10 cps to at least 6 or 7 mc and an output
voltage of at least 3.0 volts rms. The
($9
Model 650A
Test Oscillator will meet these requirements,
--
An rms reading, average responding, acvoltmeter
with a known frequency response from 10 cps to at
least 4.0 mc. The reference voltmeter can be an
@
Model 400H or Model 400L.
A
thermocouple type of
reference meter can also be used. Absolute voltage
values arenot neededwhen makingfrequency response
measurements.
An
adjustable line voltage source.
SECTION
IV
-
TEST
&
CALIBRATION PROCEDURE
When all the following procedures aretobecompleted,
they can most easily be done in the order listed. In
many instances, only one or two tests will be needed
and they can be done without completing all other
tests. For example, basic calibration can be checked
and adjusted at any time without making any other
adjustments.
A
10 to 15-minute warmup and a check of
the
power
supply output voltages
is
always recommended before
making any other tests or adjustments.
The specifications for your
@
Model 400D, 400H, or
400L Vacuum Tube Voltmeter are given
in
the front
of the manual supplied
with
the
vtvm. The following
test procedure contains extra checks to help you
analyze a particular instrument. These extra checks
and the data they contain cannot be considered as
specifications.
NOTE: The test frequencies and the voltages specified
in
many of the steps
in
this
procedure are based upon
the use of
the
test equipmentlisted
in
Section 111. Other
frequencies and voltages canbe used,
Any
vtvm can be
adjusted for optimum performance on the range you
most commonly
use.
L
00665-2
A.
SETTING MECHANICAL
ZERO
IN
MODELS400D
QQ
1)
Allow
400D
20
minute warm up. Turn instrument
off.
2)
Rotate mechanical zero-adjustment screw clock-
wise
until
meter pointer
is
to
left
of zero and moving
upscale toward zero.
Continue to rotate adjustment
screw
clockwise;
stop
when pointer
is
right on zero,
If
pointer
overshoots zero, repeat
this
adjustment.
3)
When pointer
is
exactly on zero, rotateadjustment
screw approximately 15 degrees counterclockwise.
This
is
enough to free adjustment screw from the
meter suspension,
If
pointer moves during this
step repeat entire adjustment.
B.
SETTING MECHANICAL ZERO
IN
MODEL 400L
The special meter
in
the 400L
is
adjusted
with
the vtvm turned on since the meter pointer rests
against the stop at the left end of the scale
when
the
instrument
is
turned off.

Page
4
I
In
most 400L instruments the mechanical zero
is
pre-
set
during manufacture of the meter movement, The
adjustment screw
in
such meters
is
inoperative. Most
400L instruments will have no adjusting screw on the
front of the meter case.
The following procedure
is
for use only
with
those
instruments
in
which themechanical adjustment screw
is
effective.
1) Connect a 1.0 volt rms, 400 cps signal from
the
Voltage Calibration Generator to the 400L INPUT
terminals. Set the 400L to the 1-voltrange and adjust
the feedback control (R29) for a
full
scale meter
reading of 1.0 volt. Any convenient range could also
be used along
with
a corresponding change in input
signal level. The input signal frequency
is
also not
critical.
2) Switch
the
Calibration Generatortodeliver a signal
of 0.3 volt, or 0.3 of the signal level used
in
step
1.
Set the meter mechanical zero adjusting screw to ob-
tain a reading that
is
0.3 of the reference reading
in
step
1.
Use the same vtvm rangefor both
steps
1
and
2.
If
you overshoot, continue to rotate
the
screw
clockwise and again approach
the
0.3 point from the
high side of the scale, Thescrew should not be turned
counterclockwise during
this
procedure.
3) Repeat steps
1
and
2
until
no further improvement
can be noted. Compromiseadjustment of themechani-
cal zero can be made for optimum tracking.
After
final adjustment, cover the
screw
with a small piece
of black tape.
1
I
C. CHECK REGULATED POWER SUPPLY
1)
The
B+
voltage at the outputof the regulated power
supply
should be 250 volts
i5
volts. Measure this
voltage between the chassis and the cathode of the
series regulator tube
with
the
line
voltage
set
to
115volts.
2)
Vary the line voltage between 103 and 127 volts.
The regulated
B+
will
usually
change no more than
2 volts from one extreme to the other, Ripple volt-
age
in
the
regulated
B+
is
usually 3millivolts or
less
under these same test conditions.
The dc voltage at the plate of the
series
regulator
tube
or at the cathode of
the
rectifier tube should be
between
400 and 420 volts with a 115-volt line, Low
voltage at this point may be from adefective rectifier
tube,
filter
capacitor, or power transformer.
To
check the rectifier tube,connectadcvoltmeter be-
tween chassis and the rectifier cathode. Reduce
line
voltage from 115 to 103volts. The voltmeter reading
should drop as line voltage
is
reducedandthen remain
steady.
If
the dc voltage continues to drop at a slow
rate, the rectifier tube
is
probably weak and should
be replaced.
If
the regulated
B+
voltage
is
not correct, replace-
ment of any or
all
four tubes in the power supply may
be
necessary.
If
tube replacement does not correct
the dc voltage, precision resistors R62 and/or
R64
may have changed value and should
be
replaced. Ab-
normal current drain caused by component failure
elsewhere in the vtvm can result in poor power sup-
k
\
ply regulation,
400D-2C
Excessive ac ripple may be from a defective tube in
the power supply other than
the
rectifier tube, Ca-
pacitor C36 may be open,
D.
SET DC HEATER VOLTAGE
1) Adjust control R66 to
set
the dc heater voltage for
tubes
V1
and
V2
to 6.3 volts rt0.2 volt. The dc volt-
ages across
the
heaters of tubes V3 and
V4
must also
be 6.3 volts rt0.2 volt.
DO
NOT USE
A
VOLTMETER
THAT IS CONNECTED TO
A
COMMON
GROUND
WITH
THE VTVM UNDER TEST WHEN MEASURING THESE
HEATER VOLTAGES.
A
SHORT CIRCUIT WILL
RESULT. Slight readjustment of control R66 will
often bring these two voltages
within
tolerance.
2)
If
both voltages cannotbe
set
to6.3volts,
f
0.2 volt,
adjust R66 to bring the lowest of the two voltages
within tolerance. Connect a resistor
in
arallel with
the two heaters with the highest voltage. )?he correct
resistor value
will
enable you to bring
bo*
heater
voltages within tolerance by readjusting control R66.
Use only one resistor
in
parallel
with
one pair of
tubes at a time.
A
resistor value below 220 ohms
1
watt should not be used.
3)
If
you are unable to obtain the correct heater
voltage aftercompleting steps
1
and 2, checkelectro-
lytic capacitors
in
the heater circuit.
If
both heater
voltages are low, check selenium rectifier
SR1.
E.
INPUT DIVIDER CIRCUIT IDENTIFICATION
1)
An
identification of the type of input circuit
will
enable you to select the proper
test
required for your
instrument. Instruments are classified by type of
input circuit into two general groups:
a. Models 400D, serial001-34370and below;Models
400H/L, serial 001-11226 and below
,
.
,
these
instruments may have either a “capacitive input
divider” or a
“resistive
input divider”. Com-
plete steps
2
through 6 todeterminewhich one
is
present.
b. Models 400D/H/L with serials prefixed 017- and
048-
. .
,
all these instruments employ a
“re-
sistive divider”. Omit steps
2
through 6 and
proceed with Section IV-F.
2) Set the vtvm to the 1.0 volt range and connect a
1.0 volt rms, 400 cps signal from the Calibration
Generator to the INPUT terminals.
Any
convenient
range higher than the 1-volt range can
be
used. The
signal frequency should be approximately 400 cps.
3)
Rotate capacitor C4 (on input circuit board) one
full turn while watching the vtvm meter reading. The
meter reading will vary only about
547,
in
some instru-
ments and approximately
5v0
in others.
4)
If
the meter indication varies approximately
5vo,
capacitor C4
is
a Voltage Calibration Adjustment,
This
will
be referred to as a “CAPACITIVE INPUT
DIVIDER” circuit in the balance of the procedures
in these Service Notes.
00665-3

400D-2C Page 5
5)
If the meter indication varies approximately
547,,
capacitor C4
is
a Frequency Response Adjustment.
This
will
be referred to as a “RESISTIVE INPUT
DIVIDER” circuit in the balance of the procedures
in these ServiceNotes.
i/
6) Mark the type of input circuit on the input
circuit
shield, This reference
will
be used in later steps
of this Test Procedure.
F. INPUT CIRCUIT PRELIMINARY FREQUENCY
’RESPONSE
ADJ
USTMENT
2)
For Models 400D/H/L with serials prefixed 017-:
a. Connect a
1.0
volt rms, 400 cps, signal from
Voltmeter Calibration Generator to INPUT of
vtvm. Switch vtvm to
1.0
volt range.
b. Adjust
RlOl
for a vtvm reading of
1.0
volt.
I.
MISCELLANEOUS CHECKS
NOTE:
All
checks in this section aremade with
the vtvm cabinet in place.
This adjustment
is
for “RESISTIVE INPUTDIVIDER”
circuits only:
1)
Connect a
1
kc, 2 volt peak-to-peak, square wave
signal to the INPUT
of
the vtvm under test. Connect
the OUTPUT terminalsof the samevtvm tothe vertical
input of a high frequency oscilloscope such as the
@
Model 150A.
2) Switch the vtvm to the
1.0
volt range and adjust
capacitor C4 for the best square wave pattern on the
oscilloscope.
G.
BASIC CALIBRATION (SETTING AMPLIFIER
GAIN)
1) For Models 400D serial 001-34370 and below and
Models 400H/L serial 001-11226 and below:
Connect a 0.3 volt rms, 400 cps signal from the Cali-
bration Generator to vtvm INPUT. Switch the vtvm
to 0.3 volt range and adjust the feedback control,
R29, to obtain a reading of
0.3
volt.
2) For Models 400D/H/L with serialsprefixed 017-:
Connect a 0.001 volt rms, 400 cps signal from the
Calibration Generator to vtvm INPUT. Switch the
vtvm to the 0.001 volt range and adjust the feedback
control, R107, to obtain a reading of 0.001 volt.
i/
H.
BASICCALIBRATION (SETTING INPUT DIVIDER)
1)
For Models 400D serial 001-34370 and below and
Models 400H/L serial 001-11226 and below:
a. Connect a 1.0 volt rms, 400 cps, signal from
Voltmeter Calibration Generator to INPUT of
vtvm. Switch vtvm to
1.0
volt range.
b. For “CAPACITIVE INPUT DIVIDER” circuits,
adjust C4 for a reading of 1.0 volt.
c. For “RESISTIVE INPUT DIVIDER” circuits, the
vtvm indication
will
normally be 1.0 volt.
If
reading
is
high, decrease value of pad (R87) in
L/
parallel with R3.
If
reading
is
low, increase
value of pad (R87). Resistor R3andpad R87 are
on input circuit board.
00665-2
1) Noise and Switching Transients
-
This check
will
vary with the voltmeter model. Models 400Dand 400H
have one method while the400Lhasa different method.
a. For 400D and 400H VOLTMETERS
-
Plug a
shielded connector
((8
Stock No. 1251-0019)over
the INPUT terhinals of the vtvm under
test,
A
lO0,OQO ohm resistor should be connected be-
tween the terminals inside this shielded plug.
The residual reading on the 0.001 volt scale
will
normally not be more than 0.00005 volt
(5%
of
full scale).
b. For 400L VOLTMETER
-
Connect a 0.0003 volt
rrns (0.3 millivolt) signal of about 400 cps from
the Calibration Generator
to
the INPUT termi-
nals, The voltmeter reading should be steady
with the range switch inthe0.001position. Noise
in
V1
or V2
will
cause this reading to vary
erratically.
c.
Connect the 100,000 ohm shielded resistor
(see
step a) between the INPUT termirials. Rotate
the range switch through all 12 positions in both
directions. The meter needle may be momen-
tarily deflew as high as
full
scale between
some switch positions. Themeterpointershould
always drop back to zero at a uniform rate with-
out pause or a sudden change in the rate of fall.
d. Remove the shielded 100,000 ohm resistor and
connect a
0.001
volt rms,400cps signalfrom the
Calibration Generator to the INPUT terminals,
The voltmeter reading should be steady with the
range switch in the 0.001 position.
If the results obtained in this
test
arenot satisfactory,
check tubes
V1
and V2, all coupling capacitors,
elec-
trolytic capacitors
in
screen and plate circuits, V2
plate load resistor, and cathode bypass capacitors.
a. Connect a 0.001 volt rms, acsignaltothe INPUT
terminals and set the vtvm to the 0,001 volt
range. Hold your hand palm-upward and sharply
rap the front of themetercasewithyour knuckle.
bJ
The pointer
will
usually not move more than,.
about 1/8 inch along the meter scale.
b. Repeat step a at 300 volts on the300-volt range.
The results obtained should be the same.
2) Check for Microphonics

Page 6
Replace
V1
and/or
V2
to remove excessive micro-
phonics. Pre-selected tubes are available from@for
V1
and
V2.
See Section
I1
of these Service Notes for
details,
3) Check Output
vs
Shock
a. Connect a 1.0 volt rms, ac signal to the INPUT
and set
the
vtvm to the 1-volt range. Connect
the vtvm OUTPUT to an oscilloscope and adjust
oscilloscope to display several cycles.
b. Strike either top front corner of the instrument
with
the palm of your hand, There should be no
sudden change
in
amplitude nor a momentary
collapse of the pattern. This test will detect
another
type
of microphonic tube or poor elec-
trical connections
within
the vtvm.
4)
Check Beat Notes at 60 and 120Cycles
a. Connect a battery operated oscillator to the
IN-
PUT terminals of the vtvm. Set
the
range switch
to the 1-volt range, Adjust the oscillator output
to provide a vtvm reading of 0.9 volt at about
58 cps. Adjust
the
oscillator frequencytoobtain
maximum meter swing which will normally not
be more than about 1/8
in.
alongthemeter scale.
b. Repeat
step
a at 120 cps. The maximum meter
swing will usually not be more thanabout 1/8
in.
along
the
meter scale.
High beat notes areusually caused by defective tubes
anywhere in the instrument.
J.
RECHECKDCHEATERVOLTAGE
Check the dc heater voltage by
the
method given
in
paragraph
D.
If
either electrolytic capacitor
in
the heater circuit
has been replaced, a heat-run of several hours should
be allowed.
After
the
heat-run to form
the
capacitor
plates, reset
the
heater voltage.
K.
CHECK CALIBRATION
AND
TRACKING
1).Check full scale accuracy
of
eachvoltmeter range.
Use
the Voltmeter Calibration Generator. The cali-
bration should be
within
*2% of full scale for a 400D
Voltmeter or
ilg
of full scale for a 400H or 400L
Voltmeter, The test voltage should be between 50 cps
and 500 kc. Avoid using the power line frequency or
a harmonic of
the
power line. Refer to
the
accuracy
specifications
if
you
use
a test frequency outside of
this range.
2) Check meter trackingon anymid-range. The 1-volt
range
is
usually convenient.
A
stickymetercan cause
the vtvm to be outside of
the
calibration specifications.
Defective diodes for CR1 and CR2 can also introduce
excessive tracking error. Refer to Section I1of these
Service Notes for details on suggested replacement
diodes.
400D-2C
L. CHECK EFFECT OF LINE VOLTAGE CHANGE
1) Connect a sine wave signal to the INPUT of
the
vtvm under
test,
Use
a convenient mid-range and
adjust the input signal amplitude for a convenient
ref-
erence level such as
0.9.
Use
any frequency within
the
frequency range of the voltmeter. The line volt-
age should
be
at 115volts foratleast
2
minutes before
setting your reference level.
2) When
the
line voltage
is
changed from 115 to 103
or from 115 to 127 volts, the indication on the vtvm
under test
will
normally not changefrom
the
reference
level by more than &2%of full scale after a 2-min-
Ute
period.
These
effects
are more noticeable at the upper and
lower limits of thevtvm frequencyrange.
If
the change
is
excessive, check tubes V5 through
V1
in
that order,
M.
FREQUENCY RESPONSE ADJUSTMENT
In
most applications, frequency response adjust-
ments will not be necessary; particularly
if
the vtvm
is
used at frequencies below approximately 500 kc.
The results obtained will depend entirely upon the
“reference voltmeter” used to monitor input signal
level to
the
vtvm under test. You are urged to avoid
making frequency response adjustmentsunless the
fre-
quency response characteristics of your reference
voltmeter are accurately known. The following fre-
quency response adjustment data
is
given for use in
those cases where frequency response
is
critical and
the required
test
equipment
is
available.
The voltage at the input terminals of the vtvm under
test
must be monitored by the reference voltmeter,
The reference voltmeter indication at 400 cps
is
called “reference level”
in
these instructions,
The
adjustments arelisted
in
a sequence that
is
most con-
venient
when
using the
@
Model 739AR and
200s
in-
struments described in Section
111.
If
you use other
equipment, you may have to change the sequence to
suit
the
instruments.
1) For Models 400D serial 001-34370 and below and
Models 400H/L serial 001-11226 and below:
Note: For Models 400D/H/L with serials prefixed
017-,
proceed to step
2.
a. Adjust
C21
at
4
mc on the .001 volt range after
establishing a 400 cps ‘‘reference level”
on
the
same range.
b. Adjust response at
1
mc on the ,001-volt range.
Use the same ‘‘reference level” as step a.
Capacitor C26
in
the plate circuit of
V4
can be
changed in value between limits of 15and 82 pf to
control
1
mc response.
If
you change C26,
repeat step a.
c.
Frequency response above
4
mc can be roughly
adjusted by adding or adjusting the values of
capacitor C40 and resistor R82
in
the cathode
circuit of
V2.
00665-2

400D-2C
If
you change or add
these
parts, repeat steps a and b.
Use
same range and reference level as step a.
A
re-
sponse that “falls-off’’ above
4
mc
is
more desirable
than one that
rises.
d. The 10 to 20 cps.responseadjustment varies
with
voltmeter circuitry.
If
cathode resistors R38, R47, and R53 for tubes V3,
V4, and V5 respectively all have values of 100 ohms,
the value of R45
in
the
plate circuit of
V4
can be ad-
justed between limits of 0.75 and
1.0
megohms to
adjust the 10 to 20 cps response.
In
any instrument, to increase the 10cps indication,
remove R80
if
present in
V2
grid circuit. Add R81 in
V3 grid circuit
if
additional increase
is
needed after
R80 removal. Conversely, to decrease
the
indication,
remove R81 and add R80
if
necessary. Either but not
both resistors can be added. Both resistors can be
omitted.
A
value of
2.2
megohms or higher should be
used for R80 or R81. Check tubes, cathode capacitor
C20, and coupling capacitors
if
you findthat a resistor
value below 2.2 megohms
is
required.
e. Adjust C14 at
4
mc on the .003-volt range after
establishing a 400 cps “reference level” on
the
same range.
f.
Adjust C16 at
4
mc on the .Ol-volt range after
establishing a 400 cps “reference level” on
the
same range.
g. Check frequency response on the .03, .l, and .3
volt ranges. Establish a 400 cps “reference
level” for each range and then checkresponse at
4
mc.
If
an error greater than
f
5% of full scale
is
noted, make a compromise adjustment of
C21.
If
you change C21, repeat steps a, b, c,
d, e, and
f.
The compromise setting of C21
must be used when repeating
step
a.
h.
For “CAPACITIVE INPUT DIVIDER” Circuits
See step
E
in Section
IV
to de-
Skip
step
i.
termine
input
circuit type.
i.
For “RESISTIVE INPUT DIVIDER” Circuits
Adiust C4 at 20 kc on the
1.0
volt range after
esiablishing a 400 cps “reference level” on
the
same range.
j.
Adjust R6 in the input divider to bring the
4
mc
response
within
specifications on the
1
.O-volt
range after establishing a 400 cps “reference
level” on the same range.
This resistor consists of several parallel resistors.
Increasing the resistance of R6 will raisethe response
at
4
mc. Lowering
the
resistance will decrease
the
4
mc response.
00665-2
Page 7
k.
The response of the 3-volt range can now be
checked.
If
other ranges have been properlyad-
justed, this range
will
be within specifications.
The response of any range can now be checked
at any frequency between 10 cps and
4
mc.
2)
For Models 400D/H/L
with
serials prefixed 017-:
a. Adjust C102
“HIGH
FREQUENCY COMP” at
4
mc on
the
0,001 volt range afterestablishing a
400 cps “reference level” on
the
same range.
b. The oscillator should now be tuned through the
band of
4
mc to 10 mc. Note the voltmeter indi-
cation during
this
time;
If
the readingincreases
more than
2%
above the
4
mc level, adjust
AM-
PLIFIER BIAS control R119 counterclockwise,
and repeat
4
mc ad‘ust
(step
a above). Repeat
the
4
mc response. Note: Be
sure
reference
meter
is
set
at SET LEVEL.
this
procedure
unti
II
peaking
is
less than
2%
of
c. Set oscillatoroutput to“reference level”. Adjust
LOW FREQUENCY RESPONSE control R118 to
bring the 10 to
20
cps response within specified
limits.
If
R118 will not bring both
the
10 and 20
cycle response into specifications, the AMPLI-
FIER BIAS control R119 must be readjusted
so
that R118 can bring the 10 and20cycle response
within
limits.
d. If R119
is
adjusted during the low frequency re-
sponse calibration (step c),
it
will be necessary
to repeat the high frequency response adjust-
ment in step b. The adjustment of R119 will be
a compromise to meet both low and high
fre-
quency specifications.
e.
Adjust C14 at
4
mc on the
0.003
volt range after
establishing a 400 cps reference level
on
the
same range.
f.
Adjust C16 at
4
mc on the .01 volt range after
establishing a
400
cps reference level on
the
same range.
g. Adjust C4 at 20 kc on the 1.0 volt range after
establishing a 400
cps
reference level on the
same range.
h. Adjust R6 in the
input
divider to bring the 4 mc
response
within
specifications on the 1.0 volt
range after establishing a 400 cps reference
level on the same range.
R6
consists of several
resistors connected
in
parallel. Increasing the
sponse at
4
mc. Lowering the resistance will
decrease the
4
mc response. Note: Be sure
input shield
is
in
place before taking reading.
resistance of R6
will
raise the frequency
re-
\
N.
FINAL CHECK
AND
ADJUSTMENT
in steps
G
and
H.
Repeat
the
Basic Calibration procedures given

Page
8
400D-2C
'
'
.
SECTION
V
-
TEST FOR INSTRUMENT CERTIFICATION
To
certify a
400D,400H,
or
400L
Vacuum Tube Volt-
meter
it
is
only necessary
to
check
the
accuracy
specifications, These specifications aregiven in the
Operating and Servicing Manual supplied with your
vtvm.
Certification
is
accomplished without removing the
instrument cabinet and without making anyinstrument
adjustments, Suggested procedures for checking the
accuracy specifications are given in Section
IV
of
these Service Notes in steps
K,
L,
and
M.
The procedures
in
steps
K,
L,
and
M
contain adjust-
ment methods, These adjustments must
be
omitted
when certifying an instrument. Actually,
if
aninstru-
ment meets specifications no adjustments will be
necessary.
d
00665-2

Page
9
W
la

Page
10
2
.
'i
400D-2C
"
&,,
I
00665-2

400D-2C
Page
11
I
I
1
..-
4
No
no
e0
nO
aY
00665
-
2
Other manuals for 400D
4
This manual suits for next models
2
Table of contents
Other HP Measuring Instrument manuals
Popular Measuring Instrument manuals by other brands
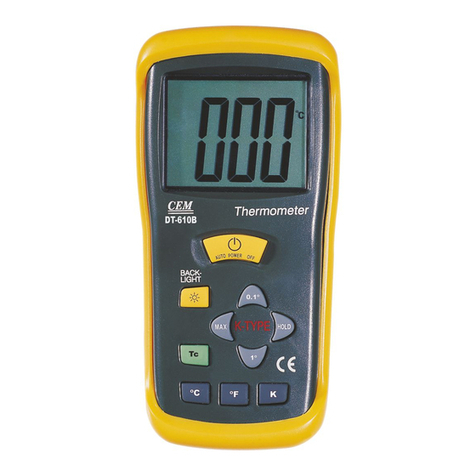
CEM
CEM DT-610B operating instructions
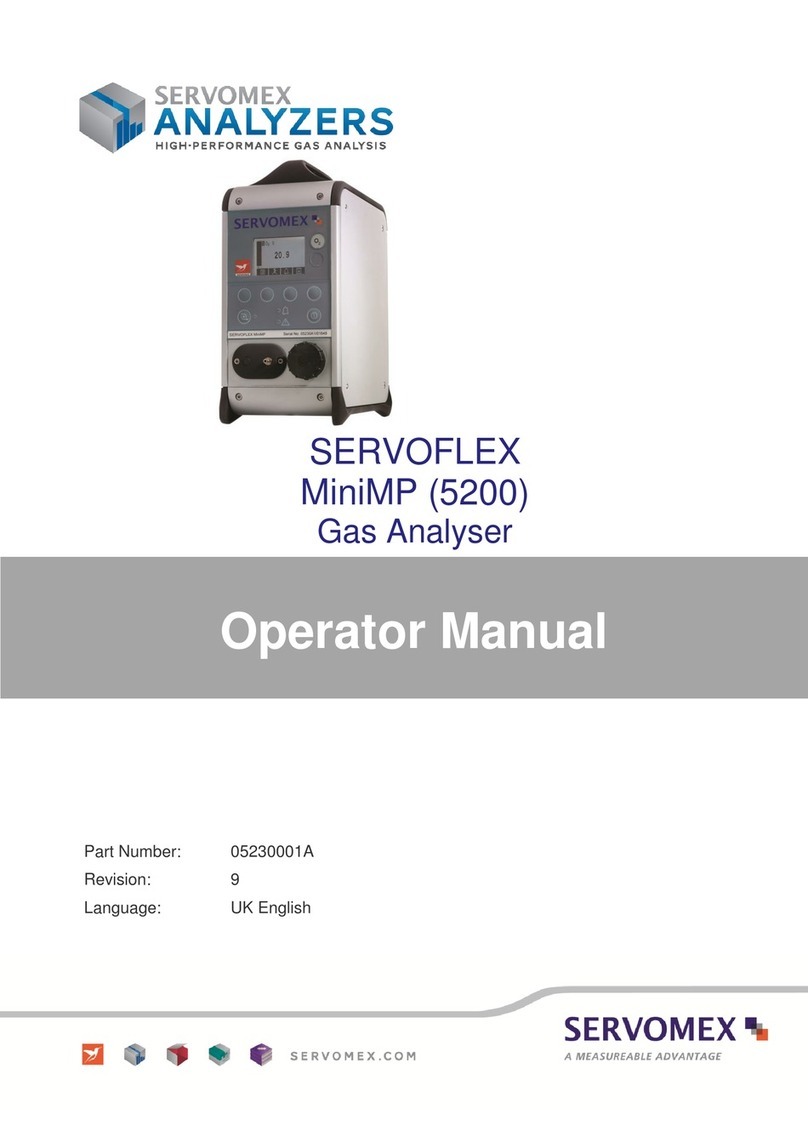
Servomex
Servomex SERVOFLEX MiniMP Operator's manual
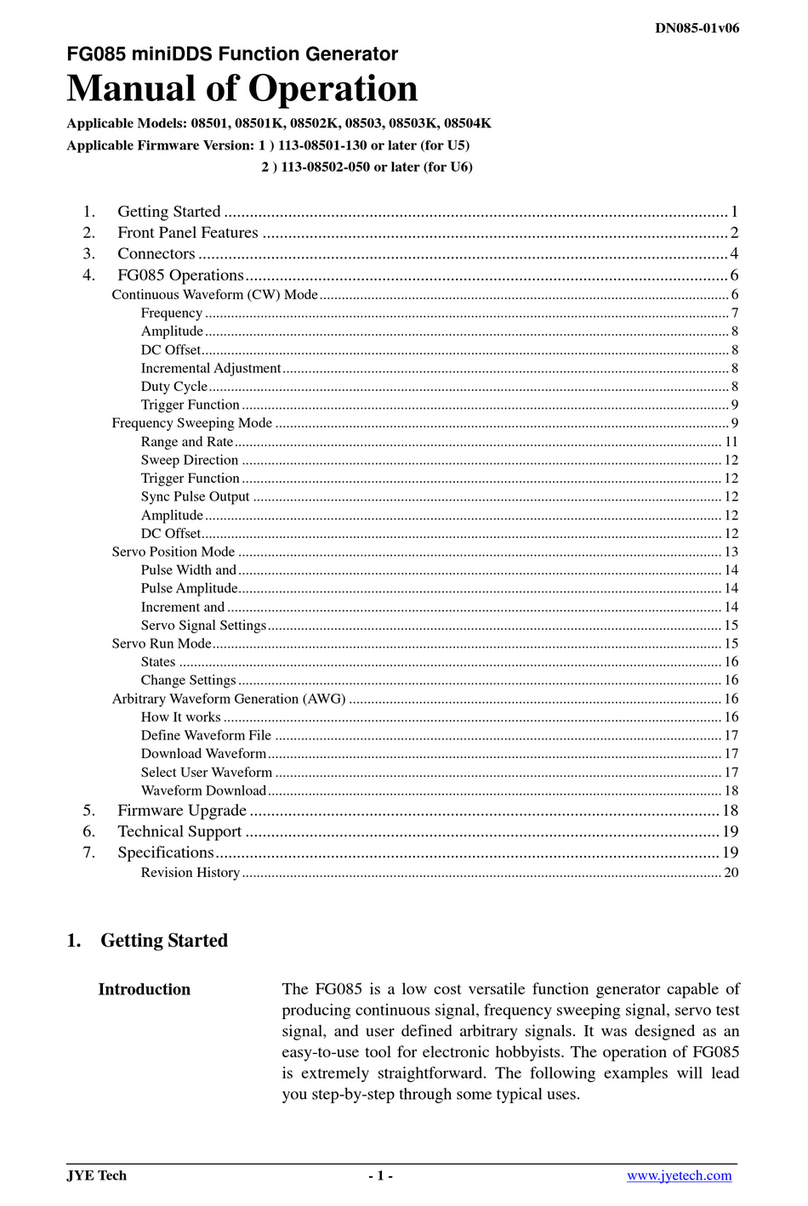
JYE Tech
JYE Tech FG085 Function Generator Operation manual
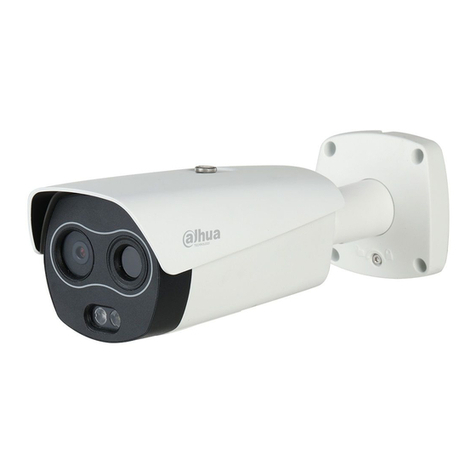
Dahua Technology
Dahua Technology DH-TPC-BF5421-T Installation and configuration guide
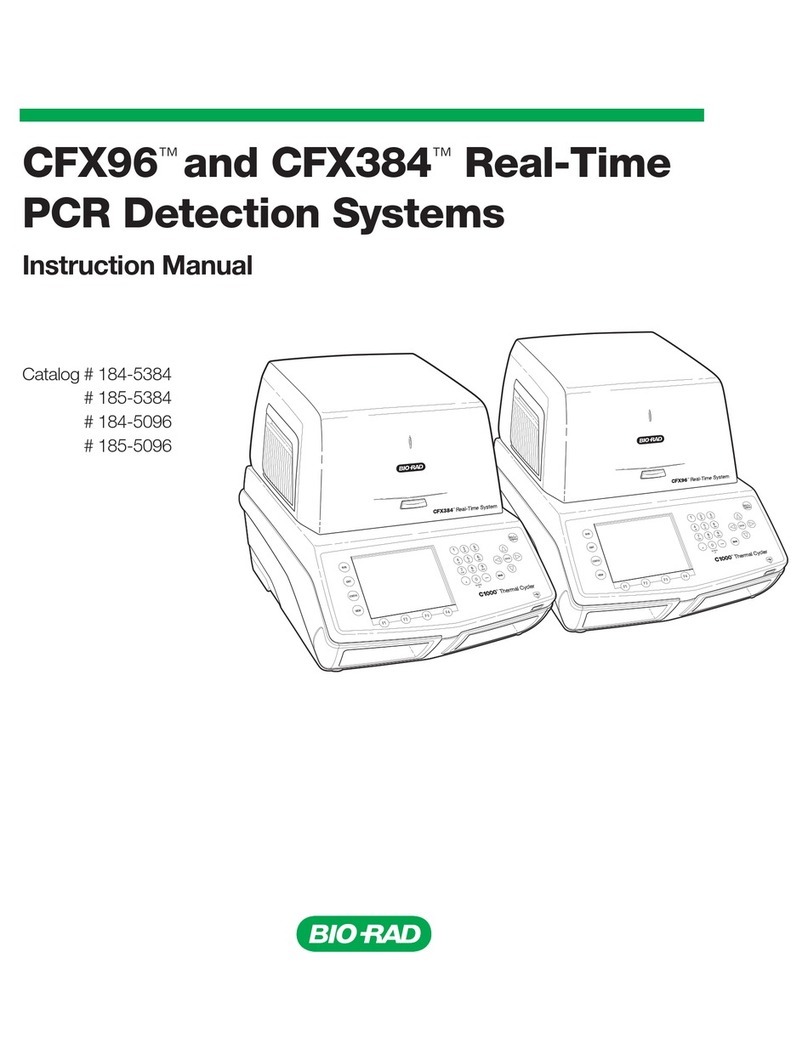
BIO RAD
BIO RAD CFX96 Touch instruction manual
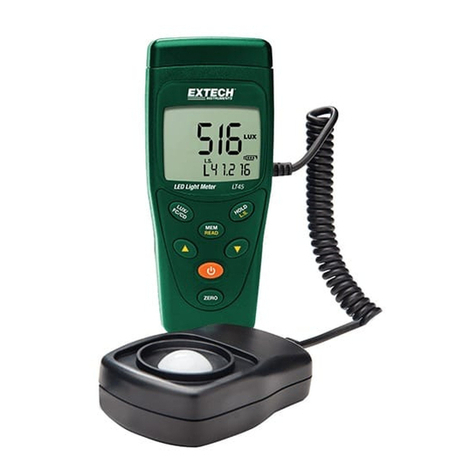
Extech Instruments
Extech Instruments LT45 user manual